RJG RIEGER LS-QTTB-J User manual

PRODUCT MANUALPRODUCT MANUAL
Training and Technology for Injection Molding
Lynx™ Quad Temperature
Modules
LS‑QTTB‑J & LS‑QTTB‑K

PRINT DATE 06.13.2022
REVISION NO. 0

Product Manual | Lynx™ Quad Temperature Modules LS‑QTTB‑J & LS‑QTTB‑K i
PRODUCT MANUAL
Lynx™ Quad Temperature
Modules
LS‑QTTB‑J & LS‑QTTB‑K
PRODUCT DESCRIPTION
APPLICATIONS 1
OPERATION 2
INSTALLATION
INSTALLATION OVERVIEW 3
INSTALLATION SPECIFICATIONS 4
MOUNTING 5
CONNECTIONS 6
SOFTWARE SETUP 7
MAINTENANCE
CLEANING 11
TESTING & CALIBRATION 11
WARRANTY 11
RJG, INC. STANDARD WARRANTY 11
PRODUCT DISCLAIMER 11

Lynx™ Quad Temperature Modules LS‑QTTB‑J & LS‑QTTB‑K | Product Manual
ii
TROUBLESHOOTING
MEASUREMENT ERRORS 13
CONNECTION PROBLEMS 13
WIRE EXTENSIONS 13
NOISE 13
INSTALLATION ERRORS 14
REVERSED CONNECTIONS 14
LOOSE CONNECTIONS 14
CUSTOMER SUPPORT 15
RELATED PRODUCTS
COMPATIBLE PRODUCTS 17
SPRING‑LOADED 1.5MM TEMPERATURE SENSOR TS‑SL01.5‑K 17
PRESS‑FIT 3MM CAVITY TEMPERATURE SENSOR TS‑PF03‑K 17
1MM FLUSH MOUNT CAVITY TEMPERATURE SENSOR TS‑FM01‑K 17
PRODUCT MANUAL
Lynx™ Quad Temperature
Modules
LS‑QTTB‑J & LS‑QTTB‑K

Product Manual | Lynx™ Quad Temperature Modules LS‑QTTB‑J & LS‑QTTB‑K iii
INTRODUCTION
Read, understand, and comply with all
following instructions. This guide must be
kept available for reference at all times.
DISCLAIMER
Inasmuch as RJG, Inc. has no control
over the use to which others may put
this material, it does not guarantee that
the same results as those described
herein will be obtained. Nor does RJG,
Inc. guarantee the effectiveness or safety
of any possible or suggested design
for articles of manufacture as illustrated
herein by any photographs, technical
drawings, and the like. Each user of the
material or design or both should make
his own tests to determine the suitability
of the material or any material for the
design as well as the suitability of the
material, process, and/or design for his
own particular use. Statements concerning
possible or suggested uses of the material
or designs described herein are not to be
construed as constituting a license under
any RJG, Inc. patent covering such use
or as recommendations for use of such
material or designs in the infringement of
any patent.
PRIVACY
Designed and developed by RJG, Inc.
Manual design, format and structure
copyright 2022 RJG, Inc. content
documentation copyright 2022 RJG, Inc. All
rights reserved. Material contained herein
may not be copied by hand, mechanical, or
electronic means, either whole or in part,
without the express written consent of RJG,
Inc. Permission will normally be granted for
use in conjunction with inter-company use
not in conflict with RJG’s best interests.
ALERTS
The following three alert types are used
as needed to further clarify or highlight
information presented in the manual:
DEFINITIONA definition or clarification of a
term or terms used in the text.
NOTESLA note provides additional
information about a discussion
topic.
CAUTIONaA caution is used to make the
operator aware of conditions that
can cause damage to equipment
and/or injury to personnel.

Lynx™ Quad Temperature Modules LS‑QTTB‑J & LS‑QTTB‑K | Product Manual
iv
NOTES

Product Manual | Lynx™ Quad Temperature Modules LS‑QTTB‑J & LS‑QTTB‑K 1
PRODUCT DESCRIPTION
The Lynx™ Quad Temperature Modules
LS-QTTB-J and LS-QTTB-K accept input
from up to four thermocouples (type J or
type K) for use with the RJG, Inc. eDART®
or CoPilot® systems.
APPLICATIONS
Temperature data can help identify cooling
circuit variation, imbalance or blockage—
including warp due to semi-crystalline
shrinkage behavior—and improper melt
temperatures.
Mold temperatures including
in-cavity,effective melt, mold, parting
line, and coolant temperatures, can be
monitored using the LS-QTTB-J/K in
conjunction with temperature sensors and
the eDART or CoPilot system, as well as
barrel and dryer temperatures.
1. Mold Temperatures
• In-Cavity Temperature Monitoring*
If the plastic contacts the sensor or the
sensor is just behind the cavity wall, the
sensor is considered “in-cavity” and can be
post gate, mid-cavity or end-of-cavity.
In-cavity temperature monitoring can be
used to identify melt flow front arrival,
which is useful in identifying balance and
warp issues.
• Effective Melt Temperature, Surface
(Mold) Temperature*, Parting Line, Sprue,
or Runner
If the sensors are located in the mold steel
the sensor can be utilized for effective melt
temperature, mold (surface) temperature,
parting line temperature, sprue, or runner.
Effective melt temperature is a summary
value that the eDART generates from a
cavity temperature sensor installed in the
wall of the cavity where the flow front
contacts the sensor as it passes by.
A calibration factor is used to compute
a number close to the actual melt
temperature; the effective melt temperature
will never read out the actual temperature
of the melt. If the value changes over
time or when transferring a mold between
machines, a change in melt temperature
can be suspected.
Changes in cycle time or breaks in
cycle dramatically affect thermodynamic
stability in injection molding; monitoring
temperature enables troubleshooting of
processing problems. Effective melt, mold,
and parting line temperatures can help
identify cooling variations.
• Coolant Temperature Monitoring*
If the coolant contacts the sensor or the
sensor is just behind the coolant channel,
the sensor is considered a coolant
temperature monitor; the sensor can be
assigned in the Sensor Locations tool as
mold output temperature.
Coolant temperature is NOT the same as
the mold surface temperature. After the
process has stabilized a flow of heat out
of the mold occurs on every cycle which
creates a temperature gradient from the
cavity surface to the coolant.
Coolant temperature monitoring can be
used to identify cooling circuit variation,
which is useful in identifying warp issues.
*Available on the CoPilot system.

Lynx™ Quad Temperature Modules LS‑QTTB‑J & LS‑QTTB‑K | Product Manual
2
2. Barrel Temperature Monitoring
A sensor or sensors can be placed in the
barrel and connected to the LS-QTTB-J/K
and the eDART system for barrel
temperature monitoring; available barrel
locations include nozzle, front, center, feed
throat, and rear.
3. Dryer Temperature Monitoring
A sensor or sensors can be placed in the
dryer and connected to the LS-QTTB-J/K
and the eDART system for dryer
temperature monitor; a dryer temperature
sensor is assigned as an auxiliary sensor
(eDART software version 9.xx) or a barrel
temperature/description not available
(eDART software version 10.xx).
APPLICATIONS (continued)OPERATION
The LS-QTTB-J/K collects temperature
readings from up to four connected
thermocouples for use with the eDART
or CoPilot systems. The LS-QTTB-J is
compatible with type J thermocouples,
while the LS-QTTB-K is compatible with
type K thermocouples; RJG, Inc. offers
a line of typeK thermocouples. The
LS-QTTB-J/K modules feature terminal
block connectors and accepts input from a
broad range of thermocouples.
The LS-QTTB-J/K requires eDART software
version 8.0 or later and CoPilot software
version 6.0 or later. The eDART computes
a range of values from the thermocouple
temperature measurements for display
and use. In-cavity sensors will provide
calculations such as Process Time/
Temperature, Minimum/Temperature,
Effective Melt Temperature, Rise/
Temperature, and Average Value at
end-of-cavity, mid-cavity, and/or post-gate;
mold temperatures are also generated for
parting line, mold surface, end-of-cavity,
mid-cavity, and post-gate locations.

Product Manual | Lynx™ Quad Temperature Modules LS‑QTTB‑J & LS‑QTTB‑K 3
INSTALLATION
INSTALLATION OVERVIEW
The LS-QTTB-J/K is grounded and mounted
over the area where the thermocouple
wires exit the mold, but away from
extensive heat or vibration/shock. The
thermocouple wires are inserted into the
module and installed using the terminal
block. A Lynx cable is attached to the
LS-QTTB-J/K Lynx port and the eDART or
CoPilot system.

Lynx™ Quad Temperature Modules LS‑QTTB‑J & LS‑QTTB‑K | Product Manual
4
INSTALLATION SPECIFICATIONS

Product Manual | Lynx™ Quad Temperature Modules LS‑QTTB‑J & LS‑QTTB‑K 5
INSTALLATION SPECIFICATIONS (continued)
MOUNTING
1. Requirements
The Lynx quad temperature module must
be mounted on a frame-grounded structure
to ensure proper operation. The ground
potential of the structure must be same
as the ground required for the eDART or
CoPilot system.
CAUTIONaThe ground connection of the
frame‑grounded structure must be
made to an adequate earth ground
to eliminate the possibility of radio
frequency noise and interference,
and to ensure a safe operation.
Always have a licensed electrician
check all wiring to ensure that all
grounds are wired correctly.
2. Mounting
The module must be mounted with the slot
over the channel where the cables exit the
mold; refer to the dimensions to determine
the correct mounting location.
3. Remove cover.
• Remove screws ( 1) from LS-QTTB-K, then
remove cover plate.
4. Insert thermocouple wire.
Feed thermocouple wire ( 2) through
the mounting gasket and wire slot ( 3) in
bottom of module.
5. Install the module.
Mount the Lynx quad temperature module
using the two provided mounting screws (
4) (10-24x0.75”).
CAUTIONaDo not mount in locations subject
to high shock or vibration (such as
ejector plates or actuating mold
components).
CAUTIONaThe module must be mounted
to surfaces with temperatures
between 32–140°F (0–60°C).
1
1
1
1
2
3
4
4

Lynx™ Quad Temperature Modules LS‑QTTB‑J & LS‑QTTB‑K | Product Manual
6
CONNECTIONS
1. Requirements
The thermocouple wires must be shielded,
however, wires that remain within the mold
may not be shielded. The shielded wires
must run through the slot in the bottom
of the module then be secured using
the shield plate to ensure good contact
and reduce radio frequency (RF) noise
susceptibility.
CAUTIONaDisconnect and lockout the main
power sources before making
electrical connections. Electrical
connections must only be made by
qualified personnel.
Keep the protective cap in place on the
Lynx connector when not in use to prevent
contamination.
2. Remove shield plate.
Remove screws ( 1) from shield plate( 2),
then remove shield plate( 2).
INSTALLATION SPECIFICATIONS (continued)
3. Connect negative (-) lead.
• Connect white wire ( 3) to the negative
terminal.
4. Connect positive lead (+).
• Connect green wire ( 4) to positive
terminal.
5. Install shield plate.
• Install shield plate ( 2) over the
thermocouple wire with screws ( 1)—
ensure the plate contacts the shield.
CAUTIONaDo not over‑tighten the plate; failure
to comply will result in damage to
equipment.
6. Install cover plate.
• Install LS-QTTB-K cover plate with screws.
7. Lynx Cable CE-LX5
Remove the protective cap from the Lynx
connector on the module. Install the female
Lynx-connector-end of the CE-LX5 cable
onto the LS-QTTB-J/K Lynx connector.
1
3
1
2
4
THERMOCOUPLE TYPE THERMOCOUPLE WIRE COLORS
IEC 5843
Type K Positive (+) Green
Negative (-) White

Product Manual | Lynx™ Quad Temperature Modules LS‑QTTB‑J & LS‑QTTB‑K 7
INSTALLATION SPECIFICATIONS (continued)
SOFTWARE SETUP
1. Requirements
The LS-QTTB-J/K requires eDART software
version 8.0 or eDART software version
10.xx or later; contact RJG Customer
Support if a software upgrade is required.
The LS-QTTB-J/K requires CoPilot software
version 6.0 or higher; refer to the CoPilot
Software User Guide for setup information.
2. Software Setup Version 8/9.xx
The LS-QTTB-J/K will appear in the Sensor
Locations 1tool for initial setup in the
eDART version 9.xx software.
• Select the Sensor Type 2from the
drop-down menu; if the module has not
1
2 3 4
5
previously been configured, all four
channels will be assigned as “Mold
temperature” with no Sensor Location
assigned.
• Select the Sensor Location 3from the
drop-down menu.
• Enter the associated sensor’s cavity
number 4in the Identification column (if
two or more sensors are set to the same
Sensor Location).
• Select the Accept 5button to save
settings.

Lynx™ Quad Temperature Modules LS‑QTTB‑J & LS‑QTTB‑K | Product Manual
8
3. Software Setup Version 10.xx
The LS-QTTB-J/K and associated sensor
may be set up during the Machine Setup/
Inputs or Mold Setup/Inputs 1in the
eDART version 10.xx software.
There are multiple sensor types and
corresponding sensor location options
depending upon the desired application;
ensure that the desired sensor type and
location match the assigned sensor type
and location.
MACHINE INPUT SETUP
• Click, drag, and drop the associated
sensor from the Available Sensors 2
INSTALLATION SPECIFICATIONS (continued)
list into the Other Sensors 3machine
location listed on the left to designate
the sensor type; a window to specify
the sensor location will appear when
selected; select Barrel Temperature 4.
• The configuration window 5will open;
select the desired sensor location from
the drop-down box 6; locations include
barrel nozzle, front, center, feed throat,
rear, and description not available (used
for dryer temperature).
1
2
3
4
5
6

Product Manual | Lynx™ Quad Temperature Modules LS‑QTTB‑J & LS‑QTTB‑K 9
INSTALLATION SPECIFICATIONS (continued)
1
8
9
7
MOLD INPUT SETUP
• Click, drag, and drop the associated
sensor from the Available Sensors 7
list into the Mold Sensors 8machine
location or the desired cavity 9listed on
the left to designate the sensor type; a
window to specify the sensor location will
appear when selected.
• For mold sensors 10 , runner, surface,
parting line, sprue, or coolant
temperature can be selected; for cavity
types 11 , end-of-cavity, mid-cavity, or
post-gate locations can be selected.
10
11

Lynx™ Quad Temperature Modules LS‑QTTB‑J & LS‑QTTB‑K | Product Manual
10
NOTES

Product Manual | Lynx™ Quad Temperature Modules LS‑QTTB‑J & LS‑QTTB‑K 11
PRODUCT DISCLAIMER
RJG, Inc. is not responsible for the
improper installation of this equipment, or
any other equipment RJG manufactures.
Proper RJG equipment installation does
not interfere with original equipment
safety features of the machine. Safety
mechanisms on all machines should never
be removed.
MAINTENANCE
CLEANING
Keep sensor pocket, cable channel, and
sensor components free from oil, dirt,
grime, and grease.
TESTING & CALIBRATION
Thermocouples are known to have drift
in calibration dependent upon time and
temperature. To test calibration, check
the thermocouple output against the
thermocouple rating and electromagnetic
field (EMF) tables in a known temperature
source.
WARRANTY
RJG, INC. STANDARD WARRANTY
RJG, Inc. is confident in the quality
and robustness of the LS-QTTB-J and
LS-QTTB-K, and so are offering a one-year
warranty. RJG’s Lynx quad temperature
modules are guaranteed against defects
in material and workmanship for one year
from the original date of purchase. The
warranty is void if it is determined that the
adapter was subjected to abuse or neglect
beyond the normal wear and tear of field
use, or in the event the adapter box has
been opened by the customer.

Lynx™ Quad Temperature Modules LS‑QTTB‑J & LS‑QTTB‑K | Product Manual
12
NOTES

Product Manual | Lynx™ Quad Temperature Modules LS‑QTTB‑J & LS‑QTTB‑K 13
TROUBLESHOOTING
MEASUREMENT ERRORS
Errors in measurement can result from
connection problems, lead resistance
issues, or electrical noise.
CONNECTION PROBLEMS
Connections must be clean and free from
oil, dirt, grime, and grease.
If shielded wire is used, the wire must run
under the LS-QTTB-J/K shield plate ( 1&
2at right. The shield plate should be
tightened and have good contact with the
shielded thermocouple wire to reduce RF
noise susceptibility.
WIRE EXTENSIONS
Thermocouple wires are typically thin,
and have a high resistance, making them
sensitive to noise. If extra wire is needed,
use thermocouple extension wire between
the thermocouple and measurement
instrument. Thermocouple wire is much
thicker and thus has a lower resistance.
NOISE
Electromagnetic interference (EMI), or RF, is
caused by electric devices such as motors,
and can result in measurement reading
errors. If noise is suspected, turn off all
equipment that is suspect while monitoring
the reading to determine the source.
Thermocouples and wiring can short or
open circuit, causing error in signals.
Check the thermocouple with a standard
volt meter across the positive and
negative leads to determine if the circuit is
functioning correctly.
1
2

Lynx™ Quad Temperature Modules LS‑QTTB‑J & LS‑QTTB‑K | Product Manual
14
INSTALLATION ERRORS
REVERSED CONNECTIONS
Connections must not be reversed ( 1&
2at right. Reversed leads will provide
a reading which will vary in the opposite
direction relative to ambient temperature.
LOOSE CONNECTIONS
Ensure connections are firmly in place, but
are no over-tightened. Over tightening may
crush the wires.
1
2
This manual suits for next models
1
Table of contents
Other RJG Control Unit manuals
Popular Control Unit manuals by other brands

LEYBOLD
LEYBOLD LEYCON BAV P AL Series user manual
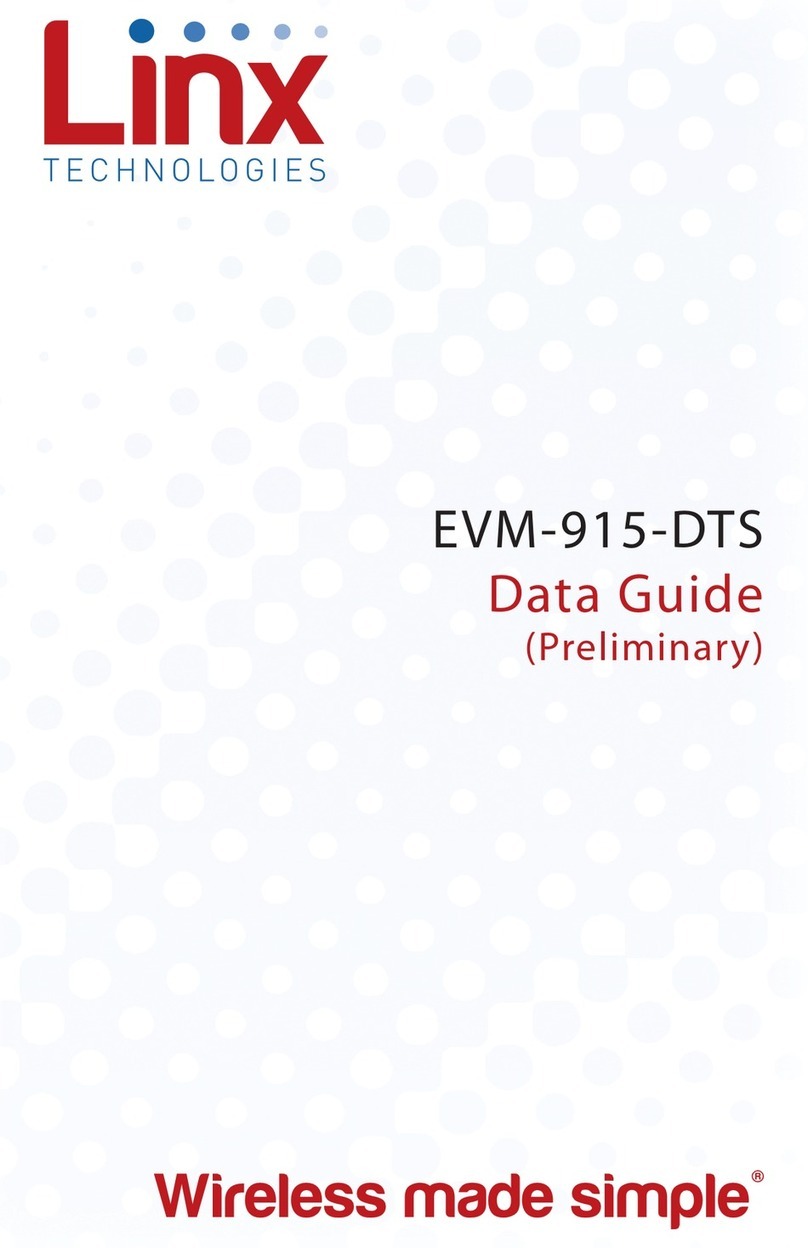
Linx
Linx EVM-915-DTS-FCR Data guide
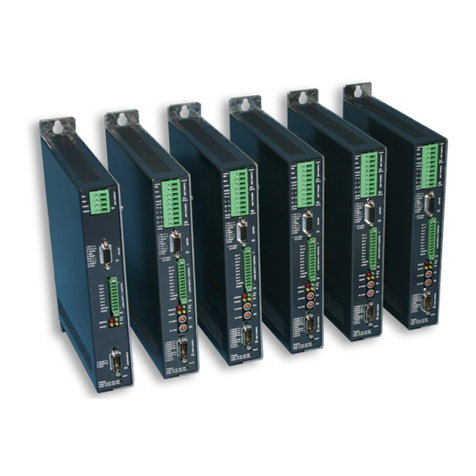
LinMot
LinMot E1100 Series user manual
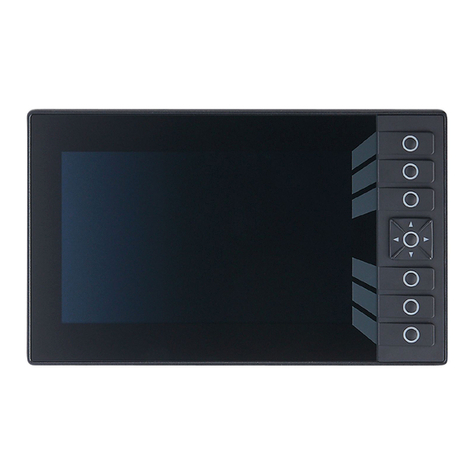
IFM
IFM ecomatDisplay CR1077 operating instructions
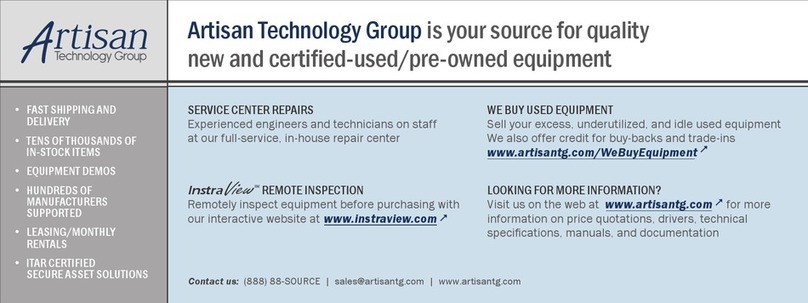
Rockwell Automation
Rockwell Automation Allen-Bradley FLEX Integra user manual
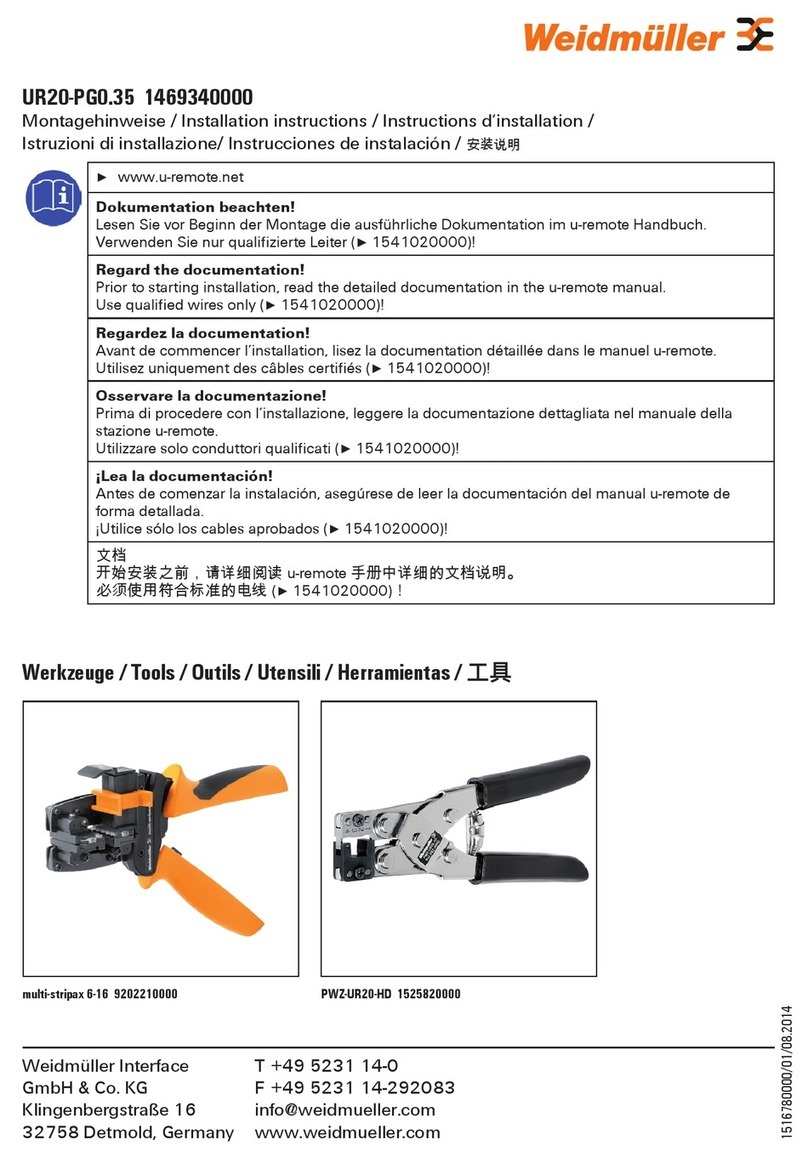
Weidmuller
Weidmuller UR20-PG0.35 installation instructions
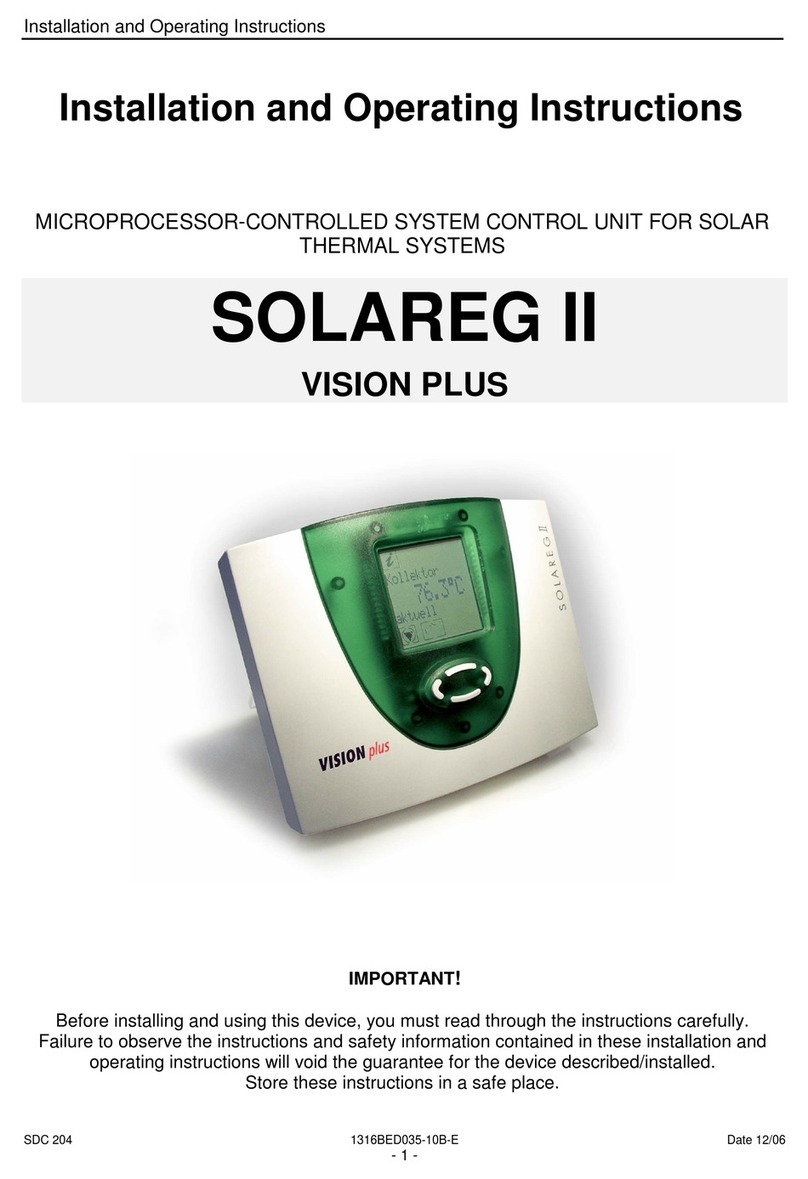
Prozeda
Prozeda SOLAREG II VISION plus Installation and operating instructions
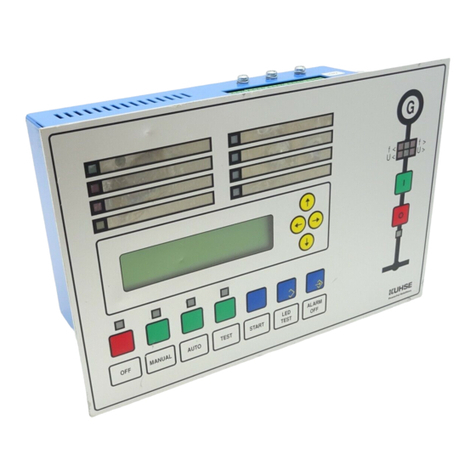
Kuhse
Kuhse KEA 101 NSTR Service manual
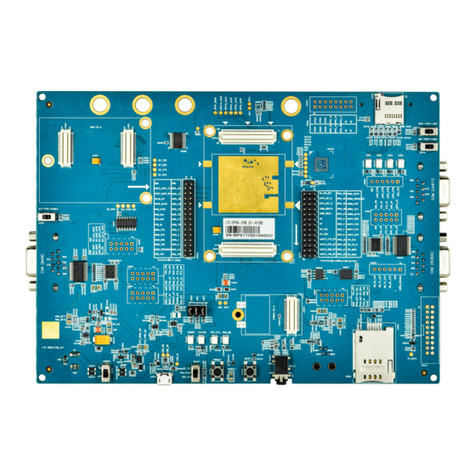
Quectel
Quectel LTE OPEN EVB user guide
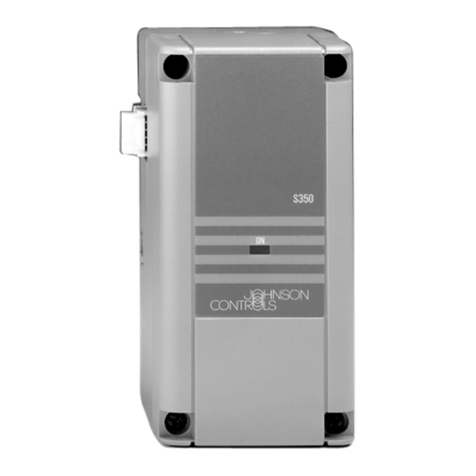
Johnson Controls
Johnson Controls System 350 Technical bulletin

DOLD
DOLD SAFEMASTER PRO UG 6951 user manual
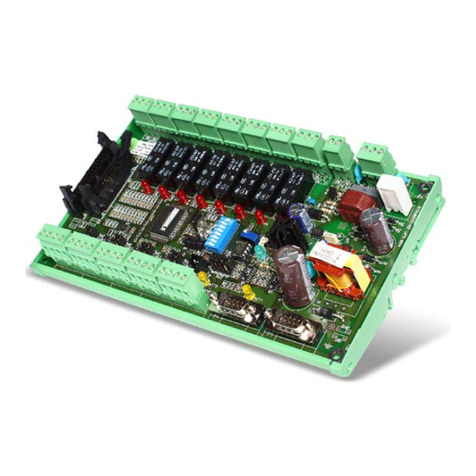
Riello UPS
Riello UPS Multi I/O Series user manual