SIP 03696 User manual

28
FOR HELP OR ADVICE ON THIS PRODUCT PLEASE CONTACT YOUR DISTRIBUTOR,
OR SIP DIRECTLY ON:
TEL: 01509500400
EMAIL: sales@sip-group.com or technical@sip-group.com
www.sip-group.com
Ref: 121216
Please dispose of packaging for the product in a responsible
manner. It is suitable for recycling. Help to protect the
environment, take the packaging to the local amenity tip and
place into the appropriate recycling bin.
Please read and fully understand the instructions in this manual
before operation. Keep this manual safe for future reference.
03696
75 Ton Shop Press
(Pneumatic/Hydraulic)

2
27
DECLARATION OF CONFORMITY
Declaration of Conformity
We
SIP (Industrial Products) Ltd
Gelders Hall Road
Shepshed
Loughborough
Leicestershire
LE12 9NH
England
As the manufacturer's authorised representative within the EC
declare that the
75 Ton Shop Press (Pneumatic/Hydraulic) - SIP Part No. 03696
Conforms to the requirements of the following directive(s), as indicated.
2006/42/EC Machinery Directive
Signed: …………………………………...
Mr P. Ippaso - Managing Director - SIP (Industrial Products) Ltd
Date: 02/09/2016.
And the relevant standard(s), including:
EN ISO 12100:2010
EN 1494:2000+A1:2008

26
NOTES
3
CONTENTS
Page No. Description
4. Safety Symbols Used Throughout This Manual
4. Safety Instructions
6. Guarantee
7. Contents and Accessories
8. Technical Specifications
9. Getting to Know Your Shop press
10. Assembly Instructions
14. Operating Instructions
15. Maintenance
16. Troubleshooting
17. Exploded drawing - Main
18. Parts List - Main
20. Exploded Drawing - Pump
21. Parts List - Pump
22. Exploded Drawing - Ram
23. Parts List - Ram
27. Declaration of Conformity

4
SAFETY SYMBOLS USED THROUGHOUT THIS MANUAL
When using your Shop press, basic safety precautions should always be followed to
reduce the risk of personal injury and / or damage to the Shop press or load.
Read all of these instructions before operating the Shop press and save this user man-
ual for future reference.
The Shop press should not be modified or used for any application other than that for
which it was designed.
It was designed for the removal or installation of bearings, universal joints, pulleys, etc.
If you are unsure of its relative applications do not hesitate to contact us and we will
be more than happy to advise you.
Before operating the Shop press always check no parts are broken, that no oil is leak-
ing and that no parts are missing.
Always operate the Shop press safely and correctly.
KNOW YOUR SHOP PRESS: Read and understand the owner's manual and labels af-
fixed to the Shop press. Learn its applications and limitations, as well as the potential
hazards specific to it.
KEEP CHILDREN AND UNTRAINED PERSONNEL AWAY FROM THE WORK AREA: All visitors
should be kept at a safe distance from the work area; never allow untrained persons
to operate the Shop press. .
STAY ALERT: Always watch what you are doing and use common sense.
NEVER LEAVE THE SHOP PRESS UNATTENDED: When in use / under load.
HAVE YOUR SHOP PRESS REPAIRED BY A QUALIFIED PERSON: The Shop press is in ac-
cordance with the relevant safety requirements. Repairs should only be carried out by
qualified persons using original spare parts, otherwise this may result in considerable
danger to the user and void the warranty.
DANGER! Check that the shop press is in sound condition and good working order;
Take immediate action to repair or replace damaged parts.
SAFETY INSTRUCTIONS
Danger / Caution: Indicates risk of personal injury and/or the possibility of
damage.
IMPORTANT: Please read the following instructions carefully, failure to do
so could lead to serious personal injury and / or damage to the Shop
press.
Note: Supplementary information.
25
NOTES

24
NOTES
5
SAFETY INSTRUCTIONS….cont
WARNING! Only operate on a level and stable surface and never use on soft ground
where the Shop press is likely to “sink” whilst in operation.
Ensure that the shop press is securely bolted to the ground before putting into service.
NEVER STAND ON THE SHOP PRESS: The Shop press is not designed for this purpose.
DO NOT dismantle or tamper with the Shop press, as this may be dangerous and will
invalidate the warranty.
If a problem with the Shop press is experienced or suspected stop using the Shop
press immediately and contact your distributor for repair.
Do not attempt to press a load that exceeds the rated capacity of the shop press.
Never work under the Shop press whilst in operation.
Regularly inspect, clean and lubricate the Shop press, ensuring that it is in good
working order and condition.
Always ensure that the work area is clean and tidy, free from unrelated materials and
has adequate lighting.
Keep hands, limbs etc. clear of moving parts during operation of the ram.
DO NOT top-up the Shop press with brake fluid, or other oil types; use hydraulic oil
only.
DO NOT adjust the safety overload valves.
Ensure that there are no persons or obstructions beneath the Shop press whilst its in
operation.
Clean the Shop press correctly, with the ram in the retracted position, DO NOT leave
it extended.
Failure to follow the warnings in this manual, may result in personal injury and/or
property damage.
Prior to applying the load, be sure that the hydraulic ram collar threads are fully en-
gaged to the head assembly.
Components of this Shop press are specially designed to withstand the rated ca-
pacity. Do not substitute bolts, pins, or any other components.
Always press the load on the centre of the ram. Offset loads can damage the ram,
and may cause a workpiece to eject.
Before operating, check for signs of cracked welds, bent bed support pins, loose or
missing bolts, or any other structural damage. Do not operate if any of these condi-
tions exist. Have repairs made only by authorised service centre.
Remove all loads and arbor plates from the bed before attempting to adjust the
bed height.
Press only on the workpiece supported by the bed and arbor plates.
When using accessories, such as arbor plates, be sure that they are centered on
the bed, and are in full contact with the bed.
Parts being pressed may splinter, shatter or eject from the press. Due to various ap-
plications, it is your responsibility to always use adequate guards, such as eye pro-
tection and heavy protective clothing, when operating this Shop press.
Do not stand in front of work area where the load is applied.

6
SAFETY INSTRUCTIONS….cont
If the Shop press appears to be damaged in any way, is found to be badly worn, or
operates abnormally IT SHOULD BE REMOVED FROM SERVICE until necessary repairs
are made by an authorised service centre.
DO NOT use the Shop press to compress springs or any other item that could disen-
gage and cause a potential hazard.
Understand the operating environment; Before each use the operator should assess,
understand and where possible reduce the specific risks and dangers associated
with the operating environment. Bystanders should also be made aware of any risks
associated with the operating environment.
CAUTION: The warnings and cautions mentioned in this user manual can not cover all
possible conditions and situations that may occur. It must be understood by the oper-
ator that common sense and caution are factors which cannot be built into this prod-
uct, but must be applied.
Danger / Caution: Never exceed the maximum capacity of 75 tons, over-
loading can lead to personal injury or damage to the Shop press.
This SIP Shop press is covered by a 12 month parts and labour warranty covering fail-
ure due to manufacturers defects. This does not cover failure due to misuse or operat-
ing the Shop press outside the scope of this manual - any claims deemed to be out-
side the scope of the warranty may be subject to charges Including, but not limited to
parts, labour and carriage costs.
This guarantee does not cover consumables such as oil, arbor plates etc.
In the unlikely event of warranty claims, contact your distributor as soon as possible.
GUARANTEE
Note: Proof of purchase will be required before any warranty can be hon-
oured.
23
Ref. No. Description Ref. No. Description
R01. big round nut R14. washer
R02. block R15. retainer ring
R03. o ring R16. o ring
R04. o ring R17. nut
R05. plug R18. spring
R06. screw R19. ram
R07. copper ring R20. pin
R08. piston rod R21. screw
R09. washer R22. connector
R10. o ring R23. steel ball
R11. piston head R24. spring
R12. valve core R25. plug
R13. screw R26. connector
PARTS LIST - RAM

22
EXPLODED DRAWING - RAM
7
CONTENTS & ACCESSORIES
Note: If any of the above are missing or damaged, contact your distributor
immediately.
1. Arbor plate x2 5. Air Pedal
2. Leg / Leg Supports x2 (c/w Fixings) 6. Bed Pin x4 inc. Clips x8
3. Manometer N/A. Frame (c/w ram/winch/pump/bed)
4. Pump Handle N/A. Instruction Manual
1
3
2
4
6
5

8
TECHNICAL SPECIFICATIONS
A. 160mm H. 1840mm
B. 880mm W. 1150
C. 250mm W1. 800mm
E. 105mm L. 800mm
F. 75mm Total Height. 1940mm
G. 280mm Operating Air Pressure. 7.5-8.5 bar
21
PARTS LIST - PUMP
Ref. No. Description Ref. No. Description
P1. breath screw P30. copper washer
P2. oil tank P31. o ring
P3. connector P32. hand pump core
P4. lock washer P33. u ring
P5. screw P34. o ring
P6. steel ball P35. washer
P7. spring P36. small pump core
P8. copper ring P37. washer
P9. screw P38. o ring
P10. limit P39. big pump core
P11. lock washer P40. pin
P12. screw P41. retainer ring
P13. washer P42. pin
P14. valve base P43. handle socket
P15. o ring P44. copper washer
P16. release valve P45. control valve core
P17. steel ball P46. o ring
P18. base for steel ball P47. washer
P19. spring P48. spring
P20. screw P49. pump
P21. o ring P50. screw
P22. screw P51. steel ball
P23. cap P52. washer
P24. steel ball P53. steel ball
P25. spring P54. steel ball
P26. spring base P55. screw
P27. copper washer P56. steel ball
P28. o ring P57. screw
P29. air pump P58. screw

20
EXPLODED DRAWING - PUMP
9
GETTING TO KNOW YOUR SHOP PRESS
Ref. No Description Ref. No Description
1. Leg 8. Manometer (gauge)
2. Leg Supports 9. Air Vent / Oil Filler Screw
3. Bed Pin 10. Hydraulic Pump
4. Bed 11. Release Valve
5. Bed Winch 12. Air Motor
6. Arbor Plate 13. Pump Handle
7. Hydraulic Ram 14. Air Pedal (Valve)
4
6
7
1
2
8
10
11
13
1
2
3
3
9
12
14
3
5

10
ASSEMBLY INSTRUCTIONS
Connect the leg (1) to either the left or right post by using the bolts (2), washers (6),
spring washers (5) and nuts (4), do not tighten fully just yet.
Connect both leg supports (3) to the post and leg, by using bolts, washers, spring
washers and nuts.
Repeat the process for the opposite post.
Ensure everything is level, then proceed to tighten all the bolts/nuts.
FITTING THE LEGS
FITTING THE GAUGE
Caution: Due to the weight of the shop press; Correct lifting equipment
should be used during assembly.
Fit the nylon seal (72) into gauge fitting (51), then fit the pressure gauge (50) to
the fitting and tighten fully.
Nylon Seal
Gauge Fitting Gauge Fitting
Gauge
19
PARTS LIST - MAIN….cont
Ref. No. Description Ref. No. Description
59. air inlet hose 68. handle grip
60. plug 69. steel cable
61. air valve 70. steel cable
62. wire protect cover 71. connector
63. steel ball 72. Nylon Seal
64. handle 73. screw
65. air inlet hose 74. connector
66. bolt 75. air hose connector
67. flat washer 76. spring

18
PARTS LIST - MAIN
Ref. No. Description Ref. No. Description
1. foot 30. pin
2. bolt 31. working table
3. support bar 32. steel block
4. nut 33. screw
5. lock washer 34. spring
6. flat washer 35. roller wheel
7. pin 36. cover
8. retainer ring 37. cover
9. big roller wheel 38. beam
10. cover 1 39. bearing
11. cover 2 40. retainer ring
12. hand winch 41. spring
13. fix plate 42. ram plate
14. bolt 43. frame
15. flat washer 44. lifting beam
16. lock washer 45. bolt
17. nut 46. ram
18. pin 47. screw
19. retainer ring 48. screw
20. bushing 49. adaptor
21. bushing assembly 50. pressure gauge
22. nut 51. gauge connector
23. lock washer 52. nut
24. flat washer 53. pump
25. retainer ring 54. bolt
26. roller wheel 55. o ring
27. cover 56. hose
28. cover 57. hose
29. screw 58. PU hose
11
Note: Ensure that the gauge is tight against the fitting so that it will not leak
oil from the connection.
Attach the gauge fitting to the upper cross beam and secure by fully tightening
the nut (52).
ASSEMBLY INSTRUCTIONS….cont
Nut Gauge Fitting
Gauge
FITTING THE PUMP
Fit the pump assembly (53) to frame by using bolts (54) and washers (15) and
fully tighten to secure.
Remove the transit bung from the shortest hose.
Ensure that an o-ring is fitted to the gauge fitting.
Fit the hose onto the gauge fitting and tighten to fully secure.
Follow these instructions to fit the longer hose from the top of the ram to the
fitting next to the gauge hose on the pump..
Transit Bung
Hose Gauge Fitting
O-Ring
Note: before assembly open the bleed valve on top of the pump.

12
ASSEMBLY INSTRUCTIONS….cont
Note: Take care when removing the transit bungs as there is oil in the sys-
tem that could leak if the hose is not handled carefully.
Remove the nut from the air fitting on top of the pump.
Locate the air pipe from the ram unit.
Fit the nut over the air pipe.
Push the pipe over the fitting on top of the ram and tighten the nut to secure.
Nut
Air Fitting
Handle
Handle Bracket
Air Motor
Air Pipe
Place some thread seal, or similar around the threads at the end of the foot
pedal air pipe.
Fit the pipe to the bottom of the air motor and fully tighten to secure.
Fit the handle into the handle bracket and use the bolt to secure in place.
17
EXPLODED DIAGRAM - MAIN

16
TROUBLESHOOTING
The following form lists the common operating issues with problems and solutions.
Please read the form carefully and follow it.
If any of the following symptoms occurs during your operation, stop using the Shop press immediately, or
serious personal injury could result. Only a qualified person or an authorised service centre should perform
repairs on the Shop press. Disconnect from the air supply before attempting repairs or adjustments. When
replacing parts etc.
Note: Repairs should be carried out by a qualified person.
FAULT POSSIBLE CAUSES POSSIBLE REMEDIES
Loses pressure under load.
Release valve is open.
Pump or piston fault.
Close release valve.
Replace pump.
Pump feels spongy during pumping, or
lever has lost stroke.
Pump low on oil.
Air trapped in pump.
Pump or ram fault.
Top up with oil.
Bleed air out of system.
Replace pump/ram.
Ram is weak or does not reach rated
pressing capacity.
Pump low on oil.
Air trapped in pump.
Release valve is open.
Pump or piston fault.
Top up with oil.
Bleed air out of system.
Close release valve.
Replace pump.
13
ASSEMBLY INSTRUCTIONS….cont
FITTING THE WINCH
Move the hand winch (12) to the outside of the post, then use bolts (02), wash-
ers (06), lock washers (05), and nuts (04) to secure it in place.

14
OPERATING INSTRUCTIONS
Place the bed to your desired height; Turn the winch clockwise to raise the bed
and anti clockwise to lower.
Use the bed support pin (x4) and bed support pin clips (x8) to secure in place.
Place the arbor plate on the bed, then place the workpiece onto the arbor
plate.
Danger / Caution: At all times use all 8 bed support pin clips to secure the bed support
pins, using without the bed support pin clips is dangerous, this could cause injury to you
or any one in the vicinity, this will also damage the Shop press and void your warranty.
Turn the release valve clockwise to close it.
Open the air vent / oil fill screw on top of the pump.
Connect the air supply to the air valve inlet connection on the foot pedal, press
the foot pedal down and the ram will start too move (use the pump handle if
no air supply is available).
Once the serrated saddle is near the workpiece take your foot off the pedal (or
stop pumping the handle).
Align the workpiece and ram to ensure centre loading.
Press the foot pedal down again (or pump the handle) to start the pressing.
Once the work is done take your foot from the foot pedal (or stop pumping the
handle).
Turn the release valve anti-clockwise to retract the ram.
When the ram has fully retracted, remove the workpiece.
If no more work is to be done, then disconnect from the air supply and retight-
en the release valve and air vent / oil fill screw.
15
MAINTENANCE
Periodically check the press frame to make sure all bolts are tight and inspect
for cracked welds, bent, loose, or missing parts.
Periodically check hydraulic connections for possible leaks, replace or properly
repair damaged or leaking hydraulic components before use.
Change hydraulic oil in the hydraulic system every 100 working hours, or more
frequently in unusual dirty or dusty areas.
If the paint becomes badly chipped, it is suggested to repaint the press. This will
prevent rusting.
Always ensure that ram is in the fully retracted position if the press is not used for
extended periods.
Make sure the ram is fully retracted.
Remove the air vent / oil fill screw.
Fill with hydraulic oil (#22 ISO6743) through the oil fill hole, until the oil reaches the
top of the oil chamber.
Refit the air vent / oil fill screw.
ADDING OIL
BLEEDING
Loosen the air vent / oil fill screw.
Insert the handle into the handle base.
Pump the handle about 10 times, this will purge the air out of the system.
retighten the air screw.
CLEANING
Periodically check the ram and ram piston for signs of rust or corrosion. Clean as
needed and wipe with an oily cloth.
Note: Never use sandpaper or abrasive material on these surfaces.
Table of contents
Other SIP Power Tools manuals
Popular Power Tools manuals by other brands
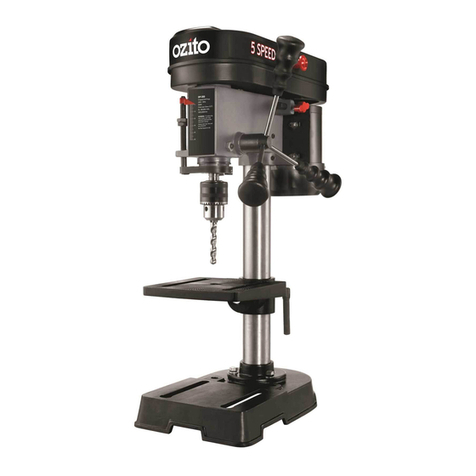
Ozito
Ozito DP-350U Additonal operating & safety instructions
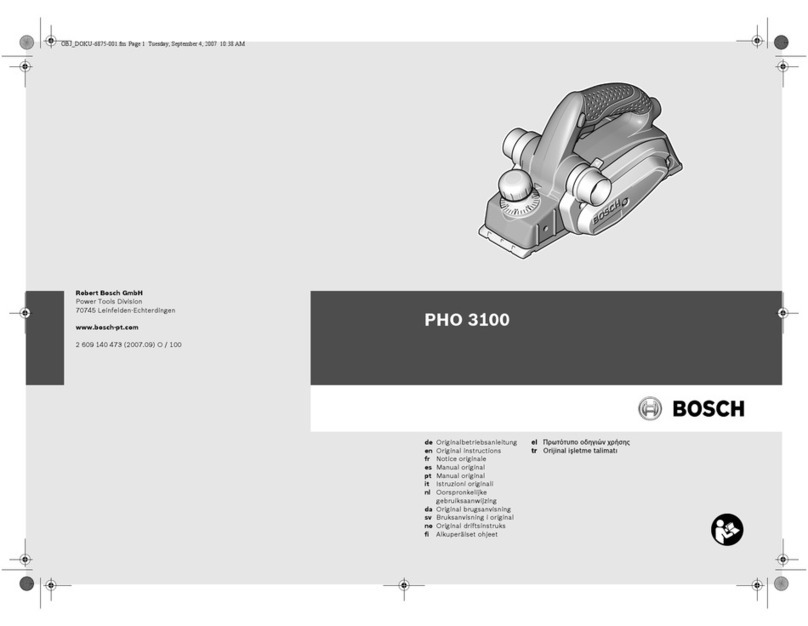
Bosch
Bosch PHO 3100 Original instructions
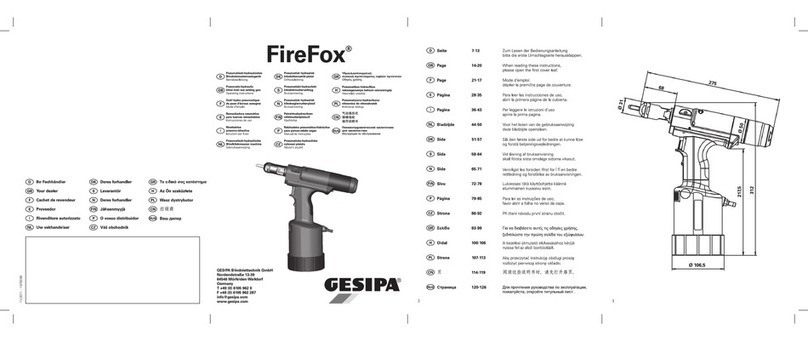
Gesipa
Gesipa FireFox operating instructions
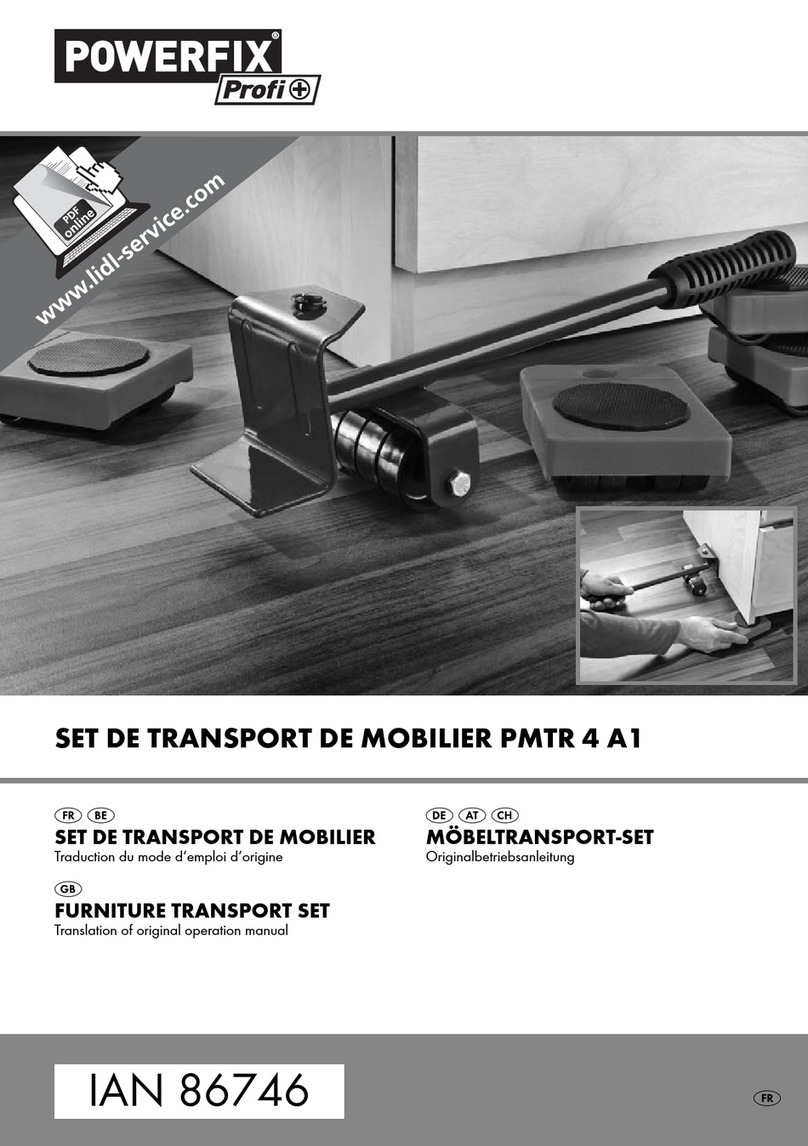
Powerfix Profi
Powerfix Profi 86746 translation of original operation manual
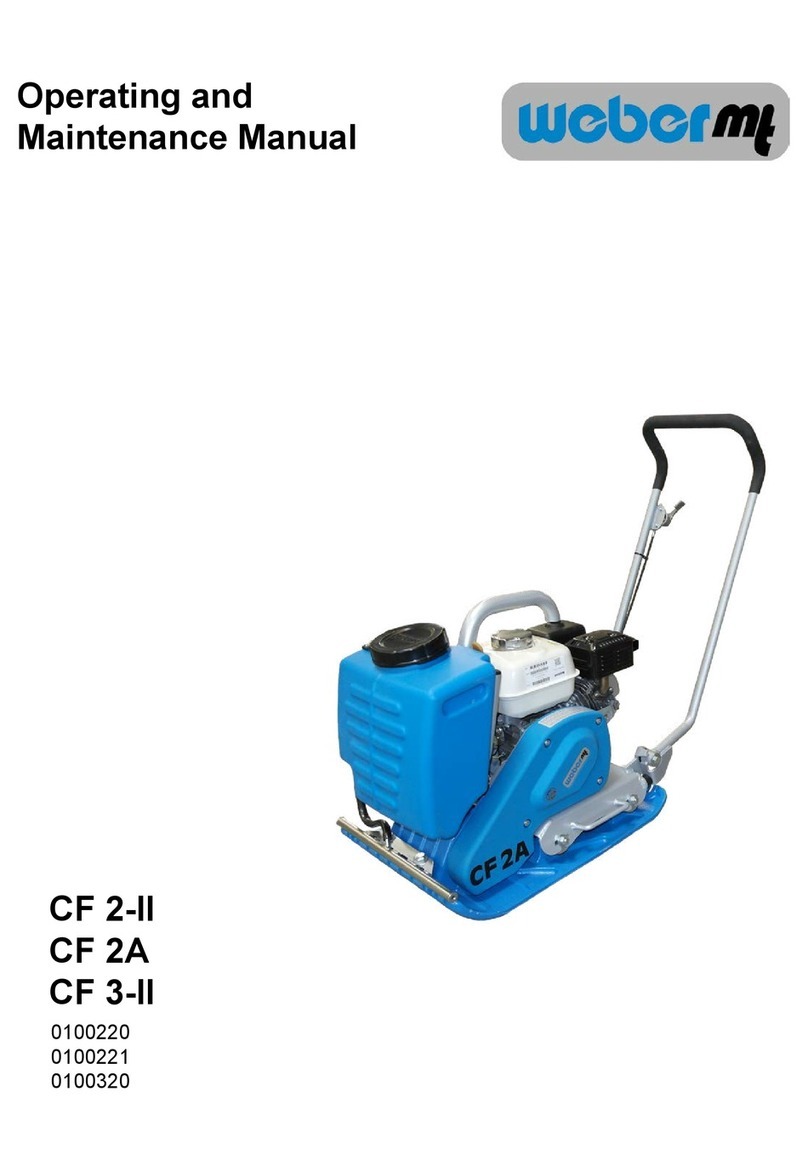
Weber mt
Weber mt CF 2-II Operating and maintenance manual

Chicago Pneumatic
Chicago Pneumatic CP5000 Series Operator's manual