Nibe ClimaCool CoolLogic Touch Instruction manual

CoolLogic Touch
Installation, Operation & Maintenance Manual

Introduction .........................................1
Communications Wiring ............................. 2-3
CoolLogic Touch Control System ........ 4-7
Standard Alarm Functions .............................8
Standard Features ................................. 9-10
Start Up and Warranty Form ........................11-13
CoolLogic Touch Screen Menu Hierarchy ..............14-17
Status User Access...............................15
Setup User Access ...............................16
Service User Access ..............................17
Table of Contents
CoolLogic Touch Control System Network Setup .........18
.................19
........20
.............21
Wiring Diagrams.................................. 22-25
.................................26

1
www.climacoolcorp.com
General Description
The CoolLogic Touch Control System provides leaving
chilled and hot water liquid temperature control algorithms
which maintain precise temperature control for cooling,
heating, heat recovery and simultaneous heating and
cooling applications. A compressor run time equalization
sequence is given to ensure even distribution of compressor
run time throughout the entire chiller bank. Chiller power
surface.
The ClimaCool®
CoolLogic Touch
Control System to incorporate one or more modules.
The controls are divided into two separate sections - the
CoolLogic Touch
The CoolLogic Touch
events, timing and compressor staging, providing operator
interface for all levels of setting and retrieving data.
The module controller resides at each module location
module’s compressor and water temperature operations.
Safety
Throughout this manual warning, danger, caution and
attempting any installation, service or troubleshooting
of the equipment. All labels on unit access panels must
be observed.
DANGER
avoided, will result in death or serious injury.
WARNING
avoided, could result in death or serious injury.
CAUTION
practice which, if not avoided, could result in minor or
moderate injury or product or property damage.
Introduction
WARNING/ADVERTISSEMENT
To avoid possible injury or death
due to electrical shock, open the
power supply disconnect switch and
secure it in an open position during
installation.
Pour éviter les blessures ou la mort
par électrocution, ouvrir la interrupteur
de sécurité et xez-le en position
ouverte lors de l’installation.
WARNING/ADVERTISSEMENT
Disconnect power supply(ies)
before servicing. Refer servicing
to qualied service personnel.
Electric shock hazard. May
result in injury or death!
Debrancher avant d’entreprendre
le dépannage de l’appareil.
Consulter un réparateur qualie
pour le dépannage. Risque de
choc électrique. Résiltat de mai
dans dommages ou la mort!
CAUTION/ATTENTION
Unit to be serviced by qualied
personnel only. Refrigerant
system under pressure. Relieve
pressure before using torch.
Recover refrigerant and store or
dispose of properly.
Conifer la maintenance à un
technicien qualie. Le systéme
frigorique sous pression.
Décomprimer avant d’exposer
à la amme. Récuperer le
frigorigene et le stocker ou le
détrulre correctement.
CAUTION/ATTENTION
Use only copper conductors for eld
installed wiring. Unit terminals are
not designed to accept other types of
conductors.
Utilisez uniquement des conducteurs en
cuivre pour le câblage. Bornes de l’unité
ne sont pas conçus pour accepter
d’autres types de conducteurs.
WARNING/ADVERTISSEMENT
For eld installation of Port 1
communication wiring, installer must
use:
• ARC-156 communication wire
• single-twisted pair
• shielded with drain
• low capacitance (12.5 pF/ft)
• 22AWG
This conductor must be daisy chained
from the CoolLogic Controller to each
chiller module.
Maximum separation of low voltage
communication and high voltage
power wiring is required.
The communication cable must be
installed in its own conduit. Routing
must enter and exit the low voltage
section of the control box where the
controller is located and should not
be ran parallel to, or any closer than,
6 inches from any high voltage AC or
DC wiring either inside or outside of
the machinery compartment.
(See IOM or contact ClimaCool for
complete specication.)
Pour l’installation sur place du
câblage de communication du port 1,
l’installateur doit utiliser:
• le câble de communication ARC-156
• Paire à simple torsion
• blindée avec drain
• faible capacité (12.5 pF/ft)
• 22AWG
Ce conducteur doit être connecté en
guirlande du contrôleur CoolLogic à
chaque module de refroidissement.
Le l doit être installé dans son propre
conduit. L’acheminement doit entrer
et sortir de la section basse tension
du boîtier de commande où se trouve
le contrôleur et ne peut pas circuler
à moins de 6 à 8 pouces de tout
câblage de tension CA à l’intérieur
ou à l’extérieur du compartiment des
machines.
(Voir l’IOM ou contacter ClimaCool
pour les spécifications complètes.)

2
www.climacoolcorp.com
CoolLogic Touch Control System Wiring
A separate 115 volt power supply is required to power the
CoolLogic Touch
CoolLogic Touch
a simple two-conductor 22 AWG shielded cable with drain
rated at 60°C minimum, daisy chain connection. Control
wiring cannot be installed in the same conduit as line
voltage wiring or with wires that switch highly inductive
loads such as contactor and relay coils. All wiring shall be in
compliance with all local and national codes.
Field Connections between CoolLogic Touch
Control Panel and Module Controller
•
with drain (under 50 feet) See page 3.
• Over 50 feet, contact factory
NOTE: Use the same polarity throughout the network segment.
Field Connections to the CoolLogic Touch
Control Panel
Field integration with CoolLogic Touch
•
•
•
• Chilled water inlet and outlet temperature sensors
and wells
• Heating water inlet and outlet temperature
sensors and wells
• Source water inlet and outlet temperature sensors
and wells if applicable
• Alarm output closes when any active latching alarm
condition occurs (parameter or compressor fault)
• Chiller status output is closed whenever there is a call for
inputs deliver a closure signal indicating a present
normal condition to allow for chiller operation
Figure 1: CoolLogic Touch Control Panel
Field Connections to the Modules
The
CoolLogic Touch
technology. It is well suited for real-time control applications
in both the industrial and commercial marketplaces. Field
connections are made at port S1 at the CoolLogic Touch
Module Controller
module’s operation, such as evaporator and condenser
leaving temperatures, both compressor’s winding
temperatures, suction and discharge* temperatures
and pressures.
* Discharge temperature sensing not available with SHC
(Simultaneous Heating and Cooling) CoolLogic Touch
Control Systems.
Figure 2: Module Control Panel
Communications Wiring

3
www.climacoolcorp.com
Avoiding Noise
Avoid running communication wires or sensor input wires
Spark igniters
Radio transmiers
Variable speed drives
Electric motors (> 1hp)
Generators
Relays
Transformers
Other electronic modules
Inducon heaters
Video display devices
Lamp dimmers
Fluorescent lights
Parallel runs with power lines
Large contactors,
(i.e., motor starters)
ARC156 Wiring Specications
provide two acceptable alternatives. Halar®has a higher
temperature rating and a tougher outer jacket than
SmokeGard®, and it is appropriate for use in applications
where there are concerns about abrasion. Halar is also less
NOTE:
ARC156 specications
Description Single twisted pair, low capacitance (12pF), CL2P, 22 AWG (7x30), TC foam FEP, plenum rated cable
Conductor 22 AWG (7x30) stranded copper (tin plated)
0.030 in. (0.762 mm) O.D.
NOTE: 24 AWG can be used for segments <200 ft. (6.7 m).
Insulation Foamed FEP
0.015 in. (0.381 mm) wall
0.060 in. (1.524 mm) O.D.
Color code Black/white
Twist lay 2 in. (50.8 mm) lay on pair
6 twists/foot (20 twists/meter) nominal
Shielding Aluminum/Mylar shield with 24 AWG (7x32) TC drain wire
Jacket SmokeGard® (SmokeGard PVC)
0.021 in. (0.5334 mm) wall
0.175 in. (4.445 mm) O.D.
Halar®(ECTFE)
0.010 in. (0.254 mm) wall
0.144 in. (3.6576 mm) O.D.
DC resistance 15.2 Ohms/1000 feet (50 Ohms/km) nominal
Capacitance 12.5 pF/ft (41 pF/meter) nominal conductor to conductor
Characteristic impedance 100 Ohms nominal
Weight 12 lbs./1000 feet (17.9 kg/km)
UL temperature rating SmokeGard®
167°F (75°C)
Halar®
-40 to 302°F (-40 to 150°C)
Voltage 300 Vac, power limited
Listing UL: NEC CL2P, or better
Communications Wiring

4
www.climacoolcorp.com
Conguration – CoolLogic Touch Control System
Conguring the CoolLogic Touch Controller
1. CoolLogic Touch Controller’s power
2. Using the rotary switches, set the CoolLogic Touch
Controller’s address. Set the Tens (10’s) switch to the
tens digit of the address, and the Ones (1’s) switch to
the ones digit.
If the CoolLogic Touch Controller’s address is 01, point
the arrow on the Tens (10’s) switch to 0, and the arrow
on the Ones (1’s) switch to 1.
Figure 3: Rotary Switches
0
1
2
3
4
5
6
7
8
9
100’s
0
1
2
3
4
5
6
7
8
9
10’s
0
1
2
3
4
5
6
7
8
9
1’s
3.
(GND). The module controller references GND, and the
CoolLogic Touch Controller references SHIELD
(see Figure 4).
Figure 4
4.
5. Turn on the CoolLogic Touch Controller’s power.
6. Default for the CoolLogic Touch Board address will be
516800. Any variance from this device number cannot be
CoolLogic Touch Control System
Operator Interface
The CoolLogic Touch
operator interface touch screen (Figure 5) which includes a
easy to navigate using logically grouped menus. This enables
the user to access important information concerning set
points, active temperatures, pressures, operating modes,
alarm conditions, chiller scheduling, servicing, diagnostics
and more.
Figure 5: EQT2
If the touchscreen is left idle for 10 minutes, the default
screen appears (Figure 6).
Figure 6: Default Screen

5
www.climacoolcorp.com
Conguration – CoolLogic Touch Control System
Starting the Chiller
CoolLogic Touch Control
will show the home screen (Figure 7). Once power has
been applied to the CoolLogic Touch
display screens are accessible by several methods. From the
menu listings for the following categories by pressing one of
Figure 7: Home Screen
after a ten minute timeout, the display will change to the
default screen (see Figure 6).
Status Menu
Items in the status menu can be used to view operational
Figure 8: Status Menu
Setup Menu
Chiller system operation is determined by the values assigned
to the system variables, as predominantly found in the Setup
• General System Settings
•
•
These variables are initially assigned a default value. For most
applications, these values will provide optimum results.
Figure 9: Setup Menu
Service Menu
Items in the service menu can be used for diagnostic and
calibration of various items (Figure 10).
Figure 10: Service Menu

6
www.climacoolcorp.com
Conguration – CoolLogic Touch Control System
Alarm Menu
Up to 100 of the most recent occurrences stored with date
and time. Access to this log is available through the keypad.
Figure 12: Alarm Menu
LOCAL/OFF/REMOTE SWITCH
LOCAL MODE
Set to ON.
And if the chiller is a 4-pipe system,
Cool Mode BAS set to ON
Or, Heat Mode BAS set to ON (if available)
Or, if the chiller is an SHC 6-pipe system, one, two or all three
modes above, (if available) can be enabled for automatic
mode control.
REMOTE MODE
With jumper installed at terminals 40 and 39 of LVTB2 and
Mode set to Digital IN.
Mode set to BAS and the BAS is sending an ON command.
To use a remote relay (enable), insert the relay in place of
To Power Down Chiller Bank
1. Locate CoolLogic Touch
be disabled.
2. Locate the bank of modules connected to this CoolLogic
Touch
3. Go to the CoolLogic Touch
If complete shut-down of main power to all equipment is
desired, the additional steps can be taken (see Controller
Memory section).
1. Inside the CoolLogic Touch
the OFF position.
2. Locate the main power disconnect or breaker panel that
place the line powered switch to the OFF position.
3.
NOTE: Do not leave the CoolLogic Touch controller or the
of time as the battery power of the controller will be
drained and program can be corrupted.
To Power Up Chiller Bank
disconnect switch.
2. Turn the main power disconnect(s) to the ON position.
the chiller modules.
4. Open the CoolLogic Touch
5. Close the CoolLogic Touch
NOTE: When re-applying power, the CoolLogic Touch
must be the last device turned on after the modules are
energized to properly restore communication.

7
www.climacoolcorp.com
Conguration – CoolLogic Touch Control System
Recommended for Extended Bank Shutdown
1.
using the BAS System or hard wire connection.
2. CoolLogic Touch
3. Leave main power ON to the CoolLogic Touch Controller.
If this procedure is not followed for scheduled shutdowns,
Controller Memory
User data is archived to non-volatile Flash memory when
parameters are changed, every 90 seconds, and when the
NOTE:When you change a parameter, you must wait 30
change to be saved.

8
www.climacoolcorp.com
Standard Alarm Functions
High Pressure Cutout
This requires resetting both the module’s manual reset high
pressure control switch and the CoolLogic Touch Control
Low Pressure Cutout
This requires resetting the CoolLogic Touch
Compressor Thermal Protector Fault
This would occur if the motor protector sensed an overload
trip in the compressor motor. The compressor thermal
protector monitors a series of thermistor temperatures
in the motor windings as an indication of overload. This
requires resetting the CoolLogic Touch
Low Suction Temperature
During operation, should this temperature drop to 32° F,
the compressor will shut down. This requires resetting the
CoolLogic Touch
High Discharge Temperature
During operation, should this temperature rise above
225°F, the compressor will shut down. This requires
resetting the CoolLogic Touch
temperature has cooled to below 175° F. Tap on the
Low Leaving Chilled Water Temperature -
Below 38° F
Evaporator freeze protection requires resetting the
CoolLogic Touch
High Leaving Condenser Water Temperature -
Above 138° F
The CoolLogic Touch
on-screen button.
Communications Error
controller and the CoolLogic Touch
No Run - No Status
This alarm occurs when a compressor is commanded to run
and the status is not sensed by the controller. The status
mounted to the compressor contactor, or a current switch
that senses a minimum compressor amperage to close its
ON status of either compressor.
Motorized Valve Alarm
switch contact closure of the motorized valves (used for
the current mode of operation) will complete a circuit (or
circuits) through the resistor board and is then input to the
Miscellaneous Alarm Functions of the
CoolLogic Touch Control System

9
www.climacoolcorp.com
Chilled Water Flow Sensor
The CoolLogic Touch
pressure drops across the chilled water main headers. If the
input signal, the chiller will not be allowed to run and a chilled
The alarm clears automatically which constitutes an “OK to
most recent 100 alarms.
Condenser Water Flow Sensor
The CoolLogic Touch
pressure drops across the condenser water main headers.
and the alarm condition is logged for permanent retention
of the most recent 100 alarms. This will constitute an “OK to
Voltage/Phase Monitor
installation with the CoolLogic Touch
and connected to the main three phase power panel that
feeds all the installed modules. Two low voltage control
wires are connected to the CoolLogic Touch
as well along with the power wiring. Do not install control
wiring in the same conduit as line voltage wiring or with
wires that switch highly inductive loads such as contactor
and relay coils.
Install one (1) monitor per bank at main power distribution
panel to monitor voltage and phasing of power to the
modules. See Wiring Diagram on page 23.
Chilled/Heating Water Reset
The CoolLogic Touch
reset the leaving water temperature set point using a hard
wired input voltage or current signal, or the voltage input
optional and must be activated through the appropriate setup
Standard Features
menus. If the chiller is operating and it receives a chilled water
reset command, the leaving chilled water temperature setting
will be allowed to ramp toward the new setting at a rate of
2°F every seven minutes. When the chiller is not operating and
it receives a chilled water reset command, the leaving chilled
water temperature setting will be fully reset immediately.
External Chilled Water Set Point Option
The CoolLogic Touch
accepts either 2-10 VDC or 4-20 mA signals to set the leaving
Building Automation System (BAS) installations. The 2-10 VDC
and 4-20 mA ranges each correspond to a preset range from
water set point.
External Condenser Water Set Point Option
Associated with heat recovery chillers, the CoolLogic Touch
VDC and 4-20 mA signals to set the leaving condenser
BAS installations. The 2-10 VDC and 4-20 mA ranges each
correspond to a preset range from the minimum condenser
Demand (or Load) Limiting
To limit the number of compressors that can be simultaneously
energized, a demand limit control is available. The CoolLogic
Touch
number of compressor stages allowable at any one time. This
input is typically used with generic BAS installations. The 2-10
VDC and 4-20 mA ranges each correspond to a range from 0%
to 100% of the total available compressor stages.
Alarm Output
The relay output contact is closed whenever there is an active
latching or non-latching alarm condition present relative to a
fault parameter.
Chiller Status Output
The relay output contact is closed whenever all input signals to
the chiller are present and normal, indicating the requirement
for the chiller to operate when able.

10
www.climacoolcorp.com
Chilled Water Temperature Sensor Connections
Chilled water temperature monitoring (entering and leaving)
is a standard feature of the CoolLogic Touch Control System. It
is accomplished by using a factory supplied pair of sensors and
supplied and installed onto the main water headers) within
NOTE:
Sensors must be fully inserted into the well to obtain
proper readings and must be 2½ pipe diameter minimum
before or after an elbow.
Condenser Water Temperature Sensor Connections
Condenser water temperature monitoring (entering and
leaving) is a standard feature of the CoolLogic Touch Control
System. It is accomplished by using a factory supplied pair
water locations. NOTE: Sensors must be fully inserted into
the well to obtain proper readings and must be 2½ pipe
diameter minimum before or after an elbow.
Building Automation System (BAS) Interface
Internal operational information is available where the
chiller is to be integrated into a building system and
monitored by the equipment of a controls manufacturer.
Available protocols built into the CoolLogic Touch Control
• BACnet
• MODBUS
• N2*
• LonWorks*
second intervals.
LonWorks LonTalk®Communications
Interface Option
The CoolLogic Touch
LonTalk®communication interface between the chiller and
the BAS. Additional hardware is required (Echelon SLTA-10
between a LonTalk compatible device and the CoolLogic
Touch Control System.
Compressor Unloading
Compressor unloading routines are programmed into
each module controller. When any one of the module or
compressor control parameters approaches a pre-limit
condition, the CoolLogic Touch
appropriate compressor unloading commands to avoid
time. The module information screen can be accessed to
view unload conditions when they are active.
Compressor Minimum O Delay
delay is 200 seconds.
Compressor Minimum On Delay
When a compressor is turned on, the compressor will
remain on for this period of time. This time can be cut short
if an alarm condition is predicted. The default minimum on is
90 seconds.
Standard Features

11
www.climacoolcorp.com
NOTE:
various menu items.
Startup and Warranty Form
CoolLogic CoolLogic Touch
Controller
Page 1 of 3
Project Name:
Start-Up Date:
Chiller # Bank #
Chiller Control Type................................
Chiller Control Source ............................
Enable Chiller from Keypad?..................
....................................
Chiller Model Type..................................
System Setup
Module Evap Water Out Low Limit .......
Module Evap Water Out Hi Limit...........
Module Cond Water Out Low Limit.......
Module Cond Water Out Hi Limit ..........
Module Water Temp Limits
Evap Water In Low Limit........................
Evap Water In Hi Limit............................
Evap Water Out Low Limit.....................
Evap Water Out Hi Limit.........................
Cond Water In Low Limit .......................
Cond Water In Hi Limit...........................
Cond Water Out Low Limit ....................
Cond Water Out Hi Limit........................
Main Water & Ambient Temps
Module 1 Size..........................................
Module 2 Size .........................................
Module 3 Size .........................................
Module 4 Size .........................................
Module 5 Size .........................................
Module 6 Size.........................................
Module Size Selector

12
www.climacoolcorp.com
NOTE:
various menu items.
Startup and Warranty Form
Page 2 of 3
Chiller # Bank #
..........................
...........................
.....................................
.......................................
..................
..........................
...........................
.....................................
......................................
.................
.........
..........
...
.....
.................
.....................
Discharge Temp Available......................
Suction Temp Available..........................
..
............................
Enable CHS Hi Alarm ..............................
....................
Lo Suction Temperature (Cool) .............
Local Evap Water Out Setpoint (Cool)..
Min Evap Water Out Setpoint (Cool) ....
....
Local Evap Water Out Setpoint (Heat)..
Min Evap Water Out Setpoint (Heat)....
...
Cool and Heat Setpoint Menus

13
www.climacoolcorp.com
Startup and Warranty Form
Page 3 of 3
Chiller # Bank #
MAC Address
............. __ __ __ __ __ __ __
Ethernet Network # ......... __ __ __ __ __
Ethernet MAC Add ...........
__ __-__ __-__ __-__ __-__ __-__ __
..................... __ __ __ __ __
...........
__ __ __-__ __ __-__ __ __-__ __ __
Current Subnet Mask .......
__ __ __-__ __ __-__ __ __-__ __ __
Current Gateway Add.......
__ __ __-__ __ __-__ __ __-__ __ __
NOTE:
various menu items.
Contractor Name:
Address:
Phone:
(Authorized Signature):

14
www.climacoolcorp.com
User Access – Home Screen (Example Only)
CoolLogic Touch Screen Menu Hierarchy
CoolLogic Touch Menu
1 – PREV – Move back to last screen
2 – General System Settings
• Heat and Cool Set Points
• Module/Compressor Status
3 – Alarm Menu - Module and CoolLogic Touch
Alarm Resets
4 – Status
• All Module unload status
• Module size & status
• Compressor run times & cycles
5 – Module Status
• Module refrigeration temps and pressures
6 – Module Level Conguration
• Module Temperature and Pressure Set Points
• Module Valve and Fan Congurations
7 – Service Menu
• Manual Mode
• Sensor Calibration
• Module Water Temperature Limit
8 – CoolLogic Touch Level Congurations
• Module Size Selector
• PID – Cooling & Heating
• Water Temperature Limits
• External Input Congurations –
Temp Resets, DPT
CoolLogic Controller
Level Conguration
(6)
Module Level
Conguration
(8)
Modules populate
screen as they
are added
Alarm Menu (3)
Status (4)
System Setup (2) Service Menu (7)
Previous
(1)
Tap any module to
see its respective
information and status
(5)

15
www.climacoolcorp.com
Status User Access
Home
Module Info Module Level
Conguration
CoolLogic Controller
Level Conguration
System Setup
Status
Alarms
Service Menu

16
www.climacoolcorp.com
Setup User Access
Remote Demand
Limiting Conguration Controller Cong
Cool & Heat
Setpoints Free Cooling Setup
System Setup

17
www.climacoolcorp.com
Service User Access
Service Menu
Congure DPT
Device
Calibrate & Lock
Temps
Congure Low
Ambient Heat
Alarm Lockout
Reset
Reset Comp
Run times & Cycles
Diagnostic Manual
Mode (FN7)

18
www.climacoolcorp.com
Connection Type
10BaseT port.
Ethernet Network
The CoolLogic Touch Controller is equipped with an interface
which may be connected directly to the Ethernet network
using the 10BaseT port. To prevent circular routes, the
CoolLogic Touch
516800.
and the Ethernet Network number set to0. NOTE: If these
settings need to be changed, please contact a ClimaCool
IP Address
typical CoolLogic Touch
IP .............................................192.168.17.100
Subnet Mask...........................255.255.255.0
Gateway..................................192.168.17.1
NOTE: If these settings need to be changed, please contact
CoolLogic Touch Control System Network Setup
Device Instance of CoolLogic Touch Controller
The device instance number for the CoolLogic Touch
CoolLogic
Touch
switches on the CoolLogic
digit, one rotary switch is for 10’s digit, and the other is for
the 1’s digit), (see Figure 3). NOTE: If these settings need to
Device Instance of Module Controller
is 243002
the SECOND Module Controller is 243003
NOTE:
If these settings need to be changed, please contact a
NOTE: Contact ClimaCool factory for network points list.
NOTE: The installation of two banks, with separate
CoolLogic Touch Control Panels, utilizing the same BAS
network must have dierent device instance numbers
to negate any conicts. Contact factory for special
programming requirements.
Table of contents
Other Nibe Control System manuals
Popular Control System manuals by other brands
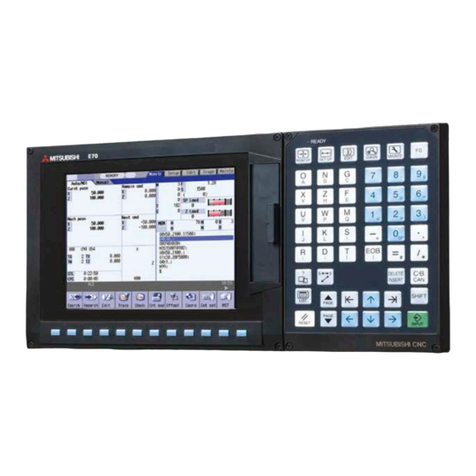
Mitsubishi Electric
Mitsubishi Electric E70 Series instruction manual
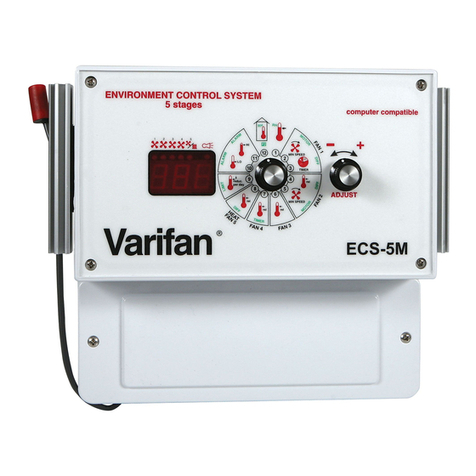
Varifan
Varifan ECS 5M user manual
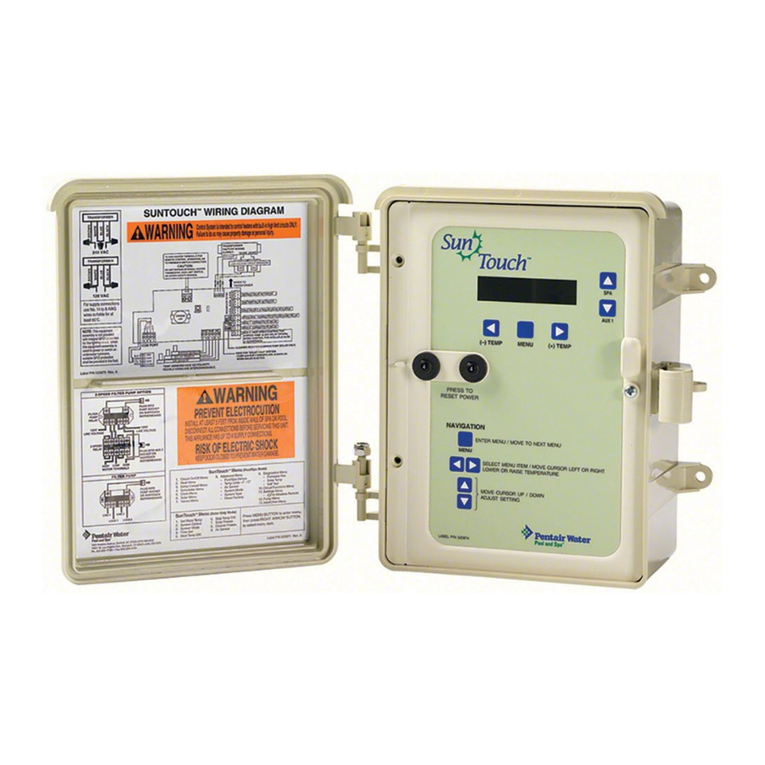
Pentair
Pentair Pool and Spa Control System SunTouch Installation and user guide

OSI
OSI 5892 Maintenance and Repair Manual
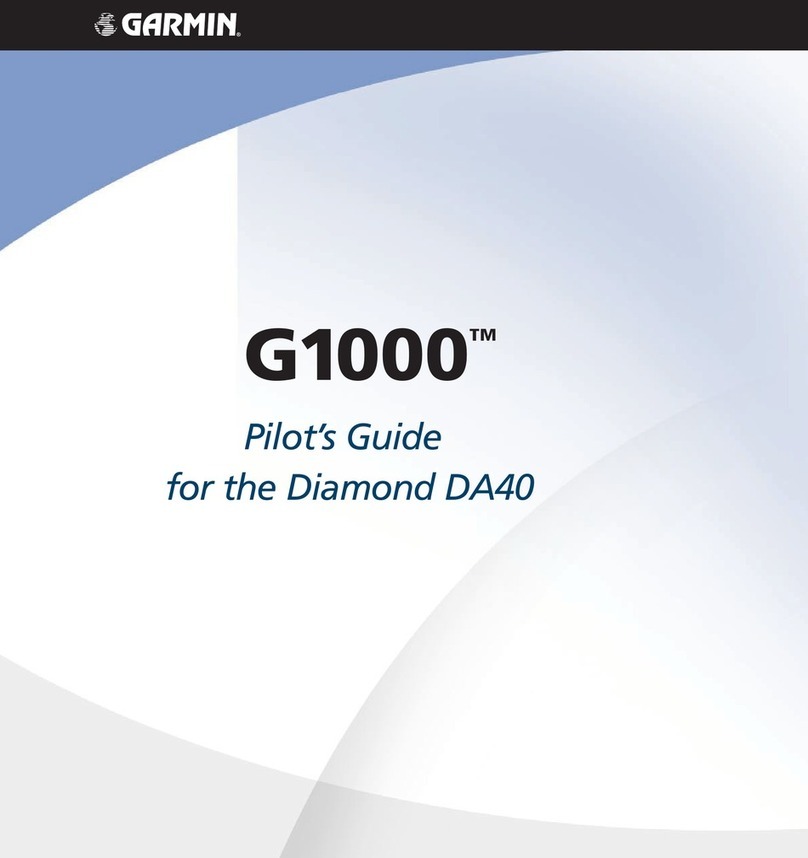
Garmin
Garmin G1000 Series pilot's guide
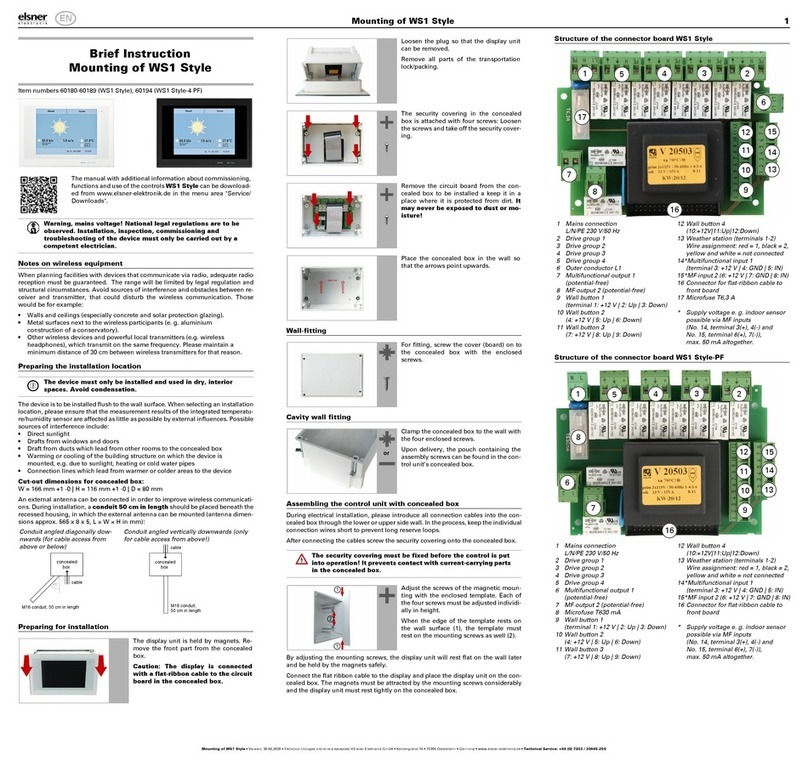
Elsner
Elsner WS1 Color Brief Instruction
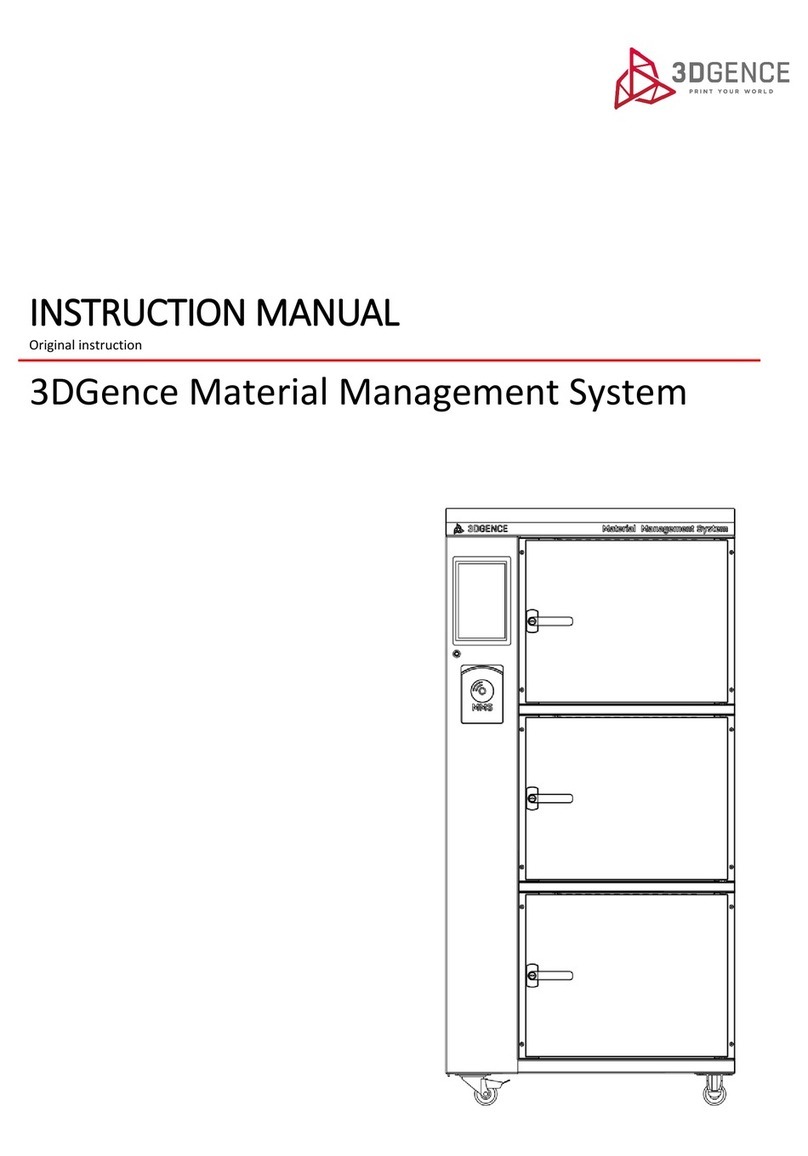
3DGence
3DGence MMS1 instruction manual
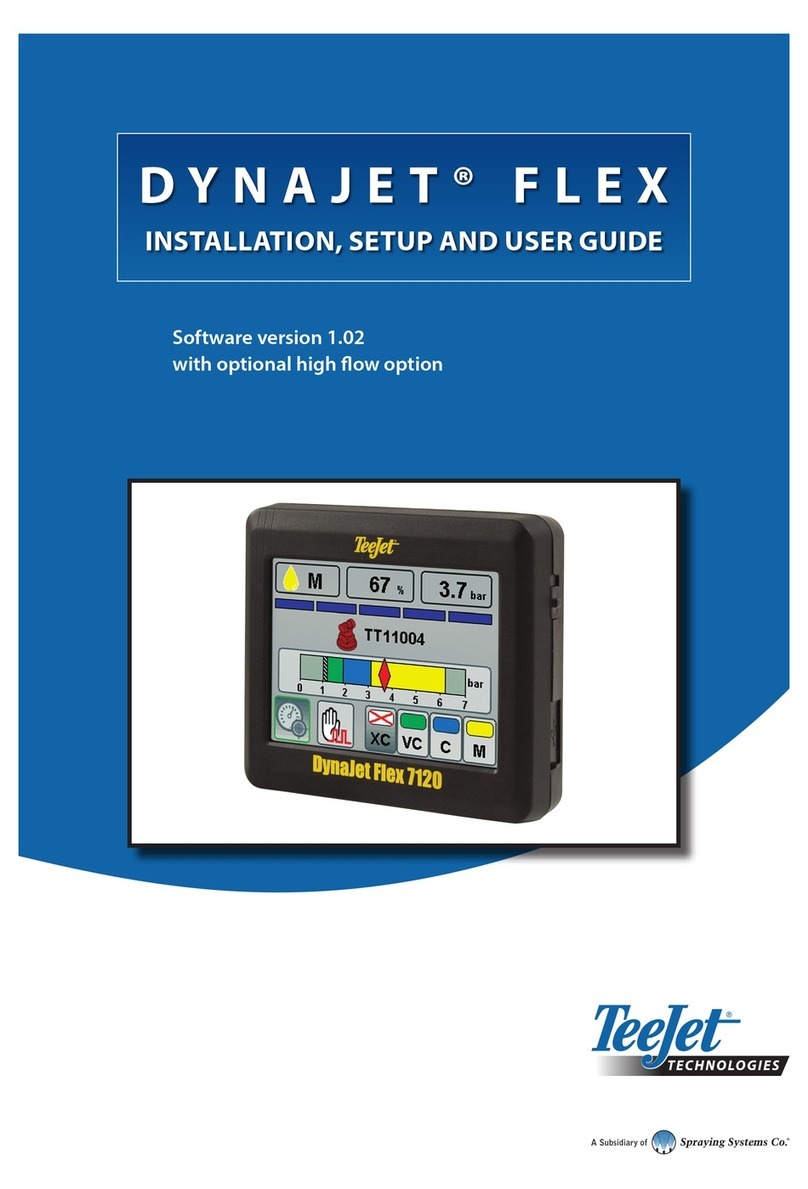
TeeJet Technologies
TeeJet Technologies DynaJet Flex Series INSTALLATION, SETUP AND USER GUIDE

CAME
CAME PST001 installation manual
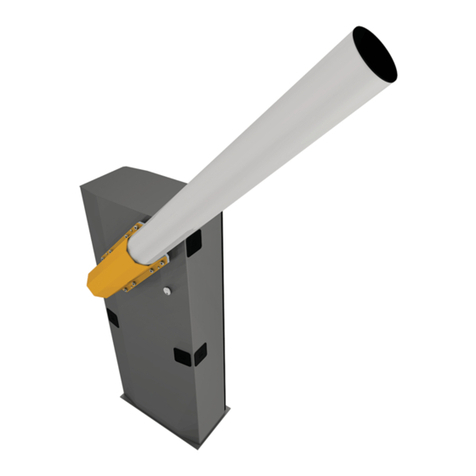
CAME
CAME G5000 Installation, operation and maintenance manual
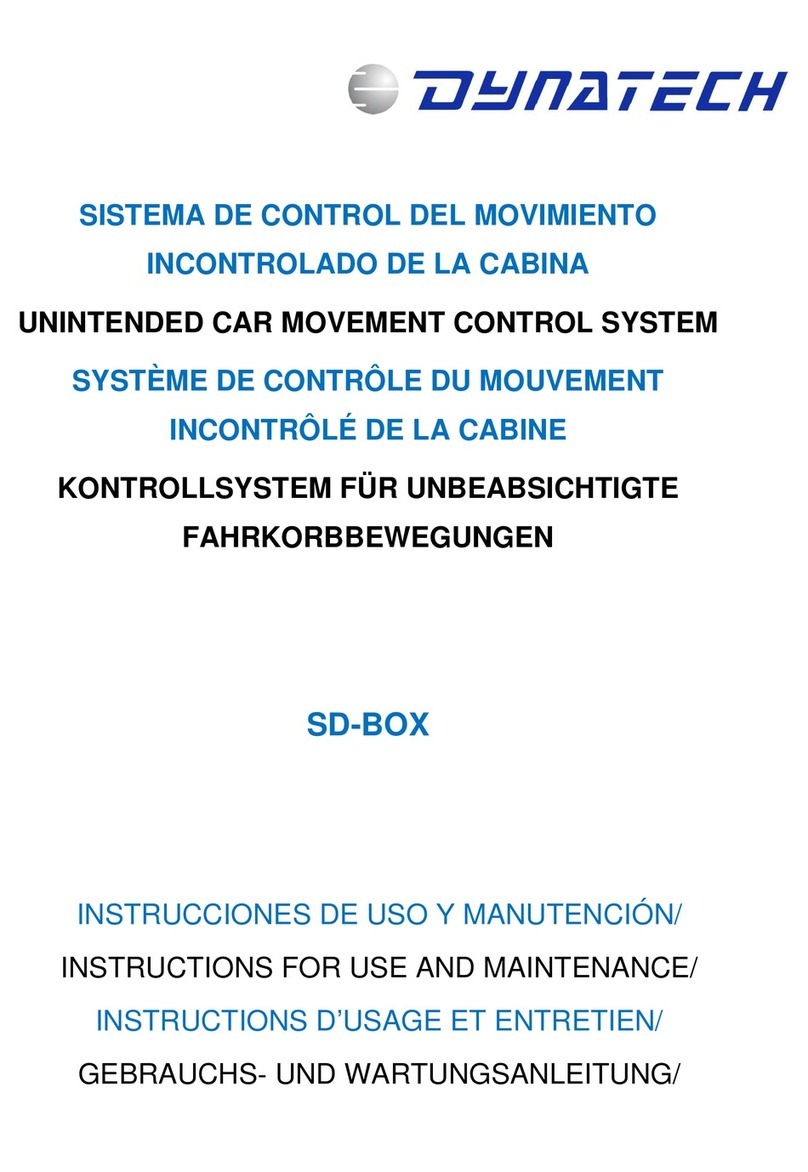
Dynatech
Dynatech SD-BOX Instructions for use and maintenance
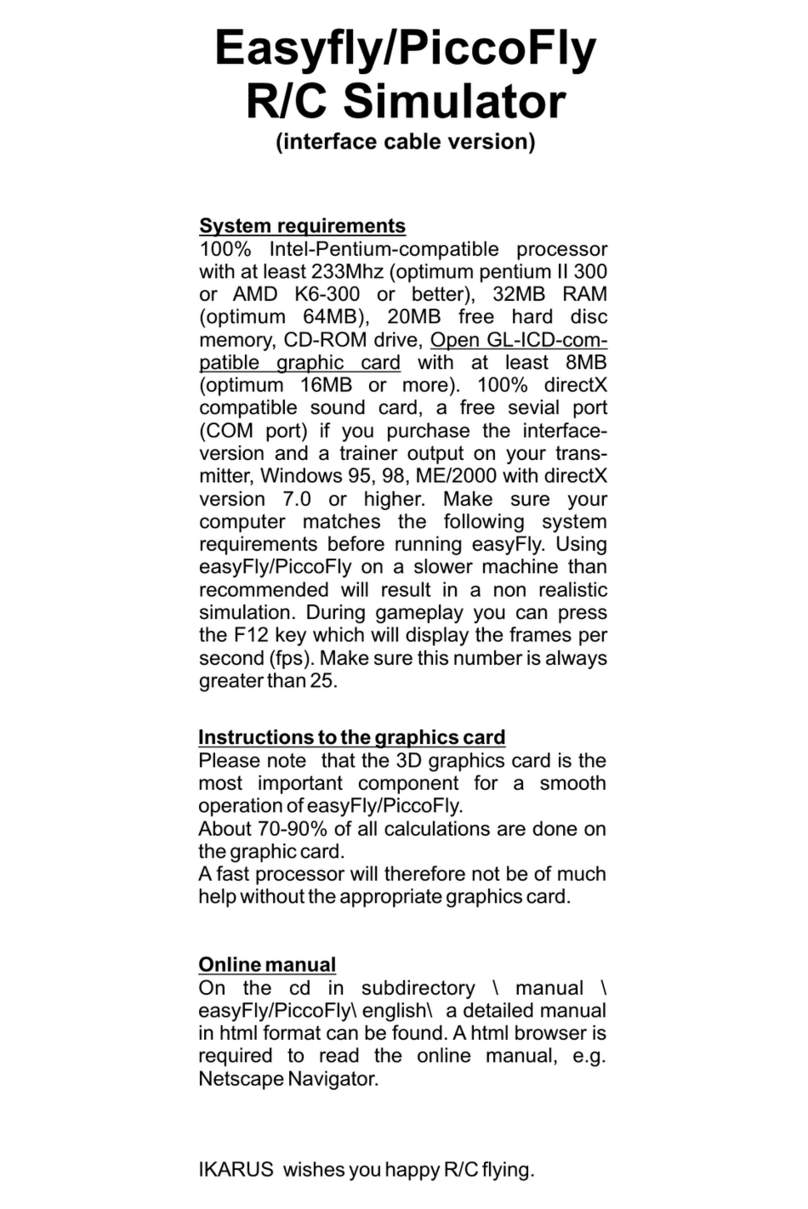
iKarus
iKarus Easyfly Quick installation guide