Ridder RW Series User manual

265003EN - 2021.12 - V01
Original product-manual
Ridder Motor Gearboxes RW 3-phase
Product Manual
Lorentzstraat 32
3846 AX Harderwijk
PO Box 360
3840 AJ Harderwijk
the Netherlands
T+31 (0)341 416 854
F+31 (0)341 416 611
Iridder.com
Einfo@ridder.com
Ridder Drive Systems B.V.
RW1000
RW1200
RW1400
RW1600
RW2000
RW70
RW100
RW140
RW200
RW800
RW240
RW400
RW600
RW45

TABLE OF CONTENTS
1. GUIDELINES, STANDARDS AND CONDITIONS
1.1 Applicable guidelines and standards 3
1.2 Approved personnel 3
1.3 Warning about discouraged use 3
1.4 Warranty provisions 3
2. SAFETY, PRECAUTIONS AND SYMBOLS
2.1 Signal words, instrucons and warnings 4
2.2 Precauons and safety instrucons 5
2.3 Residual risks 6
2.4 Symbols and abbreviaons 7
3. PRODUCT DETAILS
3.1 Idencaon 8
3.2 Descripon 9
3.3 Applicaon 10
3.4 Dimensions 11
3.5 Technical specicaons 14
4. INSTALL INSTRUCTIONS
4.1 Special tools and equipment 15
4.2 Mounng posions 16
4.3 Sprockets 19
4.4 Installaon 20
4.5 Installaon opons A–F for output shas 24
4.5.1 Basic output shas (BOS) 24
4.5.2 Special output-shas (D, LD, LK ....) 24
4.5.3 Installaon chain (for A–D) 25
4.6 TRA drive-unit onto RW45\240TRA motor gearbox 26
4.7 Belt drum onto RW45\240/400L motor gearbox 28
4.8 Cable drum onto RW45\240/400L motor gearbox 29
5. CONNECT INSTRUCTIONS
5.1 Removal covers 30
5.2 Electrical material 31
5.3 Protecon - Condions and starng points 32
5.4 Tightening-torque motor-connecons 33
5.5 Control-circuit connecon 34
5.6 Change Direcon-of-rotaon - Switching sense 35
5.7 OPTIONAL - Posion Feedback 35
6. USER INSTRUCTIONS
6.1 Usage - Condions and starng points 36
6.2 Direcon-of-rotaon RW motor-gearboxes 37
6.3 Operaon 39
6.4 Safety funcons and stop funcons 39
7. COMMISSIONING INSTRUCTIONS
7.1 Commissioning - Condions and starng points 39
7.2 RSU limit-switch system 40
7.3 Adjusng the end posions 42
7.4 Installaon covers 43
8. MAINTENANCE INSTRUCTIONS
8.1 Maintenance 44
9. SERVICE
9.1 Troubleshoong 45
9.2 Technical support 46
10. ENVIRONMENT
10.1 Decommissioning and removal 46
10.2 Waste disposal 47
Ridder Drive Systems B.V.
T+31 (0)341 416 854 - F+31 (0)341 416 611 - Iridder.com
2

1. GUIDELINES, STANDARDS AND CONDITIONS
1.1 Applicable guidelines and standards
This product complies with the provisions of the European guidelines that follow:
Machinery Direcve 2006/42/EC | Low Voltage Direcve 2014/35/EU
The harmonized standards (or parts of these standards) that follow are applicable:
NEN-EN-ISO 12100:2010 | NEN-EN-IEC 60204-1 |
NEN 82079-1 (62079: 2001) | NEN5509 | ISO 3864-2
Make sure that this product is only put into operation if the system (in which it will be installed)
complies with the provisions of the applicable standards and guidelines.
1.2 Approved personnel
This product manual contains important informaon for installers about the installaon and
commissioning of a Ridder RW motor-gearbox. Read this product manual and instrucons rst
before the work starts. Approved mechanical and/or electrical installers, with professional
competence, must do all work safely and responsibly.
TARGET GROUP FOR EACH CHAPTER CHAPTER (refer to Table of Contents)
TARGET GROUP 1 2 3 4 5 6 7 8 9 10
User (operator) • • • • (•) (•)
Installer / Approved personnel • • • • • • • • • •
(•) = Not fully applicable (for users/operators)
Keep this product manual with the product during the lifespan. Make sure it is available for users
(operators), installers and approved personnel.
1.3 Warning about discouraged use
The condions that follow are applicable:
• Do not change (the construcon of) the RW motor gearbox.
• It is not permied to weld to the RW motor gearbox or its parts.
• It is not permied to use the RW motor gearbox to li or move people.
• Do not let the torque of the RW motor gearbox be more than its maximum.
• Do not let the duty cycle of the RW motor gearbox be more than its maximum.
• It is not permied to use the RW motor gearbox in operang condions, systems or
conguraons which do not comply with the technical specicaons (in this manual). Also refer
to §3.5.
Refer to §3.3 for a descripon of the intended use.
1.4 Warranty provisions
For the warranty period and condions refer to the ‘Condions’ secon on our website at
ridder.com, or in the Ridder catalog.
Regulatory Conformity
Ridder Drive Systems B.V.
T+31 (0)341 416 854 - F+31 (0)341 416 611 - Iridder.com
3

2. SAFETY, PRECAUTIONS AND SYMBOLS
2.1 Signal words, instrucons and warnings
Signal words (ISO 3864-2)
This product manual contains safety instrucons with dierent signal words. The list that follows
gives the risk levels and possible eects of each signal word.
Instrucons and warnings on the product
Read the product manual to fully know all product
properes, before it is used or work starts!
Ê
Ê
Ê
COVERS
It is not permied to use high-pressure cleaners (and
related cleaning agents)! Use a so brush with a small
quanty of water without cleaning agents.
Warning - Electrical voltage
Aer installaon interchange the plug in the highest
posion with the vent plug! Refer to the permied
mounng posions in the product manual.*
* Not applicable to motor gearboxes lled with grease!
Suggeson to perform an operaon more eecvely.
May result in damage or problems if an acon is performed
incorrectly.
May result in minor injury if the hazard is not avoided.
Signicant injury, possible death, if the hazard is not avoided.
Severe injury and possible death if the hazard is not avoided.
Ridder Drive Systems B.V.
T+31 (0)341 416 854 - F+31 (0)341 416 611 - Iridder.com
4

2.2 Precauons and safety instrucons
Precauons
GENERAL
A system can be dangerous. Safety precauons and instrucons are important.
• If these precauons cannot be obeyed, then use warnings.
• The responsibility for precauons and warnings lies with the installer of the system. Refer to the,
local or naonal, laws and regulaons of the country if a cercaon (mark) is necessary.
• Parts of the electrical or electronic installaons are connected to dangerous electrical voltages.
This is also applicable if the drive unit is not in operaon or the motor does not turn. Work
without professional competence or not obeyed warning instrucons could cause injury and/or
material damage.
• Make sure that no foreign parcles, loose parts, moisture or dust go into the components (EM,
gearbox, RSU/RLS) during all work. There is a risk of short circuit, re and corrosion.
• Take sucient precauons to prevent ElectroStac Discharge (ESD).
• Ridder is not responsible for injury, material damage or consequenal damage if accessories are
used that Ridder did not make.
TRANSPORT, STORAGE AND PACKAGING
The condions and instrucons that follow are applicable.
• Ambient temperature: -15 to +60 °C (+5 to +140 °F).
• Ambient: A not-condensed relave humidity is necessary.
• Do a check for transport damage and missing parts immediately on incoming goods.
• Tell damages and missing parts immediately to the transport company and to your local Aer
Sales contact person.
• Do not use damaged products and if necessary do not start the work.
• Do not remove the product from the (sealed) packaging before it is sent to the installaon site.
This prevents damage (from mechanical shocks) to the product.
• Use applicable means-of-transport with dimensions which are sucient. Use (if necessary) the
correct work equipment and accessories. Refer to “Dimensions” and “Technical specicaons”.
Make sure that the working condions comply with the, local or naonal, laws and regulaons.
• Make sure that storage areas and the areas in the means-of-transport are dry and the airow is
sucient.
• Make sure that the products do not touch the (moist) boom surface of storage areas and of the
means-of-transport (use pallets or such). The boom surfaces must be smooth.
• Make sure that the products are protected from dust, dirt and direct sunlight.
• Apply an applicable corrosion-prevenve agent to metal surfaces that are not painted.
• Aer installaon discard the packaging and obey the applicable naonal and/or local regulaons.
Ridder Drive Systems B.V.
T+31 (0)341 416 854 - F+31 (0)341 416 611 - Iridder.com
5

Safety instrucons
• For a fail-safe function install redundant safety systems to prevent that loads or system parts
fall uncontrolled. Install (if necessary) protection from system parts that move. Obey the
applicable national and/or local standards and guidelines of the related type of operated
system.
• Use (if applicable) personal protecve-equipment for protecon which agrees with the dierent
types of work.
• Do not let persons and not approved personnel be near controls and systems in operaon.
• Damaged systems must be stopped immediately unl they are repaired.
• Use safety barriers for system parts that move. Refer to the applicable standards and guidelines.
• The safety distance to the danger zone (if applicable) must agree with applicable standards and
guidelines (for example ISO 13857:2008).
• Do not operate systems when the motor gearbox (internally and/or externally) is frozen in cold
and moist condions (for example because of snow or ice).
• Do not operate systems when persons are in the danger zone and can touch the system.
• Monitor the danger zone when you work with or near the system.
• Stop and de-energize systems during maintenance and cleaning work on or near the system.
• Make sure that there is sucient space between parts that move and adjacent objects.
• Stay away from or safety areas where there is a risk to become caught in a system that moves.
• The torque and the duty cycle of the system must be in the range of the motor gearbox
parameters.
2.3 Residual risks
Automac controls
The Ridder drive-units are usually used in automac controlled systems. Persons who do work or
stay near the system must know about that. If persons or their clothes touch the system during
operaon, it can be dangerous.
Forces
Ridder cannot be sure that there will be no injury to persons or damage to the system because of
the forces in the systems (in which the drive unit is installed).
If you do not obey the safety instrucons that follow it can be
dangerous and cause injury.
Persons can be in danger of life if they touch a system that is in
operaon.
Ridder Drive Systems B.V.
T+31 (0)341 416 854 - F+31 (0)341 416 611 - Iridder.com
6

2.4 Symbols and abbreviaons
This secon tells about used symbols and abbreviaons in this manual. The table that follows gives
the descripons.
Symbol Description Symbol Description
ACS Automac control-system PH Cross head “Phillips”
BOS Basic Output Shas (RW) PLC PLC Control
C Common connecon PZ Cross head “Pozidriv”
DModel with connuous worm-sha P21/1 Auxiliary contact K21
EM, M Electric motor, Motor P22/1 Auxiliary contact K22
EMC Electromagnec compability P71, P72 Automac-control contacts (ACS)
ESD ElectroStac Discharge RLL Ridder LogicLink
ES11,ES12 Duty switch RSU RMC Ridder MotorControl
ES21,ES22 Safety switch RSU rpm revoluons per minute
FTL Free Thread-Length RPT Ridder PolyTelescope
F1 Fuse RPU Ridder PosioningUnit
HEX Hexagonal width-across-ats RRD Ridder RackDrive
ICurrent in Amperes (A) RSD Ridder ScreenDrive
IP Internaonal Protecon Rang RSU Limit-switch system
KDesignaon sprocket (assembled
conguraon)
RW Motor gearbox
SBI Standard Bolt-Installaon
kb Maximum running me in minutes
(kb = KurzBetrieb/ Short operaon)
SID Screw-in depth
SS (S21) System switch (S21)
K11 Auxiliary relays (safety switches) SW Width-across-ats
K21, K22 Reversing relay (suciently specied)
for direcon-of-rotaon
S11 Manual switch (bridged safety circuit)
S21 (SS) System switch (SS)
L Model with winch sha S111 Manual switch (MC)
L1, L2, L3 Voltage source TRA Model for built-on rack unit
MC Manual Control TRI Rack drives TRI
MPCB/
Q41 Motor-Protecon Circuit-Breaker TRN Rack drives TRN
TX Screw head “Torx”
N Neutral wire T1 Safety transformer (EN 61558)
NC “normally closed” U1 Motor connecon
NO “normally open” V1 Motor connecon
PE Protecve earth W1 Motor connecon
Ridder Drive Systems B.V.
T+31 (0)341 416 854 - F+31 (0)341 416 611 - Iridder.com
7

3. PRODUCT DETAILS
3.1 Idencaon
This product manual is only applicable to:
• Ridder Motor Gearboxes RW 3-phase
• Serial numbers from 200.900.000
• Item numbers from 500000.
Idencaon is possible from the scker on the locaon shown. Refer to the explanaon that
follows on how to read the informaon. For more informaon on item numbers and models refer to
the Ridder catalog or website at ridder.com.
EXAMPLE
Ê
Ê
Ê
COVERS
= If not applicable: No symbol in idencaon.
NOTE: Possibly the sequence of symbols is dierent and/or other symbols are included in the idencaon. Not all symbols
and assembled conguraons (such as LK, LD, ...) are included in the explanaon.
* K = Sprocket in an assembled conguraon.
WI: White color nish
z16: Oponal sprockets
Alternaves: z12/3z16 (3x for D model)
IP55: Protecon rang
No symbol in idencaon = IP54
Alternaves: 11/12/14/25/29/30/37/42/44/55/63/66/75/85/
90/110/125/132/150/180/200/216/240/300/360
3: 3-phase mains voltage
400: Mains voltage [V]
09: Motor power at 50\60 Hz [daW]
86: Limit-switch range motor-gearbox
L: Model with winch sha
45 = Torque 120, 90 or 60 Nm
Alternaves: 70/100/140/200/400/600/
800/1000/1200/1400/1600/2000
RW: General designaon Ridder RW motor-gearboxes
CU: CSA/UL cercaon mark
Alternaves: 3C (CCC)/C (CSA)/U (UL)
Alternaves: 55/97/120/860
60: Mains frequency [Hz]
No symbol in idencaon = 50 Hz
Alternaves: 208–480/380/600
TRA: Model for built-on rack unit
D: Model with connuous worm-sha
No symbol in idencaon = Sprockets (K)*
1: Rotaonal speed of drive sha at 50(60) Hz [rpm]
Alternaves: 2/3/5/34(41)/68(82)
3S = Wire-screen system: 3 [rpm]
240: Torque [Nm]
V: Grease lubricaon
No symbol in idencaon = Oil lubricaon
Ridder Drive Systems B.V.
T+31 (0)341 416 854 - F+31 (0)341 416 611 - Iridder.com
8

3.2 Descripon
RW motor gearboxes are drive units to operate systems in greenhouses, livestock houses, crop-
storage buildings and such. The RW motor-gearboxes are applicable at ambient temperatures
between 0 and 60 °C. RW motor-gearboxes have a self-braking worm-gear transmission which stops
the drive unit (worm sha) when not operated and then locks the output sha. To operate manually
(externally) is possible with (electric) tools and a hexagon socket in the sha of the electric motor.
The RW motor-gearboxes (3-phase) have the linear RSU limit-switch system, with duty switches and
safety switches. RW motor-gearboxes are applicable to use intermiently (duty class s3-35%) with
a maximum duty cycle of 25 minutes. The oponal PosioningUnit RPU monitors the posions of
the drive unit and transmits the data to the automac control-system (ACS). Posion feedback is
also possible with a mounng set with potenometer. Operaon is possible, usually in automated
systems, with a manual control (MC) and/or other control components.
The RW motor-gearboxes have connecons (terminal blocks/connecon blocks) to connect the
cables and are supplied with cable glands for the power cables and control cables. The gearbox
housing of the RW motor-gearbox has a powder-coang. RW motor-gearboxes are supplied with
xing bolts and spring washers*.
* For RW1000–RW2000 motor gearboxes bolts (M12), spring washers and nuts are accessories.
RW45 series
• RW45: 12-tooth 1⁄2”x5⁄16” zinc-plated sprockets for chain couplings
are installed. Optionally 16-tooth 1⁄2”x5⁄16” sprockets are installed to
compensate for larger angle dierences (to a maximum of 6°).
• RW45L: Has a one-sided output sha to install a belt drum or cable
drum.
• RW45TRA: Has a one-sided output sha to install a TRA520 rack-drive.
• RW45D: An RW45 with a connuous worm-sha. Optionally a
16-tooth 1⁄2”x5⁄16” zinc-plated sprocket for chain couplings is
installed.
The switching range of the limit-switch system is 55 or 97 revoluons of the drive sha. The range is
related to dierent models.
RW240–600 series
• RW240/400/600: 16-tooth 5/8”x3/8” zinc-plated sprockets for chain
couplings are installed.
• RW240/400/600L: Has a one-sided output sha to install a belt drum
or cable drum.
• RW240/400/600TRA: Has a one-sided output sha to install a TRA520
rack-drive.
• RW240/400/600D: An RW240/400/600 equipped with a connuous
worm-sha. Optionally a 16-tooth 1⁄2”x5⁄16” zinc-plated sprocket for
chain couplings is installed.
The switching range of the limit-switch system is 86 revoluons of the drive sha.
Ridder Drive Systems B.V.
T+31 (0)341 416 854 - F+31 (0)341 416 611 - Iridder.com
9

RW800 series
• RW800: 16-tooth 5/8”x3/8” zinc-plated sprockets for chain couplings
are installed.
The switching range of the limit-switch system is 120 revoluons of the drive
sha.
RW1000–2000 series
• RW1000/1200/1400/1600/2000: 16-tooth 3/4”x7/16” zinc-plated
sprockets for chain couplings are installed.
The switching range of the limit-switch system is 86 revoluons of the drive
sha.
RW70–200 series
• RW70/100/140/200: 16-tooth 1⁄2”x5⁄16” zinc-plated sprockets for
chain couplings are installed.
The switching range of the limit-switch system is 860 revoluons of the drive
sha.
3.3 Applicaon
• The RW45 motor gearboxes are drive units to operate venlaon systems and screen systems in
greenhouses and livestock houses or crop-storage buildings.
• The RW45L\RW240/400L motor gearboxes with drums (belt or cable) are drive units to hoist
feeding lines and drinking lines and to open air inlets in livestock houses or crop-storage
buildings.
• The RW45TRA\RW240TRA motor gearboxes with a TRA520 rack drive are drive units to operate
venlaon systems and hoisng systems in greenhouses and livestock houses or crop-storage
buildings.
Make sure that (with RW motor gearboxes) operated systems comply
with the provisions of the applicable safety standards and safety
guidelines.
This prevents (for example) the risk:
• To become caught in a system that moves
• That loads or system parts that fall can hit persons.
Ridder Drive Systems B.V.
T+31 (0)341 416 854 - F+31 (0)341 416 611 - Iridder.com
10

• The RW45D\RW400/600D motor gearboxes are drive units to operate venlaon systems and
hoisng systems in greenhouses and livestock houses or crop-storage buildings.
• The RW240–600\RW800 motor gearboxes are drive units to operate venlaon systems, screen
systems and hoisng systems in greenhouses and livestock houses or crop-storage buildings.
• The RW1000/1400 motor gearboxes are drive units to operate venlaon systems, screen
systems and hoisng systems in greenhouses.
• The RW1200/1600/2000S motor gearboxes are drive units to operate wire screen systems in
greenhouses.
• The RW70–200-34/68 motor gearboxes are drive units to operate indirectly-operated venlaon-
systems in greenhouses and livestock houses or crop-storage buildings.
This secon tells about usual conguraons of motor gearboxes and operated systems. Possibly
other conguraons (or applicaons) are applicable.
For other (dierent) applicaons, approval from Ridder Drive Systems is necessary.
3.4 Dimensions
The dimensions and illustraons are approximate. In this product manual shown illustraons can be
dierent than the components and/or systems.
RW45:
H1 = 55–56 mm
H2=144–158mm
L1 = 166–170 mm
L2 = 108–112 mm
RW-L/(LK)
RW-TRA
M20
RW-D
68
12 34
Ø25
120
Ø28
Ø25
50
30
28
45
Ø28
Ø16
H2
157
52
192
L1
78 L2
200
H1
85
19
M10X18
151
245
(5)
45
25
Ø15
70.5
Ø17.5
1.8
1
Ridder Drive Systems B.V.
T+31 (0)341 416 854 - F+31 (0)341 416 611 - Iridder.com
11

RW240/400/600:
RW800:
RW-L/(LK)
RW-TRA
RW-D
M20
H1 = 54–89 mm
H2 = 141–213 mm
L1 = 156–246 mm
L2 = 115–195 mm
68
12 31
Ø25
116
Ø28
Ø25
50
30
45
63.5
Ø28
Ø16
H2
195
73
234.5 L1
95 L2
200
H1
105
28/34
325
(2)
M10x25
24.5
Ø24
1.2
Ø19
2.3
63
72.5
M20
H1 = 72.5–89 mm
H2 = 190–213 mm
L1 = 217–246 mm
L2 = 160–215 mm
134 15
3.5
42
62.5
H2
112
100
260 L1
L2
200
H1
100
34
340
M12x25
16.575
Ridder Drive Systems B.V.
T+31 (0)341 416 854 - F+31 (0)341 416 611 - Iridder.com
12

RW1000/1200/1400/1600/2000:
RW70/100/140/200-34\68:
M20
H1 = 75–95 mm
H2 = 205–230 mm
L1 = 248–315 mm
L2 = 130–210 mm
240 65
10
A
156
350
235
L1
L2
140
80
151 84
H1
40 65
14
H2
24
80 44
220
178
14
21
66
45
44
50
B
15 255
B
A
290
110180
43
21
40
M20
H1 = 75–88 mm
H2 = 179–230 mm
L1 = 215–246 mm
L2 = 112–153 mm
188.5
40
62
H2
77.5
234
L1
L2
200
H1
105
Ø25
268
M10x25
12
72
Ridder Drive Systems B.V.
T+31 (0)341 416 854 - F+31 (0)341 416 611 - Iridder.com
13

3.5 Technical specicaons
Mechanical
RW series RW45 RW240–600 RW800 RW1000–2000 RW70–200
Torque [Nm]
60
90
120
240
400
600 800
1000
1200
1400
1600
2000
70
100
140
200
Mains frequency [Hz] 50/60 50/60 50/60
Rotaonal speed
[revoluons per minute]
1/1.2*
2/2.4*
3/3.6
5/6.0
3/3.6
5/6.0 34/41
68/82
* Not applicable: - RW600 - - -
Limit-switch range
[revoluons of drive sha]
55
97 86 120 86 860
Drive unit Self-braking
Operate manually (externally): With (electric) tools and a hexagon socket in the sha of the
electric motor.
Dimensions [mm] WxHxD Refer to §3.4 (minimum–maximum).
Weight [kg] 15.5–17 27.5–42 40.5–44 54.5–68 30–40
Electrical
RW series RW45 RW240–600 RW800 RW1000–2000 RW70–200
Duty cycle [kb] Applicable for intermient duty, duty class s3-35%, with a
maximum running me of 25 minutes.
Maximum current Refer to the nameplate of the electric motor.
Power
Cable glands M16x1.5 mm/M20x1.5 mm. Also refer to §5.2.
Mains voltage
400 V - 50 Hz
480 V - 60 Hz • • • • •
200–415 V - 50 Hz
200–480 V - 60 Hz • • • • •*
380 V - 60 Hz - •* - - -
600 V - 60 Hz - • • • •**
* Not applicable: - RW600 - - RW100
** Not applicable: - - - - RW70–140
Ambient
RW series RW45 RW240–600 RW800 RW1000–2000 RW70–200
Protecon rang IP54*
Ambient temperature [°C (°F)] 0–60 °C (32–140 °F)
* IP55 only applicable if in idencaon.
Ridder Drive Systems B.V.
T+31 (0)341 416 854 - F+31 (0)341 416 611 - Iridder.com
14

4. INSTALL INSTRUCTIONS
Installaon is only permied to approved personnel.
Do a check of the supplied parts in the table that follows. Use these parts with the mounng plate
(selecon) which is applicable. Refer to §4.4.
Parts list *
500000 Motor Gearbox RW 3-phase ** 1x
* Minimum parts list: Motor gearbox without oponal parts and accessories.
** Motor gearboxes have spring washers and bolts M10x20 (2x), M10x25 (3x) or M12x25 (4x). Item numbers
from 500000.
NOTE: Bolts (M12), spring washers and nuts are accessories for RW1000 thru RW2000 motor gearboxes.
Installaon (general)
• This product manual gives only informaon about the installaon of RW motor-gearboxes and
related connecons to output-shas (installaon opons).
• Informaon about the dierent operated systems is not (or not fully) given or gives only general
informaon.
Installaon opons for output shas
Refer to (if applicable):
• §4.5.1 for the (most) used connecons of basic output shafts to operated systems (installaon
opons A–F)
• §4.5.2 for the installaon opons (A–F) of special output shafts
• §4.5.3 for the installaon of chains onto sprockets (for installaon opons A–D)
• §4.6 for TRA models with TRA drive-unit (installaon opons G, H, I)
• §4.7 for L models with belt drum (installaon opon J)
• §4.8 for L models with cable drum (installaon opon K).
4.1 Special tools and equipment
No special tools or equipment are necessary to install, to connect or for commissioning.
Make sure that the correct equipment and tools are used.
Ridder Drive Systems B.V.
T+31 (0)341 416 854 - F+31 (0)341 416 611 - Iridder.com
15

4.2 Mounng posions
• Refer to the illustraons and use only a permied mounng posion for installaon!
• After installation interchange the plug in the highest posion with the vent plug! This is not
applicable to motor gearboxes that are lled with grease!
RW45 [grease lubricaon]:
RW240/400/600 [oil lubricaon]:
Ridder Drive Systems B.V.
T+31 (0)341 416 854 - F+31 (0)341 416 611 - Iridder.com
16

4.3 Sprockets
• Usually Ridder installs sprockets onto the two basic output shafts (BOS) of most models (general
designaon: RW).
• Some models (such as RW-LK, RW-D, RW-LD) have:
• One special output-sha (LK) plus one basic output sha (BOS)
• One special output-sha (D) plus two basic output shas (BOS)
• Two special output-shas (L + D). (The L-sha is for installaon of a drum.).
• Some models or shas (BOS and/or special shas) are supplied without sprockets.
Thus it is possibly necessary, if applicable for the conguraon, to:
❶ Install necessary (oponal) sprockets on output shas or
❷ Interchange sprockets with necessary (oponal) sprockets on output shas.
Refer to the illustraon (step ❶ and ❷) that follows for the conguraon of sha keys (a, b),
retaining rings (c) and ring (d).
For more informaon on item numbers and models refer to the Ridder catalog or website at
ridder.com.
* Sha LK-model: Installaon of a drum is also possible. Refer to §4.7/4.8.
** Sha L-model is for installaon of a drum. Refer to §4.7/4.8.
Basic output shas [BOS] Output sha LK Output sha D
HEX 3 mm
M6 x 8 mm
Model: RW Model: RW-LK Model
2x BOS 1x Sha-LK*
+ 1x BOS RW-D: 1x Sha-D
+ 2x BOS
RW-LD: 1x Sha-D
+ 1x Shaft-[L]**
Ridder Drive Systems B.V.
T+31 (0)341 416 854 - F+31 (0)341 416 611 - Iridder.com
19

4.4 Installaon
The condions and starng points that follow are applicable for installaon. Make sure that the
working condions comply with the, local or naonal, laws and regulaons.
• Do not remove the product from the packaging unl a short me before the installaon.
• Use the correct work equipment and accessories (belts, chains, pallets or such) if it is not
permied or possible to put the product manually in posion.
• Only use a permied mounng posion when you install the RW motor-gearbox. Refer to §4.2.
• The mounng plates are available in dierent dimensions for dierent conguraons. Refer to
“Oponal mounng plates ❶”.
Install the RW motor-gearbox onto the mounng plate or an alternave (refer to “Oponal
mounng plates ❷”):
• With the supplied spring washers and bolts M10x20 (2x) for an RW45 drive unit
• With the supplied spring washers and bolts M10x25 (3x) for RW240–600 and RW70–200 drive
units
• With the supplied spring washers and bolts M12x25 (4x) for an RW800 drive unit
• With nuts, spring washers and bolts M12(4x) for RW1000–2000 drive units (supplied as
accessories).
Refer to “Minimum Screw-in depth/Free thread-length (SID/FTL)” which also shows the standard
bolt-installation (SBI).
• The RSU limit-switch system and other components (RPU and such) can give informaon
“in operaon” and/or during commissioning. Thus, easy access and a sasfactory view is
recommended for the locaon of the RW motor-gearbox.
• In the factory the reductor is lled with the necessary quanty of grease (usually only RW45) or
oil. Aer installaon interchange (of reductors lled with oil) the plug in the highest posion with
the vent plug! Refer to §4.2.
Ridder Drive Systems B.V.
T+31 (0)341 416 854 - F+31 (0)341 416 611 - Iridder.com
20
This manual suits for next models
9
Table of contents
Other Ridder Engine manuals
Popular Engine manuals by other brands
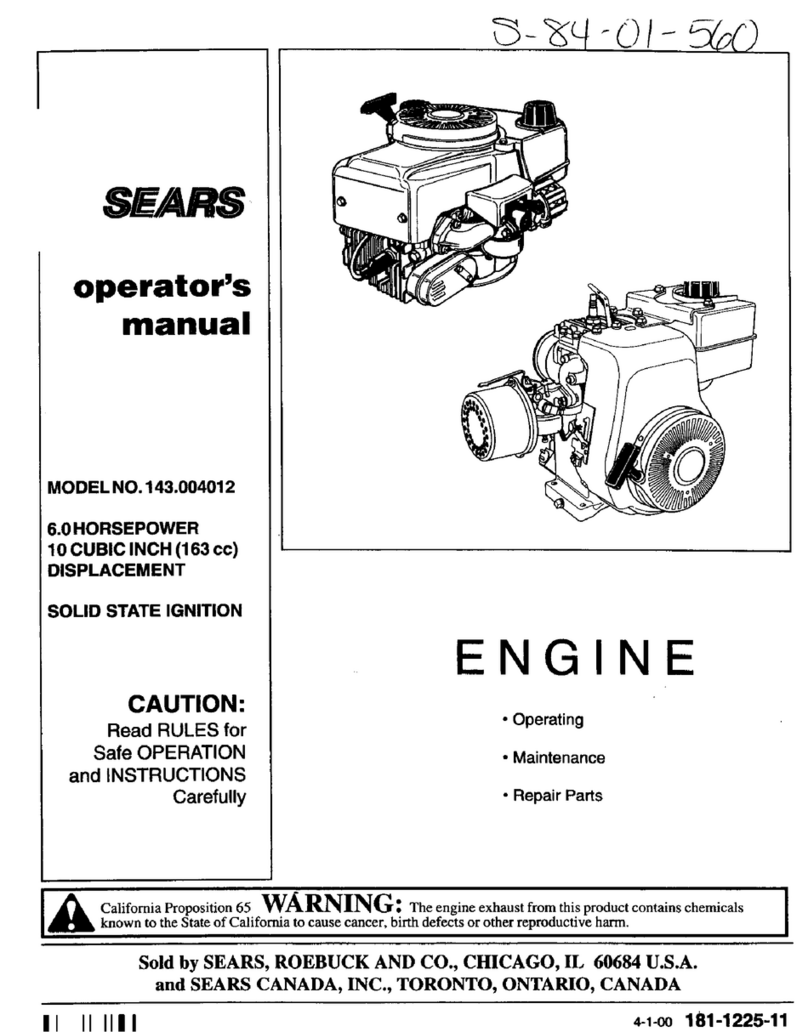
Sears
Sears 143.004012 Operator's manual
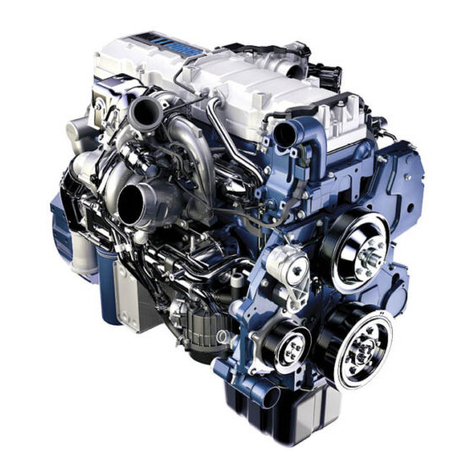
Navistar
Navistar MaxxForce DT 9 Operation and maintenance manual
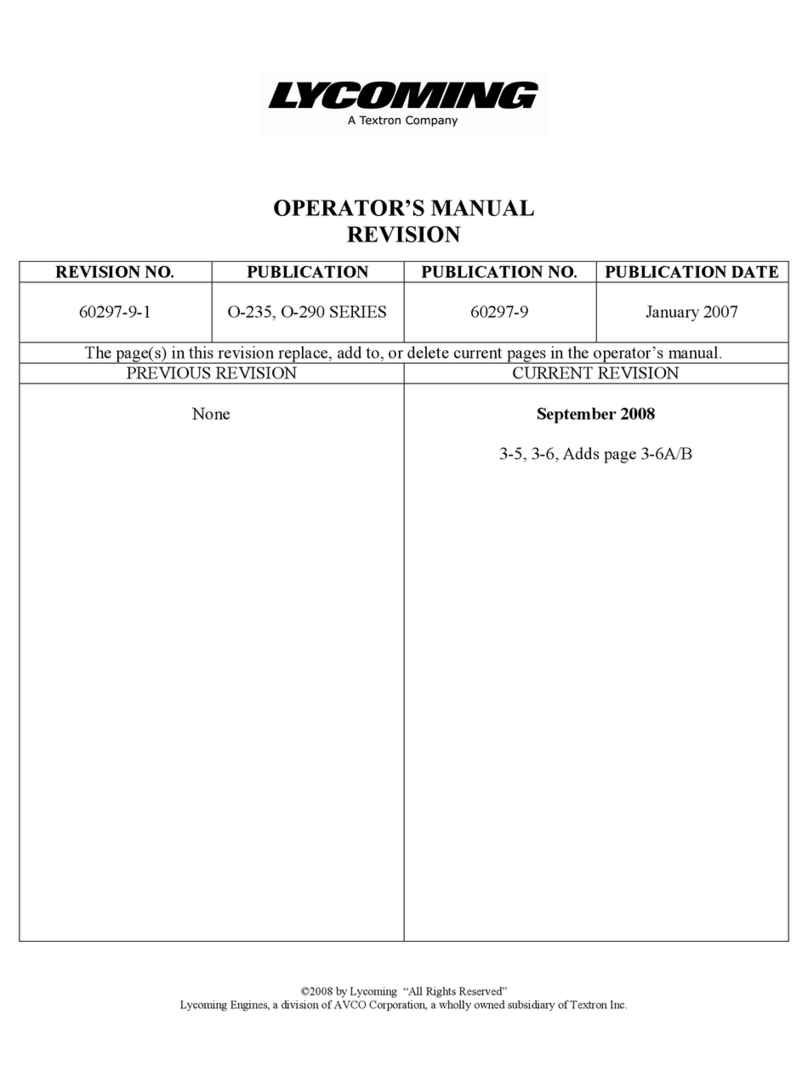
Textron
Textron Lycoming O-235-C Operator's manual

Detroit Diesel
Detroit Diesel DDFP Series Operation and maintenance instruction manual

Mitsubishi
Mitsubishi 4G1 series Workshop manual
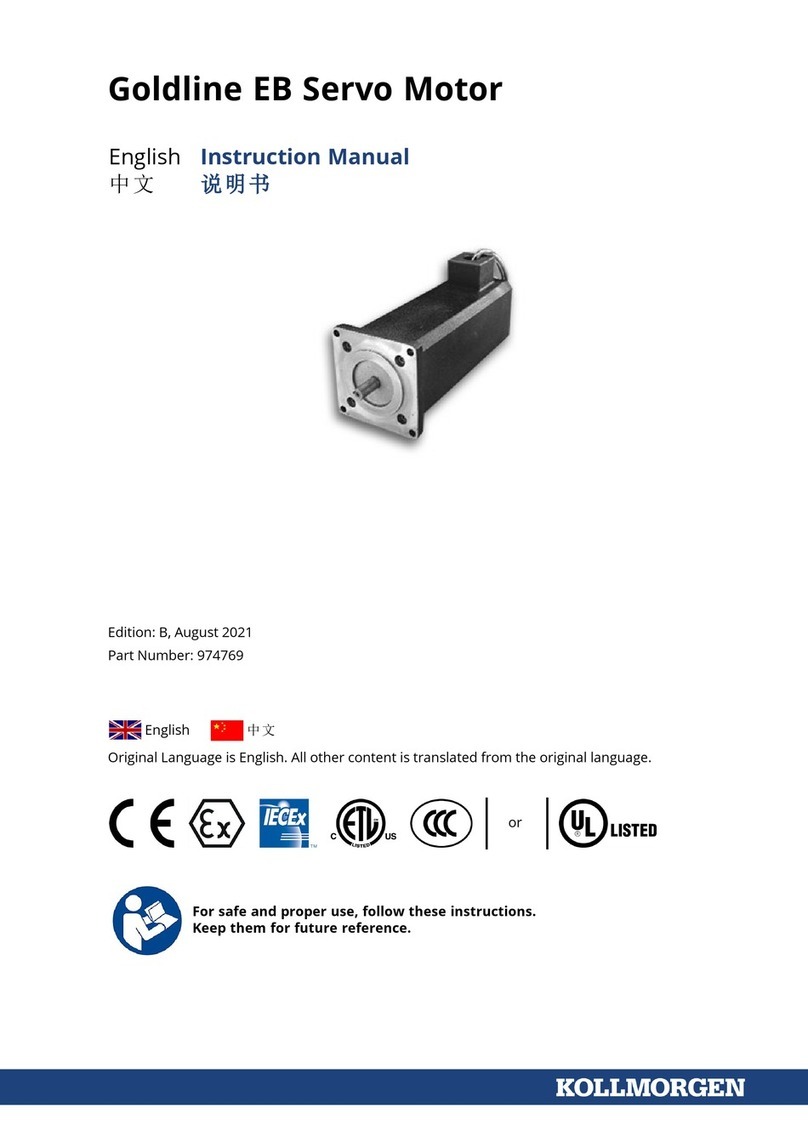
Kollmorgen
Kollmorgen Goldline EB Series instruction manual