Rausch QuickLock User manual

Rausch Electronics USA, LLC. 4757 Innovation Way Chambersburg, PA 17201
Service: (717) 263-8093 | Office: (717) 709-1005 | Fax: (717) 709-1009 | www.rauschusa.com | [email protected]
Operator Manual
QuickLock Operator Manual –Version 15.07.01
QuickLock is NSF/ANSI 61 Certified for use in potable water.
QuickLock meets ASTM Standard F3110-14.

QuickLock Operator Manual
2
QuickLock Operator Manual –Version 15.07.01
IMPORTANT DISCLAIMER:
This manual is subject to change without notice. Updates can be obtained online at
www.rauschusa.com/quicklock. This manual does not guarantee the product will work
properly. The manual cannot take the place of your own experience or practical instruction by
the manufacturer. Contact a RAUSCH Certified Installer to ensure proper installation. The
following are important disclaimers to consider before using the QuickLock system.
1. QuickLock installations are to be performed only by trained and qualified personnel, using
adequate and safe equipment.
2. Read and follow the instructions, as described in this manual before attempting installation.
3. Prior to beginning the installation, verify that all the equipment and components involved are
undamaged and in proper working condition.
4. The use of equipment other than a certified Rausch packer and components will void the
functionality warranty. Using a Rausch QuickLock packer for non-OEM installations/sleeves
risks damages to the device or potentially injuring the operator, and voids all product
warranties.
5. Pressure gaugemust have the proper range setting (0 –70psi).
6. NEVER exceed the maximum packer pressure as indicated in the manual.
7. NEVER inflate the packer outside of a pipe –serious bodily injury or death may occur!
8. QuickLock is designed for and must only be used in municipal sewer, storm sewer and potable
water environment. For use in potable water, a special rubber gasket is required. For all other
applications, please consult Rausch prior to use.
9. Do not use QuickLock in broken pipes with protruding objects.
10. Verification of lines inner diameter / I.D. must be known as accurate as possible in order to
ensure the correct sleeve is used. Refer to the Data Sheet at the end of this manual.
11. If after reading this manual you have any questions or concerns, please contact Rausch USA.

QuickLock Operator Manual
3
QuickLock Operator Manual –Version 15.07.01
Table of Contents
IMPORTANT DISCLAIMER:........................................................................................2
1. Description of the QuickLock System ................................................................5
1.1. Intended Use............................................................................................................. 5
1.2. Regulations............................................................................................................... 5
1.3. Certifications ............................................................................................................ 5
1.4. Components and functions ..................................................................................... 6
1.4.1. Stainless steel sleeve.............................................................................................. 6
1.4.2. Rubber gasket......................................................................................................... 6
1.5. Description of the system and installation procedure........................................... 7
1.6. Suitability and materials used................................................................................. 8
1.6.1. Properties of the pipe to be repaired........................................................................ 8
1.6.2. 316L Stainless Steel................................................................................................ 8
1.6.3. EPDM Rubber ......................................................................................................... 8
1.6.4. Industrial Use .......................................................................................................... 8
1.6.5. Types of Pipe Damages........................................................................................... 9
1.6.6. Durability................................................................................................................. 9
2.
How to Install QuickLock...................................................................................10
2.1. Preparation ..............................................................................................................10
2.1.1. Pipe Inspection.......................................................................................................10
2.1.2. Pipe Preparation.....................................................................................................10
2.1.3. Space required by the packer.................................................................................11
2.2. Equipment, Material and Preparations for the QuickLock Installation................12
2.2.1. Equipment..............................................................................................................12
2.2.2. Material ..................................................................................................................12
2.3. Selecting the QuickLock Sleeve.............................................................................13
2.3.1. With beveled end....................................................................................................13
2.3.2. Without beveled end...............................................................................................13
2.4. Preparing the QuickLock sleeve ............................................................................14
2.4.1. Setup & Inspection .................................................................................................14
2.4.2. Lubricating the sleeve.............................................................................................14
2.4.3. Cutting the transportation tapes..............................................................................14
2.4.4. Apply talcum powder to the rubber gasket..............................................................15
2.4.5. Slipping on the rubber gasket.................................................................................15
2.4.6. Trimming (if necessary)..........................................................................................15
2.4.7. Centering the rubber gasket...................................................................................16
2.4.8. Affixing the rubber gasket.......................................................................................16
2.5. QuickLock Installation.............................................................................................17
2.5.1. The Packer.............................................................................................................17
2.5.2. Positioning the QuickLock sleeve on the packer.....................................................18
2.5.2.1. Standard Packer - Putting on the wheels......................................................18
2.5.2.2. Adjustable Packer –set to nominal diameter................................................18
2.5.2.3. Aligning the sleeve on the packer .................................................................18
2.5.2.4. Laser alignment............................................................................................18

QuickLock Operator Manual
4
QuickLock Operator Manual –Version 15.07.01
2.5.2.5. Aligning the locking gear strip.......................................................................19
2.5.2.6. Charging Device to hold position in place .....................................................19
2.5.3. Single Installation Procedure..................................................................................20
2.5.3.1. In the manhole..............................................................................................20
2.5.3.2. Positioning the packer & sleeve....................................................................21
2.5.3.3. Positioning Pressure.....................................................................................21
2.5.3.4. Deflating & Aligning in Center.......................................................................22
2.5.3.5. Align in Middle ..............................................................................................22
2.5.3.6. Application Pressure.....................................................................................22
2.5.3.7. Inspection.....................................................................................................22
2.5.4. Serial Installation (Standard Procedure).................................................................23
2.5.4.1. Procedure Overview .....................................................................................23
2.5.4.2. Installation ....................................................................................................24
2.5.4.3. Passing through the projecting rubber end....................................................27
2.5.4.4. The correct metal overlap .............................................................................27
2.5.5. Serial Installation (Alternative Procedure)...............................................................28
2.5.6. Using the Laser Marker..........................................................................................30
2.6. Special Scenarios....................................................................................................31
2.6.1. Repairing joint offsets.............................................................................................31
2.6.2. Groundwater infiltration ..........................................................................................32
2.6.3. Root penetration.....................................................................................................33
2.6.4. Corroded steel in reinforced concrete.....................................................................34
2.6.5. Repairing plastic pipes ...........................................................................................35
2.6.6. QuickLock in non-permeable pipe systems ............................................................36
2.6.7. Using QuickLock to repair holes longer than single sleeve.....................................37
2.6.8. Removing installed QuickLock sleeves...................................................................38
2.6.9. Deflating the packer using a vent valve ..................................................................39
3.
QuickLock Technical Data Sheet......................................................................40
4.
QuickLock Wheel Set Charts ............................................................................42
5. QuickLock Adjustable Packer...........................................................................48
5.1. Description...............................................................................................................48
5.2. Operation.................................................................................................................48
5.2.1. Setting compressed air supply................................................................................48
5.2.2. Remove the wheel..................................................................................................48
5.2.3. Adjust the slide.......................................................................................................48
5.2.4. Insert the wheel......................................................................................................49
6. Table of Application Pressures.........................................................................50

QuickLock Operator Manual
5
QuickLock Operator Manual –Version 15.07.01
1. Description of the QuickLock System
1.1. Intended Use
QuickLock is an entirely mechanical, seamless assembly system for patch repairs
inside pipes ranging from 6” to 32”pipe diameter in any common wastewater, well,
or drinking water pipe system.
A perforated version is available for stabilizing drainage pipes.
1.2. Regulations
The basis and general specification for pipe repairs using the Quick-Lock system is
DWA data sheet M143 Part 5
“Repairing wastewater pipes and sewers with internal sleeves”
1.3. Certifications
The QuickLock system for pipe diameters 6” –28”:
Has been certified under building law by the German Institute for Civil Engineering (DIBt) since
2005.
The system is also certified as resistant to jetting in accordance with DIN 19523.
Meets ASTM F3110-14 Standard Practice for Proper Use of Mechanical Trenchless Point Repair
Sleeve with Locking Gear Mechanism for Pipes of Varying Inner Diameter and Offset Joints
NSF/ANSI 61 certified for use in potable water.
For pipe diameters from 6” to 24”, there is a structural standard for host pipe state II, based on a
hydrostatic water pressure of 7.25 psi (0.5 bar) and twofold structural safety.

QuickLock Operator Manual
6
QuickLock Operator Manual –Version 15.07.01
1.4. Components and functions
1.4.1. Stainless steel sleeve
1- Beveled End
The beveled end faces the direction of
flow and improves the hydrodynamics,
prevents solids from depositing, and
increases jetting resistance.
2- Metal Overlap
The steel sleeve is rolled up smaller
than its nominal diameter. The overlap
is what is left over for expanding to
the pipe wall.
3- Toothed Strip
The locks that keep the sleeve
expanded run along the toothed strip.
4- Lock
The lock is a small set of gears that only
moves in one direction, thus keeping the
sleeve expanded.
5- Adhesive Tape
The tapes are put on at the factory to
protect the sleeve during the transport and
prevent it from unrolling.
6- Plastic Rivet
The plastic rivet prevents the sleeve from
unrolling and is sheared off during inflation.
1.4.2. Rubber gasket
7- Circumferential seals
The actual seal is formed by the
circumferential seals compressed
against the host pipe. The
damaged section must always be
between these seals.
8- Trimming Line
There is a trimming line marked in
the rubber gasket. It shows you
where to cut off the projecting
rubber end (when a single sleeve
is installed).
9- Projecting Rubber End
The projecting rubber end acts as
a seals between sleeves installed
in a series.
Cross section of steel sleeve and rubber gasket.

QuickLock Operator Manual
7
QuickLock Operator Manual –Version 15.07.01
1.5. Description of the system and installation procedure
QuickLock consists of:
A rolled up 316L stainless steel sleeve
A rubber gasket
The damaged section is repaired and sealed
by permanently clamping the steel sleeve in
place.
This exerts a pressing force which compresses
the rubber gasket against the inside of the
pipe.
The area between the circumferential seals (1)
is completely sealed.
When the steel sleeve is manufactured, it is rolled
tighter than the diameter of the pipe to be repaired.
Two toothed strips are punched into the sleeve, on the
left and right.
In each toothed strip there is a lock.
The lock is for clamping the steel sleeve.
The lock can only move in one direction and
stops the sleeve from contracting once it has
been expanded.
The lock moves along the toothed strip (to the left as
shown here).
This means that the steel sleeve can only expand in
one direction.
The lock prevents it from contracting again.
The increments are only 0.65 mm (.025”), which
means that the sleeve is almost infinitely adjustable.
How it works: The middle gear wheel is on a spring
and acts as a ratchet for the others.

QuickLock Operator Manual
8
QuickLock Operator Manual –Version 15.07.01
1.6. Suitability and materials used
1.6.1. Properties of the pipe to be repaired
QuickLock can be used to repair all common types of pipe:
Vitrified clay pipes
Concrete pipes
Plastic pipes (see section 2.6.5)
Glass-reinforced plastic pipes
Cast iron pipes
Steel pipes
QuickLock is only suitable with restrictions in the following cases:
Pipes with bends and fittings
Pipes with damage near the building connections (sockets, branches)
Pipes with joint misalignments of more than 2.5 cm (0.98”)
In such cases, please contact us.
1.6.2. 316L Stainless Steel
The QuickLock sleeve is made of 316L stainless steel of grade 1.4404. This grade of stainless steel is
characterized by its high corrosion resistance.
Quick-Lock is designed for use in municipal wastewater systems.
For use with industrial wastewater or where the wastewater contains high levels of chloride salts,
the required corrosion resistance must be ascertained.
316L stainless steel of grade 1.4404 may be used up to a chloride concentration of 600 mg/l.
1.6.3. EPDM Rubber
Like the steel sleeve, the thermoset polymer EPDM gasket is designed for municipal wastewater systems.
EPDM is characterized by its excellent physical properties and its resistance to aging, ozone, weathering
and environmental effects, alkalis, and various chemicals.
EPDM is unsuitable, or only suitable with restrictions for:
Solvents
Ethers, esters, ketones, methylene chloride
Animal and vegetable fats, oils, fuels
Concentrated fruit juice, oxidizing acids
Special version for oils, greases and hydrocarbons
An NBR rubber gasket is available on request for use with oils, greases, and hydrocarbons. (NBR: nitrile
butadiene rubber)
Special version for potable water.
A special NSF61 certified rubber gasket is required for potable water installations. Available on request.
1.6.4. Industrial Use
QuickLock is also suitable, with certain restrictions, for industrial use, depending on the properties of the
fluids.
Note: Before using QuickLock in industrial, non-municipal wastewater systems, the corrosion resistance
of the 316L stainless steel and the EPDM gasket must be verified.

QuickLock Operator Manual
9
QuickLock Operator Manual –Version 15.07.01
1.6.5. Types of Pipe Damages
Crack formation (longitudinal, radial and transverse)
Fragmentation
Leaking joints
Displacement / joint offset
Closing/sealing dormant unused laterals
Corrosion/ bursting / wear (reinforced concrete pipes with exposed reinforcement)
Leaks (ground-water infiltration and exfiltration)
Improvement of the structural strength of pipes (cracks and fragmentation, deformations)
Root penetration
Length of damage
When installed individually, QuickLock can be used for instances of damage up to the following lengths:
6” – 16”: maximum damage length 10.62”- 11.81” (see Technical Data Sheet, sealed area)
18” – 32”: maximum damage length 11.02” – 13.38” (see Technical Data Sheet, sealed area)
Instances of damage that are longer than this can be repaired by installing multiple sleeves in a series.
1.6.6. Durability
QuickLock repairs are extremely durable.
The materials used –stainless steel and EPDM –have proven their worth in municipal wastewater
systems for decades. A service life of more than 50 years can be expected.
Compound cracks,
fragmentation,
weakened pipe
Water ingress
Root
penetration
Leaking
joints
Unused
laterals
Joint Offset

QuickLock Operator Manual
10
QuickLock Operator Manual –Version 15.07.01
2.
How to Install QuickLock
2.1. Preparation
2.1.1. Pipe Inspection
Before using QuickLock, the pipe must be inspected to ascertain whether it can be repaired with the
system.
There must be at least one access via a manhole or inspection chamber.
The accessible manhole should have a diameter of at least 24 inch, in order to properly ensure
setting up the camera/tractor system and the QuickLock installation packer.
2.1.2. Pipe Preparation
Prior to installing the QuickLock system, the pipe must be cleaned by using a high-pressure jetter.
Hardened deposits, root infiltration, connection sockets protruding into the pipe must be
removed by means of suitable milling or cutting tools.
The pipe must be free of obstacles that could prevent the packer from traveling through.
The section of pipe to be repaired must be free of all solids such as sand and gravel, hardened
deposits, or wastewater solids.
Joint offsets larger than 0.39 inches must be milled off, if only a single sleeve is to be installed.
If (2) sleeves are available, a different installation method can be chosen. (See 2.3.3)
As a general rule, the QuickLock repair work can be completed during normal sewer operation,
however, the flow-level should be no more than approx. 20% of the sewer’s cross section. If too
many foreign objects are washed-in during the repair process, this pipe will need closed off and
by-passed - just to play it safe.
Notes for Nominal Diameter 28” & 32”
When using the QuickLock 28” sleeve, the top rungs in the manhole have to be removed.
The QuickLock 32” sleeve will not fit through a 24.5” manhole entrance – rolled up, its diameter is 27.36”.
The cone section of the manhole must be removed.
Depending on the type of damage, the QuickLock BIG 32” sleeve, which comes in two sections,
can be used.

QuickLock Operator Manual
11
QuickLock Operator Manual –Version 15.07.01
Approx. 0.2 in
2.1.3. Space required by the packer
Example for the space required by the packer + sleeve in a pipe:
Pipe Center
Packer center
The center line of the packer is approximately 0.5 cm below that of the pipe.
This means the distances above and below the sleeve are slightly different.
Example calculation for space requirements:
Pipe diameter: 300 mm
Diameter of Q.L. rolled up, including rubber gasket: 250 mm (see technical data sheet)
300 mm –250 mm = 50 mm above and below in total
Above: 50 mm / 2 = 25 mm + 5 mm (pipe/packer offset) = 30 mm
Below: 50 mm / 2 = 25 mm –5 mm (pipe/packer offset) = 20 mm
The packer can pass through sleeves that have already been installed
The sleeves are designed so that once they have been installed, the packer can pass through them with
another rolled-up sleeve, except for the 6” version.

QuickLock Operator Manual
12
QuickLock Operator Manual –Version 15.07.01
2.2. Equipment, Material and Preparations for the QuickLock
Installation
2.2.1. Equipment
For a reliable installation of the QuickLock system, the
following equipment should be available:
Inspection camera, adjusted to the correct nominal
diameter of the pipe. Ideally, the camera is equipped
with a pan & tilt and zoom feature.
QuickLock packer for correct diameter
QuickLock transfer bar to connect camera and
packer
Quick air-vent valve (see 2.3.11)
An air compressor and tank with a minimum output
of 80 psi and pressure regulator ranging from 5 –60
psi.
An air-hose on a reel with a minimum hose length of
350ft.
A milling robot for preparatory jobs
2.2.2. Material
The following materials and tools are necessary for the preparation of the QuickLock sleeve
Sharp knife
Talcum powder
Superglue
Biodegradable penetrating oil or food-grade lubricant
Hydrophilic waterstop (for groundwater infiltration and exfiltration only)
Mineral-based flexible mortar (root penetration, corrosion on reinforced concrete pipes)

QuickLock Operator Manual
13
QuickLock Operator Manual –Version 15.07.01
2.3. Selecting the QuickLock Sleeve
Beveled and non-beveled versions of each QuickLock sleeve are available.
2.3.1. With beveled end
The beveled QuickLock sleeve improves flow,
increases jetting resistances, and makes a
better looking fit. It closes the gap between the
QuickLock sleeve and the host pipe wall with a
beveled end.
The beveled end of the stainless steel sleeve
corresponds to the thickness at which the
rubber can no longer be compressed, so that it
does not exert pressure on the damaged host
pipe.
When installed individually, a sleeve with a
beveled end is always used.
When installed in series, the first sleeve in
the direction of flow always has a beveled end.
2.3.2. Without beveled end
Sleeves without beveled ends are mainly
used for installation in series (except for the
first sleeve used in direction of flow).
Without beveled end. With beveled end.

QuickLock Operator Manual
14
QuickLock Operator Manual –Version 15.07.01
2.4. Preparing the QuickLock sleeve
2.4.1. Setup & Inspection
Check the QuickLock sleeve and rubber gasket for visible
damage.
Set up the QuickLock sleeve so that the lettering on the adhesive
tape is upside down.
2.4.2. Lubricating the sleeve
Use biodegradable lubricant.
Pry apart the metal overlap with a screwdriver.
Lubricate the metal overlap so that the sleeve will slide
apart evenly.
Lubricate both of the two locking gears.
Wipe off excess lubricant from the inside and outside of the
sleeve.
Note: The lubricant must not get on the inner or outer side
of the EPDM rubber gasket.
2.4.3. Cutting the transportation tapes
Around the sleeve there are at least two strips of tape to stop it from
unrolling during transport.
The plastic rivet (1) must remain in the sleeve! It will be
automatically sheared off during expansion.
Cut half-way through the tapes on the metal overlap.
Note: If you cut right through the tapes, there is a risk that
the sleeve might unroll when entering the pipe, thus
restricting its movement and causing the sleeve to become
unusable.
Note: If you do not cut the tapes at all there is a risk that the
sleeve might unroll too suddenly during installation when the
tape tears, and destroy the locking gears.
Note: Once you have cut the transportation tapes on a
QuickLock sleeve, the sleeve is considered used and cannot
be returned.

QuickLock Operator Manual
15
QuickLock Operator Manual –Version 15.07.01
2.4.4. Apply talcum powder to the rubber gasket
For easier handling, sprinkle talcum powder on the inside of
the rubber gasket.
Completely coat the inside surface.
Note: We also recommend applying some powder directly to
the stainless steel sleeve body, but this is not required.
This makes it easier to slide the rubber gasket over the
sleeve.
It also reduces the friction between the rubber and the steel
sleeve during expansion.
2.4.5. Slipping on the rubber gasket
If the sleeve is beveled on one side, make sure you slip the
projecting rubber end over the straight edge.
Slide the EPDM over the sleeve with the rubber extension located
at the top.
Slide the rubber gasket over the steel sleeve so that the marking
seam is flush with the edge of the sleeve.
2.4.6. Trimming (if necessary)
When installing a single sleeve, always trim the projecting rubber
end from the sleeve.
Make sure beforehand that the distance between the
circumferential seals is enough to seal the damaged area.
Single Installation
Use a sharp carpet knife or industrial scissors.
Cut along the marking seam.
Serial Installation
When installed in a series, the projecting rubber end is
left on so that the join between the sleeves is sealed,
except on the last sleeve to be installed.

QuickLock Operator Manual
16
QuickLock Operator Manual –Version 15.07.01
2.4.7. Centering the rubber gasket
Center the gasket on the sleeve so that the edge
of the rubber is at least 0.2-0.4” (5–10 mm)
behind the edge of the sleeve, or on beveled
sleeves behind the edge of the beveled end.
1) 0.2-0.4” (5-10 mm)
2) 0.2-0.4” (5-10 mm)
2.4.8. Affixing the rubber gasket
To stop the rubber gasket from shifting on the
steel sleeve during transportation to the damaged
area, affix the gasket to the sleeve with a spot of
superglue above the locks on both ends (@ 12
o’clock), as well as opposite both sides of the
stainless steel sleeve (@ 6 o’clock) using
superglue.
Glue at four locations with approx. ½ inch strip of
glue at each spot.
Note: Do not allow glue to drip onto the metal
overlap, because it will stick and prevent the
sleeve from opening.
Note: If the rubber gasket is not properly affixed,
there is a risk that it might unfold and bunch up at
a constricted point in the pipe without you
noticing.

QuickLock Operator Manual
17
QuickLock Operator Manual –Version 15.07.01
2.5. QuickLock Installation
2.5.1. The Packer
Tractor Camera Packer
The QuickLock sleeves are installed using a special OEM trolley called a packer.
Each packer can be used for at least two different nominal pipe diameters (and the special
intermediate sizes in between –see Section 3 –“Technical Data Sheets”).
For each nominal pipe diameter, there is a suitable set of wheels, or a set of wheels with a wider
track. (See Section 4 –“QuickLock Wheel Set Charts”)
Special diameter sleeves usually require special sets of wheels, which are available upon
request.
The packer is usually connected to the camera or robot using a transfer bar and two ball joints.
Using a camera
The QuickLock system can be installed most efficiently when the packer is positioning using a camera.
Push rods or other insertion apparatus can also be used. However, a camera must be used during
installation.
Adjustable packer with sliding chassis
As of 07/2015, two offset packers with adjustable sliding chassis are available:
Packer I: 8”-12” packer
Packer II: 14”-20” packer
See “Adjustable Packer” Section 5.2 – “Operation” for further instructions on Page 48 and 49.

QuickLock Operator Manual
18
QuickLock Operator Manual –Version 15.07.01
2.5.2. Positioning the QuickLock sleeve on the packer
2.5.2.1. Standard Packer - Putting on the wheels
Select the correct set of wheels for the pipe diameter (see Section
4 –“QuickLock Wheel Set Charts”)
Attach the front wheels before placing the sleeve.
Attach the rear wheels after placing the sleeve on the packer.
OR
2.5.2.2. Adjustable Packer –set to nominal diameter
Set the sliding chassis of the packer to the nominal diameter of
the host pipe
See “Adjustable Packer” Section 5.2 – “Operation”for further
instructions.
2.5.2.3. Aligning the sleeve on the packer
The sleeve is usually positioned on the packer (while in the
manhole / before placing the packer in the manhole).
When installing beveled sleeves, the beveled end should face
against the direction of the flow.
Slide the sleeve over the end of the packer without wheels.
Position the QuickLock sleeve forward so that it is flush with the
front edge of the packer.
2.5.2.4. Laser alignment
If you are using a packer equipped with a laser, position the
sleeve so that the laser beam is reflected both on the edge of the
sleeve and the host pipe.
In both cases, the camera gives you a good view of the edge of
the sleeve.

QuickLock Operator Manual
19
QuickLock Operator Manual –Version 15.07.01
2.5.2.5. Aligning the locking gear strip
It is a good habit to always position the sleeve on the packer with the ends of the toothed strips facing the
same direction.
The sleeves would be regularly aligned in the pipe, especially when multiple sleeves are installed.
Turning the toothed strip upwards, to the 11:00 or 1:00 position
Turn the QuickLock sleeve so that the middle
of the toothed strip is in the 12:00 position.
Depending on which way you look at it, the
locking gear will be in the 11:00 or 1:00
position.
After installation, the locking gear will always
end at the top, in the 12:00 position.
Turning the locking gear to the 12:00 position
Depending on the design of the camera or the
transfer bar, it may be necessary to position the sleeve on the packer
with the locking gear in the 12:00 position, especially when installing
in a series and where movement is restricted. This prevents the
transfer bar from catching in a previously installed sleeve.
It can also be preferable during serial installation if the view through
the transfer bar is impaired by the locks on a sleeve that has already
been installed.
After installation, the locking gears will be in the 11:00 or 1:00
position.
If the QuickLock sleeve is positioned on the packer with the lock in
the 12:00 position, the weight is balanced.
This makes it easier to transport, especially in narrow pipes. It is also
reduces the risk of the packer tipping over in the pipe.
2.5.2.6. Charging Device to hold position in place
The charging device is used to inflate the packer to a holding pressure
which keeps the sleeve from shifting. To be done outside of the
manhole.
Attach the charging device to the air hose.
Position the sleeve on the front of the packer.
Connect the charging device directly to the packer with the
sleeve and wheels already in place.
Inflate the packer to a holding pressure of approx. 8 psi, or
enough to hold the sleeve in place on the packer securely.
This holding pressure may vary from packer to packer,
therefore it is the user’s responsibility to safely secure onto
packer.
The holding pressure is correct when the sleeve is firmly held
on the packer but does not start to open.
When not using a camera/tractor: Proceed to next step with
the charging device still attached.
When using a camera/tractor: Close the valve on the packer
and disconnect/remove the charging device.

QuickLock Operator Manual
20
QuickLock Operator Manual –Version 15.07.01
2.5.3. Single Installation Procedure
QuickLock sleeves can be installed individually to repair areas of damage smaller than the distance
between the circumferential seals. See Appendix 1, Technical Data Sheet, Sealed Length.
Serial installations are used to install larger areas of damage.
It is advisable to install individual QuickLock sleeves from the downstream manhole so the flow
does not block the view of the camera.
The most efficient and reliable way to install a QuickLock sleeve is by pushing the packer with a camera
tractor system. However, other means are possible, too: Telescopic rods or pulling the packer through the
pipe. Nevertheless, a camera should always monitor and record the installation process.
When access to two manholes is possible, it is a lot easier
to set up the camera with the packer in one manhole, run
the tractor through the pipe to the second manhole, fetch
the sleeve and then go back. It is easier to “load” the
packer that way.
For single installations, always use beveled sleeves.
The beveled end must always face against the direction of
the flow.
2.5.3.1. In the manhole
Connect the packer to the camera and the mounting
bracket using the transfer bar.
If using a charging device: Connect the air hose to the
bracket and open the valve on the packer. IMPORTANT: if
you fail to perform this step, the packer cannot install the
device; no air flows in or out of the packer.
If not using a charging device: Connect the air hose to
the bracket and inflate the packer to a holding pressure of
approx. 8 psi, or enough to hold the sleeve on the packer
securely. This keeps the sleeve from shifting during
transportation.
Table of contents
Popular Tools manuals by other brands

Westfalia
Westfalia 25 96 14 instruction manual

Ingersoll-Rand
Ingersoll-Rand AVC10 Operation and maintenance manual

Sealey
Sealey SDC01 quick start guide

HURST
HURST Unitool SC 250 M instruction manual
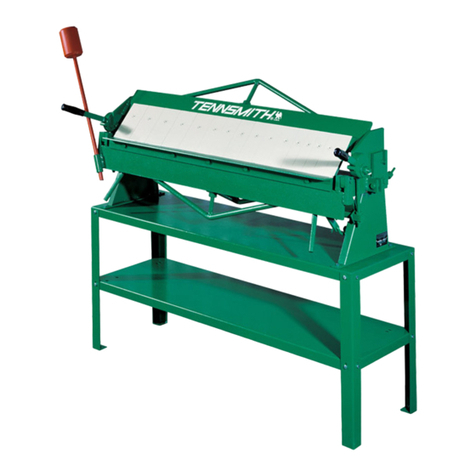
Tennsmith
Tennsmith U48-22 Operation, parts & maintenance manual

Glenair
Glenair Band-Master ATS operating instructions