SIP 07196 User manual

16
Ref: 270612
FOR HELP OR ADVICE ON THIS PRODUCT PLEASE CONTACT YOUR DISTRIBUTOR,
OR SIP DIRECTLY ON:
TEL: 01509500400
www.sip-group.com
Please dispose of packaging for the product in a responsible
manner. It is suitable for recycling. Help to protect the
environment, take the packaging to the local amenity tip and
place into the appropriate recycling bin.
1
3/8” Reversible Drill
Please read and fully understand the instructions in this manual
before operation. Keep this manual safe for future reference.
07196

2
15
Declaration of Conformity
We
SIP (Industrial Products) Ltd
Gelders Hall Road
Shepshed
Loughborough
Leicestershire
LE12 9NH
England
As the manufacturer's authorised representative within the EC
declare that the
3/8” Reversible Air Drill - SIP Pt. No. 07196
Suppliers Part No. RP7101
Conforms to the requirements of the following directive(s), as indicated.
2006/42/EC Machinery Directive
Signed: …………………………………...
Mr P. Ippaso - Director - SIP (Industrial Products) Ltd
Date: 27/06/2012.
DECLARATION OF CONFORMITY

14
Ref. No. Description SIP Part No. Ref. No. Description SIP Part No.
1. Housing AI05-00084 18. End Plate AI05-00101
2. Bolt 3×24 AI05-00085 19. Cylinder AI05-00102
3. Exhaust Deflector AI05-00086 20. Rotor vein AI05-00103
4. Air Inlet AI05-00087 21. Cylinder pin AI05-00104
5. Air inlet cover AI05-00088 22. Rotor AI05-00105
6. Pin AI05-00089 23. Front Plate AI05-00106
7. O-ring 4×2 AI05-00090 24. Washer AI05-00107
8. O-ring 4×1.1 AI05-00091 25. Gear housing AI05-00108
9. O-ring 12×3 AI05-00092 26. Idle Gear AI05-00109
10. Bushing AI05-00093 27. Pin AI05-00110
11. Reverse lever AI05-00094 28. Gear shaft AI05-00111
12. O-ring 11.5×1.8 AI05-00095 29. Bearing AI05-00112
13. Spring AI05-00096 30. Front housing cover AI05-00113
14. Trigger AI05-00097 31. Washer AI05-00114
15. Bolt M4×8 AI05-00098 32. Chuck 3/8” AI05-00115
16. Gasket AI05-00099 33. Bolt M5×16 AI05-00116
17. Bearing AI05-00100
PARTS LIST
3

4
SAFETY INSTRUCTIONS
IMPORTANT: Please read the following instructions carefully, failure to do so could lead
to serious personal injury and / or damage to the drill.
When using your drill, basic safety precautions should always be followed to reduce
the risk of personal injury and / or damage to the drill.
Read all of these instructions before operating the drill and save this user manual for
future reference.
The drill should not be modified or used for any application other than that for which it
was designed.
This air tool is designed to be used as a hand held, hand controlled tool for drilling and
similar applications.
If you are unsure of its relative applications do not hesitate to contact us and we will
be more than happy to advise you.
Before operating the drill always check no parts are broken and that no parts are miss-
ing.
Always operate the drill safely and correctly.
KNOW YOUR DRILL: Read and understand the owner's manual and labels affixed to
the drill. Learn its applications and limitations, as well as the potential hazards specific
to it.
KEEP CHILDREN AND UNTRAINED PERSONNEL AWAY FROM THE WORK AREA: All visitors
should be kept at a safe distance from the work area; never allow untrained persons
to operate the drill. .
STAY ALERT: Always watch what you are doing and use common sense.
HAVE YOUR DRILL REPAIRED BY A QUALIFIED PERSON: The drill is in accordance with the
relevant safety requirements. Repairs should only be carried out by qualified persons
using original spare parts, otherwise this may result in considerable danger to the user
and void the warranty.
DANGER! Check that the drill is in sound condition and good working order; Take im-
mediate action to repair or replace damaged parts.
DO NOT dismantle or tamper with the drill, as this may be dangerous and will invali-
date the warranty.
If a problem with the drill is experienced or suspected stop using the drill immediately
and contact your distributor for repair.
Regularly inspect and lubricate the drill, ensuring that it is in good working order and
condition.
Always ensure that the work area is clean and tidy, free from unrelated materials and
has adequate lighting.
Clean and stow the drill correctly.
Failure to follow the warnings in this manual, may result in personal injury and/or prop-
erty damage.
DO ensure that only compressed air is used to supply the air tool.
13
EXPLODED DRAWING

12
PROBLEMS POSSIBLE CAUSES REMEDIES
Tool runs at normal speed
but loses under load
Motor parts worn.
Cam clutch worn or sticking
due to lack of lubricant.
Lubricating clutch housing.
Check for excess clutch oil. Clutch cases
need only be half full. Overfilling can cause
drag on high speed clutch parts, i.e. a
typical oiled/lubricated wrench requires 1/2
ounce of oil. GREASE LUBRICATED:NOTE:
Heat usually indicates insufficient grease in
chamber. Severe operating conditions
may require more frequent lubrication.
Tool runs slowly. Air flows
slightly from exhaust
Motor parts jammed with
dirt particles
Power regulator in closed
position
Air flow blocked by dirt.
Check air inlet filter for blockage.
Pour air tool lubricating oil into air inlet as
per instructions.
Operate tool in short bursts quickly reversing
rotation back and forth where applicable.
Repeat above as needed. If this fails return
to service centre.
Tools will not run. Air flows
freely from exhaust
One or more motor vanes
stuck due to material build
up.
Pour air tool lubricating tool into air inlet.
Operate tool in short bursts of forward and/
or reverse rotation where applicable.
Tap motor housing gently with plastic mal-
let.
Disconnect supply. Free motor by rotating
drive shank manually where applicable
If tool remains jammed return to service
centre.
Tool will not shut off
‘O’ rings throttle valve dis-
lodged from seat inlet
valve.
Replace ‘O’ ring or return to service centre.
TROUBLESHOOTING…. cont
Note: Repairs should be carried out by a qualified person.
5
The compressed air supply MUST be at a suitable regulated pressure. Pipe work, reg-
ulators, hoses, isolation valves and connection devices MUST be suitable for the in-
tended application correctly installed and maintained in good condition by a com-
petent person.
Appropriate Personal protective equipment MUST be worn and MUST be designed to
protect against all hazards created. Severe permanent injury can result from using
inappropriate or insufficient protective equipment - Eyes in particular are at risk.
Long hair MUST be tied back; loose clothing MUST NOT be worn. There is a severe risk
of these being drawn in or trapped by the moving parts of the air tool.
Open or damaged compressed air lines present a significant ‘whip’ hazard; isolate
the problem hose from the air supply and repair / replace the hose immediately.
This air tool is electrically conductive DO NOT allow them to come into contact with
any source of electrical supply.
After use wait for the air tool to STOP completely before putting it aside.
When putting the air tool aside you MUST ensure that it placed in a stable position.
To avoid inadvertent operation DO NOT place the air tool where it can be knocked
or moved accidentally either directly or by the air connection hose.
If the air tool is not required or the air supply is interrupted, disconnect the air tool
from the air supply and place in secure storage to prevent unauthorised use.
Ensure the air valve (or trigger) is in the “off” position before connecting to the air sup-
ply.
Disconnect the drill from the air supply before making adjustments, changing drill
bits etc. and before servicing the tool.
Always keep your air tool clean and lubricated. Daily lubrication is essential to avoid
internal corrosion and possible failure.
Do not overload the tool. Allow the tool to operate at its optimum speed for maxi-
mum efficiency.
Do not increase the air pressure above the manufacturers recommended level, as
excessive pressure can cause the tool casing to split. This can also create excessive
wear on moving parts and possible failure.
Always ensure that the work-piece is firmly secured leaving both hands free to con-
trol the drill.
Always wear safety goggles or glasses during operation.
Do not wear watches, rings bracelets or loose clothing when using air tools.
Use as light weight a hose as possible from the tool to the wall or compressor cou-
pling.
In the interests of safety and possible damage to the machine/operator, always en-
sure that the drill has stopped before putting it down after use.
Always ensure that the accessories such as drill bits are rated / designed for use with
this drill as well as the required application, and are correctly and securely fastened
before connecting the tool to the air supply.
Do not carry or move the air drill by its air hose.
SAFETY INSTRUCTIONS….cont

6
SAFETY INSTRUCTIONS….cont
Always wear eye protection when using or maintaining any air tool.
We recommend wearing ear protection - particularly during extend-
ed periods of operation.
We recommend wearing a face mask or respiratory equipment when
using any air tool; particularly during sanding, grinding, sawing or other
operations likely to cause airborne particles.
CAUTION: The warnings and cautions mentioned in this user manual can not
cover all possible conditions and situations that may occur. It must be under-
stood by the operator that common sense and caution are factors which can-
not be built into this product, but must be applied.
3/8” Reversible Air Drill Instruction Manual Quick Coupler (Euro type)
Small Bottle of Oil Chuck Key
CONTENTS & ACCESSORIES
Note: If any of the above are missing or damaged, contact your distributor
immediately.
Understand the operating environment; Before each use the operator should assess,
understand and where possible reduce the specific risks and dangers associated
with the operating environment. Bystanders should also be made aware of any risks
associated with the operating environment.
11
MAINTENANCE
Disconnect the air tool from the air supply before changing accessories, servicing
or performing maintenance. Replace or repair damaged parts. Use genuine parts
only. Non-authorised parts may be dangerous and will invalidate the warranty.
DO NOT use the tool if it is, or has parts that are worn, damaged or missing; re-
move from service and have the parts repaired / replaced using original spare
parts.
Ensure that the air tool is lubricated daily with a few drops of air tool oil dripped into
the air inlet.
Clean the air tool after each use.
Check hose and fittings for wear or damage before each use.
Drain the air tank / receiver of the compressor daily; Water in the air line will dam-
age the drill.
In the event that it becomes necessary to store the tool for an extended period of
time (overnight, weekend, etc.), it should receive a generous amount of lubrication
at that time. The tool should be run for approximately 30 seconds to ensure oil has
been evenly distributed throughout the tool.
The tool should be stored in a clean and dry environment.
Note: Never start the drill with the bit touching the work-piece. Allow the drill
to reach full speed before starting the drilling (or similar) operation.
OPERATING INSTRUCTIONS….cont
TROUBLESHOOTING
The following form lists the common operating issues with problems and solutions.
Please read the form carefully and follow it.
If any of the following symptoms occurs during your operation, stop using the
tool immediately, or serious personal injury could result. Only a qualified person
or an authorised service centre should perform repairs of the tool. Disconnect
from the air supply before attempting repairs or adjustments. When replacing O
-rings etc. lubricate with air tool oil before assembly.

10
amounts of oil should be avoided.
In the event that it becomes necessary to store the tool for an extended period of
time (overnight, weekend, etc.), it should receive a generous amount of lubrication
at that time. The tool should be run for approximately 30 seconds to ensure oil has
been evenly distributed throughout the tool. The tool should be stored in a clean and
dry environment.
It is most important that the tool be properly lubricated by keeping the air line lubri-
cator filled and correctly adjusted. Without proper lubrication the tool will not work
properly and parts will wear prematurely.
Use the proper lubricant in the air line lubricator. The lubricator should be of low air
flow or changing air flow type, and should be kept filled to the correct level. Use only
recommended lubricants, specially made for pneumatic applications. Substitutes
may
OPERATING INSTRUCTIONS….cont
CAUTION: If a filter/regulator/lubricator is not installed on the air system, air oper-
ated tools should be lubricated at least once a day or after 2 hours work with 2
to 6 drops of oil, depending on the work environment, directly through the
male fitting in the tool housing.
FITTING A DRILL BIT (or similar)
Open the chuck (1) as far as is needed to fit the required drill bit (or similar) by using
the supplied chuck key; Insert the key into the chuck key hole (2) and turn anti-
clockwise.
Slide the bit into the chuck (1).
Secure the bit by turning the chuck key firmly clockwise.
OPERATING THE DRILL
Once the bit is fitted and secure:
Connect the drill to the air supply via the air inlet (5).
Press the air trigger (6) and the drill will operate.
Release the air trigger (6) and the drill will stop.
7
GETTING TO KNOW YOUR AIR DRILL
Ref. No. Description Ref. No. Description
1. Chuck 4. Main Handle
2. Chuck Key Hole 5. Air Inlet
3. Forward / Reverse Lever 6. Trigger
2
1
3
4
5
6

8
Guarantee:
This SIP air tool is covered by a 12 month parts and labour warranty covering failure
due to manufacturers defects. This does not cover failure due to misuse or operating
the machine outside the scope of this manual.
In the unlikely event of warranty claims, contact your distributor as soon as possible.
Proof of purchase will be required before any warranty can be honoured.
Failure to lubricate your air tool will shorten its working life and reduce performance.
Also note, the warranty does not cover rusting air tools and tools that failed due to the
lack of lubrication.
TECHNICAL SPECIFICATIONS
*Tested according to ISO 15744: 3 dB uncertainty
**Tested according to ISO 28927-5: 0.74 m/s2 uncertainty
SIP Code
07196
Drilling Capacity 3/8” (10mm)
No Load Speed 1,800 rpm
Average Air Consumption 3.3 cfm (106 l/min)
Operating Pressure 6.3 bar (90 psi)
Air Inlet 1/4” bsp
Sound Pressure (LpA) * 86.5 dB(A)
Sound Power (LwA) * 97.5 dB(A)
Vibration ** 2.49m/s2
GUARANTEE
Note: Proof of purchase will be required before any warranty can be hon-
oured.
9
Tool
Compressor
Quick Connector Quick Connector
Quick Coupler Quick CouplerAir Hose
Regulator
Lubricator
Filter
Cut Off Valve
Fig. 1
OPERATING INSTRUCTIONS
This 3/8” reversible air drill is designed with a durable lightweight aluminium housing. It
has a variable speed trigger for precise start-up and control, handle mounted exhaust
to reduce noise and direct air flow away from the operators face. It is the ergonomic
choice for drilling, honing and hole sawing etc.
1. Ensure the air drill trigger (6) is not depressed before connecting to the air supply.
2. You will require an air pressure of 90psi, and an air flow according to specification.
3. WARNING! Ensure the air supply is clean and does not exceed 90psi while operat-
ing the drill. Too high an air pressure and unclean air will shorten the product life
due to excessive wear, and may be dangerous causing damage and/or personal
injury.
4. Drain the air tank daily. Water in the air line will damage the drill.
5. Recommended hook-up procedure is shown in fig 1.
6. Line pressure should be increased to compensate for unusually long air hoses (over
8 metres). The minimum hose diameter should be 1/4” I.D. and fittings must have
the same inside dimensions.
7. Keep hose away from heat, oil and sharp edges. Check hose for wear, and make
certain that all connections are air tight secure.
LUBRICATION
An automatic in-line filter-regulator-lubricator is recommended (Fig1) as it increases
tool life and keeps the tool in sustained operation. The in-line lubricator should be
regularly checked and filled with air tool oil.
Proper adjustment of the in-line lubricator is performed by placing a sheet of paper
next to the exhaust ports and holding the throttle open approximately 30 seconds.
The lubricator is properly set when a light stain of oil collects on the paper. Excessive
DESCRIPTION
AIR SUPPLY
Table of contents
Other SIP Drill manuals
Popular Drill manuals by other brands
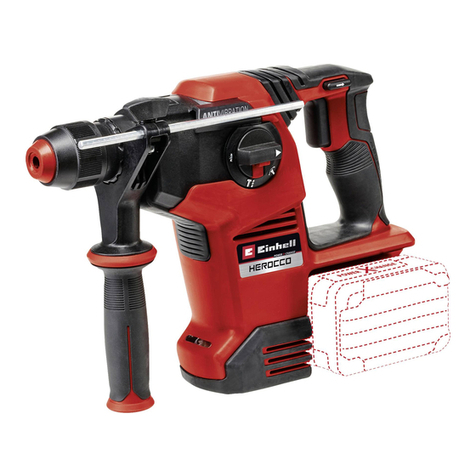
EINHELL
EINHELL HEROCCO 36/28 Original operating instructions
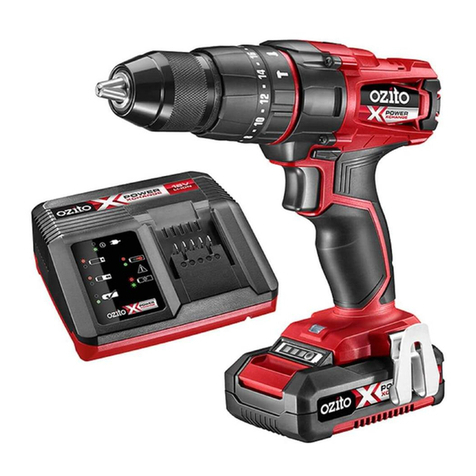
Ozito
Ozito PXHDK-350 instruction manual
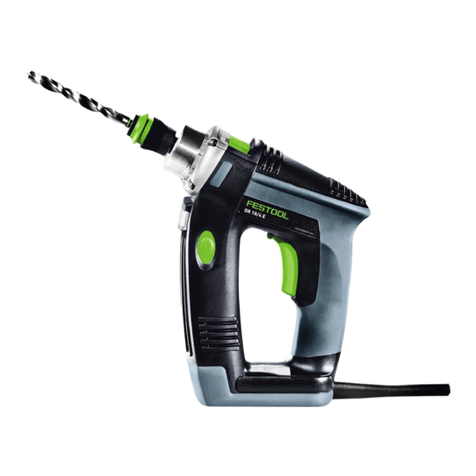
Festool
Festool DR 18/4 E Original operating manual

Dynabrade
Dynabrade 55583 Safety, operation and maintenance
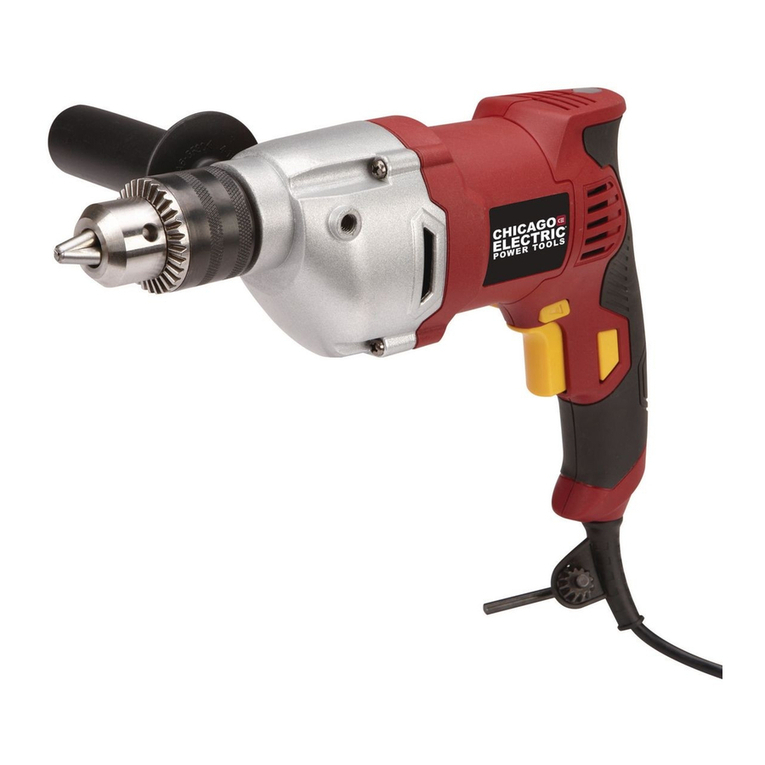
Chicago Electric
Chicago Electric 1/2" variable Speed Reversible HEAVY DUTY DRILL... Owner's manual & safety instructions

Craftsman
Craftsman 125.DD20A Operator's manual