Raptor Photonics Eagle XO User manual

1
Eagle XO
Model: EA4240-CL
USER MANUAL

2
CONTENTS
1. INTRODUCTION................................................................................................................................. 3
1.1 Scope ....................................................................................................................................................3
2. SPECIFICATION ................................................................................................................................ 4
2.1 Camera Specification ............................................................................................................................4
2.2 Specification Table ...............................................................................................................................4
3. DESIGN OVERVIEW .......................................................................................................................... 5
3.1 Mechanical Model .................................................................................................................................5
3.2 Physical Interface..................................................................................................................................6
3.3 Power Consumption..............................................................................................................................6
3.4 Trigger IN ..............................................................................................................................................6
3.5 Trigger OUT (Exposure)........................................................................................................................6
3.6 Trigger OUT (Readout) .........................................................................................................................6
4. CAMERA AND CHILLER SETUP...................................................................................................... 7
4.1 Connecting the Camera and Frame Grabber........................................................................................7
4.2 Connecting the Camera and Chiller ......................................................................................................7
4.3 Reccommended Coolants for the Chiller ..............................................................................................7
4.4 Setting the Coolant Temperature for Re-circulation..............................................................................7
5. VACUUM ENVIRONMENT AND PERCAUTIONS ............................................................................ 8
5.1 CCD Sensor Percautions and Camera Storage....................................................................................8
5.2 Chamber Pumping and Venting ............................................................................................................8
5.3 Vacuum Pressure..................................................................................................................................8
6. SOFTWARE COMPATIBILITY .......................................................................................................... 9
6.1 XCAP Compatibility...............................................................................................................................9
6.2 Micromanager Compatibility..................................................................................................................9
6.3 LabView Compatibility...........................................................................................................................9
7. XCAP IMAGING SOFTWARE.......................................................................................................... 10
7.1 Computer/Laptop System Requirements ............................................................................................10
7.2 Frame Grabber Requirements ............................................................................................................10
7.3 Downloading and Installing XCAP ......................................................................................................10
7.4 Opening the Camera Configuration ....................................................................................................10
7.5 Acquiring a Live Image Sequence ......................................................................................................12
7.6 Controlling the Camera .......................................................................................................................13
7.6.1 Gain and Exposure Time .............................................................................................................13
7.6.2 Shutter Control.............................................................................................................................14
7.6.3 Trigger Control ............................................................................................................................15
7.6.4 Region of Interest (ROI) and Binning...........................................................................................16
7.6.5 Thermoelectric Cooling (TEC) .....................................................................................................18
7.6.6 Information Tab (Manufactures Data)..........................................................................................19
7.6.7 Saving Preset Settings ................................................................................................................20
7.6.8 Contrast Modification (XCAP Std. Only)......................................................................................21

3
(b)
(a)
(c)
(d)
1. INTRODUCTION
This document provides detailed instructions for the operation of the Eagle XO, liquid cooled,
Scientific CCD camera. Raptor Photonics Limited reserves the right to change this document at
any time without notice and disclaims liability for editorial, pictorial or typographical errors.
1.1 Scope
The camera has an option of two sensor formats, but this document focuses on the Eagle XO 42-
40 model. Details of the camera’s mechanical and electrical interfaces are provided, as well as
information on setting the camera up with liquid cooling and the vacuum chamber. Important
precautions to be taken when using the camera are also stated.
Detailed information is also provided on each of the cameras control parameters. Each camera
control is discussed and explained with the use of XCAP Imaging software, which is the core
plug and play software package that is offered with Raptor cameras.
Photographs of the Camera module, Power Supply and Camera Power Cable are shown in
Figure 1.
Figure 1: (a) and (b) Camera Module, (c) Power Supply Module, (d) Power Supply Cable.

4
2. SPECIFICATION
2.1 Camera Specification
The Eagle XO is designed for high resolution soft X-ray imaging. The camera uses a choice of
back-illuminated CCD sensors with a resolution of 2048x2048 or 1024x1024 available, all with 16
bit digital output formats. Low-noise electronics provide a linear response and sensitivity. A delta
>100 C is achievable using a TEC and liquid cooling in a vacuum environment. This level of cooling
gives an ultra-low dark current reading of <0.0005e-/p/s, allowing for longer integration times.
The Camera Link digital interface provides the most stable platform for data transfer and the
camera will work with any Camera Link standard frame grabber.
2.2 Specification Table
SPECIFICATION
Sensor (Back Illuminated, AIMO)1
e2v CCD42-40
e2v CCD47-10
Active Pixel
2048x2048
1024x1024
Pixel Pitch
13.5µm x 13.5µm
13µm x 13µm
Active Area
27.65mm x 27.65mm
(39.10 diagonal)
13.3mm x 13.3mm
(18.81mm diagonal)
Readout Noise (RMS)
<3.5e- @ 75kHz (2.3e-typical)
<12e- @ 2MHz (9.0e-typical)
Binned Readout Noise (RMS)
16x16 binning: <5.0e- @75kHz pixel readout rate
Spectral Response
12ev – 20keV
Peak Quantum Efficiency2
>90%
Full Well Capacity
>80ke- (100ke- typical)
Non-linearity
<1%
Digital Output Format
16 bit Camera Link (Base Configuration)
Dark Current (e/p/s)
<0.0005 @ -80°C
Dynamic Range (typical)
90dB (2MHz pixel readout rate)
93dB (75kHz pixel readout rate)
Trigger interface
Trigger IN and OUT – TLL compatible
Power supply
12V DC ± 10%
Cooling
Active: -70°C air cooled / -80°C water cooled, ΔT > 100°C
Camera Power Consumption
3<67W with TEC ON (Steady State)
Operating Case Temperature
-20°C to +55°C
Storage Temperature
-40 C to +70 C
Dimensions4
155.08mm x 140.89mm x 110.00mm
Weight
3.5kg
Flange5
CF152 (6”)
Note 1: A range of coatings are available.
Note 2: Download the full datasheet from our website for the full QE curve.
Note 3: For more detailed power consumption information, please refer to section 3.3 of the
manual.
Note 4: Dimensions include flange. Please refer to the mechanical drawing in section 3.1 for
full measurements.
Note 5:
Other flange options are available. Contact Raptor for further information.
For the latest Eagle XO Datasheet, please refer to Eagle XO datasheet from our website: www.raptorphotonics.com

6
3.2 Physical Interface
3.3 Power Consumption
Unit input power specification is +12VDC ± 10%, power dissipation ≤10W with the TEC switched
off. Additional inrush current (peak power) is required when the cooler power is switched from
low to high. Peak power ≤75W with total, steady state power consumption ≤67W.
3.4 Trigger IN
External synchronisation with the start of integration signal may be achieved using the Trigger IN
connector. Input impedance = 510Ω, 200pF input capacitance. Input logic levels are:
- Logic HIGH > 2.31V
- Logic Low < 0.99V
Min. pulse width = 100ns
3.5 Trigger OUT (Exposure)
For all modes of the camera the Trigger output, Exposure SMA, will represent the integration
period of the sensor. The trigger output signal will be a TTL output pulse. The signal will remain
low (0V) and then be driven high during the integration period. The source impedance will be
equal to 50Ω.
3.6 Trigger OUT (Readout)
For all modes of the camera the Trigger output, Readout SMA, will represent the duration of the
CCD readout. The trigger output signal will be a TTL output pulse. The signal will remain low (0V)
and then be driven high during the readout period of the CCD. The source impedance will be
equal to 50Ω.
1
2
3
4
5
1. Liquid cooling inlet/outlet valved
coupling : CPC; MCD2402
2. Liquid cooling inlet/outlet valved
coupling : CPC; MCD2402
3. TTL Trigger output, 50ΩSMA
(Exposure)
4. TTL Trigger output, 50ΩSMA
(Readout)
5. Camera Link connector (Base)
MDR, 3M P/N 10226-6212PC
6. Label recess, (Model Number.
Serial Number)
7. TTL Trigger input, 50ΩSMA
(Trigger In)
8. Camera power connector, Fischer:
DBP 104 Z092-139 (mating cable
supplied)
6
8
6

7
4. CAMERA AND CHILLER SETUP
This section will give instruction on setting up the camera and other components, including
connecting to the frame grabber and chiller (if applicable).
4.1 Connecting the Camera and Frame Grabber
The camera has the normal MDR port on the interface. The main frame grabber that Raptor offer
with this camera has the normal MDR port (EPIX EB1). Therefore, one MDR – MDR Camera
Link cable is required to connect the camera to this frame grabber.
4.2 Connecting the Camera and Chiller
Raptor uses a Chiller from Thermotek, the T257P Precision Chiller. For the datasheet and full
user manual from Thermotek, please contact Raptor and we can provide this. The instructions to
set up the chiller are as follows:
1. Connect the T257P chiller to the Falcon III using the tubing provided. You will hear a click
which indicates a solid connection. The polarity of the tubing connections does not matter.
2. Keep the chiller horizontal and on a level surface.
3. Make sure there is a minimum 12” clearance and free path for flow of air entry and exit at the
left side and right side of the T257P chiller prior to operation.
4. Remove the reservoir cap and add coolant to the reservoir until the fluid reaches the bottom of
the neck. Please refer to section 6.3 for recommended coolants.
5. Close the cap securely to the reservoir. Make sure not to overfill the reservoir.
6. Install the appropriate end of the power cord into the unit and connect to the mains electricity.
If using another chiller model, please refer to it’s manual for start-up instructions.
4.3 Recommended Coolants for the Chiller
The recommended coolants are:
Option 1: Distilled Water
Option 2: 95% distilled water and 5% isopropyl alcohol mixture prevents bio growth.
Option 3: 80% distilled water and 20% inhibited Glycol mixture for set temperatures below 5C.
Raptor recommends using option 3. If purchasing the Thermotek model from Raptor or using a
demo kit provided by Raptor, there will be inhibited Glycol mixture provided to mix with water.
4.4 Setting the Coolant Temperature for Re-circulation
When powering up the chiller, the screen will immediately give the option to set the temperature
of the coolant. It is recommended to set a 20 C set point. After the set point has been
configured, selecting start will initiate the coolant re-circulation. For more detailed information on
all the operating modes of the T257P Precision Chiller, please refer to the Thermotek user
manual.
Please ensure the temperature set point of the chiller is above your ambient dew point,
otherwise condensation can form around the sensor package and cause damage.

8
5. VACUUM ENVIRONMENT AND PRECAUTIONS
This section outlines information regarding using the camera in a vacuum environment and
highlights important precautions to be aware of.
5.1 CCD Sensor Precautions and Camera Storage
The camera is supplied with a temporary plate attached in front of the sensor for protection
during transit. A gasket seal prevents dust ingress during shipping and handling.
Take care when removing this temporary plate as the CCD sensor surface will be exposed and
could suffer inadvertent mechanical damage (e.g. from the gasket) or contamination from the
local environment. It is recommended to keep the temporary plate and gasket for storage of the
camera when not in use or for transportation. Regarding storage temperature, this can be seen
from the specification table (-40 C to +70 C).
Please ensure that condensation does not form on the sensor when moving the camera
from a low ambient temperature to a warmer environment. Even in storage, ensure the
CCD sensor is always warmer than the local dew point.
If the sensor becomes contaminated due to an accident or misuse, please contact Raptor
immediately.
When using M8 (or 5/16”) bolts to connect the camera flange to the vacuum chamber, please
ensure the O.D. of any washers used is <16mm (or <5/8”) to prevent damage to the camera
head.
5.2 Chamber Pumping and Venting
Take care when pumping (or venting) the vacuum chamber, ensuring that any gas flow
experienced by the sensor will not cause damage to the bond wires.
Make sure that particulate material does not strike the sensor during the venting process.
Always warm the sensor up to room temperature before venting the vacuum chamber.
5.3 Vacuum Pressure
It is recommended that the local pressure around the sensor is <5x10-5 mbar (<3.75x10-5 torr) to
achieve maximum cooling. Many pressure gauges emit radiation which can be detected by the
CCD sensor, if this background signal is affecting your data acquisition it may be necessary to
switch off the pressure gauge, once you are satisfied that steady state conditions have been
achieved.
Never cool the sensor below the dew point of the environment that it is in, otherwise
permanent damage due to condensation may occur. Switch the cooling off immediately if
you suspect condensation is forming on the sensor.

9
6. SOFTWARE COMPATIBILITY
This section outlines the options relating to software that are available for the Eagle XO camera.
6.1 XCAP Compatibility
Raptor works closely with EPIX who integrate all of the Raptor camera models into their XCAP
Imaging Software package. XCAP is the core plug and play software package that is offered with
Raptor cameras.
6.2 Micromanager Compatibility
There is a selection of Raptor cameras integrated into the free open source imaging software
Micromanager. The cameras currently supported can be seen in the table outlined in section 5.1.
6.3 LabView Compatibility
Raptor can provide LabView Interface Control Document files (.icd) to image and control the
camera on National Instruments Software such as NI MAX. Contact a Raptor Sales employee to
obtain this file.

10
7. XCAP IMAGING SOFTWARE
7.1 Computer/Laptop System Requirements
The basic requirement is that the PCIe bus of the system must provide sufficient bandwidth to
handle video rate transfers. The amount of bandwidth required depends on the camera in-hand.
The Eagle XO uses a Base Camera Link interface which can be handled with a x1 PCIe bus and
PIXCI EB1 providing about 200MB/sec max bandwidth. Contact EPIX Inc. for further information
regarding minimum computer/laptop specification requirements to run the XCAP Imaging
Software.
7.2 Frame Grabber Requirements
If using a computer, it is a minimum requirement to use an PIXCI EB1 frame grabber. If using a
frame grabber from another company, the specification requirements of this frame grabber must
meet those supplied by the PIXCI EB1 model.
If using a laptop, EPIX offers base Camera Link frame grabbers for a laptop system, such as the
ECB1/ECB1-34.
7.3 Downloading and Installing XCAP
The latest version of XCAP can be downloaded from the link below:
http://www.epixinc.com/support/files.php
please select the appropriate version of XCAP for your computer. Ensure that you download
from the section labelled “Pre-release version with support for the latest cameras and
latest PIXCI® imaging boards”.Open the downloaded file when complete and follow the
onscreen instructions in the installation wizard. If a pop-up message appears asking whether
to install the PIXCI driver, ensure that you click yes.
7.4 Opening the Camera Configuration
After opening XCAP, select “PIXCI Open/Close” from the “PIXCI” tab from the top menu bar in
the main window. A PIXCI Open/Close pop-up box will open as shown in Figure 2.
Click on “Camera & Format” that is highlighted in Figure 2 and a “PIXCI Open Camera & Format”
box will appear, as shown in Figure 3.
Figure 2: PIXCI Open/Close.

11
Using the dropdown menu highlighted, search for “Raptor Photonics Eagle XO 42-40”.
Alternatively, you can use the search button and typing Eagle XO will bring up the correct
configuration. Selecting “Open w. Default Video Setup” will open the control panel with all control
parameters set to the default states. “Open w. Last used Video Setup” will open the control panel
with all parameters set at the last known state. Once this option between the two has been
selected, click “Ok”. To open the camera control panel and imaging window, click “Open” in the
“PIXCI Open/Close” window (Figure 2).
Two windows will now open in XCAP, and imaging window and control panel, as shown in Figure
4.
Figure 4: Imaging Window & Control Panel.
Figure 3: PIXCI Open Camera & Format.

12
7.5 Acquiring a Live Image Sequence
There are two things to observe in the control panel that inform you that the camera is connected
and ready to image.
The serial connect checkbox must be ticked in the control panel. This informs you that you have
established a serial connection with the camera and can control the camera.
Secondly, the symbol near the bottom right of the control panel will have three moving dots that
flash. This indicates that you are obtaining video data from the camera. The imaging statistics
displayed directly underneath the imaging window will also inform you if you are receiving a video
feed from the camera.
Once you have established a serial connection with the camera and are receiving video data,
you can now grab a live image feed. Clicking the “Live” button will grab a live image sequence
which you will now see in the imaging window.
The symbols in the control app discussed above are displayed in Figure 5.
Figure 5: Port Tab – Checking Camera

13
7.6 Controlling the Camera
The XCAP control panel provides full control over the camera. The sections below will give
information on each control tab, giving a description on how to use each control parameter on
XCAP and their effect on the camera’s performance.
7.6.1 Gain and Exposure Time
The gain and exposure can be controlled in the "Gain” tab. By default, high preamp gain will be
enabled, offering the lowest noise. If you are imaging with a brighter signal, high preamp gain
can be disabled. The exposure time and frame rate controls are shown under every tab in the
GUI.
There is an exposure time user input box and slider bar to control the exposure time. The
theoretical maximum exposure is 7.6 hours. In practice, the maximum exposure will be limited by
the amount of background radiation events and at warmer CCD temperatures the dark current of
the device.
These controls are illustrated in Figure 6.
Figure 6: Gain and Exposure Controls.
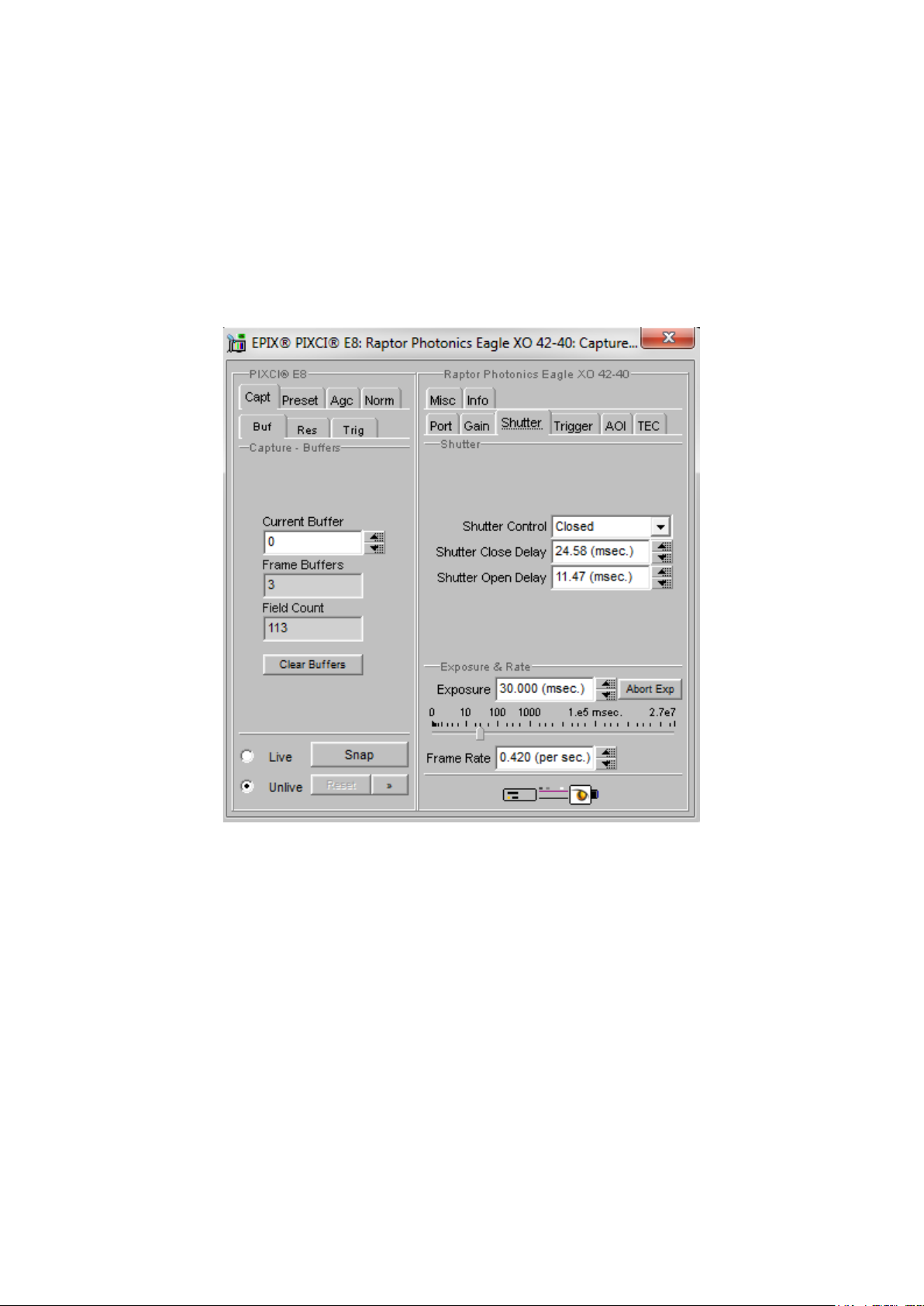
14
7.6.2 Shutter Control
The shutter state and open/close delay times can be configured from the “Shutter” tab,
highlighted in Figure 7. The three possible shutter states are closed, open and open with the
duration of exposure time.
Additional delay registers may also be programmed to allow the shutter to be fully open before
and fully closed after the exposure period, prior to the CCD being readout. This will prevent light
falling on the sensor during readout and causing smear. By default, the open and close delays
are set to 24.58ms (open) and 11.47ms (closed). These can be fine-tuned to meet the
requirements of the application at hand.
Figure 7: Shutter Tab.

15
7.6.3 Trigger Control
The trigger mode can be controlled from the “trigger” tab in the GUI. The three trigger mode
options are listed and described below:
Live ITR (Integrate then Read): In this mode, the camera uses an internal trigger to start the
integration and readout of the sensor. The camera will run with continuous integration and
readout of the sensor. This mode is used to capture a continuous sequence of images. The
camera will immediately trigger the start of a new integration period when the previous image
readout has completed.
Live FFR (Fixed Frame Rate): If the fixed frame rate mode is enabled, then the camera will
generate an internal trigger signal at a user programmable frame rate. The Frame rate user input
box under “Exposure & Rate” becomes active when this mode is selected, giving the user control
to program the frame rate.
Ext. Triggered:If this mode is enabled, then the camera will use an external trigger to start the
integration and subsequent readout of the sensor. Enabling this mode will also make the “trigger
polarity” control become active. Selecting “Rising Edge” means that the rising edge of an
incoming trigger pulse is used to trigger the start of integration. Selecting “Falling Edge” means
that the falling edge is used to trigger the start of integration.
Btn. Triggered: Selecting this mode will give the user an option to capture a single exposure.
When this mode is enabled, the “single exposure” control will become active and the customer
can manually trigger an exposure by clicking it.
Pixel Readout Clock Speed: The pixel readout clock speed can also be selected from this tab.
By default, the readout speed will be set to the fastest 2MHz. The user can change to a speed of
75kHz, which offers the lowest readout noise.
Readout Mode: The user also has the option to toggle the Readout Mode from the dropdown
box. For all readout modes of the camera, a test pattern image may be read from the camera
instead of CCD data. The test image will consist of a fixed ramp pattern that will start with a value
of 0 on the first pixel read from the camera and increment by one for each subsequent pixel read
from the camera. By default, the readout mode will be set to “Normal Data”, which reads out the
CCD data.
These controls are shown in Figure 8.

16
7.6.4 Region of Interest (ROI) and Binning
The ROI and binning controls are found in the “AOI” tab (Area of Interest) on the XCAP GUI.
ROI: A region of interest within the main active region of 2048 × 2048 may be defined. The ROI
is setup using a bank of registers to control the X offset, the ROI width, the Y offset and the ROI
height. These parameters are shown pictorially in Figure 9. The user must ensure that X offset +
ROI width is ≤ 2048 and similarly the Y offset + ROI height is ≤ 2048. Also, ROI width and ROI
height must be > 0.
Figure 8: Trigger Tab.
Figure 9: Region of Interest.

17
Binning: In addition to standard 1×1 output, various levels of pixel binning may be programmed
up to 64*64. Pixel binning is performed on the CCD and asymmetric binning combinations may
be used e.g. (1 × 2); (2 × 1); (1 × 3); (3 × 1); (4 × 7) etc. XCAP gives the user a lot of different
binning options to choose from. If there are binning formats that the user wishes to use that are
not an option in XCAP, please contact Raptor for support.
The ROI and Binning may be active simultaneously. The ROI is determined on a single pixel
basis after which binning may be applied. The ROI and binning controls in XCAP are shown in
Figure 10.
Figure 10: Region of Interest and Binning Controls.

18
7.6.5 Thermoelectric Cooling (TEC)
The “TEC” tab gives the user control over the cooling of the camera. By default, the TEC will be
disabled. When enabling the TEC, the control to adjust the TEC set point will become active and
will be set to 20 C by default. The Eagle XO can cool to -80 C with liquid cooling. If only using
the fan, the sensor can be cooled to -70 C. The fan control can be toggled from the “TEC Fan”
dropdown box. The delta between the PCB and sensor temperature is >100 C.
The sensor temperature can also be read back by clicking “Update Temp”.The current sensor
temperature is then displayed in the “Sensor Temp” box. The TEC tab is shown in Figure 11.
Figure 11: Region of Interest and Binning Controls.

19
7.6.6 Information Tab (Manufactures Data)
The “Info” tab displays information about the camera such as the manufactures data:
FPGA & Micro Version: The current firmware version of the camera is displayed.
Serial Number:States the serial number of the camera.
Build Date & Code: Gives the date that the camera was built.
ADC & DAC Calibration Values: These are calibration values that are used to set the TEC set
point and read back the sensor and PCB temperatures. They are not needed for the user as the
XCAP GUI has simple buttons to set and read back these temperatures, discussed in earlier
sections.
CCD & PCB Temperature: The current sensor and PCB temperature of the device can be read
by clicking “Update Temp”.
The parameters discussed can be seen in Figure 12.
Figure 12: Information Tab.

20
7.6.7 Saving Preset Settings
Different camera and frame grabber settings can be saved in the “Preset” tab under the PIXCI
(relevant frame grabber model number) section of the GUI, as shown in Figure 13.
Up to three different presets can be saved per settings file. If the camera is set to a desired state
outside of the default state, clicking “Save 1” will save all the current parameter states that have
been set.This can be done a further two times. These camera states can be recalled at any time
by using the recall buttons. The overall settings file can then be saved and loaded in this tab
also. Three preset states is the maximum number that can be saved in a settings file.
Figure 13: Presets Tab.
This manual suits for next models
1
Table of contents
Other Raptor Photonics Security Camera manuals