PSG Wilden XSD Series Instruction Manual

EOM
Engineering
Operation &
Maintenance
XSD
Advanced™ Metal
Surge Dampener
Where Innovation Flows
www.wildenpump.com
W I L-1 9 0 11- E - 0 7
REPLACES WIL-19011-E-06

TABLE OF CONTENTS
SECTION 1 CAUTIONS—READ FIRST! ..............................................1
SECTION 2 WILDEN PUMP DESIGNATION SYSTEM.................................2
SECTION 3 HOW IT WORKS—PUMP & AIR DISTRIBUTION SYSTEM ................3
SECTION 4 DIMENSIONAL DRAWINGS .............................................4
SECTION 5 PERFORMANCE
XSD1 ...................................................................6
XSD2 ...................................................................7
XSD3 ...................................................................8
SECTION 6 SUGGESTED INSTALLATION & TROUBLESHOOTING .....................9
SECTION 7 DISASSEMBLY / REASSEMBLY ........................................11
Reassembly Hints &Tips ..................................................14
SECTION 8 EXPLODED VIEW & PARTS LISTING
XSD1 Metal
PTFE/Rubber/SIPD/Ultra-Flex™-Fitted ...................................16
XSD2 Metal
PTFE/Rubber/SIPD/Ultra-Flex™-Fitted ...................................18
XSD2 Metal Advanced
PTFE/Rubber/SIPD/Ultra-Flex™-Fitted ...................................20
XSD3 Metal
PTFE/Rubber/Ultra-Flex™-Fitted........................................22
SECTION 9 ELASTOMER OPTIONS.................................................24

WIL-19 011- E- 07 1 WILDEN PUMP & ENGINEERING, LLC
CAUTION: Do not over-lubricate air supply —
excess lubrication will reduce performance.
CAUTION: Do not exceed 8.6 bar (125 psig) air
supply pressure.
CAUTION: When choosing dampener materials,
be sure to check the temperature limits for
all wetted components. Example: Viton®
has a maximum limit of 177°C (350°F) but
polypropylene has a maximum limit of only 79°C
(175°F).
CAUTION: Maximum temperature limits are
based upon mechanical stress only. Certain
chemicals will significantly reduce maximum
safe operating temperatures. Consult Chemical
Resistance Guide (E4) for chemical compatibility
and temperature limits.
TEMPERATURE LIMITS:
Polypropylene 0°C to 79°C 32°F to 175°F
PVDF –12°C to 107°C 10°F to 225°F
PFA 7°C to 107°C 20°F to 225°F
Neoprene –18°C to 93°C 0°F to 200°F
Buna-N –12°C to 82°C 10°F to 180°F
EPDM –51°C to 138°C –60°F to 280°F
Viton®FKM –40°C to 177°C –40°F to 350°F
Wil-Flex™ –40°C to 107°C –40°F to 225°F
Saniflex™ –29°C to 104°C –20°F to 220°F
Polyurethane –12°C to 66°C 10°F to 150°F
Polytetrafluoroethylene (PTFE)
14°C to 104°C 40°F to 220°F
EPDM –51°C to 138°C –60°F to 280°F
Nylon –18°C to 93°C 0°F to 200°F
Acetal –29°C to 82°C –20°F to 180°F
SIPD PTFE
with
Neoprene-backed
4°C to 104°C 40°F to 220°F
SIPD PTFE
with
EPDM-backed
–10°C to 137°C 14°F to 280°F
Polyethylene 0°C to 70°C 32°F to 158°F
Geolast®–40°C to 82°C –40°F to 180°F
1
4°C to 149°C (40°F to 300°F) - 13 mm (1/2”) and 25 mm (1”) models only.
NOTE: Not all materials are available for all
models. Refer to Section 2 for material options
for your pump.
WARNING: Prevent static sparking. If static
sparking occurs, fire or explosion could result.
Dampener, pump, valves and containers must
be grounded to a proper grounding point
when handling flammable fluids and whenever
discharge of static electricity is a hazard.
CAUTION: The process fluid and cleaning fluids
must be chemically compatible with all wetted
dampener components. Consult Chemical
Resistance Guide (E4).
CAUTION: Dampener(s) should be thoroughly
flushed before installing into process lines.
FDA- and USDA- approved dampeners should be
cleaned and/ or sanitized before being used.
CAUTION: Always wear safety glasses when
operating dampener. If diaphragm rupture
occurs, process fluid may be forced out air
exhaust.
CAUTION: Before any maintenance or repair
is attempted, the compressed air line to the
dampener and pump should be disconnected
and all air pressure allowed to bleed from the
system. Disconnect all intake, discharge and air
lines. Drain the dampener by allowing any fluid
to flow into a suitable container.
CAUTION: Blow out air line for 10 to 20 seconds
before attaching to dampener to make sure all
pipeline debris is clear. Use an in-line air filter.
A 5μ (micron) air filter is recommended.
CAUTION: Dampeners cannot be used in
submersible applications.
CAUTION: Tighten all hardware prior to
installation.
CAUTION: ATEX products have been assessed
for use in potentially explosive atmospheres in
accordance with the European Directive 94/9/
EC (ATEX 95). Users of ATEX products must be
familiar with ATEX requirements and follow
all safety guidelines. (Refer to Wilden Safety
Supplement WIL-18510-E).
REV 10/13/04 LKB
Section 1
CAUTIONS—READ FIRST!

WILDEN PUMP & ENGINEERING, LLC 2 WIL-19 011- E- 07
Section 2
WILDEN DESIGNATION SYSTEM
XSD EQUALIZER®
LEGEND
XSD X/XXXX / XXX / XX /XXXX
O-RINGS
DIAPHRAGM
REGULATOR BODY
AIR CHAMBER
WETTED PARTS/OUTER PISTON
INLET SIZE
EQUALIZER
®
SURGE DAMPENER
SPECIALTY CODE
(if applicable)
MATERIAL CODES
MODEL
XSD = ATEX EQUALIZER®
SURGE DAMPENER
INLET SIZE
1 = 25 mm (1”)
2 = 51 mm (2”)
3 = 76 mm (3”)
WETTED PATH/
OUTER PISTON
AA = ALUMINUM/ALUMINUM
SS = STAINLESS STEEL/
STAINLESS STEEL
AIR CHAMBER
A = ALUMINUM
S = STAINLESS STEEL
REGULATOR BODY
A = ALUMINUM
S = STAINLESS STEEL
DIAPHRAGM
BNS = BUNA-N (Red Dot)
FSS = SANIFLEX™ (Cream)
EPS = EPDM (Blue Dot)
NES = NEOPRENE (Green Dot)
PUS = POLYURETHANE (Clear)
TNU = PTFE W/NEOPRENE
TEU = PTFE W/EPDM
VTS = VITON®(Silver or
White Dot)
WFS = WIL-FLEX™ (Orange Dot)
XBS = CONDUCTIVE BUNA-N
(Two Red Dots)
ULTRA-FLEX™ DIAPHRAGM
BNU = BUNA-N (Red Dot)
EPU = EPDM (Blue Dot)
NEU = NEOPRENE (Green Dot)
VTU = VITON®(Silver or
White Dot)
O-RINGS
BN = BUNA-N
TF = PTFE (White)1
TV = PTFE Encapsulated Viton2
NOTE: MOST ELASTOMERIC MATERIALS USE COLORED DOTS FOR IDENTIFICATION.
Viton®is a registered trademark of DuPont Elastomers.
Hytrel®is a registered trademark of DuPont Elastomers.
Santoprene®is a registered trademark of Exxon Mobil Corporation.
SPECIALTY CODES
0014 BSPT
0040 ASNI Flange Connection (AdvancedTM)
REV 10/11/04 WSA
NOTE:
1XSD1 and XSD2 Only
2XSD3 Only

All reciprocating pumps generate discharge pressure
fluctuation. The Equalizer®minimizes unwanted pressure
fluctuation by providing a supplementary pumping action.
This is accomplished by using a diaphragm as a separation
membrane within the Equalizer®to trap a given volume of
liquid on one side and pressurized air on the other.
When the fluid pressure falls in the system, the Equalizer®
supplies additional pressure to the discharge line between
pump strokes by displacing fluid via diaphragm movement.
This movement provides the supplementary pumping
action needed to reduce pressure variation and pulsation.
The Equalizer®automatically sets and maintains the
correct air pressure matching the variations in liquid
flow or discharge pressure generated by the pump. A
shaft attached to the Equalizer®diaphragm triggers the
addition or removal of the air within the non-wetted side
of the Equalizer®. The Equalizer®automatically adjusts
to any pressure and/or flow setting of the pump with no
need for manual adjustment of the unit and/or system.
The Equalizer®has proven to be the cost effective choice
for protecting your liquid process system from unwanted
pulsation or pressure fluctuation. Contact your localWilden
distributor for further information on the Equalizer®and
other pumping solutions.
A compressed air line attached to the air regulator body sets
and maintains pressure on the air side of the diaphragm. As
the reciprocating pump begins its stroke, liquid discharge
pressure increases which flexes the Equalizer®diaphragm
inward.This action accumulates fluid in the liquid chamber
(see Phase 2) and the air regulator allows compressed air
to enter the air side. When the pump redirects its motion
upon stroke completion, the liquid discharge pressure
decreases and compressed air in the air side forces the
Equalizer®diaphragm to flex outward displacing the fluid
into the discharge line (see Phase 3).This motion provides
the supplementary pumping action needed to minimize
pressure fluctuation.
AIR
REGULATOR
BODY
AIR
REGULATOR
BODY
AIR
REGULATOR
BODY
LIQUID SIDE LIQUID SIDE LIQUID SIDE
DIAPHRAGM DIAPHRAGM DIAPHRAGM
AIR
SIDE
AIR
SIDE
AIR
SIDE
AIR
REGULATOR
BODY
AIR
REGULATOR
BODY
AIR
REGULATOR
BODY
LIQUID SIDE LIQUID SIDE LIQUID SIDE
DIAPHRAGM DIAPHRAGM DIAPHRAGM
AIR
SIDE
AIR
SIDE
AIR
SIDE
AIR
REGULATOR
BODY
AIR
REGULATOR
BODY
AIR
REGULATOR
BODY
LIQUID SIDE LIQUID SIDE LIQUID SIDE
DIAPHRAGM DIAPHRAGM DIAPHRAGM
AIR
SIDE
AIR
SIDE
AIR
SIDE
PHASE 1 PHASE 3PHASE 2
WIL-19 011- E- 07 3 WILDEN PUMP & ENGINEERING, LLC
Section 3
HOW IT WORKS—DAMPENER
REV 10/11/04 WSA

WILDEN PUMP & ENGINEERING, LLC 4 WIL-19 011- E- 07
Section 4
DIMENSIONAL DRAWINGS
REV 7/20/2005 ERNS
DIMENSIONS — XSD1 METAL
DIMENSION METRIC (mm) STANDARD (inch)
A 295 11.6
B 244 9.6
C 147 5.8
D 295 11.6
E 297 11.7
XSD1
XSD2
DIMENSIONS — XSD2 METAL
DIMENSION METRIC (mm) STANDARD (inch)
A 315 12.4
B 257 10.1
C 244 9.6
D 455 17.9
E 345 13.6

WIL-19 011- E- 07 5 WILDEN PUMP & ENGINEERING, LLC
DIMENSIONAL DRAWINGS
XSD3
DIMENSIONS — XSD3 METAL
DIMENSION METRIC (mm) STANDARD (inch)
A 399 15.7
B 320 12.6
C 295 11.6
D 556 21.9
E 424 16.7
XSD2 AdvancedTM
DIMENSIONS -
XSD2 ADVANCED METAL
ITEM METRIC (mm) STANDARD (inch)
A 345 13.6
B 257 10.1
C 279 11.0
D 513 20.2
E 325 12.8
DIN
F 125 DIA 4.9 DIA
G 165 DIA 6.5 DIA
H 18 DIA 0.7 DIA
ANSI
F 122 DIA 4.8 DIA
G 165 DIA 6.5 DIA
H 20 DIA 0.8 DIA

WILDEN PUMP & ENGINEERING, LLC 6 WIL-19 011- E- 07
Section 5
XSD1 PERFORMANCE
These charts show discharge head fluctuations for a
diaphragm pump with and without a dampener. By
reviewing the variation in pressure, the level of dampening
can be estimated for an application. For example, the head
pressure generated by a 25 mm (1”) pump operating at
6.89 bar (100 psig) air inlet pressure and 6.2 bar (90 psig)
head pressure varies between 1.7 bar (25 psig) and 7.2
bar (104 psig) resulting in a total pressure fluctuation of
5.5 bar (79 psig) for each stroke. When an XSD1/AAAA/
TNU/TF dampener is installed in the application, the
head pressure varies between 4.8 bar (69 psig) and 6.6
bar (96 psig) resulting in a pressure fluctuation of only
1.9 bar (27 psig). This results in a 67% reduction in head
pressure fluctuation.
XSD1 TNU
[4.1 bar (60 psig) inlet air / 3.4 bar (50 psig) discharge head]
Discharge Head [bar (psig)]
Time (sec)
0
0.7 (10)
1.4 (20)
2.1 (30)
2.8 (40)
3.4 (50)
4.1 (60)
4.8 (70)
5.5 (80)
1 2
1 1.5 2 2.5 3 3.5
XSD1 BNS
[4.1 bar (60 psig) inlet air / 3.4 bar (50 psig) discharge head]
Discharge Head [bar (psig)]
Time (sec)
4.8 (70)
4.1 (60)
3.4 (50)
2.8 (40)
2.1 (30)
1.4 (20)
0.7 (10)
0
XSD1 TNU
[6.89 bar (100 psig) inlet air / 6.2 bar (90 psig) discharge head]
Time (sec)
0 0.5 1 1.5 2 2.5 3 3.5
Discharge Head
[bar (psig)]
1.4 (20)
2.8 (40)
4.1 (60)
5.5 (80)
6.9 (100)
8.3 (120)
0
0
1.4 (20)
2.8 (40)
4.1 (60)
5.5 (80)
6.9 (100)
8.3 (120)
1 1.5 2 2.5 3 3.5
XSD1 BNS
[6.89 bar (100 psig) inlet air / 6.2 bar (90 psig) discharge head]
Discharge Head [bar (psig)]
Time (sec)
0
1.4 (20)
2.8 (40)
4.1 (60)
5.5 (80)
6.9 (100)
8.3 (120)
1 1.5 2 2.5 3 3.5
XSD1 BNU
[6.89 bar (100 psig) inlet air / 6.2 bar (90 psig) discharge head]
Discharge Head
[bar (psig)]
Time (sec)

WIL-19 011- E- 07 7 WILDEN PUMP & ENGINEERING, LLC
XSD2 PERFORMANCE
These charts show discharge head fluctuations for a
diaphragm pump with and without a dampener. By
reviewing the variation in pressure, the level of dampening
can be estimated for an application. For example
in reference to XSD2 BNS 100/90, the head pressure
generated by a 51 mm (2") pump operating at 6.89 bar (100
psig) air inlet pressure and 6.2 bar (90 psig) head pressure
varies between 0.4 bar (6 psig) and 7 bar (102 psig)
resulting in a total pressure fluctuation of 6.6 bar (96 psig)
for each stroke. When an XSD2/AAAA/BNS/BN dampener
is installed in the application, the head pressure varies
between 4.7 bar (68 psig) and 6.8 bar (99 psig) resulting in
a pressure fluctuation of only 2.1 bar (31 psig).This results
in a 68% reduction in head pressure fluctuation.
XSD2 BNS
[4.1 bar (60 psig) inlet air / 3.4 bar (50 psig) discharge head]
Discharge Head
[bar (psig)]
Time (sec)
0
0.7 (10)
1.4 (20)
2.1 (30)
2.8 (40)
3.4 (50)
4.1 (60)
4.8 (70)
0 1 2 3 4 5
0 1 2 3 4 5
XSD2 BNS
[6.89 bar (100 psig) inlet air / 6.2 bar (90 psig) discharge head]
Discharge Head
[bar (psig)]
Time (sec)
1.4 (20)
0
2.8 (40)
4.1 (60)
5.5 (80)
6.9 (100)
8.3 (120)
1 2 3 4 5
XSD2 TNU
[4.1 bar (60 psig) inlet air / 3.4 bar (50 psig) discharge head]
Discharge Head
[bar (psig)]
Time (sec)
0
1.4 (20)
2.8 (40)
4.1 (60)
5.5 (80)
0
20
40
60
80
100
120
0 1.5 2 2.5 3 3.5 4 4.5 5
XSD2 TNU
[6.89 bar (100 psig) inlet air / 6.2 bar (90 psig) discharge head]
Discharge Head [bar (psig)]
Time (sec)
0 1.5 2 2.5 3 3.5 4 4.5 5
XSD2 BNU
[6.89 bar (100 psig) inlet air / 6.2 bar (90 psig) discharge head]
Discharge Head [bar (psig)]
Time (sec)
0
1.4 (20)
2.8 (40)
4.1 (60)
5.5 (80)
6.9 (100)
8.3 (120)
1 2 3 4 5
XSD2 BNU
[4.1 bar (60 psig) inlet air / 3.4 bar (50 psig) discharge head]
Discharge Head
[bar (psig)]
Time
(sec)
0
0.7 (10)
1.4 (20)
2.1 (30)
2.8 (40)
3.4 (50)
4.1 (60)

WILDEN PUMP & ENGINEERING, LLC 8 WIL-19 011- E- 07
XSD3 PERFORMANCE
These charts show discharge head fluctuations for a
diaphragm pump with and without a dampener. By
reviewing the variation in pressure, the level of dampening
can be estimated for an application. For example
(XSD3 BNU 100/90), the head pressure generated by
a 76 mm (3”) pump operating at 6.89 bar (100 psig) air
inlet pressure and 6.2 bar (90 psig) head pressure varies
between 2.1 bar (30 psig) and 6.5 bar (94 psig) resulting
in a total pressure fluctuation of 4.4 bar (64 psig) for
each stroke. When an XSD3/AAAA/BNU/BN dampener
is installed in the application, the head pressure varies
between 4.8 bar (69 psig) and 6.3 bar (91 psig) resulting of
a pressure fluctuation of only 1.5 bar (22 psig).This results
in a 66% reduction in head pressure fluctuation.
1 2 3 4 5 6 7
XSD3 TNU
[6.89 bar (100 psig) inlet air / 6.2 bar (90 psig) discharge head]
Discharge Head
[bar (psig)]
Time (sec)
0
1.4 (20)
2.8 (40)
4.1 (60)
5.5 (80)
6.9 (100)
8.3 (120)
1 2 3 4 5 6 7
XSD3 TNU
[4.1 bar (60 psig) inlet air / 3.4 bar (50 psig) discharge head]
Discharge Head
[bar (psig)]
Time (sec)
0.7 (10)
0
1.4 (20)
2.1 (30)
2.8 (40)
3.4 (50)
4.1 (60)
1 2 3 4 5 6 7
XSD3 BNU
[6.89 bar (100 psig) inlet air / 6.2 bar (90 psig) discharge head]
Discharge Head
[bar (psig)]
Time (sec)
0
1.4 (20)
2.8 (40)
4.1 (60)
5.5 (80)
6.9 (100)
8.3 (120)
1 2 3 4 5 6 7
XSD3 BNU
[4.1 bar (60 psig) inlet air / 3.4 bar (50 psig) discharge head]
Discharge Head
[bar (psig)]
Time (sec)
0.7 (10)
0
1.4 (20)
2.1 (30)
2.8 (40)
3.4 (50)
4.1 (60)
1 2 3 4 5 6 7
XSD3 BNS
[6.89 bar (100 psig) inlet air / 6.2 bar (90 psig) discharge head]
Discharge Head
[bar (psig)]
Time (sec)
0
1.4 (20)
2.8 (40)
4.1 (60)
5.5 (80)
6.9 (100)
8.3 (120)
1 2 3 4 5 6 7
XSD3 BNS
[4.1 bar (60 psig) inlet air / 3.4 bar (50 psig) discharge head]
Discharge Head
[bar (psig)]
Time (sec)
0.7 (10)
0
1.4 (20)
2.1 (30)
2.8 (40)
3.4 (50)
4.1 (60)

WIL-19 011- E- 07 9 WILDEN PUMP & ENGINEERING, LLC
Section 6
SUGGESTED INSTALLATION
Themodel XSD1 hasa25 mm (1")inlet/discharge.Themodel
XSD2 has a 51 mm (2") inlet/discharge and the XSD3 has a
76 mm (3") inlet/discharge.The Equalizer®can be installed
in either horizontal or vertical orientations. A variety of
materials are available to satisfy temperature, chemical
compatibility, abrasion and flex concerns.
The Equalizer®installed on the discharge side of the pump
minimizes pulsation and protects in-line equipment. It can
also be connected on the suction side to prevent water
hammer associated with a positive inlet condition.
Install the Equalizer®as shown below. The use of flexible
connections and a Filter, Regulator, Lubricator (FRL) will
extend parts life. Shut-off valves on the suction side of
pump and the discharge side of Equalizer®will enable
maintenance personnel to safely service the equipment.
To maximize effectiveness, install the Equalizer®as close
as possible to the discharge of the pump.
It is important to support the pipe immediately
downstream from the Equalizer®. Use a tee connector
on the pump air supply line and connect the line to the
Equalizer®regulator body. This tee connector should be
installed after the FRL. The Equalizer®consumes very
little air, therefore, a 1/4” hose is more than adequate to
supply enough air volume. When the air supply to the
pump is shut down, the air to the Equalizer®will be shut
off as well.
NOTE: In the event of a power failure, the shut-off
valve should be closed if the restarting of the pump is
not desirable once power is regained.
AIR-OPERATED PUMPS: To stop the pump from
operating in an emergency situation, simply close
the shut-off valve (user supplied) installed in the air
supply line. A properly functioning valve will stop the
air supply to the pump, therefore stopping output. This
shut-off valve should be located far enough away from
the pumping equipment such that it can be reached
safely in an emergency situation.
SUCTION LINE
DISCHARGE LINE
SHUT-OFF VALVE
FLEXIBLE CONNECTION
FLEXIBLE CONNECTION
AIR SUPPLY
SHUT-OFF VALVE
SHUT-OFF VALVE
PRESSURE GAUGE
AIR SHUT-OFF VALVE
COMBINATION FILTER AND REGULATOR
NEEDLE VALVE
AIR INLET
SHUT-OFF VALVE
PRESSURE GAUGE

WILDEN PUMP & ENGINEERING, LLC 10 WIL-19 011- E- 07
TROUBLESHOOTING
1) When there is a significant drop in the fluid discharge
pressure, there will be a noticeable release of air
through the small bleed hole in the air regulator
body. This is how the Equalizer®automatically adjusts
itself for optimal suppression. This is a good way
of verifying proper operation of the unit. If there is
a continuous discharge of air out of this hole during
steady fluid discharge pressure, the Equalizer®is not
functioning properly and should be inspected. The air
regulator body houses three (3) Glyd rings.
2) Fluid leakage around the clamp band area is normally
stopped by tightening the clamp band bolts. If
leakage continues, unit should be disassembled and
inspected.
3) Air leakage between the adapter plate and air chamber
requires tightening of four air chamber bolts on the
inside of the air chamber.

WIL-19 011- E- 07 11 WILDEN PUMP & ENGINEERING, LLC
Section 7
DAMPENER DISASSEMBLY
Tools Required:
• Deep well sockets and
ratchet (7/16”, 1/2” and
3/4”)
• Hex (Allen®) wrenches
(3/16” and 1/4”)
• Large adjustable wrench
or channel lock pliers
Tools Recommended:
• Large pipe wrench
• Vise equipped w/soft
jaws (such as aluminum,
plastic, plywood or other
suitable material)
CAUTION: Before any maintenance or repair is attempted, the compressed
air line to the Equalizer®and the pump should be disconnected and all air
pressure allowed to bleed from the system. Disconnect all intake, discharge,
and air lines. Be aware of any hazardous effects of contact with your process
fluid. PLEASE READ ALL DIRECTIONS BEFORE STARTING DISASSEMBLY.
NOTE: The model photographed for these instructions is a XSD1. Other
Equalizer®models should be similar in design but may contain slightly
different components and fastener sizes.
Step 1
Disassembly of the surge ends/
small clamp band is needed only
in the event of leakage. Leakage is
usually stopped by tightening the
small band bolts using a 7/16” deep
well socket.
Step 2
If leakage persists, remove surge
ends and replace O-rings.
Step 3
Remove large clamp band using a
1/2” deep well socket.

WILDEN PUMP & ENGINEERING, LLC 12 WIL-19 011- E- 07
Step 4
Set liquid chamber aside.
Step 5
Remove reducer bushing at top of
regulator.
Step 6
Loosen shaft assembly by using
adjustable wrench on outer piston
and 3/4” socket on shaft bolt inside
air regulator body. Turn counter
clockwise. One of two scenarios will
occur: outer piston will loosen from
shaft, or the shaft bolt will loosen
from shaft.
Step 7
In either case, this will allow the
removal of the inner and outer
pistons, diaphragm, shaft stop,
shaft, shaft stop washer and bolt.
Step 8
Inspect shaft for nicks or abrasion.
Small nicks can usually be dressed
out. If shaft is chemically attacked or
nicks are hindering operation, shaft
should be replaced.
Step 9
Disassembly of the air chamber
from the regulator adaptor plate
is needed only in the event of air
leakage.
DAMPENER DISASSEMBLY

WIL-19 011- E- 07 13 WILDEN PUMP & ENGINEERING, LLC
Step 10
In the event of an air leak, remove
the air chamber and replace the
gasket.
DAMPENER DISASSEMBLY
Step 11
Disassembly of the regulator body
from the regulator adaptor plate
is needed only in the event of air
leakage.
Step 12
In the event of an air leak, remove
the regulator adaptor plate and
replace the O-ring.
Step 13
Using an O-ring pick, remove the
Glyd rings from air regulator body.
Step 14
The air regulator body has five
(5) grooves cut into the inside
diameter.There are three Glyd rings
installed in the 1, 3 and 5 positions.
It is important that these Glyd rings
be installed in the correct grooves
so that the Equalizer®functions
properly. Please refer to the drawing
for the correct location of the Glyd
rings.
5
3
1

WILDEN PUMP & ENGINEERING, LLC 14 WIL-19 011- E- 07
REASSEMBLY HINTS & TIPS
Figure A
SHAFT SEAL
TAPE
Figure B
SHAFT SEAL
TAPE
NEEDLE NOSE
PLIERS
ASSEM B LY:
Upon performing applicable maintenance to the
air distribution system, the Equalizer®can now
be reassembled. Please refer to the disassembly
instructions for photos and parts placement. To
reassemble the Equalizer®, follow the disassembly
instructions in reverse order. The air regulator body
needs to be assembled first, then the diaphragm and
finally the wetted path. Please find the applicable
torque specifications on this page. The following tips
will assist in the assembly process.
• Lubricate air regulator body , Glyd rings and shaft
bore center with NLGI grade 2 white EP bearing
grease or equivalent.
• Clean the inside of the air regulator body bore to
ensure no damage is done to new shaft seals.
• Stainless bolts should be lubed to reduce the
possibility of seizing during tightening.
MAXIMUM TORQUE SPECIFICATIONS
Model Description of Part Torque
XSD1
Air chamber/adapter plate 24.4 N·m (18 ft-lb)
Air regulator body/adapter plate 7.9 N·m (70 in-lb)
Outer piston/shaft bolt assembly
(all diaphragms) 54.2 N·m (40 ft-lb)
XSD2
Air chamber/adapter plate 24.4 N·m (18 ft-lb)
Air chamber/adapter plate 7.9 N·m (70 in-lb)
Outer piston/shaft bolt assembly
(rubber & PTFE) 109 N·m (80 ft-lb)
Outer piston/shaft bolt assembly
(Ultra-Flex™ & SIPD) 74.6 N·m (55 ft-lb)
XSD3
Air chamber/adapter plate 44.7 N·m (33 ft-lb)
Air regulator body/adapter plate 7.9 N·m (70 in-lb)
Outer piston/shaft bolt assembly
(all diaphragms) 136 N·m (100 ft-lb)
SHAFT SEAL INSTALLATION:
PRE-INSTALLATION
• Once all of the old seals have been removed, the
inside of the air regulator body should be cleaned
to ensure no debris is left that may cause premature
damage to the new seals.
INSTALLATION
The following tools can be used to aid in the installation
of the new seals:
Needle Nose Pliers
Phillips Screwdriver
Electrical Tape
• Wrap electrical tape around each leg of the needle nose
pliers (heat shrink tubing may also be used). This is done
to prevent damaging the inside surface of the new seal.
• With a new seal in hand, place the two legs of the needle
nose pliers inside the seal ring. (See Figure A.)
• Open the pliers as wide as the seal diameter will allow,
then with two fingers pull down on the top portion of
the seal to form kidney bean shape. (See Figure B.)
• Lightly clamp the pliers together to hold the seal into
the kidney shape. Be sure to pull the seal into as tight
of a kidney shape as possible, this will allow the seal to
travel down the bushing bore easier.
• With the seal clamped in the pliers, insert the seal into
the bushing bore and position the bottom of the seal
into the correct groove. Once the bottom of the seal is
seated in the groove, release the clamp pressure on the
pliers. This will allow the seal to partially snap back to its
original shape.
• After the pliers are removed, you will notice a slight
bump in the seal shape. Before the seal can be properly
resized, the bump in the seal should be removed as
much as possible. This can be done with either the
Phillips screwdriver or your finger. With either the side
of the screwdriver or your finger, apply light pressure
to the peak of the bump. This pressure will cause the
bump to be almost completely eliminated.
• Lubricate the edge of the shaft with NLGI grade 2
white EP bearing
grease.
• Slowly insert the center shaft with a rotating motion.
This will complete the resizing of the seal.
• Perform these steps for the remaining seal.

NOTES

XSD1 ORIGINALTM METAL EXPLODED VIEW
28
27
PTFE FITTED
SIPD FITTED
ULTRA-FLEX FITTED
19
21
24
23
25
26
20
22
27
19
20
22
23
26
27
19
23
25
21
26
29
22
21
27
26
1
2
3
4
5
6
7
8
19
20
21
22
23
25
16
15
18
13
12
9
10
11
17
14
RUBBER FITTED
Section 8
EXPLODED VIEW & PARTS LISTING
WILDEN PUMP & ENGINEERING, LLC 16 WIL-19 011- E- 07

XSD1 ORIGINALTM METAL PARTS LISTING
EXPLODED VIEW & PARTS LISTING
XSD1/AAAA/
P/N
XSD1/SSSS/
P/N
No. Part Description Qty.
1 Body, Regulator11 76-8515-01 76-8515-03
2 Ring II, Glyd 3 08-3210-55-225 08-3210-55-225
3 O-Ring -230 (Ø2.484 x Ø.139) 1 76-1285-52 76-1285-52
4 Plate, Regulator Adapter 1 76-8510-01 76-8510-03
5 Screw, 1/4-20 x .75 Soc Hd Cap 4 76-6250-03 76-6250-03
6 Gasket, Center Block 1 04-3529-52 04-3529-52
7 Chamber, Air 1 04-3660-01 04-3660-03
8 Screw, 3/8-16 x 1.00 Soc Flt Csk Hd Cap 4 71-6250-08 71-6250-08
9 Chamber, Liquid 1 04-5000-01 04-5000-03
10 Clamp Band, Half 2 04-7330-08 04-7330-03
11 Bolt, 5/16-18 x 2.50 Rnd Hd Sq Neck 2 04-6070-03 04-6070-03
12 Washer, Plain 2 01-6732-03 01-6732-03
13 Nut, 5/16-18 Hex 2 04-6420-08 08-6400-03
14 O-Ring -229 (Ø2.359 x Ø.139) 2 * *
15 End, 1” NPT Surge 2 70-8600-01 70-8600-03
End, 1” BSPT Surge 2 70-8600-01-14 70-8600-03-14
16 Clamp Band Small 4 04-7100-08 04-7100-03
17 Bolt, 1/4-20 x 2.00 Rnd Hd Sq Neck 4 04-6050-08 01-6070-03
18 Nut, 1/4-20 Hex 4 04-6400-08 04-6400-03
19 Shaft, Straight 1 76-3800-03 76-3800-03
Shaft, Ultra-Flex™ 1 04-3830-03-07 04-3830-03-07
20 Stud, 1/2-20 x 1.50 Threaded 1 04-6150-08 04-6150-08
21 Stop, Shaft 1 76-8800-17 76-8800-17
22 Piston, Rubber & TPE Inner 1 04-3700-01-700 04-3700-01-700
Piston, Ultra-Flex™ Inner 1 04-3760-01-700 04-3760-01-700
Piston, PTFE Inner 1 04-3755-01 04-3755-01
Piston, SIPD Inner 1 04-3700-08 04-3700-08
23 Diaphragm, Primary 1 * *
Diaphragm, Ultra-Flex™ 1 * *
Diaphragm, PTFE 1 * *
Diaphragm, SIPD 1 * *
24 Diaphragm, Back-Up 1 * *
25 Piston, Rubber & TPE Outer 1 04-4552-01 04-4550-03
Piston, Ultra-Flex™ Outer 1 04-4560-01 02-4550-03
Piston, PTFE Outer 1 04-4600-01 04-4600-03
26 Washer, Stop 1 70-6790-08 70-6790-08
27 Screw, Hex Cap, 1/2-20 x 1.00 1 04-6090-08 04-6090-08
Screw, Hex Hd Cap, 3/8-16 x .88, Ultra-Flex™ 1 08-6140-08 08-6140-08
28 Reducer Bushing 1 70-6950-08 71-6950-03
29 Washer, (.406 ID x .812 OD x .065 THK) Ultra-Flex™ 1 15-6740-08-50 15-6740-08-50
1Air Regulator Body includes qty. 3 Glyd Rings.
*Elastomer options listed on page 24.
All Bold face items are primary wear items.
WIL-19 011- E- 07 17 WILDEN PUMP & ENGINEERING, LLC

EXPLODED VIEW & PARTS LISTING
XSD2 ORIGINALTM METAL EXPLODED VIEW
27
26
PTFE FITTED
RUBBER FITTED
SIPD FITTED
ULTRA-FLEX FITTED
18
19
23
22
24
25
20
21
26
18
20
21
22
24
25
26
18
20
21
22
25
26
18
22
21
24
20
25
19
19
19
26
25
1
2
3
4
5
6
7
8
18
20
19
21
22
24
15
17
9
12
10
11
16
13
14
WILDEN PUMP & ENGINEERING, LLC 18 WIL-19011-E- 07
This manual suits for next models
3
Table of contents
Other PSG Control Unit manuals
Popular Control Unit manuals by other brands
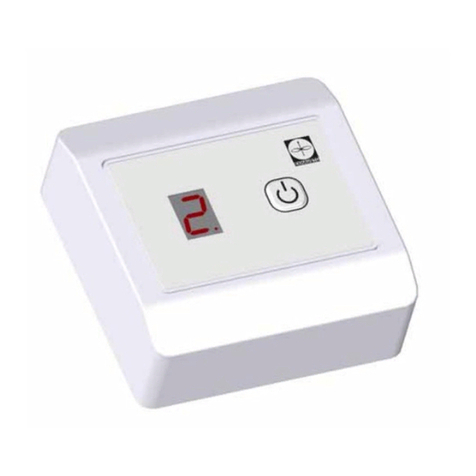
Exhausto CDT
Exhausto CDT EFC 18-EU-01 manual

Toledo
Toledo ZT-1 user manual
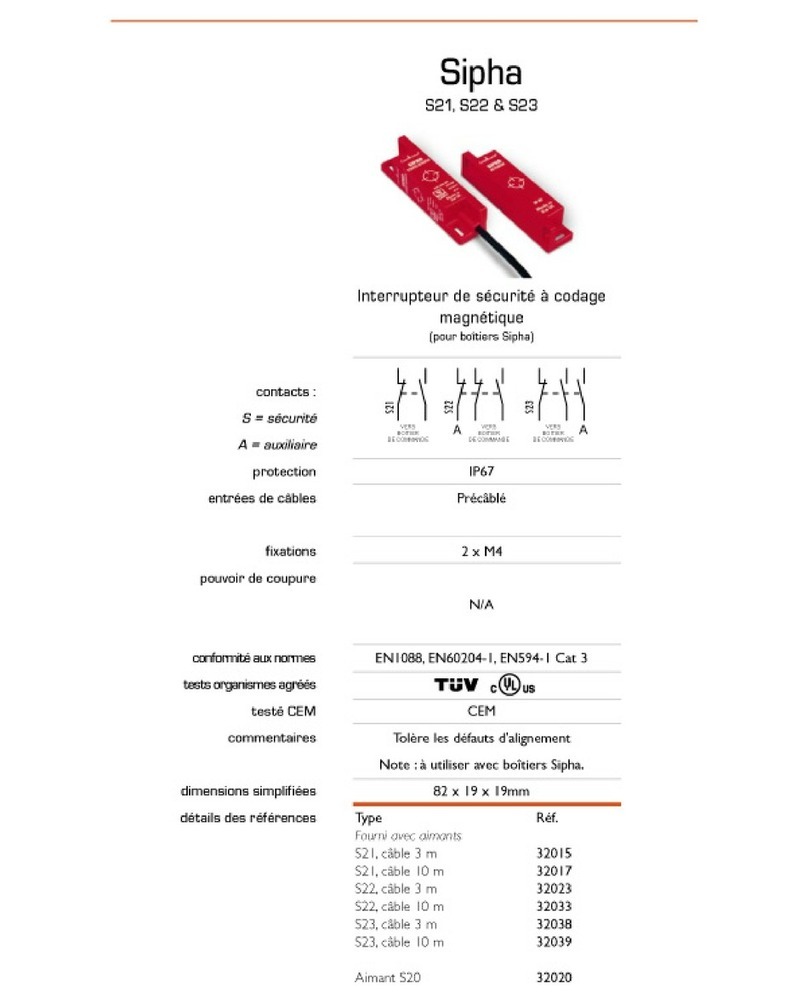
Rockwell Automation
Rockwell Automation Allen Bradley Guardmaster Sipha 2 manual
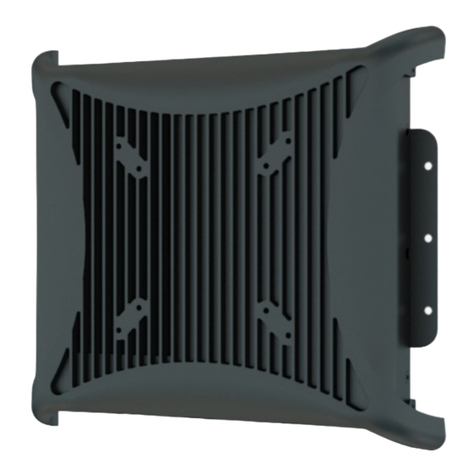
Indumicro
Indumicro IMM-M10 S Series user manual
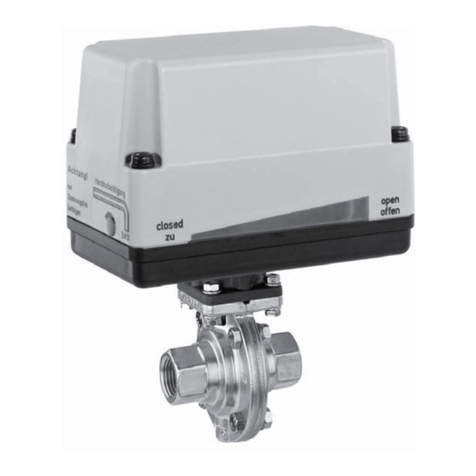
GEM
GEM 428 Installation, operating and maintenance instructions
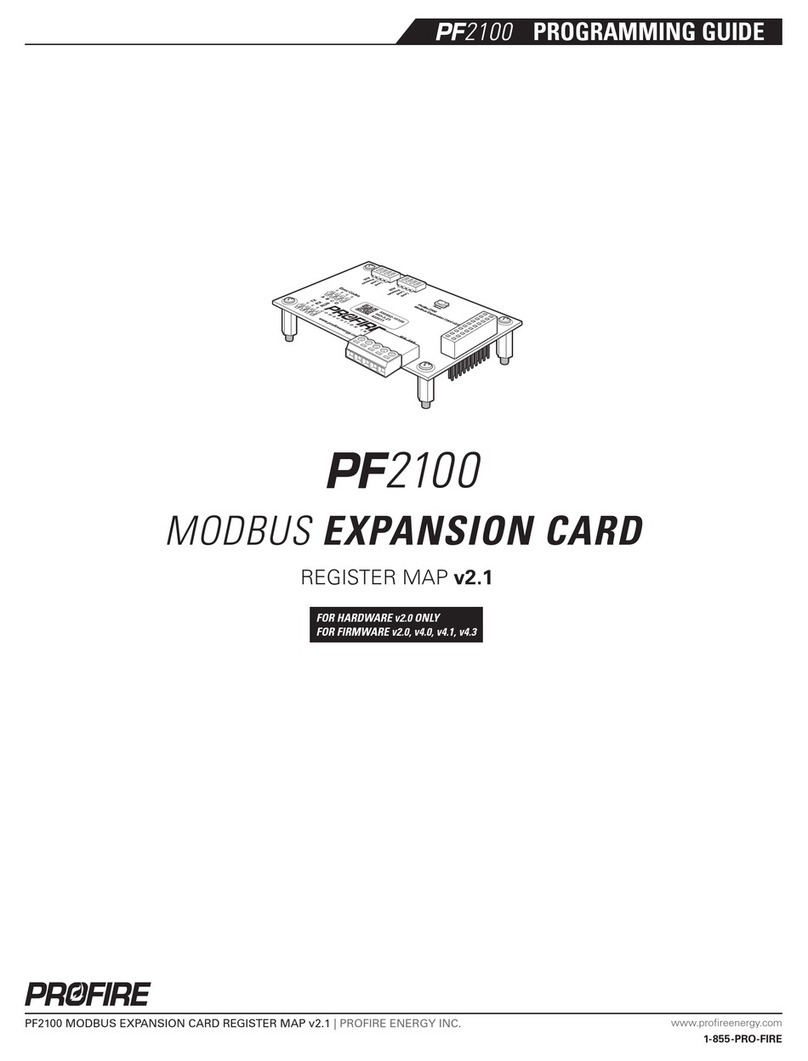
ProFire
ProFire PF2100 Programming guide
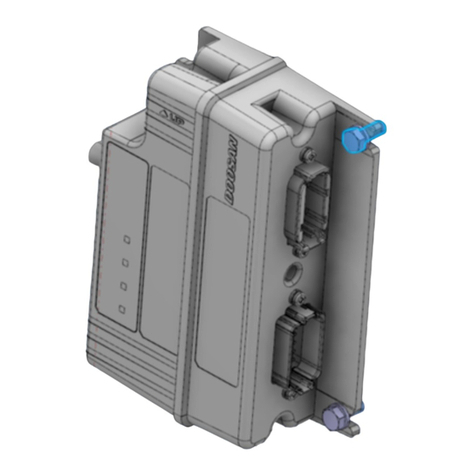
Dasan
Dasan TMS3.0 installation manual
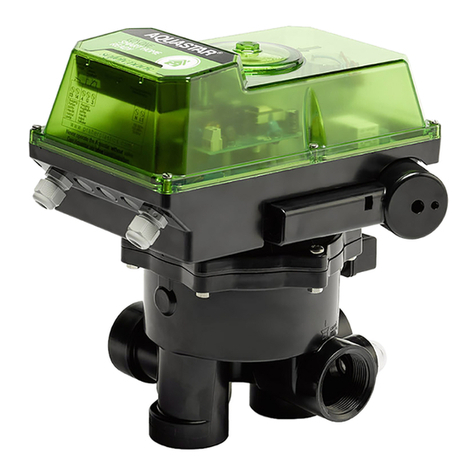
AquaStar
AquaStar Loxone Operation manual
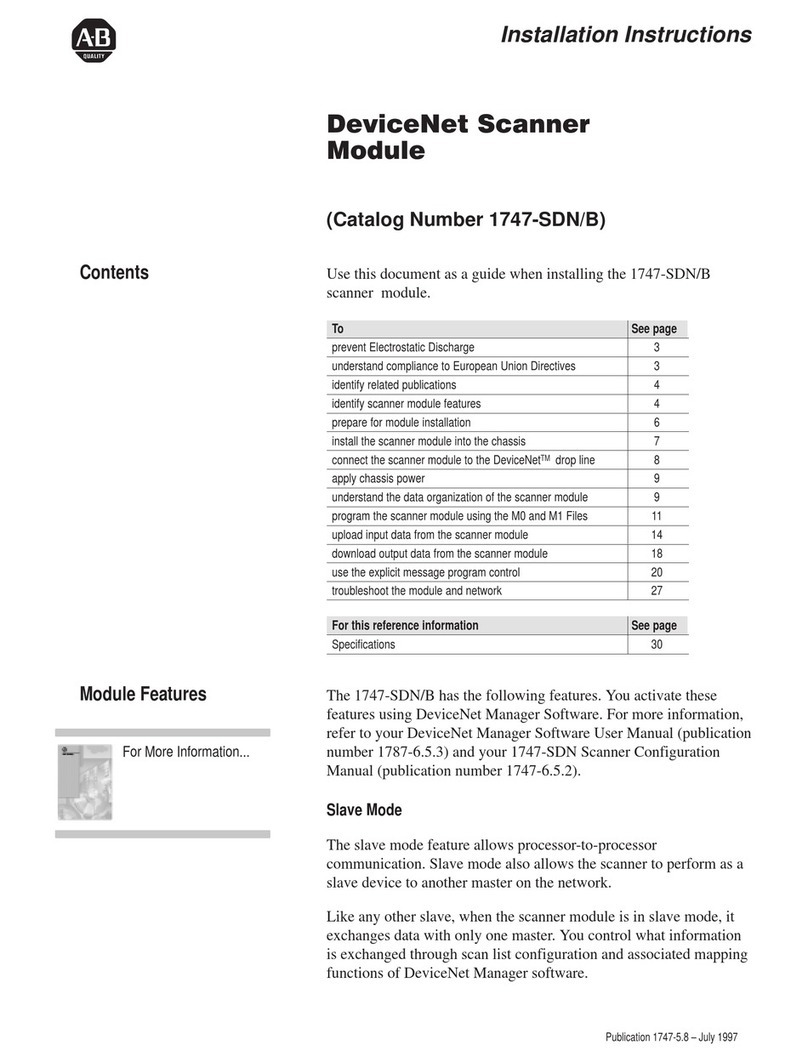
Allen-Bradley
Allen-Bradley DeviceNet 1747-SDN/B installation instructions
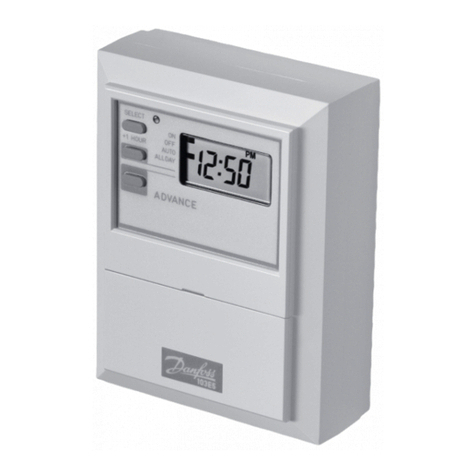
Danfoss
Danfoss 103E5 Installation & user's instructions
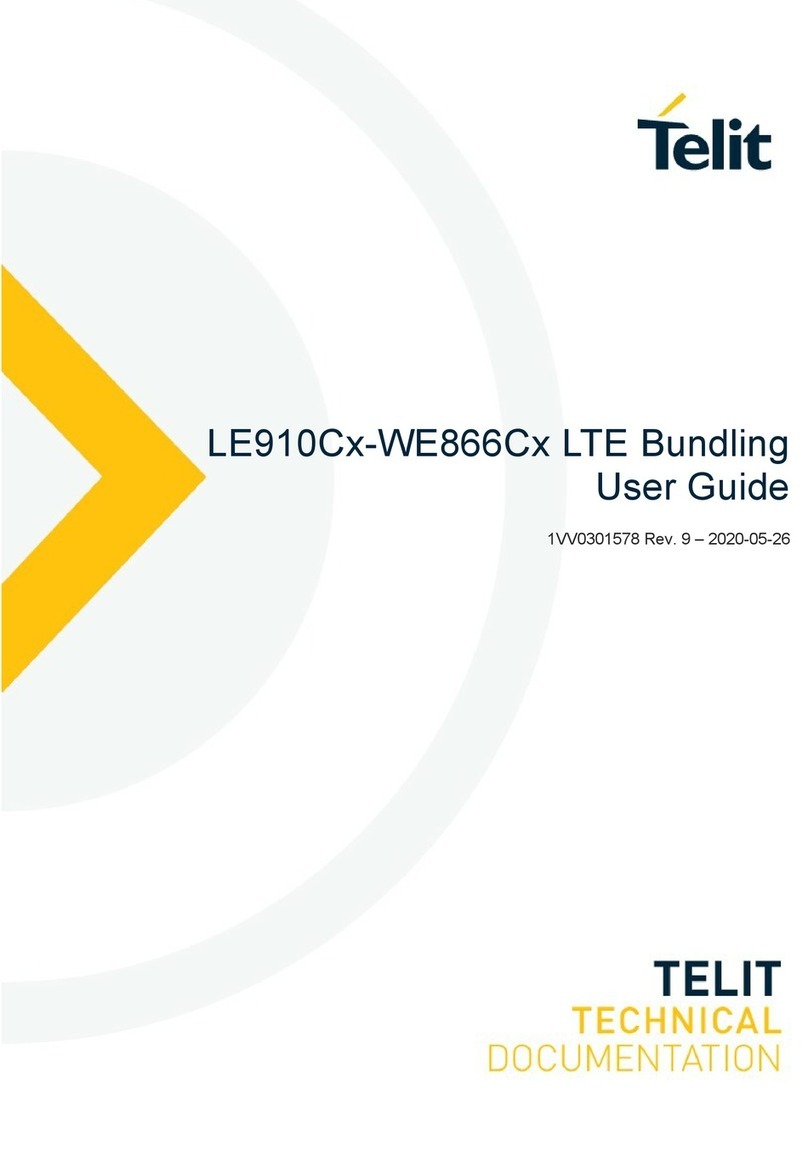
Telit Wireless Solutions
Telit Wireless Solutions LE910C series user guide

Omron
Omron V700-HMC71 Operation manual