Safe Fleet FoamPro Accumax II Fury Guide

MAX100/200-OPERATION Rev200813
1
AccuMax II Fury/Fusion
Foam Injection System
--- Vehicle Mounted & Fixed Systems ---
Document Number:
XE-MAX1PM-OPERATION-R0A
Unit
Serial
Number
All quality FoamPro products are ruggedly designed, accurately machined, carefully assembled, thoroughly inspected and tested. In order to
maintain the high quality of your unit, and to keep it in a ready condition, it is important to follow the instructions on care and operation. Proper use
and good preventive maintenance will lengthen the life of your unit. ALWAYS INCLUDE THE UNIT SERIAL NUMBER IN CORRESPONDENCE.
FoamPro • 26 Southern Blvd. • Nesconset, NY 11767 USA • 800-533-9511 • FAX 816-892-3178
MODEL MAX100
MODEL MAX200
OPERATION, SET-UP, CALIBRATION, SERVICE & PARTS MANUAL
Pumper Systems
Level #1–500 to 1250 GPM
Foam Pro Models: #3020, #3040, #3060, #3090
Industrial Pumpers and Fixed Systems
Level #2:–1500 to 2500 GPM: Models #3150 & #3300
Level #3–3000 to 6000 GPM: Model #3300

MAX100/200-OPERATION Rev200813
2
1. CONTENTS
Table of Contents
1. CONTENTS..................................................................................................................................2
2. SAFETY........................................................................................................................................3
Safety Precautions........................................................................................................................3
3. INTRODUCTION ........................................................................................................................4
Overview: How the Foam System Works....................................................................................4
4. FOAM SYSTEM DRAWINGS – BASIC ...................................................................................6
Basic Drawings for Each System.................................................................................................6
5. DISPLAYS AND CONTROLS—ACCUMAX............................................................................9
Fury, Fusion and APEX Displays ................................................................................................9
Fury Specications.....................................................................................................................10
Fusion Specications ................................................................................................................. 11
APEX Specications..................................................................................................................12
6. FOAM SYSTEM AUXILIARY FUNCTIONS .......................................................................... 13
Final Installer Mobile System: Mobile System Auxiliary
Foam Functions....................................................................................................................13
7. OPERATION OF SYSTEM .......................................................................................................17
Screen Overview........................................................................................................................ 17
Screen View ...............................................................................................................................19
Accessing Water Flow Simulation Mode...................................................................................26
8. SETUP ........................................................................................................................................27
Setup Guidelines ........................................................................................................................27
Table 1. AccuMax System Setup Process .......................................................................................28
User Access Level......................................................................................................................29
9. USER SETTINGS ......................................................................................................................38
Adjusting User Settings ............................................................................................................. 38
Display .......................................................................................................................................47
Report Functions........................................................................................................................ 49
Event Log Functions..................................................................................................................51
10. FACTORY SETTINGS.............................................................................................................53
Changing Factory Settings......................................................................................................... 53
11. DIAGNOSTICS, TROUBLESHOOTING AND TESTING ....................................................55
Diagnostics Tools.......................................................................................................................55
Active Error/Warning.................................................................................................................57
Error/Warning Codes Troubleshooting Table ............................................................................58
Table 2. Error/Warning Codes ........................................................................................................58
12. CALIBRATION & TESTING ..................................................................................................63
Calibration Procedure Instructions ............................................................................................ 63
Table 3. Calibration Requirements .................................................................................................66
Valve Position Calibration (for MAX200 Fusion models only) ................................................ 74
Water Pressure Calibration (for MAX200 Fusion models only) ...............................................74
13. MAINTENANCE & SERVICE REQUIREMENTS................................................................76
Flushing Kit Maintenance/Service.............................................................................................76
14. COMPONENT DRAWINGS & PART NUMBERS ................................................................ 80
Line Control Assembly Dimensions and Flow Capacities ........................................................80

MAX100/200-OPERATION Rev200813
3
2. SAFETY
Safety Precautions
Throughout the AccuMax foam system installation manual, three (3) levels of precautions are denoted
as follows:
Cautions are used to indicate the presence of a hazard, which will or may cause
minor injury or property damage if the notice is ignored.
Warnings denote that a potential hazard exists and indicates procedures that
must be followed exactly to either eliminate or reduce the hazard, and to avoid
serious personal injury, or prevent future safety problems with the product.
Dangers are used to indicate the presence of a hazard that will result in severe
personal injury, death, or property damage if the notice is ignored.
• Before operating an AccuMax Foam Injection System, read all of the following safety precautions and operating manual
following all sections carefully.
• Proper ear protection must be worn while operating rotary gear pumps and foam/re pump systems.
• Proper eye protection is required while operating and maintaining any foam/re pump system.
• The normal ambient operating temperatures for xed and mobile foam system applications could vary from -40°F (-40°C)
to 130°F (54°C). Special provisions shall be provided by the installer for both extremely low or high operating conditions.
• Maximum Operating Temperatures Inside of the Pump Enclosure: 160° F / 70° C.

MAX100/200-OPERATION Rev200813
4
3. INTRODUCTION
Overview: How the Foam System Works
The FoamPro AccuMax injection system is an electronically controlled, hydraulically driven, foam concentrate
proportioning system designed to provide the wide range of foam concentrate injection rates necessary for foam operations.
The FoamPro AccuMax system will accurately deliver from 0.1% to 10.0% foam concentrate.
The performance and accuracy of the foam system shall be in compliance to applicable sections of NFPA #1901
(mobile vehicle systems) or NFPA #20 (xed systems). Please note: the installer shall be responsible for nal compliance
of the assembled foam installation, setup, and testing to meet NFPA or 3rd party testing requirements.
The FoamPro AccuMax system is a ow-based proportioning system that measures water ow through specied
discharges or water manifold and injects the correct proportional amount of foam concentrate to maintain the desired
percentage. The basic system is comprised of the following ve (5) assemblies for 1 to 15 foam line injectors and discharges:
a. Hydraulic System: FoamPro shall furnish the hydraulic pump, hydraulic motor, and hydraulic controller shall be supplied
by Foam Pro. The hydraulic cooler and reservoir can be supplied by the nal installer or Foam Pro.
b. Foam System: FoamPro shall furnish foam line Injectors (FLI) for water manifold (single-point) or each discharge
(multi-point), low-ow assembly, Fury or Fusion foam displays, main foam owmeter, foam pressure transducer, FRC
TankVision level display (or optional low-level sensor), and cabling for the foam system.
c. Electrical System: FoamPro shall furnish displays and controls, electrical communication system, and cabling. The nal
installer shall supply power supply fusing and wiring.
d. Foam Pump Components: FoamPro shall furnish foam pump, relief valve, and foam pump inlet wye strainer.
e. Water Discharge Components: FoamPro shall furnish water owmeter & pressure transducer (single-point) or water
owmeters and pressure transducers on each discharge (multi-point). Fusion and APEX systems have Elkhart electric
valves furnished by Foam Pro.
The hydraulic controller operates the hydraulic drive system to supply the proper amount of foam concentrate required
for the AccuMax operation and foam line controllers in use. A ‘wye’ strainer shall be installed before the foam pump to
protect the positive displacement foam pump from debris. A safety pressure relief valve shall be installed downstream of
the foam pump to recirculate foam to the suction side of the foam pump. This relief valve shall be supplied by FoamPro
and approved by the foam pump manufacturer. Hydraulic power to operate the foam pump shall be provided by a separate
hydraulic pump, in mobile systems shall be driven by the transmission mounted PTO and xed systems by an electric
motor or diesel engine. The foam concentrate line (from the foam pump) shall have a pressure transducer to control the
hydraulic system.
The foam line controller (FLI) shall consist of foam owmeter, foam control valve, foam injection check valve, and
a calibrate/inject valve. The AccuMax Fury or Fusion or Fusion/Apex displays communicate the proper information to
ensure the proper amount of concentrate is dispensed to the foam manifold or to the discharge that it controls.
The AccuMax II displays are in constant communication with hydraulic controller, foam line injector (FLI), water
pressure transducer(s), and water owmeter(s) to determine the correct amount of foam concentrate required and to
control the hydraulic pump to provide the hydraulic ow to drive the foam pump to deliver the proper amount of foam
concentrate. Additionally, the AccuMax system monitors the foam ow through the master foam owmeter from the
discharge of the foam pump. The AccuMax Fusion or Fury display menu allows the operator in “menu mode” to display
various functions and settings for foam system operator information.

MAX100/200-OPERATION Rev200813
5
The constant comparison of the water ow and foam ow information by the AccuMax system ensures the
desired proportion of foam concentrate, based on water ow rate, independent of any variations in re pump intake or
discharge pressures. As water ow increases or decreases, the foam concentrate rate of injection is increased or decreased
automatically to correspond to water ow, maintaining the proper concentrate percentage as selected on the FLI injector.
It also controls the foam control valve to allow the proper amount of foam concentrate to be injected into water manifold
or individual discharge lines based on the input requirements controlled by the re pump operator and the information
supplied by the foam owmeter(s) and the water owmeter(s) regardless of operating pressure.
Each FLI controller operates independently and all FLI assembly(ies) shall communicate with the AccuMax
software for total system operation. With a single-point FLI, one pressure transducer is provided. On multi-point Fusion
system, a specied number of FLI controllers and water pressure transducers are provided; installed on each discharge
(to indicate discharge “line pressure” readings). Foam concentrate shall be injected directly into the water manifold or
into each discharge of specied foam/water discharges.
The water line owmeter measures the water ow and sends a signal to the display(s). A water pressure transducer
shall be installed on the water manifold (single-point) or each water/foam solution discharge line.
On vehicle mounted systems: 12/24-volt electrical power to operate the foam system shall be provided by the
chassis electrical system.
On xed systems: 12/24-volt electrical power to operate the foam system shall be provided by a separate battery
and charger system by the installer. In both electrical systems, the nal installer shall be responsible for power supply
wiring and fuse protection per the electrical section of the installation manual.

MAX100/200-OPERATION Rev200813
6
4. FOAM SYSTEM DRAWINGS – BASIC
Basic Drawings for Each System
Drawing #1–Fury Single-Point
OEM
FOAM TANK
SUMP
3"
3"
11/2"
FIRE PUMP
WATE RWAY
CHECK VALVE
OFF-BOARD PICK-UP
FOAM/WATER
MANIFOLD
WATER MANIFOLD
WATER ONLY DISCHARGES
CALIBRATE/
INJECT VALVE
300 GPM / 1150 LPM
FOAM PUMP
RELIEF
VALVE
FOAM
PUMP
MASTER PRESSURE
TRANSDUCER
MASTER FOAM
FLOWMETER
LO-FLOW RETURN LINE
ON/OFF FOAM TANK TO
FOAM PUMP VALVE
MANUALLY
OPERATED VALVE
LO-FLOW
ASSEMBLY
1.5" OR 2"
FOAM-LINE INJECTOR
ASSEMBLY
STRAINER
PRESSURE
TRANSDUCER
INJECTION CHECK VALVE
TO FOAM TANK OR
CALIBRATE LINE
WATE RWAY
FLOWMETER
FOAM TANK VENT
OPTIONAL CHECK VALVE
SUMP

MAX100/200-OPERATION Rev200813
7
Drawing #2–Fury Multi-Point
OEM
FOAM TANK
SUMP
2"
2"
FOAM TANK VENT
FLEXIBLE HOSE
SUCTION LINE
AUXILIARY
FOAM
CONCENTRATE
INTAKE
MANUALLY
OPERATED VALVE
OPTIONAL
CHECK VALVE
ON/OFF FOAM TANK TO
FOAM PUMP VALVE
STRAINER
300 GPM / 1150 LPM
FOAM PUMP
SIEMENS
FLOWMETER
FOAM
FOAM
PUMP PRESSURE
TRANSDUCER
LO-FLOW
ASSEMBLY
RELIEF
VALVE
FIRE PUMP
WATE RWAY
CHECK VALVE
WATE RWAY
FLOWMETER
FOAM-LINE INJECTORS (6)
4"
MONITOR
FOAM
2.5"
DISCHARGE
4" FOAM
LDH
SUMP
TANKVISION

MAX100/200-OPERATION Rev200813
8
Drawing #3–Fusion Multi-Point
OEM
FOAM TANK
SUMP
2"
2"
FOAM TANK VENT
FLEXIBLE HOSE
SUCTION LINE
AUXILIARY
FOAM
CONCENTRATE
INTAKE
MANUALLY
OPERATED VALVE
OPTIONAL
CHECK VALVE
ON/OFF FOAM TANK TO
FOAM PUMP VALVE
STRAINER
300 GPM / 1150 LPM
FOAM PUMP
SIEMENS
FLOWMETER
FOAM
FOAM
PUMP
PRESSURE
TRANSDUCER
LO-FLOW
ASSEMBLY
RELIEF
VALVE
FIRE PUMP
WATE RWAY
CHECK VALVE
WATE RWAY
FLOWMETER
FOAM-LINE INJECTORS (6)
4"
MONITOR
FOAM
4" FOAM
LDH 2.5"
DISCHARGE
SUMP
TANKVISION

MAX100/200-OPERATION Rev200813
9
5. DISPLAYS AND CONTROLS—ACCUMAX
Fury, Fusion and APEX Displays
Color-Coded Rain Guard
Fury, Fusion, and APEX displays shall be equipped with color-coded removable rain guard at the top of each display.
The rain guard deects water and dirt from running down the display. The colors shall comply to NFPA #1901 discharge line
colors. The discharge display color shall match the discharge color (installer responsibility).
Displays: FURY, FUSION, APEX
High brightness LCD screen shall have numerical, alpha, and graphical displays for discharge and foam system operations.
Each display (FURY, FUSION, and APEX) are unique, with various selectable buttons, menus, and functional operations.
System messages and errors are shown through indicators on the display. See further details of the screen elements in the
Operation manual. See further details of the screen elements in the later Sections in the Installation Manual #1 and Operation/
Service/Parts Manual #2.
Foam Delivery ON/OFF Button
The RED button turns foam delivery to the manifold or discharges: ON or OFF. To turn ON or OFF, press and hold
this button for two seconds. When foam delivery is ON, the foam concentrate will be delivered at a specied rate as soon
as water ow from the discharge is detected.
Up/Down Buttons
The YELLOW buttons with UP/DOWN arrows control the foam proportioning rate adjustment either incrementally
higher or lower.
a. When pressed once: a lower (DOWN) and higher (UP) preset for foam proportioning rate will be recalled (if it exists).
b. For ne adjustment of foam proportioning rate: press and hold either the UP/DOWN button. The rate will start to adjust
up/down by 0.1% steps; release this button to stop the adjustment.
c. NOTE: a temporary preset at the current value will be added when the button is released. Presets can be changed, added
or deleted by using USER SETTINGS from the main MENU button.
Select button
When the BLUE ‘SELECT’button is pushed, it changes the data displayed on selectable display located on the bottom
of display screen. The button allows operator to read out values for various system parameters as needed. Additionally, it will
also allow operator to access "Water Flow Simulation Mode". The parameters listed below are selectable with this button
can be customized to operator’s need using USER SETTINGS from the MENU button.
• Foam Total Volume *
• Foam Flow System
• Foam Total Volume System
• Foam Tank Level [1]
• Foam Tank Time to Empty* [1]
• Foam Manifold Pressure
• Water Pressure [2]
• Water Flow *
• Water Total Volume*
• Water Total Volume System
• Water Simulated Flow **
NOTE 1: * enabled to be displayed by default
NOTE 2: ** always enabled
NOTE 3: [1] - for systems equipped with TankVision Foam Tank Gauge
NOTE 4: [2] - Fusion (MAX200 Model Only)
List of Available Parameters that can be Selected:

MAX100/200-OPERATION Rev200813
10
Fury Specications
Foam/Water Discharge Control Specications
The Foam Pro AccuMax II Fury foam system shall manage: pin-point foam concentrate injection, continuous
monitoring of both water ow and foam ow, and communications to the hydraulic pump for speed and hydraulic uid
output. The foam/water discharge conguration shall include the following components:
1. FURY Display
2. RED: Foam Delivery ON/OFF button
3. YELLOW: Down button (Adjust to lower preset foam %; press and hold)
4. YELLOW: Up button (Adjust to higher preset foam %; press and hold)
5. BLUE: Select button
6. LIGHT BLUE: Menu button
7. Water Pressure Indicator (PSI/BAR)
8. Water Flow Rate (GPM/LPM)
9. Foam Tank Level Indicator
10. Rain Guard (above display)
11. Foam System ON/OFF Indicator
on Display
AccuMax Fury
2
4
3
5
6
8
10
9
1
7
11

MAX100/200-OPERATION Rev200813
11
Fusion Specications
Foam/Water Discharge and Electric Valve Controls Specications
The Foam Pro AccuMax II Fusion foam system shall manage: pin-point foam concentrate injection, continuous
monitoring of both water ow and foam ow, and communications to the hydraulic pump for speed and hydraulic uid output.
1. FUSION Display
2. RED: Foam Delivery ON/OFF button
3. YELLOW: Down button (Adjust to lower preset foam %; press and hold)
4. YELLOW: Up button (Adjust to higher preset foam %; press and hold)
5. BLUE: Select button
6 YELLOW: Water Valve Preset button
7. RED: Water Valve Close button
8. GREEN: Water Valve Open button
9. LIGHT BLUE: Menu button
10. Water Pressure Indicator (PSI/BAR)
11. Water Flow Rate (GPM/LPM)
12. Tank Level Indicator
13. Rain Guard (above display)
14. Valve position indicator (bottom bar)
15. Foam System ON/OFF Indicator
on Display
AccuMax Fusion
2
43
5
8
9
11
13
12
15
14
6
7
1
10

MAX100/200-OPERATION Rev200813
12
APEX Specications
Electric Valve Control Specications
When the Foam Pro AccuMax APEX displays are used with a Fusion multi-point foam system, they shall provide:
pin-point foam concentrate injection, continuous monitoring of both water ow and foam ow, and communications to the
hydraulic pump for speed and hydraulic uid output. The water/foam discharge components shall have either: individual
line injectors for "packaged’ discharge assemblies" for a combination of water/foam discharges piped from separate water/
foam manifold.
4
5
8
9
11
6
7
10
1. APEX Display
2. RED: Valve Close button
3. YELLOW: Valve Preset button
4. GREEN: Valve Open button
5. LIGHT BLUE: Menu button
6. Valve Preset Position Marker
7. Pressure Gauge Scale & Pointer
8. Pressure unit of measure (PSI or BAR)
9. Water Flow Rate (GPM or LPM)
10. Water Flow unit of measure (GPM or LPM)
11. Valve position indicator (red=CLOSED
and black=OPEN)
APEX
1
2
3

MAX100/200-OPERATION Rev200813
13
6. FOAM SYSTEM AUXILIARY FUNCTIONS
Final Installer Mobile System: Mobile System Auxiliary
Foam Functions
The foam system shall be supplied with “auxiliary function” components to provide several supplemental operations
of the foam system. This equipment can be provided and installed by the assembler of the system and/or certain assemblies
can be provided by Foam Pro as ‘optional’ equipment.
To assist the installer, the following section outlines:
1. OEM supplied and installed auxiliary foam functions
2. Foam Pro provided FOAM-AUX components and display system
“Simulation Mode”: Operating Foam System for Auxiliary Functions
The operation of the “simulation mode” is outlined in the SET-UP and OPERATION section of this manual. Careful
operator training and visible instructions must be in place for such operations. The “simulation mode” operation of a foam-
line-injector is required for OEM auxiliary foam operation. 1.5”/40mm size (for up to 150GPM/560LPM ow) or 2”/50mm
size for (300GPM/1125LPM ow) should be installed on FILs.
• It is extremely important all operators are trained in the operation of the “simulation mode” of a foam-line-injector. A
large instruction plaque shall be installed at the pump panel to denote the step-by-step set-up of this mode.
• When operating the FoamPro AccuMax System in the “Simulated Mode” function, an outlet for the foam concentrate
must be provided. Otherwise, dangerous excessive pressure may be built up in the apparatus water piping and/or hoses.
This outlet for the foam concentrate can be provided by turning the “CAL/INJECT” valve to the “CAL” position. A
suitable container must be provided to collect the foam concentrate. Or, The foam concentrate discharge or foam tank
rell line can be operated.
Final Installer Supplied: Auxiliary Foam Functions and Installation
The OEM supplied “Auxiliary Functions” could be as follows:
1. Valve and control of the foam tank-to-foam pump control valve (noted previously under INTAKE PLUMBING)
(Specify Size: _____inches/_____mm)
2. External foam concentrate intake valve (known as OFF-BOARD). Refer to section #15 on this installation.
(Specify Size: _____inches/_____mm)
3. Flushing of the foam system (Noted below)
4. (*) If specied, foam tank rell system (Specify Size: _____inches/_____mm)
5. (*) External foam concentrate discharge control. Refer to section #16 on this installation.
(Specify Size: _____inches/_____mm)
6. Note: opening item #1 and #4 would allow the foam concentrate to be re-circulated.
Functions #4 and #5 (*) require special plumbing and installation of three-way valves to be installed AFTER the
foam-line-injector (FLI) assembly. These three-way valves shall be the same size as the FLI and shall be separately
controlled with an ON/OFF bypass switch and diverter control switch: foam tank rell or foam concentrate discharge
(open outlet – without cap). Refer to the drawing on a typical installation arrangement.

MAX100/200-OPERATION Rev200813
14
OEM
SIZE:
_
_
_
G/L
FOAM TANK
Final Installer Auxiliary Functions # 4 And # 5
FROM FOAM PUMP
FOAM FLOW METER
FOAM TANK VENT
FOAM/WATER
DISCHARGE
FROM FIRE PUMP -
WATER MANIFOLD
FOAM LINE
INJECTOR VALVE
THREE-WAY
DIVERTER VALVE
IN-LINE
CHECK VALVE
1 1/2" IN-LINE
CHECK
VALVE
1 1/2" / 40mm
SIZES: 1 1/2" / 40mm (Standard)
2" / 50mm (Optional)
A
ELECTRIC OPERATED
VALVE
1 1/2"
1 1/2"
1 1/2"
1 1/2"
1 1/2"
1 1/2"
#4
#4
#5
B
OPEN FOAM
CONCENTRATE
DISCHARGE
THREE WAY
DIVERTER VALVE
OEM INSTALLED AUX
TANK REFILL
FOAM AUX PANEL
A
B
OFF ON
FOAM DISCHARGE
REFILL
FOAM AUX PANEL
1
2
3
4
5
FOAM TANK TO FOAM PUMP
AUXILIARY INTAKE
FLUSH
FOAM TANK REFILL
FOAM DISCHARGE
Auxiliary Foam Concentrate Intake Connection(s)
Every foam system shall be equipped with an auxiliary external foam concentrate connection intake. Such intakes
are commonly referred to as “OFF-BOARD” pick-up intakes. The nal installer shall be responsible for the auxiliary foam
concentrate intake installation. Normally, this intake valve is located at or near the pump operator’s position, so that the
operator can easily see and control foam drafting or foam intake pressure.
The foam intake valve, plumbing, and adapters must be “sized” to the same size as the foam pump intake piping; supplied
by the nal installer. An optional FoamPro FOAM-AUX system and Elkhart electric valve are available.
If specied by the end-user, the nal installer shall supply an "off-board" foam suction hose, of a minimum of 10 feet /
3 meters in length. If longer, the intake hose shall be increased in hose diameter by one size. The intake line and suction hose
shall be the same size as the foam tank to foam pump line.
The end-user shall specify one of the following alternatives for an auxiliary foam intake valve(s):
a. “Suction only” intake use: from foam totes, portable foam tank, or foam tanker supply, without a pressure and the
foam intake is for “suction only” purposes. A manual or electric gated ball valve sized to match the foam pump supply
inlet shall be installed. The intake valve, intake hose ttings and adapters shall be supplied by the nal installer.
• The nal installer shall install the following warning label next to the foam intake valve and connection: this applies
only to FireLion and Edwards foam pumps.
• Foam concentrate intake is intended for “suction ONLY” purposes. This foam intake shall NOT be used for “ushing”
foam system or pressurized foam supply.

MAX100/200-OPERATION Rev200813
15
b. “Pressurized and Suction” intake use: This is a dual-purpose intake, for both suction purposes and pressurized
foam concentrate supply from foam pumpers or tankers with foam pumps. The nal installer shall supply and install
an auxiliary foam inlet with manual or electric gated ball valve on inlet plumbing to supply the foam pump from an
external foam concentrate supply or pressurized source. This valve shall permit the pump operator to control the intake
pressure. The intake hose ttings and adapters shall be supplied by the nal installer.
Auxiliary Intake Foam Concentrate
Manual Control
Auxiliary Intake Foam Concentrate
Electric Control
(STD) OEM SUPPLIED
AND INSTALLED AUX
FOAM INTAKE VALVE
TO FOAM INTAKE
PLUMBING
TO FOAM INTAKE
PLUMBING
TO FOAM INTAKE
PLUMBING
PRESSURE GAUGE *
* ONLY FOR FIRELION AND EDWARDS PUMPS
* ONLY FOR FIRELION AND EDWARDS PUMPS
ELECTRIC BALL VALVE
AND INSTALLED AUX
FOAM INTAKE VALVE
ELECTRIC BALL VALVE
AND INSTALLED AUX
FOAM INTAKE VALVE PRESSURE GAUGE *
Foam Pro Supplied: FOAM-AUX Functions
OPTIONAL: EXTERNAL FOAM CONCENTRATE INTAKE(S)
Foam Pro supplied “off-board” foam supply valve(s): external “off-board” foam intake(s) shall be Elkhart Brass
electric valve(s) with either an APEX control or FOAM-AUX display control. The intake hose ttings and adapters shall
be supplied by the nal installer.
These valves are available in two (2) alternative methods:
a. Elkhart APEX Valve Control: foam concentrate intake electric valve shall be controlled by an APEX valve display.
b. FoamPro FOAM-AUX display control: A Foam Pro supplied FOAM-AUX auxiliary function system and display
shall be installed by the nal installer. The FOAM-AUX shall control an Elkhart electric intake valve(s).
The FOAM-AUX system shall provide the following functions:
1. Foam tank-to-foam pump valve control ON/OFF (Specify size: ___”/mm)
2. External foam concentrate valve(s) control (Specify size: ___”/mm)
a. Manually controlled valve(s) supplied and installed by nal installer
b. Elkhart electrically controlled foam concentrate intake valve(s) supplied by Foam Pro and installed by nal installer.
c. Flush system control (manual valve or electric valve) supplied and installed by nal installer.

MAX100/200-OPERATION Rev200813
16
d. Foam tank relling (Specify size: ___”/mm)
e. Foam concentrate discharge (Specify size: ___”/mm)
f. Foam concentrate recirculation
Refer to drawing on the installation of the FOAM-AUX plumbing diagrams. The setup and operation of the system
is noted under the SETUP section of this installation manual.
Foam Aux Display and Installation
OEM
SIZE:
_
_
_
G/L
FOAM TANK
OPEN FOAM
CONCENTRATE
DISCHARGE
#5
METERING VALVE
SIZES: 1 1/2" / 40mm (Standard)
2" / 50mm (Optional)
1 1/2" 1 1/2" 1 1/2"
THREE WAY DIVERTER VALVE
SIZES: 1 1/2" / 40mm (Standard)
2" / 50mm (Optional)
FOAM TANK REFILL
#4 FOAM TANK
VENT
SIZES: 1 1/2" / 40mm (Standard)
2" / 50mm (Optional)
FOAM FLOW METER
PRESSURE TRANSDUCER
FROM FOAM
CONCENTRATE
MAINIFOLD
FOAM AUX DISPLAY
DISPLAY
OPERATIONS
1
2
3
4
5
6
FT -TO- FP
FOAM INTAKE
FLUSH
FOAM TANK REFILL
FOAM CONL DISCHARGE
FOAM RECIRCULATE
On FireLion and Edwards foam pumps a pressure gauge shall be installed next to the intake valve. The nal installer
shall install the following warning label next to the foam intake valve and connection:
• WARNING: foam intake valve (from either “suction” or “pressurized” foam supply) shall be ball valve controlled to
allow a maximum pressure of no more than 50 PSI (3 BAR) or foam pump damage will result. The foam intake shall
NOT be used for “ushing” purposes.

MAX100/200-OPERATION Rev200813
17
7. OPERATION OF SYSTEM
Screen Overview
On power-up the display module will be in the normal operating mode. The red ON/OFF button, yellow decrease (-)/
increase (+) buttons and blue SELECT button are used to control the foam system operation. For the MAX200 Fusion
model, the green OPEN, red CLOSE, and yellow PRESET buttons will control the water valve position. The yellow
PRESET button will set the valve to a programmed position. The blue MENU button switches to the Menu Screen.
(Menu Screen is activated when this button is pressed and held down for two seconds.)
Foam system state and operating parameters will be shown on the display screen along with system messages,
warnings and error codes.
Operator Screen
The operator screen loads upon the initial start-up.All information needed to operate the system is shown on this screen.
• Foam on/off indicator
• Foam class indicator
• Foam proportioning rate (%)
• Fixed operational parameter shown at the top of the screen
• Toggle through Parameter display (changeable with select button)
• Foam tank level indicator (if equipped), system messages
• Warnings and error/fault messages
• User-assigned identication: name and color codes.
• NOTE: MAX200 Fusion models feature a valve position.
Button Operations
• Red ON/OFF button: Press and hold for 2 seconds to start/stop the foam proportioning.
• Yellow Decrease button (-): Press to switch to the foam percentage to a lower preset. Press and hold to make a temporary
adjustment to the foam percentage in 0.1% increments.
• Yellow Increase button (-): Press to switch to the foam percentage to a higher preset. Press and hold to make a temporary
adjustment to the foam percentage in 0.1% increments.
For MAX200 Fusion only:
• Green OPEN button: Press and hold to drive a valve toward the Open position. Valve will stop when the button is
released, or when it is fully open.
• Red CLOSE button: Press and hold to drive a valve toward the Closed position. Valve will stop when the button is
released, or when it is fully closed.
• Yellow PRESET button: Press and hold once; upon release the valve will travel to a preprogrammed position and stop
there. Press and hold PRESET button for three seconds to save the current valve position as a preset position. This will
be saved into the valve actuator's internal memory.

MAX100/200-OPERATION Rev200813
18
Menu Button Operations
The Menu is accessed by pressing and holding the MENU button. The menu system allows for the following functions:
• Parameter value adjustment & modication of options
• Display adjustments
• Diagnostics
• System Backup
• System Maintenance and Calibration
• Save and retrieve settings from external USB memory
• Review active error, warning, faults and recorded events
• Firmware Updates

MAX100/200-OPERATION Rev200813
19
• 1. Header bar – color coded
• 2. Discharge name – user dened
• 3. Error / Warning indicator (displayed only when
warning/error exists)
• 4. Message bar
• 5. Fixed Display
• 6. Fixed Display Variable ID Label
• 7. Fixed Display Value
• 8. Fixed Display Unit of Measure
• 9. Selectable Display
• 10. Selectable Display Variable ID Label
• 11. Selectable Display Value
• 12. Selectable Display Unit of Measure
• 13. Foam Tank Level Indicator
• 14. Foam Delivery ON/OFF Indicator
• 15. Foam Class Indicator
• 16. Current Foam Proportioning Rate
• 17. Water Valve Closed Indicator (AccuMax
Fusion Only)
• 18. Water Valve Position Indicator (AccuMax
Fusion Only)
• 19. Water Valve Preset Indicator (AccuMax
Fusion Only)
Operator Screen Elements
2
4
3
5
8
910
17
18 19
15
16
11
12
13
14
6
71
Screen View

MAX100/200-OPERATION Rev200813
20
Menu Screen Layout of Components (Diagram is shown on the next page.)
• A—Header Bar: Current Menu/Sub menu title and icon are displayed.
• B—Content Area: Displayed as a list of menu items/options. Each menu item is shown with a title, icon to the left
and the current value (or status). Position bar on the right side of the display screen shows the position of the selected
menu item.
• C—Footer Bar: The Footer Bar is located at the bottom of the LCD display screen and shows icons that represent
the keypad buttons. Each button icon is accompanied by a function indicator. This indicator will show the action that is
associated with this button. The button action will change depending on the selected item or menu screen.
This manual suits for next models
3
Table of contents
Other Safe Fleet Controllers manuals
Popular Controllers manuals by other brands
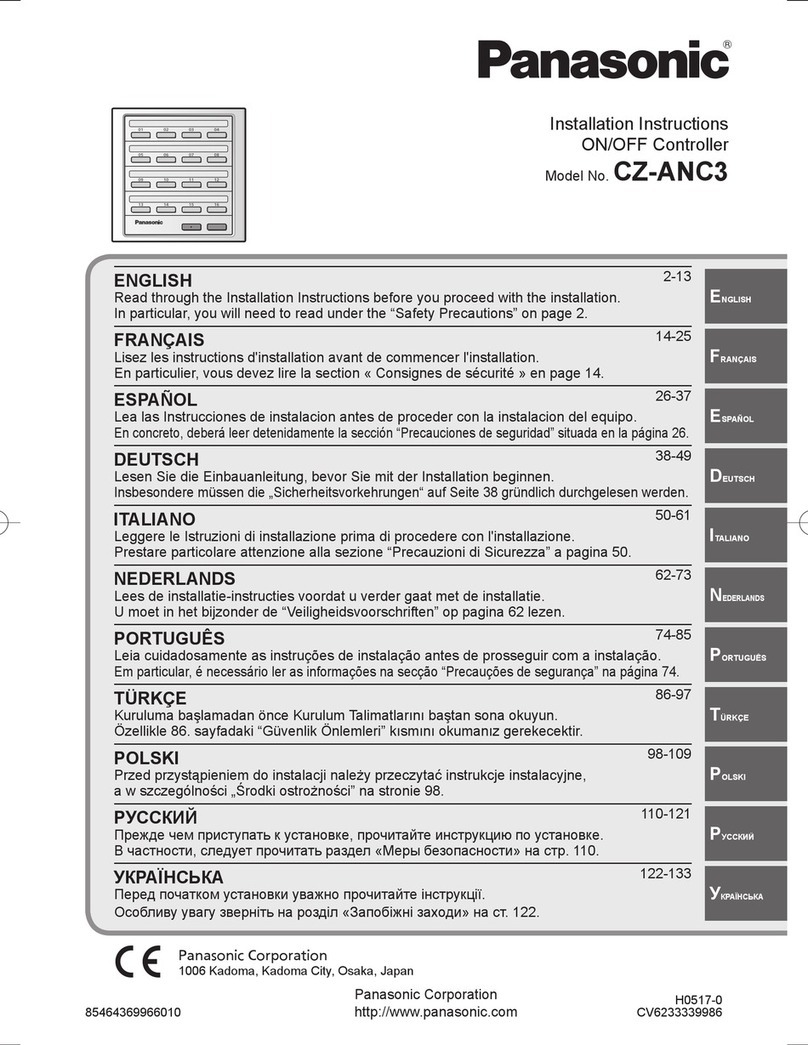
Panasonic
Panasonic CZ-ANC3 installation instructions
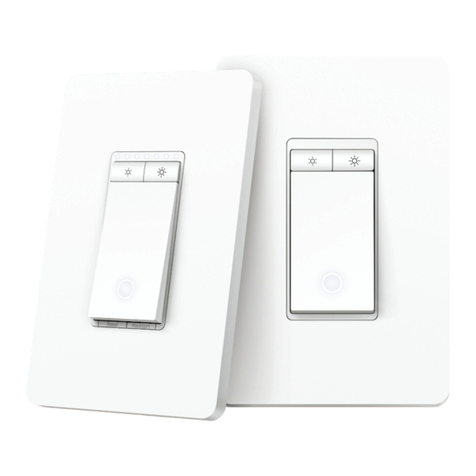
TP-Link
TP-Link KS230Kit user guide
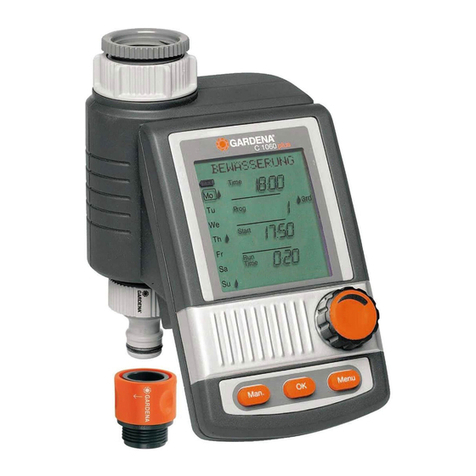
Gardena
Gardena C 1060 plus operating instructions
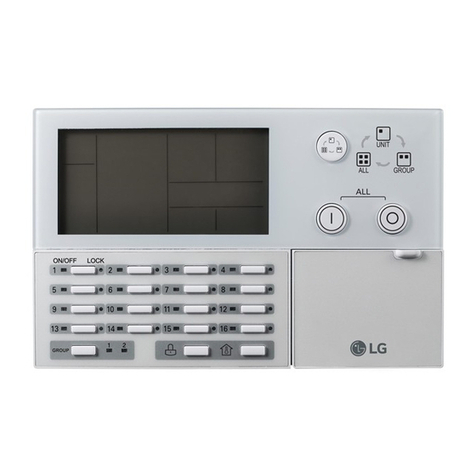
LG
LG AC Ez Installation & owner's manual
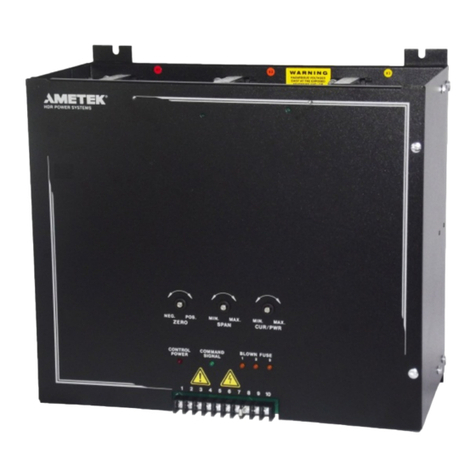
Ametek
Ametek RF3 SCR Series Instruction, Operation and Maintenance Manual
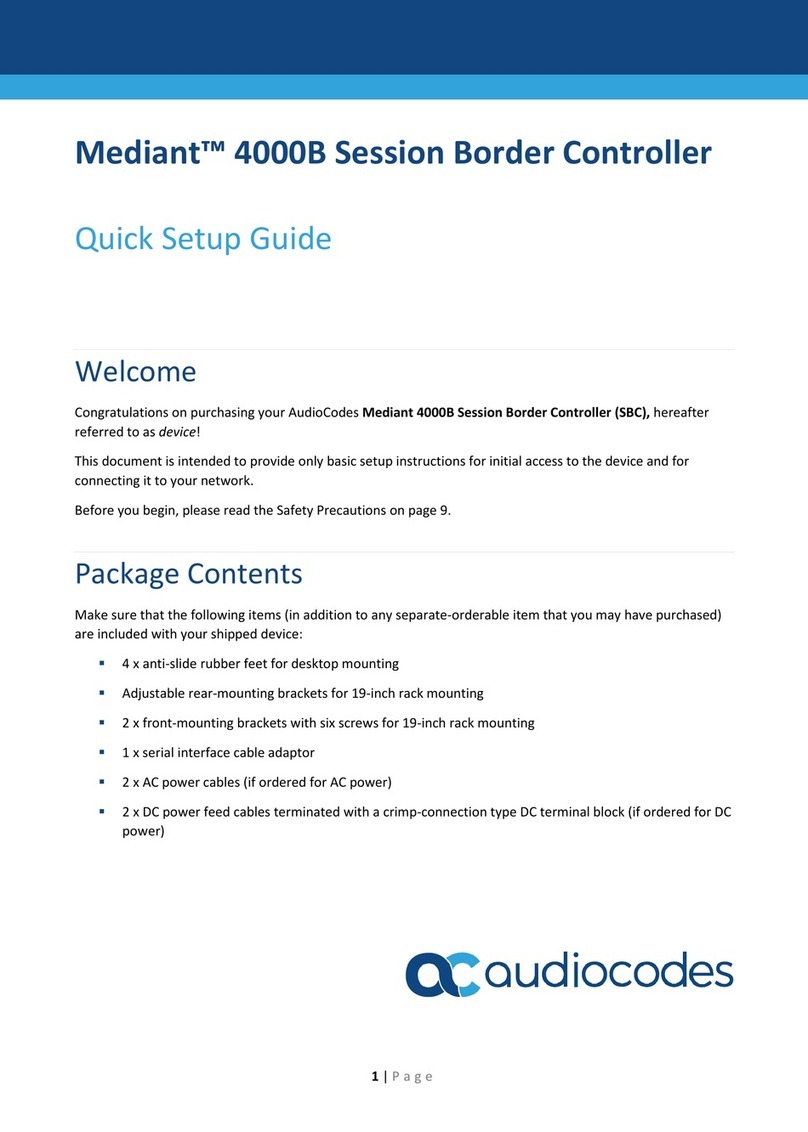
AudioCodes
AudioCodes Mediant 4000B Quick setup guide
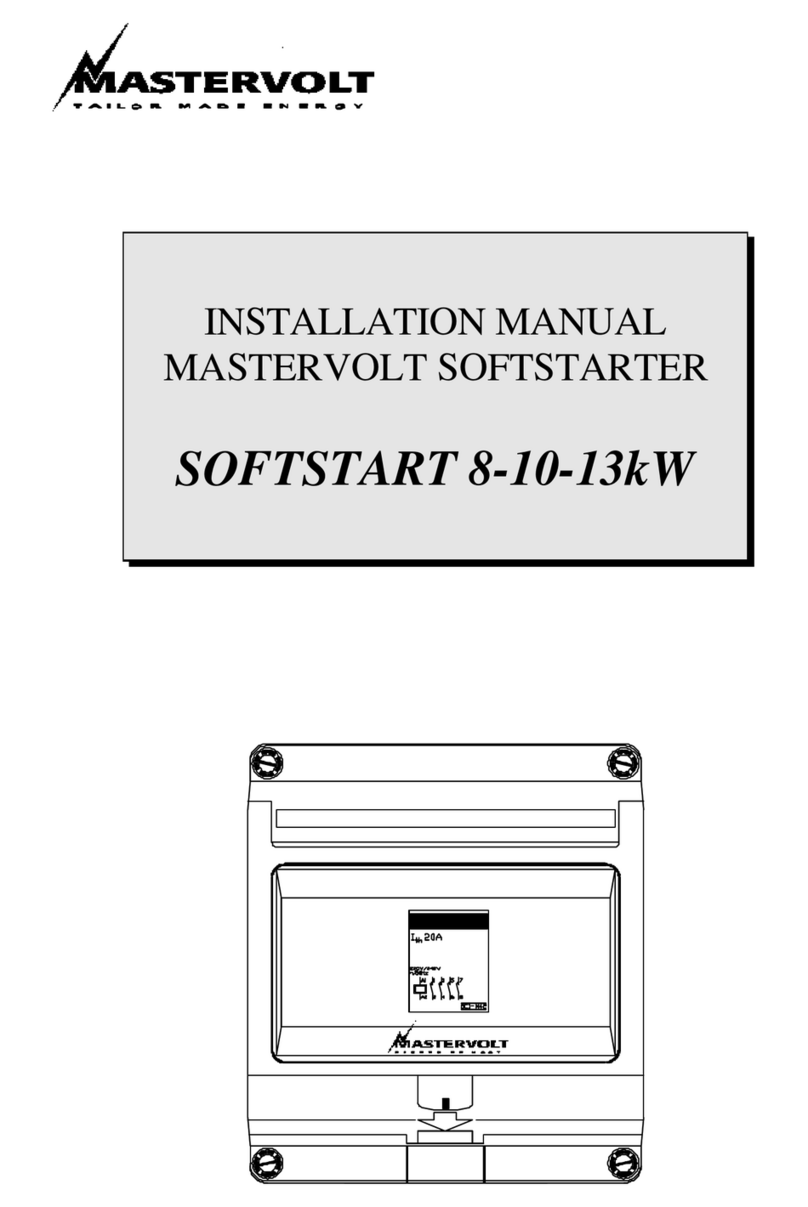
Mastervolt
Mastervolt Softstart 8kW installation manual

Afriso EURO-INDEX
Afriso EURO-INDEX RG 210 instruction manual

Oasis
Oasis GARDENER 12/16 Instruction book
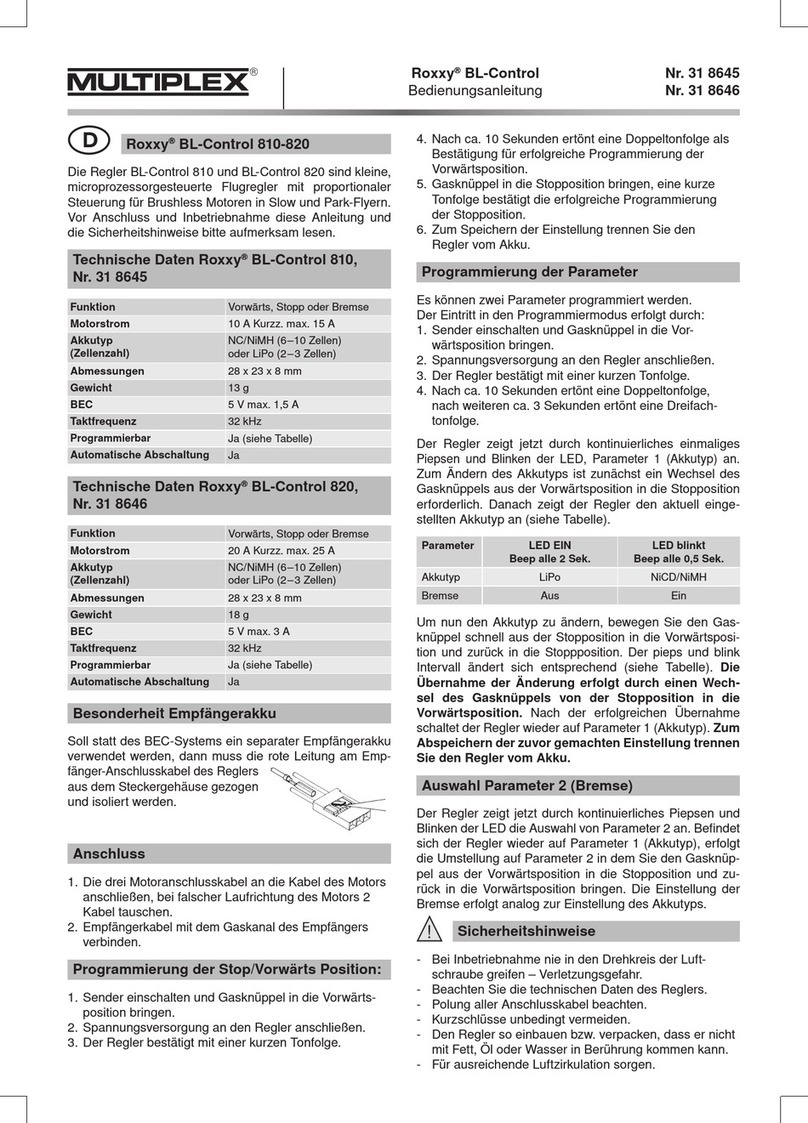
Multiplex
Multiplex Roxxy BL-Control 810 operating instructions

Future Design
Future Design MCT-MC 4.3 user manual
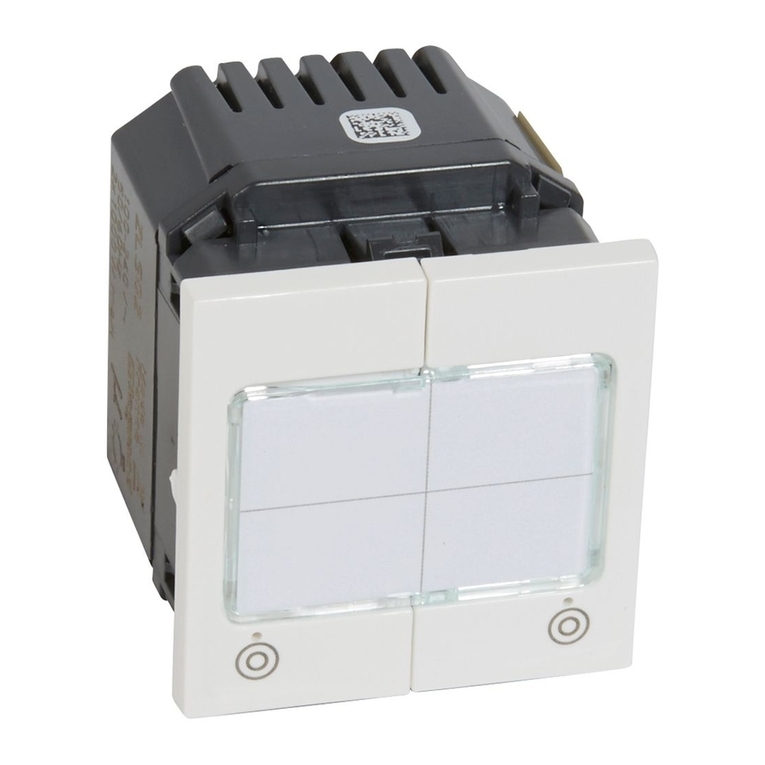
LEGRAND
LEGRAND 0 784 48 quick start guide