RDS Sands Delta 3400 Use and care manual

1
Sands Delta 3400
Sprayer Controller
Calibration
RDS Part No.:
Document Issue:
Software Issue:
S/DC/500
-
10
-
60
1.00 : 8/9/08
PS403-000 rev.09

SANDS DELTA 3400 - SPRAYER CONTROLLER
2
Electromagnetic Compatibility (EMC)
This product complies with Council Directive 2004/108/EEC when installed and used in accordance with the
relevant instructions.
IMPORTANT, READ THIS EFORE USING THE INSTRUMENT
The installation is a part of the Precision Farming System ("the System"). It is very important that you follow the
described calibration procedures before operating the instrument. Calibration and operation of the instrument
must be in accordance with these instructions. Use of the System is subject to the following disclaimer;
1. So far as is legally permissible RDS Technology ("RDS"), or its distributors, shall not be liable, whatever the
cause, for any increased costs, loss of profits, business, contracts, income, or anticipate savings or for any
special, indirect or inconsequential damage whatsover (death or personal injury excluded).
2. The capabilities and functions of the Precision Farming System ("the System") are limited as set out in the
specification of the System, details of which are contained in the Help files and product literature and which
must be read before using the System.
3. Without prejudice to the generality of the above it is hereby acknowledged that the System is not designed nor
intended to a) originate variable treatment plans or b) achieve or avoid any application rate outside application
parameters, which in both cases shall be the responsibility of the operator.
4. The standard terms and conditions of RDS (except clause ), a copy of which is available on request, apply to
the supply and operation of this System.
Our policy is one of continuous improvement and the information in this document is subject to change without
notice. Check that the software reference matches that displayed by the instrument.
© Copyright RDS Technology Ltd 2008
\UK60 100.DOC
Service and Technical Support
Sands Agricultural Machinery Ltd
Main Road, Brunstead
Stalham
Norwich
Norfolk
England NR12 9ER
T +44 (0)1692 580522
F +44 (0)1692 583324
Web: www.samltd.co.uk/pages/contact.htm

SANDS DELTA 3400 - SPRAYER CONTROLLER
3
1. INTRODUCTION 5
1.1
Selecting the Control Software ................................................................................................... 5
1.2
The "Setup" Screen page............................................................................................................. 5
Calibration on installation 5
Calibration in normal use 5
1.3
Data Entry .................................................................................................................................... 6
2“SENSOR CONFIGURATION” MENU 7
2.1
Forward Speed Sensor................................................................................................................ 7
2.1.1
Select Sensor Option
2.1.2
Wheel sensor calibration – ‘Autocal’
2.1.3
Wheel sensor calibration - manually calculating the Forward Speed Factor
2.1.4
Radar Sensor 8
2.2
oom configuration .................................................................................................................... 9
2.2.1
Set number of Boom Sections 9
2.2.2
Set No. of Nozzles per section and Nozzle Spacing 9
2.3
Flow / Pressure Sensor Setup..................................................................................................... 10
Configure for Flow-based Regulation ..................................................................................................... 10
2.3.1
Channel 10
2.3.2
Function 10
2.3.3
Sensed Width 10
2.3.4
Flow sensor Cal factor 10
2.3.5
Minimum flow and Maximum flow 11
2.3.6
Start Delay 11
2.3.
Valve Type 11
Configure for Pressure-based Regulation............................................................................................... 11
2.3.8
Function 11
2.3.9
Calibrate Pressure Sensor 12
2.3.10
Damping 12
2.3.11
Selecting the Regulation Mode 12
2.4
Configuring the Control Valve..................................................................................................... 13
2.4.1
Response 13
2.4.2
Minimum Pulse 13
2.4.3
Deadband 13
2.4.4
Startup Delay 13
2.4.5
‘Control’ 13
2.4.6
Maximum Pulse 14
2.5
Configuring a Tank Fill Sensor.................................................................................................... 14
2.5.1
Configuring a Tank Fill Sensor 14
2.6
Alarms Setup ............................................................................................................................... 15
2.6.1
Setting the Alarm thresholds 15
MAX. SPEED and MIN. SPEED 16
MAX. FLOW and MIN. FLOW (Flow-based regulation only) 16
OFF TARGET 16
2.7
Nozzle Setup ............................................................................................................................... 16
2. .1
Editing the preset Nozzle type 16
2.8
Calibrating an RPM Sensor ......................................................................................................... 17
2.8.1
LOW / HIGH RPM ALARM 1

SANDS DELTA 3400 - SPRAYER CONTROLLER
4
3. LIQUID CALI RATION 18
3.1
Initial Calibration - using the "Nozzle Calibration Routine" ........................................................ 18
3.2
Full-Tank Calibration ................................................................................................................... 19
4. TECHNICIAN CONFIGURATION MENU 20
4.1
Display Options ........................................................................................................................... 20
4.1.1
Speed Smoothing Factor 20
4.1.2
Rate Lock-On 20
4.1.3
Rate Smoothing 20
4.2
Control Options ........................................................................................................................... 20
4.2.1
Nudge Step Size 21
4.2.2
Off Target Alarm 21
4.2.3
SPEED RELATED: Options 21
4.3
oom Cutouts / Inputs ................................................................................................................ 21
Master Cutout 21
Boom Inputs 21
Cutout 21
Booms 21
4.4
Print Calibration Data .................................................................................................................. 22
4.5
Ports Setup.................................................................................................................................. 22
4.6
Change PIN for Technician Menu............................................................................................... 22
5. FACTORY CONFIGURATION MENU 23
5.1
Machine Options ......................................................................................................................... 23
“ENGINE DATA” 23
“BOOM HEIGHT” 23
5.2
oom Height Setup ..................................................................................................................... 23
“Safety Timer” 23
“End Stop Limit” 23
“Sensor Calibration” 24
5.3
Total Software Reset ................................................................................................................... 24
5.4
acking Up and Restoring Calibration Data............................................................................... 24
5.5
Change PIN for Factory Configuration Menu ............................................................................. 24
6. USER OPTIONS 25
6.1
Set Time and Date ....................................................................................................................... 25
6.2
Adjust Screen Contrast and rightness...................................................................................... 25
6.3
Set Units ...................................................................................................................................... 25
6.4
Select Language.......................................................................................................................... 26
6.5
Select Control Software .............................................................................................................. 26
7. GENERAL PF SETUP 26
8. THE SETUP MENU 27

SANDS DELTA 3400 - SPRAYER CONTROLLER
5
1. Introduction
The instrument must be calibrated before commencing normal operation. Many settings are made only on
initial installation e.g. from the 'SENSOR CONFIGURATION' screen. Other calibration settings may need to be
altered on a regular basis according to the liquid being sprayed, nozzle types in use etc.
1.1 Selecting the Control Software
With the purchase of an optional "software module" which comes in the form of an electronic chip loaded into
the back of the instrument, the Pro-Series can be instantly switched to perform another function e.g. from a
Sprayer Controller to a Data Logger for route navigation and soil mapping tasks. This is done from "Instrument
Select" in the "USER OPTIONS" menu.
1.2 The "Setup" Screen page
Press the key to select the SETUP menu (fig. 1a).
Figure 1a
Calibration on installation
Work through the 'SENSOR CONFIGURATION' menu first. Most of these settings need be done only once on
installation.
Calibration in normal use
Calibration settings that need to be accessed more frequently are highlighted in bold type on figure 1. These
settings include;
Product calibration
Tank and Product selection
Nozzle type
Speed alarm
Boom configuration
Flow/Pressure Sensor
Control valve
Valve/Actuator
Alarms/Nozzle/RPM
Fwd
Speed
Calibration
Display options
Control options
Boom/Cutout Inputs
Print Cal Data
Ports Setup
Machine Options
Boom Height Setup
Reset Factors
Store Factors
Time/Date
Contrast/Brightness
Units
Language
Instrument Select
Regulation Mode
Select/Calibrate Product
Set Simulated speed
Select ozzle
type
UK60 01A.PCX

SANDS DELTA 3400 - SPRAYER CONTROLLER
6
1.3 Data Entry
Alpha-numeric values are entered via the right-hand keypad. You must press the key from 2 to 5 times to
select the required letter. (Some keys have additional special characters not shown on the key legend).
The key will either toggle between lower and upper case characters or when preceeding a numerical
entry, will set a MINUS value.
The key will toggle between 0 and a SPACE.
The key will BACKSPACE the screen cursor if you need to re-enter a character.
The key is the RETURN key and is normally pressed to confirm the data entry into memory.

SANDS DELTA 3400 - SPRAYER CONTROLLER
2 “Sensor Configuration” Menu
Calibrate the Forward Speed Sensor and Flow / Pressure Sensor before commencing liquid calibration.
2.1 Forward Speed Sensor
2.1.1 Select Sensor Option
1. From the SETUP screen, press to select the "SPEED FACTOR" screen (fig. 1b).
Figure 1b
2. Move the arrow cursor to select the option and press to confirm.
2.1.2 Wheel sensor calibration – ‘Autocal’
If the sprayer has a standard wheel sensor and magnets installed, you can select either of two speed sensor
factors - for flotation tyres and for row crop wheels. Remember to select the appropriate factor after changing
wheels.
The Speed Sensor Factor ("SSF") is the distance travelled forward in the time between two pulses from the
forward speed sensor. This could be calculated based on the nominal tyre diameter or rolling distance and
then entered manually (ref. section 1.1.3), however this does not take into account wheel slip, compaction, or
tyre deformation under practical operating conditions.
The best method is to do an "Auto Cal".
Mark a set distance of 100 metres (or 100 yards depending on the units set on the instrument) by suitable
means. The surface should be representative of the average field conditions (i.e. not a paved surface).
Position the vehicle with the first marker level with a suitable reference point on the vehicle.
With the appropriate sensor option highlighted on the "SPEED FACTOR" page, press ENTER, then select
"Auto Cal'. Press and then follow the screen instructions.
Stop the vehicle when the second marker lines up with the pre-determined reference point on the vehicle and
press to end the "Auto Cal" procedure. The Speed Sensor Factor is automatically re-calculated and
stored in memory.
NOTE: If you overrun the mar er, do not simply reverse - repeat the "Auto Cal" procedure from the beginning.
2.1.3 Wheel sensor calibration - manually calculating the Forward Speed Factor
The smaller the speed sensor factor the better the speed update will be. Aim for a factor less than 2.000 m
( 8. 8").
NOTE: Perform the following calculations in inches or metres depending on whether the instrument is set for Imperial
or Metric units. If you calculate the factor using any other unit of measurement e.g. feet or centimetres, the
forward speed display will be incorrect.
(i) If a single magnet is installed (as with a standard RDS Propshaft Sensor kit), the distance travelled for
each turn of the prop shaft must be determined. To determine this distance, drive the vehicle forwards for
exactly 10 revolutions of the prop shaft. Measure this distance (in inches or metres) and divide by 10, to find
the Speed Sensor Factor.
Wheel Sensor - for flotation tyres
Wheel Sensor - for (larger) row crop wheels
Radar Sensor / RDS ‘Satspeed’ Interface
UK60 01B.PCX

SANDS DELTA 3400 - SPRAYER CONTROLLER
8
(ii) If 2 magnets are installed (as with a standard RDS Wheel Sensor kit), the distance is 1/2 the effective rolling
circumference of the wheel. To determine this circumference, drive the vehicle forward in field conditions (with
the implement attached if applicable), for exactly 10 revolutions of the sensed wheel. Measure this distance (in
inches or metres) and divide by 20 to find the Speed Sensor Factor.
(iii) If 4 wheel magnets are installed, the distance is 1/4 the effective rolling circumference of the wheel. To
determine this circumference, drive the vehicle forward in field conditions (with the implement attached if
applicable), for exactly 10 revolutions of the sensed wheel. Measure this distance (metres) and divide by 40 to
find the Speed Sensor Factor.
Carry out this test whenever soil conditions or wheel sizes change.
If the calibration factor works out at over 2.000 m ( 8. 8 inches), consider fitting additional magnets. Extra
magnets are recommended if the vehicle has large diameter wheels or is slow-moving. In extreme
circumstances you can find that the speed keeps going to zero as it times out before the next pulse arrives.
Number of magnets required
The table gives the number of magnets required to enable a speed update of approximately 1 Hz or greater on
the display.
Typical speed in normal operation:
Tyre diameter up to 5mph
(8km/hr)
6 to 9 mph
(9 to 15 km/hr)
10mph (16 km/hr)
or over
12" (0.3m) 1 1 1
24" (0.6m) 1 1 1
36" (0.9m) 2 2 1
48" (1.2m) 4 2 2
60" (1.5m) 4 4 2
2" (1.8m) 4 4 2
Example Calculation
A vehicle is fitted with a single magnet mounted on the propshaft. The measured distance for 10 rotations of
the sensed wheel is 4 '-6".
1. Convert the distance to inches :- (4 ' x 12")+6" = 5 0"
2. Divide by 10 (magnet pulses) to give the calibration factor:- 5 0" / 10 = 5 .0"
3. Programme the factor '05 .0' as described overleaf.
2.1.4 Radar Sensor
If an RDS Mk3 Radar sensor is installed at the correct angle of 45 ±1°, the Speed Sensor Factor is 0.0078 m
(or 0.312 inches). It is still recommended to do an ‘Autocal’ since the sensor may not be mounted exactly at
3 °.

SANDS DELTA 3400 - SPRAYER CONTROLLER
9
2.2 oom configuration
2.2.1 Set number of oom Sections
Range: 0 - 9 Default: 4
With the screen cursor opposite "BOOM SECTIONS", enter the
number of sections from 0 to 9 and press the ENTER button.
When a boom section is switched on, the boom section block is
filled in.
If boom sections are set to zero, then the whole boom is seen as
one unit. The boom section inputs are ignored and the full
spraying width is programmed.
2.2.2 Set No. of Nozzles per section and Nozzle Spacing
Switch on each section in turn and programme the number of nozzles and nozzle spacing for that section.
Figure 4 Setting number of nozzles per section and nozzle spacing
1.
Sensor Configuration
1.
Width Setup
1.
Sensor Configuration
Section Switch On
1.
Width Setup
UK60
-
04.PCX
UK60
-
03.PCX
UK60
-
02.PCX
Figure 2
Figure 3
Figure 4

SANDS DELTA 3400 - SPRAYER CONTROLLER
10
2.3 Flow / Pressure Sensor Setup
The sprayer control system is normally installed with both a flow sensor and a pressure sensor, and is set up
for pressure-based regulation. The flow sensor provides a ‘true’ flow rate display compared to the calculated
flow rate from the pressure sensor.
You can re-configure the system at any time from the SETUP page for either type of regulation (section
2.3.11).
In either case the one sensor is set for regulation and the second sensor is set either to provide information
only (flow rate or pressure display), or can be disabled.
Do the Flow / Pressure Sensor Setup before doing the liquid calibration.
Configure for Flow-based Regulation
NOTE: Do the Flow sensor setup before doing the liquid calibration.
2.3.1 Channel
Select between channel 1 for the spray line flow sensor and channel 4 (‘FILLING’- for calibrating an optional
tank fill flow sensor, see section 2.3.8).
2.3.2 Function
"NOT USED" Default setting (for a system where pressure-based only regulation is required).
"REGULATION" Enables flow-based regulation.
"INFO ONLY" Enables the flow rate display when the instrument is in pressure-based regulation mode.
2.3.3 Sensed Width
The total width of the boom sections, to which liquid is delivered via the flow sensor. This is normally the full
boom width but in some installations, for practical reasons, it may be a single boom section.
Default: 24.0 metres
2.3.4 Flow sensor Cal factor
The factor (pulses per litre or pulses per gallon) as given below, according to the size of turbine installed.
Turbine size pulses/litre pulses/Imperial gallon pulses/US gallon
1/2" 3 00 - -
3/4" 1 86 8119 6 60
1" 650.0 2955 2460
1-1/2" 165.0 49.1 624.5
2" 100.0 454.6 3 8.5
These values will be sufficient until you do a liquid calibration by means of a jug test.
NOTE: The Cal Factor will be automatically re-calculated and stored in memory after doing a flow calibration or nozzle
calibration routine. It can otherwise be changed manually following "fine tuning" of the nozzle rate. Default
setting: 650 pulses/litre for a 1" turbine
1.
Sensor Configuration
2.
Flow Sensor
Uk60
-
06.PCX
Figure 5

SANDS DELTA 3400 - SPRAYER CONTROLLER
11
2.3.5 Minimum flow and Maximum flow
Set the values according to the size of turbine fitted.
Turbine size Min. flow (l / min) Max. flow (l / min)
1/2" 3 30
3/4" 3 30
1" 10 100
1-1/4" 10 100
1-1/2" 35 350
2" 2 1100
These values set the threshold for the "FLOW LOW" and "FLOW HIGH" alarms during operation. Minimum and
maximum flow can also be set from the "ALARMS SETUP" screen. Set the maximum and minimum flow for the
sensor in use.
Default: Min. flow = 10 l/min Max. flow = 200 l/min
2.3.6 Start Delay
When the whole boom or any boom section is switched on, there may be a rush of air or liquid as the boom
line fills up which is not true flow out to ground. Flow accumulation will be ignored for this delay time
(programmable from 0 - 20 seconds) after the boom is switched on. The flow should stop immediately the
boom is switched off.
Default = 0 sec
2.3.7 Valve Type
If each boom section valve when closed, simply shuts off the flow (e.g. solenoid valves), set to "n" for a non-
recirculating system.
If each boom section valve when closed, diverts the flow back to tank (e.g. ARAG, Spray Systems valves), set
to "r" for a re-circulating 'balanced return' system.
Default: "r"
Configure for Pressure-based Regulation
NOTE: Do the Pressure sensor setup before doing the liquid calibration.
2.3.8 Function
"REGULATION" (Default setting) Enables pressure-based regulation.
"INFO ONLY" Enables the pressure display when the instrument is in flow-based regulation mode.
"NOT USED" For a system where flow-based only regulation is required.
1.
Sensor Configuration
3.
Pressure Sensor
UK60 0 B.PCX
Figure 6

SANDS DELTA 3400 - SPRAYER CONTROLLER
12
2.3.9 Calibrate Pressure Sensor
Figure 7a / 7b Calibrating the Pressure Sensor
1. Select "CALIBRATION ROUTINE" (fig. 6) and press .
2. Depressurize the manifold and press to set "PRESSURE ZERO" (fig. a).
3. Start the sprayer and set the reference pressure (the typical working pressure) using the keys (fig.
b).
4. Key-in the pressure indicated on the sprayer pressure gauge and press .
The "PRESSURE GAIN" is then set and is displayed on the "PRESSURE SENSOR" screen (fig. 6). The pressure
sensor is now calibrated ready for nozzle calibration.
2.3.10 Damping
The damping factor enables fluctuations in the pressure readings to be smoothed out. By default the damping
factor is zero.
2.3.11 Selecting the Regulation Mode
From the SETUP screen, press the button (this only appears on the SETUP screen when both sensors
are enabled).
Flow-based systems requiring high application rates for liquid fertiliser application, require a large flow sensor
to be installed. However, this turbine may not be as accurate at lower application rates required for chemical
applications. Where a large turbine is fitted, it is advantageous to use pressure-based regulation when the
flow rate drops below the programmed minimum flow rate of the flow sensor.
Figure 8 Switching between flow-based and pressure-based regulation
Select "Pressure" or "Flow" using the up / down arrow keys and press to confirm.
UK60 08B.PCX
UK60 98A.PCX
Uk60
-
05.PCX
Uk60 01A.PCX

SANDS DELTA 3400 - SPRAYER CONTROLLER
13
2.4 Configuring the Control Valve
2.4.1 Response
The Response function sets the frequency at which the system adjusts the control valve when reacting to a
change in forward speed. A lower setting results in a slower response, and increases the time taken for the
application rate to match the target rate. A higher setting results in a faster response. If the application rate is
unstable and varies about the target rate, then the response setting may be too high.
Default: 50 Range: 0 - 9999
2.4.2 Minimum Pulse
This sets the minimum pulse length (milliseconds x 4) driving the flow control valve. The pulses becomes
shorter as the application rate nears the target rate. A lower setting gives shorter pulses - too short and the
flow rate may not change sufficiently. If the pulse is too long, the system may be unstable about the target
rate.
Default: 4.0 (16 ms) Range:0 - 9999
2.4.3 Deadband
The Deadband function sets the range over which the flow rate will vary about the target rate before the control
valve will respond. A lower value will make the control respond to a smaller variation in flow and vice versa. If
the value is too low the system may be unstable about the target rate.
Default: 2.0 Range: 0 - 99.9
2.4.4 Startup Delay
If a spray boom is empty of liquid, the flow into it is rapid until it pressurises. The flow rate then reduces to the
correct flow rate. Consequently the system takes some time to stabilise at the target rate. The instrument must
be stopped from reacting to the initial flow surge.
Set the delay time to equal the time it takes for the sprayer system to reach normal working pressure. When
the whole boom or individual section is switched on, the control valve will not operate for this time period.
Default: 2.0 seconds Range: 0 - 99.5 seconds
NOTE: The power supply to the control valve is switched off when switching off the boom. Therefore, when the sprayer
is switched on at the beginning of the next bout, the control valve will be in the correct position enabling a faster
return to the target rate.
2.4.5 ‘Control’
"WORK REG'" - Auto-regulation is only enabled when the boom is switched on.
The power supply to the control valve is switched off when switching off the boom. Therefore, when the
sprayer is switched on at the beginning of the next bout, the control valve will be in the correct position
enabling a faster return to the target rate.
"CONT' REG'" - Auto-regulation is always enabled.
The control valve remains powered when the sprayer is switched off and will therefore close in response.
Default:: "WORK' REG'"
1.
Sensor Configuration
5.
Valve/Actuator
UK60
-
09.PCX
Figure 9a

SANDS DELTA 3400 - SPRAYER CONTROLLER
14
2.4.6 Maximum Pulse
This sets the maximum pulse length (milliseconds x 4) driving the flow control valve. Do not change this value
from the default of 200.0 (800 ms).
2.5 Configuring a Tank Fill Sensor
A tank-fill sensor is optional. If fitted then proceed with calibration as follows,
2.5.1 Configuring a Tank Fill Sensor
With the cursor on ‘CHANNEL’, select ‘ FILLING’.
1. Initially set the calibration factor according to the size of turbine installed.
Default: 650 pulses/litre (for a 1" turbine).
2. Select the "INFO" screen and press to access the TANK FILL screen.
3. Set the " OW" volume to zero.
4. Fill the empty tank with the known volume (e.g. 2000 litres) of water via the inflow sensor and note the "NOW"
volume displayed.
The correct Cal. factor = Initial Factor x "NOW" volume
Actual volume
e.g. Initial Cal. Factor = 100 and the " OW" volume reads 1 50 litres after filling 2000 litres;
New Cal. Factor = 100 x (1 50/2000) = 8 .5
5. Go back to the "FLOW SENSOR" screen, key-in the new Cal. Factor and press .
1.
Sensor Configuration
2.
Flow Sensor
UK60 0 A.PCX
Figure 9b

SANDS DELTA 3400 - SPRAYER CONTROLLER
15
2.6 Alarms Setup
There are a number of alarms, most being programmable by the operator. Note that setting alarm limits to
zero will disable that alarm function.
Application Rate ‘U DER APPLICATIO ’
‘OVER APPLICATIO ’
This alarm is based on % variance from the target rate.
It therefore alerts the operator to speed up or slow down
until the alarm condition is cancelled.
The limits can be set by the operator on the ‘Alarms
Setup’ screen in the SETUP menu. The default limits
are ±20% of the target rate.
The following alarms can also be configured if so desired, but would normally be overridden by the
application rate alarm if set (except for RPM alarm). The limits must be set in respect of flow sensor capacity
/ spray performance.
Forward Speed ‘FORWARD SPEED
LOW’
‘FORWARD SPEED
HIGH’
The limits can be set by the operator on the ‘Alarms
Setup’ screen in the SETUP menu.
Flow Rate
(Alarm effective in
flow-based regulation
mode only)
‘FLOW LOW 1’
‘FLOW HIGH 1’
The limits can be set by the operator on the ‘Alarms
Setup’ screen in the SETUP menu.
They must be set correctly to suit the size of flow sensor
fitted, and to ensure that the system switches properly
between flow-based regulation and pressure-based
regulation, if the instrument is operating in the ‘AUTO’
regulation mode.
NOTE: These limits are also displayed on the ‘Flow
Sensor’ setup screen in the SETUP menu.
Pressure
(Alarm effective in
pressure-based
regulation mode only)
‘PRESSURE LOW’
‘PRESSURE HIGH’
The limits are those calculated and displayed on the
nozzle wizard screen. They are not programmable by
the operator.
RPM ‘RPM LOW’
‘RPM HIGH’
The limits can be set by the operator on the ‘RPM
Setup’ screen in the SETUP menu.
'FLOW HIGH 1' may be caused by the control valve being unable to dump sufficient flow back to the sprayer
tank as a result of:- speed too slow or stationary, too small or too few nozzles in use - sections off or blocked
nozzles, pump capacity too large or control valve too small.
'FLOW LOW 1' may be caused by:- forward speed too high, insufficient pump capacity, low pump speed, low
or empty tank, blocked filters or incorrect jets.
2.6.1 Setting the Alarm thresholds
1. Press to select the "SETUP" menu.
2. Select the "ALARMS SETUP" screen (fig.10).
1.
Sensor Configuration
6.
Alarms Setup
UK60
-
10.PCX
Figure 10

SANDS DELTA 3400 - SPRAYER CONTROLLER
16
MAX. SPEED and MIN. SPEED
These values set the thresholds for the forward speed alarms. They are automatically set according to the
Target Speed on the "Nozzle Setup" screen, however, you can manually key-in another value via the alpha-
numeric keypad.
When another nozzle type is selected via the "Nozzle Setup" screen, any manually programmed thresholds will
be overwritten.
Default = 0 (Alarms Off)
MAX. FLOW and MIN. FLOW (Flow-based regulation only)
These values set the thresholds for the "FLOW HIGH" and "FLOW LOW" alarms during operation. Minimum
and maximum flow can also be set from the "FLOW SENSOR" screen. Set the values according to the size of
turbine fitted (ref. section 1.4.4).
Default: Min. flow = 10 l/min Max. flow = 200 l/min
OFF TARGET
This sets the threshold at which the instrument will alarm "UNDER APPLICATION" or "OVER APPLICATION"
when spraying in automatic control mode. It is set as a percentage either side of the current target rate.
Default = ± 20%
2.7 Nozzle Setup
Figure 11: The Nozzle Setup screen
NOTE: The Nozzle Setup is also accessed by pressing the ey directly from the "SETUP" screen.
The instrument is pre-programmed with nozzle data for 8 ISO standard nozzle types.
Press to select a nozzle type. Press repeatedly to cycle through nozzle types A to H. Press to
confirm the nozzle selection.
Press to start the nozzle calibration procedure (see section 3).
2.7.1 Editing the preset Nozzle type
If the nozzles fitted do not correspond to any of the 8
preset types, then you can easily edit the data for
any of the nozzle types A to H.
Press to select the "NOZZLE EDIT"
screen (fig. 12). For all parameters, move the cursor
to the appropriate line and enter the new data via the
alpha-numeric keypad.
1.
Sensor Configuration
7.
Nozzle Setup
UK60 10B.PCX
Uk60 11B.PCX
Figure 12:
Editing preset nozzle data

SANDS DELTA 3400 - SPRAYER CONTROLLER
1
2.8 Calibrating an RPM Sensor
The following calibration procedure applies regardless of the speed output being sensed e.g. Engine RPM,
PTO Speed, Shaft Speed, Fan Speed etc, depending on the particular installation.
In all cases, run the sensed component at a known speed. If necessary measure this speed using a hand-held
tachometer. Note the speed displayed on the "INFO" screen.
The correct Cal. factor = Initial Factor x Displayed Speed
Actual Speed
Go back to the "RPM SETUP" screen, key-in the new Cal. Factor and press .
Default: 1 pulse per rev (PPR)
2.8.1 LOW / HIGH RPM ALARM
From the RPM SETUP screen, you can also set a minimum and maximum RPM at which an alarm is triggered.
Set as necessary.
Default = 0 (Alarms Off)
1.
S
ensor Configuration
8.
RPM Setup
UK5 2
-
11.PCX
Figure 13

SANDS DELTA 3400 - SPRAYER CONTROLLER
18
3. Liquid calibration
It is important to ensure that the flow / pressure sensors have been properly configured before doing a liquid
calibration.
NOTE: Liquid calibration is always done with water. When spraying denser liquids such as liquid fertilizers, after doing
the jug test you should programme the correct density for that product, from the "PRODUCT SELECTION"
screen (section 2.5.1- Operation).
3.1 Initial Calibration - using the "Nozzle Calibration Routine"
The following procedure applies for both pressure-based and flow-based regulation.
1. First set the desired target speed and target rate (ref. section 2.2 - Operation).
2. Then select the most suitable nozzles using the ‘Nozzle Setup” screen (ref. section 2.3 - Operation).
3. From the ‘Nozzle Setup’ screen, first select the appropriate spray line, then press . The current
calibration speed is displayed.
4. Change the calibration speed if desired, from that displayed and press to accept. The adjusted
speed is used for calibration only and will not change the target speed set. The "CAL TEST" screen is then
displayed. It flashes "CAL" to indicate that speed is being simulated, and gives the message "TURN ON NOW"
(fig. 15).
5. Switch the sprayer on. It is better the calibration test is carried out with the full boom spraying, as this
reproduces the field conditions and any pressure drops across the system.
6. When a boom section is switched on, the "CAL TEST" screen appears. All parameters will display ’- - - -.’ Until
the control system has stabilized. The screen then displays the calculated application rate and individual
nozzle flow rate. If a pressure sensor is fitted, the pressure is also displayed (fig. 16).
Figure 14 Nozzle calibration routine Figure 15
Figure 16 Figure 17
When a steady state is achieved, carry out the jug test by collecting a quantity of water from a single nozzle,
and record the collection time
. Press the ‘STOP’ key to end the metering period.
8. Enter the actual time the jug was under the nozzle (default = 60 sec) and press .
9. Enter the test volume (or averaged test volume – see note 1) and press .
The instrument then calculates and displays the new calibration factors (fig. 18). If you can have both a flow
sensor and pressure sensor enabled, you will see both:-
- NOZZLE FLOW RATE in litres/min/nozzle ("REF' FLOW" on the nozzle data page) for pressure-based
regulation.
UK60
-
014.PCX
UK60
-
16.PCX
UK60
-
15.PCX
UK60
-
1 .PCX

SANDS DELTA 3400 - SPRAYER CONTROLLER
19
- FLOW SENSOR CALIBRATION FACTOR in pulses per litre for flow-based regulation.
Figure 18 Flow Calibration Factors
NOTE 1 It is advisable to repeat the jug test for several nozzles across the boom and enter the average of the individual
test volumes.
10. Press to accept the settings, (or first enter revised figures e.g. the averaged flow rate over a number
of jug tests).
If you don’t want to accept the calculated result, press ESC to return to the “Nozzle Setup” screen.
NOTE 2 Performing the jug test changes the previous nozzle flow rate ("REF FLOW") figure stored in the "Nozzle Setup",
and will also correct the calibration factor for the flow turbine.
The jug test is not the most accurate method of calibration particularly for the flow turbine on flow-regulated
systems, as the test volume is relatively small. It is therefore recommended to subsequently perform a full-tan
calibration, spraying a full tan out in the field.
3.2 Full-Tank Calibration
The calibration figure should be subsequently "fine-tuned" after spraying out a full tank in the field. Be certain
of the volume sprayed out since the sprayer sight gauge may not be accurate enough for calibration
purposes. The liquid calibration should be checked and adjusted regularly over the season to compensate for
factors including nozzle wear.
1. From the SETUP page press to select the "PRODUCT SELECTION" page.
2. If you are spraying clean water or chemicals, check that the product (default name = "Spray A") has density
set to 1.00. If spraying liquid fertiliser, check the product and density is selected and programmed.
3. Select the "INFO" screen and reset the "PART TOTAL" to zero.
4. Spray out the whole tank then select the "INFO" screen and note the "PART TOTAL" clocked.
5. Compare this with the known volume sprayed out. If there is a difference between the two figures, then correct
the error via the CAL NUDGE screen as follows:
6. Go back to the "PRODUCT SELECTION" page, select "PRODUCT CALIBRATION" and press (fig.
19).
. Select "CAL NUDGE" and press .
Figure 19 Nudging the cal factors Figure 20 Figure 21
8. Enter the instrument total ( ) and press , then the known volume sprayed out ( ), and
press . Finally, press again to confirm the nudge
The calibration factors are then adjusted accordingly.
UK60
-
18.PCX
UK60
-
19.PCX
UK60
-
20.PCX
UK60
-
21.PCX

SANDS DELTA 3400 - SPRAYER CONTROLLER
20
4. Technician Configuration Menu
The operator is unlikely to need access in normal use. Access to this menu can be restricted by changing the
PIN number from within the menu.
Enter the factory default PIN number 1234 to access the menu.
4.1 Display Options
Figure 22 "Display Options" page
4.1.1 Speed Smoothing Factor
The Forward Speed display is electronically damped. If the readouts are constantly changing by small
increments, you can increase the damping time to give a steadier readout.
Adjustable from 0 to 19 seconds. Default = 2 seconds
4.1.2 Rate Lock-On
"RATE LOCK-ON" sets the % by which the application rate fluctuates either side of a nominal application rate
before the instrument display changes.
For example, if your actual application rate fluctuates in normal operation from 9 to 103 l/ha for a target
application rate of 100 l/ha, you may decide that it is acceptable for the instrument to display a steady readout
of 100 l/ha between those limits i.e. ±3%. In this case the rate lock-on figure should be set to 3.0.
Adjustable from 0 to 50% Default = 2%
4.1.3 Rate Smoothing
The Application rate display is electronically damped. If the readouts are constantly changing by small
increments, you can increase the damping time to give a steadier readout.
Adjustable from 0 to 19 seconds. Default = 4 seconds
4.2 Control Options
Figure 23 "Control Options" page
2.
Technician Config.
1.
Display Options
UK60
-
22.PCX
2.
Technician Config.
2.
Control Options
UK5 2
-
13.PCX
Table of contents
Other RDS Controllers manuals
Popular Controllers manuals by other brands
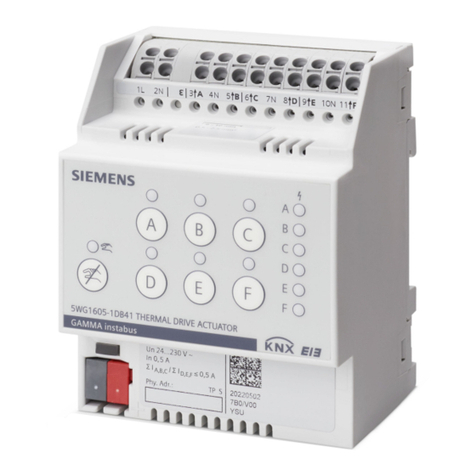
Siemens
Siemens N 605D41 manual
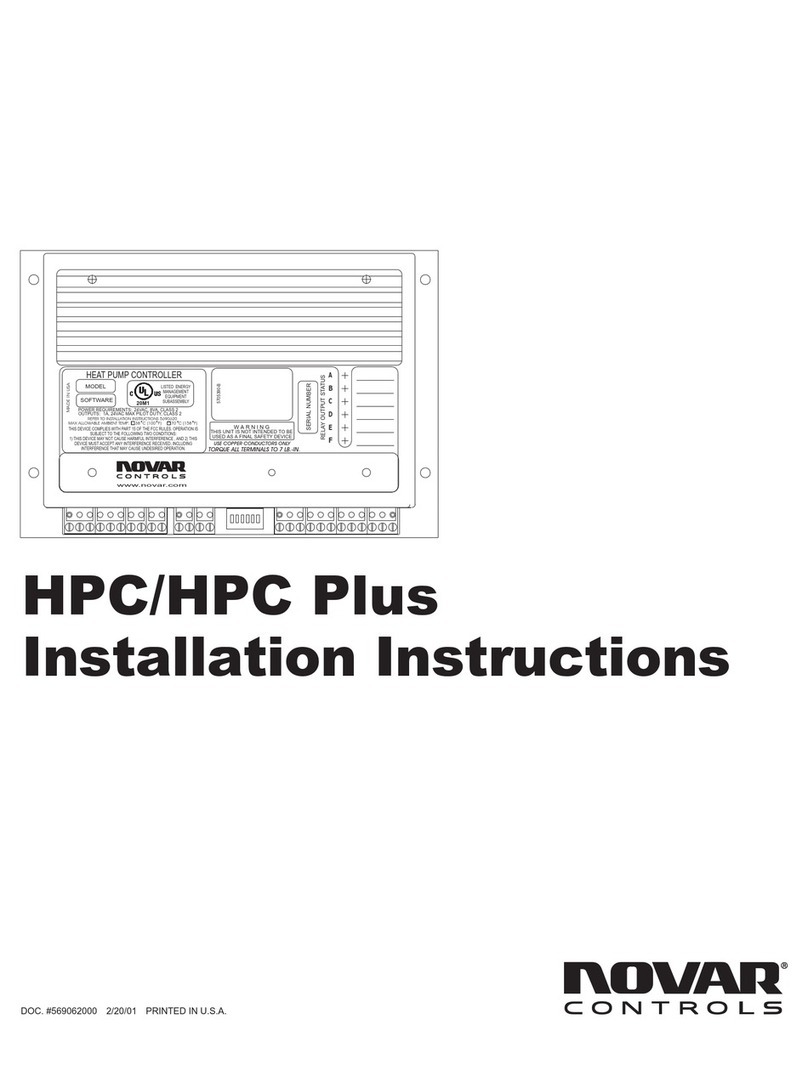
Novar
Novar HPC installation instructions
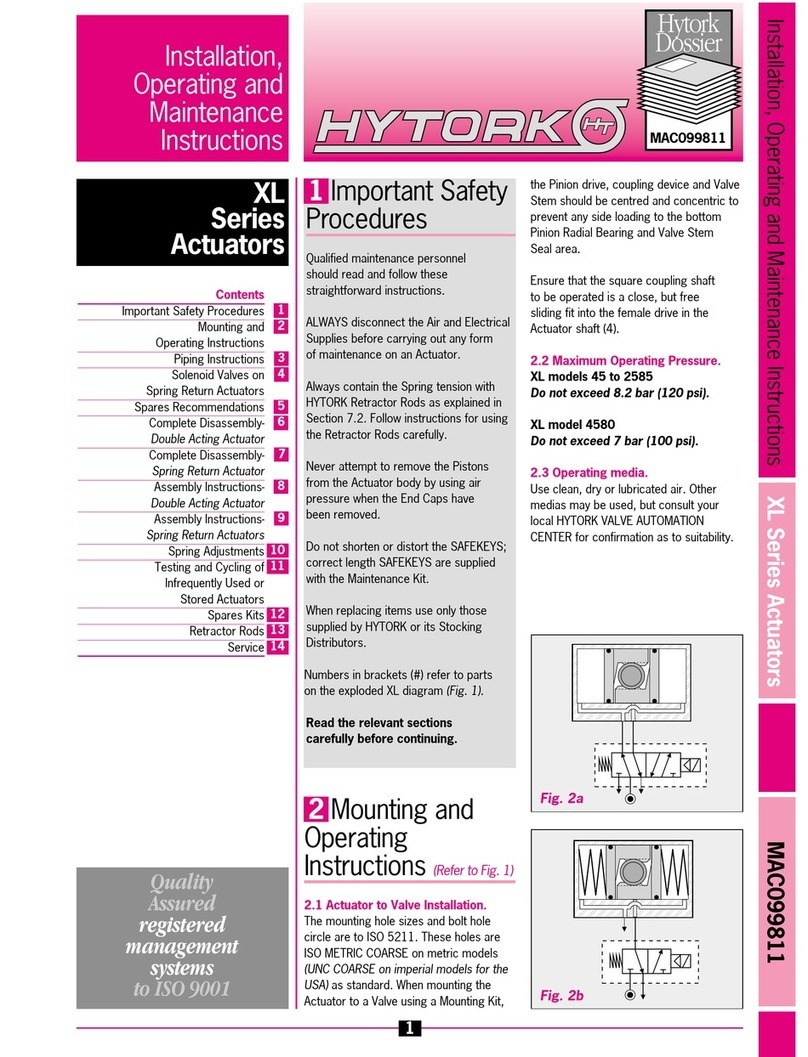
Hytork Dossier
Hytork Dossier XL 45 Installation, operating and maintenance instructions
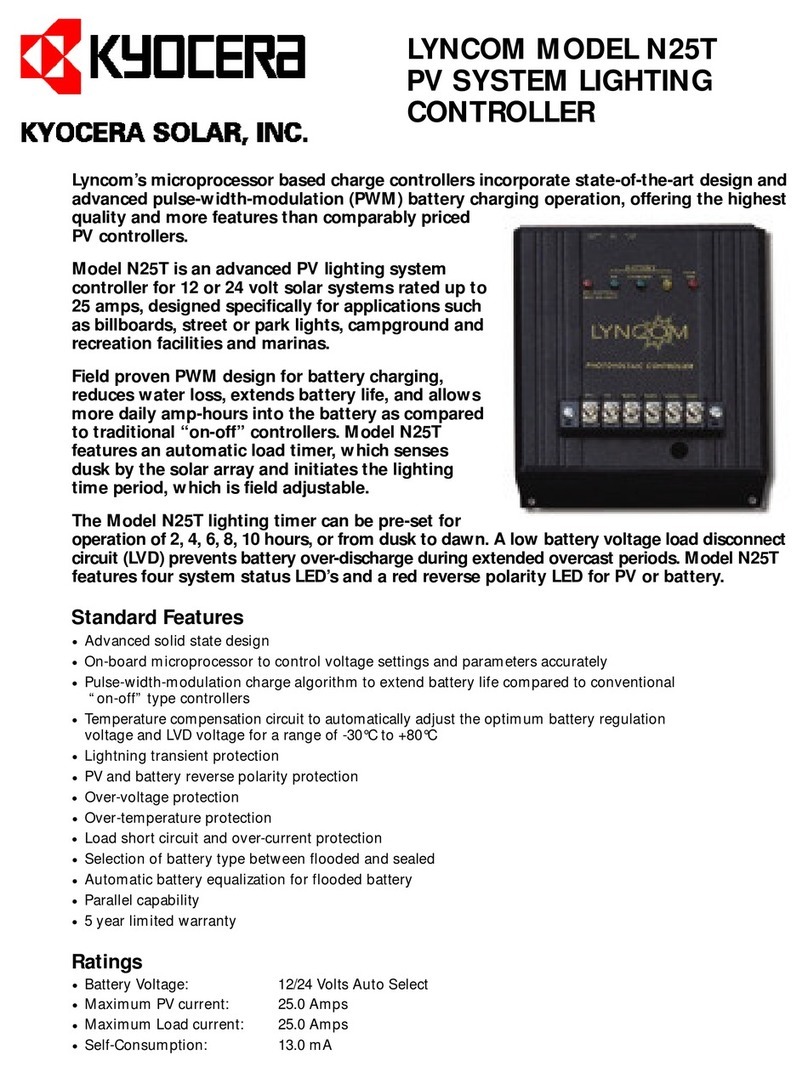
Kyocera
Kyocera LYNCOM N25T datasheet
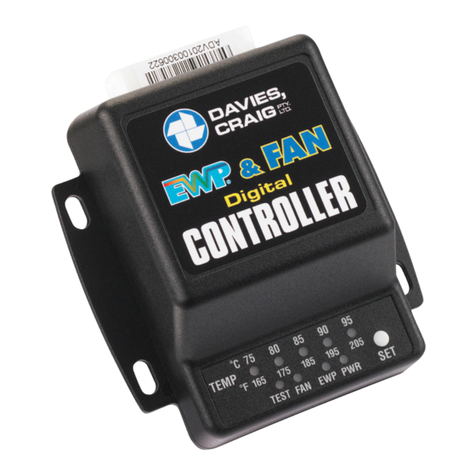
Davies Craig
Davies Craig EWP-FAN installation instructions
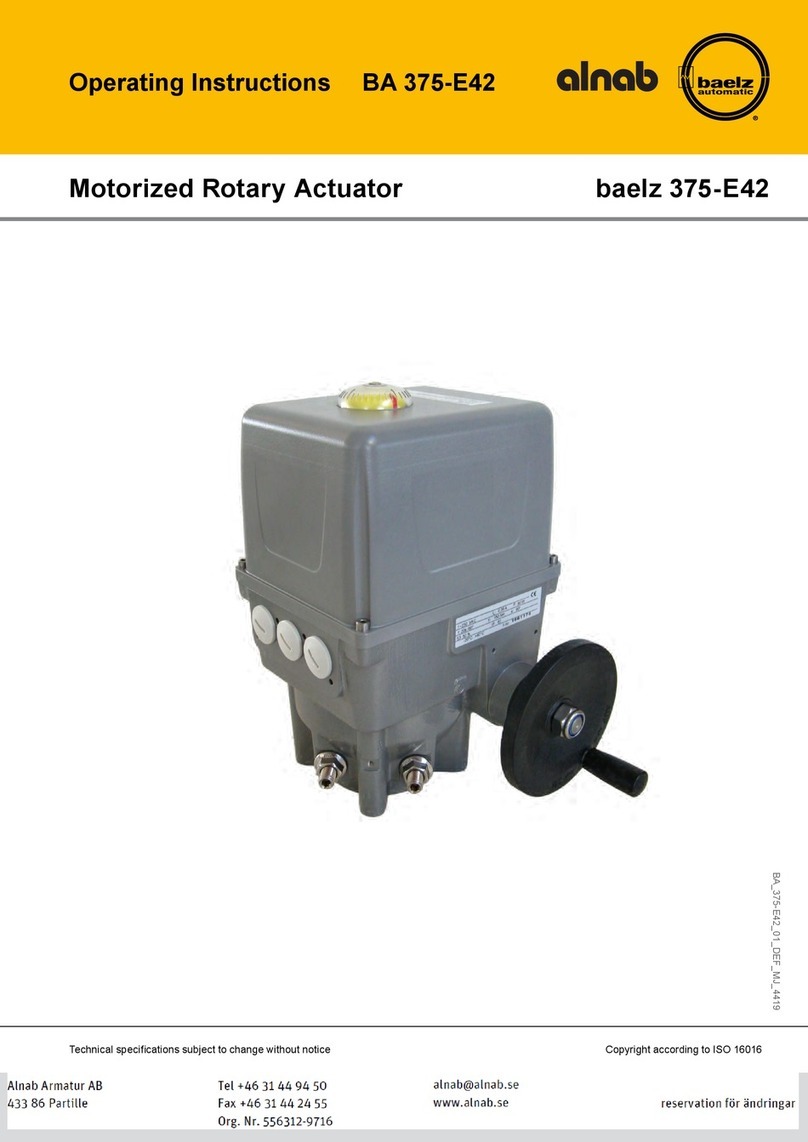
Baelz Automatic
Baelz Automatic BA 375-E42 operating instructions
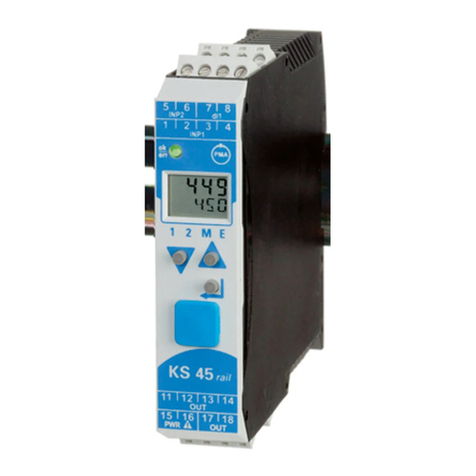
PMA
PMA KS 45 manual
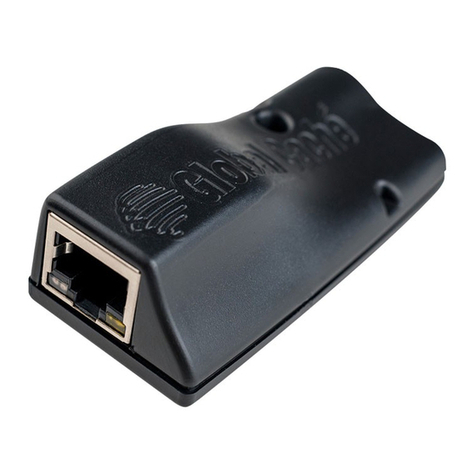
Global Cache
Global Cache iTach Flex IP quick start
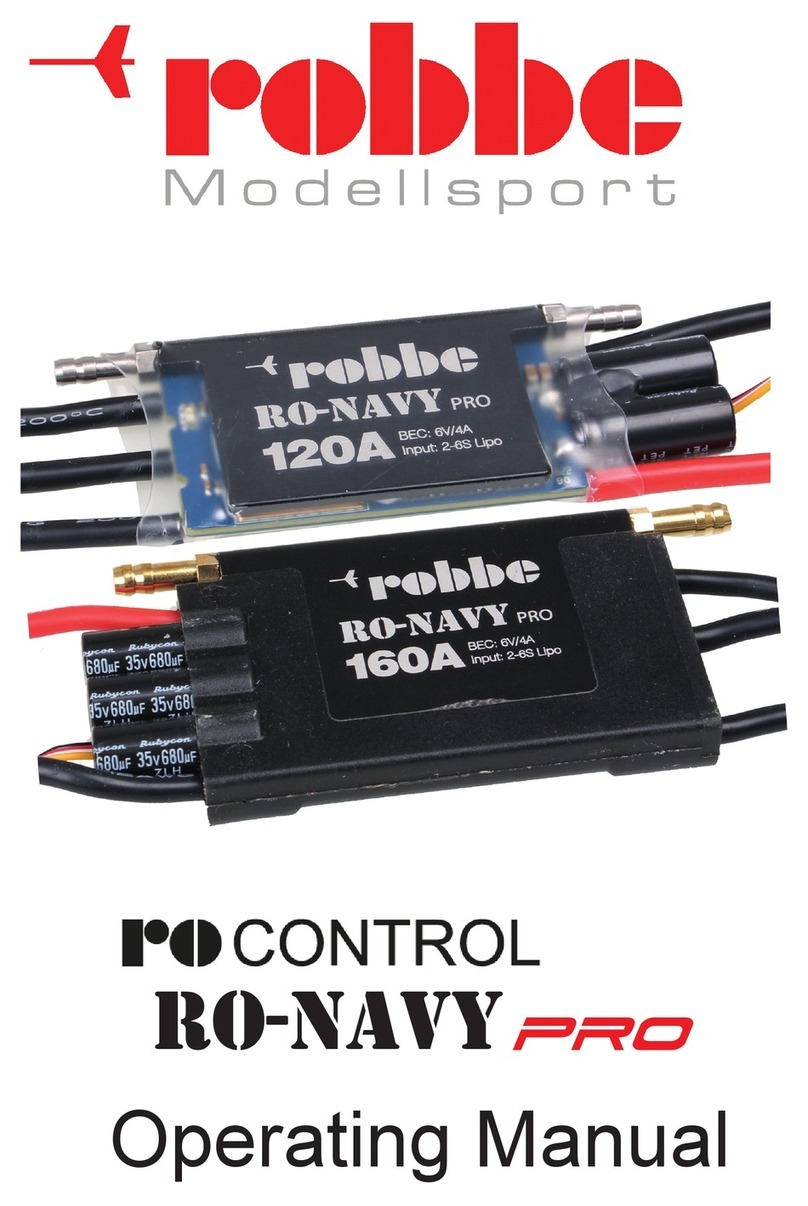
ROBBE
ROBBE RO-Control NAVY Pro Series operating manual
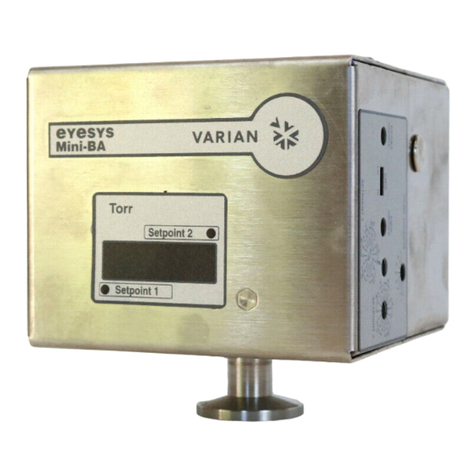
Agilent Technologies
Agilent Technologies Eyesys Mini-B/A instruction manual
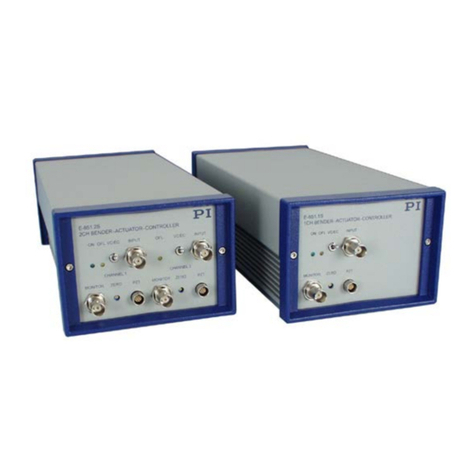
PI
PI E-651.1S operating manual
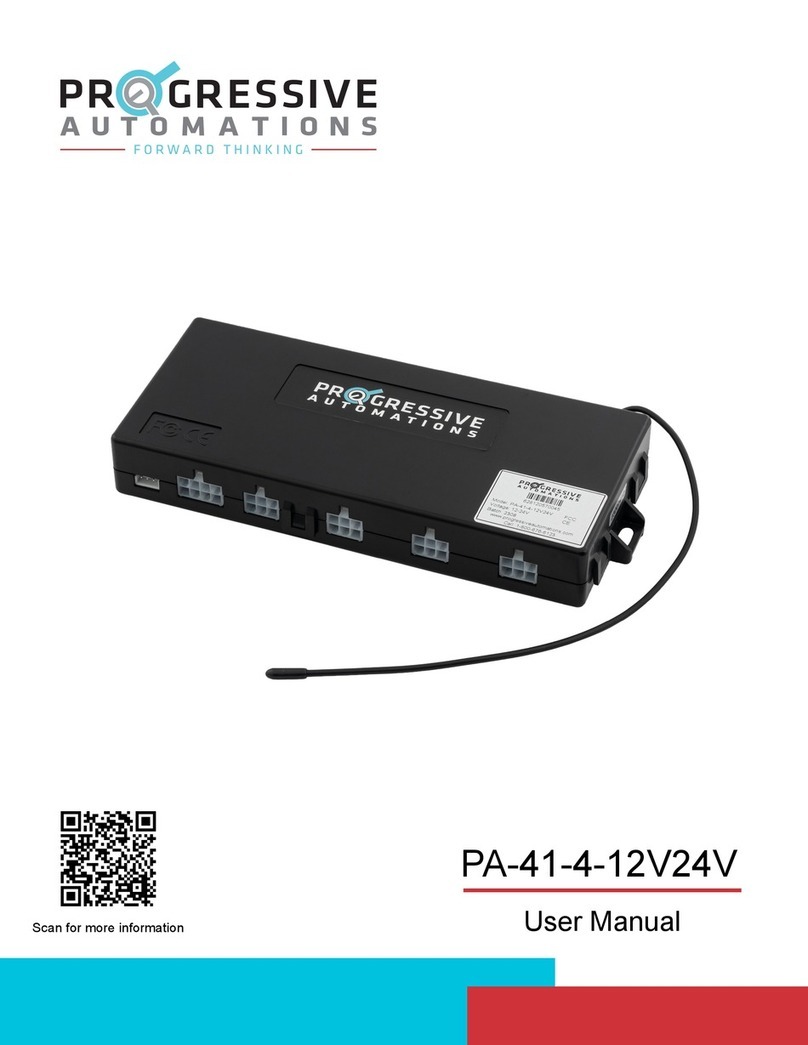
progressive automations
progressive automations PA-41-4-12V24V user manual