RBR ecom LSG User manual

rbr Messtechnik mbH • Am Großen Teich 2 • D-58640 Iserlohn • Tel. +49 (0)237 /945-5 • Fax +49 (0)237 /40305
Internet www.rbr.de • E-Mail info@rbr.de
Service

Content
1. Test of the basic functions............................................................... 2
1.1 Switch On functions........................................................................................ 2
1.2 Buttons............................................................................................................. 2
1.3 Red LED ........................................................................................................... 2
1.4 LED for lightening the L D............................................................................. 2
1.5 L D................................................................................................................... 3
1.6 Battery voltage measurement........................................................................ 3
1.7 Beep ................................................................................................................. 3
1.8 Jack plug.......................................................................................................... 3
2. Start-up.................................................................................................4
2.1 Warm-up phase ............................................................................................... 4
2.2 Measurement................................................................................................... 4
2.3 Scale of the bar graph display....................................................................... 5
2.4 Sensitivity......................................................................................................... 5
2.5 Automatic Switch Off...................................................................................... 5
2.6 Battery.............................................................................................................. 5
2.7 Operation via the Jack Plug ........................................................................... 6
3. alibration............................................................................................6
3.1 hange in the software for calibration V02................................................... 6
4. alibration Device LSG and LSK .......................................................7
5. Failure Display .....................................................................................8
6. Setting of the soldering bridges ........................................................9
7. Testing Bottle.....................................................................................10
8. Software Update LSG .......................................................................11
9. Exchange the Sensor unit ...............................................................12
10. hanges at the software version...................................................13

2
1. Test of the basic functions
1.1 Switch On functions
With the „I/O“ button the LSG/LSK is switched on. All LCD-segments, die red LED, the beep
and the LCD lightning are switched on. By pressing the I/O Taste longer this function check will
be done correspondingly longer.
Switch on display with all LCD segments
After that the firmware version is displayed shortly. Version = right bar etc.
LSG : Display firmware version
LSK : display firmware version
1.2 Buttons
With the „I/O“ button the instrument is switched on and the display mode can be changed.
By long pressing of the „I/O“ button the LSG-LSK will be switched off. Press the button as long
as the bars cannot be seen anymore.
By pressing the “Hold“ button a later zero setting of the ppm display is possible and the
selection of the options can be done.
1.3 Red LED
The red LED is for the display of the gas concentration. The blinking frequency increases with
the gas concentration. Is a calibration possible the LED is blinking with Hz.
1.4 LED for lightening the LCD
During switch on the LCD lightening is always activated. During normal operation the lightening
can be switched on optionally.

3
1. LCD
The little point in the lower left corner is blinking in every display mode. The battery symbol is
displayed in the mode “Battery display”.
1.6 Battery voltage measurement
When inserting new batteries the display must show 3 bars minimum. When using
accumulators minimum 0 bars.
The LSG/LSK consumes without lightning in normal operating 35mW (± 5mW). With lightning
the consumption increases to 80mW (±20mW).
Attention: The energy consumption is pulse shaped.
1.7 Beep
The beep will sound for function control during switch on.
The ppm-beep can be switched off optionally.
1.8 Jack plug
Via the jack plug the LSG/LSK can be powered with 6 to 4 Volt. The instrument must be
equipped with batteries.
When powered by 2V the energy consumption is: :
- 55mA without LCD lightning
- 70mA with LCD lightning
- 75mA with LCD lightning and piezoelectronic
Attention: The energy consumption is pulse shaped with a peek of less than 0.5A and
a frequency of 200Hz.

4
2. Start-up
2.1 Warm-up phase
After switch on the warm-up phase starts. It lasts between 60 seconds and four minutes.
Should the EPROM in the sensor head have no valid parameters the warm-up phase will always
last four minutes.
The maximum warm-up time will arise when the instrument has not been used for a long time.
During warm-up time a running bar can be seen in the bar graph display which is a symbol for
the progress of the warm-up phase.
At the end of the warm-up phase a zero calibration will be done. Should the sensor resistance
be out of the tolerance window a failure message will be indicated.
During warm-up phase the actual battery voltage can be displayed via the „I/O“ button. The
display will return to the running bar after some seconds.
An exchange of the sensor head should just be done when the instrument is switched off. It is
done when the instrument is switched on a warm-up phase will be run automatically.
During the first 0 seconds of the warm-up phase the voltage consumption of the LSG/LGK is
higher than in normal operation.
2.2 Measurement
At the end of the warm-up phase a signal beep will sound and the actual sensor value will be
taken as „Zero Concentration“ (zero setting). Out of this zero setting and the value of 000 ppm
calibration which is stored in the sensor head the senor characteristics for the measurement will
result.
In this mode following display mode can be selected via the “I/O” button:
− Display of gas concentration. With the “Hold” button a new zero point can be taken
(smallest button is blinking). The former zero point can be restored by long pressing of
the “Hold” button.
− Setting of the sensitivity (blinking bar). Selection via “Hold” button.
− Battery display (Battery symbol is displayed ). Via the “Hold“ button the activation of the
LCD lightning and the ppm beep is possible.

5
2.3 Scale of the bar graph display
Bar : 0 ppm
2 Bars : > 40 ppm
3 Bars : > 80 ppm
4 Bars : > 25 ppm
5 Bars : > 75 ppm
6 Bars : > 250 ppm
7 Bars : > 350 ppm
8 Bars : > 500 ppm
9 Bars : > 700 ppm
0 Bars : > 900 ppm
Bars : > 50 ppm
2 Bars : > 500 ppm
3 Bars : > 3000 ppm
4 Bars : > 4500 ppm
These data are just approximate values and are not for end users information. Since the
LSG/LSK are calibrated with calibration gas at 000 ppm following statement can be made:
at 000 ppm the display will be between 9 and bars!
2.4 Sensitivity
The sensitivity can be set to “ /5“ (left bars blinking), “normal” (middle bars blinking) and
“factor 5” (right bars are blinking)..
At „factor 5“ ten bars will be shown already at a concentration of 200 ppm.
2. Automatic Switch Off
Should no button be pressed the instrument will switch off after 20 minutes.
2.6 Battery
At all display mode the grey battery symbol will be shown once the battery voltage is be below
2. 0V. Below 2.0V the battery symbol will be shown as black.
When the battery voltage is below .9V the instrument will switch off..
The operating time without lightning is at approximately 6 hours and at approximately 2 hours
with lightning.
It appears that the contact resistance between the batteries and the clip contacts have a
negative impact on the operating time. . If might be useful to turn the inserted batteries in the
clip contacts several times.

6
2.7 Operation via the Jack Plug
The LSG/LSK can be energised also via the jack plug. The allowed range is 6 to 4 Volt. For
switch on the LSG/LSK batteries must be inserted to the instrument. These batteries might
even be discharged.
3. Calibration
The calibration will be cleared via the 0Kohm jack plug. The red LED is blinking with Hz.
To start the 000 ppm calibration the sensor head has to be aerated. Starting with the “Hold”
button both buttons have to be pressed simultaneously until a signal can be heard and the red
LED is lightning permanently.
With the “Hold“ button the calibration value is taken.
In case the resistor value of the sensor is less than 50 % of the zero calibration the new
calibration is set and will be stored in the sensor head. Calibration is finished by this.
In case the resistor value is out of the foresaid range a permanent signal will sound. With the
“Hold” button a new calibration value can be taken or the calibration mode can be left via the
“I/O” button.
Together with the data for the 000 ppm calibration the value of the zero point will be stored in
the sensor head. This zero point is relevant for the tolerance range for the future zero
calibration. Therefore its very important to ensure suitable conditions when making the factory
setting of the zero calibration! The detectable gas may not be in the ambient air!
The zero calibration will be done automatically after every warm-up phase. The resistance of the
sensor must be in the range of 0.333 to 3.0 of the value of the zero calibration stored in the
sensor head. Otherwise a failure message will be indicated.
Example : Stored value in the sensor head of the zero calibration: 5 KOhm
Min. resistance for the zero calibration: 5KOhm
Max. resistance for the zero calibration: 45KOhm
During calibration the function „automatic switch off“ is not active
The gas concentration will be indicated as bar graph.
During calibration a code will be stored in the EPROM of the sensor head for the sensor type
LSG respectively LSK. Afterwards the sensor head can just be operated with the same
instrument type.
Besides the calibration data the settings for the LCD lightning and the ppm beep will be stored
in the EPROM of the sensor head.
3.1 Change in the software for calibration V02
After clearance of the calibration via the „ 0KOhm lug jack“ the 0th bar will be displayed grey
blinking for the 000 ppm concentration. Furthermore the red 3 mm LED is blinking with higher
frequency as soon as the concentration is between 800 ppm and 200 ppm. When checking
the LSG/LSK with 000 ppm span gas the bar indication must be between nine and eleven
bars. The function for zero setting via the mode button and the adjustment of different
sensitivities are blocked as soon as the calibration is cleared.

7
4. Calibration Device LSG and LSK
• Before calibration fill up the wash bottle
with water (up to middle position
between „MIN.“ and „MAX.“)
• the very left connection is for the
humidity probe and both right
connections are for the instruments
which should be calibrated
humidity probe
• connect gas bottle (LSG with 000ppm Methane in synth. air, LSK with R 34A in
synth.air)
• adjust the left flow meter up to one (gas flow)
• the humidity probe is adjusted with the right flow meter (45- 55 % rF synthetic air)
• then follow the calibration procedures

8
. Failure Display
Instrument failures will be displayed as bars in the LCD display. By confirming with the “I/O”
button the instruments may be operated nevertheless. The failure will be displayed in exchange
to the normal display. (bar 4 is the very right one)
Failure Discription
Failure DiscriptionFailure Discription
Failure Discription
Failure reason
Failure reason Failure reason
Failure reason
Bar 4 (wrong calibration) • when making the zero calibration a gas
concentration was present
• to less difference between zero and
000ppm calibration
• Sensor defect
•
Bar (Sensor head)
• no sensor head present
• Heating element of the sensor defect
Bar 8 (wrong sensor head)
• Wrong sensor head has been mounted
(LSK head at LSG instrument)
• see setting of the soldering bridges
Bar 5 (EEPROM data failure)
• EEPROM contains no valid calibration data
• failure appears when first switch on after
mounting until calibration

9
6. Setting of the soldering bridges
The board „LSG/LSK CPU completely equipped and programmed“ with the item no. 005 7 is
completely identical for LSG and LSK. The firmware recognises according to the upper
soldering bridges whether it is the LSG or LSK. Via the lower soldering bridges the multiplier for
the sensor element is switched.
Instrument
Instrument Instrument
Instrument
Sensor
Sensor Sensor
Sensor
app. sensor resistance
app. sensor resistance app. sensor resistance
app. sensor resistance
in air
in air in air
in air
multiplier
multipliermultiplier
multiplier
LSG
LSGLSG
LSG
SB A
SB A SB A
SB A
5kOhm
5kOhm5kOhm
5kOhm
kOhm
kOhmkOhm
kOhm
LSK
LSKLSK
LSK
SB42A
SB42ASB42A
SB42A
50KOhm
50KOhm 50KOhm
50KOhm
0KOhm
0KOhm 0KOhm
0KOhm
= soldering point
LSG (Sensor SB A)
Gnd
Heater
Sensor
Vcc
SDA
SCL
soldering point for
the LSG

0
LSK ( Sensor SB42A)
Gnd
Heater
Sensor
Vcc
SDA
SCL
Soldering points for the
LSK
7. Testing Bottle
A mixture is made of 40 parts water and one part Ethanol ( Ethanol 652, EG No: 200-578-8 ).
Of this mixture 8 ml will be filled in the cotton of the bottle.
The closing of the bottle has to be closed to the arrester.
The ordering number of this testing bottle is 00237.

8. Software Update LSG
The firmware can be transferred with the Cyclone Pro to the LSG/LSK. The six pin BDM cable
has to be used. The cable can be plugged one to one to the vertical plug J . The energising of
the target hardware is done via the Cyclone Pro. The jumpers have to be set according to the
picture.
yclone Pro Jumper Setting Anschluss BDM Kabel am yclone Pro
The image „LSG-LSK_V0 .sap“ can be transferred directly to the Cyclone Pro and contains all
settings..
When programming t
When programming tWhen programming t
When programming the sensor head may not be populated !
he sensor head may not be populated ! he sensor head may not be populated !
he sensor head may not be populated !
Attention: In case another tool is used the CPU might be set:
Freescale MC9S08LL08. The voltage of 3V has to be selected
. At a setting of 5V the micro controller might be destroyed !
The software version will be shown during switch on.
Version 0 = bar at switch on notice
Version 02 = 2 bar at switch on notice
Example: switch on notice LSG : switch on notice LSK :

2
• 6 pin BDM cable
• The cable is plugged to the vertical plug.
• Press the button menu on the Cyclone Pro
• “Select SAP Image“ and confirm with the button menu
• select requested image and confirm with the button menu
• than press the start button on the Cyclone Pro
• transfer starts
9. Exchange the Sensor unit
The customer and all service department could exchange the sensor unit.
The sensor unit is pre calibrated.
Order number is:
Sensor unit LSG, pre-calibrated– 005 3
Sensor unit LSK, pre-calibrated – 005 4
• turn off the black cap
• release the sensor with board
• put on the new sensor
• turn on the black cap

3
10. Changes at the software version
• With software V0
• New characteristics of the software V02:
Switch On Notice LSG : Switch On Notice LSK :
. Normal Operation
Even after the warm up phase is finished a new zero point is determined cyclical and the
linearization is calculated new when having a positive sensor drift (resistor bigger than to the
end of the warm up phase). By this even small gas concentrations (< 50 ppm) can be detected
safely.
2. Calibration (see point 3. „Change in the software for calibration V02“)
This manual suits for next models
1
Table of contents
Popular Security Sensor manuals by other brands
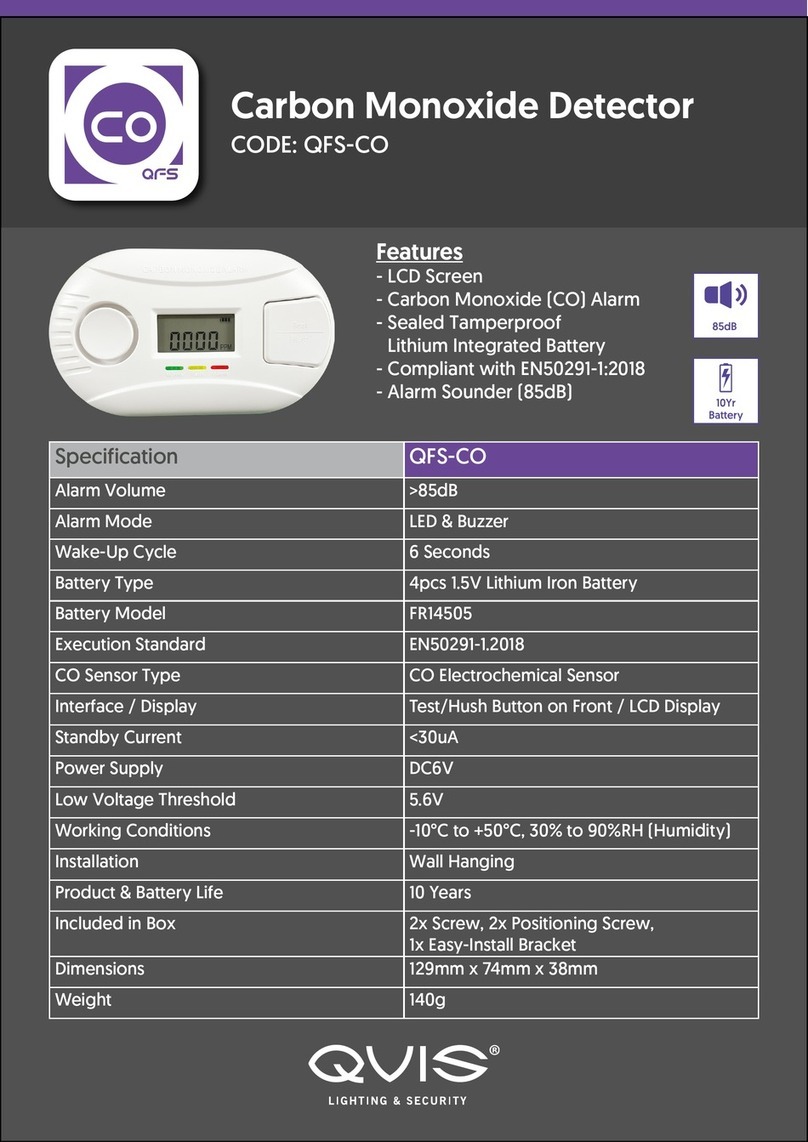
Qvis
Qvis QFS-CO manual
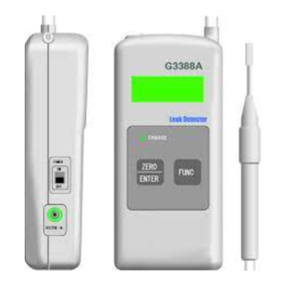
Agilent Technologies
Agilent Technologies G3388A Operation manual
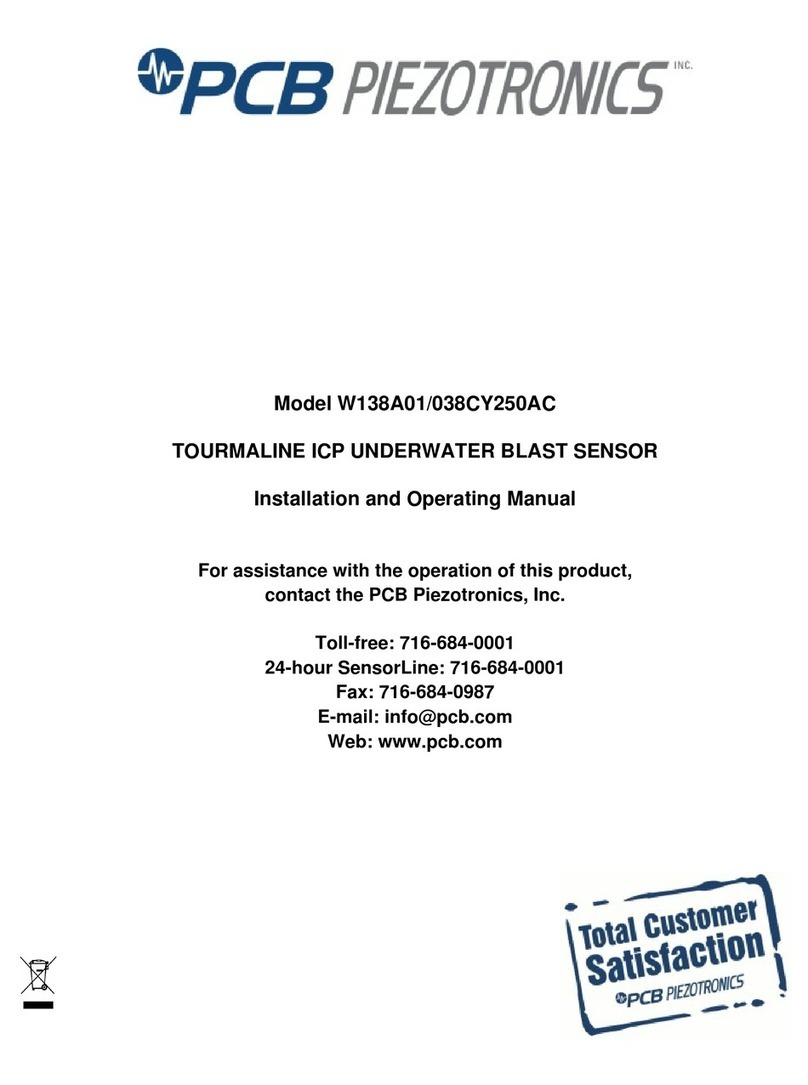
PCB Piezotronics
PCB Piezotronics W138A01/038CY250AC Installation and operating manual
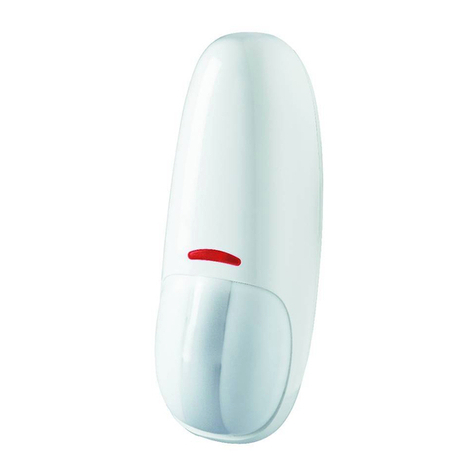
Visonic
Visonic CLIP PG2 installation instructions

Nortech Detection Pty Ltd
Nortech Detection Pty Ltd PD130 Short form User Manual
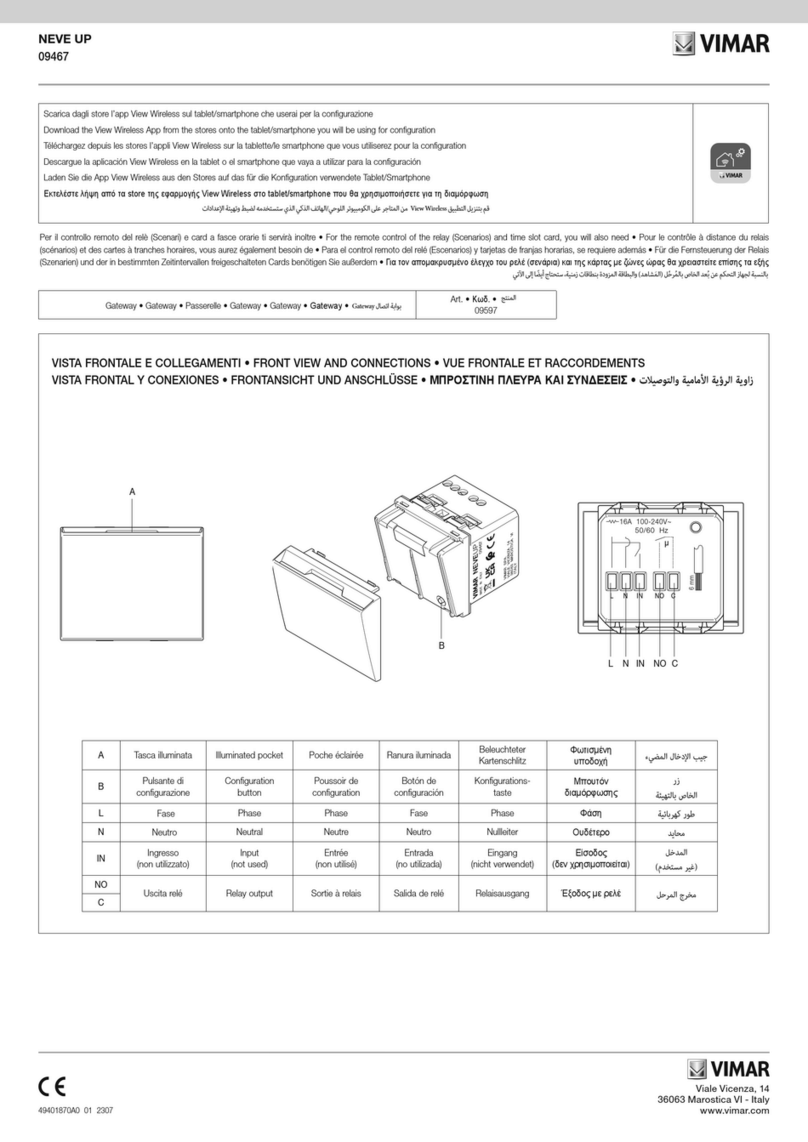
Vimar
Vimar NEVE UP 09467 manual