SMC Corporation D-F6P Instruction Manual

1.1.1.
The compatibility of pneumatic equipment is the
responsibility
of the person who designs the pneumatic
system or decides
its specifications.
Since the products specified here are used in various operating
conditions,their compatibility for the specific pneumatic system
must be based on specifications or after analysis and/or tests to
meet your specific requirements.
1.1.2.
Only trained personnel should operate pneumatically
operated machinery and equipment.
Compressed air can be dangerous if an operator is unfamiliar with it
Assembly, handling or repair of pneumatic systems should be
performed by trained and experienced operators.
1.1.3.
Do not service machinery/equipment or attempt to remove
component until safety is confirmed.
1) Inspection and maintenance of machinery/equipment should only be
performed after confirmation of safe locked-out control positions.
2) When equipment is to be removed, confirm the safety process as
mentioned above. Switch off air and electrical supplies and exhaust all
residual compressed air in the system.
3) Before machinery/equipment is re-started, ensure all safety measures to
prevent sudden movement of actuators etc. (Supply air into the system
gradually to create backpressure, i.e. incorporate a soft-start valve).
1.1.4.
Contact SMC if the product is to be used in any of the following
conditions:
1) Conditions and environments beyond the given specifications, or if
product is used outdoors.
2) Installations in conjunction with atomic energy, railway, air navigation,
vehicles, medical equipment, food and beverage, recreation equipment,
emergency stop circuits, press applications, or safety equipment.
3) Equipment intended for use in potentially explosive atmospheres.
Applications which have the possibility of having negative effects on
people, property or animals.
Special safety analysis is required.
Installation & Maintenance Manual
Auto Switch (Solid State)
Series D-F6N/D-F6P/D-F6B
Read this manual before using this product.
For future reference, please keep this manual in a safe place.
This manual should be read in conjunction with the current catalogue.
1.1 General recommendation
These safety instructions are intended to prevent a hazardous
situation and/or equipment damage.
These instructions indicate the level of potential hazard by label of
"Caution", "Warning" or "Danger".
To ensure safety of personnel and equipment the safety instructions in
this manual and the product catalogue must be observed, along with
other relevant safety practices.
Operator error could result in injury or
equipment damage.
Operator error could result in serious injury
or loss of life.
In extreme conditions, there is a possible
result of serious injury or loss of life.
Design and selection
Confirm the specifications.
Read the specifications carefully and use this product appropriately. The
product may be damaged or malfunction if it is used outside the range of
specifications for load current, voltage, temperature or impact.
Take precautions when multiple actuators are used close together.
When multiple auto switch actuators are used in close proximity,
magnetic field interference may cause the switches to malfunction.
Maintain a minimum actuator separation of 40mm.
Pay attention to the length of time that a switch is ON at an
intermediate stroke position.
When an auto switch is placed at an intermediate position of the stroke and
a load is driven at the time the piston passes, the auto switch will operate,
but if the speed is too great the operating time will be shortened and the
load may not operate properly. The maximum detectable piston speed is:
Keep wiring as short as possible
Although longer wiring does not affect the function, please keep it to
100m or shorter
Do not use a load that generates surge voltage.
Although a zener diode for surge protection is connected at the output side of
a solid state auto switch, damage may still occur if the surge is applied
repeatedly. When a load such as a relay or solenoid which generates surge is
directly driven, use a type of switch with a built-in surge absorbing element.
Cautions for use in an interlock circuit
When an auto switch is used for an interlock signal requiring high reliability,
devise a double interlock system to avoid trouble by providing a mechanical
protection function, or by also using another switch (sensor) together with
the auto switch.
Also perform periodic maintenance and confirm proper operation.
Ensure sufficient clearance for maintenance activities.
When designing an application, be sure to allow sufficient clearance for
maintenance and inspections.
Mount / adjustment
Do not drop or bump.
Do not drop, bump or apply excessive impacts (1000m/s2or more for solid state
switches) while handling. Although the body of the switch may not be damaged,
the inside of the switch could be damaged and cause a malfunction.
Do not carry an actuator by the auto switch lead wires.
Never carry an actuator by its lead wires. This may not only cause broken
lead wires, but it may cause internal elements of the switch to be damaged
by the stress.
Mount switches using the proper tightening torque.
If a switch is tightened beyond the range of tightening torque, the mounting
screws, mounting brackets or switch may be damaged.
On the other hand, tightening below the range of tightening torque may
allow the switch to slip out of position.
Mount a switch at the center of the operating range.
Adjust the mounting position of an auto switch so that the piston stops at
the center of the operating range (the range in which a switch is ON).
(The mounting position shown in the catalog indicates the optimum
position at stroke end.) If mounted at the end of the operating range
(around the borderline of ON and OFF), operation may be unstable.
Wiring
Avoid repeatedly bending or stretching lead wires.
Broken lead wires can result from wiring patterns which repeatedly apply
bending stress or stretching force to the lead wires.
Confirm proper insulation of wiring.
Be certain that there is no faulty wiring insulation (contact with other
circuits, ground fault, improper insulation between terminals, etc.)
Damage may occur due to excess current flow into a switch.
Do not wire with power lines or high voltage lines.
Wire separately from power lines or high voltage lines, avoiding parallel wiring
or wiring in the same conduit with these lines. Control circuits containing auto
switches may malfunction due to noise from these other lines.
Do not allow short circuit of loads.
All models of switches do not have built-in short circuit protection circuits.
Note that if a load is short circuited, the switch will be instantly damaged
because of excess current flow into the switch.
Avoid incorrect wiring
I
f wiring is incorrect, the switches will be damaged.
When stripping the cable envelope, please pay attention to the
stripping direction.
Insulator might be split or hurt depending on the directions.
Operating environment
Do not use in an area where a magnetic field is generated.
Auto switches can malfunction or magnets inside actuators can become
demagnetized.
Do not use in an environment where the auto switch will be
continually exposed to water.
Although switches satisfy IEC standard IP67 construction ( IS C 0920:
watertight construction), avoid using switches in applications with continual
exposure to water splash or spray. Poor insulation or swelling of the potting
resin inside switches may cause malfunction.
Do not use in an environment with oil or chemicals.
Consult SMC if auto switches are to be used in an environment with coolant,
cleaning solvent, various oils or chemicals. If auto switches are used under
these conditions for even a short time, they may be adversely affected by
improper insulation, malfunction due to swelling of the potting resin, or
hardening of the lead wires.
Do not use in an environment with temperature cycles.
Consult SMC if switches are used where there are temperature cycles
other than normal air temperature changes, as there may be adverse
effects inside the switches.
Do not use in an area where surges are generated.
When there are units (solenoid type lifter, high frequency induction furnace,
motor, etc.) which generate a large amount of surge in the area around
actuators with solid state auto switches, this may cause deterioration or
damage to the switches. Avoid sources of surge generation and crossed lines.
2. INSTALLATION AND OPERATING ENVIRONMENT
4.INTENDED CONDITIONS OF USE
Impact resistance 1000m/s
2
Insulation resistance 50M or more at 500V DC mega
Withstand voltage 1000V AC for 1 minute (lead wire, between cases)
Ambient temperature -10 to 60
Protection structure IEC60529 standard IP67, ISC0920
3.Model Indication Method
N
P
B
D
-
F6
0.5m
L 3m
Z 5m
S 0.5m
M 1m
D
-
F6 PC
Switch model number D-F6N D-F6P D-F6B
Wiring 3 wire 2 wire
Output NPN PNP
-
Application IC circuit/Relay/PLC
24V DC Relay/PLC
Power voltage 5/12/24V DC (4.5 to 28V DC)
-
Current consumption 10mA or less
-
Load voltage 28V DC or less
-
24V DC(10 to 28V DC)
Load current 40mA or less 2.5 to 40mA
Internal voltage drop 0.8V or less 4V or less
Current leakage 100 A or less at 24V DC 0.8mA or less
Operating time 1ms or less
Indication light ON: Red light emitting diode
Electrical entry system Grommet
Lead wire Oilproof heavy-duty vinyl cord
2.7 3.2 oval, 0.15mm2, 2 wire (D-F6B), 3 wire (D-F6N,D-F6P)
Avoid accumulation of iron waste or close contact with magnetic
substances.
When a large amount of iron waste such as machining chips or spatter has
accumulated, or a magnetic substance (something attracted by a magnet) is
brought into close proximity with an auto switch actuator, it may cause auto
switches to malfunction due to a loss of the magnetic force inside the
actuator.
Maintenance
Perform the following maintenance periodically in order to prevent
possible danger due to unexpected auto switch malfunction.
1) Securely tighten switch mounting screws.
If screws become loose or the mounting position is dislocated,
retighten them after readjusting the mounting position.
2) Confirm that there is no damage to lead wires.
To prevent faulty insulation, replace switches or repair lead wires,
etc., if damage is discovered.
Others
For durability against water, elasticity, application at welding
site, please consult us.
If ON and OFF position (hysteresis) cause problems, please
consult us.
D-#S-TFI110GB-A
Piston moving
direction
Piston moving
direction
OFF position
ON position
Hysteresis
3wire NPN output
3wire PNP output
2wire
Output
Switch No.
N3wire NPN output
P3wire PNP output
B2wire
Lead wire length
No number
Output
Switch No.
Lead wire length
Pre-wired connector
Connector pin assignment
AM8-3pin connector
B M8-4pin connector
DM12-4pin connector
Caution
Warning
Danger
Autoswitch operating range [mm]
Load operating time [ms]

6.How to mount / Mounting bracket
When mounting an auto switch on an actuator it should be done with
the actuator clamp.
“How to mount” depends on actuator type and tube I.D. Please refer
the actuator catalogue.
When an auto switch is mounted for the first time, please ensure the
actuator is of the magnet built in type, then perpare the
corresponding brackets for the actuator.
•Proper tightening torque
Use special tool or torque wrench for tightening the set screw.
M3 mount screw tightening torque shall be 0.8 to 1.4 N•m.
7.Basic wiring
8.Exterior dimension
9.Check flow
When detection failure occurs (stay ON/OFF), please check
based on the next flow.
5.Names and Functions of Individual Parts
H
I
J
K
2003
2004
2005
2006
O
P
Q
R
S
T
U
V
W
X
Y
Z
•Setting the detecting position
Set the actuator at the stroke end. Set the switch in the area to where
the auto switch red lamp lights. (Detecting actuator end)
Based on A and B dimensions in the actuator catalogue, set the switch.
44
14
10
31.4
D-F6 PC
A
B
D-F6 DPC
Exterior dimension of Pre-wired connector
3.2 2.7
500(3000)(5000)
7
(22)
D-F6B
10.6
16
(24)
29
8.5
D-F6N
D-F6B D-F6B
D-F6P
Insert mount groove
to the rail.
Loosen set screws
for this.
Tighten set screws after deciding the position
Rail
Connection with PLC (sequence controller)
2
43
1
4
3
1
43
21
ABA C DEBB A A FD
A
B
C
D
E
F
---
---
---
---
---
---
D-#S-TFI110GB-A
Mounting screw
Lead wire
Indicator light
Month
anuary
February
March
April
May
une
uly
August
September
October
November
December
MarkMark Year
Year Month
Connector size M12
Connector size M8
Switch output parts failure(replace)
Check wiring and correct fault
Replace switch 2 wires --> 3 wires
Switch failure
Replace cylinder. Detectable magnet field in adequate (No magnet)
Replace PLC input board or replace switch 2 wires --> 3 wires
Load spec. check(1) ----- ON voltage > Load voltage-Internal voltage drop
Load spec. check(2) ----- OFF current > Leak current
Trouble occurs
2wires / 3wires
Replace the Switch
Load spec.check(1)
Wiring
(output)check
2wires / 3wires
Indicator light
Trouble
condition
Indicator light
Load spec.check(2)
Source voltage
or load voltage
Stay ON(Sometimes OFF)
Stay ON
Stay OFF(sometimes ON)
3wires
Normal
Normal Abnormal
Normal Abnormal Normal Abnormal
AbnormalNormal
Stay OFF Normal
2wires
3wires
Normal Abnormal
Stay ON
2wires
M8-3pin connector M8-4pin connector M12-4pin connector
Switch
main
circuit
Switch
main
circuit
Switch
main
circuit
Switch
main
circuit
Load
Brown
(PinNo.1)
(PinNo.4)
Brown
(PinNo.1)
Load
Load
Load
OUT
Black
(PinNo.1)
Blue
(PinNo.3)
Blue
(PinNo.3)
Power
supply
Power
supply
Power
supply
OUT
Black
Power
supply
(Sink input mode) (Source input mode)
OUT(+)
Black
OUT(+)
Black
OUT (-)
Blue
(PinNo.4)
OUT (-)
Blue
(PinNo.4)
(PinNo.1) (PinNo.1)
Indicator light
Most sensitive position
AUSTRIA (43) 2262 62280 NETHERLANDS (31) 20 531 8888
BELGIUM (32) 3 355 1464 NORWAY (47) 67 12 90 20
CZECH REP. (420) 541 424 611 POLAND (48) 22 211 9600
DENMARK (45) 7025 2900 PORTUGAL (351) 21 471 1880
FINLAND (358) 207 513513 SLOVAKIA (421) 2 444 56725
FRANCE (33) 1 6476 1000 SLOVENIA (386) 73 885 412
GERMANY (49) 6103 4020 SPAIN (34) 945 184 100
GREECE (30) 210 271 7265 SWEDEN (46) 8 603 1200
HUNGARY (36) 23 511 390 SWITZERLAND (41) 52 396 3131
IRELAND (353) 1 403 9000 UNITED KINGDOM (44) 1908 563888
ITALY (39) 02 92711
URL http://www.smcworld.com (Global) http://www.smceu.com (Europe)
Specifications are subject to change without prior notice from the manufacturer.
The descriptions of products in this document may be used by other companies.
© SMC Corporation All Rights Reserved.
Contact
This manual suits for next models
2
Other SMC Corporation Switch manuals
Popular Switch manuals by other brands

Digital Equipment
Digital Equipment VNswitch 900EF Installation and configuration
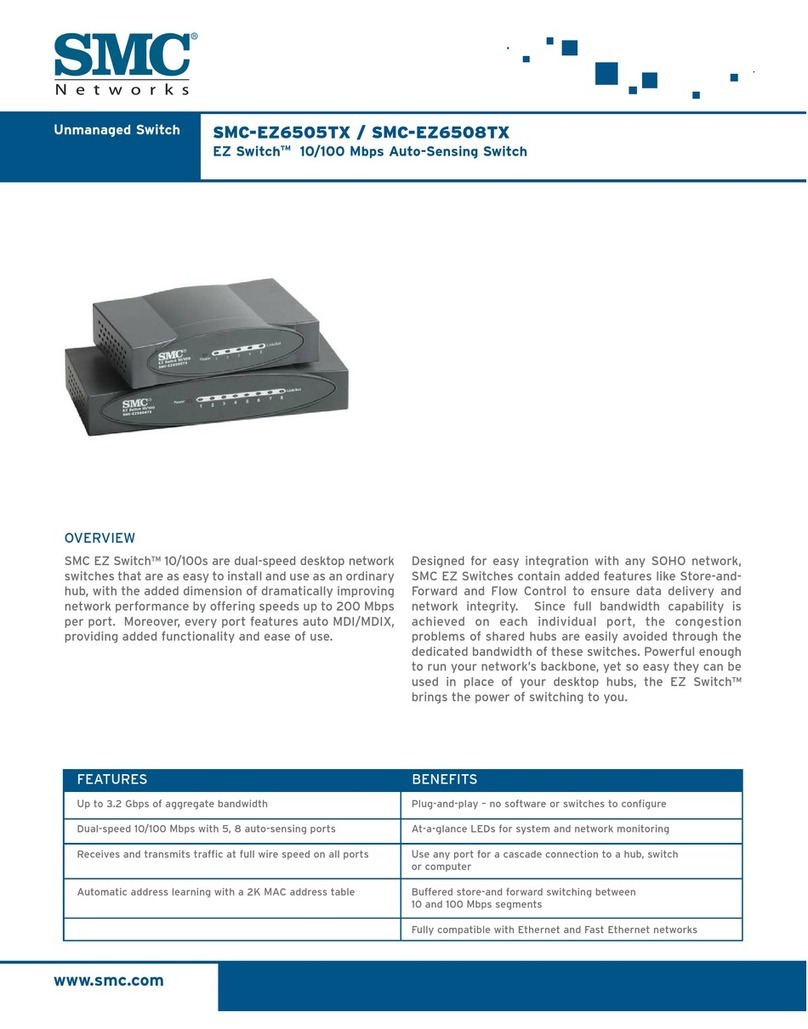
SMC Networks
SMC Networks EZ Connect SMC-EZ6505TX Technical specifications
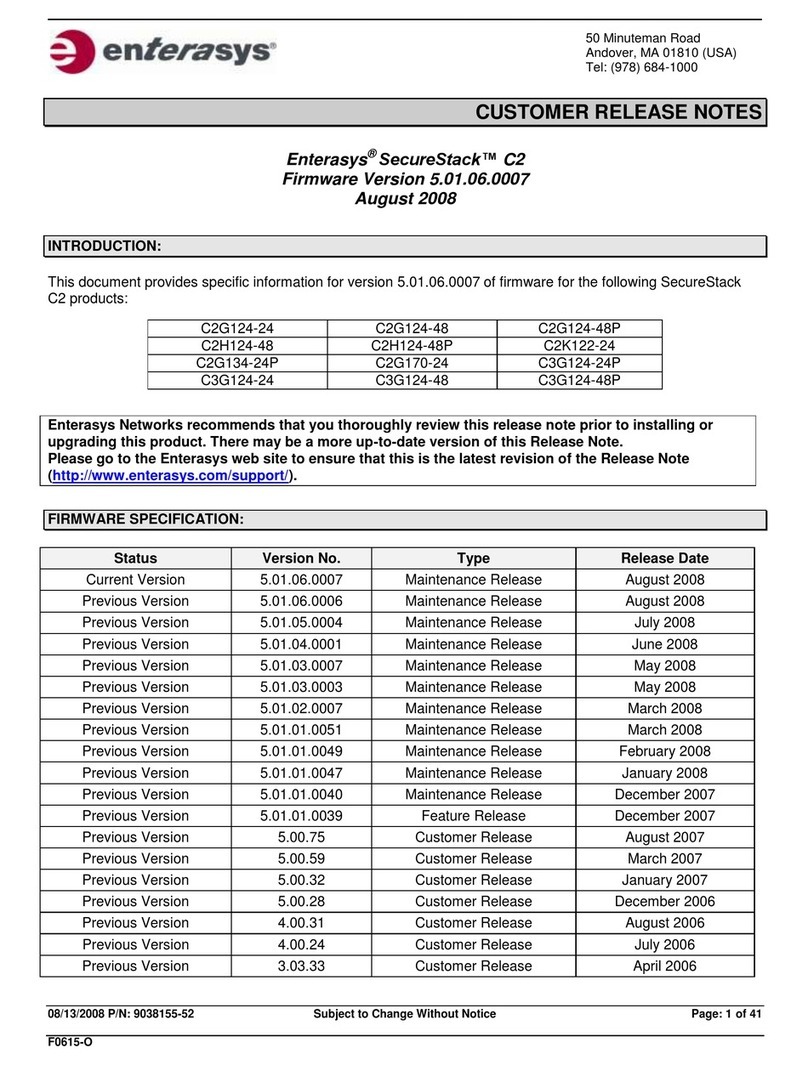
Enterasys
Enterasys SecureStack C2 C2K122-24 release note
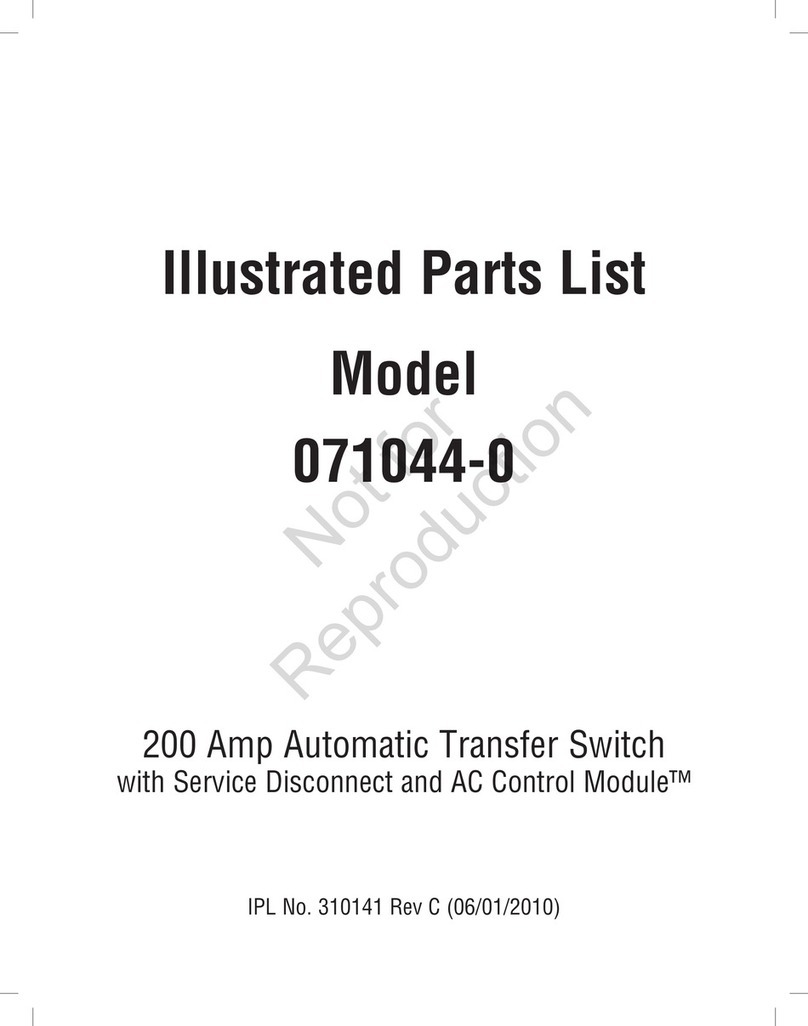
Briggs & Stratton
Briggs & Stratton 071044-0 Illustrated parts list

Panasonic
Panasonic Swtich-M48eG Series installation guide

HPE
HPE FlexNetwork 10500 SERIES Configuration guide