SofTA 1300 ELSD Operating instructions

SofTA 1300 ELSD
Installation and Operation Guide
#8-243104
Copyright © 2016 Teledyne Technologies Incorporated. All rights reserved.
Rev. A, November 2018


SofTA 1300 ELSD
Safety
3
SofTA 1300 ELSD
Safet y
Before installing, operating, or maintaining this equipment, it is
imperative that all hazards and preventive measures are fully
understood. While specific hazards may vary according to
location and application, take heed in the following general
warnings:
WARNING
LASER SAFETY: This ELSD is a Class I laser product with
a Class IIIa (3R) embedded laser. The embedded laser beam
is less than 5 mW, 650 nm, and is collimated. There are no
user adjustments for power, alignment, or collimation.
Under use conditions, the laser is never visible, and
presents no special safety considerations.
As required by regulation, the back panel has the following
laser related labels, in addition to a serial number label.
Internal components may have the following label:
Never remove a component with this label. Doing so could
expose a user to a potentially hazardous laser beam. Always
refer service to qualified personnel.
WARNING
Do not use gases that support combustion with
combustible solvents. Always use inert gases.To avoid
inhaling harmful organic solvents and other materials, the
detector exhaust should not be allowed to enter the
laboratory atmosphere.
DANGER
To avoid burns, turn off the power at least 30
minutes before performing maintenance
procedures.

SofTA 1300 ELSD
Safety
4
WARNING
Liquids associated with this instrument may be classified
as carcinogenic, biohazard, flammable, or radioactive.
Should these liquids be used, it is highly recommended that
this application be accomplished in an isolated
environment designed for these types of materials in
accordance with federal, state, and local regulatory laws,
and in compliance with your company’s chemical/hygiene
plan in the event of a spill.
WARNING
Avoid hazardous practices! If you use this instrument in
any way not specified in this manual, the protection
provided by the instrument may be impaired.
WARNING
If you are using flammable solvents or chemicals with this
system, vapor concentration levels may exceed the
maximum exposure levels as recommended by OSHA
Guide 1910.1000. To reduce those levels to a safe exposure,
Teledyne Isco recommends that you place the system in a
laboratory hood designed for the purpose of ventilation.
This hood should be constructed and operated in
accordance with federal state and local regulations. In the
event of a solvent or chemical spill, your organization
should have a plan to deal with these mishaps. In all cases,
use good laboratory practices and standard safety
procedures.
Hazard Severity Levels This manual applies Hazard Severity Levels to the safety alerts.
These three levels are described in the sample alerts below.
CAUTION
Cautions identify a potential hazard, which if not avoided, may
result in minor or moderate injury. This category can also warn
you of unsafe practices, or conditions that may cause property
damage.
WARNING
Warnings identify a potentially hazardous condition, which
if not avoided, could result in death or serious injury.
DANGER
DANGER – limited to the most extreme situations
to identify an imminent hazard, which if not
avoided, will result in death or serious injury.

SofTA 1300 ELSD
Safety
5
Hazard Symbols The equipment and this manual use symbols used to warn of
hazards. The symbols are explained in the table below.
Hazard Symbols
Warnings and Cautions
The exclamation point within the triangle is a
warning sign alerting you of important instructions
in the instrument’s technical reference manual.
The lightning flash and arrowhead within the trian-
gle is a warning sign alerting you of “dangerous
voltage” inside the product.
Symboles de sécurité
Ce symbole signale l’existence d’instructions
importantes relatives au produit dans ce manuel.
Ce symbole signale la présence d’un danger
d’électocution.
Warnungen und Vorsichtshinweise
Das Ausrufezeichen in Dreieck ist ein Warn-
zeichen, das Sie darauf aufmerksam macht, daß
wichtige Anleitungen zu diesem Handbuch
gehören.
Der gepfeilte Blitz im Dreieck ist ein Warnzeichen,
das Sei vor “gefährlichen Spannungen” im
Inneren des Produkts warnt.
Advertencias y Precauciones
Esta señal le advierte sobre la importancia de las
instrucciones del manual que acompañan a este
producto.
Esta señal alerta sobre la presencia de alto
voltaje en el interior del producto.

SofTA 1300 ELSD
Safety
6
For Additional
Information
Technical assistance for the 1300 ELSD can be obtained from:
Teledyne Isco
4700 Superior St.
Lincoln NE 68504
Phone: (800) 775-2965 or (402) 464-0231
Fax: (402) 465-3001
E-mail: IscoService@teledyne.com

SofTA 1300 ELSD
Table of Contents
1
SofTA 1300 ELSD
Table of Contents
Section 1 Introduction
1.1 ELSD Principle of Operation . . . . . . . . . . . . . . . . . . . . . . . . . . . . . . . . . . . . . . . . . . 1-1
1.1.1 Operation . . . . . . . . . . . . . . . . . . . . . . . . . . . . . . . . . . . . . . . . . . . . . . . . . . . . 1-1
Section 2 Unpacking and Installation
2.1 Requirements and Steps . . . . . . . . . . . . . . . . . . . . . . . . . . . . . . . . . . . . . . . . . . . . . . 2-1
2.1.1 Unpacking . . . . . . . . . . . . . . . . . . . . . . . . . . . . . . . . . . . . . . . . . . . . . . . . . . . 2-1
2.2 Connections . . . . . . . . . . . . . . . . . . . . . . . . . . . . . . . . . . . . . . . . . . . . . . . . . . . . . . . . 2-1
2.3 Installation Qualification Checklists . . . . . . . . . . . . . . . . . . . . . . . . . . . . . . . . . . . . 2-3
2.3.1 Overview . . . . . . . . . . . . . . . . . . . . . . . . . . . . . . . . . . . . . . . . . . . . . . . . . . . . . 2-3
2.3.2 Installation Qualification (IQ) for SofTA ELSDs . . . . . . . . . . . . . . . . . . . . . 2-4
2.3.3 Operational Qualification (OQ) for SofTA ELSDs . . . . . . . . . . . . . . . . . . . . 2-5
2.3.4 Performance Qualification (PQ) for SofTA ELSDs . . . . . . . . . . . . . . . . . . . 2-7
2.3.5 Overall Detector Performance for SofTA ELSDs . . . . . . . . . . . . . . . . . . . . . 2-9
Section 3 Operation
3.1 Instrument Controls . . . . . . . . . . . . . . . . . . . . . . . . . . . . . . . . . . . . . . . . . . . . . . . . . 3-1
3.1.1 Power Key . . . . . . . . . . . . . . . . . . . . . . . . . . . . . . . . . . . . . . . . . . . . . . . . . . . 3-1
3.1.2 A/Z Key . . . . . . . . . . . . . . . . . . . . . . . . . . . . . . . . . . . . . . . . . . . . . . . . . . . . . . 3-1
3.2 Display Screens . . . . . . . . . . . . . . . . . . . . . . . . . . . . . . . . . . . . . . . . . . . . . . . . . . . . . 3-1
3.3 Operating Conditions . . . . . . . . . . . . . . . . . . . . . . . . . . . . . . . . . . . . . . . . . . . . . . . . 3-7
3.3.1 Start Up Procedure . . . . . . . . . . . . . . . . . . . . . . . . . . . . . . . . . . . . . . . . . . . . 3-7
3.3.2 Shut Down Procedure . . . . . . . . . . . . . . . . . . . . . . . . . . . . . . . . . . . . . . . . . . 3-8
3.4 Choosing Operating Conditions . . . . . . . . . . . . . . . . . . . . . . . . . . . . . . . . . . . . . . . . 3-8
3.4.1 Thermo-Split Spray Chamber Temperature . . . . . . . . . . . . . . . . . . . . . . . . 3-9
3.4.2 Drift Tube Temperature . . . . . . . . . . . . . . . . . . . . . . . . . . . . . . . . . . . . . . . 3-10
3.4.3 Mobile Phase Flowrate . . . . . . . . . . . . . . . . . . . . . . . . . . . . . . . . . . . . . . . . 3-11
3.4.4 Gradient Separations . . . . . . . . . . . . . . . . . . . . . . . . . . . . . . . . . . . . . . . . . 3-11
3.5 Mobile Phase Considerations . . . . . . . . . . . . . . . . . . . . . . . . . . . . . . . . . . . . . . . . . 3-12
3.5.1 Selecting a Solvent . . . . . . . . . . . . . . . . . . . . . . . . . . . . . . . . . . . . . . . . . . . . 3-12
3.5.2 Mobile Phase Flowrate and Composition . . . . . . . . . . . . . . . . . . . . . . . . . . 3-12
3.5.3 Buffer Compatibility . . . . . . . . . . . . . . . . . . . . . . . . . . . . . . . . . . . . . . . . . . 3-12
3.5.4 Column Pre-Treatment . . . . . . . . . . . . . . . . . . . . . . . . . . . . . . . . . . . . . . . . 3-12
3.5.5 QC Test Conditions . . . . . . . . . . . . . . . . . . . . . . . . . . . . . . . . . . . . . . . . . . . 3-13
Appendix A Speciations
A.1 Specifications . . . . . . . . . . . . . . . . . . . . . . . . . . . . . . . . . . . . . . . . . . . . . . . . . . . . . . A-1

SofTA 1300 ELSD
Table of Contents
2

1-1
SofTA 1300 ELSD
Section 1 Introduction
1.1 ELSD Principle of
Operation
ELSDs are near universal detectors primarily used in High Per-
formance Liquid Chromatography (HPLC), though they have
been used successfully in other types of chromatography as well.
Their principal requirement is that the analyte be less volatile
than the mobile phase. An ELSD cannot detect highly-volatile
analytes. However, most analytes of interest are less volatile
than the eluting solvents.
Evaporative light scattering detectors are complementing ultra-
violet (UV) detection because they can detect most analytes, are
stable during gradient elutions, and respond to the relative mass
of the analyte (even those that do not absorb UV radiation). This
is an important feature that is useful when detecting unknown
materials. The ELSD is superior to the refractive index detector
(RID) as it can be used with gradient chromatography, it is not
susceptible to ambient temperature changes, and it does not
produce negative peaks (which can be difficult to quantify). The
ELSD does not respond to the mobile phase disruption seen as
solvent front peaks in the void volume with UV and RI detectors,
so early eluting analytes can be easily quantified. Mass spec-
trometry (MS) detection is also a nearly universal detector, but
its high cost and complexity may be unnecessary in many appli-
cations. In fact, the operation requirements of MS closely match
that of the ELSD. This allows the less expensive and less compli-
cated ELSD to be used as a method development detector for
methods to be used on the MS systems.
1.1.1 Operation The 1300 ELSD employs a unique method of detection. The
process involves the nebulization of the column eluent which
transforms it into an aerosol cloud. As this cloud travels through
a heated zone within the instrument, the more volatile mobile
phase evaporates and leaves a smaller cloud of analyte particles.
These particles pass through a beam of light and scatters some of
the light which is converted into an electronic signal.
Nebulization Nebulization transforms the liquid phase leaving the column into
an aerosol cloud of fine droplets. The size and uniformity of the
droplets are extremely important in achieving sensitivity and
reproducibility. The 1300 ELSD uses a special concentric flow
nebulizer and a constant flow of an inert gas to ensure a narrow
droplet size distribution. This nebulizer is constructed entirely
from PTFE which accumulates fewer deposits than either glass
or stainless steel.
To handle flow rates and mobile phases common in HPLC, all
ELSDs need a way to divert part of the aerosol cloud to waste.
The 1300 ELSD uses patented Thermo-Split technology.

SofTA 1300 ELSD
Section 1 Introduction
1-2
The Thermo-Split chamber combines a gentle bend with temper-
ature-controlled walls. When the aerosol exiting the nebulizer
encounters a cool environment, it partially condenses into larger
particles whose momentum carries them into the wall and down
the drain (Figure 1-1).
Figure 1-1 Thermo-Split chamber without heating
To increase sensitivity with easy-to-evaporate solvents, the tem-
perature of the spray chamber may be elevated. As the aerosol
traverses the chamber, it partially evaporates and shifts the par-
ticle size distribution low enough for essentially all the particles
to negotiate the bend. Under these conditions, a majority of the
aerosol particles pass through the chamber and are carried into
the evaporative zone (Figure 1-2).
Figure 1-2 Thermo-Split chamber with heating
Evaporation After passing through the nebulization chamber, the aerosol
cloud is propelled through the heated evaporation tube assisted
by the carrier gas. In the evaporation tube, the solvent is vola-
tilized to produce particles or droplets of pure analyte.

SofTA 1300 ELSD
Section 1 Introduction
1-3
The temperature of the drift tube is set at the temperature
required to evaporate the solvent. The temperature is kept as low
as possible to avoid particle shape distortion, evaporation of the
analyte, or when working with thermally sensitive compounds.
Detection The particles emerging from the evaporation tube enter the
optical cell where the sample particles pass through the light
emitted by a low power laser. The particles scatter the light
which is detected by a silicon photodiode located at a 90° angle
from the laser. A light trap is located opposite the laser to collect
the light not scattered by particles. The quantity of light detected
is proportional to the solute concentration and solute particle
size distribution. The photodiode produces a signal which is sent
to the outputs for collection.
Figure 1-3 Nebulization chamber

SofTA 1300 ELSD
Section 1 Introduction
1-4

2-1
SofTA 1300 ELSD
Section 2 Unpacking and Installation
2.1 Requirements and
Steps
In addition to the 1300 ELSD and its accompanying accessories,
you will need:
• Gas Supply: Clean, dry, inert gas regulated to 65 ± 5 psi
is needed for nebulization. Either Argon or Nitrogen is
acceptable. Do not use gases that support combustion.
• Exhaust Device: The carrier gas containing volatilized
mobile phase and sample components will exit the 1300
ELSD. You should provide a means of removing this
from the laboratory. The 1300 ELSD should be located
close to a fume hood or other ventilation device.
• Tubing, fittings, and tools to connect your HPLC system
to the 1300 ELSD.
2.1.1 Unpacking Carefully unpack the accessory items included with the ELSD
shipment and confirm that all the items are present. The 1300
ELSD comes in a high-quality shipping container engineered to
avoid damage in transit. Save the shipping container and pack-
aging for future shipments.
2.2 Connections
Power Connection The 1300 ELSD operates at either 120 V or 240 V, 50/60 Hz.
CAUTION
Confirm that the 1300 ELSD is configured for the correct volt-
age before plugging it into line voltage. Plug the modular power
cord provided into the power input module on the back of the
detector.
If the power input module is set to the wrong voltage:
1. Unplug the power cord from the module.
2. Open the fuse compartment by gently prying the cover
from the module with a flat blade screwdriver.
3. Remove the fuse block.
4. Remove the voltage configuration card from the module by
gently pulling with pliers or tweezers.
5. Rotate the plastic voltage selector until the correct voltage
appears on the side opposite the voltage selector.
6. Replace the card and fuse block.
7. Confirm that the correct voltage is indicated through the
cover before securing the cover.

SofTA 1300 ELSD
Section 2 Unpacking and Installation
2-2
8. Plug the modular power cord provided into the power input
module on the back of the detector.
Exhaust A portion of the solvent and analyte sent to the ELSD will exit
the exhaust as vapors or aerosol particles. To manage this
exhaust, the 1300 ELSD uses a 1” O.D. stainless steel tube. The
included black corrugated exhaust tube extension must be
installed to eliminate sensitivity to ambient lighting conditions.
The outlet of this tube must be routed to a fume hood during
operation. Alternatively, connect the tubing and direct exhaust to
a cooled collection vessel for later disposal.
RS-232 The 1300 ELSD should be connected to a Windows computer
for access of its full list of functions. Connect the serial port of a
1300 ELSD to the computer serial port.
Communication An output jack can be found on the back of the 1300 ELSD for
connection to a chart recorder, computing integrator, or comput-
erized data system. The maximum signal output is 1 V.
I/O Connections Pin 1 and Pin 2: A contact closure output. Pins are open when
error conditions exist.
Pin 3 and Pin 4: A contact closure input to turn on/off gas
remotely. Gas control toggles with electrical continuity between
these two pins. Maintain connectivity for a minimum of 500 ms.
A subsequent toggle command within 2 seconds may be ignored.
Pin 5 and Pin 6: A TTL output for instrument status. A logical
high indicates the detector is in standby.
Pin 7 and Pin 8: A contact closure input to reset baseline
remotely. Maintain connectivity for a minimum of 500 ms. A sub-
sequent toggle command within 2 seconds may be ignored.
Gas Connections Connect a supply of clean, dry, inert gas regulated to 65 ± 5 psi to
the GAS INLET port on the back of the unit. The internal gas regu-
lator maintains the gas pressure at the factory set value dis-
played on the front panel.
Fluid Connections Connect the outlet from your column to the LIQUID INLET on the
front of the unit. The length and volume between the column
outlet and the detector inlet should be kept as short as possible
to avoid unnecessary band broadening. Use the supplied tubing
for the best results.
Nebulization Chamber
Drain
The instrument’s internal "P" trap must be full during operation.
Restricting the drain port with liquid is very important to ensure
detection sensitivity. Introduce 10 ml of mobile phase into the
drain using a squirt bottle or syringe.
Note
If you use volatile solvents which are completely vaporized,
you may not see solvents exiting the drain during operation. If
this is true, you may need to periodically refill the "P" trap for
optimal operation.

SofTA 1300 ELSD
Section 2 Unpacking and Installation
2-3
Place the ¼” stainless steel drain adapter provided in the
accessory kit on the drain port located on the front of the
instrument. Direct the outlet of the tube to a collection vessel
located below the trap. Watch the liquid level in the vessel during
operation and empty when full.
2.3 Installation
Qualification
Checklists
2.3.1 Overview This qualification procedure will document that the SofTA ELSD
is operating as designed. This documentation is important when
working in a regulated environment to demonstrate to various
auditors that the detector is working properly. This process is
called qualification or validation. Qualification can be divided
into the following steps:
• Installation Qualification (IQ) documents that the
correct detector was received and installed properly.
• Operational Qualification (OQ) tests that the detector
meets specifications in the user environment. OQ
generally requires specialized test detectors that have
been calibrated against NIST standards.
• Performance Qualification (PQ) tests that the system
performs the selected application correctly. The original
test report is shipped with each detector to certify that
the detector passed the final test.

SofTA 1300 ELSD
Section 2 Unpacking and Installation
2-4
2.3.2 Installation
Qualification (IQ) for
SofTA ELSDs
Model Number:
Detector Serial Number:
Location of the Detector:
The undersigned individual, certified by the manufacturer, com-
pleted the manufacturer’s procedure for the proper Installation
Qualification of this detector.
Name:
Title/Affiliation:
Signature:
Date:
Step Description Yes No Installer
Initials
Operator
Initials
1 Is the detector the same as specified on the purchase
order?
2 Has the detector been inspected for damages and found
unharmed?
3 Has the required documentation identified by model
number and date been supplied?
4 Have details of all services and utilities required to oper-
ate the detector been provided?
5 Have methods and instructions for user maintenance
been provided along with a contact point for service and
spare parts?
6 Is the selected environment suitable for the detector (i.e.
is adequate room provided for installation, operation, and
servicing)? Have appropriate solvent services and utili-
ties (electricity, Nitrogen gas, ventilation, solvent waste
recovery, etc.) been provided?
7 Has health, safety, and environmental information relat-
ing to the operation of this detector been provided?

SofTA 1300 ELSD
Section 2 Unpacking and Installation
2-5
2.3.3 Operational
Qualification (OQ) for
SofTA ELSDs
Model Number:
Detector Serial Number:
Location of the Detector:
Set-up Turn on the detector. Confirm the following settings are
accurate:
Modify if necessary. Set the drift tube temperature to 60 °C and
the spray chamber temperature to 30 °C. Wait until the temper-
ature stabilizes (approx. 60 minutes).
The display should read 60 °C ± 1 °C.
PASSFAIL
The display should read 30 °C ± 1 °C.
PASSFAIL
Gas Sensor Apply air or Nitrogen pressure monitored by a regulator and
checked with a pressure gauge. Set the pressure to 65 psi. Record
the gas pressure value displayed on the ELSD.
The display should read 50 ± 10psi.
PASSFAIL
Baseline Noise Connect a digital voltmeter calibrated with an NIST-traceable
standard to the analog output of the ELSD. The meter must also
be able to record a minimum and maximum voltage with a
response time of at least 10 ms (Fluke 45 or equivalent).
Fill the ELSD drain tube with HPLC Grade Water.
Occasionally, liquid will be aspirated from the inlet line or drain
which will result in a spike in the signal. The test should be
restarted if this occurs.
Set the detector filter to RC 5. Reset the baseline. Monitor the
output signal for 2 minutes. Record the lowest voltage and the
highest voltage. Calculate the difference.
Full Scale 1 V
Gain Normal
Calibration 100%
Drift tube SET TEMPERATURE
Drift tube DISPLAYED TEMPERATURE
Spray chamber SET TEMPERATURE
Spray chamber DISPLAYED TEMPERATURE
ELSD Value

SofTA 1300 ELSD
Section 2 Unpacking and Installation
2-6
The difference should be less than 2.5 mV.
PASSFAIL
Baseline Drift Set the detector filter to RC 5. Autozero the detector to change
the signal to about 20 mV, and monitor the signal for 30 minutes.
The baseline drift should be less than 2.5 mV.
PASSFAIL
The undersigned individual, certified by the manufacturer, com-
pleted the manufacturer’s procedure for the proper Operational
Qualification of this detector.
Name:
Title/Affiliation:
Signature:
Date:
Maximum Value mV
Minimum Value mV
Difference mV
Initial Signal Value mV
Final Signal Value mV
Difference mV

SofTA 1300 ELSD
Section 2 Unpacking and Installation
2-7
2.3.4 Performance
Qualification (PQ) for
SofTA ELSDs
Model Number:
Detector Serial Number:
Location of the Detector:
Note
Before this procedure is performed, it is necessary to complete
the Installation Qualification and the Operational Qualification.
Sensitivity Set the HPLC System and ELSD conditions to: 1 ml/min of 50/50
Water/Methanol.
Add a backpressure regulator or a length of small ID tubing
between the pump outlet and the injector inlet. Ideally, this will
maintain 1000 psi pressure on the pump check valves enough to
minimize baseline pulsation on the ELSD.
The injection standard (Sodium Benzoate) should be delivered in
20 µl (10 ng/µl) or smaller loop.
Enter the conditions into the detector. Start the HPLC pump and
the gas flow and wait for temperatures to reach the set points.
When the temperatures reach equilibrium, reset the baseline to
about 20 mV. Monitor the ELSD signal for stability. The signal
should be stable within 2 mV.
Connect a digital voltmeter calibrated with an NIST traceable
standard to the analog output of the ELSD. (Alternatively, a cali-
brated Chromatography Data System can be used.) When the
signal is stable, inject the 100 ng sample three times. Record the
maximum signal for each peak.
The Average Peak Height should be at least 3 mV.
PASSFAIL
Full Scale 1 V
Gain Normal
Calibration 100%
Spray chamber 30 °C
Drift tube 60 °C
Filter 5
Injection Standard 100 ng Sodium Benzoate
Peak 1 Height mV
Peak 2 Height mV
Peak 3 Height mV
Average Peak Height mV

SofTA 1300 ELSD
Section 2 Unpacking and Installation
2-8
Reproducibility Without changing conditions, make six 20 µl (max) injections of a
1000 ng standard. (100 ng/µl or appropriate for loop.) Deliver 5x
the loop volume for manual injections.
The reproducibility of six injections should be no greater
than 4.0% RSD (area) or 5.0% RSD (height).
PASSFAIL
The undersigned individual, certified by the manufacturer, com-
pleted the manufacturer’s procedure for the proper Performance
Qualification of this detector.
Name:
Title/Affiliation:
Signature:
Date:
Peak Area 1 Peak Height 1
Peak Area 2 Peak Height 2
Peak Area 3 Peak Height 3
Peak Area 4 Peak Height 4
Peak Area 5 Peak Height 5
Peak Area 6 Peak Height 6
Peak Area% RSD Peak Height % RSD
Table of contents
Popular Security Sensor manuals by other brands

Inficon
Inficon Ecotec E3000 Technical handbook
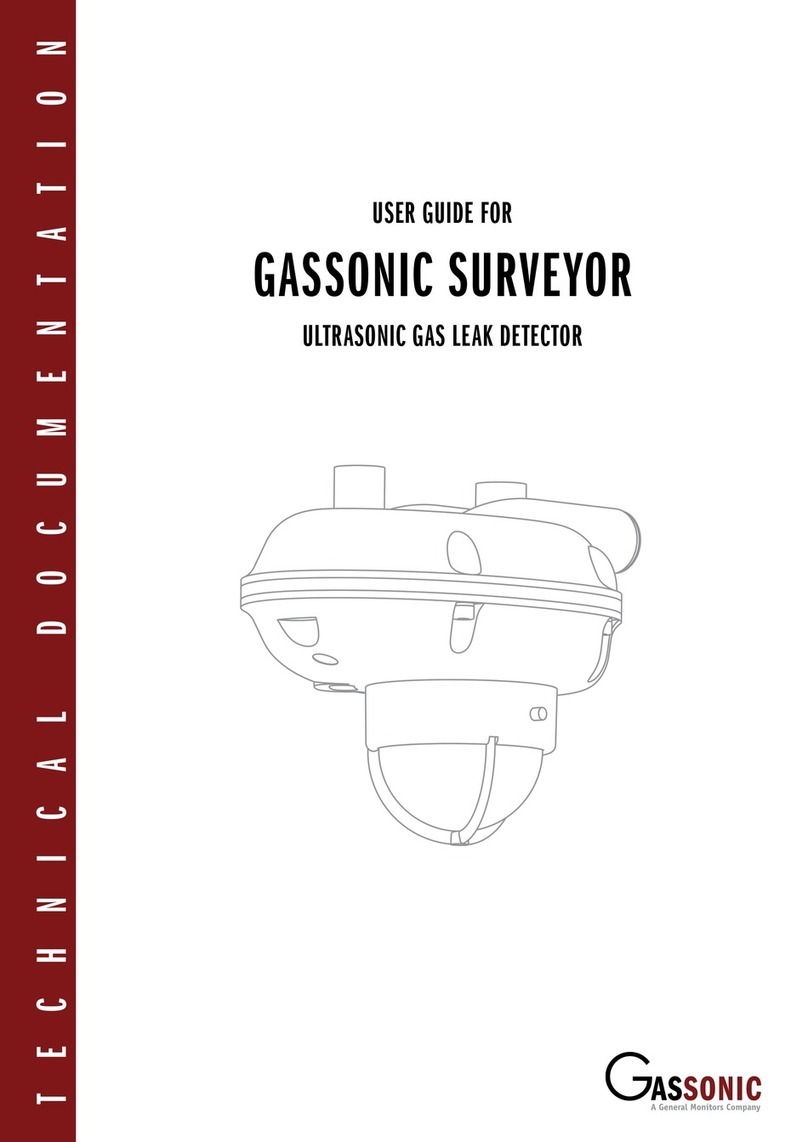
GASSONIC
GASSONIC SURVEYOR user guide
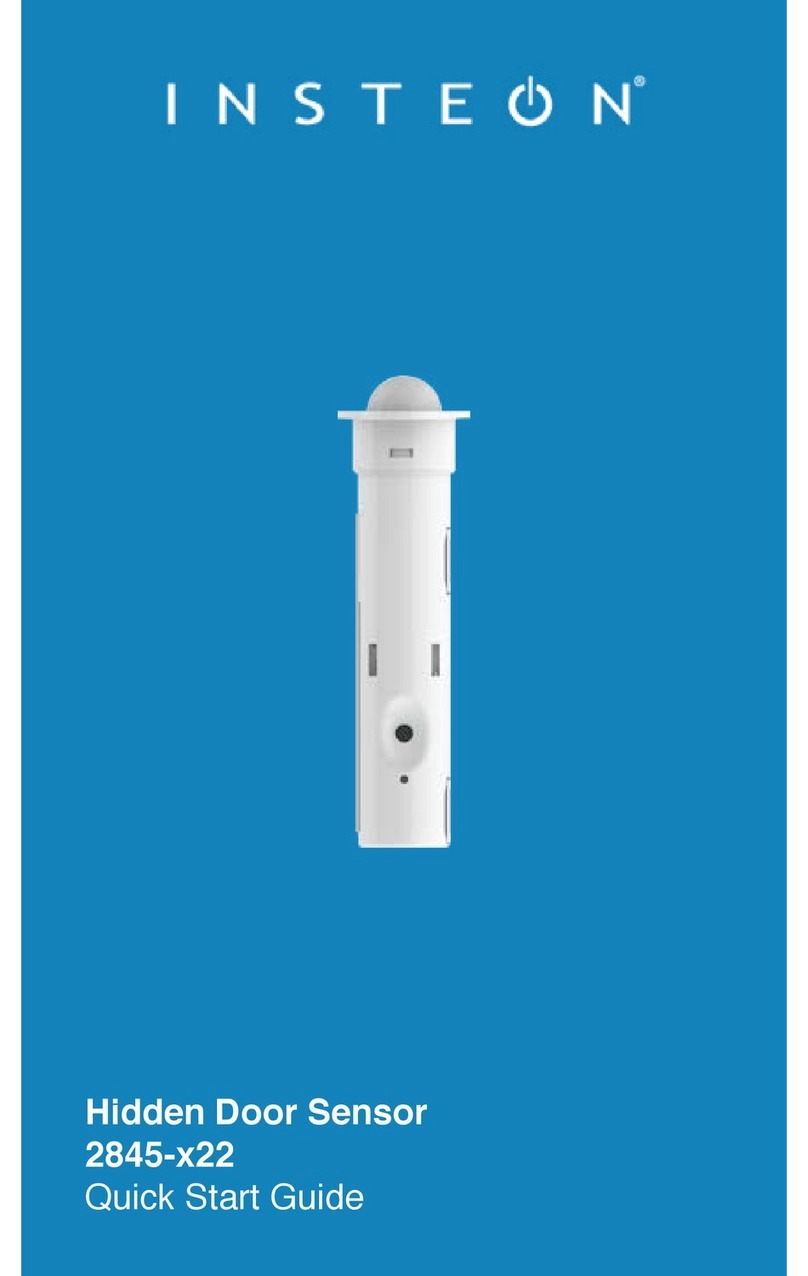
INSTEON
INSTEON 2845-x22 quick start guide

SUREN
SUREN CDL-608 Installation, operation and specification manual
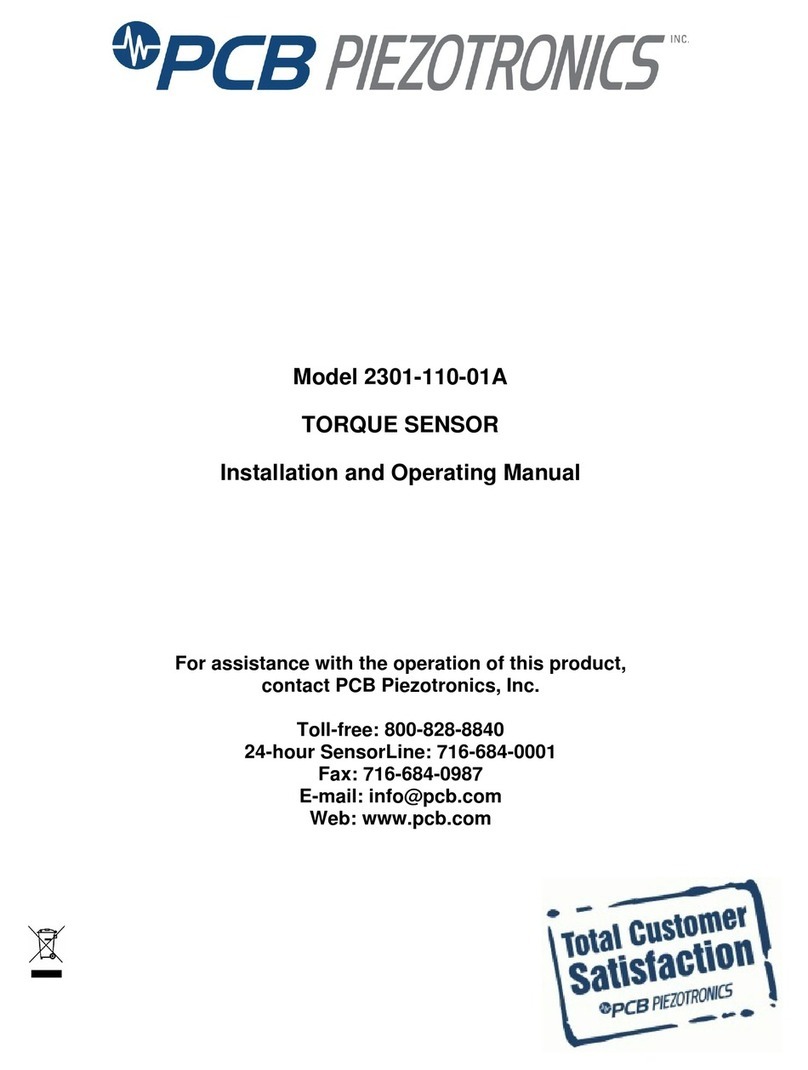
PCB Piezotronics
PCB Piezotronics 2301-110-01A Installation and operating manual
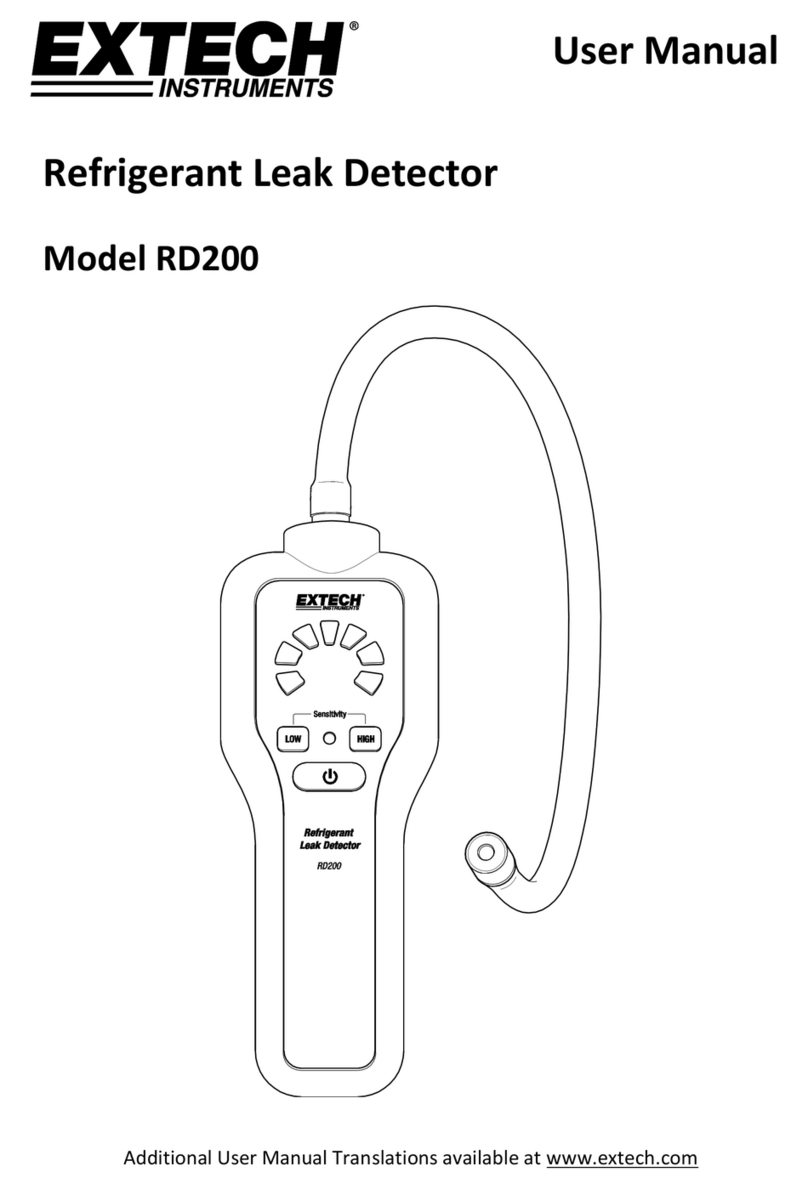
Extech Instruments
Extech Instruments RD200 user manual