Sachs SA 2-440 Setup guide

(SJ
SACHS
Repair Instructions No.4072.8 E
SACHS
SA
2-440
Snowmobile Engine
Edition December
1970
FICHTEL
&
SACHS
AG
.
D-8720
SCHWEINFURT


CONTENTS
Introduction
In
stallation
dimensions
Te
chnical
deta
R
epoi
r tools
end
ossembly
i
ig
Di
smontling the engine
Work
on
ind
ivi
dual
components
Replocing
crankshaft
beorings
Reploci
ng
fan shoft
beor
ings
Receil
starter
. . . . . . . .
Mogneto
generator
Poge
2
(fold
-
out
poge)
(fold-out page)
4
6
Replocing ignition
ceils
end
ignition
lead
s with
spark
plug
terminals
Replocing
the
flonged
hub,
the
mogneto
fl
yw
heel
ond
the
cam
10
12
12
15
16
17
18
22
23
27
32
33
35
Corburettor
. . . . . . . . . . . . . . . . . . . . . . . . . . .
Decorbonizing
the
exhaust
muffler,
the
cylinders
ond
the
cylinder
heads
Assembling
the
engine
. . . . . . . . . . . . . _
Ignition
ti
ming
........
.....
.
...
.
Engine with BaSCH Bendix.
pinion
type
electric
starter
(type DG)
Operation,
mointenance
ond
lubricotion
of
the
electric
storter
Storter
Fa
ults . . . . . . . . . . . . . . . . . . . . . . .
In
structions
end
wiring
diegram
for
magneto
generator
12
V
40
W
ond
12 V 75 W
36
Instructions
ond
wiring
diogram
for
mogneto
generator
12 V
75
W
end
BOSCH Bendix-pinion
type
electric
starter
(type DG)
38
Test-running
end
running-in
period
loying
up
the
engine
..
_
...
lubricotion
ond
moi
ntenonce
chert
Tightening
torques
for bolts
ond
nuts
Trouble-s
hooting
chart
. . .
...
.
40
41
42
43
44

INTRODUCTION
This manual is designed to
give
dealers and
their
staff
all
guidance and information necessary
to
enable them to
pro-
vide
and efficient
repair
and maintenance service, but
it
is in
no way intended as a substitute
for
the
practical and theo-
retical training available to personneI
at
our
Service
Training
School.
It will be found useful as a ready reference in
day-to-day
workshop
practice.
Gur
illustrated Spare Parts List, which shows the
various
components in detail, will also be found helpful when used in
conjunction with
this
booklet.
Naturally
, good maintenance and
repair
work
and
efficient
servicing call
for
good
equipment, a
we
ll-equipped
workshop
and skilied personnel.
Dealers are requested to make this manual and all
SACHS
Service Bulletins, which contain technical
modifications
,
available to
every
individual
responsible
for
actual
servicing
.
The
proper
place
for
this
kind
of
technical
infor-
matio
l1'
,
is
in
the
workshop
and
not
in
the
filing
cabinet.
We hope that this manual will be
of
real practical assistance
to all
our
dealers, agents and associates.
FICHTEL
&
SACHS
AG
0-8720
SCHWEINFURT
Service Department

><
~
z
cn
-I
>
r
r
>
-I
0
I><
Z
c
3:
l'T1
Z
cn
0
z
cn
~F
e-
'
.
:~
, '
F'1
~~
~
,", ,
_L
(:
't:;
"
>:.l!
--
,
~l
I
f
:~
-
'If
~
x
~
.
.
,
ö ..
~
~
>i
------
-----
'"
''''

TECHNICAL
DATA
f'SiMP)
..
'"
"
"
,~
"-
,
-
glP5h
,
..
'"
..
,
W,
..
,
''',
-
5000
,~
~
4000
...
,
,
~OOO
""
U/minl.pm)
It
,
lb
M
'"
~
"
•
'""
1000
V/m'"
(.pm)
(b/HPh
'.'
..,
...
U
..
.,
....
,,,
.
U/mi"
(r
p
",j
I
.....
,,,ted po"'.'
OIItp
..t
opplie.
10
" fully
/un·'"
I"
gine ond
;.
mtO'ured
01
11
boro-
....tri< pr
."u,.
01
b"
_
760
mm
HiI
on<!
"I
on
oi.
temperatur.
of
'L
_
2O'C
(68'FI,
...ilh " toleron
ee
01
± S.,..
Fot date.minin" Ihe
pow"
output
o,cordin
g
1o
Ge.mon Stondord
DIN
6270
(b
o
..
736
mm
Hg
ond
'l
= 2O'C),
Ihe
IlbovI outp"t
h,"lo
b.
multiplied by
Ihe
<orr.er
io
..
10"0.
0
.97.
In
'he
in
'
".u
01
ledoni,ol
p.ogr
...
""1
r•
••
rv.
,h,
r'''"
'1o
in
trod
...
ce
modilicoti
onl
wilhout
noti'
l.

Technical
data
Type:
Tw
o-cylinder Iwo-cycle
gosoline
engine
Cooling : Fon-Iype oir coolil1g
---
Direclion of rololion Anliclockwise (seen on cronkshofl p. I. o. side)
of
engine
:
Copocily:
43
7 ce (
26
.
646
cu. in
.)
Bore :
(/)
67.5 mm (2.
657
in
.)
---
Strake:
61
mm
(2.402 in
.)
Compression
ratio
: 9.3 10 1
---
Oulput:
35
HP
(OIN)
01
6500
rpm
Cronkshoft beo rings : 4 onli-friclion
beoring
s
Eng
ine lubricotion :
Oil.in.gasoline
lubri
cotion
,
goso
li
ne
/oil
ratio
25
: 1
Ignition : BOSCH
mognelo
generolor
12
V
75
W or 40 W
---
Ignition timi
ng:
Siopped
engine
:
Runn
ing
engine
: 0.25...0.
30
mm
bef
ore
TD
C
!O
.
0098
...0.0118 in'l
3.
50
...4
.00
mm
before
TDC
0.
1378
...0.
1575
in
.
--
Contocl
breoker
gop
: 0.4 ± 0.
05
mm
(0.0
16
± 0
.002
in
.)
Pole shoe
gop
:
Siopped
engine:
Running engin
e:
25
...
29
mm
\0.
9843
...1.1417
in
'l
7...
11
mm
0.2756...
0.4331
in
.
---
Spork plug: BOSCH
W260T2
orW240
T 1
(see note on
poge
24)
Corburetlor
:
TlllOTSON
diophrogm
corburellor
HO
131'
/1-
(0 38.10
mm
)
Corb
urellor
sett
ina . Moin jel: 1'1. lurns
open
Idl
ing jet: 1 lurn
open
Air inlok
e:
via 1 inloke stock
--
Recoil slor
ler
Storling m
elhod
,
on
request BOSCH Bendix-pinion type
electr
ic
stor
l
er
12 V - 0.4
HP
(necessory
bollery
12
V 32...
38
Ah
)
bhoust
pipe: Exhousl moni
fo
ld (F & S
pari
no.
3673
003
001)
ond
in
lerm
ediole
pipe
42
mm
(1.654
in
.)
L C.,
lenglh
150
mm
(5.906 in.)
(n
ol
supplie
d by F & S)
Exhousl muffler : (F & S Swirl type
part
no
. 1473019001) I
3

REPAIR
TOOLS AND ASSEMBLY
JIG
n
~
~
11
,8
Ä
~
1
7,8
2
~17.9
4
3
tj
7
5
6
~
~
10
8 9
~
11
13
21
~
14
16
r:ri
C1i
18
12
15
17
4

IlIuslr. Porl No.
No
.
1 0276065
101
2
0977
069
000
3 0977
068
000
4 3676004001
5 3676005000
6 3676002000
7
0976
111
100
8 0276035100
9 1476018000
10
0276170000
11
0276175000
12
14
76013000
1476011000
1440027001
14
760
120
00
13
1447009000
14
1476014025
15
1476014000
16
144701 0
000
17 1476015000
18
0276081000
19
0276082000
20
0276085005
21
0977
041
000
I Denominat
io
n
Repair
.oolt
Gudgeon pin extroclor
In
ser
t for gudgeon pin extroctor
locoti
ng
pin for piston
WithdrowoJ
1001
Fitting tool for flonged hub
Retaining fork
Retoining lever
Ignition timing gauge
Adju
sting
pin for flyweight
Torque wrench
Revolution counter
Extroctor sleeve
ossy.
H
ex
head bolt . replocement ports
Threoded sleeve f
Thrust
beoring for
1476
013 000
Clomping ring,
58
mm
I.
D.
Extroctor
she
ll
s for cylindricol
roller beoring inner roce NJ 206 E C3
NA
Extroctor
shells
for bearing
bush
(recoil starter)
Clompi
ng
ring,
75
mm
I.
D.
Extractor sh
ells
for
deep
groove ball bearing
6305
N
C3
Ass.mbly jig
Clomping ba
se
Swivel unit
Clamping ball
Assemb
ly brocket
5

DISMANTLING
THE ENGINE
Detach
all
contral
cables
between
engine
ond
frame
.
$crew
off
cover
(wit
h inscriptio n SACHS).
Pul1
ignition
leads
with
rubber
boots
out
of
the
recesses
ond
remove
cover.
Disconnect
electrical
wir
ing
bet
wee
n
engi
ne
end
frame
cf
the
terminals
(2
end
3,
F
ig.42).
Remove
exhaust
muffler,
exhoust
tube
end
manifold
.
Remove
the
engine
end
clean
it
thoroughly
be
fore
toking
it
aport.
When
giving
the
engine
0
general
overhaul,
components
should
be
dismounted
in
the
seque
nce
ind
icated
.
f ig. l
Fig. 2
6
I"take stack,
ca
r
bu
rettor
and recoil starter
Fig. l
Mount
en
gine
on
asse
mbly
i
i~
(repair
t
ools
no. 18, 19, 20 ond 21)
with 2 hex
head
bolts M
'0
x
30
,
os
shown
in
the
i
ll
ustration
.
Sc
rew
off
in
toke
stack
(5)
with
rei
nforcement
ring
(4)
.
Pull
off
impulse
pi
pe
(2)
.
Remove
carburettor
(3)
(ta king
co
re
of
insulating sl
eeves
a nd
go,ket).
Unscrew
rec
oi l
starte
r
(1)
to-
gether
with
in
ser
ted
l
aby
rinth
ring.
V-pulle
ys
and V-belt
Fig. 2
Use retoining
fork
\3,
repoir
too
l
no
. 6)
to
ho
ld
the
id
er
pulley ha lf
(l),
os
shown
in
the
illust
ratio
n.
Unscrew
nut
and
remove
idle
r
pulley
half
(taking
ca
re
of
wosh-
ers).
Un
s
crew
pulley
(4)
and
remo
ve
it
together
with
V-belt
(5).
Remo
ve
secand
idler
pulle
y
half
tog
e
ther
with
washers.
Remove
Woodruff
key from
fan
shaft
(2).

Magneto
flywh
ee
l
F
ig
. 3
Use
retaining
lever
(3,
repo;r
tao
I
no
.
7)
10
hold
magneto
flywheel,
os
shown
in
Ihe
illustration,
end
unscrew
nut
(2).
Remove
washer
(1)
.
Fig. 4
Reposition
retaining
lever,
os
shown
in
the illustration,
end
re·
move mogneto Ilywheel
(2)
by
means
cf
withdrowol
tao
I (1, re-
pair
tao
I no. 4
).
Remo
ve
Woodruff
key
from
crankpin
.
Fan housing, fan
end
armature
plote
F
ig
. 5
Unscrew
fan
housing
(2)
end
take
out
Ion
(1)
(sliding lit).
Detoch
leads
fram
ormoture
plote
(3)
ot
the
terminals
ond
uns
crew
ormature
plote
.
Fig. 4
Fig
. S
7

F
ig
. 6
Fi
g.7
Fi
g.8
8
Cylinder cover halves
and
upper
part
of
intake manifold
Fig
. 6
Unscrew self-Iocking nut (1,
Fig
.
41)
end
threoded
pin.
Unscrew 4 serews
(1)
ond
remove
eylinder cover hclves intoke ond
exhaust
side
(2
ond
3
).
Unscrew
upper
port
of
inloke
monifold.
Lower
part
of
intake
manifold
F
ig.7
Unloek nuts (1), unscrew lower
port of intoke monifold
(2)
and
remove both gaskets.
Exhaust tubes, cylinder
heads
and
cylinders
Fi
g.8
Unscrew exhoust tubes
(1)
with
on
ordinory
strap
wrench, only
if
neee
ss
ory.
Un
serew eylinder
heeds
(3)
end
remove eylinder heod geskets.
AHention
Mark
ey
linder
ond
piston (power
lakeoff
side)
tagether.
Remove eylinders
(2)
end
eylinder
flonge
gasket
s.
Note
:
The Alu-Chromel cylinders eon-
not
be
rebored
.
eylinders
end
pistons
are
divid-
ed
info tol
erance
groups A, B
and
C.
M
ount
only pistons
and
eylinders
which belong 10 the
same
toler
-
enee
group.
The eylinders
are
morked with
eorresponding letters
(A,
B
or
Cl
01
Ih
e uppermosl eooling fin. In
toleronee
group
A pistons with-
out rings
end
gudgeon
pins
are
ovailable
separately
(see
spore
parts
l
ist)
,

Pistons
and
ne
edle
bearing
s
Fig. 9
Piece piston
on
home-mode
slol-
led
wooden
board
(41.
Cover the cronkcose,
toke
out
wire circlips.
If
necessory, force
out
gudgeon
pin with
gudgeon
pin extroctor
(3,
repair
tao
I no. 1)
ond
insert
(2,
repOlr
tao
I
no
.
2).
When
fitting the steel bond,
make sure
thot
the piston rings
ore
in
their
grooves
. (Donger of
breoking piston rings.)
Remove ,slotted
wooden
board
.
Remave
needle
bearing
(1)
and
mark
it
taget
her
with
the
cor- F
ig
. 9
responding connecting rod eye.
Note
:
When
replocing
needle
bearings,
wolch toleronce mark
on
con-
necting rads (see
spore
pari
s
lisll·
Unscrew crankcose from as-
sembly jig.
Crankcase
and
crankshaft
Fig
.
10
Unscrew
Ihreaded
nipple
(11
ond
screw plug
(21.
Unscrew 12 nuts from lower
part
of crankcose.
Split crank.case by slightly top- Fig.
10
ping with 0
rubber
mallet.
F
ig.1
1
Remove
ai
l seals
(1
and
3), take
out
cronkshaft (4) both locking
disc halves (
1,
Fi~
.
321
ond
bolh
cylindricol pins
(2).
Fig.
11
Clean
oll ports thorough
ly,
check for
weor
and
reploce
if
necessory.
F&
S40U
'
1I
When
giving the
engine
a
general
overhoul oll sealing elements should be reploced.
Use
only
genuine
SACHS
spare parts.
9

WORK
ON
INDIVIDUAL
COMPONENTS
Replacing
crankshaft
bearings
Of
Ihe cronkshoft
beorings
only Ihe
deep
groo
ve ball
beoring
on Ihe
mogneto
side
end
Ihe cylindrical roller
bearing
on the
power
tokeoff s
ide
can
be
replaced
.
Removal
cf
inner roc
es
cf
cylindricol roller
bearings
end
deep
gr
oove
ball
bearing
s.
--4
Fe
S
4072:
27
F
ig
.
12
Remove
outer race
(4)
cf
cylindricol roller bearing end roller eoge from inner
roc::e
(
1)
01
beoring
.
Remove
inner
race
(1)
of
cylindricol roll
er
bearing
ond
the
deep
groove
ball
bear
ing
(7)
by
meons
of
suitable
edrector
shells (5
end
6),
clamping
rings
(2)
ond
extroctor
sleeve
(3
,
repoir
tools no. 12, 13, 14, 15, 16
ond
1
7)
.
Remove shims
{Bl
.
A"ention
If
shims
have
been
domoged
dur
ing the
operation
cf
removing
Ih
e i
nn
er
race
of
Ihe
cylindricol roller
bearing
,
reploce
Ihem by
new
ones
.
10

Measurin9
.he
axial
play
of
.he
cra
nks
haf.
Permissib
le
a
xi
al
ploy 0.3...0.6
mm
(0.0118...0.0236 in.)
Fig. 13 Fig.
14
Fig.13
Before meosuri ng,
clean
the
g
roove
s
for
the
locking disc halves
in
the
upper
po
rt
of
the
crankcose
.
In
sert
locking d
is
c halves
(1)
into
upper
port
of
cronkcose
.
Example:
Upper
port
of
cronkcose:
Distonce
between
the two locking disc halves
Fig.
14
Fitting d imension
of
cronkshaft
:
Dimension
of
crankshaft
fram
deep
groove
ball
bearing
seat
to cylindrical
roller
bearing
seat
Widlh
01
ball
bearing
Width
of
roller
bearing
Distance
in
upper
port
of
cronkcose
Fitting dimension
of
cronkshoft
Existing axial
ploy
Perm
issi
ble aXial
play
Difference
to
be
compensoted
209.4
mm
175
.5
mm
+ 17.0
mm
+ 16.0
mm
208.5
mm
209.4
mm
-208.5
mm
0.
9mm
0.
5mm
OAmm
8.2441
in
.
6.9095
in
.
0.6693
in
.
0.6299
in
.
8.2087
in
.
8.
2441
in
.
8.2087
in
.
0.0354 in.
0.0197
in
.
0.0157
in.
The
difference
of
0.4
mm
is
compensated
by
inserting shims
(8,
Fig. 12)
on
.he
crankp
in
p. t. o.
side
. The shims
are
to
be
placed
directly
below
the
inner
roce
of
the cylindrical
roller
bearing.
Fitting
the
deep
9roove
ball
bearing
and
the
inner
race
of
the
cylindrical roller
beari
ng.
H
eot
deep
9roove
ball
bearing
(wilh
0-rin9
removed)
ond
i
nner
roce
of
roller
bearing
10
aboul
70...80 'e (158...176 'F).
Slip d
eep
9roove
ball
bearing
on
cronkp
in
mogneto
side
unlil a
stop
is
reached
(0 -
ring
9roo
ve
po
i
nt
ing
towards
cronkweb).
In
sert
shims
(8
, Fig. 12) on
crankpin
p. t.
o.
side
and
fit
inner
ro
ce
of
cylindrical roller
beoring
unlil
it
reache
s 0 s
fop
(collor
facing
towards
cronkweb).
After the
bearing
has
cooled
off
, press
inner
roces
completely
into
the
ir seafs.
During this
operation
, a suitable pie
ce
of
material
should
be
ploced
between
the
cronkwebs. This
piece
must
be
lorge e
nough
10
be
supported
ct
bolh ends
so
thot
the
crcnkshaft
con lie freely in position.
11

Never
clamp
the
crankshoft
in
0 vise
ol:a
cronkpin
or
of
the
webs,
ond
never
Iry
10
fit
the
inner
roces
by
hommering
. This will crush
the
webs
end
render
the
cronkshoft
unserviceoble
. •
Piece
auter
race
cf
cylindricol
roller
bearing
with
roller
cage
onlo
the
i
nner
ra
ce
(groove
for
O-rin~
facing
towords
cronkweb)
.
Wel
O-rings
(5
, Fig.
11
) slightly with oil
end
insert
them
i
nto
the
auter
roces
of
the
bearings
.
~eplacing
fan
shaft
bearings
. F
ig
.
15
Removal
F
ig
.
1S
There
is
0 lock
ri
n9
between
baln
bearings
in
the
fon
housing.
Deep
groove
boll
bearings
can
only
be
remo
v.
ed
towords
the
side
from which they nove
been
fitted.
Heat
fon housing (
1)
10
cbaut
100
...
150'(
(2
12...
302'F)
end
take
out
balh
deep
groove
ball
beerings
by slightlY knocking
the
housing
ogoinst
0
wooden
sup·
port
.
Take
core
of
w
osher
be·
tween
the
beorings
.
Note:
't
' Remove lock ring
in
bearing
seat
o
nl
y if
necessary
.
)Mtallation . .
:. F-
i11
deep
gtöove
ball
bearing
half
with"hi
gh
temperature
bearing
grease
. Take
car
e
.
when
instolling thot
the
encosed
sides
\Ji!P
pointing
towords
the
outside
.
~
\ \
"'"
Force first
deep
groove
ball
bearin
.g into
the
warm
houslng
onJite
cylinder
side
until
a
stop
is
reoched
(in
doing
so,
exert
press
ure
on
the
outer
race
of
the
bearing).
In
s
ert
fan
shaft
and
fit
washer
(2
~
mm = 0.0787 in. thick)
:-
.,
F
orce
in
s
econd
deep
groove
ball
beoring
until 0
stop
••s
reac~ed
(in
doing
so,
ex
erl
pressure
on
the
outer
roce
of
the
beoring
).
Recoil
starter
Fig.
16
12
Dismantling
...
F
ig
.
16
,
Take
out
laby
~i
nth
ring
(1)
.
•
,~e~
out
brake
s
pr
ing
(2).
s
him,
.
7
s'p
flng ring, fricti
on
plate
(3),
/ /
woshe
r
(0.1
~
0.0039
in
. thick)
",
and
starter
pawls
(4
and
5)
.
""s
«171
:J1

Fig. 17
Pull
out
sterter
ro
pe
opprox
.
50
cm
(19
in.1
ond
hold
pulley
(11
with
horne-mode
retaining
clip
(2)
,
os
show"
in
the
illustration.
Take
clamping
ring
(6)
with
clomping
taper
out
of
starter
hondle
{51
.
Withdraw
clomping
taper
(7)
from
clomping
ring
end
detoch
rope
.
Remove
clomping
ring
end
star-
ter
handle
with
Hanged
sleeve
(SI
,
,top
(4)
ond
f10nged
sleeve
(9)
from
rope
.
Remove
retoining
clip
ond
let
starter
rope
run
back
completely.
Remove
ro
pe
guide
(3)
on
ly
if
necessory.
Carefully
toke
out
pulley
with
coil
spring
,
toking
care
not
10
let
coil
spring
jump
out
.
Toke
core
of
disc
{3,
Fig. 19
1.
Remave
rope
from
pulley
.
Fig.18
Re
i
se
spring
end
10
toke
out
coil
spring.
Hold
coil
spring
firmly
with
both
thumbs
(see
illustrotion)
end,
by
roising
eoch
thumb,
let
out
spring
o~
oltl!ro.0te sides.
Note
;
Replece
bush
(1
, Fig.
201
only
if
necessary
, using the
extroctor
shells,
clamp
i
n~
ring
and
ex-
tractor sleeve
(repair
tools no.
15
,13
ond
121
.
Take
ca
re
of
toleronce
ring
in
bush
{I
, Fig.
201
.
Assembly
Fig
.19
B
efore
assembling,
grease
spring
with
Aero-SHEll-Grease
14
and
fi
l/
the
4 lubricating
grooves
in
the pul/ey with
~he
.same lubri-
cont
.
In
s
ert
co
il s
pr
i
ng
, os
sh
ow
n
in
illustration, with
end
of
sprin~
(2)
in
stud
(1)
, fitting
co
il by co.!
in
anti-clockwi
se
direction.
Ensure
that
the ccil spring lies
flat
ond
even.
FI54
11
11
'32
Fi
g.
17
f 1!o4071;
lI
F
ig
.
19

F
ig
.
20
r&5""012
,
)",,
Fig.
21
F
'~40
72'
JI
F
ig.22
Fig.20
Before inserting pulley, stick
wasller
(3,
Fig
. 19, 0.8
mm
thick
= 0.032
in.)
with 0 little
grease
into recess
of
pulley.
Fit
pulley
onto
bearing
pin
ond
insert
end
of
spring
(4,
Fig
.
19
)
ot
stud
(2
).
Tension pulley/coil spring
in
storting direction until 0 s
top
is
encountered.
Release coil s
pring
appr
ox.
112
•.•
1 turn until tlle recess for the sol·
dered
nipple
in
the pulley rests
near
the
rope
passage
of the
housing.
Hold pulley with
home-made
retoining
clIP
(2,
Fig.
21)
.
Pull
the
starter
r
ope
through
a
rag
moistened with
SAE
10 oil be-
fore
assemb
ling.
Fig.
21
Fit
rope
guide
(3,
if
remove
d)
,
lIonged
sleeve(B),stop (4),lIonged
sleeve
(7),
starter
handle
(5)
ond
clamping
ring
(6
)
onto
Ihe
rope
.
(Iamp
rope
guide
with
filI
ister
heod
cop
screw
(9)
M 4 x
10
.
lay
starter
rope
around
clomp-
ing
taper
and
pull
it
into
clamp
-
ing ring.
Pull
clamping ring into s
tarter
handle
and
let
sta
rter
rope
run
back.
Fig.22
lubricate
starter
pawl
bed
and
star
te
r powls ligMly with
SAE
10
oil.
~
Fit
star
ter
powls
(4
ond
5)
.
Th
e
open
side
of
the
starter
pawl
seating
and
the long side
of
the
s
tarter
pawl face
in
storting di-
rection.
F
it
was
her 0.1
mm
(0
.0039
in
.)
thick, friction
plote
(3),
spring
ring and shims os required.
Insert
broke
ring
(2)
.
Insert labyrinth ring
(1)
.
After
"'ounting
the
bra
ke
spr
ing, the friction
plate
should have
an
<llöillElil,
ay
of
0.1...0.2
mm
(0.0039
...0.0079
in
.).
CQ
,r
rect this play by inserting shims
under
the
broke
spring.

Magneto
generator
The cyli
nder
on
the
p. t. o. si
de
of
the
cronk
s
haft
is
r
efer
r
ed
10 os cylinder 1.
Fig.
23
1 = Sei
of
conlocl
points
I
2 =
(apacito
r
3 =
tgnition
armolure
4 = Ign
ilion
arme/ure
I
S = Sei
of
conlocl poi
nt
s
6 =
(apacitor
7 = Armolure
plole
8 = l ubricoling wiek
9 =
Generator
ormalure
10'
cylinder
2
'0'
cylinder
1
F
ig
.
23
Replacing
th
e ignition or generator armatur.
Open
up
the
strop
holding
the
armoture
which
is
to
be
re
ploc
ed
ond
unsold
er
leads
.
Screw
off
ormoture
.
Generator
ond
ignition
armeture
ore
avoiloble
os
spore
ports
. The
armoture
poles
are lothe-turned ond con be mounted 10 the armeture plote
without
special equipment.
Ploce new
ormature
in
position
, os
shown
in
the
illustration,
ond
screw it
on
Iightly
(toke
core
cf
ground
wire
on
generator
armature
J.
After
installation
it
is
necessary
under
all circums
tance
s 10
mea
sure
the
air
gap
be·
t
wee
n
armoture
p,0les
and
flywh
ee
l,
becau
se ma
xi
mum ignition
and
lighting
power
is
oblained
only
1I
Ine
gap
is
0.
25
...0.
35
mm
(0
.
0098
...0.
0138
in
.).
Note:
Far
corr
ect
meo
surement
ond
adjustment
it
is
nece
ss
ary
that
the
crankshaft
rests
cor·
rectly on ils
bearings
.
Fig.24
Air
gap
0
.25
...0
.3
5
mm
(0.
0098
...
0.
0138
in
.).
The
gap
is
m
ea
sured
in
s
everal
places
,
through
the sials
in
the
flywheel.
If
the
gap
is
not
correct,
it
can
be
slightly
odjusted
by repositioning
the
armeture
ofter
having sleck-
ened
the
fastening
screws. The
adjustment
can
be
made
through
the
apertures
in
the
fl
ywhee
l.
Fig.
24
15

Replacing
the
sets
01
eontad
points
In
order
10
cchieve
0 uniform i9nition setting
for
both
cylinder
.s
il
is
necessory
10
re·
ploce both sets
of
contoet points
together
.
The
contoet
breoker
should
be
rep
l
oced
if
the
contocts,
the
slider
or
the pivot
shoft
are
badly
wo
rn
,
if
the
beoring
bush
is
worn
cr
if
the
co
ntoet
brecker
arm
cr
the
spring
are
damoged
.
1.
Screw
off
primory
lead
end
copacitor
l
ead
.
2. Remove r
eloiner
ond
contoet
brecker
arm
from pivot
shaft
(take
care
of
shims).
3. Unscrew filiister
head
cop
s
crew
end
remo
ve
contoct
ca
rrier.
4. Unscrew pivot
shoft
from
armeture
plote.
New
parts
should
be
fitted
in
reverse
ord
er,
proceeding
os fellows :
Coulk
the
piv
ot
shoft
after
screwing
il
in
.
Use only the sets
of
contact
point
s
spec
ified
for
th.s
engine
.
When
fi
tted
in position,
the
contact
br
e
aker
points must
not
be
displaced
or
tilted.
Apply
BaSCH
Ft 1 v 8
greo
se 10
bear
ing
bu
sh
before
fitting.
Smeer
BOSCH
greose
Ft
1 v 4
on
the lubricating
pad
ond
on
the
greose
wedge
in
the
slider. (BOSCH
greose
is av
ailabl
e
in
tube
s
at
all
BaSCH
suppliers.)
Da
not
allow
any
grease
or
oil
to
reach
the
contacts
.
Replacing the
capacitor
1. Unsolder
leads
.
2.
Pu
sh
the
capacitor
out
of
the
armature
plote
with a
round
piece
of
wood
.
3. Remave the
caulked
spots
from the
hole
with a sc
rape
r.
4.
In
ser
t new
copacitor
ond
carefully caulk
agoin
.
5. Sold
er
bot
h l
eads
to their terminals.
Replacing ignition coils and ignition leads with
spark
plug terminals
Attention
Removal
F
ig.
2S
Unscrew ignition coil
(5
,
for
cy·
linder
1)
end
coil
(4
, for cylinder
2).
Remove
coble
shaes
(3
)
and
cab
le
shoes
(2)
and
un
screw
ig·
ni
tian
leads
(1)
.
Installation
~crew
!gnition l
eads
(11
to igni·
Ilon cods.
Pl
ac.
cabl.
,
ho.,
(2)
far
graund
wi
re
(brown)
on
terminal
15
and
cabl.
,hae,
(3)
f
ar
pri
mary le
ad
(
blue
)
on
terminal 1
of
the igni.
tion coils.
Scr
ew
on
ignition coils with
ground
wire using 3 filIister
head
cap
screws M 5 x
25
and
spring
w
asher
s, as shown
in
the
illustr
a·
tion.
When
replac
ing
spark
plug termina ls,
hang
spring into ignition
lead
(make s
ure
thot
the
spring
gels
in
cantael
with the
core
of the ignitio.n
lead
),
and
insert the
spr
ing
tagether
with the ignition
lead
into the
spark
plug terminal.
16
Table of contents
Other Sachs Engine manuals
Popular Engine manuals by other brands
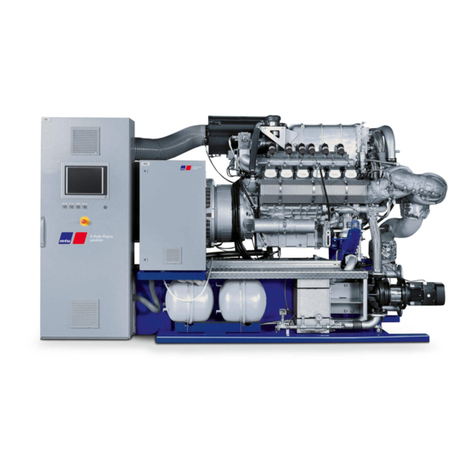
MTU
MTU 12 V 4000 M33F operating instructions
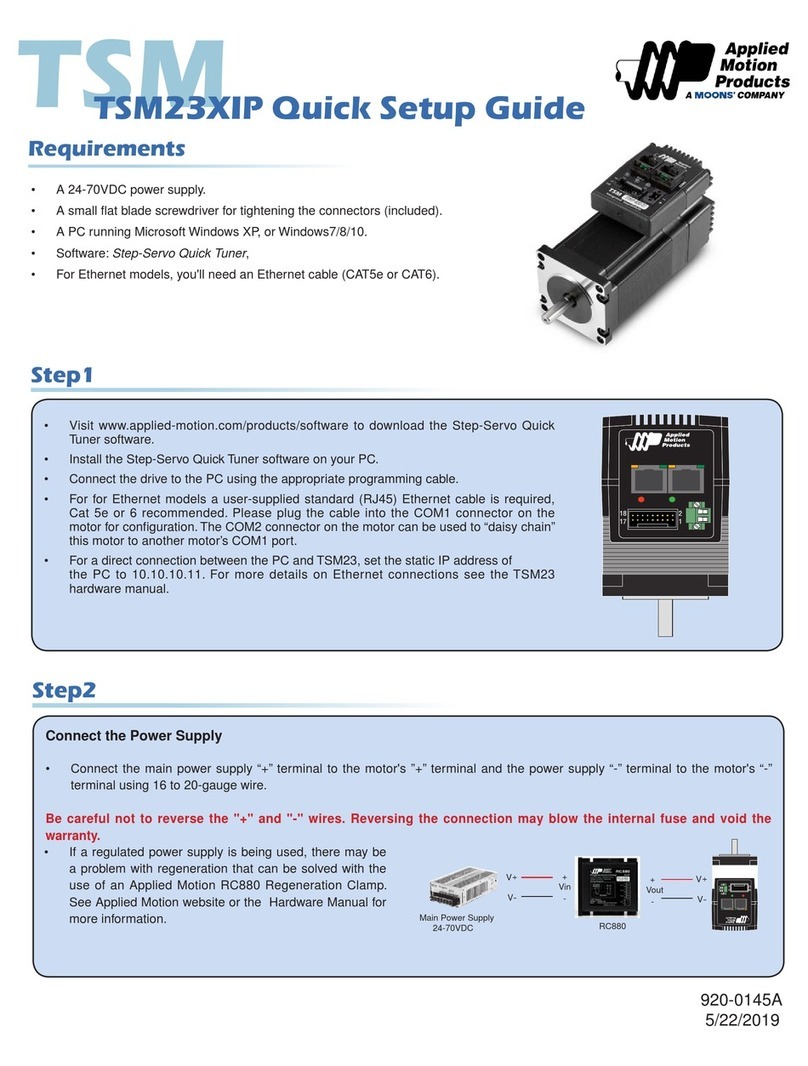
Moons'
Moons' Applied Motion Products TSM23XIP Quick setup guide

Perkins
Perkins 4016-61TRS1 Operation and maintenance manual
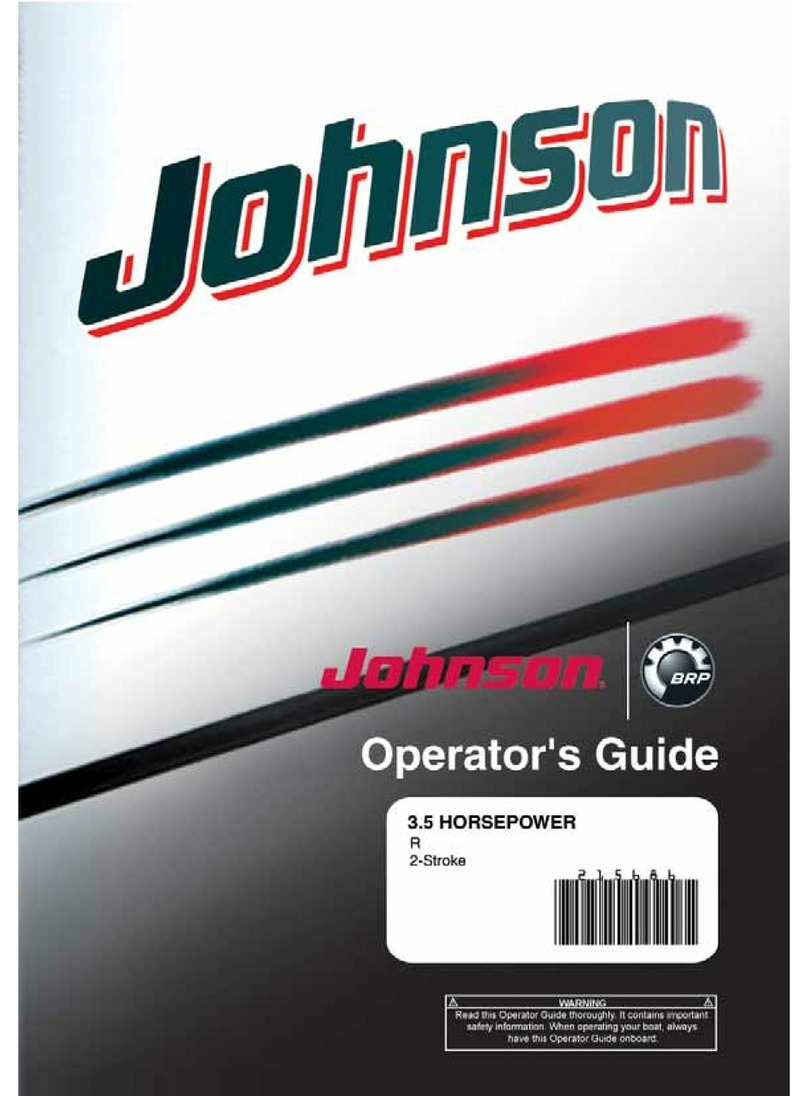
Johnson
Johnson R Operator's guide

Marine Power Solutions
Marine Power Solutions MP-4120Ti Operation manual
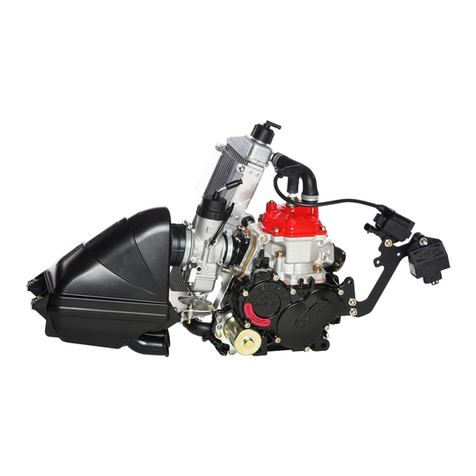
Rotax
Rotax 125 MAX evo Installation instructions and operators manual