Rühle IR 17 Quick guide

Lebensmitteltechnik
Translation of the original operating instructions
Injector
Type: IR 17

Injector IR 17
2
Table of contents
1 Safety instructions............................................................................. 3
1.1 Safety instructions ................................................................... 3
1.2 Remaining risk of accidents .................................................. 6
1.3 Intended use ............................................................................... 7
2 Installation instructions ................................................................... 7
2.1 Machine transport and setup ............................................... 8
2.2 Workplace description............................................................. 8
2.3 Connecting the machine ......................................................... 9
3 Operating instructions...................................................................... 9
4 Cleaning instructions.......................................................................10
4.1 Safety instructions .................................................................10
4.2 Cleaning agents and disinfectants....................................12
4.3 Cleaning procedure.................................................................12
5 Service: care, maintenance, repair .............................................13
5.1 Regular care ..............................................................................14
5.2 Regular maintenance.............................................................15
5.3 Repairs and spare parts........................................................15
6 Disposal................................................................................................16
7 Technical documentation ..............................................................16
7.1 Technical data ..........................................................................16
7.2 Circuit diagram .........................................................................17
8 EC Declaration of Conformity according to Directive
2006/42/EC........................................................................................18
Version: 24/10/2018
Subject to change

Injector IR 17
3
1Safety instructions
!!! Observe the safety instructions during installation, operation,
cleaning and maintenance of the Rühle Injector!
Hazard potentially causing irreversible injuries if
disregarded.
Warning potentially causing serious injuries if
disregarded.
Note
Work on electrical equipment of the machine may only
be carried out by qualified technicians!
Always disconnect machine from the mains during this
process!
Non-ionising radiation is not specifically generated, but
is only emitted by the electrical equipment (e.g. electric
motors, power lines or solenoid coils) for technical
reasons. In addition, the machine has no strong
permanent magnets. If a safety distance (distance field
source to implant) of 30 cm is maintained, the influence
on active implants (e.g. cardiac pacemakers,
defibrillators) can be excluded with a high degree of
probability.
1.1 Safety instructions
!!! A supervisor (responsible person) must be appointed for the
machine!
This person must:
a) Completely read and understand these operating instructions
before transport, commissioning, setup, operation, cleaning,
decommissioning, care/maintenance as well as
dismantling/disposal!
b) Prepare work instructions for intended and safe transport,
commissioning, setup, operation, cleaning, decommissioning,
care/maintenance as well as dismantling/disposal!

Injector IR 17
4
c) Ensure that the qualified workers have completely read and
understood the respective work instructions according to
section 1.1b!
d) Proper functioning of the protective devices must be checked
at least once a year by a Rühle service engineer!
e) Provide personal protective equipment!
All life cycle phases:
Use foot protection according to EN ISO 20345!
(e.g. recommended for butcher stores, dairies, meat and fish
processing: safety boots S4 with steel cap)
Use hand protection according to EN ISO 388!
(e.g. gloves with high cutting/puncture resistance)
Wear protective clothing according to EN ISO
13688!
(e.g. appropriate aprons / coats / overalls)
Cleaning; care/maintenance; dismantling:
Use eye protection according to EN ISO 166!
(e.g. tightly closing safety goggles)
Use light breathing masks according to EN ISO
149!
(e.g. simple breathing mask protection class FFP1)
Use hand protection according to EN ISO 374!
(acid-resistant, butyl rubber, Viton)
Wear protective clothing according to EN ISO
13688, EN ISO 17491!
(e.g. appropriate coats / overalls)
[The information on the proposed personal protective
equipment has only an advisory function. A full risk
assessment should be carried out before using the product
to assess whether the indicated personal protective
equipment is suitable for local conditions. Personal
protective equipment should conform to the relevant EU
standards.]
!!! The operator must operate the machine according to the intended
use and strictly observe all points listed in the “Operation” work
instructions prepared by the supervisor.

Injector IR 17
5
!!! Before putting the machine into operation for the first time and on
each working day, the operator must check the functionality of the
following safety devices:
a) Visual check for changes or damage on all machine sides and
accessible machine parts, e.g. the curing needles. The
machine must be shut down in the event of any damage or
changes!
b) Check the safety switches as follows:
Close curing compartment door with “discharge” safety guard
as well as the “intake” safety guard.
•Start the machine. –Turn the main switch to “0 – Off”. –If
the machine has not switched off, it must be shut down
immediately!
•Start the machine. –Lift the “Inlet” safety guard by 20
mm. –If the machine has not switched off, it must be
shut down immediately!
•Start the machine. –Lift the “Outlet” safety guard by 20
mm. –If the machine does not switch off, it must be shut
down immediately!
!!! To shut down the machine, turn the main switch to “0” - OFF" and
the disconnect the power plug from the outlet! Secure the machine
against further use!
!!! The supervisor must arrange for the repair of the non-functional
safety device by a Rühle service engineer. Until the corresponding
parts have been repaired, the supervisor must ensure that the
machine or parts of the machine are not put into operation under any
circumstances!
!!! The cleaning personnel must observe the work procedures from the
“Cleaning” work instructions prepared by the supervisor.

Injector IR 17
6
!!! The maintenance personnel may only carry out work specified as
“regular care”, unless any other authorisation has been issued in
writing by the manufacturer of the machine. The maintenance
personnel must observe the work procedures from the “Maintenance”
work instructions prepared by the supervisor.
Disconnect the power plug for maintenance work!
!!! Do not modify the machine.
!!! Only use Rühle spare parts and accessories.
!!! The operating instructions as well as all other technical documents
included must be supplied completely when reselling the machine.
1.2 Remaining risk of accidents
!!! All life cycles phases
Risk of injury when touching or handling curing needles or
softer blades!
Observe the safety instructions from the manufacturers
when handling curing, cleaning or disinfecting agents!
!!! Stability
The machine is top-heavy; this represents an increased
risk of tipping over when moving it!
Clear all obstacles before moving the machine!
The castors must always be locked with the locking
devices except when moving the machine!
!!! Maintenance
Disconnect the machine from the mains power when
performing maintenance work!
Only remove the protective covers (control box) while
carrying out maintenance work!
Do not operate the machine if the pump has no filter
basket!

Injector IR 17
7
1.3 Intended use
The Injector may only be used for injecting curing solution into fish
and meat products. The room temperature must not exceed 12 °C for
reasons of food hygiene!
This machine must not be operated by persons under the age of 18!
This machine is intended:
•for use during work
•for use by persons from 18 years old
•for use by instructed persons
Claims of any type for damage caused by use other than
the intended use are excluded!
Misuse
•Any use other than the use listed above is strictly prohibited
and is considered misuse!
•Operating the machine in explosive atmospheres is
prohibited!
•Handling/processing products and materials which are not
foodstuffs is prohibited!
•The loading ramp may only be loaded with max. 30 kg!
2Installation instructions
Installation and commissioning of the Injector may only be carried out
in the presence of a Rühle service engineer or by persons authorised
by Rühle.
Rühle GmbH Lebensmitteltechnik accepts no liability for any damage
resulting from failure to comply with these operating instructions.

Injector IR 17
8
2.1 Machine transport and setup
Please refer to the short instructions supplied with the machine
regarding transport and setup of the Injector.
The machine and machine parts must be transported by 2
persons (1 person to operate the floor truck/1 person to
supervise transport).
The power supply line must not be damaged by driving
over or crushing it!
The machine must be shut down until a damaged power
supply line has been repaired!
There is an increased risk of tipping over during transport
and movement!
To prevent this, do not drive over any objects such as
hoses, cables, etc. and watch out for protruding edges or
persons in the surrounding area!
The brakes on the two steering castors on the operator
side must always be locked except during transport!
Ensure that the machine is stable!
2.2 Workplace description
swivel range
curing chamber door
swivel range
loading ramp

Injector IR 17
9
The work area around the machine, plus a container on the discharge
and operator side, is at least 0.5 m on all sides; for maintenance work
it is at least 1 m; if used as a passageway, it is at least 1.2 m.
2.3 Connecting the machine
The machine is connected to a three-phase outlet (clockwise rotating
field), the specifications (voltage, amperage) must correspond to the
specifications on the type plate of the machine.
The machine must be shut down until a damaged power
supply line has been repaired!
Check the power supply line regularly!
Check the correct direction of the rotary field by starting
the machine. The machine cannot be started if the
rotational field is wrong.
•In this case, an electrician has to change the rotary
field inside the mains plug.
•The power supply to the machine must be fuse-
protected with 16 A and protected with an AC/DC
sensitive RCD (type B).
3Operating instructions
Please refer to the short instructions supplied with your machine for
operation of your Injector.
Also follow the safety instructions in chapter 1.1!
In its respective life cycle phases (transport,
commissioning, setup, operation, cleaning,
decommissioning, care/maintenance,
dismantling/disposal) this machine is designed for single
person operation!

Injector IR 17
10
When using this machine, no other persons may be
present near the machine!
The following is strictly prohibited and failure to comply
represents gross negligence:
•Lifting the lamella of the safety guard on the outlet
side and reaching into the curing chamber during
operation; the same applies the inlet side
•Operating the machine without protective enclosure
•Operating the machine without perforated basket on
the curing solution mixer/centrifugal pump
•Manipulating or deactivating the safety devices on
the machine
Working on the machine without the protective enclosure
installed is only permitted for Rühle service engineers
during the service phase!
The operator must ensure that
•No persons who do not know the hazards of the
machine or cannot anticipate them are present in the
area of the machine
4Cleaning instructions
The Injector IR 17 has been designed to allow for complete cleaning
both of the curing solution system and all parts that come into
contact with the food product.
4.1 Safety instructions
•Also follow the safety instructions in chapter 1.1!
•The cleaning staff must notify the supervisor immediately of any
defects on the machine.
•The cleaning staff must use the specified cleaning agents and
disinfectants.
•Germ reduction can only be achieved through correct cleaning
and subsequent disinfection.

Injector IR 17
11
•Appropriate materials (e.g. brushes, rags) are required and must
be provided for the correct execution.
•Cleaning products and disinfectants approved for use with
foodstuffs and suitable against the contamination (e.g. protein,
limescale, ...) must be used!
•The cleaning agents and disinfectants must be prepared as a
solution as described in the product data sheet from the
manufacturer.
Personal protective equipment must be worn as described
in Chapter 1.1!
Cleaning with high-pressure cleaners
is permitted only for:
•all external surfaces (all external stainless steel
surfaces + machine feet/castors)
•safety guard (intake)
•safety guard (discharge)
•curing chamber door
•needle bar (needle register, spring magazine)
•conveyor belt
•filter
•cleaning plate
The operator controls must be cleaned manually and must
not be exposed to a water jet!
All other parts and surfaces may be cleaned only with
normal water pressure!

Injector IR 17
12
4.2 Cleaning agents and disinfectants
The following cleaning agents and disinfectants must be used:
Cleaning agents:
Alkaline cleaning:
Acidic cleaning:
P3 –topax 19, P3 –topax 66
P3 –topax 56
Disinfectants:
P3 –topax 99, P3 –topax 66
Supplier:
Henkel Hygiene GmbH
Bonner Str. 117
40589 Düsseldorf
Germany
Tel.: +49 211 9893-0
Or:
Cleaning agents:
Alkaline cleaning:
Acidic cleaning:
Somplex F fat solvent
Somplex foam, acidic
Disinfectants:
Tego 2000, Tego IMC
Supplier:
Th. Goldschmidt AG
Goldschmidtstr. 100
45116 Essen
Germany
Tel. +49 201 1730-1
4.3 Cleaning procedure
Please refer to the short instructions supplied with your machine for
carrying out the cleaning procedure.
Before starting internal cleaning, remove any coarse soiling and
product residue from the curing chamber.
Preparation for external cleaning:
•To ensure optimum cleaning, some components of the machine
must be removed.
•Open the curing chamber door.
•Remove the cleaning plate.
oPlace the cleaning plate into the bracket provided.
•Remove the conveyor belt.
oPlace the conveyor belt into the bracket provided.

Injector IR 17
13
oIf necessary, the rod mesh belt can be separated from the
belt frame and cleaned individually.
•Remove the filter.
oPlace the filter into the bracket provided.
5Service: care, maintenance, repair
Any work related in any way to service may be carried out only by
Rühle service engineers and by persons authorised by Rühle in
writing. In this regard, a distinction is made between regular care and
maintenance and repair. The respective qualification certificate must
be issued explicitly for the corresponding task.
Also follow the safety instructions in chapter 1.1!
Notify and obtain permission from Rühle customer service if
welding or cutting work is required on the machine!
When working on the electrical equipment of the machine,
ensure that
•this is only done by qualified personnel
•the machine is always disconnected from the power
supply
•a waiting time of at least 10 minutes is observed after
switching off the machine to allow the capacitors of
the frequency converter to discharge to a harmless
voltage level
Use of lubricants –Hygiene area
•Multipurpose grease OKS 476 white, for food technology NSF H1
Reg. No. 137619
➢Needle bar (switching mechanism)
Use of lubricants –Other
•Multipurpose grease OKS 476 white, for food technology NSF H1
Reg. No. 137619
➢Pump (pump motor pump shaft connection)

Injector IR 17
14
➢Transport system (free-wheeling belt feed)
•Synthetic high-performance lubricant TEROSON VR 500 /
PLASTILUBE, on basis of super-refined mineral oils, free from metallic
soaps or fatty acids
Protective equipment:
Protective gloves (EN 374), eye protection (EN 166),
breathing mask (EN 14387), protective clothing (EN 14605)
➢Needle bar (drive sealing ring on motor)
[The information on the proposed personal protective equipment has only
an advisory function. A full risk assessment should be carried out before
using the product to assess whether the indicated personal protective
equipment is suitable for local conditions. Personal protective equipment
should conform to the relevant EU standards.]
5.1 Regular care
Regular care of the machine must be carried out at least once per
week. This prevents malfunctions and signs of wear.
Any abnormalities detected during regular care must be reported to
the supervisor! The supervisor must immediately initiate correction or
maintenance or notify Rühle Service!
Care schedule
a) Disassemble the machine according to the cleaning
instructions. Check for any parts moving with difficulty,
material abrasion or other signs of wear and tear.
b) Check curing needles for wear, damage and clear passage.
c) Check the needle system for leaks.
d) Check all safety switches as described in chapter 1.1 “Safety
instructions”.
e) Check steering castors and locking devices for damage and
correct function.
f) Visually check for changes or damage on all machine sides
and accessible machine parts, e.g. the needle bar. The
machine must be shut down in the event of any damage or
changes!

Injector IR 17
15
5.2 Regular maintenance
Regular maintenance of the machine must be carried out at least
once per year.
Maintenance schedule
a) Inspect the safety devices as described in chapter 1.1 “Safety
instructions”!
b) Read out the error memory (frequency converter)!
c) Replace the needle seals in the needle register!
d) Check curing needles for wear, damage and clear passage!
e) Check curing solution system (centrifugal pump, hoses, pipes,
needle register) for leaks!
f) Check the sliding guides of all joints of the curing solution
system for wear!
g) Check correct function of the pressure gauge!
h) Lubricate machine parts according to the list “Lubricant use”
at the beginning of this chapter!
i) Carry out a test run with open machine (caution: moving
parts)!
j) Check the needle bar switching mechanism (needle register,
spring magazine). All needles must close completely and
without delay after each stroke!
k) Check the conveyor belt frame for distortion!
l) Check the conveyor belt tension!
m) Check the centrifugal pump for smooth running!
5.3 Repairs and spare parts
As a damaged part on a machine is usually damaged due to causes
unrelated to the part, always carry out a fault diagnosis.
Contact our Service Hotline at +49 7748 523-11 for spare parts or
malfunctions. Please keep the machine type and number to hand.

Injector IR 17
16
6Disposal
1. The following components contain oil or lubricant:
•Beam drive
•Centrifugal pump (food oil)
All gear units/motors are equipped with oil drain plugs.
Subsequently, dispose of the oil correctly.
2. In addition, remove the lubricating oil and grease from all
lubricated parts properly and disposed of the oil and grease
afterwards.
3. All other materials must be sorted and disposed of at a
recycling facility.
7Technical documentation
7.1 Technical data
Supply voltage: 400 V 50/60 Hz 3~ / N / PE
Power consumption: 5.3 kW
Full-load current: 9.7 A
Back-up fuse max.: 16 A
Protection class: IP54
Ambient temperature: +2 to 40 °C
Dimensions, W x H x D: 1027 x 1849 x 854 mm
Work space, W x H x D: 1914 x 1849 x 1753 mm
Machine weight: 255 kg
Transport weight: max: 350 kg
Output: 1500 kg/h
Speed: Off: 0 strokes/min
Slow: 21 strokes/min
Fast: 42 strokes/min
Feed: 28 mm/stroke
Needles: 17 needles, in 2 rows
Clear opening dimensions,
W x H: 265 x 280 mm
Width of conveyor belt: 250 mm
Injection volume: 5 –60 %

Injector IR 17
17
Operating pressure max.: 4.2 bar
Emission sound pressure level: LpA = 77,4 ± 2,5 dB(A)
Measured according to: DIN EN ISO 11204
accuracy class 2
Measured in: idling without product, at maximum
speed
However, the data on the type plate principally apply; this is located
at the rear of the machine next to the power supply connection. In
case of deviations, please contact the manufacturer for a written
confirmation of the data.
If your country requires an RCD as protective measure, an RCD (type
B), AC/DC sensitive, must be used.
7.2 Circuit diagram
The circuit diagram of your machine is located in the electrical control
cabinet and must be supplied when reselling the machine.

Injector IR 17
18
8EC Declaration of Conformity according to
Directive 2006/42/EC
The manufacturer hereby declares
that the following product
Name, legal form:
Rühle GmbH
Lebensmitteltechnik
Type:
IR 17
Address:
Beim Signauer Schachen 10
79865 Grafenhausen
Germany
Designation:
from serial no.:
Injector
0500
complies with all relevant provisions of the directive indicated above, including any changes
that are valid at the time of this declaration.
The product complies with all relevant provisions of the following additional EU Directives and
standards, including any changes to these that are valid at the time of the declaration:
•DIN EN 1672-2: 2009-07
Food processing machinery –Basic concepts –Part 2:
Hygiene requirements
•DIN EN 60204-1: 2007-06
+ A1: 2009-10
Safety of machinery –Electrical equipment of
machines –Part 1: General requirements
•DIN EN 13534: 2011-02
Food processing machinery –Curing injection
machines –Safety and hygiene requirements
•EC 1935/2004
Regulation on materials and articles intended to
come into contact with food.
Nominated body:
Reason for the involvement of the
nominated body:
Name, legal form:
DGUV Test Prüf- u.
Zertifizierungsstelle
Type testing
Address:
Fachbereich
Nahrungsmittel
Dynamostraße 7-11
68165 Mannheim
Germany
Identification number:
0556
Signed by:
Person authorised for the documentation:
Place of issue:
79865 Grafenhausen
Germany
Name: Jürgen Stegerer
Date of issue:
08/12/2016
Address: Rühle GmbH
Position of the
signing person in the
company:
Management
Beim Signauer Schachen 10
79865 Grafenhausen
Germany
Name of the signing
person:
Mr. Claus Rühle
Signature:
Table of contents
Popular Laboratory Equipment manuals by other brands
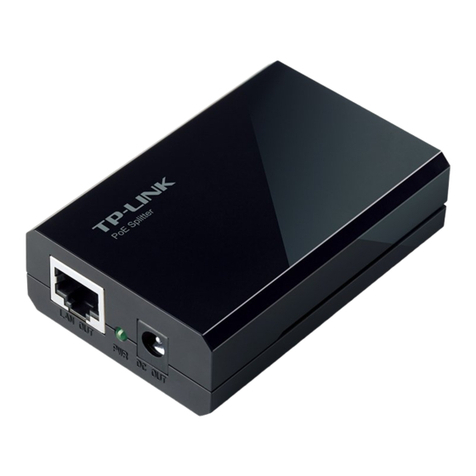
TP-Link
TP-Link TL-POE10R installation guide
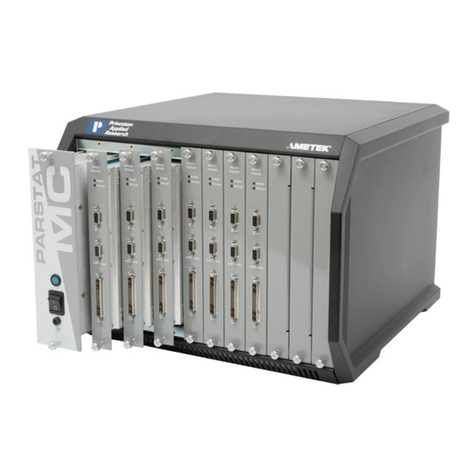
Ametek
Ametek PMC-200 Hardware manual

Optika Italy
Optika Italy M-1157 instruction manual
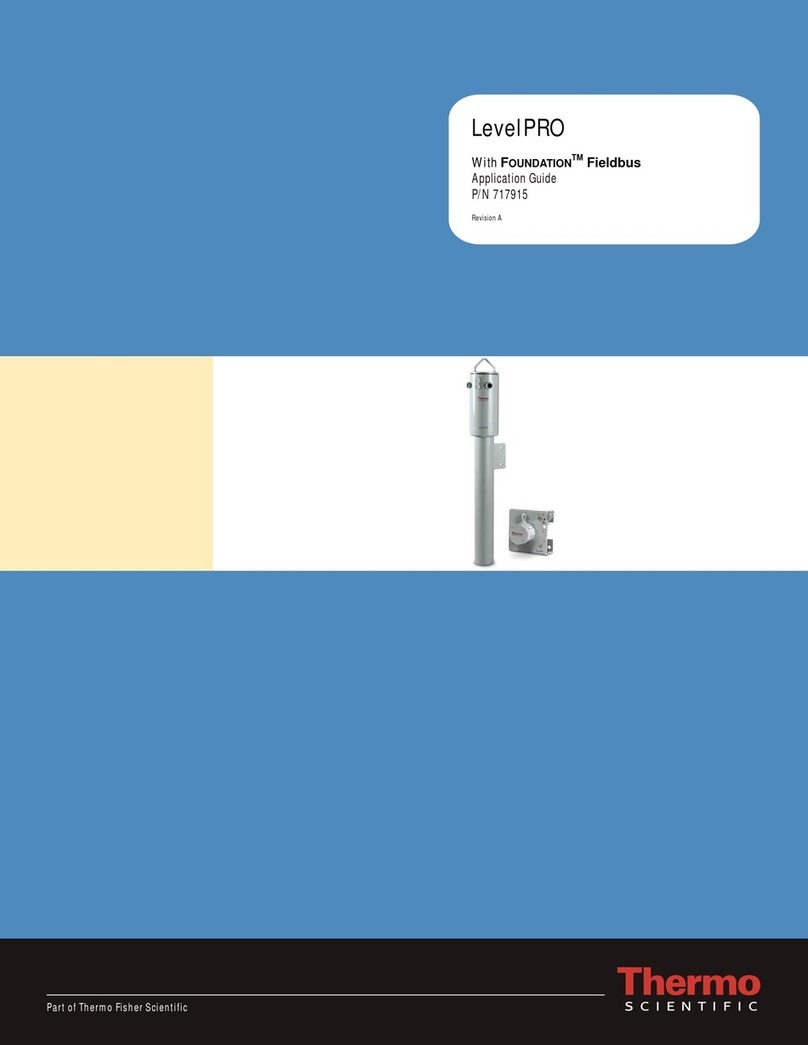
Thermo Scientific
Thermo Scientific LevelPRO Series Application guide
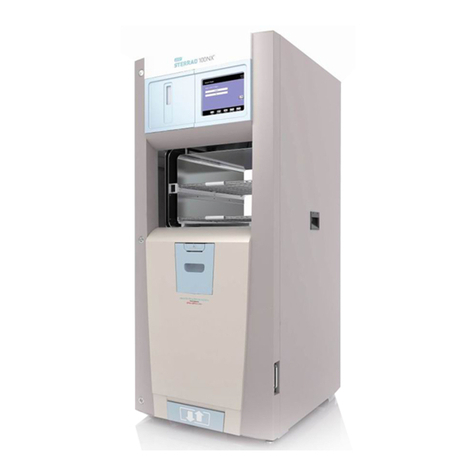
ASP
ASP Sterrad 100NX user guide

ThermoFisher Scientific
ThermoFisher Scientific ThermoScientific SpeedVac SPD120 Assembly, Installation and Operation