RJG Lynx ID7-M-SEQ User manual

PRODUCT MANUAL
Training and Technology for injecTion Molding
Lynx™ Shielded Sequence Module
ID7‑M‑SEQ

PRINT DATE 12.16.2019
REVISION NO. 0

Product Manual | Lynx™ Shielded Sequence Module ID7‑M‑SEQ RJG, Inc. i
PRODUCT MANUAL
Lynx™ Shielded Sequence Module
ID7‑M‑SEQ
INTRODUCTION
DISCLAIMER III
PRIVACY III
ALERTS III
PRODUCT DESCRIPTION
APPLICATIONS 1
PROCESS MONITORING AND CONTROL 1
OPERATION 2
MACHINE SEQUENCE SIGNALS 2
eDART SEQUENCE SIGNALS 4
DIMENSIONS 5
CABLE LENGTHS 5
INSTALLATION
INSTALLATION OVERVIEW 7
ID7‑M‑SEQ 7
eDART CONNECTION 7
INSTALLATION SPECIFICATIONS 8
REQUIREMENTS 8
MOUNTING 8
WIRING 9
CONNECTIONS 10

Lynx™ Shielded Sequence Module ID7‑M‑SEQ | Product Manual
ii RJG, Inc.
MAINTENANCE
CLEANING 11
REGULAR CLEANING 11
TESTING 11
eDART VERSION 9.XX SOFTWARE 11
eDART VERSION 10.XX SOFTWARE 11
RJG, INC. STANDARD WARRANTY 11
PRODUCT DISCLAIMER 11
TROUBLESHOOTING
COMMON ERRORS 13
SIGNAL ERRORS 13
ACCEPTABLE SIGNAL SUBSTITUTIONS 14
CUSTOMER SUPPORT 15
RELATED PRODUCTS
COMPATIBLE PRODUCTS 17
SHIELDED SEQUENCE MODULE CABLE C‑ID7‑M‑3M 17
LYNX CABLES CE‑LX5 17
eDART PROCESS CONTROLLER 17
SIMILAR PRODUCTS 18
LYNX COMMUNICATIONS ADAPTER
DIN/LX‑D 18
LYNX SHIELDED DUAL‑RELAY OUTPUT MODULE OR2‑M 18
LYNX SHIELDED ANALOG INPUT MODULE IA1‑M‑V 18
PRODUCT MANUAL
lynx™ Shielded Sequence Module
ID7‑M‑SEQ

Product Manual | Lynx™ Shielded Sequence Module ID7‑M‑SEQ RJG, Inc. iii
INTRODUCTION
Read, understand, and comply with all following
instructions. This guide must be kept available
for reference at all times.
DISCLAIMER
Inasmuch as RJG, Inc. has no control over the
use to which others may put this material, it
does not guarantee that the same results as
those described herein will be obtained. Nor
does RJG, Inc. guarantee the effectiveness or
safety of any possible or suggested design for
articles of manufacture as illustrated herein by
any photographs, technical drawings, and the
like. Each user of the material or design or
both should make his own tests to determine
the suitability of the material or any material
for the design as well as the suitability of the
material, process, and/or design for his own
particular use. Statements concerning possible
or suggested uses of the material or designs
described herein are not to be construed as
constituting a license under any RJG, Inc. patent
covering such use or as recommendations
for use of such material or designs in the
infringement of any patent.
PRIVACY
Designed and developed by RJG, Inc. Manual
design, format and structure copyright 2018
RJG, Inc. content documentation copyright
2018 RJG, Inc. All rights reserved. Material
contained herein may not be copied by hand,
mechanical, or electronic means, either whole
or in part, without the express written consent
of RJG, Inc. Permission will normally be granted
for use in conjunction with inter‑company use
not in conflict with RJG’s best interests.
ALERTS
The following three alert types are used as
needed to further clarify or highlight information
presented in the manual:
Term
A definition of a term or terms used in the
text.
NOTE A note provides additional information
about a discussion topic.
CAUTION A caution is used to make the
operator aware of conditions that can cause
damage to equipment and/or injury to personnel.

Lynx™ Shielded Sequence Module ID7‑M‑SEQ | Product Manual
iv RJG, Inc.

Product Manual | Lynx™ Shielded Sequence Module ID7‑M‑SEQ RJG, Inc. 1
PRODUCT DESCRIPTION
The Lynx™ shielded sequence module is a
DIN‑rail‑mounted module that is wired to the
molding machine in order to collect 24 V DC
timing signals for use with the eDART®system,
including injection forward, screw run, mold
closed/clamped, first stage, and mold opening.
The use of an ID7‑M‑SEQ (or a
DIN/LX‑D) module is required to physically
connect to the eDART system.
APPLICATIONS
PROCESS MONITORING AND CONTROL
The eDART system requires various inputs
from the injection molding machine in order to
accurately calculate significant process values for
monitoring and control.
The ID7‑M‑SEQ gathers the machine sequence
state signals from the injection molding machine
for the eDART.
The eDART performs computations using
the machine sequence state signals from the
injection molding machine for various process
parameters during a typical cycle. In order for
these to be accurate, the eDART generates
internal machine sequence signals. These
sequences are not necessarily wired to the
sequence module, but can be created from
signals collected from the module.
For example, the plastic cooling machine
sequence is not directly derived from the
molding machine, instead it is calculated by the
eDART using the mold open signal—a machine‑
outputted sequence signal.

Lynx™ Shielded Sequence Module ID7‑M‑SEQ | Product Manual
2 RJG, Inc.
OPERATION
MACHINE SEQUENCE SIGNALS
The ID7‑M‑SEQ collects up to seven machine
sequence signals from the following: injection
forward, first stage, second stage, screw run,
mold closed/clamped, mold opening, mold
closing, machine in manual mode, machine in
auto or semi‑auto mode, shuttle position, and
DC common.
The eDART requires, at minimum, the injection
forward, screw run, and mold closed/clamped
signals from the injection molding machine/
ID7‑M‑SEQ. It is critical that the selected signals
are correct for the eDART to properly calculate
summary values.
1. Injection Forward
Injection forward is the first portion of the
molding cycle, during which the ram is being
pushed forward; it begins when the injection
unit starts to push plastic into the mold and
ends when it stops applying pressure (when
hold begins).
The eDART uses the injection forward signal
as the start of the cycle. Without the injection
forward signal, the eDART assumes the machine
has stopped.
The eDART computes injection integrals while
the injection forward signal is on, ignores peaks
in cavity pressures after injection forward is
off (a selectable setting), computes hold time,
hold pressure, and various other items (detailed
below). Injection forward is used by controls
such as V→P transfer, shuttle, basic three‑stage,
and valve gate to cause the eDART to take
certain actions.
2. First Stage
First stage is the portion of the molding cycle
during which the machine is injecting; it begins
when injection starts, and ends when transfer
beings.
3. Second Stage
Second stage is the portion of the molding
cycle during which the machine transfers from
injection to hold pressure; it begins when
transfer starts, and ends when hold ends/
recovery begins.

Product Manual | Lynx™ Shielded Sequence Module ID7‑M‑SEQ RJG, Inc. 3
4. Screw Run
Screw run is the portion of the molding cycle
during which the machine begins to rotate the
screw to build the next shot; it beings when
recovery begins and ends when recovery ends
(the next shot has been built).
5. Mold Closed/Clamped
The mold closed/clamped signal indicates when
the mold is closed during a cycle. If the signal is
on only when the mold is clamped, assign it as
“mold closed/clamped”. If the signal is on when
the mold is closing, assign it as “mold closing”.
6. Mold Opening
The mold opening signal indicates when the
mold is opening during a cycle. If the signal is
on when the mold is opening, assign it as “mold
opening”.
7. Manual
The “manual” signal is assigned to indicate the
machine’s current operational mode—machine
in manual (mode). The signal must be on only
when the machine is in manual mode, and must
turn off when it is in auto or semi‑auto mode.
This enables the operator to verify that the
other sequence signals are correctly wired and
assigned by cycling the different functions while
in manual mode to verify that the corresponding
sequence signal module light is activated.
8. Shuttle Position
The shuttle position signal (for use with shuttle
molding tables only) indicates to the eDART in
which position the table is currently—Shuttle
Position A, B, C, etc.
OPERATION (continued)

Lynx™ Shielded Sequence Module ID7‑M‑SEQ | Product Manual
4 RJG, Inc.
eDART SEQUENCE SIGNALS
The eDART can calculate the following
sequences from the aforementioned,
hard‑wired machine sequence signals. These
sequences will vary based on the available hard‑
wired signals provided from the machine.
1. Fill
The fill signal is generated by the eDART
from machine signals; fill will go on as the
screw passes through the position to which
it recovered just before decompress and will
go off when the second‑to‑last velocity profile
begins.
If the fill signal is not available on the machine,
the eDART generates it, turning it on at the zero
point of shot volume and off at a selected fill
threshold in the sequencer.
If the fill button is greyed out (version 9
software/Sequence Lights tool), the eDART
cannot generate fill.
2. Pack
The pack signal is generated by the eDART from
hard‑wired machine signals; the pack signal will
go on at the end of fill, and is turned off by the
eDART, which uses the transfer pressure set
in cavity pressure control. If cavity pressure
control is not in use, pack will only exist if the
fill signal is considered to be a fill and pack
combined signal.
OPERATION (continued)
If the pack button is greyed out (version 9
software/Sequence Lights tool), the eDART
cannot generate pack.
3. Hold
The hold signal is generated by the eDART from
hard‑wired machine signals; the eDART turns on
the hold signal at the end of pack or, if there is
no pack, at the end of fill. It then turns it off at
the end of injection forward.
If the hold button is greyed out (version 9
software/Sequence Lights tool), the eDART
cannot generate hold.
4. Plastic Cooling
The plastic cooling signal is generated by the
eDART from hard‑wired machine signals; the
eDART turns the plastic cooling signal on at
the end of fill and turns it off on one of the
following (listed in order of priority):
• mold open goes on
• mold closed/clamped goes off (if there is no
mold open)
• screw run goes off (neither mold open nor
mold closed/clamped exist)
If the Plastic Cooling button is greyed out
(version 9 software/Sequence Lights tool), the
eDART cannot generate plastic cooling.

Product Manual | Lynx™ Shielded Sequence Module ID7‑M‑SEQ RJG, Inc. 5
DIMENSIONS
CABLE LENGTHS
The C‑ID7‑M‑3M is 9.8 ft. (3 m) long.
CABLE LENGTH

Lynx™ Shielded Sequence Module ID7‑M‑SEQ | Product Manual
6 RJG, Inc.

Product Manual | Lynx™ Shielded Sequence Module ID7‑M‑SEQ RJG, Inc. 7
INSTALLATION
INSTALLATION OVERVIEW
The shielded machine interface modules are
mounted to a solid surface, such as the machine
frame, inside the molding machine on a DIN
rail.
ID7‑M‑SEQ
The shielded machine sequence module cable
C‑ID7‑M‑3M is wired directly to the machine
(usually to an output card) on one end and
connected to the ID7‑M‑SEQ on the other
using the eight‑pin connector.
eDART CONNECTION
A Lynx cable CE‑LX5 is connected to the Lynx
port on the ID7‑M‑SEQ and a Lynx port on
the eDART to provide it with the machine’s
sequence signals for process monitoring and
control calculations, along with the other
installed machine interface module signals.
C‑ID7‑M‑3M CABLE TO MACHINE
CE‑LX5 CABLE TO eDART

Lynx™ Shielded Sequence Module ID7‑M‑SEQ | Product Manual
8 RJG, Inc.
INSTALLATION SPECIFICATIONS
The instructions that follow are a general guide; actual steps necessary to install this product will
vary based on injection molding machine manufacturer, model, and options.
REQUIREMENTS
At minimum, the following signals must be wired
to the module:
• injection forward,
• screw run, and
• mold closed/clamped.
If the machine sequence signals are wired
and assigned correctly, the eDART system’s
sequencer function easily calculates accurate
machine signals. If the signals do not exist, the
eDART can calculate some machine sequence
signals, but may require the user to input
settings.
If the signals are misnamed, or do not go on and
off as specified, the system‑generated machine
sequence signals will likely be incorrect, as
will the data calculated from them. Refer to
“Machine Sequence Signals” on page 2 and
“Wiring” on page 9 for more information on
sequence signals and acceptable substitutions (if
applicable).
MOUNTING
CAUTION Before beginning ID7‑M‑SEQ
installation, disconnect and lockout/tag‑out any
and all power to the molding machine. Failure to
comply will result in personal injury or death, and
damage or destruction of equipment.
Mount the ID7‑M‑SEQ module to a solid
surface—such as the molding machine frame—
using the supplied 1.38” (35 mm) DIN rail. A
clearance height of 6” (152,4 mm) from the face
of the module is recommended.
NOTE Modules and connecting cables must
be located away from any static sources, such as
feeder tubes and material hoppers.

Product Manual | Lynx™ Shielded Sequence Module ID7‑M‑SEQ RJG, Inc. 9
WIRING
The following table details machine sequence signals wiring and functions.
SIGNAL WIRING ON OFF PURPOSE REMARKS
Injection
Forward IF Injection
Starts End of Hold
Primary signal for fill, pack, and
hold times calculation; also peak
injection pressure and effective
viscosity calculations.
A form of this signal is required.
If no injection forward signal
is present, the cycle graph will
not refresh; will not calculate
integral values.
First Stage 1ST Start of Fill Transfer to
Hold
Calculates fill time in DII
processes; calculates injection
forward if signal is not available.
Fill time can be created by
manually setting the Fill Volume
at Cursor function on the
eDART with only the injection
forward signal.
Second
Stage
any
unused
Switch
to Hold
(Pressure)
End of Hold
Calculates hold time; calculates
injection forward if signal is not
available.
Calculates more accurate
hold time, hold pressure, and
average hold pressure.
Screw Run SR
Screw
Motor
Starts
Screw
Motor Stops
Calculates screw run on time;
detects stroke direction; zeroes
plastic volume at cycle.
This signal is required.
Mold
Closed/
Clamped
MC
Mold
Clamped
to High
Tonnage
Mold Begins
to Open
Primary signal for cycle time
calculation; zeroing of sensors,
cycle reset for piezoelectric
equipment.
This signal is required.
Mold
Opening MO Mold Begins
to Open
Mold Fully
Open
Cycle reset for piezoelectric
equipment.
Pinched part detection when
used in conjunction with a part
diverter.
Mold
Closing
any
unused
Mold Begins
to Close
Mold
Clamps
Calculates cycle time when mold
closed/clamped is not available;
zeroing of sensors, cycle reset
for piezoelectric equipment.
Zeroing of sensors when mold
closed/clamped signal is not
available.
Manual
Mode MAN
Machine
in Manual
Mode
Machine
in Auto or
Semi‑Auto
Mode
Enables the average cycle time
calculation to discard time the
machine spends in manual mode.
May allow valve gates to open
to purge through manifold in
this mode.
Shuttle
Position SHTL
Start of
Cycle at
Position 2
Start of
Cycle at
Position 1
Detects rotary table position in
shuttle molding applications.
The eDART shuttle control
software uses this signal to
identify which position is active
for use with template control,
alarm outputs, and summary
value calculation.
INSTALLATION SPECIFICATIONS (continued)

Lynx™ Shielded Sequence Module ID7‑M‑SEQ | Product Manual
10 RJG, Inc.
NOTE The following required signals may be
obtained from a machine output card.
Confirm the machine’s sequence output card
can supply a reliable 24 V signal. Input for all
signals 24 V ON; 0 V OFF. Maximum Input
Voltage 36 V; Minimum Trigger‑On Voltage
18 V. Wire the machine sequence signals to the
module cable C‑ID7‑M‑3M.
NOTE Note the signals which are wired to the
machine for future software setup and use.
The C‑ID7‑M‑3M cable has colored‑coded
wires to simplify installation. Refer to the table
below for the correct wire/signal combinations
for installation.
SIGNAL WIRING COLOR
Injection
Forward IF Blue
First Stage 1ST Blue or Pink
Second Stage any
unused any unused
Screw Run SR Red
Mold
Clamped MC Brown
Mold
Opening MO Yellow
Mold Closing any
unused any unused
Manual Mode MAN White
Shuttle
Position SHTL Green
INSTALLATION SPECIFICATIONS (continued)
CONNECTIONS
Connect the C‑ID7‑M‑3M cable to the
ID7‑M‑SEQ module. Connect the ID7‑M‑SEQ
to the JLX‑1 junction using the CE‑LX5‑2M
Lynx cable.
C‑ID7‑M‑3M CABLE WIRING

Product Manual | Lynx™ Shielded Sequence Module ID7‑M‑SEQ RJG, Inc. 11
MAINTENANCE
The shielded sequence module requires little
to no maintenance provided that all installation
instructions are followed.
CLEANING
REGULAR CLEANING
Cables must be installed in areas free from oil,
dirt, grime, and grease.
RJG, Inc. recommends the following cleaners:
• Microcare MCC‑CCC Contact Cleaner C
• Microcare MCC‑SPR SuprClean™
• Miller‑Stephenson MS‑730L Contact Re‑Nu®
TESTING
Test the ID7‑M‑SEQ inputs after assignment
using the Sequence Lights/Sequence Inputs tool
in eDART version 9.xx software, or in Machine
Setup/Test Inputs in eDART version 10.xx
software, or utilize the integrated LED on the
ID7‑M‑SEQ to verify that the corresponding
light goes on/off for the machine sequence.
eDART VERSION 9.XX SOFTWARE
The Sequence Lights tool displays what stage of
the process is taking place showing the on/off
status of machine sequences. If a “light” is on,
then the signal is on; if a “light is off, the signal is
off. The Sequence Lights tool displays machine
sequences that are not necessarily wired to
the sequence module. To view the status of
the hard‑wired sequence signals, select the
Sequence Inputs inputs button on the Sequence
Lights tool.
Similarly, the Sequence Inputs tool displays the
hard‑wired signals statuses. With the machine in
manual mode, cycle the machine while watching
to verify that the corresponding “light” goes on/
off for the machine sequence.
eDART VERSION 10.XX SOFTWARE
The Machine Setup/Test Inputs function displays
the hard‑wired signal statuses. With the
machine in manual mode, cycle the machine
while watching to verify that the corresponding
“light” goes on/off for the machine sequence.
WARRANTY
RJG, INC. STANDARD WARRANTY
RJG, Inc. is confident in the quality and
robustness of the shielded machine interface
modules, and so are offering a one‑year
warranty. RJG’s products are guaranteed against
defects in material and workmanship for one
year from the original date of purchase. The
warranty is void if it is determined that the
adapter was subjected to abuse or neglect
beyond the normal wear and tear of field
use, or in the event the adapter box has been
opened by the customer.
PRODUCT DISCLAIMER
RJG, Inc. is not responsible for the improper
installation of this equipment, or any other
equipment RJG manufactures.
Proper RJG equipment installation does not
interfere with original equipment safety features
of the machine. Safety mechanisms on all
machines should never be removed.

Lynx™ Shielded Sequence Module ID7‑M‑SEQ | Product Manual
12 RJG, Inc.

Product Manual | Lynx™ Shielded Sequence Module ID7‑M‑SEQ RJG, Inc. 13
TROUBLESHOOTING
COMMON ERRORS
SIGNAL ERRORS
1. Signal(s) do not appear on module test
lights
Any signals that never appear “on” must be
named “Not Used”, even if wired to the
module. In eDART version 9.xx software Sensor
Locations tool, assign the Sensor Location as
“Not Used”. In eDART version 10.xx software
Machine Setup/Inputs, the ID7‑M‑SEQ will
automatically assign itself in the Sequence Signal
(ID7) box; select the “i” to open the Locations
selector, then select “Not Used” for a signal(s).
2. Signal(s) are unknown
If a signal does go on and off but is unknown,
then name it “Unknown” and review it later
(with the cycle graph or sequence lights
functions).
Signals that have been assigned and have lights
that go on and off at the wrong time must be
corrected. In eDART version 9.xx software
Sensor Locations tool, select the correct
signal name. If none of the signal names listed
correlate to the signal, then select “Not Used”
(or “Unknown” to review it later).
3. Injection forward signal
On some machines the injection forward
signal may not perform as specified; the
eDART sequencer can adjust for some of
these abnormalities. For example, if the screw
run signal is available it will reject additional
injection forward on signals until after the screw
stops.
With other problems, such as a half‑second
variation of the start of injection signal from shot
to shot, or signal “bounce” at the beginning that
causes the eDART to read the injection forward
was on for a quarter of a second.
In eDART software version 9.xx, use the
“Sequence Settings” “Injection” page:
• If the start of the signal is unreliable, select the
“Ignore Injection Forward Sequence Module
Input at Start”. The eDART will use screw
motion (or injection pressure, if no screw) to
determine the start.
• If the end of injection is not stable, or does
not go off at the end of injection, select the
“Ignore Injection Forward Sequence Module
Input at End”. The eDART will use the falling
pressure (corner or threshold) to determine
where injection ends.
• If no Screw Run signal is available, then the
“Ignore Injection Forward OFF→ON” setting
may need to be adjusted if the injection
forward signal comes on twice. Set the
“ignore” time long enough so that the eDART
does not detect the second event.
Each of these settings are saved with the
machine; the settings only have to be applied
once on a machine and are saved with the
setup.

Lynx™ Shielded Sequence Module ID7‑M‑SEQ | Product Manual
14 RJG, Inc.
ACCEPTABLE SIGNAL SUBSTITUTIONS
1. No injection forward signal
If the injection forward signal is not available the
eDART uses several techniques determine when
injection forward is on. In lieu of an injection
forward signal, the following may be used as a
substitute (in descending order of quality):
• Wired and assigned first stage or second stage
sequence input signals
• Screw motion forward/falling edge of injection
pressure (detected by eDART)
• Screw motion forward/screw motion
backward for a time (detected by eDART)
• Injection pressure thresholds (detected by
eDART)
• Mold clamped plus a set time to turn on and
a set injection forward on time (detected by
eDART)
2. No mold closed/clamped signal
If no mold closed/clamped signal is available,
but both mold opening and mold closing are
available, then the sequencer will create the
mold closed/clamped signal from those two.
It will use the end of mold closing for mold
closed/clamped on and the start of mold
opening for mold closed/clamped off.
3. No machine‑in‑manual signal
If a machine‑in‑semi‑auto mode or
machine‑in‑auto mode signal is hard‑wired
and assigned, then the sequencer inverts it and
creates an internal machine‑in‑manual mode
signal.
4. No screw run signal available
If no screw run signal is available, refer to the
eDART version 9.xx or eDART version 10.xx
software manuals for more information and
instructions for screw run setup.
Table of contents
Other RJG Control Unit manuals
Popular Control Unit manuals by other brands
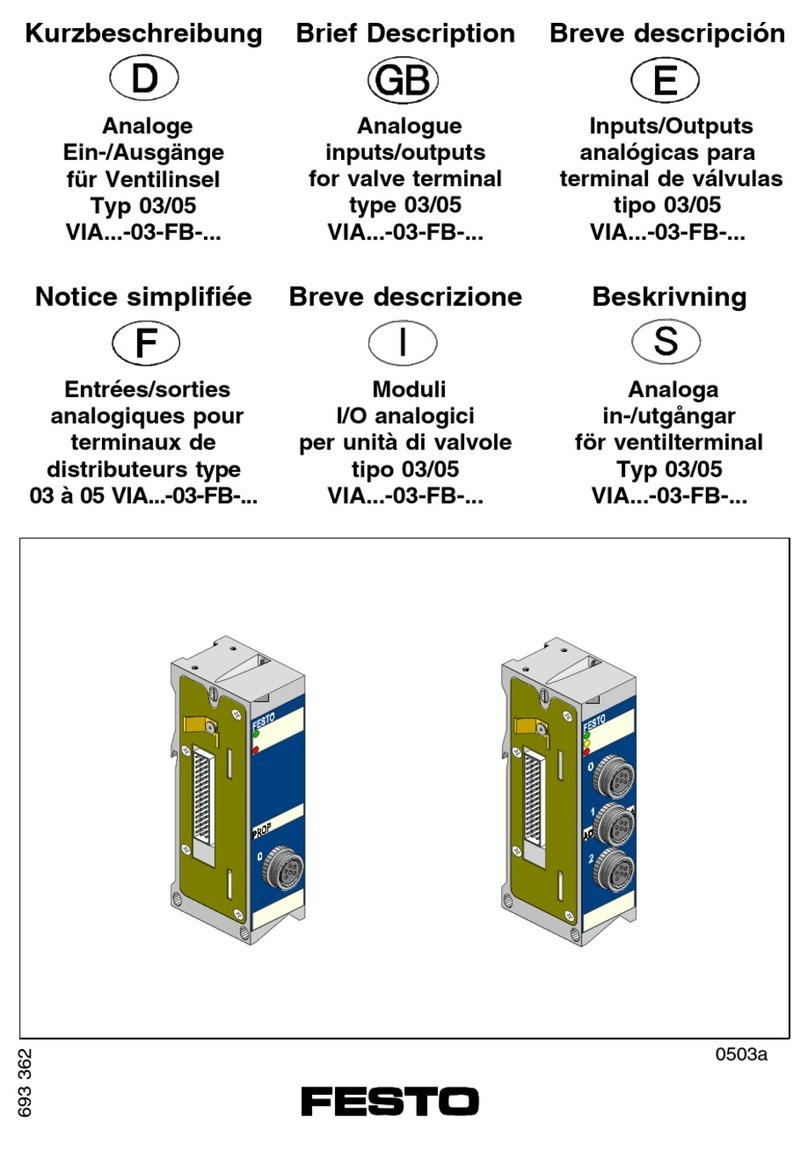
Festo
Festo VIA 03-FB Series Brief description
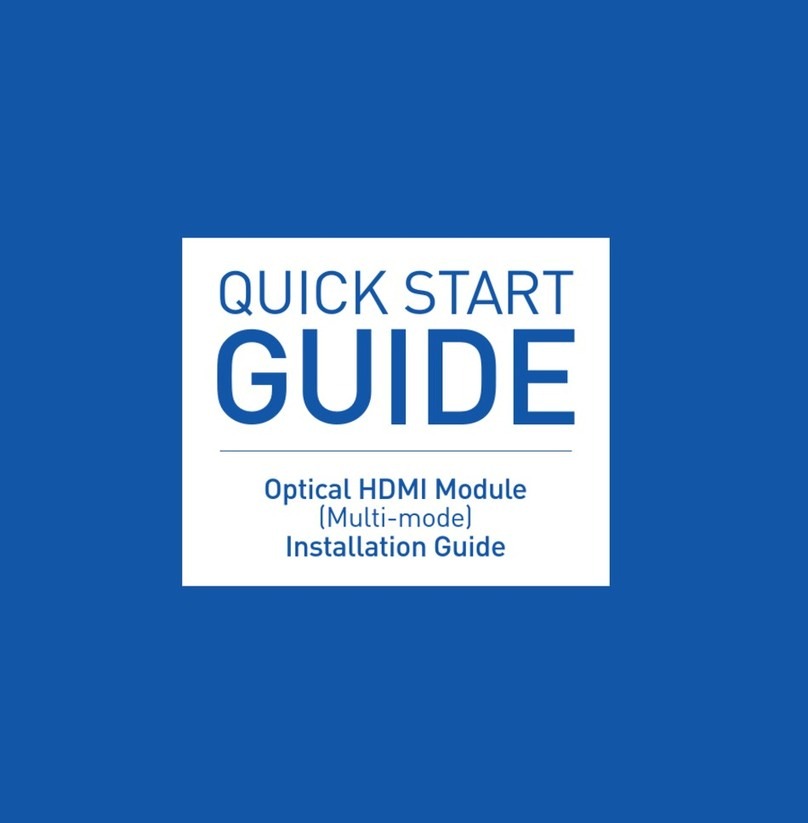
Clarion
Clarion HMML-0034K3 quick start guide
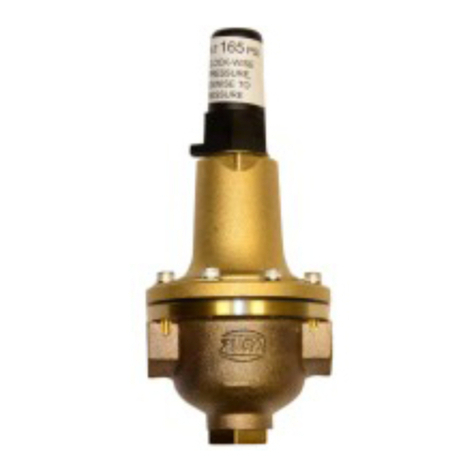
ZURN
ZURN WILKANS PV-PRD quick start guide
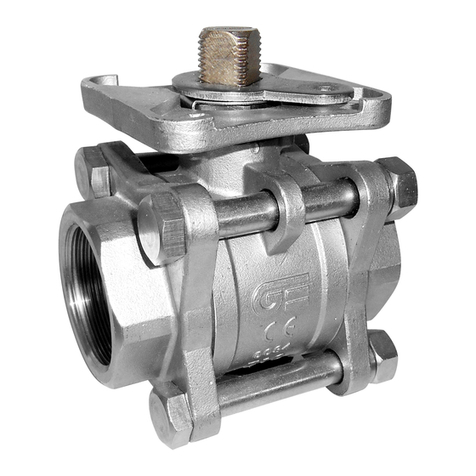
OMAL S.p.A
OMAL S.p.A 424 Series Maintenance and spare parts

Allen-Bradley
Allen-Bradley Series B user manual
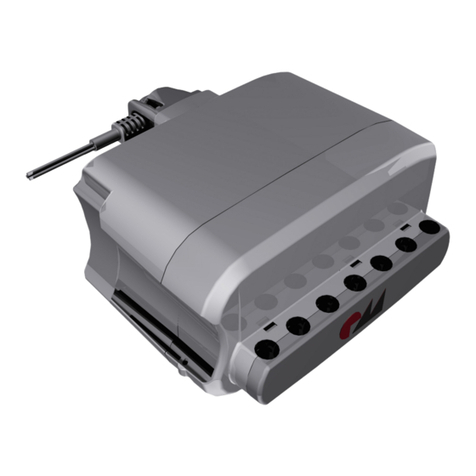
Phoenix Mecano
Phoenix Mecano DewertOkin MC11 installation instructions