SAS ST-550 zPID User manual


User’s manual
2
Tabel of contents
I. Safety ............................................................................................................................... 4
II. Description of the device ..................................................................................................... 5
III. Installation ...................................................................................................................... 5
IV. How to use the controller .................................................................................................. 8
IV.1. Principle of operation .................................................................................................. 8
IV.2. Stages of operation .................................................................................................... 8
IV.3. zPID control .............................................................................................................. 8
IV.4. Controller operation without zPID control ...................................................................... 9
IV.5. How to navigate....................................................................................................... 10
V. Controller functions– main menu ........................................................................................ 10
V.1. Block diagram of the main menu................................................................................... 10
V. 2. Fire-up....................................................................................................................... 12
V. 3. Screen view................................................................................................................ 12
V. 4. Fuel tank full .............................................................................................................. 12
V. 5. Temperature settings................................................................................................... 12
V. 5.a) Pre-set CH temperature ......................................................................................... 12
V. 5.b) CH hysteresis ....................................................................................................... 12
V. 5.c) Pre-set DHW temperature ...................................................................................... 12
V. 5.d) DHW hysteresis .................................................................................................... 12
V. 5.e) Temperature of pump activation.............................................................................. 12
V. 5.f) Pre-set room temperature...................................................................................... 13
V. 6. Manual mode.............................................................................................................. 13
V. 7. Operation settings....................................................................................................... 13
V. 7.a) Feeding time ........................................................................................................ 13
V. 7.b) Pause time ........................................................................................................... 13
V. 7.c) Blow force............................................................................................................ 13
V. 7.d) Operation in sustain mode ..................................................................................... 13
V. 7.e) Pause in sustain mode ........................................................................................... 13
V. 7.f) Fan in sustain mode .............................................................................................. 13
V.7.g) Fan speed in sustain mode ..................................................................................... 13
V. 8. Fuel granulation .......................................................................................................... 13
V. 9. Operation modes......................................................................................................... 14
V. 9.a) House heating ...................................................................................................... 14
V. 9.b) Water tank priority ................................................................................................ 14
V. 9.c) Parallel pumps ...................................................................................................... 14
V. 9.d) Summer mode...................................................................................................... 14
V. 10.Weekly control ......................................................................................................... 14
V. 11.Operation algorithm selection .................................................................................... 15
V. 12.Fitter’s menu ........................................................................................................... 15
V. 13.Service menu .......................................................................................................... 15
V. 14.Software version ...................................................................................................... 15
V. 14.a) Software update ................................................................................................ 16
V. 15.Factory settings ....................................................................................................... 16

ST-550 zPID
3
VI. Controller functions - Fitter’s menu................................................................................... 16
VI.1. PID coefficient ......................................................................................................... 18
VI.1.a)CH boiler power coefficient .................................................................................. 18
VI.1.b) Fan correction bottom / Fan correction top ............................................................ 18
VI.2. PID supervision........................................................................................................ 18
VI.3. Buffer parameters .................................................................................................... 18
VI.3.a) Buffer............................................................................................................... 18
VI.3.b) DHW function .................................................................................................... 18
VI.3.c) Pre-set temperature top...................................................................................... 19
VI.3.d) Pre-set temperature bottom ................................................................................ 19
VI.4. Valve settings .......................................................................................................... 19
VI.4.a) Built-in valve, Additional valve 1 and 2 ................................................................. 19
VI.5. Additional pump 1 / Additional pump 2 ....................................................................... 23
VI.5.a) Algorithm selection ............................................................................................ 23
VI.5.b) Short circuit pump ............................................................................................. 23
VI.5.c) Floor pump ....................................................................................................... 23
VI.5.d) Circulating pump................................................................................................ 23
VI.6. Time settings........................................................................................................... 24
VI.7. Date settings ........................................................................................................... 24
VI.8. Internet module....................................................................................................... 24
VI.9. Fuel level calibration................................................................................................. 27
VI.10.Language ................................................................................................................ 28
VI.11.Room regulator........................................................................................................ 28
VI.12.External temperature correction................................................................................. 28
VI.13.GSM module............................................................................................................ 28
VI.14.Factory settings ....................................................................................................... 29
VII. ST-66P pellet module...................................................................................................... 29
VIII. Protections ................................................................................................................. 32
VIII.1. Temperature alarm................................................................................................ 33
VIII.2. Thermal protection of CH boiler (STB) ..................................................................... 33
VIII.3. Automatic sensor control ....................................................................................... 33
VIII.4. Protection against boiling of water in the CH boiler.................................................... 33
VIII.5. Temperature protection.......................................................................................... 33
VIII.6. Fuel feeder protection............................................................................................ 33
VIII.7. Limt switch in the fuel tank .................................................................................... 33
VIII.8. Fuse .................................................................................................................... 33
IX. Maintenance .................................................................................................................. 34

User’s manual
4
I. Safety
Before using the device for the first time the user should read the following regulations carefully. Not
obeying the rules included in this manual may lead to personal injuries or controller damage. The user’s
manual should be stored in a safe place for further reference. In order to avoid accidents and errors it
should be ensured that every person using the device has familiarized themselves with the principle of
operation as well as security functions of the controller. If the device is to be sold or put in a different
place, make sure that the user’s manual is there with the device so that any potential user has access to
essential information about the device.
The manufacturer does not accept responsibility for any injuries or damage resulting from negligence;
therefore, users are obliged to take the necessary safety measures listed in this manual to protect their
lives and property.
WARNING
•High voltage! Make sure the regulator is disconnected from the mains before performing any
activities involving the power supply (plugging cables, installing the device etc.)
•The device should be installed by a qualified electrician.
•Before starting the controller, the user shoud measure earthing resistance of the electric motors
as well as the insulation resistance of the cables.
•The regulator should not be operated by children.
WARNING
•The device may be damaged if struck by a lightning. Make sure the plug is discon-
nected from the power supply during storm.
•Any use other than specified by the manufacturer is forbidden.
•Before and during the heating season, the controller should be checked for condition of its ca-
bles. The user should also check if the controller is properly mounted and clean it if dusty or
dirty.
Changes in the merchandise described in the manual may have been introduced subsequent to its
completion on August 25th 2016. The manufacturer retains the right to introduce changes to the
structure. The illustrations may include additional equipment. Print technology may result in differences
in colours shown..
We are committed to protecting the environment. Manufacturing electronic devices
imposes an obligation of providing for environmentally safe disposal of used electronic
components and devices. Hence, we have been entered into a register kept by the
Inspection For Environmental Protection. The crossed-out bin symbol on a product
means that the product may not be disposed of to household waste containers.
Recycling of wastes helps to protect the environment. The user is obliged to transfer
their used equipment to a collection point where all electric and electronic components
will be recycled.

ST-550 zPID
5
II. Description of the device
ST–550zPID temperature regulator is intended to control CH boiler with a screw feeder. Due to its
advanced software it offers a range of functions:
•Control of the fan and the feeder
•Control of CH pump
•Control of DHW pump
•Control of two additional pumps
•Control of two mixing valves actuators
•Possibility of connecting a room regulator with traditional or RS communication
•Possibility of connecting ST-65 GSM module
•Built-in Ethernet module enabling the user to view certain parameters and control
certain functions via the Internet
•Possibility of controlling two valves via additional modules (e.g. ST-431N)
Controller equipment:
•CH temperature sensor
•Feeder temperature sensor (protection)
•Floor temperature sensor
•DHW sensor
•Temperature protection (bimetallic mini sensor)
•Supply cable
•Pump supply cables
•Hall-sensor of the fan
•Feeder flap limit switch
III. Installation
The controller should be installed by a qualified person.
WARNING
Risk of fatal electric shock from touching live connections. Before working on the controller
switch off the power supply and prevent it from being accidentally switched on.
WARNING
Incorrect connection of the wires may lead to controller damage!

User’s manual
6

ST-550 zPID
7

User’s manual
8
IV. How to use the controller
IV.1. Principle of operation
The regulator controls the fan and the fuel feeder operation so that the pre-set temperature of the CH
boiler and the water tank is reached. Additionally, it controls CH and DHW pump operation activating
them once a pre-defined temperature of the CH boiler has been reached.
IV.2. Stages of operation
Fire-up – this phase is initiated when the flue gas temperature reaches a pre-set value and does not
drop below this value for 30seconds (default fire-up time).
Operation – when the fire-up phase has been completed, the controller enters operation mode and the
display shows the message ‘PID: OPERATION’. It is the primary mode of controller functioning when the
blow force and fuel feeding are regulated with PID algorithm, oscillating around the pre-set temperature
defined by the user. When the temperature increases unexpectedly by more than 5oC above the pre-set
value, the supervision mode is activated.
Supervision mode – this mode is activated automatically when the temperature exceeds the pre-set
value by more than 5oC in operation mode. In such a case, the controller disables PID control and uses
manual settings (according to parameters defined in the fitter's menu).The display shows the following
message: ‘PID: SUPERVISION’
IV.3. zPID control
ST-550zPID is a controller with continuous output signal, using zPID algorithm. This type of controller
calculates the blow force on the basis of CH boiler temperature and the flue gas temperature measured
at the CH boiler outlet. The fan operates continuously and the blow force depends on the CH boiler
temperature, the flue gas temperature as well as the difference between these parameters and their pre-
set values. One of the greatest advantages of zPID regulators is their ability to maintain a stable pre-set
temperature without unnecessary overregulation and oscillations.
Apart from zPID control, the controller operation is adjusted on the basis of the the readings from
the air flow sensor mounted on the fan.
Using this type of regulator with a flue gas sensor helps to reduce fuel costs by up to several percent.
Moreover, it ensures stable temperature of output water thus prolonging the life of the heat exchanger
(of the CH boiler). Flue gas temperature control results in low emission of dust and environmentally
harmful gases. Flue gas heat is not disposed of through the chimney, but it is utilised for heating
purposes.
TEST RESULTS - TECH controller with PID control:

ST-550 zPID
9
TEST RESULTS - TECH controller without PID control:
IV.4. Controller operation without zPID control
zPID control may be disabled at any time using Operation algorithm selection parameter.
Additional submenu will appear in the controller menu, allowing the user to configure boiler operation
parameters.
Once zPID control is disabled, the principle of operation is changed - after the fire-up stage the
controller enters operation mode which is followed by sustain mode:
Operation – once the controller is switched on, it enters operation mode and OPERATION appears on
the display. It is the primary mode of controller operation in which the fan operates continuously and the
fuel feeder operation is adjusted according to user’s settings. The user defines both the operation time
and pause time.
Sustain mode – this mode is activated automatically if the temperature is equal or higher than the pre-
set temperature value. Fuel feeding process slows down in order to smoothly reduce the temperature of
the circulating water. SUSTAIN appears on the display. In order for the temperature to decrease properly,
it is necessary to configure operation and pause time in sustain mode as well as the fan speed.

User’s manual
10
IV.5. How to navigate
During standard operation of the controller, graphic display shows the main page.
By pressing MENU button the user enters the first level menu. In order to move on to the next option,
twist the pulser knob. Press the knob to select an option. Follow a similar procedure when adjusting
parameters. In order for the changes to be saved, use the pulser knob to select CONFIRM. In order not
to introduce any changes, use the pulser knob to select CANCEL. In order to leave the menu, use EXIT
button.
1. USB port
2. Panel showing current parameters of the sensors and the fan
3. CH boiler operation stage
4. Current time
5. Right parameter panel – use pulser knob to switch between CH boiler parameters and DHW or
valve parameters (if activated).
6. Operation status bar - it displays icons indicating all devices which are currently active:
- fan and its speed (%); if Hall sensor of the fan is active, letter H is displayed;
- feeder; if burning without feeder option is active, a crossed out feeder icon is displayed.
- CH pump
- DHW pump
- additional pump 1
- additional pump 2
7. Enter the controller menu. While viewing the controller functions use this button to return to the
main screen view.
8. Pulser knob. Twist the knob in the main screen view to change the parameter view or press it to
edit the selected parameter. While viewing the menu options use the knob to move on to the next
function or configure CH boiler operation parameters.
9. EXIT button
10. Active operation panel bar:
- CH boiler
- DHW
- built-in valve (if switched on)
- additional valves (if switched on; additional valve modules e.g. ST-431N are required).
V. Controller functions– main menu
V.1. Block diagram of the main menu.
Due to multiple functions offered by the controller, the menu is divided into Main Menu and Fitter’s Menu.
The main menu allows the user to set the basic controller options such as pre-set temperature values,
operation modes, screen view etc.
6
7
5
4
3
2
1
10
8
9

ST-550 zPID
11
*Parameters available in the controller menu only if the additional valve module has been connected and
module registration process has been completed in the additional valve menu.
**Submenu available only if Operation without PID is selected.
***Parameter available only if TECH room regulator with RS communication has been connected and
activated.
Main menu
Fire-up
Screen view Standard screen
Test screen
Fuel tank full
Temperature settings
Pre-set CH temperature
CH hysteresis
Pre-set DHW temperature
DHW hysteresis
Pump activation temperature
Pre-set room temperature***
Manual mode
Fan
Blow force
Feeder
CH pump
DHW pump
Additional pump 1
Additional pump 2
Built-in valve 1
Built-in valve 2
Additional valve 1*
Additional valve 2*
Operation settings**
Feeding time
Pause time
Blow force
Operation in sustain mode
Pause in sustain mode
Fan in sustain mode
Fan speed in sustain mode
Fuel granulation Fine granulation
Coarse granulation
Operation modes
House heating
Water tank priority
Parallel pumps
Summer mode
Weekly control
Mode
Set mode 1
Set mode 2
Delete settings
Operation algorithm PID
Operation without PID
Fitter’s menu
Service menu
Software version
Factory settings

User’s manual
12
V.2. Fire-up
This function enables the user to easily fire-up the CH boiler. After initiating the fire manually (preparing
the furnace and starting the fire), the user activates automatic fire-up phase in the controller menu. The
controller conducts the fire-up process maintaining the blow and gradually feeding fuel. Thanks to
optimum parameters, CH boiler smoothly switches to operation mode.
Once the CH boiler entered operation mode, instead of Fire-up function the menu displays
Damping function, which may be used to activate damping process.
V.3. Screen view
This function is used to choose between standard screen view and test screen view (secured with a code).
V.4. Fuel tank full
This function should be used after the fuel tank has been fully filled, in order to reset the fuel consumption
percentage to 100% (the value displayed in the top right-hand corner of the main screen, below the
clock).
NOTE:
Before using this function for the first time it is necessary to calibrate the fuel feeder operation
in the fitter’s menu.
V.5. Temperature settings
V.5.a) Pre-set CH temperature
This option is used to define the pre-set CH boiler temperature. The setting rage is 45⁰C do 80⁰C.
The pre-set temperature may also be changed with the use of weekly control function. The pre-
set temperature is the sum of all these values but within the range of 45⁰C do 80⁰C.
V.5.b) CH hysteresis
This option is used to set the hysteresis of the pre-set temperature. It is the difference between the
temperature of entering the sustain mode and the temperature of restoring operation mode (for example:
when the pre-set temperature is 60 ºC, the hysteresis is 3ºC, entering sustain mode takes place at the
temperature of 60 ºC whereas returning to the operation mode takes place at 57 ºC).
V.5.c) Pre-set DHW temperature
This function is used to define the pre-set temperature of the domestic water (this function is inactive
when house heating mode is selected). This value may be adjusted directly from the main screen view.
After the tank water reaches this temperature, DHW pump is disabled. The pump will be enabled again
when the temperature drops below the pre-set temperature by a pre-defined value.
V.5.d) DHW hysteresis
This option is used to set the hysteresis of the pre-set water tank temperature. It is the difference
between the pre-set temperature (desired temp. of the water tank when DHW pump is switched off) and
the temperature at which DHW pump is activated again (for example: when the pre-set temperature is
55 ºC, the hysteresis is 5ºC, DHW pump is switched off and CH pump is enabled when the pre-set
temperature of 55 ºC is reached. DHW pump is activated again when the temperature drops to 50 ºC).
V.5.e) Temperature of pump activation
This option is used to define the temperature of CH pump and DHW pump activation (temperature
measured on the CH boiler). Below this temperature value both pumps remain inactive whereas above
this value the pumps are enabled and operate according to the operation mode (see: pump operation
modes).

ST-550 zPID
13
V.5.f) Pre-set room temperature
Once a room regulator with RS communication has been connected and activated in the controller menu
(Fitter’s menu/Room regulator), the user may adjust the pre-set room temperature.
V.6. Manual mode
For the user's convenience, the regulator offers manual mode function. In this function, each executive
device may be activated and deactivated independently of others. It is an easy way of checking if the
following devices work properly: feeder, blow (fan), CH pump, DHW pump, additional pump 1, additional
pump 2, built-in valve1, built-in valve 2, valve 1, valve 2). Additionally, the user may adjust the fan speed
in manual operation mode using blow force function.
V.7. Operation settings
NOTE: This submenu is available only when PID control is disabled - see: Controller operation
without zPID control.
V.7.a) Feeding time
This option is used to set the operation time of the fuel feeder. It should be adjusted to the type of fuel
and CH boiler used.
V.7.b) Pause time
This option is used to set the pause time of the feeder. The length of the pause should be adjusted to
the type of fuel used.
Incorrect pause time may result in inefficient operation of the CH boiler, i.e. unburnt coal left or failure
to reach the pre-set temperature of the CH boiler. Appropriate pause time ensures efficient operation of
the CH boiler.
V.7.c) Blow force
This function is used to control the fan speed. The setting range is 1-100% (it may be regarded as fan
gears). The higher the gear is, the faster the fan works. 10% is the minimum fan speed whereas 100%
is the maximum fan speed.
Initially the fan always operates at a full speed, which enables successful activation even if the
motor is dusty.
V.7.d) Operation in sustain mode
This option is used to set the operation time of the feeder and the fan when the CH boiler operates in
sustain mode.
V.7.e) Pause in sustain mode
This option is used to set the fuel feeding pause time when the CH boiler operates in sustain mode.
Incorrect setting of pause and operation time may result in farther temperature increase, unintended CH
boiler damping or lead to fuel ignition hazard in the fuel tank.
V.7.f) Fan in sustain mode
This option is used to set the fan operation and pause time in sustain mode.
V.7.g) Fan speed in sustain mode
This option is used to set appropriate fan gear (blow force) in sustain mode.
V.8. Fuel granulation
This function is used to choose one of the two levels of fuel granulation: coarse or fine. For each level
there is suitable blow force and fuel feeding frequency programmed.

User’s manual
14
V.9. Operation modes
V.9.a) House heating
When this function is selected, only the house is heated. CH pump is activated when the temperature is
above the pump activation threshold (factory setting). Below this temperature value (minus 2OC –
hysteresis) the pump is disabled.
V.9.b) Water tank priority
In this mode, the DHW pump is activated first and it operates until the pre-set DHW temperature is
reached. After the pre-set temperature has been reached, the pump is switched off and the CH pump is
activated.
CH pump operates continuously until the water tank temperature drops below the pre-set value
minus DHW hysteresis. Then, the CH pump is disabled and the DHW pump is activated.
In this mode, the fan and the feeder operation is limited to 72 OC at the CH boiler in order to prevent the
CH boiler from overheating.
WARNING:
Return valves should be installed on the circuits of the CH and DHW pumps. The valve on
DHW pump prevents hot water from being sucked out of the water tank.
V.9.c) Parallel pumps
In this mode, both pumps are activated simultaneously above the pre-set activation temperature (default
setting: 40 ºC).
CH pump operates all the time whereas DHW pump is disabled when the pre-set water tank temperature
is reached.
V.9.d) Summer mode
In this mode, CH pump is switched off and DHW pump is enabled above the pump activation threshold
(default setting: 40OC) and operates all the time above this threshold.
In summer mode the user defines only the pre-set temperature of the CH boiler which heats the
domestic hot water (this value also serves as the pre-set water tank temperature). After this function
has been activated, the screen displays current CH temperature and two DHW temperature values (the
current temperature value and the pre-set one).
V.10. Weekly control
Weekly control function enables the user to program changes of the pre-set CH boiler temperature
(CH weekly control) or water tank temperature (DHW weekly control) for particular hours and days of
the week.
In order to activate this function, select mode 1 or mode 2. Detailed settings of each mode are
available further in the submenu: Set mode 1 and Set mode 2.
Once a given mode is selected, the main screen displays the value of current temperature deviation
(below the pre-set CH temperature, alternately with Pre-set) informing the user that the function is
active.
How to change weekly control settings:
ST-491 controller enables the user to program weekly control function in two modes:
MODE 1 – the user sets the temperature deviations for each day of the week separately;
MODE 2 – the user sets the temperature deviations for all working days (Monday-Friday) and for the
weekend (Saturday-Sunday) separately.
How to configure mode 1:
In order to configure mode 1, select Set mode 1 – the display shows the panel with particular days of
the week.
Once a given day of the week is selected, the screen shows the editing panel – the upper line shows
current deviation, the lower line shows the time period. Twist the pulser knob to change the time
period. In order to edit the deviation value, press the pulser knob and select Change.
In order to copy the setting for the next time period, press the pulser knob and select Copy.

ST-550 zPID
15
Example:
Monday
set: 300 AM, temp -100C (weekly control setting– 100C)
set: 4 00 AM, temp -100C (weekly control setting– 100C)
set: 5 00 AM, temp -100C (weekly control setting– 100C)
In this case, if the pre-set temperature of the CH boiler is 600C, from 300 AM to 600 AM on
Monday the pre-set temperature will drop by 100C, so it will be 500C.
How to configure mode 2:
In order to configure mode 2, select Set mode 2 – the display shows a panel with two day groups –
Monday-Friday and Saturday-Sunday. Select the group to be edited and follow the same procedure as
with mode 1.
Example:
Monday-Friday
set: 3 00 AM, temp -100C (weekly control setting – 100C)
set: 4 00 AM, temp -100C (weekly control setting – 100C)
set: 5 00 AM , temp -100C (weekly control setting – 100C)
Saturday-Sunday
set: 4 00 PM, temp 50C (weekly control setting +50C)
set: 5 00 PM, temp 50C (weekly control setting +50C)
set: 6 00 PM, temp 50C (weekly control setting +50C)
In this case, if the pre-set temperature of the CH boiler is 600C, on each weekday (Monday –
Friday) from 300AM to 600AM the pre-set temperature will drop by 100C, so it will be 500C. During the
weekend, from 4 00 PM to 7 00 PM the pre-set temperature of the CH boiler will increase by 50C, so it will
be 650C.
NOTE
In order for the weekly control to function properly it is necessary to set current time and
day of the week in Fitter’s menu >> Clock.
Delete data
This function enables the user to delete all weekly control settings.
V.11. Operation algorithm selection
This function is used to select the operation algorithm. If the user does not want to use zPID control
function, it may be disabled by selecting Operation without PID.
V.12. Fitter’s menu
Functions available in this menu are described in detail in the following sections of this manual.
V.13. Service menu
In order to enter the service menu of ST-550zPID controller, it is necessary to enter a 4-digit code
provided by TECH company staff.
V.14. Software version
W funkcji tej użytkownik może sprawdzić jaką wersję programu posiada sterownik. Po przekręceniu
impulsatora na ekranie wyświetlona zostanie informacja o wersji programowej modułów dodatkowych
sterujących zaworem.

User’s manual
16
V.14.a) Software update
•Software update should be conducted when the CH boiler is damped.
•The memory stick which is going to be used to save the set-up file should be empty (prefer-
ably formatted)
•Make sure that the file saved on the memory stick has exactly the same name as the down-
loaded file so that it is not overwritten.
Insert the memory stick with the software into the controller USB port.
Reset the device by unplugging it and plugging it back in.
When the controller starts again, wait until the software update process starts.
oOnce restarted, the controller display shows the starting screen.
oSoftware update starts automatically.
oDuring installation process colourful stripes appear on the screen illustrating the installation
progress.
oOnce the installation process is completed, the display shows the main screen.
Once the software update has been completed, you can remove the memory stick from the USB
port.
The software update of ST-66P module may be conducted in a similar way by inserting the memory
stick with the software into the USB port of the additional module.
V.15. Factory settings
The controller is pre-configured for operation. However, the settings should be customized to the user's
needs. Return to factory settings is possible at any time. When the factory settings option is activated,
all customized settings of the CH boiler (saved in the user's menu) are lost and replaced with the
manufacturer's settings. Then, the parameters may be customized anew.
VI. Controller functions - Fitter’s menu
Fitter’s menu should be accessed by a qualified person. It is used to configure additional functions of the
controller such as CH boiler parameters, additional valves, additional pumps etc. as well as advanced
settings of basic functions (such as built-in valve parameters).
Block diagram of fitter’s menu is presented below:

ST-550 zPID
17
*Submenu available only when Operation with zPID control is selected
**Submenu available only when Operation without zPID control is selected
***Submenu available only when additional module ST-66B is used
Fitter’s menu
PID coefficient*
CH boiler power coefficient
Fan correction top
Fan correction bottom
PID supervision*
Feeding time
Feeding pause
Fan operation time
Fan pause time
Fan revolutions
Buffer parameters***
Buffer
DHW function
Pre-set bottom buffer temp.
Pre-set top buffer temp.
Valve settings
Additional pump 1
Operation algorithm selection
Short circuit pump
Floor pump
Circulating pump
Additional pump 2
Operation algorithm selection
Short circuit pump
Floor pump
Circulating pump
Fuel level calibration
Full tank
Empty tank
Time settings
Date settings
Internet module Module ON
Room regulator
CH pump control
CH boiler control
TECH regulator
External temperature correction
Language
GSM module
OFF
ON
Factory settings

User’s manual
18
VI.1. PID coefficient
NOTE
This submenu concerns CH boiler operation with PID control and t is available only when
zPID control is active.
VI.1.a) CH boiler power coefficient
CH boiler power coefficient serves to control the feeder and fan operation at the same time. 100% is the
default value but it may be adjusted within the range of 50-110%. Once a change is introduced, the
upper limit of zPID parameters is moved (operation/pause time of the feeder and blow force). The lower
limit of parameters remains unchanged.
VI.1.b) Fan correction bottom / Fan correction top
This function is used to adjust the fan speed. If the blow force is too low/high, the coefficient should be
adequately increased/decreased in order to ensure efficiency.
The user may adjust the fan speed for both minimum and maximum CH boiler power indicated by zPID
(Fan correction bottom and Fan correction bottom parameters).
VI.2. PID supervision
NOTE
This submenu concerns CH boiler operation with PID control and t is available only when zPID
control is active.
In this function the user configures the combustion parameters for the situation when the CH boiler
temperature exceeds the pre-set value by 5°C. If Damping mode function is selected, the damping
process is initiated when the pre-set temperature value is exceeded by 5°C. Once the process is
completed, the controller constantly monitors the CH boiler temperature. If it drops by a pre-defined
vale, the fire-up process is initiated again.
NOTE
Damping mode concerns only pellet-fired CH boilers controlled with the use of an additional
ST-66P module.
The remaining options should be configured if the user does not want the CH boiler to be damped when
the controller enters supervision mode. The user sets fuel feeding time, feeding pause as well as fan
operation and pause time during fuel feeding (blow-by gear)
The function is deactivated automatically when the CH temperature drops to the pre-set value.
VI.3. Buffer parameters
NOTE
Function available only when ST-66B module is used.
These parameters enable the user to configure controller operation settings in the case of heating
systems with a buffer.
VI.3.a) Buffer
Once buffer function is activated (by selecting ON) , CH pump serves as pump of the buffer in which two
sensors are installed: upper (C1) and lower (C2). The pump remains active until the pre-set temperature
of buffer bottom is reached. When the temperature drops below the pre-set buffer top temperature, the
pump is activated again.
VI.3.b) DHW function
If buffer is used in the heating system, it is necessary to specify how the water tank is connected:
- from CH boiler – the heating system in which DHW tank is connected directly to the CH boiler (a
separate circuit).
- from buffer – the heating system in which DHW tank is built in or connected to the buffer.

ST-550 zPID
19
VI.3.c) Pre-set temperature top
This function enables the user to define the pre-set temperature for the upper part of the buffer (sensor
should be placed in the upper part of the tank). After this value is reached, the pump is disabled (provided
that the pre-set buffer temperature bottom has also been reached).
VI.3.d) Pre-set temperature bottom
This function enables the user to define the pre-set temperature for the lower part of the buffer (sensor
should be placed in the lower part of the tank).
VI.4. Valve settings
VI.4.a) Built-in valve, Additional valve 1 and 2
These options are used to configure operation of the built-in valve. The built-in module controls two
valves without the need to use additional devices. It the heating system requires other devices, an
additional module controlling the valve (e.g. ST-431N) may be connected to the ST-550zPID controller.
The parameters included in the submenus Valve 1 and Valve 2 are intended for controlling such valves.
In the case of valves 1 and 2, it is necessary to register in order for the valve to operate correctly. To
register the valve, enter the module number (placed on the casing) and configure a few parameters.
There is a range of parameters intended for configuring the operation of the valves and adjusting it to
the user’s needs. Both the parameters of the built-in valve and the parameters of the valves are similar,
which is illustrated by the following block diagrams:
Built-in valve 1, 2
Valve status ON
OFF
Pre-set valve temperature
Temperature control
Opening time
Single stroke
Minimum opening
Valve type CH valve
Floor valve
Weather-based control
ON
OFF
Pre-set temperature for -20⁰C
Pre-set temperature for -10⁰C
Pre-set temperature for 0⁰C
Pre-set temperature for 10⁰C
Room regulator
Room regulator
Room reg. temp. lower
Room temperature difference
Change of pre-set valve temperature
Return protection
ON
OFF
Minimum return temperature
Maximum temperature
Valve pump Operation modes
Pump activation temperature
Factory settings

User’s manual
20
Registration
Option available only for valve 1 and valve 2.
This function is used by the fitter to enter the serial number of the module controlling the three-
way valve actuator (a 5-digit number given on the module casing). Without this number the function
remains inactive.
Valve status
This function allows the user to deactivate the valve temporarily without the need to remove it
altogether. After re-activating the valve, it is not necessary to register again.
Pre-set valve temperature
This function is used to define the pre-set temperature of the valve. The setting range differs depending
on the valve type. The pre-set temperature value may be adjusted directly from the main screen view
by twisting the pulser knob.
Valve1, Valve 2
Registration
Valve status
ON
OFF
Pre-set valve temperature
Temperature control
Opening time
Single stroke
Maximum opening
Valve type
CH valve
Floor valve
Weather-based control
ON
OFF
Pre-set temperature for -20⁰C
Pre-set temperature for -10⁰C
Pre-set temperature for 0⁰C
Pre-set temperature for 10⁰C
Sensor selection
Room regulator
Room regulator
Room reg. temp. lower
Change of pre-set valve temperature
Room temperature difference
Return protection
ON
OFF
Minimum return temperature
Maximum temperature
External sensor correction
Factory settings
Valve removal
Valve pump
Operation modes
Pump activation temperature
Table of contents
Popular Controllers manuals by other brands
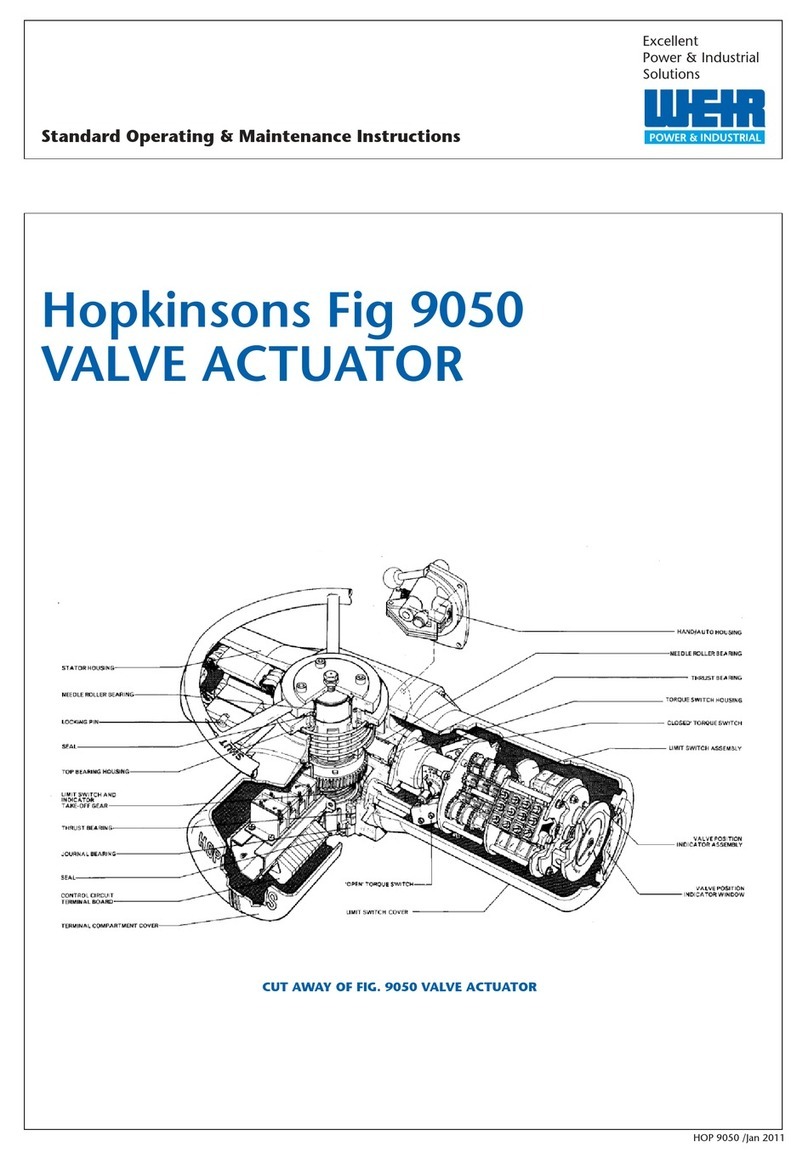
Weir
Weir Hopkinsons Fig 9050 Standard Operating & Maintenance Instructions
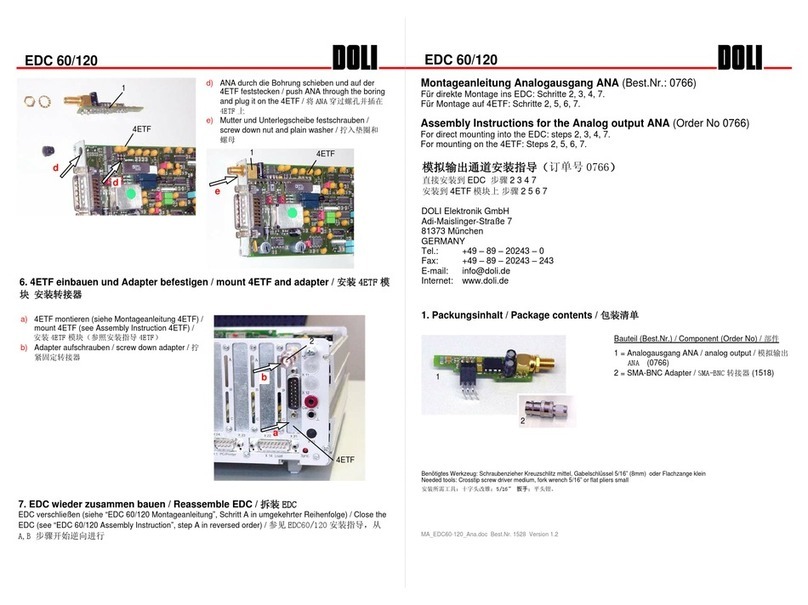
Doli
Doli EDC 120 Assembly instruction
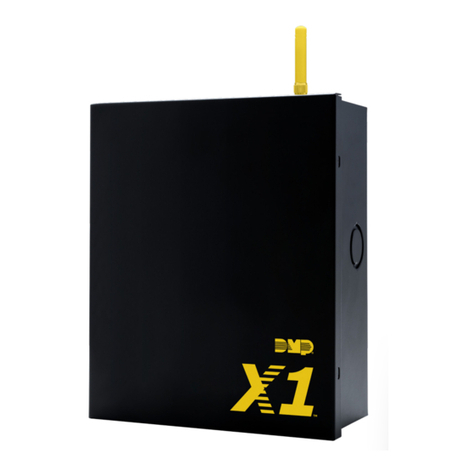
DMP Electronics
DMP Electronics X1 Installation and programming guide
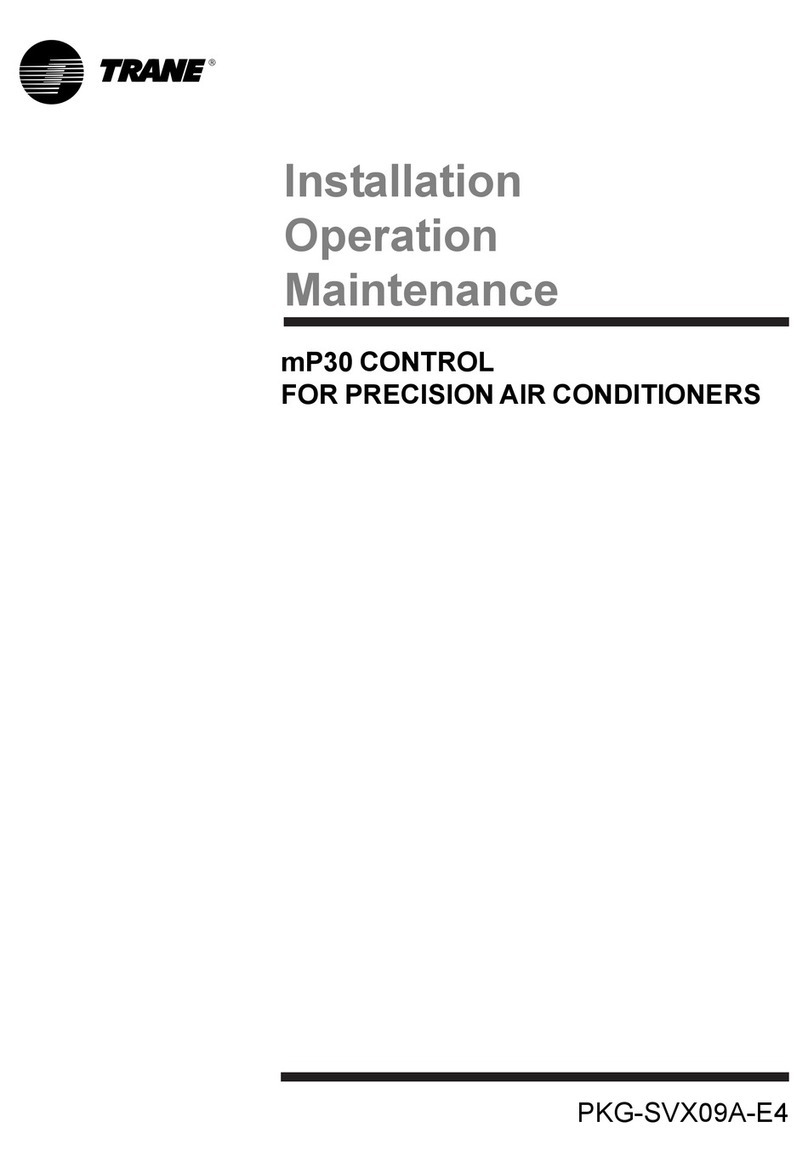
Trane
Trane mP30 Installation operation & maintenance

Shinko
Shinko FCR-13A instruction manual
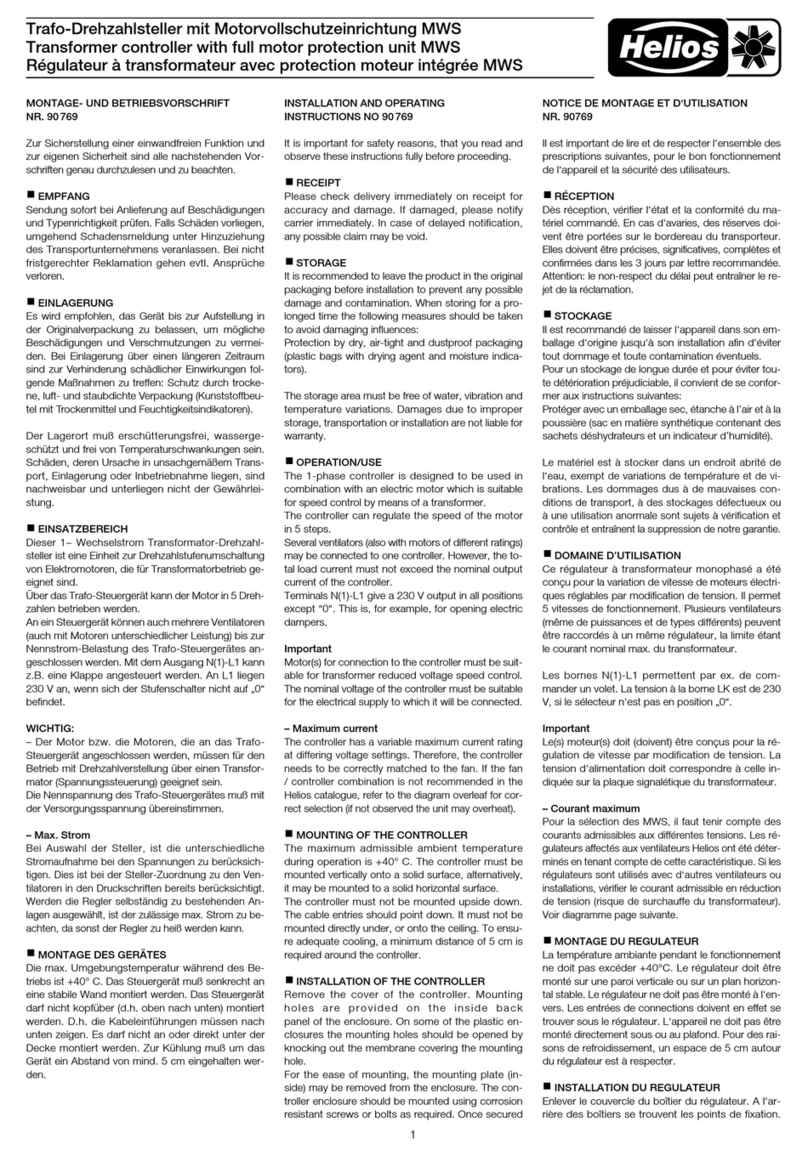
Helios
Helios WS 1,5 Installation and operating instructions
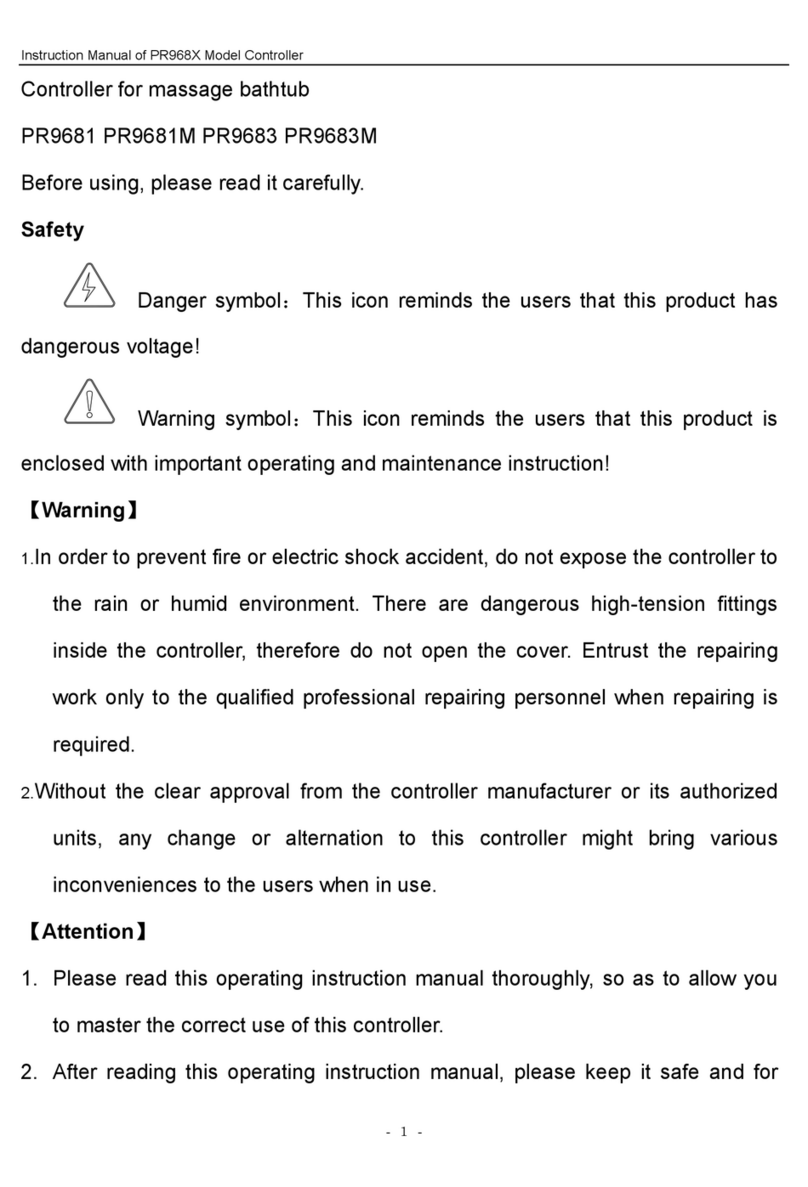
Sparmax
Sparmax PR968 Series instruction manual
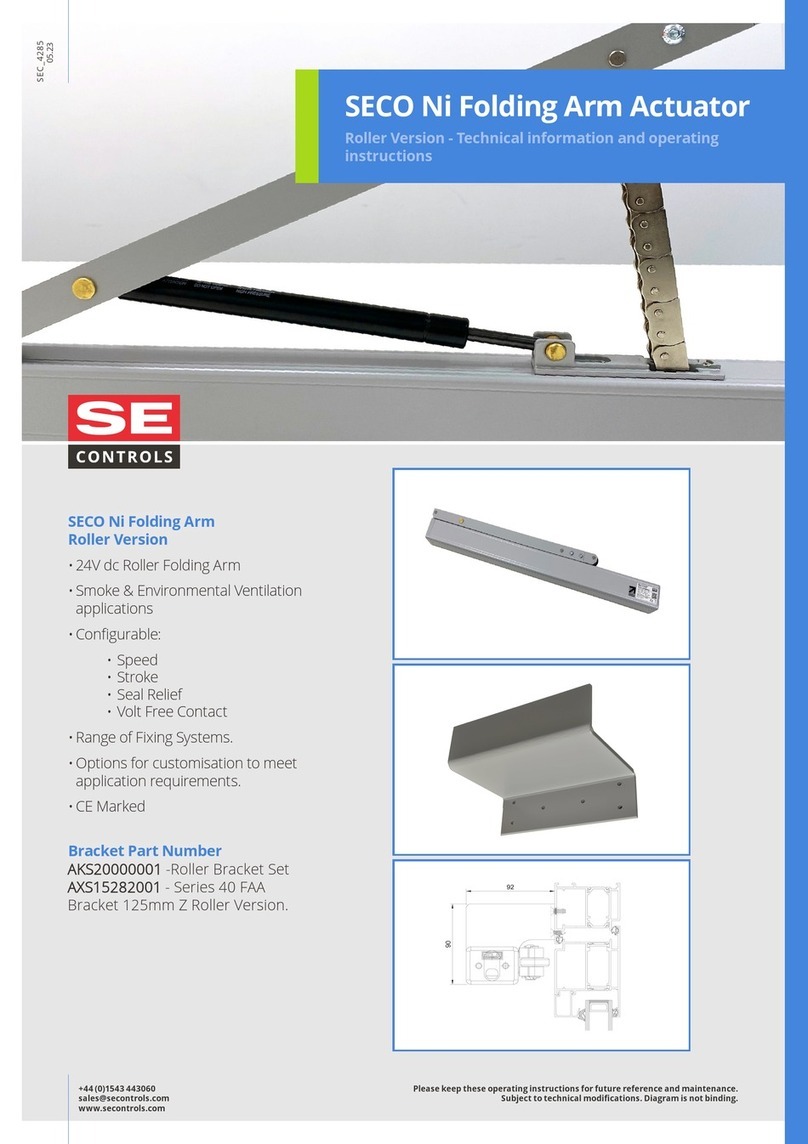
SE Controls
SE Controls SECO Ni AKS20000001 quick start guide
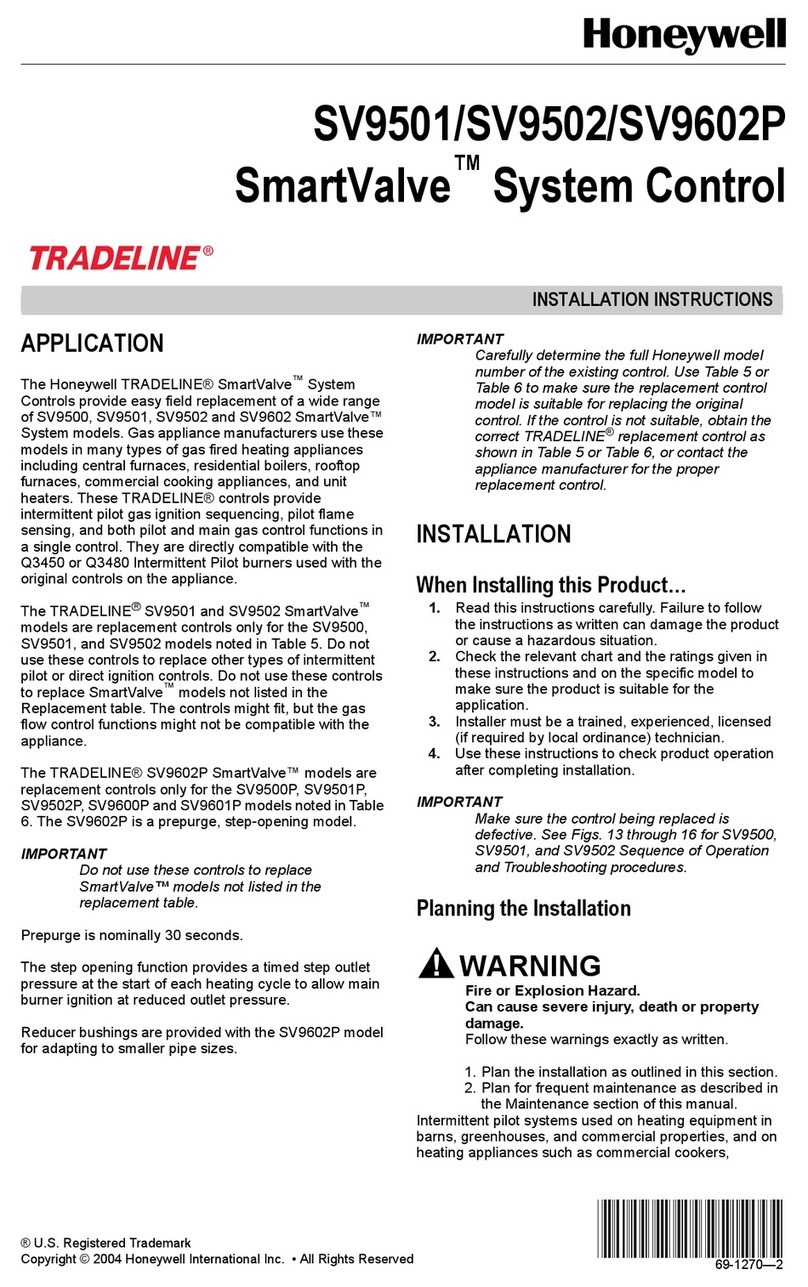
Honeywell
Honeywell TRADELINE SmartValve SV9602P installation instructions
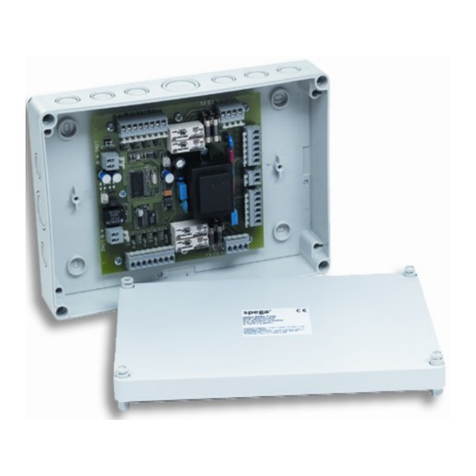
spega
spega BSK4-F Technical manual
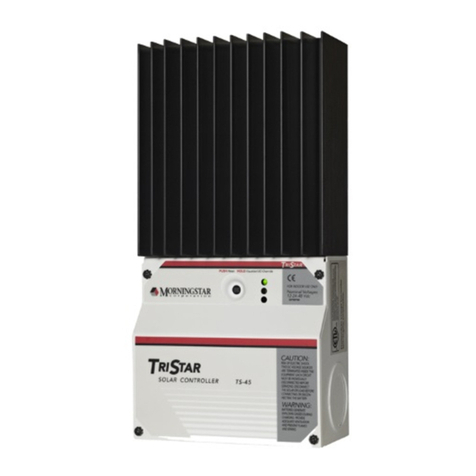
Morningstar
Morningstar TriStar TS-60M Installation, operation and maintenance manual
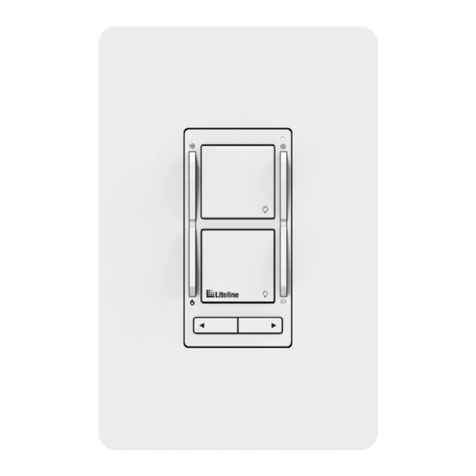
SPEX
SPEX SLWZ-SNC-01 user manual