Speakman SV-4116 User manual

800-537-2107 www.speakman.com
NEED HELP?
For additional assistance or service please contact:
INSTALLATION INSTRUCTIONS
SV-4116
SV-4128
Sensor Flushometer
92-SV-41XX-01
IMPORTANT
SAFETY TIPS:
Be sure to read and understand all instructions
before beginning installation.
Inspect all connections after installation.
Cover the drain to avoid loss of parts.
Be sure to wear proper eye protection.
Do NOT over tighten any connections or damage
may occur.
Shut OFF water supplies before beginning
installation.
Observe all local plumbing and building codes.
Do NOT used toothed wrenches on any part of
the Flushometer. This will damage the finish and
void the finish warranty.
Do NOT use pipe sealant/plumbing grease/etc.
on any threaded connection except for the
connection between the control stop body and the
supply pipe.
VALVE SPECIFICATIONS:
EPA regulation prohibits using a higher flushing
volume than is described on the product and/or
tampering with the flow controller inside of the
adjustable tail piece.
Ensure proper structure is in place to support the
Valve and plumbing during use.
Be sure to wear proper eye protection during
installation.
CAUTION
FINISH MAINTENANCE:
Your new product is designed for years of
trouble-free performance. Keep it looking new
by cleaning it periodically with a soft cloth. Avoid
abrasive cleaners, steel wool, and harsh
chemicals as these will dull the finish and void
your warranty.
MAINTENANCE
While designed for years of trouble-free
performance, this product contains several
mechanical and electrical components that are
subject to normal wear and tear. These
components should be inspected on a regular
basis to ensure this product is working properly.
These components include but are not limited to,
the Control Stop, internal O-Rings and Seals,
Sensor Eye Mechanism, Solenoid Mechanism,
Piston, Override Button Assembly, and Vacuum
Breaker. Repair kits are available for purchase for
each of the components given above as well as
components that will need to be serviced less
frequently, such as the spud nut assembly and
inlet piping assembly. See “Repair Parts” section
of this document for a full list of repair kits that are
offered for this product.
NOTE: Regulations prohibit using replacement
parts for this product that would increase the
flushing volume beyond what is stated on the
label. As such, replacement parts are not designed
or intended to be interchangeable with parts that
would cause this product to exceed said flushing
volume.
Battery replacement will be the most common
maintenance item. Standard AA alkaline batteries
will supply approximately 335,000 flush cycles.
Frequency of battery replacement will be
determined by how often the flushometer is
activated. This product is equipped with a low
battery warning system to notify you when
replacement is required. See troubleshooting
guide for additional information.
TOOLS & SUPPLIES NEEDED
Eye Protection
Thread Seal
Tape
Level
Measuring
Tape
Solder Kit
Flat Tip
Screwdriver
Tubing
Cutter
2.5mm Hex Key
Wrench (included)
Bucket
Strap
Wrench
Deburring
Tool
Hacksaw
Phillips
Screwdriver
Drill 3/4”
Hole Saw
Pencil
Wire Nuts
1”
(25.4mm)
FROM CENTERLINE
OF SPUD
2-1/4” MIN
(57mm)
11-1/2” MAX
(292mm)
4-5/16” MIN
5-5/16” MAX
(110mm-135mm)
1”
SUPPLY
NOTE: If you are cutting the vacuum breaker tube to size, consult local plumbing codes to ensure
that the critical line is properly located above the fixture. Typically, the critical line is 6” above the fixture.
ROUGH IN OF SUPPLY PIPE
Before you begin: Your supply pipe must be properly located. The pipe should be no more than
11 ½” above the fixture surface (measured to the centerline of the supply pipe), and within 4-5/16”
to 5-5/16” to the left or right of the fixture’s spud (measured from centerline to centerline). This
product has the ability to receive a supply line from the left or right. Simply rotate the position of the
Valve Body Cover to adapt. See rough-in.
1
A
B
1”
(25.4mm)
FROM CENTERLINE
OF SPUD
2-1/4” MIN
(57mm)
PREPARE SUPPLY PIPE
If your Supply Pipe is already threaded and is the proper length per the rough-in diagram, skip
to STEP 4.
A. Cut supply pipe 1” back from the center line of the fixture’s spud using a hacksaw or tubing
cutter.
B. Deburr both the inside and outside of the supply pipe.
2
A
B
SOLDER THREADED ADAPTER
A. Slide the Threaded NPT Adapter fully over the cut and chamfered supply pipe.
B. Sweat solder the Adapter to the pipe using soldering wire and torch.
3

A
B
C
INSTALL ESCUTCHEON TRIM
4A. Measure from the finished wall to the first thread of the Adapter. Cut the Cover Tube to this length.
B. Slide Escutcheon over the supply pipe until it is against the wall.
C. Slide Cover Tube over the supply pipe and press into the Escutcheon.
A
B
TOWARDS
VALVE INLET
INSTALL CONTROL STOP
A. Apply Thread Sealant Tape to the Threaded Pipe Adapter.
B. Thread the Control Stop onto the Threaded Pipe Adapter. Using a Strap Wrench, tighten into the
final position. Outlet should point towards the Valve Inlet and be parallel to the floor.
5
A
B
REMOVE CONTROL STOP COVER
A. Loosen, but do not remove, the Set Screw of the Control Stop Cover using the included 2.5mm
Hex Key.
B. Remove Control Stop Cover.
6
D
C
C
A
B
FLUSH SUPPLY LINE AND INSPECT FOR LEAKS
A. Using a Flat Tip Screwdriver, verify that the Control Stop Valve is fully closed by turning
Adjustment Screw clockwise until fully seated.
B. Slowly turn ON water supplies and inspect for leaks and piping issues.
C. Hold a bucket or catch basin at the outlet of the Control Stop. Slowly open the Control Stop
Adjustment Screw by turning a Flat Tip Screwdriver counter-clockwise and flush out any debris.
D. Return the Adjustment Screw to a fully closed position.
7
B
A
VERIFY VACUUM BREAKER INSTALLATION
A. Verify that the Split Ring and Vacuum Breaker are properly installed within the Tailpiece.
B. Slide the Coupling Nut onto the Tailpiece as shown below.
8
Spud Nut
Fiber Washer
Rubber Gasket
Escutcheon
C
B
A
Coupling Nut
D
NOTE: Dry connections only! Do NOT use any thread sealant!
TAILPIECE INSTALLATION
A. Verify the Coupling Nut is installed as per the previous step.
B. Slide the Spud Nut, Fiber Washer, Rubber Gasket, and Escutcheon onto the Tailpiece in the
order specified.
C. Install the Tailpiece Assembly into the fixture’s Spud.
D. Hand tighten the Spud Nut to the fixture’s Spud. You can use a Strap Wrench, but do NOT fully
tighten.
9

LUBRICATE VALVE BODY O-RING
Remove protective covering from the Valve Body Inlet. Slide the Nut and Locking Ring towards the
Valve Body to reveal the O-ring. Lubricate the O-ring with water.
10
B
A
C
NOTE: Dry connections only! Do NOT use any thread sealant!
INSTALL VALVE BODY
A. Insert the Valve Body into the Control Stop.
B. Align the Valve Body directly over the Vacuum Breaker tubing, adjusting the Valve Body
horizontally along the connection to the Control Stop as needed to properly align it. Loosely make
threaded connections.
C. Verify correct alignment with the Vacuum Breaker tubing. It may be necessary to cut the Vacuum
Breaker tubing to length.
NOTE: If you are cutting the vacuum breaker tube to size, consult local plumbing codes to ensure
that the critical line is properly located above the fixture. Typically, the critical line is 6” above the
fixture.
11
C
B
A
TIGHTEN CONNECTIONS
Tighten connections in the following order using a Strap Wrench. Do NOT use Toothed Wrench on
any connections as this will damage the finish.
A. Tighten the connection between the Valve Body and Tailpiece Assembly.
B. Tighten the connection between the Valve Body and Control Stop.
C. Tighten the connection between the Tailpiece Assembly and Spud Nut.
12
C
A
B
D
E
ACCESS BATTERY BOX
A. From behind the Valve Body, loosen, but do not remove the Set Screw with the included 2.5mm
Hex Key Wrench.
B. Lift off the Valve Body Cover.
C. Disconnect the BLACK wire connection to the Solenoid.
D. Remove the Battery Box from within the Valve Body Cover.
E. Disconnect the RED wire connection between the Sensor Eye and Battery Box.
13
B
A
D
INSTALL BATTERIES
A. Use a Phillips Head Screwdriver to remove the Battery Box Lid.
B. Install the Batteries per the orientation shown on the Battery Box.
C. Re-assemble the Battery Box while taking care to properly align the tabs in the Lid with the
notches in the Box.
D. Reposition the Battery Box back into the Valve Body Cover, but do NOT make electrical
connections.
14
C
D
A
B
MARK LOCATION FOR CONDUIT
A. Mark vertical centerline from fixture Spud up the wall using a level.
B. Cut Conduit to approximate length taking into account the thickness of the wall and the amount
that is threaded into the Valve Body Cover.
C. Hand thread Conduit Pipe to Valve Body Cover.
D. Position the Valve Body Cover onto the Valve Body with the Conduit extending out the side.
15

A
B
MARK LOCATION FOR CONDUIT
A.
Rotate the Valve Body Cover until the Conduit Pipe makes contact with the wall.
B. Mark the horizontal centerline of the Conduit Pipe on the wall.
C. Remove Valve Body Cover assembly from the Valve Body.
16
C
A
B
Ø 3/4”
MARK LOCATION FOR CONDUIT AND DRILL HOLE
A. Using a level, extend the horizontal centerline until it intersects the vertical centerline.
B. At the intersection of the vertical and horizontal centerlines, drill a Ø 3/4” hole.
C. Unthread and remove the Conduit from the Valve Body Cover.
17
C
E
D
A
B
MARK LOCATION FOR MOUNTING FLANGE
A. Slide the Mounting Flange onto the Conduit.
B. Position the Conduit into the previously drilled hole in wall.
C. Place the Valve Body Cover onto the Valve Body.
D. From behind, thread the Conduit into the Valve Body Cover.
E. Position the Mounting Flange against the wall and mark the two (2) mounting locations.
F. Unthread the Conduit from the Valve Body Cover and remove the Valve Body Cover, Conduit,
and Mounting Flange.
18
A
B
C
D
E
Ø 3/16”
INSTALL MOUNTING FLANGE
A. In the previously marked locations, drill Ø 3/16” holes.
B. Position the two (2) Anchors into the drilled holes.
C.
Place the Mounting Flange against the wall and secure into position using the two (2) Mounting Screws
D. Position the Escutcheon over the Mounting Flange.
E. Slide the Conduit into the Escutcheon and Mounting Flange.
19
AB
C
C
D
MAKE ELECTRICAL CONNECTIONS
A. Attach the Red wire of the Sensor Eye Assembly to the Red T-shaped Converter.
B. Attach the Red wire of the Battery Box to the Red T-shaped Converter.
C. Guide the included power cable through the Conduit piping, then through the hole in the Valve
Body Cover. Attach this to the lower port of the T-shaped converter.
D. Attach Sensor Cable to Solenoid Cable.
20
A
B
C
D
INSTALL CONDUIT TO VALVE BODY COVER
A. Place the Valve Body Cover into position on the Valve Body.
B. Thread the Conduit into the Valve Body Cover.
C. Slide the Escutcheon back to access and secure the Set Screw to the Conduit with the included
2.5mm Hex Key Wrench.
D. From behind secure the Set Screw at the rear of the Valve Body Cover with the included 2.5mm
Hex Key Wrench.
21

A
B
C
NOTE:
Each flushometer requires 6 VAC of power and a between 0.35A and 0.5A of current
to operate properly. 18-gauge wire is recommended to connect units. The number of
Flushometers that can be wired in parallel depends on the capabilities of the sourced
transformer. Example wiring diagram is below. Consult local electrical codes before
installing.
120 VAC
6 VAC
HARDWIRE ELECTRICAL CONNECTIONS
IMPORTANT! BEFORE MAKING ANY ELECTRICAL CONNECTIONS, VERIFY THAT THE INCOMING POWER SUPPLY IS OFF AND LOCKED OUT!
A. From behind the wall, strip the ends of the Power Cable leading to the Flushometer.
B. Make electrical connections from the Flushometer to a 6 VAC Class 2 Transformer (not included). Ensure all connections are properly protected within an electrical box and/or follow all local electrical codes.
C. Make connections to incoming 120V AC supply.
D. Turn power supply back ON and continue with the installation.
22
The factory set range is 25-1/2”. Sensors in the wash closet models are pointed 15 degrees up,
while urinal sensors are pointed 15 degrees down.
A
B
C
CALIBRATE THE SENSOR
A. Remove the protective film covering the Sensor Eye.
B. Test the Sensor by standing in front the Flushometer for about 10 seconds, then stepping away
from the Sensor.
C. You should hear a click as the Solenoid actuates, and see a red-light flash in the Sensor Eye.
23
C
D
B
A
1/2 TURN
TIGHTEN CONNECTIONS
A. Using a Flat Tip Screwdriver, slowly open the Control Stop by about ½ turn. A flush sequence
should begin immediately.
B. Use this time to check for leaks or any loose connections.
C. Continue to loosen the Control Stop Adjustment Screw until desired flush sequence is achieved.
D. Test the Flushometer by activating the Sensor, or by pressing the manual override button for
1 second.
• A flush sequence should begin again.
• Continue to operate the Flushometer until desired flow is achieved, it may take a few
actuations for the flushometer to become hydraulically balanced, this is normal.
24
REINSTALL CONTROL STOP COVER
Reinstall the Control Stop Cover using the included 2.5mm Hex Key Wrench.
25
CALIFORNIA PROPOSITION 65
CALIFORNIA PROPOSITION 65:
WARNING: This product can expose you to chemicals including lead, which is known
to the State of California to cause cancer and birth defects or other reproductive harm.
For more information go to www.P65Warnings.ca.gov.
Wash hands after installation, repair, or removal of this product.
PRODUCT WARRANTY
This product is warranted to be free of defects in material and workmanship for the period listed
below from the date of installation.
Consumer/Residential: Limited Lifetime Warranty
Commercial Use: 5 Year Limited Warranty
Speakman warrants to its purchasers only (“Buyer”) that goods are sold free from defects in materials and
workmanship and conform to Speakman’s specifications at the time of manufacturing, provided the goods
are properly installed and maintained. Buyer’s sole and exclusive remedy for any goods that may prove to
have had a non-conformance within the Warranty Period shall be, at Speakman’s sole option, the repair or
replacement of the non-conforming goods. For additional information please go to www.speakman.com.

COMPLIANCE
CONNECTIONS
ASSE 1037/ASME A112.1037
ASME A112.18.1/CSA B125.2
WaterSense
(1.28 GPF model only)
Inlet: 1” NPT Female
Outlet: 1-1/2” NPSM
ROUGH-IN DIAGRAM
DIMENSIONS SUBJECT TO CHANGE WITHOUT NOTICE. FOR ADA MOUNTING
LOCATIONS, CONSULT ADAAG, ANSI A117.1, AND LOCAL/STATE REGULATIONS.
NOTES
Installer to supply necessary inlet connections.
If you are cutting the vacuum breaker tube to size,
consult local plumbing codes to ensure that the critical
line is properly located above the fixture. Typically, the
critical line is 6” above the fixture.
FLOW RATE
SV-4128 1.28 GPF
SV-4116 1.60 GPF
11
2
"
38mm
9"
228mm
1/2" [13mm] MIN
1 1/2" [38mm] MAX
8 1/8" [206mm] MIN
9 1/8" [232mm] MAX
4 5/16" [111mm] MIN
5 5/16" [137mm] MAX
11
8
"
28mm
13
8
"
35mm
29
16
"
65mm
17
8
"
48mm
1" [25mm] MIN
6" [152mm] MAX
2 5/8" [67mm] MIN
7 5/8" [194mm] MAX
4 9/16" [116mm] MIN
9 9/16" [243mm] MAX
17 5
16
"
440mm
11 1
2
"
293mm
1"-11 1/2
NPT THREAD
1 1/2"-11 1/2
NPSM THREAD
25 1/2" [650mm]
FACTORY SET RANGE
15°
SENSOR EYE
RPG01-118143
SPUD NUT KIT
(SV-4012/4016/4116/4128)
RPG01-118147
TAILPIECE NUT
RPG05-118138
PISTON KIT
(SV-4012/4016/4116/4128)
RPG05-118142
VACUUM BREAKER KIT
RPG11-118155
MANUAL OVERRIDE KIT
RPG11-118156
MANUAL OVERRIDE
INTERNAL KIT
RPG11-118157
MANUAL OVERRIDE
GASKET AND SEAL KIT
RPG11-118158
MANUAL OVERRIDE
COVER KIT
RPG20-118134
SENSOR AND VALVE
COVER KIT (SV-4128)
RPG20-118136
SENSOR AND VALVE
COVER KIT (SV-4116)
RPG31-118140
TAILPIECE PIPING
(SV-4012/4016/4116/4128)
RPG31-118148
CONTROL STOP TO
VALVE BODY PIPING
(SV-4012/4016/4116/4128)
RPG31-118163
INLET SUPPLY KIT
(SV-4012/4016/4116/4128)
RPG39-118160
SOLENOID REPLACEMENT
(SV-4012/4016/4116/4128)
RPG45-118145
SPUD GASKET AND SLIP RING
(SV-4012/4016/4116/4128)
RPG49-118150
O-RING & LOCK RING
FOR CONTROL STOP TO
VALVE BODY PIPE
RPG58-118152
CONTROL STOP
(SV-4012/4016/4116/4128)
RPG58-118153
CONTROL STOP
INTERNAL KIT
RPG58-118154
CONTROL STOP
BONNET, COVER,
& ADJUSTMENT SCREW
RPG05-118162
“AAA” BATTERY BOX
REPAIR PARTS
NOTE: Regulations prohibit using replacement parts for this product that would increase the flushing volume beyond what is stated on the label.
As such, replacement parts are not designed or intended to be interchangeable with parts that would cause this product to exceed said flushing volume.

TROUBLESHOOTING
Note: Before performing any service or troubleshooting, turn off the water supply at the control stop and if possible, flush out remaining water in the flushometer.
1. The Sensor is Not Detecting a User, or the Valve is Not Flushing.
a. The batteries may need to be replaced – check to see if the sensor light is blinking. If it is, replace the batteries before proceeding with the below.
b. The electronic sensor module may need to be replaced. A repair kit is available to do this. See repair parts section of this installation manual for the part number.
c. Try replacing the potentially faulty sensor module with a working one from another unit first as a test.
i. If the replacement works, then the problem lies with the sensor module and a repair kit should be ordered.
ii. If the replacement does not work, then the problem may lie with the solenoid. Follow below troubleshooting steps to diagnose.
d. Listen for an audible click from the solenoid after obstructing the lens for 6 to 7 seconds.
i. If there is an audible click, then there may be debris in the valve body that is preventing the piston from moving. Wash the piston and valve body under running water.
ii. If there is no audible click, then the solenoid may be stuck in the closed position. Order a replacement solenoid. See repair parts section of this installation manual for the part number.
2. The Red Sensor Light is Blinking Once per Second.
a. The batteries are running low. We recommend replacing the batteries.
3. The Red Sensor Light is Blinking Twice per Second.
a. The batteries have been used up. The batteries must be replaced.
4. The Flush Valve is Flushing Continuously or Does Not Shut Off.
a. Check for an audible click from the solenoid.
i. If there is an audible click, proceed with troubleshooting step 4.b
ii. If there is no audible click, order a replacement solenoid.
b. The bypass in the valve body is likely clogged with debris or build-up from the water supply. Remove the valve body and all internal components. Note that there is a small spring which acts as a filter
inside of the bypass. Remove this by turning the valve body upside-down. Wash the filter under running water. Wash the inside of the valve body, including the bypass, under running water.
5. Not Enough Water is Being Supplied to the Ceramic Fixture.
a. Ensure that the correct model of flushometer has been installed. (e.g., ensure a 1.28 GPF flushometer has not been installed to a 1.6 GPF toilet)
b. Ensure that the control stop is adjusted properly. Open the stop further to allow for more water flow.
c. Ensure the supply has enough pressure to support the flushometer.
6. Too Much Water is being Supplied to the Ceramic Fixture.
a. Ensure that the correct model of flushometer has been installed. (e.g., ensure a 1.6 GPF flushometer has not been installed to a 1.28 GPF toilet)
b. Ensure that the control stop is adjusted properly. Close the stop further restrict flow.
7. Flushometer Performs a Flush Cycle on its Own With no User Present.
a. The flushometer is designed to perform a courtesy flush once every 24 hours. This behavior is normal.
b. If the behavior happens more frequently, ensure there is nothing obstructing the sensor lens. Try wiping the lens clean if no physical object is creating an obstruction.
This manual suits for next models
1
Table of contents
Popular Measuring Instrument manuals by other brands

HEIDENHAIN
HEIDENHAIN ID 737748-01 Mounting instructions
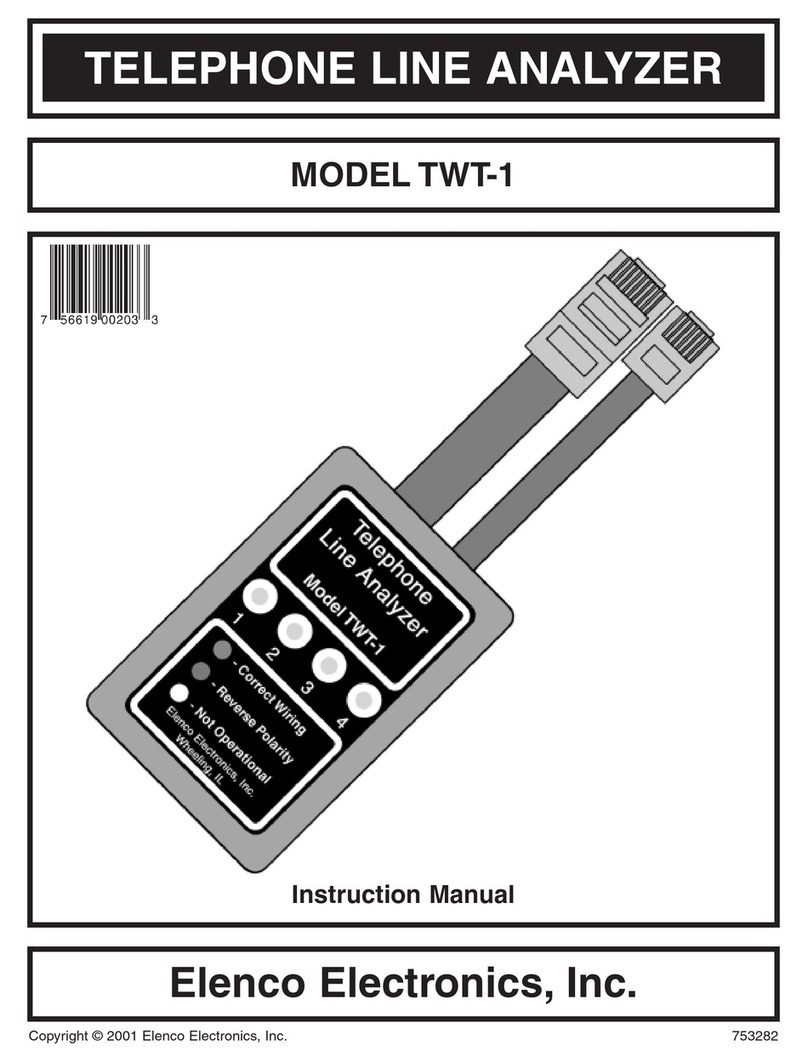
Elenco Electronics
Elenco Electronics TWT-1 instruction manual
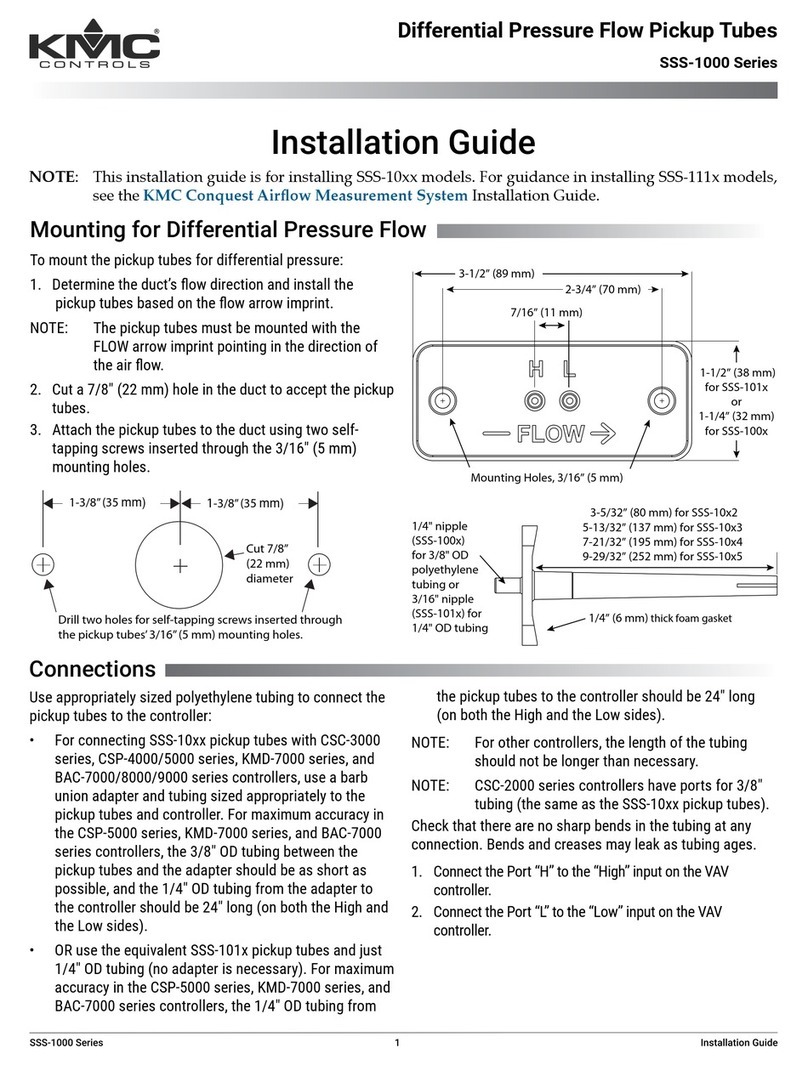
KMC Controls
KMC Controls SSS-1000 Series installation guide
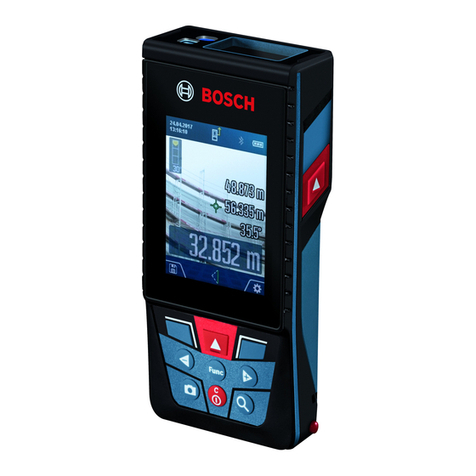
Bosch
Bosch GLM 120 C Professional Original instructions
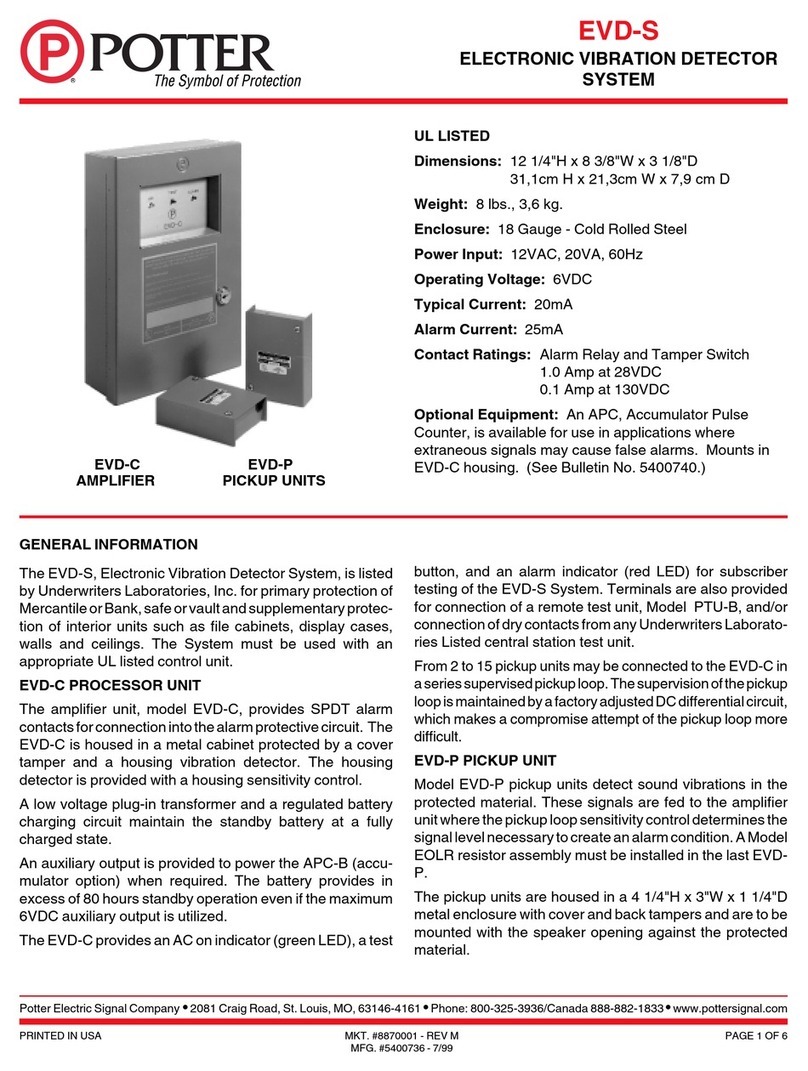
Potter
Potter EVD-S manual
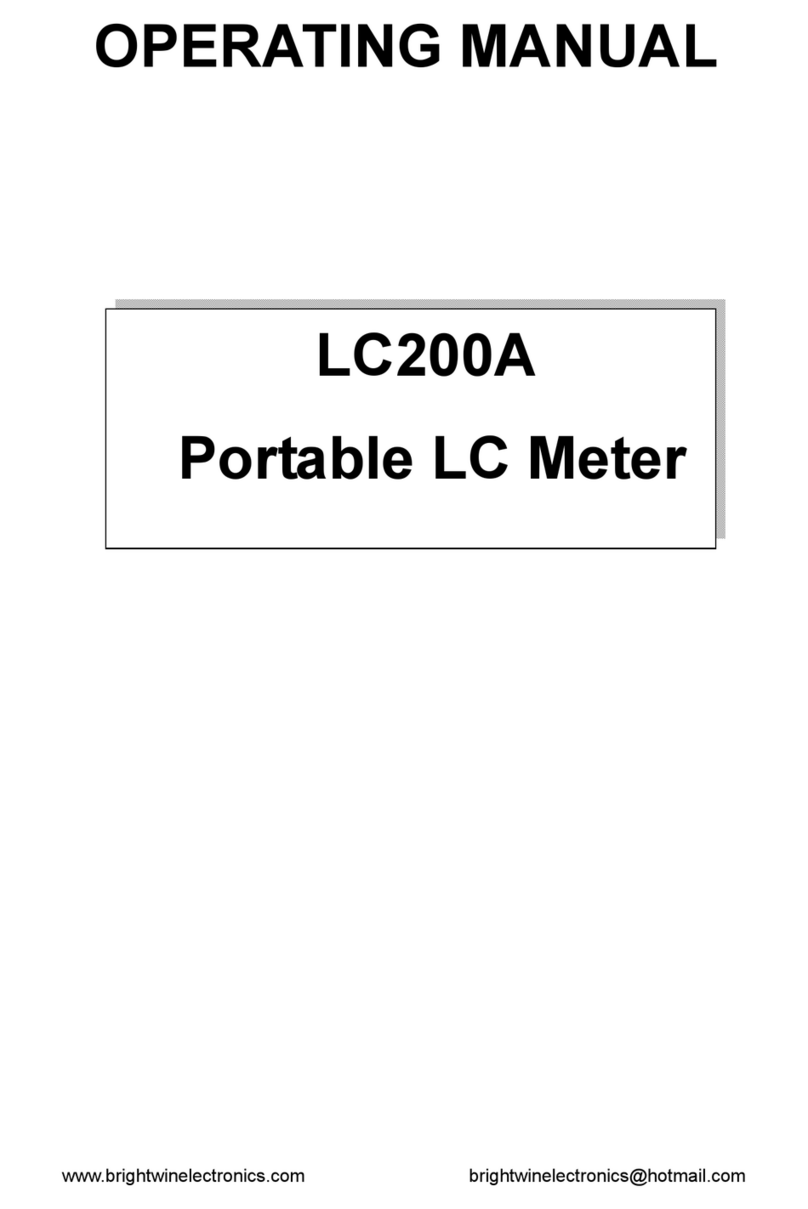
Brightwin Electronics
Brightwin Electronics LC200A operating manual