Shield LH-DCM-M User manual

Shield Fire, Safety and Security Ltd Page 1 of 14 Revision DCM01.01
Shield Digital Control Module Installation Manual
Shield Digital Control Module
(DCM)
Installation Manual

Shield Fire, Safety and Security Ltd Page 2 of 14 Revision DCM01.01
Shield Digital Control Module Installation Manual
Contents:
Important Guidelines – read before commencing installation Page 3
General Description Page 4
Specications Page 5
Leader Cable Page 6
Mounting Dimensions Page 6
Static Discharge Cautionary Page 6
Installation Page 7
Connections Diagram Page 7
Operating Modes Wiring Diagram Independent Page 7
Operating Modes Wiring Diagram Interlock Page 8
Commissioning Page 9 -11
Self Test Page 12
Two-wire RS-485 Modbus RTU/ASCII Communications Page 13
Resetting the Shield DCM Unit Page 14

Shield Fire, Safety and Security Ltd Page 3 of 14 Revision DCM01.01
Shield Digital Control Module Installation Manual
Important Guidelines
Please read this instruction leaet thoroughly before commencing installation.
Install the Digital Control Module (DCM) accordingly to meet local and country
installation requirements.
The DCM must be installed in accordance with NFPA 70 & 72, NEC 760 (National
Electric Code) and Authorities Having Jurisdiction.
Ensure the product is installed, commissioned and maintained by persons
according to good engineering practices and who have received sucient training
on the unit.
Only use Shield Digital Linear Heat Detection (LHD) cable.
Test the LHD Cable before connecting it to the DCM using
a multimeter.
Ensure the end of line resistor (1kohm) is securely connected at the end each LHD
cable.
If only one zone is required leave the end of line resistor (1kohm) connected across
the terminals of the unused zone.
Ensure any cable glands used are tightened to form a secure and moisture proof
seal around the detection cable and any other cable in or out of the unit.
Do not exceed the maximum operating voltage of the DCM (36Vdc).
Do not connect lengths of LHD cable in ‘T’ connections or spurs.

Shield Fire, Safety and Security Ltd Page 4 of 14 Revision DCM01.01
Shield Digital Control Module Installation Manual
General Description
Digital Control Module
The Shield Digital Control Module (DCM) is a dual zone module for
monitoring up to two zones of Shield Digital LHD Cable. If an overheat or
re situation triggers either zone of the cable the unit automatically
calculates and displays the distance along the cable, in feet and metres,
to the alarm point. The two zones can operate independently of each
other, or in interlock mode and a separate alarm and normally conducting
fault output are provided for each zone. The unit is intended to be installed
between the Digital LHD cable and a conventional or addressable re
alarm control panel. It has power, fault and alarm lights, as well as volt
free outputs for fault and alarm, corresponding to each zone. It may also
be connected to a industrial process control system using the two wire
RS-485 Modbus RTU/ASCII output.
Figure 1: Typical Installation of the Shield Digital Control Module
Shield Digital
LHD Cable
Shield Digital
Control Module
Shield Digital
LHD Cable

Shield Fire, Safety and Security Ltd Page 5 of 14 Revision DCM01.01
Shield Digital Control Module Installation Manual
Specications
Part No: LH-DCM (-M sux M16 knockouts on bottom)
(-Pg sux PG16 knockout on bottom)
Description: Digital Control Module – LH-DCM – SHIELD
Revision: 1.0
Enclosure:
...Dimensions H180mm x W120mm x D60.5mm (H7.1in x W4.72in x D2.38in)
...Rating NEMA 4, 4X (IP65)
...Finish Light Gray with clear lid
...Display 2 line, 16 character backlit display showing zone status
Approvals: UL 864 10th ed.
Power Requirements: All circuits power limited if powered from a power limited supply
Min. Nominal Max.
...Operating Voltage (UL tested) 14Vdc — to — 36Vdc
...Operating Voltage 12Vdc — 24Vdc — 36Vdc
Current Consumption:
...Normal Operation (standby) <15mA <7mA <5mA
...Alarm <40mA <23mA <15mA
Operating Temperature Range: -20°C – +50°C (-4°F – +122°F)
Terminal Blocks:
...Spacing 5mm Rising Clamp
...Rating 16A
...Wire Size 0.08mm2(28AWG) to 4mm2(11AWG)
Supervised Circuits: Power, Input Zone 1 & Input Zone 2
Inputs: Up to two Class B zones of Shield Digital LHD Cable
...Max Zone Length 3000m (10,000ft)
...Min Zone Length 1m
...End of line resistor 1kohm (included)
...Short circuit current 0.5mA
...Max Voltage 5V
...Ground fault impedance 0ohms
Outputs:
...Communications Two wire RS-485 Modbus RTU/ASCII
...Sounder 2.4kHz 92dBa @ 10cm Buzzer
...Alarm 2x Form C volt-free relay contacts (resistive, common)
Max V 30Vac or 42.4Vdc
Max Current 2A
Max Switching Power 60W, 62.5VA
...Fault 2x Optoisolated phototransistor output (resistive, common)
Max V 35Vdc
Max Current 80mA
Max Power Dissipation 150mW

Shield Fire, Safety and Security Ltd Page 6 of 14 Revision DCM01.01
Shield Digital Control Module Installation Manual
Leader Cable
The Shield DCM can be connected via leader cable to the start of the
Digital LHD cable. During installation the voltage drop across the leader
cable is calibrated out to give an accurate distance reading when an
alarm is triggered (see page 9 for calibration procedure).
The maximum length of leader cable that can be used per zone is
dependent upon the cable diameter. The following is a guideline for
typical cable sizes and maximum length:
Cable Size Max Leader Cable Length
20AWG
(16x0.2mm or 0.8mm dia, copper) 1000m
22AWG
(7x0.25mm or 0.6mm dia, copper) 600m
24AWG
(7x0.2mm or 0.5mm dia, copper) 390m
Mounting Dimensions
Static Discharge Cautionary
The following items are cautionary notes that will help prevent
equipment damage or malfunction caused by static discharge:
CAUTION
Static charges produce voltages high enough to damage electronic
components. Follow these precautions when installing, servicing, or
operating the DCM:
• Work in a static-free area.
• Discharge any static electricity you may have accumulated.
• Discharge static electricity by touching a known, securely
grounded object.
• Do not handle the printed circuit board (PCB) without proper
protection against static discharge.
In the event that the DCM malfunctions after encountering a static
discharge correct operation of the unit can be restored by interrupting
power to unit for a brief period (approximately 10s). Setup information
can be veried by following the steps in the installation procedure
section. In the event of the setup information being corrupted the unit
should be reset following the Resetting the DCM procedure.
Figure 2: Mounting Dimensions for the Shield DCM

Shield Fire, Safety and Security Ltd Page 7 of 14 Revision DCM01.01
Shield Digital Control Module Installation Manual
Installation
The DCM allows accurate location of an alarm point along a length of
Shield Digital LHD cable. It continuously monitors up to two zones of
cable for a fault (open circuit) or an alarm (overheat or re condition).
Because of the wide range of applications that Digital LHD cable can
be used for, it may not always be possible, or be too time consuming,
to locate where along the cable an alarm has occurred. Using the
DCM, when an alarm occurs the distance to the overheat condition is
immediately calculated and displayed on the integrated display.
If a fault is detected, the corresponding fault output stops conducting,
triggering a fault at the re alarm control panel. If an alarm is detected, the
corresponding alarm output changes state, triggering an alarm at the re
alarm panel. The fault outputs also stop conducting on power loss to the
unit or microprocessor fault, triggering a fault at the re alarm control panel.
The two wire RS-485 Modbus RTU/ASCII output also outputs the
current state of both zones. See the section “Modbus RTU/ASCII
Communications” for more detail.
There are two primary congurations of the DCM (see gure 1):
1) The Digital LHD cable can be connected directly to the DCM
2) The Digital LHD cable is connected to a length of leader cable
which is connected to the DCM. In this scenario the leader cable
must be “calibrated out” during commissioning of the DCM.
Connections Diagram
Figure 3 shows the connections diagram for the DCM. The unit is
provided with a 1kohm end of line resistor in each zone input. If only one
zone is required, leave the 1kohm resistor connected across the zone
which is not in use. Otherwise the 1kohm resistor should be connected at
the end of the Digital LHD cable.
Figure 3: Wiring Diagram for the Shield DCM
Operating Modes Wiring Diagram Independent
There are two operating modes for the Digital Control Module:
1. Independent – This is when the DCM is used as a two zone system. When a fault or overheat condition occurs on an LHD zone, the corresponding fault
or alarm output respectively is triggered. The two zones operate independently and both sets of outputs should be connected to a re alarm control panel.
If the zone is not required leave the 1kohm resistor in the zone input terminals as supplied. In this mode, the two zones can either contain identical rated
temperature LHD cables or two dierent rated temperature LHD cables, e.g. a 68 deg C in zone 1 and a 105 deg C in zone 2.

Shield Fire, Safety and Security Ltd Page 8 of 14 Revision DCM01.01
Shield Digital Control Module Installation Manual
Operating Modes Wiring Diagram Interlock
2. Interlock – this mode is for applications which require a fail-safe guarantee that an alarm is only triggered when an overheat condition has been detected.
This mode may also be known as coincidence detection. In this case, the same rated temperature Digital LHD cable should be attached to both zones of the
DCM. The alarm output is only activated when both LHD cables trigger an alarm due to an overheat condition. If one LHD cable zone input registers an alarm
but the second does not, the alarm output will not be activated. This is to prevent an alarm if a mechanical or other issue has triggered one LHD cable and not
an overheat condition.
• Only use Zone 1 fault and alarm outputs in Interlock mode.
• Two linear heat detectors with the same temperature rating must be used and a minimum of
two linear heat detectors must be installed in each protected space.
• The spacing between detectors should be less than 0.7 times the rated linear spacing, in
accordance with National Fire Alarm Code, NFPA 72.
See the Shield Digital LHD Installation Instructions for the linear spacing specication.

Shield Fire, Safety and Security Ltd Page 9 of 14 Revision DCM01.01
Shield Digital Control Module Installation Manual
1. After wiring the unit up (see wiring diagram) power up the device.
Device will show screen including software revision number.
2. If the unit is being setup for the rst time the following options will
be shown. If the unit has previously been installed the display will
automatically cycle through the options, showing the stored settings.
3. After the initial title screen the next screen will show a menu (see
right) with three options: Load Congs, New Congs and Self Test. On a
previously congured device, after 10s of no button press the device will
automatically proceed to loading saved congs.
4. If “Load Congs” is selected or no button has been pressed after 10s
on a previously congured device, the screen will show “Loading Saved
Congs”. The previously saved parameters will then be displayed.
5. Select the operating mode. (see “Operating modes” (pages 7-8)
for more detail.
Independent: the two zones operate independently of each
other (default).
Interlock: Both fault outputs activate when a fault occurs on either zone
1 or zone 2. Both alarm outputs activate only when both LHD zones
trigger an alarm.
6. Select the cable type connected to Zone 1 (68°C/88°C/105°C/185°C)
7. Select the cable type connected to Zone 2 (68°C/88°C/105°C/185°C)
8. If leader cable is connected between the LHD cable and the DCM for
this zone, press the Select button and select Yes. Press the Set button to
continue.
9. The controller will then ask if the zone is ready to be calibrated.
The leader cable must be connected to the DCM and shorted out at the
end where it connects to the START of the LHD cable. Once this is done
press the Set button.
10. The DCM will display the voltage drop across the leader cable.
Remove the short from the leader cable and connect it to the START
of the LHD cable as normal.
11. If the LHD cable is connected directly to the DCM then select No and
press the Set button to continue.
Commissioning
Shield Dual
Zone DCM R1234
MAIN MENU
LOAD CONFIGS
LOADING SAVED
C O N F I G S...
Z1 Cable Type:
68C
Operating Mode:
INDEPENDENT
Z2 Cable Type:
68C
Zone 1 ldr cable
Yes
R ea dy to
ca lib rate?
Zone 2 cal:
109 mV
ZONE 2 ldr cable
no

Shield Fire, Safety and Security Ltd Page 10 of 14 Revision DCM01.01
Shield Digital Control Module Installation Manual
Commissioning (Cont.)
12. Select whether you would like the alarm outputs for both zones to
be latching. If set to Yes, then if an alarm is triggered the unit will either
require the power supply to be interrupted (min. 2s) or the Set button
to be pressed to reset to normal once the alarm conditioned has
been cleared.
13. Select whether the Modbus output should be enabled. If this is not
enabled then proceed to step 17.
14. Select required Modbus type, either RTU or ASCII.
15. Set the Modbus address for this device (1-247).
16. Cycle through the possible Baud Rates for the Modbus RTU/ASCII
output. (2400, 4800, 9600, 19200, 38400, 57600, 115200).
17. Select the number of data bits for the Modbus RTU/ASCII output.
(7 or 8)
18. Select the number of stop bits for the Modbus RTU/ASCII output.
(1 or 2).
19. Select the parity for the Modbus RTU/ASCII output.
(even/odd/none).
20. Once the unit has been commissioned the display will show the zone
status. In normal operation the display will show OK for each Zone.
In Interlock mode the display will show
{Zone 1: OK
{Zone 2: OK
to indicate the zones are linked and an alarm is only transmitted if both
zones are triggered.
21. If an alarm condition occurs the DCM automatically calculates the
distance along the cable to the trigger point and rst displays this value
in metres.
Modbus TYPE
RTU
Modbus address
1
BAUD RATE
2400
DATA BITs
7
Stop BITs
1
PariTY
Even
Zone 1: OK
Zone 2: OK
Zone 1: 534 m
Zone 2: OK
Latching outputs
No
Modbus output on
yes

Shield Fire, Safety and Security Ltd Page 11 of 14 Revision DCM01.01
Shield Digital Control Module Installation Manual
Commissioning (Cont.)
22. The display alternates showing the distance along the cable to the
trigger point in metres and in feet.
23. The unit monitors for relay faults. If an alarm condition occurs but the
relay does not switch state (due to a coil failure for example) the device
will go into relay fault and show the screen to the right, depending upon
which zone is in fault
24. The unit monitors for interference faults when the input may be
changing between alarm, ok and fault conditions, for example, too rapidly.
In this case an I/F fault is displayed on the corresponding zone. Check all
cable teminations are securely fastened and for other sources of noise.
25. The unit monitors for cable faults (open circuit) and ground faults
(where one conductor of LHD cable may be touching bare metal at some
point). An open circuit will be displayed as fault (as per zone 1 shown
right). A ground fault will be shown as ‘gnd t” (as per 2 shown right).
Zone 1: RLY FLT
Zone 2: OK
Zone 1: OK
Zone 2: I/F FAULT
Zone 1: FAULT
Zone 2: GND FAULT
Zone 1: 1751 ft
Zone 2: OK

Shield Fire, Safety and Security Ltd Page 12 of 14 Revision DCM01.01
Shield Digital Control Module Installation Manual
Self Test
1. If self test mode is selected the device will rst load the saved congs
then proceed to cycle through normal operation, alarm and fault.
This is to allow the installer/maintenance engineer verify that the unit
is corrected to an external system correctly. The screen will ash “SELF
TEST/MODE” every few seconds.
2. In self test mode the device cycles between normal operation, alarm
and fault every approx. 8 seconds. In normal operation the display will
show ok. The alarm relays will be o and the fault output normally
conducting (on).
3. In self test mode and alarm condition the display will show alarm.
The alarm relays will be on. After approx. 8 seconds the unit will go into
fault condition.
4. In self test mode and fault condition the display will show fault.
The fault outputs will stop conducting (o). After approx. 8 seconds the
unit will return to normal condition. To exit self test mode, press and hold
both SET and SELECT buttons for 10s or more until the device resets.
Zone 1: OK
Zone 2: OK
Zone 1: ALM
Zone 2: ALM
Zone 1: FAULT
Zone 2: FAULT
SELF TEST
MODE

Shield Fire, Safety and Security Ltd Page 13 of 14 Revision DCM01.01
Shield Digital Control Module Installation Manual
Two-wire RS-485 Modbus RTU/ASCII Communications
The Shield DCM includes a two wire RS-485 Modbus output which can be enabled to output the
status of each zone of Digital LHD Cable. The DCM Modbus output supports the Modbus RTU/
ASCII protocol and the following functions:
• Function code 4 (Read Input Registers)
The request for reading the input registers should be constructed in the following manner:
• Address of rst register to be read (16-bit)
• Number of registers to read (16-bit)
The DCM will respond in the following manner:
• Number of bytes of register values to be read (8-bit)
• Register values (16-bits per register)
The DCM stores the information for each zone of the cable in the following format:
Register Description Possible Values
0 Zone 1 status -1 or 65535=fault on zone
0=zone ok
1-32767=distance in metres to trigger point
1 Zone 2 status -1 or 65535=fault on zone
0=zone ok
1-32767=distance in metres to trigger point
2 Zone 1 cable type 1=68°C, 3=88°C, 4=105°C, 5=185°C
3 Zone 2 cable type 1=68°C, 3=88°C, 4=105°C, 5=185°C
If the start address plus the requested number of registers exceed 4, the DCM will return an
ILLEGAL DATA ADDRESS error.
If the request contains a function code other than those supported the DCM will return an
ILLEGAL FUNCTION error.

Shield Fire, Safety and Security Ltd Page 14 of 14 Revision DCM01.01
Shield Digital Control Module Installation Manual
Resetting the Shield DCM Unit
WARNING: This procedure will erase ALL stored settings and reset the Shield DCM unit back to
its factory default state. The cable types, leader cable calibration, latching output selection
and Modbus setup will all require selecting after this procedure.
To reset the Shield DCM unit back to the factory state, when the unit is powered up and in normal operation
(see step 15 in the Commissioning procedure), press and hold the SET and SELECT buttons for a minimum of
10 seconds continuously. While the SET and SELECT buttons are held down the power LED will ash quickly
to conrm this procedure is about to take place. After approximately 10 seconds, the unit will restart and
return to step 1 in the Commissioning procedure. The settings are only erased if the menu option “New
Congs” is selected.
This manual suits for next models
1
Table of contents
Popular Control System manuals by other brands
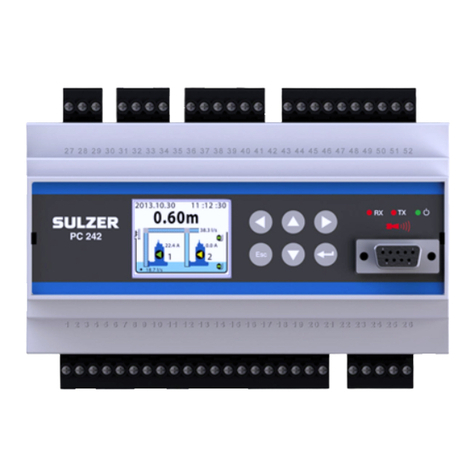
Sulzer
Sulzer ABS PC 242 user guide
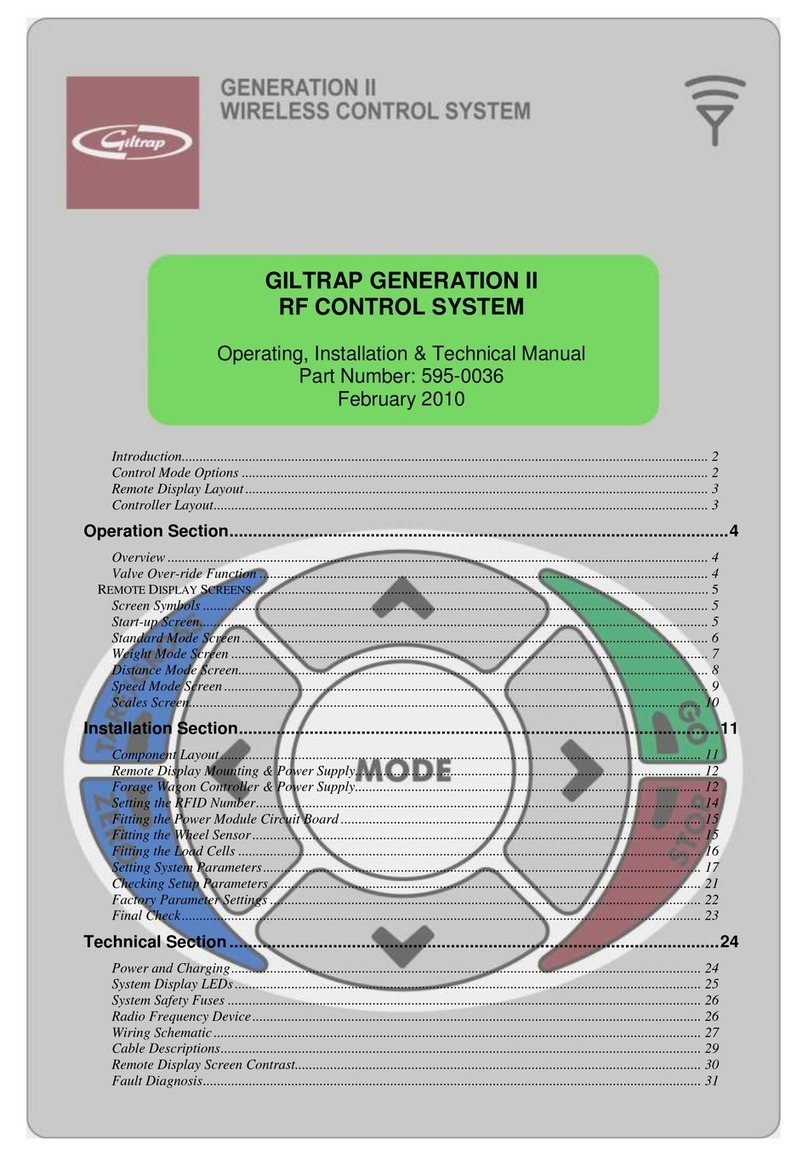
Giltrap
Giltrap Generation II RF Instructions, Operating, Installation
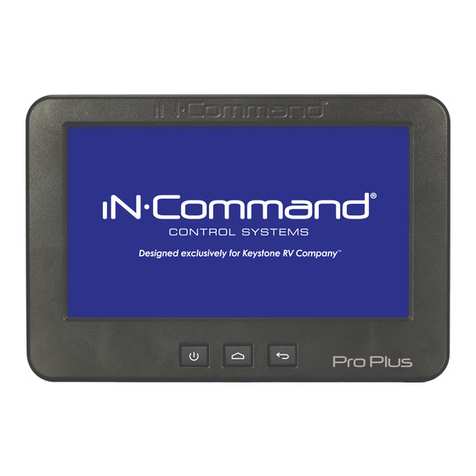
ASA Electronics
ASA Electronics iN-Command Pro Plus JRVCS2 Getting started
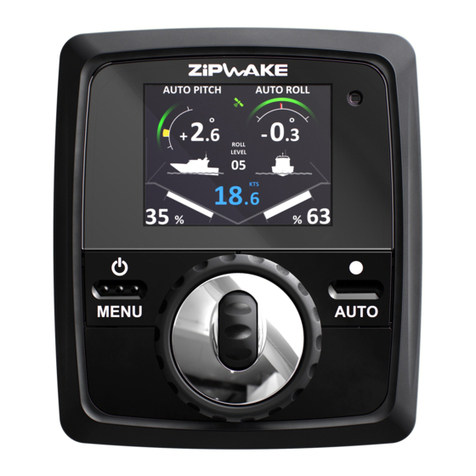
zipwake
zipwake E Series installation guide
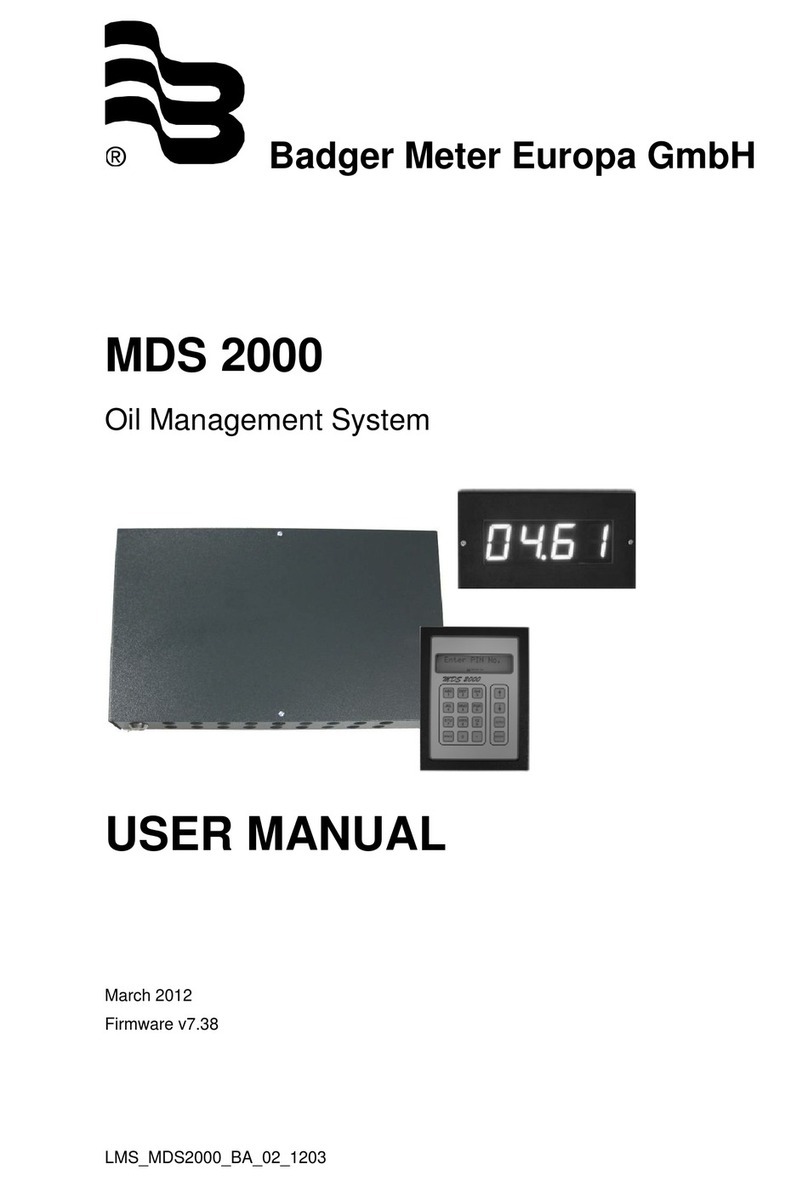
Badger Meter
Badger Meter MDS 2000 user manual
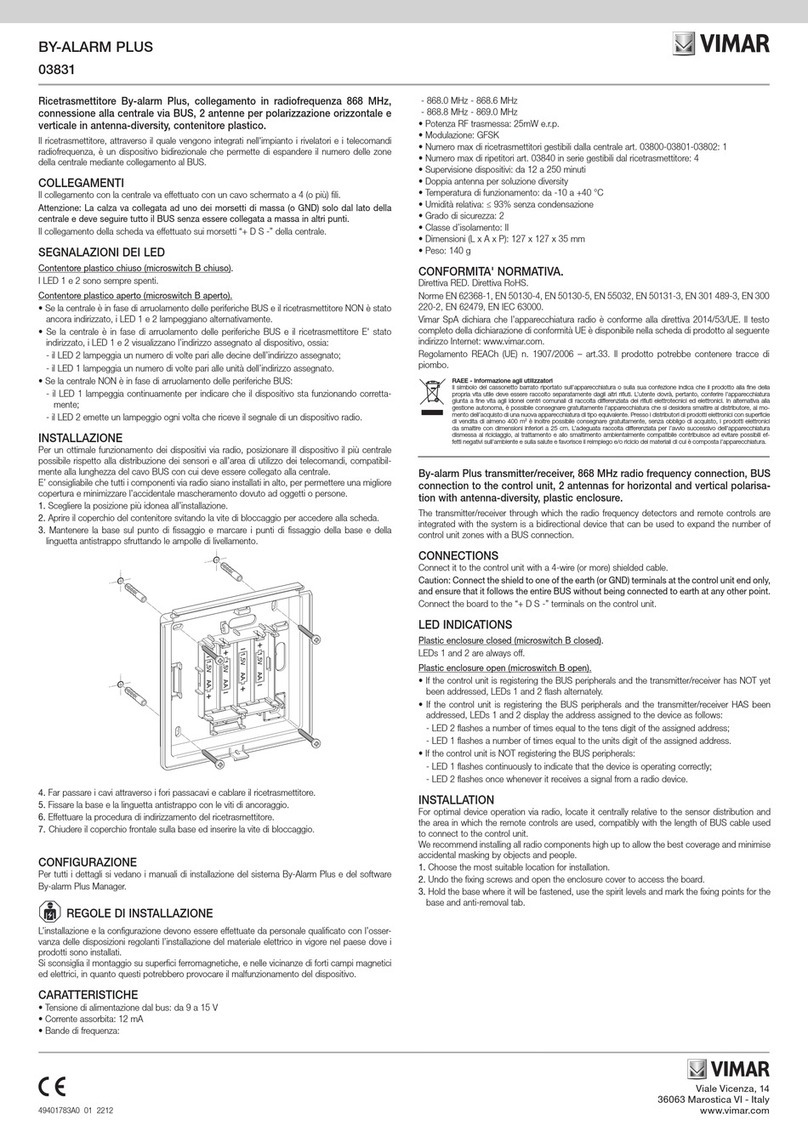
Vimar
Vimar BY-ALARM PLUS Installation