Rockwell Automation Allen-Bradley Guardmaster SafeZone 3 User manual

Installation Instructions
Original Instructions
SafeZone 3 Safety Laser Scanner Mounting
Catalog Numbers 442L-SZNMZCP, 442L-SZNCPMOD
Summary of Changes
This publication contains the following new or updated information. This list
includes substantive updates only and is not intended to reflect all changes.
About This Document
This document applies to the SafeZone™ 3 Safety Laser Scanner and the
associated system plug with catalog numbers 442L-SZNMZCP and
442L-SZNCPMOD.
Safety Information
The safety laser scanner is not suitable for the following applications, among
others:
• Outdoors
• Underwater
• Explosive environments
For detailed information on the application and configuration of the SafeZone 3
safety laser scanner, see publication 442L-UM008.
Device Overview
Install the System Plug
The SafeZone 3 safety laser scanner and the system plug are sold separately and
require the system plug to be installed on the SafeZone 3 safety laser scanner.
The SafeZone 3 safety laser scanner has a protective cover over both the back and
bottom mounting slots. When you install a system plug on the safety laser scanner,
the environment must be clean and free of fog, moisture, and dust. Follow these
steps to install the system plug:
1. Determine how the SafeZone 3 safety laser scanner must mount in the
application.
2. Determine the best location to mount the system plug, either in the back
or bottom of the scanner.
3. Remove the protective cover from the chosen mounting slot with a T20
torx driver.
4. Carefully insert the system plug into the opening and tighten the two
screws with a T20 torx driver to secure the module. Torque to
2.25…2.75 N•m (19.9…24.3 lb•in).
See Change System Plug Location if the installed system plug must relocate from
one mounting slot to the other.
Change System Plug Location
This process requires a TX20 torx driver.
1. Loosen the screws of the system plug.
2. Remove the system plug from the safety laser scanner slot.
3. Loosen the cover plate screws.
4. Remove the cover plate from the new mounting slot of the safety laser
scanner.
5. Carefully insert the system plug into the opening and tighten the two
screws with a T20 torx driver to secure the module. Torque to
2.25…2.75 N•m (19.9…24.3 lb•in).
6. Attach the cover plate to the open slot of the safety laser scanner and
tighten the screws. Torque to 2.25…2.75 N•m (19.9…24.3 lb•in).
Topic Page
Added Declaration of Conformity 3
ATTENTION: Hazard due to lack of effectiveness of the
SafeZone 3 safety laser scanner. If non-compliant, it is
possible that the dangerous state of the machine does not
stop or not stop in a timely manner.
Observe the safety information provided.
Item Description Item Description
1 Optics cover 6 Additional indicators
2 Display 7 Network indicators
3 Keypad 8 Four M5 mounting inserts
4 USB port (disabled) 9 System plug (mounted in the back)
5 Status indicators 10 System plug (mounted on the bottom)
1
6
3
7
6
5
4
2
8
9
10
IMPORTANT Perform all changes/modifications to the SafeZone 3
safety laser scanner and/or system plug that are
described in this document only after you remove
power to the devices.
See Table 2 on page 2 for XD1 pin assignment and Table 3 on page 2
for XF1 and XF2 connections.

2Rockwell Automation Publication 442L-IN006D-EN-P - November 2022
SafeZone 3 Safety Laser Scanner Mounting Installation Instructions
Direct Mounting
The safety laser scanner has four M5 threaded inserts on the back. If you can drill
through the mounting surface from the rear, you can mount the safety laser
scanner directly with these threaded holes.
• Use either the M5 threaded holes at the back (1) or the M5 threaded holes
at the side (2) for direct mounting.
• Use all four M5 threaded holes at the back or all four M5 threaded holes at
the side for direct mounting, so that the values given in the data sheet for
vibration and shock resistance are achieved.
• Maximum depth of thread engagement is 7.5 mm (0.29 in.).
• Torque to 4.5…5.0 N•m (39.8…44.2 lb•in).
Connection Overview
Pin Assignment
Voltage Supply (Pwr) — XD1
Figure 1 - M12 Convex, 4-pin, A-coded
EtherNet/IP Connection (E/IP) — XF1 and XF2
Figure 2 - M12 Concave, 4-pin, D-coded
Alternative FE Connection
Screw the connection of the alternate FE connection:
• Screw: M5 x 12
• Torque: 3.5…5 N•m
Suitable cable lugs:
• Forked cable lug or ring cable lug
• Width: ≤ 10 mm (0.4 in.)
• Hole diameter for screw: typically 5.2 mm (0.2 in.)
The functional earth must connect via one, and only one, of the available
FE connections:
• Pin on the M12 plug connector
• Thread on the M12 plug connector
• Alternative FE connection
The functional earth must connect in a low-inductance manner and with an
adequate cross-section while keeping the cable length as short as possible.
Functional earth and protection earth must be isolated.
Table 1 - Connection Cables
Description Cat. No.
Power Connection Cable
4-pin, straight M12 QD concave with flying leads, yellow PVC jacket,
22 AWG, 250V, 4 A 889D-F4AC-x (1)
(1) Replace the x with a 2 [2 m (6.56 ft)], 5 [5 m (16.4 ft)], or 10 [10 m (32.81 ft)] for standard cable lengths.
See rockwellautomation.com/en-us/products/hardware/allen-bradley/connection-devices/cables-
and-cordsets/dc-micro--m12-/dc-micro-cordsets-and-patchcords.html for additional information.
4-pin, right M12 QD concave with flying leads, yellow PVC jacket, 22
AWG, 250V, 4 A 889D-R4AC-x (1)
Ethernet Cabling
M12 to flying leads
1585 Ethernet cables, 4 conductors, M12, straight convex, standard,
flying leads, teal PUR, shielded, 100BASE-TX, 100 Mbit/s, high flex,
PUR, halogen-free, 10 million cycles
1585D-M4UB-x (2)
(2) Replace the x with a 2 [2 m (6.56 ft)], 5 [5 m (16.4 ft)], or 10 [10 m (32.81 ft)] for standard cable lengths.
See rockwellautomation.com/en-us/products/hardware/allen-bradley/connection-devices/network-
media/ethernet/1585-m12-and-variant-1.html for additional information.
M12 to M12
1585 Ethernet cables, 4 conductors, M12, straight convex, standard,
M12, teal PUR, shielded, 100BASE-TX, 100 Mbit/s, high flex, PUR,
halogen-free, 10 million cycles
1585D-M4UBDM-x (2)
M12 to M12
1585 Ethernet cables, 4 conductors, M12, straight convex, standard,
M12, right-angle convex, teal PUR, shielded, 100BASE-TX, 100 Mbit/s,
high flex, PUR, halogen-free, 10 million cycles
1585D-M4UBDW-x (2)
M12 to RJ45
1585 Ethernet cables, 4 conductors, M12, straight convex, standard,
RJ45, straight convex, teal PUR, shielded, 100BASE-TX, 100 Mbit/s,
high flex, PUR, halogen-free, 10 million cycles
1585D-M4UBJM-x (2)
1
1
2
2
Table 2 - Voltage Supply Pin Assignment
Pin Designation Function Wire Color (1)
(1) Applies to the recommended connection cables (see Table 1).
1 +24V DC Supply voltage +24V DC Brown
2 NC Not connected White
3 0V DC Supply voltage 0V DC Blue
4 FE Functional earth/shield Black
Table 3 - EtherNet/IP Pin Assignment
Pin Designation Function Wire Color (1)
(1) Applies to the recommended connection cables (see Table 1).
1 TX+ Send data + White/orange
2 RX+ Receive data + White/green
3 TX- Send data - Green
4RX- Receivedata- Orange
12
3 4
4
3
21

Rockwell Automation Publication 442L-IN006D-EN-P - November 2022 3
SafeZone 3 Safety Laser Scanner Mounting Installation Instructions
Replace the Safety Laser Scanner
If the safety laser scanner is damaged or does not function properly, you must
replace the scanner.
This process requires a TX20 torx driver.
Replace the Safety Laser Scanner Without System Plug
1. Verify that the environment is clean and clear of fog,
moisture, and dust.
2. Unscrew the system plug screws and remove the system
plug from the non-functioning safety laser scanner.
3. Unscrew the mounting screws and remove the
non-functioning safety laser scanner.
4. Mount the system plug on the new safety laser scanner,
see Replace the System Plug.
5. Mount the new safety laser scanner, see Direct Mounting on page 2.
6. Check the effectiveness of the SafeZone 3 safety laser scanner. For more
information, see publication 442L-UM008.
Replace the Total Safety Laser Scanner
1. Disconnect the connecting cables from the system plug.
2. Unscrew the mounting screws and remove the
non-functioning safety laser scanner.
3. Mount the new safety laser scanner, see Direct Mounting
on page 2.
4. Reconnect the connecting cables to the system plug.
5. Configure the safety laser scanner.
6. Perform commissioning again. Conduct all thorough checks as described.
For more information, see publication 442L-UM008.
Replace the System Plug
This process requires a TX20 torx driver.
1. Verify that the environment is clean and clear of fog,
moisture, and dust.
2. Disconnect the connecting cables from the system plug.
3. If necessary, move the safety laser scanner to a clean
location.
4. Unscrew the system plug screws from the non-functioning
and remove the system plug from the safety laser scanner.
5. Carefully insert the new system plug into the appropriate mounting slot of
the safety laser scanner.
6. Screw in the system plug with the captive screws. Torque to 2.25…2.75
N•m (19.9…24.3 lb•in).
7. Reconnect the connecting cables to the system plug.
8. Perform commissioning again. Conduct all thorough checks as described.
For more information, see publication 442L-UM008.
Declaration of Conformity
CE Conformity
Rockwell Automation declares that the products that are shown in this document
conform with the Essential Health and Safety Requirements (EHSRs) of the
European Machinery Directive (2006/42/EC) and the EMC Directive (2014/30/EU).
For a comprehensive CE certificate visit: rok.auto/certifications.
UKCA Conformity
Rockwell Automation declares that the products that are shown in this document
are in compliance with the Supply of Machinery (Safety) Regulations (2008 No. 1597)
and the Electromagnetic Compatibility Regulations (2016 No. 1091).
For a comprehensive UKCA certificate visit: rok.auto/certifications.
ATTENTION: Hazard due to lack of effectiveness of the
protective device.
Persons and parts of the body to be protected are not
recognized if not observed.
If an unsuitable configuration is saved in the system plug, the
dangerous state does not end or does not end in time.
After replacement:
• Verify that you use the same system plug or a system plug with
the same configuration.
• Confirm that the safety laser scanner aligns correctly.
IMPORTANT The IP65 enclosure rating only applies if the safety
laser scanner is closed and the system plug is
mounted.
• Mount the system plug and cover plate.
• Close each M12 connector on the safety laser scanner
with a convex cable connector or a protective cap.
- Torque for connection:
0.4…0.6 N•m (3.54…5.31 lb•in)
- Torque for protective caps:
0.6…0.7 N•m (5.31…6.19 lb•in)
• Mount the optics cover.
IMPORTANT Carefully plug in the system plug. Do not force it. The
contacts can break off or bend if too much force is
used.
IMPORTANT The IP65 enclosure rating only applies if the safety
laser scanner is closed and the system plug is
mounted.
• Mount the system plug and cover plate.
• Close each M12 connector on the safety laser scanner
with a convex cable connector or a protective cap.
- Torque for connection:
0.4…0.6 N•m (3.54…5.31 lb•in)
- Torque for protective caps:
0.6…0.7 N•m (5.31…6.19 lb•in)
• Mount the optics cover.
IMPORTANT Carefully plug in the system plug. Do not force it. The
contacts can break off or bend if too much force is
used.

Publication 442L-IN006D-EN-P - November 2022 | Supersedes Publication 442L-IN006C-EN-P-February 2021
Copyright © 2022 Rockwell Automation, Inc. All rights reserved. Printed in the U.S.A.
Rockwell Otomasyon Ticaret A.Ş. Kar Plaza İş Merkezi E Blok Kat:6 34752 İçerenköy, İstanbul, Tel: +90 (216) 5698400 EEE Yönetmeliğine Uygundur
8020211
10002383263 Ver 01
Allen-Bradley, expanding human possibility, Guardmaster, Rockwell Automation, and SafeZone are trademarks of Rockwell Automation, Inc.
EtherNet/IP is a trademark of ODVA, Inc.
Trademarks not belonging to Rockwell Automation are property of their respective companies.
Your comments help us serve your documentation needs better. If you have any suggestions on how to improve our content, complete the form at rok.auto/docfeedback.
For technical support, visit rok.auto/support.
Waste Electrical and Electronic Equipment (WEEE)
Rockwell Automation maintains current product environmental compliance information on its website at rok.auto/pec.
At the end of life, this equipment should be collected separately from any unsorted municipal waste.
Rockwell Automation Support
Use these resources to access support information.
Documentation Feedback
Your comments help us serve your documentation needs better. If you have any suggestions on how to improve our content, complete the form at rok.auto/docfeedback.
Technical Support Center Find help with how-to videos, FAQs, chat, user forums, and product notification updates. rok.auto/support
Knowledgebase Access Knowledgebase articles. rok.auto/knowledgebase
Local Technical Support Phone Numbers Locate the telephone number for your country. rok.auto/phonesupport
Literature Library Find installation instructions, manuals, brochures, and technical data publications. rok.auto/literature
Product Compatibility and Download Center
(PCDC) Download firmware, associated files (such as AOP, EDS, and DTM), and access product release notes. rok.auto/pcdc
This manual suits for next models
2
Other Rockwell Automation Scanner manuals
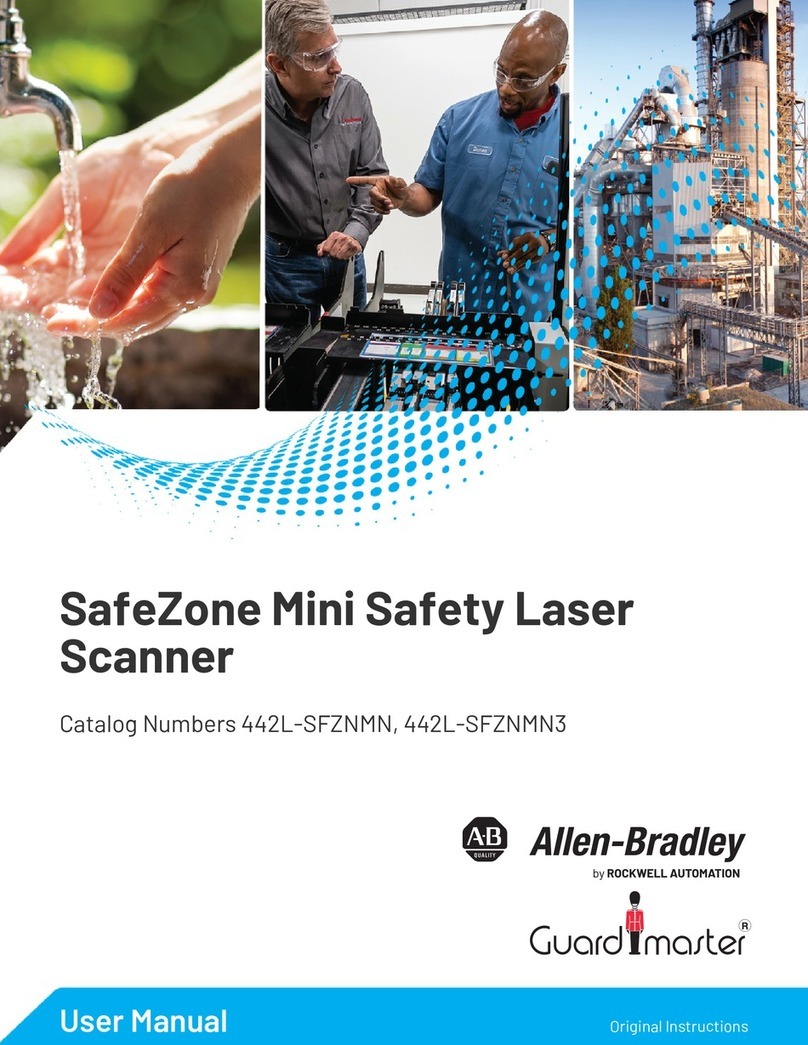
Rockwell Automation
Rockwell Automation Allen-Bradley SafeZone Mini User manual
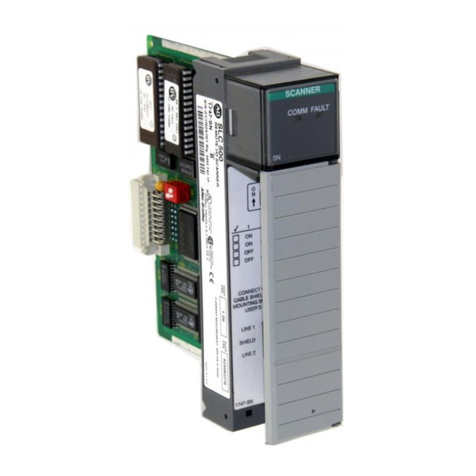
Rockwell Automation
Rockwell Automation Allen-Bradley 1747-SN User manual
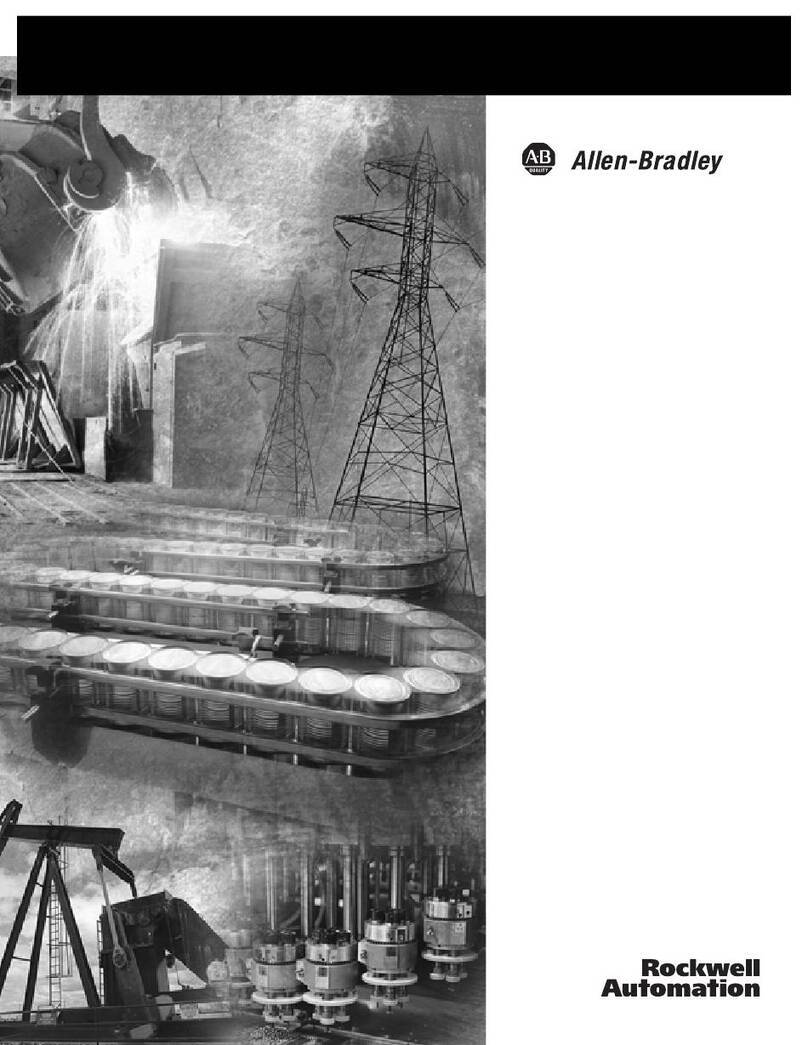
Rockwell Automation
Rockwell Automation AB Quality Allen-Bradley 1753-DNSI User manual
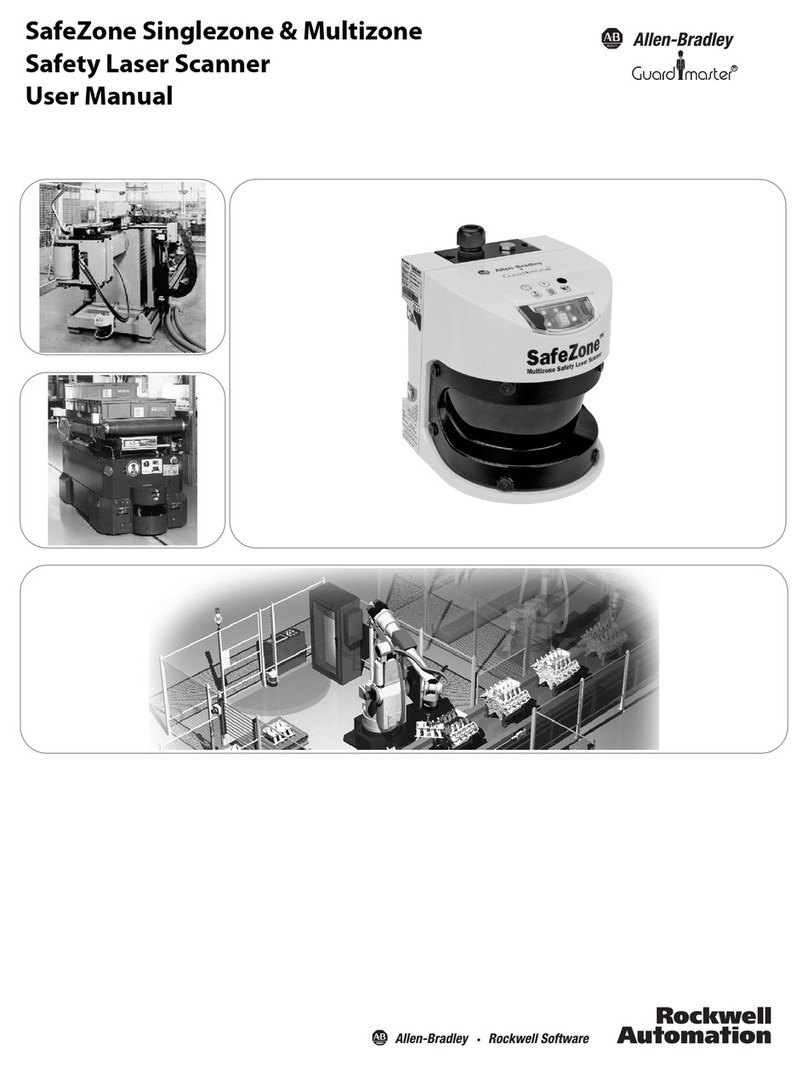
Rockwell Automation
Rockwell Automation Allen-Bradley Guard Master SafeZone User manual
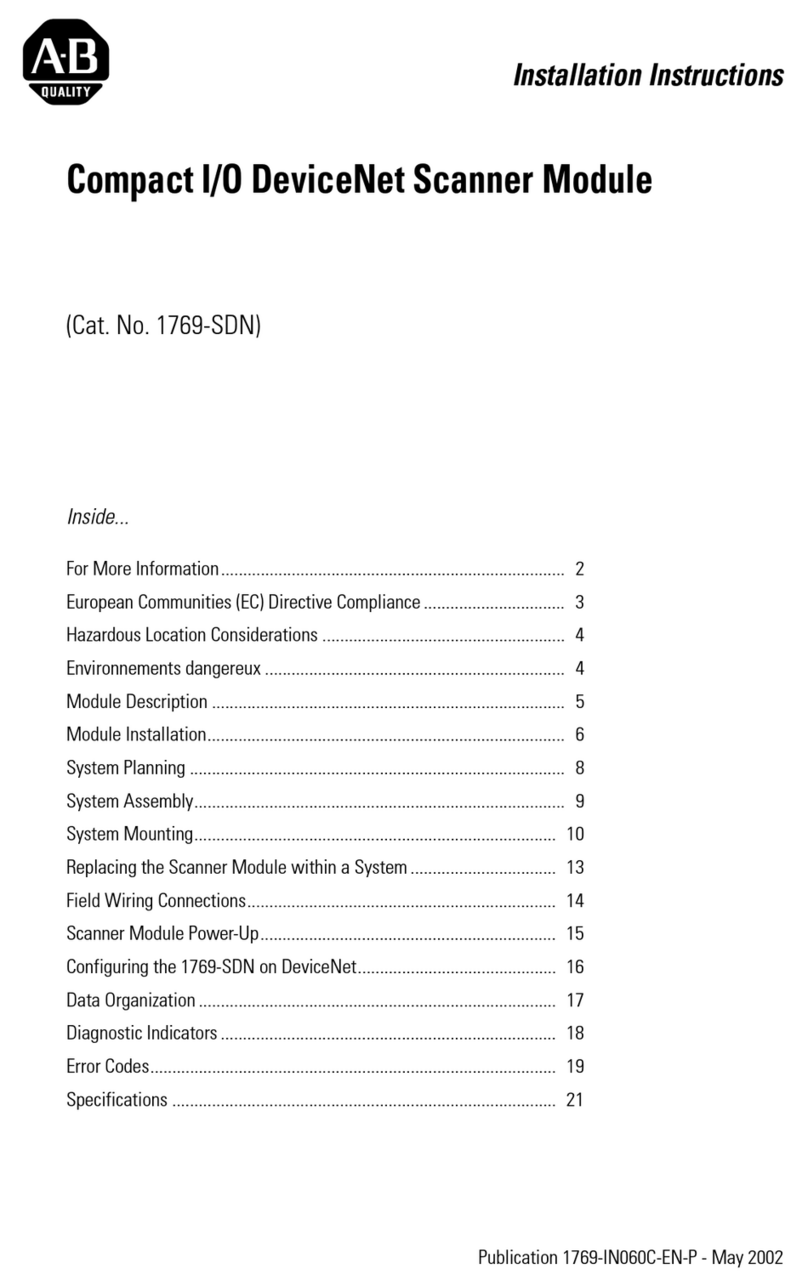
Rockwell Automation
Rockwell Automation 40072-107-01 User manual