RTK MV 5051 Series User manual

Einbau- und Betriebsanleitung
Installation and operating instructions
Instructions de montage et de service
Dampfumformventile
Steam converting valves
Vanne de transformation de vapeur
5702-8010
Baureihe / Series / Séries
MV 5051 / PV 6051
08/2017
1
Inhaltsverzeichnis
Seite
1 Allgemeine Informationen 2
2 Montage und Anschluss 2
3 Inbetriebnahme 4
4 Wartung 5
Content
page
1 General Information 7
2 Installation and connection 7
3 Commissioning 8
4 Maintenance 10
Index
page
1 Informations générales 11
2 Installations et connexions 11
3 Mise en service 12
4 Maintenance 13
Anhang / Appendix / Annexe
1 Drehmoment für Schrauben / torque for nuts / page
Couple de serrage 15
2 Ersatzteilliste / spare parts list / liste des
pièces de rechange MV 52 / PV 62; MV 53 / PV 63 18
3 Ersatzteilliste / spare parts list /
liste des pièces de rechange MV 54 / PV 64 20
4 CE Konformitäterklärung / CE declaration of confirmity /
déclaration de conformité 23
Gültigkeitsbereich der Einbau- und Betriebsanleitung /
Use this Installation and Operation Instruction for /
Utiliser ce manuel d‘instructions de montage et d‘utilisation pour
MV 5351, MV 5451, MV5951
PV 6351, PV 6451, PV 6951

Einbau- und Betriebsanleitung
Installation and Operating instructions
Instructions de montage et de service
5702-8010
2
08/2017
1Allgemeine Informationen
Dampfumformventile dienen zur Regelung des Dampfdruckes (Reduzierung) und dessen Temperatur (Dampfkühlung).
Die Dampfkühlung geschieht, ähnlich dem Dampfzerstäuberprinzip, durch Einspritzung des Kühlmediums über ein Düsenrohr
von unten in den Ventilsitz. Auf diese Weise wird das Kühlmedium optimal und fein zerstäubt. Die Verdampfung des
Kühlmediums ist meist innerhalb von 0,1 .. 0,2 s abgeschlossen.
Die Auswahl der Dampfumformventile erfolgt nach den Betriebsbedingungen und der vorgesehenen Regelaufgabe.
Die Ventile unterscheiden sich durch Anschlussmaße, Nenndruckstufe sowie Gehäusewerkstoff, Dichtungswerkstoff und
Flanschausführung.
Achtung! : Dampfumformventile dürfen nur für die vorgesehenen Einsatzbedingungen eingesetzt werden.
Der Werkstoff und die Nenndruckstufe können am Gehäuse des Stellventiles abgelesen werden. Diese müssen für die maximal
zulässigen Betriebsbedingungen (Druck und Temperatur) geeignet sein.
Jedes Ventil hat eine eindeutige Seriennummer, die auf dem Typenschild unter "W. Nr." angegeben ist. Bei der Bestellung von
Ersatzteilen oder bei Rückfragen sollte die "W. Nr." immer angegeben werden. Siehe Anhang, Bild 1.
Die Dampfumformventile werden im Herstellerwerk verschiedenen Prüfungen (Druckprüfungen, Dichtheit nach außen,...) und
Funktionsproben unterzogen.
Eine Einstellung der Dampfumformventile ist daher nicht notwendig.
Achtung! : Bevor Sie mit dem Einbau oder Betrieb von Ventilen beginnen, lesen Sie bitte die Druckschrift "Warnung vor
Gefahren...". 0000-7004
Einbau und Inbetriebnahme sind nur dem hierfür ausgebildeten und qualifizierten Fachpersonal
gestattet.
2Montage und Anschluss
2.1 Einbau Dampfumformventil
Beim Einbau des Dampfumformventils muss folgendes beachtet werden:
Einbauraum:
Die Einbaustelle sollte gut zugänglich sein. Es muss genügend Raum zur Wartung und zum Öffnen der Antriebshaube
vorhanden sein. Werden Dampfumformventile im Freien montiert, so sollten Sie durch ein Regendach gegen Witterung und
direkte Sonnenbestrahlung geschützt werden. Der Kühlwasseranschluss sowie zuführende Rohrleitungen sind durch
geeignete Maßnahmen gegen mögliche Frosteinwirkung zu schützen.
vor dem Einbau:
Die Schutzkappen sind von den Flanschöffnungen zu entfernen.
Reinigung der Rohrleitungen:
Um einen dichten Abschluss des Dampfumformventils zu gewährleisten, sind die Rohrleitungen vor dem Einbau
entsprechend zu reinigen / auszublasen. Dies verhindert, dass Schmutzteile wie Rost, Zunder oder Schweißperlen den Sitz
bzw. Kegel des Dampfumformventils beschädigen.
Zum Schutz vor Verunreinigungen während des normalen Betriebes muss mittels geeigneter Maßnahmen für sauberen
Dampf gesorgt werden.
Anströmungsrichtung:
Gemäß Richtungspfeil auf dem Ventilgehäuse
Einbaulage:
Vorzugsweise in waagerechte Rohrleitung mit stehendem Antrieb.
Spannung auf Ventilkörper:
Mögliche Zug- und Druckkräfte auf den Ventilkörper müssen durch geeignete Maßnahmen verhindert werden.
Rohrleitungsführung:
Für eine einwandfreie Funktion des Dampfumformventils sollte eine Einlaufstrecke vor dem Ventil von > 5x DN gerade,
unverzweigt und ungestört vorgesehen werden.

Einbau- und Betriebsanleitung
Installation and Operating instructions
Instructions de montage et de service
5702-8010
3
08/2017
Hinter dem Ventil soll die Verdampfungsstrecke / Auslaufstrecke auf mindestens 4,5 –6 m gerade, unverzweigt und
ungestört ausgeführt werden.
Der bei überkritischer Entspannung dem Ventil i.d.R. nachgeschaltete Silencer, ist Teil der Verdampfungsstrecke.
Für eine ausreichende Entwässerung der Rohrleitung vor und nach dem Dampfumformventil ist zu sorgen.
Bei Verwendung des Dampfumformventils als Turbinenumleitstation und zur Vermeidung von unnötigem Temperaturstress,
empfiehlt es sich das Ventil und die Rohrleitungen vor und nach dem Ventil durch geeignete Maßnahmen entsprechend
warmzuhalten.
Der Kühlwasseranschluss soll so ausgeführt werden, dass keinerlei Kräfte auf den Düsenrohranschluss einwirken können
bzw. bauseits ein entsprechend flexibles Verbindungsstück zwischen Rohrleitung und Düsenrohranschluss vorsehen.
Schutz vor Wärmestrahlung:
Um den Stellantrieb vor zu hoher Wärme zu schützen sind die Rohrleitungen zu isolieren. Dies muss vor der ersten
Inbetriebnahme (ggf. auch provisorisch) erfolgen.
Schutz vor Schallemission
Verwendung / Nachschaltung eines Silencers nach Herstellerangabe
Verwendung einer kombinierten Wärme-Schallschutzisolierung im Bereich des Dampfumformventiles und der
Verdampfungsstrecke bei Bedarf
Vermeidung von Körperschallübertragung der Rohrleitung auf Konstruktion und Gebäude mittels geeigneter Maßnahmen
2.2 Montage Stellantrieb
Der Stellantrieb ist normalerweise auf das Ventil montiert und eingestellt. Beim Austausch, Umbau oder Drehen des
Stellantriebes ist gemäß der Bedienungsanleitung des Stellantriebes zu verfahren.
2.3 Elektrischer Anschluss
Der elektrische Anschluss erfolgt nach der Bedienungsanleitung des Stellantriebes.
Achtung! : Sicherheitsvorschriften beim elektrischen Anschluss beachten.
Vor dem Anschluss Kontrolle der Stromart, Netzspannung und Frequenz mit den Daten auf dem Typenschild
vergleichen.
2.4 Pneumatischer Anschluss
Der Anschluss erfolgt nach der Bedienungsanleitung des Stellantriebes.
Für jeden pneumatischen Antrieb sollte ein Druckminderer vorgesehen werden, um für einen stabilen Zuluftdruck zu sorgen.
Achtung: Nur saubere, trockene und ölfreie Instrumentenluft nach ISO 8573-1 verwenden!
(nicht geölt, Drucktaupunkt 20 K unter niedrigster Umgebungstemperatur, Feststoffgehalt < 30 µm)
2.5 Anordnung der Sensoren und Begrenzer für Druck und Temperatur
Druckmessung (z.B. DR1226) ca. 2 .. 2,5 m nach dem Dampfumformventil bzw. ca. 0,5 m .. 1 m nach Silencer positionieren.
Einbau DR1226 gemäß Datenblatt 1226-7010
Temperaturfühler Pt100 möglichst in schnellansprechender Ausführung verwenden. (siehe Datenblatt 1100-7010 z.B. WT1102)
Positionierung des Temperaturfühlers Pt100 in der Rohrleitung erst nach Abschluss des Verdampfungsvorganges, also frühestens im
Abstand von ca. 7 m, besser 8 .. 12 m, nach dem Dampfumformventil.
Bei problematischer Temperaturmessung vier Stück Pt100 zu einem Pt100 elektrisch verschalten (je 2 Stück in Reihe und beide Paare
parallel schalten) und diese je im Abstand von ca. 1 m zueinander versetzt, auf dem Umfang der Rohrleitung verteilt, positionieren.
STB und SDB jeweils in unmittelbarer Nähe des Temperaturfühlers bzw. Druckmessumformers in der Rohrleitung positionieren.

Einbau- und Betriebsanleitung
Installation and Operating instructions
Instructions de montage et de service
5702-8010
4
08/2017
3Inbetriebnahme
Die Inbetriebnahme darf erst erfolgen, wenn die Punkte unter Kapitel „ 2 Montage und Anschluss“ abgearbeitet ist.
Die Dampfumformventile sind werksseitig eingestellt und einer Funktionsprüfung unterzogen. Eine Einstellung der Stellantriebe
ist daher nicht notwendig.
3.1 Kaltinbetriebnahme
3.1.1. Dampfumformventil mit elektrischem Stellantrieb
Kontrolle der Wirkungsrichtung des Stellantriebes in Bezug auf die Regelgröße (z.B. ansteigender Druck bewirkt
Schließen des Ventils) im Zusammenwirken mit dem Prozessregler / Leittechnik
Kontrolle der Funktion der elektronischen Rückmeldung (sofern vorhanden) Stellantrieb im Zusammenwirken mit dem
Prozessregler / Leittechnik
Kontrolle der Funktion und Schaltpunkt des zusätzlichen Wegschalters ZU zur Verriegelung des Einspritzventiles (ca.
1,5 mm vor ZU Position Dampfumformventil)
Kontrolle der elektrischen Schaltung von Sicherheitstemperatur- und Druckbegrenzer sowie „Notaus“ (sofern
vorhanden) im Zusammenwirken mit dem Dampfumformventil zur Prüfung der sicherheitsgerichteten Funktion des
Dampfumformventils (sofern vorgesehen)
3.1.2. Dampfumformventil mit pneumatischem Stellantrieb
Druckluftversorgung auf den vorgegebenen Arbeitsdruck (siehe Antriebsbeschreibung) am Filterdruckminderer
einstellen und Ablass-Schraube kurz öffnen (Ausblasen von möglichen Verunreinigungen in der Zuluftleitung)
Kontrolle der elektrischen Schaltung von Sicherheitstemperatur- und Druckbegrenzer sowie „Notaus“ (sofern
vorhanden) im Zusammenwirken mit dem Dampfumformventil zur Prüfung der sicherheitsgerichteten Funktion des
Dampfumformventils (sofern vorgesehen)
Kontrolle der elektrischen Schaltung von „Schnell AUF“ im Zusammenwirken mit dem Dampfumformventil zur Prüfung
der Funktion des Dampfumformventils (sofern vorgesehen / bei Turbinenumleitstation)
Initialisierung des Stellungsreglers (nach Vorschrift des jeweiligen Herstellers)
Schließen des Ventils) im Zusammenwirken mit dem Prozessregler / Leittechnik
Kontrolle der Wirkungsrichtung des Stellantriebes in Bezug auf die Regelgröße (z.B. ansteigender Druck bewirkt
Kontrolle der Funktion der elektronischen Rückmeldung (sofern vorhanden) Stellantrieb im Zusammenwirken mit dem
Prozessregler / Leittechnik
Kontrolle der Funktion und Schaltpunkt des zusätzlichen Wegschalters ZU zur Verriegelung des Einspritzventiles (ca.
1,5 mm vor ZU Position Dampfumformventil)
Das Kühlwassereinspritzventil ist in gleicher Vorgehensweise wie vor beschrieben in Betrieb zu setzen.
Die Schaltpunkte der Sicherheitsbegrenzer (STB und SDB) sind nach Vorgabe des Anlagenplaners einzustellen.
3.2 Warminbetriebnahme
Temperaturregelung gewünschten Sollwert der Dampftemperatur einstellen und einschalten
Druckregelung gewünschten Sollwert des Dampfdruckes einstellen
Entwässerungen vor und nach Station betriebsbereit machen
Warmhaltung (sofern vorhanden) öffnen und Rohrleitung damit langsam Vorwärmen
Dampfumformventil in (sehr) kleinen Schritten über einen Zeitraum per Handsteuerung (sehr) langsam auffahren und die
Rohrleitungen / Dampfumformventil vorsichtig auf Temperatur und Druck bringen. Dabei beobachten ob Temperaturregelung ab
eingestellter Solltemperatur arbeitet. Druck weiter bis nahe des gewünschten Sollwertdruckes erhöhen.
Druckregelung einschalten
Spindelabdichtungen der Kegelspindel und Einspritzdüsenrohr Presspackung aus Reingrafit bei Bedarf nachziehen.
Alle anderen Spindelabdichtungen sind durch ein vorgespanntes Federpaket wartungsfrei.
Achtung!: Ein zu festes Anziehen der Reingrafitpackung führt zu hohen Reibkräften, welche die Funktionsweise des
Regelventils beeinträchtigen.
Solange die Armatur unter Druck- und Temperatur steht dürfen die Deckelschrauben nicht gelöst oder nachgezogen
werden.

Einbau- und Betriebsanleitung
Installation and Operating instructions
Instructions de montage et de service
5702-8010
5
08/2017
Auslegung des Dampfumformventils überprüfen
Das Regelventil sollte im normalen Betriebszustand bei ca. 70 bis 100 % des Hubes arbeiten.
Max. Durchfluß wird nicht erreicht: Überprüfung, ob das Ventil 100 % offen ist
Überprüfung ob alle Handabsperrventile offen und die Schmutzfänger sauber sind.
Überprüfung der Auslegungsdaten mit den tatsächlichen Betriebsdaten.
Ventil arbeitet bei kleinem Hub: Um einen vorzeigen Verschleiß der Regelarmatur zu vermeiden sollte das Ventil
auf die tatsächlichen Betriebsdaten angepaßt werden.
Maßnahmen mit dem Herstellerwerk abstimmen.
Dampftemperatur ist zu hoch: Überprüfen, ob Kühlwasserdruck in vorgesehener Höhe und Menge ansteht und alle
Handabsperrventile offen und die Schmutzfänger sauber sind.
Temperaturmessung prüfen.
Maßnahmen mit dem Herstellerwerk abstimmen
Dampftemperatur instabil: Anordnung Temperaturmessung zu nah am Dampfumformventil –Verdampfung des
Kühlwassers noch nicht abgeschlossen
Zu kurze Verdampfungsstrecke
Ungünstige Messstelle ggf. anderen Messpunkt auswählen (siehe auch Kapitel 2.5.)
Maßnahmen mit dem Herstellerwerk abstimmen
.
Überprüfung der Regelung
Die Regelung muss unbedingt auf Stabilität überprüft werden. Das Regelventil sollte nach erreichen des Sollwertes im
Idealfall stehen bleiben. Eine instabile Regelung (ständig Schritt vor und zurück) führt zu einem vorzeitigen Verschleiß.
Bitte nehmen Sie in diesem Fall Kontakt mit dem Herstellerwerk auf.
Beim Betrieb von elektrischen Stellantrieben sollte bei Richtungsänderung zwischen den Stellschritten eine Pause von
mindestens 200 ms eingehalten werden. Die minimale Schrittdauer sollte 60 ms nicht unterschreiten, bei maximal
1200 Schaltungen pro Stunde.
Um einen vorzeitigen Verschleiß des Stellventils zu vermeiden, müssen Pendelungen im Schließbereich vermieden werden.
4Wartung
4.1 Spindelabdichtung
Generell müssen beschädigte Spindelabdichtungen sofort ausgewechselt oder nachgezogen werden (bei Reingrafitpackungen),
da sonst eine neue Packung innerhalb kurzer Zeit wieder undicht werden kann.
Der Aufbau der Spindelabdichtungen ist im jeweiligen technischen Datenblatt beschrieben. Spindelabdichtungen sind als
Ersatzteilset beim Hersteller zu beziehen. Bitte geben Sie bei der Bestellung immer die "W. Nr." des Ventils an. Diese steht auf
dem Typenschild, das auf der Querträgerplatte des Ventildeckels angebracht ist.
4.2 Austausch der Stopfbuchspackung
Ventil drucklos machen und Rohrleitungen entleeren gemäß Vorschriften
Zum Tausch der Spindelabdichtung muß der Stellantrieb abgebaut werden. Der Auf- und Abbau
des Stellantriebes ist in der Betriebsanleitung des jeweiligen Stellantriebes beschrieben.
Die Überwurfmutter lösen und abnehmen.
Alte Packung entfernen (Packungszieher) und Packungsraum säubern.
Ventilspindel säubern
Neue Packung, Stopfbuchse und Feder gemäß beigefügtem Schnittbild einlegen.
Überwurfmutter befestigen

Einbau- und Betriebsanleitung
Installation and Operating instructions
Instructions de montage et de service
5702-8010
6
08/2017
Achtung!: Ein zu festes Anziehen der Reingrafitpackung führt zu hohen Reibkräften, welche die Funktionsweise des
Regelventils beeinträchtigen.
4.3 Austausch der Kegelgruppe
Es empfiehlt sich beim Tausch der Kegelgruppe auch die Spindelabdichtung zu erneuern. Für den Tausch der Kegelgruppe ist
die Flachdichtung (503) zwischen Gehäuse und Deckel notwendig.
Ventil drucklos machen und Rohrleitungen entleeren gemäß Vorschriften.
Zum Tausch der Kegelgruppe muß der Stellantrieb abgebaut werden (siehe hierzu die Betriebsanleitung des jeweiligen
Stellantriebes).
Deckel (201) vom Gehäuse (101) lösen
Kegelgruppe aus Deckel (201) herausziehen und austauschen.
Dichtflächen am Gehäuse reinigen
Deckel (201) mit Kegelgruppe (300) auf Gehäuse (101) aufsetzen und kreuzweise festschrauben (Anzugsmomente siehe
Tabelle im Anhang)
Stellantrieb gemäß Betriebsanleitung auf Ventil aufbauen und Endabschaltung überprüfen.
4.4 Austausch des Düsenrohres
Beim Tausch des Düsenrohres ist die Stopfbuchsabdichtung mit zu erneuern.
Ventil drucklos machen und Rohrleitungen entleeren gemäß Vorschriften.
Alte Stopfbuchse (Packungszieher) entfernen und Düsenrohr aus Deckel herausziehen.
Packungsraum säubern
Neues Düsenrohr einsetzen
Neue Packung in Stopfbuchse gemäß beigefügtem Schnittbild einlegen.
Überwurfmutter befestigen

Einbau- und Betriebsanleitung
Installation and Operating instructions
Instructions de montage et de service
5702-8010
7
08/2017
1General Information
Steam converting valves are used to regulate the steam pressure (reduction) and the temperature (steam cooling). Steam
cooling occurs similar to the steam atomizer principle. A cooling agent is injected from below into the valve seat over a nozzle
pipe. The cooling agent is optimally and finely dispersed. The cooling medium has usually evaporated within 0.1-0.2 seconds.
The selection of the steam-converting valve depends on the working conditions and the intended standard task. They differ in
connecting dimensions, nominal pressure level, as well as housing and seal material and the flange design.
Attention! Steam converting valves should only be used for the designated working conditions.
The housing material and nominal pressure level are stated on the housing of the control valve. These data must be suited to the
maximum permissible working conditions (pressure and temperature).
Every valve has a unique serial number, which is written on the identification plate of the valve as "W. Nr.". When ordering spare
parts, always state the serial number of the valve. See Appendix Figure 1.
The steam converting valves are subjected to several tests (pressure testing, leakage testing,...) including performance checks in
the manufacturing plant. That means that the valve does not need to be adjusted.
Attention! Before installing or commissioning valves, please read the pamphlet 0000-7004 "Hazard warning...“
Only trained and qualified specialist staff may install and commission valves.
2Installation and connection
2.1 Installation steam converting valve
Observe the following when installing the steam-converting valve:
Clearance
The installation position should be easily accessible. There must be adequate space for maintenance work to be performed
and to open the actuator hood. Steam converting valves installed outdoors should have suitable weather protection such as
a sun and rain hood. The cooling water connection and feed piping must be protected suitably against possible freezing.
Before installing:
Remove protective caps from the flange openings.
Cleaning the piping:
To ensure a tight connection of the steam converting valve, the piping must be rinsed / blown through thoroughly before installing the
valve. This prevents dirt particles such as rust, scale or welding beads from damaging the seat or the cone of the steam-converting
valve. Appropriate measures must be taken in order to ensure that clean steam is fed into the system and protect the system from
soiling during normal working conditions.
Direction of inflow:
The flow direction must correspond to the arrow on the valve housing.
Installation position:
The valve should be preferably installed in horizontal piping with upright actuator.
Tension on valve body:
Precautions must be taken to prevent any tensile and pressure forces on the valve.
Pipework routing:
For smooth operation of the steam-converting valve, the feed-in distance to the valve should be > 5x DN, straight, unbranched and not
interrupted. Downstream from valve, the evaporation / discharge distance should be > 10x DN straight, unbranched and not
interrupted.
The silencer that is usually installed downstream from the valve for over-critical decompression is part of the evaporation zone.
Appropriate drainage of the piping both up and downstream from the steam-converting valve must be ensured. We recommend
keeping the valve and the piping warm with appropriate means both up and downstream from the valve when the steam-converting
valve is being used as a turbine bypass station and to avoid unnecessary temperature stress.

Einbau- und Betriebsanleitung
Installation and Operating instructions
Instructions de montage et de service
5702-8010
8
08/2017
The cooling water connection should be fitted so that no forces act on the nozzle pipe connection i.e. with a flexible connecting part
between piping and nozzle pipe connection.
Protection against heat radiation:
The piping should be insulated to protect the actuator against excessively high temperatures. This must be performed
before the initial commissioning (provisionally).
Protection against noise emissions:
Use / downstream installation of silencer according to manufacturer specifications
Use combined heat-noise protective insulation around the steam converting valve and the evaporating zone as required
Implement suitable measures to prevent mechanical vibrations being transferred from the piping to the system construction
and the building.
2.2 Assembly actuator
Actuators are normally delivered mounted and calibrated on the valve. For replacing, reworking or turning the actuator please
refer to installation and operating instructions of actuators.
2.3 Electrical connection
Electrical connection is performed according to operating and installation instructions of the actuator.
Attention! Observe safety regulations when connecting device to power supply
Compare type of current, voltage and frequency with data on identification plate of actuator before connecting it
to the power supply.
2.4 Pneumatic connection
Connect according to operating instructions of actuator.
Provide every valve with a separate pressure regulator to ensure constant incoming air pressure.
Attention! Only use clean, dry and oil-free instrument air according to ISO 8573-1!
(Not lubricated, pressure dew point 20 K below lowest ambient temperature, solids content < 30µm)
2.5 Configuration of sensors and limiters for pressure and temperature
Position pressure measurement (e.g. DR1226) 2-2.5 downstream from steam converting valve or approx. 0.5 –1m downstream from
silencer. Installation DR1226 according to data sheets 1226-7010
Temperature sensor Pt100 preferably fast-acting version. (See data sheet 1100-7010 e.g. WT1102)
Position temperature sensor Pt100 in the piping only after the evaporation process has been completed, i.e. at the earliest 7 m downstream
from the steam converting valve, better still 8-12 m.
For problematic temperature measurements connect four Pt100 to create one Pt100 (two each in series and both pairs parallel) and install
these staggered at 1-metre intervals and distributed on the circumference of the pipeline.
Position one each STB and SDB close to the temperature sensor or pressure transducer in the piping.
3Commissioning
Commissioning may only take place once the points in Chapter "2 Installation and connection” have been completed.
The steam converting valves are already adjusted and a function testing performed by the manufacturer. An adjustment of the
actuators is therefore not necessary.
3.1 Cold commissioning
3.1.1 Steam converting valve with electric actuator
Check the direction of action of the actuator regarding the control variable (e.g. increase in pressure effects closing of valve) in
interaction with process controller / control technology
Check function of the actuator's electronic feedback (where applicable) in interaction with process controller / control technology
Check function of additional limit switch OFF to lock the injection valve (ca. 1.5mm before OFF position steam converting valve)

Einbau- und Betriebsanleitung
Installation and Operating instructions
Instructions de montage et de service
5702-8010
9
08/2017
Check electric switching of safety temperature and pressure limiter as well as "Emergency OFF" (where applicable) in interaction
with the steam converting valve to check the safety relevant functioning of the steam converting valve (where applicable)
3.1.2 Steam converting valve with pneumatic actuator
Set compressed air supply at the filter pressure reducer to the given working pressure (see actuator instructions) and open
drainage screw shortly (blow-out of potential dirt in the supply air line)
Check electric switching of safety temperature and pressure limiter as well as "Emergency OFF" (where applicable) in interaction
with the steam converting valve to check the safety relevant functioning of the steam converting valve (where applicable)
Check electric switching of "Quick OPEN" in interaction with steam converting valve to check the function of the steam converting
valve (where applicable / turbine by pass station)
Initialise positioner (according to manufacturer instructions)
Check the direction of action of the actuator regarding the control variable (e.g. increase in pressure effects closing of valve) in
interaction with process controller / control technology
Check function of the actuator's electronic feedback (where applicable) in interaction with process controller / control technology
Check function and switch point of additional limit switch OFF to lock the injection valve (approx. 1.5mm before OFF position of
steam converting valve)
The cooling water injection valve is to be commissioned as described above.
The switch points of the safety limiters (STB and SDB) are to be adjusted according to the specification of the system designer
3.2 Warm commissioning
Set temperature controller to desired target value of steam temperature and switch on
Set pressure controller to desired target value of steam temperature
Drainage up and downstream ready and operational
Open pre-heater (where applicable) and pre-heat piping
Start up steam converting valve in very small steps using manual controls i.e. very slowly and bring both pipework and
steam converting valve carefully up to temperature and pressure. Check whether temperature controller works as of
set target temperature. Increase pressure until close to desired target pressure value.
Switch on pressure controller
Tighten spindle seals of cone spindle and injection nozzle pipe (pure graphite press assembly) as required.
All other spindle seals are maintenance-free thanks to a pre-loaded spring assembly.
Attention! Tightening the pure graphite assembly too much may cause high friction, which can impair the functioning
of the control valve.
Check dimensioning of steam converting valve
The control valve should work at about 70 to 100% of the stroke under normal operating conditions.
Maximum flow rate is not achieved: Check whether the valve is 100% open
Check that all manual shut off valves are open and the dirt traps are clean
Compare the dimensioning data with the actual operating data.
Valve is working with small stroke: The valve should be adjusted to the actual operating data to avoid premature wear
of the control fitting.
Coordinate measures with manufacturer.
Steam temperature is too high: Check whether cooling water pressure is available in designated amount and
pressure and that all manual shut off valves are open and the dirt traps are clean.
Check temperature measurement.
Coordinate measures with manufacturer.
Checking control system
The stability of the control system must be checked. The control valve should ideally remain in position when the target
value has been reached. Instable control systems (constantly moving back and forth one step) cause premature wear. In
this case please contact the manufacturer.

Einbau- und Betriebsanleitung
Installation and Operating instructions
Instructions de montage et de service
5702-8010
10
08/2017
When operating electric actuators, the interval between changing the direction of the actuator should be at least 200 ms.
The minimum tracking time in one direction should not be lower than 60 ms. and a maximum of 1200 switches per hour.
In order to prevent premature wear of the control valve, oscillations in the closing range must be avoided.
4Maintenance
4.1 Spindle packing
Generally spindle packings have to be changed or tightened immediately (for pure graphite assemblies), new packings can
otherwise leak again after a short period.
The design of the spindle packing is described in the technical data sheets. Spindle packings are available as spare parts set
from the manufacturer. When ordering spindle packing always state the valve serial number ("W. Nr."). This is on the
identification label that is attached to the cross carrier plate.
4.2 Changing stuffing box packing
Release pressure from valve and discharge piping according to regulations
The actuator must be removed to exchange the spindle packing. Assembly and disassembly of the actuator are described
in the operating instructions of the respective actuator.
Loosen and remove cap nut
Remove old packing set and clean packing compartment
Clean valve spindle
Insert new packing set according to cross-section drawing
Tighten cap nut
Attention!: Tightening the pure graphite assembly too much may cause high friction, which can impair the functioning of the
control valve.
4.3 Changing cone assembly
We recommend renewing the spindle packing at the same time as replacing the cone assembly. The flat gasket (503) between
housing and lid is required when replacing the cone assembly necessary.
Release pressure from valve and discharge piping according to regulations
The actuator must be removed to exchange the cone assembly (please refer to the operating instructions of the respective
actuator).
Release cover (201) from housing (101)
remove cone assembly from housing (101) and replace
Clean housing seal areas
Place cover (201) with cone assembly (300) on housing (101) and screw tight in crosswise order (for tightening torque see
table in appendix)
Mount actuator onto valve according to operating instructions and check limit stops.
4.4 Changing nozzle pipe
We recommend renewing the stuffing box packing when changing the nozzle pipe.
Release pressure from valve and discharge piping according to regulations
Remove old stuffing box (extractor) and remove nozzle pipe from cover
Clean stuffing space
Insert new nozzle pipe
Insert new packing in stuffing box according to cross-section drawing
Tighten cap nut

Einbau- und Betriebsanleitung
Installation and Operating instructions
Instructions de montage et de service
5702-8010
11
08/2017
1Informations générales
Les vannes de régulation sont conçues pour être utilisées avec divers types de fluide. Le choix d’une vanne dépend de son
application et des caractéristiques techniques requises ( diamètres nominaux des canalisations, pression nominale, matériau du
corps de la vanne ainsi que la forme des brides). En fonction du type de contrôle désiré, différents types de clapets peuvent être
adaptés.
Attention!! : Les vannes de régulation doivent être seulement utilisées dans leur champ d’application.
Le matériau du corps ainsi que la pression nominale de la vanne sont distinctement indiqués sur la vanne. Ces données doivent
être adaptées aux conditions d’utilisation ainsi qu’aux fluides employés .
La tracabilité des vannes est assurée par leur numéro de série unique ,“ W.Nr “( situé sur la vanne) afin de faciliter les
commandes de pièces détachées, communiquer le numéro de série de la vanne employée.
Les vannes sont mise au point et soumises à plusieurs tests après production (Exemple : Test de pression , test
d’étanchéité).Aucun réglage supplémentaire n’est nécessaire.
Attention ! : Veuillez avant toute installation ou utilisation consulter les précautions d’emplois.
L’installation ou la mise en service des vannes ne devra être réalisée que pas des personnes qualifiées.
2Installations et connexions
2.1 Instructions d’installation
Avant toute installation lire attentivement les chapitres ci-dessous
Espace d’installation :
La place nécessaire pour assurer une maintenance convenable doit être prévue (Prévoir l’ouverture du couvercle du
moteur). Lors du montage des soupapes motorisées à ciel ouvert, il y a lieu de les protéger par des auvents contre les
intempéries.
Pré installation :
Les carters de protection des brides doivent être retirés.
Nettoyage des canalisations :
Les canalisations doivent être nettoyées afin d’éliminer toute pollution (rouille , calamine, billes de soudure) avant
l’insertion d’une vanne de régulation afin d’éviter d’endommager le clapet ainsi que son étanchéité. Un filtre en amont de la
vanne peut être inséré afin de limiter le passage de particules résiduelles .
Direction du flux :
Pour les vannes à deux voies, le sens de circulation est indiqué sur la vanne par une flèche .
Pour les vannes à trois voies mélangeuses, l’évacuation est indiquée par les lettres « AB » sur la vanne
Pour les vannes à trois voies divergentes, l’admission est indiquée par les lettres « AB » sur la vanne .
Orientation de l’installation :
L’ensemble peut être installé soit à l’horizontal soit en pointant vers le haut à la vertical . Si l’ensemble se trouve à
l’horizontal les colonnettes doivent se situées l’une au dessus de l’autre afin de pouvoir supporter le poids du moteur.
Tension sur le corps de la vanne :
Toutes les précautions doivent être prises afin de protéger la vanne de toutes contraintes extérieures.
Positionnement des canalisations :
Afin d’obtenir un fonctionnement optimal de la vanne, l’admission doit être située axialement à une distance dégagée de
tout encombrement >5x DN. L’échappement doit être situé axialement à une distance dégagée de tout encombrement >
10xDN.
Avec les gazes de faible densité le canal d’amenée et le canal de sortie doit être de double longueur
Protéger le moteur de la chaleur :
Afin de protéger le moteur de la chaleur, les canalisations ainsi que le corps de la vanne doivent être isolés avant le
démarrage.

Einbau- und Betriebsanleitung
Installation and Operating instructions
Instructions de montage et de service
5702-8010
12
08/2017
2.2 Assemblage du moteur
Les vannes sont généralement livrées avec le moteur pré-assemblé .Pour pivoter, remplacer ou démonter les servomoteurs, il
est fortement conseillé de se référer aux instructions de maintenance.
Attention ! : La tige du clapet des vannes avec système de soufflet d’étanchéité, ne doit pas pivoter sous peine
d’endommager l’étanchéité.
Lors de l’enlèvement du moteur, la tige du clapet peut être propulsée vers le haut à cause de la pression
dans la vanne .
2.3 Connexions électriques
Le câblage du servomoteur doit être effectué en accord avec les instructions de montage.
Attention ! Couper l’alimentation avant toutes connexions
Avant toutes connexions prendre soin de comparer les données d’alimentation, de tension d’ampérage et de
fréquence indiquées avec la plaque signalétique du moteur.
2.4 Connexions pneumatiques
Pour chaque servomoteur pneumatique prévoir un régulateur de pression, afin d’éviter aux moteurs de s’influencer.
Attention ! la condensation dans le système doit être absolument évitée, L’emploi d’un air sec est donc obligatoire, en
particulier pour le positionneur (Absence de graissage).
3Mise en service :
Toutes les vannes sont ajustées et pré-testées sur notre site. Un ajustement avant montage n’est pas nécessaire .
Le démarrage ne doit être effectué qu’après la lecture des paragraphes précédents ainsi que leurs applications .
Etanchéité de la tige de la vanne
Les vannes comportant une étanchéité réalisée à l’aide de graphite pure doivent être resserrées nécessairement, toutes
les autres tiges comportent un ressort de prétention, ce qui ne nécessite aucun resserrage.
Attention ! : Un resserrage trop énergique pourrait causer des efforts de friction et détériorer le coulissement de la tige.
Lorsque la vanne se trouve sous pression et en température il est formellement déconseiller d’effectuer un resserrage .
Contrôle de démarrage :
Les vannes, pour fonctionner normalement doivent être utilisées avec une course comprise entre 70% et 100% .
Débit désiré non atteint : Vérifier que la vanne s’ouvre bien à 100%
Vérifier que la vanne ainsi que le filtre sont propres .
Vérifier que la vanne correspond bien aux spécifications définies
La vanne fonctionne seulement avec une petite course :
Afin d’éviter une usure prématurée il convient d’employer une vanne adaptée aux
caractéristiques de fonctionnement qui lui sont attribuées.
Le dimensionnement d’une vanne peut être discuté avec le fabricant.
Contrôle de la régulation :
La régulation doit être stable (stabilité du clapet), Une régulation toujours oscillante peut entraîner une usure prématurée.
Dans ce cas contacter le fabricant.
Pour les servomoteurs électriques le temps de changement de direction doit être au moins de 200ms.
Le temps d’une impulsion doit être au minimum de 50ms.
Afin d’éviter une usure prématurée, l’oscillation du clapet doit être évité, chez 1200 nombres d’opérations par heure

Einbau- und Betriebsanleitung
Installation and Operating instructions
Instructions de montage et de service
5702-8010
13
08/2017
4Maintenance
4.1 Garniture d’étanchéité de tige
Une garniture endommagée doit être ou changée ou resserrée nécessairement (dans le cas d’un système en graphite).Sinon la
garniture de remplacement pourrait à son tour, après une courte période ne plus être étanche .
La structure des garnitures est détaillée dans les fiches techniques correspondantes. Les garnitures sont aussi disponibles en
pièces détachées. Afin de faciliter la commande, communiquer le numéro de série de la vanne ( plaque signalétique « W.Nr »)
4.2 Changement de la garniture de la tige
Purger les canalisations et désactiver la vanne
Afin de pouvoir changer la garniture, le servomoteur doit être démonté. Afin de pouvoir démonter le servomoteur veuillez
vous référer aux instructions prévues à cet effet.
l’écrou d’accouplement doit être retiré.
Enlever l’ancienne garniture et nettoyer son emplacement.
Insérer une nouvelle garniture (Voir schéma).
Resserrer l’écrou d’accouplement ,remonter le moteur et replacer les capteurs fin de course.
Attention ! : Pour les garnitures graphite, un resserrage trop important pourrait engendrer des efforts de friction et
compromettre le bon déplacement de la tige.
4.3 Changement du soufflet d’étanchéité
Le soufflet d’étanchéité ainsi que le groupe clapet ne forment qu’une seule pièce .Lors d’un problème avec le soufflet,
l’ensemble doit être changé. Il est aussi nécessaire de remplacer le joint plat (503).
Purger les canalisations et désactiver la vanne
Désassembler le servomoteur (Voir fiche technique de démontage )
Vannes à passage direct et divergentes : retirer le couvercle (201) du corps(101)
Vanne mélangeuse :retirer les brides-B(601) du corps(101)
Retirer les vis latérales (451) ainsi que le goujon fileté (449)
Retirer la garniture étanche (441) et l’ensemble clapet(300)
Retirer le joint plat (444) et nettoyer son emplacement
Mettre en place le nouvel ensemble clapet (300) et le nouveau joint plat (444),rajouter le goujon fileté (449) afin d’éviter les
distorsions.
Visser la nouvelle garniture de sécurité (441)
Nettoyer l’emplacement des joints et le bâtis
Vannes à passage direct et divergentes : Assembler le couvercle (201) avec l’ensemble clapet sur le corps(101) en
croisant le resserrage.
Vanne mélangeuse : Assembler les brides-B(601) du corps(101) en croisant le resserrage.
Remonter le servomoteur, recaler les capteurs fin de course et vérifier leur calibration

Einbau- und Betriebsanleitung
Installation and Operating instructions
Instructions de montage et de service
5702-8010
14
08/2017
4.4 Changement de l’ensemble clapet
Il est recommandé de changer la garniture lors d’un changement de l’ensemble clapet ainsi que le joint plat (503) qui est aussi
nécessaire.
Vannes à soufflet d’étanchéité
Voir mode opératoire de changement du soufflet
Vannes à garniture de tige
Purger les canalisations et désactiver la vanne
Afin de pouvoir changer la garniture le servomoteur doit être démonté (Voir instructions de démontage).
Vannes a deux voies et divergentes : retirer le couvercle (201) du corps(101)
Vanne mélangeuse :retirer les brides-B(601) du corps(101)
Retirer et changer l’ensemble clapet(300) du couvercle(201)
Nettoyer l’emplacement des joints
Vannes a deux voies et divergentes : Assembler le couvercle (201) avec l’ensemble clapet sur le corps(101) en
croisant le resserrage
Vanne mélangeuse : Assembler les brides-B(601) du corps(101) et serrer les vis graduellement tour
après tour en croisant le resserrage.
Remonter le servomoteur, recaler les capteurs fins de course et vérifier leur calibration

Einbau- und Betriebsanleitung
Installation and Operating instructions
Instructions de montage et de service
5702-8010
15
08/2017
Anhang / Appendix / Annexe
1Drehmoment für Schrauben / torque for nuts / Couple de serrage
DN
PN
Gewinde / threat /
filetage
Dichtungsmaße / dimension gasket /
dimensions
Anzugsmomente /
torque / couple
n
D / mm
d1/ mm
d2/ mm
s / mm
Ma / Nm
15 / 20
16 / 25 / 40
4
M 10
40
54
1,5
35
25 / 32
16 / 25 / 40
4
M 12
54
68
1,5
61
40 / 50
16 / 25 / 40
4
M 16
68
82
1,5
147
65
16 / 25 / 40
4
M 16
93
113
1,5
147
80
16 / 25 / 40
8
M 16
110
130
1,5
147
100
16 / 25 / 40
8
M 16
135
160
1,5
147
125
16 / 25 / 40
8
M 20
160
190
2,0
285
150
16 / 25 / 40
8
M 20
190
220
2,0
285
200
16 / 25 / 40
12
M 20
240
270
2,0
285
250
16 / 25 / 40
12
M 24
290
325
2,0
490
DN
PN
Gewinde / threat /
filetage
Dichtungsmaße /
dimension gasket / dimensions
Anzugsmomente /
torque / couple
n
D / mm
d1/ mm
d2/ mm
s / mm
Ma / Nm
15
63 / 100
4
M 16
48
65
1,5
147
25
63 / 100
4
M 20
55
75
1,5
285
40
63 / 100
4
M 24
76
100
1,5
490
50
63 / 100
4
M 24
90
115
2,0
490
65
63 / 100
4
M 24
110
135
2,0
490
80
63 / 100
8
M 24
115
145
2,0
490
100
63 / 100
8
M 27
135
165
2,0
725
125
63 / 100
8
M 30
165
205
2,0
985
150
63 / 100
8
M 30
200
240
2,0
985
200
63 / 100
12
M 33
240
280
2,0
1330
250
63 / 100
12
M 36
280
340
2,0
1710

Einbau- und Betriebsanleitung
Installation and Operating instructions
Instructions de montage et de service
5702-8010
16
08/2017
Bild 1/ Figure 1 : Typenschild auf Ventil / nameplate on valves /
Maximal zulässige Temperatur / Betriebsdruck siehe technische Dokumentation
Maximum allowable operation temperature / pressure see technical documentation
Température maximum d’opération / pression d’opération voir documentation technique
Prüfdruck / test pressure / pression de contrôle
PT = 1,5 x PN
PN...Nenndruck, nominal pressure, pression nominale
Type
Hub
Kvs
DN TS
PS
W. Nr.
0036
Temperatur / temperature / température
°C
zul. Betriebsdruck/ allowable operation pressure /
pression d’operation
Nennweite / nominal diometer / diamétre nominale
Seriennummer / Serial number / numero de vannes
Stellweg / stroke / course
Baureihe / Serie / series
Jmm xxxx
Jahr / year / annéc
Monat / month / mois

Einbau- und Betriebsanleitung
Installation and Operating instructions
Instructions de montage et de service
5702-8010
17
08/2017
Druck / Temperatur Einsatzgrenzen Werkstoffe
Pressure / Temperature ratings of material
Pressure / Température pour les matériaux
Einsatzgrenzen nach DIN EN 1092-1:2008 / DIN EN 1092-2:1997
PN
Werkstoff / material / matière
Zulässiger Betriebsüberdruck (stoßfrei) in bar bei Temperatur °C / max. pressure in bar at temperature °C
-10
100
150
200
250
300
350
400
425
450
500
510
520
530
16
EN-GJL-250 (0.6025)
16
16
14
13
11
10
-
-
-
-
-
-
-
-
EN-GJS-400-18-LT (0.7043)
16
16
16
15
14
13
11
-
-
-
-
-
-
-
GP240GH (1.0619)
16
15
14
13
12
11
10
9
-
-
-
-
-
-
GX5CrNiMo19-11-2 (1.4408)
16
16
14,5
13
12,5
11,5
11**
10,5**
25
EN-GJS-400-18-LT (0.7043)
25
25
24
23
22
20
18
-
-
-
-
-
-
-
GP240GH (1.0619)
25
23
22
19
18
17
16
15
-
-
-
-
-
-
GX5CrNiMo19-11-2 (1.4408)
25
25
23
21
20
18
18**
17**
-
-
-
-
-
-
40
GP240GH (1.0619)*
40
40
39
38
36
32
28
22
-
-
-
-
-
-
GX5CrNiMo19-11-2 (1.4408)
40
40
36
33,5
31,5
29,5
28,5**
27**
-
-
-
-
-
-
GX5CrNiMoNb19-11-2
(1.4581)
40
40
39
37
35
33
32
31
31
30
30
30
30
30
63
GP240GH (1.0619)
63
59
55
52
48
43
40
37
-
-
-
-
-
-
G17CrMo 5-5 (1.7357)
63
63
63
63
63
63
60
57
55
53
41
35
28
23
GX5CrNiMo19-11-2 (1.4408)
63
63
57
53
50
47
45**
43**
-
-
-
-
-
-
GX5CrNiMoNb19-11-2
(1.4581)
63
63
62
59
56
52
51
49
49
48
47
47
47
47
100
GP240GH (1.0619)
100
93
88
83
76
69
64
60
-
-
-
-
-
-
G17CrMo 5-5 (1.7357)
100
100
100
100
100
100
95
90
87
84
65
55
45
37
GX5CrNiMo19-11-2 (1.4408)
100
100
91
84
79
74
71**
68**
-
-
-
-
-
-
GX5CrNiMoNb19-11-2
(1.4581)
100
100
98
93
88
83
80
78
76
76
75
74
74
74
160
GP240GH (1.0619)
160
160
141
130
112
96
90
80
-
-
-
-
-
-
G17CrMo 5-5 (1.7357)
160
160
160
160
160
160
153
146
142
139
118
100
79
62
Werte sind gerundet
* DIN EN 1092-1: 1997
** Ausschluss von Interkristalliner Korrosion (keine Säuren und säurehaltigen Medien)
Einsatzgrenzen nach ASME B16.34:1996
CLASS
Werkstoff / material / matière
Zulässiger Betriebsüberdruck (stoßfrei) in bar bei Temperatur °C / max. pressure in bar at
temperature °C
-29
40
95
150
205
260
315
345
375
400
425
455
480
510
530
#150
A 216 WCB
20
20
18
16
14
12
10
8,5
7,5
6,5
5,5
-
-
-
-
#300
50
50
47
45
44
42
38
37
37
35
28
-
-
-
-
#600
100
100
93
90
87
82
75
74
73
69
56
-
-
-
-
#900
150
150
140
135
131
124
113
111
110
104
85
-
-
-
-
#150
A 351 CF8M
20
20
16
15
13
11
9
8
7
6
5,5
4
3,5
2,5
1
#300
50
50
43
38
35
33
31
30
29
29
29
29
28
26
24
#600
100
100
85
77
71
66
62
61
60
59
58
57
57
53
48
#900
150
150
128
116
106
98
93
92
90
88
87
86
86
80
72
#600
A 217 WC9
100
100
100
100
97
92
83
81
78
73
70
67
62
52
36
#900
150
150
150
150
146
137
125
121
117
110
105
100
93
78
54

Einbau- und Betriebsanleitung
Installation and Operating instructions
Instructions de montage et de service
5702-8010
18
08/2017
2Ersatzteilliste / spare parts list / liste des pièces de rechange MV 52 / PV 62; MV 53 / PV 63
Pos
D
GB
FR
101
GP-240-GH; G 17 CrMo 5-5
BVG...
Gehäuse
body
corps
102
1.4571
FSIR...
Sitzring
seat ring
siege
201
GP-240-GH; G 17 CrMo 5-5
BVD...
Deckel
bonnet
couverde
300
BVK....
Kegelgruppe
cone assembly
clapet
301
1.4122
FKKP...
Kegelkopf
cone head
clapet
302
1.4571
Kegelspindel
cone spindle
tige
400
CVSHHNAE
Spindelabdichtung
spindel packing
garniture tige
401
Ms 58
Überwurfmutter
cap nut
ecrou à chapeau
402
Rg 7
Führungsbuchse
fairlead bush
douille
403
Rg 7
Führungsring
bush
douille
405
N 90
Abstreifring
scraper ring
anneau racleur
406
PTFE
GDID....
Dachmanschetten
chevron rings
manchettes
407
1.4301
Scheibe
wahser
rondelle
408
X 12 CrNi 177
Druckfeder
spring
ressort
409
NBR
O-Ring
o-ring
joint torique
420
CVSHONAE
Spindelabdichtung
spindel packing
garniture tige
421
Rg 7
Führungsring
bush
douille
422
X 12 CrNi 177
Druckfeder
spring
ressort
423
1.4301
Scheibe
wahser
rondelle
424
PTFE
GDID....
Dachmanschetten
chevron rings
manchettes
425
EPDM
O-Ring
o-ring
joint torique
426
Rg 7
Führungsbuchse
fairlead bush
douille
427
DIN 933-A2 M10X20
Sechskantschraube
bolt
vis á tete
428
N 90
Abstreifring
scraper ring
anneau racleur
460
CVSHHTBE
Spindelabdichtung
spindel packing
garniture tige
461
Ms 58
Überwurfmutter
cap nut
ecrou à chapeau
462
Rg 7
Führungsbuchse
fairlead bush
douille
463
Rg 7
Führungsring
bush
douille
464
N 90
Abstreifring
scraper ring
anneau racleur
465
PTFE
GDID....
Dachmanschetten
chevron rings
manchettes
466
1.4301
Scheibe
wahser
rondelle
467
X 12 CrNi 177
Druckfeder
spring
ressort
468
EPDM
O-Ring
o-ring
joint torique
501
C 35 Y
Sechskantmutter
nut
ecrou six pans
502
Ck 35 Yk
Stiftschraube
stud
tige filetée
503
Reingraphit
FDIF...
Flachdichtring
gasket
joint plat
601
1.4571
Axial-Hohlkegeldüse
nozzle
buse
701
St 35.8
Lochkäfig
perforated cage
cage perforeé
702
GP-240-GH / G 17 CrMo 5-5
BVD...
Deckel
bonnet
couverde
703
Reingraphit
Presspackung
packing
garniture
704
1.4122
Düsenrohr
blast pipe
lance
705
1.4571
Axial-Hohlkegeldüse
nozzle
Tobe buse
706
DIN 939
Stiftschraube
stud
tige filetée
707
1.4541
Stopfring
stuffing-ring
bourrage anneau
708
DIN 934
Sechskantmutter
nut
ecrou six pans
709
1.4571
Flansch
flange
bride
800
CVSHHNAA
Spindelabdichtung
spindel packing
garniture tige
802
Rg 7
Führungsring
bush
douille
803
Reingraphit
Presspackung
packing
garniture
804
Rg 7
Stopfbuchse
stuffing box
boite
805
Ms 58
Überwurfmutter
cap nut
ecrou à chapeau
810
Rg 7
Buchse
bush
douille
820
CVSHONAA
Spindelabdichtung
spindel packing
garniture tige
821
Rg 7
Buchse
bush
douille
822
Reingraphit
Presspackung
packing
garniture
823
Ck 35 Yk
Stiftschraube
stud
tige filetée
824
Rg 7
Stopfbuchse
stuffing box
boite
825
DIN 934 1.4301
Sechskantmutter
nut
écrou six pans
826
DIN 938 1.4301
Stiftschraube
stud
tige filetée
827
DIN 934 1.4301
Sechskantmutter
nut
ecrou six pans
860
CVSHHTBA
Spindelabdichtung
spindel packing
garniture tige
861
Rg 7
Führungsring
bush
douille
862
Reingraphit
Presspackung
packing
garniture
863
Rg 7
Stopfbuchse
stuffing box
boite
864
Rg 7
Überwurfmutter
cap nut
ecrou à chapeau

Einbau- und Betriebsanleitung
Installation and Operating instructions
Instructions de montage et de service
5702-8010
19
08/2017
Ersatzteilliste / spare parts list / liste des pièces de rechange MV 52.. / PV 62..; MV 53.. / PV 63..
MV5251 / MV 5351 PN 40
MV 5251 / MV 5351 PN 100
201
302
301
102
101
501
502
503
810
701
501
502
503
702
703
704
709
707
706
708
400
800
805
804
803
802
405
402
401
409
406
407
408
403
428
427
426
425
424
423
422
421
420
825
824
823
822
821
820
201
302
301
102
101
810
811
501
502
503
701
502
503
501
702
703
706
707
708
704
601
709
860
460
464
462
461
468
465
466
467
864
863
862
861
463

Einbau- und Betriebsanleitung
Installation and Operating instructions
Instructions de montage et de service
5702-8010
20
08/2017
3Ersatzteilliste / spare parts list / liste des pièces de rechange MV 54 / PV 64
POS
D
GB
FR
101
GP-240-GH / G 17 CrMo 5-5
BVG...
Gehäuse
body
corps
102
1.4571
FSIR...
Sitzring
seat ring
siège
201
GP-240-GH / G 17 CrMo 5-5
BVD...
Deckel
bonnet
couverte
300
BVK....
Kegelgruppe
cone assembly
clapet
301
1.4122
FKKP...
Kegelkopf
cone head
clapet
302
1.4571
Kegelspindel
cone spindle
tige
400
CVSNHNAE
Spindelabdichtung
spindle packing
garniture tige
401
Rg 7
Führungsbuchse
fairlead bush
douille
402
DIN 933-A2 M10x20
Sechskantschraube
bolt
vis á tête
403
N 90
Abstreifring
scraper ring
anneau racleur
404
PTFE
GDID....
Dachmanschetten
chevron rings
manchettes
405
1.4310
Druckfeder
spring
ressort
406
DIN 1804; M85x2 verz.
Nutmutter
slotted ring nut
écrou à rainures
407
H II
Trägerplatte
mounting plate
Plaque support
408
EPDM
O-Ring
o-ring
joint torique
409
EPDM
O-Ring
o-ring
joint torique
410
1.4301
Distanzrohr
spacer
tube d'écartement
411
G-Bz 12
Führungsring
bush
douille
412
DIN 1473 6x25 1.4305
Zylinderkerbstift
grooved dowel pin
goupille
405
N 90
Abstreifring
scraper ring
anneau racleur
406
PTFE
GDID....
Dachmanschetten
chevron rings
manchettes
407
1.4301
Scheibe
washer
rondelle
408
X 12 CrNi 177
Druckfeder
spring
ressort
409
NBR
O-Ring
o-ring
joint torique
501
C 35 Y
Sechskantmutter
nut
écrou six pans
502
Ck 35 Yk
Stiftschraube
stud
tige filetée
503
Reingraphit
FDIF...
Flachdichtring
gasket
joint plat
601
1.4571
Axial-Hohlkegeldüse
nozzle
buse
701
St 35.8
Lochkäfig
perforated cage
cage perforeé
702
GP-240-GH / G 17 CrMo 5-5
BVD...
Deckel
bonnet
couverde
703
Reingraphit
Presspackung
packing
garniture
704
1.4122
Düsenrohr
blast pipe
lance
705
1.4571
Axial-Hohlkegeldüse
nozzle
Tobe buse
706
DIN 939
Stiftschraube
stud
tige filetée
707
1.4541
Stopfring
stuffing-ring
bourrage anneau
708
DIN 934
Sechskantmutter
nut
ecrou six pans
709
1.4571
Flansch
flange
bride
800
CVSQ_NAA
Spindelabdichtung
spindle packing
garniture tige
801
G-Bz 12
Führungsring
bush
Douille
802
Reingraphit
Presspackung
packing
garniture
803
P 265 GH
Trägerplatte
mounting plate
Plaque support
804
DIN 1804 M85x2 verz.
Nutmutter
slotted ring nut
écrou à rainures
805
1.4541.
Stopfbuchse
stuffing box
boite
806
DIN 939 1.4301
Stiftschraube
stud
tige filetée
807
DIN 934 1.4301
Sechskantmutter
nut
écrou six pans
808
1.4301
Distanzrohr
space
tube d'écartement
810
G-Bz 12
Buchse
bush
douille
811
St 37
Scheibe
washer
Rondelle
820
CVSQHRBA
Spindelabdichtung
spindle packing
Garniture tigé
821
1.4541
Stopfring
stuffing-box
boite
822
DIN 939 1.4301
Stiftschraube
stud
tige filetée
823
DIN 934 1.4301
Sechskantmutter
nut
écrou six pans
824
Reingraphit
Presspackung
packing
Garniture
825
1.4122
Führungsring
bush
douille
826
DIN 1804 M85x2 verz
Nutmutter
slotted ring nut
écrou à rainures
827
P 265 GH
Trägerplatte
mounting plate
Plaque support
828
1.4301
Distanzrohr
space
tube d'écartement
829
DIN 1473 1.4305
Zylinderkerbstift
grooved dowel pin
goupille
This manual suits for next models
1
Table of contents
Languages:
Other RTK Control Unit manuals
Popular Control Unit manuals by other brands

Telit Wireless Solutions
Telit Wireless Solutions UE910 series Hardware user's guide
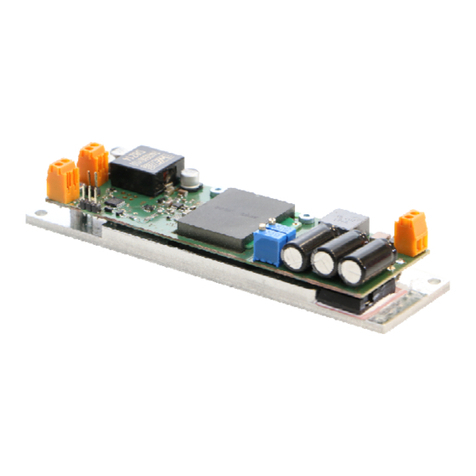
PICOLAS
PICOLAS LDP-VRM 025-100 CA user manual
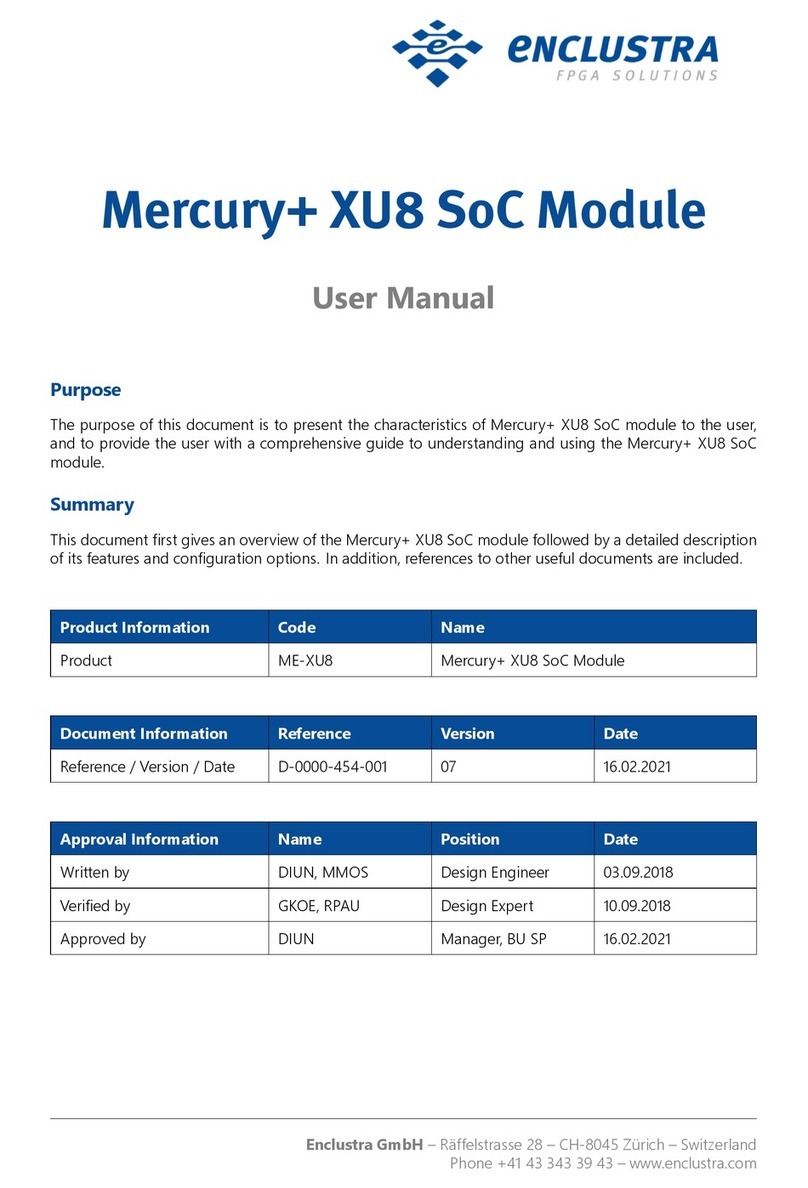
Enclustra
Enclustra Mercury+ XU8 SoC user manual

W&T
W&T 57641 manual

ZIEHL-ABEGG
ZIEHL-ABEGG U-EK230E operating instructions
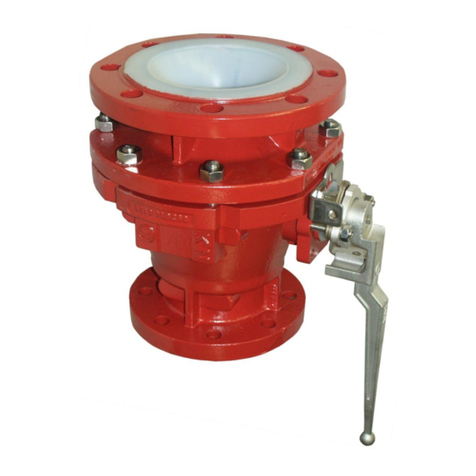
Richter
Richter KA-N/F Series Installation and operating manual