SealMaster R-1 User manual

S:\Engineering\13-Operator Manuals\Current\CHIPSPREADER_V2.0_APR2019.docx

S:\Engineering\13-Operator Manuals\Current\CHIPSPREADER_V2.0_APR2019.docx
R-1 AGGREGATE CHIP SPREADER
Owner’s Manual
Version 2.0
Issue Date: April 2019
Effective Date: April 2019
Version
Date
Changes
Approval
1.0
Original Issue
2.0
4/19
New Format and Updates
DS

Table of Contents
CORRESPONDENCE....................................................................................................................................... 2
SealMaster® LIMITED WARRANTY............................................................................................................... 3
SAFETY PRECAUTIONS AND CAUTIONS ....................................................................................................... 4
PRECAUTIONS ........................................................................................................................................... 4
CAUTIONS ................................................................................................................................................. 4
R-1 AGGREGATE CHIP SPREADER................................................................................................................. 5
MODEL R-1 ................................................................................................................................................ 5
SET UP ....................................................................................................................................................... 5
LUBRICATION ............................................................................................................................................ 7
TRANSMISSION DRIVE TRAIN: PICTURE 1 ............................................................................................. 8
SPIRAL ROLLER DRIVE: PICTURE 2......................................................................................................... 8
TRUCK HITCH: PICTURE 3 ...................................................................................................................... 8
OPERATION ............................................................................................................................................... 9
MAINTENANCE........................................................................................................................................ 10
TROUBLE SHOOTING GUIDE ...................................................................................................................11
STORAGE ................................................................................................................................................. 12
TRAILER ................................................................................................................................................... 12
IDLER AXLE & BALANCE ROLLERS...............................................................................................................13
PARTS LIST............................................................................................................................................... 13
DRIVE TRAIN ............................................................................................................................................... 14
PARTS LIST............................................................................................................................................... 16
DRIVE TRAIN AND SHIFTER ........................................................................................................................17
PARTS LIST............................................................................................................................................... 18
TRUCK HITCH .............................................................................................................................................. 19
PARTS LIST............................................................................................................................................... 21
AUGER......................................................................................................................................................... 22
PARTS LIST............................................................................................................................................... 24
TRAILER ASSEMBLY- OPTIONAL................................................................................................................. 25
PARTS LIST............................................................................................................................................... 26
OPERATOR’S PLATFORM............................................................................................................................27
PARTS LIST............................................................................................................................................... 27

2
ThorWorks Industries, Inc.
Purchased by __________________________ Model NO. _______________________
Company Name _______________________ Serial NO. _______________________
Address ________________________________ Acceptance Date ________________
City _____________ State______ Zip _______
CORRESPONDENCE
All Correspondence regarding this equipment, as well as general correspondence should be addressed to:
ThorWorks Industries, Inc.
PO Box 2277
Sandusky, OH 44870
In referring to the equipment, kindly state the Model Number, Serial Number and any part number involved
`

3
SealMaster® LIMITED WARRANTY
SealMaster warrants that its products are of quality material and workmanship. SealMaster
agrees to replace, within a period of one (1) year from date of delivery, or at its option, repair,
without charge, any part of their manufacture which proved defective. The repair or
replacement will be free of charge F.O.B. Sandusky, Ohio, proving the damaged part or parts
are returned, freight prepaid, to SealMaster and investigation show such repair or replacement
is made necessary by an inherent defect of material or workmanship.
It is hereby understood that engines, motors, pumps, or other components purchased by
SealMaster for use on its equipment are not warranted by SealMaster and are sold only with
the standard warranty of the manufacturer of that component.
SealMaster will make no allowances for repairs or alterations completed by outside sources
unless authorization is in writing and approved by an authorized SealMaster representative.
Any claims for defective material or workmanship must be made prior to the expiration of thirty
(30) days from the date failure occurs, and in all cases prior to the expiration of the warranty
period of one (1) year. It is the intent of this paragraph to limit SealMaster’s liability solely to
the cost of replacement parts, F.O.B. factory, or at the option of SealMaster to repair of the
defective part or parts. No allowances for damages, lost time, or any other claim will be
recognized.
This warranty is null and void if other than genuine SealMaster parts are used.
SealMaster is constantly striving to improve their products. Changes in design and
improvement will be made whenever the manufacturer believes the efficiency of the product
will be improved, without incurring any obligation to incorporate such improvements in any
machines which have been shipped or are in service.
In an effort to continue to improve product quality, SealMaster reserves the right to change
specifications without notice.
Any modification or alteration of this machine without prior approval of the manufacturer may
void this warranty.

4
SAFETY PRECAUTIONS AND CAUTIONS
PRECAUTIONS
•Always wear eye and ear protection, and gloves.
•Be aware of all CAUTION, WARNING, DANGER signs on the unit.
•Read all Owners Manuals that come with this unit.
•Make sure the operator is familiar with units’ operation.
CAUTIONS
•Keep hands, feet, and clothing away from moving parts.
•Do not operate the machine without all guards in place.
WARNING!
When backing the truck up to the spreader, and hitching the spreader,
stand at the end of the spreader hopper to avoid being crushed
between the truck and the spreader.

5
R-1 AGGREGATE CHIP SPREADER
MODEL R-1
When you receive your MODEL R-1 from the factory, it may be packed in many
different ways. This is due to the rules of different Common Carriers. In general,
this manual will try to explain how to set up your machine, from the shipping skid,
lubricate, operate, maintain, and store it.
SET UP
Remove the spreader from the shipping skid, after inspecting it for any bent,
damaged, or broken parts. Should there be any damage in shipping, consult the
carrier who delivered the machine. Unpack all unattached parts. These parts may
be attached to the inside of the hopper, to the skid, in the built-in tool box.
Lay out all parts and check the parts section of this manual for identification.
Check the operation of the shift lever. The spreader may have to be moved
slightly to obtain full throw on the shifting lever. Check the feed gate operation.
Check the operation of the agitator clutch if spreader is so equipped.

6
R-1 AGGREGATE CHIP SPREADER
The truck hitch should now be mounted to the rear cross member of the truck
frame. A diagonal brace is recommended with this type of hitch but is not
furnished due to the wide variance in truck frames (see illustration). Clamp the
truck hitch to the rear cross member, drill the mounting holes, and bolt it in place.
Make a pair of braces to fit your truck.
LUBRICATION
Every 50 operating hours lubricate the following:
•Page 15 Drive axle bearings ---------- item 6
•Page 13 Idler axle bearings ----------- item 1
•Page 14 Transmission bearings ------ item 9 and 10
•Page 17 Feed Roller bearings -------- item 13
•Page 23 Agitator bearings ------------ item 5
•Page 19 Truck Hitch -------------------- item 18
BRACE
TRUCK HITCH IS STRONGER
THAN ANY CROSSMEMBER

7
R-1 AGGREGATE CHIP SPREADER
LUBRICATION
On this type of bearing assembly use a low pressure grease gun. Add grease until
a fine bead of grease appears around the seal on the front of the bearing. Too
much grease or too much pressure of the grease could damage this seal.
NOTE: DO NOT OVER GREASE OR USE A HIGHPRESSURE GREASE GUN.
Typical damage to this seal from high pressure grease gun is blowing the seal
completely out of the bearing assembly.
TRANSMISSION DRIVE TRAIN: PICTURE 1
•Remove the transmission cover and lubricate the following:
•Reverse sprocket
•Shifter yoke-coat generously
•Jaw clutch-coat shaft and key generously
•Forward gear
•Gear teeth-coat generously
•Drive chain-clean in clean solvent, dry thoroughly and re-lubricate
Replace transmission cover and shift linkage after inspecting for any worn or
damaged parts. Replace damaged parts immediately.
SPIRAL ROLLER DRIVE: PICTURE 2
Remove chain guard from feed roller drive chain. Clean chain in good clean
solvent, dry thoroughly and re-lubricate. Replace drive chains, adjust chain
tightness and inspect all moving parts at this time. Replace any worn or damaged
parts at this time. Replace chain shields.
TRUCK HITCH: PICTURE 3
Lubricate hitch guide angles by coating them generously with chassis grease.
In general, linkages on this unit do not need lubricant. However, should any
linkage begin to rust up or seize, a small amount of oil will free it up again. Check
with your local bulk plant or lubricant merchant or appropriate merchant for
appropriate lubricants.

8
R-1 AGGREGATE CHIP SPREADER
TRANSMISSION DRIVE TRAIN: PICTURE 1
SPIRAL ROLLER DRIVE: PICTURE 2
TRUCK HITCH: PICTURE 3
12 CLUTCH
GEAR
13 CLUTCH
SLIDING
14 GEAR
DRIVE
15 SPROCKET
DRIVE
16 CHAIN
ROLLER
17 SHIFTER
SHAFT
18 SHIFT YOKE
22 CLUTCH
SHAFT
23 CLUTCH
SPROCKET
26 SHAFT
DRIVE
11 CHAIN
ROLLER #80
14 HITCH WELD

9
R-1 AGGREGATE CHIP SPREADER
OPERATION
When preparing for the daily spreading operation a quick inspection of the
spreader is suggested.
Be sure the
truck hitch
draw bar is
in the set of
holes
closest to
14-1/2 inches from the ground. Back the truck up to the spreader. Adjust the
height of the spreader hitch by means of the jack crank located on the LH end
panel of the spreader. Open the jaws of the hitch with the trip lever. Using the
trip lever and the tilting bars, guide the spreader hitch as the truck makes contact.
Be sure both hitch jaws are locked over the drawbar.
It will be noted in operation that a slight forward rake to the spreader hopper is
best. This will keep the spreader balance rollers from scuffing the tack coat or the
finished blanket. Use the hitch jack to obtain a 1-1/2° - 5° rake on the hopper. This
angle may change due to the springs of the tow truck. As the load decreases, the
back of the truck will rise. Find the rake of the spreader that will keep balance
rollers out of contact until the truck is empty.
Install the operator’s platform (if so equipped). Shift transmission into gear, either
forward (back) or reverse (front). Install the block-off plates if the spread width is
to be less than the spreader width. Insert the block-off plates into the slot formed
between the closed feed gate and the rear hopper panel. This is done easiest
when the hopper is empty. Open feed gate to desired depth, each notch is
approximately 1/4". Fill the spreader hopper and proceed to spread. If a shifting
error was made the transmission will snap to neutral, preventing damage to the
drives. Try to avoid excessive shifting errors.
WARNING:
Stand at the end of the spreader hopper to avoid
being crushed between the truck and the spreader.

10
R-1 AGGREGATE CHIP SPREADER
Normal spreading speeds are from 1 to 3 miles per hour, depending on the
material being spread, depth of blanket, or type of base to be covered.
Streaking of the blanket usually is caused by large lumps in the hopper between
the feed roller and the feed gate. Should streaking become a problem, a better
grade of material should be obtained
The agitator (if so equipped) is use to keep the material being spread from
becoming packed over the feed roller and to convey material to the ends of the
hopper. The agitator is engaged or dis-engaged by means of the clutch lever on
the RH end of the spreader. It is most desirable when materials are extremely
difficult to spread.
The feed roller is considered in good condition when the spiral grooves are visible.
When these groves wear off, replace the feed roller immediately. Do not regroove
this roller because it has already been worn to its minimum allowable diameter.
MAINTENANCE
During the 50-hour lubrication stop, inspect all operating parts. Should any
damaged or excessive wear be evident, replace the parts immediately. Straighten
any bent parts as soon as possible. Clean and re-paint any exposed parts to retard
rust.
For any specific problems, see the following troubleshooting chart.

11
R-1 AGGREGATE CHIP SPREADER
TROUBLE SHOOTING GUIDE
PROBLEM
FEED ROLLER
DOES NOT OPERATE
TOWING HITCH
DOES NOT LATCH
TRACTION WHEELS
BINDING
SUPPORT WHEELS
BINDING
FEED GATE
NOT OPERATING PROPERLY
CHAINS NOT CONTACTING
SPROCKETS PROPERLY
TRANSMISSION
WILL NOT ENGAGE
AGITATOR
DOES NOT OPERATE
POSSIBLE CAUSES/SOLUTIONS
DRIVE CHAIN BROKEN / REPLACE CHAIN
CHAIN OFF OF A SPROCKET / REINSTALL CHAIN
GEAR TEETH BROKEN / REPLACE GEAR
CLUTCH NOT ENGAGING / REPLACE OR REPAIR CLUTCH
MATERIAL JAMMED BETWEEN HOPPER AND ROLLER / CLEAN MATERIAL OUT
BEARINGS NOT TURNING FREELY / REPLACE BEARINGS
TENSION SPRING BROKEN / REPLACE SPRING
HITCH JAW HOOKS BROKEN / REPLACE HITCH
DRAWBAR BENT / STRAIGHTEN OR REPLACE DRAWBAR
BEARINGS NOT TURNING FREELY / REPLACE BEARINGS
MATERIAL JAMMED BETWEEN HOPPER AND ROLLER / CLEAN MATERIAL OUT
GEAR TEETH BROKEN / REPLACE GEAR
BEARINGS NOT TURNING FREELY / REPLACE BEARINGS
KEY IN HUB LOST OR LOOSE / REPLACE KEY AND TIGHTEN SET SCREWS
LEVER BROKEN OR WORN OUT / REPLACE OR REPAIR LEVER
CHAIN TENSION IMPROPERLY ADJUSTED / ADJUST CHAIN TIGHTENER
SPROCKET TEETH BROKEN / REPLACE SPROCKET
KEY IN SHIFTER YOKE LOST OR LOOSE / REPLACE KEY AND TIGHTEN SET SCREWS
CLUTCH BROKEN OR WORN OUT / REPLACE CLUTCH
DRIVE CHAIN BROKEN / REPLACE CHAIN
CHAIN OFF OF A SPROCKETS / REINSTALL CHAIN
CLUTCH NOT ENGAGING / REPLACE OR REPAIR CLUTCH
SPROCKET TEETH BROKEN / REPLACE SPROCKET
DRIVE BOLT BROKEN / REPLACE BOLT
BEARINGS NOT TURNING FREELY / REPLACE BEARINGS
FEED ROLLER DOES NOT OPERATE / SEE (1) TROUBLE SHOOT

12
R-1 AGGREGATE CHIP SPREADER
STORAGE
Perform all required maintenance and lubrication procedures. Coat all shafts with
grease. Clean and paint all exposed parts. Block spreader up off the ground or
turn upside down and deflate tires.
NOTE: Normal tire pressure is 100 pounds.
TRAILER
With the unit secured to the pintle hook on the truck, install the lifting jack
assemblies to their mounting points. Raise the spreader evenly with jacks. Unbolt
the trailer axle and roll it out from under the spreader. Lower the spreader to the
ground with the hitch tongue still attached to the truck. Unlash the pintle hook. It
may be necessary to lift the spreader with the jacks to do this. Lower the spreader
evenly to the ground. Remove the hitch tongue and jack assemblies.
To reinstall the trailer, place the jacks under their lifting pads. Reinstall the hitch
tongue. Raise the spreader and attach it to the truck pintle hook. Raise the
spreader. Roll the axle into place and bolt it there. Lower the jacks and remove
them.
NOTE: The hydraulic jacks must be operated together to keep from twisting the
jacks or dumping the spreader.
WARNING:
Use extreme caution when using a shovel in the
hopper. Keep all tools away from the rotating augers.

13
R-1 AGGREGATE CHIP SPREADER
IDLER AXLE & BALANCE ROLLERS
PARTS LIST
ITEM
PART NO.
QTY.
10’
DESCRIPTION
1
P435A004
2
BEARING –PILLOW BLOCK
2
P576A008
2
WHEEL –TIRE ONLY
P574A003
2
TUBE
4
9599
2
HUB –WHEEL
5
44709A
1
SHAFT –IDLER AXLE
6
P577A003
2
SPLIT RIM ASSEMBLY
7
44705
2
ASSEMBLY –BALANCE ROLLER
`
44706
2
BALANCE –ROLLER
P438A002
2
BEARING –F1100
8
44708
2
SHAFT –ROLLER
7BALANCE
ROLLER
ASSEMBLY
2TIRE & TUBE
1PILLOW
BLOCK BRG.
6SPLIT RIM
ASSEMBLY
4HUB
WHEEL
5SHAFT
IDLER AXLE
8SHAFT

14
R-1 AGGREGATE CHIP SPREADER
DRIVE TRAIN
7COUPLINGS
8CHAIN
9FLANGE
BRG. 1-1/2”
10 FLANGE
BRG. 1-1/4”
12 CLUTCH
GEAR
13 CLUTCH
SLIDING
14 GEAR
DRIVE
15 SPROCKET
DRIVE
16 CHAIN
ROLLER
17 SHIFTER
SHAFT
18 SHIFT YOKE
22 CLUTCH
SHAFT
23 CLUTCH
SPROCKET
26 SHAFT
DRIVE

15
R-1 AGGREGATE CHIP SPREADER
DRIVE TRAIN
1SHAFT
DRIVE AXLE
2HUB
WHEEL
3SPLIT RIM
ASSEMBLY
4TIRE & TUBE
6PILLOW
BLOCK BRG.
27 BOTTOM
COVER

16
R-1 AGGREGATE CHIP SPREADER
DRIVE TRAIN
PARTS LIST
ITEM
PART NO.
QTY.
10’
DESCRIPTION
1
44696
1
SHAFT –DRIVE AXLE
2
9599
2
HUB –WHEEL
3
P577A003
2
SPLIT RIM ASSEMBLY
4
P576A008
2
WHEEL –TIRE ONLY
P574A003
2
TUBE
6
P435A004
2
BEARING –PILLOW BLOCK 1-1/2”
7
P630A017
2
HALF CHAIN COUPLING
8
P631A003
1
ASSEMBLY –CHAIN
9
P434A003
2
BEARING –FLANGE 1-1/2”
10
P434A002
2
BEARING –FLANGE 1-1/4”
12
6647
1
CLUTCH GEAR
P911A003
1
BUSHING –(PART OF 6647)
13
6552
1
CLUTCH - SLIDING
14
10702
1
GEAR –DRIVE
15
10757
1
`SPROCKET –DRIVE
16
6176-33
1
CHAIN –ROLLER #80 –33LINKS
P1035A004
1
LINK –CONNECTING #80
17
10291
1
SHIFTER SHAFT
18
6651
1
SHIFT YOKE
22
44695B
1
CLUTCH SHAFT –DRIVEN
23
6641
1
CLUTCH –SPROCKET
26
44697
1
SHAFT –DRIVE
27
10292
1
BOTTOM COVER

17
R-1 AGGREGATE CHIP SPREADER
DRIVE TRAIN AND SHIFTER
16 HANDLE
FEED GATE
2BAR-SECTOR
BACKING
4CLUTCH
LEVER SECTER
5LEVER
19 BRACE
SECTOR
6SHIFT
LINKAGE
ASSEMBLY
10 SHIELD - CHAIN
9SPROCKET
19T #80
3FEED GATE
SECTOR
15 SHIFT LEVER
18 HANGER
13 BEARING
FLANGE
11 CHAIN
ROLLER #80
12 SPROCKET
12T #80

18
R-1 AGGREGATE CHIP SPREADER
DRIVE TRAIN AND SHIFTER
PARTS LIST
ITEM
PART NO.
QTY.
DESCRIPTION
1
2128
5
SPACER 3/8 PIPE X 7/8
2
44814
2
BAR –SECTOR BACKING
3
44719
1
SECTOR –FEED GATE
4
10273
1
WELDMONT - CLUTCH LEVER SECTOR
5
9079A
1
WELDMONT - LEVER
6
10274
1
ASSEMBLY –SHIFT LINKAGE
6A
P495A001
1
BALL JOINT
6B
10272
1
ROD
6C
P1057A002
1
JAM NUT
6D
P1024A002
1
YOKE
7
P1034A007
1
PIN –CLEVIS 1/2” DIA X 1-3/4”
9
P429A016
1
SPROCKET 19T #80
10
9071
1
SHIELD –CHAIN
11
6176-37
1
CHAIN –ROLLER #80
P1035A004
1
LINK CONNECTOR
12
P429A017
1
SPROCKET 12T #80
13
P434A002
1
BEARING –FLANGE
14
45123
1
WELDMONT –FEED ROLLER 10’
15
9089
1
WELDMONT –SHIFT LEVER
16
44718
2
HANDLE –FEED GATE
18
9078
1
HANGER –END LH
19
44720
2
BRACE - SECTOR
20
44712
1
FEED GATE WELDMENT 10’
20 FEED GATE 10’
14 FEED ROLLER 10’
Table of contents
Popular Spreader manuals by other brands
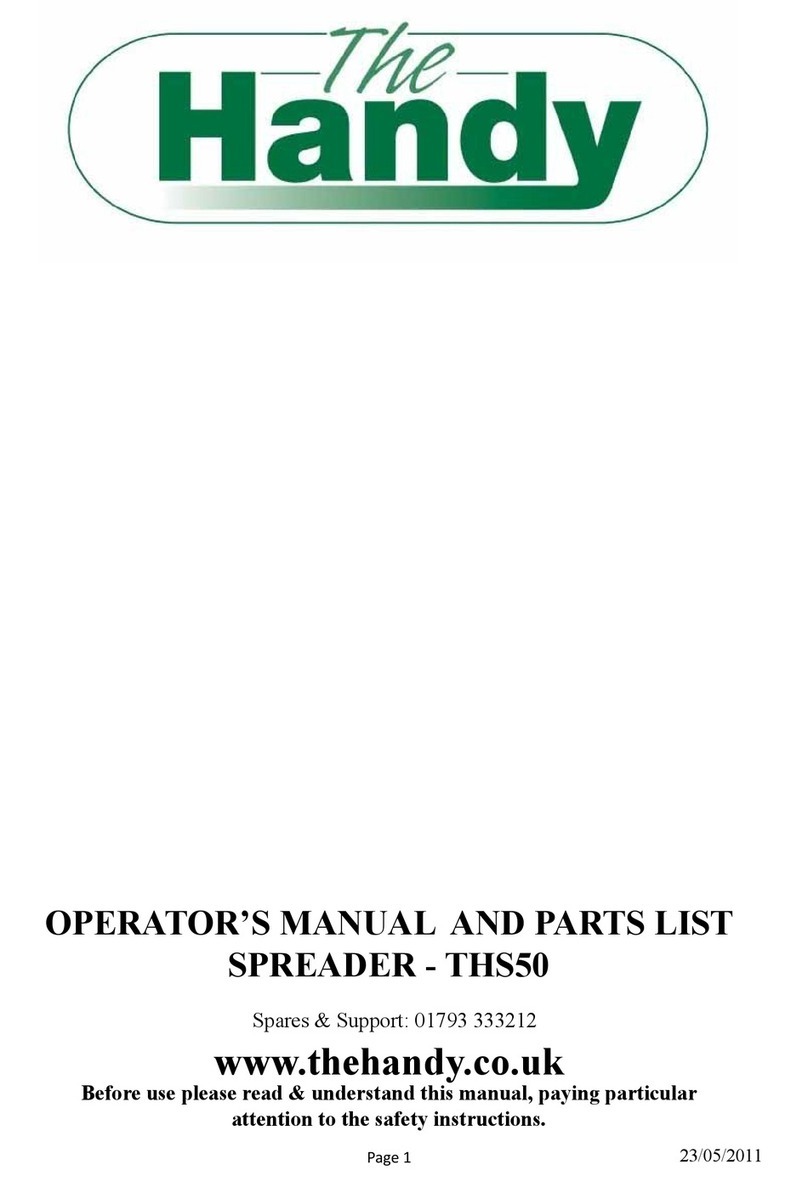
The Handy
The Handy THS50 Operator's manual and parts list

Dalton
Dalton Mobility 100 Operating and parts manual

JYDELAND
JYDELAND BOBMAN FL instructions

Krampouz
Krampouz Easy Crep System Instructions for use
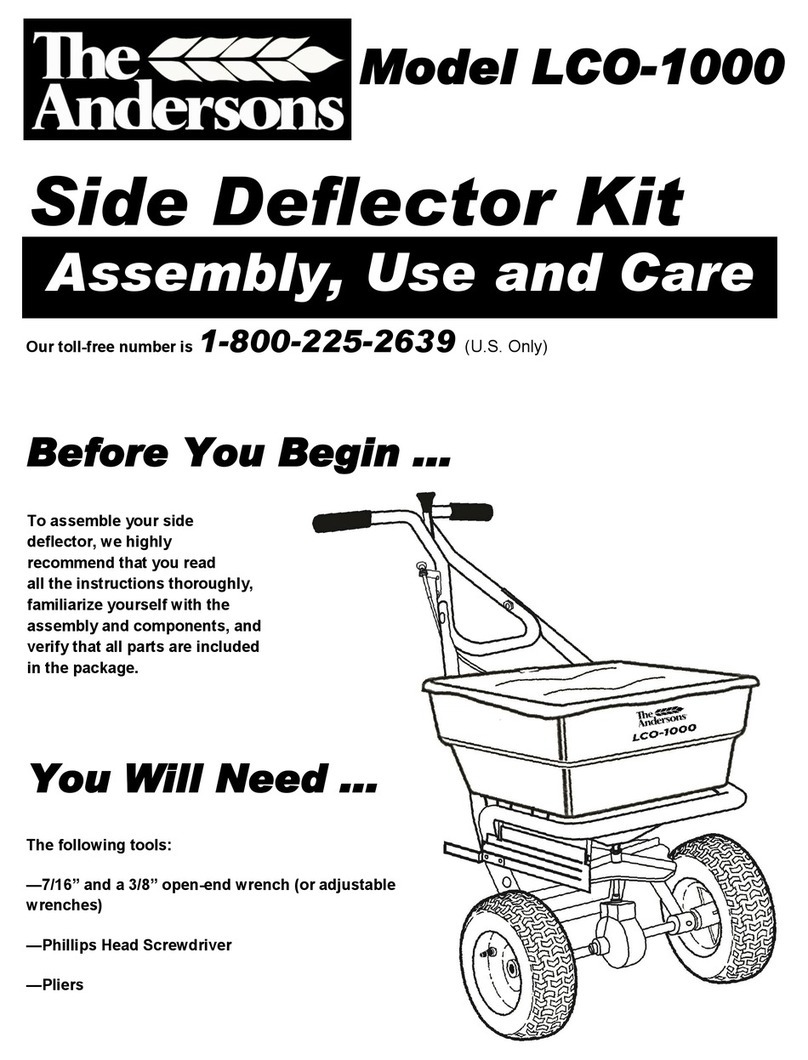
The Andersons
The Andersons LCO-1000 Assembly, use and care

Art's Way
Art's Way V180 Operator's manual and parts list