Sharp UH-3 User manual

OPERATIONS MANUAL / PARTS LIST UH-3 MILL





1-3 Specifications
Table
Working surface length x width 51-3/16 x 11-13/16 in.
Travel longitudinal x cross x vertical 37-3/8 x 13 x 1/2 in.
T-slot nominal size x No. x pitch 5/8 in. x 13 x 2-3/4 in.
Feeds (12 steps)
Longitudinal x cross 50Hz 7/16-20-3/8 ipm.
Vertical 50Hz 3/16-10-3/8 ipm.
Rapid traverse Longitudinal x cross 50Hz 97-1/8 ipm.
Vertical 50Hz 49-7/8 ipm.
Swivel table (left & right) 45deg
Universal spindle head (optional)
Spindle nose
Spindle speed
Change of spindle speed
Distance from spindle end to table
Distance from center of spindle to column
Horizontal spindle
Spindle nose ISO R297 No.40
Spindle speed (12 steps) 50Hz 36-1415 RPM
Distance from center of spindle to over arm 5-5/16 in.
Distance from center of spindle to table
Motors
For horizontal spindle AC3.7kW-4P
For table feed and rapid traverse AC2.2kW-4P
For cutting fluid pump AC0.1kW-2P
Machine size
Overall height 67-5/16 in.
Floor area 26-3/8 x 47-1/4 in.
Net weight (approx.) 2350 kgs
Chung Sing 2-2
VERSION: 2



Chung Sing 3-2
VERSION: 2

2. Installation and preparation
2-1 Transportation of the machine
Make certain the load is on balance and that the sling does not touch the table or head before lifting.
If a crane is used in lifting, exercise care that none of the mechanism is damaged.
When lifting the machine, insert two round bars of about 35mm in diameter and use a wire
suspension rope, be certain that they are strong enough to safety carry the weight of the machine.
The finished surface of the machine must be protected by using wooden blocks and cloth.
Fig. 2
Chung Sing 4
VERSION: 2

2-2 Inspection and cleaning
After you received the machine, please check if the packing contents all the accessories you
ordered. Then wipe off dirt and protective coating.
2-3 Storage and Installation
The surrounding condition of storage is that
Temperature range: -25° to +75°
Relative humidity range: 30% to 95% (non-condensing)
Damage from shock and vibration should be avoided
Ingress of solid bodies and liquid should be avoided
Four leveling bolt should be adjustment the machine level.
When installing the machine must be adjustment four leveling bolt (Fig.3) for level.
2-4 Maintenance and inspection
(1) Precautions for operating
1) Always supply lubricating oil to designated oiling points before starting.
2) onfirm that the work and setting jigs do not strike anything before actuating table feed.
3) The power table longitudinal feed should not exceed the range limitations of the machine.
Always set the automatic reversing dog on both sides within the moving range.
Chung Sing 5
VERSION: 3

2-5 Cutting oil
There are two general types of cutting oil, i.e., water-soluble cutting oil and water insoluble
cutting oil and these are further divided into many groups. As selection of the cutting oil depends
on each cutting condition particular trade names or groups cannot be specified here but it is
necessary to observe the following;
(1) Use of water-insoluble cutting oil
Examples: Mineral oil Light oil machine oil and spindle oil
Animal and Lard olive oil colza oil soybean oil,
Vegetable oil castor oil
(2) apacity of the cutting oil tank is about 9.25 gallon.
(3) utting oil should be supplied through an oil strainer into the cutting oil intake provided on the
lower part of the column.
Warning: 1. To avoid fire, prohibited use low flash point cutting oil for machining magnesium,
aluminum or similar pyrophoric or explosive articles.
2. Do not dump waste cutting fluid at any place. Dispose the waste fluid under
regulation of local low for environmental
protection.
2-6 Wiring
The power cable should be connected to the terminals R.S.T.
(1) (Fig.4). On completion of the connection, turn on the
power switch provided on the cabinet.
After finishing the above preparations, start the main spindle.
(See section for spindle starting, spindle stopping).
If the rotation direction of the main spindle is clockwise,
connections are correct. If rotation is counter-clockwise,
exchange connections of two of the three wires of the power
cable.
2-7 Lubrication
Prior to starting, each moving part must be lubricated with suitable lubricating oil. Refer to table 1
for instructions to lubricate the spindle gears and sideways.
The lubrication oil to be used for each part is also listed in tables 2, and 3, it can be used for
selecting the correct lubricant to keep the machine in its best condition.
①
①
Fig. 4
Chung Sing 6
VERSION: 3

Chung Sing 7
VERSION: 3

Table - 2 The general lubricants for machine tool
SYMBOL CPC ESSO/EXXON SHELL MOBIL DAPHNE
GEARS
CB 32
CB 68
CB 150
R 32
R 68
R 150
Teresso 32
Teresso 68
Teresso 150
Tellus Oil C 32
Tellus Oil C 68
Tellus Oil C 150
DTE Oil Light
DTE Oil Heavy Medium
DTE Oil Extra Heavy
Mechanic Oil 32
Mechanic Oil 68
Mechanic Oil 150
CC 150
CC 320
CC 460
R 150
R 320
R 460
Spartan EP 150
Spartan EP 320
Spartan EP 460
Omala Oil 150
Omala Oil 320
Omala Oil 460
Gear 629
Gear 632
Gear 634
CE Compound 150S
CE Compound 320S
CE Compound 460S
BEARINGS
FC 2
FC 10
FC 22
R 12
R 22
Spinesso 10
Spinesso 22
High spin oil C2
Tellus Oil C 10
Tellus Oil C 22
Velocite Oil No. 3
Velocite Oil No. 6
Velocite Oil No. 10
Mechanic Oil 2
Mechanic Oil 10
Mechanic Oil 22
SLIDE WAYS
G 68
G 220
Slide way oil
Slide way oil
Febis K 68
Febis K 220
Tonna T 68
Tonna T 220
Vactra Oil No. 2
Vactra Oil No. 4
Multiway 68C
Multiway 220C
HYDRAULIC
SYSTEMS
HL 32
HL 68
HM 32
HM 68
HG 32
HG 68
R 32
R 68
32 AW
68 AW
─
─
Teresso 32
Teresso 68
Nuto HP 32
Nuto HP 68
Powerex DP 32
Powerex DP 68
Tellus Oil C 32
Tellus Oil C 68
Tellus Oil 32
Tellus Oil 68
Tonna Oil T 32
Tonna Oil T 68
DTE Oil Light
DTE Oil Heavy Medium
DTE 24
DTE 26
Vacuoline Oil 1405
Vacuoline Oil 1408
Hydraulic Fluid 32
Hydraulic Fluid 68
Super Hydraulic Fluid 32
Super Hydraulic Fluid 68
Multiway 32
Multiway 68
GREASE XM 1
XM 2
Gulfcrown Grease
E.P. No.1
Gulfcrown Grease
E.P. No.2
Listan 1
Listan 2
Alvania Grease 1
Alvania Grease 2
Mobilux EP 1
Mobilux 2
Cornex Grease No. 1
Cornex Grease No. 2
Chung Sing 8
VERSION: 2

Table - 3 Instruction for correct lubricant
Application Fields Properties Symbol and
Viscosity Grade
Kinematic Viscosity CST (130℉)
REMARKS
Mean. min. max.
GEARS
Enclosed moderately
loaded gear (spur gear,
bevel gear)
Refined mineral oils with good oxidation
stability.
CB 32
CB 68
CB 150
32
68
150
28.8
61.2
135
35.2
74.8
165
Pinion speeds(motor output)
2,000-5,000rpm(within 5HP)
1,000-2,000rpm(within 10HP)
-1,000rpm(within 20HP)
Enclosed heavily loaded
gears (worm and wheel)
Refined oils with good oxidation stability
and with improved load-carrying ability.
CC 150
CC 320
CC 460
150
320
460
135
288
414
165
352
506
Worm speeds
2,000- rpm
1,000-2,000rpm
-2,000rpm
BEARINGS Spindles bearings and
associated clutches
Refined mineral oils with superior
anticorrosion and anti-oxidation
performances.
FC 2
FC 10
FC 22
2.2
10
22
1.98
9.00
19.8
2.42
11.0
24.2
Shaft speeds (shaft dia.)
10,000- rpm( 1/8 in)
2,000-10,000rpm(1/8-5.7/8 in)
-2,000rpm(5.7/8 in)
SLIDE WAYS Slide ways
Refined mineral oils with improved
lubricity and tackiness performance
preventing stick-slip.
G 68
G 220
68
120
61.2
198
74.8
242
Slide way (surface pressure)
Horizontal (under57Ib/
)
Vertical (under57Ib/
)
HYDRAULIC
SYSTEMS
Hydraulic systems
Refined mineral oils with superior
anti-corrosion and anti-oxidation
performances.
HL 32
HL 68
32
68
28.8
61.2
35.2
74.8
Oil temperature (Rate pressure)
0-148℉ (under500Ib/
)
85-175℉ (under500Ib/
)
Refined mineral oils with superior
anti-corrosion, anti-oxidation and
anti-wear performances.
HM 32
HM 68
32
68
28.8
61.2
35.2
74.8
Oil temperature (Rate pressure)
0-148℉ (under2000Ib/
)
85-175℉ (under2000Ib/
)
Hydraulic and Slide ways
Refined mineral oils of HM type with
anti-stick-slip properties.
HG 32
HG 68
32
68
28.8
61.2
32.2
74.8
Oil temperature (Rate pressure)
0-148℉ (under1000Ib/
)
85-175℉ (under1000Ib/
)
GREASE
Premium, quality greases with superior
anti-oxidation and anti-corrosion
properties.
XM 1
XM 2
Viscosity (102℉) SSU
Centralized systems
Cup or hand gun
310-340
265-295
Chung Sing 9
VERSION: 2


3-2 Electric operation panel (Fig. 6)
1. Horizontal spindle start button
2. Horizontal spindle stop button
3. Table feed motor start button
4. Table feed motor stop button
5. Emergency stop button
6. Cutting oil pump switch
Fig. 6
3-3 Start and stop for horizontal spindle
Push the horizontal spindle start button (1) (Fig. 6) to run the spindle.
Push the horizontal spindle stop button (2) (Fig. 6) to stop the spindle.
3-4 Start coolant system
The machine is provided a coolant system. Turning the coolant oil pump switch (6) (Fig. 6) to
the right and the cutting oil can be provided.
3-5 Emergency stop
This button (5) (Fig. 6) is pushed to put a stop in case of emergency. If this button is pushed, all
the movements of the mill are stopped immediately. It is released when push this button again.
Chung Sing 11
VERSION: 2

3-6 Change of horizontal spindle speed
Move lever (1)(Fig.7) to position . or depending upon the spindle speed
range required,and move lever (2)(Fig.7) to the position of the particular speed reuqired.Speed
changes must not be made while the main motor is running. To facilitate changing spindle
speed,stop main motor by depressing horizontal spindle stop button (2)(Fig.6). Turn spindle
rotated direction switch (3)(Fig.7) to position 1 or 2 and then intermittently press the inching
button (4)(Fig.7), at the same time moving lever (2)(Fig.7) until the required gears are engaged.
It should be noted that the feed motor will automatically stop when the inching button is
operated.
Fig. 7
3-7 Table feed
3-7-1 Operation of manual feed
Operate longitudinal feed by hand wheel (1) (Fig.5), cross feed by habd wheel (2) (Fig. 5),
and vertical feed by hand lever (3) (Fig. 5).
If directional changing lever (4) (Fig. 5) at central frontof saddle is in neutral position,
longitudinal manual feed can not be operated.
Chart of rotation of manual feed hand wheel and moving direction of working table.
Hand wheel
Table
Rotation direction
(clockwise)
Displacement
One division
Scale collar
One revolution
Longitudinal Feed Right hand 0.02 mm
(0.001 inch) 5mm
(0.2 inch)
Cross feed Forward(go far from
operator)
0.02mm
(0.001 inch)
Vertical feed Upward 0.01mm
(0.0005 inch)
1.2mm
(0.05 inch)
1
2
3
4
Chung Sing 12
VERSION: 2

3-7-2 Operation of cross power feed
Start feed motor by turning button (3) (Fig. 6) and then lever (5) (Fig.5) upwards for the
saddle to feed towards the column, and for the saddle to feed away from the column move
lever (5) (Fig.5) downwards.
3-7-3 Operation of vertical power feed
Start feed motor by turning button (3) (Fig. 6) and then move lever (6) (Fig. 5) upward to
feed the knee upwards to move lever (5) (Fig. 5) downward, to feed the knee downward.
3-7-4 Operation of longitudinal power feed
Start feed motor by turning button (3) (Fig.6) and then move lever (6) (Fig.5) and then
move lever (4) (Fig.5) right for the table to feed from the left move the right and for the
table to feed from right to left mover lever (4) (Fig. 5) to left.
3-7-5 Choice of feed speed
Feeding speed is dependent on the spindle speed, material of work piece, tips if cutter and
diameter of cutter (Table 6). With this machine, 12 steps of cutting feed and rapid feed are
carried out from the feed box which is under the side of saddle.
Turning the switch (3) (Fig. 6) to “ON” position to start the table longitudinal feed motor.
Move lever (10) (Fig. 5) to position A, B or C dependent upon feed range required and
move lever (9) (Fig. 5) to the position for the particular feed rate required. It is not
necessary to stop the feed motor when changing the feed rate.
“WARNING”
1. Don’t change feeding speed if the table is moving.
2. Before stopping the spindle or when the table auto feed is not used push back the feed
engagement lever (4) (5) (6) (Fig. 5) to neutral.
3-7-6 Operation of rapid traverse
This can be operated on any of the foregoing movements by having the fees motor running
which is independent of the main spindle motor and moving the lever whichever direction
engages the feed required into the correct position and then moving lever (11) (Fig. 5)
upwards until the appropriate distance has been moved. Then lever (11) (Fig. 5) should be
returned to its neutral position.
Chung Sing 13
VERSION: 2

3-7-7 Backlash eliminator
The use of the backlash eliminator device allows “climb milling” to be carried out on this
machine. The backlash eliminator controller (8) (Fig. 5) is situated on the front of the
saddle. When climb milling is to take place with the cutter revolving clockwise and the
table moving from right to left, the backlash eliminator control should be rotated counter –
clockwise.
To set the backlash eliminator turn the controller (8) (Fig. 5) in the appropriate direction
and at the same time rotate the table hand wheel. Continue turning the controller (8) (Fig. 5)
until resistance is felt at the table hand wheel.
Do not over tighten the backlash eliminator.
The table must not be put into rapid traverse when the backlash eliminator is engaged.
3-7-8 Operation of dog
The auto-stop longitudinal feed is worked by dogs which are located in the T-slot front of
table. The two fixed dogs (2) (3) (Fig. 8) on the outsides are safety stops which prevent
over travel. These should not be moved.
The two inside dogs (4) (5) (Fig. 8) can be set at any position so that the table stops
automatically in set range.
Fig. 8
Chung Sing 14
VERSION: 2
Table of contents
Other Sharp Power Tools manuals
Popular Power Tools manuals by other brands
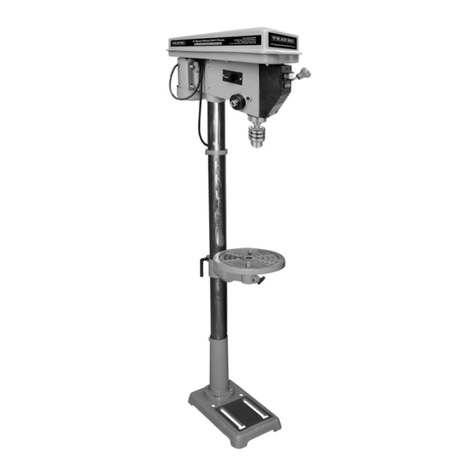
Buffalo Tools
Buffalo Tools Black Bull DP16UL Assembly & operating instructions
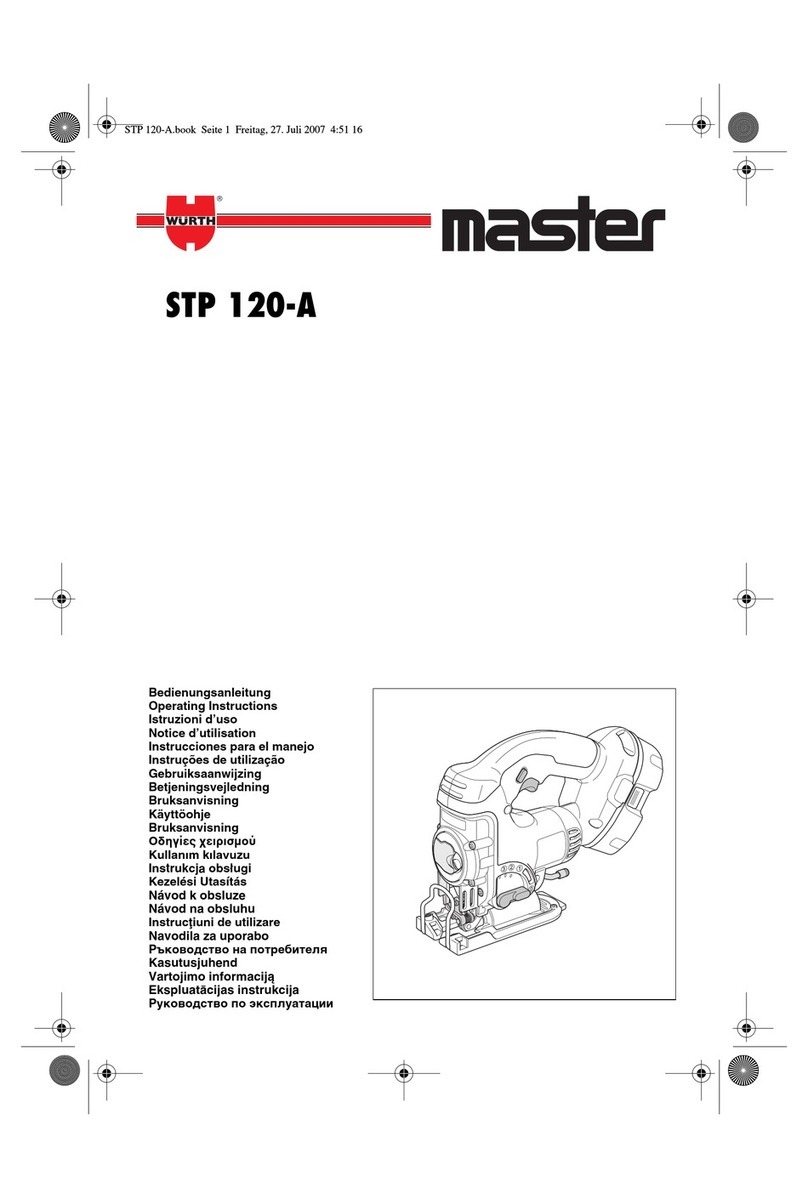
wurth
wurth STP 120-A operating instructions

EINHELL
EINHELL TE-MG 200 E Original operating instructions
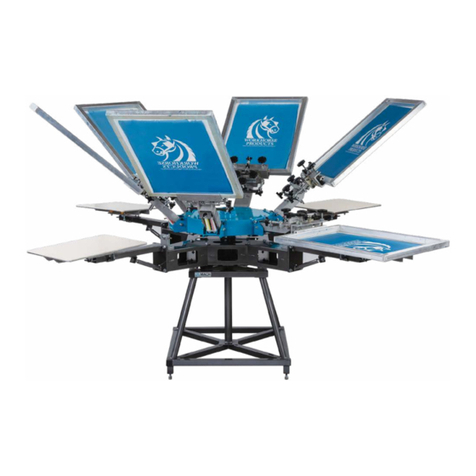
Workhorse Products
Workhorse Products MACH Series owner's manual
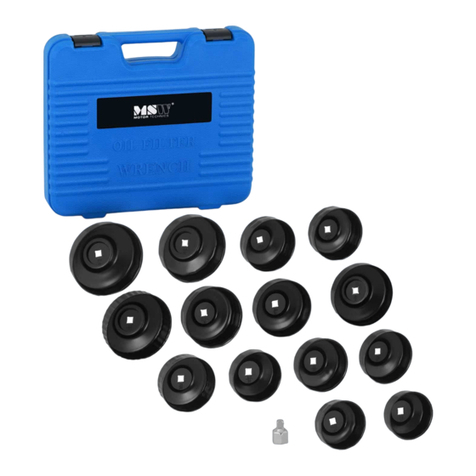
MSW
MSW MSW-OFC-11 user manual
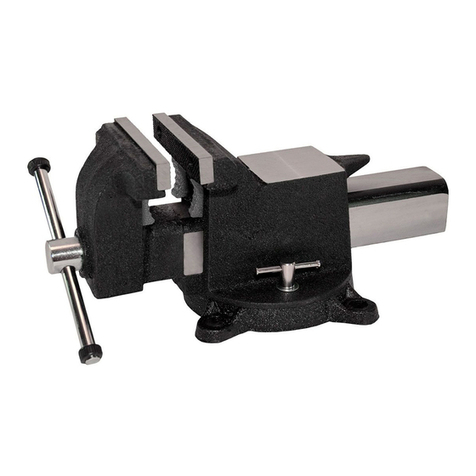
Yost Vise
Yost Vise 905-AS manual