SENSY 5510 Series User manual

MA-5510_EN.doc Page 1 on 14 Rev: 27-03-19
5510 CELL SERIES
INSTALLATION MANUAL
1. GENERAL INFORMATION .................................................................................................................................................................2
1.1. Placement at level.......................................................................................................................................................................2
1.2. Shocks.........................................................................................................................................................................................2
1.3. Electrical weldings.......................................................................................................................................................................2
1.4. Lightning......................................................................................................................................................................................3
1.5. Protection hood ...........................................................................................................................................................................3
1.6. Exterior mechanical influences....................................................................................................................................................3
2. ADJUSTEMENT THRUST...................................................................................................................................................................4
2.1. Setting of anti-reverse .................................................................................................................................................................4
2.2. Setting of overload protection......................................................................................................................................................4
3. CABLING.............................................................................................................................................................................................5
3.1. Cable ...........................................................................................................................................................................................5
3.2. Wiring ..........................................................................................................................................................................................5
3.3. Parallel wiring ..............................................................................................................................................................................5
3.4. Calibration ...................................................................................................................................................................................6
3.5. Measurement errors....................................................................................................................................................................6
3.6. Insulation test ..............................................................................................................................................................................6
3.7. Output impedance .......................................................................................................................................................................7
3.8. Input impedance..........................................................................................................................................................................7
4. USE IN POTENTIALLY EXPLOSIVE ATMOSPHERE (OPTION).......................................................................................................8
4.1. Intrinsic safety protection.............................................................................................................................................................8
5. Periodic inspections.............................................................................................................................................................................8
6. Use features ........................................................................................................................................................................................9
7. Guarantee............................................................................................................................................................................................9
8. DRAWINGS AND WIRING DIAGRAMS..............................................................................................................................................9
9. EU Declaration of Conformity ............................................................................................................................................................14

MA-5510_EN.doc Page 2 on 14 Rev: 27-03-19
1. GENERAL INFORMATION
1.1. Placement at level
Differences of a few tenths can usually be tolerated
with the 5510 bending cell series.
Nevertheless, when the differences are greater and
when the mounting is higher than three feet, it is
important, for correct use, to install shim packs that
ensure equal force distribution between them.
The references of these shim packs are:
e.g. G5510-0.6-XX
G5510-1 -XX
G5510-2 -XX
where 0.6/1/2 mm = thickness
XX =load
e.g. for a 0.5-2 t EASY-MOUNT
REF: G5510-0.6-0.5 t
1.2. Shocks
If shocks are to be expected, it is preferable to install a
shock absorber between the load and the cell. The former
is made from a stack of rubber and metal plates.
1.3. Electrical weldings
When arc welding must be done on the structure, it
is advised to install stranded ground wire in order
that the derived current does not pass through the
cell, damaging it.
It is also advised to disconnect the cells of the
measurement instrument.
Rev.
Date
Reason
1
27/03/2019
Adding point 4, 5, 6, 7, 8 and 9 (EU Declaration of Conformity)

MA-5510_EN.doc Page 3 on 14 Rev: 27-03-19
1.4. Lightning
If there is a risk of lightning, it is advised to isolate the
cell the best possible and derive the former by
stranded wire. In order to do that; place a rubber sheet
under the sole and polyamide waterproof washers
under the fixing screws.
REF: Washers VI-NMG-500-12 for M12
VI-NMG-500-16 for M16
Rubber SM-I5510-CA500 (0.5 - 2 t)
SM-I5510-CA5T (3 - 5 t)
SM-I5510-CA10T (7.5 - 10 t)
1.5. Protection hood
The load cells with strain
gauges are sensitive to
differential changes in
temperature.
Measurement errors may occur if the temperature changes fast. In which case, it can be useful to install a
protecting screen to avoid solar radiation or abrupt thermal convection (strong wind). The hood has another
function: to protect against shocks, projections (mud, water, etc.) and to avoid dirt at the level of the cell.
Screws that join the cell to the structure ensure the fixation. It is important that this hood does not hinder the
movement during the loading. If necessary, isolate the sides of the hood.
1.6. Exterior mechanical influences
In order to avoid measurement errors, the load
to be weighed should not be subject to parasitic
contributions: connecting pipes cables and stops
or draw-bolts. If there are any, they must be
installed with the greatest flexibility.
Also ladders, bridges for access should be
suitably articulated, etc (clamping).
Caoutchouc
Stranded ground wire

MA-5510_EN.doc Page 4 on 14 Rev: 27-03-19
2. ADJUSTEMENT THRUST
2.1. Setting of anti-reverse
This setting is done when the cell is UNLOADED.
Using wrenches, lock the central nuts A&B to the
middle of the threaded rod.
To turn the stop screw upwards, move nut A.
To go down, move nut B.
The setting is done when the base plate is in contact
with the head of the screw.
When the two threaded rods are adjusted, lock the D
nuts.
2.2. Setting of overload protection
This setting is done when the cell is COMPLETELY
loaded.
Unlock the central nuts A + B. Move the upper bolts E
upwards until it is against base plate F.
The setting is done when the base plate is in contact
with the seat of the nuts.
When the two nuts are adjusted, lock the G nuts.

MA-5510_EN.doc Page 5 on 14 Rev: 27-03-19
3. CABLING
3.1. Cable
The cells are delivered with a 4-wire screened cable. The screen (shielded wire) cannot in any case be in
contact with the ground, e.g.; in metallic junction boxes, it is necessary to isolate the screen with a sheath
(thermal).
The screen can only be connected to standardized earth.
It is advised to install a thermo-retractable sheath
(retracted 4x) at the end of the cable inside a
waterproof paste in order to avoid any leak. If there is
any possible danger of damage along its wiring, it is
necessary to use an additional cable protection,
passing the cable through a pipe (steel, preferably).
3.2. Wiring
The cell wiring should be far away from power lines
(motors, transformers), and placed in separate pipes.
Soldered connections have to be applied in the
junction box, (preferably screwed connections). It is
advised to place a bag of SILICA GEL to keep dry
inside the junction box. SENSY could provide PVC
junction box with a PG9 packing-gland, which could
receive 4 or 6 parallel cells.
REF: Junction box
JBOX-4R (4 inputs - 1 output)
JBOX-6R (6 inputs - 1 output)
3.3. Parallel wiring
The cells must be installed in parallel, with the stranded mass wire joined to itself. The sense must be joined to
the cell supply, before the points of parallel wiring and the stabilising resistances.
COLOR CODE
1) Excitation- (Yellow)
2) Excitation+ (Brown)
3) Signal+ (Green)
4) Signal- (White)
5) Screen
A) Cable PVC
B) Thermo-retractable sheath
A) Display (ex. dv680)
B) Junction box
C) Cell
R) Adjusting resistance
1) – out measure (green)
2) – in supply (yellow)
3) + in supply (brown)
4) + out measure (green)
5) Ref. (sense) + (pink)
6) Ref. (sense) + (grey)

MA-5510_EN.doc Page 6 on 14 Rev: 27-03-19
3.4. Calibration
It must be done after the sensor has been turned on for
a while (10-15 minutes) to obtain a uniform
temperature of the installation. The cells do not usually
need to be adjusted with each other. However, when
greater precision is needed, it is sometimes necessary
to stabilise the cells individually with the resistances in
the junction box. Those resistances are of several
ohms (±10) and are installed in the supply circuit.
A parallel adjustable resistance is mounted with a fixed
resistance. The most sensitive cell will have its input
resistance increased and the least sensitive will have
its lowest input resistance. You will see that it is
preferable to work on both supply cables: schematic
mounting is given for your information and allows a
variation of 0 to 20 ohms in series on the input
impedance (2x10 Ω).
Note: A well known weight of more than 20% of the
nominal load of the system can be expected. The
calibration error is always much higher than the error
made on the evaluation of the load.
3.5. Measurement errors
When the calibration is difficult and measurement errors are observed, it is necessary
to check the installation. Mechanically, the cells must be free in the direction of the
load and well positioned. Electrically, the connections must be securing, the junction
boxes exempt from humidity and the cables intact.
If there is no fault to be seen, it is necessary to verify the internal circuit. SENSY can help to diagnose on the
basis of the associated diagnosis sheet provided in the appendix and filled in beforehand.
3.6. Insulation test
The measuring of the insulating resistance is done with
a multimeter. The standardized testing voltage is 10 V.
It is applied to a conductor. It can be determined by
disconnecting the measuring instrument and applying
voltage between one of the conductors and the metallic
mounting structure, or individually, cell by cell to situate
the leakage with precision. The insulation must not, in
any case, be lower than 2 GΩfor a 10 V voltage. This
insulation default will generate measurement errors if
the insulation resistance is lower than several hundred
MΩ. Insulation default can also be generated by
environmental conditions (temperature, humidity).

MA-5510_EN.doc Page 7 on 14 Rev: 27-03-19
3.7. Output impedance
The Wheatstone bridge is made up of 350 Ωgauges.
At the output signal (OUT+: green, OUT-: white), the
resistance is 350 Ω ± 3 Ω.
This impedance must be in accordance with the
individual cell data sheet, which can easily be
determined with a multimeter. If a wider varying
resistance is read, it means that there is a break-off or
a short circuit current; a resistance variation of several
ohms would instead be a consequence of a severe
overvoltage problem.
3.8. Input impedance
Input signal (IN+: brown, IN-: yellow): its resistance is
usually of 350 Ω ± 3 Ω. Its impedance must be in
accordance with the individual cell data sheet. If a
different resistance is read, it means that there is a
break-off or a short circuit current. It is at the input that
one finds drift compensation, slope and sensitivity
adjusted resistance.
Rm Sensitivity drift compensation
Rms Sensitivity drift adjustement
Rs Sensitivity calibration
Rzb Zéro calibration
Rzc Zéro drift compensation

MA-5510_EN.doc Page 8 on 14 Rev: 27-03-19
4. USE IN POTENTIALLY EXPLOSIVE ATMOSPHERE (OPTION)
4.1. Intrinsic safety protection
Use of sensors in hazardous zones can only be done with Ex marked sensors,
delivered with one or more of the certificates hereunder:
ATEX: ISSeP07ATEX012X
SENSY’s load cells which are marked Ex i comply with the following standards:
ATEX
EN 60079-0: 2012
EN 60079-26: 2007
EN 60079-11: 2012
The use of junction boxes or additional cable lengths must be considered in the choice of protection. The
electrical characteristics of the cable being limited (see certification), it is recommended to carefully chose the
cable length and avoid any winding of the cable. After having defined all elements, it is mandatory to control if
the sensor’s output tension is still compatible with the electronic device in use and the requested accuracy.
See certificate for the special conditions for safe use.
5. PERIODIC INSPECTIONS
1. Check output for zero load (annually)
Output signal
Min acceptable
Max acceptable
mV/V / 4 wires
-0.15 mV/V
0.15 mV/V
4-20mA / 2 wires
3 mA
6 mA
4-20mA / 3 wires
3 mA
6 mA
0- 5V / 3 wires
0 V
0.8 V
0- 10V / 3 wires
0 V
0.8 V
1-5V / 3 wires
0.5 V
1.5 V
1 -10V / 3 wires
0.5 V
1.5 V
-10 / 0 / + 10V
-1.5 V
1.5 V
2. Make sure that the axle beam has not been knocked (markings) or chemically attacked (some corrosive
greases). If points 1 and 2 are not accounted for, just take preventive measures. (annually)
3. In case of doubt, reply to the diagnostic questionnaire available on Web: www.sensy.com/support.
4. Verify the integrity of the cable.
5. After any serious functioning incident, repeat operations 1 to 4.

MA-5510_EN.doc Page 9 on 14 Rev: 27-03-19
6. USE FEATURES
(The exact characteristics are systematically given in the control sheet delivered with every load cell and
function of the output signal!)
Output signal:
mV/V
4-20 mA
4-20 mA
1-5 V
0-10 V
-10…0…+10 V
RS-232
RS-485
2 wires
3 wires
3 wires
3 wires
3 wires
Compensated temp. range
-10…+45°C
Operating temperature range
-30… +70°C1
Storage temperature range
-50…+85°C
-50…+85°C
Power supply
(VDC)
5…10…152
9 – 303
13 – 30
13 – 30
15 - 184
6…12…18
Load impedance e
(Ω)
NA
≤750
≤ 1.000
> 5k
Nominal sig. range
0 – 1…2 mV/V
4 - 20 mA
4 - 20 mA
0.1-5 V
0.1-10 V
-10…0…+10 V
Saturation
> 3 mV/V
> 24 mA
> 24 mA
> 11 V
1Max +60°C for EX-I T4, T6 and C6 options
25 to 12VDC for EX-I T2 GD, EX-I T4 GD and EX-I T6
GD options
39-28VDC for EX-I C6 options
415 to 27VDC with a 1000 Ωbridge
7. GUARANTEE
The manufacturer’s guarantee is applicable as far as mounting recommendations and general use principle,
like above described, are respected.
For any particular use, not described in this document, it is mandatory to obtain a prior written agreement from
SENSY S.A. for the validity of the guarantee.
8. DRAWINGS AND WIRING DIAGRAMS

Ref. Item Capacities Weight (kg)
5510-A 0.5 - 2 t 0.95
Rev. 17/04/2018
Accessories
Other capacities and dimensions available on request
Load direction
Wiring
Dimensions in mm
STANDARD DIMENSIONS5510 >
TECHNICAL DRAWINGS: SHEAR BEAM LOAD CELL

Ref. Item* Capacities
F5510-A 0.5 - 2 t
* Material: stainless steel
(SEE ARROW DIRECTION
AND CABLE POSITION)
Other views
Other capacities and dimensions available on request
STANDARD DIMENSIONS
F5510 >
Dimensions in mm
Rev. 16/04/2018
TECHNICAL DRAWINGS: MOUNTING ACCESSORIES FOR 5510
X-VIEW
X-VIEW

Electrical
ground strap
Other views
Other capacities and dimensions available on request
STANDARD DIMENSIONS
I5510-I5515 >
Dimensions in mm
Ref. Item* Capacities
A B C D E F G M N O Ø1 H2 Weight (kg)
I551x-A 0.5 - 2 t 50 84 174 210 15 90 120 20 25 140 12.5 98 ±6.76
* x=Material: I5510 - stainless steel; I5515 - alloy steel
Rev. 16/04/2018
TECHNICAL DRAWINGS: EASY MOUNT FOR 5510

R5510-A1
Range: 500 kg - Weight: 0.097 kg
R5510-A2
Range: 750 kg - Weight: 0.127 kg
Ref. Item* Capacities
R5510-A1 500 kg
R5510-A2 750 kg - 2 t
* Material: R5510 - stainless steel
70.5
53
Other views
Other capacities and dimensions available on request
STANDARD DIMENSIONS
R5510 >
Dimensions in mm
Rev. 16/04/2018
TECHNICAL DRAWINGS: COMPRESSION BALL JOINTS FOR 5510

MA-5510_EN.doc Page 14 on 14 Rev: 27-03-19
9. EU DECLARATION OF CONFORMITY
Manufactured by:
SENSY SA
Z.I. Jumet – Allée Centrale
B – 6040 JUMET
Phone: +32 71 25.82.00
Fax: +32 71 37.09.11
Website: http://www.sensy.com
CONCERNED ITEMS: 5510, see calibration certificate related to model and serial number.
SENSY S.A. certify that the items described here above have been duly designed, manufactured and tested for use in accordance
with the essential requirements defined in the European Directives listed here under.
2014/30/EU Electro-Magnetic Compatibility Directive
2011/65/EU Restriction of the use of certain hazardous substances in the electrical and electronic equipment
(RoHS)
2014/35/EU Safety / low voltage directive
Conception and compliance of this equipment is made according to all of part of the following standards:
EN 61326 (2006)
If designed, manufactured and tested safety ref. D-DP SIL3 READY (option):
see specific and separate certificate according to ISO 13849-1 and/or EN 62061
If designed, manufactured and tested for use in potentially explosive atmospheres (option):
see specific and separate certificate.
Jumet,
March 27th, 2019
Augustin DUBOIS
Product Development Division
Table of contents
Other SENSY Measuring Instrument manuals
Popular Measuring Instrument manuals by other brands

Powercor
Powercor Sprint 200 reference guide
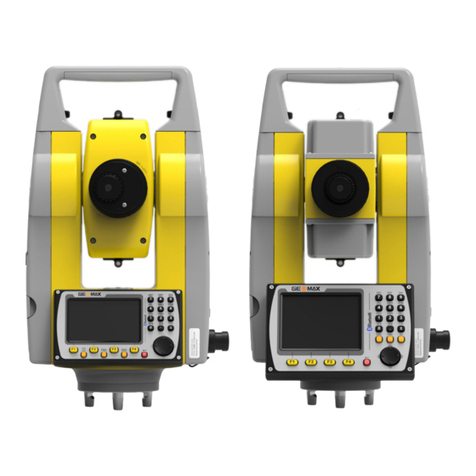
GeoMax
GeoMax Zoom 25 Series quick guide
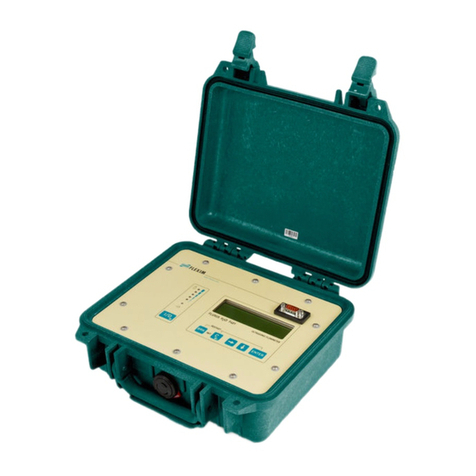
Flexim
Flexim FLUXUS F401 Operating instruction
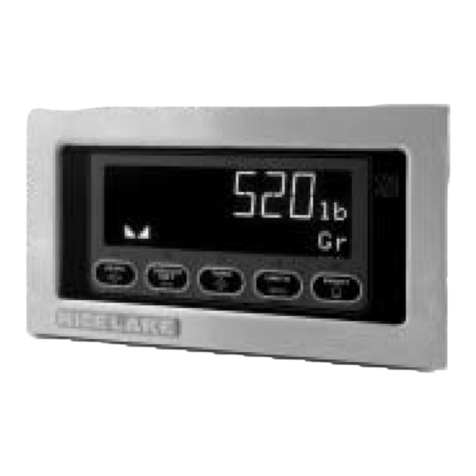
Rice Lake
Rice Lake PROFIBUS DP Installation and programming manual

GREISINGER
GREISINGER G 1107 Quick reference guide
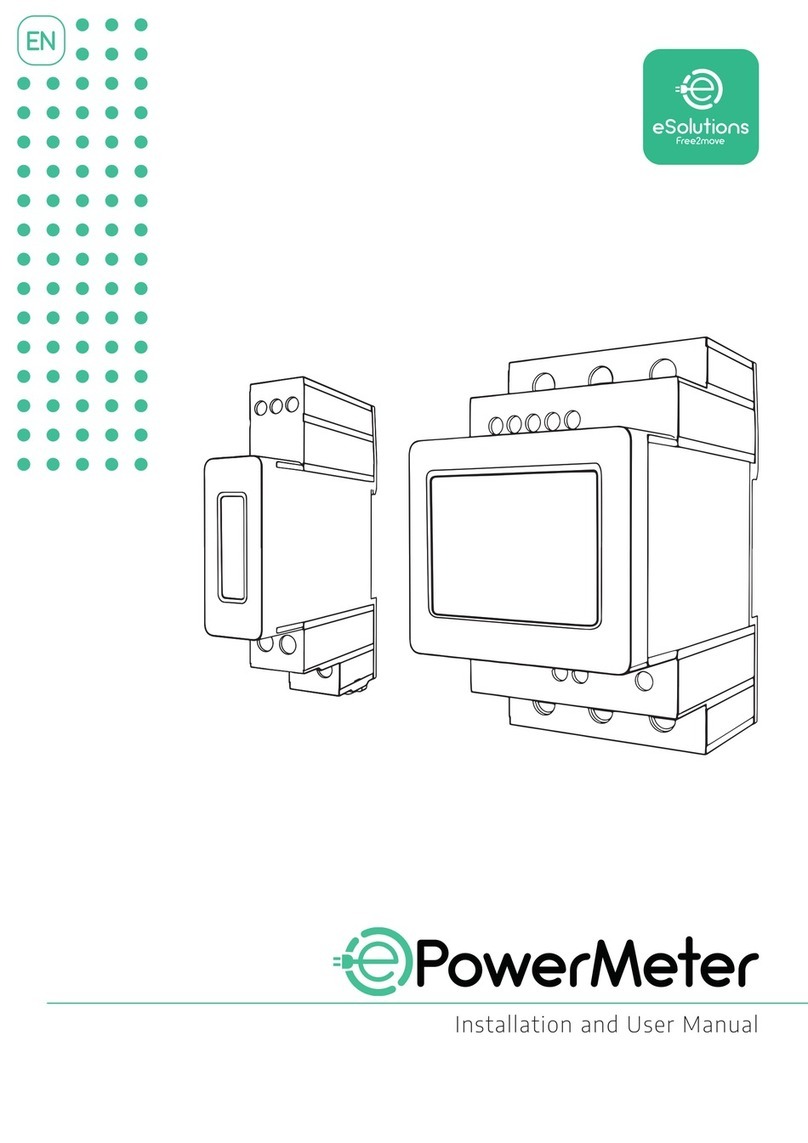
eSolutions
eSolutions PowerMeter Installation and user manual