SOR 2210 Instruction manual

Form 1428 (05.16) ©SOR Inc.
1/8
Design and
specifications are
subject to change
without notice.
For latest revision, go to
SORInc.com
The SOR®2210 Side Mounted Level Switch is a horizontally mounted, float-operated
level switch. The 2210 is suitable for plant and OEM applications where open or
closed contacts are required to signal presence or absence of liquid at a discrete level.
When the liquid rises, the float extension arm moves a magnet which repels an
internal magnet de-actuating a microswitch. When the liquid level falls, the float
extension arm moves the magnet in the opposite direction, actuating the microswitch.
The 2210 is recommended for use in clean liquids only.
Table of Contents
Installation...................................... 2
Single Switch ............................... 3
Multiple Switch............................. 4
SIL ............................................ 5
Electrical .................................... 5
Maintenance.................................... 6
Troubleshooting ................................ 6
Replacement Parts ............................ 7
Maximum Operating
Pressure Ratings ........................... 7
Registered Quality System to ISO 9001
2210 Side Mounted
Level Switch
General Instructions
NOTE: If you suspect that a product is defective, contact the factory or the SOR Representative
in your area for a return authorization number (RMA). This product should only be installed by
trained and competent personnel.
p
c
a
t
i
o
n
s
w
h
e
r
g
a
l
p
r
e
s
e
n
c
e
or absence of liquid a
t
es, th
e
f
l
o
a
t
e
x
t
e
i

2/8
Form 1428 (05.16) ©SOR Inc.
ISO-9001
14685 W 105TH ST LENEXA, KS
913-888-2630
SORINC.COM
459.6±14.2
18.10±0.56
112.6
4.43
118.6
4.67
*95.1±6.3
3.75±0.25
*95.1±6.3
3.75±0.25
176.4±11.1
6.95±0.44
63.5
2.50
1" NPT
81
3.
1
1" SW
S
PRODUCT CERTIFICATION DRAWING
ALL DIMENSIONS ARE ±1/16 IN
UNLESS OTHERWISE SPECIFIED
MM
LINEAR =
IN
DR
A
J
R
CHE
M
EN
G
R
S
10-32 EXTERNAL
GROUND SCREW
4 IN SCH 40
EXTERNAL CHAMBER
ELECTRICAL CONNECTION
1 NPTF STD
3/4 NPTF OPT
1/2 NPTF OPT
M20 X 1.5 F OPT
2X 1 IN 3000# SW
PROCESS CONNECTION
NAMEPLATE
FRONT VIEW
LEFT SIDE VIEW
1
Installation
Multiple
Switch
Chambers
External switch chambers must be mounted so that the centerline is within 3º of
horizontal. The conduit connection centerline must be within 3° of vertical and the
nameplate at 12 o’clock (facing up - see ). Switch actuation cannot be reversed
by rotating the unit 180°.
Pipe support hangers or stands should be used where necessary.
All isolation valves must be fully open during service, as restricted valves may
cause erroneous level switching.
Single
Switch
Chamber
In addition to the Single Switch installation instructions, multiple chamber
installations have the following requirements:
Headers connecting multiple chambers to the process must be larger
than the chamber process connection diameter to allow adequate liquid
flow to all chambers. Header diameters are listed below:
- Header diameter must be 1.5 times larger than process connection
diameter for two chambers.
- Header diameter must be 2 times larger than process connection
diameter for three or four chambers.
- Header diameter must be 2.5 times larger than process connection
diameter for five or more chambers.
Valves, tees, elbows and other pipe fittings in a header must be the
same diameter as the recommended header diameter.
External chamber piping should be short, straight and unrestricted.
Pipe must be of a diameter equal to or greater than the process
connection diameter.
Valves and other equipment between the chamber and process
must be of the same diameter or larger than the process connection
diameter to allow adequate liquid flow into the chamber.
Dimensions are for reference
only. Contact the factory for
certified drawings for a
particular model number.
Linear = mm/inches
Drawing 0390698
NOTES:
112.8
1. ADD MINIMUM CLEARANCE
4.44
REQUIRED TO REMOVE HOUSING COVER
1

Form 1428 (05.16) ©SOR Inc.
3/8
Insulation of the control chamber is acceptable, but switch housing and
cover must not be insulated.
Not following these installation instructions, including pipe and valve
diameter and pipe lengths can affect operation of the switch, including
differential. See Single Switch Chamber Installation
and Multiple
Switch Chamber Installation
.
Locate switch chamber process connection 12” to 24” (300mm to 600mm) away from
the process pipe or tank.
Locate the switch chamber so that the switch actuates or deactuates at the desired level.
For liquids with a specific gravity of 1.0, switch actuation will occur approximately 3/4”
(20mm) above the chamber centerline and deactuation will occur at approximately 3/8”
(10mm) above the chamber centerline. Consult factory for other specific gravity values.
Connect the bottom chamber process connection to the process pipe or tank 6” to 12”
(150mm to 300mm) below the centerline of the chamber. This will ensure liquid level
in the switch chamber is as close as possible to process liquid level.
Inside diameter of piping, including elbows, tees and valves, must be equal to or
greater than process connection diameter.
One elbow is recommended to connect the level switch with the process pipe or tank.
Single Switch Chamber Installation
Deviating from any
of these instructions
may adversely affect
operation of the level
switch by restricting
liquid ow into the
switch chamber.
The recommended
dimensions allow
adequate space for
isolation valves,
pipe ttings and
insulation. Structural
support (not shown)
must be provided
for level switch
chambers.
152.4 304.8
TO
6.0 12.0
RECOMMENDED
304.8 609.6
TO
12.0 24.0
RECOMMENDED
ELBOW
ISOLATION
VALVE
2210 LEVEL
SWITCH WITH
EXTERNAL
CHAMBER
LIQUID SET
POINT
PROCESS TANK
PIPE
Drawing 0390736

4/8
Form 1428 (05.16) ©SOR Inc.
ISO-90
0
1
152.4 304.8
TO
6.0 12.0
RECOMMENDED
TO LOWEST
SET POINT
203.2 406.4
TO
8.0 16.0
RECOMMENDED
304.8 457.2
TO
12.0 18.0
RECOMMENDED
LIQUID
SET POINTS
152.4 304.8
TO
6.0 12.0
PRODUCT C
ALL DIME
UNLESS
O
PROCESS TANK
THREE 2210
LEVEL SWITCHES
WITH EXTERNAL
CHAMBERS
50.8
2.0 HEADER PIPE
ISOLATION VALVE
25.4
1.0 PIPE TO
EACH CHAMBER
ELBOW
TEE TO
PROCESS TANK
SUPPLY
HEADER
VENT
HEADER
Multiple Switch Chamber Installation
Deviating from any of these recommendations may adversely affect
operation of the level switch by restricting liquid ow into the switch
chamber. The recommended dimensions leave adequate space for
isolation valves, ttings and insulation. Structural support (not shown)
must be provided for level switch chambers.
The header pipe diameter for three (3) or four (4) chambers needs to be two times the
process connection diameter. For 1” (25mm) process connections, the pipe header must
be 2” (50mm) in diameter. This includes pipe connecting the header to the process,
fittings, valves and other pipe equipment installed as part of the header piping. Headers
should be arranged to use one elbow or tee to connect to the process pipe or tank.
Pipe connecting the header to individual chambers can be the same size as the process
connection on the switch chamber. Fittings and valve diameters must also be equal
to or greater than the process connection diameter. One elbow is recommended to
connect the level switch chamber to the header pipe.
Install each chamber so that the actuate or deactuate point is at the desired process
liquid level. See Single Switch Chamber Note 2 for set point locations.
Locate the header 8” to 16” (200mm to 400mm) away from the process tank.
Locate switch chamber process connection 12” to 18” (300mm to 450mm) away from
the header pipe.
Horizontal spacing of level switch chambers should be 6” to 12” (150mm to 300mm).
Drawing 0390736

Form 1428 (05.16) ©SOR Inc.
5/8
Electrical Installation
Remove the end cover to gain acess to the switch mechanism and terminal block.
Feed the switching wires into the housing through the electrical connection. Wire
to the terminal block(s) as shown in . Select wires which are compatible with
temperature and electrical load required by the application. Keep wire length as
short as possible to prevent damage when cover is installed.
Connect the ground wire to the green ground screw located on the outside of the housing.
Replace the switch cover. Ensure switch cover is screwed on all the way.
Housing becomes very hot during regular use, high temp. conduit connections are
necessary.
Test the switch action by varying the liquid level in the chamber or tank.
The cover can become
extremely hot during
operation. Use adequate
protection to prevent
severe personal injury.
LIQUID
LEVEL
LOW
LIQUID
LEVEL
HIGH
SPDT DPDT
WIRING CONTINUITY
1
2
3
4
5
6
SPDT DPDT
Safety Integrity Level (SIL) Installation Requirements
The SOR pressure switches have been evaluated as Type-A safety related hardware.
To meet the necessary installation requirements for the SIL system, the following
information must be utilized:
Proof Test Interval shall be one year.
Units may only be installed for use in Low Demand Mode.
Products have a HFT (Hardware Fault Tolerance) of 0, and were evaluated in a
1oo1 (one out of one) configuration. Form 1538 (03.12) ©2012 SOR Inc.
All housings must be
properly sealed at
conduit connection
to maintain NEMA
classication.

6/8
Form 1428 (05.16) ©SOR Inc.
Maintenance
Keep the cover tightly secured to the housing.
Prevent moisture or dirt from entering the housing when the cover is off.
Check all screw terminal connections periodically. Vibration may loosen the
screw terminals.
Clean the float and counterweight mechanism periodically to assure continued
free movement.
Make no adjustments to the switch mechanism. It is factory calibrated for
optimum performance.
Do not remove the cover when the unit is energized. Risk of electrical shock
resulting in serious injury and/or death.
Troubleshooting
Symptom Probable Cause
The float is in actuated position
but the switch does not actuate.
a. The terminal block is wired incorrectly. Check wiring.
b. The unit is installed upside-down. Rotate housing so
that the nameplate faces up.
c. The switch is damaged. Contact the factory.
The float is in de-actuated position
but the switch remains actuated.
a. The terminal block is wired incorrectly. Check wiring.
b. The switch is damaged. Contact the factory.
The control will not function
when installed but operates when
removed from process connection.
a. Float travel is inadequate. Check for internal
vessel obstructions.
See Mounting Requirements
Liquid is in the vessel at the
actuation level but the unit does
not respond.
a. The float pivot pin is bound up or dirty. Clean the float pivot pin.
b. The unit is installed upside-down. Rotate housing so that the
nameplate faces up.
c. The specific gravity of the liquid is not sufficient to lift the float.
d. The float is leaking or collapsed. Contact the factory.

Form 1428 (05.16) ©SOR Inc.
7/8
Replacement Parts
Replacement switch assemblies include: bracket, terminal block, magnet, microswitch(es)
installation screws and ground screw. Order replacement parts by part number.
Part Number Description
3698150 SPDT Switch Assembly (A1)
3698151 DPDT Switch Assembly (A4)
3698158
SPDT Switch Assembly (S1)
3698159
DPDT Switch Assembly (S4)
3698184 Interface & Float Assembly
3698185 Interface Gasket
2414001 Interface Screws
* Maximum operating pressure is limited by the float or chamber, depending on the temperature.
Maximum Operating Pressure Ratings*
Chamber
Designator
Chamber
Description
Pressure at Listed Temperature in psig (bar)
100°F
(38°C)
200°F
(93°C)
300°F
(149°C)
400°F
(204°C)
500°F
(260°C)
600°F
(316°C)
650°F
(343°C)
700°F
(371°C)
750°F
(399°C)
A
S40
Carbon Steel
(includes float)
1435
(99)
1435
(99)
1435
(99)
1435
(99)
1435
(99)
1435
(99)
1435
(99)
1378
(95)
1244
(86)
C
S40
Stainless Steel
(includes float)
1799
(124)
1550
(107)
1397
(96)
1282
(88)
1196
(82)
1129
(78)
1110
(77)
1081
(75)
1072
(74)

8/8
Form 1428 (05.16) ©SOR Inc.
14685 West 105th Street, Lenexa, KS 66215
913-888-2630
800-676-6794 USA
Fax 913-888-0767
Registered Quality System to ISO 9001
SORInc.com
Table of contents
Other SOR Switch manuals
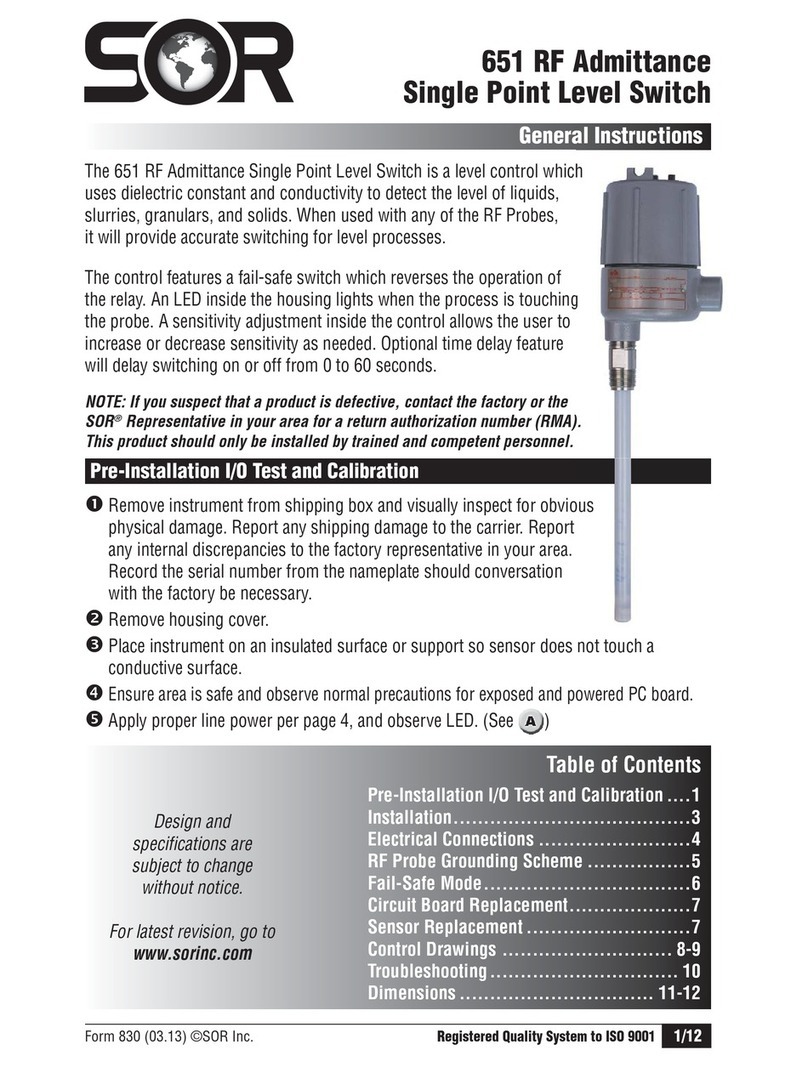
SOR
SOR 651 Series Instruction manual
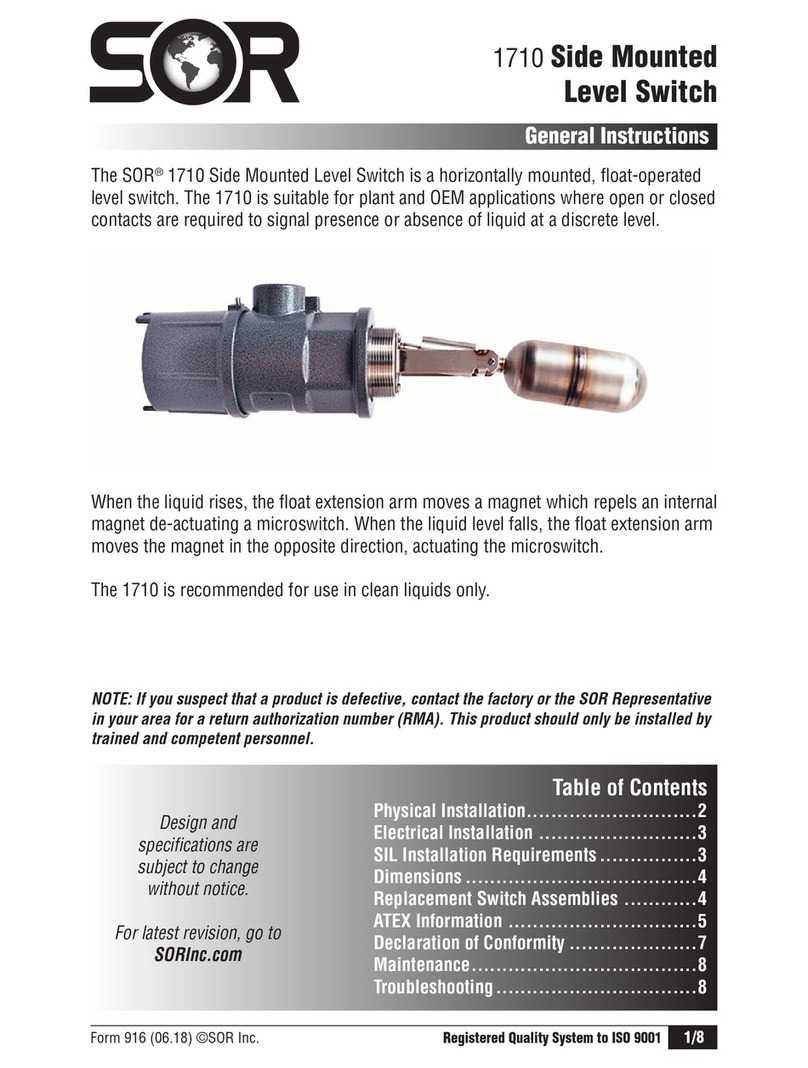
SOR
SOR 1710 Instruction manual
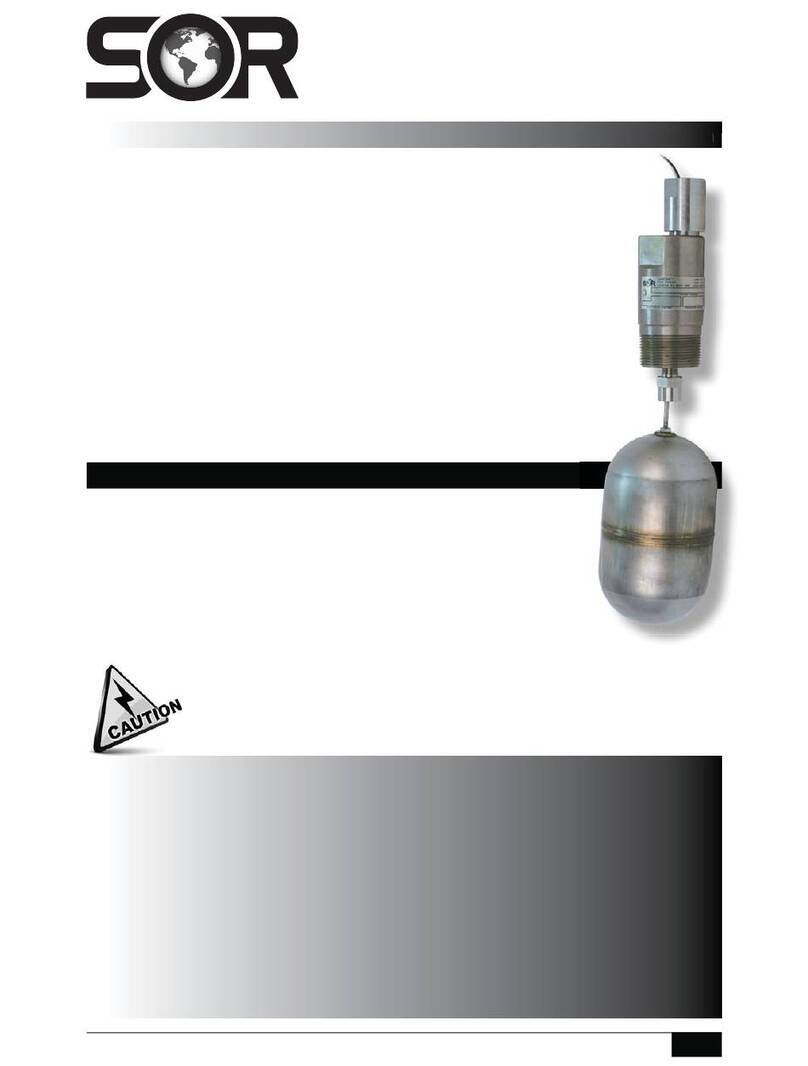
SOR
SOR 1550 Instruction manual

SOR
SOR 102 Instruction manual

SOR
SOR 200 series User manual
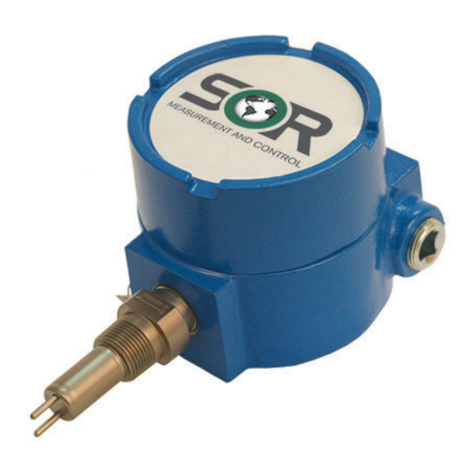
SOR
SOR T21 Instruction manual
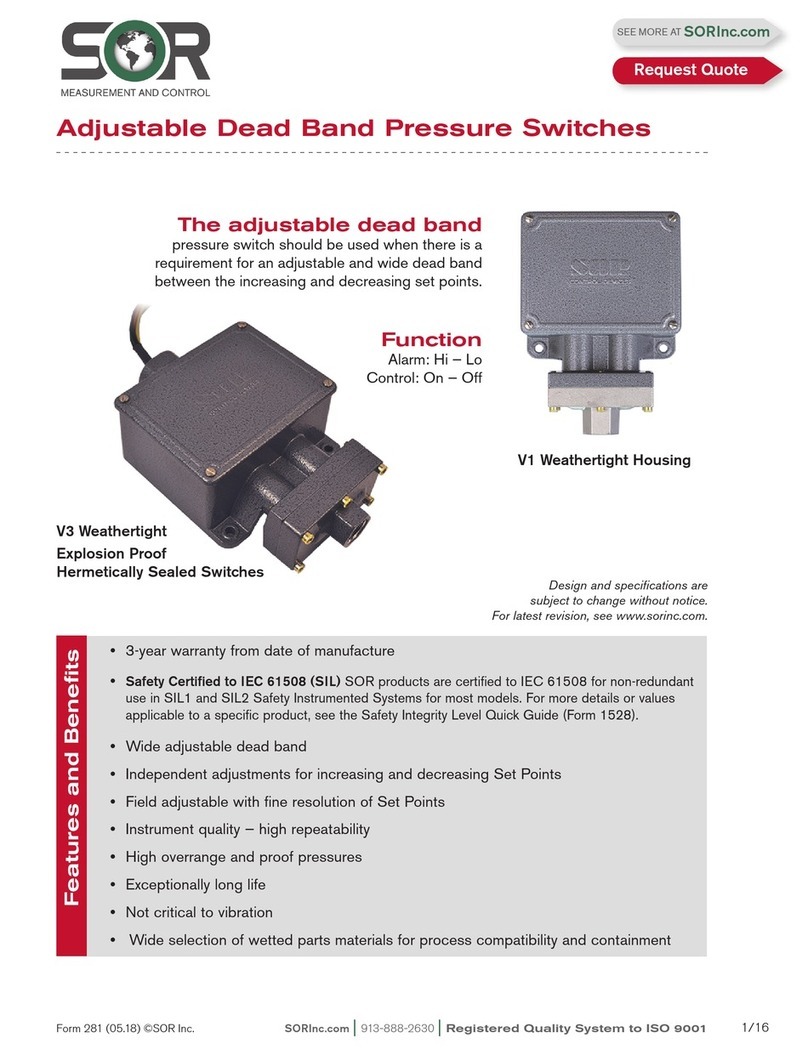
SOR
SOR V1 User manual
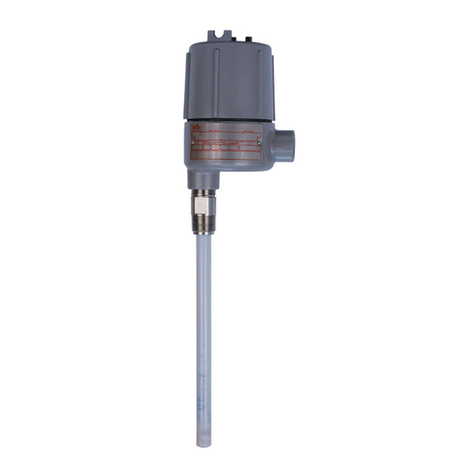
SOR
SOR 651 K9 RF Instruction manual
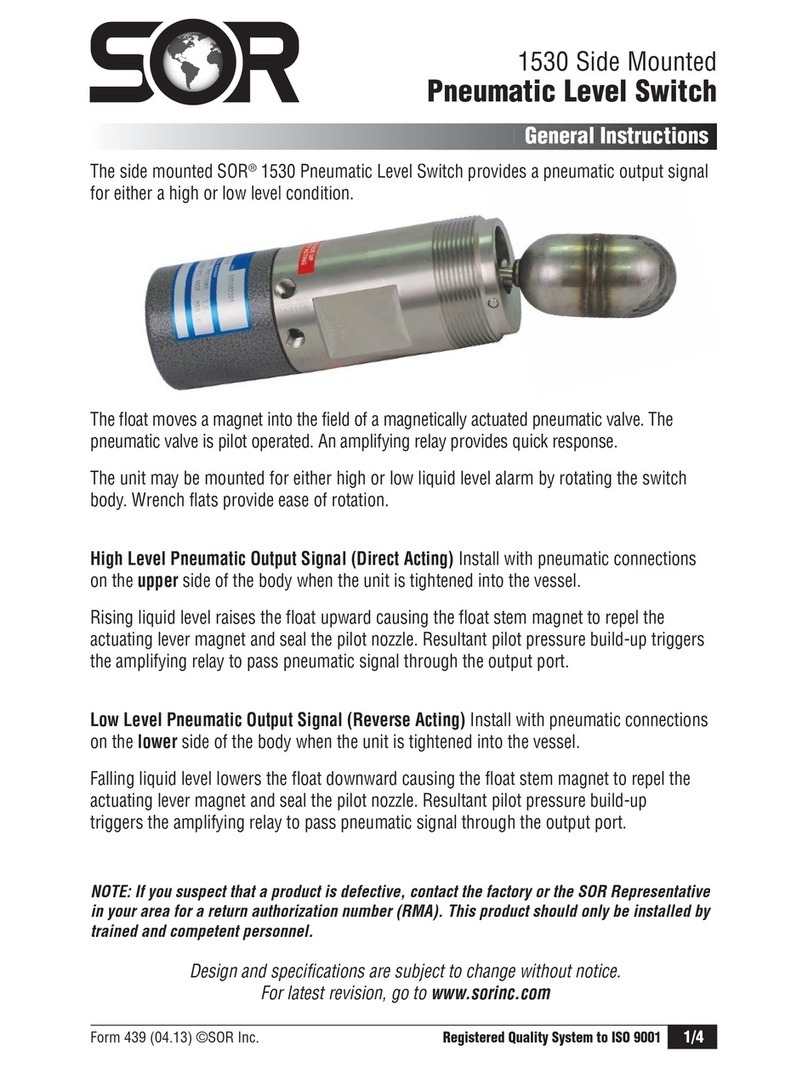
SOR
SOR 1530 Instruction manual
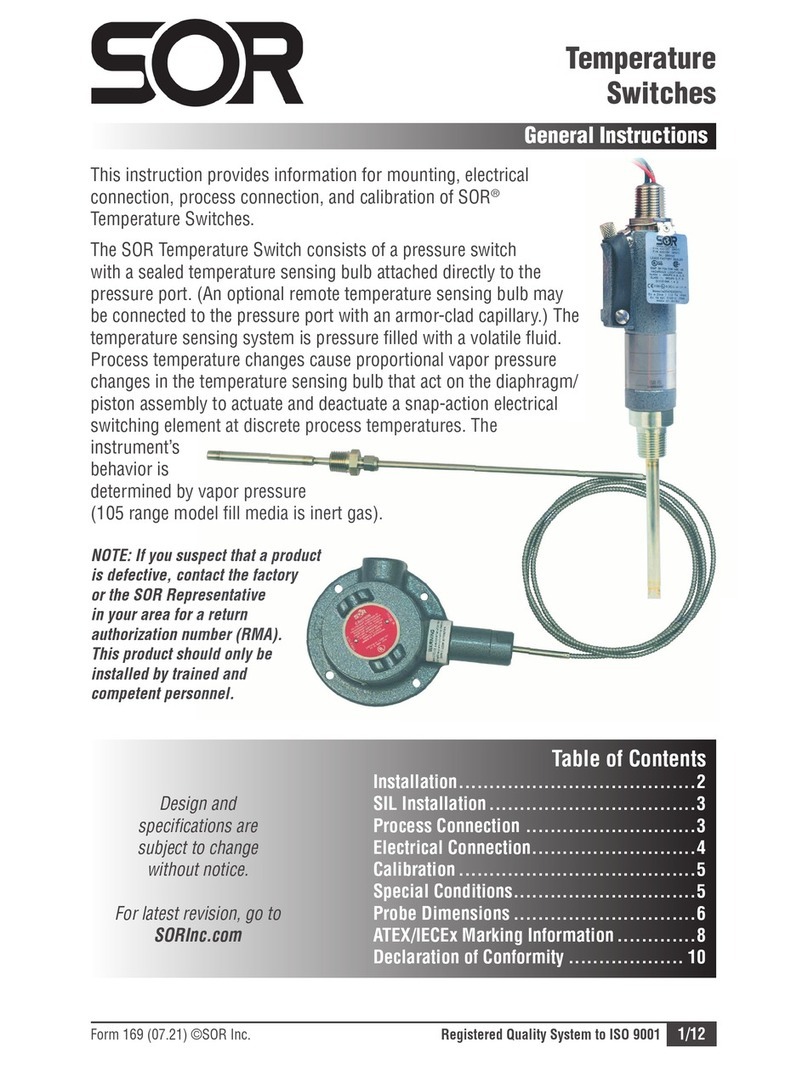
SOR
SOR GI169 Instruction manual