Sharp AR-LC6 User manual

Parts marked with “ ” are important for maintaining the safety of the set. Be sure to replace these parts with
specified ones for maintaining the safety and performance of the set.
SHARP CORPORATION This document has been published to be used
for after sales service only.
The contents are subject to change without notice.
SERVICE MANUAL
CONTENTS
CODE: 00ZARLC6//A2E
DIGITAL COPIER/PRINTER/
MULTIFUNCTIONAL SYSTEM OPTION
LARGE CAPACITY TRAY
MODEL AR-LC6
[1] OUTLINE OF THE PRODUCT . . . . . . . . . . . . . . . . . . . . . . . . . . . . 1-1
[2] SPECIFICATIONS . . . . . . . . . . . . . . . . . . . . . . . . . . . . . . . . . . . . . 1-1
[3] INTERNAL CONSTRUCTION . . . . . . . . . . . . . . . . . . . . . . . . . . . . 3-1
[4] OPERATIONAL DESCRIPTIONS . . . . . . . . . . . . . . . . . . . . . . . . . 4-1
[5] DISASSEMBLY, ASSEMBLY, MAINTENANCE. . . . . . . . . . . . . . . 5-1
[6] ADJUSTMENT . . . . . . . . . . . . . . . . . . . . . . . . . . . . . . . . . . . . . . . . 6-1
[7] TROUBLESHOOTING . . . . . . . . . . . . . . . . . . . . . . . . . . . . . . . . . . 7-1
[8] ELECTRICAL SECTION. . . . . . . . . . . . . . . . . . . . . . . . . . . . . . . . . 8-1

: Jan. 9 2004
1
AR-LC6 OUTLINE OF THE PRODUCT 1 - 1
[1] OUTLINE OF THE PRODUCT
This model is a large capacity paper feed tray installed to the main unit.
It stores 3,500 sheets, eliminating troublesome paper supply.
[2] SPECIFICATIONS
AR-LC6
Transport speed Corresponds to 55 –70 sheet/min.
Transport reference Center reference
Paper size AB series A4
Inch series 8.5" x 11"
Paper size setting Not provided.
Factory setting of
paper size
AB series A4
Inch series 8.5" x 11"
Kind/weight of
applicable paper
Normal paper 60 –105g/m2(16 –28lbs)
Paper capacity 3,500 sheets (80g/m2)
Remaining paper
detection
Enable (Paper empty and 6 steps)
Paper feed system Front loading, paper feed from the upper
section
Tray lift time Up: max. 15sec
Down: max. 5sec
Power consumption Normal operation 26.4W or less
Lift up 42W or less
Power source 24V and 5V are supplied from the main unit
External dimensions 376 (W) x 545.5 (D) x 517.5 (H) mm
Occupying area 376 (W) x 545.5 (D) mm
Weight About 35kg or less
Paper feed system Paper pick-up by the take-up roller, Torque
limiter reverse rotation separation system
Humidifying heater Power supplied from the main unit, ON/OF
control by the main unit
Heater kit support
Factory setting AB series A4
Inch series LT
1

: Jan. 9 2004
1
AR-LC6 INTERNAL CONSTRUCTION 3 - 1
[3] INTERNAL CONSTRUCTION
1. Motor, clutch, solenoid
No. Parts MODEL NOTE
Code Signal name Name Type Function/Operation Active condition
1 LTM LTM Transport
motor
Brushless
motor
Drives the paper feed, and the
paper transport section.
When paper feed is started,
"H" level.
2 LLM LLM Lift motor Brush motor Lifts the paper feed table. When the lower limit sensor
is ON, "H" level. When the
upper limit sensor is ON, "L"
level.
3 LTCL LTCL Transport
clutch
Controls ON/OFF of the
transport roller.
4 LPFCL LPFCL Paper feed
clutch
Controls ON/OFF of the paper
feed roller.
When paper feed is started,
"H" level. After starring
transport (pickup OFF), it is
turned OFF by the timer.
5 LPSL LPSL Paper feed
solenoid
Presses the paper pickup roller
onto paper.
Turned OFF after starting
transport. Turned ON by the
timer.
∗Lift-up –When paper
empty detection is made:
ON
3
5
41
2
1
1
1
1

: Jan. 9 2004
1
AR-LC6 INTERNAL CONSTRUCTION 3 - 2
2. PWB, sensor, switch, heater
No. Parts MODEL NOTE
Code Signal name Name Type Function/Operation Active condition
7 MAIN PWB –LCC main
PWB
Controls and drives the LCC.
8 LLD LLD Lower limit
sensor
The lower limit of the tray is
detected.
When lifting up, "L" level.
9 LRE LRE Lift motor
encoder
The lift motor rotation is
detected.
Pulse signal
10 LCD LCD Cassette
detection
The tray insertion is detected. When inserted, "H" level.
11 LTOD LTOD The main unit
connection
sensor
Detects connection to the main
unit.
When connected, "H" level.
12 LTD LTD Transport
sensor
Detects paper transport. "L" level at paper
remaining detection.
13 LUD LUD Upper limit
sensor
Detects the paper upper limit
position.
When "H" level (ON), the
lift-up motor stops.
14 LPED LPED Paper
presence/
empty sensor
Detects paper presence/empty
on the paper tray.
When paper is detected,
"H."
∗When lifting up, if "L"
with LRE 800 pulse, the
paper feed solenoid is
ON.
15 LLSW LLSW Upper limit
switch
Protects the paper feed unit
from breakage due to lifting the
tray too much.
16 LOSW LOSW Upper open/
close switch
Detects open/close of the
upper door.
17 DH DH Thermal
heater
Keeps temperature in the LCC
tray.
Japan
only
1
7
8
9
10
11
14 13
15 16
17
12
1
1
1
1

: Jan. 9 2004
1
AR-LC6 OPERATIONAL DESCRIPTIONS 4 - 1
[4] OPERATIONAL DESCRIPTIONS
1. Lift operation
When the main unit is turned ON, if the tray is at the lower limit position
(lower limit sensor: LLD ON position), the lift motor is turned ON to lift
the tray.
When the paper presence/empty sensor (LPED) is turned ON within
800 pulses of the encoder signal from start of lifting up the tray, the lift
motor is turned OFF to stop the tray, and the paper feed solenoid is
turned ON to mode down the pickup roller. After that, the lift motor is
turned ON to lift the tray. The tray is stopped when the upper limit sen-
sor (LUD) is turned ON.
If the paper presence/empty sensor (LPED) is not turned on within 800
pulses, the paper feed solenoid is turned ON with the lift motor ON to
move down the pickup roller. Then, the lift motor is turned ON again to
lift the tray. The lift motor is stopped at the upper limit sensor (LUD) ON
position, and the paper feed solenoid is turned OFF.
When the machine power is turned on, if the tray is on the paper feed
position, lifting is not performed.
When the tray is pulled out, it moves down by its own weight.
Lifting up operation (When LPED is turned ON within 800 pulses
of encoder.)
Lifting up operation (When LPED is not turned ON within 800
pulses of encoder.)
2. Paper feed operation
When the tray is stationary at the paper feed position (upper limit sen-
sor: LUD ON position) and there is paper on the tray, paper feed oper-
ation can be performed.
Paper feed operation is performed by the transport motor (LTM), the
transport clutch (LTCL), the paper feed clutch (LPFCL), and the paper
feed solenoid (LPSL) at the following timing.
When the transport clutch (LTCL) is turned ON with the transport motor
(LTM) ON (rotating), the transport roller rotates. When the paper feed
clutch (LPFCL) is turned on under this state, the paper feed roller and
the take-up roller rotate. When the paper feed solenoid (LPSL) is
turned ON, the take-up roller is pushed down to press paper.
LCC paper feed time chart
LLM
(Lift motor output)
LLD
(Lower limit sensor)
LUD
(Upper limit sensor)
LPED
(Paper empty detection)
LPSL
(Solenoid) Within 800 pulses
200 msec
LRE
(Encoder signal)
LLM
(Lift motor output)
LLD
(Lower limit sensor)
LUD
(Upper limit sensor)
LPED
(Paper empty detection)
LPSL
(Solenoid)
LRE
(Encoder signal)
Within 800 pulses
1
LTM
(Transport motor)
LTD
(Transport sensor)
TRC
(Main unit
synchronous signal)
LTCL
(Transport clutch)
LPFCL
(Paper feed clutch)
LPSL
(Paper feed solenoid)
Paper feed start
Clearance-between-
papers control timer
PIC drop timer PIC drop timer PIC drop timer PIC drop timer
Clearance-between-
papers control timer Clearance-between-
papers control timer Clearance-between-
papers control timer
Resist stop Resist stop Resist stop
Paper feed clutch
OFF timer Paper feed clutch
OFF timer Paper feed clutch
OFF timer Paper feed clutch
OFF timer Paper feed clutch
OFF timer
Preliminary
paper feed start
First sheet
Preliminary
paper feed start
Second sheet
Preliminary
paper feed start
Third sheet
Preliminary
paper feed start
Fourth sheet
Preliminary
paper feed start
Fifth sheet
Preliminary paper
feed complete
Paper feed start
Preliminary paper
feed complete
Paper feed start
Preliminary paper
feed complete
Paper feed start
Preliminary paper
feed complete Preliminary paper
feed complete
1

: Jan. 9 2004
1
AR-LC6 OPERATIONAL DESCRIPTIONS 4 - 2
3. Paper empty detection
When the tray lifts and stops at the paper feed position and during
paper feed operation, paper presence/empty is detected by the paper
presence/empty sensor (LPED).
When paper empty is detected in the tray during paper feeding, paper
feeding is stopped.
3
4
51
2
6
7
1
1 Paper feed roller clutch
2 Take-up roller
3 Paper feed roller
4 Paper feed solenoid
5 Transport clutch
6 Transport motor
7 Lift-up motor
1

AR-LC6 DISASSEMBLY, ASSEMBLY, MAINTENANCE 5 - 1
[5] DISASSEMBLY, ASSEMBLY, MAINTENANCE
1. Maintenance system table
✕: Checking (clean, replace or adjust as required) ❍: Cleaning ▲: Replace ∆: Adjust ✩: Lubricate ❏: Position shift
(Note) Replacement reference: For replacement, refer to each paper feed port counter value.
Paper feed roller related section: 200K or 1 year
Torque limiter: 800K
2. Maintenance parts replacement procedures
A. Paper feed roller
1) Pull the lever, and open the upper cover.
2) Remove the screw, and remove the sheet.
3) Remove the pawl, and remove the pickup roller and the paper feed
roller.
4) Remove the screw, and remove the paper guide block.
5) Remove the pawl, and remove the reverse roller.
AR-M550U/M550N
(PM: 250K) When
calling
250K 500K 750K 1000K 1250K 1500K 1750K 2000K
Remark
AR-M620U/M620N
(PM: 300K) 300K 600K 900K 1200K 1500K 1800K 2100K 2400K
Unit name No. Part name (Note)
Paper feed
separation
section
1 Paper pickup roller/
Paper feed rollers ✕❍❍❍❍❍❍❍❍
(Note)
2 Torque limiter ✕ ✕✕✕ ✕ ✕ ✕ ✕ ✕
Transport
section
3 Transport rollers ✕❍❍❍❍❍❍❍❍
4 Transport paper guides ❍❍❍❍❍❍❍❍❍Gears (Specified position)
Drive
section
5 Gears ✕ ✩✩✩ ✩ ✩ ✩ ✩ ✩
6Belt ✕✕✕ ✕ ✕ ✕ ✕ ✕
Others 7 Sensors ✕ ✕✕✕ ✕ ✕ ✕ ✕ ✕

AR-LC6 DISASSEMBLY, ASSEMBLY, MAINTENANCE 5 - 2
3. Each unit removal
A. Paper feed unit
1) Pull out the tray.
2) Open the upper cover, and remove three screws.
3) Remove the upper cabinet.
4) Disconnect the connectors (2 positions).
5) Remove the screw, and remove the paper feed unit.
B. Paper feed tray
1) Pull out the tray.
2) Remove the screws from the left and right rail sections.
3) Remove the tray unit from the rail.
C. Drive unit
1) Remove the screw, and remove the rear cover.
2) Remove the connectors (2 positions).

AR-LC6 DISASSEMBLY, ASSEMBLY, MAINTENANCE 5 - 3
3) Remove the screw, and remove the drive unit.
4. Major parts removal
A. Motor (Main)
1) Remove the screw, and remove the rear cover.
2) Disconnect the connector.
3) Remove the screw, and remove the motor.
B. Lift motor
1) Remove the drive unit.
2) Remove the E-ring, and remove the parts.
3) Remove the screw, and remove the cover.
4) Remove the screw, and remove the lift motor.
5) Remove the ring, and remove the pulley.
C. Clutch
1) Remove the paper feed unit. (Refer to "3. Each unit removal.")
2) Remove the screw, and remove the cover.
3) Remove the E-ring, and remove the parts.

: Jan. 9 2004
1
AR-LC6 DISASSEMBLY, ASSEMBLY, MAINTENANCE 5 - 4
4) Disconnect the connector, and remove the screw.
5) Remove the frame.
6) Remove the connector, and the E-ring, and remove the paper feed
transport clutch.
D. Paper feed solenoid
1) Remove the paper feed unit.
2) Remove the cover.
3) Remove the screw, and remove the unit.
4) Disconnect the connector.
5) Remove the screw, and remove the solenoid.
E. Torque limiter
1) Remove the paper feed unit.
2) Remove the cover.
3) Remove the E-ring and the screw, and remove the parts.
4) Lift the shaft, and remove the torque limiter.
1
1

AR-LC6 DISASSEMBLY, ASSEMBLY, MAINTENANCE 5 - 5
F. Transport roller
1) Remove the paper feed unit.
2) Remove the cover.
3) Remove the spring, and remove the screw.
4) Remove the plate cover, and remove the lever.
5) Remove the clutch.
6) Remove the screw and the E-ring, and remove the parts.
7) Remove the transport roller.

AR-LC6 ADJUSTMENT 6 - 1
[6] ADJUSTMENT
Each adjustment item in the adjustment item list is indicated with its JOB number. Perform the adjustment procedures in the sequence of Job numbers
from the smallest to the greatest.
However, there is no need to perform all the adjustment items. Perform only the necessary adjustments according to the need.
Unnecessary adjustments can be omitted. Even in this case, however, the sequence from the smallest to the greatest JOB number must be observed.
If the above precaution should be neglected, the adjustment would not complete normally or a trouble may occur.
1. Setting item list
2. Details
1) Set the print off-center adjustment mode of SIM 50-10 by the key
operation of the machine. (Press the keys as shown below to enter
SIM 50-10.)
2) In SIM 50-10, the display is shown as follows. The print off-center
adjustment value can be set for each paper feed tray.
3) Select "0: TRAY SELECT" and press START key.
The display is shown as follows. Select "6: LCC" as the paper feed
tray, and press START key.
4) The display is shown as follows again. Select "8: LCC" and press
START key.
5) Then enter the adjustment value with 10-key.
(Default: 50, Adjustment range: 0 –99)
•When the adjustment value is decreased by 1, the image is
shifted to the rear side by 0.1mm.
•When the adjustment value is increased by 1, the image is
shifted to the front side by 0.1mm.
6) Enter the adjustment value and press START key, and printing is
started and the set value is stored.
7) Check the printed self-print result, and repeat procedures 5) –6)
until the value is in the range of 0 ± 3mm.
When the value is in the above range, press CA key to terminate
the simulation.
Job No. Adjustment item list Simulation to
be used
ADJ 1 Print off-center adjustment 50-10
ADJ 2 Resist amount adjustment ADJ 2A Adjustment in the resist amount adjustment mode 51-2
ADJ 2B Adjustment in the print lead edge adjustment mode 50-5
ADJ 1 Print off-center adjustment
Adjustment position Set value
Display
item Item description Default Set
range
TRAY1 TRAY1 Print off center
adjustment position
TRAY2 TRAY2
(LCC left
side)
Print off center
adjustment position
TRAY3 TRAY3
(LCC right
side)
Print off center
adjustment position
TRAY4 TRAY4 Print off center
adjustment position
MFT Manual
paper feed
Print off center
adjustment position
LCC Large
capacity tray
Print off center
adjustment position
50 0 to
99
Shift by
0.1mm for
set value 1
ADU Duplex Print off center
adjustmentposition
(ADU)
#/P C
∗50 10
∗
2
SIMULATION 50-10
PRINT OFF-CENTER ADJUSTMENT. SELECT 0-9, AND PRESS
START.
0.TRAY SELECT 11.COPY START
2.MAGNIFICATION 100
(ADJUSTMENT DATA)
3.TRAY1 50 4.TRAY2 50 5.TRAY3 50
6.TRAY4 50 7.BPT 50 8.LCC 50 9. ADU 50
1
SIMULATION 50-10
PRINT OFF-CENTER
ADJUSTMENT. SELECT 1-16, AND PRESS
START.
(FEED TRAY)
1.TRAY1 2.TRAY2 3.TRAY3 4.TRAY4
5.BPT 6.LCC
(ABOVE+10: DUPLEX MODE)
2
SIMULATION 50-10
PRINT OFF-CENTER ADJUSTMENT. SELECT 0-9, AND PRESS
START.
0.TRAY SELECT 11.COPY START
2.MAGNIFICATION 100
(ADJUSTMENT DATA)
3.TRAY1 50 4.TRAY2 50 5.TRAY3 50
6.TRAY4 50 7.BPT 50 8.LCC 50 9. ADU 50
50
SIMULATION 50-10
PRINT OFF-CENTER ADJUSTMENT. INPUT VALUE 0-99, AND
PRESS START.
8.LCC
SIMULATION 50-10
PRINT OFF-CENTER ADJUSTMENT. NOW COPYING.
Print lead edge
(Rear side)
a
b
(Front side)
(Print back surface)
Adjust in the range
of the figure
(0 ± 3mm).

AR-LC6 ADJUSTMENT 6 - 2
1) Set the resist amount adjustment mode of SIM 51-02 by the key
operation of the machine.
2) In SIM 51-02, the display is shown as follows. The resist amount
adjustment value can be set for each paper feed tray.
3) Select "0: TRAY SELECT" and press START key.
The display is shown as follows. Select "6: LCC" as the paper feed
tray, and press START key.
4) The display is shown as follows again. Select "7: LCC" and press
START key.
5) Then enter the adjustment value with 10-key.
(Default: 50, Adjustment range: 0 –99)
•When the adjustment value is increased by 1, the resist amount
is increased by 1msec.
6) Enter the adjustment value and press START key, and printing is
started and the set value is stored.
7) After completion of the adjustment, press [CA] key to terminate the
simulation mode.
1) Set the print lead edge adjustment mode of SIM 50-5 by the key
operation of the machine.
2) In SIM 50-5, the display is shown as follows. The resist amount
adjustment value can be set for each paper feed tray.
3) Select "0: TRAY SELECT" and press START key.
The display is as shown below. Select "6: LCC" as the paper feed
tray and press START key.
4) The display is as shown below again. Select "8: LCC" and press
START key.
5) Then, enter the adjustment value with 10-key.
(Default: 50, Adjustment range: 0 –99)
•When the adjustment value is increased by 1, the resist amount
is increased by 1msec.
6) After entering the adjustment value, press START key, and print-
ing is started and the set value is stored.
7) After completion of the adjustment, press [CA] key to terminate the
simulation mode.
ADJ 2 Resist amount adjustment
ADJ 2A Adjustment in the resist amount
adjustment mode
#/P C
∗51 2
∗
1
SIMULATION 51-2
RESIST TIMING ADJUSTMENT. SELECT 0-14, AND PRESS START.
0.TRAY SELECT 11.PRINT START
2.TRAY1 50 3.TRAY2 50 4.TRAY3 50
5.TRAY4 50 6.BPT 50 7.LCC 50
8.ADU 50 9.SPF(TOP) 50 10.SPF(HIGH) 50
11.SPF(LOW) 50 12.SPF FEED(TOP) 50
13.SPF FEED(HIGH) 50 14.SPF FEED(LOW) 50
1
SIMULATION 51-2
RESIST TIMING ADJUSTMENT. SELECT 1-6, AND PRESS START.
(FEED TRAY)
1.TRAY1 2.TRAY2 3.TRAY3 4.TRAY4
5.BPT 6.LCC
(ABOVE+10: DUPLEX MODE)
1
SIMULATION 51-2
RESIST TIMING ADJUSTMENT. SELECT 0-14, AND PRESS START.
0.TRAY SELECT 11.PRINT START
2.TRAY1 50 3.TRAY2 50 4.TRAY3 50
5.TRAY4 50 6.BPT 50 7.LCC 50
8.ADU 50 9.SPF(TOP) 50 10.SPF(HIGH) 50
11.SPF(LOW) 50 12.SPF FEED(TOP) 50
13.SPF FEED(HIGH) 50 14.SPF FEED(LOW) 50
50
SIMULATION 51-2
RESIST TIMING ADJUSTMENT. INPUT VALUE 0-99, AND PRESS
START.
7.LCC
SIMULATION 51-2
RESIST TIMING ADJUSTMENT. NOW PRINTING.
ADJ 2A Adjustment in the print lead edge
adjustment mode
#/P C
∗50 5
∗
2
SIMULATION 50-5
LEAD EDGE ADJUSTMENT. SELECT 0-12, AND PRESS START.
0.TRAY SELECT 11.PRINT START
(ADJUSTMENT DATA)2.RRCB 50
3.TRAY1 50 4.TRAY2 50 5.TRAY3 50
6.TRAY4 50 7.BPT 50 8.LCC 50 9.ADU 50
(VOID AREA SETTING) 10.DENA 50 11.DENB 30 12.FR VOID 30
1
SIMULATION 50-5
LEAD EDGE ADJUSTMENT. SELECT 1-6, AND PRESS START.
(FEED TRAY)
1.TRAY1 2.TRAY2 3.TRAY3 4.TRAY4
5.BPT 6.LCC
(ABOVE+10: DUPLEX MODE)
2
SIMULATION 50-5
LEAD EDGE ADJUSTMENT. SELECT 0-12, AND PRESS START.
0.TRAY SELECT 11.PRINT START
(ADJUSTMENT DATA)2.RRCB 50
3.TRAY1 50 4.TRAY2 50 5.TRAY3 50
6.TRAY4 50 7.BPT 50 8.LCC 50 9.ADU 50
(VOID AREA SETTING) 10.DENA 50 11.DENB 30 12.FR VOID 30
50
SIMULATION 50-5
LEAD EDGE ADJUSTMENT. INPUT VALUE 0-99, AND PRESS
START.
8.LCC
SIMULATION 50-5
LEAD EDGE ADJUSTMENT. NOW PRINTING.

AR-LC6 TROUBLESHOOTING 7 - 1
[7] TROUBLESHOOTING
1. General
When a trouble occurs in the machine or when the life of a consumable
part is nearly expired or when the life is expired, the machine detects
and displays it on the display section or notifies to the user or the ser-
viceman by voice messages. This allows the user and the serviceman
to take the suitable action. In case of a trouble, this feature notifies the
occurrence of a trouble and stops the machine to minimize the dam-
age.
2. Function and purpose
1) Securing safety. (The machine is stopped on detection of a trou-
ble.)
2) The damage to the machine is minimized. (The machine is
stopped on detection of a trouble.)
3) By displaying the trouble content, the trouble position can be
quickly identified. (This allows to perform an accurate repair,
improving the repair efficiency.)
4) Preliminary warning of running out of consumable parts allows to
arrange for new parts in advance of running out. (This avoids stop-
ping of the machine due to running out the a consumable part.)
3. Self diag message kinds
The self diag messages are classified as shown in the table below.
4. Self diag operation
A. Self diag operation and related work flow
The machine always monitors its own state.
When the machine recognizes a trouble, it stops the operation and dis-
plays the trouble message.
A warning message is displayed when a consumable part life is nearly
expired or is expired.
When a warning message is displayed, the machine may be or may
not be stopped.
The trouble messages and the warning messages are displayed by the
LCD.
Some trouble messages are automatically cleared when the trouble is
repaired. Some other troubles must be cleared by a simulation.
Some warning messages of consumable parts are automatically
cleared when the trouble is repaired. Some other warning messages
must be cleared by a simulation.
Class 1 User Warning of troubles which can be recovered by
the user. (Paper jam, consumable part life
expiration, etc.)
Service
man
Warning of troubles which can be recovered
only by a serviceman. (Motor trouble,
maintenance, etc.)
Other —
Class 2 Warning Warning to the user, not a machine trouble
(Preliminary warning of life expiration of a
consumable part, etc.)
Trouble Warning of a machine trouble. The machine is
stopped.
Other —
Troubleshoot the cause.
YES
NO
Detects/analyzes
the content.
Trouble/Warning Warning
Trouble
The machine is stopped.
The content is displayed.
Trouble/Warning Warning
A consumable
part has reached
its lifetime.
Trouble
Replace or supply
the consumable part.
Cancel the self-
diagnostic message with
the diagnostics
(test commands).
Reset
Standby state
Monitors the machine
conditions.
Repair

AR-LC6 TROUBLESHOOTING 7 - 2
5. List
6. Details
No. MAIN
CODE
SUB
CODE Title (Content) Section Operation mode Countermeasure (Remedy) Note
1 U6 09 Lift motor trouble LCC Tray lift-up Check connection.
2 20 Communication trouble LCC LCC communication Turn OFF/ON the power.
3 21 Transport motor trouble LCC Paper feed Check connection.
4 22 24V trouble LCC Power ON Check connection.
Main Sub Title Lift motor trouble
U6 09 Display Message
Phenomenon Detail LCC lift motor operation
trouble. Tray lift-up trouble
Section LCC
Case 1 Cause Defective connection or
disconnection of connector
and harness
Check
and
Remedy
Check the connector and
the harness in the motor
line. Connect the connector
properly. Replace the
harness.
Case 2 Cause Motor lock, motor rpm
abnormality, motor
overcurrent, LRE trouble,
intrusion of foreign material
Check
and
Remedy
Use SIM 4-2 to select LRE
and check the operation of
the single unit. Use SIM 4-3
to select LLM and check the
operation of the single unit.
Check for intrusion of any
foreign material in the drive
system.
Case 3 Cause LC main PWB trouble, lift
motor trouble
Check
and
Remedy
Replace the LCC main PWB
or the lift motor.
Main Sub Title Communication trouble
U6 20 Display Message
Phenomenon Detail Communication error with
LCC, communication line
test error after turning on the
power or canceling an
exclusive simulation.
Section LCC
Case 1 Cause Defective connection or
disconnection of connector
and harness
Check
and
Remedy
Check the connector and
the harness of the
communication line.
Connect the connector
properly. Replace the
harness.
Case 2 Cause LCC main PWB trouble,
control PWB (PCU) trouble
Check
and
Remedy
Replace the LCC PWB.
Replace the control PWB
(PCU).
Case 3 Cause Malfunction caused by
noises
Check
and
Remedy
Cancel by turning OFF/ON
the power.
Main Sub Title Transport motor trouble
U6 21 Display Message
Phenomenon Detail LCC transport motor
operation trouble
Section LCC
Case 1 Cause Defective connection or
disconnection of connector
and harness
Check
and
Remedy
Check the connector and
the harness in the motor
line. Connect the connector
properly. Replace the
harness.
Case 2 Cause Motor lock, motor rpm
abnormality, motor
overcurrent, intrusion of
foreign material
Check
and
Remedy
Use SIM 4-3 to select LTM
and check the operation of
the single unit. Check for
intrusion of any foreign
material in the drive system.
Case 3 Cause LCC main PWB trouble,
transport motor trouble
Check
and
Remedy
Replace the LCC main PWB
or the transport motor.
Main Sub Title 24V trouble
U6 22 Display Message
Phenomenon Detail 24V supply for LCC is cut
off.
Section LCC
Case 1 Cause Defective connection or
disconnection of connector
and harness
Check
and
Remedy
Check the connector and
the harness which connect
LCC and the main unit.
Connect the connector
properly. Replace the
harness.
Case 2 Cause Power source fuse blown-off
Check
and
Remedy
Check for short circuit
between 24V and GND.
Check for pinched harness
and the LCC main PWB
trouble. Replace the fuse,
the harness, and the LCC
main PWB.
Case 3 Cause Power source abnormality in
the main unit
Check
and
Remedy
Check 24V output on the
main unit side.

: Jan. 9 2004
1
AR-LC6 ELECTRICAL SECTION 8 - 1
[8] ELECTRICAL SECTION
1. Actual wiring chart
LIFT
MOTOR
LRE LRE
+5V
1GND2
Input lift motor encoder
2
3
+5V
B8B-PH-K-S
CN-B
GND2
3
1
6
4
8
2
7
5
LTLSL
+24V
+5V
GND2
LRE
LLD
1
2
LLM+
LLM-
N.C.
LCC MAIN PWB
+5V
LLM 5
GND2
6
9
N.C. 7
B14B-PHDSS-B
2
8
3GND2
LTM
LCD
4
LTM-T 10
LLM(GND)
11
LTM-CLK
CN-E
1
N.C.
B12B-PHDSS-B
11
/DSR-LCC
RES-LCC
9
GND1
4
1
3
+5V
/TRC-LCC
5
2
CN-A
12
N.C.
7
/DTR-LCC
6
+24V
8
10
RXD-LCC
GND2
TXD-LCC
+5V LTOD
Paper feed clutch
12
11
10
9
9
10
11
12
3
65
3
SMP-18V-NC
5
2
1
77
2
SMR-18V-N
8
2
1
3
4
6
8
1
4
1
2
2
1
2
1
GND2
1
5
LCC transport motor
4
/LPED
2
LTM-T
+24V
GND1
The main unit connection sensor
/LUD LUD
LPED
LTM
LTM-CLK
2LTM
3
+5V
1 GND2
2
3
NC
3
+5V
3
PHR-5
1
LTOD
Tray upper limit sensor
Paper feed solenoid
3
3
2
1COM
LPSL
LLSWON
1
Upper limit switch
Tray paper sensor
2
GND2
LPFCL
1
Main unit connection
13
6
3
11
12
8
9
ELP-15V
4
15
10
2
7
5
14
10
16
14
1
18
12
5
+5V
GND1
11
17
LTCL
7GND2
GND2
LPSL(+24V)
+24V
CN-C
+24V
15
+5V
4
13
LTOD
20
22
9
B24B-PHDSS-B
2
8
/LPED
+5V
23 +5VR24
3
/LTD
+5V
19
GND2
LPFCL
21
GND2
NC3
2
1COM LOSWON
Upper open/close switch
15
16
17
18
13
14 13
14
15
16
17
18
<Paper feed unit>
11
22
33
2
1
3
4
5
6
+24V
+24V(LOSW)
GND2
CN-D
B10B-PHDSS-B
211 2
Heater
7
9
10
GND2
GND2
8
+24V(LOSW)
GND2
GND2
4
12
ELP-12V
5
Earth
+5V3
2
1 LCD LCDGND2
Cassette detection
ELP-02V ELR-02V
1
3
ELP-03V
23
2
1
3
2
12
3
1
ELR-03V
SMP-03V-NC SMR-03V-N
SMR-03V-N SMP-03V-NC
SMP-03V-NC
SMR-02V-NSMP-02V-NC
SMR-03V-N
Lift motor
LLD LLD
+5V
1GND2
Lower limit sensor
2
3
3
2
12
3
1
SMP-03V-NC SMR-03V-N
1
SMP-03V-NC
32
SMR-03V-N
21
3
2
11
2
SMR-02V-NSMP-02V-NC
Paper transport sensor
GND2
1
3
+5VR
2/LTD
LTD
Paper transport clutch
1
21
2
ELR-04NV ELP-04NV
4
34
3
GND2
GND2
+5V
EXIN2
EXIN1
+24V(LLSW)
+24V
/RXD
B11B-PH-K-S
11
GND2(VD)
TEST
9
/RES
4
3
N.C. 5
2
CN-F
/TXD
7
TXD
6
MD
8
10
RES
+5V(VD)
FVpp
1
GND1 12
GND1 13
+24V(LOSW) 14
SMR-03V-N SMP-03V-NC
3
2
1
2
1
3
Main unit
LTCL3
2
1+24V
N.C. LTCL
/LUD
6
1
13
6
3
11
12
8
9
ELR-15V
4
15
10
2
7
5
14
4
12
ELR-12V
5
N.C.
N.C.
TXD-LCC
RXD-LCC
/DTR-LCC
/DSR-LCC
RES-LCC
F.G.
+5V
GND2
+24V
GND1
/TRC-LCC
N.C.
N.C.
AC-L(H)
F.G.
AC-N(H)
179228-3
FPS-187
PHR-3
CZHR-03V-S
PHR-3
179228-3
1
1
1
PS-187-3V

: Jan. 9 2004
1
AR-LC6 ELECTRICAL SECTION 8 - 2
2. Block diagram
EEPROM
RXD-LCC
DSR-LCC
TXD-LCC
DTR-LCC
RES-LCC
GND2
5V
24V
GND1
F.G.
Main unit
Communication
buffer circuit
Xtal
7.37MHz
24V monitor
circuit
24V
Upper door open/close
switch (LOSW)
Upper limit switch (LLSW)
Lift motor (LLM)
Upper limit sensor
(LUD)
Lower limit sensor
(LLD)
Paper presence/empty
sensor (LPED)
Paper exit sensor (LTD)
Main unit connection
sensor (LTOD)
Cassette sensor (LCD)
Remaining quantity
sensor (LRE)
Paper feed clutch
(LPFCL)
Transport clutch
(LTCL)
Paper feed solenoid
(LPSL)
Transport motor
(LTM)
Upper door detection
monitor circuit
Upper limit detection
monitor circuit
Poly-switch 1.1A
Lift motor drive
circuit
Current limit
circuit
Sensor input circuit
Solenoid/clutch drive circuit
CPU (HD64F3644H)
Arithmetic section
On-board write circuit
Power 12V circuit
Communication write circuit
24V 12V
LCC MAIN PWB
LCC
1

LEAD-FREE SOLDER
The PWB’s of this model employs lead-free solder. The “LF”marks indicated on the PWB’s and the Service Manual mean “Lead-Free”solder.
The alphabet following the LF mark shows the kind of lead-free solder.
(1) NOTE FOR THE USE OF LEAD-FREE SOLDER THREAD
When repairing a lead-free solder PWB, use lead-free solder thread.
Never use conventional lead solder thread, which may cause a breakdown or an accident.
Since the melting point of lead-free solder thread is about 40°C higher than that of conventional lead solder thread, the use of the exclusive-use
soldering iron is recommendable.
(2) NOTE FOR SOLDERING WORK
Since the melting point of lead-free solder is about 220°C, which is about 40°C higher than that of conventional lead solder, and its soldering capacity is
inferior to conventional one, it is apt to keep the soldering iron in contact with the PWB for longer time. This may cause land separation or may exceed
the heat-resistive temperature of components. Use enough care to separate the soldering iron from the PWB when completion of soldering is
confirmed.
Since lead-free solder includes a greater quantity of tin, the iron tip may corrode easily. Turn ON/OFF the soldering iron power frequently.
If different-kind solder remains on the soldering iron tip, it is melted together with lead-free solder. To avoid this, clean the soldering iron tip after
completion of soldering work.
If the soldering iron tip is discolored black during soldering work, clean and file the tip with steel wool or a fine filer.
Example:
5mm
Lead-Free
Solder composition
code (Refer to the
table at the right.)
<Solder composition code of lead-free solder>
Solder composition
Sn-Ag-Cu
Sn-Ag-Bi
Sn-Ag-Bi-Cu
Sn-Zn-Bi
Sn-In-Ag-Bi
Sn-Cu-Ni
Sn-Ag-Sb
Bi-Sn-Ag-P
Bi-Sn-Ag
a
b
z
i
n
s
p
Solder composition code
a

(Danish) ADVARSEL !
Lithiumbatteri –Eksplosionsfare ved fejlagtig håndtering.
Udskiftning måkun ske med batteri
af samme fabrikat og type.
Levér det brugte batteri tilbage til leverandoren.
(English) Caution !
Danger of explosion if battery is incorrectly replaced.
Replace only with the same or equivalent type
recommended by the manufacturer.
Dispose of used batteries according to manufacturer’s instructions.
(Finnish) VAROITUS
Paristo voi räjähtää, jos se on virheellisesti asennettu.
Vaihda paristo ainoastaan laitevalmistajan suosittelemaan
tyyppiin. Hävitäkäytetty paristo valmistajan ohjeiden
mukaisesti.
(French) ATTENTION
Il y a danger d’explosion s’il y a remplacement incorrect
de la batterie. Remplacer uniquement avec une batterie du
même type ou d’un type équivalent recommandépar
le constructeur.
Mettre au rebut les batteries usagées conformément aux
instructions du fabricant.
(Swedish) VARNING
Explosionsfara vid felaktigt batteribyte.
Använd samma batterityp eller en ekvivalent
typ som rekommenderas av apparattillverkaren.
Kassera använt batteri enligt fabrikantens
instruktion.
(German) Achtung
Explosionsgefahr bei Verwendung inkorrekter Batterien.
Als Ersatzbatterien dürfen nur Batterien vom gleichen Typ oder
vom Hersteller empfohlene Batterien verwendet werden.
Entsorgung der gebrauchten Batterien nur nach den vom
Hersteller angegebenen Anweisungen.
CAUTION FOR BATTERY REPLACEMENT
CAUTION FOR BATTERY DISPOSAL
(For USA, CANADA)
"BATTERY DISPOSAL"
THIS PRODUCT CONTAINS A LITHIUM PRIMARY
(MANGANESS DIOXIDE) MEMORY BACK-UP BATTERY
THAT MUST BE DISPOSED OF PROPERLY. REMOVE THE
BATTERY FROM THE PRODUCT AND CONTACT YOUR
LOCAL ENVIRONMENTAL AGENCIES FOR INFORMATION
ON RECYCLING AND DISPOSAL OPTIONS.
"TRAITEMENT DES PILES USAGÉES"
CE PRODUIT CONTIENT UNE PILE DE SAUVEGARDE DE
MÉMOIRE LITHIUM PRIMAIRE (DIOXYDE DE MANGANÈSE)
QUI DOIT ÊTRE TRAITÉE CORRECTEMENT. ENLEVEZ LA
PILE DU PRODUIT ET PRENEZ CONTACT AVEC VOTRE
AGENCE ENVIRONNEMENTALE LOCALE POUR DES
INFORMATIONS SUR LES MÉTHODES DE RECYCLAGE ET
DE TRAITEMENT.

All rights reserved.
Printed in Japan.
No part of this publication may be reproduced,
stored in a retrieval system, or transmitted,
in any form or by any means,
electronic; mechanical; photocopying; recording or otherwise
without prior written permission of the publisher.
Trademark acknowledgements
•Microsoft®Windows®operating system is a trademark or copyright of Microsoft
Corporation in the U.S.A. and other countries.
•Windows®95, Windows®98, Windows®Me, Windows NT®4.0, Windows®2000,
and Windows®XP are trademarks or copyrights of Microsoft Corporation in the
U.S.A. and other countries.
•IBM and PC/AT are trademarks of International Business Machines Corporation.
•Acrobat®Reader Copyright®1987- 2002 Adobe Systems Incorporated. All rights
reserved. Adobe, the Adobe logo, Acrobat, and the Acrobat logo are trademarks of
Adobe Systems Incorporated.
•All other trademarks and copyrights are the property of their respective owners.
SHARP CORPORATION
Digital Document System Group
Products Quality Assurance Department
Yamatokoriyama, Nara 639-1186, Japan
2004 January Printed in Japan
Table of contents
Other Sharp All In One Printer manuals
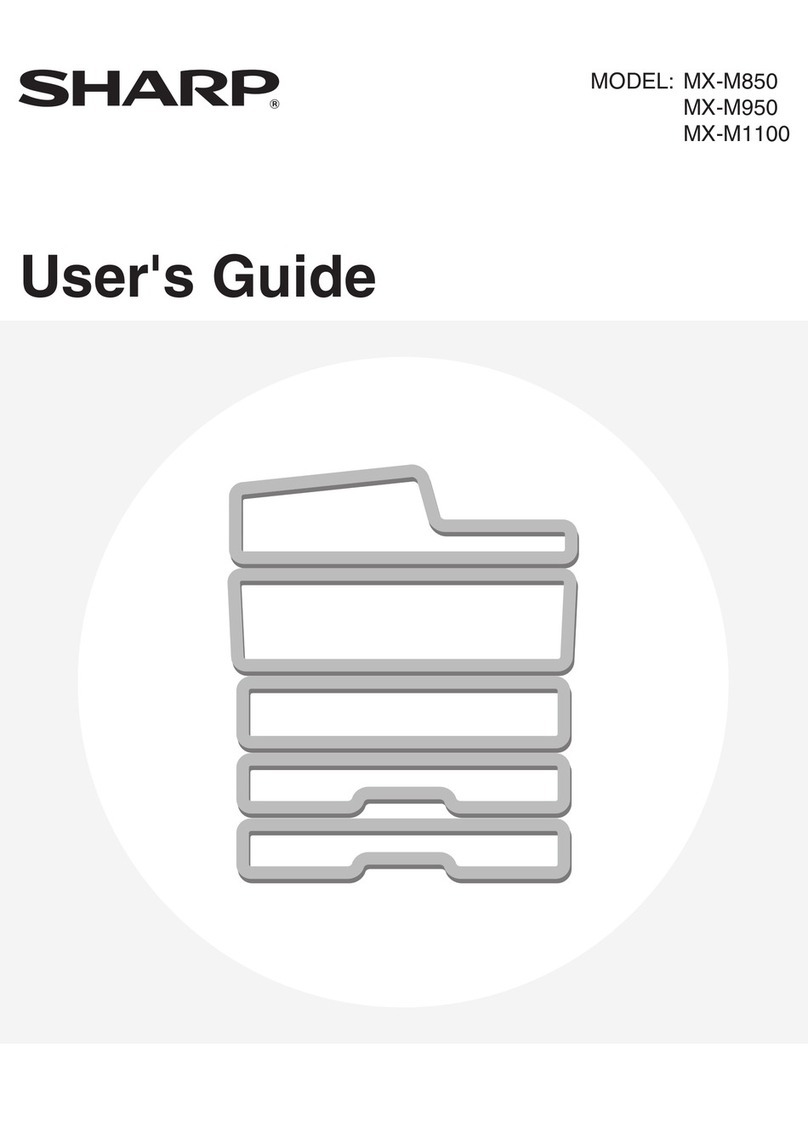
Sharp
Sharp MX-M850 User manual
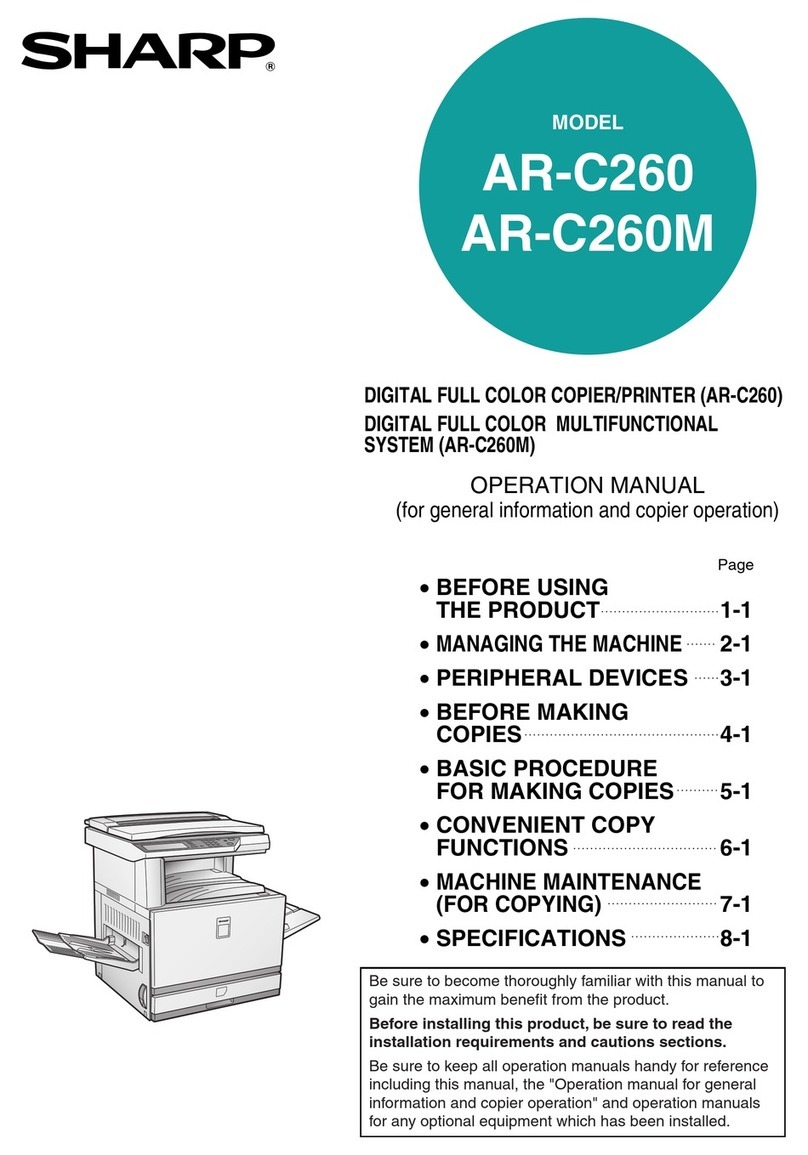
Sharp
Sharp AR-C260 User manual
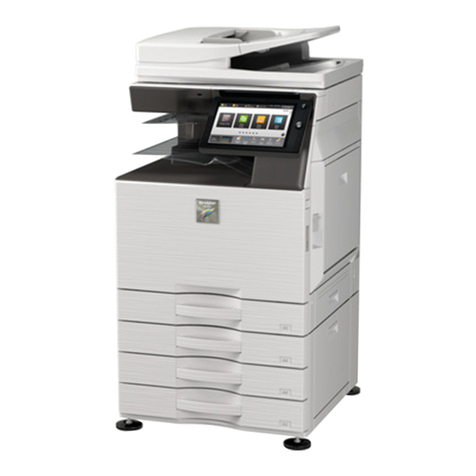
Sharp
Sharp MX-3051 Instruction manual
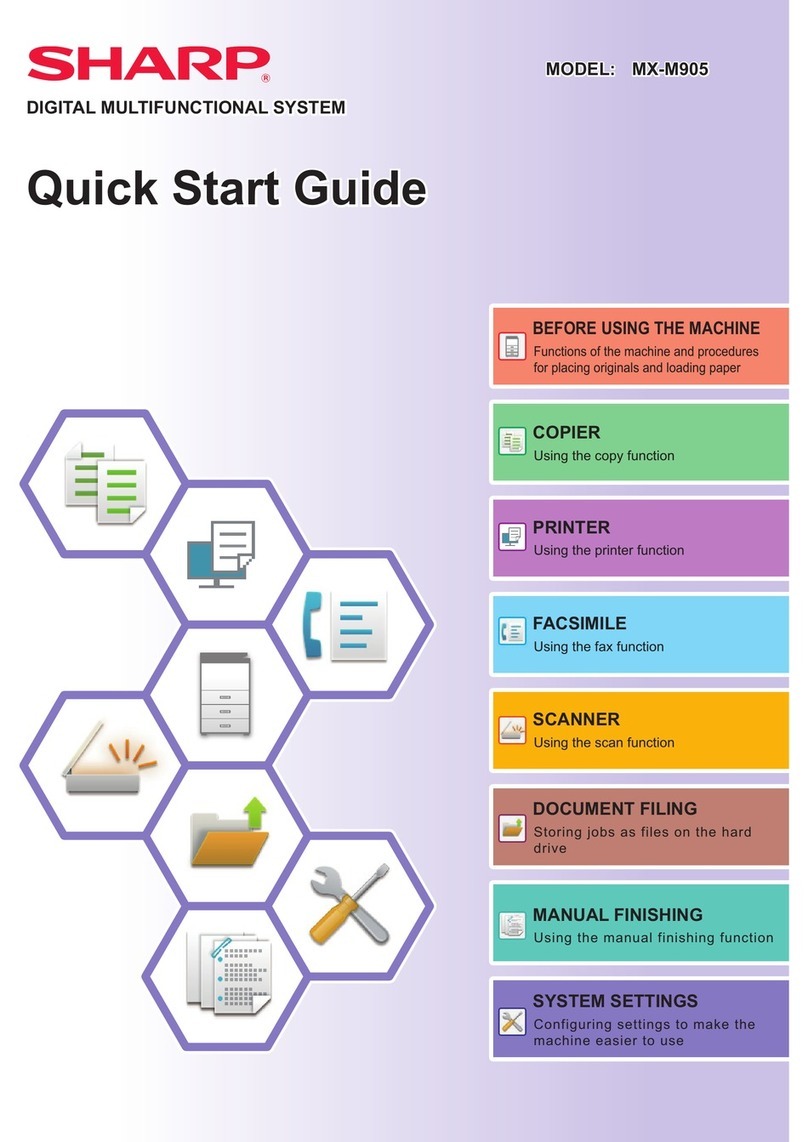
Sharp
Sharp MX-M905 User manual
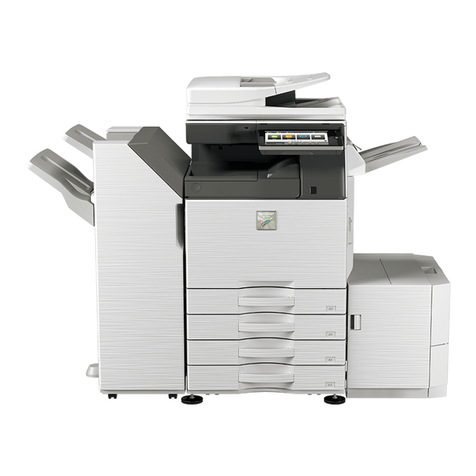
Sharp
Sharp MX-3050N User manual
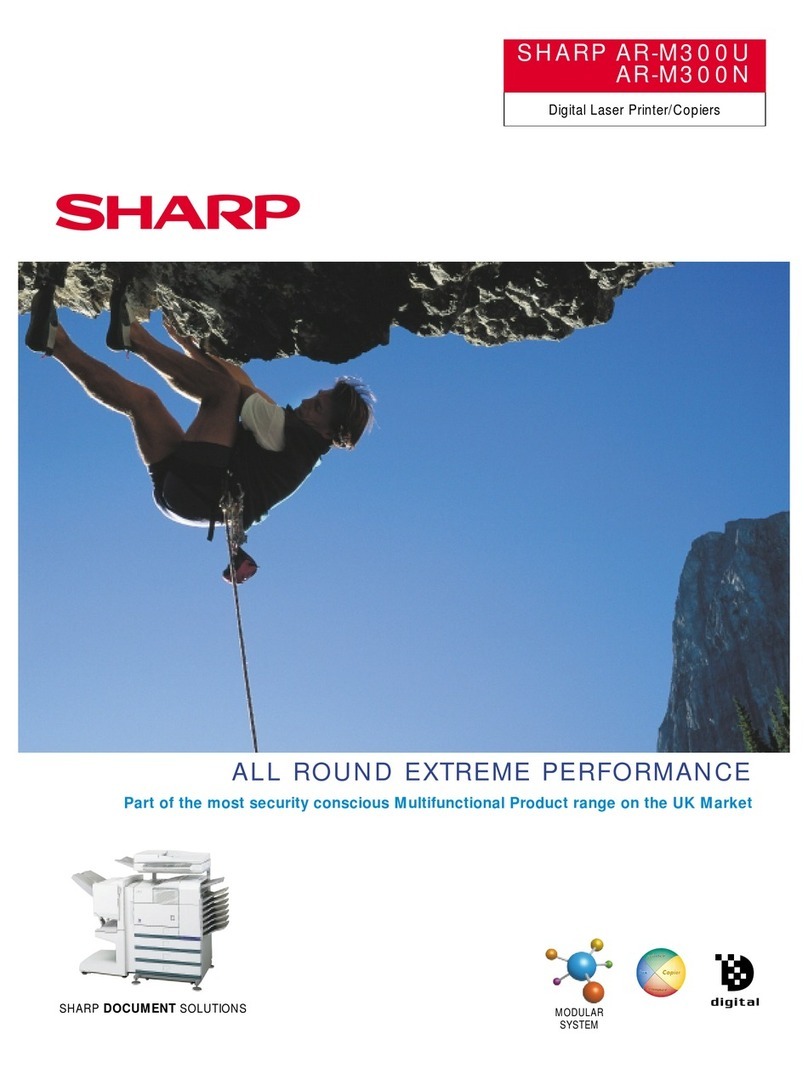
Sharp
Sharp AR-M300N. User manual
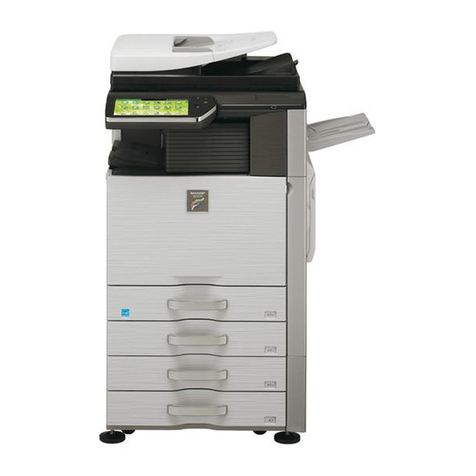
Sharp
Sharp MX-4110N User manual
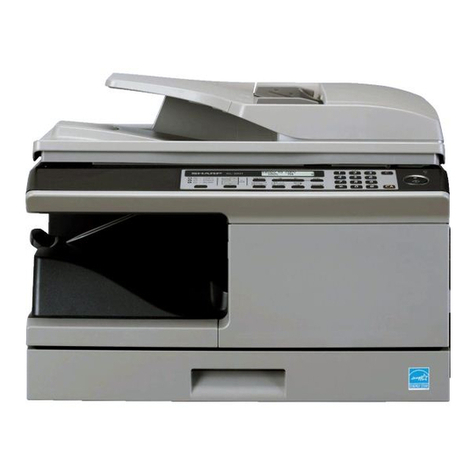
Sharp
Sharp AL-2021 User manual

Sharp
Sharp AL-1642CS User manual
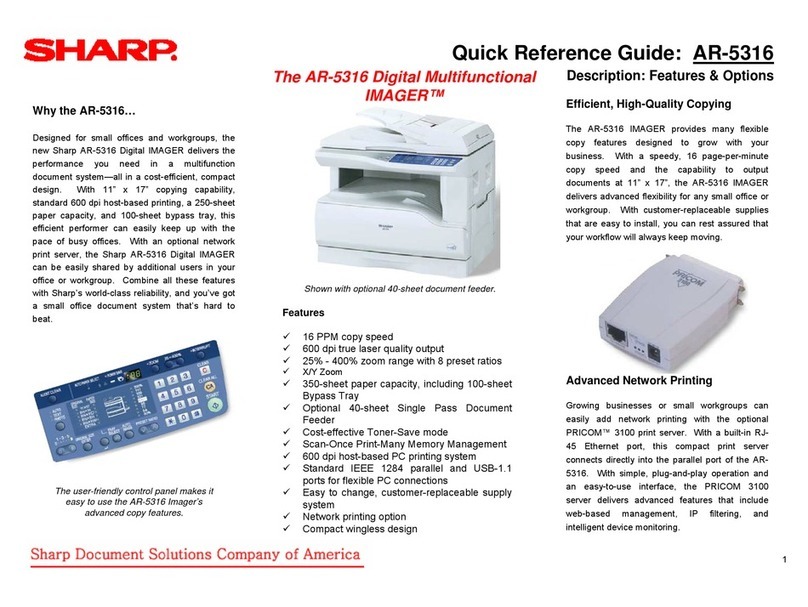
Sharp
Sharp IMAGER AR-5316 User manual
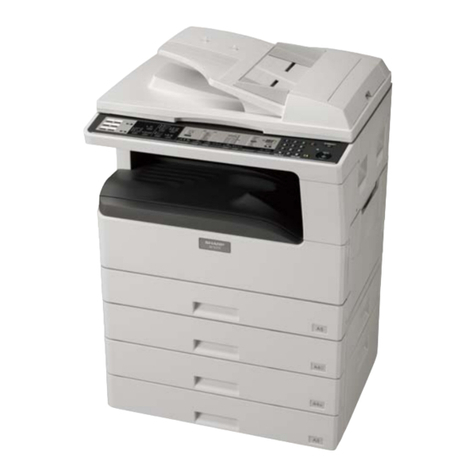
Sharp
Sharp AR-5623N User manual
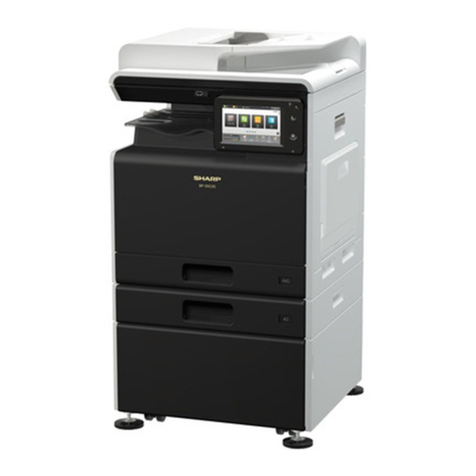
Sharp
Sharp BP-30C25 Instruction manual

Sharp
Sharp MX-B381 Installation and operating manual
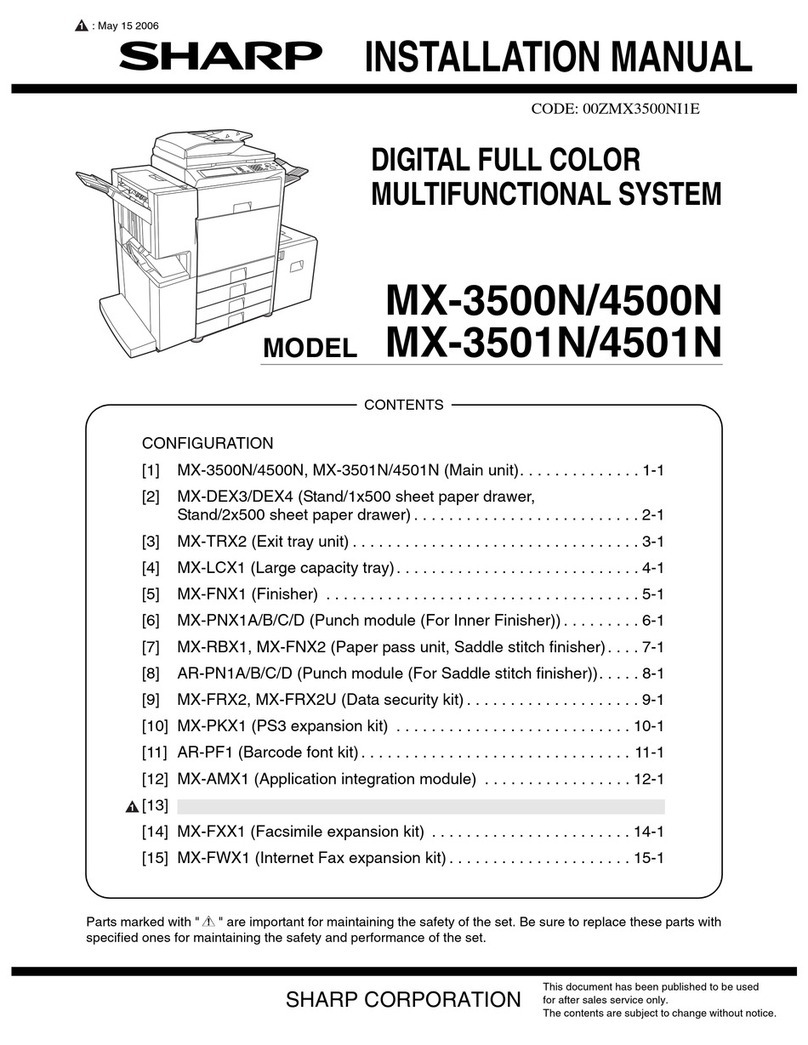
Sharp
Sharp MX-4501N User manual
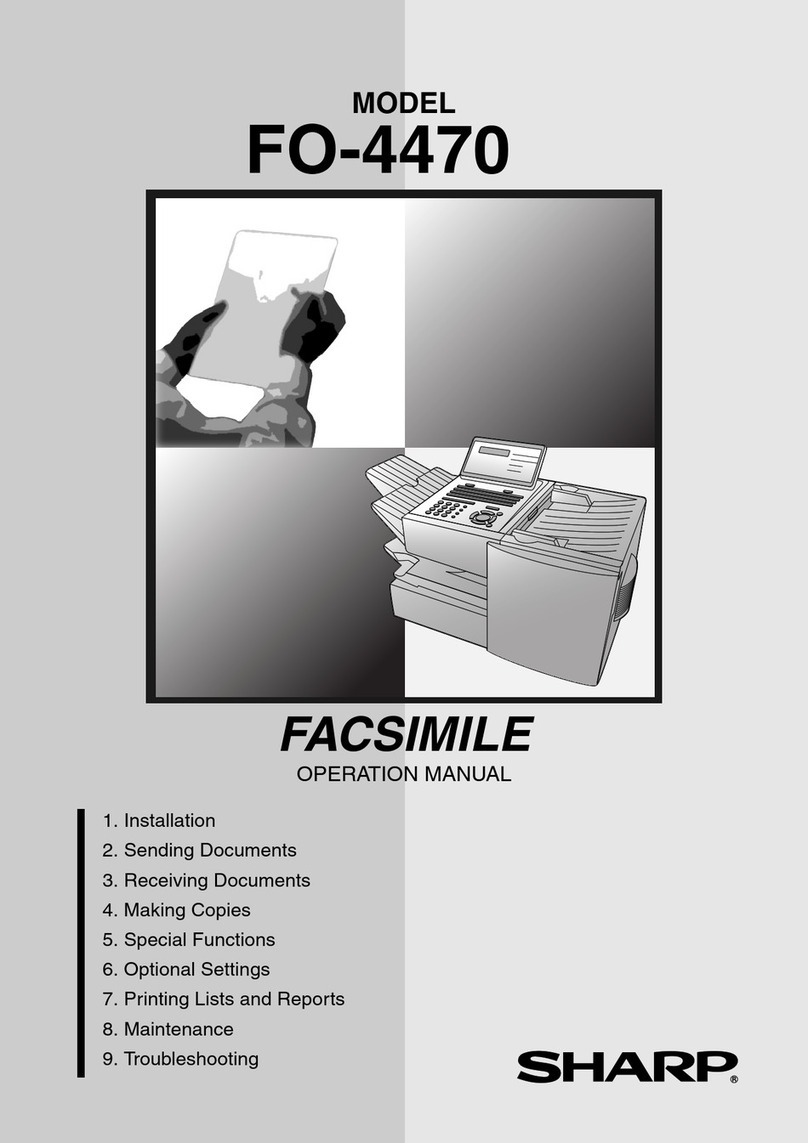
Sharp
Sharp FO-4470 User manual
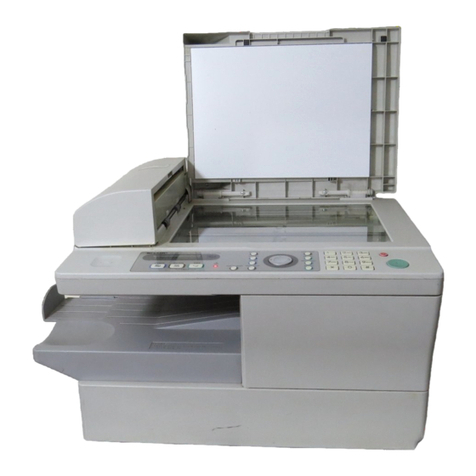
Sharp
Sharp AM-400 User manual
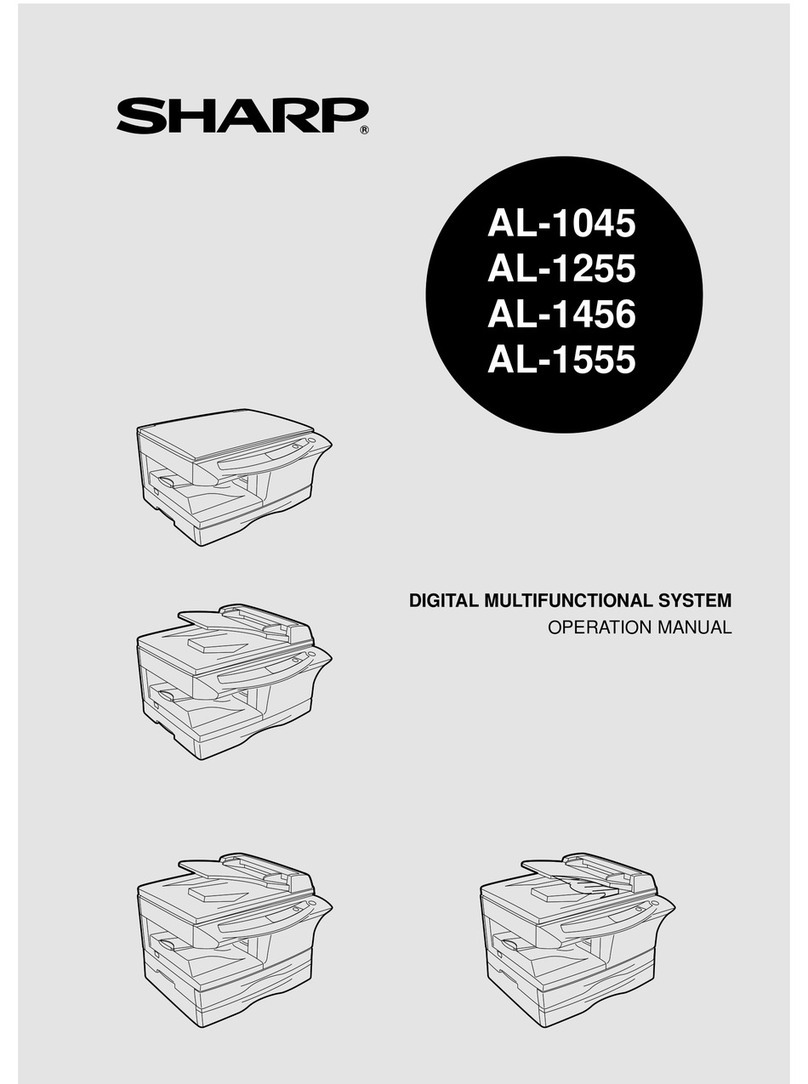
Sharp
Sharp AL-1045 User manual

Sharp
Sharp AR-M355N User manual

Sharp
Sharp FO-2081 User manual
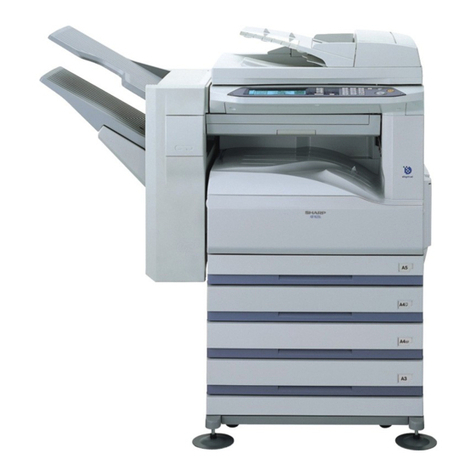
Sharp
Sharp AR-M237 IMAGERs User manual