PSM APT 1000 Series User manual

Installation & Operation
Instruction Manual
APT 1000 Series Transmitters
&
RFM Series Barriers & Termination Modules
Doc Ref: Man 087 Iss C October 2019
Burrell Road Industrial Estate
Haywards Heath, West Sussex RH16 1TW, UK
Tel: +44 (0)1444 410040 Fax: +44 (0)1444 410121
www.psmmarine.com E-mail: sales@psmmarine.com
PSM INSTRUMENTATION LTD

2
SECTION
TITLE
PAGE
1.0 Introduction 3
2.0 General Information 3
3.0 Product liability and warranty 3
4.0 Normal operation and maintenance 3
5.0 Instrument Return 3
6.0 EU conformity 3
7.0 Scope of delivery 4
8.0 Storage 4
9.0 Instrument identification 4
10.0 Instrument measurement principle 5
11.0 Instrument configuration 5
12.0 Measurement type 5
12.1 Absolute Sensors 5
12.2 Gauge Sensors 5
13.0 Installation of APT 1000 6
13.1 Mechanical installation 6
13.2 Electrical installation 8
14.0 ATEX and IECEx requirements 10
14.1 Barrier selection 10
15.0 Electromagnetic Compatibility 11
16.0 Mechanical Installation of RFM Series 11
16.1 Dimensional drawings RFM 1 & 4 and RFM ISR 12
16.2 RFM mounting Dimensions 14
16.3 Electrical connection of APT 1000 to RFM 1 (single transmitter) 15
16.4 Electrical connection of APT 1000 to RFM 4 (up to 4 transmitters) 16
16.5 Electrical connection of RFM ISR 17
17.0 System Interconnections 18
18.0 Network Cabling 21
19.0 Use of terminating resistors 22
20.0 APT 1000 Specification 23
21.0 APT 1000 Model Code 24
22.0 APT 1000 Dimensions 25

3
1.0 Introduction
This manual provides guidance on the installation and operation of the PSM APT 1000 Series of hydrostat-
ic pressure and level transmitters and the RFM family of termination modules and Safety Barriers. The
APT 1000 is a programmable instrument which features an RS485 communication port. Where this com-
munication capability is to be used to set the unit up and / or to read the instruments measured data, a sep-
arate PSM manual MAN 088 APT 1000 Functionality and Communications is also available which covers
this functionality.
2.0 General Information
Safety instructions for APT 1000 & RFM Series Barriers/Termination Enclosures.
To prevent any damage to the device or any injury to the user it is essential that you read the information in
this document and observe applicable national standards and safety requirements.
This document is provided to help facilitate the safe and efficient operation of the instrument.
3.0 Product liability and warranty
All apparatus is carefully examined and tested before leaving the PSM workshop and is sent out in perfect
order and condition. We, therefore, give the following Guarantee which takes the place of any Guarantee
by Statute, common law or otherwise. If within 12 months from date of despatch, any defect or fault is
discovered in any component of our manufacture, due to faulty material or bad workmanship, we undertake
to make good the defect without charge, provided that notice is given to us immediately on the discovery of
the defect and the defective components or parts thereof, are forwarded to us carriage paid for inspection.
This guarantee does not apply to defects caused by ordinary wear and tear, misuse, neglect, or by
circumstances over which we have no control.
Full terms and conditions are available from our website: www.psmmarine.com/about-us
4.0 Normal operation and maintenance
There is no routine schduled maintenance requirement for the APT 1000 or RFM modules. Periodic checks
should be made to ensure all wiring/cable glands are in good condition and terminations secure. Where the
APT 1000 is used in tanks liable to sludge or sedimentation, the sensing diaphragm should be examined at
appropriate intervals to ensure it is free from contaminants which may obstruct true reading of pressure.
If cleaning is required then EXTREME CARE must be taken to avoid damage to the diaphragm. Use a
solvent or water to loosen and flush the deposits and on no account use sharp or hard objects to scrape the
diaphragm. If necessary a soft brush may be used with care.
Damage caused to the diaphragm will result in loss of calibration and likely non-linearity / thermal sensitivity
to the instrument.
5.0 Instrument return
All equipment is carefully examined and tested before leaving the PSM workshop and is sent out in perfect
order and condition.
Should it prove necessary to return any equipment for inspection, please ensure you follow the process:
• Contact PSM for an RVN form and number
• The equipment must be accompanied by an RVN with clear instructions as to the reason for return
and what actions are requested.
• An explanation of the apparent fault together with details of the service conditions are also required.
• Health & Safety requirements mean that we must be fully aware of any potential hazards prior to
working on returns.
Full terms and conditions are available from: www.psmmarine.com/about-us
6.0 EU conformity
This product meets all of the applicable EU Directives and is supplied with an EU Declaration. Copies of
which are available on request.

4
7.0 Scope of delivery
Inspect the packaging and immediately report any signs of damage to your local agent or PSM Instrumen-
tation.
• APT 1000 Series - Specific model code will depend on your order specification
• Installation Operation & Maintenance Instruction Manual
• EU Declaration
8.0 Storage
• Store the instrument in a dry location
• Storage Temperature range –35°C to +85°C
9.0 Instrument identification
Each instrument is marked with a unique information, that identifies type and
construction options.
(1) The model code defines the construction of the sensor.
Refer to section 17.0 and 18.0 of this manual.
(1) Unique Serial number consisting of the PSM sales order . For example 190251 (03), followed by two
digits denote the sensors specific identification from the sales order.
(2) This is the actual range the sensor has been calibrated too and in what units of measure.
(3) The specific amount of cable that has been fitted to the sensor.
(4) The date of when the instrument was factory manufactured.
(5) The operating temperature of the instrument.
(6) The range of voltage that can be used for the instrument to operate.**
(7) Analogue Output signal that the instrument outputs (Can be disabled for digital only networks)
RS485 Modbus digital communications - always on
(8) The specific materials that have been used in the construction of the instrument
(9) Will identify the certificate number and any other additional conditions when the
Instrument is going to be installed into the hazardous area.
(11) Red is positive (+) of the 4—20mA loop.
(12) Black is negative (-) of the 4—20mA loop.
(13) White Data (A+) of the RS485 digital communications
(14) Green Data (B-) of the RS485 digital communications
(15) The screen can be connected to instrument earth
** Where the APT1000 is used as a 2 wire 4-20mA transmitter the maximum load in ohms that can be ap-
plied is determined by the available supply voltage based on the following formula
Supply Voltage -10 =Load in Ohms
0.02
Where the supply voltage is insufficient the transmitter will not be able to reach its full scale 20mA output.

5
10.0 Instrument measurement principle
APT 1000 Series level transmitters are designed for monitoring liquid levels and pressures on a wide range
of applications. The measurement principle is based on a highly accurate and stable pressure sensitive
MEMS piezo-resistive cell
The pressure measurement cell is isolated from the process by a diaphragm and an internal fluid fill
transmits the process pressure to it. Precise compensation for the effects of operating temperature change
is applied during manufacture by laser trimming of compensation resistors.
The output from the measurement cell is processed by the transmitters internal circuitry to generate a
numeric representation of pressure. This value may then be additionally scaled by user configurable
settings to provide both a Modbus RTU output and an industry standard 4-20mA signal.
The Modbus communication is bi-directional (half-duplex) it allows the user to set scaling and offset factors
such as SG values, sensor fitting height, and tank linearization tables. This means the APT1000 can output
meaningful data to a host Master Modbus device.
The transmitters 4-20mA may also be scaled to represent a number of different parameters. Full details of
scaling options are provided in PSM manual MAN 088 APT 1000 Functionality and Communications.
The Modbus communication is via an RS485 connection. This permits multiple APT1000 transmitters to be
connected on a single multi-drop network. PSM provide purpose designed Termination and Safety Barrier
modules - the RFM family - to facilitate simple network construction. These are covered later in this manual.
After assembly, all joints of the transmitter are laser welded and it is fully encapsulated internally.
A choice of construction materials for the wetted parts of the transmitter provide compatibility with most
process fluids.
11.0 Instrument configuration
The APT 1000 is fully user configurable in respect of both the Modbus and Current output signals. PSM
provide a free Windows PC utility to allow access to all user settings. Full details of the configuration
options are provided in PSM manual MAN 088 APT 1000 Functionality and Communications.
12.0 Measurement type
The APT 1000 is offered in two pressure measurement types.
12.1 Absolute sensors
Absolute pressure is measured relative to absolute zero pressure, as would be found in an absolute
vacuum. For this measurement the measurement cell is sealed with full vacuum applied internally.
The output from an absolute sensor will change both as a result of any change in process pressure and any
change in local barometric pressure. As a result, in order to determine actual process pressure / level from
the sensors output a barometric reference value must be applied. This is usually provided by a separate
input to the monitoring system from a sensor calibrated to measure barometric pressure.
12.2 Gauge sensors
In this case the measurement cell is vented to ambient air pressure through a vent tube in the sensors ca-
ble. This allows the outside ambient air pressure to be applied to the internal side of the cell to balance out
ambient barometric pressure. Therefore a vented gauge pressure sensor reads zero pressure when there
is no process pressure applied.
Calibration of the sensors is undertaken at PSM Instrumentations facility, all equipment used is externally
verified and traceable to UKAS standards.

6
13.0 Installation APT 1000 Transmitters
13.1 Mechanical Installation
Prior to installation it is recommended that the following checks are made:
• That any the units configuration is in accordance with the process parameters / tank height and that
the nominal range is suitable for the intended duty.
• Verify any instrument identification or tag number to ensure it is fitted in the correct location.
The cable is factory fitted to the APT 1000 ensure a pressure and liquid tight seal. and no attempt
should be made to remove the cable gland.
Instrument handling
Before and during installation the following precautions should be taken
• Do not touch the measurement cell of the transmitter
• Do not apply mains voltage to any cable conductor
• Ensure the APT cable sheathing is free from damage and defects
Sensor cable
The cable that is factory fitted to the transmitter is purpose designed for the application. It contains a nylon
vent tube which provides an atmospheric reference for the sensor if constructed for a “gauge” measure-
ment application. The end of the nylon tube has a short section of silicon tube fitted, which carries a sin-
tered filter. This filter provides a pressure path, but prevents any moisture entering the vent tube and
MUST remain in place. The cable may be shortened during installation but if so this filter must be trans-
ferred to the new cable end.
Note that the cable has 4 cores. The Red and Black cores are used for both excitation and the 4-20mA sig-
nal as what is commonly called a 2 wire transmitter. The White and Green cores are used for the RS485 /
Modbus connection to the unit. If the transmitter is to be used only in 4-20mA mode, these can be secured
to unused terminals or individually insulated by sleeving.
Note that if the transmitter is constructed as an “absolute” measuring device, then there is no requirement
to vent the instrument cable to atmosphere. Precautions must still be taken however to prevent moisture
ingress into the cable vent tube.
The cable construction is of sufficient strength to enable the sensor to be directly suspended in deep tanks
and reservoirs. The outer sheathing is a special material suitable for continuous immersion in water,and
many oils and chemicals. When handling the cable take particular care not to damage the outer sheathing,
and when securing using cable ties ensure that no sharp edges can cut the outer insulation or that the ca-
ble might be exposed to chafing by moving parts or vibration.
Ensure the cable is not bent to a radius less than 50mm.
When mounting the sensor allow sufficient free cable at the transmitter end to allow easy removal for test-
ing without straining the connection into the transmitter body.

7
Sensor fitting height
When a transmitter is used in tank level or volume applications it is essential to ensure that the sensor is
fitted at a known position and height above the bottom of the tank.
This data must be accurately recorded in the form of X,Y,Z coordinates referenced to known datums on the
vessel e.g. baseline, keel or frame numbers.
All calibration data, and any trim or heel tank level measurement correction in the monitoring equipment will
be related to this fitting position. If the sensor position is not accurately identified and in agreement with the
correction factors the displayed values will be incorrect.
Mounting
When mounting the unit, and depending upon the type of mounting, ensure that suitable gaskets or
sealants are employed to provide pressure tight seals. The sensor should not be mounted where it will be
subject to excessive or continuous vibration, extreme temperature fluctuation or risk of mechanical damage,
especially to the pressure sensitive diaphragm.
Secure the cable as necessary to prevent mechanical abrasion if it moves.
Do not secure the cable to any localised sources of high temperature heating such as steam coils used in
heavy oil tanks.
Mounting Options
The standards APT 1000 has an 1/2” BSPP male process connection with a Viton sealing ring. PSM can
provide a number of components and adapters for alternative mounting of the APT 1000. Please contact
PSM for further details.

8
13.2 Electrical installation APT 1000 Transmitters
Isolated power supplies
For all installations of the APT 1000 it is important that the instrument is powered from an isolated power
supply. The use of a non-isolated power source in a situation where the sensor is grounded by its installa-
tion could to lead to issues with any onboard earth fault monitoring system, unwanted earth current loops
and the possibility of instability / interference caused by any other equipment on the same power supply
The APT 1000 has dual outputs. Firstly it may be used as a standard analogue 2 wire 4-20mA output trans-
mitter, and secondly as a digital output device communicating via RS485 and using Modbus protocol. Either
or both modes can be used simultaneously and the electrical connection required will depend on the
intended use.
The sensor cable has 4 cores, Red, Black, Green, & White.
Connect Red conductor to +ve supply.
Connect Black conductor to –ve supply.
Where only the 4-20mA signal is being used then only the Red and Black conductors are used as shown in
the diagram below.
The Green and White conductors are used for the RS485 Serial communication. If only the 4-20mA signal
is to be used these should be connected to unused terminals or individually sheathed such that they cannot
make contact, either to each other or anything else.
Because the RS485 communications can also be used for configuring the 4-20mA signal it is suggested
that they are terminated such that temporary connection can be made if needed.
The ability to connect multiple APT 1000 transmitters on a single Multi-drop network provides savings in
cabling required and the possibility to communicate with a transmitter from any point on the network.
For simple construction of multi-drop networks PSM also provide three Remote Function Modules (RFM).
The RFM1 allows for termination of a single APT 1000 and network cables
The RFM4 allows for termination of up to 4 APT 1000 and network cables.
The RFM-ISR is a purpose designed and approved Safety Barrier. The APT 1000 may be supplied with
ATEX or IECEx certification suitable for hazardous area installation*. For such installations the RFM-ISR
provides energy limiting and protection for both power and communication lines feeding these APT 1000
transmitters.
* Approved Zener Safety Barriers and Galvanic Isolators to provide Intrinsic Safety protection.

9
Cable Termination
The cable is also provided with an overall braided screen. This braid can be cut back as below
The transmitter's cable is normally provided to the required length but if it is to be shortened on a Gauge
pressure type transmitter the nylon vent tube should be cut to a free length of approximately 20mm within
the enclosure, it must be ensured that this tube is not blocked or otherwise restricted and the silicon tube
containing the sintered filter must be re-fitted to the shortened length.
The termination enclosure MUST be vented where the APT 1000 transmitter is of the vented gauge type.
PSM’s RFM1 & RFM4 termination modules include a suitable vent.

10
14.0 ATEX and IECEx requirements
For intrinsically safe installations APT 1000 transmitters in the hazardous area must be connected to the
safe area via approved safety barriers. These barriers fall broadly into two categories:
• Zener barriers (based on the shunt diode principle)
• Galvanic isolators
Either type of barrier may be employed subject to it meeting the required safety description. PSM can pro-
vide guidance on a range of suitable barriers.
Shunt diode Zener barriers provide a resistor to limit the current flow, a (non-replaceable) fuse to limit pow-
er and a Zener diode arrangement to limit voltage levels and provide a safe path to earth. Zener barriers tie
the 0v side of the transmitter supply to earth either directly or via a
diode arrangement. They must be connected to a high integrity earth to function as intended.
Intrinsically Safe Earth Connections are required to be made but should be made to a separate instrumen-
tation ‘Clean Earth’
There are generally two earthing systems recognised. The so-called 'dirty earth' has all the non-critical data
equipment and general equipment attached to it. The 'clean earth' has all the critical data systems attached
to it on the basis that less ‘noise’ will be found on this earth
Galvanic Isolators provide full galvanic isolation between safe and hazardous area circuits with power limit-
ing achieved by using a diode resistor network similar to that of a shunt-diode barrier. They do not require a
high integrity earth, each side may be earthed independently overcoming potential issues with earth loops.
For all intrinsically safe installations of the APT 1000 it is essential that this instrument is powered from an
isolated power supply. When a zener barrier is employed for power limiting this will effectively tie the sensor
supply 0V to earth, meaning a non-isolated power source can lead to issues with any onboard earth fault
monitoring system, resulting in unwanted earth current loops and instability / interference caused by any
other equipment on the same power supply
The use of an isolated supply means that there is no direct connection between the 0 volts / I.S. earth at the
sensor and the 0 volts at the ships supply
The PSM RFM-ISR is a purpose developed Zener Safety Barrier. It provides an advantage over general
single channel Zener Barriers or Galvanic Isolators in that ia single RFM-ISR can be used to protect multi-
ple APT 1000 transmitters. Protection is provided for both the DC power and Serial communication lines
into the Hazardous zone.
Certificates available on request
14.1 Barrier selection
When selecting a Barrier the following parameters must be complied with:
Ui = 28Vdc
Ii = 150mA
Pi = 0.8W
Li = 0
Ci = 0

11
15.0 Electromagnetic Compatibility
No special conditions are required to maintain EMC protection.
16.0 Mechanical Installation of RFM series
There are two versions of the RFM enclosure, a lightweight Aluminium version intended for installation in
locations where it will be protected from corrosive effects of Salt Water etc, and a heavy duty Steel enclo-
sure suitable for installation on open deck conditions onboard a Ship.
In general the location should be selected to protect the enclosure from damage from impact or excessive
vibration.
Connection of cabling via the correct cable glands is essential to ensure a weather-tight seal. The enclosure
is provided with M20 cable gland threads. Any unused cable entry points must be sealed off with suitable
blanking plugs.
Where the RFM modules are to be used with Gauge type APT 1000 transmitters they are fitted with a sin-
tered filter plug in the enclosure to provide a an atmospheric reference for the APT 1000 cable vent tube,
This vent must remain in place and not removed or painted over.
If the RFM module is installed in an area subject to flooding, or local pressurisation / vacuum, then a vent
pipe should replace the filter plug. This should be a minimum diameter of 6mm and terminate in a dry, at-
mospheric pressure location. Where there is no possibility of moisture ingress.
For Sealed Absolute type transmitters no atmospheric pressure reference is needed within the RFM
module.
Refer to the following drawings for outline and mounting dimensions for the two RFM enclosure types.

12
16.1 Dimensional drawings RFM 1 & 4 and RFM ISR
Aluminium case construction
Painted carbon steel case construction
105
235
200
271
233
165
300
325
87
140
105
235
200
271
233
165
300
325
87
140

13
Aluminium RFM enclosure
Epoxy Painted Mild Steel RFM enclosure
6 X M20
Cable Glands
Earth tags

14
16.2 RFM Mounting Dimensions
The Aluminum RFM enclosure is provided with a mounting bracket, which is installed prior to the enclosure
being fitted.
Bracket dimensions
Once the mounting bracket is fixed in place, the enclosure simply clips in and the centre M20 glands at
either end are screwed down, securing the enclosure in place.
Painted mild steel RFM enclosure has four mounting holes located around the base
The enclosure can also be welded around the base to the specified location. If this mounting option is cho-
sen a suitable protective coating must be applied to all welded areas.
Location of RFM modules
Both RFM1 and RFM4 modules may be mounted in either a Safe or Hazardous Area. If located in a Haz-
ardous Area both the power and communication cabling MUST be protected in accordance with I.S. re-
quirements meaning a suitable Safety Barrier or Galvanic Isolator must be used. As detailed earlier in this
manual. This Safety Barrier / Isolator MUST be fitted in the Safe Area.
NOTE: If an RFM-ISR module is used to provide the required safety it must be ensured that the Hazardous
and Safe area cables are routed via the correct cable glands. i.e. Hazardous area on one side and Safe
area on the other. Cables MUST NOT pass internally across the Barrier’s circuit assembly.
45 mm 100 mm
178.50 mm
236 mm
140mm
300mm
325mm
165mm

15
16.3 Electrical connection of APT 1000 to RFM 1 (single transmitter)
Refer to the earlier section covering APT 1000 electrical connection for details of the cable termination
method.
The RFM 1 module provides connection and Modbus termination for one APT 1000 transmitter
Termination descriptions
Links LK6, LK7, LK8 MUST NOT be fitted when used in an intrinsically safe
installation.
Ensure Link LK9 IS FITTED FOR ALL INSTALLATIONS
J5 8-30Vdc Power supply
J8 RS485/Modbus communications (A + Data / B - Data)
J9 Supply (Red + Black -)
J10 RS485/Modbus (White + Data / Green - Data)
J11 Optional connection to local 4-20mA Gauge.
LINK FITTED IF NOT CONNECTED TO GAUGE
J6 8-30Vdc Power supply - On to next RFM
J7 RS485/Modbus - On to next RFM
J4 & J3 9 way D-Sub connector to optional Modules

16
16.4 Electrical connection of APT 1000 to RFM 4 (up to 4 transmitters)
Refer to the earlier section covering APT 1000 electrical connection for details of the cable termination
method.
The RFM 4 module provides connection and Modbus termination for up to four APT 1000 transmitters
Links LK6 - LK12 MUST NOT be fitted when used in an intrinsically safe installation.
Ensure Link LK9 IS FITTED FOR ALL INSTALLATIONS
PWRIN 8-30 Vdc Power supply
COMMSIN RS485/Modbus communications (A + Data B -
Data)
Transmitter
Connections
Connection to APT 1000
(Red + Black -)
(A White + Data B Green - Data)
PWRONW 8-30 Vdc Power supply - On to next RFM
COMMSONW RS485 Modbus communications - On to next RFM

17
16.5 Electrical connection of RFM ISR
The RFM ISR module provides safety barriers for power and data connections to RFM 1 & 4 modules
when used as part of an APT 1000 network
J9/J10 are connected either directly to an APT 1000 or an RFM termination enclosure.
Ensure Links LK2—LK8 are NOT FITTED (links 6 to 8 under barrier board)
Ensure Link LK1,9 and 10 IS FITTED (Link 1 under barrier board)
REMOVE the factory fitted earth bonding strap between the “IS earth” stud and the case ONLY IF an
external clean instrument earth is available.
The I.S. earth stud on the circuit board should then be connected directly to the external clean instrument
earth via either:
• 2 x Copper conductors each minimum csa 1.5mm2
• 1 x Copper conductor minimum csa 4mm2
These Links
Omitted If
Module
Fitted
+
-
+
-
+
-
IS
Earth
4 - 20mA
Gauge
Power
Comms
Power In Comms In Power On Comms On
+
-
ABAB
A
B
J5
J8
J6
J7
J9
J10
J11
LK2
LK4
LK5
LK3
LK9
Transmitter /RFM1/RFM4
Connections
Power & RS485
Connections
Power & RS485
Connectionst to
Next RFM-ISR
RFM-ISR Connection Details
Link Always Fitted
Safe Area Connections
Hazardous Area Connections
LK10
LK1
J5 15-35Vdc Power supply
J8 RS485 Modbus communications (A + Data B - Data)
J9 12Vdc Intrinsically Safe Supply (Red + Black -)
J10 Intrinsically Safe RS485/Modbus (White + Data Green - Data)
J11 Optional connection to local 4-20mA Gauge. Linked out if not used
J6 15-35Vdc Power supply - On to next RFM-ISR (in safe area)
J7 RS485/Modbus - On to next RFM-ISR (in safe area)
J4 & J3 9 way D-Sub connector to Barrier Module

18
17.0 System Interconnections
Analog and Digital cable identification
Single APT 1000 Safe Area Connection
Single APT
1000 Hazardous Area Connection using a Zener Barrier
Red + Power Analogue
(4-20 mA)
White A (+ Data) RS485
Digital
(Modbus)
Black - Power Green B (- Data)
2 CORE SCREENED CABLE
2 CORE SCREENED CABLE
2 CORE SCREENED CABLE
INSTALLATION WITH EXISITING INSTRUMENTATION WITH ADDITIONAL REMOTE DISPLAY
Existing Instrumentation
providing isolated 24Vdc
supply on 2 wire
4-20mA signal inputs
Breather Port
LOCAL JB
RFM 1
4-20 mA Remote
Display / Measurement
Device
Existing Instrumentation
providing isolated 24Vdc
supply on 2 wire
4-20mA signal inputs
Isolated 24Vdc
Supply
4-20 mA Remote
Display / Measurement
Device
RFM 1
STAND ALONE INSTALLATION
INSTALLATION WITH EXISITING INSTRUMENTATION
2 CORE SCREENED CABLE
2 CORE SCREENED CABLE
Isolated 24Vdc
Supply
4-20 mA Remote
Display / Measurement
Device
Existing Instrumentation
providing isolated 24Vdc
supply on 2 wire
4-20mA signal inputs
4-20 mA Remote
Display / Measurement
Device
LOCAL JB
I.S. RATED
Breather Port
Existing Instrumentation
providing isolated 24Vdc
supply on 2 wire
4-20mA signal inputs
STAND ALONE INSTALLATION
INSTALLATION WITH EXISITING INSTRUMENTATION
INSTALLATION WITH EXISITING INSTRUMENTATION WITH ADDITIONAL REMOTE DISPLAY
2 CORE SCREENED CABLE
LOCAL JB
I.S. RATED
Breather Port
2 CORE SCREENED CABLE
IS
ZENER
BARRIER
SAFE
ZONE
HAZARDOUS
ZONE
I.S.
EARTH
2 CORE SCREENED CABLE
2 CORE SCREENED CABLE
IS
ZENER
BARRIER
SAFE
ZONE
HAZARDOUS
ZONE
I.S.
EARTH
2 CORE SCREENED CABLE
LOCAL JB
I.S. RATED
Breather Port
2 CORE SCREENED CABLE
IS
ZENER
BARRIER
SAFE
ZONE
HAZARDOUS
ZONE
I.S.
EARTH
2 CORE SCREENED CABLE
2 CORE SCREENED CABLE

19
Single APT 1000 4—20 mA hazardous area using a Galvanic Isolator
Single APT
1000 digital mode Safe Area Connection
Single APT 1000 digital mode hazardous area using a Zener Barrier connection
Isolated 24Vdc
Supply
4-20 mA Remote
Display / Measurement
Device
4-20 mA Remote
Display / Measurement
Device
STAND ALONE INSTALLATION
INSTALLATION WITH EXISITING INSTRUMENTATION WITH ADDITIONAL REMOTE DISPLAY
LOCAL JB
I.S. RATED
Breather Port
2 CORE SCREENED CABLE
IS
GALVANIC
BARRIER
SAFE
ZONE
HAZARDOUS
ZONE
2 CORE SCREENED CABLE
2 CORE SCREENED CABLE
LOCAL JB
I.S. RATED
Breather Port
2 CORE SCREENED CABLE
SAFE
ZONE
HAZARDOUS
ZONE
2 CORE SCREENED CABLE
2 CORE SCREENED CABLE
Isolated 24Vdc
Supply
INSTALLATION WITH EXISTING INSTRUMENTATION
LOCAL JB
I.S. RATED
Breather Port
2 CORE SCREENED CABLE
IS
GALVANIC
BARRIER
SAFE
ZONE
HAZARDOUS
ZONE
2 CORE SCREENED CABLE
2 CORE SCREENED CABLE
Existing Instrumentation
4-20mA signal inputs
IS
GALVANIC
BARRIER
Existing Instrumentation
4-20mA signal inputs
Isolated 24Vdc
Supply
2 CORE SCREENED CABLE
Isolated 24Vdc
Supply
Modbus Display
Device
RFM 1
2 CORE SCREENED CABLE
TWISTED PAIR
SCREENED CABLE
Isolated
RS 485
Interface
TWISTED PAIR
SCREENED
CABLE
Isolated 24Vdc
Supply
Modbus Display
Device
RFM - ISR
2 CORE SCREENED CABLE
TWISTED PAIR
SCREENED CABLE
Isolated
RS 485
Interface
TWISTED PAIR
SCREENED
CABLE
I.S.
EARTH
SAFE
ZONE
HAZARDOUS
ZONE
Minimum 4mm
²
Copper Conductor
2 x TWISTED PAIR
SCREENED CABLE
RFM 1

20
Single APT 1000 digital mode hazardous area using a Galvanic Isolator connection
Multiple APT 1000 digital mode hazardous area using a Zener Barrier connection
Isolated 24Vdc
Supply
Modbus Display
Device
2 CORE SCREENED CABLE
TWISTED PAIR
SCREENED CABLE
Isolated
RS 485
Interface
TWISTED PAIR
SCREENED
CABLE
SAFE
ZONE
HAZARDOUS
ZONE
2 CORE SCREENED CABLE
RFM 1
IS
GALVANIC
POWER
BARRIER
2 CORE SCREENED CABLE
IS
GALVANIC
COMMS
BARRIER
TWISTED PAIR SCREENED CABLE
Isolated 24Vdc
Supply
Modbus Display
Device
RFM - ISR
2 CORE SCREENED CABLE
TWISTED PAIR
SCREENED CABLE
Isolated
RS 485
Interface
TWISTED PAIR
SCREENED
CABLE
I.S.
EARTH
SAFE
ZONE
HAZARDOUS
ZONE
Minimum 4mm
²
Copper Conductor
2 x TWISTED PAIR
SCREENED CABLE
RFM 1
RFM 1
RFM 4RFM 4
2 x TWISTED PAIR
SCREENED CABLE
2 x TWISTED PAIR
SCREENED CABLE
2 x TWISTED PAIR
SCREENED CABLE
2 x TWISTED PAIR
SCREENED CABLE
This manual suits for next models
2
Table of contents
Other PSM Transmitter manuals
Popular Transmitter manuals by other brands
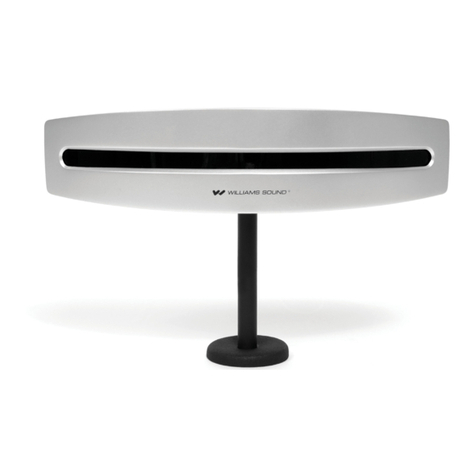
Williams Sound
Williams Sound WIR TX75 PRO user manual

Kistler-Morse
Kistler-Morse STXplus Installation and operation manual

IFM Electronic
IFM Electronic efector 600 operating instructions
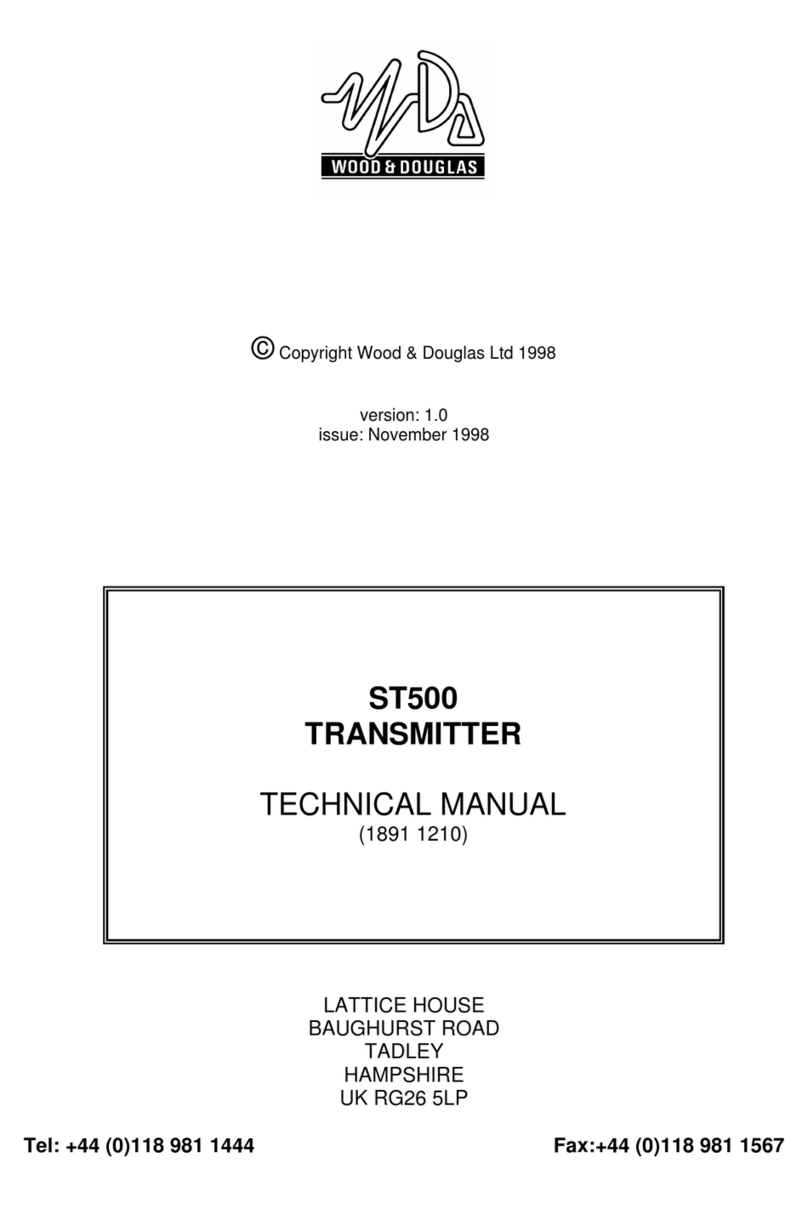
Wood and Douglas
Wood and Douglas ST500 Technical manual
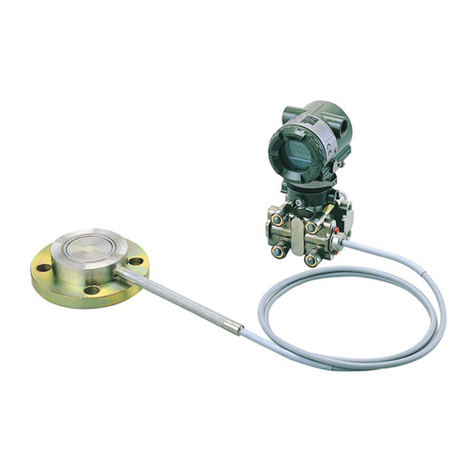
YOKOGAWA
YOKOGAWA Dpharp EJA438N user manual
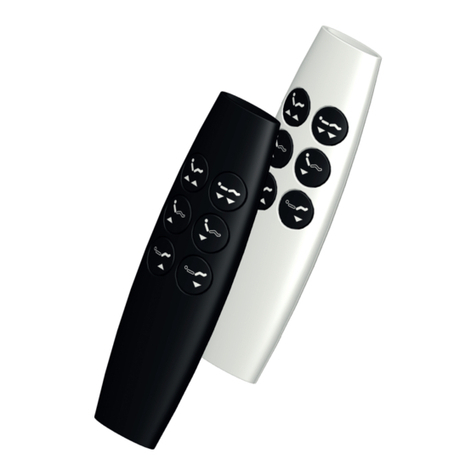
Vibradorm
Vibradorm VFF/DB-Basic operating instructions