Pyropress Perseus User manual

Page 1 of 15
User Guide for The Perseus Switch Range
D_6, F_6, L_6, P_6, T_6 & V_6
IMPORTANT: READ CAREFULLY BEFORE USE AND KEEP FOR FUTURE REFERENCE
Symbols Used
!
CAUTION/Requirement for safe use
EX
Hazardous area installation requirement
The Perseus must be maintained, installed, repaired & decommissioned by qualified
personnel only.
Hazardous area products must be installed in accordance with IEC/EN 60079-14.
The Perseus must not be used outside of its specifications. This may adversely affect
performance, product life and may cause a hazard to people, animals and the
environment. Check the product’s identification label before installation to ensure the
correct product has been selected.
Contents
Description of The Equipment .................. 1
Storage ................................................. 1
General Dimensions & Features ................ 2
Product Identification .............................. 2
CE Marking ............................................ 2
Standards Applied .................................. 3
Hazardous Area Marking .......................... 3
Conditions for Safe Use (X Conditions) ...... 4
Pressure & Temperature Ratings .............. 4
Environmental Limitations ....................... 4
Electrical Installation ............................... 5
Set Point Adjustment .............................. 6
Differential & Second Set Point Adjustment
(Optional) .............................................. 7
Mechanical Installation ............................ 7
Maintenance ........................................ 14
Troubleshooting ................................... 14
Spares & repair .................................... 14
Materials of Construction ....................... 15
Disposal .............................................. 15
Contact Details ..................................... 15
Description of The Equipment
The Perseus is designed to be used in volatile and hazardous atmospheres to sense changes in
flow, level, pressure, or temperature using mechanical actuators and converting the physical
change into an electrical signal.
Storage
The Perseus can be stored in temperatures of -40°C to +85°C, excluding T_6 types with L*/M*
ranges that can be stored at -20°C to 85°C. If being stored in a damp/humid environment, it is
recommended to store the product without its packaging.
!
EX
!

Page 2 of 15
General Dimensions & Features
111
87
62
50
6
30
70
31
2
35
4
1
6 2
3
4
1
6
5
92
49
118
60
38
30
70
72
7
60
4
Aluminium Case - General Dimensions and Features Stainless steel Case - General Dimensions and Features
All dimensions in mm
Product Identification
Please see the identification label on the left-hand side of the switch case. Ensure that the
correct type of instrumentation is selected before installation.
TYPE
MODEL
PROCESS TEMP. RANGE
MAX WORKING PRESSURE
TAG No. RANGE
SERIAL No.
Pyropress Limited
+44(0)1752 333939
www.pyropress.com
Perseus Weatherproof Differential Pressure Switch
DF61AA/*** ******
min. to max.
max.
min. setting to max.
D - Differential Pressure Switch
F - Flow Switch
L - Mechanical Level Switch
P - Pressure Switch
T - Temperature Switch
V - Vacuum Switch
F - Without Resistors
R - With Resistors
6 - Perseus Switch Range
A - Aluminium Case
S - 316 Stainless steel Case
A - Weatherproof
B - Flameproof Gas
O - Intrinsically Safe Gas & Dust
T- Flameproof Gas + Dust
D F 6 1 _ A A / * * *
1 - Single Microswitch
2 - Dual Microswitch
3 - Adjustable Differential Microswitch
4 - Dual Set Point Microswitch
9 - High Differential Microswitch
Product Specific
(refer to website for details)
Model Code Breakdown
CE Marking
Perseus products for use in non-hazardous (weatherproof) applications carry a CE mark to
signify conformity with the Low Voltage Directive 2014/35/EU.
Perseus products for use in explosive atmospheres carry a CE mark to signify conformity with
the ATEX Directive 2014/34/EU.
Features
1
Identification Label
2
Top Cover &
C
ertification
L
abel
3
Adjustment Cover
4
External
E
arth
5
Ø5.5 mounting holes
6
M20 x 1.5
S
ide
E
lectrical
E
ntry
7
M20 x 1.5
T
op
E
lectrical
E
ntry
(option)

Page 3 of 15
All Perseus switch types fall within the Sound Engineering Practice category, as defined by
chapter 1, article 4, paragraph 3 of the Pressure Equipment Directive 2014/68/EU. For this
reason, the CE mark on the Perseus does not signify conformance with the Pressure Equipment
Directive.
Standards Applied
For Non-Explosive Atmosphere (Weatherproof) Applications:
EN 61010-1:2010
IEC 61010-1:2010
For Explosive Atmosphere Applications:
Flameproof, Ex db and Ex tb – (Zones 1 & 2 and Zones 21 & 22) (CAT 2 & CAT 3)
EN 60079-0:2018
EN 60079-1:2014
EN 60079-31:2014
IEC 60079-0:2017
IEC 60079-1:2014
IEC 60079-31:2013
Intrinsic Safety, Ex ia – (Zones 0, 1, & 2 and Zones 20, 21 & 22) (CAT 1, CAT 2 & CAT 3)
EN 60079-0:2018
EN 60079-11:2012
EN 60079-26:2015
IEC 60079-0:2017
IEC 60079-11:2011
IEC 60079-26:2014
Hazardous Area Marking
Flameproof gas, without
resistors (Ex db only)
xxxx
DO NOT OPEN WHEN
FLAMMABLE ATMOSPHERE
IS PR ESENT, EVEN WHEN
DE-ENERGIZED
WARNING
SEE INSTALLATION
INSTRUCTION DOCUMENT
USE CABLES WITH
OPERATING T EMP. >105°C
Flameproof gas, with
resistors (Ex db only)
DO NOT OPEN WHEN
FLAMMABLE ATMOSPHERE
IS PRESENT, EVEN WHEN
DE-ENERGIZED
WARNING
xxxx
SEE INSTALLATION
INSTRUCTION DOCUMENT
USE CABLES WITH
OPERATING TEMP. >105°C
Flameproof gas + dust,
(Ex db & Ex tb)
xxxx
SEE INSTALLATION
DO NOT OPEN WHEN
FLAMMABLE ATMOSPHERE
IS PRESENT, EVEN WHEN
DE-ENERGIZED
WARNING
Tamb-50°C to +75°C T85°C/-50 to +90°C T100°C
INSTRUCTION DOCUMENT
USE CABLES WITH
OPERATING TEMP. >105°C
Intrinsically safe, gas + dust
without resistors (ia)
XXXX
MAXIMUM COMBINED INPUT
SWITCH APPLICATIONS
FOR SINGLE AND DUAL
Ui:28V Ii:93mA Pi:0.65W
Intrinsically safe, gas
with resistors (ia)
MAXIMUM COMBINED INPUT
SWITCH APPLICATIONS
FOR SINGLE AND DUAL
Ui:28V Ii:93mA Pi:0.65W
XXXX
Ensure the correct protection method has been selected for the application.
EX

Page 4 of 15
Conditions for Safe Use (X Conditions)
Ex db and Ex tb
Under rated conditions, the cable temperature can reach 9K above ambient temperature.
Ensure selection of correctly rated cable for the application.
Flameproof joints not intended for repair.
Ex ia
For Ga installations – The equipment may be constructed using aluminium for the
housing and internal parts and may only be used when the ignition hazard assessment
shows there is no risk of ignition from incendive impact or abrasion sparks.
All Perseus Products
WARNING: End–users are advised to carry out assessments in accordance with the
requirements of appropriate, recognised standards. The person or persons undertaking this task
must be suitably qualified.
Pressure & Temperature Ratings
Process Temperature:
Please see the product identification label for the process temperature range, max working
pressure & range.
Ambient Temperature:
Maximum ambient temperature permissible, changes depending on the Perseus’ application.
Type
Process r
ange
A
mbient
range
T_6 (Rigid Stem
Temperature types)
200°C to 240°C range
-40°C to + 75°C
175
°C to 2
25
°C range
150°C to 200°C range -40°C to + 80°C
All other types and
ranges
<150°C -40°C to + 85°C
Upper ambient temperatures will be further restricted if products are:
Ex II 2 G Ex db IIC / Ex II D Ex tb IIIC certified
Installed in a T6/T85°C environment: +75°C
OR Ex II 1 G Ex ia IIC / Ex II 1 D Ex ia IIIC certified
Without resistors, installed in a T6 environment: +78°C
With resistors, installed in a T5 environment: +72°C
Without resistors, installed in a T135°C environment: +70°C
Upper temperature limits for ambient temperature can be further restricted. If the
temperature on the certificate is lower than the temperature range specified on the
identification label, the one on the certificate prevails.
Environmental Limitations
Perseus products are rated for both IP66 & IP67 in accordance with IEC/EN 60529.
Perseus products should not be installed at altitudes greater than 2000m.
Contact Pyropress for information regarding shock and vibration limits or SIL information.
EX
EX

Page 5 of 15
5
6
Electrical Installation
Weatherproof products
Terminals must not be accessed unless the product has been electrically isolated.
Flameproof (Ex db) and Flameproof + Dust (Ex db & Ex tb) products
Do not remove the top cover whilst a flammable atmosphere is present, even when
de-energized.
Intrinsically safe (Ex ia) products
The top cover can be removed when the switch is energized, but installation should only
be carried out when the product has been electrically isolated.
Single microswitch
options
(codes 1 & 9)
12
3
Dual microswitch
option
(code 2)
2 1
3
Adjustable differential &
dual set point options
(codes 3 & 4)
4
2
3
1
Ratings
Weatherproof & Flameproof (Ex db) &
Flameproof + Dust (Ex db & Ex tb) 250VAC 5A or 30VDC 5A
Intrinsically Safe (Ex ia) Ui:28Vdc Ii:93mA Pi:0.65W Ci:0F Li:0H
We recommend that suitably rated cable glands, adaptors, or blanking plugs with an
IP66/IP67 rating are fitted.
Flameproof (Ex db) and flameproof + dust (Ex db & Ex tb) certified products must be
fitted with appropriately rated Ex db or Ex tb certified cable glands, adaptors or
blanking plugs with an IP66/IP67 rating.
Earthing
The Perseus must be earthed to ensure safe use. Use a conductor of at least 4mm2 for
the external earth & a conductor up to 2.5mm2 for the protective conductor terminal.
Flameproof (Ex db), Flameproof + Dust (Ex db & Ex tb) and Intrinsically safe (Ex ia)
products should be earthed in accordance with 60079-14.
Electrical features
1 Slotted Screw Terminal
2
Protective
C
onductor
T
erminal
3 External Earth
4
Differential/Second Set Point Adjustment Screw
5
Top Cover
6
1.5
mm
Hex Screw
EX
!
EX
!
EX
!
!

Page 6 of 15
1
2
2
1
Over Current Protection
Perseus Weatherproof, Flameproof (Ex db) and Flameproof + Dust (Ex db & Ex tb)
switches should be fitted with a maximum of 5A over current protection with the ring
or separate breaker suitably located, easily reached and marked as the disconnecting
device for this instrument.
Wiring
Cables with an operating temperature greater than 105°C must be used.
The screw terminals can accept conductors of a cross-sectional area of up to 2.5mm2 solid or up
to 1.5mm2 flexible.
All types, excluding the Vertical Reed Level are wired as follows:
For
r
ising
s
ignal
For falling
s
ignal
Common Terminal 1 (and terminal 4) Terminal 1 (and terminal 4)
Normally Open
Terminal 2 (and terminal 5)
Terminal 3 (and terminal 6)
Normally Closed
Terminal 3 (and terminal 6)
Terminal 2 (and terminal 5)
For LF6, Reed Level Types, please see the label on the inside of the top cover.
To prevent damage to the instrument, we recommend wiring the terminals prior to
tightening cable gland and carrying out any mechanical installation whilst the mains is
disconnected.
To Connect the Terminals
1. Loosen the 1.5mm Hex Screw and unscrew the Top Cover.
2. Wire Terminals and Earthing then tighten to 0.5Nm. CAUTION: Do not over tighten.
3. Tighten any cable glands and adaptors. CAUTION: ensure wires are not pulled tight.
4. Screw the Top Cover back on ensuring the O-ring seal is still in position.
5. Re-tighten the 1.5mm Hex Screw to 1Nm.
Ensure the 1.5mm Hex Screw it re-tightened as this retains the flamepath
threads and prevents people from accessing the terminals without tools.
The information on the top cover is unique to the unit it is sold with. Do not mix the
top covers.
Set Point Adjustment
The Perseus is supplied calibrated as requested at point of sale. If a fixed set point was
supplied, no further adjustment should be required. If required, the set point can be adjusted by
following the steps below.
Adjustment Chamber (excluding T_6
Rigid Stem Temperature,
L_6 Level switches)
Adjustment Chamber (T_6 Rigid Stem
Temperature ONLY)
Adjustment
Features
1
Adjuster Screw
2
Scale (for indication only)
!
EX
!
!
EX !
!

Page 7 of 15
1. Remove the Adjustment Cover screws (use 4mm Hex Key for Aluminium Switch Case
and 3mm hex key for Stainless Steel Case) Washers, and Gaskets. CAUTION: Do not lose
any of these components as they ensure an environmental seal. Contact Pyropress for spares if required.
2. Insert a 3mm Tommy Bar (or 2.5mm Hex Key) into the hole in the Adjuster Screw and
rotate the Adjuster Screw to the desired set point using the Scale. For all ranges
excluding the Rigid Stem Temperature, the groove in the Adjuster Screw should align
with the marking on the Scale. For Rigid Stem Temperature adjustment, the centre point
of the switch is the setting point.
3. Replace the Adjustment Cover, Gasket, Washers and Screws. Tighten the Screws to
1.5Nm. WARNING: Take care not to over tighten as this will distort the Gasket.
Differential & Second Set Point Adjustment (Optional)
1
Weatherproof products
Terminals must not be accessed unless the product has been electrically isolated.
Flameproof (Ex db) and Flameproof + dust (Ex db & Ex tb) products
Do not open whilst a flammable atmosphere is present, even when de-energized.
Intrinsically safe (Ex ia) products
The Top Cover can be removed, and adjustment can take place whilst the mains is live
if the ignition hazard assessment shows there is no risk of ignition from incendive
impact or abrasion sparks.
1. Loosen the 1.5mm Hex Screw and unscrew the Top Cover.
2. Using a 7mm Nut Spinner (7mm Socket Drive suitable) rotate the Differential/Second Set
Point Adjustment Screw clockwise to increase the differential/the distance between set
points and anti-clockwise to decrease the differential/the distance between set points.
3. Screw the Top Cover back on ensuring the O-ring seal is still in position.
4. Re-tighten the 1.5mm Hex Screw to 1Nm.
Ensure the 1.5mm Hex Screw it re-tightened as this retains the flamepath
threads and prevents people from accessing the terminals without tools.
Mechanical Installation
For this part, first read the General Information section and then navigate to your product type.
General Information
In the case of pressure seal failure, all Perseus switches
vent from a detachable Blow-disc located in the rear of
the product. Should any pressure seal fail, the process
media will vent through this hole. Ensure a gap between
any wall or bulkhead of 6mm.
Adj
ustable
Differential &
Dual Set Point Features
1
Differential/Second Set Point
Adjustment Screw
EX
!
EX
!
6mm MIN
EX !

Page 8 of 15
Before undertaking any mechanical installation, ensure that all switch wiring has been
completed and left disconnected at the mains side and any holes (if) required for
mounting have been drilled.
The Perseus can be mounted in any orientation (excluding the 8” D_6, P_6 & V_6 Differential
Pressure, Ultra low Pressure & Vacuum and Level types).
If products are being fitted to a system where fluid flow can become unstable and cause
pressure to pulsate or surge rapidly, it is imperative that a means of protecting the sensing
element be provided; by adding a pressure snubber or over-range protector for example.
If products are being fitted to a system where the process temperature could exceed the limits
stated for that configuration (see the identification label), they must be remote mounted to
allow for enough heat dissipation.
Products should always be mounted such that any free movement is minimal. To avoid
damage from vibration or accidental impact, products mounted via the process connection
should be properly supported.
We recommend that PTFE tape is used on tapered process connections (to improve the seal
and prevent cold welding) and appropriately sized bonded seals on parallel process
connections.
All compression fittings must be sufficiently tightened to prevent leakage.
The Perseus can be supplied with accessories such as chemical seals, gauges and manifolds.
Please refer to any separate documentation supplied when installing accessories not covered
by this user guide.
For “case mounted” Perseus, feed 2 X M5 screws (or equivalent) with washers though the
switch case and tighten.
We recommend that anti-vibration washers are used when mounting the product.
For products fitted with a 2” (52mm) pipe bracket, place the
‘U’ Bolt around the pipe, slide the saddle onto
the U-Bolt, feed the switches mounting bracket onto the ‘U’ Bolt
and then tighten the 2 M8 full nut.
8” - D_6, P_6 & V6, (Differential Pressure, Pressure & Vacuum)
This version must be mounted as shown.
If mounted in any other orientation, the
switch may not operate within its
specification.
For P_6 versions the Low-Pressure Entry
is fitted with a vented plug.
For V_6 versions the High-Pressure Entry
is fitted with a vented plug.
To Mount: Feed 4 x M8 screws (or
equivalent) with washers through the
bracket.
8” D_6, P_6 & V_6 Differential Pressure,
Ultra Low Pressure & Vacuum
1
High
-
P
ressure
E
ntry
2 Low-Pressure Entry
3
Bracket
!
Mass
With Aluminium switch case 11.5 kg
With Stainless Steel switch case 12 kg
MOUNT IN THIS ORIENTATION
1
2
3
dimensions in mm
8" D_6, P_6 & V_6 (Aluminium or Stainless steel case)
`U' Bolt
Mounting Bracket
M8 Full Nut
Saddle

Page 9 of 15
1” & 3” - D_6, P_6 and V_6 (Differential Pressure, Pressure & Vacuum)
1
2
3
3
2
4
1
4
dimensions in mm
Mass
With Stainless Steel switch case 4.5 kg
Aluminium Case - 3" D_6, P_6 & V_6 Stainless Steel Case - 3" D_6, P_6 & V_6
Mass
With Aluminium switch case 4 kg
For P_6 versions the Low-Pressure Entry is fitted
with a vented plug.
For V_6 versions the High-Pressure Entry is fitted
with a vented plug.
To mount 3”: Feed 2 x M6 Screws (or equivalent)
with washers through the Bracket.
To mount 1”: Case mounted.
3” & 4” - P_6 (Low Pressure)
To mount: Feed 2 x M6 (or equivalent) Screws with washers through the Bracket.
1” & 3” D_6, P_6 & V_6
Differential Pressure & Vacuum
1
High
-
Pressure Entry
2
Low
-
Pressure Entry
3 Bracket
4 ½” Process Adaptor (option)
3” & 4” P_6 Low
Pressure
1 Bracket
2
Process Entry
dimensions in mm
Mass
With Aluminium switch case 2.5 kg
With Stainless Steel switch case 3 kg
1" D_6, P_6 & V_6 (Aluminium or Stainless steel case)
1
2
4
3" P_6 4" P_6
dimensions in mm
Mass
With Stainless Steel switch case 5 kg
Aluminium Case - 3" P_6 Stainless Steel Case - 4" P_6
2
1
2
1
Mass
With Aluminium switch case 4.5 kg

Page 10 of 15
Diaphragm - P_6 (Medium Pressure)
To mount: Case mounted or
swivel connection.
Swivel Connection: Loosen
Coupling Nut from the Stem
Head Tighten the Stem
Head into your assembly
Holding the Switch Case in the
desired position, tighten the
coupling nut.
Flush Diaphragm – P_6 (Medium Pressure)
Pyropress supply many types of flanges
based on system requirements. Flanges
should be installed in accordance with
their relevant standards (ANSI/ASME or
ISO for example).
Take note of any marking etched or
stamped into the flange to ensure safe
use.
Check flange surfaces are clean to
prevent contamination.
Ensure any gasket material is suitable
for the process medium.
If liquid gasket is being applied, ensure
the manufacturers cure time is adhered
to prevent leakage.
Metal Diaphragm & Piston - P_6 (High Pressure)
To mount: Case mounted or swivel
connection.
Swivel Connection: Loosen coupling
nut from the Stem Head Tighten
the Stem Head into your assembly
Holding the Switch Case in the
desired position, tighten the
Coupling Nut.
Diaphragm P_6 Medium
Pressure
1
Female
Process Entry
2 Stem head
3
Coupling Nut
4
Internal Nipple
Metal Diaphragm & Piston
P_6 High Pressure
1
¼” Female Process Entry
2
½” Female Process Entry
3
Stem Head
4
Coupling Nut
5
Internal Nipple
6
Sealing Band
1
2
3
4
dimensions in mm
Mass
With Aluminium switch case 2 kg
With Stainless Steel switch case 2.5 kg
Diaphragm - P_6 (Medium Pressure with Aluminium or Stainless steel case)
dimensions in mm
Mass
Mass depends on the required flange specification
Flush Diaphragm - P_6 (Medium Pressure with Aluminium or Stainless steel case)
dimensions in mm
Mass
With Aluminium switch case 2 kg
With Stainless Steel switch case 2.5 kg
Metal Diaphragm - P_6 (High Pressure with Aluminium or Stainless steel case)
1
2
3
4
5
6

Page 11 of 15
The Sealing Band allows
process media to vent if a
pressure seal fails.
Temperature – T_6 Rigid Stem
To Mount: Loosen coupling
nut from the Stem
Head/Thermowell Tighten
the Stem head/Thermowell
into your assembly Holding
the switch case in the desired
position, tighten the Coupling
Nut.
For variations installed with a flange please follow this part and refer to the “Flush Diaphragm”
mechanical installation section.
For Sliding Gland types: Torque coupling nut to 20Nm. Do not over tighten as this will
damage the olive/temperature probe.
Temperature – T_6 Capillary
To mount: Case mounted.
Process Entry Connection:
Loosen Coupling Nut from
the Stem Head/Thermowell
Tighten the Stem
Head/Thermowell into your
assembly Holding the
Switch Case in the desired
position, tighten the
Coupling Nut.
Temperature T_6 (Rigid
Stem)
1 Stem Head/
Thermowell
2
Coupling Nut
3
Nipple
4
Olive
5
Temperature Probe
Temperature T_6 (Capillary)
1
Stem Head
2
Coupling
N
ut
3
Capillary
4
Bulb
5
Thermowell
!
!
dimensions in mm
Mass
With Aluminium switch case 2.5 kg
With Stainless Steel switch case 3 kg
Piston - P_6 (High Pressure with Aluminium or Stainless steel case)
1
2
3
4
5
6
With Thermowell
Without Thermowell
Sliding Gland
dimensions in mm
Mass
Mass Varies based on `U' Dimension
Temperature - T_6 (Rigid Stem with Aluminium or Stainless steel case)
1
2
3
4
Thread 'L'
1
2" BSP.P.
3
4" BSP.P.
1" BSP.P.
1
2" NPT.
3
4" NPT
1" NPT
16
20
25
5
Temperature - T_6 (Capillary with Aluminium or Stainless steel case)
dimensions in mm
Mass
Mass Varies based on Bulb & Capillary Length
12
3
4
Thermowell
Thread 'L'
1
2" BSP.P.
3
4" BSP.P.
1" BSP.P.
1
2" NPT.
3
4" NPT
1" NPT
16
20
25
5

Page 12 of 15
Mechanical level – L_6_1 Horizontal
Tank wall hole size: Ø27mm
Mount in the orientation shown
depending on the required set
point.
To mount: remove the Locknut but
keep the Bonded Seal in place
feed the assembly though the Tank
Wall Holding the Switch Case in
the desired position, tighten the
Locknut screw the Float onto the
assembly, holding the float with
you hand, tighten the nut.
For variations installed with a flange please follow this section and refer to the “Flush Diaphragm”
mechanical installation section.
Mechanical Level – L_6_2 Vertical
Tank wall hole size: Ø27mm
Mount in the orientation shown.
To mount: remove the Locknut but keep the
Bonded Seal in place Feed the assembly
though the Tank Wall Holding the Switch
Case into the desired position, tighten the
Locknut Take the Float assembly, feed the
Locking Collar over the shaft and tighten the
Set Screw in the Locking Collar.
For variations installed with a flange please
follow this section and refer to the “Flush
Diaphragm” mechanical installation section.
Mechanical Level L_6_1
(Horizontal)
1
Bonded
S
eal
2
Locknut
3
Nut
4
Float
5
Tank
W
all
Mechanical Level L_6_2
(Vertical)
1
Bonded Seal
2
Locknut
3
Locking Collar
4
Float
1
2
3
4
5
Falling Level
Rising Level
Mechanical Level - L_6_1 (Horizontal with Aluminium or Stainless steel case
dimensions in mm
Mass
With Aluminium switch case 3.5 kg
With Stainless steel switch case 4 kg
Mechanical Level - L_6_2 (Vertical with Stainless steel or
Aluminium case
dimensions in mm
Mass
With Aluminium switch case ˜ 5 kg
With Stainless steel switch case ˜ 5.5 kg
1
2
4
3

Page 13 of 15
Reed Level – L_6 Vertical
To mount: Screw the whole assembly into
the tank by the Stem Head and lock tight
For BSP.P., ensure supplied Bonded Seal is
in place slightly loosen the Coupling Nut
and rotate the Switch Case into the desired
position retighten the Coupling Nut.
DO NOT ROTATE SWITCH CASE
MORE THAN 270° FROM THE STEM
HEADS LOCKED POSITION. DOING
SO COULD DAMAGE THE INTERNAL
WIRING.
For variations installed with a flange please
follow this section and refer to the “Flush
Diaphragm” mechanical installation section.
Flow – F_6 All types
Pyropress supply many
types of flanges based on
system requirements.
Flanges should be installed
in accordance with their
relevant standards
(ANSI/ASME or ISO for
example).
Check flange surfaces are
clean to prevent
contamination.
Ensure any gasket material
is suitable for the process
medium.
If liquid gasket is being applied, ensure the manufacturers cure time is adhered to prevent
leakage.
Reed Level R_6 (Vertical)
1
Coupling Nut
2
Stem Head
3
Internal Wiring
4
Internal Nipple
5
Bonded seal (BSP.P. only)
Flow
-
F_6
1
Inlet Plate
2
Outlet Plate
3
Indicator
(option)
!
Reed Level - R_6 (Vertical with Aluminium or Stainless steel case)
dimensions in mm
1
2
3
4
5
Mass
With Aluminium switch case ˜ 3 kg
With Stainless steel switch case ˜ 3.5 kg
dimensions in mm
Mass
Mass varies based on the required flange specification
Flow - F_6 (with Aluminium or Stainless steel case)
1
2
Non-Metallic VersionMetallic Version
3

Page 14 of 15
Maintenance
Before undertaking any maintenance, ensure that the Perseus is de-energised and
isolated from pressurised media. Check that any surfaces are cool to the touch.
Flameproof (Ex db) and Flameproof + Dust products (Ex db & Ex tb) must not have
their top covers removed when an explosive atmosphere is present even if de-
energised.
Maintenance procedure
F
requency
*
Check
process and electrical connection remain tight
Every 6 months
Cycle product if not in use
Check ePTFE vents for damage
(low pressure only)
Replace seals and diaphragms Every 3-5 years
Replace
m
icroswitch assemblies
Every
5
-
10 years
*depending on usage
Troubleshooting
Problem
Likely cause
Solution
Leak of media
Diaphragm/O
-
ring failure.
Replace diaphragm/O
-
ring.
Shift in set
point
Excessive shock or impact.
Diaphragm or O-ring at end of life.
Wear of adjustable differential or Dual
set point
mechanism.
Re-adjust the set point.
Replace diaphragm/O-ring.
Replace the adjustable
differential mechanism.
Slow response
Media too viscous.
Blockage in system.
Valve not fully opened within system.
Use a chemical seal.
Ensure lines are free of debris.
Ensure valves are fully opened.
No signal or
intermittent
signal
Microswitch failure.
Diaphragm/O-ring failure.
Loose electrical connection.
Replace microswitch.
Replace diaphragm/O-ring.
De-energize the system and
tighten electrical connection.
Note: only replace with Pyropress original parts
Spares & Repair
Diaphragm, pressure seal and environmental seal kits are available for the following switch
types.
Vacuum (V_6)
Ultra-Low Pressure (P_6)
Low Pressure (P_6)
Medium Pressure (P_6)
High Pressure Piston (P_6)
Differential Pressure (D_6)
Fully assembled and pressure tested High-Pressure Piston (P_6) and High-Pressure Metal
Diaphragm (P_6) assemblies are available for onsite repair.
Standard and High differential Single/dual microswitch assemblies are also available.
All switches should be thoroughly tested before re-introducing them into service. It is likely the
set points will vary slightly from their original setting and will require recalibration.
All switch types can be returned to Pyropress for Repair and overhaul.
Before returning Switches to Pyropress, ensure that the process medium has been fully
decontaminated.
!
EX
!

Page 15 of 15
Materials of Construction
External parts
316 stainless steel
Aluminium (Aluminium Switch Case only)
304 stainless steel (Aluminium Switch
Case only)
Glass reinforced epoxy resin (Rigid Stem
only)
Phosphor Bronze (Metallic Flow only)
Brass (Metallic Flow only)
Fasteners
A2 & A4 stainless steels
Wetted parts
316 Stainless steel (standard)
Monel® 400 (if specified)
Inconel (if specified)
Hastelloy® C276 (if specified)
Polypropylene (if specified)
Nylon (8” types & if specified)
303 & 304 stainless steels (Rigid Stem
without thermowell only)
Aluminium (Rigid Stem with Sliding Gland
only)
PH15-7Mo (1” types only)
Gunmetal (Metallic Flow only)
Brass (Metallic Flow only)
Polyvinyl chloride (Metallic Flow only)
Cotton fabric reinforced epoxy resin
(Non-Metallic Flow only)
Acetal (Non-Metallic Flow only)
Diaphragms & pressure seals (upon request)
Viton®
Nitrile
PTFE
EPDM
Neoprene
Kalrez® (Temperature types)
Silicone (Temperature types)
Neoprene cork (Metallic Flow only)
Disposal
Ensure components that have come into contact with harmful substances are dealt with
correctly.
Temperature stems contains mineral oil – do not ingest and avoid eye or skin contact.
Flush eyes with copious amounts of water wash skin with soap and water. If vomiting
occurs due to ingestion or persistent irritation occurs, seek medical attention.
Mineral oil should be disposed of at an authorised collection point. Do not discharge into drains,
soil, or water.
Electrical components should be disposed in accordance with local regulations.
Most of the components are made from stainless steel or aluminium. Once the electrical
components have been removed the switch can be recycled.
Contact Details
Pyropress Limited
Bell Close
Plymouth
PL7 4JH
Tel: +44 (0)1752 333933
E-mail: sales@pyropress.com
Website: www.pyropress.com
User Guide revision: 14 Dated: 01/06/2020
!
Table of contents
Popular Switch manuals by other brands
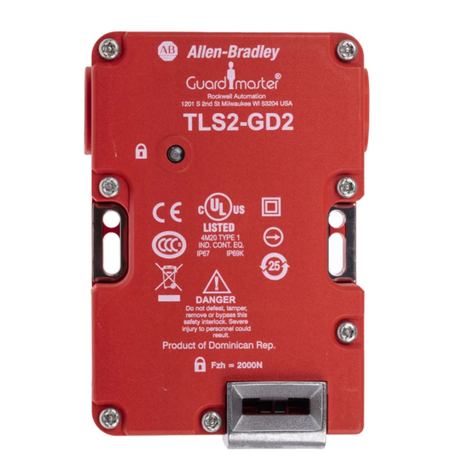
Allen-Bradley
Allen-Bradley TLS-GD2 installation instructions
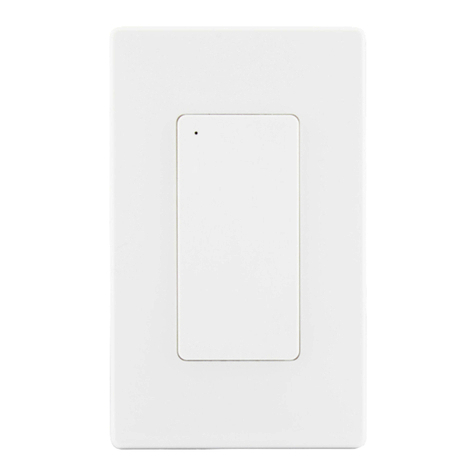
Satco
Satco STARFISH S11267 installation guide
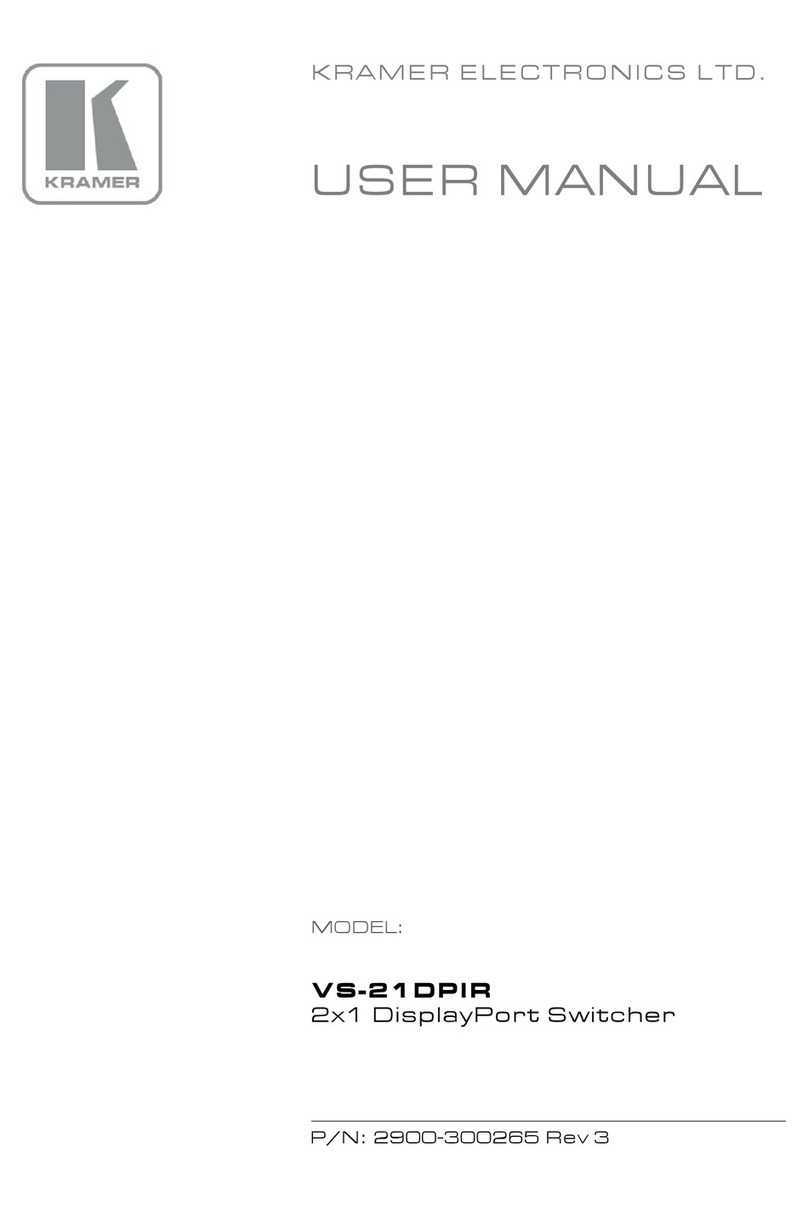
Kramer
Kramer VS-21DPIR user manual
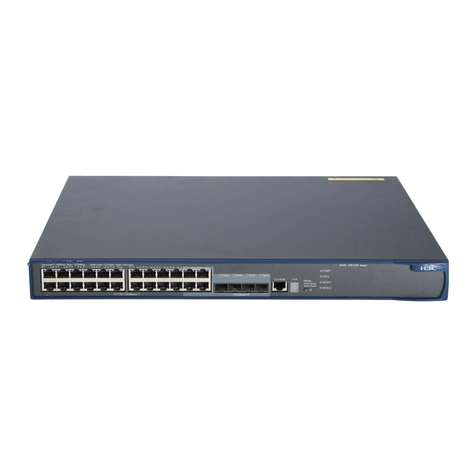
HP
HP 5120-24G EI TAA Configuration guide
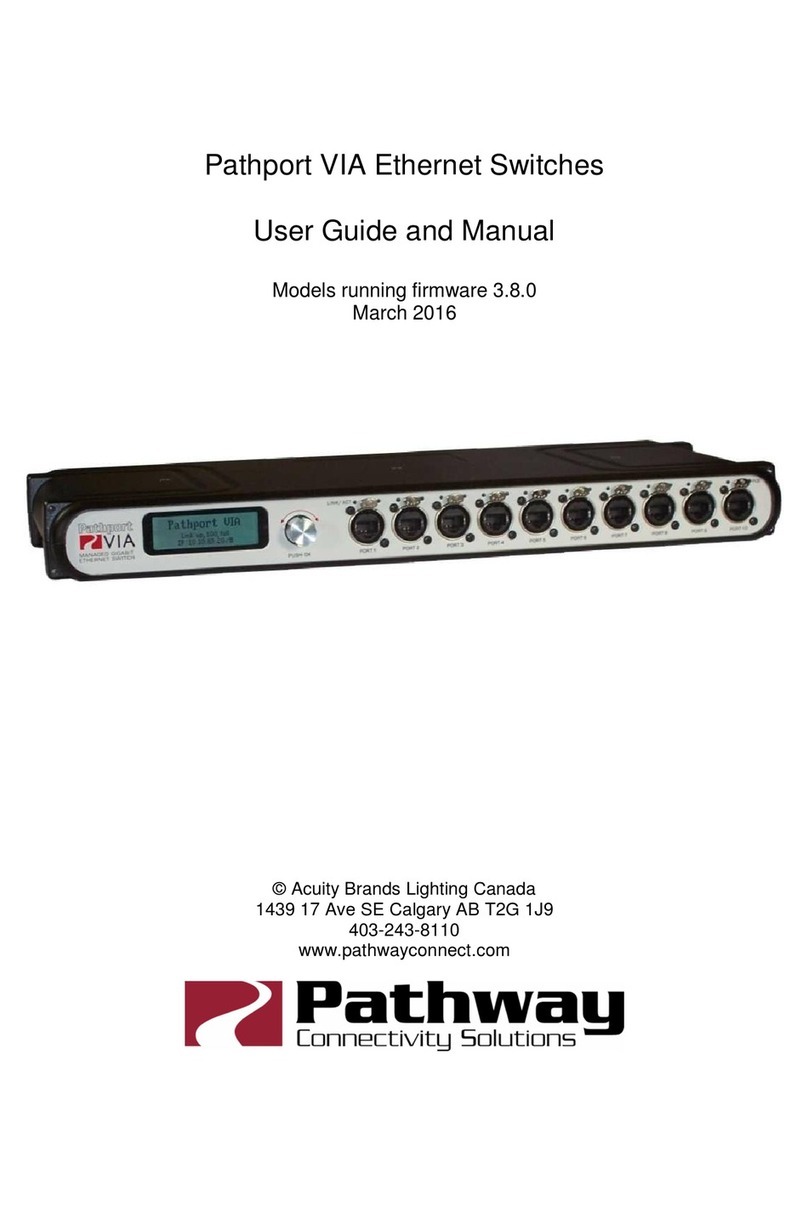
Pathway connectivity solutions
Pathway connectivity solutions Pathport VIA 6730 User guide and manual
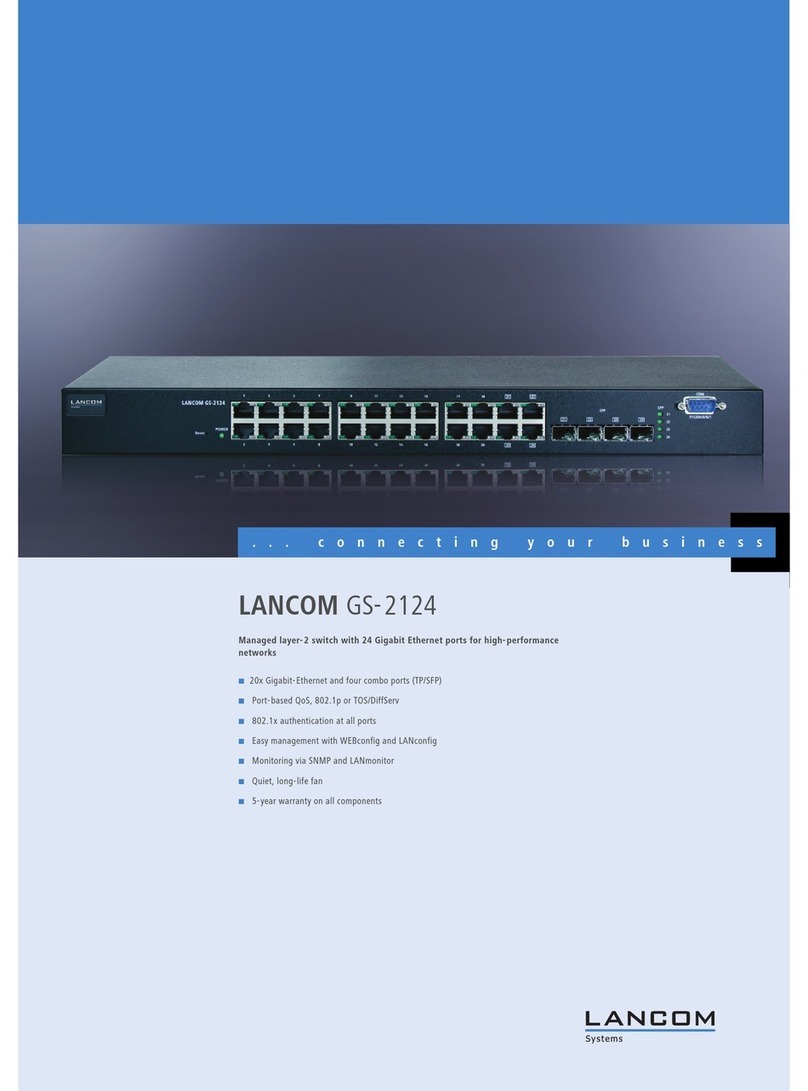
Lancom
Lancom GS-2124 user manual