Ruska Instrument 7010 User manual

RUSKA MODEL 7010
DIGITAL PRESSURE CONTROLLER
USER’S MANUAL

DIGITAL PRESSURE CONTROLLER
MODEL 7010
USER’S MANUAL
RUSKA INSTRUMENT CORPORATION
10311 WESTPARK DRIVE, HOUSTON, TEXAS 77042
(713) 975-0547 FAX: (713) 975-6338
Release: 7010-1D01
Revision: F
Date: 01/02/02

WARRANTY
Ruska Instrument Corporation warrants its products to conform to or exceed the
specifications as set forth in its catalogs in use at the time of sale and reserves the right,
at its own discretion, without notice and without making similar changes in articles
previously manufactured, to make changes in materials, designs, finish, or specifications.
Ruska Instrument Corporation warrants products of its own factory against defects of
material or workmanship for a period of one year from date of shipment.
Liability of Ruska Instrument Corporation under this warranty shall be limited to
replacing, free of charge (FOB Houston, Texas), any such parts proving defective within
the period of this warranty, but will not be responsible for transportation charges or
consequential damages.
This warranty is not made for products manufactured by others which are illustrated and
described in Ruska catalogs or incorporated in Ruska products in essentially the same
form as supplied by the original manufacturer. However, Ruska Instrument Corporation
agrees to use its best efforts to have original suppliers make good their warranties.
-ii-

COPYRIGHT NOTICE
Copyright © 1997 by Ruska Instrument Corporation. All rights reserved. This document
may not be reproduced in part or in whole without the express written consent of Ruska
Instrument Corporation.
DISCLAIMER
No representations or warranties are made with respect to the contents of this user’s
manual. Further, Ruska Instrument Corporation reserves the right to revise this manual
and to make changes from time to time in the content hereof without obligation to notify
any person of such revision.
TRADEMARK NOTICE
® is a registered trademark of Ruska Instrument Corporation.
Trademarks or tradenames are subject to state and federal laws concerning their unauthorized
use or other infringements. The fact that the product marks or names in this manual do not bear
a trademark symbol DOES NOT mean that the product name or mark is not registered as a
trademark or tradename. Any queries concerning the ownership or existence of any trademarks
or tradenames mentioned in this manual should be independently confirmed with the
manufacturer or distributor of the product.
-iii-

REVISION NOTICE
RELEASE
NUMBER REV DATE OF
RELEASE
DESCRIPTION
7010-1D01 A 11/10/93 Original release
7010-1D01 B 9/16/94 Text changes, ECO-19492
7010-1D01 C 4/20/95
Text & drawing changes, ECO-
19578
7010-1D01 D 6/16/97
Text & drawing changes, ECO-
17791
7010-1D01 E 07/29/99 Text changes per ECO-17805.
7010-1D01 F 01/02/02 Equation change per DC/RO-
23192
-iv-

REVISION HISTORY
RELEASE 7010-1D01 Revision A (11/10/93)
.Original release.
RELEASE 7010-1D01 Revision B (9/16/94)
Text changes, ECO 19492.
RELEASE 7010-1D01 Revision C (4/20/95)
Text & drawing changes, ECO 19578.
RELEASE 7010-1D01 Revision D (6/16/97)
Text & drawing changes, ECO 17791.
RELEASE 7010-1D01 Revision E (07/29/99)
Text changes per ECO-17805.
RELEASE 7010-1D01 Revision F (01/02/02)
Equation change per DC/RO-23192
-v-

SAFETY SUMMARY
The following are general safety precautions that are not related to any specific procedures and
do not appear elsewhere in this publication. These are recommended precautions that personnel
must understand and apply during equipment operation and maintenance to ensure safety and
health and protection of property.
KEEP AWAY FROM LIVE CIRCUITS
Operating personnel must at all times observe safety regulations. Do not replace components or
make adjustments inside the equipment with the voltage supply connected. Under certain
conditions, dangerous potentials may exist when the power control is in the off position due to
charges retained by capacitors. To avoid injuries, always remove power from, discharge, and
ground a circuit before touching it.
DO NOT SERVICE OR ADJUST ALONE
Do not attempt internal service or adjustment unless another person capable of rendering aid
and resuscitation is present.
RESUSCITATION
Personnel working with or near dangerous voltages shall be familiar with modern methods of
resuscitation. Such information may be obtained from your local American Medical Association.
ELECTROSTATIC DISCHARGE SENSITIVE PARTS
CAUTION: Electrostatic discharge sensitive (ESDS) is applied to low power, solid-state
parts which could be damaged or destroyed when exposed to discharges of static
electricity. Maintenance personnel are often not aware that an ESDS part has been
damaged or destroyed because electrostatic discharges at levels less than 4,000 volts
cannot be seen, felt, or heard.
When the ESDS symbol appears between a paragraph number and paragraph title, the
entire paragraph and all subparagraphs shall be considered ESD sensitive. When the ESDS
symbol appears between a step number and the step test, the step shall be considered ESD
sensitive.
COMPRESSED GAS
Use of compressed gas can create an environment of propelled foreign matter. Pressure system
safety precautions apply to all ranges of pressure. Care must be taken during testing to ensure
that all pneumatic connections are properly and tightly made prior to applying pressure.
Personnel must wear eye protection to prevent injury.
PERSONAL PROTECTIVE EQUIPMENT
Wear eye protection approved for the materials and tools being used.
INERT GASES
Operation of pressure equipment may be accompanied by the discharge of inert gases to the
atmosphere. The result is a reduction of oxygen concentration. Therefore, it is strongly suggested
that exhaust gases not be trapped in the work area.
-vi-

TABLE OF CONTENTS
WARRANTY .............................................................................................................................ii
COPYRIGHT NOTICE .............................................................................................................iii
REVISION NOTICE .................................................................................................................iv
REVISION HISTORY .................................................................................................................v
SAFETY SUMMARY..................................................................................................................vi
TABLE OF CONTENTS ........................................................................................................... vii
SECTION 1.0: GENERAL INFORMATION
1.1 INTRODUCTION........................................................................................... 1-1
1.2 GENERAL INFORMATION.............................................................................. 1-1
1.3 FEATURES ..................................................................................................... 1-1
1.4 STANDARD EQUIPMENT & OPTIONS ............................................................1-2
SECTION 2.0: THEORY OF OPERATION
2.1 INTRODUCTION........................................................................................... 2-1
2.2 POWER SUPPLY............................................................................................. 2-1
2.3 ELECTRONICS MODULE ............................................................................... 2-2
2.3.1 CONTROL BOARD............................................................................. 2-2
2.3.2 MICROPROCESSOR BOARD ............................................................... 2-2
2.3.3 OPTION BOARD ................................................................................ 2-3
2.3.4 IEEE-488 INTERFACE.......................................................................... 2-3
2.3.5 FRONT PANEL ................................................................................... 2-3
2.4 PNEUMATICs MODULE ................................................................................. 2-4
2.4.1 MEASURE MODE PNEUMATICS .......................................................... 2-6
2.4.1.1 Reference Port ....................................................................... 2-6
2.4.1.1.1 Special Consideration for 1 psi 7010 ......................................... 2-6
2.4.1.2 Test Port................................................................................ 2-7
2.4.1.3 Vent Port............................................................................... 2-7
2.4.2 CONTROL MODE PNEUMATICS......................................................... 2-8
2.4.2.1 Pressure Supply Port .............................................................. 2-8
2.4.2.2 Vacuum Supply (exhaust) Port ................................................ 2-8
2.4.2.3 Pressure Control.................................................................... 2-8
2.4.3 CONTROL STRATEGY ........................................................................ 2-8
2.5 TRANSDUCER MODULE .............................................................................. 2-11
2.5.1 QUARTZ BOURDON TUBE SENSOR (TRANSDUCER01) .....................2-11
2.5.2 SENSOR BOARD .............................................................................. 2-12
2.5.3 LINEARIZATION TERM ...................................................................... 2-12
2.5.4 AUXILIARY SENSORS ........................................................................ 2-13
2.5.4.1 Case Reference Vacuum Sensor ........................................... 2-13
2.6 SOFTWARE ............................................................................................ 2-13
2.6.1 SAFETY CONSIDERATIONS .............................................................. 2-13
2.6.1.1 Preventing Operator Errors .................................................. 2-13
2.6.1.2 Pneumatic Errors ................................................................. 2-13
2.6.1.3 Shutoffs .............................................................................. 2-13
2.6.1.4 Oven Control...................................................................... 2-13
2.6.1.5 Pressure Reading and Correction .........................................2-13
2.7 USING OPTO 22 MODULES........................................................................ 2-15
-vii-

SECTION 3.0: INSTALLATION
3.1 INTRODUCTION........................................................................................... 3-1
3.2 UNPACKING THE DPC.................................................................................. 3-1
3.3 CAUTIONS .............................................................................................. 3-1
3.4 POWERING UP THE DPC............................................................................... 3-1
3.4.1 OBSERVING THE DPC’S FULL SCALE RATING .....................................3-1
3.5 PNEUMATIC CONNECTIONS........................................................................ 3-2
3.5.1 PRESSURE SUPPLY PORT..................................................................... 3-2
3.5.2 SUPPLY VACUUM............................................................................... 3-2
3.5.3 TEST PORT ......................................................................................... 3-3
3.5.4 REFERENCE PORT .............................................................................. 3-3
3.5.5 VACUUM TRANSDUCER INSTALLATION ............................................. 3-5
SECTION 4.0: LOCAL OPERATION
4.1 TUTORIAL .............................................................................................. 4-3
4.2 MEASURING PRESSURE ................................................................................. 4-4
4.2.1 SELECTING MODE OF OPERATION.................................................... 4-5
4.2.1.1Gauge Only Instruments.......................................................... 4-5
4.2.1.2Absolute Only Instruments ....................................................... 4-5
4.2.1.3Differential Instruments............................................................ 4-5
4.2.1.3.1 Absolute Mode .................................................................. 4-5
4.2.1.3.2 Gauge Mode..................................................................... 4-5
4.2.1.3.3 Differential Model .............................................................. 4-5
4.2.2 SELECTING PRESSURE UNITS.............................................................. 4-6
4.2.3 DEFINING A NEW PRESSURE UNIT ..................................................... 4-6
4.2.4 CHANGING THE NUMBER OF DECIMALS........................................... 4-6
4.2.5 SETTING THE ALARM LIMITS............................................................... 4-7
4.2.6 USING HEAD PRESSURE CORRECTION............................................... 4-7
4.2.7 ZEROING .......................................................................................... 4-7
4.3 CONTROLLING PRESSURE ............................................................................ 4-8
4.3.1 SETTING THE PRESSURE SETPOINT..................................................... 4-8
4.3.2 ENTERING/EXITING CONTROL MODE ............................................... 4-8
4.3.3 SETTING SLEW RATE .......................................................................... 4-8
4.3.4 STEPPING AND LOGGING................................................................. 4-8
4.4 PROGRAMMING SEQUENCES....................................................................... 4-9
4.4.1 STORING A SEQUENCE IN MEMORY ................................................. 4-9
4.4.2 PREPARING TO PROGRAM ................................................................. 4-9
4.4.3 ENTERING A NEW PROGRAM ..........................................................4-10
4.4.4 AUTOMATICALLY GENERATING A PROGRAM................................... 4-10
4.4.5 CHANGING THE NAME OF A PROGRAM ......................................... 4-11
4.4.6 CHANGING AN EXISTING PROGRAM ..............................................4-11
4.4.7 CHANGING THE CONFIGURATION STORED WITH A PROGRAM...... 4-11
4.4.8 RUNNING A PROGRAM ................................................................... 4-12
4.4.9 SWEEP TEST ..................................................................................... 4-12
4.5 CONFIGURATION ...................................................................................... 4-13
4.5.1 CALIBRATION PASSWORD ............................................................... 4-13
4.5.2 TEST ACCESS PASSWORD ................................................................ 4-13
4.5.3 BAR GRAPH MAXIMUM..................................................................... 4-13
4.5.4 KEY CLICK ....................................................................................... 4-14
-viii-

4.5.5 ENABLE ERROR ................................................................................ 4-14
4.5.6 DATE/TIME ...................................................................................... 4-14
4.6 MEMORY CARD .......................................................................................... 4-14
4.6.1 CARD SUPPORT ............................................................................... 4-14
4.6.2 SAVING/RESTORING SETUP INFORMATION ..................................... 4-14
4.6.3 SAVING/RESTORING CALIBRATION INFORMATION ......................... 4-15
4.6.4 SAVING/RESTORING PROGRAMS..................................................... 4-15
SECTION 5.0: REMOTE OPERATION
5.1 CAPABILITIES 5-1
5.1.1 IEEE-488............................................................................................ 5-1
5.1.2 RS-232 .............................................................................................. 5-1
5.2 REMOTE/LOCAL OPERATION........................................................................ 5-2
5.3 CONFIGURATION ........................................................................................ 5-2
5.4 DEVICE MESSAGES ....................................................................................... 5-2
5.4.1 SCPI COMMAND FORMAT................................................................. 5-2
5.4.2 SCPI RESPONSE FORMAT ................................................................... 5-3
5.4.3 ANSI/IEEE 488.2-1987 COMMAND SUMMARY................................... 5-3
5.4.4 SCPI COMMAND SUMMARY .............................................................. 5-3
5.4.5 EXAMPLE SCPI COMMANDS............................................................... 5-6
5.4.6 SCPI STATUS REGISTERS..................................................................... 5-7
5.5 6005 INTERFACE PANEL EMULATION............................................................ 5-8
5.6 SERIAL OPERATION....................................................................................... 5-8
SECTION 6.0: MAINTENANCE
6.1 INTRODUCTION........................................................................................... 6-1
6.2 OBSERVING THE SOFTWARE VERSION NUMBER............................................ 6-1
6.3 PREVENTIVE MAINTENANCE.......................................................................... 6-1
6.3.1 INITIATING THE DPC’S SELF TEST....................................................... 6-1
6.3.2 REMOVING THE DPC’S COVER .......................................................... 6-3
6.3.3 MOISTURE FILTER .............................................................................. 6-3
6.3.4 PARTICLE FILTERS ............................................................................... 6-3
6.3.5 VACUUM PUMPS ............................................................................... 6-3
6.3.6 PROCESSOR BATTERY ........................................................................ 6-3
6.4 CALIBRATION 6-4
6.4.1 CALIBRATION INSTRUCTIONS ........................................................... 6-4
6.4.1.1 Preparation........................................................................... 6-4
6.4.1.2 Storing the Coefficients .......................................................... 6-5
6.4.2 VACUUM (NEGATIVE GAUGE) CALIBRATIONS.................................... 6-6
6.4.3 EDITING THE CALIBRATION COEFFICIENTS ....................................... 6-7
6.4.4 ZEROING .......................................................................................... 6-7
6.4.4.1 Gauge Only Instruments........................................................6-8
6.4.4.2 Differential Instruments .......................................................... 6-8
6.4.4.2.1 Gauge Mode ..................................................................... 6-8
6.4.4.2.2 Absolute Mode ................................................................... 6-8
6.4.4.2.3 Absolute Instruments .......................................................... 6-8
6.5 SENSOR PHOTOCELL ZEROING.................................................................... 6-9
-ix-

SECTION 7.0: PREPARATION FOR STORAGE & SHIPMENT
7.1 DISCONNECTING THE DPC.......................................................................... 7-1
7.2 PACKING INSTRUCTIONS ............................................................................. 7-1
7.3 SHIPPING INSTRUCTIONS............................................................................. 7-3
APPENDIX A: SUMMARY OF SPECIFICATIONS
A.1 ACCURACY ..................................................................................................A-1
A.2 SPECIFICATIONS ..........................................................................................A-2
APPENDIX B: SUMMARY OF ERROR MESSAGES................................................B-1
LIST OF FIGURES
FIGURE 2-1: MODEL 7010 BLOCK DIAGRAM .............................................................. 2-1
FIGURE 2-2A: MODEL 7010 DPC DIFFERENTIAL PNEUMATICS DIAGRAM .......................2-4
FIGURE 2-2B: MODEL 7010 DPC ABSOLUTE PNEUMATICS DIAGRAM............................ 2-5
FIGURE 2-2C: MODEL 7010 DPC HIGH PRESSURE PNEUMATICS DIAGRAM.................... 2-5
FIGURE 2-3: PRESSURE CONTROL (MULTIPLE STEPS)....................................................2-9
FIGURE 2-4: PRESSURE CONTROL (10% TO 20% STEPS) ............................................ 2-10
FIGURE 2-5: SHAFT/MAGNET SECTION ....................................................................2-11
FIGURE 2-6: PHOTOCELL/LIGHT SPOT...................................................................... 2-12
FIGURE 2-7: AUXILLARY SENSOR DISPLAY ................................................................. 2-13
FIGURE 3-1A: MODEL 7010 BACK PANEL...................................................................... 3-1
FIGURE 3-1B: MODEL 7010 ABSOLUTE BACK PANEL..................................................... 3-4
FIGURE 3-1C: MODEL 7010 HIGH PRESSURE BACK PANEL ............................................3-4
FIGURE 4-1: MODEL 7010 FRONT PANEL ...................................................................4-1
FIGURE 4-2: MENU TREE.............................................................................................4-2
FIGURE 6-4: VACUUM CALIBRATION .......................................................................... 6-6
FIGURE 6-5: PHOTOCELL LOCATION ....................................................................... 6-10
FIGURE 7-1: PACKING THE DPC .................................................................................7-2
LIST OF TABLES
TABLE 1-1: OPTIONS LIST FOR THE MODEL 7010 ..................................................... 1-3
TABLE 2-1: CONVERSION FACTORS ......................................................................... 2-3
TABLE 2-2: SOLENOID VALVE STATES ....................................................................... 2-6
TABLE 2-3: OPTO 22 MODULES .............................................................................2-16
TABLE 3-1: GENERAL SPECIFICATIONS: GENERAL PARAMETERS................................. 3-1
TABLE 6-1: ELECTRONIC SELF TEST........................................................................... 6-2
TABLE 6-2: PNEUMATIC SELF TEST ............................................................................ 6-2
TABLE A-1: PERFORMANCE SPECIFICATIONS ............................................................A-3
TABLE A-2: RELIEF VALVE SETTINGS...........................................................................A-4
-x-

SECTION 1.0
GENERAL INFORMATION
1.1 INTRODUCTION
This manual contains operation and routine and preventive maintenance instructions for the
Model 7010 Digital Pressure Controller (DPC) manufactured by Ruska Instrument Corporation,
Houston, Texas. This section of the manual provides general information about the DPC and
presents its features and options.
1.2 GENERAL INFORMATION
The Ruska Model 7010 DPC uses force-balanced, fused-quartz Bourdon tube technology to
provide the precise measurement of pressure. During normal operation, the DPC performs in
either Measure mode or Control mode.
In Control mode, the DPC simultaneously measures and controls pressure. Control mode is
commonly used in the calibration and testing of pressure gauges, transducers, pressure switches,
and production pressure instruments.
In Measure mode, the DPC measures pressure. Typically, Measure mode applications are found
in research laboratories, wind tunnel testing, power plant testing, and bubbler tank volume
accountancy systems. It is also used to monitor barometric pressures, vacuum systems, and
differential pressure devices.
1.3 FEATURES
The following features are standard on all Model 7010 DPCs.
Fused-Quartz Bourdon Tube Technology: Ruska’s force-balanced, fused-quartz Bourdon tube
sensor makes use of the stability, high elasticity, low hysteresis, and excellent fatigue strength of
fused quartz. This time-proven technology eliminates the need for gear trains, bearings, shafts,
and other moving parts that can wear out or introduce hysteresis or deadband into the process.
Mercury-Free: All components in the DPC are mercury-free. This includes the temperature
controller for the quartz Bourdon tube, which is totally electronic.
NIST Traceability: All DPCs are calibrated per ANSI/NCSL Z-540-1-1994 using Ruska
deadweight gauges that are directly traceable to the National Institute of Standards and
Technology (NIST).
Universal Power Supply: The DPC’s universal power supply accepts AC voltages between 90 and
260 volts, and DC voltages between 100 and 370 volts. To “reconfigure” the DPC for use in
another country, the user simply changes the power cord.
DPCs with ranges from 501 to 2500 psi can be either 115 or 230 VAC.
Please refer to section 3.4.
H
I
G
H
P
R
E
S
S
U
R
E
Measure While Control: The DPC simultaneously displays the commanded pressure, the actual
pressure, and the difference between the two. A bar graph indicates how close the actual
pressure is to the commanded pressure, as well as how close the commanded pressure is to the
DPC’s full scale pressure.
INTRODUCTION
1-1

Friendly Display: The DPC’s vacuum fluorescent display combines a bright, low-glare readout
with a wide viewing angle. During normal operation, the measured pressure is easily visible from
a distance of 10 feet (3 meters).
Adjustable Pressure Display: The pressure display may be adjusted to show one decimal greater
than or less than the default resolution.
Ease of Operation: An intuitive, menu-driven interface makes the DPC easy to use. Frequently
used selections such as the units of measure are restored to memory each time the DPC powers
up.
Easily Programmable: The DPC’s powerful microprocessor provides the basis for smart
electronics. With a few simple keystrokes, the user can set limits on the system pressure, create
unique units of measure, program a test sequence, and more.
Modular Design: The sensing element, pneumatics, electronics, and user interface are separated
into modules, making maintenance faster and easier.
Attractive Desktop Packaging: A sturdy aluminum case houses all of the DPC’s pneumatics,
electronics, and user controls. With the optional rack mount kit, this standard 19" EIA chassis fits
easily into a rack mount system.
Power On Self Test: Upon power-up, the DPC quickly tests its hardware and software. After the
DPC completes this test, the user can select more extensive self-tests for the pneumatics and
electronics.
Ease of Calibration: A three-point calibration may be performed either remotely or entirely from
the front panel. No disassembly is required, and there are no potentiometers to tune.
Automatic Zero Adjust: At the user’s request, the DPC’s software automatically performs the zero
adjustment, with no potentiometers to tune.
Automatic Head Correction: The DPC automatically corrects for head pressure between the DPC
and the device under test (DUT), taking into account the density of the test gas; e.g., air or
nitrogen.
Choice of Medium: Although the DPC is not sensitive to the type of gas used within the system,
the user can select either instrumentation air or nitrogen, allowing the DPC to automatically make
pressure head corrections.
Choice of Display Units: Standard units include inHg at 0 °C and 60 °F, kiloPascals, bars, pounds
per square inch, inH2O at 4 °C, 20 °C, and 25 °C, kilograms per square centimeter, mmHg,
cmHg at 0 °C, and cmH2O at 4 °C. Altitude and airspeed units include feet, meters, knots, and
kilometers per hour. In addition to these predefined units, four user-defined units are
programmable.
Communications Interface: The DPC includes standard RS-232 serial and IEEE-488 interfaces.
The user’s computer communicates with the DPC through the Standard Commands for
Programmable Instruments (SCPI) protocol. The DPC can also be configured to accept existing
software written for the Ruska Series 6000 Digital Pressure Gauge/Controller.
1.4 STANDARD EQUIPMENT & OPTIONS
A standard DPC includes this manual, a power cord, and a small tools kit. Although the standard
DPC is fully functional with just these items and the appropriate pressure and vacuum supplies,
the following options are also available.
INTRODUCTION 1-2

Rack Mount Kit: This 6.969" kit meets ANSI/EIA requirements for a 4U, 19" rack mount kit.
Memory Card: The DPC accepts a credit-card sized memory card through the front panel. This
allows the user to move test sequences from machine to machine and to easily upgrade software.
Additional Power Cords: Additional power cords are available for most countries.
All options are summarized in Table 1-1. To order these items, please contact Ruska Instrument
Sales in the U.S. at (713) 975-0547.
TABLE 1-1
OPTIONS LIST FOR THE MODEL 7010 DPC
Option Ruska Part Number (RIC #)
Opto 22 Kit Based on application
LabView Driver (National Instruments) 7000-LABDRV
Rack Mount Kit - Cabinets 18-24 inches deep 7000-903
Rack Mount Kit - Cabinets 24-30 inches deep 7000-904
Memory Card 35-403
Vacuum Pump - 139 L/min
115 VAC 50/60 Hz
230 VAC 50/60 Hz
Vacuum Pump - 69 L/min
115 VAC 50/60 Hz
230 VAC 50/60 Hz
99876-900
99876-960
99875-900
99875-960
Power Cord - USA, Canada, Central Europe 16-81, 16-81, 16-86
Power Cord - India, Japan, Israel 16-96, 16-93, 16-97
Power Cord - Australia/New Zealand 16-95
Battery, Processor, Spare 4-720
Battery, Memory Card 4-715
Test Port Isolation Kit, 110 VAC 7000-8101
Test Port Isolation Kit, 220 VAC 7000-8201
1Test port isolation kits are only required for DPCs from 501-2500 psi.
INTRODUCTION
1-3

THIS PAGE LEFT INTENTIONALLY BLANK
INTRODUCTION 1-4

SECTION 2.0
THEORY OF OPERATION
2.1 INTRODUCTION
The DPC's power supply, electronics, pneumatics, and sensor combine to form a complete, stand-
alone, measure and control instrument. This section of the manual describes the DPC's
component modules (Figure 2-1) and provides a general discussion of each.
FIGURE 2–1
DPC BLOCK DIAGRAM
2.2 POWER SUPPLY
The DPC's universal power supply accepts AC voltages from 90 to 260 volts at 47-63 Hz. And DC
voltages from 100 to 370 volts. This triple-output supply produces +5VDC, +12VDC, and -
12VDC, which are distributed to the Control Board.
DPC’s with ranges from 501 to 2500 psi are either 115 or 230 VAC. See Section
3.4.
H
I
G
H
P
R
E
S
S
U
R
E
THEORY OF OPERATION
2-1

2.3 ELECTRONICS MODULE
2.3.1 CONTROL BOARD
The Control Board monitors every major component of the Electronics Module. The
Microprocessor Board, the Option Board, the IEEE-488 Interface, and the optional memory cards
all plug into the Control Board. The Sensor Board and Front Panel both communicate with the
Control Board via ribbon cables.
The three voltages produced by the Power Supply are distributed to the Control Board where they
are conditioned to produce four additional voltages of +5VDC, -5VDC, +15VDC, and -15VDc
for analog use. The resulting seven DC voltages are then used either directly or indirectly
throughout the entire DPC.
Data that is subject to change after the DPC leaves the factory are held in electrically erasable,
programmable, read-only memory (EEPROM) on the Control Board. This includes the current
units of measure, the coefficients from the zeroing process, the current pressure medium,
calibration coefficients, and the conversion factors for the four user-defined units of measure.
These values are used by the Microprocessor Board as described below.
The Control Board also holds the OPTO 22 connector, which communicates with the user's OPTO
22 modules through a cable that connects to the back panel.
2.3.2 MICROPROCESSOR BOARD
All of the DPC's software resides in nonvolatile, programmable, read-only memory (Flash EPROM)
on the Microprocessor Board, which plugs directly into the Control Board. This software contains
all of the instructions that operate the DPC, as well as the conversion factors that the DPC uses to
translate the detected pressure into the units selected by the user. These factors are given in
Table 2-1.
When the DPC powers up, its software is loaded into random access memory (RAM), also on the
Microprocessor Board. At the same time, the values stored in EEPROM on the Control Board are
restored to memory.
Another important component on the Microprocessor Board is the lithium battery. The battery
continuously updates the DPC's date and time, even when the unit is powered down.
The Microprocessor Board also supports the RS-232 serial interface that allows the user's
computer to communicate with the DPC.
THEORY OF OPERATION 2-2

TABLE 2–1
CONVERSION FACTORS
Unless specified otherwise, conversion factors are based on ANSI 268–1982.
Symbol Description Conversion Factor
inHg inches of mercury (0 °C) = kPa x 0.2952998
inHg inches of mercury (60 °F) = kPa x 0.296134
kPa kiloPascals = kPa x 1.0
bar bars = kPa x 0.01
psi pounds per square inch = kPa x 0.1450377
cmH20 centimeters of water (4 °C) = kPa x 10.19744
inH20 inches of water (4 °C) = kPa x 4.014742
kg/cm2kilograms per square centimeter = kPa x 0.0101972
mmHg millimeters of mercury (0 °C) = kPa x 7.500605
cmHg centimeters of mercury (0 °C) = kPa x 0.7500605
knots indicated airspeed per NASA TN D–822
km/hr kilometers per hour = knots x 1.852
feet feet of altitude per MIL–STD–859A
meters meters of altitude per MIL–STD–859A
user1 user defined = kPa x user defined
user2 user defined = kPa x user defined
Pa user defined (Pascals) = kPa x 1000.0
hPa user defined (hectoPascals) = kPa x 10.0
%FS percent of full scale
2.3.3 OPTION BOARD
Future models of the DPC may include an Option Board that plugs directly into the Control
Board. In the future, this board could be used to provide nonstandard options.
2.3.4 IEEE–488 INTERFACE
The DPC's IEEE-488 (GPIB) interface card, which plugs directly into the Control Board, provides
the DPC with an IEEE-488 interface. This interface allows the user to automate the measurement
and control processes.
2.3.5 FRONT PANEL
The Microprocessor Board and Control Board work together to interpret all input from the Front
Panel. The Front Panel contains the vacuum fluorescent display and rubberized keys used to
operate the DPC.
The DPC also accepts an optional memory card that slides through a slot in the Front Panel and
plugs directly into the Control Board.
THEORY OF OPERATION
2-3

2.4 PNEUMATICS MODULE
The DPC's Pneumatics Module varies depending on whether the DPC is a Gauge mode,
Differential mode, or an Absolute mode instrument. Differential mode DPCs reference their
measurements to pressures between vacuum and 15 psi inclusive, whereas Absolute mode DPC
measurements are made with respect to vacuum. Thus, a Differential mode DPC can operate as
an Absolute mode instrument if the user selects vacuum as the reference pressure. Similarly, a
Differential mode DPC can operate as a gauge instrument if ambient is used as the reference
pressure.
For the user, the only difference between the Differential mode and Absolute mode instruments
occurs on the DPC's back panel. On Differential mode instruments, there is a functioning
reference port, whereas on Absolute mode DPCs, no connection is made to this port.
The valves, filters, transducers, and regulators that make-up the pneumatics module of a
Differential mode PC are shown in Figure 2-2A. The schematic for the Absolute mode DPC is
shown in Figure 2-2B. The schematic for high pressure DPCs is shown in Figure 2-2C.
In the sections that follow, components SV01 through SV06 are all 12-volt, DC solenoid valves
that are either open or closed depending on the DPC's operational mode. Their behavior is
summarized in Table 2-2.
DPCs with ranges from 501 to 2500 psi have solenoids that operate on
115 or 230 VAC.
Components RG01 and RG02 are low pressure regulators. Component SRV01 is a three-port,
DC servo valve, with one supply port, one exhaust port, and one output port. RV01 through RV04
are relief valves. See Figures 2-2A and 2-2C.
H
I
G
H
P
R
E
S
S
U
R
E
FIGURE 2–2A
MODEL 7010 DPC DIFFERENTIAL PNEUMATICS DIAGRAM
THEORY OF OPERATION 2-4

FIGURE 2–2B
MODEL 7010 DPC ABSOLUTE PNEUMATICS DIAGRAM
FIGURE 2–2C
MODEL 7010 DPC HIGH PRESSURE PNEUMATICS DIAGRAM
THEORY OF OPERATION
2-5
Table of contents
Other Ruska Instrument Controllers manuals
Popular Controllers manuals by other brands

Heatcraft Refrigeration Products
Heatcraft Refrigeration Products H-IM-79B Installation & operation manual
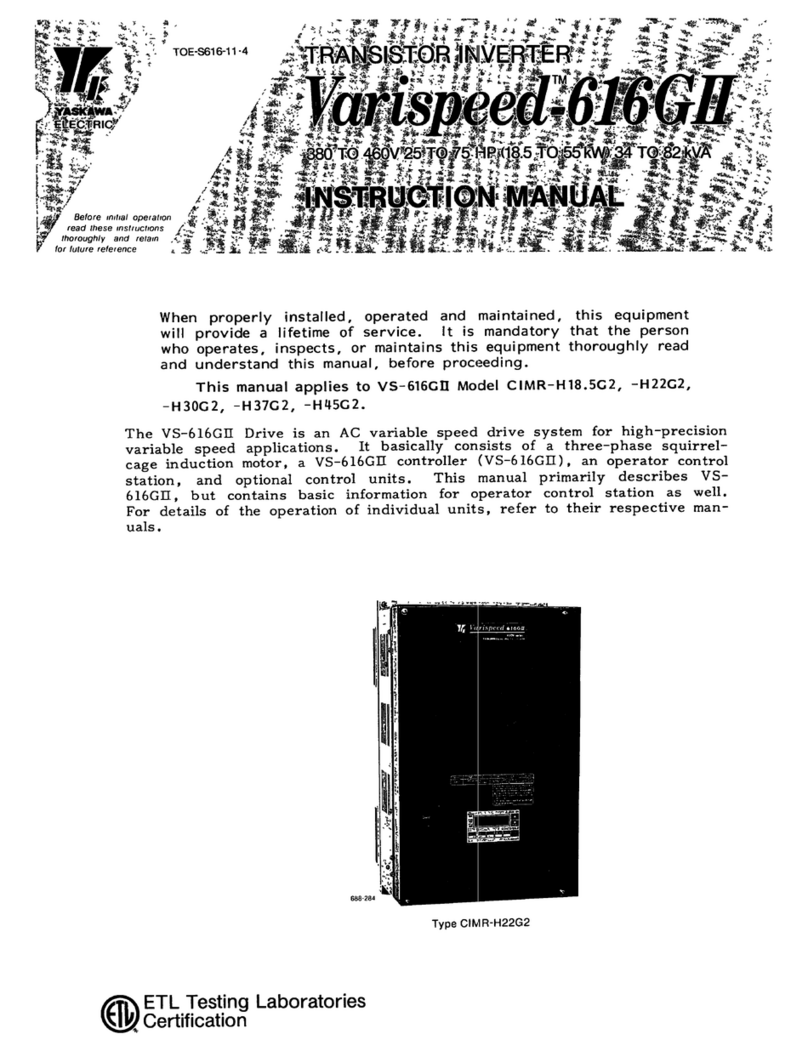
YASKAWA
YASKAWA Varispeed-616GII instruction manual
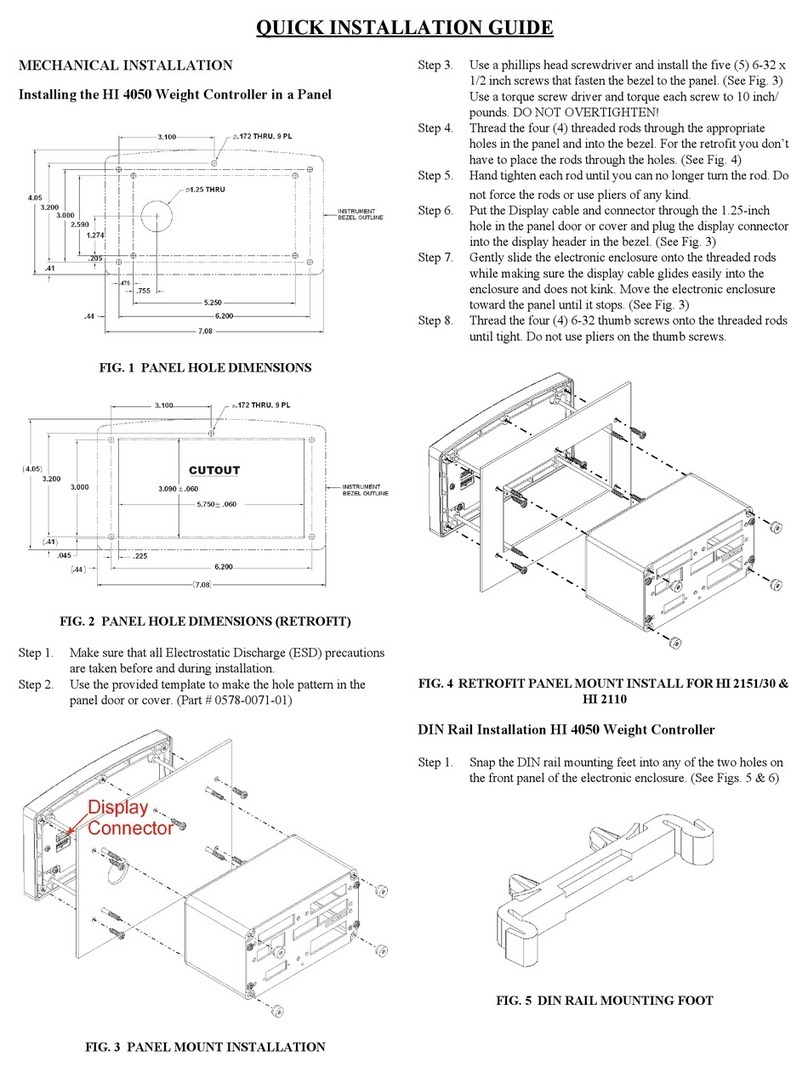
Hardy Process Solutions
Hardy Process Solutions HI 4050 Quick installation guide
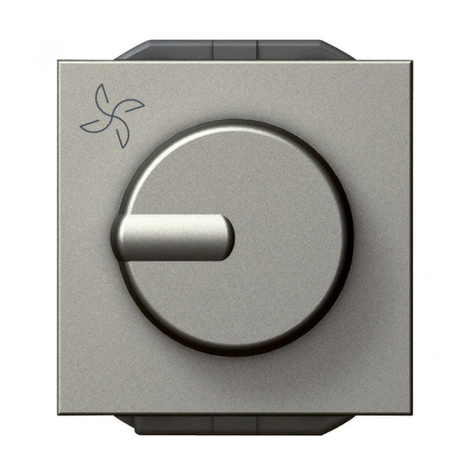
LEGRAND
LEGRAND Arteor quick start guide
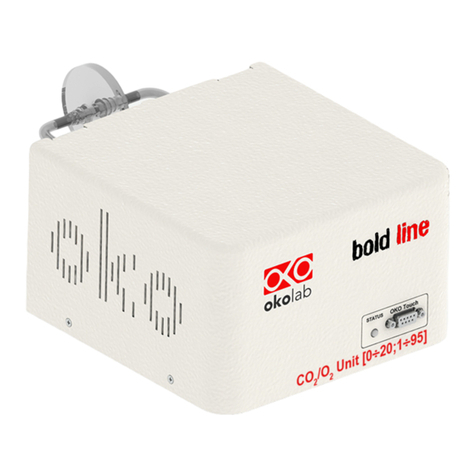
Okolab
Okolab CO2-O2-UNIT-BL manual
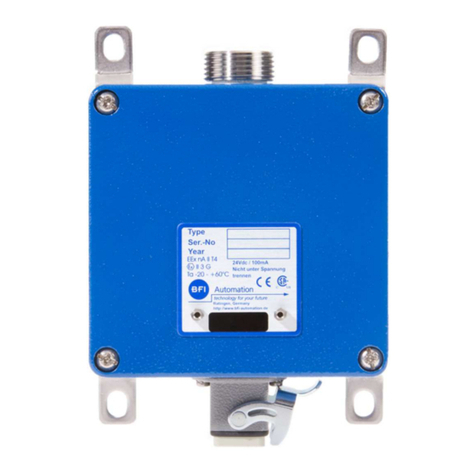
BFI Automation
BFI Automation CFC 1000L Original operating instructions