SMC Networks HRS400 Series User manual

Air-cooled refrigeration
MCooling capacity: 38 kW
M Power supply:
3-phase 380 to 415 VAC (50/60 Hz)
3-phase 460 to 480 VAC (60 Hz)
MSet temperature range: 5 to 35°C
MMax. ambient temperature: 45°C
MTemperature stability: ±0.1°C
MWith heating function
MImmersion pump (Mechanical sealless)
MWaterproof specification: IPX4
M Touch panel, Improved usability and
visibility (For details, refer to page 5.)
¡Home screen
¡Graphical representation of the temperature
allows for grasping of the temperature history.
¡Display of alarm details allows for quick
response.
Circulating Fluid Temperature Controller
Thermo-chiller (UL Standards)
Standard Type
¡Chiller operation status can be monitored on a
single screen.
INFORMATION
HRS400 Series
22-E780

(UL Standards)
How to Order
Option 1
Nil None
AWith caster adjuster-foot
DElectric conductivity control
K∗1With fluid fill port
M
Applicable to deionized water piping
∗1 This is a manual fluid fill port that is
different from the automatic fluid fill
port. Fluid can be supplied manually
into the tank without removing the
side panel. (Fluid can be supplied
manually for models without option K
if the side panel is removed.)
Power supply
46
3-phase 380 to 415 VAC (50/60 Hz)
3-phase 460 to 480 VAC (60 Hz)
Pipe thread type
Nil
Rc
F
G (With Rc-G conversion fitting)
N
NPT (With Rc-NPT conversion fitting)
Cooling method
A
Air-cooled refrigeration
Cooling capacity
400
38 kW
HRS 400 A
46
Thermo-chiller
Air-cooled 460 V Type
Standard Type
HRS400 Series
Specifications
Model HRS400-A-46
Cooling method Air-cooled refrigeration
Refrigerant R410A (HFC)
Refrigerant charge kg 3.7
Control method PID control
Ambient temperature/Altitude
∗1, 7, 9 °CTemperature: –5 to 45, Altitude: less than 3000 m
Circulating fluid system
Circulating fluid∗1, 2
Tap water, 15% Ethylene glycol aqueous solution, Deionized water
Set temperature range∗1°C5 to 35
Cooling capacity∗3, 7 kW 38
Heating capacity∗4kW 8
Temperature stability∗5°C±0.1
Pump
capacity
50/60 Hz
Rated flow (Outlet) L/min 125 (0.45 MPa)
Maximum flow rate L/min 180
Maximum pump head m68
Minimum operating flow rate∗6L/min 40
Tank capacity L 60
Circulating fluid outlet, circulating fluid return port
Rc1 (Symbol F: G1, Symbol N: NPTG1)
Tank drain port Rc3/4 (Symbol F: G3/4, Symbol N: NPTG3/4)
Automatic
fluid fill
system
(Standard)
Supply side pressure range
MPa 0.2 to 0.5
Supply side fluid temperature
°C5 to 35
Automatic fluid fill port Rc1/2 (Symbol F: G1/2, Symbol N: NPTG1/2)
Overflow port
Rc1 (Symbol F: G1, Symbol N: NPTG1)
Fluid contact material Metal
Stainless steel, Copper (Heat exchanger brazing), Brass, Bronze
Resin PTFE, PU, FKM, EPDM, PVC, NBR, POM, PE, NR, PBT
Electrical system
Power supply
3-phase 380 to 415 VAC (50/60 Hz)
Allowable voltage range ±10% (No continuous voltage fluctuation)
3-phase 460 to 480 VAC (60 Hz)
Allowable voltage range ±4%, –10% (Max. voltage less than
500 V and no continuous voltage fluctuation)
Applicable earth leakage
breaker (Standard)
Rated current
A40
Sensitivity of leak current
mA 30
Rated operating current∗5A22
Rated power consumption∗5
kW(kVA)
14.3 (15.2)
Noise level (Front 1 m/Height 1 m)∗5
dB(A) 71
Waterproof specification IPX4
Accessories
Operation Manual (for installation/operation) 1 pc. (English),
Y-strainer (40 meshes) 25A, Barrel nipple 25A,
Anchor bolt fixing brackets 2 pcs. (including 6 M8 bolts)
Weight (dry state) kg Approx. 340
∗1 When the ambient temperature or circulating fluid
temperature is 10°C or below, refer to "Operation at
low ambient temperature or low circulating fluid tem-
perature" (page 15).
∗2 Use fluid in condition below as the circulating fluid.
Tap water: Standard of The Japan Refrigeration And
Air Conditioning Industry Association (JRA GL-02-
1994)
15% ethylene glycol aqueous solution: Diluted with
clean water, without any additives such as antisep-
tics.
Deionized water: Electric conductivity 1 μS/cm or
higher (Electric resistivity 1 MΩ·cm or lower)
∗3 qAmbient temperature: 32°C, wCirculating fluid:
Tap water, eCirculating fluid temperature: 20°C, r
Circulating fluid flow rate: Rated flow, tPower sup-
ply: 400 VAC
∗4 qAmbient temperature: 32°C, wCirculating fluid:
Tap water, eCirculating fluid flow rate: Rated flow,
rPower supply: 400 VAC
∗5 qAmbient temperature: 32°C, wCirculating fluid:
Tap water, eCirculating fluid temperature: 20°C, r
Load: Same as the cooling capacity, tCirculating
fluid flow rate: Rated flow, yPower supply: 400 VAC,
uPiping length: Shortest
∗6 Fluid flow rate to maintain the cooling capacity. If the
actual flow rate is lower than this, install a bypass
piping.
∗7 If the product is used at an altitude of 1000 m or
higher, refer to “Operating Environment/Storage Envi-
ronment” (page 14) Item 13 “For altitudes of 1000 m
or higher.”
∗8 The anchor bolt fixing brackets (including 6 M8 bolts)
are used for fixing to wooden skids when packaging
the thermo-chiller. No anchor bolt is included.
∗9 For the product operation in the UL compliant condi-
tions, refer to “Operating Environment/Storage Envi-
ronment” (page 14).
1

Cooling Capacity Pump Capacity
0 10 20 30 40
Circulating fluid temperature [°C]
Cooling capacity [kW]
60
50
40
30
20
10
0
Ambient temperature 32°C
Ambient temperature 45°C
HRS400-Am-46-mHRS400-Am-46-m
2
Thermo-chiller Standard Type HRS400 Series
0 20 40 60 80 100 120 140 160
180
Circulating fluid flow rate [L/min]
Circulating fluid outlet
Circulating fluid return port
Circulating
fluid pressure
[MPa]
0.9
0.8
0.7
0.6
0.5
0.4
0.3
0.2
0.1
0
Pump
head
[m]
90
80
70
60
50
40
30
20
10
0
Usable flow rate range

752
700
1350 (Thermo-chiller dimension)
850
(Thermo-chiller dimension)
294756
1380
1416 (Dimension of anchor bolt fixing bracket)
8 x ø1
2
50
Barrel nipple 25A
Y-strainer
(40 mesh) 25A
Flow direction
∗
Mount it by yourself on the
circulating fluid return port.
130
Barrel nipple (25A)
(Accessory)
Y-strainer
(Accessory)
Ventilation air inlet
Ventilation air outlet
Ventilation air inlet
A A
1350
1722
589
527
487
351
312
850
277
510
527
607
Dustproof filter
Dustproof filter
Eye bolt M16
(4 places)
Touch panel
Handle
Breaker handle
Automatic fluid fill port
Rc1/2
Overflow port
Rc1
Fluid level indicator
Power cable entry
Signal cable entry
115
Tank drain
Rc3/4 (Valve stopper)
172
Handle
113
Anchor bolt fixing bracket (Accessory)
For details about the fixing position, refer to
“Anchor bolt fixing position” shown below.
Circulating fluid
return port
Rc1
Circulating fluid outlet
Rc1
Dimensions
HRS400-Am-46-m
Anchor bolt fixing position Accessory: Y-strainer mounting view
View A-A
3
HRS400 Series Standard Type

Recommended External Piping Flow
External piping circuit is recommended as shown below.
Cable Specifications
Power Cable Specifications
Rated value for thermo-chiller Power cable examples
Power supply
Applicable breaker
rated current
Terminal block
thread size
Cable size
Crimped terminal on
the thermo-chiller side
3-phase 380 to 415 VAC (50/60 Hz)
3-phase 460 to 480 VAC (60 Hz)
40 A M5
4 cores x 8 mm2(4 cores x AWG8)
∗Including grounding cable
R8-5
∗An example of the cable specifications is when two kinds of vinyl insulated wires with a continuous
allowable operating temperature of 70°C at 600 V, are used at an ambient temperature of 30°C.
Select the proper size of cable according to an actual condition.
Circulating fluid
outlet
Thermo-chiller
automatic fluid
fill port
3
Customer’s
equipment
To wastewater collection pit
Fluid supply
Circulating fluid
return port
Overflow port
Tank drain port
4
5
2 2
2 2
1
1
6
∗Ensure that the overflow port is connected to the wastewater collection pit in order to avoid damage to the tank of the thermo-chiller.
No. Description Size
Recommended part no.
Note
1Valve Rc1/2 — —
2Valve Rc1 — —
3Y-strainer Rc1 #40 Accessory
Install either the strainer or filter. If foreign matter with a size of 20 μm or more are likely to enter, install
the particle filter. For the recommended filter, refer to the optional accessory HRS-PF005 (page 11).
Filter Rc1 20 μm HRS-PF005∗1
4Flow meter — — Prepare a flow meter with an appropriate flow range.
5
Valve (Part of thermo-chiller)
Rc3/4 — —
6Y-strainer Rc1/2 #40 — Install either the strainer or filter. If foreign matter with a size of 20 μm or more
are likely to enter, select and prepare a particle filter.
Filter Rc1/2 20 μm —
∗1 The filter shown above cannot be directly connected to the thermo-chiller. Install it in the customer’s piping system.
Power cable
Partially enlarged view A
A
4
Thermo-chiller Standard Type HRS400 Series

The basic operation of this unit is controlled through the operation display panel on the front of the product.
Home Screen and Setting Items
No. Classification Item Explanation
q
Displayed
value
Circulating fluid temperature Indicates the current temperature
wCompressor Displays the operation and stop state of the compressor
ePump Displays the operation and stop status of the pump
rTank fluid level
Indicates the tank fluid level with 3 levels: “Sufficient,” “Low,” or “Insufficient”
“Sufficient”
Blue
“Low”
Yellow
“Insufficient”
Red
tCirculating fluid flow rate
Indicates the fluid flow rate
This value is not measured by a flow meter.
It should be used as a reference value (rough indication).
yCirculating fluid discharge pressure Indicates the discharge pressure
u
Pressure gauge on the high-pressure side of the refrigeration circuit
Displays the pressure gauge on the high-pressure side of the refrigeration circuit
i
Pressure gauge on the low-pressure side of the refrigeration circuit
Displays the pressure gauge on the low-pressure side of the refrigeration circuit
oCirculating fluid electric conductivity Indicates the electric conductivity∗1
!0 Circulating fluid set temperature Indicates the current temperature
!1
Button
Operation mode
To select an operation mode from the touch panel ( mode), an operation mode from the
contact input ( mode), or an operation mode from the serial communication ( mode)
!2 Independent pump operation Operates the pump independently while the button is pressed
!3 Run/Stop To run/stop the product
∗1 When option “D” (Electric conductivity control) is purchased, a numerical value is displayed.
!0
q
w
e
r
!1 !2 !3
t
y
u
i
o
Alarm code Explanation
AL01 Abnormally low tank fluid level
AL02 Low tank fluid level
AL06 Fan failure
AL09
Abnormal rise of circulating fluid temperature
AL10 Circulating fluid temperature rise
AL11 Circulating fluid temperature drop
AL12 TEMP READY alarm
AL17
Abnormal rise in heat exchanger inlet temperature
AL18
Failure of circulating fluid discharge pressure sensor
AL19 Circulating fluid discharge pressure rise
AL20 Circulating fluid discharge pressure drop
AL28 (Option “D” only) Electric conductivity increase
AL29 Power supply failure
Alarm code Explanation
AL30 Contact input 1 signal detection
AL31 Contact input 2 signal detection
AL34 Communication error
AL35 Outside of the ambient temperature range
AL36 Maintenance alarm
AL37 Compressor circuit failure
AL38 Sensor failure
AL39 Controller failure
AL40 Compressor inverter error
AL41 Compressor inverter communication error
AL42 Pump inverter error
AL43 Pump inverter communication error
5
HRS400 Series Standard Type
Operation Display Panel
Alarm
This product may display the alarm messages shown in the table below.

Contact Input/Output
Communication Functions
Contact Input/Output, Analog Output Communication Specifications
Item Specifications
Contact
input signal
1, 2, 3
Insulation method Photocoupler
·Run/Stop signal
·External switch signal
·Operation mode request signal (Contact input 3 fixed)
Rated input voltage 24 VDC
Operating voltage range 21.6 to 26.4 VDC
Rated input current 5 mA TYP
Input impedance 4.7 kΩ
Contact
output signal
1, 2, 3, 4, 5, 6
Rated load voltage 48 VAC or less/30 VDC or less ·Run status signal
·Alarm signal
·TEMP READY signal, etc.
Maximum load current 800 mA AC/DC or less∗1
Minimum load current 5 VDC 10 mA
Analog
output signal
1, 2
Output voltage range 0 to +10 V
—Maximum output current 10 mA
Output accuracy ±0.4% F.S. or less
Output voltage 24 VDC ±10% 200 mA MAX∗1 (No inductive load)
Circuit diagram
∗1 Make sure that the total load current is 800 mA or less. When using the power supply of this product, make sure that the total load current is 200 mA or
less.
Customer’s system side
To the thermo-chiller
24 VDC
+
–
+
–
–15 V
100 Ω
ANALOG COM
24 COM
1
24 COM
+24 VDC (Output)
4.7 kΩ
4.7 kΩ
4.7 kΩ
+15 V
–15 V
100 Ω
+15 V
ANALOG COM
Internal circuit
14
3
16
4
6
19
7
20
8
15
5
18
11
23
10
22
Contact output 4: OFF
Contact output 5: OFF
Analog output 1
Run/Stop
Operation mode request (Momentary)
Contact output 3: “WRN”
[Warning alarm occurrence OFF]
Contact output 2: “FLT”
[Fault alarm occurrence OFF]
Contact output 1: Operation status
[Operation ON]
Contact output 6: OFF
2
24 VDC
+24 VDC (Input)
EXT 24 VDC
EXT 24 COM
Power
supply
Analog output 2
External switch
24 COM (Output)
Contact output 1-5 common
Contact output 6 common
Analog output 1 common
Analog output 2 common
24 VDC 1
14
2
1
14
3
2
Power
supply
24 VDC
24 COM
4
4
3
When using this product’ s
power supply, connect pin 1
to pin 2 and the COM side
of each contact input signal
to pin 14. (Example 1)
When using a customer’s
power supply, connect the 24
VDC + side to pin 2 and the
COM side of each contact
input signal to the customer’s
power COM. (Example 2)
Power supply usage example
This product’s power supply
usage example (Example 1)
Customer’s power supply
usage example (Example 2)
6
Thermo-chiller Standard Type HRS400 Series

Communication Functions
Contact Input/Output, Analog Output Pin Nos.
Pin no.
Application Division Default setting
124 VDC output Output —
224 VDC input Input —
3Contact input signal 1 Input Run/Stop∗1
4Contact input signal 3 Input Operation mode request signal (fixed)∗2
5Contact output signal 6 Output OFF∗1
6Contact output signal 1 Output Run status signal [N.O. type] (fixed)∗2
7Contact output signal 3 Output
Operation continuation “WRN” alarm signal [N.C. type] (fixed)∗2
8Contact output signal 5 Output OFF∗1
9None — Cannot be connected∗3
10 Analog output signal 2 Output Circulating fluid discharge temperature signal∗4
11 Analog output signal 1 Output Circulating fluid discharge temperature signal∗4
12 None — Cannot be connected∗3
13 None — Cannot be connected∗3
14 24 COM output (Common of contact input signal) Output —
15 Common of contact output signals 1, 2, 3, 4, 5 Output —
16 Contact input signal 2 Input External switch signal∗1
17 None — Cannot be connected∗3
18 Common of contact output signal 6 Output —
19 Contact output signal 2 Output Operation stop “FLT” alarm signal [N.C. type] (fixed)∗2
20 Contact output signal 4 Output OFF∗1
21 None — Cannot be connected∗3
22 Common of analog output signal 2 Output —
23 Common of analog output signal 1 Output —
24 None — Cannot be connected∗3
25 None — Cannot be connected∗3
∗1 It is possible to change the setting.
∗2 It is not possible to change the setting. (“N.O. type/N.C. type” can be changed.)
∗3 Do not connect wiring.
∗4 When option “D” (With electrical conductivity control) is selected, the setting can be changed.
D-sub 25-pin female (socket) type
Holding screw: M2.6 x 0.45
14
25
1
13
∗Prepare a cable tie. Fasten the
signal cable to the mount on the
base with the cable tie.
Mount for cable tie Inlet of the signal cable
7
HRS400 Series Standard Type

Communication Functions
Wiring of Interface Cable for Serial Communication
Item Specifications
Connector type D-sub 9-pin female (socket) type
Configuration of connection RS-485
Circuit diagram
One thermo-chiller for one host computer, or multiple thermo-chillers for one host computer.
(31 thermo-chillers can be connected at maximum.)
Controller
Terminal
resistance
Terminal
resistance
This product
(2nd device)
This product
(31st device)
SD+ SD− SG
2
SD+
7
SD−
5
SG
This product
(1st device)
2
SD+
7
SD−
5
SG
2
SD+
7
SD−
5
SG
∗Do not connect with other pins.
Standards RS-232C
Circuit diagram
One thermo-chiller for one controller
Controller
RD
2
SD
3
SG
5
This product
RD
2
SD
3
SG
5
∗Do not connect with other pins.
Serial Communication
The following operations can be performed by the serial communication RS-232C/RS-485.
To run/stop the product
To change the set value of
circulating fluid temperature
Writing Readout
To readout the circulating fluid temperature, pressure, flow rate and electrical conductivity∗1
To readout the status of respective parts of the product (e.g., operation status and content of alarm)
∗1 For Option D (With electric conductivity control)
D-sub 9-pin female (socket) type
Holding screw: M2.6 x 0.45
6
9
1
5
8
Thermo-chiller Standard Type HRS400 Series

HRS400 A 46
A
Unfixed casters and adjuster feet stops are mounted
With caster adjuster-foot
HRS400 A 46 K
When the automatic fluid fill in port is not used, water can be supplied
manually without removing the panel.
With Fluid Fill Port
HRS400 A 46 D
This set can be used to display and control the electric conductivity of the circulating fluid. Refer to the Operation Manual for details.
Electric conductivity control
Fluid
fill port
Fluid fill port
Cap
1232
1839
536
118
HRS400 A 46 M
Deionized water (Pure water) piping
Option symbol
With Caster Adjuster-foot
A
HRS400 Series
Options ∗Options have to be selected when
ordering the thermo-chiller.
It is not possible to add them after
purchasing the unit.
Option symbol
With Fluid Fill Port
K
Option symbol
Electric Conductivity Control
D
701
56
252
Option
[K: With fluid fill port
]
Thread size: G1 1/2
(With cap)
Option symbol
Deionized Water (Pure Water) Piping
M
Applicable model
HRS400-Am-46-M
Contact materials
of circulating fluid
Stainless steel (including heat exchanger brazing), Alumina ceramic,
SiC, Carbon, PP, PE, POM, FKM, NBR, EPDM, PVC
The contact materials of the circulating fluid circuit are made
from non-copper materials.
Select this when using deionized water with a conductivity of
1 MΩ·cm or more (1 µs/cm or less).
9

Protrusion when the conversion
fitting for circulating fluid
is mounted
Conversion fittings for circulating
fluid outlet, circulating fluid
return port, overflow port
Material: Stainless steel
3 pcs./set
Conversion fitting for automatic
fluid fill port
Material: Stainless steel
1 pc./set
Conversion fitting for tank drain
port
Material: Stainless steel
1 pc./set
Approx. 35 mm
HRS400 Series
Optional Accessories
wCaster Adjuster-foot Kit
This is a set of unfixed casters and adjuster feet stop.
When installed by customer, it is necessary to lift the thermo-chiller by a forklift or sling work.
Carefully read the procedure manual included with this kit before performing the installation.
Part no. Applicable model
HRS-KS004 HRS400-A-46-
Parts List
Description
Procedure manual
Caster adjuster-foot bracket (2 pcs.)
Fixing bolt (M8) (8 pcs.)
HRS-EP013, HRS-EP014
qPiping Conversion Fitting
This is a fitting to change the port from Rc to G or NPT.
· Circulating fluid outlet, Circulating fluid return port, Overflow port Rc1 →NPT1 or G1
· Drain port Rc3/4 →NPT3/4 or G3/4
· Automatic fluid fill port Rc1/2 →NPT1/2 or G1/2
(It is not necessary to purchase this when pipe thread type F or N is selected in “How to Order” since it is included in the product.)
Part no. Contents Applicable model
HRS-EP013
NPT thread conversion fitting set
HRS400-A-46-
HRS-EP014 G thread conversion fitting set
Fig. 2 Caster adjuster-foot bracket (2 pcs.) Fig. 3 Fixing bolt (8 pcs.)
Fig. 1 Mounting view
1232
1839
536
Unfixed caster
(Caster O.D.: ø75)
Adjuster foot
Fixing bolt (M8)
118
10

eBypass Piping Set
When the circulating fluid goes below the minimum operating flow rate (as shown below), cooling capacity will be reduced and the
temperature stability will be badly affected. Use the bypass piping set to ensure a circulating fluid flow rate of the minimum
operating flow rate or more.
Part no. Applicable model
Minimum operating flow rate [L/min]
HRS-BP005 HRS400-Am-46-m25
To circulating fluid outlet
To circulating fluid return port
rt
r
w
q
rt
r
e
yu
Parts List
No. Description
Fluid contact material
Qty.
qHose (I.D.: 15 mm) PVC 1
(Approx. 700 mm)
wOutlet piping assembly
(With globe valve)
Stainless steel,
Brass, Bronze
1
e
Return piping assembly
Stainless steel, Brass
1
rNipple
(Size: 1 inch)
Stainless
steel 4
tUnion
(Size: 1 inch)
Stainless
steel 2
ySealant tape PTFE 1
uOperation Manual — 1
rParticle Filter Set
Removes foreign matter in the circulating fluid. This set cannot be directly connected to the thermo-chiller. Install it in the customer’s
piping system. Refer to the Operation Manual for details.
tDI Filter Replacement Cartridge
DI filter cartridge for replacement for Option D [Electric conductivity control type]
HRS PF005 H
HRR DF002
HRS PF006
Symbol Accessory
Nil None
HWith handle
Particle Filter Set
DI Filter Replacement Cartridge
Replacement Element
Parts List
No. Description Material Qty. Note
qBody PC, PP 1—
wElement∗1PP 1—
eExtension piece Stainless steel 2
Conversion from NPT to Rc
rHandle —1 When -H is selected
tSealant tape PTFE 1—
∗1 The product should be replaced when the pressure drop reaches 0.1 MPa.
Fluid Tap water
Max. operating pressure 0.65 MPa
Operating temperature range
5 to 35°C
Nominal filtration accuracy
5 µm
Installation environment Indoors
Accessory
The product should be replaced
when the pressure drop reaches
0.1 MPa.
(343)
(256)
Rc1
NPT1
NPT1
Rc1
t
r
w
q
e
e
11
HRS400 Series

HRS400 Series
Cooling Capacity Calculation
Required Cooling Capacity Calculation
Example 1: When the heat generation amount in the customer’s equipment is known.
The heat generation amount can be determined based on the power consumption or output of the
heat generating area — i.e. the area requiring cooling — within the customer’s equipment.*1
qDerive the heat generation amount from the power consumption.
Power consumption P: 20 [kW]
Q = P = 20 [kW]
Cooling capacity = Considering a safety factor of 20%, 20 [kW] x 1.2 =
wDerive the heat generation amount from the power
supply output.
Power supply output VI: 20 [kVA]
Q = P = V x I x Power factor
In this example, using a power factor of 0.85:
= 20 [kVA] x 0.85 = 17 [kW]
Cooling capacity = Considering a safety factor of 20%,
17 [kW] x 1.2 =
*1 The examples above calculate the heat generation amount based on the power consumption.
The actual heat generation amount may differ due to the structure of the customer’s equipment.
Be sure to check it carefully.
Example 2: When the heat generation amount in the customer’s equipment is not known.
Obtain the temperature difference between inlet and outlet by circulating the circulating fluid inside the customer’s equipment.
Heat generation amount by customer’s equipment Q
: Unknown [W] ([J/s])
Circulating fluid : Tap water*1
Circulating fluid mass flow rate qm : (= ρx qv ÷60) [kg/s]
Circulating fluid density ρ: 1 [kg/L]
Circulating fluid (volume) flow rate qv : 70 [L/min]
Circulating fluid specific heat C : 4.186 x 103[J/(kg·K)]
Circulating fluid outlet temperature T1: 293 [K] (20 [°C])
Circulating fluid return temperature T2 : 297 [K] (24 [°C])
Circulating fluid temperature difference iT : 4 [K] (= T2– T1)
Conversion factor: minutes to seconds (SI units) : 60 [s/min]
*
1
Refer to the next page for the typical physical property value of tap water or other circulating fluids.
Q = qm x C x (T2 –T1)
= =
= 19535 [J/s] ≈19535 [W] = 19.5 [kW]
Cooling capacity = Considering a safety factor of 20%,
19.5 [kW] x 1.2 =
24 [kW]
20.4 [kW]
ρx qv x C x iT
60
1 x 70 x 4.186 x 103x 4.0
60
23.4 [kW]
eDerive the heat generation amount from the output.
Output (shaft power, etc.) W: 13 [kW]
Q = P =
In this example, using an efficiency of 0.7:
= = 18.6 [kW]
Cooling capacity = Considering a safety factor of 20%,
18.6 [kW] x 1.2 =
W
Efficiency
13
0.7
22.3 [kW]
Example of conventional units (Reference)
Heat generation amount by customer’s equipment
Q
:
Unknown [cal/h] →[W]
Circulating fluid : Tap water*1
Circulating fluid weight flow rate qm
: (= ρx qv x 60) [kgf/h]
Circulating fluid weight volume ratio
: 1 [kgf/L]
Circulating fluid (volume) flow rate
qv
: 70 [L/min]
Circulating fluid specific heat C
: 1.0 x 103[cal/(kgf·°C)]
Circulating fluid outlet temperature
T1
: 20 [°C]
Circulating fluid return temperature
T2
: 24 [°C]
Circulating fluid temperature difference
iT : 4 [°C] (= T2– T1)
Conversion factor: hours to minutes : 60 [min/h]
Conversion factor: kcal/h to kW : 860 [(cal/h)/W]
Q =
=
=
=
≈19534 [W] = 19.5 [kW]
Cooling capacity = Considering a safety factor of 20%,
19.5 [kW] x 1.2 =
qmx C x (T2– T1)
860
x qvx 60 x C x iT
860
1 x 70 x 60 x 1.0 x 103x 4.0
860
16800000 [cal/h]
860
23.4 [kW]
Q: Heat generation
amount
Customer’s
equipment
I: Current
Power consumption
V
: Power supply
voltage
P
Thermo-chiller
Customer’s
equipment
T1: Outlet
temperature
T2: Return
temperature
qv: Circulating
fluid flow
rate
∆T = T2–T1
Q: Heat generation amount
12

Required Cooling Capacity Calculation
Example 3: When there is no heat generation, and when cooling the object below a certain temperature and period of time.
Heat quantity by cooled substance (per unit time) Q
: Unknown [W] ([J/s])
Cooled substance : Water
Cooled substance mass m : (= ρx V) [kg]
Cooled substance density ρ: 1 [kg/L]
Cooled substance total volume V : 300 [L]
Cooled substance specific heat C : 4.186 x 103[J/(kg·K)]
Cooled substance temperature when cooling begins T0
: 305 [K] (32 [°C])
Cooled substance temperature after t hour Tt : 293 [K] (20 [°C])
Cooling temperature difference iT : 12 [K] (= T0– Tt)
Cooling time it: 900 [s] (= 15 [min])
*Refer to the following for the typical physical property values by circulating fluid.
Q = =
= = 16744 [J/s] ≈16.7 [kW]
Cooling capacity = Considering a safety factor of 20%,
16.7 [kW] x 1.2 =
m x C x (T0– Tt)
it
ρx V x C x iT
it
1 x 300 x 4.186 x 103x 12
900
20 [kW]
Precautions on Cooling Capacity Calculation
1. Heating capacity
When the circulating fluid temperature is set above room temperature, it needs to be heated by the thermo-chiller. The heating capacity depends on the circulating
fluid temperature. Consider the radiation rate and heat capacity of the customer’s equipment and check beforehand if the required heating capacity is provided.
2. Pump capacity
<Circulating fluid flow rate>
Circulating fluid flow rate varies depending on the circulating fluid discharge pressure. Consider the installation height difference
between the thermo-chiller and the customer’s equipment, and the piping resistance such as circulating fluid pipings, or piping size,
or piping curves in the machine. Check beforehand if the required flow is achieved, using the pump capacity curves.
<Circulating fluid discharge pressure>
Circulating fluid discharge pressure has the possibility to increase up to the maximum pressure in the pump capacity curves.
Check beforehand if the circulating fluid pipings or circulating fluid circuit of the customer’s equipment are fully durable against this pressure.
Circulating Fluid Typical Physical Property Values
1. This catalog uses the following values for density and specific heat in calculating the required cooling capacity.
Density ρ: 1 [kg/L] (or, using conventional units, weight volume ratio = 1 [kgf/L] )
Specific heat C: 4.19 x 103[J/(kg·K)] (or, using conventional units, 1 x 103[cal/(kgf·°C)])
2.
Values for density and specific heat change slightly according to temperature shown below. Use this as a reference.
Water
Physical property
value
Temperature
Density
ρ
[kg/L]
Specific heat C
[J/(kg·K)]
Conventional units
Weight volume ratio
[kgf/L]
Specific heat C [cal/(kgf·°C)]
5°C1.00 4.2 x 1031.00 1 x 103
10°C1.00 4.19 x 1031.00 1 x 103
15°C1.00 4.19 x 1031.00 1 x 103
20°C1.00 4.18 x 1031.00 1 x 103
25°C1.00 4.18 x 1031.00 1 x 103
30°C1.00 4.18 x 1031.00 1 x 103
35°C0.99 4.18 x 1030.99 1 x 103
40°C0.99 4.18 x 1030.99 1 x 103
15% Ethylene Glycol Aqueous Solution
Physical property
value
Temperature
Density
ρ
[kg/L]
Specific heat C
[J/(kg·K)]
Conventional units
Weight volume ratio
[kgf/L]
Specific heat C [cal/(kgf·°C)]
5°C1.02 3.91 x 1031.02 0.93 x 103
10°C1.02 3.91 x 1031.02 0.93 x 103
15°C1.02 3.91 x 1031.02 0.93 x 103
20°C1.01 3.91 x 1031.01 0.93 x 103
25°C1.01 3.91 x 1031.01 0.93 x 103
30°C1.01 3.91 x 1031.01 0.94 x 103
35°C1.01 3.91 x 1031.01 0.94 x 103
40°C1.01 3.92 x 1031.01 0.94 x 103
*
Shown above are reference values. Contact circulating fluid supplier for details.
Example of conventional units (Reference)
Heat quantity by cooled substance (per unit time)
Q
: Unknown [cal/h] →[W]
Cooled substance : Water
Cooled substance weight m
: (= ρx V) [kgf]
Cooled substance weight volume ratio : 1 [kgf/L]
Cooled substance total volume V : 300 [L]
Cooled substance specific heat C
: 1.0 x 103[cal/(kgf·°C)]
Cooled substance temperature when cooling begins
T0
: 32 [°C]
Cooled substance temperature after t hour
Tt
: 20 [°C]
Cooling temperature difference iT : 12 [°C] (= T0– Tt)
Cooling time it: 15 [min]
Conversion factor: hours to minutes : 60 [min/h]
Conversion factor: kcal/h to kW : 860 [(cal/h)/W]
Q = =
=
≈16744 [W] = 16.7 [kW]
Cooling capacity = Considering a safety factor of 20%,
16.7 [kW] x 1.2 =
m x C x (T0– Tt)
it x 860
x V x 60 x C x iT
it x 860
1 x 300 x 60 x 1.0 x 103x 12
15 x 860
20 [kW]
*
This is the calculated value by changing the fluid temperature only.
Thus, it varies substantially depending on the water bath or piping shape.
13
HRS400 Series
Water bath
V
After 15 minutes, cool 32°C down to 20°C.
20°C
Q x t: Heat capacity [kJ]
Thermo-chiller

Design
Warning
1. This catalog shows the specifications of a single
unit.
1) Check the specifications of the single unit (contents of this
catalog) and thoroughly consider the adaptability between
the customer’s system and this unit.
2) Although a protection circuit as a single unit is installed,
prepare a drain pan, water leakage sensor, discharge air
facility, and emergency stop equipment, depending on the
customer’s operating conditions. Also, the customer is
requested to carry out a safety design for the whole system.
2. When attempting to cool areas that are open to the
atmosphere (tanks, pipes), plan your piping system
accordingly.
When cooling open-air external tanks, arrange the piping so
that there are coil pipes for cooling inside the tanks and to
carry back the entire flow volume of circulating fluid that is
released.
3. Use non-corrosive material for circulating fluid con-
tact parts.
Using corrosive materials such as aluminum or iron for fluid
contact parts such as piping may cause clogging or leakage in
the circulating fluid circuit. Provide protection against corrosion
when you use the product.
Selection
Warning
Model selection
When selecting a thermo-chiller model, the amount of heat
generation from the user’s equipment must be known. Obtain this
value, referring to “Cooling Capacity Calculation” on pages 12
and 13 before selecting a model.
Handling
Warning
Thoroughly read the operation manual.
Read the operation manual completely before operation, and
keep the manual where it can be referred to as necessary.
Operating Environment/Storage Environment
Warning
1. Do not use in the following environment as it will
lead to a breakdown.
1) In locations where water vapor, salt water, and oil may
splash on the product.
2) In locations where there are dust and particles.
3) In locations where corrosive gases, organic solvents,
chemical fluids, or flammable gases are present. (This
product is not explosion proof.)
4) In locations where the ambient temperature exceeds the
limits as mentioned below.
During transportation/storage: –15°C to 50°C (But as long
as water or circulating fluid
are not left inside the pipings)
Operating Environment/Storage Environment
Warning
During operation: –5°C to 45°C
∗
When the ambient tempera-
ture or circulating fluid tem-
perature is 10°C or below,
use the circulating fluid spec-
ified in "Operation at low am-
bient temperature or low cir-
culating fluid temperature".
5) In locations where condensation may occur.
6) In locations which receive direct sunlight or radiated heat.
7) In locations where there is a heat source nearby and the
ventilation is poor.
8) In locations where temperature substantially changes.
9) In locations where strong magnetic noise occurs.
(In locations where strong electric fields, strong magnetic
fields and surge voltage occur.)
10) In locations where static electricity occurs, or conditions
which make the product discharge static electricity.
11) In locations where high frequency occurs.
12)
In locations where damage is likely to occur due to lightning.
13) In locations at an altitude of 3000 m or higher (Except
during storage and transportation)
∗
For altitudes of 1000 m or higher
Because of lower air density, the heat radiation efficiencies
of the devices in the product will be lower in the location at
an altitude of 1000 m or higher. Therefore, the maximum
ambient temperature to use and the cooling capacity will
lower according to the descriptions in the table below.
Select the thermo-chiller considering the descriptions.
q
Upper limit of ambient temperature: Use the product in ambient
temperature of the described value or lower at each altitude.
wCooling capacity coefficient: The product's cooling
capacity will lower to one that multiplied by the
described value at each altitude.
14) In locations where strong impacts or vibrations occur.
15) In locations where a massive force strong enough to
deform the product is applied or a weight from a heavy
object is applied.
16)
In locations where there is not sufficient space for maintenance.
17)
In locations where liquid that exceeds the conditions required
for the degrees of protection IPX4 may splash on the product.
18)
Insects or plants may enter the unit.
2. The product is not designed for clean room usage. It
generates particles internally.
Caution
For the product operation in UL compliant conditions,
use the product in the environment shown below:
Environment at an altitude of 2000 meters or less
Environment at an ambient temperature of 40°C or less
Environment at a pollution degree of 2 or less
Location where the ambient humidity is within the following range:
During transportation or storage: 15% to 85% (No condensation)
During operation: 30% to 70% (No condensation)
Altitude [m]
qUpper limit of ambient temperature [°C]
wCooling capacity coefficient
Less than 1000 m 45 1.00
Less than 1500 m 42 0.85
Less than 2000 m 38 0.80
Less than 2500 m 35 0.75
Less than 3000 m 32 0.70
Be sure to read this before handling the products. For safety instructions and
temperature control equipment precautions, refer to the “Handling Precautions for SMC
Products” and the “Operation Manual” on the SMC website: https://www.smcworld.com
HRS400 Series
Specific Product Precautions 1
14

Operation at Low Ambient Temperature or
Low Circulating Fluid Temperature
Caution
1. Circulating fluid
In order to avoid freezing of the circulating fluid, use aqueous
solution of ethylene glycol.
Circulating fluid temperature[°C]
Recommended circulating fluids
10 to 35
Tap water, ethylene glycol aqueous solution 15 (wt)%
5 to 10 Ethylene glycol aqueous solution 15 (wt)%
2. And following instructions must be executed. If fol-
lowing instructions are not executed, not only Ther-
mo-chiller alarm will be generated, but also damage
of the product can result.
Power has to be supplied to the Thermo-chiller all the time.
Turn on anti-freezing function all the time.
When the power supply to the Thermo-chiller is stopped for a
long period of time, discharge all the circulating fluid in the
Thermo-chiller and customer’s device and piping. When the
Thermo-chiller is refilled with the circulating fluid, supply the
fluid at normal temperature.
Transportation/Carriage/Movement
Warning
1.
This product will require an acceptance with the product
not unloaded from the truck, and the customer will need
to unload the product by himself. Prepare a forklift.
The product will be delivered in the packaging shown below.
Polyester band
Cardboard box
Forklift insertion side
Wooden skid
Forklift insertion side
Less than
150 mm
Less than
150 mm
<When packaged>
Model
Weight [kg]
Dimensions [mm]
HRS400-Am-46-m410
Height 1650 x Width 1060 x Depth 2020
HRS400-Am-46-A 424
HRS400-Am-46-D 411
HRS400-Am-46-K
Ambient temperature [°C]
Recommended circulating fluids
10 to 45
Tap water, ethylene glycol aqueous solution 15 (wt)%
−5 to 10 Ethylene glycol aqueous solution 15 (wt)%
2. Transporting with forklift
1) A licensed driver should drive the forklift.
2) The proper place to insert the tines of the forklift differs
depending on the model of cooler. Check the insert position,
and be sure to drive the fork in far enough for it to come out
the other side.
3) Be careful not to bump the fork to the cover panel or piping
ports.
3. Hanging transportation
1) Crane manipulation and slinging work should be done by an
eligible person.
2) Do not grip the piping on the right side or the handles of the
panel.
3) When hanging by the eye bolts, be sure to use a 4-point
hanging method. For the hanging angle, use caution regarding
the position of the center of gravity and hold it within 60°.
Hanging position
60°or less
Less than 150 mm
Forklift
insertion side
Less than 150 mm
Less than 150 mmForklift
insertion side
Less than 150 mm
(When using option A/With caster adjuster-foot and
optional accessories/Caster adjuster-foot kit KS004)
4. Transporting with casters
1) This product is heavy and should be moved by at least two
people.
2) Do not grip the piping port on the right side or the handles
of the panel.
3) When transporting using a forklift, be sure not to let it hit the
casters or adjusters, and drive the fork all the way through
until it comes out the other side.
4) Do not get across steps with casters.
Caution
If this product is to be transported after delivery, please
use the original packaging the product was delivered
in. If other packaging is to be used, carefully package
the product so as to prevent the product from incurring
any damage during transport.
Transportation/Carriage/Movement
Warning
Be sure to read this before handling the products. For safety instructions and
temperature control equipment precautions, refer to the “Handling Precautions for SMC
Products” and the “Operation Manual” on the SMC website: https://www.smcworld.com
HRS400 Series
Specific Product Precautions 2
15

Piping
Caution
1. Regarding the circulating fluid piping, consider
carefully the suitability for temperature and
circulating fluid.
If the operating performance is not sufficient, the pipings may burst
during operation. Also, the use of corrosive materials such as alu-
minum or iron for fluid contact parts, such as piping, may not only
lead to clogging or leakage in the circulating fluid circuit but also
refrigerant leakage and other unexpected problems. Provide
protection against corrosion when you use the product.
2.
Select the piping port size which can exceed the rated flow.
For the rated flow, refer to the pump capacity table.
3. When tightening at the drain port of this product,
use a pipe wrench to clamp the connection ports.
4. Supply water pressure to the automatic fluid fill port
of this product should be 0.2 to 0.5 MPa.
This product has a built-in ball (float) tap. If you attach it to the
faucet of a sink, etc. it will automatically supply water to the
rated fluid level of the tank (halfway between HIGH and LOW.)
If the water supply pressure is too high, the pipes may burst
during use. Proceed with caution.
5.
Ensure that piping is connected to the overflow port
so that the circulating fluid can be exhausted to the
drainage pit when the fluid level in the tank increases.
6. For the circulating fluid piping connection, install a
drain pan and wastewater collection pit just in case
the circulating fluid may leak.
7. This product series are constant-temperature fluid
circulating machines with built-in tanks.
Do not install equipment on your system side such as pumps
that forcibly return the circulating fluid to the unit. Also, if you
attach an external tank that is open to the air, it may become
impossible to circulate the circulating fluid. Proceed with caution.
Mounting/Installation
Warning
Do not place heavy objects on top of this product, or step on it.
The external panel can be deformed and danger can result.
Caution
1. Install on a rigid floor which can withstand this
product’s weight.
2. Secure with bolts, anchor bolts, etc.
3. Refer to the operation manual for this product, and
secure an installation space that is necessary for
the maintenance and ventilation.
1.
The air-cooled type product exhausts heat using the fan that is
mounted to the product. If the product is operated with insuffi-
cient ventilation, ambient temperature may exceed 45°C, and
this will affect the performance and life of the product. To pre-
vent this ensure that suitable ventilation is available (see below).
2. For installation indoors, ventilation ports and a ventilation fan
should be equipped as needed.
Required installation space
for ventilation and
maintenance
Ventilation
2000 mm or more
800 mm or more
800 mm or more
800 mm or more
400 mm
or more
3.
If it is impossible to exhaust heat from the installation area in-
doors, or when the installation area is conditioned, provide a
duct for heat exhaustion to the air outlet port of this product for
ventilation. Do not mount the inlet of the duct (flange) directly to
the air vent of the product, and keep a space larger than the di-
ameter of the duct. Additionally, consider the resistance of the
duct when making the air vent port for the duct.
<Heat radiation amount/Required ventilation rate>
Heat
radiation
amount
[kW]
Required ventilation rate [m3/min]
Differential temp. of 3°C
between inside and outside
of installation area
Differential temp. of 6°C
between inside and outside
of installation area
Approx. 52 865 435
4. When using the product at a low ambient tempera-
ture (10°C or less), refer to “Operation at low ambi-
ent temperature or low circulating fluid tempera-
ture” (page 15).
Be sure to read this before handling the products. For safety instructions and
temperature control equipment precautions, refer to the “Handling Precautions for SMC
Products” and the “Operation Manual” on the SMC website: https://www.smcworld.com
HRS400 Series
Specific Product Precautions 3
16

Warning
Grounding should never be connected to a water line,
gas line or lightning rod.
Caution
1. Power supply and communication cables should be
prepared by customer.
2. Provide a stable power supply which is not affected
by surge or distortion.
If the voltage increase ratio (dV/dt) at the zero cross should
exceed 40 V/200 msec., it may result in malfunction.
3. This product is installed with a breaker with the
following operating characteristics.
For the customer’s equipment (inlet side), use a breaker whose
operating time is equal to or longer than the breaker of this
product. If a breaker with shorter operating time is connected,
the customer’s equipment could be cut off due to the inrush
current of the motor of this product.
dV
dV
dt
dt
= Voltage increase ratio
Time
Voltage
4 h
2 h
1 h
30 min
20 min
14 min
10 min
6 min
4 min
2 min
1 min
30 s
20 s
10 s
5 s
2 s
1 s
0.5 s
0.2 s
0.1 s
0.05 s
0.02 s
0.01 s
100 135 200 300 400 500 600 700 1000 1500 2000 3000 4000
Current (% for chiller main breaker volume)
Operating time
Min.
Max.
Electrical Wiring Electrical Wiring
Caution
4. For the product operation in the UL compliant
conditions, the conditions shown below must be
satisfied:
Use power supply of overvoltage category 2*
For power supply cable, it is to be properly prepared by the
customer in accordance with National Electrical Code and
Canadian Electrical Code.
Bending radius of the power supply cable must be 38.1 mm
or more.
*When using a power supply in the overvoltage category 3,
take measures such as mounting an isolation transformer
between the product and the power supply or keep the
transient overvoltage of the power supply to 2200 V or
less by using a varistor, etc.
Circulating Fluid
Caution
1. Avoid oil or other foreign matter entering the
circulating fluid.
2. When water is used as a circulating fluid, use tap
water that conforms to the appropriate water quality
standards.
Use tap water that conforms to the standards shown below (includ-
ing water used for dilution of ethylene glycol aqueous solution).
Tap Water (as a Circulating Fluid) Quality Standards
The Japan Refrigeration and Air Conditioning Industry Association
JRA GL-02-1994 “Cooling water system – Circulation type – Make-up water”
Item Unit Standard value
Influence
Corrosion
Scale
generation
Standard item
pH (at 25°C) — 6.0 to 8.0 v v
Electric conductivity (25°C)
[mS/cm]
100*1to 300*1v v
Chloride ion (Cl–) [mg/L] 50 or less v
Sulfuric acid ion (SO42–) [mg/L] 50 or less v
Acid consumption amount (at pH4.8)
[mg/L] 50 or less v
Total hardness [mg/L] 70 or less v
Calcium hardness (CaCO3)
[mg/L] 50 or less v
Ionic state silica (SiO2) [mg/L] 30 or less v
Reference item
Iron (Fe) [mg/L] 0.3 or less v v
Copper (Cu) [mg/L] 0.1 or less v
Sulfide ion (S2–) [mg/L]
Should not be detected.
v
Ammonium ion (NH4+) [mg/L] 0.1 or less v
Residual chlorine (Cl) [mg/L] 0.3 or less v
Free carbon (CO2) [mg/L] 4.0 or less v
*1 In the case of [MΩ·cm], it will be 0.003 to 0.01.
v: Factors that have an effect on corrosion or scale generation.
Even if the water quality standards are met, complete prevention of corrosion
is not guaranteed.
3. Use an ethylene glycol aqueous solution that does
not contain additives such as preservatives.
4.
Refer to "Operation at low ambient temperature or low
circulating fluid temperature" (page 15) for the con-
centration of the ethylene glycol aqueous solution.
5. When deionized water is used, the electric conductivity
should be 1 mS/cm or higher (Electric resistivity: 1
MΩ·cm or lower).
Be sure to read this before handling the products. For safety instructions and
temperature control equipment precautions, refer to the “Handling Precautions for SMC
Products” and the “Operation Manual” on the SMC website: https://www.smcworld.com
HRS400 Series
Specific Product Precautions 4
17

Refrigerant with GWP reference
Refrigerant
Global warming potential (GWP)
Regulation (EU) No 517/2014
(Based on the IPCC AR4)
Revised Fluorocarbons
Recovery and Destruction
Law (Japanese law)
R134a 1,430 1,430
R404A 3,922 3,920
R407C 1,774 1,770
R410A 2,088 2,090
*This product is hermetically sealed and contains fluorinated
greenhouse gases (HFC). When this product is sold on the market
in the EU after January 1, 2017, it needs to be compliant with the
quota system of the F-Gas Regulation in the EU.
*See specification table for refrigerant used in the product.
Operation
Warning
1. Confirmation before operation
1)
The fluid level of a tank should be within the specified range of “HIGH” and “LOW.”
When exceeding the specified level, the circulating fluid will overflow.
2) Remove the air.
Conduct a trial operation, looking at the fluid level.
Since the fluid level will go down when the air is removed
from the customer’s piping system, supply water once again
when the fluid level is reduced. When there is no reduction
in the fluid level, the job of removing the air is completed.
Pump can be operated independently.
2. Confirmation during operation
Check the circulating fluid temperature.
The operating temperature range of the circulating fluid is be-
tween 5 and 35°C.
When the amount of heat generated from the customer’s equipment
is greater than the product’s capability, the circulating fluid tempera-
ture may exceed this range. Use caution regarding this matter.
3. Emergency stop method
When an abnormality is confirmed, stop the machine immedi-
ately. After the machine has stopped, make sure to turn off the
breaker of the customer’s equipment (on the upstream side).
Operation Restart Time/Operation and Suspension Frequency
Caution
1. Wait five minutes or more before restarting operation
after it has been stopped. If the operation is restarted
within five minutes, the protection circuit may acti-
vate and the operation may not start properly.
2. Operation and suspension frequency should not ex-
ceed 10 times per day. Frequently switching be-
tween operation and suspension may result in the
malfunction of the refrigeration circuit.
Protection Circuit
Caution
If operating in the below conditions, the protection
circuit will activate and an operation may not be
performed or will stop.
Power supply voltage is not within the rated voltage range of ±10%.
In case the water level inside the tank is reduced abnormally.
Circulating fluid temperature is too high.
Compared to the cooling capacity, the heat generation amount
of the customer’s equipment is too high.
Ambient temperature is over 45°C.
Ventilation hole is clogged with dust or dirt
Maintenance
Caution
<Periodical inspection every one month>
Clean the ventilation hole.
If the dustproof filter of water-cooled type product becomes clogged
with dust or debris, a decline in cooling performance can result.
In order to avoid deforming or damaging the dustproof filter, clean
it with a long-haired brush or air gun.
Maintenance
Caution
<Periodical inspection every three months>
Inspect the circulating fluid.
1. When using tap water or deionized water
Replacement of circulating fluid
Failure to replace the circulating fluid can lead to the
development of bacteria or algae. Replace it regularly
depending on your usage conditions.
2. When using ethylene glycol aqueous solution
Use a concentration meter to confirm that the concentration
does not exceed 15%.
Dilute or add as needed to adjust the concentration.
<Periodical inspection during the winter season>
1. Make water-removal arrangements beforehand.
If there is a risk of the circulating fluid freezing when the
product is stopped, release the circulating fluid in advance.
2. Consult a professional.
This product has an “anti-freezing function”, “warming-up
function”, and “anti-snow coverage function.” Read the
operation manual carefully, and if any additional anti-freezing
function (e.g. tape heater) is needed, ask for it from the vendor.
Be sure to read this before handling the products. For safety instructions and
temperature control equipment precautions, refer to the “Handling Precautions for SMC
Products” and the “Operation Manual” on the SMC website: https://www.smcworld.com
HRS400 Series
Specific Product Precautions 5
18

Akihabara UDX 15F,
4-14-1, Sotokanda, Chiyoda-ku, Tokyo 101-0021, JAPAN
Phone: 03-5207-8249 Fax: 03-5298-5362
https://www.smcworld.com
© 2022 SMC Corporation All Rights Reserved
Specifications are subject to change without prior notice
and any obligation on the part of the manufacturer.
D-G
Safety Instructions
Be sure to read the “Handling Precautions for SMC Products” (M-E03-3) and “Operation Manual” before use.
This manual suits for next models
4
Table of contents
Other SMC Networks Temperature Controllers manuals
Popular Temperature Controllers manuals by other brands

Omron
Omron E5GC-6 Series instruction manual
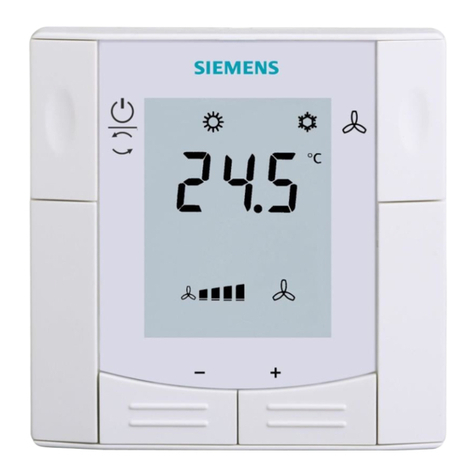
Siemens
Siemens RDF300 Series Documentation
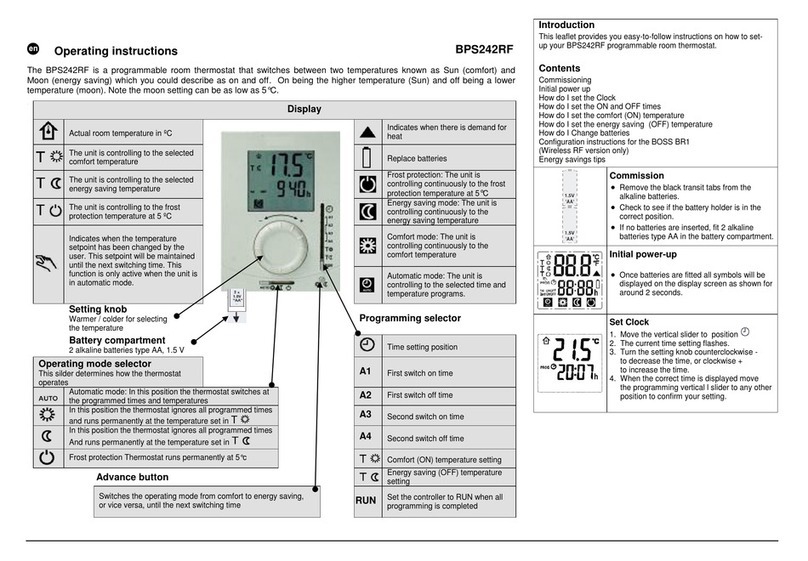
Siemens
Siemens BPS242RF operating instructions
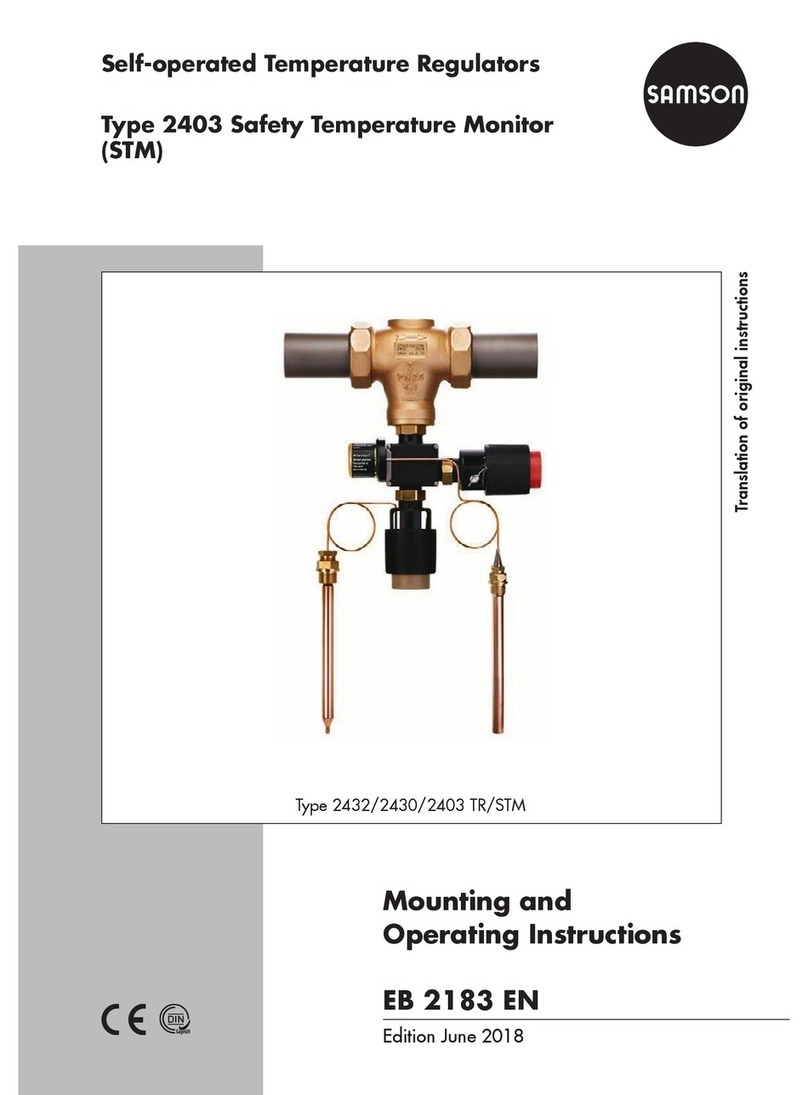
Samson
Samson 2432 Mounting and operating instructions
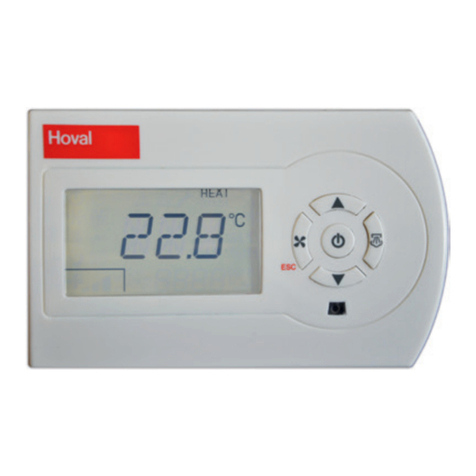
Hoval
Hoval EasyTronic EC Operation
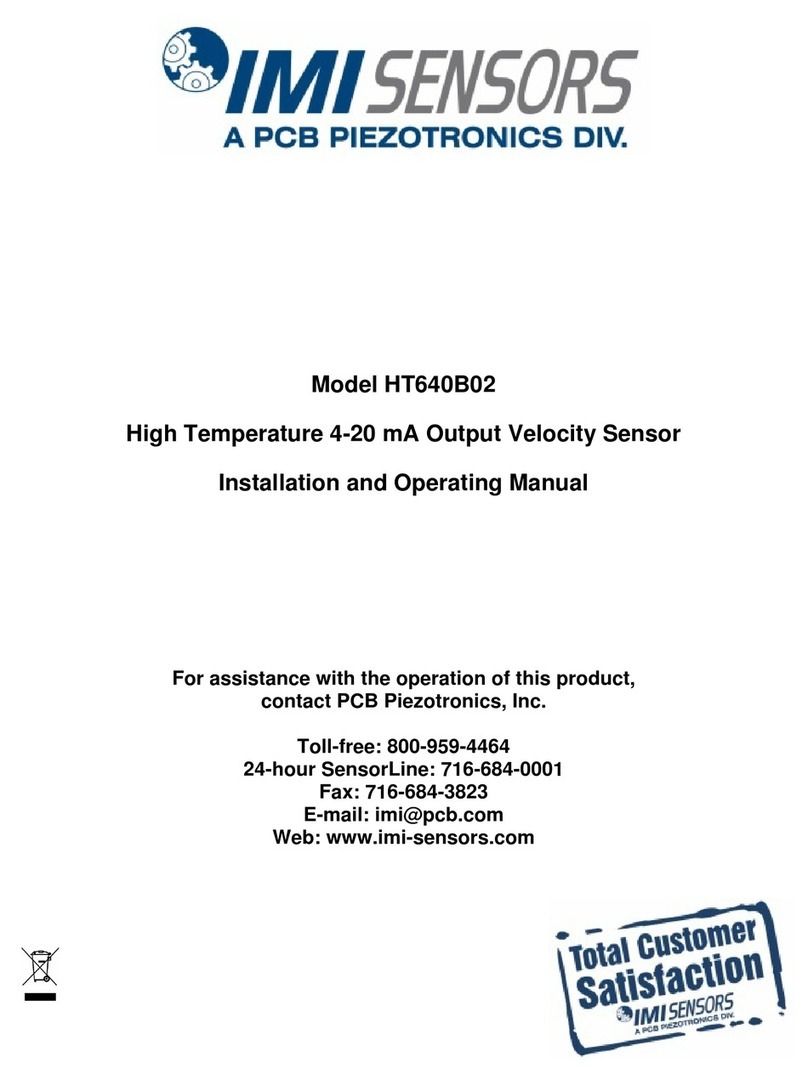
PCB Piezotronics
PCB Piezotronics IMI SENSORS HT640B02 Installation and operating manual
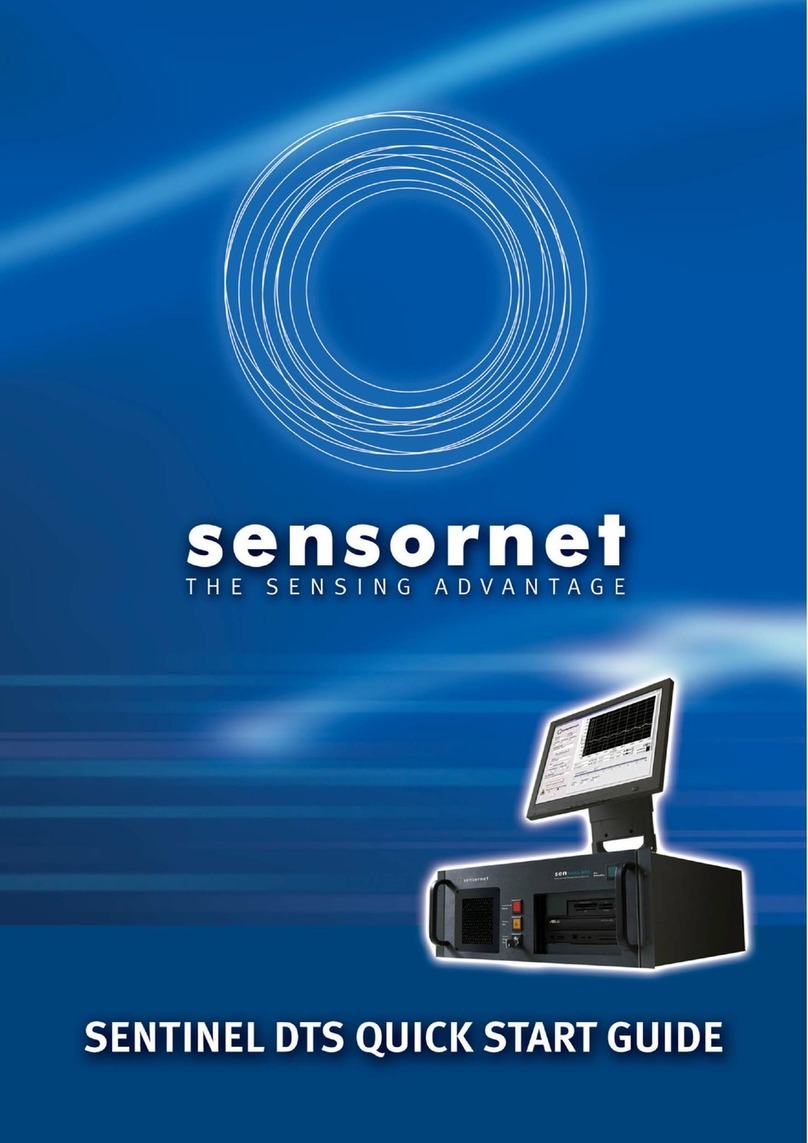
Sensornet
Sensornet Sentinel DTS quick start guide
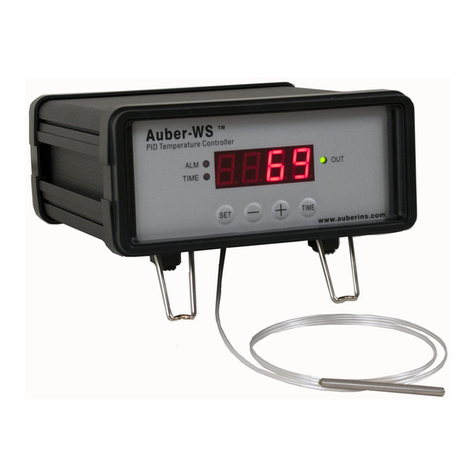
Auber Instruments
Auber Instruments WS-1500C Operation & instruction manual
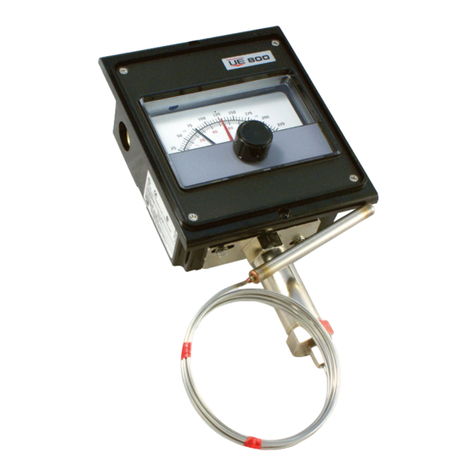
UE
UE 800 Series Installation and maintenance instructions
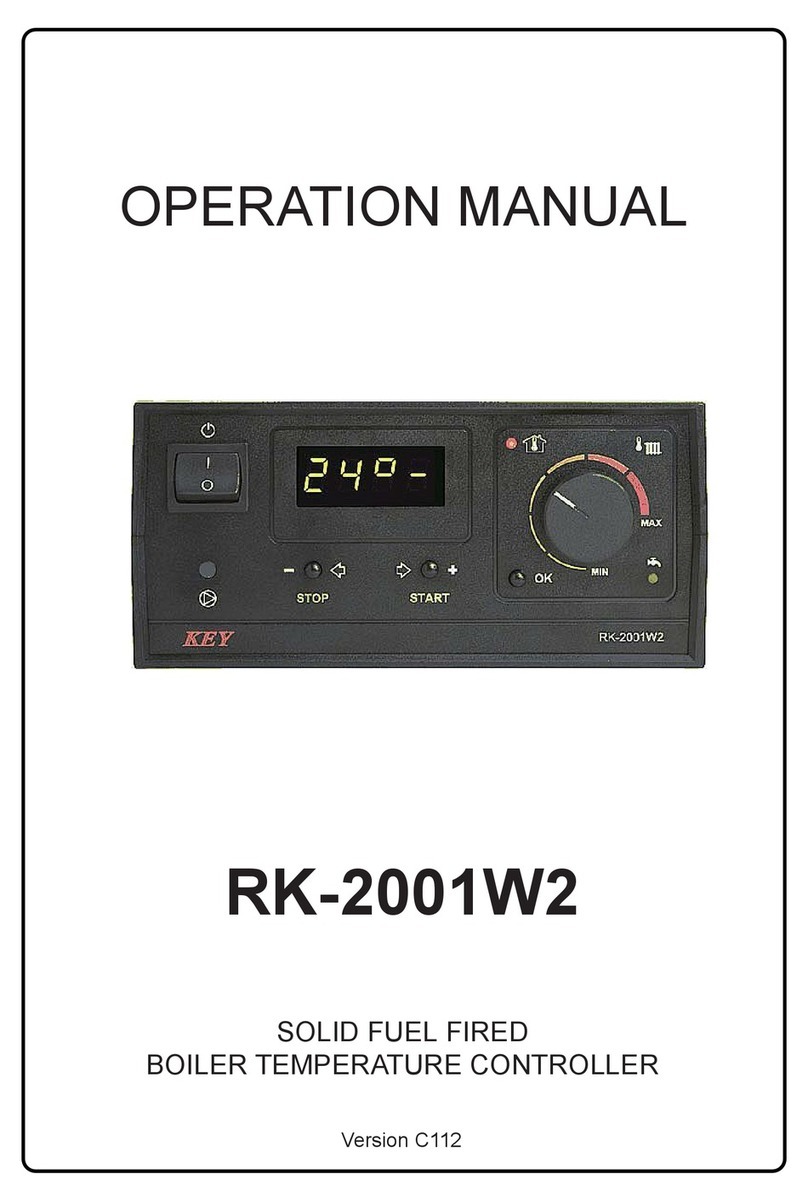
KEY
KEY RK-2001W2 Operation manual
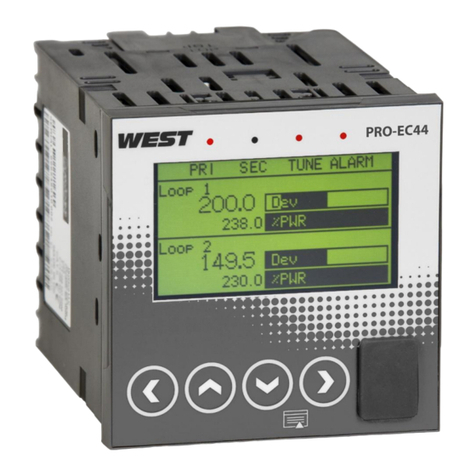
West Control Solutions
West Control Solutions Pro-EC44 user guide
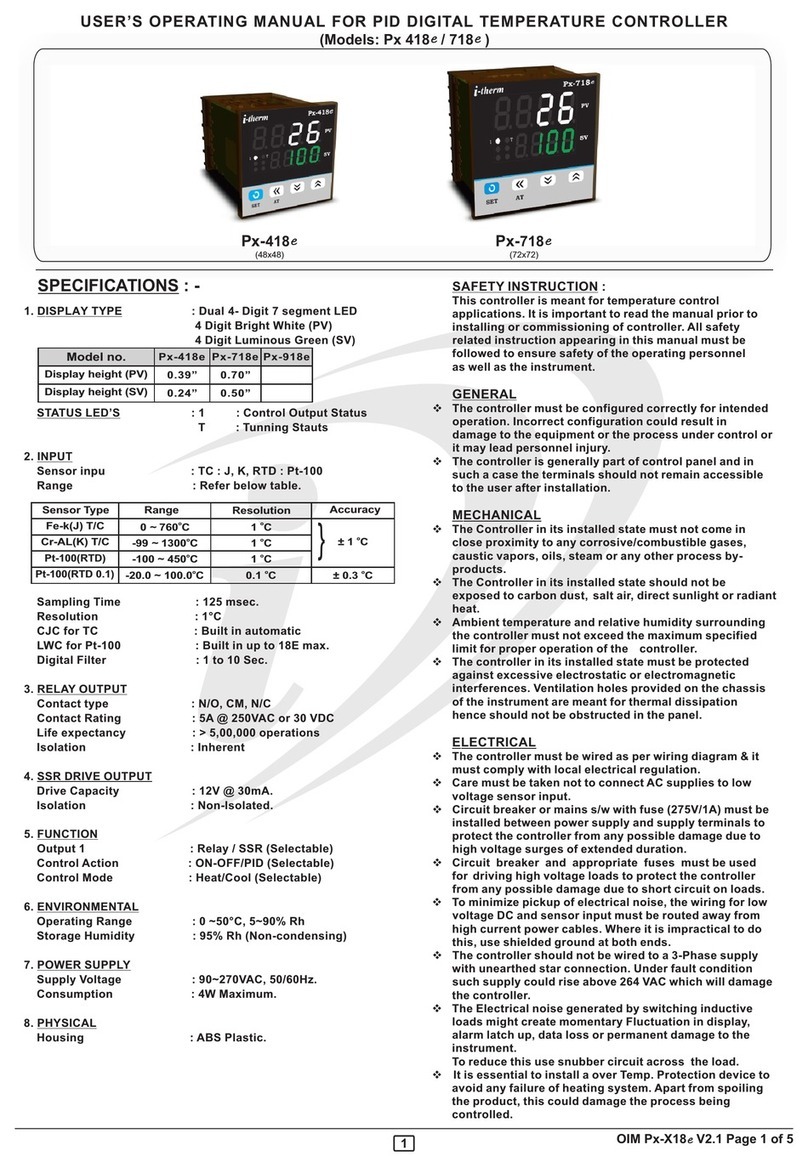
i-therm
i-therm Px-418e User's operating manual