QTS Level-Trac LT-310 User manual

Level-Trac Model LT-310 Control Unit
INSTALLATION, OPERATION AND INSTRUCTION MANUAL
Note: This document should be reviewed in its entirety prior to installation of equipment.
1.0 Operating Principle 2
2.0 System Configuration 2
2.1 Channel Assignment 3
2.2 Alarm/Trip and Fault Detection Relays 3
2.2.1 Alarm Relays 3
2.2.2TripRelays 3
2.3Sensitivity 3
2.4TestSwitches 4
2.5 System Fault 4
2.5 Process Fault 4
3.0 Installation & Cabling 4
3.1Enclosure
3.2 Main Power Supply 4
3.3 Wiring Control Unit to Probes 5
3.4WiringAlarm/TripRelays 6
3.5 Panel Mount Remote Indicator 7
4.0 Commissioning 7
5.0 System Specification 8
6.0 Field Programming 9
6.1.DiscriminatorPCB 9
6.2. Power Supply/Relay PCB 10
Figures
1.1 System Overview 2
3.3.1 Wiring Control Unit to Probes 5
3.3.1 Wiring Alarm/Trip Relays 6
Appendices
Appendix A: Instructions for Mounting Stahlin Enclosures 11
Appendix B: 16 Conductor High Temp Cable Specification 12
330-35
8/5/11
13960 South Wayside Drive • Houston, TX 77048 • USA
www.QTSLevel.com
QTS
Quest-Tec Solutions
The New Standard of Level

1.0 Operating Principle
The Level-Trac LT-310 is a remote level indication system, as described in ASME Section I, PG-60. The system
may also be used as an alarm or trip device.
Discrimination between water and steam is based on the significant difference in resistivity between the two
states over the saturation range. The sensing element is a probe with an insulated tip inserted in a probe mani-
fold (Figure 1.1.) If a voltage is applied to the probe tip, conduction occurs between the tip and the inside wall of
the column, resulting in an indication of water. Probe and manifold dimensions are selected to provide a resis-
tance typically less than 100 KΩwhen the probe is immersed in water, as compared to a resistance greater than
5 MΩwhen in contact with steam. An electronic discrimination circuit is arranged to sense whether the Probe
resistance is less than 100 KΩrepresenting water or greater than 5 KΩrepresenting steam.
With probes spaced vertically in a manifold attached to the boiler (Figure 1.1) and with each probe connected to
its own sensing and water/steam indication circuit, a vertical display of Green/Red indicators provides a simula-
tion of water level in the steam drum. Spacing between probes is per customer requirements to cover the visible
range and alarm or trip points.
Typical Probe Manifold
Cross Section
Figure 1.1
2
2.0 System Configuration
Probes are installed in the probe manifold. A length of high temperature wire connects the probes and the mani-
fold to the control unit. The probe manifold itself serves as a common conductor. The presence of water will
complete a circuit between the manifold and the probe tip. The LT-310 is designed with the flexibility to control
six probes from up to six places with complete discrete settings.
Two printed circuit boards contained in a NEMA 4X (IP65) wall mounted enclosure provide up to 6 discrete
water/steam discrimination circuits, LED display, relay alarm/trip outputs, fault detection and terminals for the
connection of a remote display Unit.
To avoid galvanic interaction with the probe and variations in sensing voltage due to changing electrolytic poten-
tials, an alternating voltage source is applied to the probe and the sensing circuit responds only to an alternating
waveform. Two low frequency oscillators are provided for the source voltage; one drives the odd numbered
channels and the other the even numbered channels. The voltage applied to the probe is less than 6 volts, cur-
rent limited to 50 µA, and presents no risk to personnel.
The LT-310 is designed for use with two discrete power sources. In the event of failure of one power source, the
remaining power source will maintain all system functions.
Control Unit
4 probes from two sources

2.1 Channel Assignment
Alarm/Trip State: Each channel is individually assigned an alarm/trip state, wet or dry.
Cable Monitoring: Each probe is individually set as normally wet or dry. Normally wet probes require one
conductor and normally dry probes require two.
2.1 Local Indication
Each channel output drives a green LED for water or a red LED for steam, along with yellow flashing LEDs for
system and process fault, to a door mounted display.
2.2 Alarm/Trip and Fault Detection Relays
Seven 8A DPDT relays are supplied to provide contacts for alarms, trips or system fault annunciation.
RL1 through RL6 are independently selected to operate in energized (failsafe) or de-energized normal state.
When operated in the energized state, trip will occur in the event of power loss to the system.
RL1through RL6 are independently set to delay 1 second, 5 seconds, 10 seconds or 15 seconds.
RL7 System Fault, is set to a normally energized state with a delay of 15 seconds; these functions are not ad-
justable.
2.2.1 Alarm/Trip Modes
RL1through RL6 can be set to operate on a single channel state or in channel pairs. The following table shows
the options and pairing.
See 7.1 for location of the solder jumps to invoke these options. Voting logic is effected by making all of the
channel pairings for the given relay.
3
Relay Alarm/Trip
Single Channel Channel Pairings Voting Logic
2 out of 3 Channels
RL1 Channel 1 Channels 1 & 2
Channels 1 & 3
Channels 2 & 3
Poll Channels
1, 2 & 3
RL2 Channel 2 Channels 1 & 2
Channels 2 & 3
Channels 1 & 3
Poll Channels
1, 2 & 3
RL3 Channel 3 Channels 2 & 3
Channels 3 & 4
Channels 2 & 4
Poll Channels
2, 3 & 4
RL4 Channel 4 Channels 3 & 4
Channels 4 & 5
Channels 3 & 5
Poll Channels
3, 4 & 5
RL5 Channel 5 Channels 4 & 5
Channels 5 & 6
Channels 4 & 6
Poll Channels
4, 5 & 6
RL6 Channel 6 Poll Channels
4, 5 & 6
Channels 5 & 6
Channels 4 & 6
Channels 4 & 5

4
2.3 Sensitivity
Each probe channel of the LT-310 can be set to one of three sensitivity ranges:
>4 mS/cm²
>2 mS/cm²
>1 mS/cm²
These values are effectively halved by using a shrouded probe. This increases the surface area of the system
common and places the common much closer to the probe sensing element. Sensitivity is rarely an issue, and it
is suggested that the mid-range setting be used initially to evaluate system performance in the actual applica-
tion.
2.4 Test Switches
The LT-310 is supplied with two test switches, that simulate an all Wet or all Dry state. There is an On/Of slide
switch that activates the Red/Green test switches and prevents the corresponding relays from going into alarm
state during a simulation. When the slide switch is in the “On” position, System Fault will be indicated as a re-
minder that the LT-310 is in the simulation mode.
2.5 System Fault
System Fault is indicated by a flashing yellow LED labeled “SF” on the indicator and the activation of RL7.
There are three triggers for System Fault:
1. A failed power supply. If one of the switching power supplies fails, the remaining switching power supply will
power the unit until the fault is corrected.
2. The On/Off slide switch that enables the Red/Green test switches is in the “On” position.
3. When the invoked via solder jumps on the discriminator PCB: out of sequence logic (i.e. Water over Steam).
This is only valid where the probes are installed in a vertical progression respective of water level.
A failed probe insulator will typically cause the probe to be grounded, regardless of whether it is normally Wet or
Dry. Hence, a dry probe with a failed insulator will indicate as Wet. If this occurs with a probe that has a func-
tioning Dry probe below it, the out of sequence logic will declare a System Fault.
Probe cable monitoring is achieved by verifying continuity between two wires to probes that are expected to be
normally Dry. A break in continuity between these two wires will simulate a Wet probe, and cause a System
Fault. For the single wire connection to the normally Wet probes, an open-circuit connection will indicate Dry,
activating the out of sequence Fault Detection circuit.
2.6 Process Fault
Process Fault is indicated by a flashing yellow LED labeled “PF” on the indicator, and is invoked by any channel
that is not in its normal state, wet or dry.
3.0 Installation and Cabling
3.1 Enclosure
The LT-310 Electronic Unit enclosure is usually located adjacent to the probe manifold. The LT-310 enclosure
should be located to provide clear routing of cables, minimum risk of damage from surrounding plant or activi-
ties and adequate visibility of the display. The standard enclosure is a Stahlin Diamond Shield, Model
DS100806HPL, supplied with mounting foot kit. The instructions for mounting this enclosure are provided as
Appendix A of this manual.
3.2 Main Power Supply
Line, Neutral and Earth Ground are connected directly to the switching power supplies located in the base of the
enclosure. The power requirements are: 100 to 240 VAC ± 10% @ 15VA, 48 - 63 Hz. If two power sources are
not available, install a wire jump to connect the switching power supplies.

5
Figure 3.3.1
3.3 Wiring Control Unit-to-Probes
It is recommended that a continuous length of high temperature cable be used to cover the span from the probes
to the LT-310 control unit. Quest-Tec Solutions has a custom fabricated cable, available as an option, in 8, 12,
16 and 25 conductor versions. (The specification for 16 conductor cable is attached as Appendix B to this man-
ual.) 20 AWG, nickel plated copper conductors should be used where elevated temperatures are expected. A
maximum run of no more than 100 feet is recommended. Two conductors are required for each normally Dry
probe, one conductor for each normally Wet probe, and two conductors for system Common.
Figure 3.3.1 shows the terminals provided for wiring the probes. Four terminals are supplied for each probe.
Terminals 1 and 2 are for the probes, terminals 3 and 4 are for the Common Ground. To the right of each termi-
nal block are two sets of solder pad jumps. The “A” jumps tie the two probe wires together, and should be
jumped for all probes that are expected to be wet in the normal state. When “A” is jumped, a single wire can be
used for the probe, either terminal 1 or 2.

The Common Ground terminals (3 and 4) are common across the entire system, meaning that the common con-
nection for any probe will work for any probe. Each probe holding device should have at least one common
ground connection at minimum. The “B” jump invokes a continuity check of the probe wire, if required. (Units
from the factory will normally have this jump made.)
For unused channels, making the “A” solder jump will cause the display to indicate a Dry state.
3.4 Wiring Alarm/Trip Relays
Figure 3.4 shows the connection point for relays and remote indicator. Each terminal block is supplied with a
Phoenix Series MSTB plug.
There is an LED located at each relay to indicate the current status of the relay. When illuminated, the corre-
sponding relay is energized. The relays are rated 8A at 250 VAC. Note: If the continuous load is anticipated to
be greater than 5A at 250 VAC, the board traces must be replaced with wire. This is a factory modification.
6
Figure 3.4.1

3.5 Panel Mount Remote Level Indicator
The Model LT-310 Control Unit can power up to two remotely mounted displays. The Model LTI-310 is de-
signed to be mounted on a panel, with a cut-out size of 4.2” H X 2-5/8” W (107 mm H x 67 mm W). The
quantity of conductors required is calculated by taking the number of channels used and adding 6. See Figure
3.4 for the location of terminal blocks TB8 and TB9. Terminal functions of the LT-310 Control Unit are as fol-
lows:
1 thru 6: Channel Drivers
7: Process Fault (Yellow) Driver
8: System Fault (Yellow LED) Driver
9: Ground
10: +12 VDC
11: Ground
12: +12 VDC
These correspond directly with the numbered terminals on the LTI-310. The remote display will operate with a
single Ground and +12 VDC, the second pair is redundant.
4.0 Commissioning
4.1 Prior to initially powering up, verify that the ribbon cable connecting the two PCBs is oriented correctly and
fully seated. The red conductor must be towards the “1” marked on the PCB.
4.2 Before installing the wired plugs for the probes, remote indicators, 4-20 mA output and relays, power up the
unit, slide the test enabler switch to the “ON” position, depress and hold the green test switch and check that
all green LEDs are illuminated. Release the green test switch, then depress and hold the red test switch and
check that all red LEDs are illuminated. Slide the test enabler switch to the “OFF” position
4.3 Turn off the power, and install the wired probe plugs. Power up the unit, and observe. If the column is
empty all probe channels should have the red LEDs illuminated. Short each probe in turn by touching a wire
between the knurled nuts and probe body, checking that the corresponding green LED becomes illuminated.
4.4 Turn off the power and install the wired remote display plugs, if used. To prevent permanent damage to
the discriminator PCB, confirm that the wiring to the indicator is correct before powering up. Power up the unit
and check correct illumination of LED's by operation of the green and red test buttons.
4.5 Verify that the RL1 thru RL6 relays are receiving power as intended by observing the LED associated with
each relay. When an LED is illuminated the associated relay has power and should be energized. If the “E”
solder jump is made the relay LED will be illuminated when in normal state and will turn off when in the alarm
or trip state. This is reversed when the “D” solder jump is made. (The relay LED Is powered by the current
that activated the relay. It will verify that the relay has power, but does not verify that the relay has actually
closed. Continuity must be checked at the terminals to verify that the relay is performing properly.)
When configuring the wiring for relays, note that the PCB labels “NC” and “NO” are based on the relays being
in a de-energized (solder jump “D” mode).
5.0 Routine Maintenance
The LT-310 control unit requires no routine maintenance. However, it is recommended to periodically clean
the external probe insulators with a small brush to keep free of accumulated dust, and to remove, clean and
inspect the probes after one year’s service.
7

5.0 LT-310 Control Unit Specifications
Enclosure:
Wall mounted glass-fiber reinforced polyester, IP65/NEMA4X protection for location in harsh environments.
Dimensions: 11.42” H X 9.79” W X 6.56” D (290 mm H X 249 mm W X 167 mm D)
Mounting Legs: (4) 0.50” X 0.31” (13 mm X 8 mm) Slots on 12.19” H X 6” W Centers (310 mm H X 152 mm W)
Inputs:
Discrimination between water and steam for up to 6 channels numbered in ascending order.
Sensitivity: Discrimination threshold may be selected for a minimum conductivity of 1 mS/cm², 2 mS/cm² or 4
mS/cm². (Use of a shrouded probe insert effectively reduces these values by half.)
Probe Normal State: This is set by solder jumps, making a jump for all probes anticipated to be in the wet state
as normal. Probes that are normally wet require a single wire, probes that are normally dry require two wires.
Display:
Two vertical columns having 0.4” (10 mm) square LED’s on the front of the enclosure. One row of Green LED's
represents water and another row of Red LED’s represents steam. A Yellow flashing LEDs signal a
System or Process Fault Condition.
Supply Requirements:
100 to 240 VAC ± 10%, 48 - 63 Hz
Utility Consumption:
20 Watts
Temperature Rating:
Operating: -13º F (-25º C) to 158º F (70º C), Storage: -58º F (-50º C) to 212º F (100º C)
Relay Outputs:
Alarms/Trips: RL1 through RL6 can be set to activate on the input of one probe channel, or any of three par-
ings. Enabling all three parings results in a voting logic circuit that polls three probes, activating in a 2 of 3 sce-
nario.
Fault Alarm: One relay (RL7) is dedicated to activate when a Fault is indicated.
Alarm and Trip Relays may be set to a direct (de-energized) or inverse (energized) normal state The Fault relay
is set to an inverse (energized) normal state.
Relay Ratings:
DPDT, Max. Current: 8 Amps @ 250VAC
Remote Display:
Twelve terminals are provided for direct connection to a Remote Display Unit. The Remote Display Unit option
LTI-310 duplicates the display on the front of the main unit and is intended for control room location.
Panel Mounted, 7.75” H X 3” W (197 mm H x 76 mm W), Panel cut-out: 4.2” H X 2.625” W (107 mm H x 67
mm W)
8

6
6 Field Programming
6.1 Discriminator PCB
1) Time Delay (6 Places): No Jump = 15 seconds (See Part 2.2)
2) Alarm/Trip Relays (6 Places): Assigns relay activation conditions. (See Part 2.2.1)
3) Alarm/Trip State (6 Places): Assigns alarm state, wet or dry. (Make jump if Alarm state is Dry. See Part 2.1)
4) Sensitivity (6 Places): No Jump >4
µ
S/cm², Sa to Center is >2
µ
S/cm², Sb to Center is >1
µ
S/cm² (See Part 2.3)
5) Sequence Check: Invokes sequence logic.
6) LED Brightness (2 Places): Doubles voltage to indicator to make it brighter (See Part 2.5)
7) Probe Assignment (6 Places): Jump “A” to set probe to normally Wet state. (See Part 3.3 and Figure 3.4.1)
8) Common Ground (6 Places): Jump “B” should be made unless a Common Ground continuity check is desired.
9
2
4
5
7
8
3
1

10
6.2 Power Supply/Relays PCB
Normal Relay State
E = Inverse (Energized)
D = Direct (De-energized)
100-240 VAC
Neutral
Earth
100-240 VAC
Neutral
Earth

13
Appendix A
Installing and Removing Covers
To remove cover:
1) Open the enclosure completely and provide adequate support to keep the cover from being damaged dur-
ing disassembly.
2) Using a hammer and screwdriver, gently tap on the end of the hinge pin nearest the middle of the enclosure
(closed end) so that the pin becomes unseated at the other end (approx. 1/4”)
3) Using pliers, grasp the opposite end (flattened) of the hinge pin and pull completely out. Repeat steps 1
and 2 to remove the second hinge pin.
To install new cover
4) Assemble hinge pins to the cover by inserting the round end of the pin into the hinge core in the cover. You
may need to use a hammer to gently tap the pin into place. Repeat this for the second pin.
5) Align the cover with the base in the open position.
6) Using a small hammer, gently tap the hinge pin into the corresponding hole in the base until the end of the
pin is fully seated and flush with the cover surface. Repeat this step for the second hinge pin.
Changing out the latches
7) Remove existing latch by gently tapping the latch off the dovetail on the side of the enclosure.
8) Assemble the new latch by sliding the latch base onto the corresponding dovetail on the enclosure base
UNTIL COMPLETELY SEATED. Repeat steps 7 & 8 for the other latches.
Adding Mounting Feet
9) Place mounting foot on the back side of enclosure so that the countersink hole is directly over the brass
insert.
10) Using a screw driver and the #10-32 x 7/16” flat head screw, tighten the mounting foot to the enclosure.
Torque to approximately 25 in-lbs. Repeat steps 9 and 10 for the remaining mounting feet.
Step 1 Steps 2, 3, 4, 5 & 6
Steps 9 & 10

Spec: M22759-12-20-16C Date: July 16, 2009
By:
Approved:
M22759/12-20 16 CONDUCTOR CABLE UNSHIELDED
EXTRUDED WHITE PFA JACKET
Scope: This cable is designed specifically for use with Level-Trac Remote Level Indicator Sys-
tems for the span between the probe manifold and control unit. The probe side will be termi-
nated with high temperature, nickel plated steel, un-insulated ring terminals for connection to
the probes and common lug. Although designed specifically for Level-Trac equipment it is suit-
able for most high temperature, unshielded, instrument applications.
PRIMARY WIRE TYPE M22759/12-20-9
CONDUCTOR SIZE 20 19/32
CONDUCTOR MATERIAL NICKEL PLATED COPPER
CONDUCTOR DIAMETER .037" - .041"
PRIMARY INSULATION MATERIAL PTFE
PRIMARY WIRE DIAMETER .056" - .060"
CABLE CONSTRUCTION
NUMBER OF CONDUCTORS 16
COLOR CODE 9-96-93-954-92-90-94-97-98-91
901,902,903,904,905,906
JACKET MATERIAL PFA
JACKET COLOR WHITE
JACKET THICKNESS .015” NOMINAL
CABLE FINISHED DIAMETER .305" NOMINAL
PERFORMANCE CHARACTERISTICS
TEMPERATURE RATING 500º F / 260º C
VOLTAGE RATING 600 VOLTS
Appendix B
14
Table of contents
Other QTS Control Unit manuals
Popular Control Unit manuals by other brands
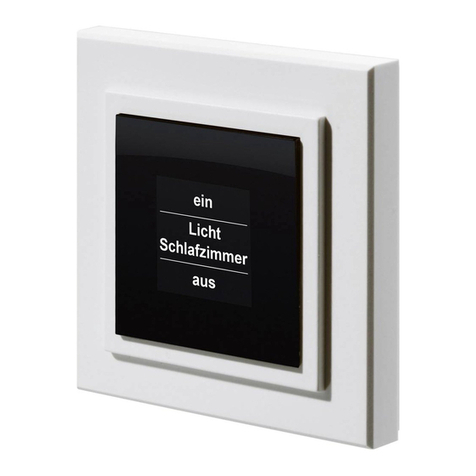
HomeMatic
HomeMatic HM-PB-2-WM Installation and operating manual
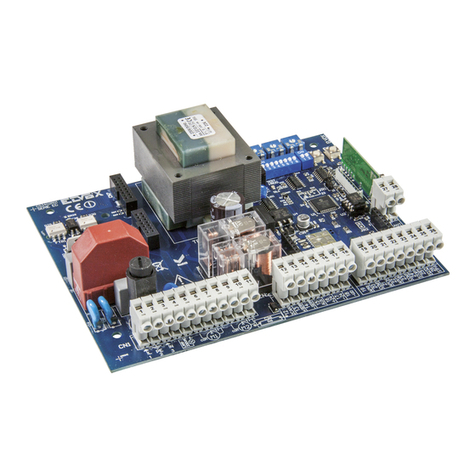
Vimar
Vimar ELVOX RS11 Installation and operation manual
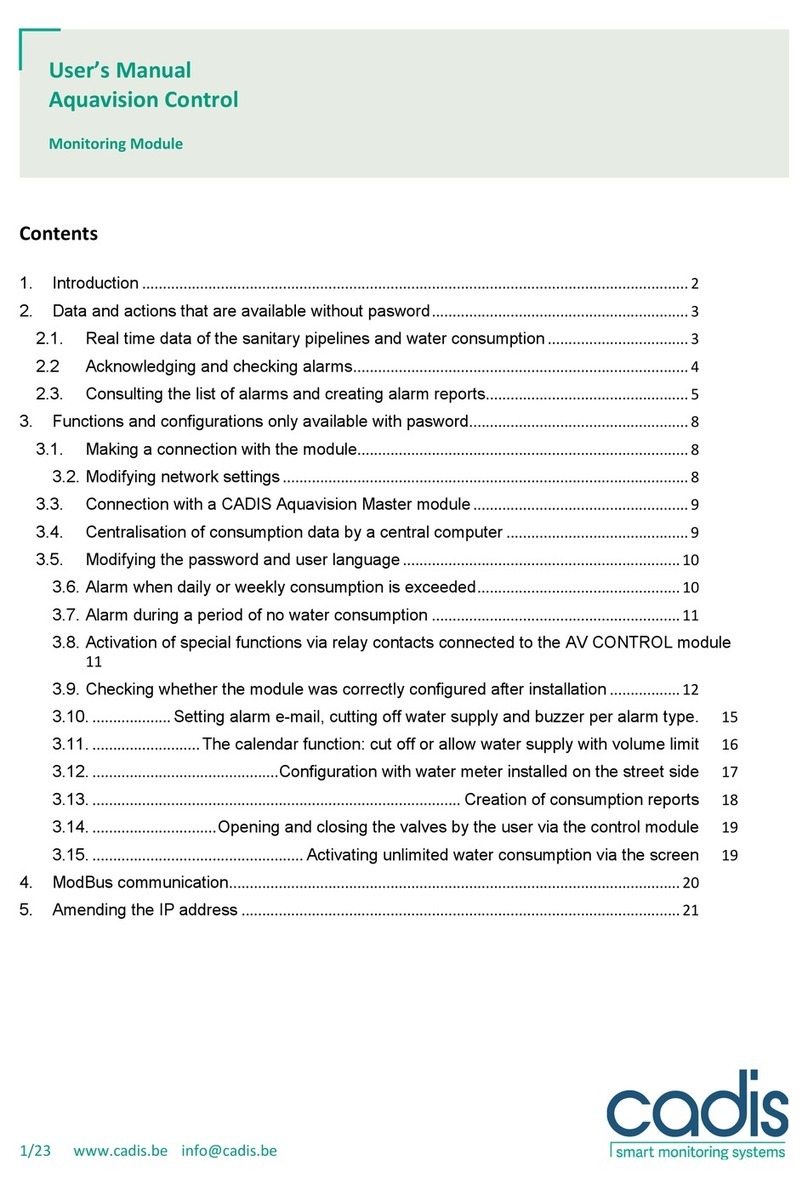
Cadis
Cadis Aquavision Control user manual

Bike Sport Developments
Bike Sport Developments Blip Box-Pro manual

Viessmann
Viessmann VITOTRONIC 300 Technical data manual

KLINGER SCHÖNEBERG
KLINGER SCHÖNEBERG INTEC K411-T&L-STD Assembly and Repair Instructions