SME AC-M1 User manual

AC Induction Motor Controller
U
US
SE
ER
R
M
MA
AN
NU
UA
AL
L
(
(R
Re
ev
v.
.
3
3.
.0
0:
:
M
Ma
ar
rc
ch
h
2
20
01
16
6)
)
M
Mo
od
de
el
l
A
AC
C-
-M
M1
1
SME S.p.A.
Via della Tecnica, n° 40
36071 Arzignano (VI) - ITALY
Phone:+39 (0444) 470511
Fax: +39 (0444) 451803
E-mail: info@grupposme.com
www.grupposme.com

ACM1_TAU_UserManual_En
Page 2 of 35
SME s.p.a. Via della Tecnica 40 Z.I.
36071 ARZIGNANO (VI) ITALY
Phone +39 0444 470511 - Fax +39 0444 451803
Table of Contents
Table of Contents .............................................................................................................................................. 2
1. Introduction .............................................................................................................................................. 4
1.1 About SME Company ....................................................................................................................... 4
1.2 About this manual............................................................................................................................ 4
1.3 About warning, caution and information notices............................................................................ 4
1.4 Product warranty information ......................................................................................................... 5
1.5 How to find us .................................................................................................................................. 5
2. AC SmartMotion AC-M1 Overview ........................................................................................................... 6
2.1 Product description.......................................................................................................................... 6
2.1.1 Product Indication Label.............................................................................................................. 7
2.2 General Specifications...................................................................................................................... 8
2.3 Electrical Specifications.................................................................................................................... 8
2.3.1 Input and Output Ratings ............................................................................................................ 8
2.3.2 Signal: Inputs and Outputs........................................................................................................... 9
2.3.3 Interfaces ................................................................................................................................... 11
2.3.4 EMC............................................................................................................................................ 11
2.3.5 Safety ......................................................................................................................................... 11
2.4 Operating Environment Specifications .......................................................................................... 11
3. Installation and Wiring............................................................................................................................ 12
3.1 Controller ....................................................................................................................................... 13
3.2 Power Terminals ............................................................................................................................ 17
3.3 Main Contactor .............................................................................................................................. 18
3.4 Fuse ................................................................................................................................................ 19
3.5 Signal .............................................................................................................................................. 20
3.5.1 Digital Inputs.............................................................................................................................. 21

ACM1_TAU_UserManual_En
Page 3 of 35
SME s.p.a. Via della Tecnica 40 Z.I.
36071 ARZIGNANO (VI) ITALY
Phone +39 0444 470511 - Fax +39 0444 451803
3.5.2 Analog Inputs............................................................................................................................. 22
3.5.3 Driver Outputs (PWM)............................................................................................................... 23
3.5.4 Digital Outputs (ON/OFF)........................................................................................................... 24
3.5.5 Speed Sensor Inputs .................................................................................................................. 25
3.5.6 Thermal Probe ........................................................................................................................... 26
3.5.7 Serial .......................................................................................................................................... 27
3.5.8 CAN Network ............................................................................................................................. 28
3.6 SME external devices description .................................................................................................. 29
3.6.1 Encoder...................................................................................................................................... 29
3.6.2 Displays ...................................................................................................................................... 29
4. Graphical Interface ................................................................................................................................. 30
5. Diagnostic and troubleshooting.............................................................................................................. 31
5.1 Overview ........................................................................................................................................ 31
6. EMC suggestions..................................................................................................................................... 32
6.1 General overview on EMC.............................................................................................................. 32
6.2 EM emissions ................................................................................................................................. 32
6.3 Immunity to EM disturbances........................................................................................................ 33
Appendix B: Document History ....................................................................................................................... 34

ACM1_TAU_UserManual_En
Page 4 of 35
SME s.p.a. Via della Tecnica 40 Z.I.
36071 ARZIGNANO (VI) ITALY
Phone +39 0444 470511 - Fax +39 0444 451803
1. Introduction
1.1 About SME Company
SME group, founded in 1974, is a high technology company, manufacturer of electronic controllers
and related products for application in battery powered vehicles, particularly forklift trucks and
specialized in the development of AC power controllers.
The group provides intelligent and innovative solutions to satisfy market requirements, achieving
worldwide customer satisfaction.
SME group is able to offer a complete motion system for the different industrial lift truck ranges
guaranteeing a high and safe performance customized to the client's requirements.
1.2 About this manual
This manual presents important information on configuring traction or pump systems using the AC
SmartMotion AC-M1 as well as details on sizing and selecting system components, options and
accessories in an electrically powered vehicle.
This version replaces all previous existing versions of the manual, if any.
1.3 About warning, caution and information notices
Special attention must be paid to the information presented in Warning, Caution and other kinds
of information notices when they appear in this manual.
Failure to follow those recommendations may result in dangerous situations or in damages to the
components, for which SME will not respond.
Warnings. A Warning informs the user of a hazard or a potential hazard
which could result in serious or fatal injury if the precautions or instructions
given in the warning notice are not observed.
Cautions. A caution informs the reader of a hazard or a potential hazard
which could result in a serious damage to the appliance.
Information Notices. An information notice contains additional, not
essential pieces of information to complete or to clarify the meaning of the
paragraph they are placed into.
User Manual Reference. A User Manual Reference informs the user to look
up specified user manual for more details.
Interactive Documentation Tips: An advice about where to find the related
section in the Interactive Documentation

ACM1_TAU_UserManual_En
Page 5 of 35
SME s.p.a. Via della Tecnica 40 Z.I.
36071 ARZIGNANO (VI) ITALY
Phone +39 0444 470511 - Fax +39 0444 451803
1.4 Product warranty information
SME offers a two-year warranty on all the products, unless a different agreement has been put in
place. Refer to the sales agreement or contract under which the AC SmartMotion was purchased
for a complete statement of the product warranty.
1.5 How to find us
For any information on commercial and technical issues, please contact either your dealer or SME
at the following address for your region:
SME S.p.A. (Europe - Headquarters)
Via della Tecnica, n°40
36071 Arzignano (VI), Italy
Phone:+39 (0444) 470511
Fax: +39 (0444) 451803
E-mail: info@sme-group.com
support@sme-group.com
SME (Shangai) Co. Ltd (Asia)
No 2, Bldg. 8, 1st floor,
388, Xujing Shuanglian Road
201702 Qingpu District
Shanghai, China
Phone: +86 (021) 6025.3818
Fax: +86 (021) 59501502
E-mail: info@sme-group.com
SME Drives Inc (America)
1404 King St N, Box 154,
St Jacobs
Ontario, Canada
N0B 2N0
Phone: +1 (519) 591-0965
E-mail: info@sme-drives.com

ACM1_TAU_UserManual_En
Page 6 of 35
SME s.p.a. Via della Tecnica 40 Z.I.
36071 ARZIGNANO (VI) ITALY
Phone +39 0444 470511 - Fax +39 0444 451803
2. AC SmartMotion AC-M1 Overview
Figure 1 - AC-M1
2.1 Product description
The AC-M1 Controller is designed to control AC motors.
Being based on high reliable DCB technology and exceptionally stable ITC Control Algorithm, AC-
M1 Controller is a revolutionary and high quality solution for medium power applications.
The product is suitable for the following range of applications: Counterbalanced Lift Trucks,
Cleaning Machines, Golf cars, Aerial Lifts, Tractors, Utility Vehicles, Tow Trucks.

ACM1_TAU_UserManual_En
Page 7 of 35
SME s.p.a. Via della Tecnica 40 Z.I.
36071 ARZIGNANO (VI) ITALY
Phone +39 0444 470511 - Fax +39 0444 451803
2.1.1 Product Indication Label
The product label shows important data
regarding the specific product.
The meaning of each field is described in the table below.
Field
Description
Model
Product description.
Type Code
SME code for the specific product.
Rating Data
It contains the indication of the input voltages and the output currents supplied
by the product.
Batch Number
Production batch number (the same value as in barcode below).
Lot
Production Month and Year

ACM1_TAU_UserManual_En
Page 8 of 35
SME s.p.a. Via della Tecnica 40 Z.I.
36071 ARZIGNANO (VI) ITALY
Phone +39 0444 470511 - Fax +39 0444 451803
2.2 General Specifications
Motor Type: AC Asynchronous 3-Phase
Braking: Regenerative
Modulation: PWM (Pulse Width Modulation)
Switching Frequency: 9kHz
Low RDS,on MOSFET
16 bits DSP controlling 1 AC motor
Integrated Hall Effect Current Sensors
2.3 Electrical Specifications
2.3.1 Input and Output Ratings
Model Chart for 24V version
Model Name
AC Inverter Max Arms(2’)
Max Power(2’) at 24V
AC-M1 24V 350A
350 Arms
9.7kVA
AC-M1 24V 450A
450 Arms
12.5 kVA
Model Chart for 36/48V version
Model Name
AC Inverter Max Arms(2’)
Max Power (2’) at 48V
AC-M1 36/48V 375A
375 Arms
20.8 kVA
AC-M1 36/48V 500A
500 Arms
27.5 kVA
Model Chart for 72/80V version
Model Name
AC Inverter Max Arms(2’)
Max Power (2’) at 80V
AC-M1 72/80V 350A
350 Arms
32.3 kVA
AC-M1 72/80V 450A
450 Arms
41.6 kVA

ACM1_TAU_UserManual_En
Page 9 of 35
SME s.p.a. Via della Tecnica 40 Z.I.
36071 ARZIGNANO (VI) ITALY
Phone +39 0444 470511 - Fax +39 0444 451803
2.3.2 Signal: Inputs and Outputs
Digital Inputs: 19
Analog Inputs: 6
Digital Outputs (ON/OFF): 2
Driver Outputs (PWM): 3
Motor Speed Sensor Inputs: 2 (A+B Channels)
Refer to following tables for a complete AC-M1 controller K1 and K2 connectors pin-out.
K1 connector pin-out for AC-M1 SPECIFICATIONS
Pin
Name
I/O
Specification
Typical Function
1
KEY SWITCH IN
Supply Input
Rated battery +25/-30%, 6Amax
Positive supply of the control section of
the AC-M1
2
DIGITAL IN 1
Digital Input
4mA pull-up, VL<=1V, VH>=3,5V
TO BE ASSIGNED
3
DIGITAL IN 2
Digital Input
4mA pull-up, VL<=1V, VH>=3,5V
TO BE ASSIGNED
4
DIGITAL IN 3
Digital Input
4mA pull-up, VL<=1V, VH>=3,5V
TO BE ASSIGNED
5
DIGITAL IN 4
Digital Input
4mA pull-up, VL<=1V, VH>=3,5V
TO BE ASSIGNED
6
DIGITAL IN 5
Digital Input
4mA pull-up, VL<=1V, VH>=3,5V
TO BE ASSIGNED
7
DIGITAL IN 6
Digital Input
4mA pull-up, VL<=1V, VH>=3,5V
TO BE ASSIGNED
8
DIGITAL OUT 1
Digital Output
Low side 0,5A
TO BE ASSIGNED
9
COIL RETURN
Supply Output
High side 5A max
Positive common
10
RS-232 RX
Com Input
-
Serial port
11
RS-232 TX
Com Output
-
Serial port
12
DIGITAL IN 7
Digital Input
4mA pull-up, VL<=1V, VH>=3,5V
TO BE ASSIGNED
13
DIGITAL IN 8
Digital Input
4mA pull-up, VL<=1V, VH>=3,5V
TO BE ASSIGNED
14
LIN IN/OUT
Com Input/Output
12mA pull-up
LIN display connection
15
CAN-H
Com Input/Output
CAN-bus
CAN H (No internal termination resistor)
16
DRIVER OUT 1
PWM Output
Low side 2A
TO BE ASSIGNED
17
DRIVER OUT 2
PWM Output
Low side 1,5A
TO BE ASSIGNED
18
I/O GROUND
-
-
Negative logic supply
19
DIGITAL OUT 2
Digital Output
Low side 1,5A
TO BE ASSIGNED
20
DRIVER OUT 3
PWM Output
Low side 1,5A (*)
TO BE ASSIGNED
21
+12V OUT
Supply Output
12V 300mAmax
12V supply
22
CAN GROUND
-
-
CAN- bus negative supply
23
CAN-L
Com Input/Output
CAN-bus
CAN L (No internal termination resistor)

ACM1_TAU_UserManual_En
Page 10 of 35
SME s.p.a. Via della Tecnica 40 Z.I.
36071 ARZIGNANO (VI) ITALY
Phone +39 0444 470511 - Fax +39 0444 451803
K2 connector pin-out for AC-M1 SPECIFICATIONS
Pin
Name
I/O
Specification
Function
1
+5V OUT
Supply Output
5V+/-5%, 200mAmax
5V supply
2
DIGITAL IN 9
Digital Input
20mA pull-up, VL<=1V, VH>=3,5V
TO BE ASSIGNED
3
DIGITAL IN 10
Digital Input
20mA pull-up, VL<=1V, VH>=3,5V
TO BE ASSIGNED
4
ENCODER 1 B
Peripheral Input
20mA pull-up, VL<=1V, VH>=3,5V
Quad encoder channel B
5
ENCODER 1 A
Peripheral Input
20mA pull-up, VL<=1V, VH>=3,5V
Quad encoder channel A
6
DIGITAL IN 11
Digital Input
4mA pull-up, VL<=1V, VH>=3,5V
TO BE ASSIGNED
7
DIGITAL IN 12
Digital Input
4mA pull-up, VL<=1V, VH>=3,5V
TO BE ASSIGNED
8
DIGITAL IN 13
Digital Input
4mA pull-up, VL<=1V, VH>=3,5V
TO BE ASSIGNED
9
I/O GROUND
-
-
Negative logic supply
10
MOTOR
THERMAL
PROBE 1
Analog Input
Pull-up
Motor temperature probe
11
MOTOR
THERMAL
PROBE 2
Analog Input
Pull-up
TO BE ASSIGNED
12
ANALOG IN 1
Analog Input
0/12V pull-down
TO BE ASSIGNED
13
ANALOG IN 2
Analog Input
0/12V pull-down
TO BE ASSIGNED
14
DIGITAL IN 14
Digital Input
4mA pull-up, VL<=1V, VH>=3,5V
TO BE ASSIGNED
15
DIGITAL IN 15
Digital Input
4mA pull-up, VL<=1V, VH>=3,5V
TO BE ASSIGNED
16
DIGITAL IN 16
Digital Input
4mA pull-up, VL<=1V, VH>=3,5V
TO BE ASSIGNED
17
DIGITAL IN 17
Digital Input
4mA pull-up, VL<=1V, VH>=3,5V
TO BE ASSIGNED
18
DIGITAL IN 18
Digital Input
4mA pull-up, VL<=1V, VH>=3,5V
TO BE ASSIGNED
19
ANALOG IN 3
Analog Input
0/12V pull-down
TO BE ASSIGNED
20
ANALOG IN 4
Analog Input
0/12V pull-down
TO BE ASSIGNED
21
ANALOG IN 5
Analog Input
0/12V pull-down
TO BE ASSIGNED
22
ANALOG IN 6
Analog Input
0/12V pull-down
TO BE ASSIGNED
23
DIGITAL IN 19
Digital Input
4mA pull-up, VL<=1V, VH>=3,5V
TO BE ASSIGNED

ACM1_TAU_UserManual_En
Page 11 of 35
SME s.p.a. Via della Tecnica 40 Z.I.
36071 ARZIGNANO (VI) ITALY
Phone +39 0444 470511 - Fax +39 0444 451803
2.3.3 Interfaces
Serial Communication: RS-232
CAN:
Protocol: CAN Open
Physical layer: ISO11898-2
Baud rates: 1Mbps, 800kbps, 500kbps, 250kbps, 125kbps, 50kbps
Lin Bus
2.3.4 EMC
EN12895 (Industrial Trucks –Electromagnetic Compatibility)
2.3.5 Safety
EN1175-1 (Safety of Industrial Trucks –Electrical Requirements)
The vehicle OEM takes full responsibility of the regulatory compliance of the
vehicle system with the controller installed.
2.4 Operating Environment Specifications
Storage ambient temperature range: -40°C ÷ +70°C
Operating ambient temperature range: -40°C ÷ +55°C
Heatsink operating temperature range: -40°C ÷ +95°C
With linear derating: +80°C ÷ +95°C
Protection Level: IP65
Vibration: Tested under conditions suggested by EN60068-2-6 [5g, 10÷500Hz, 3 axes]
Shock & Bump: Tested under conditions suggested by EN60068-2-27
Cold & Heat: Tested under conditions suggested by EN60068-2-1
Mechanical size: 210 x 145 x 91 [mm]
Weight: 3 kg

ACM1_TAU_UserManual_En
Page 12 of 35
SME s.p.a. Via della Tecnica 40 Z.I.
36071 ARZIGNANO (VI) ITALY
Phone +39 0444 470511 - Fax +39 0444 451803
3. Installation and Wiring
For specific application, refer to the About Controllers Area of the
Interactive Documentation.
Figure 2 - AC-M1 Wiring Diagram

ACM1_TAU_UserManual_En
Page 13 of 35
SME s.p.a. Via della Tecnica 40 Z.I.
36071 ARZIGNANO (VI) ITALY
Phone +39 0444 470511 - Fax +39 0444 451803
3.1 Controller
The Controller contains ESD-sensitive components. Use appropriate precautions in
connecting, disconnecting, and handling it.
Mechanical Drawing
AC - M1 Top View
Working on electrical systems is potentially dangerous; you should protect yourself against :
Uncontrolled operation: some conditions could cause the motor to run out of control:
disconnect the motor or jack up the vehicle and get the drive wheels off the ground before
attempting any work on the motor control circuitry.
Voltage hazard and high current arcs: batteries can supply high voltage and very high power,
and arcs can occur if they are short circuited. Always disconnect the battery circuit before
working on the motor control circuit.
Wear safety glasses and use properly insulated tools to prevent shorts.
Never energize the system if the terminals –B and +B are not tightly connected.
Lead acid batteries: charging or discharging generates hydrogen gas, which can build up and
go around the batteries. Follow the battery manufacturer’s safety recommendations and
wear safety glasses.
For high resolution diagram, refer to the About Controllers Area of the
Interactive Documentation.
Figure 3 –Top View

ACM1_TAU_UserManual_En
Page 14 of 35
SME s.p.a. Via della Tecnica 40 Z.I.
36071 ARZIGNANO (VI) ITALY
Phone +39 0444 470511 - Fax +39 0444 451803
AC - M1 General View
AC - M1 Side View
AC - M1 Back View
Figure 5 –Side View
Figure 4 –General View
Figure 6 -Back View

ACM1_TAU_UserManual_En
Page 15 of 35
SME s.p.a. Via della Tecnica 40 Z.I.
36071 ARZIGNANO (VI) ITALY
Phone +39 0444 470511 - Fax +39 0444 451803
Mounting and Replacement
The Controller meets IP65 environmental protection rating against dust and water.
The mounting location should be carefully chosen in order to be clean and dry, to minimize shock,
vibration, temperature changes and exposure to water & contaminants. If this kind of location
can’t be ensured, then a cover should be used to shield the controller. Cables must be routed to
prevent liquids flowing into the connections. The mounting location should also allow access to all
connections.
The replacement of the Controller must be done with the hand brake engaged, the drive wheels
off the ground, the key switch in off position, battery plug disconnected and the capacitors of the
inverter completely discharged.
The capacitors in the inverter can be discharged by connecting a load across the inverter’s +B and
–B terminals.
Avoid to swap K1 and K2 connectors. This operation can seriously damage
the Controller
Cooling
It is recommended that the Controller is assembled to a flat, free of paint surface preferably lightly
coated with a thermal transfer compound using the 4 holes provided. Ideally, this surface will
provide maximum heat dissipation and ensure full rated power output. When designing a cooling
system, please refer to the following step:
1. Apply thermal grease to the Controller before mounting for better cooling effect.
2. The Controller is cooled by the surface contact to the vehicle body, so it is important to pay
much attention to the flatness and the roughness of the surface of the vehicle frame where
it is mounted. The roughness Rzshould be between 1.6 μm and 3.2μm, while the planarity
of the surface should be under 0.5mm, as shown in the following image:
Planarity specifications for the AC-M1 with
aluminium baseplate.
Figure 7 - Planarity

ACM1_TAU_UserManual_En
Page 16 of 35
SME s.p.a. Via della Tecnica 40 Z.I.
36071 ARZIGNANO (VI) ITALY
Phone +39 0444 470511 - Fax +39 0444 451803
3. Any airflow around the controller will further enhance the thermal performance.
4. Additional heatsink could be necessary to meet the desired continuous ratings. The heat
sink material and system should be sized on the performance requirement of the machine.
We recommend ambient temperature air to be directed over the heatsink fins to maintain
heatsink temperature below 75 °C.
5. In systems where either ventilation is poor, or heat exchange is difficult, forced air
ventilation should be used.
Clearances
For all AC-M1 models 50 mm clearances in front of and behind the AC-M1 are required for airflow;
50 mm clearance above the AC-M1 is required for installation/removal of interface connectors and
wiring.

ACM1_TAU_UserManual_En
Page 17 of 35
SME s.p.a. Via della Tecnica 40 Z.I.
36071 ARZIGNANO (VI) ITALY
Phone +39 0444 470511 - Fax +39 0444 451803
3.2 Power Terminals
Wiring
The Controller has five Power Terminals, which are clearly marked on Controller’s body as B+, B-,
U, V, W(figure 4).
Power Terminals on Controller
Terminal
Meaning
B+
Positive Battery coming from the Main Contactor
B-
Negative Battery
U
U Motor Phase
V
V Motor Phase
W
W Motor Phase
The recommended screw torque for fixing the Power Terminals is 6.4 Nm. This value is reported
on the label placed on the cover, exceeding the recommended value may cause damages.
Sizing
The environment conditions strongly affect the current carrying capacity of a single wire.
Temperature and wire length can decrease the cable performance and other factors such as
Controller duty cycles and airflow should also be taken into consideration when sizing the power
cables.
The following formula gives an advice on the cable size needed in welding cable, not grouped with
other cables:
Ambient Temperature = 25°C
Maximum Temperature rise on the cable surface = 60°C
Suggested Current Density [Arms/mm2] = 5 Arms/mm2

ACM1_TAU_UserManual_En
Page 18 of 35
SME s.p.a. Via della Tecnica 40 Z.I.
36071 ARZIGNANO (VI) ITALY
Phone +39 0444 470511 - Fax +39 0444 451803
The following table shows you the most common cases:
Average Current [Arms]
Minimum Wire
Section Suggested
[mm2]
Wire Size
mm2
AWG
100
20
21.1
4
150
30
33.6
2
200
40
42.4
1
250
50
53.5
0
300
60
67.4
2/0
350
70
85
3/0
3.3 Main Contactor
The Controller must be connected to one Main Contactor for two basically reasons:
Capacitors Pre-Charge : The Controller handles all this phase internally by
discharging/charging its DC-Bus through the Key Input. As soon as a certain voltage value is
reached by the DC-Bus, the Controller can close the Main Contactor connecting it to the
Battery. In this way dangerous shocks on Controller's capacitors are avoided.
Safety: In case of dangerous situations, the Main Contactor must be opened disconnecting
the Battery from Controller. If the main contactor coil is not connected to the controller,
the system will not meet EEC safety requirements.
Sizing
In order to select the Main Contactor, it must be considered the Controller Ratings, the Duty Cycle
of the System and several other working conditions. The following empirical formula can be useful
to quickly find the Main Contactor minimum rating IMC:
with

ACM1_TAU_UserManual_En
Page 19 of 35
SME s.p.a. Via della Tecnica 40 Z.I.
36071 ARZIGNANO (VI) ITALY
Phone +39 0444 470511 - Fax +39 0444 451803
3.4 Fuse
A fuse protects the Controller and the entire system against shorts circuit in the power section
and it can be mounted in the Controller between the +B and the related terminal.
Anyway, consider that the fuse doesn’t be used to avoid overloads on the Controller or on the AC
Motor. The firmware inside the Controller already manages them so they don’t usually cause the
fuse to blow.
Sizing
In order to select the Fuse Rating, refer to the following formula:
with and
You must choose a fuse with specific rating and time delay characteristics.
It must carry IFUSE indefinitely, but blow within maximum 3 seconds for 2 x IFUSE .
The following diagram shows common dimensions for fuse on Controller.
Suggested Manufacturers are FERRAZ, BUSSMAN, LITTELFUSE and others which satisfy the time
delay and dimensions required.
Dimensions[mm]
A
82
B
60
D
20
E
11
Figure 8 –Fuse Dimensions

ACM1_TAU_UserManual_En
Page 20 of 35
SME s.p.a. Via della Tecnica 40 Z.I.
36071 ARZIGNANO (VI) ITALY
Phone +39 0444 470511 - Fax +39 0444 451803
3.5 Signal
The Controller uses two Ampseal connectors:
Figure 9 - Ampseal Connector
Refer to the following specifications for these connectors:
Number of Positions: 23 Position
Mounting Style: Wire
Termination Style: Crimp
Contact Type: Plug
Current Rating: 17 A
Housing Material: Thermoplastic
Material: Plastic
Number of Rows: 3 Row
Packaging: Bulk
Type: Female
Wire Gauge Range: 20 AWG - 16 AWG
For detailed product information, please refer to the AMPSEAL Connectors: Product Specification
108-1329.
In order to ensure a fine wiring, please refer to the AMPSEAL Automotive Plug Connector and
Header Assembly: Application Specification 114-16016.
Other manuals for AC-M1
1
Table of contents
Other SME Controllers manuals
Popular Controllers manuals by other brands

Lutron Electronics
Lutron Electronics seeTouch installation instructions
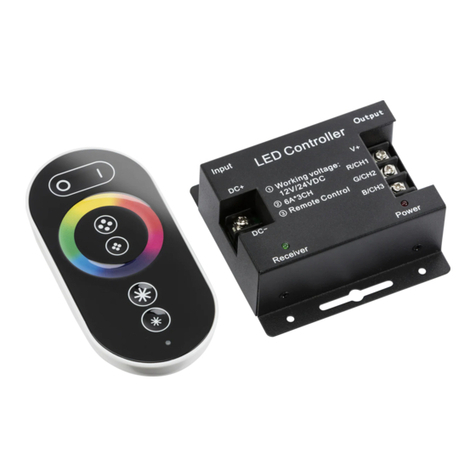
Knightsbridge
Knightsbridge LEDFRA9 Installation & maintenance manual

Munters
Munters BA1701 instruction manual
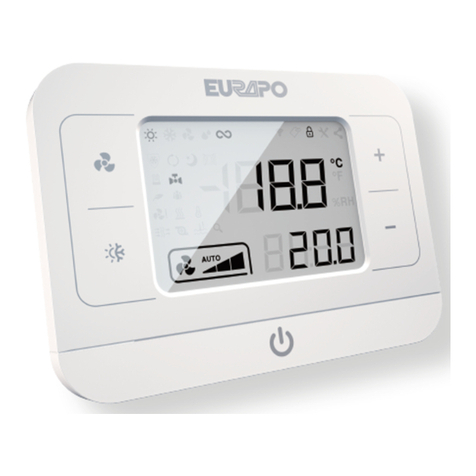
Eurapo
Eurapo OMNIBUS 360 MAINTENANCE and Operation manual
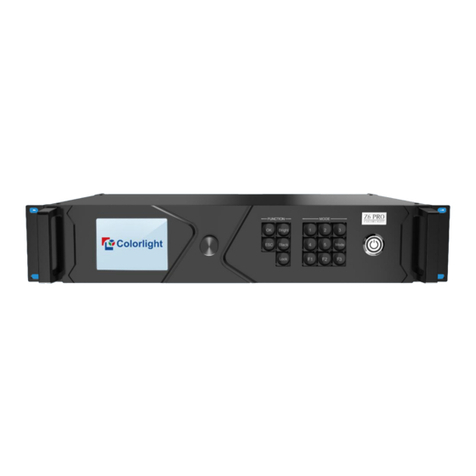
Colorlight
Colorlight Z6 PRO user manual
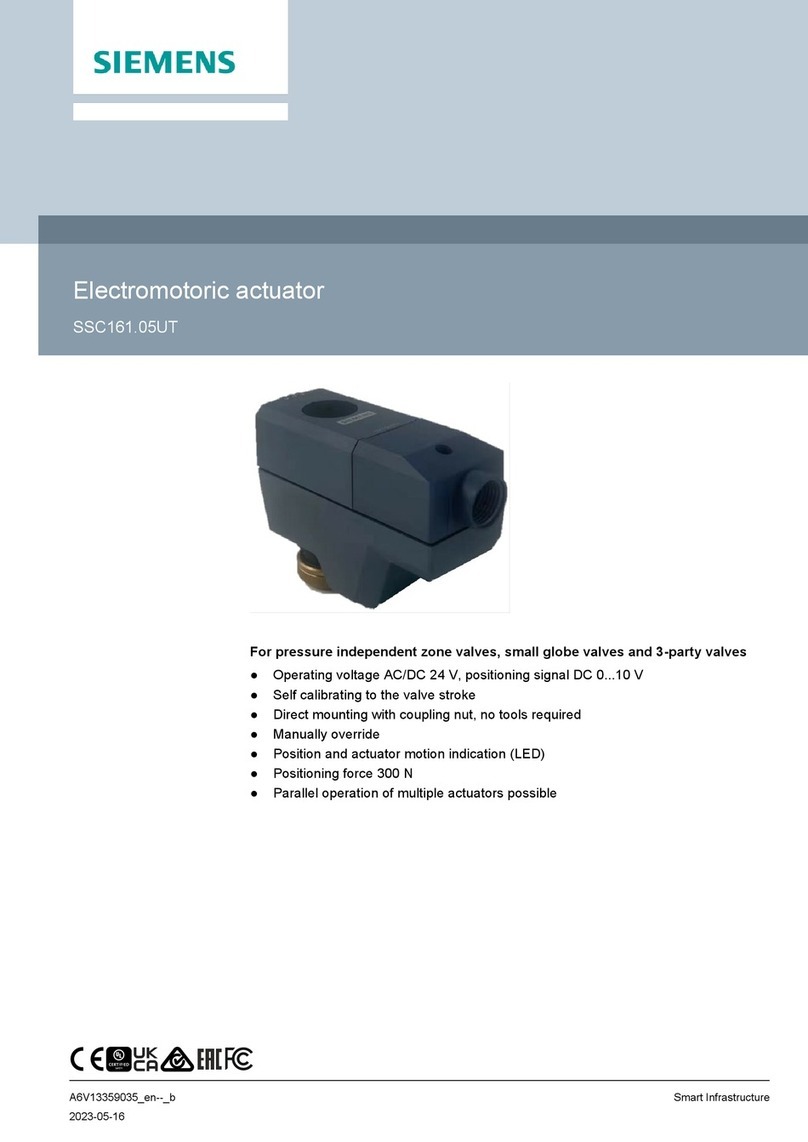
Siemens
Siemens SSC161.05UT manual