Specified Air Solutions VIRTUAL WALL User manual

WARNING
Installation must be done by an electrician qualified
in the installation and service of control systems
for heating equipment.
Improper installation, adjustment, alteration, service
or maintenance can result in death, injury or
property damage. Read the Installation, Operation
and Service Manual thoroughly before installing or
servicing this equipment.
Installer
Please take the time to read and understand
these instructions prior to any installation.
Installer must give a copy of this manual to the owner.
Owner
Keep this manual in a safe place in order to provide
your service technician with necessary information.
Specified Air Solutions
1250 William Street
Buffalo, New York 14206
Telephone: +1.716.852.4400
Fax: +1.716.852.0854
Toll Free: 800.828.7450
www.specifiedair.com
© 2017 Specified Air Solutions
Installation Manual
P/N 1010100NA Orig


© 2017
Roberts-Gordon LLC
All rights reserved. No part of this work covered by the copyrights herein may be reproduced
or copied in any form or by any means - graphic, electronic, or mechanical, including
photocopying, recording, taping or information storage and retrieval systems - without the
written permission of Roberts-Gordon LLC.
TABLE OF CONTENTS
SECTION 1: Introduction........................................................ 1
1.1 Safety ........................................................................... 1
1.2 California Proposition 65 .............................................. 1
1.3 What is SPECIFIED AIR SOLUTIONS™VIRTUAL
WALL™ Controller? ..................................................... 1
1.4 General Requirements ................................................. 1
1.5 Example Site Layout..................................................... 1
1.6 Carton Contents ........................................................... 3
SECTION 2: Specifications .................................................... 5
2.1 VIRTUAL WALL™Controller......................................... 5
2.2 Repeater ...................................................................... 5
SECTION 3: Installation.......................................................... 7
3.1 Preparation .................................................................. 7
3.2 Positioning the VIRTUAL WALL™ Controller...............7
3.3 Cable Requirements .................................................... 7
3.4 Check Installation Materials ......................................... 7
3.5 Electrical Installation Requirements of VIRTUAL
WALL™ Controller ....................................................... 8
SECTION 4: WiringDiagram .................................................. 9
SECTION 5: Communications.............................................. 11
5.1 WebCTRL®................................................................ 11
5.2 Communications Between Multiple SAS Products..... 11
5.3 Setting Baud Rate...................................................... 12
5.4 Control Board Setup .................................................. 12
5.5 Sequence of Operations ............................................ 15
SECTION 6: WebCTRL® ....................................................... 17
6.1 Touchscreen Gestures............................................... 17
6.2 Navigating.................................................................. 17
6.3 Graphics .................................................................... 18
6.4 Managing Connections.............................................. 19
6.5 Miscellaneous Actions ............................................... 20
6.6 User Login & Operator Access .................................. 21
6.7 Scheduling ................................................................. 22
6.8 Trending ..................................................................... 25
6.9 Alarms ....................................................................... 29
6.10 Reports .................................................................... 30
6.11 Refining the System ................................................. 33
SECTION 7: Replacement Parts .......................................... 34
7.1 VIRTUAL WALL™ Controller Replacement Parts ...... 35
SECTION 8: The VIRTUAL WALL™Controller Limited
Warranty............................................................ 36


SECTION 1: INTRODUCTION
1
SECTION 1: INTRODUCTION
1. 1 S a f e t y
Yo ur Safety is Important to Us!
This symbol is used throughout
the manual to notify youof
possible fire, electrical or burn
hazards. Please pay special atten-
tion when reading and following
the warnings in these sections.
Installation, service and annual inspection of
controller must be done by an electrician qualified in
the installation and service of control systems for
heating equipment.
Read this manual carefully before installation,
operation, or service of this equipment.
The controller must be applied and operated under
the general concepts of reasonable use and installed
using best building practices.
This controller is not intended for use by persons
(including children) with reduced physical, sensory or
mental capabilities, or lack of experience and knowl-
edge, unless they have been given supervision or
instruction concerning use of the controller by a per-
son responsible for their safety.
Children should be supervised to ensure that they do
not play with the controller.
For optimum performance and safe operating condi-
tions, inspect and maintain controller(s) before every
use and as necessary. If yourequire additional man-
uals, contact your SPECIFIED AIR SOLUTIONS™
independent distributor or Specified Air Solutions at
(716) 852-4400, (800) 828-7450 or at www.specifie-
dair.com.
1.2 California Proposition 65
In accordance with California Proposition 65 require-
ments, a warning label must be placed in a highly
visible location on the outside of the equipment (i.e.,
near equipment’s serial plate).
1.3 What is SPECIFIED AIR SOLUTIONS™
VIRTUAL WALL™ Controller?
The VIRTUAL WALL™Controller is an integrated
control system designed to automate the environ-
ment control and energy usage of all heating, cool-
ing, and ventilation products supplied by SPECIFIED
AIR SOLUTIONS™via a single access point. Capa-
ble of communicating directly with Specified Air
HVAC equipment to allowfor custom set points in
occupied or unoccupied areas and/or times. This
customization of the facility's environment maximizes
efficiency by dividing occupied areas into separate
zones while improving indoor air quality.
For the overall viewof connected components for
VIRTUAL WALL™Controller, see Page 2, Figure 1.
System status and settings are viewed and altered
from a PC or smart device (not supplied).
1. 4 G e n e r a l Re quirements
The VIRTUAL WALL™ Controller series of control-
lers are supplied pre-configured for use with Speci-
fied Air HVAC equipment. Failure to comply with the
installation instructions and configuration may invali-
date the VIRTUAL WALL™Controller limited war-
ranty. See Page 36, Section 8.
The controller must be electrically grounded in accor-
dance with the National Electrical Code®ANSI/NFPA
70 - latest revision.
1.5 Example Site Layout
Page 4, Figure 2 is an example layout for a building
where SPECIFIED AIR SOLUTIONS™VIRTUAL
WALL™ Controller will be used to control the HVAC
systems shown. The layout consists of zones of VIR-
TUAL WALL™Controller.
DANGER
Electrical Shock Hazard
Disconnect electric before service.
Controller must be properly grounded to an
electrical source.
Failure to follow these instructions can
result in death or electrical shock.

VIRTUAL WALL™ CONTROLLER INSTALLATION MANUAL
2
FIGURE 1: Connected Components

SECTION 1: INTRODUCTION
3
1.6 Carton Contents
VWCCPXX: VIRTUAL WALL™ Controller Central Controller
NG
24Vac
N1/Gnd
H1 H3 H2 H4
L
N
G
NL
G
N
88F0
E143900
TYPE: 002003
Power
Off On
Power
Gnd
24Vac
Port 1
485
ARC-
Shield
Net -
Net +
156
Port 2a
Rnet
Gnd
Rnet +
Rnet -
+12V
Xnet +
Xnet -
Gnd Xnet Expansion
Local
Rnet+
Gnd
Sense
+12V
Rnet-
Access
EIA-485
EIA-232
Thermistor/
dry-contact/
Mode Select
Universal Input
mA
RTD
Volts
10V Max, 20mA Max
Inputs: All
UI-4
UI-3
UI-2
UI-1
Gnd
+
Gnd
Gnd
+
+
Gnd
+
8
7
6
5
4
3
2
1
UI-8
Gnd
UI-6
UI-7
UI-5
Gnd
+
+
Gnd
+
Gnd
+
UI-12
UI-11
UI-10
UI-9
+
Gnd
+
Gnd
Gnd
+
Gnd
+
24 Vdc
24 Vdc
200mA maximum
Auto Off On
0-20mA
0-10Vdc
Relay
Controller
Address
1's
10's
Archive Valid
Port 2a Rx
Port 2a Tx
Port 1 Rx
Port 1 Tx
Battery low
Ext. Batt.
Int. Batt.
External
Battery
Gnd
+3V
Status
Module
3V Lithium Battery
CR-123A
0 = Download required
3 = Comm setup error
1 = Control Program Error
4 = System error
8 = Formatting
2 = RAM full
Chase = OK
Status Codes
Class 2
ONLYUse Copper
24Vac, 50VA
Without Keypad:
26Vdc, 23W, 0.9A
Outputs
24Vdc Max, 50mA Max
Format
Pot
2-wire
4-wire
2 wire4 wire
Rx -
Net-
Net+
n/c
Tx -
Tx +
Rx +n/c
EIA-232
DCD
Rx
Tx
DTR
Signal Ground
®
BACnet
OverARCNET156 KBaud
Made in USA
Port 2a BT485
Port 1
Port 1 BT485
Conductors
2A, 50-60 Hz
Blinking Dot = 'Run'
On Off
Enhanced
8
7
6
5
4
3
2
1
8
7
6
5
4
3
2
1
IP Addr
Assigned Default
10/100 BaseT
Ethernet Port E1
100 LAN LINK
®
8
7
6
5
See BAS TableBelow
Protocols 6
MS/TP m
MS/TP s
Off
N2 On
Lon SLTA
Off
BAUD 45
9600 Off Off
19.2 K Off On
38.4 K On Off
76.8 K On On
On
Modbus
8
Off
Off
On
On
Off
4
BACnet
3
7
Off
On
Off
Off
Off
PTP Off Off
On
Access Port 2a
Lon OptionOff On
On
2
1
UO-1
UO-2
UO-3
UO-4
UO-8
UO-7
UO-6
UO-5
On
Off
21
BAS Port
BAS Port Settings
Set Pot Full CW
24Vac
DO NOT APPLY24Vac TO
UNIVERSAL OUTPUTS
External 24Vdc relay coil only
Brownout
3
UO-2
UO-1 2
1
UO-4
UO-3 6
5
4
7
8
6
UO-7
UO-6
UO-5
3
1
2
4
5
UO-8 7
8
+
Gnd
+
Gnd
+
Gnd
+
Gnd
+
Gnd
+
Gnd
+
Gnd
+
Gnd
Aux Power Out Port 2b
Port 2a
IOPro812u
07/10/12
Rev 6
Open Energy
Management Equipment
26Vdc
I/O Pro 812u
CONTROLLER
CB
20A
BLK WHT GRN
L N GND
120V 60HZ
1Ø 20A
POWER IN
TO ADDITIONAL
CONTROLLERS
ETHERNET
CONNECTION TO
TOUCHSCREEN
(RJ45)
ETHERNET
CONNECTION
TO CONTROL
BOARD
WIFI CONNECTION
TO LOCAL
NETWORK
TOUCHSCREEN ADAPTER
OUTPUT: 12VDC 4.0A
COMPUTER ADAPTER
OUTPUT: 12VDC 5.0A
TOUCHSCREEN & COMPUTER
POWER IN
TRANSFORMER
VIRTUAL WALL™ Controller Installation Manual
(P/N 1010100NA)
Inside View
VIRTUAL WALL™ Controller

VIRTUAL WALL™ CONTROLLER INSTALLATION MANUAL
4
FIGURE 2: Example Site Layout
NOTE: Conceptual drawing, not to scale. Venting not shown.

SECTION 2: SPECIFICATIONS
5
SECTION 2: SPECIFICATIONS
2.1 VIRTUAL WALL™Controller
2.1.1 Standard Enclosure
Construction: 16 gauge painted steel, hinged
door, removable knockouts
provided.
Dimensions: W x H x D
(in): 19 x 19 x 7
(cm): 48.3 x 48.3 x 17.8
To uchscreen Dimension: 15" Wide Screen
Weight: 35 lbs (15.9 kg)
2.1.2 Electrical
Power Supply: 120 V (+/- 10%) 1 Ø, 60 Hz
To uchscreen Power Supply:
Input: 120VAC, 1A, 60Hz
Output: 12VDC, 4A
CPU Power Supply:
Input: 120VAC, 1.5A, 60Hz
Output: 12VDC, 5A
Universal Inputs:
Twelve Universal Inputs
0-5 Vdc
0-10 Vdc
0-20 mA
Thermister (10k ohm type II)
1K ohm RTD
Dry Contact
Universal Outputs:
0-10 Vdc
0-20 mA
Relay
HOA (hand/off/auto) switches for
all outputs
Communication Ports:
Port 1: Configurable for ARC156 or EIA-485 (2-wire).
Built-in support for BACnet (MS/TP or ARC156), N2,
and Modbus
Port 2a: Configurable for EIA-232 or EIA-485 (2-wire
or 4-wire). Network protocol selectable for BACnet
(MS/TP or PTP), Modbus, N2, LonWorks SLTA, or
modem.
Rnet port: Interface with a BACview5, BACview6, RS
sensors, ZS sensors or local laptop.
Battery: CR123A, 10 yr life, 720 cumulative hours of
power outage
NOTE: Battery for time keeping purposes and saving
trend data during power outages.
Control Board Listed by: UL-916, CE, FCC Part 15-
Subpart B - Class A. BTL (BACnet Test Labs) - BAC-
net Building Controller (B-BC)
2.2 Repeater
2.2.1 Standard Enclosure
Construction: Fabricated in accordance with UL
specifications from code gauge steel,
NEMA 1.
Finish: Austin screwcover boxes standard
construction galvanized steel with
ANSI 61 gray polyester powder
coating.
Dimensions: W x H x D
(in): 12 x 12 x 4
(cm): 30.5 x 30.5 x 10.5
2.2.2 Electrical
Power Supply: 120 V (+/- 10%) 1 Ø, 60 Hz
Ports: RS-485 Communications Bus
RS-232 Direct Connect Bus

VIRTUAL WALL™ CONTROLLER INSTALLATION MANUAL
6
FIGURE 3: VIRTUAL WALL™Controller Specifications

SECTION 3: INSTALLATION
7
SECTION 3: INSTALLATION
3.1 Preparation
Before installing the controller, observe the following:
3.1.1 Ensure that youhave a copy of the site layout
for the project that clearly identifies all controllers on
the network chain.
3.1.2 Familiarize yourself with the controller compo-
nents and the board diagram. See Page 10, Figure 4.
3.2 Positioningthe VIRTUAL WALL™ Controller
3.2.1 Choose a mounting location for the controller.
The Virtual Wall controller may lie at any node along
the MS/TP daisy chain. For serviceability, it is conve-
nient to mount the controller at occupant level. It is
recommended to mount the controller in the vicinity
of exhaust fan and/or lighting control.
Do not mount controller outdoors. Controller must not
be installed where subjected to adverse conditions
such as: combustible, oily, or hazardous vapors or
dust; excessive moisture or dirt; vibration. To avoid
damage from possible drips, do not mount controller
directly beneath CORAYVAC®vacuum pump. Avoid
installing the controller in mezzanines, direct sun-
light, or near external heat sources because these
locations usually have unpredictable temperature
rises.
Maximum length of communication wire from the first
controller to the last is 4000' (1219 m) without the use
of a repeater. A repeater is available for wire length
greater than 4000' (1219 m). See Page 14, Section
5.4.1.
3.2.2 Position the controller at occupant level for
ease of service.
Recommended screwsize: 1/4" - 5/16" x 2" with
washers.
3.3 Cable Requirements
3.3.1 VIRTUAL WALL™ Controller
Belowis the recommended cable for the various
connections for VIRTUAL WALL™ Controller:
• Control Power Supply
The power connection should be made with cable,
size 12 AWG.
• Local Network Connection
The local connection to the network should be
made with a standard Ethernet cable
• Communications between Multiple Controllers
(MS/TP)
One twisted pair of 22 AWG minimum or equivalent
shielded high speed, lowcapacitance cable. Maxi-
mum network length: 4000' (1219 m) at 19.2K Baud
Rate.
3.4 Check Installation Materials
3.4.1 Control Wiring
Shielded cable: one twisted pair of stranded 22 AWG
minimum high speed, lowcapacitance wire is
required for MS/TP communications between con-
trollers.
3.4.2 ProgrammingDetails
Controllers are pre-programmed. See product spe-
cific IOS manual for details.
3.4.3 Repeater
Belowis the recommended cable for the various con-
nections for the repeater:
• Line Power Supply
The power connection should be made with
cable, size 18 AWG.
• RS485 Communications
One twisted pairs of 22 AWG minimum or equiva-
lent shielded cable; Belden #3105A.
DANGER
Electrical Shock Hazard
Disconnect electric before service.
Controller must be properly grounded to an
electrical source.
Failure to follow these instructions can
result in death or electrical shock.
18.000
14.000
Ø0.359 (4X)

VIRTUAL WALL™ CONTROLLER INSTALLATION MANUAL
8
3.5 Electrical Installation Requirements of
VIRTUAL WALL™ Controller
• VIRTUAL WALL™ Controller must be feeding from a
local fused isolator for a total amperage not exceed-
ing 20A.
DANGER
Electrical Shock Hazard
Disconnect electric before service.
Controller must be properly grounded to an
electrical source.
Failure to follow these instructions can
result in death or electrical shock.

SECTION 4: WIRING DIAGRAM
9
SECTION 4: WIRING DIAGRAM
DANGER
Electrical Shock Hazard
Disconnect electric before service.
Controller must be properly grounded to an
electrical source.
Failure to follow these instructions can
result in death or electrical shock.

VIRTUAL WALL™ CONTROLLER INSTALLATION MANUAL
10
FIGURE 4: VIRTUAL WALL™ Controller WiringDiagram
NG
24Vac
N1/Gnd
H1 H3 H2 H4
L
N
G
NL
G
N
88F0
E143900
TYPE: 002003
Power
Off On
Power
Gnd
24Vac
Port 1
485
ARC-
Shield
Net -
Net +
156
Port 2a
Rnet
Gnd
Rnet +
Rnet -
+12V
Xnet +
Xnet -
Gnd Xnet Expansion
Local
Rnet+
Gnd
Sense
+12V
Rnet-
Access
EIA-485
EIA-232
Thermistor/
dry-contact/
Mode Select
Universal Input
mA
RTD
Volt s
10V Max, 20mA Max
Inputs: All
UI-4
UI-3
UI-2
UI-1
Gnd
+
Gnd
Gnd
+
+
Gnd
+
8
7
6
5
4
3
2
1
UI-8
Gnd
UI-6
UI-7
UI-5
Gnd
+
+
Gnd
+
Gnd
+
UI-12
UI-11
UI-10
UI-9
+
Gnd
+
Gnd
Gnd
+
Gnd
+
24 Vdc
24 Vdc
200mA maximum
Auto Off On
0-20mA
0-10Vdc
Relay
Controller
Address
1's
10's
Archive Valid
Port 2a Rx
Port 2a Tx
Port 1 Rx
Port 1 Tx
Battery low
Ext. Batt.
Int. Batt.
External
Battery
Gnd
+3V
Status
Module
3V Lithium Battery
CR-123A
0 = Download required
3 = Comm setup error
1 = Control Program Error
4 = System error
8 = Formatting
2 = RAM full
Chase = OK
Status Codes
Class 2
ONLY Use Copper
24Vac, 50VA
Without Keypad:
26Vdc, 23W, 0.9A
Outputs
24Vdc Max, 50mA Max
Format
Pot
2-wire
4-wire
2 wire 4 wire
Rx -
Net-
Net+
n/c
Tx -
Tx +
Rx +n/c
EIA-232
DCD
Rx
Tx
DTR
Signal Ground
®
BACnet
Over ARCNET156 KBaud
Made in USA
Port 2a BT485
Port 1
Port 1 BT485
Conductors
2A, 50-60 Hz
Blinking Dot = 'Run'
On Off
Enhanced
8
7
6
5
4
3
2
1
8
7
6
5
4
3
2
1
IP Addr
Assigned Default
10/100 BaseT
Ethernet Port E1
100 LAN LINK
®
8
7
6
5
See BAS Table Below
Protocols 6
MS/TP m
MS/TP s
Off
N2 On
Lon SLTA
Off
BAUD 45
9600 Off Off
19.2 K Off On
38.4 K On Off
76.8 K On On
On
Modbus
8
Off
Off
On
On
Off
4
BACnet
3
7
Off
On
Off
Off
Off
PTP Off Off
On
Access Port 2a
Lon OptionOff On
On
2
1
UO-1
UO-2
UO-3
UO-4
UO-8
UO-7
UO-6
UO-5
On
Off
21
BAS Port
BAS Port Settings
Set Pot Full CW
24Vac
DO NOT APPLY 24Vac TO
UNIVERSAL OUTPUTS
External 24Vdc relay coil only
Brownout
3
UO-2
UO-1 2
1
UO-4
UO-3 6
5
4
7
8
6
UO-7
UO-6
UO-5
3
1
2
4
5
UO-8 7
8
+
Gnd
+
Gnd
+
Gnd
+
Gnd
+
Gnd
+
Gnd
+
Gnd
+
Gnd
Aux Power Out Port 2b
Port 2a
IOPro812u
07/10/12
Rev 6
Open Energy
Management Equipment
26Vdc
I/O Pro 812u
CONTROLLER
CB
20A
BLK WHT GRN
L N GND
120V 60HZ
1Ø 20A
POWER IN
TO ADDITIONAL
CONTROLLERS
ETHERNET
CONNECTION TO
TOUCHSCREEN
(RJ45)
ETHERNET
CONNECTION
TO CONTROL
BOARD
WIFI CONNECTION
TO LOCAL
NETWORK
TOUCHSCREEN ADAPTER
OUTPUT: 12VDC 4.0A
COMPUTER ADAPTER
OUTPUT: 12VDC 5.0A
TOUCHSCREEN & COMPUTER
POWER IN
TRANSFORMER

SECTION 5: COMMUNICATIONS
11
SECTION 5: COMMUNICATIONS
When multiple SAS products are networked together,
the controllers communicate through MS/TP wiring
arranged in series from one controller to the next.
See Page 12, Figure 5
5.1 WebCTRL®
WebCTRL® comes standard with the Virtual Wall
Controller package. This webbased monitoring soft-
ware allows for quick and easy control of every
device on the MS/TP network chain. Plant layout
graphics, product graphics, scheduling, alarm moni-
toring, parameter trending and much more are avail-
able from the comfort of a desk. Software is installed
on the touchscreen computer and connected to the
local network and all other computers are able to
gain access through this point. The Virtual Wall Con-
troller acts as the IP connection point to the local net-
work.See Section 6 for WebCTRL® details.
5.2 Communications Between Multiple SAS
Products
The controllers from each SAS product must have
MS/TP communications wired in series. Page 12,
Figure 5. Connect the MS/TP (Port 1) terminal on
controller #1 to the MS/TP (Port 1) terminal on con-
troller #2 and so on in a daisy chain fashion. Shield
wires for MS/TP cables should be twisted together,
but not grounded, at all satellite controllers in daisy
chain. Ground shield wire at central panel only.
Maximum of 32 controllers in series. For communica-
tion cable requirements, see Page 7, Section 3.3
A unique MAC address is required for each controller
on the MS/TP network. Set the MAC address using
the Rotary Switches. For help locating these, see the
labeled control board diagram in Figure 3. There are
2 rotary switches. The upper rotary switch is labeled
"1's" and lower rotary switch is labeled "10's". To set
the MAC address for the first 9 controllers, the lower
rotary switch (10's) is set to "0", the upper rotary
switch (1's) is set to the appropriate controller num-
ber. To set the MAC address for controller numbers
10 and up, the setting of the lower rotary switch (10's)
must be combined with the value of the upper rotary
switch (1's). For example: To set the MAC address to
"17", adjust the lower rotary switch (10's) to "1" and
adjust the upper rotary switch (1's) to "7".
NOTE: The Virtual Wall Controller should be set to
"1". Changes to the rotary switches are acknowl-
edged only after the board has been power cycled.
Contact Specified Air Solutions or your SPECIFIED
AIR SOLUTIONS™independent distributor, if more
than 32 satellite controllers are required.

VIRTUAL WALL™ CONTROLLER INSTALLATION MANUAL
12
FIGURE 5: MS/TP Communications Between Controllers
5.3 SettingBaud Rate
To set the baud rate for the MS/TP network on Port 1
configure the board for a baud rate of 19.2K by set-
ting DIP switch #5 to "ON". See chart in Figure 6 for
baud rate settings.
NOTE: Changes to the DIP switches are acknowl-
edged only after the board has been power cycled.
NOTE: Higher baud rates can be used over shorter
distances. The maximum rate of 76.8k can be used
for distances up to 2000ft (609m). A terminating
resistor is required for 76.8k. A baud rate of 38.4k
can be used without terminating resistors for dis-
tances up to approximately 3000 ft.
FIGURE 6: SettingBaud Rate
5.4 Control Board Setup
Universal Inputs and Outputs, Ports, Rotary Switches
and DIP switch must all be configured for the board to
work properly. Reference the labeled control board,
Figure 3, for help locating parts on the control board.
Each Input and Output has a configurable jumper.
For the Universal Inputs (UI) the jumpers are located
next to the input terminals. A diagram of the jumper
configurations is shown on the board.
For the Universal Outputs (UO) the jumpers are
located next to the HOA switches. A diagram consist-
ing of the jumper, the indicator light, the Pot dial and
HOA switch is also shown on the board. Each HOA
switch should be set to AUTO.
Port 1 needs to be configured to operate as the BMS
port. To do this, a combination of the Port jumpers
and the DIP switch configuration is required. To
ensure Port 1 is operating as the BMS/BAS Port,
switch 3 of the DIP switch should be OFF. Switches
6, 7 & 8 should be configured for BACnet MS/TP
m(master) as shown in the diagram on the board.
Each should be set to OFF. Finally, the Baud Rate for
Port 1 is set using switches 4 & 5. It is important to
note that the maximum communication distance
achievable before a REPEATER is necessary is
dependent on the Baud Rate. A maximum Baud Rate
of 19.2 K can be used for distances up to 4000 ft
(1219 m). If the maximum Baud Rate of the Port is
Archive Valid
Port 2a Rx
Port 2a Tx
Port 1 Rx
Port 1 Tx
Battery low
External
Battery
Gnd
+3V
Brownout
88F0
E143900
TYPE: 002003
Power
Off On
Power
Gnd
24Vac
485
ARC-
Shield
Net -
Net +
156
Port 2a
Rnet
Gnd
Rnet +
Rnet -
+12V
Xnet +
Xnet -
Gnd Xnet Expansion
Local
Rnet+
Gnd
Sense
+12V
Rnet-
Access
EIA-485
EIA-232
Thermistor/
dry-contact/
Mode Select
Universal Input
mA
RTD
Volts
10V Max, 20mA Max
Inputs: All
UI-4
UI-3
UI-2
UI-1
Gnd
+
Gnd
Gnd
+
+
Gnd
+
8
7
6
5
4
3
2
1
UI-8
Gnd
UI-6
UI-7
UI-5
Gnd
+
+
Gnd
+
Gnd
+
UI-12
UI-11
UI-10
UI-9
+
Gnd
+
Gnd
Gnd
+
Gnd
+
24 Vdc
24 Vdc
200mA maximum
Auto Off On
0-20mA
0-10Vdc
Relay
Controller
Address
1's
10's
Ext. Batt.
Int. Batt.
Status
Module
3V Lithium Battery
CR-123A
0 = Download required
3 = Comm setup error
1 = Control Program Error
4 = System error
8 = Formatting
2 = RAM full
Chase = OK
Status Codes
Class 2
ONLY Use Copper
24Vac, 50VA
Without Keypad:
26Vdc, 23W, 0.9A
Outputs
24Vdc Max, 50mA Max
Format
Pot
2-wire
4-wire
2 wire 4 wire
Rx -
Net-
Net+
n/c
Tx -
Tx +
Rx +n/c
EIA-232
DCD
Rx
Tx
DTR
Signal Ground
®
BACnet
Over ARCNET156 KBaud
Made in USA
Port 2a BT485
Port 1
Port 1 BT485
Conductors
2A, 50-60 Hz
Blinking Dot = 'Run'
On Off
Enhanced
8
7
6
5
4
3
2
1
8
7
6
5
4
3
2
1
IP Addr
Assigned Default
10/100 BaseT
Ethernet Port E1
100 LAN LINK
8
7
6
5
See BAS Table Below
Protocols 6
MS/TP m
MS/TP s
Off
N2 On
Lon SLTA
Off
BAUD 45
9600 Off Off
19.2 K Off On
38.4 K On Off
76.8 K On On
On
Modbus
8
Off
Off
On
On
Off
4
BACnet
3
7
Off
On
Off
Off
Off
PTP Off Off
On
Access Port 2a
Lon OptionOff On
On
2
1
UO-1
UO-2
UO-3
UO-4
UO-8
UO-7
UO-6
UO-5
On
Off
21
BAS Port
BAS Port Settings
Set Pot Full CW
24Vac
DO NOT APPLY 24Vac TO
UNIVERSAL OUTPUTS
External 24Vdc relay coil only
3
UO-2
UO-1 2
1
UO-4
UO-3 6
5
4
7
8
6
UO-7
UO-6
UO-5
3
1
2
4
5
UO-8 7
8
+
Gnd
+
Gnd
+
Gnd
+
Gnd
+
Gnd
+
Gnd
+
Gnd
+
Gnd
Aux Power Out Port 2b
Port 2a
IOPro812u
07/10/12
Rev 6
Open Energy
Management Equipment
26Vdc
I/O Pro 812u
CONTROLLER
Rotary Switches
Range 1-99
Archive Valid
Port 2a Rx
Port 2a Tx
Port 1 Rx
Port 1 Tx
Battery low
External
Battery
Gnd
+3V
Brownout
88F0
E143900
TYPE: 002003
Power
Off On
Power
Gnd
24Vac
485
ARC-
Shield
Net -
Net +
156
Port 2a
Rnet
Gnd
Rnet +
Rnet -
+12V
Xnet +
Xnet -
Gnd Xnet Expansion
Local
Rnet+
Gnd
Sense
+12V
Rnet-
Access
EIA-485
EIA-232
Thermistor/
dry-contact/
Mode Select
Universal Input
mA
RTD
Volts
10V Max, 20mA Max
Inputs: All
UI-4
UI-3
UI-2
UI-1
Gnd
+
Gnd
Gnd
+
+
Gnd
+
8
7
6
5
4
3
2
1
UI-8
Gnd
UI-6
UI-7
UI-5
Gnd
+
+
Gnd
+
Gnd
+
UI-12
UI-11
UI-10
UI-9
+
Gnd
+
Gnd
Gnd
+
Gnd
+
24 Vdc
24 Vdc
200mA maximum
Auto Off On
0-20mA
0-10Vdc
Relay
Controller
Address
1's
10's
Ext. Batt.
Int. Batt.
Status
Module
3V Lithium Battery
CR-123A
0 = Download required
3 = Comm setup error
1 = Control Program Error
4 = System error
8 = Formatting
2 = RAM full
Chase = OK
Status Codes
Class 2
ONLY Use Copper
24Vac, 50VA
Without Keypad:
26Vdc, 23W, 0.9A
Outputs
24Vdc Max, 50mA Max
Format
Pot
2-wire
4-wire
2 wire 4 wire
Rx -
Net-
Net+
n/c
Tx -
Tx +
Rx +n/c
EIA-232
DCD
Rx
Tx
DTR
Signal Ground
®
BACnet
Over ARCNET156 KBaud
Made in USA
Port 2a BT485
Port 1
Port 1 BT485
Conductors
2A, 50-60 Hz
Blinking Dot = 'Run'
On Off
Enhanced
8
7
6
5
4
3
2
1
8
7
6
5
4
3
2
1
IP Addr
Assigned Default
10/100 BaseT
Ethernet Port E1
100 LAN LINK
8
7
6
5
See BAS Table Below
Protocols 6
MS/TP m
MS/TP s
Off
N2 On
Lon SLTA
Off
BAUD 45
9600 Off Off
19.2 K Off On
38.4 K On Off
76.8 K On On
On
Modbus
8
Off
Off
On
On
Off
4
BACnet
3
7
Off
On
Off
Off
Off
PTP Off Off
On
Access Port 2a
Lon OptionOff On
On
2
1
UO-1
UO-2
UO-3
UO-4
UO-8
UO-7
UO-6
UO-5
On
Off
21
BAS Port
BAS Port Settings
Set Pot Full CW
24Vac
DO NOT APPLY 24Vac TO
UNIVERSAL OUTPUTS
External 24Vdc relay coil only
3
UO-2
UO-1 2
1
UO-4
UO-3 6
5
4
7
8
6
UO-7
UO-6
UO-5
3
1
2
4
5
UO-8 7
8
+
Gnd
+
Gnd
+
Gnd
+
Gnd
+
Gnd
+
Gnd
+
Gnd
+
Gnd
Aux Power Out Port 2b
Port 2a
IOPro812u
07/10/12
Rev 6
Open Energy
Management Equipment
26Vdc
I/O Pro 812u
CONTROLLER
Controller
Address
1's
10's
On Off
Enhanced
IP Addr
Assigned Default
8
7
6
5
See BAS Table Below
Protocols 6
MS/TP m
MS/TP s
Off
N2 On
Lon SLTA
Off
BAUD 45
9600 Off Off
19.2 K Off On
38.4 K On Off
76.8 K On On
On
Modbus
8
Off
Off
On
On
Off
4
BACnet
3
7
Off
On
Off
Off
Off
PTP Off Off
On
Access Port 2a
Lon OptionOff On
On
2
1
On
Off
21
BAS Port
BAS Port Settings

SECTION 5: COMMUNICATIONS
13
used, 76.8 K, a REPEATER is required after 2000 ft
(609 m) and terminating resistors put in line. Set
switch 4 to OFF and switch 5 to ON for 19.2K. DIP
switch set up is complete. Only switch 5 should be
ON. Lastly locate the Port 1 jumper. This should be
set to 485.

VIRTUAL WALL™ CONTROLLER INSTALLATION MANUAL
14
5.4.1 Repeater
If the MS/TP communications wire length is above 4000' (1219 m), a repeater must be used to extend the
signal. The repeater can also be used to install in different methods:
• To extend communications beyond the standard 4000' (1219 m) limitation. See Page 14, Figure 7.
• To add parallel branches of VIRTUAL WALL™Controller communications bus wiring.
See Page 15, Figure 8.
NOTE: The maximum number of VIRTUAL WALL™Controllers that can be installed is 32.
FIGURE 7: Repeater External Wiring
®
Archive Valid
Port 2a Rx
Port 2a Tx
Port 1 Rx
Port 1 Tx
Battery low
External
Battery
Gnd
+3V
Brownout
88F0
E143900
TYPE: 002003
Power
Off On
Power
Gnd
24Vac
485
ARC-
Shield
Net -
Net +
156
Port 2a
Rnet
Gnd
Rnet +
Rnet -
+12V
Xnet +
Xnet -
Gnd Xnet Expansion
Local
Rnet+
Gnd
Sense
+12V
Rnet-
Access
EIA-485
EIA-232
Thermistor/
dry-contact/
Mode Select
Universal Input
mA
RTD
Volts
10V Max, 20mA Max
Inputs: All
UI-4
UI-3
UI-2
UI-1
Gnd
+
Gnd
Gnd
+
+
Gnd
+
8
7
6
5
4
3
2
1
UI-8
Gnd
UI-6
UI-7
UI-5
Gnd
+
+
Gnd
+
Gnd
+
UI-12
UI-11
UI-10
UI-9
+
Gnd
+
Gnd
Gnd
+
Gnd
+
24 Vdc
24 Vdc
200mA maximum
Auto Off On
0-20mA
0-10Vdc
Relay
Controller
Address
1's
10's
Ext. Batt.
Int. Batt.
Status
Module
3V Lithium Battery
CR-123A
0 = Download required
3 = Comm setup error
1 = Control Program Error
4 = System error
8 = Formatting
2 = RAM full
Chase = OK
Status Codes
Class 2
ONLY Use Copper
24Vac, 50VA
Without Keypad:
26Vdc, 23W, 0.9A
Outputs
24Vdc Max, 50mA Max
Format
Pot
2-wire
4-wire
2 wire4 wire
Rx -
Net-
Net+
n/c
Tx -
Tx +
Rx +n/c
EIA-232
DCD
Rx
Tx
DTR
Signal Ground
®
BACnet
Over ARCNET156 KBaud
Made in USA
Port 2a BT485
Port 1
Port 1 BT485
Conductors
2A, 50-60 Hz
Blinking Dot = 'Run'
On Off
Enhanced
8
7
6
5
4
3
2
1
8
7
6
5
4
3
2
1
IP Addr
Assigned Default
10/100 BaseT
Ethernet Port E1
100 LAN LINK
8
7
6
5
See BAS Table Below
Protocols 6
MS/TP m
MS/TP s
Off
N2 On
Lon SLTA
Off
BAUD 45
9600 Off Off
19.2 K Off On
38.4 K On Off
76.8 K On On
On
Modbus
8
Off
Off
On
On
Off
4
BACnet
3
7
Off
On
Off
Off
Off
PTP Off Off
On
Access Port 2a
Lon OptionOff On
On
2
1
UO-1
UO-2
UO-3
UO-4
UO-8
UO-7
UO-6
UO-5
On
Off
21
BAS Port
BAS Port Settings
Set Pot Full CW
24Vac
DO NOT APPLY 24Vac TO
UNIVERSAL OUTPUTS
External 24Vdc relay coil only
3
UO-2
UO-1
2
1
UO-4
UO-3
6
5
4
7
8
6
UO-7
UO-6
UO-5
3
1
2
4
5
UO-8
7
8
+
Gnd
+
Gnd
+
Gnd
+
Gnd
+
Gnd
+
Gnd
+
Gnd
+
Gnd
Aux Power Out Port 2b
Port 2a
IOPro812u
07/10/12
Rev 6
Open Energy
Management Equipment
26Vdc
I/O Pro 812u
CONTROLLER
®
Archive Valid
Port 2a Rx
Port 2a Tx
Port 1 Rx
Port 1 Tx
Battery low
External
Battery
Gnd
+3V
Brownout
88F0
E143900
TYPE: 002003
Power
Off On
Power
Gnd
24Vac
485
ARC-
Shield
Net -
Net +
156
Port 2a
Rnet
Gnd
Rnet +
Rnet -
+12V
Xnet +
Xnet -
Gnd Xnet Expansion
Local
Rnet+
Gnd
Sense
+12V
Rnet-
Access
EIA-485
EIA-232
Thermistor/
dry-contact/
Mode Select
Universal Input
mA
RTD
Volt s
10V Max, 20mA Max
Inputs: All
UI-4
UI-3
UI-2
UI-1
Gnd
+
Gnd
Gnd
+
+
Gnd
+
8
7
6
5
4
3
2
1
UI-8
Gnd
UI-6
UI-7
UI-5
Gnd
+
+
Gnd
+
Gnd
+
UI-12
UI-11
UI-10
UI-9
+
Gnd
+
Gnd
Gnd
+
Gnd
+
24 Vdc
24 Vdc
200mA maximum
Auto Off On
0-20mA
0-10Vdc
Relay
Controller
Address
1's
10's
Ext. Batt.
Int. Batt.
Status
Module
3V Lithium Battery
CR-123A
0 = Download required
3 = Comm setup error
1 = Control Program Error
4 = System error
8 = Formatting
2 = RAM full
Chase = OK
Status Codes
Class 2
ONLY Use Copper
24Vac, 50VA
Without Keypad:
26Vdc, 23W, 0.9A
Outputs
24Vdc Max, 50mA Max
Format
Pot
2-wire
4-wire
2 wire 4 wire
Rx -
Net-
Net+
n/c
Tx -
Tx +
Rx +n/c
EIA-232
DCD
Rx
Tx
DTR
Signal Ground
®
BACnet
Over ARCNET156 KBaud
Made in USA
Port 2a BT485
Port 1
Port 1 BT485
Conductors
2A, 50-60 Hz
Blinking Dot = 'Run'
On Off
Enhanced
8
7
6
5
4
3
2
1
8
7
6
5
4
3
2
1
IP Addr
Assigned Default
10/100 BaseT
Ethernet Port E1
100 LAN LINK
8
7
6
5
See BAS Table Below
Protocols 6
MS/TP m
MS/TP s
Off
N2 On
Lon SLTA
Off
BAUD 45
9600 Off Off
19.2 K Off On
38.4 K On Off
76.8 K On On
On
Modbus
8
Off
Off
On
On
Off
4
BACnet
3
7
Off
On
Off
Off
Off
PTP Off Off
On
Access Port 2a
Lon OptionOff On
On
2
1
UO-1
UO-2
UO-3
UO-4
UO-8
UO-7
UO-6
UO-5
On
Off
21
BAS Port
BAS Port Settings
Set Pot Full CW
24Vac
DO NOT APPLY 24Vac TO
UNIVERSAL OUTPUTS
External 24Vdc relay coil only
3
UO-2
UO-1
2
1
UO-4
UO-3
6
5
4
7
8
6
UO-7
UO-6
UO-5
3
1
2
4
5
UO-8
7
8
+
Gnd
+
Gnd
+
Gnd
+
Gnd
+
Gnd
+
Gnd
+
Gnd
+
Gnd
Aux Power Out Port 2b
Port 2a
IOPro812u
07/10/12
Rev 6
Open Energy
Management Equipment
26Vdc
I/O Pro 812u
CONTROLLER
Description Part Number
Repeater URVRP

SECTION 5: COMMUNICATIONS
15
FIGURE 8: Repeater Communication WiringBetween Multiple Controllers
5.5 Sequence of Operations
All control equipment shall operate in stand-alone mode according to its sequence of operation in the
absence of the Virtual Wall Controller.
Occupancy
WebCTRL® shall centrally coordinate the monitoring and control of all equipment. WebCTRL® allows the
user to create plant wide schedules, trend graphs, and reports as well as adjust heating setpoints, pressure
control, cooling and more.
In the unoccupied mode, the Exhaust Fans (EF) and Outside Air Handling Unit (OAHU) shall be off. The
Infrared Heating equipment (IRH) will maintain unoccupied heating setpoints.
A predictive, learning, optimal start routine shall start the Infrared Heating equipment to achieve the target
occupancy setpoint by the start of occupancy.
In the occupied mode, the OAHU shall be cycled on and operate according to its sequence of operation. The
EF's shall be enabled and will operate according to the exhaust fan control routines outlined below.
Description Part Number
Repeater URVRP

VIRTUAL WALL™ CONTROLLER INSTALLATION MANUAL
16
IRH and OAHU Setpoint Coordination
The IRH shall maintain the space temperature heating setpoint (occupied and unoccupied) according to its
sequence of operations as performed by the IRH controller.
Should the IRH be operating at 100% capacity and not be able to achieve or maintain the space temperature
heating setpoint after the prescribed adjustable runtime (15 min), the discharge air temperature setpoint of
the OAHU shall be raised to supplement the heating capacity of the IRH system. Once the heating setpoints
are achieved, the OAHU shall return to normal operation.
BuildingPressure
In the occupied mode, the OAHU shall maintain the space at the higher of:
1. A positive pressure of 0.01" wc (adjustable) relative to the outside static pressure.
2. The required outside air CFM as measured by the equipment and defined by code or process
requirements.
Unoccupied Free Cooling
In the cooling season, if the night time outside air conditions are suitable and the OA temperature is at least
3°F lower than the space temperature, the OAHU shall be switched on to pre-cool the space.
Preoccupancy Purge
If desired, the system can perform a pre-occupancy purge by staging on the EF's and OAHU prior to the start
of occupancy by a user adjustable time period to ensure sufficient air change. Outside air temperature limits
shall be provided to prevent the purge operation during times when the OA conditions are unsuitable.
Exhaust Fan Control
In the occupied mode, Exhaust Fans shall be enabled and cycle on according to one or more of the following
conditions:
1. Continuous during the occupied mode
2. Upon a rise in space temperature above the cooling setpoint
Table of contents
Popular Controllers manuals by other brands
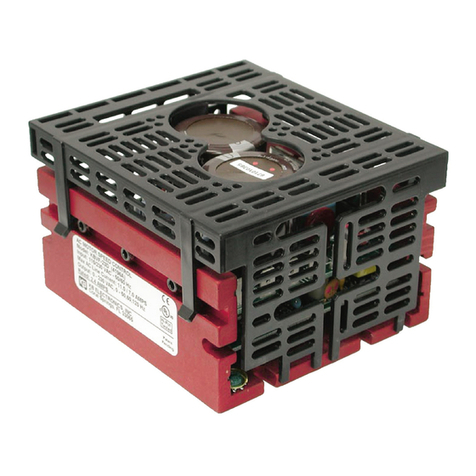
KB Electronics
KB Electronics KBVF-21D Installation and operation manual
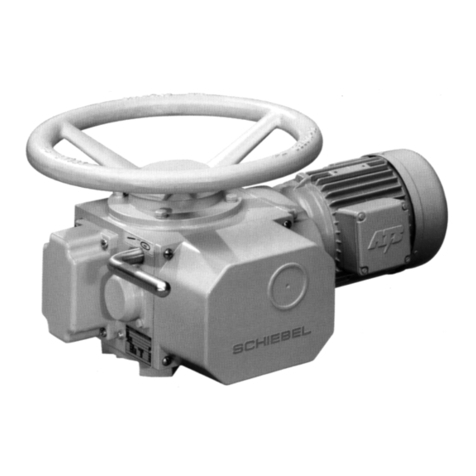
SCHIEBEL
SCHIEBEL AB3 operating instructions
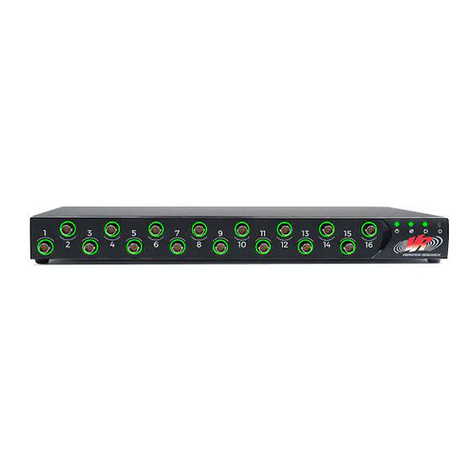
Vibration Research
Vibration Research VR10500 Hardware manual
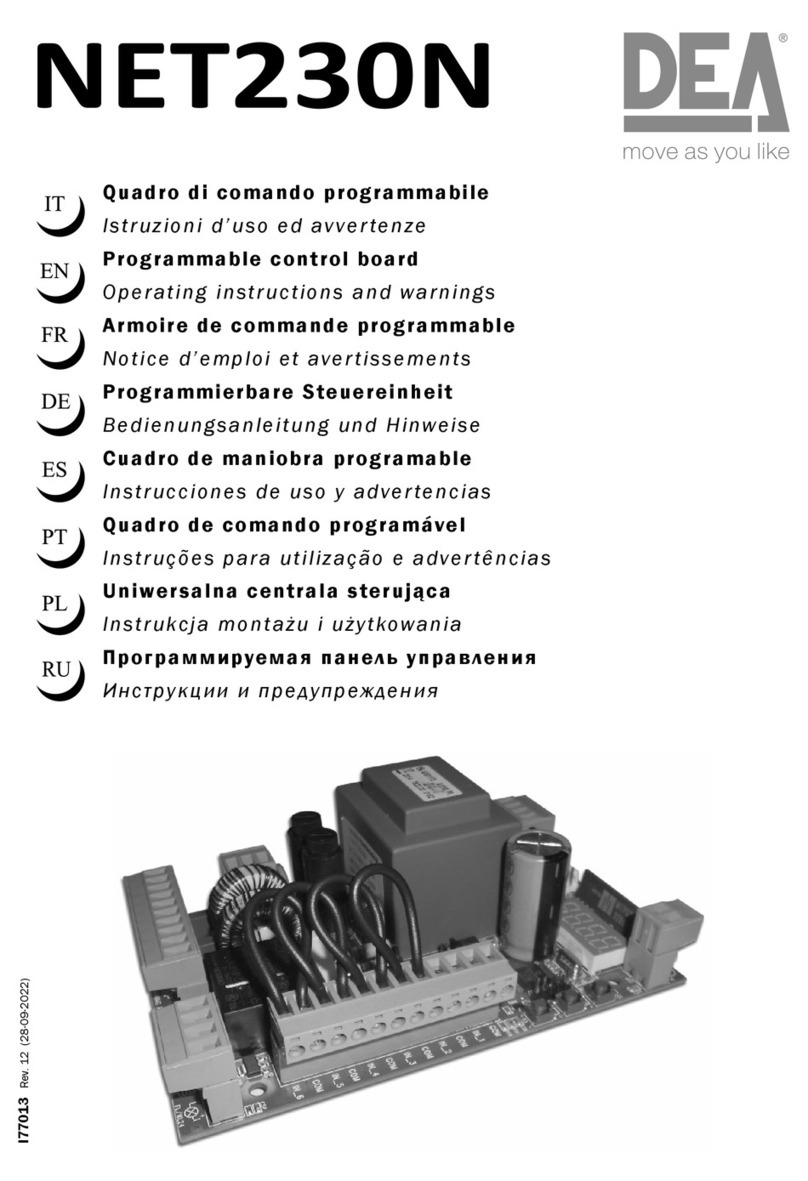
Dea
Dea NET230N Operating instructions and warnings
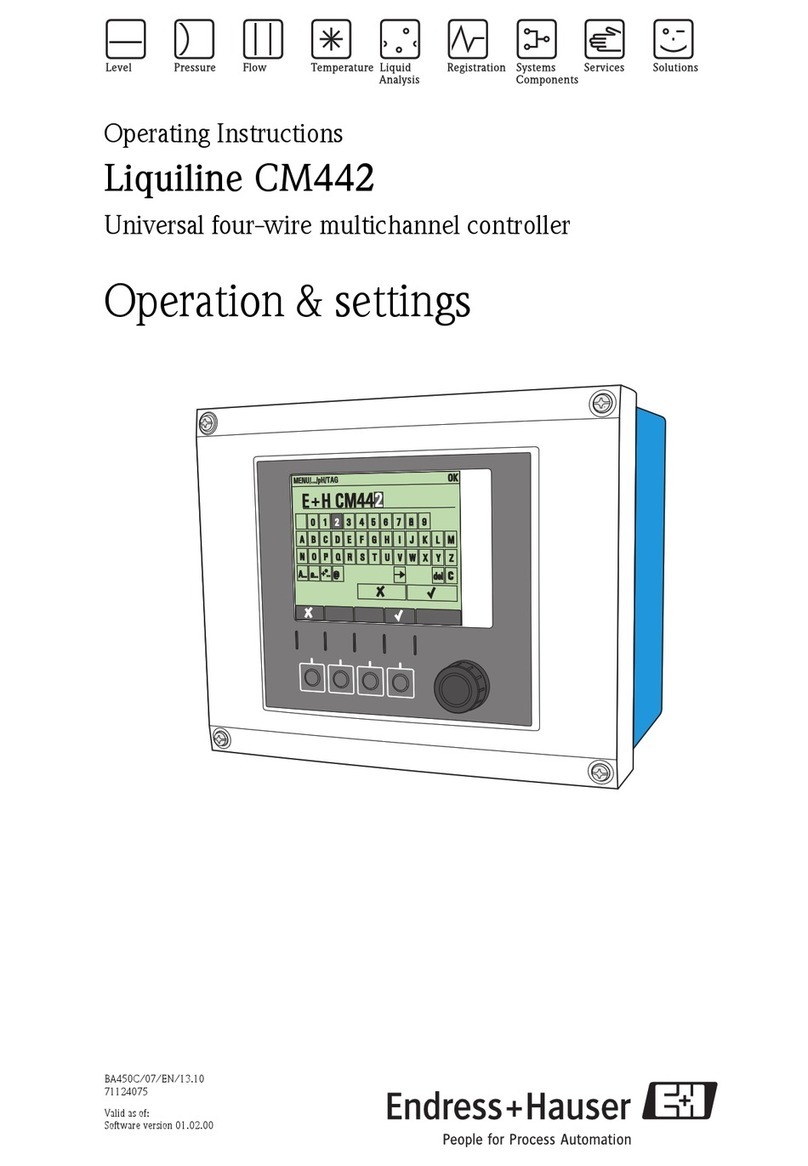
Endress+Hauser
Endress+Hauser Liquiline CM442 operating instructions
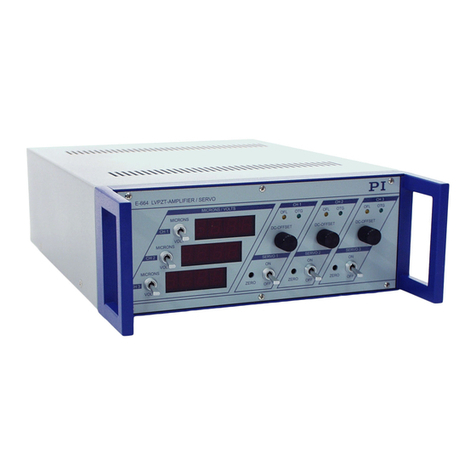
PI
PI E-664 user manual