Protectowire PIM-530 Series Operating instructions

An ISO 9001 Registered Company
PIM-530 Series Interface Module
with Modbus Over RS-485
Installation and Operation Guide
APPROVED

MAN-2007 Last modified 4/2/2020 Contains
updates included in Firmware v1.3.5
2020 The Protectowire Co., Inc.
60 Washington Street
Pembroke, MA 02359
Phone 781-826-3878 • Fax 781-826-2045
E-Mail: pwire@protectowire.com
WWW.PROTECTOWIRE.COM
PIM-530 Series Interface Module
Installation and Operation Guide

Table of Contents
How Digital Linear Heat Detectors Work
igital Linear Heat Introduction . . . . . . . . . . . . . . . . . . . . . . . . . . . . . . . . . . . . . . . . . . . . . . . . . . .1
igital Linear Heat etection Operation . . . . . . . . . . . . . . . . . . . . . . . . . . . . . . . . . . . . . . . . . . .1-2
The PIM-530 Interface Module
General Information . . . . . . . . . . . . . . . . . . . . . . . . . . . . . . . . . . . . . . . . . . . . . . . . . . . . . . . . . . . .3
escription . . . . . . . . . . . . . . . . . . . . . . . . . . . . . . . . . . . . . . . . . . . . . . . . . . . . . . . . . . . . . . . . . . .3
Specifications . . . . . . . . . . . . . . . . . . . . . . . . . . . . . . . . . . . . . . . . . . . . . . . . . . . . . . . . . . . . . . . . . .4
4-20mA Output Information . . . . . . . . . . . . . . . . . . . . . . . . . . . . . . . . . . . . . . . . . . . . . . . . . . . . . .5
Installation and Wiring . . . . . . . . . . . . . . . . . . . . . . . . . . . . . . . . . . . . . . . . . . . . . . . . . . . . . . . . . .6
Mounting & Location . . . . . . . . . . . . . . . . . . . . . . . . . . . . . . . . . . . . . . . . . . . . . . . . . . . . .6
Wiring iagram . . . . . . . . . . . . . . . . . . . . . . . . . . . . . . . . . . . . . . . . . . . . . . . . . . . . . . . . .6
etector Wiring . . . . . . . . . . . . . . . . . . . . . . . . . . . . . . . . . . . . . . . . . . . . . . . . . . . . . . . . .7
Interface Wiring . . . . . . . . . . . . . . . . . . . . . . . . . . . . . . . . . . . . . . . . . . . . . . . . . . . . . . . . .7
Power Wiring . . . . . . . . . . . . . . . . . . . . . . . . . . . . . . . . . . . . . . . . . . . . . . . . . . . . . . . . . . .7
4-20mA Outputs wiring . . . . . . . . . . . . . . . . . . . . . . . . . . . . . . . . . . . . . . . . . . . . . . . . . . .8
Configuration & Feature Selection . . . . . . . . . . . . . . . . . . . . . . . . . . . . . . . . . . . . . . . . . . . . . . . . . .9
Configuration Prerequisites . . . . . . . . . . . . . . . . . . . . . . . . . . . . . . . . . . . . . . . . . . . . . . . . .9
isplay, Menus and Navigation Controls . . . . . . . . . . . . . . . . . . . . . . . . . . . . . . . . . . . . . .9
Initial Power Up . . . . . . . . . . . . . . . . . . . . . . . . . . . . . . . . . . . . . . . . . . . . . . . . . . . . . . . . .9
Accessing the Menu . . . . . . . . . . . . . . . . . . . . . . . . . . . . . . . . . . . . . . . . . . . . . . . . . . . . . .9
Resetting the etector . . . . . . . . . . . . . . . . . . . . . . . . . . . . . . . . . . . . . . . . . . . . . . . . . . .10
etector Type Selection . . . . . . . . . . . . . . . . . . . . . . . . . . . . . . . . . . . . . . . . . . . . . . . . . .11
isplay Units . . . . . . . . . . . . . . . . . . . . . . . . . . . . . . . . . . . . . . . . . . . . . . . . . . . . . . . . . .12
Alarm Point Location (APL) Setup . . . . . . . . . . . . . . . . . . . . . . . . . . . . . . . . . . . . . . .12-15
Time and ate Setup . . . . . . . . . . . . . . . . . . . . . . . . . . . . . . . . . . . . . . . . . . . . . . . . . . . .16
Password Setup . . . . . . . . . . . . . . . . . . . . . . . . . . . . . . . . . . . . . . . . . . . . . . . . . . . . . . . . .16
Factory Restore . . . . . . . . . . . . . . . . . . . . . . . . . . . . . . . . . . . . . . . . . . . . . . . . . . . . . . . . .16
Event History . . . . . . . . . . . . . . . . . . . . . . . . . . . . . . . . . . . . . . . . . . . . . . . . . . . . . . . . . .17
4-20mA Outputs Calibration . . . . . . . . . . . . . . . . . . . . . . . . . . . . . . . . . . . . . . . . . . . . . .18
Testing Notes . . . . . . . . . . . . . . . . . . . . . . . . . . . . . . . . . . . . . . . . . . . . . . . . . . . . . . . . . .19
Inspection of the installation . . . . . . . . . . . . . . . . . . . . . . . . . . . . . . . . . . . . . . . . . . . . . . .19
etection Operation and Testing . . . . . . . . . . . . . . . . . . . . . . . . . . . . . . . . . . . . . . . . . . .19
1. Test Open Circuit Monitoring . . . . . . . . . . . . . . . . . . . . . . . . . . . . . . . . . . . . . . . . . .20
2. Test Alarm Monitoring . . . . . . . . . . . . . . . . . . . . . . . . . . . . . . . . . . . . . . . . . . . . .21-22
Hazardous Location Applications (Factory Mutual Approved Only)
Intrinsic Safety Barrier, Option I . . . . . . . . . . . . . . . . . . . . . . . . . . . . . . . . . . . . . . . . . . . .23
ISB Illustration rawing IL-1626 . . . . . . . . . . . . . . . . . . . . . . . . . . . . . . . . . . . . . . . . .24

Table of Contents
Modbus Over RS-485 Operation Guide
escriptions . . . . . . . . . . . . . . . . . . . . . . . . . . . . . . . . . . . . . . . . . . . . . . . . . . . . . . . . . . . . . . . . . . . . .25
RS-485 Serial Bus . . . . . . . . . . . . . . . . . . . . . . . . . . . . . . . . . . . . . . . . . . . . . . . . . . . . . . . . . . . . .25
Modbus Protocol . . . . . . . . . . . . . . . . . . . . . . . . . . . . . . . . . . . . . . . . . . . . . . . . . . . . . . . . . . . . . .25
PIM-530 Modbus over RS-485 . . . . . . . . . . . . . . . . . . . . . . . . . . . . . . . . . . . . . . . . . . . . . . . . . . .25
Specifications . . . . . . . . . . . . . . . . . . . . . . . . . . . . . . . . . . . . . . . . . . . . . . . . . . . . . . . . . . . . . . . . . . . .26
Port Specifications . . . . . . . . . . . . . . . . . . . . . . . . . . . . . . . . . . . . . . . . . . . . . . . . . . . . . . . . . . . . .26
Protocol Specifications . . . . . . . . . . . . . . . . . . . . . . . . . . . . . . . . . . . . . . . . . . . . . . . . . . . . . . . . . .26
Wiring
Wiring escription . . . . . . . . . . . . . . . . . . . . . . . . . . . . . . . . . . . . . . . . . . . . . . . . . . . . . . . . . . . .27
Wiring iagram . . . . . . . . . . . . . . . . . . . . . . . . . . . . . . . . . . . . . . . . . . . . . . . . . . . . . . . . . . . . . . .27
Example Bus iagram . . . . . . . . . . . . . . . . . . . . . . . . . . . . . . . . . . . . . . . . . . . . . . . . . . . . . . . . . . 27
Configuration Settings
Configuration Settings escriptions . . . . . . . . . . . . . . . . . . . . . . . . . . . . . . . . . . . . . . . . . . . . . . . .28
Accessing the Modbus Menu . . . . . . . . . . . . . . . . . . . . . . . . . . . . . . . . . . . . . . . . . . . . . . . . . . . . .28
Setting the Slave Address . . . . . . . . . . . . . . . . . . . . . . . . . . . . . . . . . . . . . . . . . . . . . . . . . . . . . . . .29
Setting the Parity . . . . . . . . . . . . . . . . . . . . . . . . . . . . . . . . . . . . . . . . . . . . . . . . . . . . . . . . . . . . . .29
Setting the Baud Rate . . . . . . . . . . . . . . . . . . . . . . . . . . . . . . . . . . . . . . . . . . . . . . . . . . . . . . . . . . .30
Modbus Communications
Modbus Protocol Info . . . . . . . . . . . . . . . . . . . . . . . . . . . . . . . . . . . . . . . . . . . . . . . . . . . . . . . . . .30
Register Overview . . . . . . . . . . . . . . . . . . . . . . . . . . . . . . . . . . . . . . . . . . . . . . . . . . . . . . . . . . . . .30
Module Status . . . . . . . . . . . . . . . . . . . . . . . . . . . . . . . . . . . . . . . . . . . . . . . . . . . . . . . . . . . . . . . .31
Event istance Measurements . . . . . . . . . . . . . . . . . . . . . . . . . . . . . . . . . . . . . . . . . . . . . . . . . . . .32
Module Temperature . . . . . . . . . . . . . . . . . . . . . . . . . . . . . . . . . . . . . . . . . . . . . . . . . . . . . . . . . . .32
Initialize / Reset . . . . . . . . . . . . . . . . . . . . . . . . . . . . . . . . . . . . . . . . . . . . . . . . . . . . . . . . . . . . . . .32

1
Introduction to Digital Linear
Heat Detection Technology
Protectowire Linear Heat etector is a sensor cable that detects heat anywhere along its length. The sensor
cable is comprised of two steel conductors individually insulated with a heat sensitive polymer. The insulated
conductors are twisted together to impose a spring pressure between them, then wrapped with a protective
tape and finished with an outer jacket suitable for the environment in which the etector will be installed.
Invented and Patented by The Protectowire Co., Inc. in 1938, igital Linear Heat etectors have been uti-
lized in the fire protection industry for over 80 years.
Ideally suited to industrial high risk hazards as well as many types of commercial applications, Protectowire
Linear Heat etector has unique advantages over other types of detectors, especially when difficult installation
factors or severe environmental conditions are present.
How Digital Linear Heat Detection Works
Digital Linear Heat Detection Operation
To understand how igital Linear Heat etectors work it is important to have an understanding of how they
are constructed.
Figure 1 - igital linear heat detectors are constructed of a twisted pair of spring conductors
coated with a thermoplastic coating designed to soften at a specific temperature. An initiating device circuit
monitors a length of this detector installed in an area to be protected.
Figure 1

2
Figure 2 - When the detector is exposed to heat at a point along its length the thermoplastic coating at that
point softens and the spring pressure between conductors causes them to contact each other creating a short
circuit. The short circuit is sensed by the initiation device circuit which reports an alarm.
Figure 2
This very reliable method of detection has been in use for over 75 years in the fire protection industry and is
ideally suited to industrial high risk hazards as well as many types of commercial applications.
HEAT

The PIM-530 Series
Interface Module
General Information
The Protectowire PIM-530 is a detection control module that is an interface between a main fire alarm
control panel detection circuit or addressable node and Protectowire igital Linear Heat etector. The
module provides one (1) supervised detection circuit that may be field wired for either Class A (Style ) or
Class B (Style B) service. The alarm initiating circuit is capable of operating up to 6,560 feet (2,000m) of
Protectowire igital Linear Heat etector. The PIM-530 initiating circuit is designed to monitor Protectowire
igital Linear Heat etector and also supports other types of normally open contact alarm initiating devices.
Two wire smoke detectors which require initiating device circuit power to operate are not supported.
Description
The PIM-530 operates using standard initiating device circuit technology. When paired with Protectowire
igital Linear Heat etectors, the module provides full supervision and alarm condition monitoring of the
detector loop.
The PIM-530 is designed for easy installation and is available in an optional NEMA-4X rated enclosure for
mounting outside of the host fire alarm control panel or remotely near the hazard to be protected. In order to
ensure proper operation, each PIM-530 module requires regulated resettable external power which is normally
provided by the host fire alarm panel. Each module contains a green “Power-On” LE indicator, one (1) red
“Alarm” LE indicator, and one (1) yellow “Trouble” LE indicator. One (1) set of Form C alarm contacts
and one (1) set of Form C trouble contacts are provided to connect the unit to the host fire alarm panel. The
module also provides two 4-20mA outputs. One allows monitoring of the module status and the other for
alarm point location information.
In addition to the features listed above the standard version of the module, model PIM-530, provides a 4x20
LE backlit LC display and navigation buttons for access to a complete menu driven user interface. Also
available is model PIM-530LT which is intended for use in low temperature applications. The LT version of
the interface module contains no LC display or navigation buttons and no menu accessible user interface.
3

4
Specifications
Electrical
• Power input - Regulated 12 to 24 V C (+10% / -15%) @ 1.6 Watt
• Power Limited, onboard surge and EMI protection devices
Inputs
• One initiating device circuit capable of monitoring up to 6,560 feet (2,000m) of Protectowire
PHSC and PLR igital Linear Heat etectors
• For intrinsically safe applications (Option I), the maximum detector length per zone is 6,560 feet
(2,000m) or less, as permitted by the hazardous location calculation and application
Environmental
• Ambient temperature range:
Standard version (With integrated LC display) -20° to 120°F (-29° to 49°C)
LT version (Without integrated LC display) -40° to 120°F (-40° to 49°C)
Standard & LT Versions FM tested to 140°F (60°C) max
• Humidity: Max. 95% non-condensing
Visual Annunciation
• 4x20 Character LE backlit LC display (PIM-530 only)
• One green “Power” indicator
• One red “Alarm” indicator
• One yellow “Fault” indicator
Status Relay Contacts (Rated 1 amp @ 24VDC Resistive)
• One (1) set of Form C (SP T) Fault Contacts
• One (1) set of Form C (SP T) Alarm Contacts
4-20mA Outputs
• One (1) 4-20mA Output for module status
• One (1) 4-20mA Output for Alarm Point Location Readings
Board Assembly Dimensions
• 6” W x 4” H x 1.5” (15.24cm x 10.16cm x 3.8cm)
•Mounting holes #4 holes at 5.5” (13.97cm) x 3.5” (8.89cm) spacing
Enclosure Option
• 10.5” H x 8.5” W x 4.5” (27cm x 21.5cm x 11.4cm)
• Add 1.6” (4cm) to overall height for external mounting feet
• Clear full view door
• *NEMA 4X Rated (Rating UL listed only)
(Closest IEC equivalent - IP66)
Note: Option I (ISB) increases enclosure size
* Additional enclosures and sizes available. Consult Factory.

5
4-20mA Output Information
Description - The PIM-530 provides two 4-20mA outputs that allow for monitoring of the module status
and active alarm point location reading. These outputs are intended for annunciation purposes only. Module
monitoring is intended to be accomplished using the on board supplied dry contacts connected to a listed or
approved fire detection control panel initiating device circuit.
For Class “A” wiring configurations the status output will also indicate which detector input is currently being
measured by the alarm point location meter. The measurement is alternated between inputs approximately
every 3 seconds with the status output indicating which input is currently being read.
The output levels are detailed below.
Status Output - 4-20mA Output Loop 1:
Fault – 4mA or less
Open – 6mA
Normal – 10mA
Initiating evice Circuit Out Alarm – 17mA
Initiating evice Circuit Return Alarm – 19mA
Note: For systems employing an isolated power source for the 4-20mA loops; Module Power Failure will
report at greater than or equal to 20mA
Alarm Point Location Output – 4-20mA Output Loop 2:
4-20mA Full Scale corresponds to 0-8,000 Feet.
4mA = 0 Feet – 20mA = 8,000 Feet
To calculate current to distance in feet use the following formula:
Current in mA = (I)
(I - 4) / 0.002 = istance in Feet
To convert to Meters:
istance in Feet x 0.3048

Installation and Wiring
Mounting and location – The PIM-530 can be provided as a complete module assembly for installation in
a customer supplied enclosure or pre-mounted in a factory supplied enclosure. Please refer to the specifications
section for enclosure information. When mounting the PIM-530 please follow the installation guidelines
below.
The PIM-530 interface module shall be located in a clean, dry, vibration free environment and shall not be
subjected to temperatures or humidity that exceeds the modules specifications.
The PIM-530 should be mounted in an accessible location where the user interface can be viewed without
obstruction.
The enclosure rating should meet or exceed that which is required for the installation environment. All
enclosure penetrations should be via connectors and/or conduit hardware that meet or exceed the rating of
the enclosure.
To utilize the maximum detector length capacity of the PIM-530, feed cable lengths should be kept to a
minimum by locating the PIM-530 as close to the area of detection as possible.
Wiring Diagram
Figure 3
6
OK
NC NO C NO NC CRTN OUT +V RTN OUT +V
LOOP 2 LOOP 1 FAULT ALARM
GND +24 COM
PWR
+ - + -
OUT RET
ESC
POWER
ALARM
FAULT
ZONE
BOX
FEED CABLE
END LINE
BOX
PROTECTOWIRE LINEAR
HEAT DETECTOR
(CLASS B)
END LINE
RESISTOR
10K 1
2WATT
(+)
(-)
(+)
(-)
(+)
(-)
+ - + -
OUT RET
ZONE
BOX
FEED CABLES
PROTECTOWIRE LINEAR
HEAT DETECTOR
(CLASS A) (+)
(-)
(+)
(-)
ZONE
BOX
(+)
(-)
(+)
(-)
J10
J11
J11
(+)
(-)
POWER
12-24VDC
1.6 WATT
EARTH GND
LCD DISPLAY
STATUS
INDICATORS
NAVIGATION
SWITCHES
Note: If dedicated earth ground is not
available, GND terminal and COM terminal
must be connected to each other.
J9 J13 J12
IDC
FROM HOST
PANEL
(+) (-)
HOST ELD
Note: Connections shown are typical. Other
monitoring scenarios can be congured as
required by the authority having jurisdiction.
(+)(-)
A
RES
SUPPLY (-)
SUPPLY (+)
WIRING TYPICAL
FOR LOOP 1 & 2
SUPPLY OF 5-24VDC
MAY BE
LOCAL OR REMOTE
SEE LOOP 1
FOR WIRING
4-20ma
ALARM POINT OUTPUT
4-20ma
STATUS OUTPUT
SUPPLY @ 12V - 300 Ohms
SUPPLY @ 24V - 800 Ohms
TOTAL MEASURMENT LOOP RESISTANCE
INCLUDING FEED CABLE AND LOAD
RESISTOR NOT TO EXCEED BELOW VALUES
CONNECTION
DIAGRAM #1
Interface Contact wiring 12 AWG to 30 AWG. When
using maximum of two conductors within a single
terminal; 18 AWG Maximum. Wires must be
individually inserted to terminal and not twisted
together as that could aect circuit supervision.
**
** Fault contacts shown normally engergized.
RS-485
CONNECTION

7
Installation and Wiring – (continued)
Wire the system according to this manual using Figure 3 as reference. Wiring should be in accordance with
applicable National and/or Local Electrical Fire Alarm Codes.
Detector Wiring – The PIM-530 provides one (1) supervised detection circuit that may be field wired for
either Class A (Style ) or Class B (Style B) service. The alarm initiating circuit is capable of operating up to
6,560 feet (2,000m) of Protectowire igital Linear Heat etector. The PIM-530 initiating circuit is designed
to monitor Protectowire igital Heat etector and also supports other types of normally open contact alarm
initiating devices. Two wire smoke detectors which require initiating device circuit power to operate are not
supported.
Step 1 - Remove the factory supplied 10K 1/2w end-of-line resistor (ELR) from terminal J11 OUT (+)
and (–). Retain this resistor for installation at the end of the detector run as shown in the Class “B”
field wiring diagram on this page. For Class “A” configuration the ELR shall be removed and
discarded.
Step 2 - Connect the Protectowire Linear Heat etector to the PIM-530 interface module at terminal
J11 as shown in the field wiring diagram (Figure 3) in either a Class “B” or Class “A” configuration.
Wiring Terminations – All terminations and or splices in the detector loop must be made utilizing
Protectowire recommended terminals. Only zone boxes and splicing connectors specifically recommended by
The Protectowire Co., Inc. shall be utilized.
Interface Wiring – The PIM-530 is a detection control module that is an interface between a main fire alarm
control panel detection circuit or addressable node and Protectowire igital Linear Heat etector. The most
common interface connections utilize the two form “C” contacts provided for Fault and Alarm conditions.
Step 3 - Connect the host panel’s initiating device circuit(s) to terminals J13 as shown on the field
wiring diagram (Figure 3). Reference the host panel wiring specifications for correct wiring
configuration and requirements.
Power Wiring – The PIM-530 requires external regulated, uninterruptible C power. The module provides
an internal switching regulator which supports input voltages between 12 to 24 V C (+10% / -15%) @ 1.6
Watt. To implement remote resetting of the module from the host panel, the supplied power may be interrupt-
ed during the hosts panels reset sequence. This “resettable power” function is the only means of resetting PIM-
530LT version of the module which is provided without an integrated user interface.
Step 4 – Connect a regulated 12-24V C resettable power supply to terminal J10 as shown on the field
wiring diagram (Figure 3). See the “Specification” section for power requirements.
Important ! – The PIM-530 must be connected to earth ground via the J10 GN terminal as depicted in the
field wiring diagram. If earth ground is unavailable, for example in vehicle applications, the GN and COM
terminals must be connected to each other with a jumper wire.

8
Installation and Wiring – (continued)
4-20mA Output Wiring – The PIM-530 provides two 4-20mA outputs which allow the status of the module
to be remotely monitored. See the specifications section of this manual and the 4-20mA Output Information
section for additional information on each outputs function.
Step 1 – Connect a regulated 12-24V C regulated power voltage to Loop -1 terminal J9 +V and to
terminal J9 RTN as shown on the field wiring diagram (Figure 3). Repeat this step for Loop - 2.
Step 2 – Select a conditioning resistor value from the list below based on the supply voltage and the
loop resistance of the measurement wiring. The total loop resistance including the resistor value should
not exceed the resistance value shown for the supply voltage.
Supply @ 12V – 300 Ohms
Supply @ 24 – 800 Ohms
Step 3 – Connect the measurement device wiring and load resistor selected in step 2 to terminals J9
OUT and J9 RTN as shown on field wiring diagram (Figure 3). Repeat this step for Loop 2 if second
loop is to be monitored also.

9
Configuration and Feature Selection
Configuration Prerequisites - The PIM-530 must be configured and tested before service. Configuration
and testing of detection equipment shall be performed by competent, qualified personnel having jurisdiction
over this detection equipment. Monitoring equipment connected to the PIM-530 should be bypassed or dis-
abled prior to setup to avoid unintended activation of the monitoring equipment.
Display, Menus and Navigation Controls – The standard version of the PIM-530 has an integrated LC
display and navigation controls which allow user access to the detectors status information and the setup
menu.
Navigation Switches Status Screen
Note: The PIM-530LT version of the detector is provided without an integrated LC display or navigation
controls. The PIM-530LT version of the detector can be field programmed with a separate external program-
ming interface.
Initial Power p – When power is applied, PIM-530 will go through a short boot sequence. The green
power on LE will illuminate and the boot screen will display the currently configured detector type followed
by the firmware version and date. When the boot sequence is complete the module will display a normal status
message.
Boot Screen Status Screen
Accessing the Menu – The PIM-530 menu is password protected. The two levels of access are User level
(USER) and Technician (TECH) level. User level access is limited to etector Reset and Event History view-
ing functions. Technician level access permits full access to the configuration menu.
To enter the Menu press the center navigation button labeled “OK” and the password entry screen will appear.
Note: uring menu access detection monitoring is halted. While detection monitoring is halted the PIM-530
will report a fault condition via the “FAULT” led indicator and the fault contacts will transfer. Normal standby
operation will be restored once the menu is exited and detection monitoring resumes.
MPIETH -DOMECTERFANI530
noitarugifnCo SeleurFeatdan
The
testingand of equipmentdetection beshall
this equipment.detection equipment
to setup to avoid unintended activation of the monitoring equipment.
navigationanddisplayLCD controls which
menu.
LEU
noiSel
service.beforetestedandconfiguredbemust530 Configuration
personnelqualifiedcompetent,byperformedbe
thetoconnectedequipment disabledorbypassedbeshould530
activation of the monitoring equipment.
–The theofversionstandard andhas530
which userallow access andinformationstatusdetectorstheto
Configuration
oversdiction
disabled prior
integratedand
setuptheand
navigationor
programming
powergreen
thebyfollowed
TheNote: detectortheofversion530LT
controls. The 530LT detectorversion
interface.
–When ispower applied,
screenboottheandilluminatewillLEDon
firmware version and date. When the boot sequence is complete the module
/
$
0
5
2
1
Z
R
W
F
H
W
R
U
3
0
$
detector anwithoutprovidedis
detector programmed
&
6
+
3
H
U
L
an integrated ordisplayLCD
separatewithprogrammed
Configuration
oversdiction
disabled prior
integratedand
setuptheand
navigationor
programming
powergreen
thebyfollowed
9
&
6
+
3
H
U
L
Z
R
W
F
H
W
R
U
3
TheNote: detectortheofversion530LT
controls. The 530LT detectorversion
interface.
–When ispower applied,
screenboottheandilluminatewillLEDon
firmware version and date. When the boot sequence is complete the module
&
/
$
0
5
2
1
W
F
H
W
R
U
3
detector programmedcan
applied, throughgowill530
thedisplaywillscreen
and date. When the boot sequence is complete the module
&
6
+
3
H
U
L
Z
R
W
separateawithprogrammed
greenThesequence.bootshortathrough
typedetectorconfiguredly followed
and date. When the boot sequence is complete the module will display a normal status message
and(USER)
9
–The 530
level.(TECH)Technicianand
. Technician level access
/
$
0
5
2
1
0
$
530 menu passwordis protected
isaccesslevelUser limited Detectorto
full access to the configuration menu.
areaccessoflevelstwoThe
EvenandResetDetector tHistory
menu.
levelUserare
viewingHistory
appear.will
will530
standbyNormal

10
Use the left and right navigation buttons to select each character and the up and down navigation buttons to
change the character. Once all characters have been entered press the center navigation button labeled OK to
access the menu.
Entering an incorrect password will produce a password entry error and the user will be returned to the pass-
word entry screen. Press the escape ESC key at any time to return to the main display.
The PIM-530 is supplied from the factory with default passwords for the user and technician level. uring
initial setup it is recommended the technician level password be set to a new value to prevent unauthorized
access to the settings. The User level password can also be set to a new value at the installer’s discretion but is
not required in most cases.
efault User level password = 1000
efault Technician level password = 2000
Once the correct user level password has been entered the setup menu will be displayed. The current user level
will be shown in the setup menu heading as seen below. The available menu items are numbered and can be
accessed by using the up and down navigation keys. The “>” symbol indicates the currently selected menu
item.
The setup menu can be exited at any time by either pressing the “ESC” key or by selecting the “1: EXIT”
menu item and then pressing the “OK” key. While accessing the setup menu the inputs will remain inactive.
After 30 seconds of inactivity the module will automatically exit the setup menu and resume normal operation.
Menu Screen
Resetting the Detector – Once an alarm or short fault condition has been detected the module status will
remain in that condition until the detector has been reset. To reset the detector enter the setup menu and
select the “2: RESET ETECTOR” option.
'
5
2
:
6
6
$
3
3
8
7
(
6
5
(
7
1
(
MPIETH -DOMECTERFANI530
R
\
U
W
H
5
U
R
Z
V
V
D
3
LEU
&
6
(
V
V
H
U
S
U
R
U
R
U
U
H
G
U
tobuttonstion
accesstoOK
passwordthe
buttonstionnatndaethUse
havecharactersallOncecharacter.thechange
the menu.
incorrectanEntering producewillpassword
entry screen. Press the escape ESC key at any time
ndarcteraachchcttobuttons
centerthepressenteredbeenhave
anderrorentrypasswordaproduce
ress the escape ESC key at any time to return to the main display.
tionnadownndaupeth
OKlabeledbuttonnavigationcenter
thetoreturnedbewillusertheand
return to the main display.
Password Entry Screen Password Error Screen
entry screen. Press the escape ESC key at any time
The is530
leveltechniciantherecommendedisitsetup
alsocanpasswordlevelUserThesettings.
most cases.
Default User level password = 1000
Default Technician level password = 2000
beenhaspasswordlevelusercorrecttheOnce
be shown in the setup menu heading as seen below.
timeanyatexitedbecanmenusetupThe
key.“OK”thepressingthenanditem While
seconds of inactivity the module will automatically exit the setup menu and resume normal operation.
ress the escape ESC key at any time to return to the main display.
anduserthedefaultwith Duringlevel.
accessunauthorizedpreventtovaluenewatosetbepasswordlevel
theatvaluenewatosetbe installer’s notisbutdiscretion
Default Technician level password = 2000
usercurrentThedisplayed.bewillmenusetuptheenteredbeen
be shown in the setup menu heading as seen below. The available menu items are numbered and can be accessed by
ion keys. The “>” symbol indicates the currently selected menu item.
“1:theselectingbyorkey“ESC”thepressingeitherbytime EXIT”
inactive.remainwillinputsthemenusetuptheaccessingWhile
seconds of inactivity the module will automatically exit the setup menu and resume normal operation.
thatinremain
(
3
<
7
5
2
7
&
(
7
(
'
5
2
7
&
(
7
(
'
7
(
6
(
5
7
,
;
(
+
&
(
7
3
8
7
(
6
–alarmanOnce
conditionthat detectortheuntil
>
5
alarm faultshortor condition
reset.beenhasdetector detectortheresetTo
thedetectedbeenhas module
andmenusetuptheenterdetector

11
The display will show an “EVENT CLEARE ” message while the detector resets. All outputs should return
to normal standby states. Once the reset process has completed the display will return to a normal standby
display.
Note: If a detectable condition exists in the field, for example a short in the linear heat detector, the
condition must be repaired before resetting the detector. Failure to do so will result in the condition being
detected again after a reset completes.
Open conditions do not require the detector be reset. Once the open condition is repaired in the field the
module will return to a normal standby automatically.
Detector Type Selection – The PIM-530 is designed to operate with all the available detector types (PHSC
& PLR) in the igital Heat etector family. A etector Type selection menu has been included to allow for
future support of other detector types.
Currently the PIM-530 has no selectable options in the etector Type Selection screen and will display the
detector type configured for PHSC (Protectowire Heat Sensitive Cable) and then return the user to
the main menu.
initialDuring
thetoaccess
required in
willleveluser
The available menu items are numbered and can be accessed by
menuEXIT”
30Afterinactive.
willstatusmodule
theselectand
&
6
+
3
H
U
L
Z
R
W
thedetectedbeenhas module
andmenusetuptheenterdetector
'
(
5
$
(
/
&
7
1
(
9
(
&
6
+
3
H
U
L
Z
R
W
F
H
W
R
U
3
“2: RESET DETECTOR” option.
/
$
0
5
2
1
W
F
H
W
R
U
3
0
$
Boot Screen Status Screen
>
(
3
<
7
5
2
7
&
(
7
(
'
5
2
7
&
(
7
(
'
7
(
6
(
5
7
,
;
(
+
&
(
7
3
8
7
(
6
&
6
+
3
V
D
X
J
L
I
Q
R
F
R
W
F
H
W
H
'
MPIETH -LEUDOMECTERFANI530
messageCLEARED”“EVENTanshowwilldisplayThe detectorthewhile
normal standby states. Once the reset process has completed the display will return to a normal standby display.
conditiondetectableNotes: shortexampleforin thein
theinresultwillsodotoFailuredetector.theresettingbeforerepairedbe
reset completes.
conditionopentheOncereset.bedetectortherequirenotdoconditionsOpen
will return to a normal standby automatically.
–The withoperatetodesignedis530
Digital family.DetectorHeat beenhasmenuselectionTypeDetectorA
other detector types.
&
G
H
U
X
V
L
U
R
detector toreturnshouldoutputsAll
normal standby states. Once the reset process has completed the display will return to a normal standby display.
thedetector,heatlinearthe must
aafteragaindetectedbeingconditionthe
moduthefieldtheinrepairediscondition le
theallwith typesdetectoravailable in the
futureforallowtoincludedbeen ofsupport
theCurrently
is currently configured for PHSC (Protectowire Heat Sensitive Cable) and then return the user to the main menu.
(
3
<
7
5
2
7
&
(
7
(
'
the optionsselectablenohas530
is currently configured for PHSC (Protectowire Heat Sensitive Cable) and then return the user to the main menu.
>
SelectionTypeDetectortheinoptions
is currently configured for PHSC (Protectowire Heat Sensitive Cable) and then return the user to the main menu.
displaywillandscreenSelection
is currently configured for PHSC (Protectowire Heat Sensitive Cable) and then return the user to the main menu.
detectorthe
is currently configured for PHSC (Protectowire Heat Sensitive Cable) and then return the user to the main menu.
Menu Screen Detector Type Selection Screen
theCurrently
is currently configured for PHSC (Protectowire Heat Sensitive Cable) and then return the user to the main menu.
5
2
7
&
(
7
(
'
7
(
6
(
5
7
,
;
(
+
&
(
7
3
8
7
(
6
the optionsselectablenohas530
is currently configured for PHSC (Protectowire Heat Sensitive Cable) and then return the user to the main menu.
>
SelectionTypeDetectortheinoptions
is currently configured for PHSC (Protectowire Heat Sensitive Cable) and then return the user to the main menu.
(
3
<
7
5
2
7
&
(
7
(
'
5
2
7
&
(
7
(
'
7
(
6
(
5
Menu Screen

12
Display nits – The PIM-530 can be configured to display measurement information in either Standard
(Temperature = ˚F, istance = Feet) or Metric units (Temperature = ˚C, istance = Meters). Select a unit type
by entering the setup menu and selecting the “4: ISPLAY UNITS” menu item and press the “OK” button.
The units selection screen will be displayed.
Using the Up/ own navigation buttons select the desired units from the drop down list. The currently select-
ed type is followed by the “>” character. Once your selection is made press the “OK” button and you will be
returned to the main setup menu. Choose the “1: EXIT” menu item and press “OK” to return to the status
display.
Alarm Point Location (APL) Setup – The PIM-530 features an integrated Alarm Point Location Meter
(APL) which will identify the distance from the beginning of a detector run to the shorted portion of the
detector. Field calibration of the Alarm Point Location reading increases accuracy and provides the user a
means to compensate for changes introduced by addition of extension cable and also reading variations due to
ambient temperature.
Before calibrating the Alarm Point Location feature please follow these guidelines:
1. Calibration should be performed at the expected nominal ambient temperature for the installed
detector. For example, refrigerated storage installations should be calibrated after cool down.
2. To perform a calibration you must have access to the connections at the beginning of the detector
run and the end of the detector run.
3. All shorts placed in the detector loop during calibration should be created with a low resistance
jumper wire screwed directly under the junction terminals to ensure a true short. Using clip leads or
pressing jumpers across terminations does not insure a true short and can affect calibration accuracy.
This method is the suggested best practice for shorting the detector loop and should be used to
insure the best results.
Before starting the APL Calibration routine the detection loop must be installed and confirmed to be in a
NORMAL standby condition. Figure 4 depicts a typical Class B field wiring arrangement. Figure 4A depicts a
typical Class A field wiring arrangement. The procedure is the same for both Class B and A wiring configura-
tions unless otherwise noted. Where feed wire is not utilized shorts should be placed across the detector termi-
nations on the PIM-530 inputs.
d(Tem
Siunaectel
OK“sspre
CH
TE
P:
TU
SE
TOR
EC
DET
T
ESE
R
2:
PE
TY
OR
CT
ETE
D
3:
TS
NI
Y U
LA
ISP
D
4:
ceiDF,˚=eturaerp(Tem
etypti by teren ing setupeth
heTon.bu itsun selectio
>
P:
TU
SE
S
U
1:
ETR
M
2:
ydispfigur
Feet)= sniturictMeor (Tem
ectselduenmsetup ing “4:eth
e dispwill beenscrnselectio
ITS
UN
>
IC
ETR
y
ceiD,C˚=eturaerp(Tem
uenm”TSINUSID“4:
yed.
s)eterM= .
dnatemiu
tlyenrcureTh
dnuttob
toK”“Oess
oniatocLnt
notiropted
Up/Us
typselected
ebllwiuyo
otrnre
LretMe
onsbuonnavnowDUp/
“>ethybfoisetyp ch”
setupamethtoedr
.ayplsidsshe
fytiendillwichiwh staideth
dreisedtcelesons itsun fr
nselectiouryocenO.cterach
E“1:ethseoohCu.enmsetup
–TMCeTh -530 turfea
ogninbethmofrce
Thlist.podrethmofr
bK”“Oethessrpdemaisn
essrpdtemiuenmT”XI
estur an geint ParmAlderat
oshethtoretectodaf
Menu Screen Units Selection Screen

13
Figure 4
Figure 4A
Step 1 – Before beginning the calibration procedure place a short across the beginning (ZERO distance) of
the digital linear heat detector run as depicted in Figure 5.
Figure 5
To calibrate the Alarm Point Location ZERO distance enter the setup menu and select the “5: APL SETUP”
menu item and press the “OK” button. The “APL SETUP:” screen will be displayed. Select the “1: CAL
ZERO PT.” option from the menu and press the “OK” button. The AUTO CALIBRATE: ZERO istance
message will be displayed.
MPIETH -LEUDOMECTERFANI530
Before beginning the calibration procedure place a short across the beginning (ZERO distance) of the
Before beginning the calibration procedure place a short across the beginning (ZERO distance) of the
Before beginning the calibration procedure place a short across the beginning (ZERO distance) of the
digital linear heat detector run as depicted in Figure 8.
Before beginning the calibration procedure place a short across the beginning (ZERO distance) of the
linear heat detector run as depicted in Figure 8.
PT.” option from the menu and press the “OK” button. The AUTO CALIBRATE: ZERO Distance message will
Before beginning the calibration procedure place a short across the beginning (ZERO distance) of the
Before beginning the calibration procedure place a short across the beginning (ZERO distance) of the
digital linear heat detector run as depicted in Figure 8.
Before beginning the calibration procedure place a short across the beginning (ZERO distance) of the
linear heat detector run as depicted in Figure 8.
PT.” option from the menu and press the “OK” button. The AUTO CALIBRATE: ZERO Distance message will
To calibrate the Alarm Point Location ZERO distance enter the setup menu and select t
PT.” option from the menu and press the “OK” button. The AUTO CALIBRATE: ZERO Distance message will
be displayed.
To calibrate the Alarm Point Location ZERO distance enter the setup menu and select t
PT.” option from the menu and press the “OK” button. The AUTO CALIBRATE: ZERO Distance message will
be displayed.
U
S
Q
H
K
7
L
G
2
5
(
=
G
W
U
R
K
6
$
&
2
7
8
$
.
2
V
V
H
U
H
F
Q
D
W
V
L
W
D
U
R
W
F
H
W
H
G
(
7
$
5
%
,
/
$
APL Setup Menu Screen ero Calibration Start Screen
APL SETUP:
1: CAL ZERO PT.
>
2: CAL END PT. /SPAN

14
Press the OK button to begin the ZERO distance calibration. The module will measure the resistance to the
beginning of the detector run and offset future readings by this value.
ero Calibration Measurement Screen APL Setup Menu Screen
Once the ZERO distance calibration has been completed you will automatically be returned to the “APL
SETUP:” screen. Remove the short placed across the beginning of the detector run and proceed to Step 2.
Step 2 - Place a short across the end (EN distance) of the digital linear heat detector run as depicted in
Figure 6 for Class B and as depicted in Figure 7 for Class A.
Figure 6
Figure 7
To calibrate the Alarm Point Location EN point and SPAN distance enter the setup menu and select the “5:
APL SETUP” menu item and press the “OK” button. The “APL SETUP:” screen will be displayed. Select the
“2: CAL EN PT./SPAN” option from the menu and press the “OK” button. The AUTO CALIBRATE:
EN istance message will be displayed.
Press the OK button to begin the EN distance calibration. In the case of Class A installation (Figure 7)
the module will first measure feed cable resistance between the Input 2 terminals and the detectors end
terminations.
otesisre
OethessPr
ninbeth
:
TE
BRA
LI
CA
TO
AU
t
tar
S
ing
ad
Re
si
Re
REZethbtonuttobKO
odnaretectodethfogn
SET
L
AP
1:
L
CA
AL
C
2:
eTh.notibilcacenstaidOR
vasithybgsnidearefuturffset
:
UP
SET
PT.
O
ZER
>
N
PA
/S
T.
D P
EN
ethesureamllwieuldome re
va
ZERO diseOnc
:” scPSETU
2.
P
e…
nc
sta
si
Re
003
:
RES
T
OU
MS
OH
ion hasalibratceZERO dis
shormoven. Reeer:” sc
era shorelac
AL
C
2:
2:
EW
VI
ill auwoud yetomplen cebeion has
ginning of tberd aceplac
CTI line)e
N
PA
/S
T.
D P
EN
AL
C
ENT
RR
CU
EW
o td trnereicomattill au
d teeoctcetde
tcetCTI line
LAP“
peo Std t
d inetpic
Once the ZERO distance calibration has been completed you will automatically be returned to the “APL
SETUP:” screen. Remove the short placed across the beginning of the detector run and proceed to Step 2.
linear heat detector run as depicted in Figure 9
for Class B and as depicted in Figure 10 for Class A
lace a short across the end (END distance) of the digital linear heat detector run as depicted in Figure
To calibrate the Alarm Point Location END point and SPAN distance enter the setup menu and select the “5:
screen will be displayed. Select the “2:
ress the “OK” button. The AUTO CALIBRATE: END
(Figure 10) the
put 2 terminals and the detectors end terminations.
To calibrate the Alarm Point Location END point and SPAN distance enter the setup menu and select the “5:
screen will be displayed. Select the “2:
ress the “OK” button. The AUTO CALIBRATE: END
(Figure 10) the
put 2 terminals and the detectors end terminations.
To calibrate the Alarm Point Location END point and SPAN distance enter the setup menu and select the “5:
Distance message will be displayed.
Press the OK button to begin the END distance calibration. In the case of Class A installation
measure feed cable resistance between the In
To calibrate the Alarm Point Location END point and SPAN distance enter the setup menu and select the “5:
option from the menu and press the “OK” button. The AUTO CALIBRATE: END
Press the OK button to begin the END distance calibration. In the case of Class A installation (Figure 10)

15
The module will then measure the resistance of the linear heat detector and store it to be used in the final
span adjustment of Step 3.
End Calibration Start Screen End Calibration Return Measurement Screen
Step 3 – When the PIM-530 has completed all calibration measurements the detector end distance adjustment
screen will be displayed. This screen displays the current measured distance to the end of the detector using the
default distance multiplier and offsets obtained in steps 1 and 2. The distance should be very close to the actu-
al installed detector length at this point. To improve the accuracy of the measurement the actual installed
length of detector can be entered in place of the displayed reading.
End Calibration Detector Measurement Screen End Distance Adjustment Screen
Enter the new end distance value by using the Left and Right navigation buttons to select a digit of the
displayed value and use the Up and own navigation buttons to change the value.
Once the desired distance has been entered, press OK to accept the distance reading and calculate the new
calibration value. At this point the calibration process is completed and the APL SETUP menu is displayed.
Remove the short placed across the end of the detector run.
View the current calibration settings by selecting the “3: VIEW CURRENT CAL” option from the APL
SETUP menu. The current calibration settings screen is displayed. Line one shows the current Ohms per foot
or Ohms per Meter multiplier used to convert resistance to distance. Line two shows the outgoing offset resist-
ance in Ohms which should be equivalent to the outgoing extension wire total resistance. Line three shows the
return offset resistance in Ohms which should be equivalent to the return extension wire total resistance.
:
TE
BRA
LI
CA
TO
AU
CTMTHE -MRFACEETNI530
Entiocat Loinlae Ate tharlibcaTo
pdtemiuenmP”TUES“5:eth
T./SP“2: CAL END Pcled. Seedisplay
me
eanct
END Dis
E:RATIBO CALAUT
DNEethbtonuttobKOethessPr
llwieuldometh stfir abled cefeeasurme
s.notianimter meaendule will the moTh
f Stept odjustmenanal spae finthused in
LEDUO
terce ennN distad SPAnt ainoND pE nauenmsetupeth
llwieenscrP:”TUESeTh.nuttobK”“Oethessr
“OK” butenu and prmeT./SP
ill be
w
eagss
me d.edisplay
notiallstaniAssalCfosecaethnI.notiarbilcaceidD (Fi
tcetdereeebeeancsisterable
e it tord stot detectoeaeae linf thce onesistae re thsurmea
3.f Step
Whe
metsadju
:
TE
BRA
LI
CA
TO
AU
o
ect
et
t d
or
Sh
r
at
nce
ta
dis
D
EN
K.
s O
es
pr
en
Th
MCTWhe -mps coa530 h
hisTd.eplaydisill ben werecs
surmeantioarlibll caleted amp
ntrreucsplayn diserecshis
:
TE
BRA
LI
CA
TO
AU
ad
Re
END
g
in
LEDUO
terce ennN distad SPAnt ainoND pE nauenmsetupeth
llwieenscrP:”TUESeTh.nuttobK”“Oethessr
“OK” butenu and prmeT./SP
ill beweagssme d.edisplay
notiallstaniAssalCfosecaethnI.notiarbilcaceidD (Fi
tcetdereeebeeancsisterable
e it tord stot detectoeaeae linf thce onesistae re thsurmea
3.f Step
ectseldn
eb
on. Thet“OK” but
10)egur(Fi
nds eort
ebe it to
ad
Re
g
in
sta
si
Re
RES
T
RE
surmeantioarlibll caleted amp
ntrreucsplayn diserecshis
END
g
e…
nc
sta
003
:
RES
MS
OH
re detectots themensur staidden
ted disreuas en
ce
ethfoden
euld boce sh
ading.
adju
ortcetde usin
se to
ntmeeasurme
:
TE
BRA
LI
CA
TO
AU
ND
E
ing
ad
Re
e…
nc
sta
si
Re
T
OU
S:
RE
S
OHM
5
16
play
ce multipe defag thusin
lled detectstal inctuae athse to or le
d leac
play
ffsetsd oce multip d in s
o improvT.pointor le
d in placerentean betceth of de
Erent eth ne
d valueedisplay
deeOnc
alic brat
d.edisplay Re
ealuveanctnd dis ings
p and DowUand used value
entn eebehaseanctd disiresde
c.ealuion vbrat
oss trd aceshormoveRe
ing antghdLefteth
hangeo cons t
eco acsspred,ree
omplecissseion procalibratc
tcetdee
14
Press the OK button to begin the ZERO distance calibration. The module will measure the resistance to the
beginning of the detector run and offset future readings by this value.
Zero Calibration Measurement Screen APL Setup Menu Screen
Once the ZERO distance calibration has been completed you will automatically be returned to the “APL
SETUP:” screen. Remove the short placed across the beginning of the detector run and proceed to Step 2.
Step 2 - Place a short across the end (END distance) of the digital linear heat detector run as depicted in
Figure 6 for Class B and as depicted in Figure 7 for Class A.
Figure 6
Figure 7
To calibrate the Alarm Point Location END point and SPAN distance enter the setup menu and select the “5:
APL SETUP” menu item and press the “OK” button. The “APL SETUP:” screen will be displayed. Select the
“2: CAL END PT./SPAN” option from the menu and press the “OK” button. The AUTO CALIBRATE:
END Distance message will be displayed.
Press the OK button to begin the END distance calibration. In the case of Class A installation (Figure 7)
the module will first measure feed cable resistance between the Input 2 terminals and the detectors end
terminations.
15
The module will then measure the resistance of the linear heat detector and store it to be used in the final
span adjustment of Step 3.
End Calibration Start Screen End Calibration Return Measurement Screen
Step 3 – When the PIM-530 has completed all calibration measurements the detector end distance adjustment
screen will be displayed. This screen displays the current measured distance to the end of the detector using the
default distance multiplier and offsets obtained in steps 1 and 2. The distance should be very close to the actu-
al installed detector length at this point. To improve the accuracy of the measurement the actual installed
length of detector can be entered in place of the displayed reading.
End Calibration Detector Measurement Screen End Distance Adjustment Screen
Enter the new end distance value by using the Left and Right navigation buttons to select a digit of the
displayed value and use the Up and Down navigation buttons to change the value.
Once the desired distance has been entered, press OK to accept the distance reading and calculate the new
calibration value. At this point the calibration process is completed and the APL SETUP menu is displayed.
Remove the short placed across the end of the detector run.
View the current calibration settings by selecting the “3: VIEW CURRENT CAL” option from the APL
SETUP menu. The current calibration settings screen is displayed. Line one shows the current Ohms per foot
or Ohms per Meter multiplier used to convert resistance to distance. Line two shows the outgoing offset resist-
ance in Ohms which should be equivalent to the outgoing extension wire total resistance. Line three shows the
return offset resistance in Ohms which should be equivalent to the return extension wire total resistance.
CA
TO
AU
st
ju
Ad
pr
en
Th
R D
TE
EN
:
TE
BRA
LI
CA
e.
nc
sta
di
K.
s O
es
pr
0
T:
IS
R D
8
ft
APL Setup Menu Screen Current Calibration Settings Screen
: 0.185
2
!
$
&
7
1
(
5
5
8
&
:
(
,
9
6
7
3
'
1
(
/
$
&
7
3
2
5
(
=
/
$
&
3
8
7
(
6
/
3
$
calibration value. At this point the calibration process is completed and the APL SETUP menu is displayed.
Remove the short placed across the end of the detector run.
View the current calibration settings by select
menu. The current calibration settings screen is displayed. Line one shows the current Ohms per foot or Ohms per
Meter multiplier used to convert resistance to distance. Line two shows the outgoing offset resistance in Ohms
which should be equivalent to the outgoing extension wire total resistance. Line three shows the return offset
resistance in Ohms which should be equivalent to the return extension wire total resistance.
!
!
!
/
$
N
$
3
bration value. At this point the calibration process is completed and the APL SETUP menu is displayed.
Remove the short placed across the end of the detector run.
: VIEW CURRENT CAL” option from th
menu. The current calibration settings screen is displayed. Line one shows the current Ohms per foot or Ohms per
Meter multiplier used to convert resistance to distance. Line two shows the outgoing offset resistance in Ohms
valent to the outgoing extension wire total resistance. Line three shows the return offset
resistance in Ohms which should be equivalent to the return extension wire total resistance.
14
Press the OK button to begin the ZERO distance calibration. The module will measure the resistance to the
beginning of the detector run and offset future readings by this value.
Zero Calibration Measurement Screen APL Setup Menu Screen
Once the ZERO distance calibration has been completed you will automatically be returned to the “APL
SETUP:” screen. Remove the short placed across the beginning of the detector run and proceed to Step 2.
Step 2 - Place a short across the end (END distance) of the digital linear heat detector run as depicted in
Figure 6 for Class B and as depicted in Figure 7 for Class A.
Figure 6
Figure 7
To calibrate the Alarm Point Location END point and SPAN distance enter the setup menu and select the “5:
APL SETUP” menu item and press the “OK” button. The “APL SETUP:” screen will be displayed. Select the
“2: CAL END PT./SPAN” option from the menu and press the “OK” button. The AUTO CALIBRATE:
END Distance message will be displayed.
Press the OK button to begin the END distance calibration. In the case of Class A installation (Figure 7)
the module will first measure feed cable resistance between the Input 2 terminals and the detectors end
terminations.
15
The module will then measure the resistance of the linear heat detector and store it to be used in the final
span adjustment of Step 3.
End Calibration Start Screen End Calibration Return Measurement Screen
Step 3 – When the PIM-530 has completed all calibration measurements the detector end distance adjustment
screen will be displayed. This screen displays the current measured distance to the end of the detector using the
default distance multiplier and offsets obtained in steps 1 and 2. The distance should be very close to the actu-
al installed detector length at this point. To improve the accuracy of the measurement the actual installed
length of detector can be entered in place of the displayed reading.
End Calibration Detector Measurement Screen End Distance Adjustment Screen
Enter the new end distance value by using the Left and Right navigation buttons to select a digit of the
displayed value and use the Up and Down navigation buttons to change the value.
Once the desired distance has been entered, press OK to accept the distance reading and calculate the new
calibration value. At this point the calibration process is completed and the APL SETUP menu is displayed.
Remove the short placed across the end of the detector run.
View the current calibration settings by selecting the “3: VIEW CURRENT CAL” option from the APL
SETUP menu. The current calibration settings screen is displayed. Line one shows the current Ohms per foot
or Ohms per Meter multiplier used to convert resistance to distance. Line two shows the outgoing offset resist-
ance in Ohms which should be equivalent to the outgoing extension wire total resistance. Line three shows the
return offset resistance in Ohms which should be equivalent to the return extension wire total resistance.
8
2
+
&
2
+
1
,
2
3
%
2
+
1
,
'
$
!
(
(
,
,
0
.
-
%
,
,
0
.
-
%
2
,
.
-
%
(
'
"
APL Setup Menu Screen Current Calibration Settings Screen
: 0.185
2
APL Setup Menu Screen Current Calibration Settings Screen

16
Time and Date Setup – The PIM-530 features a real time clock with date. Time is displayed in 12 hour for-
mat and the date is displayed in Month/ ay/Year format. The clock will maintain time and date settings even
in the event of complete power failure via a backup battery.
To set the time and date enter the setup menu and select the “7: TIME AN ATE” menu item and press
the “OK” button. The TIME AN ATE setup screen will be displayed.
Menu Screen Time and Date Setup Screen
Using the Left/Right navigation buttons select the Hours/Minutes or Month/ ay/Year as required. The cur-
rently selected value will be highlighted with a blinking curser. Use the Up/ own navigation buttons to
change the value of the current section. Once all values are set press the OK button to save changes and exit to
the setup menu. Choose the “1: EXIT” menu item and press “OK” to return to the status display.
Password Setup – All menu access to the PIM-530 is password protected. The two levels of access are User
level (USER) and Technician (TECH) level. User level access is limited to etector Reset and Event History
viewing functions. Technician level access allows full access to the setup menu including the ability to change
the USER and TECH level password.
To change a password enter the setup menu and select the “8: USER PASSWOR ” or “9: TECH PASS-
WOR ” menu item and press the “OK” button. The SET USER PASSWOR or SET TECH PASSWOR
setup screen will be displayed along with the current password value
Menu Screen Password Setup Screen
Using the Left/Right navigation buttons select each character of the password as required. The currently
selected value will be highlighted with a blinking curser. Use the Up/ own navigation buttons to change the
value of the current section. Once all values are set press the OK button to save changes and exit to the setup
menu. Choose the “1: EXIT” menu item and press “OK” to return to the status display.
Factory Restore – The PIM-530 features a factory restore option. A factory restore will reset all module set-
tings back to the original factory supplied state. A factory restore will affect the following settings.
1. isplay Units – efaults to US (Standard)
2. APL Setup – All offset data set to a zero value, Per Foot multiplier defaults to 0.282
3. Time and ate – Time and ate not affected
4. Passwords – USER level reset to 1000, TECH level reset to 2000
5. Event History – History is cleared
CH
TE
P:
TU
SE
TUP
SE
PL
A
5:
ST
TE
ON
TI
UNC
J
6:
7
E
AT
D D
AN
ME
TI
:
CTMTHE -MRFACEETNI530
–TMCeTh
indeplaydisisedatandrhou
lete pmpf cot oe eventhings evensettin
setuethterentedadtimeethsetTo
IME AND DATTheTon.bu“sspre
>
LEDUO
TM-ctimelearaesturfea530 displayisTime.edatwkloc
imetainmaintillwkloccheT.ar/Yein
abckupabilurlete p
setu “tcleesandnumep 7umen”NDAETIM:
d.eplaydisill ben werecp seE sIME AND DAT
E
DAT
D
AN
ME
TI
me.
ti
st
ju
Ad
K.
s O
es
pr
en
Th
3
201
0/
8/2
0
5AM
:4
10
LEDUO
TM-ctimelearaesturfea530 displayisTime.edatwkloc
imetainmaintillwkloccheT.ar/Yein
abckupabilurlete p
setu “tcleesandnumep 7umen”NDAETIM:
d.eplaydisill ben werecp seE sIME AND DAT
12indedisplay
edatandime
ditemu
edrequi eTh.
ntio onsbu
geschve
sso
eraccessaf
tvenEdna
CH
TE
P:
TU
SE
7
E
AT
D D
AN
ME
TI
:
Us Left/Right aignav nuttobnoti
ectedselytlenrcur lighighhebwilllueva
sectitenethfovaethgenachto
.numepesotxiteand eChoos
.display
–otssecacnumeAll
ECH)anichniceTandUS(levelreUs
ingvorytHis snctiofun nicianTech.
ECH leUSER and Tehango c
setupethterendrsswoapagechTo
thessrpdtemiuenm”OWSSPA
eescrsetupOWSSPA playdisill ben w
equirsareaYD/thnoMroutesMs/uroHethectselsn
tiovigaanpUethseU.sercurgkinlinbawithtedligh
tonuttobKOethessrpseteravallacenO.nosecti
otrnreot“sspreandmeitnume”ITEX:1“he
o TMCeth -drsswoapis530 detceprot folevelstwoeTh.
velECH) el isccessalevelserU. delimit esetRretectoDto
umensetupethtoccessafullaccessalevel inc
ord.wsl pasevECH le
“ethselectdnaumensetup 8roRD”OSSWPARSEU:
ESroOWSSPARESUTESeTh.nuttobK”“Oeth
.ealuord vwsrreuceplay
LUs
luevaselected
fovaeth
seth metup
8
D
OR
SSW
PA
ER
US
:
9
D
OR
SSW
PA
CH
TE
:
onsttbuonnavR/eL
awithtedlighighhebwilllue
cenO.nosectitenrcurethf
T”XIE“1:ethseoohCu.enm
>
ofretharacchacetcelesons th
pUethseU.sercurgkinlinba
Oethessrpseteravalla
K”“OessrpdtemiuenmT”
R
USE
T
SE
00
10
D:
WOR
SS
PA
equirsareaYD/thnoMroutesMs/uroHethectselsn
tiovigaanpUethseU.sercurgkinlinbawithtedligh
tonuttobKOethessrpseteravallacenO.nosecti
otrnreot“sspreandmeitnume”ITEX:1“he
o TMCeth -drsswoapis530 detceprot folevelstwoeTh.
velECH) el isccessalevelserU. delimit esetRretectoDto
umensetupethtoccessafullaccessalevel inc
ord.wsl pasevECH le
“ethselectdnaumensetup 8roRD”OSSWPARSEU:
ESroOWSSPARESUTESeTh.nuttobK”“Oeth
.ealuord vwsrreuceplay
ludinginc
“9HCTE:
HCTE
ofretharacchacetcelesons th
pUethseU.sercurgkinlinba
Oethessrpseteravalla
K”“OessrpdtemiuenmT”
Th.edrequirsadrsswoapeth
snuttobntionp
gesnachtonuttobKO
lspidtusstaethtortoK”
enrcureTh
gechtos
totiexd
l
Table of contents
Other Protectowire Control Unit manuals
Popular Control Unit manuals by other brands
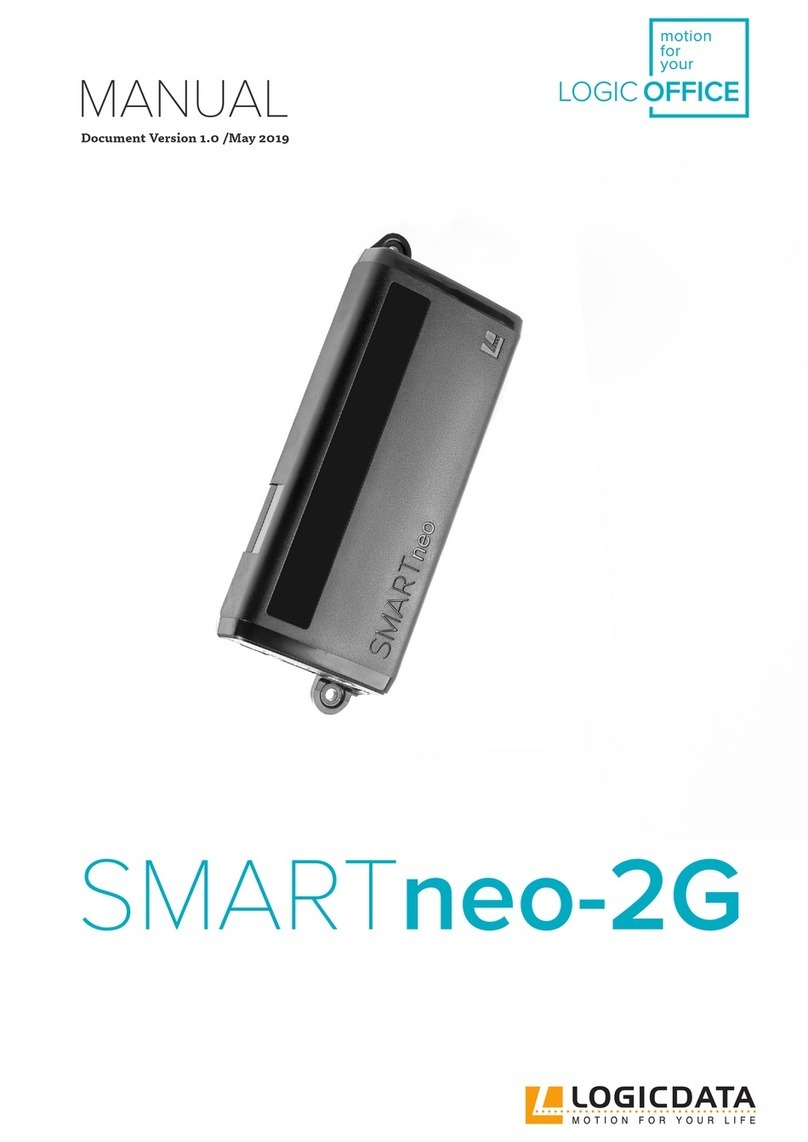
LOGICDATA
LOGICDATA SMARTneo-2G manual
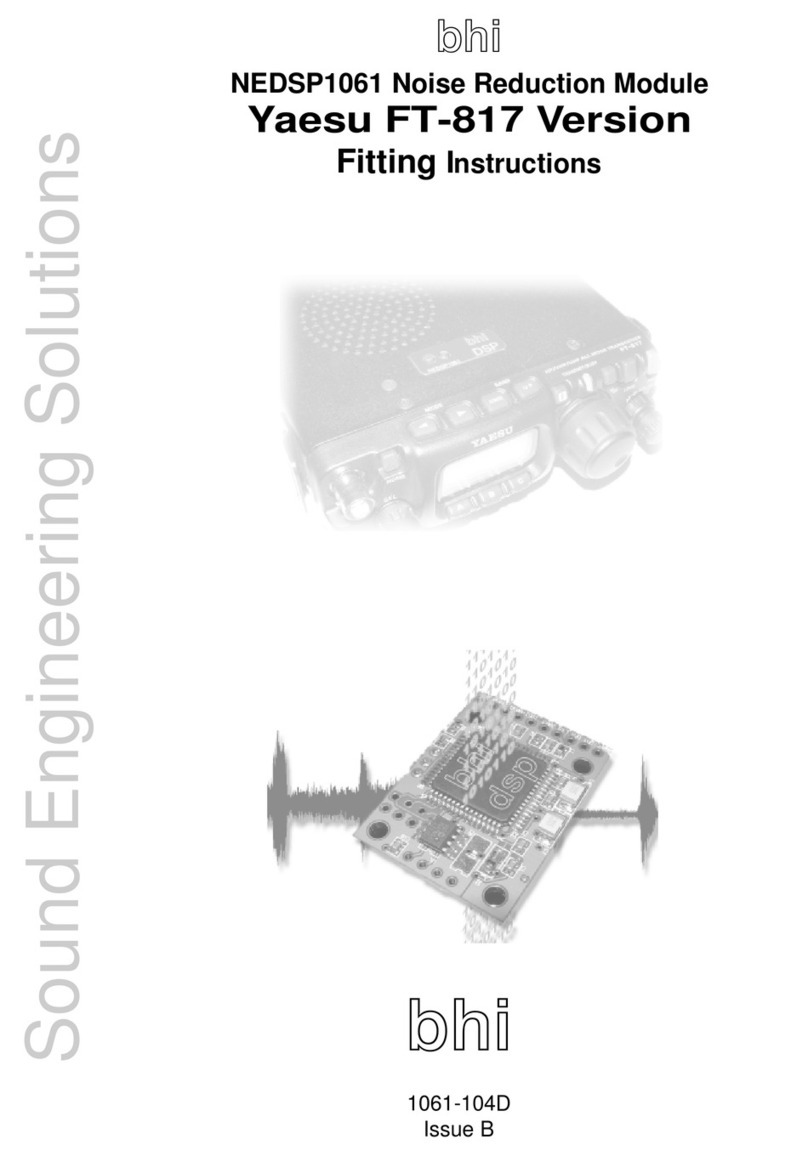
BHI
BHI NEDSP1061 Fitting instructions
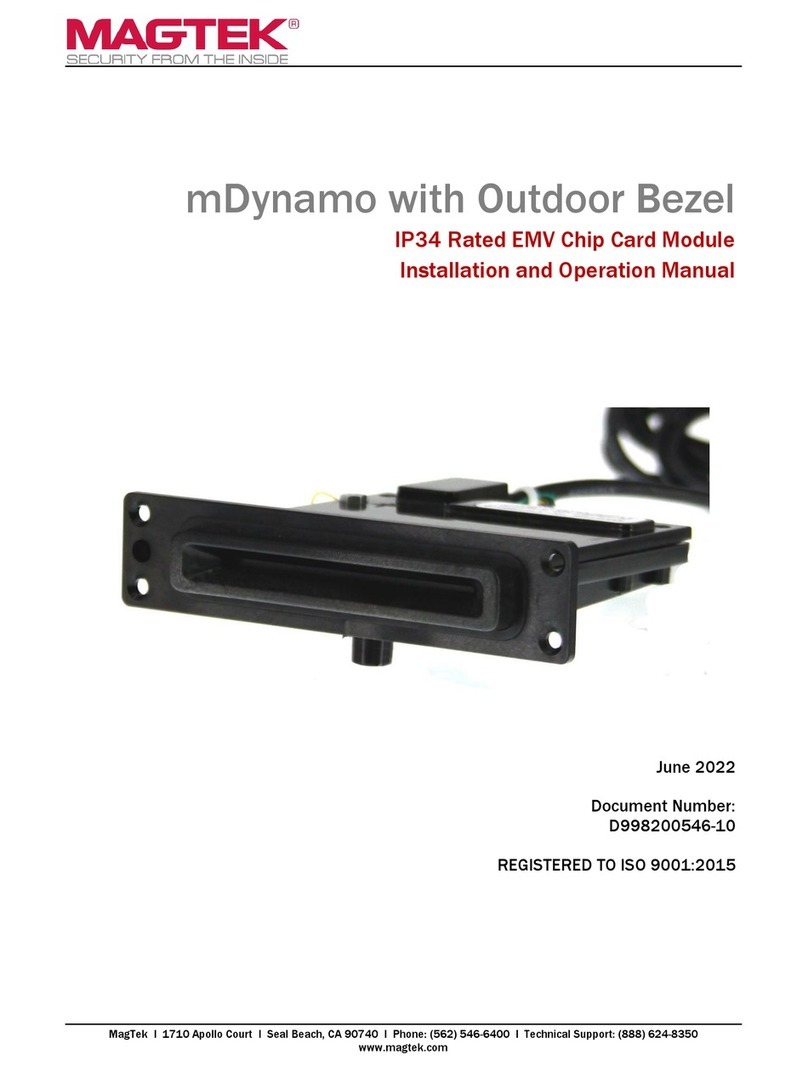
Magtek
Magtek MDYNAMO Installation and operation manual
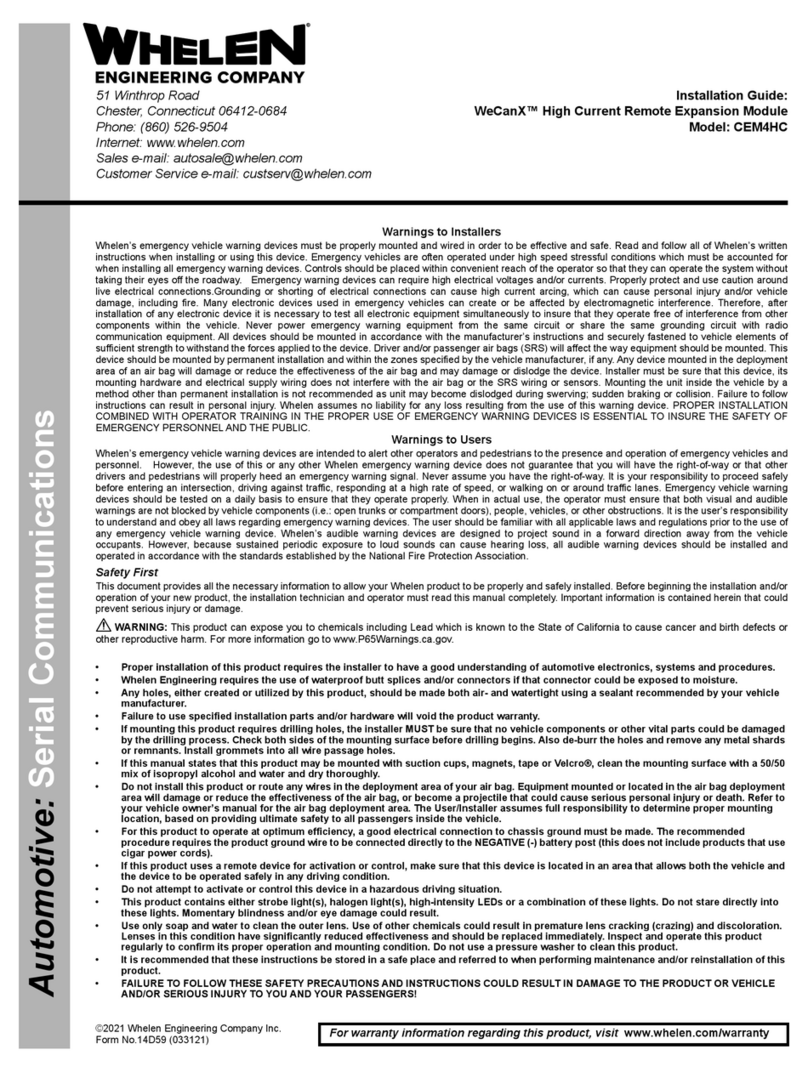
Whelen Engineering Company
Whelen Engineering Company CenCom Core-R CEM4HC installation guide
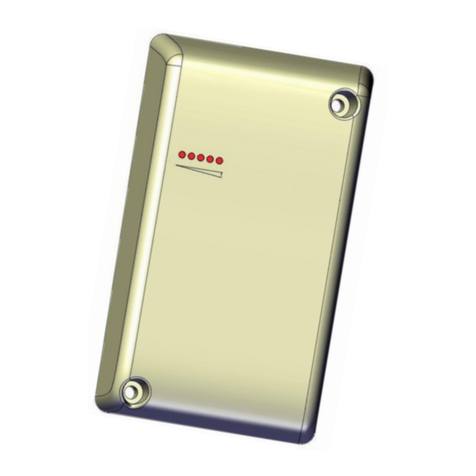
Intratone
Intratone 17-0104 manual

Pentair
Pentair Sapag 1100 Installation & maintenance instructions