Giltrap Generation II RF User manual

GILTRAP GENERATION II
RF CONTROL SYSTEM
Operating, Installation & Technical Manual
Part Number: 595-0036
February 2010
Introduction..................................................................................................................................................... 2
Control Mode Options .................................................................................................................................... 2
Remote Display Layout................................................................................................................................... 3
Controller Layout............................................................................................................................................ 3
Operation Section..........................................................................................................4
Overview ......................................................................................................................................................... 4
Valve Over-ride Function ............................................................................................................................... 4
REMOTE DISPLAY SCREENS................................................................................................................................. 5
Screen Symbols ............................................................................................................................................... 5
Start-up Screen................................................................................................................................................ 5
Standard Mode Screen.................................................................................................................................... 6
Weight Mode Screen ....................................................................................................................................... 7
Distance Mode Screen..................................................................................................................................... 8
Speed Mode Screen......................................................................................................................................... 9
Scales Screen................................................................................................................................................. 10
Installation Section......................................................................................................11
Component Layout........................................................................................................................................ 11
Remote Display Mounting & Power Supply.................................................................................................. 12
Forage Wagon Controller & Power Supply.................................................................................................. 12
Setting the RFID Number.............................................................................................................................. 14
Fitting the Power Module Circuit Board ...................................................................................................... 15
Fitting the Wheel Sensor............................................................................................................................... 15
Fitting the Load Cells ................................................................................................................................... 16
Setting System Parameters............................................................................................................................ 17
Checking Setup Parameters.......................................................................................................................... 21
Factory Parameter Settings .......................................................................................................................... 22
Final Check................................................................................................................................................... 23
Technical Section........................................................................................................24
Power and Charging..................................................................................................................................... 24
System Display LEDs.................................................................................................................................... 25
System Safety Fuses ...................................................................................................................................... 26
Radio Frequency Device............................................................................................................................... 26
Wiring Schematic.......................................................................................................................................... 27
Cable Descriptions........................................................................................................................................ 29
Remote Display Screen Contrast................................................................................................................... 30
Fault Diagnosis............................................................................................................................................. 31

Generation II RF Control System –Operating, Installation & Technical Manual
RF Gen II System Technical Manual Rev02_12_10
2
Introduction
The Giltrap Generation II RF Control System consists of a Controller that is mounted on the
wagon that uses wireless technology to relay data such as feed rate, load weights or feed-
out amounts (depending on options purchased) from the wagon and displays it on the
Remote Display mounted near the operator on the tractor, allowing the operator to control
the feed rate using different modes.
Powerfully capable, yet simple to use, the controller has large buttons and an easy-to-read
display allowing the operator to constantly monitor, and adjust the feed rate when needed, all
while on the move.
Control Mode Options
The system has a total of five different operation modes available. The availability of these
are dependant on the hardware options fitted to the machine.
Hardware available: Load cells –for weight readings
Solenoid coil –for floor control
Wheel sensor –for ground speed calculation
Standard Mode
The operator controls the feed rate through a percentage range from 0 to 100%.
Requires a solenoid coil to be fitted. Load cells are optional.
Weight Mode
The operator can enter a target weight to feed. The feed rate control is the same as Standard
mode.
Requires load cells and solenoid coil to be fitted.
Distance Mode (also known as Fully Automatic mode)
The wagon will unload the required amount over the required distance, and will compensate
for changes in ground speed.
Requires load cells, solenoid coil and wheel sensor to be fitted.
Speed Mode
The operator controls the feed out rate through a percentage range from 0 to 100% and the
feed rate is automatically adjusted according to ground speed.
Requires a solenoid coil and wheel sensor to be fitted. Load cells are optional.
Scales Mode
Only has a weight display. Requires load cells to be fitted.
Floor rate is controlled manually.

Generation II RF Control System –Operating, Installation & Technical Manual
RF Gen II System Technical Manual Rev02_12_10
3
Display screen
UP button
GO button
STOP button
RIGHT button
MODE button
DOWN button
Power plug
Power switch
TARE/GROSS button
LEFT button
ZERO button
Power light
Signal light
Signal light
Valve light
Weight connection
Valve connection
Power connection
Power ON
button
Power OFF
button
Remote Display Layout
Controller Layout

Generation II RF Control System –Operating, Installation & Technical Manual
RF Gen II System Technical Manual Rev02_12_10
4
IMPORTANT
Manual over-ride located beneath this
cover
To operate in case of electronic
malfunction, undo locking ring and
screw in adjuster.
Use ¼ - ½ turn adjustments.
Operation Section
Overview
Assuming installation (page 11 –23) has been completed, the power for the system is
controlled by the switch adjacent to the Remote Display.
1. Turn the switch on to provide power to the Remote Display and the wagon.
2. If the wagon is disconnected, press and hold the ON button on the Controller for one
second. The Controller is now operating on its own battery.
3. Begin loading the wagon. See more detailed information regarding modes and
buttons.
4. Once completed loading, connect the wagon to the tractor and connect the 7-pin
plug.
5. Once ready to feed, select the appropriate mode and press GO button. You are now
ready to proceed.
Note: The Controller power light will illuminate when the ON button is pressed or the wagon
is plugged into the tractor. To turn off, the wagon must be un-plugged before pressing the
OFF button.
Valve Over-ride Function
When a solenoid is fitted for floor control, a manual over-ride function will also be provided.
Note: This function over-rides all RF floor rate control.
Use ¼ - ½ turn adjustments per time. Do not over-adjust.
For electronic operation with RF control, the screw adjuster must be unscrewed all the way
out (anti-clockwise) and the locking ring tightened.
Locking ring
Over-ride adjuster
Label on cover

Generation II RF Control System –Operating, Installation & Technical Manual
RF Gen II System Technical Manual Rev02_12_10
5
Remote Display Screens
Screen Symbols
Apart from usual text characters, the screen can display other symbols at various times.
Start-up Screen
When the Remote Display is powered up, the start-up screen is displayed for 3 seconds as
below. After this the screen will change to the operating screen.
If the wagon is not connected i.e. not getting power from the tractor, the controller will not
start. The screen below will display until communication has begun by plugging in the wagon
or pressing and holding the GO button on the controller for 1 or more seconds.
After establishing communication, it will proceed directly to the next screen.
Once communication has begun between the devices, a screen similar to the one below will
show.
The modes that are available are dependant on the hardware options fitted to the machine.
The battery symbol indicates when the system is operating on its own battery. The
voltage display indicates the condition of the battery.
The antenna symbol indicates when the Controller and Remote Display have
communication between them. This must show at all times for successful operation.
GILTRAP GEN II
CONTROL SYSTEM
Channel: 1 Rev
3.4
Remote Display software
revision
Remote Display RF
channel
FEED RATE: 50%
DISPENSED: 0kg
GROSS: 2950kg
STOP Std 12.5V
Waiting for
RF Forage Wagon
Communications...

Generation II RF Control System –Operating, Installation & Technical Manual
RF Gen II System Technical Manual Rev02_12_10
6
Standard Mode Screen
In standard mode, the feed rate is shown as a percentage. A range of 1-100% is available
with 100% being maximum feed rate. This rate is shown on the top line of the screen. This
mode is useful for general operation and is the most simple to use.
Screen Features:
The top line shows the feed rate.
The bottom line of the screen shows the status of the system (STOP), the mode of operation (Std)
and connectivity status.
Additional features that show if load cells are fitted:
The second line will show the weight dispensed since GO was pressed.
The third line will display the present wagon weight. This may be gross or tare.
The bottom line of the screen shows the status of the system (STOP), the mode of operation
(Std), the battery voltage (highest voltage available to the unit. When disconnected from the
tractor, this will be the internal battery voltage), and connectivity status.
Operating Notes:
Screen Warnings:
“WAGON POWER NOT CONNECTED” will flash on the display if the GO button on the Remote
Display is pressed without the wagon being plugged into the tractor and/or power not getting from
the tractor to the Controller.
FEED RATE: 50%
DISPENSED: 1050kg
GROSS: 2950kg
STOP Std 12.5V
FEED RATE: 50%
STOP Std
Rate control only
Rate control with
load cells fitted
Feed Rate
System status
Mode of operation
Connectivity status
Dispensed amount
Product amount in machine
Battery voltage
System battery indicator
The operator can adjust the rate percentage figure by pressing UP or
DOWN on the keypad.
The operator can select between gross and tare weight to be
displayed by pressing TARE/GROSS on the keypad.
The operator can zero only the dispensed weight by pressing GO on
the keypad.
The operator can start and stop the feed-out by pressing GO and
STOP on the keypad.
The operator can switch to other available operating modes by
pressing MODE on the keypad.
The operator can zero the gross and dispensed weight by pressing
ZERO on the keypad.

Generation II RF Control System –Operating, Installation & Technical Manual
RF Gen II System Technical Manual Rev02_12_10
7
Weight Mode Screen
In Weight mode, the feed rate is shown as a percentage. A range of 1-100% is available
with 100% being maximum feed rate. This rate is shown on the top line of the screen.
The operator can enter a target weight to feed out before the wagon floor will stop moving
and the system status will return to STOP.
(V3.9 onwards) The operator can enter a target weight to feed out before a beeper will
sound and the wagon floor will stop moving and the system status will return to STOP.
(All) The TO FEED value must be greater than zero else the system will not operate. Use
STANDARD mode for feeding if weight quantities are required.
Screen Features:
The top line shows the feed-out rate.
The second line shows the weight to feed out before a beeper sounds.
The third line shows the weight of the current load. This may be gross or tare.
The bottom line of the screen shows the status of the system (STOP), the mode of operation
(Weight), the battery voltage (highest voltage available to the unit. When disconnected from the
tractor, this will be the internal battery voltage), and connectivity status.
Operating Notes:
Screen Warnings:
“WAGON POWER NOT CONNECTED” will flash on the display if the GO button on the Remote
Display is pressed without the wagon being plugged into the tractor and/or power not getting from
the tractor to the Controller.
FEED RATE: 50%
TO FEED: 560kg
GROSS: 2950kg
STOP Weight 12.5V
Mode of operation
System status
System battery indicator
Feed Rate
Target weight to feed
Product weight in machine
Connectivity status
Battery voltage
The operator can alter the feed-out rate by adjusting the rate
percentage by pressing UP or DOWN on the keypad.
The operator can adjust the weight to be dispensed by adjusting the
‘TO FEED’ figure. This is done by pressing UP or DOWN on the
keypad when the ‘TO FEED’ figure is underlined. Use the RIGHT
or LEFT button to move the underline cursor.
The operator can start and stop the feed-out by pressing GO
and STOP on the keypad.
The operator can switch to other available operating modes
by pressing MODE on the keypad.
The operator can select between gross and tare weight to be
displayed by pressing TARE/GROSS on the keypad.
The operator can zero the gross and dispensed weight by
pressing ZERO on the keypad.

Generation II RF Control System –Operating, Installation & Technical Manual
RF Gen II System Technical Manual Rev02_12_10
8
Distance Mode Screen
In Distance mode, the feed rate is automatically set by dispensing feed over a set distance.
Screen Features:
The top line shows the weight to feed out.
The second line shows the distance over which to feed this weight.
The third line shows the present wagon weight. This may be gross or tare.
The bottom line of the screen shows the status of the system (STOP), the mode of operation (Dist), the
battery voltage (highest voltage available to the unit. When disconnected from the tractor, this will be the
internal battery voltage), and connectivity status.
Operating Notes:
Screen Warnings:
“WAGON POWER NOT CONNECTED” will flash on the display if the GO button on the Remote Display is
pressed without the wagon being plugged into the tractor and/or power not getting from the tractor to the
Controller.
“INCREASE GROUND SPEED” will flash on the display when the wagon is travelling too slow and causing
the machine to overfeed. Note that ground speed needs to increase not tractor revs.
“DECREASE GROUND SPEED” will flash on the display when the wagon is travelling faster than the
machine can feed. Note that ground speed needs to decrease not tractor revs.
TO FEED: 1800kg
LENGTH: 100m
GROSS: 2950kg
STOP Dist 12.5V
Mode of operation
System status
Feed to dispense
Distance to travel
Product weight in machine
Connectivity status
Battery voltage
System battery indicator
The operator can adjust the weight to be dispensed by adjusting the
‘TO FEED’ figure. This is done by pressing UP or DOWN on the
keypad when the ‘TO FEED’ figure is underlined. Use the RIGHT or
LEFT button to move the underline cursor.
The operator can adjust the distance to feed the weight over by
adjusting the ‘LENGTH’ figure. This is done by pressing UP or DOWN
on the keypad when the ‘LENGTH’ figure is underlined. Use the
RIGHT or LEFT button to move the underline cursor.
The operator can start or stop the operation by pressing GO or STOP
on the keypad. If the feed bins are unequal in length, enter the total
length of the bins in the ‘LENGTH’ figure and the total amount to feed
in the ‘TO FEED’ figure. After travelling the first bin, press STOP on the
keypad. The display will change from RUN to WAIT. You can then
travel forward or backward without the distance changing. Press GO to
continue or press and hold the STOP button for 3 or more seconds to
reset the system status to STOP. The system will automatically return
to STOP mode after counting down the distance to zero.
The operator can switch to other available operating modes by
pressing MODE on the keypad.
The operator can select between gross and tare weight to be displayed
by pressing TARE/GROSS on the keypad.
The operator can zero the gross and dispensed weight by pressing
ZERO on the keypad.

Generation II RF Control System –Operating, Installation & Technical Manual
RF Gen II System Technical Manual Rev02_12_10
9
Speed Mode Screen
In Speed mode, the machine will maintain a consistent feed-rate relative to ground speed.
The feed rate percentage is adjustable from 1 –100%.
Screen Features:
The top line shows the feed rate.
The bottom line of the screen shows the status of the system (STOP), the mode of operation
(Speed) and connectivity status.
Additional features that show if load cells are fitted:
The second line shows the weight fed out since the wagon was loaded.
The third line shows the present wagon weight. This may be gross or tare.
The bottom line of the screen shows the status of the system (STOP), the mode of operation
(Speed), the battery voltage (highest voltage available to the unit. When disconnected from the
tractor, this will be the internal battery voltage), and connectivity status.
Operating Notes:
Screen Warnings:
“WAGON POWER NOT CONNECTED” will display if the GO button on the Remote Display is
pressed without the wagon being plugged into the tractor and/or power not getting from the tractor
to the Controller.
FEED RATE: 50%
STOP Speed
FEED RATE: 50%
DISPENSED: 940kg
GROSS: 3540kg
STOP Speed 12.5V
Rate control only
Rate control and
load cells fitted
Feed Rate
System status
Mode of operation
Connectivity status
Dispensed amount
Product weight in machine
Battery voltage
System battery indicator
The operator can alter the feed-out rate by adjusting the rate percentage by
pressing UP or DOWN on the keypad while in STOP mode only.
The operator can adjust the weight to be dispensed by adjusting the ‘TO
FEED’ figure. This is done by pressing UP or DOWN on the keypad when
the ‘TO FEED’ figure is underlined. Use the RIGHT or LEFT button to move
the underline cursor.
The operator can start or stop the feed-out by pressing GO or STOP on the
keypad.
The operator can zero only the dispensed weight by pressing GO on the
keypad.
The operator can switch to other available operating modes by pressing
MODE on the keypad.
The operator can select between gross and tare weight to be displayed by
pressing TARE/GROSS on the keypad.
The operator can zero the gross and dispensed weight by pressing ZERO
on the keypad.

Generation II RF Control System –Operating, Installation & Technical Manual
RF Gen II System Technical Manual Rev02_12_10
10
Scales Screen
In Scales mode, the screen will only display weight figures. This mode is used when no rate
control is fitted to the wagon.
No other modes are available if only load cells are fitted.
The operator can enter a target weight to feed when a beeper will sound, the wagon floor will
stop moving (if the floor control solenoid is fitted) and the system status will return to STOP.
Features:
The top line shows the weight to feed out before a beeper sounds.
The second line shows the weight dispensed since GO was pressed.
The third line shows the tare or gross weight in the machine.
The bottom line of the screen shows the mode of operation (Scales), the battery voltage (highest
voltage available to the unit. When disconnected from the tractor, this will be the internal battery
voltage), and connectivity status.
Operating Notes:
Screen Warnings:
None
TO FEED: 560kg
DISPENSED: 733kg
GROSS: 3440kg
STOP Scales 12.5V
Mode of operation
System status
Target weight to feed
Dispensed amount
Amount in machine
Connectivity status
Battery voltage
System battery indicator
The operator can adjust the weight to be dispensed by adjusting the
‘TO FEED’ figure. This is done by pressing UP or DOWN on the
keypad when the ‘TO FEED’ figure is underlined. Use the RIGHT or
LEFT button to move the underline cursor.
The operator can select between gross and tare weight to be
displayed by pressing TARE/GROSS on the keypad.
The operator can zero only the dispensed weight by pressing
GO on the keypad.
To allow the dispensed weight to accumulate and the target
feed weight to work, the operator must press GO before
commencing feeding.
The operator can zero the gross weight and dispensed weight
by pressing ZERO on the keypad.

Generation II RF Control System –Operating, Installation & Technical Manual
RF Gen II System Technical Manual Rev02_12_10
11
Installation Section
Component Layout
Valve cable
#TCS-V2CABVAL
Data cable (1m) #TCS-V2CABWGT
Wheel sensor (5m)
#TCS-OEM-PROX
Load cells (4 or 6)
#ES-WLY00003P
Weight module
#TCS-V2WGTMOD
Remote display
#TCS-V2DISP
Valve assembly
#HYSUPERVC-DPBM
Power module
#TCS-V2PB
Cable from switch to tractor plug (2m)
Controller power cable (1m)
#TCS-V2CABCON
Battery
#TCS-BATTERY2
7 core cable (5.5m) with plug
#TCS-LOOM2
Cab switch
12 –24VDC Supply
(Tractor battery)
Brown - Positive
Blue - Negative
5A Fuse
Battery cable (0.55m)
#TCS-V2CABBAT
Controller
#TCS-V2CONTR
Cable from battery to switch (5m)
5A Fuse
Tail lights
7 pin plug
#PLUG7PINM
Install loom #TCS-LOOM1 (with box)
Install loom #TCS-LOOM1V2 (no box)
#LIGHTLED-LH
#LIGHTLED-RH
Remote display cable
#TCS CABLE

Generation II RF Control System –Operating, Installation & Technical Manual
RF Gen II System Technical Manual Rev02_12_10
12
Remote Display Mounting & Power Supply
The Remote Display is designed to be mounted in the tractor cab and be easily accessible to
the driver. It contains a radio frequency (RF) communication device to control the Forage
Wagon Controller (Controller).
It will require shielding from the weather elements of sun and rain etc.
The Remote Display requires 12-24 volts DC to operate. It will typically only draw 0.2A. The
power supply must originate from the tractor battery as part of the installation loom (supplied
with the machine).
Forage Wagon Controller & Power Supply
The Forage Wagon Controller is powered from the tractor while operating. When
disconnected from the tractor, it draws power from its own sealed lead acid battery.
No installation wiring is required on the Forage Wagon.
The tractor requires an installation loom (supplied) which provides a switched and fused
positive and negative supply from the tractor battery to the rear 7-pin socket. The tractor
battery is the best power supply point as it provides the most stable and “quiet” power
source. Do not use any other power source.
Tractor Plug
There are three CPC connectors on the Controller module.
If a connector is not used, place the terminal cap over it.
RF positive supply from
wiring loom (BROWN)
RF negative supply from
wiring loom (BLUE)
Terminal cap
Wagon plug:
RF positive supply
(BLACK) wire to be in
pin 2
RF negative supply
(BLUE) wire to be
combined with (WHITE)
wire into pin 3

Generation II RF Control System –Operating, Installation & Technical Manual
RF Gen II System Technical Manual Rev02_12_10
13
Mounting the Modules
Modules should be mounted as illustrated.
Power wires should be kept separate where possible from the load cell cables.
Only 2 screws are required at opposite corners of each module.
Keep all cables clear of moving parts.
Control Module
Control Module mounting bracket
Battery
Weight Module
Power Module
Battery base plate
Run power
cables this
side
Run load cell
cables this
side

Generation II RF Control System –Operating, Installation & Technical Manual
RF Gen II System Technical Manual Rev02_12_10
14
DIP switches
*** SETUP ***
RFID Number
1.00
Setting the RFID Number
The RFID Number setup screen is used to assign a wireless address to the Controller. This
feature is available to prevent interference between two systems when they are operated in
close proximity to each other.
To access the Remote Display RFID screen, re-power the display and press and hold the
MODE button until a setup screen appears.
The operator can press the UP button or the DOWN button to adjust this value. Press GO to
enter then STOP to escape. Re-power the Remote Display to access the new channel.
Controller Settings
After removing the Controller cover, a DIP switch with 8 white switches is visible.
The D.I.P. (dual inline plastic) switches which are labelled 1 to 8 are used to select
the RF channel ID.
The switch is considered to be ‘on’ when switched to the right hand side.
The channel ID of the Controller MUST match the software setting of the Remote
Display.
If the channel ID is changed in either the Remote Display or Controller then you must
re-power both devices for the new setting to take effect. To re-power the Controller,
unplug the POWER cable for 5 seconds.
The DIP switch settings are shown in the following table.
RFID #
0
1
2
3
4
5
6
7
8
9
10
11
12
13
14
Switch
On
None
1
2
1
3
1
2
1
4
1
1
1
3
1
2
2
3
3
2
4
2
2
4
3
3
3
4
4
4

Generation II RF Control System –Operating, Installation & Technical Manual
RF Gen II System Technical Manual Rev02_12_10
15
Fitting the Power Module Circuit Board
The power board will need to be fitted if load cells are fitted. It is fitted into the power module.
Open the Power Module lid.
Remove the wire joining block.
Fit the circuit board with the supplied screws.
Attach the wires as noted on the board.
Remove white wire from Power Module to control module cable and install Red, Green and
Blue wires into Power Module circuit Board.
Fitting the Wheel Sensor
The wheel (proximity) sensor has to be adjusted halfway between the range of being
always on and always off. This is approximately 5mm between the end of the sensor and
the wheel plate.
Take care when running the cable that there is enough slack to allow the axle to fully
oscillate.
Approx. 5mm

Generation II RF Control System –Operating, Installation & Technical Manual
RF Gen II System Technical Manual Rev02_12_10
16
Recommended Load Cell Bolt Torque Settings
M20 - 280 ft/lbs or 380Nm
M24 - 490 ft/lbs or 660Nm
Fitting the Load Cells
Fit the studs to the load cell first before fitting the load cells to the machine using the bolts
provided.
Lower the top half of the wagon onto the studs.
Tighten the top nut then back off ½ turn.
Route the wiring through the pipe/brackets provided through to the junction box taking
care to keep the wiring tidy and away from moving objects.
Note: If installing PT brand load cells, there will be two extra blue and brown
wires. Connect the Sense +ve (brown) together with Excitation +ve (red) and
Sense –ve (blue) together with Excitation –ve (black).
Weight Module Connection
When fitting load cells or a wheel sensor, see below for fitting information about connecting
wires into the weight module.
Concave washer
Convex washer
Load cell
Stud and nut
Insert screw driver for top layer here
Top layer
Insert screw driver for bottom layer here
Bottom layer

Generation II RF Control System –Operating, Installation & Technical Manual
RF Gen II System Technical Manual Rev02_12_10
17
*** SETUP ***
Scale Damping Value
1.00
RANGE: 1-15
*** SETUP ***
Load Cell Type
5000.00kg
RANGE: 5000-10000
*** SETUP ***
Number of Load
Cells
4.00
RANGE: 0-6
*** SETUP ***
Load Cell Sens.
2.00mV/V
RANGE: 0-10
Setting System Parameters
Parameters are required to be set for the machine to function correctly.
Entering Configuration Screens
To enter set-up, press TARE/GROSS and ZERO together for 4 seconds or until the
set-up screen appears.
Press UP or DOWN to adjust the parameter.
Press MODE to move to the next configuration screen. It will save what is displayed
on the screen.
Press STOP to exit the configuration screens.
Scale Damping Value
The “Scale Damping Value”parameter is a weighting
value over which the weight is averaged. A higher
value will display a smoother weight display but won’t
react to weight changes as quickly.
The operator can press UP or DOWN to adjust this
value. Press MODE to continue.
Load Cell Type
The “Load Cell Type”parameter specifies the
maximum load for each individual load cell used on the
wagon.
The operator can press UP or DOWN to adjust this
value. Press MODE to continue.
Number of Load Cells
The “Number of Load Cells”parameter specifies the
total amount of load cells fitted to the machine. Enter 0
if no load cells are fitted.
The operator can press UP or DOWN to adjust this
value. Press MODE to continue.
Load Cell Sensitivity
The “Load Cell Sens.” parameter specifies sensitivity of
the load cells used on the wagon. The setting is in mV
per Volt. This means mV output per Volt of excitation.
This is a characteristic of the load cells used.
The operator can press UP or DOWN to adjust this
value. Press MODE to continue.

Generation II RF Control System –Operating, Installation & Technical Manual
RF Gen II System Technical Manual Rev02_12_10
18
*** SETUP ***
Scale Hysteresis
10.00kg
RANGE: 1-200
*** SETUP ***
Scale Increments
10.00kg
RANGE: 1-200
*** SETUP ***
Wheel Diameter
760.00mm
RANGE: 0-1400
*** SETUP ***
No. of Wheel Holes
15.00
RANGE: 0-50
*** SETUP ***
Max Valve PSI
2100.00psi
RANGE: 0-3000
*** SETUP ***
Wheel Sensor Fitted
YES
RANGE: 0-1
Scale Hysteresis
The “Scale Hysteresis” parameter specifies how much
a weight reading needs to change before the reading
on the screen will change.
The operator can press UP or DOWN to adjust this
value. Press MODE to continue.
Scale Increments
The “Scale Increments”parameter specifies minimum
scale increment displayed on the screen.
The operator can press UP or DOWN to adjust this
value. Press MODE to continue.
Maximum Valve Pressure
The ‘Max Valve PSI’ parameter sets the elevator load
sensing pressure. Reduce this value if the elevator
stalls too often. Ideally this should be set
approximately 200 –300 PSI below tractor relief
pressure.
The operator can press UP or DOWN to adjust this value. Press MODE to continue.
Wheel Sensor Fitted
The ‘Wheel Sensor Fitted’ parameter indicates if the
wheel sensor is fitted or not and displays appropriate
modes to suit.
The operator can press UP or DOWN to adjust this
value. Press MODE to continue.
Wheel Diameter
The “Wheel Diameter” parameter is used to calibrate
the wheel size on the machine.
The operator can press UP or DOWN to adjust this
value. Note: For accuracy, measure from the ground to
the centre of the hub (and double) when the machine is
half loaded. This will compensate for tyre pressure.
Press MODE to continue.
Number of Wheel Holes
The “Number of Wheel Holes” parameter is used to
calibrate the distance measurement for the number of
holes on the encoder disk used by the speed sensor.
The operator can press UP or DOWN to adjust this
value. Press MODE to continue.

Generation II RF Control System –Operating, Installation & Technical Manual
RF Gen II System Technical Manual Rev02_12_10
19
*** SETUP ***
Low Batt Level
11.50V
RANGE: 0-30
*** SETUP ***
Valve Fitted
YES
RANGE: 0-1
*** SETUP ***
Min Valve Setting
30.00
RANGE: 0-100
*** SETUP ***
Valve Ramp Up Time
0.00sec
RANGE: 0-10
*** SETUP ***
Valve Startup Dist.
85.00%
RANGE: 0-100
*** SETUP ***
Valve Ramp Up Time
0.00sec
RANGE: 0-10
Low Battery Level
The "Low Batt Level" parameter defines the minimum
battery voltage level at which the screen will switch
from displaying voltage to displaying “LOBAT”. This
function can be cancelled by setting the voltage to
0.00V.
The operator can press UP or DOWN to adjust this
value. Press MODE to continue.
Solenoid Valve Fitted
The ‘Valve Fitted’ parameter indicates if the solenoid
valve is fitted or not and displays appropriate modes to
suit.
The operator can press UP or DOWN to adjust this
value. Press MODE to continue.
Minimum Valve Setting
The "Min Valve Setting" parameter defines the
minimum valve opening percentage when in Distance
and Speed mode, while running. When stopped, the
valve will go to 0.
The operator can press UP or DOWN to adjust this
value. Press MODE to continue.
Valve Ramp Up Time
The ‘Valve Ramp Up Time’ parameter changes the
valve ramp up time.
The operator can press UP or DOWN to adjust this
value. Press MODE to continue.
Valve Ramp Down Time
The ‘Valve Ramp Down Time’ parameter changes the
valve ramp down time.
The operator can press UP or DOWN to adjust this
value. Press MODE to continue.
Valve Start-up for Distance Setting
The “Valve Startup Dist.” parameter is the initial valve
setting to use when the machine is started in Distance
mode.
The operator can press UP or DOWN to adjust this
value. Press MODE to continue.

Generation II RF Control System –Operating, Installation & Technical Manual
RF Gen II System Technical Manual Rev02_12_10
20
*** SETUP ***
Speed Mode Max
Speed
10.00km/h
RANGE: 1-20
*** SETUP ***
Speed Mode Min
Speed
1.00km/h
RANGE: 0-5
*** SETUP ***
Speed Mode Strt.
Time
1.00sec
RANGE: 0-20
*** SETUP ***
Dist. Before Finish
1.00m
RANGE: 0-10
*** SETUP ***
Shut Down Timer
20.00min
RANGE: 1-60
Minimum Speed while in Speed Mode
The "Speed Mode Min Speed" parameter is only used
for Speed mode. It defines the minimum speed the
machine must be moving before the machine begins to
operate. This function is adjustable between 0 and 5
km/h, with increments of 0.1km/h.
The operator can press UP or DOWN to adjust this
value. Press MODE to continue.
Maximum Speed while in Speed Mode
The "Speed Mode Max Speed" parameter is only used
while in Speed mode. It defines the theoretical
maximum speed the machine will reach at which point
the machine will be operating at maximum feed rate.
The lower this is set, the more aggressive the machine
will operate. This function is adjustable between 1 and
20 km/h with increments of 1km/h.
Any speed over this parameter will cause the machine to run at the percentage setting on the
display.
The operator can press UP or DOWN to adjust this value. Press MODE to continue.
Speed Mode Start-up Time
The "Speed Mode Strt. Time" parameter is only used
while in Speed mode. It defines the length of time the
machine must be moving above the minimum speed
before it begins its usual function. This function is
adjustable between 1 and 20 seconds with increments
of 1 second.
The operator can press UP or DOWN to adjust this value. Press MODE to continue.
Distance before Finish
The "Dist. Before Finish" parameter is only used while
in Distance mode. It defines the length before the end
of the run at which the valve controller will return to
zero hence stopping the floor operation and clearing
the machine. When set on zero, the machine will
continue functioning until the distance reads zero. This
function is adjustable between 0 and 10 metres with increments of 0.5 m.
The operator can press UP or DOWN to adjust this value. Press MODE to continue.
Shut Down Timer
The shut down timer controls the time that the
Controller will stay powered up while running on
battery power.
The operator can press UP or DOWN to adjust this
value. Press MODE to continue.
This manual suits for next models
1
Table of contents
Popular Control System manuals by other brands

Böhnke + Partner
Böhnke + Partner bp308 installation manual
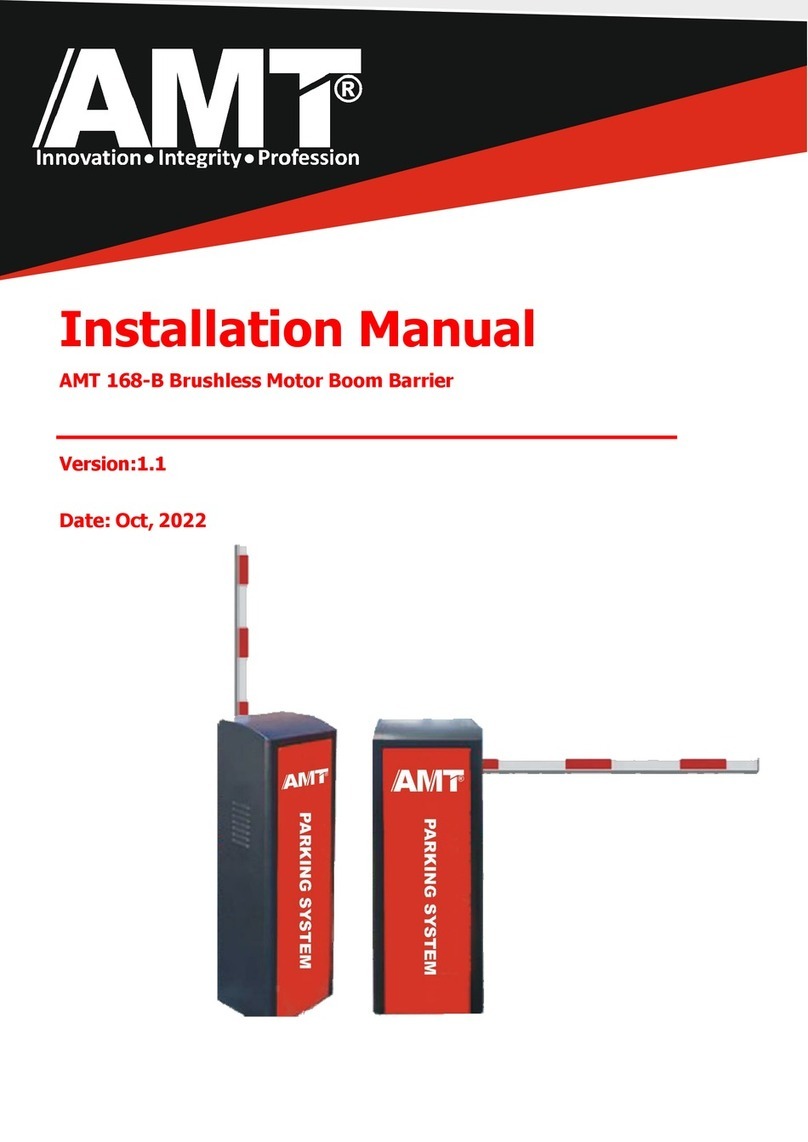
AMT
AMT 168-B installation manual
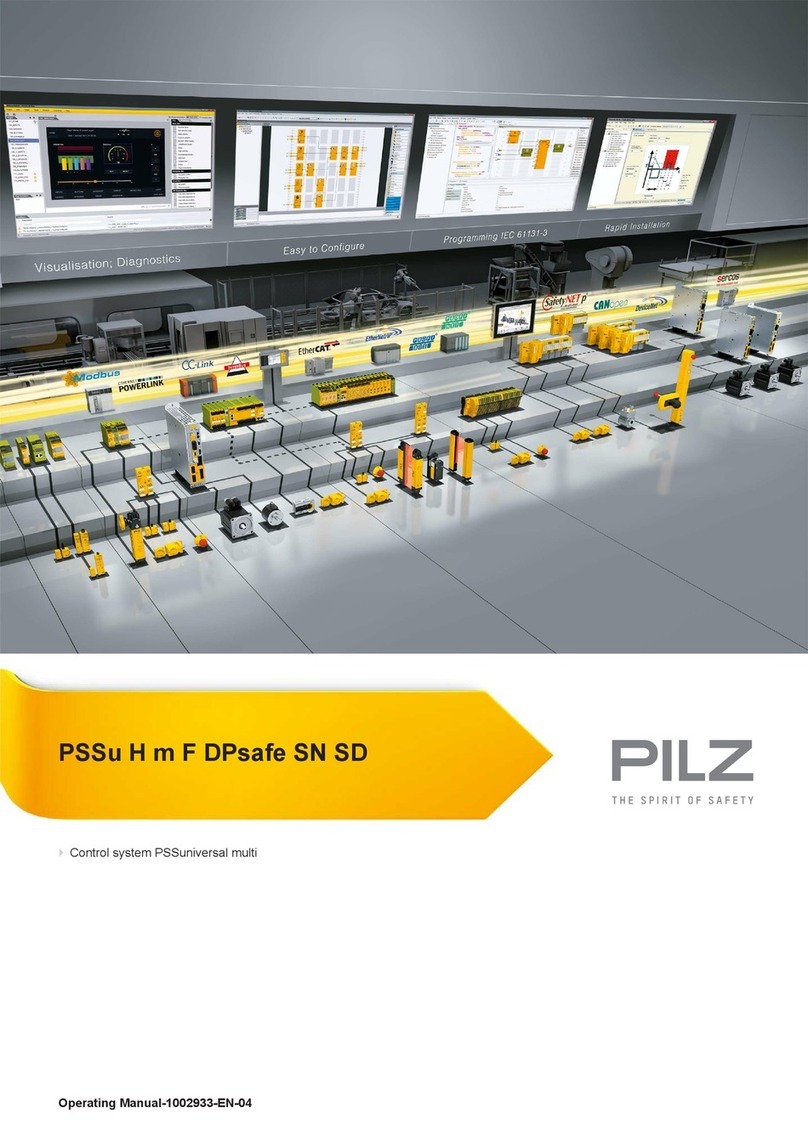
Pilz
Pilz PSSuniversal multi PSSu H m F DPsafe SN SD operating manual
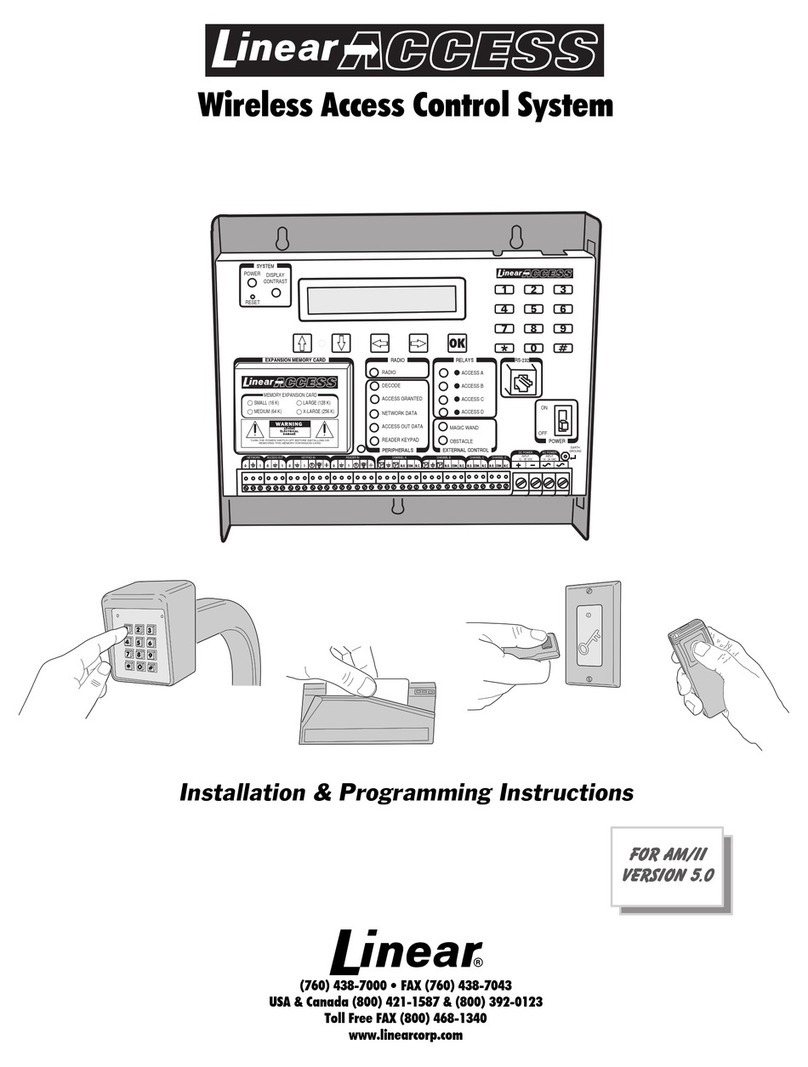
Linear Access
Linear Access AM/II Installation and programming instructions
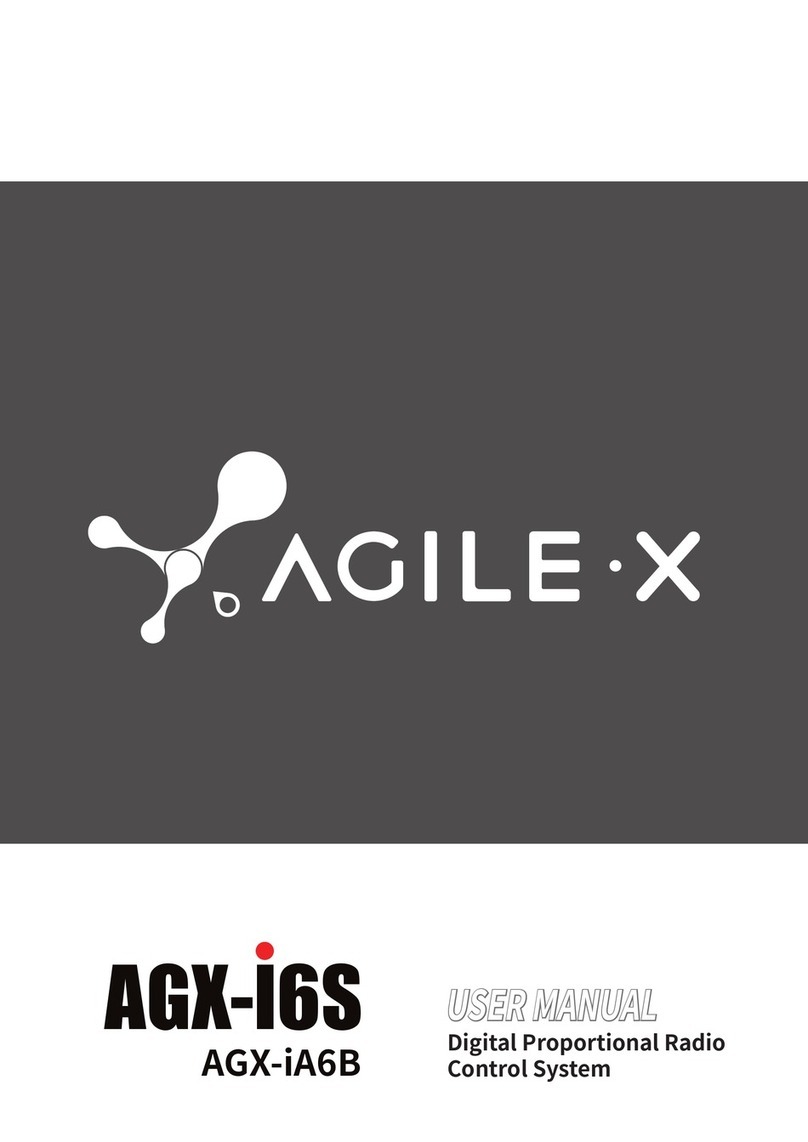
AgileX
AgileX AGX-l6S user manual
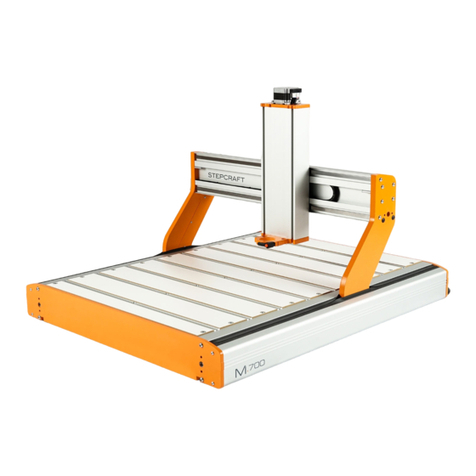
STEPCRAFT
STEPCRAFT M Series operating manual