Safran LRF 3013 User manual

Document number: TML 913655 ver A
Public: 13.03.2017
Confidential & Proprietary Safran Vectronix AG –All rights reserved
page: 1/36
Integrator Manual
LRF 3013

LRF 3013 Integrator Manual
Document number: TML 913655 ver A
Public: 13.03.2017
Confidential & Proprietary Safran Vectronix AG –All rights reserved
page: 2/36
Disclaimer
The information presented in this operator manual is believed to be accurate and correct for the
intended use of the LRF module. (Intended use means distance measurement when integrated into
a host system without any modification to the LRF module). Should the LRF module be used for
other applications and purposes not covered herein, please contact Safran Vectronix AG to validate
its suitability. This manual, all of its contents and the LRF module specifications are subject to
change without notice.
Without the prior written permission of Safran Vectronix this document may neither be copied in
part or in whole by mechanical, photographic, electronic or any other means (this includes
converting it to any machine-readable form), nor be stored in an information storage system, nor be
used for any purpose other than that intended, nor be made available or passed on to any third
party who has not been expressly authorized by Safran Vectronix. Relevant information for the end
user is allowed to be copied into user instructions of the host system.
Warranty: Safran Vectronix AG provides this publication “as is” without warranty of any kind,
either express or implied, including, but not limited to, the implied warranties of merchantability or
suitability for any particular purpose.
Revisions/Errors: Safran Vectronix AG reserves the right to revise this publication, and to make
changes in the content hereof from time to time without notification. This publication may include
technical inaccuracies or typographical errors. Changes are made periodically to the information
herein; these changes will be incorporated in new editions of the publication. Safran Vectronix AG
may make improvements and/or changes in the products and/or the software described in this
publication at any time.
Notice to User: This manual should not be construed as a representation or warranty with respect
to the software and hardware named herein. Occasionally, changes or variations exist in the
software and hardware that are not reflected in the manual.
Publication: The descriptions, specifications, design and procedures contained in this manual
were effective at the time of publication of this manual. Safran Vectronix AG reserves the right to
modify any of the above at any time without notice and without incurring obligations.

LRF 3013 Integrator Manual
Document number: TML 913655 ver A
Public: 13.03.2017
Confidential & Proprietary Safran Vectronix AG –All rights reserved
page: 3/36
Safety Notices
For safe use of the LRF module, please note the safety instructions in this Integrator Manual.
LRF 3013 is exclusively designed for use in OEM products. The LRF 3013 is designed and
configured as a Class 1 Laser device. Use of controls or adjustments or performance of
procedures other than those specified herein may result in hazardous laser light exposure. Do
not open or modify any parts of the LRF module or attempt your own repairs. Do not manipulate
or adjust the performance of the LRF module.
The LRF module is not a safety critical component. Therefore a plausibility or sanity check of
each measurement value must be performed by the integrators system.
Be careful with ESD: The LRF module is an electrostatic discharge sensitive device.
Do not touch any electronics or components unless protective measures are in place.
Always keep the instructions in direct access for users and any personnel working with the
instrument.
Power the LRF module only within the specified voltage and power range.
Handle the LRF module only in a clean, dry and ESD protected area.
Do not touch the glass lenses.
Do not contaminate any parts with oil or grease.
Avoid abrupt temperature changes.
Inappropriate use
Use without a plausibility check
LRF module use without prior knowledge of the operating instructions and safety notices
Unauthorized changes and modifications made to the LRF module by the customer
The use of commands other than specified
Use of third-party accessories not expressly approved by Safran Vectronix AG
Working in an explosive environment
Testing or inspection of LRF module in a manner not specified under intended use
Use of the LRF module without instruction
Use outside of the specified limits (see data sheet of LRF 3013)
Opening any part of the LRF module components
Use after misappropriation
Use of LRF module with obvious damage or defects
Inappropriate use may result in the risk of
misinterpretation of results
eye injuries
instrument errors
damage to property
malfunction

LRF 3013 Integrator Manual
Document number: TML 913655 ver A
Public: 13.03.2017
Confidential & Proprietary Safran Vectronix AG –All rights reserved
page: 4/36
Integrator obligations
Understanding the contents of this manual is the basic requirement in order to use the instrument
safely.
The person responsible for the product must ensure that integrators are qualified and all users
understand and adhere to these instructions.
Avoiding storage and transport damage
When not in use, always keep the LRF module packed in a dry, clean condition.
Remove power prior to prolonged storage.
Observe the specified storage temperatures.
Do not expose the LRF module to strong mechanical shocks
Do not expose the LRF module to abrupt temperature transitions (moisture condensation)
Avoiding measurement errors
Note the factors affecting measurement accuracy as described in chapter 2.1.3 Ranging
Conditions.
Always perform test measurements on targets at known distances if the LRF module was
exposed to rough handling (vibration, shock, drop etc.), and before carrying out any important
measurement tasks.
Changes
Revision
Chapter
Description
A
All
New Demonstration Software, grammatical text revisions, document design

LRF 3013 Integrator Manual
Document number: TML 913655 ver A
Public: 13.03.2017
Confidential & Proprietary Safran Vectronix AG –All rights reserved
page: 5/36
Contents
Disclaimer................................................................................................................................. 2
Safety Notices.......................................................................................................................... 3
1General............................................................................................................................... 7
1.1 Main Elements and functions of the LRF Module...........................................................................7
1.1.1 Main parts ................................................................................................................................7
1.1.2 Interface parts..........................................................................................................................8
2LRF Background Information........................................................................................... 8
2.1 Rangefinder Principle......................................................................................................................8
2.1.1The “Pulsed Diode” ..................................................................................................................8
2.1.2 Electronics................................................................................................................................9
2.1.3 Ranging Conditions..................................................................................................................9
3Getting Started .................................................................................................................11
3.1 First steps with the LRF Interface Kit........................................................................................... 11
3.2 Using the Safran Vectronix Terminal Software............................................................................ 14
3.3 First steps without LRF Interface Kit............................................................................................ 16
3.4 Checklist in case of problems with LRF modules ........................................................................ 16
4Integration.........................................................................................................................17
4.1 Mechanical Mounting & Handling................................................................................................. 17
4.2 Design recommendations ............................................................................................................ 17
4.2.1 Preparation............................................................................................................................ 17
4.2.2 Mounting ............................................................................................................................... 17
4.2.3 Boresighting.......................................................................................................................... 18
4.2.4 Nitrogen flushing................................................................................................................... 19
4.3 Front Protection............................................................................................................................ 19
4.4 Eye Safety.................................................................................................................................... 20
5HW Interface .....................................................................................................................21
5.1 System Connector and Signal Description .................................................................................. 21
5.2 Power Supply & Timing................................................................................................................ 22
5.3 Serial Interface: UART ................................................................................................................. 24
5.4 Ground Concept........................................................................................................................... 24
6SW Interface......................................................................................................................25
6.1 Communication Protocol.............................................................................................................. 25
6.1.1 Command structure .............................................................................................................. 25
6.1.2ACK and NACK..................................................................................................................... 26
6.1.3 Timing constraints................................................................................................................. 26
6.2 Operational Commands ............................................................................................................... 26
6.2.1Distance measurement......................................................................................................... 26
6.2.2 Continuous distance measurement ...................................................................................... 27
6.2.3 Software versions, hardware configuration and serial number............................................. 28
6.2.4 Built-In Self Test.................................................................................................................... 29

LRF 3013 Integrator Manual
Document number: TML 913655 ver A
Public: 13.03.2017
Confidential & Proprietary Safran Vectronix AG –All rights reserved
page: 6/36
6.2.5 Low-Power Continuous Lasing Mode................................................................................... 30
6.3 Power on...................................................................................................................................... 30
7Maintenance......................................................................................................................31
7.1 Cleaning....................................................................................................................................... 31
7.2 Service ......................................................................................................................................... 31
7.2.1 Service Levels....................................................................................................................... 31
8LRF Interface Kit...............................................................................................................32
9Appendix...........................................................................................................................33
9.1 System Connector........................................................................................................................ 33
9.2 Mechanical Interface Drawing...................................................................................................... 35

LRF 3013 Integrator Manual
Document number: TML 913655 ver A
Public: 13.03.2017
Confidential & Proprietary Safran Vectronix AG –All rights reserved
page: 7/36
1 General
The LRF 3013 (Vectronix article number 913461) is the smallest and most lightweight member of
Vectronix’ LRF Modules family. It combines unsurpassed range performance with outstanding
robustness. The rangefinder module is class 1 eye-safe according to IEC 60825 and ANSI Z136.1 (2007).
1.1 Main Elements and functions of the LRF Module
1.1.1 Main parts
a receiver, containing electronics and a receiver diode
a transmitter, containing electronics and a transmitter laser diode
a mainboard which manages all electronic elements and calculates the results
stable aluminum bench including optics
Figure 1: LRF 3013 main parts (top view)
Figure 2: LRF 3013 main parts (bottom view)
Receiver
Transmitter
Mainboard
Bench
Receiver
optics
Transmitter optics
System connector
2x Positioning holes
3x threaded holes

LRF 3013 Integrator Manual
Document number: TML 913655 ver A
Public: 13.03.2017
Confidential & Proprietary Safran Vectronix AG –All rights reserved
page: 8/36
1.1.2 Interface parts
The mechanical interface of the LRF module base plate is defined by
Three point mounting base with three threaded holes
Two positioning holes
The electronic interface of the LRF module is defined by one system connector for
Power supply & Serial interface
2 LRF Background Information
2.1 Rangefinder Principle
2.1.1 The “Pulsed Diode”
When the laser rangefinder is activated, a series of laser pulses from the transmitter diode are sent
through the objective lens to the target. For a good
result, most of the laser pulses have to hit the target.
The main part of the laser light is absorbed or diffusely
reflected by the target and only very small percentage
of the light is reflected back to the LRF module. This
remaining laser light is received by the opposite
objective lens and focused on the receiver diode. The
receiver diode (detector) starts sampling its echo with
a very high frequency.
Figure 3 below indicates how laser pulses are emitted from the transmitter, reflected at the target and
sampled by the receiver.
Figure 3: Pulsed Diode –Laser Pulses
Measurement Example:
Measurement time (return flight) = 6.66 µs
Time of flight (one way)= 6.66 µs / 2 = 3.33 µs
Slope Distance r = light speed x time of flight
= 300’000 km/sec x 3.33 µs = 1’000 m

LRF 3013 Integrator Manual
Document number: TML 913655 ver A
Public: 13.03.2017
Confidential & Proprietary Safran Vectronix AG –All rights reserved
page: 9/36
The following Figure 4 illustrates the sampled signal of the receiver diode. This information is used to
calculate the distance.
Figure 4: Pulsed Diode –sampled signal at the receiver diode
2.1.2 Electronics
Vectronix range finding technology is based on semiconductor diode lasers in combination with a multi-
pulse measurement system. This allows pulses with low energy compared to a single high energy pulse.
2.1.3 Ranging Conditions
In general two kind of ranging conditions are described:
Range capability: The possible laser range performance on a beam filling target.
Range performance: The guaranteed range performance on a defined target under defined
conditions.
The range performance depends on visibility, target size and albedo (reflectivity) and is calculated relating
to a certain detection probability e.g. 90%.
Visibility
The visibility is the greatest distance from an observer where a prominent dark object against the sky at
the horizon can be seen and identified by an unaided eye. A high visibility allows the measuring of longer
ranges. Fog, snow, dust, sand, smog and rain reduce the visibility and therefore the range performance of
the LRF module.
Sunlight
Bright back light or high sunlight reflections on the target can reduce the range performance.
Object Size
A typical target size for range performance comparison is the NATO target with a similar size like the front
of a tank. The size of a NATO target is 2.3x2.3 m. Additionally, the LRF performance is defined on a man
size target with 1x1 m size.
Small targets reflect only a part of the laser beam and therefore only allow lower range performance.
A large target allows longer ranges because more of the laser light is returned to the LRF module.

LRF 3013 Integrator Manual
Document number: TML 913655 ver A
Public: 13.03.2017
Confidential & Proprietary Safran Vectronix AG –All rights reserved
page: 10/36
50 m 500 m 3000 m2000 m1000 m100 m
NATO (2.3x2.3m )
Man (1x1 m)
Laser beam
Figure 5.: Example of a 1 mrad laser beam size on target
Object Albedo
The albedo is the surface's reflectivity of an object, or rather is the ratio of reflected to incident light in the
wavelength of the LRF Module (1550 nm).
-> An object with a high albedo reflects more laser radiation and allows longer range performance. High
albedos on very short distances and low albedos on very long distances can either cause the LRF Module
to provide an invalid range measurement or is unable to find a target.
Object Orientation
The angle of the target in relation to the laser beam is also important. Similarly, targets with a very high
albedo can give only a very small reflection towards the LRF module when the reflected laser radiation is
not at 90° and reflected away, e.g. on water or pitched roofs.
-> 90° is optimal.
Object Hardness
The accuracy of “soft objects” like snow, smoke, clouds etc. depends on the condition of the object itself.
-> Hard objects allow a longer range and higher accuracy.
Mirror-like objects
The accuracy and range performance on mirror-like objects like water, glass surfaces or reflective traffic
signs can cause incorrect measurements or no measurement results at all.
-> Avoid mirror-like surfaces and aim at a target next to it.
Kinetic tremor
If the host system with an integrated LRF module is firmly installed or mounted (e.g. on a Tripod), longer
distances can be measured more easily. If the LRF module is shaking during a measurement, it can lead
to wrong or no measurement results. This is due to the fact that only a few pulses hit the target during the
measurement. The example below shows a laser beam with 1mrad divergence on targets in 1km
distance. The range measurement on the large NATO target is still OK, on the man size target it is lost.
-> Firmly mounted modules allow a longer range, e.g. on tripod.
NATO size (2.3x2.3 m)
Man size (1x1 m)
Laser beam
Figure 6.: Laser beam (1 mrad) on target (1’000 m) with kinetic tremor

LRF 3013 Integrator Manual
Document number: TML 913655 ver A
Public: 13.03.2017
Confidential & Proprietary Safran Vectronix AG –All rights reserved
page: 11/36
3 Getting Started
This chapter will help you with the first steps with a LRF module.
3.1 First steps with the LRF Interface Kit
We highly recommend using the LRF Interface Kit (see chapter 8) to connect your LRF
Module to your PC.
By following the steps below, you can perform your first measurements very quickly and
easily.
Figure 7: Setup of using LRF with the Universal Interface and PC
1. Plug the SafranVectronix-USB-Stick into your PC USB socket.
2. Open the “setup.exe” file on the USB-Stick.
Select your installation language (English selected as an example).
At the welcome screen, click “Next” to continue.
Choose the folder in which to install the software, either accepting the default option
or browsing for a folder. Click “Install” to continue.

LRF 3013 Integrator Manual
Document number: TML 913655 ver A
Public: 13.03.2017
Confidential & Proprietary Safran Vectronix AG –All rights reserved
page: 12/36
Click “Finish” to complete the setup program.
Read and either accept or decline the terms of use. If declined, the program will
abort.
If the terms of use are accepted, the demonstration program will load.

LRF 3013 Integrator Manual
Document number: TML 913655 ver A
Public: 13.03.2017
Confidential & Proprietary Safran Vectronix AG –All rights reserved
page: 13/36
3. Insert a fully charged 9 V battery into the Universal Interface or connect to it an external
power supply. Safran Vectronix recommends the use of an external power supply of approx.
12V DC / 3 A. When battery operated, only a limited number of measurements are possible.
USB socket –connection to PC
Connection to module (hard wired)
External power supply input –recommended 12V DC
4. Connect the Universal Interface to your PC via RS232 or USB.
5. Connect the Universal Interface to your LRF Module
6. Switch the Universal Interface on by pressing the “ON/OFF” button . The status indicator
light will illuminate, flashing approximately once per second showing that the LRF is being
powered. If the output voltage is not available, then the status indicator light will flash three
times per second.
The status indicator will also show the condition of the battery.
Green: battery voltage sufficient
Yellow: change battery –only short working time left
Red: battery voltage insufficient –output voltage to LRF will be disconnected
If the Error Indicator light shows:
a. Red. The external power is polarity reversed
b. Yellow. External voltage is above 30V and too high. The Universal Interface will turn
off automatically
A complete troubleshooting guide can be found in the Universal Interface short guide
supplied in the LRF Interface kit.

LRF 3013 Integrator Manual
Document number: TML 913655 ver A
Public: 13.03.2017
Confidential & Proprietary Safran Vectronix AG –All rights reserved
page: 14/36
3.2 Using the Safran Vectronix Terminal Software
To run a LRF Module with the Terminal Software, ensure that the Terminal Software is
installed on your PC and the LRF Module is connected correctly to your PC. The below
mentioned guide shows how to use the Terminal Software:
Select the module you are using from the drop down list.
Select the settings tab and select Interface.
Either set the settings manually and press OK or select “Search for LRF Module…”.
After making sure that you have connected and powered up the interface, selected
the right module, press “Start Search”

LRF 3013 Integrator Manual
Document number: TML 913655 ver A
Public: 13.03.2017
Confidential & Proprietary Safran Vectronix AG –All rights reserved
page: 15/36
Module Found
Module not found
If the module is found, press OK and the correct interface values are saved. If not
found, try once more. If the module is still not found, enter the interface values
manually.
Press OK to return to the main screen.
Press “Connect”. The “Connect” button will change color.
Use the commands as required. Note that the commands change depending on the
model chosen. Make sure you have selected the right module in stage .
The response from the LRF will be shown in the dialog box.
Note: You can use the symbol to clear the log.

LRF 3013 Integrator Manual
Document number: TML 913655 ver A
Public: 13.03.2017
Confidential & Proprietary Safran Vectronix AG –All rights reserved
page: 16/36
3.3 First steps without LRF Interface Kit
LRF modules can be connected to your PC without an Interface box. In this case we recommend reading
this manual carefully before using the LRF module. Please be aware of the risk of wrong pin-connection
or destroying the module by applying overvoltage and other errors.
For the correct pin configuration see chapter 5.1
Power supply must not exceed the range of 4.5…16 V
The default Baud rate for LRF 3013 modules is 57’600 Bd
First range measurements can be performed by sending the software commands “>Md1<CR>” to the LRF
module. To achieve a valid range result, aim at targets of at least 30 m distance and ensure that you hit
the target and that no obstacles like closed windows are between the LRF and the target.
3.4 Checklist in case of problems with LRF modules
- Check if the Universal Interface battery is fully charged.
- Check if the COM-Port in the Terminal Software is the same as the COM-Port to
which the Universal Interface is connected.
- Ensure that power is supplied to the correct LRF module pins (see chapter 5.1).
- Check if Baudrate is set to 57’600.

LRF 3013 Integrator Manual
Document number: TML 913655 ver A
Public: 13.03.2017
Confidential & Proprietary Safran Vectronix AG –All rights reserved
page: 17/36
4 Integration
4.1 Mechanical Mounting & Handling
Open the packaging:
Be careful with ESD: The LRF module is sensitive to electrostatic discharge. Do not touch any
electronics or components unless protective measures are applied.
Be careful with EMC: To avoid / reduce noise emittance, noise susceptibility and coupling
between sources and receptors, the LRF module shall be mounted inside an electrical shielded
housing. EMC disturbance can cause wrong or no measurement results.
Be careful with optics: scratches and fingerprints on the optics will reduce range performance.
Front glass to mechanical part is not sealed and is therefore not gas or water tight.
Remove stickers on bench holes only before flushing the air out of the system, so that nitrogen
also fills the optical system of the LRF module.
4.2 Design recommendations
The mechanical interface drawing of LRF 3013 can be found in the appendix (chapter 9.2).
4.2.1 Preparation
The surface that the LRF module will be mounted on must be equally flat or preferable better than the
surface represented by the LRF’s mounting pads. Please refer to the mechanical drawing in your LRF
package.
Tolerance of the positioning pins is recommended to be h6.
The tolerance of the positioning holes in the bench is H8.
All material inside the host system is recommended to be black matte, to avoid optical cross coupling
between the transmitter’s and receiver’s optical channels.
4.2.2 Mounting
When mounting the module onto the positioning pins, the module’s positioning pin holes must be aligned
sufficiently well to the mating positioning pins, to avoid damage of the positioning holes.
The three screws must be tightened with a torque of 60 Ncm. The screws shall be made of steel A2.
The laser beam is aligned to the mechanical interface with a tolerance of ±3 mrad. The host
system must allow the LRF module to align with the tolerance of ±3 mrad to its main optical
axis.

LRF 3013 Integrator Manual
Document number: TML 913655 ver A
Public: 13.03.2017
Confidential & Proprietary Safran Vectronix AG –All rights reserved
page: 18/36
Mechanical stress due to tolerance and thermal expansion coefficient mismatches between the
module’s and application‘s mechanical interface should be avoided as much as possible. An
undefined stress could result in a misalignment of the module’s transmitter and receiver
channel and reduces the range performance.
Assembly personnel must be experienced in handling precision, sensitive electronic,
mechanical and optical assemblies.
Vibration and shocks outside the specified values can destroy or shift parts inside the LRF in a
way that proper use is no longer possible.
4.2.3 Boresighting
The module receiver and transmitter are boresighted in the factory. For this reason, the module and can
be mounted and replaced easily. For a professional boresighting of the LRF module with the main optical
axis of the host system, we recommend the use of a collimator and a camera that can see the 1’550 nm
wavelength of the laser module. Vendors of 1’550 nm cameras (SWIR cameras):
XenICs (www.xenics.com) (e.g. XEVA-1.7-320)
Sensors Unlimited (www.sensorsinc.com) (e.g. 640HS-1.7RT)
Allied Vision Technologies (www.alliedvisiontec.com) (e.g. Goldeye P-008 SWIR)
Collimators can be sourced from Möller Wedel Opical (http://www.moeller-wedel-optical.com).
Note: The LRF module provides a low power continuous lasing mode to make its line of sight visible to
SWIR cameras. Please see chapter 6.2.5 for details.
Figure 8 below illustrates the alignment set-up with a collimator and 1550 nm camera.
Figure 8: Alignment Set-up with collimator and 1550 nm camera
1550 nm
Camera
Screen
Host System
LRF module
Main optical axis
Collimator

LRF 3013 Integrator Manual
Document number: TML 913655 ver A
Public: 13.03.2017
Confidential & Proprietary Safran Vectronix AG –All rights reserved
page: 19/36
If such equipment is not available, an alternative method can be used to show
the path of the invisible laser light. Place a vertical and horizontal small pole
(approx. 10 cm of width) at several hundred meters distance. Start with one
orientation (horizontal or vertical) and measure until the laser hits the pole
and gives the correct distance back. You can then center the laser to this first
orientation and then do the same with the second orientation. With this
method you can align the laser to any equipment, however its more time
consuming and not as precise as with a camera.
A quick and easy tool to make laser light visible are laser viewing cards. Those cards have a
photosensitive area which emits a visible spot at the location of the laser beam. However, this only works
when the card is quite close to the LRF module. To see the laser beam of LRF 3013 modules, the laser
viewing card must absorb light of 1550 nm wavelength. Vendors of such cards are:
Laser2000 (www.laser2000.de) (e.g. QTX-Q42-T)
Thor Labs (www.thorlabs.de) (e.g. VCR4)
Please see the mechanical ICD in the appendix 9.2 to determine the required mechanical tolerances for
alignment.
4.2.4 Nitrogen flushing
To avoid condensation of humidity in the optical system, the module is recommended to be operated in a
‘dry’ atmosphere inside a housing. Several ventilation holes may be provided in the mechanical system
holding the optics, which are covered by small pieces of tape. The pieces of tape are intended to avoid
dust penetrating the optical system and should be removed just before the application is sealed and
purged. With respect to dust, the unit is recommended to be handled observing standard practices for
sensitive optical components and assembly procedures.
4.3 Front Protection
The LRF module itself is not gas tight. Therefore implementing an LRF module into a host system
requires a protecting environment with a protective window in front of the LRF module.
The laser diode emits laser light towards the objective lens. This lens sends out a mainly parallel beam,
with some angular spread called beam divergence.
Care has to be taken, that there is no substantial absorption of the laser energy at 1’550 nm wavelength.
Standard optical quality glass should be used, the material of the window needs to be transparent for the
1’550 nm wavelength (i.e. BK7 from Schott).
The antireflection coating of the window is recommended to be “broadband”, in other words, effective for
visible light as well as for the laser wavelength. Choosing a narrow band must also allow the transmission
of temperature shifted laser light (e.g. 1’550 nm = 1’500 ...1’600 nm depending on temperature).
If the coating reflects visible light, one will not see inside the LRF module, which is not a problem, but it
can appear like a mirror and reflect a lot of sunlight.
The coating should fulfill the following specs:
visible light: R < 1 % for lambda = 420 ... 650 nm, light angle 0°+/- 15°
If this is not fulfilled, you have an optical mirror. However, it is the decision of the system
integrator to specify transmission for visible light of the front windows.
laser light: R < 0.5 % for lambda = 1’500 ...1’600 nm, light angle 0°+/- 15°
If this is not fulfilled, the laser energy is reduced and internally reflected. This can cause optical
cross talk and lead to incorrect or no measurement results.
Figure 9: Boresighting

LRF 3013 Integrator Manual
Document number: TML 913655 ver A
Public: 13.03.2017
Confidential & Proprietary Safran Vectronix AG –All rights reserved
page: 20/36
It is recommended to use 2 separate windows, one for the receiver channel and one for the transmitter
channel. Both windows should be sufficiently flat. A window with poor flatness will lead to a boresight
issue, resulting in a reduction of achievable range performance.
In addition, the optical Rx & Tx channels must be optically isolated from each other. This is required to
prevent optical cross talk between both channels (scattered laser light from transmitter to receiver). The
two windows have to be aligned with a wedge error of less than 10 seconds of arc.
Figure 10: Tilted window (view from side)
Figure 11: Optical isolation of transmitter and receiver
To avoid sunlight reflections on the front window which can be seen by others, a tilt angle of 5°-10°
downwards can be implemented. The LRF Module itself does not require a tilt angle, range performance
can be achieved with a 0° tilt angle.
4.4 Eye Safety
LRF 3013 meets Class 1 eye safety requirements according to IEC 60825 and ANSI Z136.1. The eye
safety of the host system has to be tested and guaranteed at the system level by the OEM system
integrator. To meet Class 1 requirements on system level, mind the maximum measurement repetition
rate of 2 Hz (details can be found in chapter 6.2.2).
Table of contents
Other Safran Measuring Instrument manuals
Popular Measuring Instrument manuals by other brands
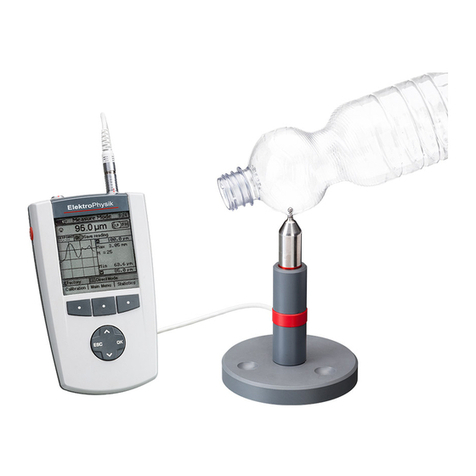
ElektroPhysik
ElektroPhysik MiniTest 7200 FH Technical manual and operating instructions
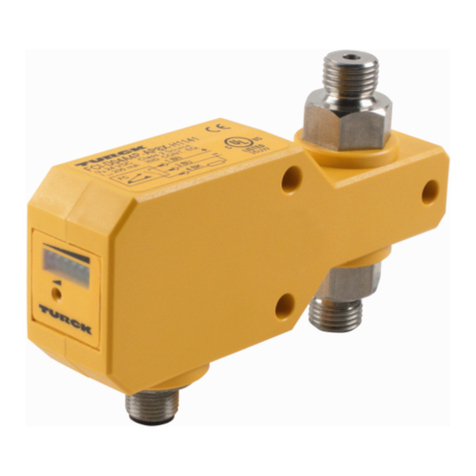
turck
turck FCI-X-H114 Series quick start guide
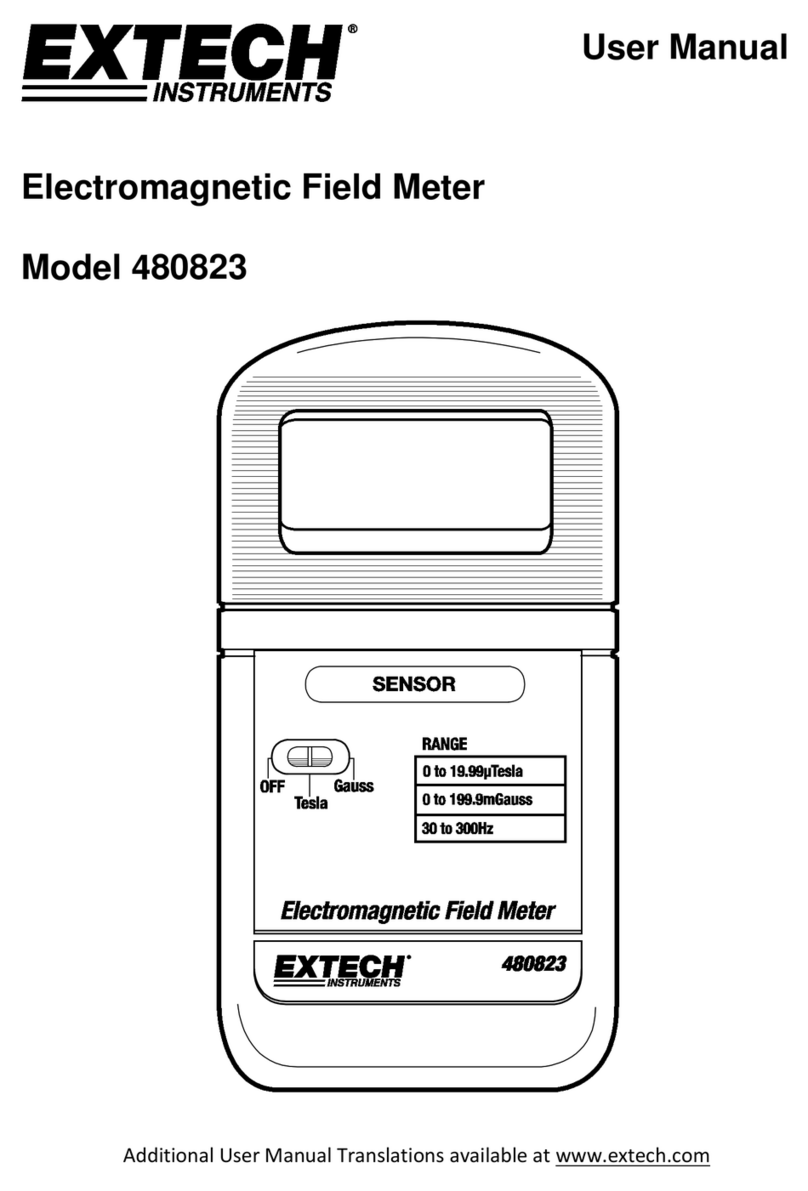
Extech Instruments
Extech Instruments 480823 user manual

CARLO GAVAZZI
CARLO GAVAZZI EM24DINAV53XE1SFB user manual
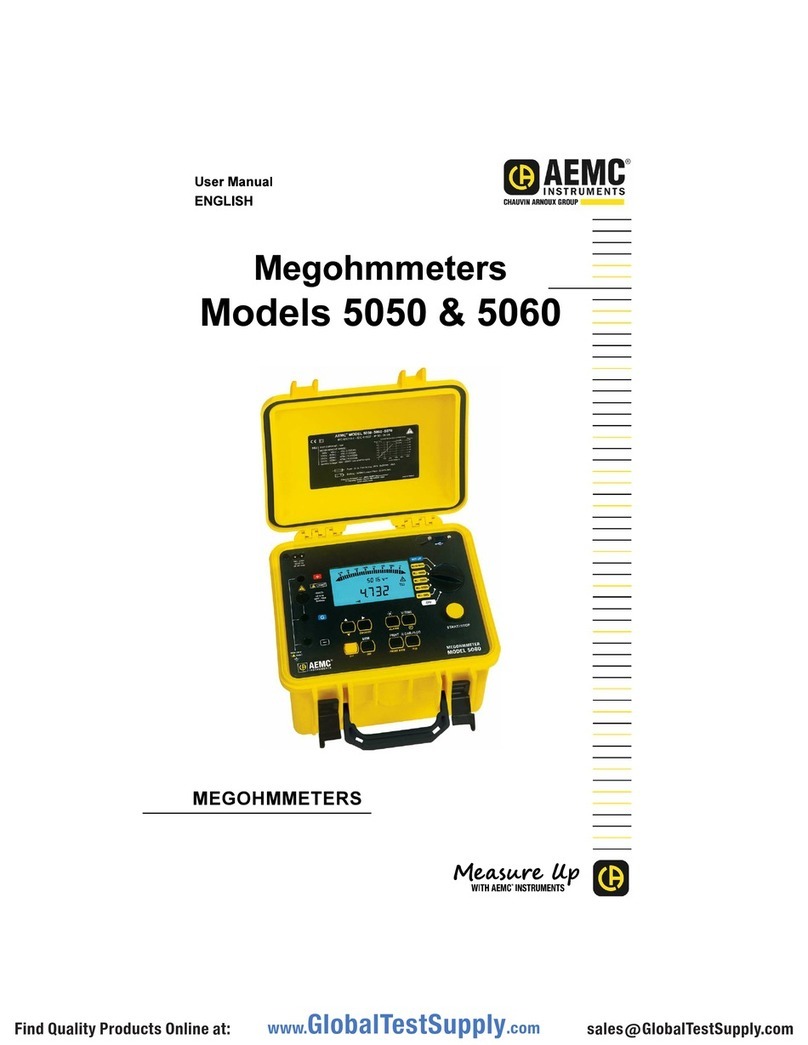
AEMC instruments
AEMC instruments 5050 user manual
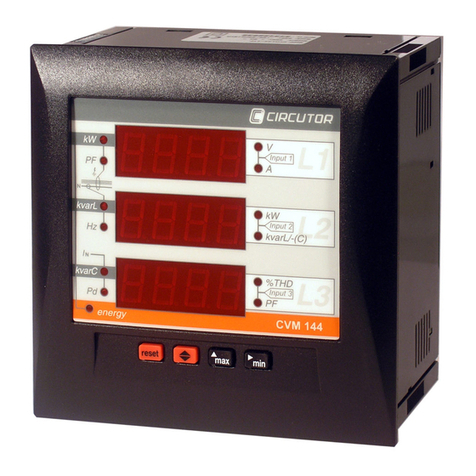
Circutor
Circutor CVM-144 (HAR) user manual