RR-Concepts YardMaster-5 User manual

1
This manual contains detailed hookup and programming instructions for the
YardMaster-5 Model Train Controller.
Please download additional hookup diagrams from http://www.RRConcepts.com
Before we Start- Please do not attach Power wires (from your power pack)
to any other terminals except the designated power inputs 3, 4, 5 and 6.
o The YardMaster contains a micro-controller and will be damaged if power is put on any of the sensor terminals.
o Since the YardMaster contains flash memory it will return to the previous state when powered up.
The turnouts will be thrown and the on-board relays will return to their previous states.
o Detachable screw-down terminal blocks allow quick-disconnect for long term storage keeping all wires in place.
ONLY ATTACH WIRES WHILE THE POWER IS OFF.
YardMaster-5
Turnout (Track switch) Controller
Lamp / LED Driver
Siding Controller
Auto-Reversing Controller
Block Controller
3 Color Status LED Sensor LED
StationMaster Data Port
Sensor common
Switch GREEN relay Terminals
Switch RED relay Terminals
Lamp 1 OUT
Lamp 2 OUT
Common Relay Terminals
Switch RED
Sensor
Switch GREEN
Sensor
1
2
3
4
5
6
20
19
18
17
16
15
711
812
913 14
ALTERNATE
Sensor
ALTERNATE
pushbutton
Power
IN 6-18V
TURNOUT To electric switch (out)
Apr 2019
+5 volts OUT
+6 to 20 volts OUT
Switch Red
Pushbutton (Program Laps and Node ID)
Switch GREEN
Pushbutton (Program Time Delay)
RR Concepts
The Swiss Army Knife of Model Train Electronics
External Relay Ports

2
RRConcepts.com
YardMaster- 5
Table of Contents
Sensor Descriptions ........................................................................3
StationMaster Data Cable ................................................................4
YardMaster Power In Description for Stand-alone systems .............5
Output to Electric Switches (turnouts) ..............................................6
Internal Switching Contacts ...............................................................7
Signal light connections ....................................................................8
Factory Reset ................................................................................... 9
Operating Modes..............................................................................10
Time Delay .....................................................................................11
ID number .......................................................................................12
Laps .................................................................................................13
Forced Alternate ...............................................................................14
Auxiliary Relay Module ...................................................................15
STOP / GO Relay Modue Descriptions ...........................................16
Block Control ..................................................................................17
Station Stop ....................................................................................18
Smart Turnout .................................................................................23
Alternating Paths ............................................................................24
Turn on/off an accessory ...............................................................25
Alternating Trains ...........................................................................27
Back and forth Automatic Reversing .............................................30
Reversing Loops ................................................ .............................35
Alternating between 2 loops of track ..............................................38
LED indicators ................................................................................40
Sensor Placements on Track ...........................................................41

3
1
2
3
4
5
6
20
19
18
17
16
15
711
812
913 14
Terminals 1 and 2 are the Alternate sensor.
When this sensor detects a magnet or these terminals are shorted the
on-board relay will change state and the TURNOUT will fire to the other
side. The Alternate pushbutton simulates the sensor.
At Power Up, if these terminals are shorted the current sensor will
be enabled and a force RED will occur. When a train is sensed the
YardMaster will switch GREEN and perform a time delay.
This is the “no sensor” station stop. See the No Sensor hookup for details
Terminal 7 is the switch RED sensor input.
Terminal 8 is the switch GREEN sensor input
Terminal 9 is the switch common terminal
Alternate Sensor
Alternate Pushbutton
Switch RED and Switch GREEN
Sensors
These sensors will cause the YardMaster to switch to the appropriate side. Switch GREEN
will cause the Common Relay Terminals to connect to the Switch GREEN relay Terminals, and
Switch RED will cause the Common Relay Terminals to connect to the Switch RED Terminals.
The TURNOUT will also fire in synchronization and the lamps outputs will change.
The Switch RED and Switch GREEN pushbuttons simulate the sensors.
If a time delay has been programmed the YardMaster will switch back to the previous
state after the timer has expired.
If the Switch RED sensor is CLOSED on power up, the YardMaster will perform automatic
switching (self running mode) using the programmed delay value and these sensors will be ignored.
If the Switch GREEN sensor is CLOSED on power up the internal current sensor will be enabled and
the YardMaster will ALTERNATE when a train is sensed and then “not sensed”. This will occur in a
reversing operation when the train enters the diode blocks on the ends of the main reversing line.
Sensors
Switch GREEN
Sensor
Switch RED
Sensor
Switch RED
Pushbutton
Switch GREEN
Pushbutton
RRConcepts.com
1
2
3
4
5
6
20
19
18
17
16
15
711
812
913 14
For General
Information
only. Each
hookup
diagram will
show how
to hook these
up

4
The YardMaster obtains power and signals from a data cable when attached
to a StationMaster.
The data cable can be in a single or double configuration. The double configuration
is used to connect multiple YardMaster systems to a single StationMaster.
The connecting plugs are keyed for correct orientation. The tab on the plug will be
on the top when attached correctly.
If the center wire is cut the StationMaster will only provide power to the YardMaster.
This sometimes simplifies wiring.
StationMaster Data Cable
RRConcepts.com
To StationMaster
To StationMaster
Single connection cable
Multiple connection cable for 3 track
sidings, 4 track sidings, etc.
1
2
3
4
5
6
20
19
18
17
16
15
711
812
913 14

5
The YardMaster Power input (Pins 5 and 6) supplies
power to the YardMaster controller, power for the Lamps,
and power for the TURNOUT outputs.
The YardMaster can operate at voltages from 6 thru 18 volts DC, or 6 thru 12 volts AC.
Typically power is obtained from the transformer from either the TRACK terminals or the
ACCESSORIES terminals.
In a nutshell, the minimum voltage must be about 6 volts and the maximum voltage is
about 18 volts. (AC or DC). Also the minimum voltage required depends upon what is attached
to the outputs. For example if LGB turnouts will be controlled then the input voltage must be between
12 and 18 volts. (AC or DC) for the turnouts to fire. Similarly the lamp output voltage will be
the same as the input voltage. (Except for the +5 volt LED output which is constant)
ALSO IMPORTANT: When turnouts are attached the AMPERAGE must be sufficient to power
them without a voltage drop which would reset the YadMaster. For example a LGB style turnout
motor draws about 1 AMP. Two in parallel would draw 2 AMPS so a transformer of at least 2500ma
would be required. (2.5AMPS, or about a 50VA transformer or better)
““Wall warts” can also be used to power a stand-alone YardMaster.
An example of a 6VDC “wall wart” is the following part:
(Any equivalent 6VDC wall wart can be used)
“Enercell™ 6V/300mA AC Adapter Model: 273-313 ” (Not firing turnouts)
An example of a 12VDC “wall wart” is the following part:
(Any equivalent 12VDC wall wart can be used)
“Enercell™ 12V/1500mA AC Adapter Model: 273-358” (Firing ONE turnout)
YardMaster Power In details for stand-alone systems
(Not attached to a StationMaster)
RRConcepts.com
1
2
3
4
5
6
20
19
18
17
16
15
711
812
913 14

6
To 2 wire switch motor.
Pins 15 and 16 are the output signals for 2 wire and
slow motion switch machines which inverse the voltage polarity.
These terminals provide power to directly throw switch turnouts.
Up to 4 AMPS of power is available to throw up to 4 LGB style turnouts simultaneously if wired in parallel.
A pulsed DC output of 0.6 seconds is provided to drive the turnouts.
The output voltage is pure DC and is not half wave rectified AC. This provides maximum power output to the turnout.
For slow motion switch machines the power is continuous and changes polarity. (Tortoise, Aristocraft, or
pneumatic Ea-Ze Air) Program the YardMaster for slow motion turnouts.
The output voltage level is directly proportional to the input voltage. For example, a 12VAC input will
provide approximately 16VDC turnout voltage, etc. If a short circuit condition is present on these terminals
the YardMaster will blink the BLUE LEDs when energized. After a delay the YardMaster will attempt to resume.
Connecting to Electric Switch machines (turnouts)
RRConcepts.com
1
2
3
4
5
6
20
19
18
17
16
15
711
812
913 14
To control 3 wire switch machines use the Auxiliary relay module us used as shown below. This provides
reliable switching of any voltage necessary for the turnout. Some 3-wire turnouts have excessive voltage and
current requirements which the Auxiliary relay can handle. A very quick burst of voltage is given to the switch motor
which prevents overheating and operates without the need for capacitive discharge units.
3 wire switch machines.
To Turnout voltage source required
for switch motor: AC, DC, etc.
Peco PL-11 shown
3 Wire Switch Hookup
1
2
4
5
61
2
3
4
5
6
20
19
18
17
16
15
711
812
913 14

7
Internal Switching Contacts
The YardMaster contains a DPDT relay which can control up to 8 AMPS with live voltage,
or more than 10 AMPS with no current flowing when the switch occurs.
When the “Switch GREEN” sensor or pushbutton is detected the status LED will turn
GREEN and the two Common relay terminals will connect to the “Switch green relay terminals”.
Terminal 3 will internally connect to terminal 20.
Terminal 4 will internally connect to terminal 19.
When the “Switch RED” sensor or pushbutton is detected the status LED will turn
RED and the two Switch relay Common terminals will connect to the “Switch RED relay terminals”.
Terminal 3 will internally connect to terminal 18.
Terminal 4 will internally connect to terminal 17.
The Alternate sensor or alternate pushbutton will alternate these contacts.
Since this is a simple relay there are no polarity or voltage restrictions.
(AC, DC or DCC can be switched, and up to 110V).
The CURRENT SENSOR is located on terminal 4 and will measure the current entering on that
terminal and flowing through the relay. This is only used to sense the train for “no-sensor” hookups.
If an auxiliary relay is connected to the AUX relay data port then the auxiliary relay will switch
in parallel with the internal relay. This will provide an additional 10 Amp DPDT relay for additional uses.
Switch GREEN relay Terminals
Switch RED relay Terminals
Alternate pushbutton
Switch RED
Pushbutton
Switch GREEN
Pushbutton
Common Relay Terminals
RRConcepts.com
1
2
3
4
5
6
20
19
18
17
16
15
711
812
913 14

8
If the input to the signal lamp is
12 volts use terminal 11 as the common.
This terminal provides a constant voltage
and the lamp terminals are grounded to
turn on the lamps.
Pins 12 and 13 are the Lamp output signals.
These are open circuit when OFF and
grounded when ON.
Note that the lamp output voltage is the
same as the input voltage, but converted to
DC. For example, a 12 VAC or 12 VDC input
will provide a 12VDC lamp output, etc.
Flashing the lamps
Signal lamps will enter a slow blinking state after a few minutes to give your RR a very
realistic look. The YardMaster can be heard “clicking” as the flashing feature is operating.
See the programming section for details on disabling this feature. Some
signal lamps already have built-in electronics to do the flashing so this feature can be
turned off if needed by programming a different operating mode.
If direct driving LED’s use pin 14 as the
constant +5 volt voltage source and wire
as shown for either separate LEDs or a
single dual color LED.
A 220 ohm resistor is required to provide the
current limiting and prevent them from damage.
When controlling flashing RR crossing signals use
separate red LEDs and program accordingly.
LEDs may be available free from RR Concepts.
Check the order page for availability.
Signal Lamp Connections
+ voltage
+5 VCD notch
Common Anode
Bi-color RED/GREEN
LED
Lamp1
Use this hookup for Shiloh
Signal lamps.
Lamp 2
+12V Output LED direct connect
notch
The YardMaster can control both 12 volt lamps and 5 volt LEDs synchronized with the
turnouts and relay. When programmed for crossing light control the lamps will alternately flash
when triggered.
RRConcepts.com
1
2
3
4
5
6
20
19
18
17
16
15
711
812
913 14
1
2
3
4
5
6
20
19
18
17
16
15
711
11
812
12
913
13
14
14

9
To perform a factory reset:
1. Enter Programming Mode: (Remove any jumpers if present)
Press the ALTERNATE button and either one of the Switch RED or Switch GREEN buttons
simultaneously.
The YardMaster will display BLUE when in programming mode.
2. Press and hold the ALTERNATE pushbutton The for at least 10 seconds.
YardMaster will slowly flash the blue sensor LED many times but keep holding down
the button. After a delay the blue status LED will twinkle to indicate a factory reset.
Release the button.
Factory Reset
.
A factory reset will set the following:
Turnout control for LGB style turnouts (electric switches).
Time delay OFF
Lap count: 1
Signal lamp flashing enabled
Node ID: “1”
.
RRConcepts.com
1
2
3
4
5
6
20
19
18
17
16
15
711
812
913 14
Hold this button down for 10 seconds
Blue LED will twinkle when done.

10
Programming the Operating Mode
The YardMaster can be programmed
to control different types of turnouts
(electric switches), or disable the
realistic signal light blinking feature.
All programming is stored in flash memory and retained until re-programmed.
To program the YardMaster perform the following:
1. Enter Programming Mode:
Press the ALTERNATE and either one of the Switch RED or Switch GREEN buttons simultaneously.
The YardMaster will turn BLUE when in programming mode.
2. Program the operating mode:
Press and hold down the Alternate pushbutton for the desired number of blinks.
The blink count corresponds to the following table.
To exit programming mode quickly press the Alternate button.
1 Control LGB style turnouts (electric switches)
This is the default setting after a factory reset.
2 Control SLOW_MOTION turnouts (electric switches)
These include Tortoise, Aristocraft slow motion, etc.
3 Synchronize Auxiliary relay to internal relay. (Can not use with 3 wire switch
motor control)
4 Directly control Railroad Crossing signals
Alternately flash the lamp outputs to directly control lamps or LED’s.
5 Disable signal light flashing for LGB style turnouts.
This is required if the signal lamp already has flashing circuitry.
6 Disable signal light flashing for SLOW MOTION turnouts.
Control Pneumatic turnouts by keeping the output voltage on continuously.
This is required if the signal lamp already has flashing circuitry.
7 Alternate the auxiliary relay when switching to RED
Provides control for bi-direction operations with alternating trains. See hookup.
Keep pressing the Alternate button for 10 seconds to force a Factory Reset
RRConcepts.com
1
2
3
4
5
6
20
19
18
17
16
15
711
812
913 14

11
All programming is stored in flash memory and retained until re-programmed.
1. Enter Programming Mode:
Simultaneously press the ALTERNATE and either one of the Switch RED or Switch GREEN
buttons. The YardMaster will display BLUE when in programming mode.
2. Change the time delay:
Press and hold the Switch green button and count the number of blinks, Release when
the desired time delay is programmed. The YardMaster will echo the number. EACH BLINK
will correspond to 5 seconds. 5 blinks = 25 seconds, etc.
3. Quickly press the ALTERNATE pushbutton to exit programming mode.
Notes: 1. The time delay will not be operational when attached to a StationMaster.
2. To clear the time delay either program for 1 blink or perform a factory reset.
Programming a Time Delay
Used for
Station stops,
Reversing, or
Signal Light on/off Operations
.
A time delay will cause the YardMaster to self-trigger after
the delay time. Only the GREEN sensor will perform the
time delay. When triggered the YardMaster will switch
GREEN, perform the delay, and then swich RED. The
YardMaster will blink when counting seconds before switching.
If jumpered for “self triggering” the YardMaster will continuously
self-trigger using this time delay which can be used for back and
forth operations.
RRConcepts.com
1
2
3
4
5
6
20
19
18
17
16
15
711
812
913 14
1
2
3
4
5
6
20
19
18
17
16
15
711
812
913 14

12
1
2
3
4
5
6
20
19
18
17
16
15
711
812
913 14
1. Enter Programming Mode:
Simultaneously press the ALTERNATE and either one of the Switch RED or Switch GREEN
buttons. The YardMaster will display BLUE when in programming mode.
2. Program the ID Number:
Press and hold the Switch RED button until the proper number of blinks have occurred.
The programming blinks correspond as follows:
1 blink = Normal operation using sensors. (This is the factory default)
2 blinks = Program as Yardmaster #1 (Automatically set, see below)
3 blinks = Program as YardMaster #2
4 blinks = Program as YardMaster #3
5 blinks = Program as YardMaster #4
4 IDs are possible to allow 4 YardMasters to be wired together.
3. Quickly press the ALTERNATE pushbutton
to exit programming mode.
Notes:
1. Unless programmed for an ID other than #1, the YardMaster will Self-Program to ID #1
when attached to a StationMaster. It is not necessary to program for ID #1..
Programming ID number
Only necessary when TWO or MORE
YardMasters are attached to a StationMaster.
When multiple YardMasters are wired in parallel they must be identified so
that they fire in sequence. This programming is only necessary when 2
or more YardMasters are attached to a single StationMaster. This
programming is not necessary when a single StationMaster is attached
to a single YardMaster. SEE NOTES
RRConcepts.com
1
2
3
4
5
6
20
19
18
17
16
15
711
812
913 14

13
1
2
3
4
5
6
20
19
18
17
16
15
711
812
913 14
Lap counting will not occur when attached to a StationMaster.
All programming is stored in flash memory and retained until re-programmed.
1. Enter Programming Mode:
Simultaneously press the ALTERNATE and either one of the Switch RED or Switch
GREEN buttons. The YardMaster will display BLUE when in programming mode.
2. Program the node ID:
Press and hold the Switch RED button until the proper number of blinks have occurred.
The programming blinks correspond as follows:
1 blink = Normal operation, or 1 lap.
2 blinks = 2 laps
3 blinks = 3 laps
4 blinks = 4 laps
3. Quickly press the ALTERNATE pushbutton to exit programming mode.
Notes:
1. The lap counter will not function when attached to a StationMaster.
2. When attached to a StationMaster this lap number will become the Node ID.
3. To erase the lap counter either program for 1 lap or perform a factory reset.
5. When programmed for maximum laps(6) the “Forced Alternate” feature will be turned on and lap
counting will not be done. See the Forced Alternate section for details.
Programming Laps
The YardMaster can be programmed to respond after
counting sensors.
The lap counting ONLY occurs on the GREEN channel
(terminals 8 & 9) The other channels instantly respond without
counting sensors.
RRConcepts.com
1
2
3
4
5
6
20
19
18
17
16
15
711
812
913 14

14
Programming Forced
Alternate
The YardMaster has a “Forced Alternate” feature which allows control
of Wyes, Switchbacks, etc.
When the Forced Alternate feature is turned on the Alternate sensor will
switch to the direction opposite of the most recent “Switch” sensor, regardless
of the number of times the Alternate sensor is hit.
For example, when the Switch RED sensor is hit, the Alternate sensor will
always switch to GREEN, regardless of the number of times it is hit. This allows
the turnout to be set correctly for operations where the train reverses and triggers
the Alternate sensor a second time.
How to Program Forced Alternate
1. See the previous page for Programming Laps.
2. Set the lap count to maximum (6)
3. See the hookup diagrams for actual wire-to-wire connections..
Reversing train Switchbacks
Wye
Turn Around
RRConcepts.com

15
1
2
3
4
5
6
20
19
18
17
16
15
711
812
913 14
Auxiliary Relay Module and 3 wire Turnout control
RRConcepts.com
Red wire
this end
Attach relay cable between
relay and YardMaster
Auxiliary RELAY MODULE
Red wire this
end
For reference only! Use the hookup diagram for proper usage.
The YardMaster-5 contains data ports to control external DPDT relays for enhanced operations.
When an Auxiliary relay module is attached to the external port 1 it can be configured to either
control 3 wire turnouts, or switch in synchronization with the YardMaster on-board relay.
The default operation after a factory reset will control 3 wire turnouts sometimes used on
N and HO track switch machines.
The hookup diagram is shown on page 6. Some 3-wire turnouts
have excessive voltage and current requirements which the relay can handle. A very quick burst
of voltage is given to the switch motor which prevents overheating and operates without the need
for capacitive discharge units.
When the YardMaster is programmed for “blink 3” then the Auxiliary relay will switch in
synchronizationwith the on-board YardMaster relay.
This can provide additional switching capability if needed.
When the YardMaster is programmed for “blink 7” then the Auxiliary relay will ALTERNATE
every time the YardMaster switches to RED.
This is used for reversing track polarity on an alternating trains hookup. (See alternating trains
hookup in this manual) This can not be done when using 3 wire turnouts since this relay will
control the switch motor.
When attaching the StationMaster relay cable note the location of the red wire and attach as shown.
Some cable assemblies have an arrow on the connector on this wire however this is not always true.
Use the wire color as the guide. If the relay does not operate then try swapping the connector
polarity on the relay.
See note

16
1
2
3
4
5
6
20
19
18
17
16
15
711
812
913 14
STOP / GO relay module
RRConcepts.com
Red wire
this end
Attach relay cable between
relay and YardMaster
STOP / GO RELAY MODULE Red wire
this end
For reference only! Use the hookup diagram for proper usage.
The YardMaster-5 contains data ports to control external DPDT relays for enhanced operations.
When a stop / go Relay Module is attached to external port 2 it will be automatically sensed on
power up. When sensed the YardMaster will blink ORANGE two times. This indicates that the
STOP/GO relay module has been detected and the YardMaster will operated differently.
The YardMaster will operate as follows when the relay is detected:
When an ALTERNATE sensor is triggered the relay will energize for the programmed
time delay, and then the alternate function will occur. This allows a time delay station stop.
When the FORCE RED sensor is triggered the external relay will energize for the programmed
time delay only. No other switching will occur. This allows an in-between station stop
in a reversing operation.
When the FORCE GREEN sensor is triggered the force green operation will occur as
normal and this relay will not activate.
See the hookup diagrams in this manual for exact operations and details.
When attaching the cable note the location of the red wire and attach as shown. Some cable
assemblies have an arrow on the connector on this wire however this is not always true.
Use the wire color as the guide. If the relay does not operate then try swapping the connector
polarity on the relay.

17
To
Power Pack
TRACK
Terminals
Attach to
Isolated
TRACK
Attach to
Common
TRACK
Isolator Isolator
2 Trains on 1Track - Block Control Hookup Diagram
Place MAGNET
on bottom of engines.
For two trains on one track this is all you need to do.
“Power In” can be attached to the track power to supply voltage (DC trains only) or to a fixed 6 volt “wall wart”. See
the power page for more details.
Remove any YardMaster time delays or lap counts if they have been programmed. A factory reset will do this also.
Change the direction of transformer so train runs as shown and adjust the speed as desired. It may be necessary
to experiment with the switch GREEN sensor location to obtain the desired results.
The signal light is optional but adds to the fun.
Switch Green
Sensor
Switch RED
Sensor
Green Terminal
Optional
Signal Light
Block
Control
Power in
goes to
transformer
Operation:
When a train exits the isolated block the switch RED sensor
will kill power to the block and cause the next train that enters
the block to stop.
When the train crosses over the switch GREEN sensor the
block will energize and the stopped train will run
.
For both trains to run at the same time place the switch GREEN sensor
about half way around, and closer to the switch RED sensor. For a
longer stop at the isolated block place the switch Green sensor closer
to the isolated block.
RRConcepts.com
1
2
3
4
5
6
20
19
18
17
16
15
711
812
913 14
Attach
to Signal light terminals

18
To
Power Pack
TRACK
Terminals
Attach to
TRACK
anywhere
Station Stop Hookup Diagram
Place MAGNET
on bottom of engine.
Add additional sensors in PARALLEL
for additional station stops.
For a simple station stop, this is all you need to do!
Make sure to program the YardMaster for the desired time delay.
When the power supply is turned on the train should run. If it does not then press the
Alternate button. This is a one-time operation since the YardMaster will remember the
switch state in memory.
Change the direction of the train as required. The YardMaster will operate in both directions.
Adding a signal light is optional, but adds to the fun. Attach to signal light terminals.
Switch GREEN
Sensor
8 & 9
RED Relay
Terminals 17 & 18
Station
Stop using sensors
Common
Relay
Terminals
3 & 4
Programming:
* Set time delay as
desired.
* Set lap count as
desired.
YardMaster Power
DC trains only.
See power page
for AC trains using
wall wart.
RRConcepts.com
1
2
3
4
5
6
20
19
18
17
16
15
711
812
913 14

19
To
Power Pack
TRACK
Terminals
Attach to
TRACK
anywhere
on loop
Station Stop Hookup Diagram
Place MAGNET
on bottom of engine.
Add additional sensors in PARALLEL
for additional station stops.
For a simple station stop, this is all you need to do!
Make sure to program the YardMaster for the desired time delay.
When the power supply is turned on the train should run. If it does not then press the
Alternate button. This is a one-time operation since the YardMaster will remember the
switch state in memory.
Change direction of the train as required. The YardMaster will operate in both directions.
Terminals 3 & 4 connect to the AC transformer, polarity is not important.
Terminals 5 & 6 connect a “wall wart” DC voltage source. The voltage must be between 6 and
12 volts. Polarity is not important.
Terminals 17 & 18 connect to the track, polarity is not important.
Switch GREEN
Sensor
RED Terminals
AC trains,
Station
Stop using sensors
Programming:
* Set time delay as
desired.
* Set lap count as
desired.
RRConcepts.com
1
2
3
4
5
6
20
19
18
17
16
15
711
812
913 14

20
To
Power Pack
TRACK
Terminals
Attach to
TRACK
Station Stop Hookup Diagram
with no train modifications
(Full Featured YardMaster only)
For a simple station stop, this is all you need to do!
Make sure to program the YardMaster for the desired time delay before adding the jumper.
When the power supply is turned on the YardMaster will switch to RED and the
train should run. When a train enters the isolated section it will be sensed and the
YardMaster will switch to GREEN. The train will stop. After the programmed
time delay the YardMaster will switch to RED and the train will run again.
Change direction of the train as required. The YardMaster will operate in both directions.
Adding a signal light is optional, but adds to the fun.
Station
Stop NO SENSORS
Programming:
* Set time delay as
desired.
* Set lap count as
desired.
RRConcepts.com
1
2
3
4
5
6
20
19
18
17
16
15
711
812
913 14
YardMaster
Power In
Jumper Wire between 1 & 2
Attach to transformer accessories or any 12 to 18 volt
AC or DC power source.
Isolators
on inside rail
Parts List
YardMaster 1
Track Isolators 2
wire as required
Terminal
17
Outside
rail
Inside rail
Table of contents
Other RR-Concepts Controllers manuals
Popular Controllers manuals by other brands
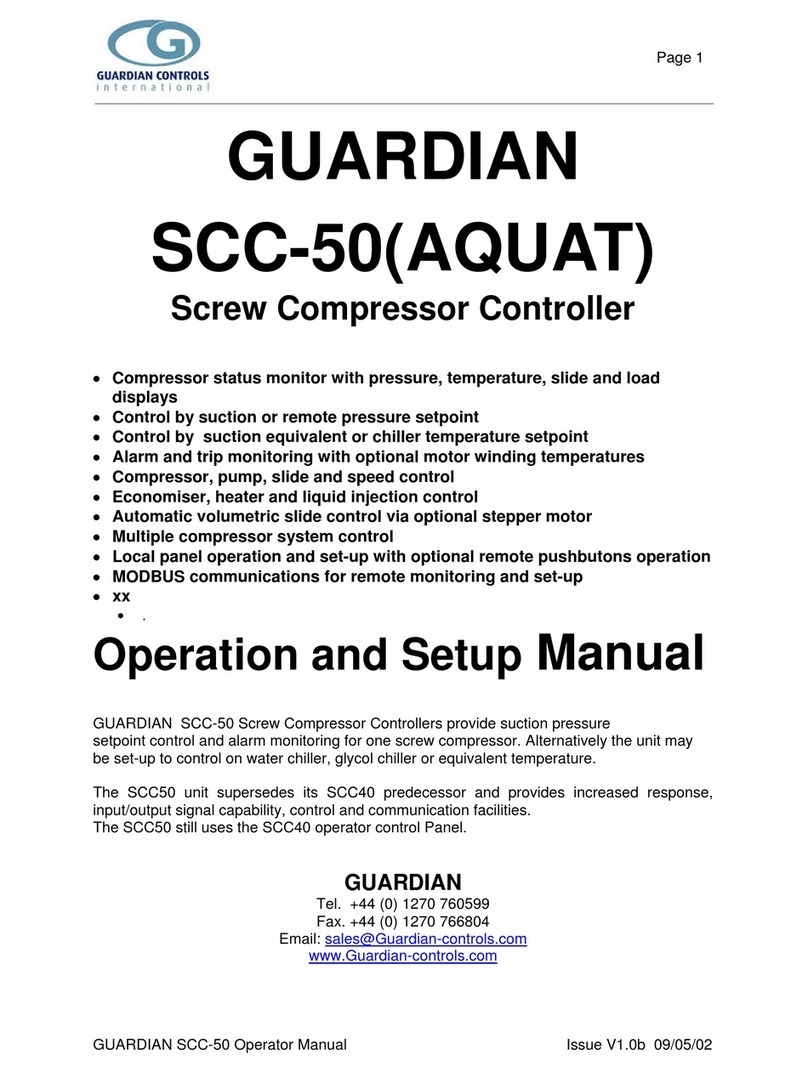
Guardian
Guardian SCC-50 OPERATION AND SETUP MANUAL
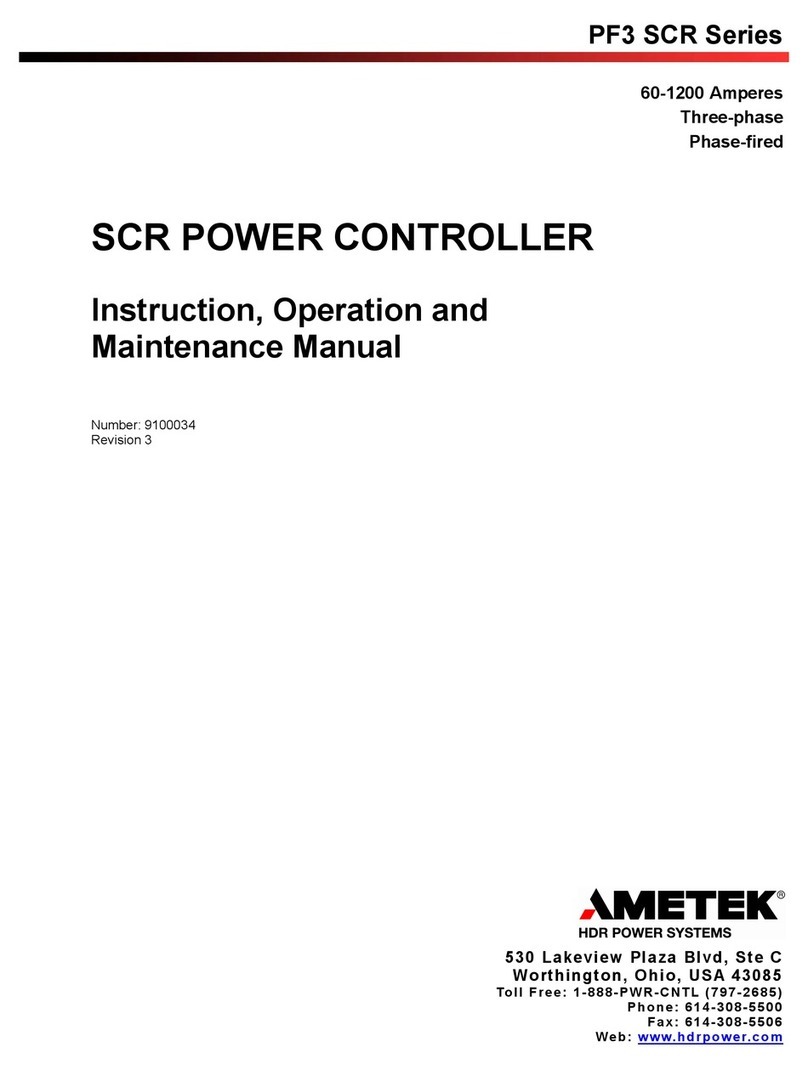
Ametek
Ametek PF3 SCR Series Instruction, Operation and Maintenance Manual
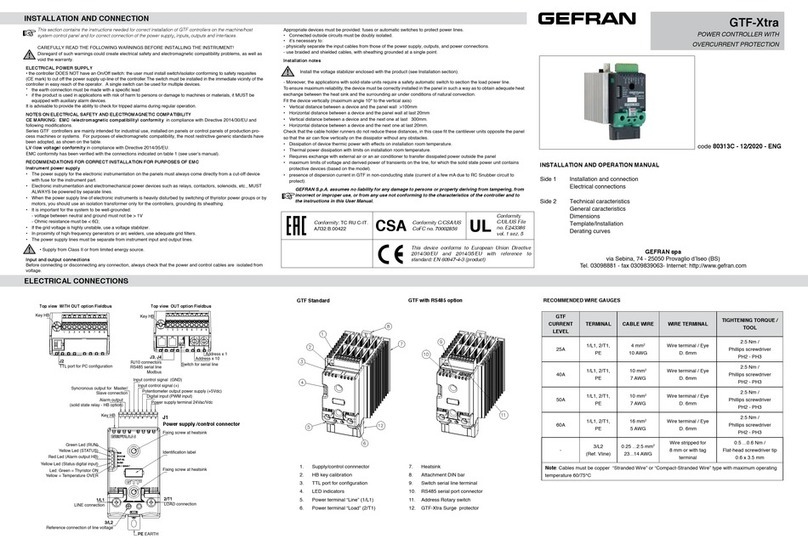
gefran
gefran GTF-Xtra installation and connection
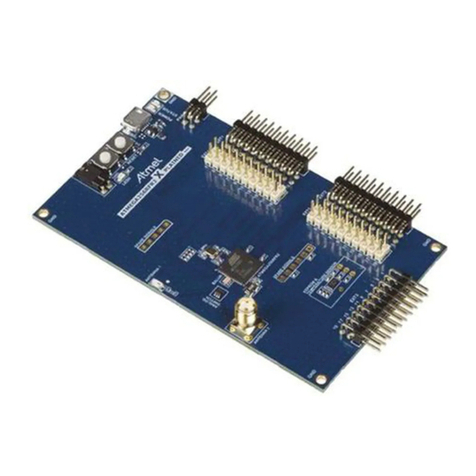
Atmel
Atmel ATMEGA256RFR2 Xplained Pro manual
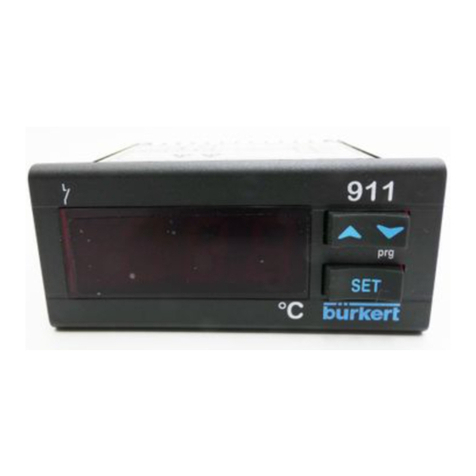
Burkert
Burkert 0911 operating instructions
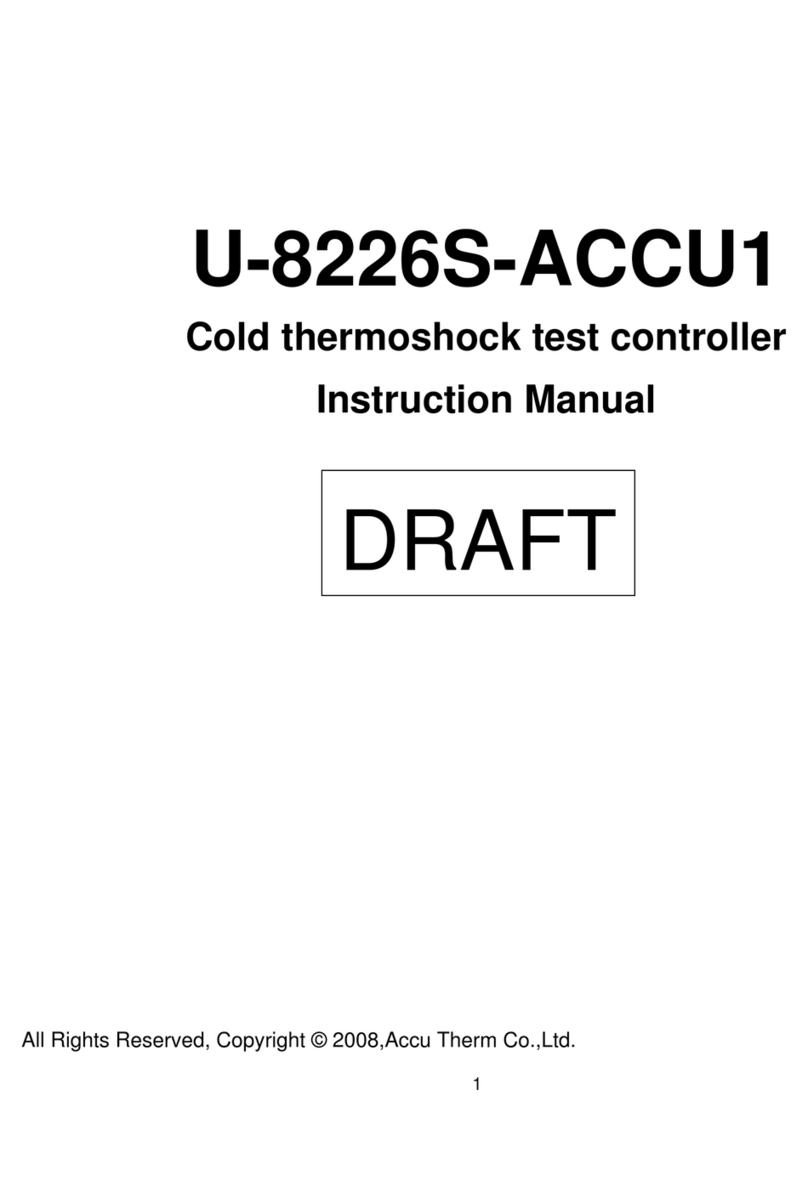
AccuTherm
AccuTherm U-8226S-ACCU1 instruction manual