Robotis XM540-W150 User manual

2/22/2018 XM540-W150
http://support.robotis.com/en/product/actuator/dynamixel_x/xm_series/xm540-w150.htm 1/17
Show
Home > Product Information > Actuator > Dynamixel X > XM Series > XM540-W150
XM540-W150-T / XM540-W150-R
Part Photo
[XM540-W150-T / XM540-W150-R]
H/W Specifications
MCU : ST CORTEX-M3 ( STM32F103C8 @ 72MHZ,32BIT)
POSITION SENSOR : Contactless absolute encoder (12BIT, 360°)
Motor : Coreless
Baud Rate : 9600 bps ~ 4.5 Mbps
Control Algorithm : PID CONTROL
Degree of Precision : 0.088°
Operating Modes
Current Control Mode
Velocity Control Mode
Position Control Mode (0° ~ 360°)
Extended Position Control Mode (Multi-turn)
Current-based Position Control Mode
PWM Control Mode
Weight : 165g
Dimensions(W x H x D) : 33.5mm x 58.5mm x 44mm
Gear Ratio : 152.3 : 1
Stall Torque
6.9N.m (at 11.1V, 4.2A)
7.3N.m (at 12.0V, 4.4A)
8.9N.m (at 14.8V, 5.5A)
No load speed
50rpm (at 11.1V)
53rpm (at 12.0V)
66rpm (at 14.8V)
Operating Temperature : -5℃ ~ +80℃
Input Voltage : 10 ~ 14.8V (Recommended : 12V)
Command Signal : Digital Packet
Protocol Type
XM540-W150-T (Half duplex Asynchronous Serial Communication (8bit, 1stop, No Parity)
XM540-W150-R (RS485 Asynchronous Serial Communication (8bit, 1stop, No Parity)
Link (Physical)
XM540-W150-T (TTL Level Multi Drop Bus)
XM540-W150-R (RS485 Multi Drop Bus)
ID : 253 ID (0~252)
Feedback : Position, Velocity, Current, Real-time tick, Trajectory, Temperature, Input Voltage, etc.
Material : Full Metal Gear, Metal Body(Front, Middle), Engineering Plastic Body(Back)
ROBOTIS e-Manual v1.31.30

2/22/2018 XM540-W150
http://support.robotis.com/en/product/actuator/dynamixel_x/xm_series/xm540-w150.htm 2/17
Standby current : 40 mA
The max torque measurement method for the Stall Torque and Performance Graph are different. Stall torque is measured from the max torque that it can reach. This is generally how
traditional RC servos measure maximum torque. The Performance graph which is also called the N-T Curve, measured by gradually increasing the load. The actual motor operating
environment is similar to the performance graph, not stall torque measurement method. For this reason, the performance graph is broadly used in the industrial market. Generally the max
torque of the performance graph is measured smaller than the stall torque.
Precautions when connecting to power supply!
- For a stable power supply, it is recommended using ROBOTIS controller or SMPS2Dynamixel.
- Connect your DYNAMIXEL to power supply while it’s off and turn on/off with the power switch.
Control Table
The Control Table is a structure of data implemented in the Dynamixel. Users can read a specific Data to get status of the Dynamixel with Read Instruction Packets, and modify Data as well to control
Dynamixels with WRITE Instruction Packets.
Control Table, Data, Address
The Control Table is a structure that consists of multiple Data fields to store status of the Dynamixel or to control the Dynamixel. Users can check current status of the Dynamixel by reading a specific
Data from the Control Table with Read Instruction Packets. WRITE Instruction Packets enable users to control the Dynamixel by changing specific Data in the Control Table. The Address is a unique
value when accessing a specific Data in the Control Table with Instruction Packets. In order to read or write data, users must designate a specific Address in the Instruction Packet. Please refer to the
Protocol section of e-Manual for more details about Packets.
Note : Two's complement rule is followed to find the negative value.
For more information, please refer to the following link (Two's complement link).
Area (EEPROM, RAM)
The Control Table is divided into 2 Areas. Data in the RAM Area is reset to initial values when the Dynamixel is turned on (Volatile). On the other hand, modified data in the EEPROM Area keeps their
values even when the Dynamixel is turned off (Non-Volatile). Data in the EEPROM Area can only be changed when the value of Torque Enable(64) is cleared to ‘0’.
Access
The Control Table has two different access properties. ‘RW’ property stands for read and write access permission while ‘R’ stands for read only access permission. Data with the read only property
cannot be changed by the WRITE Instruction. Read only property(‘R’) is generally used for measuring and monitoring purpose, and read write property(‘RW’) is used for controlling Dynamixels.
Initial Value
Each data in the Control Table is restored to initial values when the Dynamixel is turned on. Default values in the EEPROM area are initial values of the Dynamixel (factory default settings). If any
values in the EEPROM area are modified by a user, modified values will be restored as initial values when the Dynamixels is turned on. Initial Values in the RAM area are restored when the
Dynamixels is turned on.
Size
The Size of data varies from 1 to 4 bytes depend on their usage. Please check the size of data when updating the data with an Instruction Packet.
Area Address Size
[byte] Data Name Description Access Initial Value
E
E
P
R
O
M
0 2 Model Number Model Number R 1130
2 4 Model Information Model Information R -
6 1 Version of Firmware Firmware Version R -
7 1 ID Dynamixel ID RW 1
8 1 Baud Rate Communication Baud Rate RW 1
9 1 Return Delay Time Response Delay Time RW 250
10 1 Drive Mode Drive Mode RW 0
11 1 Operating Mode Operating Mode RW 3
12 1 Secondary(Shadow) ID Secondary(Shadow) ID RW 255

2/22/2018 XM540-W150
http://support.robotis.com/en/product/actuator/dynamixel_x/xm_series/xm540-w150.htm 3/17
13 1 Protocol Version Protocol Version RW 2
20 4 Homing Offset Home Position Offset RW 0
24 4 Moving Threshold Velocity Threshold for Movement Detection RW 10
31 1 Temperature Limit Maximum Internal Temperature Limit RW 80
32 2 Max Voltage Limit Maximum Voltage Limit RW 160
34 2 Min Voltage Limit Minimum Voltage Limit RW 95
36 2 PWM Limit Maximum PWM Limit RW 885
38 2 Current Limit Maximum Current Limit RW 2047
40 4 Acceleration Limit Maximum Acceleration Limit RW 32767
44 4 Velocity Limit Maximum Velocity Limit RW 380
48 4 Max Position Limit Maximum Position Limit RW 4095
52 4 Min Position Limit Minimum Position Limit RW 0
56 1 External Port Mode 1 External Port 1 Mode RW 3
57 1 External Port Mode 2 External Port 2 Mode RW 3
58 1 External Port Mode 3 External Port 3 Mode RW 3
63 1 Shutdown Shutdown Dynamixel RW 52
R
A
M
64 1 Torque Enable Motor Torque On/Off RW 0
65 1 LED Status LED On/Off RW 0
68 1 Status Return Level Select Types of Status Return RW 2
69 1 Registered Instruction Check Reception of Instruction R 0
70 1 Hardware Error Status Hardware Error Status R 0
76 2 Velocity I Gain I Gain of Velocity RW 1920
78 2 Velocity P Gain P Gain of Velocity RW 100
80 2 Position D Gain D Gain of Position RW 0
82 2 Position I Gain I Gain of Position RW 0
84 2 Position P Gain P Gain of Position RW 800
88 2 Feedforward 2nd Gain 2nd Gain of Feed-Forward RW 0
90 2 Feedforward 1st Gain 1st Gain of Feed-Forward RW 0
98 1 Bus Watchdog Dynamixel Bus Watchdog RW 0
100 2 Goal PWM Target PWM Value RW -
102 2 Goal Current Target Current Value RW -
104 4 Goal Velocity Target Velocity Value RW -
108 4 Profile Acceleration Acceleration Value of Profile RW 0
112 4 Profile Velocity Velocity Value of Profile RW 0
116 4 Goal Position Target Position Value RW -
120 2 Realtime Tick Count Time in millisecond R -
122 1 Moving Movement Status R 0
123 1 Moving Status Detailed Information of Movement Status R 0
124 2 Present PWM Present PWM Value R -
126 2 Present Current Present Current Value R -
128 4 Present Velocity Present Velocity Value R -
132 4 Present Position Present Position Value R -
136 4 Velocity Trajectory Target Velocity Trajectory Generated by
Profile R -
140 4 Position Trajectory Target Position Trajectory Generated by
Profile R -
144 2 Present Input Voltage Present Input Voltage R -
146 1 Present Temperature Present Internal Temperature R -
152 2 External Port Data 1 The Data of External Port 1 RW -
154 2 External Port Data 2 The Data of External Port 2 RW -
156 2 External Port Data 3 The Data of External Port 3 RW -
168 2 Indirect Address 1 Indirect Address 1 RW 224
170 2 Indirect Address 2 Indirect Address 2 RW 225
172 2 Indirect Address 3 Indirect Address 3 RW 226
… … …… … …
218 2 Indirect Address 26 Indirect Address 26 RW 249
220 2 Indirect Address 27 Indirect Address 27 RW 250

2/22/2018 XM540-W150
http://support.robotis.com/en/product/actuator/dynamixel_x/xm_series/xm540-w150.htm 4/17
222 2 Indirect Address 28 Indirect Address 28 RW 251
224 1 Indirect Data 1 Indirect Data 1 RW 0
225 1 Indirect Data 2 Indirect Data 2 RW 0
226 1 Indirect Data 3 Indirect Data 3 RW 0
… … …… … …
249 1 Indirect Data 26 Indirect Data 26 RW 0
250 1 Indirect Data 27 Indirect Data 27 RW 0
251 1 Indirect Data 28 Indirect Data 28 RW 0
578 2 Indirect Address 29 Indirect Address 29 RW 634
580 2 Indirect Address 30 Indirect Address 30 RW 635
582 2 Indirect Address 31 Indirect Address 31 RW 636
… … …… … …
628 2 Indirect Address 54 Indirect Address 54 RW 659
630 2 Indirect Address 55 Indirect Address 55 RW 660
632 2 Indirect Address 56 Indirect Address 56 RW 661
634 1 Indirect Data 29 Indirect Data 29 RW 0
635 1 Indirect Data 30 Indirect Data 30 RW 0
636 1 Indirect Data 31 Indirect Data 31 RW 0
… … …… … …
659 1 Indirect Data 54 Indirect Data 54 RW 0
660 1 Indirect Data 55 Indirect Data 55 RW 0
661 1 Indirect Data 56 Indirect Data 56 RW 0
Note : Protocol 1.0 does not support addresses greater than 256.
Therefore, Indirect Address 29 ~ 56 and Indirect Data 29 ~ 56 can only be accessed with Protocol 2.0.
Address Description
EEPROM Area
Note : Any Data in EEPROM Area can only be modified when the value of Torque Enable(64) is cleared to ‘0’.
Model Number (0)
This address stores model number of the Dynamixel.
Firmware Version (6)
This address stores firmware version of the Dynamixel.
ID (7)
The ID is a unique value in the network to identify each Dynamixel with an Instruction Packet.
0~252 (0xFC) values can be used as an ID, and 254(0xFE) is occupied as a broadcast ID. The Broadcast ID(254, 0xFE) can send an Instruction Packet to all connected Dynamixels simultaneously.
Note : Please avoid using an identical ID for multiple Dynamixels.
In order to change the ID in the EEPROM Area, Torque Enable(64) has to be cleared to ‘0’ in advance.
Baud Rate (8)
Baud Rate determines serial communication speed between a controller and Dynamixels.
Baud Rate Baud Rate[bps] Margin of Error
09,600 0.000%
1(Default) 57,600 0.000%
2115,200 0.000%
31M 0.000%
42M 0.000%
53M 0.000%
64M 0.000%
74.5M 0.000%
Note : Less than 3% of the baud rate error margin will not affect to UART communication.
Return Delay Time (9)
After the Dynamixel receives an Instruction Packet, it delays transmitting the Status Packet for Return Delay Time (9).

2/22/2018 XM540-W150
http://support.robotis.com/en/product/actuator/dynamixel_x/xm_series/xm540-w150.htm 5/17
For instance, if the Return Delay Time(9) is set to ‘10’, the Status Packet will be returned after 20[μsec] when the Instruction Packet is received.
Values Description
Unit 2[μsec] -
Range 0 ~ 254 Default value ‘250’(500[μsec]), Maximum 508[μsec]
Drive Mode (10, Available after Firmware version 38)
Driver Mode Definition Values
Bit 7 0x80 - Unused, always ‘0’
Bit 6 0x40 - Unused, always ‘0’
Bit 5 0x20 - Unused, always ‘0’
Bit 4 0x10 - Unused, always ‘0’
Bit 3 0x08 - Unused, always ‘0’
Bit 2 0x04 - Unused, always ‘0’
Bit 1 0x02 Master / Slave Configuration
(Dual Joint)
Master mode('0') : Operate as a Master DYNAMIXEL
Slave mode('1') : Operate as a Slave DYNAMIXEL
Bit 0 0x01 Direction of Rotation Normal mode(‘0’) : CCW(Positive), CW(Negative)
Reverse mode(’1’) : CCW(Negative), CW(Positive)
Setting Reverse mode('1') for Direction of Rotation, DYNAMIXEL will switch rotating direction.
Therefore the direction of Position, Velocity, Current, PWM will be affected.
This feature can be very useful when configuring symmetrical joint system or wheel system.
Master / Slave Configuration (Dual Joint) is intended to control two DYNAMIXELs as a single module.
The Master DYNAMIXEL and the Slave DYNAMIXEL has to be interconnected with a Synchronization cable.
The Slave DYNAMIXEL is controlled by the PWM signal sent from the Master DYNAMIXEL via the synchronization cable.
Therefore, Goal Position, Goal Current, Goal PWM of the Slave DYNAMIXEL will be ignored in this mode.
Synchronization Cable Description
General Mode The Slave DYNAMIXEL is controlled by the PWM signal from the Master DYNAMIXEL.
Master / Slave DYNAMIXELs have an identical rotational direction.
Reverse Mode (Twisted) The Slave DYNAMIXEL is controlled by inverted PWM signal from the Master DYNAMIXEL.
Master / Slave DYNAMIXELs have opposite rotational directions.
If Master / Slave DYNAMIXELs are not mechanically connected to each other, each DYNAMIXEL could have minor differences during
operation.
Please mount both DYNAMIXELs as shown in the below image.
Operating Mode (11)
Each operating mode has a significant characteristic. Please select most appropriate operating mode for designed system.
Value Operating Mode Description
0Current Control Mode
Dynamixel only controls current(torque) regardless of speed and position.
This mode is ideal for a gripper or a system that only uses current(torque) control or a system that has additional
velocity/position controllers.
1Velocity Control Mode
(0° ~ 360°)
This mode controls velocity.
This mode is identical to the Wheel Mode(endless) from existing Dynamixels. This mode is ideal for wheel-type robots.
3(Default) Position Control Mode This mode controls position.

2/22/2018 XM540-W150
http://support.robotis.com/en/product/actuator/dynamixel_x/xm_series/xm540-w150.htm 6/17
This mode is identical to the Joint Mode from existing Dynamixels. Operating position range is limited by Max Position
Limit(48) and Min Position Limit(52). This mode is ideal for articulated robots that each joint rotates less than 360 degrees.
4Extended Position Control
Mode(Multi-turn)
This mode controls position.
This mode is identical to the Multi-Turn Mode from existing Dynamixels. 512 turns are supported(-256[rev] ~ 256[rev]).
This mode is ideal for multi-turn wrists or conveyer systems or a system that requires an additional reduction gear.
5Current-based Position
Control Mode
This mode controls both position and current(torque). Up to 512 turns are supported(-256[rev] ~ 256[rev]).
This mode is ideal for a system that requires both position and current control such as articulated robots or grippers.
16 PWM Control Mode
(Voltage Control Mode)
This mode directly controls PWM output.
(Voltage Control Mode)
Note : Switching Operating Mode will reset gains(PID, Feedfoward) properly to the selected Operating Mode. The profile generator and limits will also be reset.
① Profile Velocity(112), Profile Acceleration(108) : Reset to ‘0’
② Goal PWM(100), Goal Current(102) : Reset to PWM Limit(36), Current Limit(38) respectively
③ Current-based Position Control Mode : Reset to Position Gain(PID) and PWM Limit(36) values
Changed Position Gain(PID) and PWM Limit(36) values can be read from the Control Table.
Note : PWM is the abbreviation for Pulse Width Modulation that modulates PWM Duty to control motors. The PWM Control Mode changes pulse width to control average supply voltage to the motor
and this technique is widely used in the motor control field.
Therefore, PWM Control Mode uses Goal PWM(100) value to control supply voltage for Dynamixel. PWM Control Mode is similar to the Wheel Mode of Dynamixel AX and RX series.
Secondary(Shadow) ID (12, Available from Firmware Version 38)
Set the Dynamixel’s Secondary ID. Secondary ID(12) is a value to identify each Dynamixel, just like ID(7).
However, unlike ID(7), Secondary ID(12) is not a unique value. Therefore, Dynamixels with the same Secondary ID value form a group. The differences between Secondary ID(12) and ID(7) are as follows :
① Secondary ID(12) is not a unique value. i.e., a lot of Dynamixels may have the same Secondary ID value.
② ID(7) has a higher priority than Secondary ID(12). i.e., if Secondary ID(12) and ID(7) are the same, ID(7) will be applied first.
③ The EEPROM area of the Control Table cannot be modified with Secondary ID(12). Only the RAM area can be modified.
④ If Instruction Packet ID is the same as Secondary ID(12), the Status Packet will not be returned.
⑤ If the value of Secondary ID(12) is 253 or higher, the Secondary ID function is deactivated.
Values Description
Range 0 ~ 252
253 ~ 255
Activate Secondary ID function
Deactivate Secondary ID function, Default value ‘255’
The following are examples of operation when there are five Dynamixels with ID (7) set from 1 to 5.
① Set all five Dynamixels' Secondary ID(12) to '5'.
② Send Write Instruction Packet(ID = 1, LED(65) = 1).
③ Turn on LED of Dynamixel with ID '1' and return the Status Packet.
④ Send Write Instruction Packet(ID = 5, LED(65) = 1).
⑤ Turn on LED on five Dynamixels. However, Status Packet of Dynamixel with ID ‘5’ will be returned.
⑥ Set the Secondary ID(12) of all five Dynamixels to ‘100’.
⑦ Send Write Instruction Packet(ID = 100, LED(65) = 0).
⑧ Turn off LED on five Dynamixels. However, as there is no Dynamixel with ID ‘100’, Status Packet is not returned.
Protocol version (13)
Users can select Dynamixel protocol version (1.0 and 2.0). It is recommended to use an identical protocol version for multiple Dynamixels.
Protocol Version Compatible Dynamixels
11.0 AX, DX, RX, MX, EX Series
2(Default) 2.0 MX Series (MX-28, MX-64, MX-106 with FW V39 or above),
X Series, Dynamixel-PRO Series
Note : The protocol 2.0 greatly improved the protocol 1.0.
Accessing some of the Control Table area might be denied if protocol 1.0 is selected.
This manual complies with protocol 2.0.
Please refer to the Protocol section of e-Manual for more details about the protocol.
Homing Offset (20)
Users can adjust the Home position by setting Home Offset(20). The Homing Offset value is added to the Present Position(132).
Present Position(132) = Actual Position + Homing Offset(20).
Values Description
Unit about 0.088[deg] 4096 resolution. All position related Data uses the same unit
Range -1,044,479 ~ 1,044,479 ±255[rev] range
Note : In case of the Position Control Mode(Joint Mode) that rotates less than 360 degrees, any invalid Homing Offset(20) values will be ignored(valid range : -1024 ~ 1024).
Moving Threshold (24)

2/22/2018 XM540-W150
http://support.robotis.com/en/product/actuator/dynamixel_x/xm_series/xm540-w150.htm 7/17
This value helps to determine whether the Dynamixel is in motion or not. When the absolute value of Present Velocity(128) is greater than the Moving Threshold(24), Moving(122) is set
to ‘1’, otherwise it is cleared to ‘0’.
Values Description
Unit about 0.229[RPM] All speed related Data uses the same unit
Range 0 ~ 1,023
Temperature Limit (31)
This value limits operating temperature. When the Present Temperature(146) that indicates internal temperature of Dynamixel is greater than the Temperature Limit(31), the Over Heating
Error Bit(0x04) in the Hardware Error Status(70) will be set, and the Hardware Error Bit(0x80) will be transmitted in the Error field of the Status Packet. If Overheating Error Bit(0x04) is
set to '1' in the Shutdown(63), Torque Enable(64) is cleared to ‘0’ and Torque is disabled. For more details, please refer to the Shutdown(63) section.
Values Description
Unit about 1[℃] All temperature related Data uses the same unit
Range 0 ~ 100 -
Max Voltage Limit (32), Min Voltage Limit (34)
These values are maximum and minimum operating voltages. When present input voltage acquired from Present Input Voltage(144) exceeds the range of Max Voltage Limit(32) and Min
Voltage Limit(34), the Voltage Range Error Bit(0x01) in the Hardware Error Status(70) will be set, and Hardware Error Bit(0x80) will be transmitted in the Error field of the Status Packet. If
Input Voltage Error Bit(0x10) is set to '1' in the Shutdown(63), Torque Enable(64) is cleared to ‘0’ and Torque is disabled. For more details, please refer to the Shutdown(63) section.
Values Description
Unit about 0.1[V] All voltage related Data uses the same unit
Range 95 ~ 160 9.5 ~ 16.0[V]
PWM Limit (36)
This value indicates maximum PWM output. Goal PWM(100) can’t be configured with any values exceeding PWM Limit(36). PWM Limit(36) is commonly used in all operating mode as
an output limit, therefore decreasing PWM output will result in decreasing torque and velocity. For more details, please refer to the Gain section of each operating modes.
Values Description
Range 0 ~ 885 885 = 100[%] output
Current Limit (38)
This value indicates maximum current(torque) output limit. Goal Current(102) can’t be configured with any values exceeding Current Limit(38). The Current Limit(38) is used in Torque
Control Mode and Current-based Position Control Mode, therefore decreasing Current Limit(38) will result in decreasing torque of Dynamixel. For more details, please refer to the
Position PID Gain(80 ~ 84).
Values Description
Unit about 2.69[mA] All current related Data uses the same unit
Range 0 ~ 2,047 -
Note : Current Limit(38) could be differ by each Dynamixel so please check the Control Table.
Acceleration Limit (40)
This value indicates maximum Profile Acceleration(108). Profile Acceleration(108) can’t be configured with any values exceeding Acceleration Limit(40). Profile Acceleration(108) is used
in all operating mode except Torque Control Mode in order to generate a target trajectory. For more details, please refer to the Profile Velocity(112).
Values Description
Unit 214.577[Rev/min2]All acceleration related Data uses the same unit.
Range 0 ~ 32,767 -
Note : Bit information of the Error field in the Status Packet is different from protocol 1.0 and protocol 2.0. This manual complies with protocol 2.0. Please refer to the Protocol section of e-Manual for
more details about the protocol.
Velocity Limit (44)
This value indicates maximum velocity of Goal Velocity(104) and Profile Velocity(112). For more details, please refer to the Profile Velocity(112).
Values Description
Unit 0.229[RPM] All velocity related Data uses the same unit
Range 0 ~ 1,023 -
Max Position Limit (48), Min Position Limit (52)
These values limit maximum and minimum target positions for Position Control Mode(Joint Mode) within the range of 1 rotation(0~4095). Therefore, Goal Position(116) should be
configured within the position limit range. These values are not used in Extended Position Control Mode and Current-based Position Control Mode.
Values Description
Unit 0.088[deg] All position related Data uses the same unit
Range 0 ~ 4095 The range is limited by 1 rotation

2/22/2018 XM540-W150
http://support.robotis.com/en/product/actuator/dynamixel_x/xm_series/xm540-w150.htm 8/17
Note : Max Position Limit(48) and Min Position Limit(52) are only used in Position Control Mode with a single turn.
External Port Mode 1, 2, 3 (56, 57, 58)
External ports that can be used for various purposes are provided.
The property of each port is configured by the External Port Mode and data of external port is controlled by the External Port Data(152~157).
For more details, please refer to External Port Data(152~157).
External Port
Mode Mode Description
0AI Analogue Input Converts External Port signal to 12[bit] digital value
1DO_PP Digital Output Push-Pull Use External Port as a digital output port(3.3V level)
2DI_PU Digital Input Pull-Up Use External Port as a digital input port
Floating connection will be considered as '1'
3 (default) DI_PD Digital Input Pull-Down Use External Port as a digital input port
Floating connection will be considered as '0'
Shutdown (63)
The Dynamixel can protect itself by detecting dangerous situations that could occur during the operation.
Each Bit is inclusively processed with the ‘OR’ logic, therefore, multiple options can be generated.
For instance, when ‘0x05’ (binary : 00000101) is defined as Shutdown(63), Dynamixel can detect both Input Voltage Error(binary : 00000001) and Overheating Error(binary : 00000100).
The controller can confirm present status of DYNAMIXEL by checking if the Hardware Error Bit(0x80) is set in the Error field of the Status Packet or by directly reading the Hardware
Error Status(70).
If those errors are detected, Torque Enable(64) is cleared to ‘0’ and the motor output becomes 0[%].
REBOOT is the only method to reset Torque Enable(64) to ‘1’(Torque ON) after the shutdown.
The followings are detectable situations.
Shutdown Definition Description
bit 7 0x80 - Unused, always ‘0’
bit 6 0x40 - Unused, always ‘0’
bit 5 0x20 Overload Error(Default) Detect persistent load that exceeds maximum output
bit 4 0x10 Electrical Shock Error(Default) Detect electrical shock on the circuit, or input power is insufficient to operate the motor
bit 3 0x08 Motor Encoder Error Detect malfunction of the motor encoder
bit 2 0x04 Overheating Error(Default) Detect internal temperature exceeds the configured operating temperature
bit 1 0x02 - Unused, always ‘0’
bit 0 0x01 Input Voltage Error Detect input voltage exceeds the configured operating voltage
Note : If Shutdown occurs, use below method to REBOOT Dynamixels.
① H/W REBOOT : Turn off the power and turn on again
② S/W REBOOT : Transmit REBOOT Instruction (For more details, please refer to the Protocol section of e-Manual.)
If Shutdown occurs, LED will flicker every second.(Firmware v41 or above)
RAM Area
Torque Enable (64)
Controls Torque ON/OFF. Writing ‘1’ to this address will turn on the Torque and all Data in the EEPROM area will be protected.
Values Description
0(Default) Torque OFF(Free-run) and the motor does not generate torque.
1Torque ON and all Data in the EEPROM area will be locked.
Note : Present Position(132) can be reset when Operating Mode(11) and Torque Enable(64) are updated. For more details, please refer to the Homing Offset(20) and Present Position(132).
LED (65)
Turn on or turn off the LED. Dynamixel LED can only be controlled by LED(65).
Values Description
Values Description
0(Default) Turn off the LED.
1Turn on the LED.
Status Return Level (68)
This value decides how to return Status Packet when Dynamixel receives an Instruction Packet.
Values When to return
Status Packet Description

2/22/2018 XM540-W150
http://support.robotis.com/en/product/actuator/dynamixel_x/xm_series/xm540-w150.htm 9/17
0PING Instruction Status Packet will not be returned for all Instructions. (Exception : PING Instruction)
1PING Instruction
READ Instruction
Status Packet will only be returned for READ Instruction.
exceptionally returns Status Packet to all Instruction.
2All Instructions Status Packet will be returned for all Instructions.
Note : If the ID of Instruction Packet is set to Broad Cast ID(0xFE), Status Packet will not be returned for READ and WRITE Instructions regardless of Status Return Level(68). For more details, please
refer to the Protocol section of e-Manual
Registered Instruction (69)
This value will be set to ‘1’ when Dynamixel receives REG_WRITE Instruction Packet while processing ACTION Instruction Packet will clear this value to ‘0’.
Hardware Error Status (70)
This value indicates hardware error status. For more details, please refer to the Shutdown(63).
Velocity I Gain (76), Velocity P Gain (78)
These values indicate Gains of Velocity Control Mode. Gains of Dynamixel’s internal controller can be calculated from Gains of the Control Table as shown below. The constant in each equations include
sampling time. Velocity P Gain of Dynamixel’s internal controller is abbreviated to KVP and that of the Control Table is abbreviated to KVP(TBL).
Controller Gain Conversion Equations Range Description
Velocity I Gain(76) KVIKVI = KVI(TBL) / 65,536 0 ~ 16,383 I Gain
Velocity P Gain(78) KVPKVP = KVP(TBL) / 128 0 ~ 16,383 P Gain
Below figure is a block diagram describing the velocity controller in Velocity Control Mode. When the instruction transmitted from the user is received by Dynamixel, it takes following steps until driving the
horn.
① An Instruction from the user is transmitted via Dynamixel bus, then registered to Goal Velocity(104).
② Goal Velocity(104) is converted to target velocity trajectory by Profile Acceleration(108).
③ The target velocity trajectory is stored at Velocity Trajectory(136).
④ PI controller calculates PWM output for the motor based on the target velocity trajectory.
⑤ Goal PWM(100) sets a limit on the calculated PWM output and decides the final PWM value.
⑥ The final PWM value is applied to the motor through an Inverter, and the horn of Dynamixel is driven.
⑦ Results are stored at Present Position(132), Present Velocity(128), Present PWM(124) and Present Current(126).
Note : Ka stands for Anti-windup Gain and ‘β’ is a conversion coefficient of position and velocity that cannot be modified by users. For more details about the PID controller, please refer to the below
website.
http://en.wikipedia.org/wiki/PID_controller
Position D Gain (80), Position I Gain (82), Position P Gain (84)
Feedforward 2nd Gain (88), Feedforward 1st Gain (90)
These Gains are used in Position Control Mode and Extended Position Control Mode. Gains of Dynamixel’s internal controller can be calculated from Gains of the Control Table as shown below. The
constant in each equations include sampling time. Position P Gain of Dynamixel’s internal controller is abbreviated to KPP and that of the Control Table is abbreviated to KPP(TBL).
Controller Gain Conversion Equation Range Description
Position D Gain(76) KPDKPD = KPD(TBL) / 16 0 ~ 16,383 D Gain
Position I Gain(76) KPIKPI = KPI(TBL) / 65,536 0 ~ 16,383 I Gain
Position P Gain(78) KPPKPP = KPP(TBL) / 128 0 ~ 16,383 P Gain
Feedforward 2nd Gain(88) KFF2nd KFF2nd = KFF2nd(TBL) / 4 0 ~ 16,383 Feedforward Acceleration Gain
Feedforward 1st Gain(90) KFF1st KFF1st = KFF1st(TBL) / 4 0 ~ 16,383 Feedforward Velocity Gain
Below figure is a block diagram describing the position controller in Position Control Mode and Extended Position Control Mode. When the instruction from the user is received by Dynamixel, it takes
following steps until driving the horn.
① An Instruction from the user is transmitted via Dynamixel bus, then registered to Goal Position(116).
② Goal Position(116) is converted to target position trajectory and target velocity trajectory by Profile Velocity(112) and Profile Acceleration(108).
③ The target position trajectory and target velocity trajectory is stored at Position Trajectory(140) and Velocity Trajectory(136) respectively.
④ Feedforward and PID controller calculate PWM output for the motor based on target trajectories.
⑤ Goal PWM(100) sets a limit on the calculated PWM output and decides the final PWM value.
⑥ The final PWM value is applied to the motor through an Inverter, and the horn of Dynamixel is driven.
⑦ Results are stored at Present Position(132), Present Velocity(128), Present PWM(124) and Present Current(126).

2/22/2018 XM540-W150
http://support.robotis.com/en/product/actuator/dynamixel_x/xm_series/xm540-w150.htm 10/17
Note1) : In case of PWM Control Mode, both PID controller and Feedforward controller are deactivated while Goal PWM(100) value is directly controlling the motor through an Inverter. In this manner,
users can directly control the supplying voltage to the motor.
Note2) : Ka is an Anti-windup Gain that cannot be modified by users.
Below figure is a block diagram describing the current-based position controller in Current-based Position Control Mode. As Current-based Position Control Mode is quite similar to Position Control Mode,
differences will be focused in the following steps. The differences are highlighted with a green marker in the block diagram as well.
① Feedforward and PID controller calculates target current based on target trajectory.
② Goal Current(102) decides the final target current by setting a limit on the calculated target current.
③ Current controller calculates PWM output for the motor based on the final target current.
④ Goal PWM(100) sets a limit on the calculated PWM output and decides the final PWM value.
⑤ The final PWM value is applied to the motor through an Inverter, and the horn of Dynamixel is driven.
⑥ Results are stored at Present Position(132), Present Velocity(128), Present PWM(124) and Present Current(126).
Note : Ka is an Anti-windup Gain that cannot be modified by users. For more details about the PID controller and Feedforward controller, please refer to the below websites.
http://en.wikipedia.org/wiki/PID_controller
https://en.wikipedia.org/wiki/Feed_forward_(control)
Bus Watchdog (98, Available after Firmware version 38)
Bus Watchdog (98) is a safety device (Fail-safe) that stops the Dynamixel if the communication between the controller and Dynamixel communication (RS485, TTL) is disconnected due to an unspecified
error.
Communication is defined as all the Instruction Packet in the Dynamixel Protocol.
Values Description
Unit 20[ms]
Range
0 Deactivate Bus Watchdog Function, Clear Bus Watchdog Erro
1 ~ 127 Activate Bus Watchdog
-1 Bus Watchdog Error Status
The Bus Watchdog function monitors the communication interval (time) between the controller and Dynamixel when Torque Enable (64) is '1'.
If the measured communication interval (time) is larger than Bus Watchdog (98), the Dynamixel will stop. Bus Watchdog (98) will be changed to '-1' (Bus Watchdog Error).
If the Bus Watchdog Error screen appears, the Goal Value (Goal PWM(100), Goal Current(102), Goal Velocity(104), Goal Position(116)) will be changed to read-only-access.
Therefore, when a new value is written to the Goal Value, a Range Error will be returned via the Status packet.
If the value of Bus Watchdog (98) is changed to '0', Bus Watchdog Error will be cleared.
Note: For details of Range Error, please refer to the protocol of the e-Manual.
The following are examples of the operation of the Bus Watchdog function.
① After setting the operating mode (11) to speed control mode, change the Torque Enable (64) to '1'.
② If '50' is written in the Goal Velocity (104), the Dynamixel will rotate in CCW direction.
③ Change the value of Bus Watchdog (98) to '100' (2,000 [ms]). (Activate Bus Watchdog Function)
④ If no instruction packet is received for 2,000 [ms], the Dynamixel will stop. When it stops, the Profile Acceleration (108) and Profile Velocity (112) are applied as '0'.
⑤ The value of Bus Watchdog (98) changes to '-1' (Bus Watchdog Error). At this time, the access to the Goal Value will be changed to read-only.
⑥ If '150' is written to the Goal Velocity (104), Range Error will be returned via Status Packet.
⑦ If the value of Bus Watchdog (98) is changed to '0', Bus Watchdog Error will be cleared.
⑧ If “150” is written in the Goal Velocity (104), the Dynamixel will rotate in CCW direction.

2/22/2018 XM540-W150
http://support.robotis.com/en/product/actuator/dynamixel_x/xm_series/xm540-w150.htm 11/17
Goal PWM (100)
In case of PWM Control Mode, both PID controller and Feedforward controller are deactivated while Goal PWM(100) value is directly controlling the motor through an Inverter. In other control modes, this
value is used to limit PWM value. This value cannot exceed PWM Limit(36). Please refer to the Gain section in order to see how Goal PWM(100) affects to different control modes.
Values Description
Range -PWM Limit(36) ~ PWM Limit(36) Initial Value of PWM Limit(36) : ‘885’
Goal Current (102)
In case of Torque Control Mode, Goal Current(102) can be used to set a target current. This value sets a limit to current in Current-based Position Control mode. This value cannot exceed Current Limit(38).
Values Description
Unit about 2.69[mA] All current related Data uses the same unit
Range - Current Limit(38) ~ Current Limit(38) -
Note : Applying high current to the motor for a long period of time could damage the motor.
Goal Velocity (104)
In case of Velocity Control Mode, Goal Velocity(104) can be used to set a target velocity. This value cannot exceed Velocity Limit(44). For now, Goal Velocity(104) is used for target velocity, but this value is
not used to limit the velocity.
Values Description
Unit 0.229[RPM] All velocity related Data uses the same unit
Range -Velocity Limit(44) ~ Velocity Limit(44) -
Note1) : The maximum velocity and maximum torque of Dynamixel is affected by supplying voltage. Therefore, if supplying voltage changes, so does the maximum velocity. This manual complies with
recommended supply voltage.
Note2) : If Profile Acceleration(108) and Goal Velocity(104) are modified simultaneously, modified Profile Acceleration(108) will be used to process Goal Velocity(104).
Profile Acceleration (108)
The acceleration of Profile can be set with this value. Profile Acceleration(108) can be used in all control modes except Torque Control Mode. Profile Acceleration(108) cannot exceed Acceleration Limit(40).
For more details, please refer to the Profile Velocity(112).
Values Description
Unit 214.577[Rev/min2]All acceleration related Data uses the same unit,
Range 0 ~ Acceleration Limit(40) The value '0' on Profile Acceleration(108) means infinite acceleration.
Profile Velocity (112)
The Maximum velocity of Profile can be set with this value.
Profile Velocity(112) can be used in all control modes except Torque Control Mode and Velocity Control Mode.
Profile Velocity(112) cannot exceed Velocity Limit(44).
Velocity Control Mode only uses Profile Acceleration(108) instead of Profile Velocity(112).
Values Description
Unit 0.229[RPM] All velocity related Data uses the same unit
Range 0 ~ Velocity Limit(44) If Profile Velocity(112) is set to ‘0’, it stands for infinite velocity.
The Profile is an acceleration/deceleration control method to reduce vibration, noise and load of the motor by controlling dramatically changing velocity and acceleration.
It is also called Velocity Profile as it controls acceleration and deceleration based on velocity.
Dynamixel provides 4 different types of Profile. The following explains 4 Profiles and how to select them.
Profiles are usually selected by a combination of Profile Velocity(112) and Profile Acceleration(108).
Triangular and Trapezoidal Profiles exceptionally consider total travel distance(ΔPos, the distance difference between target position and present position) as an additional factor.
For convenience, Profile Velocity(112) is abbreviated to VPRFL and Profile Acceleration(108) is abbreviated to VPRFL.
'X' stands for "Don't Care" case.
When given Goal Position(116), Dynamixel's profile creates target velocity trajectory based on present velocity(initial velocity of the Profile).
When Dynamixel receives updated target position from a new Goal Position(116) while it is moving toward the previous Goal Position(116), velocity smoothly varies for the new target velocity trajectory.
Maintaining velocity continuity while updating target velocity trajectory is called Velocity Override.
For a simple calculation, let's assume that the initial velocity of the Profile is '0'.
The following explains how Profile processes Goal Position(116) instruction in Position Control mode, Extended Position Control Mode, Current-based Position Control Mode.
① An Instruction from the user is transmitted via Dynamixel bus, then registered to Goal Position(116).
② Acceleration time(t1) is calculated from Profile Velocity(112) and Profile Acceleration(108).
③ Types of Profile is decided based on Profile Velocity(112), Profile Acceleration(108) and total travel distance(ΔPos, the distance difference between target position and present position)
Condition Types of Profile

2/22/2018 XM540-W150
http://support.robotis.com/en/product/actuator/dynamixel_x/xm_series/xm540-w150.htm 12/17
VPRFL(112) = 0 Profile not used (Step Instruction)
(VPRFL(112) ≠ 0) & (APRF(108) = 0) Rectangular Profile
(VPRFL(112) ≠ 0) & (APRF(108) ≠ 0) & (VPRFL_TRI ≤ VPRFL(112))Triangular Profile
(VPRFL(112) ≠ 0) & (APRF(108) ≠ 0) & (VPRFL_TRI > VPRFL(112))Trapezoidal Profile
④ Selected Profile type is stored at Moving Status(123).(Refer to the Moving Status(123))
⑤ Dynamixel is driven by the calculated target trajectory from Profile.
⑥ Target velocity trajectory and target position trajectory from Profile are stored at Velocity Trajectory(136) and Position Trajectory(140) respectively.
⑦ VPRFL_TRI of ③ and Travel time(t3) to reach Goal Position(116) is calculated as below..
Note1) : Dynamixel supports Jerk control in order to minimize dramatic change of acceleration. Therefore, actual travel time by the target trajectory of Profile could be longer than t3(t4 of above figure).
Note2) : Velocity Control Mode only uses Profile Acceleration(108). Step and Trapezoidal Profiles are supported. Velocity Override and Jerk control are supported as well. Acceleration time(t1) can be
calculated as below equation.
Goal Position (116)
Target position can be set with Goal Position(116). From the front view of Dynamixels, CCW is an increasing direction whereas CW is a decreasing direction.
The way to reaching Goal Position(116) is differ by 4 Profiles provided by Dynamixels. Please refer to the Profile Velocity(112) for more details.
Values Description
Unit 0.088[deg] 1[rev] : 0 ~ 4,095
Range
Position Control Mode Min Position Limit(52) ~ Max Position Limit(48) Initial Value : 0 ~ 4,095
Extended Position Control Mode
-1,048,575 ~ 1,048,575 -256[rev] ~ 256[rev]
Current-based Position Control Mode
Note : If Profile Acceleration(108), Profile Velocity(112) and Goal Position(116) are modified simultaneously, Goal Position(116) is processed based on updated Profile Acceleration(108) and Profile
Velocity(112).
Realtime Tick (120)
This value indicates Dynamixel's time.
Values Description
Unit 1[ms] -
Range 0 ~ 32,767 The value resets to '0' when it exceeds 32,767
Moving (122)

2/22/2018 XM540-W150
http://support.robotis.com/en/product/actuator/dynamixel_x/xm_series/xm540-w150.htm 13/17
This value indicates whether Dynamixel is in motion or not. If absolute value of Present Velocity(128) is greater than Moving Threshold(24), Moving(122) is set to '1'. Otherwise, it will be cleared to '0'.
However, this value will always be set to '1' regardless of Present Velocity(128) while Profile is in progress with Goal Position(116) instruction.
Moving Description
0Movement is not detected
1Movement is detected, or Profile is in progress(Goal Position(116) instruction is being processed)
Moving Status (123)
This value provides additional information about the movement. Following Error Bit(0x08) and In-Position Bit(0x01) only work with Position Control Mode, Extended Position Control Mode, Current-based
Position Control Mode.
Moving Status Details Description
Bit 7 0x80 - Unused
Bit 6 0x40 - Unused
Bit 5
~
Bit 4
0x30
Profile Type(0x30) Trapezoidal Velocity Profile
Profile Type(0x20) Triangular Velocity Profile
Profile Type(0x10) Rectangular Velocity Profile
Profile Type(0x00) No Profile Used (Step)
Bit 3 0x08 Following Error Dynamixel fails to reach target position trajectory
Bit 2 0x04 - Unused
Bit 1 0x02 Profile Ongoing Profile is in progress with Goal Position(116) instruction
Bit 0 0x01 In-Position Dynamixel is reached to target position
Present PWM (124)
This value indicates present PWM. For more details, please refer to the Goal PWM(100).
Present Current (126)
This value indicates present Current. For more details, please refer to the Goal Current(102).
Present Velocity (128)
This value indicates present Velocity. For more details, please refer to the Goal Velocity(104).
Present Position (132)
This value indicates present Position. For more details, please refer to the Goal Position(116)
Note : Present Position(132) represents 4[byte] continuous range(-2,147,483,648 ~ 2,147,483,647) when Torque is turned off regardless of Operating Mode(11).
However, Present Position(132) is reset in those cases:
Case 1) Present Position(132) is reset with the value within 1[rev] (0 ~ 4,095) when Operating Mode(11) is changed to Position Control Mode.
Case 2) Present Position(132) is reset with the value within 1[rev] (0 ~ 4,095) when Torque is turned on in Position Control Mode.
Homing Offset(20) can affect to the Present Position(132) value.
Velocity Trajectory (136)
This is a target velocity trajectory created by Profile. Operating method can be changed based on control mode. For more details, please refer to the Profile Velocity(112).
① Velocity Control Mode : When Profile reaches to the endpoint, Velocity Trajectory(136) becomes equal to Goal Velocity(104).
② Position Control Mode, Extended Position Control Mode, Current-based Position Control Mode : Velocity Trajectory is used to create Position Trajectory(140).
When Profile reaches to endpoint, Velocity Trajectory(136) is cleared to '0'.
Position Trajectory (140)
This is a target position trajectory created by Profile. This value is only used in Position Control Mode, Extended Position Control Mode, Current-based Position Control Mode. For more details, please refer
to the Profile Velocity(112).
Present Input Voltage (144)
This value indicates present voltage that is being supplied. For more details, please refer to the Max/Min Voltage Limit(32, 34).
Present Temperature (146)
This value indicates internal temperature of Dynamixel. For more details, please refer to the Temperature Limit(31).
External Port Data 1, 2, 3 (152, 153 ~ 156, 157)
Through External Port Data, signal on the External Port can be read or data can be written on the External Port.
The External Port is not electrically insulated, therefore abide by the electrical specifications.
For more accurate measurement, use shielded cable or twisted cable.
The shorter the length, the better the result.

2/22/2018 XM540-W150
http://support.robotis.com/en/product/actuator/dynamixel_x/xm_series/xm540-w150.htm 14/17
External Port
Mode
External Port Data External Port
Electrical Characteristics
Access Details
Common - -
0 ~ 3.3[V], 0 ~ 5[mA]
VESD(HBM) : 2[kV]
0(AI) Read Converts External Port signal to digital value
External Data = signal x (4,095 / 3.3) Resolution : 12[bit] (0 ~ 4,095)
1(DO_PP) Write 0 : Set External Port output to 0[V]
1 : Set External Port output to 3.3[V]
Output High level(VOH) : 2.4 [V] (min)
Output Low level(VOL) : 0.5 [V] (max)
2(DI_PU)
3 (DI_PD) Read 0: External Port input is 0[V]
1 : External Port input is 3.3[V]
Input High level(VIH) : 2.3 [V] (min)
Input Low level(VIL) : 1.0 [V] (max)
Pull-Up/Down : 40 [kΩ] (typ)
※ VESD(HBM) : ESD(Electrostatic Discharge) Voltage(human body model)
The External Port is not electrically insulated, therefore, abide by the electrical specifications.
If the electrical specification is exceeded or there is a problem with the signal connection, special caution is required because
DYNAMIXEL can be damaged.
1. Be careful not to cause electric shock by static electricity (ESD), short circuit, open circuit.
2. Be careful not to let water or dust get into the External Port connector.
3. If you are not using the External Port, remove the cable.
4. To connect or disconnect the External Port, proceed with power off.
5. Do not connect the GNDext pin of External Port directly to the GND pin of DYNAMIXEL connector. Noise from power may affect
on the External Port.
Indirect Address 1 ~ 28 (168, 170 ~ 220, 222), Indirect Address 29 ~ 56 (578, 580 ~ 630, 632)
Indirect Data 1 ~ 28 (224, 225 ~ 250, 251), Indirect Data 29 ~ 56 (634, 635 ~ 660, 661)
Indirect Address and Indirect Data are useful when accessing two remote addresses in the Control Table as sequential addresses. Sequential addresses increase Instruction Packet efficiency. Addresses
that can be defined as Indirect Address is limited to RAM area(Address 64 ~ 661).
If specific address is allocated to Indirect Address, Indirect Address inherits features and properties of the Data from the specific Address. Property includes Size(Byte length), value range, and Access
property(Read Only, Read/Write). For instance, allocating 65(Address of LED) to Indirect Address 1(168), Indirect Data 1(224) can perform exactly same as LED(65).
① Example 1) Allocating Size 1[byte] LED(65) to Indirect Data 1(224)
A. Indirect Address 1(168) : change the value to '65' which is the address of LED
B. Set Indirect Data 1(224) to ‘1’ -> LED(65) also becomes '1' and LED is turned on.
C. Set Indirect Data 1(224) to ‘0’ -> LED(65) also becomes ‘0’ and LED is turned off.
② Example 2) Allocating Size 4[byte] Goal Position(116) to Indirect Data 2(225), all 4[byte] has to be allocated.
A. Indirect Address 2(170) : change the value to '116' which is the first address of Goal Position.
B. Indirect Address 3(172) : change the value to '117' which is the first address of Goal Position.
C. Indirect Address 4(174) : change the value to '118' which is the first address of Goal Position.
D. Indirect Address 5(176) : change the value to '119' which is the first address of Goal Position.
E. Set 4[byte] value '1024' to Indirect Data 2 -> Goal Position(116) also becomes '1024 and Dynamixel moves.
Indirect Address Values Description
Range 64~661 Indirection Address can't be allocated with EEPROM area
Note 1) : In order to allocate Data in the Control Table longer than 2[byte] to Indirect Address, all address must be allocated to Indirect Address like the above Example 2.
Note 2) : Indirect Address 29 ~ 56 and Indirect Data 29 ~ 56 can only be accessed with Protocol 2.0.
Wiring Instructions through hollow back case

2/22/2018 XM540-W150
http://support.robotis.com/en/product/actuator/dynamixel_x/xm_series/xm540-w150.htm 15/17
Caution for Dynamixel X-Series cable assembly through hollow case
Organize the entangled cable before assembling the back case.
Do not assemble the back case with entangled cable. The entangled cable can be squashed by the case and cause communication error.

2/22/2018 XM540-W150
http://support.robotis.com/en/product/actuator/dynamixel_x/xm_series/xm540-w150.htm 16/17
Combination
This manual suits for next models
2
Table of contents
Other Robotis Controllers manuals
Popular Controllers manuals by other brands
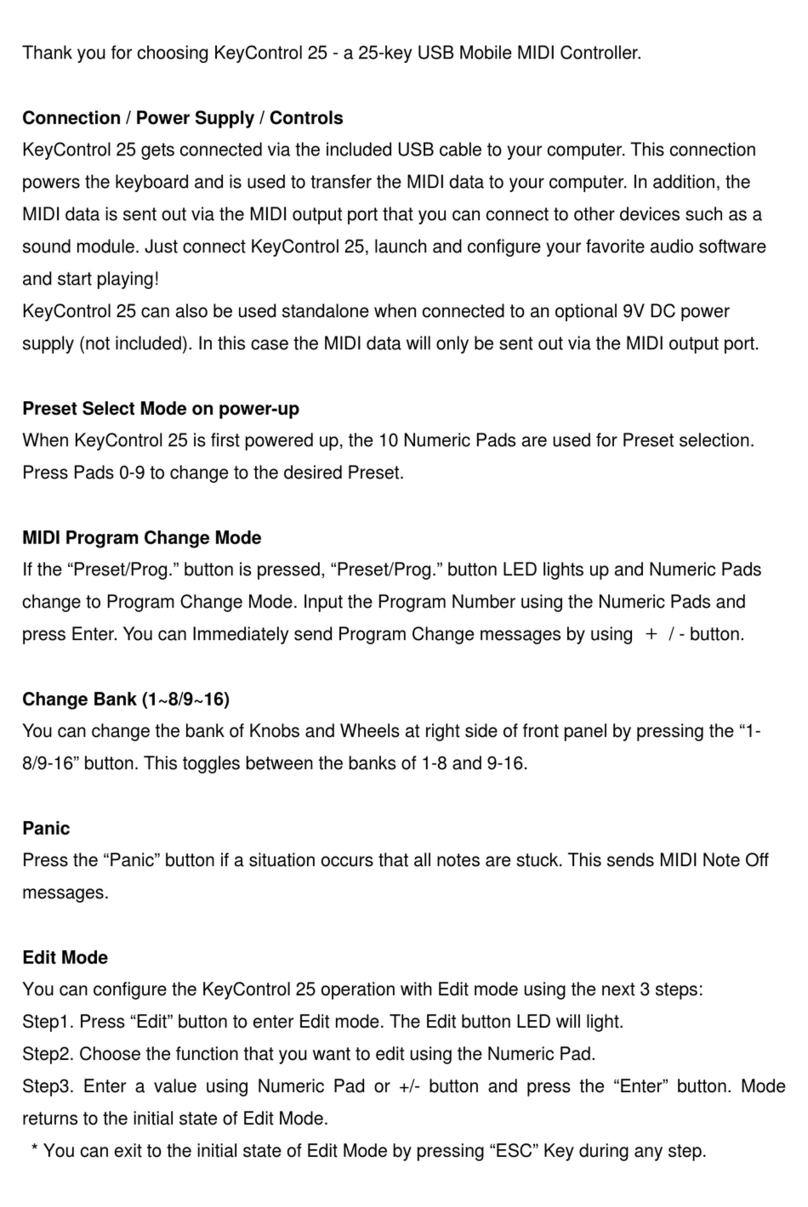
ESI
ESI KeyControl 25 XL manual
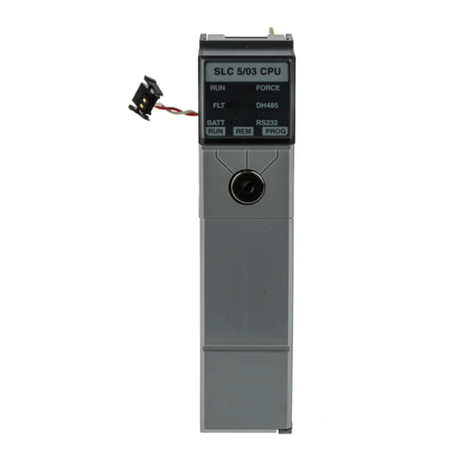
Allen-Bradley
Allen-Bradley SLC 500 Series manual
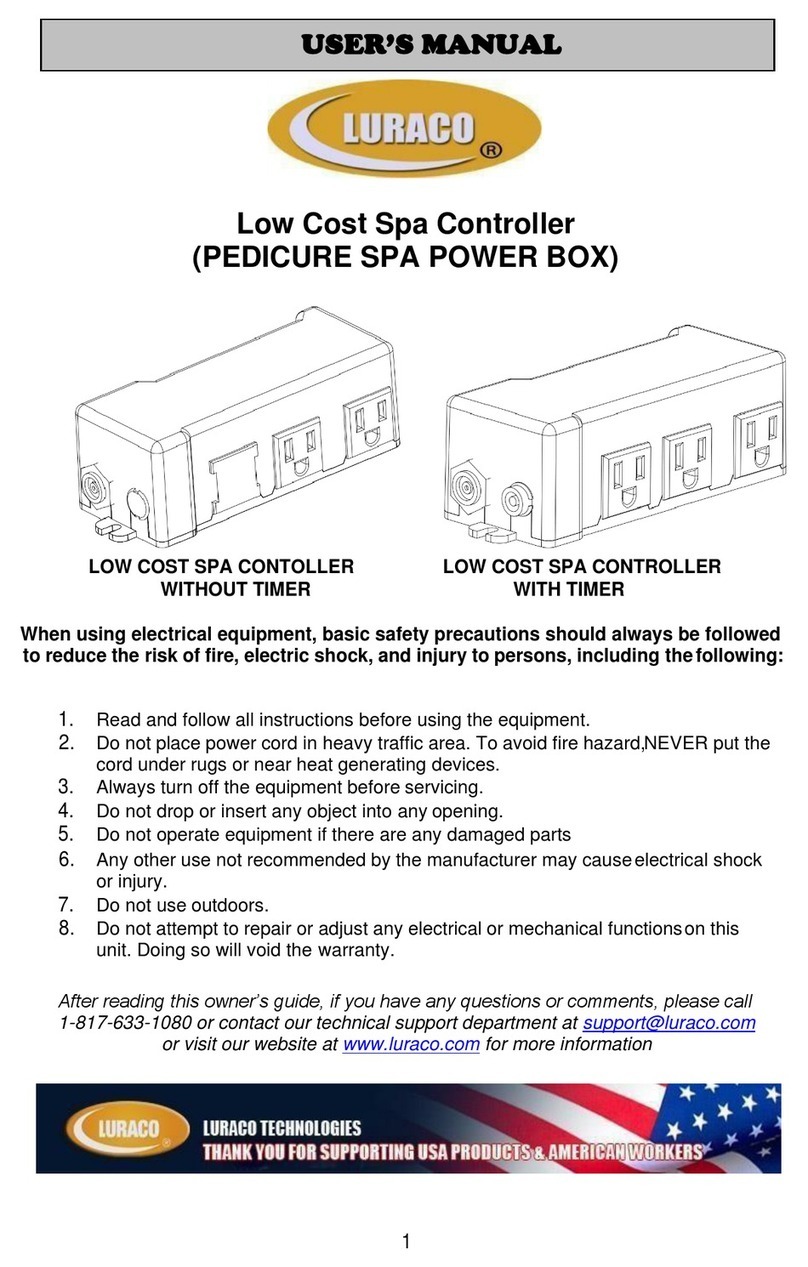
Luraco
Luraco LOW COST SPA CONTOLLER WITHOUT TIMER user manual
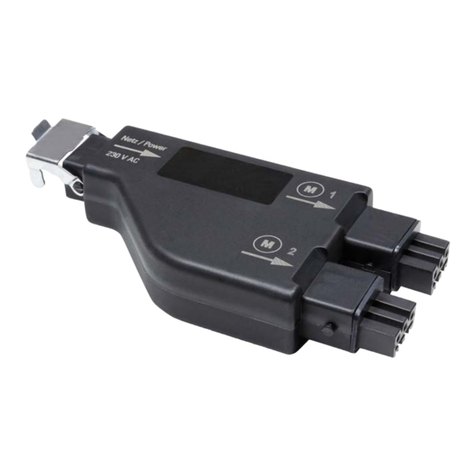
elsner elektronik
elsner elektronik RF-MSG2-DST Technical specifications and installation instructions
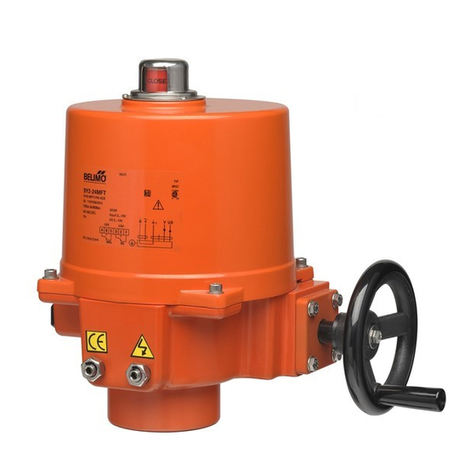
Belimo
Belimo SY4 Series QUICK MOUNT VISUAL INSTRUCTION MANUAL
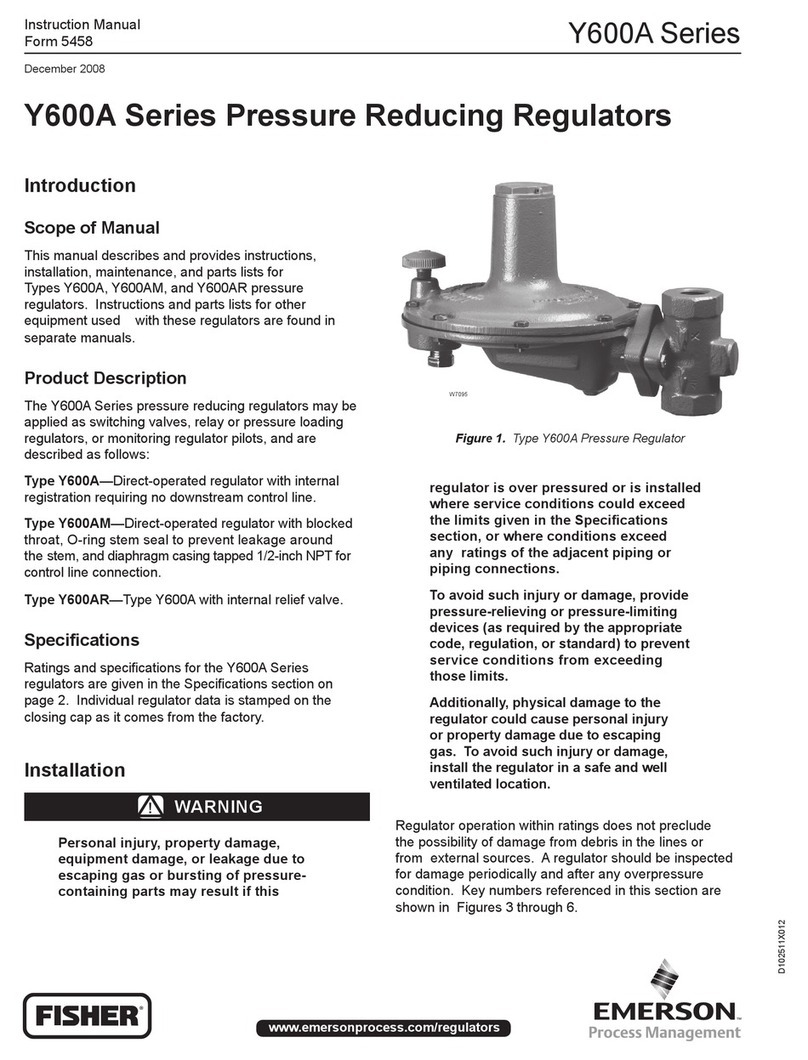
Emerson
Emerson Fisher Y600A Series instruction manual
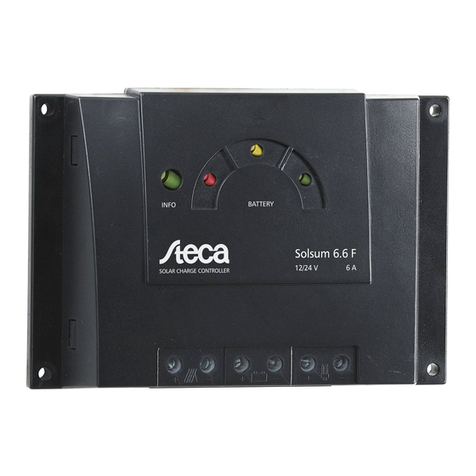
Steca
Steca Solsum 6.6F operating manual
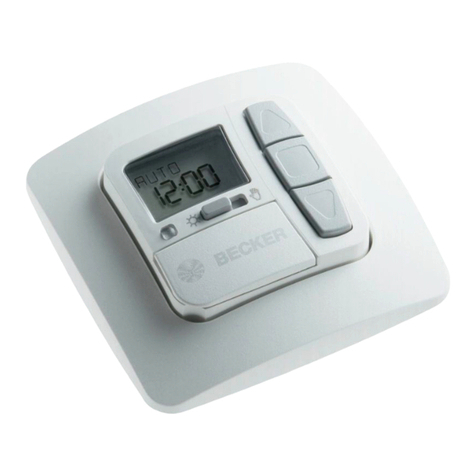
Becker
Becker Centronic SunWindSet SWS42 Assembly and operating instructions

DigiTrace
DigiTrace TCONTROL-CONT-03 manual
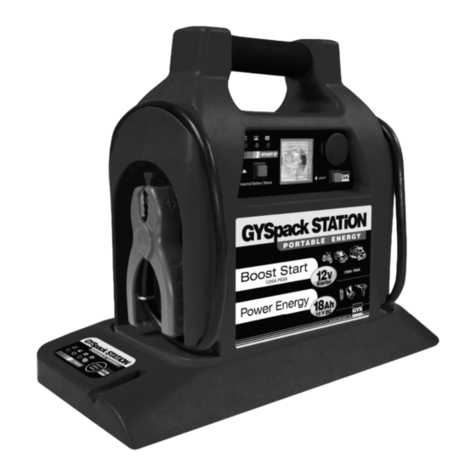
GYS
GYS GYSPACK AIR manual
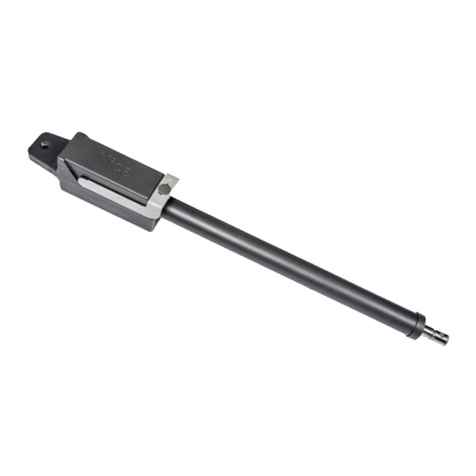
Nice HySecurity
Nice HySecurity TITAN 912L Series Installation & reference manual
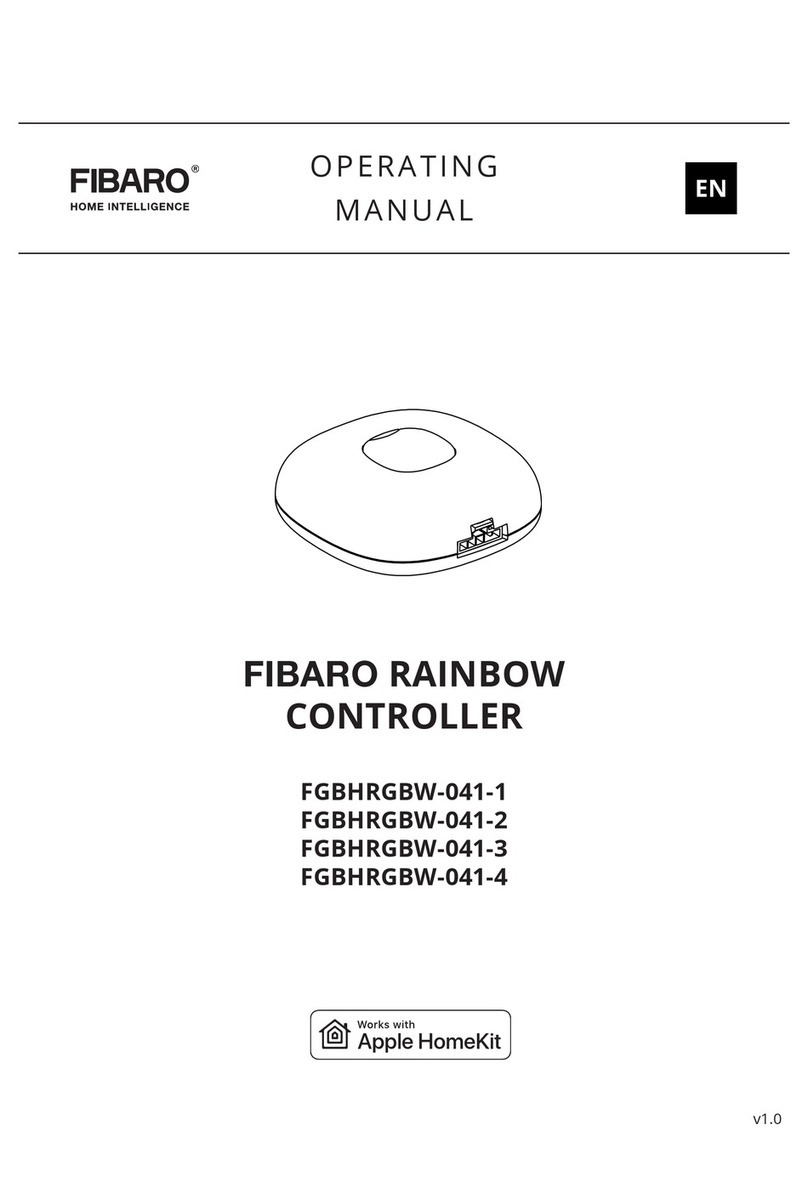
FIBARO
FIBARO FGBHRGBW-041-1 operating manual