PureAire Monitoring Systems BC TX-FM User manual

Model TX-FM/FN
Sensor Head
Instruction Manual
PureAire Monitoring Systems, Inc.
1140 Ensell Road
Lake Zurich, Illinois 60047
Phone: 847-726-6000
Fax: 847-726-6051
Toll-Free: 888-788-8050
Pureairemonitoring.com
Rev 1.0 August 2023

PureAire Monitoring Systems, Inc.
1
Welcome to PureAire Monitoring Systems
I’d like to thank you for investing in our continuous life safety and process control toxic gas
monitoring systems.
PureAire offers an unbeatable combination of experience and innovation in solving the safety
and environmental needs of our customers. We’re capable of providing small systems of a few
points to a total multi-point turnkey computerized package.
PureAire’s proprietary sensor cell technology and state-of-the-art electronics are designed to
interface with the latest distributive or PLC based control systems. We believe that our experience,
innovative products and commitment to service will satisfy your specific monitoring needs now and
in the future.
Our growth is a result of our total commitment to supporting our customers. We’re available 24
hours a day, 7 days a week to help you when you need us. Our 24 hour Emergency phone number
is 1-847-541-1968. We can provide field service, preventative maintenance programs and training
to your technicians in the operation of our equipment. Our goal is to provide the best after sale
service and support in the industry. That’s just one way PureAire takes that extra step to ensure
your complete satisfaction.
Thank you again for investing in PureAire Monitoring Systems for your monitoring needs and
I’m proud to welcome you to our family of valued and satisfied customers.
Sincerely,
Albert A. Carrino
President

PureAire Monitoring Systems, Inc.
2

PureAire Monitoring Systems, Inc.
3
Table of Contents
1: Introduction........................................................................................... 3
1.1 Component Identification............................................................. 3
1.2 Component Identification TX-1100FK ........................................ 4
2: Specifications........................................................................................ 6
2.1 Performance Specifications.......................................................... 6
2.2 Gas Detection System .................................................................. 6
2.3 Signal Outputs .............................................................................. 6
2.4 Electrical Requirements ............................................................... 6
2.5 Physical Characteristics................................................................ 7
3: Installation ............................................................................................ 8
3.1 Site Requirements ........................................................................ 8
3.2 Mounting ...................................................................................... 8
3.3 Sensor Installation ........................................................................ 8
3.4 Wiring......................................................................................... 10
3.5 Initial Startup.............................................................................. 11
4: Normal Operation ............................................................................... 12
4.1 Concentration Display and Indicator Lights............................... 12
4.2 Routine Maintenance Schedule.................................................. 12
4.3 Loss of Power Indicator ............................................................. 13
5: Maintenance & Calibration................................................................. 14
5.1 Sensor Cell Removal and Installation ........................................ 14
5.2 Electrolyte Replacement............................................................. 16
5.3 Sensor Calibration ...................................................................... 21
6: Diagrams and Schematics
6.1 TX-FMD Dimensional Schematic.............................................. 25
6.2 TX-FM Dimensional Schematic ................................................ 26
6.3 TX-FN Dimensional Schematic ................................................. 27
7: Appendix ............................................................................................ 28

PureAire Monitoring Systems, Inc.
4
1: Introduction
TX-FM/FN series sensor heads are self-contained gas detection systems suitable
for a wide range hazardous gases, including ammonia, chlorine, HCl, and
hydrogen. Each system consists of an amperometric, electrochemical sensor cell
and two-wire transmitter. TX-FM/FN series sensor heads may be used as stand-
alone gas detectors or linked to an optional controller (RX-1G) or your own
centralized control and surveillance system.
The transmitter is available either with a local display (FM series) or without a
local display (FN series).
1.1 Component Identification
1.1.1 Overall System Composition
The TX-FM/FN may be integrated into the overall hazardous gas monitoring
system as shown in the following drawing. It may also be used as a stand-alone
detection system.
1.1.2 Front View
VR1
VR4
VR2
VR3
CN3
CN1
CN2
J1
VR5
SPAN
ZERO
max.
min.
123
4
5
6
7
89
10
11
12
13
1 2 3
1 2 3 4
1. 4-20 mA Signal Output Terminal — This connection serves as both the
4-20 mA output connection and 24 VDC power input connection. See section
3: Installation for more information.
2. Calibration Jack — This port is used when calibrating non-display units.
13

PureAire Monitoring Systems, Inc.
5
3. Sensor Cable Terminal Block — This terminal is used to connect the
sensor cable.
4. Span Potentiometer — This potentiometer is used to adjust the sensitivity
of the sensor cell. It should only be adjusted when calibrating the instrument.
5. Zero Potentiometer — This potentiometer is used to adjust the instrument’s
4 mA analog output signal to ensure that it is transmitting a 4 mA signal
when the instrument is reading a zero concentration. On FM units, this pot is
located on the front panel; on FN units, it is located on the left hand
connector.
6. Sensor Holder — Serves as a mounting bracket for the sensor.
7. Sensor Fastening Screw — Holds sensor to the sensor holder.
8. Sensor Cover — This cover protects the gas sensor. It threads onto the
sensor holder.
9. Gas Sensor — An amperometric, electrochemical sensor which detects and
measures the target gas. Different gas sensors are required to detect different
gases. When exposed to the target gas, the sensor outputs an electrical signal
proportional to the gas concentration.
10. Cable Port — This is the opening in the transmitter housing for connecting
the 4-20 mA output and 24 VDC power cable.
11. Transmitter Cover — A removable, waterproof cover that protects the
interior of the transmitter.
12. Mounting Holes — Mounting brackets/holes are provided on both sides of
the transmitter housing as well as within the housing itself to permit
convenient wall mounting.
13. Transmitter Cover Fasteners — These captive screws secure the
transmitter cover in place.
1.2 Component Identification TX-1100FK O2
1.2.1 Overall System Composition
The TX-1100FK may be integrated into the overall hazardous gas monitoring
system as shown in the following drawing. It may also be used as a stand-alone
detection system.

PureAire Monitoring Systems, Inc.
6
1.2.2 Front View
1. Sensor Cover — This cover protects the gas sensor. It fastens directly to the
transmitter Nema 4X enclosure.
2. Gas Sensor — An amperometric, electrochemical sensor which detects and
measures the target gas. Different gas sensors are required to detect different
gases. When exposed to the target gas, the sensor outputs an electrical signal
proportional to the gas concentration.
3. Cable Port — This is the opening in the transmitter housing for connecting
the 4-20 mA output and 24 VDC power cable.
4. Transmitter Cover — A removable, waterproof cover that protects the
interior of the transmitter.
5. Transmitter Cover Fasteners — These captive screws secure the
transmitter cover in place.
6. Panel Knob — Pull to unlock and open the front panel. This provides
access to the power terminal Phoenix connector.
1 & 2
3
4
5
6

PureAire Monitoring Systems, Inc.
7
2: Specifications
NOTE: Due to our commitment to continual product improvement, all
specifications are subject to change without notice.
2.1 Performance Specifications
Models: TX-FM — Single point, with local analog display.
TX-FMD — Single point, with local digital display.
TX-FHD — Single point, with local digital display and remote sensor cell
TX-FN — Single point, without local analog display.
TX-1100FK — Single point, with local analog display
Sensor Type: Diffusion type electrochemical cell (2 or 3 wire);
plug-in sensors and sensors configured for remote installation also available.
TX-1100FK – zirconium oxide sensor cell
Response Time: Within 30 seconds to T90.
Repeatability: ±10% of full scale.
Fault Indicators: Loss of VDC power (4 mA signal drops to 0).
Operating Temperature: 14° to 113°F (-10° to +45°C); consult PureAire for lower operating temperatures.
Humidity: Sensor dependent; typically 20 to 95% RH; consult PureAire for sensors which
can operate in 100% condensing RH environments.
2.2 Gas Detection System
Type: Proprietary electrochemical gas sensor; renewable.
Disposable sensors also available.
Sensor Life: 4 to 5 years under normal conditions;
1-2 years for disposable sensors.
Detectable Gases: Consult PureAire.
2.3 Signal Outputs
Local Display: TX-FM — Analog meter calibrated for the specific target gas.
TX-FMD — Digital display calibrated for the specific target gas.
TX-FHD — Digital display calibrated for the specific target gas.
TX-FN — No local readout.
TX-1100FK — Analog meter calibrated for oxygen
Analog Output: DC 4-20 mA (2-wire system).
TX-1100-FK DC 4-20mA (3-wire system)
2.4 Electrical Requirements
Power: 24 VDC external power.
Consumption: Approximately 1.0 watt
TX-1100FK - 500mA current
NOTE: The TX-1100FK O2 monitor requires a 5-minute warm-up.

PureAire Monitoring Systems, Inc.
8
2.5 Physical Characteristics
Dimensions: 4.9 (W) x 6 (H) x 2.54 (D) inches;
125 x 177 x 75 mm
Weight: 1.1 pounds (0.5 kg)
Enclosure Type: General purpose IP 65 NEMA 4X; not intended for explosive atmospheres.
Optional intrinsic safety barrier available for installation in Class I, Division 1,
Group B,C, and D hazardous areas.
Installation Options: Low temperature sensor enclosure.
Bulkhead fittings for remote sensor installation.

PureAire Monitoring Systems, Inc.
9
3: Installation
3.1 Site Requirements
The TX-FM/FN/FK Sensor Head should be mounted in an area free of vibration
and electrical noise or interference. If possible, avoid areas with high
temperatures or relative humidity.
The unit should be installed in a location where gas leaks are likely to occur or
where released gases may accumulate. Air flow within the monitored area, the
characteristics of the target gas (lighter or heavier than air), and the position of
work stations and personnel should all be considered in determining the most
suitable installation location.
Allow sufficient space around the instrument to permit access for maintenance
and calibration.
WARNING: The TX-FM/FN is not designed for installation in hazardous areas.
Consult PureAire for information on enclosures for use in hazardous
environments.
3.2 Mounting
IMPORTANT: The TX-FM/FM must be mounted with the sensor pointed
directly down. Do not install with the sensor at greater than a 45° angle from
vertical. Do not install the sensor cell horizontal.
The TX-FM/FN is designed primarily for wall mounting and should be installed
no closer than 8.85 inches (260 mm) above floor level.
See Section 6 for mounting schematics.
3.3 Sensor Installation
NOTE: The following applies to type “D” diffusion sensors only. Consult
PureAire for installation information on plug-in type sensors.
IMPORTANT: Be careful not to turn the sensor or touch the membrane on the
bottom of the sensor during installation.
1. Remove the transmitter cover. It is held in place by captive screws mounted
in each of its four corners.
2. Remove the sensor cover by rotating it counterclockwise (right to left).
3. Insert the sensor cable through the sensor holder and into the transmitter
housing.
4. Carefully push the top of the sensor into the sensor holder and fasten it in
place by gently turning the fastening screw. Do not overtighten!
5. Replace the sensor cover.
6. Connect the sensor cable to the sensor cable terminal block. Depending on
the gas being monitored, the sensor cable will have either three or four wires.
IMPORTANT: Remove the shorting wire or current generator from the black
and white sensor cell wires before connecting the sensor cell to the transmitter.

PureAire Monitoring Systems, Inc.
10
NOTE: The terminal block may be removed from the printed circuit board to
make these connections. Be sure to replace the terminal block securely once all
connections have been made.
Sensor Cable Type Wire Color Location
3-Wire Sensor Cable
White
Black
Shield
Terminal 2
Terminal 3
Terminal 4
4-Wire Sensor Cable
Black
White
Red
Shield
Terminal 1
Terminal 2
Terminal 3
Terminal 4
1 2 3 4
SENSOR CABLE
white
black
shield
2-Electrode Sensor Wiring
1 2 3 4
black
white
shield
red
SENSOR CABLE
3-Electrode Sensor Wiring
NOTE: The TX-1100FK oxygen zirconium sensor cell is supplied permanently
connected to the transmitter board.

PureAire Monitoring Systems, Inc.
11
3.4 Wiring
The TX-FM/FN and TX-1100FK uses a three conductor, 18 AWG stranded
shielded cable. PureAire recommends the use of a General Cable #E2203S.30.86
or equivalent for analog output and 24 VDC power input. The maximum
permissible cable length is 0.62 miles (1 km).
The analog out and VDC power in connections are made on the 4-20 mA signal
output terminal inside the transmitter housing. These connections are made as
follows:
Terminal
Number
Connection Terminal
Number
Connection
Terminal 1 + Terminal 1 +
Terminal 2 -- Terminal 2 mA
Terminal 3 Shield Terminal 3 Common
3.4.1 Non-Hazardous Areas
TWO WIRE TRANSMITTER
1Km MAX.
LOAD
+
TX-[ ] FM
Gas Monitoring System
4
2
3
1
2
3
1
1.25sq x2 CVV-S
4-20mA Signal
GS-[ ] DX
White
Black
Shield
Shield
Sensor
CN1
CN3
+
-
GND
Max. 600ohm
Power Supply
DC 24V
5
CN1
CN2
123C
MA
+
DC 24V POWER SUPPLY
GAS
MONITORING
SYSTEM
LOAD
EARTH
+ 24 V DC
MA
C
MAX. 600
PC-1280A
TX-1100FK Oxygen Monitoring System
TX-1100FK Oxygen
Two wire Transmitter TX-[ ]FM

PureAire Monitoring Systems, Inc.
12
3.4.2 Hazardous Areas
If the TX-FM/FN transmitter is installed in a Class I, Division 1, Group B, C, or
D hazardous area, the optional safety barrier must be installed between the
transmitter and control panel.
CAUTION: The TX-1100FK O2system cannot operate in Class 1
environments.
E
1
2
3
4
1
2
3
Hazadorous Area Non Hazadorous Area
Two wire transmitter
White
B lac k
Shield
Sensor
GS-[ ] DX
TG-[ ] FM
CN1 CN2
+
-
Shield
GND
1
2
3
4
Safety Barrier
MTL 788+
Gas Monitoring System
LOAD
+
-
DC 24V
Power Supply
Max.250ohm
3.5 Initial Startup
Once installation of the gas detector has been completed, it is ready for startup.
The following procedures should be performed before putting the instrument into
operation:
1. Check the integrity of all wiring.
2. Apply 24 VDC power.
The instrument should now be operating properly.
NOTE: The TX-1100FK O2 monitor requires up to a 5-minute warm-up. The
indicator needle will remain at zero until initial warm-up

PureAire Monitoring Systems, Inc.
13
4: Normal Operation
The Model TX-FM/FN Sensor Head is a single point monitor designed for the
continuous detection and measurement of hazardous gas leaks.
4.1 Concentration Display and Indicator Lights
NOTE: The following applies to Model TX-FM and Model TX-FMD instruments
only. The TX-FN is a non-display unit.
4.1.1 Concentration Meter
This is a real time display of the measured concentration of the target gas. The
target gas and units of measure (PPM, PPB, etc.) are indicated on the front of the
instrument.
NOTE: Upon initial power up, the TX-1100FK O2 indicator will remain at
zero until initial warm-up. Time for warm-up is approximately 3-5 minutes.
4.1.1 Power LED
This LED is lit when the instrument is operating properly. It will get brighter as
the measured gas concentration increases. (Not available on TX-1100FK)
4.1.2 Test Button
This button is used to test the 4-20 mA output signal. When pressed, it outputs a
22 mA signal. (Not available on TX-1100FK)
CAUTION: Disable any connected alarms before testing. Failure to do so will
activate any connected alarm contacts.
4.2 Routine Maintenance Schedule
Continuous gas detection systems depended upon to measure and detect
hazardous gas leaks in the workplace require periodic maintenance to ensure
proper operation. The frequency with which this routine maintenance is required
depends on the environment, since temperature, humidity, gas concentrations,
and dust all affect system operation.
The following table is intended to serve as a general guideline for routine
maintenance. The conditions in your particular application, as well as your
organization’s maintenance policies, will ultimately determine the best routine
maintenance schedule for your equipment.

PureAire Monitoring Systems, Inc.
14
4.2.1 Routine Visual Checks
TX-FM
(DISPLAY UNIT)
TX-FN
(NO DISPLAY)
Items to check Check for power and
proper operation
Check for power and
proper operation
Condition / status
when operating
properly
Should read “0”
when no gas is
present
Unit should be
outputting a 4 mA
signal when no gas
is present
Corrective actions If meter reads higher
than “0” in a zero
gas condition, adjust
as required to the
environment
If analog signal is
higher than 4 mA in
a zero gas condition,
adjust as required to
the environment
TX-1100FK O2 Meter must indicate
ambient O2levels of
20.9%. The mA
output for normal
ambient O2level is
17.37mA.
4.2.2 Recommended Routine Maintenance Schedule
Routine Visual Checks Monthly
Electrolyte Replacement Every 6 months *
Sensor O-ring and Membrane Replacement Every 6 months *
Sensor Calibration Every 6 months *
TX-1100FK O2Test with N2every 6 months**
*NOTE: Scrubber monitoring systems will require more preventative
maintenance due to the harsh scrubber environment. Precipitate build-up and dirt
will inhibit the gas transfer to the cell and result in a lower sensor cell signal
output.
**NOTE: The O2monitoring system will always read 20.9% in a normal
ambient environment. To test the O2monitoring system, subject it to nitrogen
and the reading will fall to zero.
4.3 Loss of Power Indicator
In the event the TX-FM/FN Sensor Head loses VDC power, the 4-20 mA analog
output signal drops to 0.

PureAire Monitoring Systems, Inc.
15
5: Maintenance & Calibration
Maintenance and calibration should be performed only by qualified personnel.
5.1 Sensor Cell Removal and Installation
5.1.1 Sensor Removal
1. Remove the cover from the transmitter housing.
2. Unplug the sensor connection terminal block from the printed circuit board.
3. Remove the sensor cover by rotating counter-clockwise (right to left).
4. Loosen the sensor fastening screw.
5. Pull the sensor out of the sensor holder.
CAUTION: Do not twist the sensor; this may loosen the cap covering the
working electrode.
CAUTION: Avoid spilling electrolyte out of the small opening on the side of the
sensor.
IMPORTANT: Do not touch the membrane at the bottom of the sensor. Oil
from your hands or fingers will adversely affect performance.
123
VR1
VR4
VR2
VR3
CN3
CN1
CN2
J1
VR5
SPAN
ZERO
max.
min.
SPAN ADJUSTMENT
ZERO ADJUSTMENT
INDICATOR JACK
SENSOR
SENSOR ADAPTER
CALIBRATION GAS
INLET
1 2 3 4
NOTE: Zero adjustment pot is located directly on the printed circuit board for
the TX-FN. On the TX-FM and FMD, the zero pot is located on the face plate of
the instrument.

PureAire Monitoring Systems, Inc.
16
5.1.2 Sensor Installation
NOTE: If sensor is supplied with a shorting wire, it must be removed before
installation.
IMPORTANT: Be careful not to turn the sensor or touch the membrane on the
bottom of the sensor during installation.
1. Remove the transmitter cover. It is held in place by screws mounted in each
of its four corners.
2. Remove the sensor cover by rotating it counterclockwise (right to left).
3. Insert the sensor cable through the sensor holder and into the transmitter
housing.
4. Carefully push the top of the sensor into the sensor holder and fasten it in
place by gently turning the fastening screw. Do not overtighten!
5. Replace the sensor cover.
6. Connect the sensor cable to the sensor cable terminal block. Depending on
the gas being monitored, the sensor cable will have either three or four wires.
NOTE: The terminal block may be removed from the printed circuit board to
make these connections. Be sure to replace the terminal block securely once all
connections have been made.
Sensor Cable Type Wire Color Location
3-Wire Sensor Cable
White
Black
Shield
Terminal 2
Terminal 3
Terminal 4
4-Wire Sensor Cable
Black
White
Red
Shield
Terminal 1
Terminal 2
Terminal 3
Terminal 4
CAUTION: Do not twist the sensor. This may loosen the cap covering the
working electrode.
1 2 3 4
SENSOR CABLE
white
black
shield
2-Electrode Sensor Wiring
1 2 3 4
black
white
shield
red
SENSOR CABLE
3-Electrode Sensor Wiring
NOTE: The TX-1100FK oxygen zirconium sensor cell is supplied
permanently connected to the transmitter board.

PureAire Monitoring Systems, Inc.
17
5.2 Electrolyte Replacement (for renewable type sensor cells only)
CAUTION: PureAire recommends wearing protective gloves and safety glasses
when replacing sensor electrolyte. Be sure to adhere to your facility’s chemical
handling guidelines and procedures.
1. Remove the sensor as outlined in section 5.1.1.
2. Place your finger over the pressure compensation port and turn the sensor
upside down. Remove the box nut, membrane retainer ring, membrane,
O-ring, and silicon sheet (depending on sensor model).
Box Nut
Membrane Retainer Ring
Membrane
O-ring
Sensing Electrode
Silicon Sheet
3. Place the sensor over the beaker as shown and pour the old electrolyte into
the beaker. Some will remain in the sensor until the pressure compensation
plug is removed. Remove the milli seal covering the plug and then the plug
to release the electrolyte into the beaker.
Pressure
Compensation
Screw
Beaker for
Old Electrolyte
NOTE:
The Pressure
Compensation Screw has
a Teflon membrane fixed
to the inside of the screw.
Never remove this
membrane.

PureAire Monitoring Systems, Inc.
18
4. Hold the sensor in your hand with the sensing electrode up. Hold a piece of
paper tissue over the pressure compensation port with your thumb. Pour
10 cc’s of fresh electrolyte into the sensor and rinse. Discard into the beaker.
Sensing Electrode
Nozzled Electrolyte
Bottle
Pressure Compensation Port
Electrolyte
5. Wipe the sensing electrode and the surrounding area with a dry paper tissue.
Sensing Electrode
Paper Tissue

PureAire Monitoring Systems, Inc.
19
6. Place a new silicone sheet (if used) and O-ring on the sensor. Make sure that
the area is dry of electrolyte.
Silicon Sheet
O-ring
7. Apply a drop of electrolyte on the sensing electrode.
Enlarged View
Drop of
Electrolyte
Sensing
Electrode
8. Place a new membrane on the sensor, with the bead of electrolyte between
the electrode and the membrane.
Enlarged
View
Mmebrane
Electrolyte
Bead
Sensing
Electrode
Mmebrane
NOTE: Do not touch center of membrane with bare fingers. Oil from your
fingers may adversely affect performance.
Membrane
Membrane
This manual suits for next models
4
Table of contents
Popular Security Sensor manuals by other brands

STEINEL PROFESSIONAL
STEINEL PROFESSIONAL DALI-2 IS 3360 Information
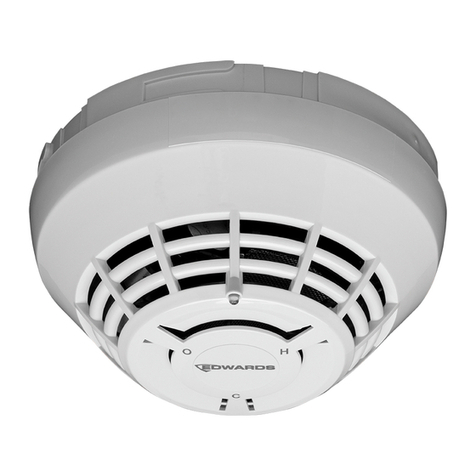
United Technologies
United Technologies Edwards SIGA-OSHD Installation sheet
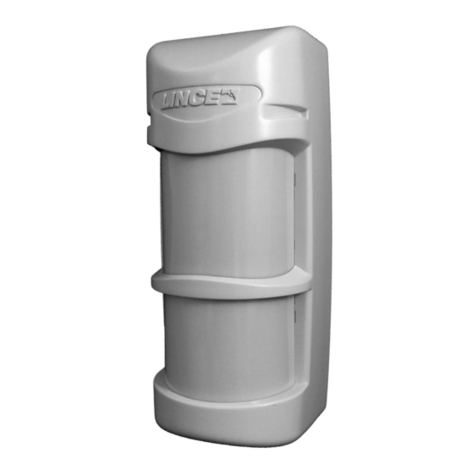
Lince
Lince BOBBY GOLD Series Installation, operation and maintenance manual
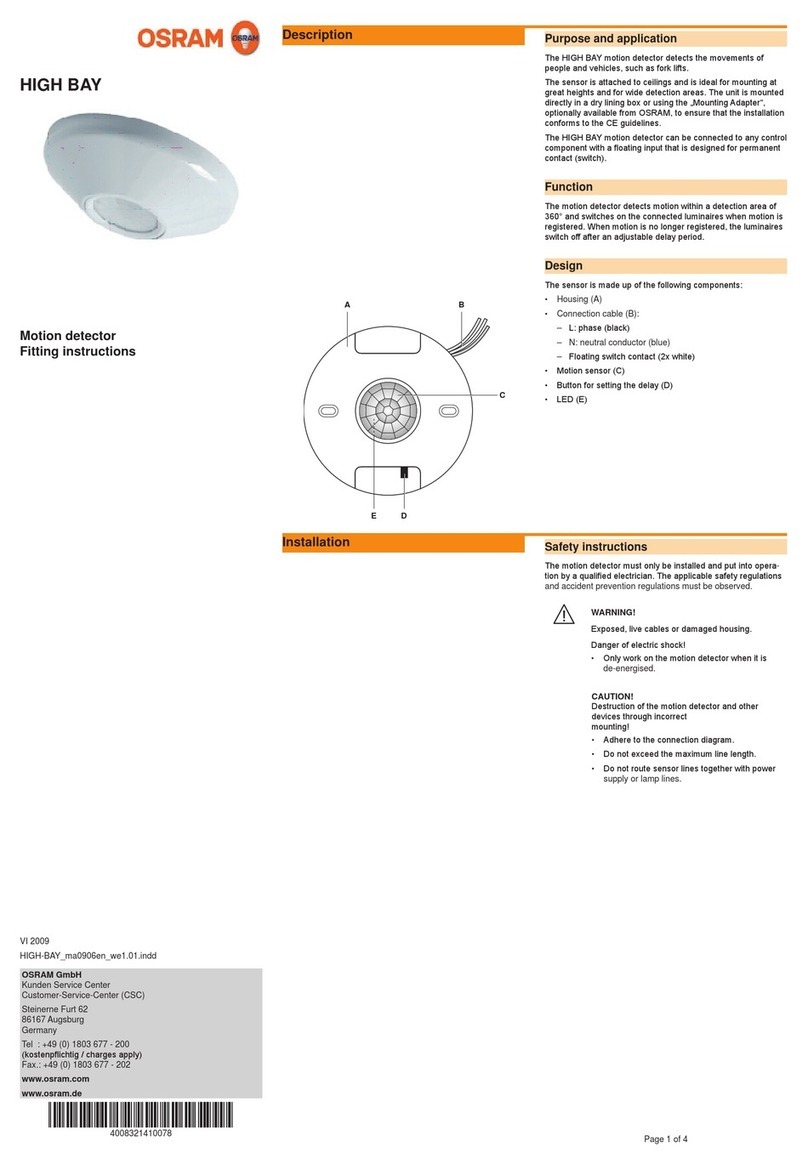
Osram
Osram HIGH BAY Fitting instructions

Bavaria
Bavaria BARM6 user manual

EMX Industries
EMX Industries VMD202 quick start guide