Robot Pumps RS Series Manual

782-020-GB HS 09-W46 Edition 4
OPERAOPERA
OPERAOPERA
OPERATIONTION
TIONTION
TION
&&
&&
&
MAINTENMAINTEN
MAINTENMAINTEN
MAINTENANCE MANUANCE MANU
ANCE MANUANCE MANU
ANCE MANUALAL
ALAL
AL
RS-SERIESRS-SERIES
RS-SERIESRS-SERIES
RS-SERIES
www.robotpompen-onderdelen.nl
T +31(0)294-457712

Operation &
Maintenance Manual
Pump
RS
782-020-GB HS 09-W46 Edition 4 3/26
Contents............................................................................................................................... page
1. FOREWORD................................................................................................................. 4
2. GUARANTEE ............................................................................................................... 4
3. SAFETYAND ENVIRONMENT .................................................................................... 5
3.1 Symbols ............................................................................................................................................... 5
3.2 General safety instructions................................................................................................................... 5
3.3 Environment......................................................................................................................................... 5
4. TECHNICALDATA ....................................................................................................... 6
4.1 General ................................................................................................................................................ 6
4.2 Main parts ............................................................................................................................................ 6
5. FIRST PUMP START.................................................................................................... 7
5.1 Delivery check...................................................................................................................................... 7
5.2 Oillevel ................................................................................................................................................. 7
5.3 Power supply........................................................................................................................................ 7
5.4 Thermoswitches ................................................................................................................................... 7
5.5 Cable entry........................................................................................................................................... 7
5.6 Motor protection ................................................................................................................................... 7
5.7 Motor check.......................................................................................................................................... 8
5.8 Installation parts ................................................................................................................................... 8
5.9 Direction of rotation.............................................................................................................................. 8
5.10 Current-check....................................................................................................................................... 8
5.11 Medium temperature / max. motorload ................................................................................................ 9
5.12 Start frequency...................................................................................................................................... 9
5.13 Min. and max. submersible depth ........................................................................................................ 9
6. INSTALLATION OPTIONS ........................................................................................... 10
6.1 Installation -H ....................................................................................................................................... 10
6.2 Installation -V ....................................................................................................................................... 11
6.3 Installation -F ....................................................................................................................................... 12
6.4 Installation -T ....................................................................................................................................... 12
7. MAINTENANCE............................................................................................................ 13
7.1 General ................................................................................................................................................ 13
7.2 Maintenanceschedule .......................................................................................................................... 13
7.3 Lubricants............................................................................................................................................. 13
7.4 Cable entry........................................................................................................................................... 14
7.5 Oil level................................................................................................................................................ 14
7.6 Oil change............................................................................................................................................ 15
7.7 Motor housing ...................................................................................................................................... 15
7.8 Adjustment suction cover-impeller-cutter............................................................................................. 15
8. TRANSPORT AND STORAGE..................................................................................... 16
9. OPTIONS...................................................................................................................... 17
9.1 Waterdetector ...................................................................................................................................... 17
9.2 Thermoswitches ................................................................................................................................... 17
9.3 Thermistors .......................................................................................................................................... 17
9.4 Cable protection ................................................................................................................................... 18
9.5 Special oil ............................................................................................................................................. 18
9.6 Special tool ........................................................................................................................................... 18
10. TROUBLE SHOOTING ................................................................................................ 19
APPENDIX 1; Dataplate ....................................................................................................... 20
APPENDIX 2; Direct-on-line start motor ............................................................................ 21
APPENDIX 3; Star-delta start motor ................................................................................... 23
APPENDIX 4; Single phase start ........................................................................................ 25
APPENDIX 5; Notes ............................................................................................................. 26
www.robotpompen-onderdelen.nl
T +31(0)294-457712

Operation &
Maintenance Manual
Pump
RS
782-020-GB HS 09-W46 Edition 4 5/26
3. SAFETYAND ENVIRONMENT
3.1 Symbols
* In this manual
General warning
Danger !
Electrical hazard !
Attention !
* On the pump
Danger of physical injury
Rotating parts !
Electrical hazard !
EC-conformity symbol
3.2 General safety instructions
* Onlytrained andauthorized personnel mayinstall and
maintain the pump after carefully reading this
manual.
* Only use the pump for its intended purpose and
under the regulated circumstances.
* Don’t go near rotating parts.
* Clean the pump before maintenance and inspection.
* Observe the local regulations when working with
agressive,corrossive, toxic, flammableandexplosive
chemicals.
* Never remove safety signs, keep them clean.
* Always connect to a grounded circuit.
* Before maintenance and inspection always
disconnect the pump from the mains.
* Use a proper hoist for lifting and handling the pump.
* Do not leave a large loop of cable in the sump,
as the pump may eventually damage it.
* Never drop the loose cable end in water.
The water may enter the cable and finally enter the
motorhousing, eventually causing motor failure.
3.3 Environment
Parts which are replaced during repair, maintenance or
renewal, could contain materials which could be harmful
to the environment.
Please take care in the disposal of these parts.
Do this in accordance with the local environmental
regulations.
www.robotpompen-onderdelen.nl
T +31(0)294-457712

Operation &
Maintenance Manual Pump
RS
6/26 Edition 4 HS 09-W46 782-020-GB
4. TECHNICALDATA
4.1 General
The RS-pump is a cast iron grinder pump designed to
pumpsmall quantityof water.
Large solids are cut into very small particles.
Thepump canbeused forsewageand othernon-
agressivewaste water applications.
The cutting device, installed in the suction opening,
effectively cuts larger solids into very small particles that
can easily pass through the pump.
1 Pumpcasing
2 Impeller
3 Cutting device
4 Suction cover
5 Delivery
6 Motorcasing
7 Rotor
8 Stator
9 Shaft
10 Bearings
11 Mechanical seal
(2x)
12 Oil reservoir
13 Oil plug
14 Cable entry
15 Cable
16 Inspection plug
4.2 Main parts
Construction:
- High efficiency motor, standard class F
insulation (up to 155oC).
- Two independent mechanical seals, running in oil,
form an effective barrier between pump and motor.
- Heavyduty bearings, greasedforlife.
- Hardened stainless steel grinder device, cutting
solids in small particles.
- Vanes at the backside prevent solids entering the
seal area and reduce the pressure on the seal.
Fig. 4.1
www.robotpompen-onderdelen.nl
T +31(0)294-457712

Operation &
Maintenance Manual
Pump
RS
782-020-GB HS 09-W46 Edition 4 7/26
5. FIRST PUMSTART
After unpacking the pump, carry out the following check
points:
5.1 Delivery-check
Check for possible transport damage and especially
check that the cable has not been nicked or
damaged.
Check for complete delivery.
When the delivery is incomplete or damaged, please,
contact your dealer immediately.
5.2 Oil level
Check the oil level. (see 7.5)
5.3 Power supply
Before making the electrical connections, check if
the line voltage and frequency are the same as on the
pump dataplate.
If thermostats are supplied make sure that they are
correctly connected.
For examples of electrical diagrams and pump
cable coding, see appendix 2, 3 and 4.
5.4 Thermoswitches
Check if the pump is equipped with thermoswitches
(optional).
Contact rating: max. 250V-1.6A
The contacts are normally closed.
5.5 Cable entry
Especially when the pump has been in store for a
long time, the cable gland should be checked and
if necessary tightened (see 7.4).
5.6 Motor protection
The pump should always be connected to the line by
means of a suitable motor protection circuitbreaker.
If the pump is started direct on line (DOL), the protection
breaker should be set to the current, as given on the
dataplate.
For star delta start (YD), it is good practice to install the
overcurrent relay directly after the main contactor. In this
case, the pump is also adequately protected in star-
connection. The maximum setting of the overcurrent
relay is 0.6x the current as given on the dataplate.
It is good practice to set the protection breaker at a 10%
lower current, because all breakers require at least
110% of the adjusted current before tripping.
www.robotpompen-onderdelen.nl
T +31(0)294-457712

Operation &
Maintenance Manual Pump
RS
8/26 Edition 4 HS 09-W46 782-020-GB
5.7 Motor check
If in doubt about the condition of the motor or cable,
Megger test motorwindings against grounding wire.
The phase resistance against grounding wire should be
at least 1 MOhm.
Turn the impeller clockwise by hand, using a proper
socket wrench (see fig.5.1)
This should be possible without much force.
With this procedure sticking mechanical seal
surfaces will be loosened smoothly.
5.8 Installation parts
Check if all components for your installation
are delivered. See also chapter 6.
5.9 Direction of rotation
A correct direction of rotation is essential for proper
operation. This can be checked as follows:
- Put the pump in horizontal position and start the
pump.
Looking on the impeller through the suction
opening, the correct direction of rotation is
counter-clockwise
(See arrow on pumpcasing, Fig. 5.2).
or:
- Starting the pump will give a recoil on the
pump frame.
Looking at the motor (in vertical position see
Fig. 5.3), the recoil is counter-clockwise.
Take care !
The recoil can be very powerful !
Don’tgo nearrotating parts!
5.10 Current-check
Notethe maximumcurrent fromthedataplate.
Apply an ammeter to one of the phase wires during
normaloperation. Checkthatthe current
is not higher than the value on the dataplate.
(see appendix 1). If so check for:
- voltage (too low ?)
- specific gravity or viscosity of the fluid
(too high ?)
- blocked impeller ?
- direction of rotation correct ?
If the problem cannot be solved contact your dealer.
Fig. 5.1
Fig. 5.2
Fig. 5.3
www.robotpompen-onderdelen.nl
T +31(0)294-457712

Operation &
Maintenance Manual
Pump
RS
782-020-GB HS 09-W46 Edition 4 9/26
5.11 Medium temp. / max.motorload
When the medium temperature is higher than 40oC, the
maximum motorload must be reduced.
The relationship between medium temperature and
maximum absorbed motor current is shown below.
Checkthe readingofthe dataplateagainst thereadingof
anAmmeter.
Ifthe motorcurrent exceedsthe max. motorcurrentfrom
the table below the pump is not suitable or the
motorcurrent must be reduced.
The motorcurrent can be reduced by installing a
smaller impeller. Contact your dealer.
Temperature Max.motorcurrent
oCoF %
40 104 100
50 122 95
60 144 90
70 158 80
80 176 70
5.12 Start frequency
When the pump is controlled by level regulators, the on
and off levels should be adjusted in such a way, that the
pump does not make more than 20 starts per hour.
5.13 Min. and max. submersion depth
Themotorhousing shouldbeat least2/3submerged for
continuous operation at full load (see Hmin.1 Fig. 5.4). It
is good practice, whenever possible to keep the
motorhousing completely under water.
For interrupted level controlled operation, less cooling is
required.
We recommend not to run the pump with the water level
below the top of the volute in order to avoid air being
drawn in (see Hmin.2 Fig. 5.4).
Air in the discharge pipes might impair performance.
The maximum submersion depth is 20m / 60ft.
Fig. 5.4
www.robotpompen-onderdelen.nl
T +31(0)294-457712

Operation &
Maintenance Manual Pump
RS
10/26 Edition 4 HS 09-W46 782-020-GB
6. INSTALLATION OPTIONS
For the submersible pump the following installations are
possible:
-H Stationary wet installation with a header
coupling type HK.
-V Stationary wet installation with a guide bar
quick release coupling type V.
-F Freestanding wet installation.
-T Transportable wet installation.
6.1 INSTALLATION - H
Stationary wet installation with a ROBOT quick-release
header coupling type HK.
A flexible hose connects pump and coupling.
Except for the pump the following components are
necessary:
1. Hose connection, which is fastened to the
pump;
2. Flexible hose, between pump and coupling;
3. Header coupling, consisting of coupling
bend, rubber joint and a fixed coupling part;
4. Suspension bracket and chain, for lifting the
pump;
5. Level regulators for start-, stop- and alarm-
signals;
6. Suspension for level regulators and power
supply cable;
7. Piping, non return valve, bends etc.
Checkpoints before operating:
- Ensure a good free passage beneath
the suction opening of the pump
(at least the same as the suction diameter).
- Adjust the start- and stoplevels in such a
way that the motor does not make more
than 20 starts per hour.
- Check that the motor is adequately cooled.
The motorhousing should be at least 2/3 submerged
for continuous operation at full load (see Hmin.1
Fig. 6.1).
It is good practice, whenever possible to keep the
motorhousing completely under water.
For interrupted level controlled operation, less cooling is
required. We recommend not to run the pump with the
water level below the top of the volute in order to avoid
air being drawn in (see Hmin.2 Fig. 6.1).
Air in the discharge pipes might impair performance.
Fig. 6.1
www.robotpompen-onderdelen.nl
T +31(0)294-457712

Operation &
Maintenance Manual
Pump
RS
782-020-GB HS 09-W46 Edition 4 11/26
6.2 INSTALLATION -V
Stationary wet installation with a ROBOT quick-release
guide bar coupling type -V. The pump is automatically
coupledto thedischarge.
Except for the pump the following components are
necessary:
1. Bottom elbow, rubber joint and coupling
adapter;
2. One guide bar
3. Top bracket,mountedwithin thewell cover
clearance;
4. Level regulators for start-, stop- and alarm-
signals;
5. Suspension for level regulators and power
supply cables;
6. Piping, non return valve, discharge bends etc.
Checkpoints before operating:
- The guide bar must stand vertical
(maximum tolerance 3o).
- The installation angle must be about 0-5o
(see Fig. 6.3). If necessary, this angle can be
changed by alterating of the position of the
lifting hook at the top of the motorhousing
(Pos. 1)
- Adjust the start- and stoplevels in such a
way that the motor does not make more
than 20 starts per hour.
- Check that the motor is adequately cooled.
The motorhousing should be at least 2/3 submerged
for continuous operation at full load (see Hmin.1
Fig. 6.3).
It is good practice, whenever possible to keep the
motorhousing completely under water.
For interrupted level controlled operation, less cooling is
required. We recommend not to run the pump with the
water level below the top of the volute in order to avoid
air being drawn in (see Hmin.2 Fig. 6.2).
Air in the discharge pipes might impair performance.
Fig. 6.2
Fig. 6.3
www.robotpompen-onderdelen.nl
T +31(0)294-457712

Operation &
Maintenance Manual Pump
RS
12/26 Edition 4 HS 09-W46 782-020-GB
6.3 INSTALLATION - F
Freestanding:semi-permanent fixedwet installation.
Except for the pump the following components are
necessary:
1. Hose or threaded connection, which is fastened to the
pump;
2. Flexible hose or pipe;
3. Levelregulators.
Checkpoints before operating:
- Adjust the start- and stoplevels in such a
way that the motor does not make more
than 20 starts per hour.
- Check that the motor is adequately cooled.
The motorhousing should be at least 2/3 submerged
for continuous operation at full load (see Hmin.1
Fig. 6.4).
It is good practice, whenever possible to keep the
motorhousing completely under water.
For interrupted level controlled operation, less cooling
is required. We recommend not to run the pump with
the water level below the top of the volute in order to
avoid air being drawn in (see Hmin.2 Fig. 6.4).
Air in the discharge pipes might impair performance.
6.4 INSTALLATION - T
Transportablewetinstallation.
Except for the pump the following components are
necessary:
1. Hose connection, which is fastened to the pump;
2. Flexiblehose;
Checkpoints before operating:
- Do not let the pump bury itself in the mud.
- Do not leave a large loop of the cable in
the sump, as the pump may eventually
damage it.
- Check that the motor is adequately cooled.
The motorhousing should be at least 2/3 submerged
for continuous operation at full load (see Hmin.1
Fig. 6.5).
It is good practice, whenever possible to keep the
motorhousing completely under water.
For interrupted level controlled operation, less cooling
is required. We recommend not to run the pump with
the water level below the top of the volute in order to
avoid air being drawn in (see Hmin.2 Fig. 6.5).
Air in the discharge pipes might impair performance.
Fig. 6.4
Fig. 6.5
www.robotpompen-onderdelen.nl
T +31(0)294-457712

Operation &
Maintenance Manual
Pump
RS
782-020-GB HS 09-W46 Edition 4 13/26
7. MAINTENANCE
7.1 General
Always disconnect the pump from the
mains before inspection or disassembly.
Clean the pump thoroughly.
The motor housing can be hot when the
pump is just switched off.
7.2 Maintenance schedule
* Afterthe first100 running hours:
- Check the oil level (see chapter 7.5).
If there is more than a few drops of water
in it, contact your dealer.
* Everyyear or 1000runninghours:
- Check the oil and oil level (see chapter 7.5).
If there is more than a few cm3 water in it,
contact your dealer.
- Refresh the oil every year or when it is no
longertransparent. (seechapter 7.6)
7.3 Lubricants
* The bearings are greased for life and need
no refill.
*Theoil reservoiris filled withExxonMobil Marcol152
Viscosity: 32 cSt.
When another kind of oil is used this is
marked on a label on the pump.
*Oil quantities:
RS 22: 0.6 L.
www.robotpompen-onderdelen.nl
T +31(0)294-457712

Operation &
Maintenance Manual Pump
RS
14/26 Edition 4 HS 09-W46 782-020-GB
7.4 Cable entry
Especially when the pump has been in use for a long
time, the compression of the rubber cable
seal might be deminished, which can cause leakage. By
screwing-in the cable entry the seal will be retentioned.
7.4.1 Cable entry without cable clamp
See fig. 7.1
Turn the hexagon head of the entry (1) for 1/6 of a turn
clockwise using the right tool.
7.4.2 Cable entry with cable clamp
See fig. 7.2
Unscrew the 2 hexagon socket screws (1).
Remove the cable clamp (2).
Turn the hexagon head of the entry (3) clockwise, using
the right tool, so far that it is possible to replace the
cable clamp again.
Screw-in the 2 hexagon socket screws (1).
7.5 Oil level
Put the pump in a horizontal position so that the 2
hexagonal socket screws are on top (see fig.7.3).
Unscrew the level plug (1) and the vent plug (2).
Theoil levelshould beat thelowerside ofthe openings
(see drawing).
By turning the pump a bit this should be visible.
If not so fill up to the right level.
Always use the right kind of oil!
1
2
3
A
3
2
1
Fig. 7.1
Fig. 7.2
Fig. 7.3
www.robotpompen-onderdelen.nl
T +31(0)294-457712

Operation &
Maintenance Manual
Pump
RS
782-020-GB HS 09-W46 Edition 4 15/26
7.6 Oil change
Collection, storage and removal of the
oil should be done according to the
regulations of the local authorities.
When necessary replace the sealing rings.
Always use the right kind of oil !
(see chapter 7.3).
Put the pump in a horizontal position so that oil plug 3 is
at the bottom ( fig.7.4 position B).
Remove plugs(1) and(2).
Puta receivingbinunderneath thedrainplug (3).
Removethe pluganddrain theoil.
Replacethe drainplug (3) (Fig.7.4position C).
Refillthe oilhousing.
Theoil levelshould beatthe lowerside ofplug (2). (fig.7.4
positionA).
Replace the plugs.
7.7 Motor housing
Unscrew the inspection plug of the motorhousing (see
Fig. 7.5 pos 1).
Put the pump in horizontal position with the inspection
openingdownwards.
If water is present this will come out this way.
A small amount of water, due to condensation, is
permissable.
More water is an indication of leakage of
the construction. Oil is an indication of
seal failure between motorhousing and oil
chamber. If so, contact your dealer.
7.8 Adjustment suction cover-impeller
-cutter
Ifpumpcasing andimpeller areinspected,re-assembling
must take place in the next sequence:
See Fig. 7.6.
1. Fix the impeller, without cutter (3), on the shaft with a
temporarythrustring andbolt.
2. Turn the adjusting bolts (2) into the pump casing.
3. Put the suction cover with cutting disc (4) in the
pumpcasing, and push it down until it touches the
impellervanes.
4. Fasten the three connecting bolts (1) by hand and
unscrewthem halfa turn.
5. Unscrew the adjusting bolts (2) , to fix the suction
cover.
6. Check that the impeller can rotate without much
force.
7. Removethe temporarythrustringand bolt,mountthe
cutter(3).
Nowthe pumpisoperational again.
Fig. 7.4
Fig. 7.5
Fig. 7.6
1
www.robotpompen-onderdelen.nl
T +31(0)294-457712

Operation &
Maintenance Manual Pump
RS
16/26 Edition 4 HS 09-W46 782-020-GB
8. TRANSPORTAND STORAGE
The pump can be transported and stored in both
horizontal and vertical position.
Never lift the pump by the motorcable or
discharge hose.Always use the suspension
bracket !
In case of long storage, the pump must be protected
against moisture and heat.
Before storing the pump clean it with a waterjet and
check the motor housing for water ingress (see chapter
7.7) .
On a regular base (every three months), turn the
impeller by hand, this is necessary to prevent
sticking of the impeller and mechanical seal surfaces
(see Fig. 8.1).
After 6 months of storage, a general inspection is
advised, before installing the pump.
Follow the instructions of chapter 5.
Fig. 8.1
www.robotpompen-onderdelen.nl
T +31(0)294-457712

Operation &
Maintenance Manual
Pump
RS
782-020-GB HS 09-W46 Edition 4 17/26
9. OPTIONS
9.1 Waterdetector
As a safeguard against water ingress into the motor, the
pump can be equipped with a waterdetector.
When your pump is equipped with a waterdetector, this
can be found on the dataplate.
See appendix 1: at position 1 a “W” is stamped as fore
lastcharacter.The waterdetectordetectswaterwhich
mighthave enteredtheoilhousing ormotorhousing dueto
sealfailure orcabledamage.
Thewaterdetector causesthe pumpto switch off,
before damage to the motor is done.
Theprobe itselfis anon-activeelectrode, placedin oiland
motorhousing. It is used in conjunction with a relay in the
control circuit that measures the resistance between
probe and frame.
If only air or oil is present, the resistance is over
5000 Ohm. If water enters, the resistance will
decrease to as low as 300 to 500 Ohm.
We advise to use OMRON relay 61 F-GP or an
equivalent.
This relay switches at 5000 ohm.
Nowater present:
- highresistance betweenterminals1and 7
(>5000 Ohm)
- terminals 2 and 4 closed
- terminals 3 and 4 open
Water present:
- low resistance between terminals 1 and 7
(300-500 Ohm)
- terminals 2 and 4 open
- terminals 3 and 4 closed
9.2 Thermoswitches
Thermoswitches are optional .
When your pump is equipped with thermoswitches,
a “T” is stamped at position 1 the last character on the
dataplate. (see appendix 1).Acopy of your dataplate is
on page 2. For connection values see par. 5.4.
9.3 Thermistors
Insteadof thermoswitches,thepump canbe equipped
with thermistors (on special request).
This will be marked with a “U” on the dataplate at
position 1 the last last character.
Normally the resistance is about 200-500 Ohm.
Whenthe switch-offtemperatureis reachedthe
resistancewill bebetween 1650-4000Ohm.
Themaximum voltageis7.5V.
A thermistor is not a circuit breaker but a
resistance.
Fig. 9.1
electrode
frame
oil
water
www.robotpompen-onderdelen.nl
T +31(0)294-457712

Operation &
Maintenance Manual Pump
RS
18/26 Edition 4 HS 09-W46 782-020-GB
9.4 Cable protection
When chemical or mechanical protection for the
cable is needed a tube can be fitted around the
cable (Fig. 9.2 pos 1).
This is a flexible stainless steel tube (1) connected to a
special cable entry (Fig.9.2 pos 2).
9.5 Special oil
Upon request the oil housing can be filled with special oil.
If so, a label on the pump shows which kind of oil is used.
Fig. 9.2
9.6 Special tool
Use a hand puller like Bacho 4614-1 with crossed legs to
removethe impeller. (See Fig9.3)
Fig. 9.3
www.robotpompen-onderdelen.nl
T +31(0)294-457712

Operation &
Maintenance Manual
Pump
RS
782-020-GB HS 09-W46 Edition 4 19/26
10. TROUBLE SHOOTING
10.1 Safety
When working on the motor, make sure
that the power is switched off.
When working on the pump make sure it
cannot start unexpectedly!
Only qualified electricians may do the
electrical work.
When starting the pump ensure nobody
goes near rotating parts.
Observe local electrical and safety regulations!
MELBORPESUACELBISSOPNOITCADERIUQERSTNIOPKCEHC
tratstonseodpmuP
slanimretrotomnoegatlovoN
ylppusrewopkcehC rewopoN* hctiwsrotalosiniaM* sesuF*
noitcetorprotomkcehC
yalereg
akaelhtraE* yalernoitcetorprotoM* erutarepmetrotoM* rotcetedretaW*
slangispotsdna-tratskcehC
levelretawwol
ooT* sehctiwsleveldetcurtsbO* degnahcretnisehctiwS* lenaplortnoC*
eruliafrotoMgniriwrotomkcehC noitalosidna
ytiunitnoC* ecnatsiseresahP*
potstonseodpmuP
langispotsoNnoitalugerlevelkcehC sehctiwstaolF* lenaplortnoC*
levelpotsdna-tratsgnorWnoitalugerlevelkcehC sehctiwsleveldetcurtsbO* levelpotsdna-tratstsujdA* elbatstonylppusrewoP*
spotsdnastratspmuP yldetaeper
ylppusrewopnitluaFylppusrewopkcehC egatlovwoL* elbaliavasesahp3llatoN* noitcetorprotomfognitteS*
dedaolrev
orotoMpmupkcehC noitatorfonoitceridgnorW* dekcolbrellepmI* edomtesercitamotuaninoitcetorP*
detaehrevorotoM gniloockcehC rotomkcehC noitalosidnaytiunitnoC* sesuF*
hgihoottnerruC
ylppusrewopnitluaFylppusrewopkcehCegatlovwoL*
eruliafpmuPpmupkcehC dekcolbrellepmI* hgihootytivarg.cepsroyt
isocsiV* noitatorfonoitceridgnorW*
ootrowolfontubsnurpmuP wolfwol
kcolriarogniggolCgnilpuocdnaegrahcsidkcehC
detcurtsboegrahcsiD* desolcyltraproyllufevlaV* egrahcsidropmup
nitekcopriA* skaelgnilpuoC*
eruliafpmuPpmupkcehC dekcolbetulovrorellepmI* riahcumootgnikcussipmuP* rellepmi
nekorbronroW*
ylppusrewopnitluaFylppusrewopkcehC lenaplortnoC* sesuF* egatlovwoL*
yticapacwolooTegrahcsidkce
hC detcurtsboegrahcsiD* desolcyltraproyllufevlaV* tekcopriA*
mralalevelhgiH
eruliafpmuPpmupkcehC
dekcolbetulovrorellepmI* riahcumootgnikcussipmuP* rellepminekorbronroW* sgniraebnekor
bronroW*
ylppusrewopnitluaFylppusrewopkcehC sesuF* lenaplortnoC*
eruliafrotoMrotomkcehCnoitalosidnaytiunitno
C*
www.robotpompen-onderdelen.nl
T +31(0)294-457712

Operation &
Maintenance Manual
Pump
RS
782-020-GB HS 09-W46 Edition 4 21/26
APPENDIX 2; Direct-on-line start motor (DOL)
PUMP CABLE CONNECTIONS
PUMP CABLE CONTROL PANEL
BR =brown U,V,W =line
BL =blue(orgray) T =thermostats
B =black Wa =waterdetector
G/Y =green/yellow =earthconnection
In some situations where a longer pump cable is used an
extra 10 mm2 earth cable is fitted to the motorhousing to
fulfill the demands of the Low Voltage Directive.
Always connect this cable also to the earth connection!
Star- high voltage Delta-low voltage
www.robotpompen-onderdelen.nl
T +31(0)294-457712

Operation &
Maintenance Manual Pump
RS
22/26 Edition 4 HS 09-W46 782-020-GB
EXAMPLE OFADIRECT-ON-LINE CONNECTION DIAGRAM
opposite
direction
of rotation
motor in delta motor in star
CODING
e1, e2, e3 Line fuses
e4, e5 Fuses, primary control-circuit
e6 Fuses, secondary control-circuit
C Maincontactor
F1 Motor protection circuit breaker with manual reset
D1 Auxiliary relay for motor protection
D2 Auxiliary relay for power failure
Tr Transformer
S Manual-off -auto selector switch
Start Level switch pump start
Stop Level switch pump stop
Re Reset push button
M Pump motor
T Thermostats (if fitted)
www.robotpompen-onderdelen.nl
T +31(0)294-457712

Operation &
Maintenance Manual
Pump
RS
782-020-GB HS 09-W46 Edition 4 23/26
APPENDIX 3; Star-delta start motor (YD)
PUMP CABLE CONNECTIONS
PUMP CABLE
BR = brown
BL =blue (orgray)
B = black
G/Y =green/yellow
CONTROLPANEL
U,V,W = line
T = thermostats
Wa = water detector
= earth connection
In some situations where a longer pump cable is used an
extra 10 mm2 earth cable is fitted to the motorhousing to
fulfill the demands of the Low Voltage Directive.
Always connect this cable also to the earth connection!
Star- high voltage Delta-low voltage
www.robotpompen-onderdelen.nl
T +31(0)294-457712
Table of contents
Other Robot Pumps Water Pump manuals
Popular Water Pump manuals by other brands

Graco
Graco ChemSafe 205 Instructions - parts
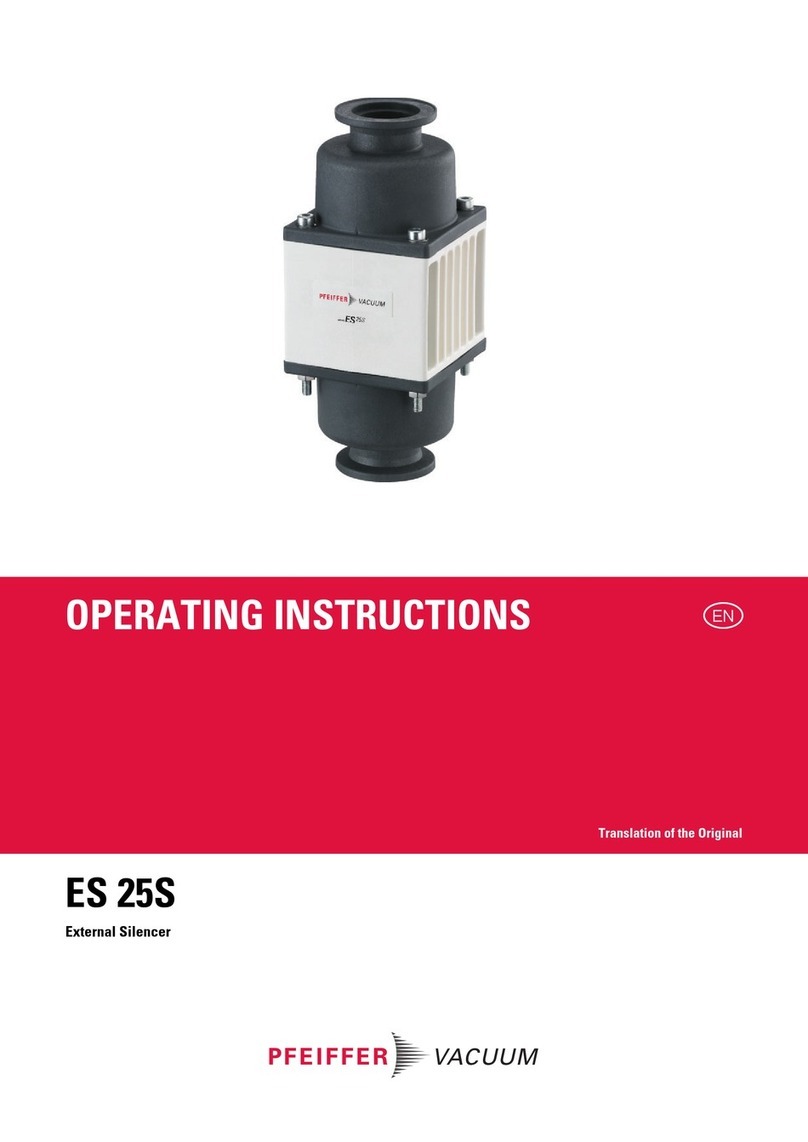
Pfeiffer Vacuum
Pfeiffer Vacuum ES 25S operating instructions

Crane
Crane Barnes 3SEH-L Installation and operation manual
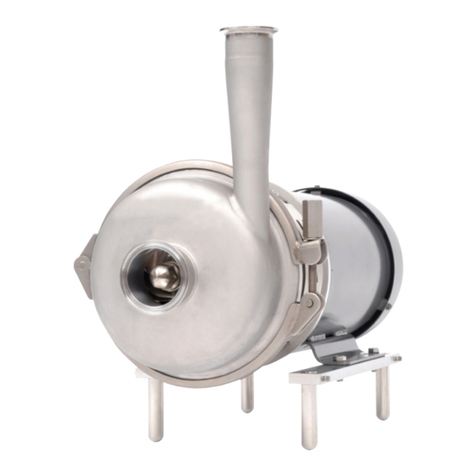
SPX
SPX W+ instruction manual
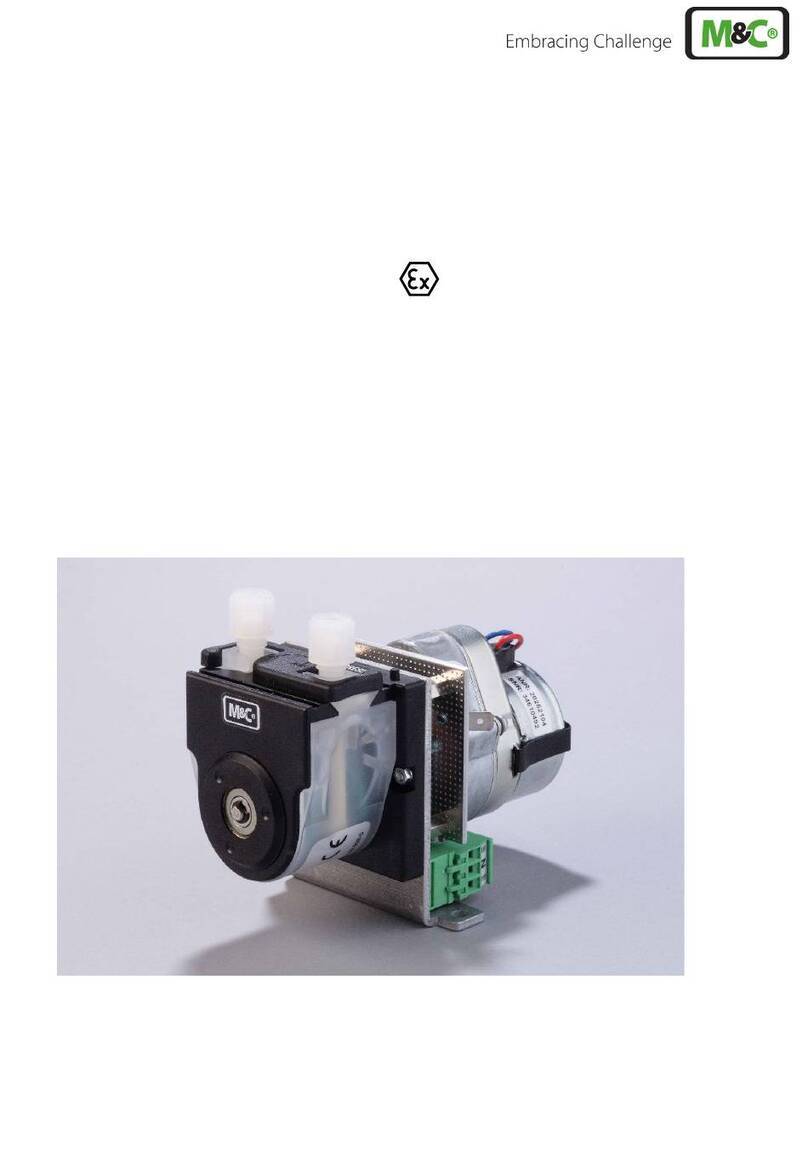
M&C
M&C SR Series instruction manual
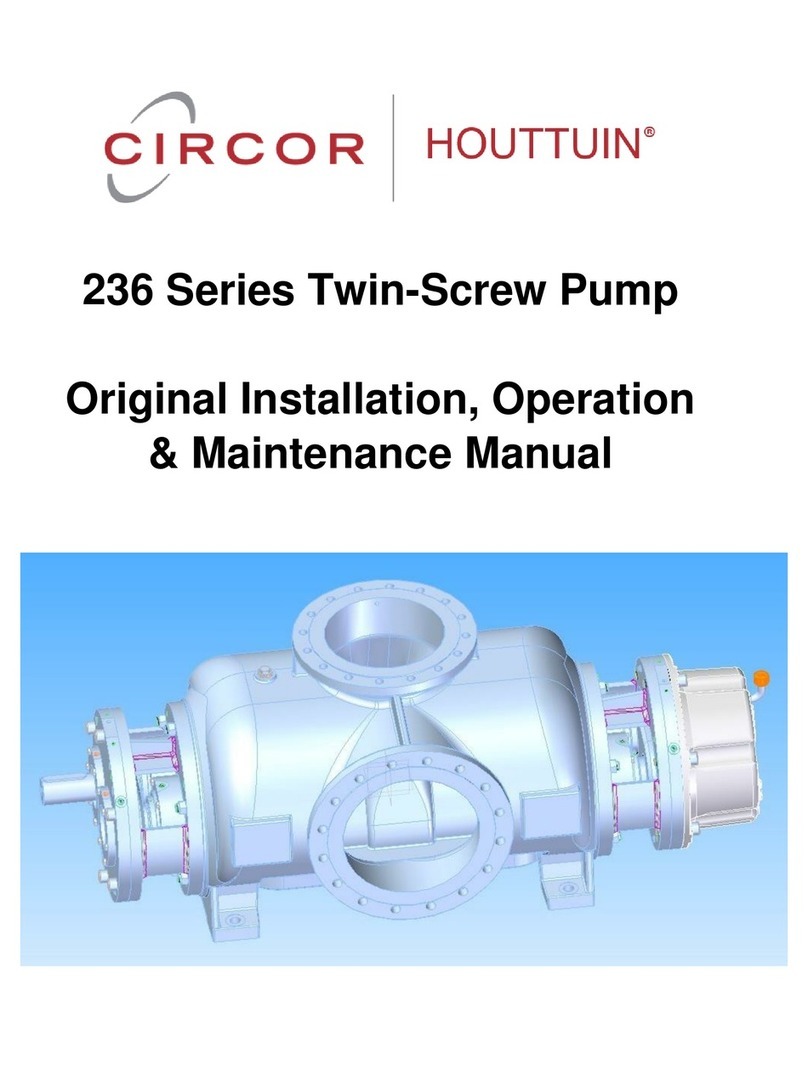
Circor
Circor HOUTTUIN 236 Series ORIGINAL INSTALLATION, OPERATION AND MAINTENANCE MANUAL