Vibration Research VR10500 User manual


Notes, Notices, and Cautions
The NOTE icon indicates important information for better use of the
controller.
The CAUTION icon indicates a potential for propertydamage, personal
injury, or death.
© 2021 Vibration Research Corporation is a registered trademark in the
United States and other countries.
Information in this document is subject to change without notice.
Document last revised Wednesday, March 24, 2021 - Jenison, Michigan.
Vibration Research Corporation may have patents including but not limited
to U.S. Patent No. 7,426,426, Japan Patent No. 4429358, Canada Patent
No. 2,568,178, China Patent No. 058001235.2, E.U. Patent No. 1766358,
and other patent applications, trademarks, copyrights, or other intellectual
property rights covering subject matter in this document. Except as
expressly provided in any written license agreement from Vibration
Research Corporation, the furnishing of this document does not give you
any license to these patents, trademarks, copyrights, or other intellectual
property.
Products that are referred to in this document may be either trademarks
and/or registered trademarks of the respective owners. The publisher and
the author make no claim to these trademarks.
While every precaution has been taken in the preparation of this document,
the publisher and the author assume no responsibility for errors or
omissions, or for damages resulting from the use of information contained
in this document or from the use of programs and source code that may
accompany it. In no event shall the publisher and the author be liable for
any loss of profit or any other commercial damage caused or alleged to
have been caused directly or indirectly by this document.

Table of Contents
VR10500 Hardware Manual
................................................................................. 1
Hardware Overview
................................................................................. 4
Capabilities & Specifications
................................................................................. 6
Installation
................................................................................. 9
Connection
................................................................................. 13
Remote I/O
................................................................................. 21
Maintenance
................................................................................. 22
Troubleshooting & Diagnostics
................................................................................. 27
Warranty


1support@vibrationresearch.com
Hardware Overview
Front and Back Panel Inputs/Outputs

VR10500 Hardware Manual2
Hardware Overview CONTINUED
·
The three Gigabit Ethernet ports each operate up to 1,000Mbps. The UPLINK
port connects to the workstation computer, and the two expansion ports
connect to additional controllers for higher channel count systems. The ports
support auto-negotiation, full duplex, and flow control. They also support auto
MDXoperation to eliminate any requirements for crossover network cables.
·
The front panel has16 BNC input connectors that support various analog input
devices including accelerometers, microphones, and external conditioners.
Each input channel supports single ended and capacitor coupled operation for
IEPE transducers and smart transducers (TEDS). Each channel includes
support for multiple input voltage ranges:
Input Voltage Range
Input Impedance
0-20V peak
100 kΩ
±10V peak
100 kΩ
±1V peak
100 kΩ
±5V peak
10 MΩ
±0.5V peak
10 MΩ
·
The rear panel has four BNC output connectors that support various analog
drive devices up to ±10V. For single-axis control, the DRIVE 1 port is typically
used to drive an amplifier or servo-hydraulic controller. The AUXport is
typically used to support synchronization with constant level adapter (COLA)
devices such as stroboscopes or data acquisition devices. The DRIVE 2 and
DRIVE 3 ports can be used for multi-shaker control or as additional
AUX/COLA channels. Pairs of outputs can be used to support differential
mode output.
·
The digital drive output interface has two additional drive signals. They can be
used in conjunction with the four analog drive signals for six channels of
DRIVE/AUX/COLA or separately for two remote drive outputs. The digital drive
interface has several advantages over the traditional analog drive interface,
including longer cable lengths without signal degradation and higher immunity
to low and high frequency electrical noise. A separate unit is typically required
to convert the digital drive signal into an analog signal that can drive a
standard amplifier input. This unit would be located near the input to the
amplifier or servo-hydraulic controller.
·
The rear panel has an interbox port for loop synchronization of multiple
VR10500 units. Loop sync can be completed with hardware or software
clocks. Hardware clocks via interbox connection are only recommended for
systems with more than 48 input channels.

3support@vibrationresearch.com
·
The rear panel has an AUXinputs/outputs DB37 connector that supports eight
digital outputs and eight analog/digital inputs. They can be used to integrate
with other systems or to monitor analog signals. The DB37 connector can
also support a tachometer.
System Ventilation Fan
The VR10500 has one fan for system ventilation. Make sure the fan and vent
openings remain unobstructed to allow for proper airflow.

VR10500 Hardware Manual4
Capabilities & Specifications
Item Check List
The following items are included with the VR10500:
·
VR10500 I/O
·
AC power cable
·
Drive cable
·
Network (Ethernet) cable
·
Rack-mount kit for installation
·
Software CD
·
VibrationVIEW software manual
VR10500 General Specifications
·
16 to 512 channels, 16 channel units (mix & match)
·
Total harmonic distortion < -100dB THD+N
·
24-bit resolution inputs; 32-bit resolution outputs
·
·
Compatible with VibrationVIEW control software and ObserVIEW analysis
software
Analog Inputs
·
256kHz simultaneous sample rate
·
IEPE (4mA) and TEDS
·
200V peak transient protection
·
0-20V peak, ±10V peak, and ±1V peak 100 kΩ input range; ±0.5V and ±5V
10MΩ input range
·
>110dB dynamic range; >130dB with tracking filters
·
Analog multiple pole anti-aliasing filter and digital anti-aliasing filter with
>105dB attenuation
Analog Outputs
·
216,000 samples per second
·
Analog multiple pole filter plus a digital filter and analog reconstruction filters
·
50,000Hz frequency range
·
COLA/AUX output
·
Up to 4 independent outputs for multi-shaker control

5support@vibrationresearch.com
Environmental Specifications
TEMPERATURE
Operating: 35° to 122°F (2° to 50°C)
Storage: -40° to 185°F (-40° to 85°C)
Humidity: Up to 95% Relative Humidity, Non-Condensing
Altitude: Up to 3,000m MSL (9,842ft)
VIBRATION
Random: MIL-PRF-28800F, Class 3
Shock: MIL-PRF-28800F, Class 3

VR10500 Hardware Manual6
Installation
Installation Precautions
CAUTION: Before performing any of the following procedures, read and follow
the safety instructions.
CAUTION: If the equipment is used in a manner not specified by the
manufacturer, the protection provided by the equipment may be impaired.
CAUTION: Observe the following points before performing the procedures in
this section:
·
Make sure the rack or cabinet housing the VR10500 is adequately secured to
prevent instability or a fall.
·
Make sure the power source circuits are properly grounded.
·
Observe and follow the service markings. Do not service any device that is not
defined in the system documentation. Opening or removing covers marked
with a triangular symbol with a lightning bolt may cause electrical shock.
These components are to be serviced by trained service technicians only.
·
Make sure the power cable, extension cable, and plug are not damaged.
·
Make sure the VR10500 is not exposed to water.
·
Make sure the VR10500 is not exposed to radiators or heat sources.
·
Make sure the cooling vents are not blocked.
·
Do not push foreign objects into the VR10500 as it may cause a fire or electric
shock.
·
Use the VR10500 with approved equipment only.
·
Allow the VR10500 to cool before removing covers or touching internal
equipment.
·
Make sure the VR10500 does not overload the power circuits, wiring, or over-
current protection. To determine the possibility of overloading the supply
circuits, add the ampere ratings of all the loads installed on the same circuit
as the VR10500. Compare the sum with the rating limit for the circuit.
·
Do not install the VR10500 in an environment where the operating ambient
temperature might exceed 122ºF (50ºC).
·
Make sure the airflow around the front, sides, and back of the VR10500 is not
restricted.
·
All external connections must be double insulated circuits or reinforced
insulated circuits from mains.
·
For indoor use, over voltage category II, PD2.

7support@vibrationresearch.com
Site Requirements
The VR10500 can be mounted on a standard equipment rack or placed on a
tabletop.
Before installing the VR10500, verify that the site selected for the device meets
the following site requirements:
·
Power — The VR10500 is installed within 5ft (1.5m) of a grounded and easily
accessible outlet 220/110VAC, 50/60Hz.
·
General — The power source is correctly installed.
·
Clearance — There is adequate frontal clearance for operator access. Allow
clearance for cabling, power connections, and ventilation.
·
Cabling — Cabling is routed to avoid sources of electrical noise such as radio
transmitters, broadcast amplifiers, power lines, and fluorescent lighting
fixtures.
·
Ambient Requirements — The ambient VR10500 operating temperature range
is 36° to 122°F (2° to 50°C) at a relative humidity of up to 95%RH, non-
condensing. Verify that water or moisture cannot enter the VR10500 case.
·
Do not operate this product near volatile or flammable materials.
Physical Dimensions
Height — 1.75in (44.5mm) (1U)
Width — 17in (432mm) (19in rack mount with included brackets)
Depth — 11in (280mm)
Weight — 9.25lbs (4.2kg)

VR10500 Hardware Manual8
Installation CONTINUED
Installing on a Flat Surface
The surface must be able to support the weight of the VR10500 and its cables.
·
Set the VR10500 on a flat surface; leave 2in (5.08cm) on each side and 5in
(12.7cm) at the back.
·
Make sure the device has proper ventilation.
Installing on a Device Rack
CAUTION: Read the safety information in this guide as well as the safety
information for other devices that connect to or support the VR10500.
CAUTION: Disconnect all cables from the VR10500 before mounting the
device in a rack or cabinet.
CAUTION: When mounting multiple devices into a rack, mount the devices
from the bottom up.
·
Place the supplied rack-mounting bracket on one side of the VR10500. The
mounting holes on the VR10500 should line up with the mounting holes on the
rack mounting bracket. The following figure illustrates where to mount the
brackets.
·
Remove the feet from the bottom of the VR10500.
Other Installation Methods
CAUTION: Always mount the VR10500 horizontally.
The VR10500 requires the ventilation provided by a normal horizontal orientation;
mounting in other orientations is not recommended.

9support@vibrationresearch.com
Connection
Connecting the Device to a Power Supply
CAUTION: This product must be reliably earthed and installed in accordance
with the prevailing electrical wiring regulations and safety standards.
·
Connect the standard AC power cable to the AC connector on the back panel.
·
Connect the power cable to a grounded AC outlet. When used in a control
system, all grounds must be common. This is most easily accomplished by
connecting the power cable to the amplifier's controller outlet. No operator
settings are required for voltage configuration.
·
After connecting the VR10500 to a power source, confirm that the device is
connected and operating correctly by examining the LEDs on the front panel.
·
The standard AC power cable is the primary disconnecting device. Position
the equipment so that it is easy to disconnect the AC power cord.
100/1000BASE-T CABLE REQUIREMENTS
All category 5 UTP cables used for 100BASE-TX connections also operate with
1000BASE-T provided that all four wire pairs are connected. However, it is
recommended that an enhanced category 5e or newer cable is used for all
critical connections or any new cable installations. The category 5e or newer
specification includes test parameters that are only recommended for category 5
and comply with the IEEE 802.3ab standards.
The VR10500 supports auto-detection of straight through and crossed cables on
all switching 10/100/1000BASE-T ports. The automatic correction of errors in
cable selection makes the distinction between a straight through cable and a
crossover cable irrelevant.

VR10500 Hardware Manual10
Connection CONTINUED
Connecting the Device to a Network
NOTE: Do not plug a phone jack connector into an RJ-45 port. This will
damage the Ethernet device. Use only twisted-pair cables with RJ-45 connectors
that conform to FCC standards.
·
Attach one end of a twisted-pair cable to the device's uplink RJ-45 connector
and the other end to a switch or workstation computer.
·
Make sure the twisted pair cable does not exceed 328ft (100m) in length.
After connection, the network LED will illuminate green to indicate that the
connection is valid.
RJ-46 CONNECTOR
CAUTION: The terminals on the unit should only be connected to passive
load transducers or source transducers that apply no more than 10V to the
circuit that originates from the VR10500 (or a value that equates to no more than
33Vac RMS/46.7V peak or 70Vdc total on the circuit).
CAUTION: Other than the IEC inlet for input power to the unit, the terminals
on the rear of the unit should only be connected to SELV/double insulated
circuits of other equipment.
The 10/100/1000 BASE-T ports are
copper twisted-pair ports.
RJ-45 Pin Number Allocation for Ethernet Port
Pin No
Function
1
Pair 1+
2
Pair 1-
3
Pair 2+
4
Pair 3+
5
Pair 3-
6
Pair 2-
7
Pair 4+
8
Pair 4-

11support@vibrationresearch.com
Connecting the Device to an Amplifier
CAUTION: Always connect the power cable to an AC outlet prior to
connecting or disconnecting the drive cable.
Connect the 50Ω BNC cable (or equivalent) between the DRIVE output of the
VR10500 and the DRIVE input on the power amplifier.
Connecting the Device to an Accelerometer
CAUTION: Always connect the power cable to an AC outlet prior to
connecting or disconnecting the drive cable.
CAUTION: Always verify that the mounting surface of the accelerometer is
floating or grounded.
CAUTION: Terminals provided on the unit should only be connected to
passive load transducers or source transducers that apply no more than 10V to
the circuit that originates from the VR10500 (or a value that equates to not more
than 33Vac RMS /46.7V peak or 70Vdc total on the circuit).
CAUTION: Other than the IEC inlet for input power to the VR10500,
terminals provided on the rear of the unit should only be connected to
SELV/double insulated circuits of other equipment.
CAUTION: If any sourcing transducers (accelerometers) add voltage to the
existing voltage originating from the VR10500, the total shall not exceed the
70Vdc or 33Vac (RMS).
Connect the accelerometer to the front panel input.

VR10500 Hardware Manual12
Connection CONTINUED
Connecting the Device to Software
The user can control the VR10500 with one of the three Vibration Research
software applications.
VibrationVIEW: To connect the VR10500 to the VibrationVIEW software for
vibration control, please refer to the VibrationVIEW Quick Start Guide.
VibrationVIEW must be configured to use the appropriate network connection
after the hardware is set up and PC communication is established.
ObserVIEW: To connect the VR10500 to the ObserVIEW software for signal
analysis, please refer to the ObserVIEW Quick Start Guide. Live Analyzer is the
default connection in ObserVIEW. In Live Analyzer, the user can access the full
spectrum of analysis controls in ObserVIEW as live data streams in from the
device.
VR Mobile: To connect the VR10500 to VR Mobile for remote monitoring, the
VR10500 must be connected to the same network as the smart phone or tablet
running the application. The smart phone/tablet serves as the user interface
display following connection and can be used to check system configuration and
configure live analyzer.
FCC Notice
This device complies with part 15 of the FCC Rules. Operation is subject to the
following two conditions: (1) this device may not cause harmful interference, and
(2) this device must accept any interference received, including interference that
may cause undesired operation.
Changes or modifications not expressly approved by the party responsible for
compliance could void the user’s authority to operate the equipment.
NOTE: This equipment has been tested and found to comply with the limits
for a Class A digital device, pursuant to part 15 of the FCC Rules. These limits
are designed to provide reasonable protection against harmful interference when
the equipment is operated in a commercial environment. This equipment
generates, uses, and can radiate radio frequency energy and, if not installed and
used in accordance with the instruction manual, may cause harmful interference
to radio communications. Operation of this equipment in a residential area is
likely to cause harmful interference in which case the user will be required to
correct the interference at his own expense.

13support@vibrationresearch.com
Remote I/O
CAUTION: Terminals provided on the unit shall be connected only to passive
load transducers or source transducers that apply no more than 10V to the
circuit that originates from the VR10500 (or a value that equates to not more
than 33Vac RMS/46.7V peak or 70Vdc total on the circuit).
CAUTION: Other than the IEC inlet for input power to the unit, terminals
provided on the rear of the unit shall be connected only to SELV/double
insulated circuits of other equipment.
BNC Inputs and Outputs
BNC connectors are manufactured with 50Ω and 75Ω impedance capability. 50Ω
cables are typically used in this application. BNC inputs are typically used with
accelerometers. Nominal ranging allows for maximum 10V peak input devices.
BNC output ranging allows driving maximum 10V peak devices, including
COLA/AUX.
The BNC inputs support IEPE sensors by providing a current limited power
source that can be enabled and disabled through the software. When enabled, it
provides 4.4mA at up to 26VDC to power the sensor.
Power Connectors
The VR10500 is powered by the AC internal power supply.
Internal Power Supply Connector
The VR10500 supports a single internal power supply to provide power for
switching operations. The AC power connector is located on the back panel of
the hardware.
Interbox
The interbox interface on the back panel of the VR10500 supports
synchronization of multiple VR10500 units with greater accuracy than
synchronization with Ethernet connection alone. The interbox interface uses
standard Ethernet RJ-45 connectors and Ethernet pinout. The electrical signals
on this interface are different than Ethernet at 2.4V and up to 24mA.
The interbox interface operates using standard Ethernet cabling; however, this
interface must use shielded cabling.

VR10500 Hardware Manual14
Remote I/O CONTINUED
AUX Outputs/Inputs
The AUX outputs/inputs interface allows for data acquisition and control of
additional devices. This interface uses a standard DB37 connector and an AMP
5747375-2 (or equivalent) mating connector.
The pinout on the back of the VR10500 is displayed below.
AUX INPUTS
The eight AUXinputs can be used to read an analog signal up to ±12V at 16-bit
resolution or a digital TTL signal. AUX inputs should be referenced to
AGND/Analog Ground and are protected from transients up to ±30V. Digital input
signals must be greater than 2.2V to ensure they are registered high and less
than 0.6V to ensure they are registered low. Note, AUX inputs 1 and 2 also
support tachometer functionality as described in the proceeding text.

15support@vibrationresearch.com
TACHOMETER INPUTS
Logic Level Configuration ("Unfiltered")
The tachometer logic level configuration is generally used with sensors that
output a 5V or 3.3V digital signal. This interface uses the AUXinput 1 and 2
connections. Input signals in this configuration must be greater than 2.2V to
ensure they are registered high and less than 0.6V to ensure they are registered
low. Input signals may be up to 1MHz. The VR10500 supports quadrature
decoding by using both tachometer inputs simultaneously.
Zero Crossing Configuration ("Filtered")
The zero crossing configuration is generally used with variable reluctance
magnetic sensors. This interface uses the dedicated tachometer inputs. Input
signals in this configuration must be bipolar where the voltage swings above and
below ground and may be up to 1MHz. These inputs should be referenced to
DGND/Digital Ground and are protected from transients up to ±100V.
In this configuration, the VR10500 detects zero crossings in the negative-going
direction. Zero crossings will only be detected after the input signal exceeds a
positive-going "arming" voltage, which is selectable between three different
values:
·
Arm when ~0V is exceeded
·
Arm when ~200mV is exceeded
·
Arm when adaptive* threshold is exceeded
*The adaptive threshold monitors the input signal level and adjusts to be
approximately 80% of the peak input voltage. At input signal levels less than
230mV peak, the adaptive threshold is fixed at approximately 45mV. At input
signal levels less than 30mV peak, the adaptive mode will not arm.

VR10500 Hardware Manual16
Remote I/O CONTINUED
AUX INPUT BIAS
This output supplies 5VDC at up to 0.15A and can be used to power external
circuitry such as signal conditioners and relay coils.
AUX OUTPUTS
AUX outputs are nominally 5V TTL voltage levels but can drive up to +24VDC at
0.5A when supplied with appropriate external power via the AUXpower
interfaces. AUXoutputs should be referenced to DGND/Digital Ground and are
protected from transients up to +26.5V. The internal 5VDC power source can
supply up to 0.2A and is shared between the eight AUX outputs.
AUX output HIGH voltage (active):
·
4.5V minimum at 10mA source current
·
4.0V minimum at 200mA source current
AUX output LOW voltage (inactive):
·
0.3V maximum at 200mA sink current
·
0.8V maximum at 500mA sink current
AUX output OPEN
·
200kΩ to DGND/Digital Ground
NOTE: The AUX output drivers have a small pull-up leakage current (20uA
max) that may cause the voltage to drift above 0V when no load is connected.
AUX POWER
The AUX power interfaces accept an external DC power supply and allow the
AUX outputs to drive higher voltages and currents up to +24VDC at 0.5A per
output. The eight AUXoutputs are divided into two groups where AUXPWR_A is
associated with AUX outputs 1 to 4 and AUXPWR_B is associated with AUX
outputs 5 to 8. The two AUXPWR groups may be powered independently of each
other. Exceeding +26VDC on the AUXpower interfaces may permanently
damage the VR10500.
For example, AUXoutputs 1 to 4 could be configured for +12VDC operation by
connecting an external 12VDC power source between the AUXPWR_A pin and
DGND/Digital Ground, and AUXoutputs 5 to 8 could be left at 5VDC operation
by leaving the AUXPWR_B pin disconnected. The +12VDC external power
source would need to be capable of supplying enough current to drive all loads
connected to AUXoutputs 1 to 4.
Table of contents
Other Vibration Research Controllers manuals
Popular Controllers manuals by other brands
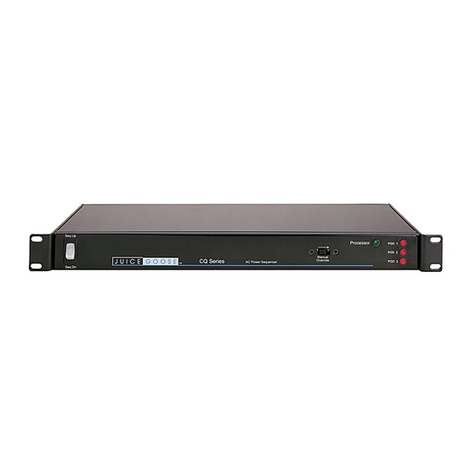
JuiceGoose
JuiceGoose CQ Series owner's manual
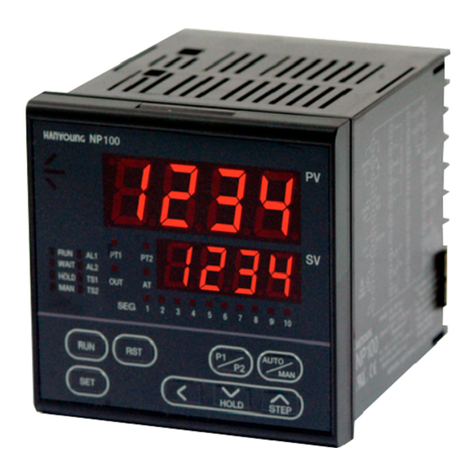
HANYOUNG NUX
HANYOUNG NUX NP100 manual
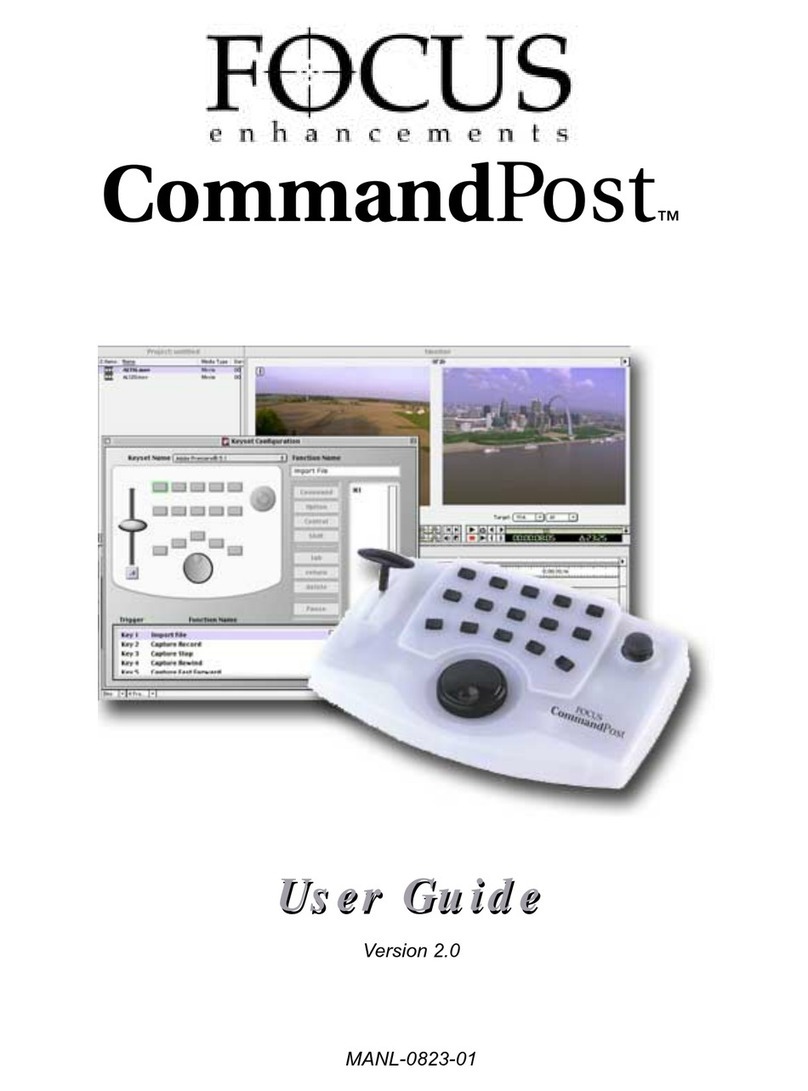
foc.us
foc.us CommandPost user guide
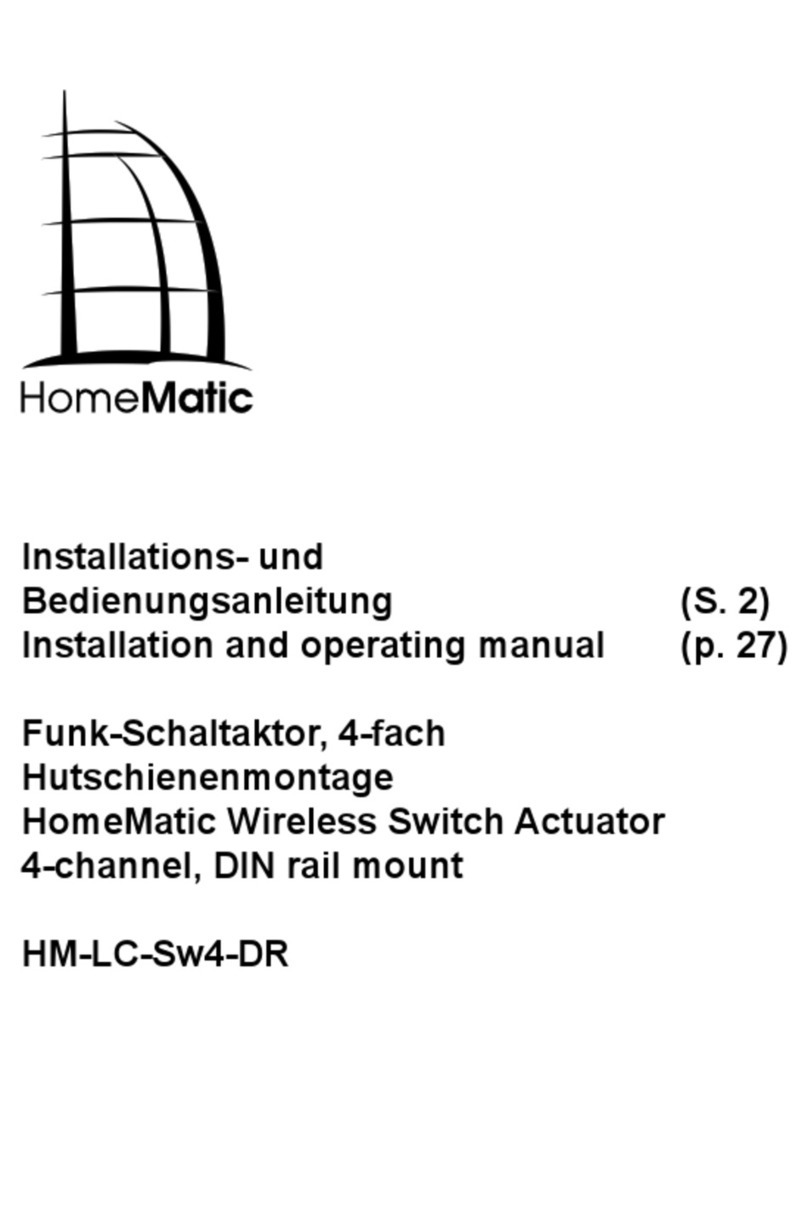
EQ3
EQ3 Homematic HM-LC-Sw4-DR Installation and operating manual
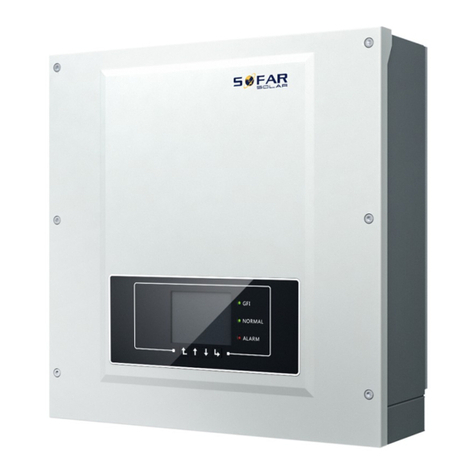
Sofar solar
Sofar solar 4-12KTL-X Quick installation guide
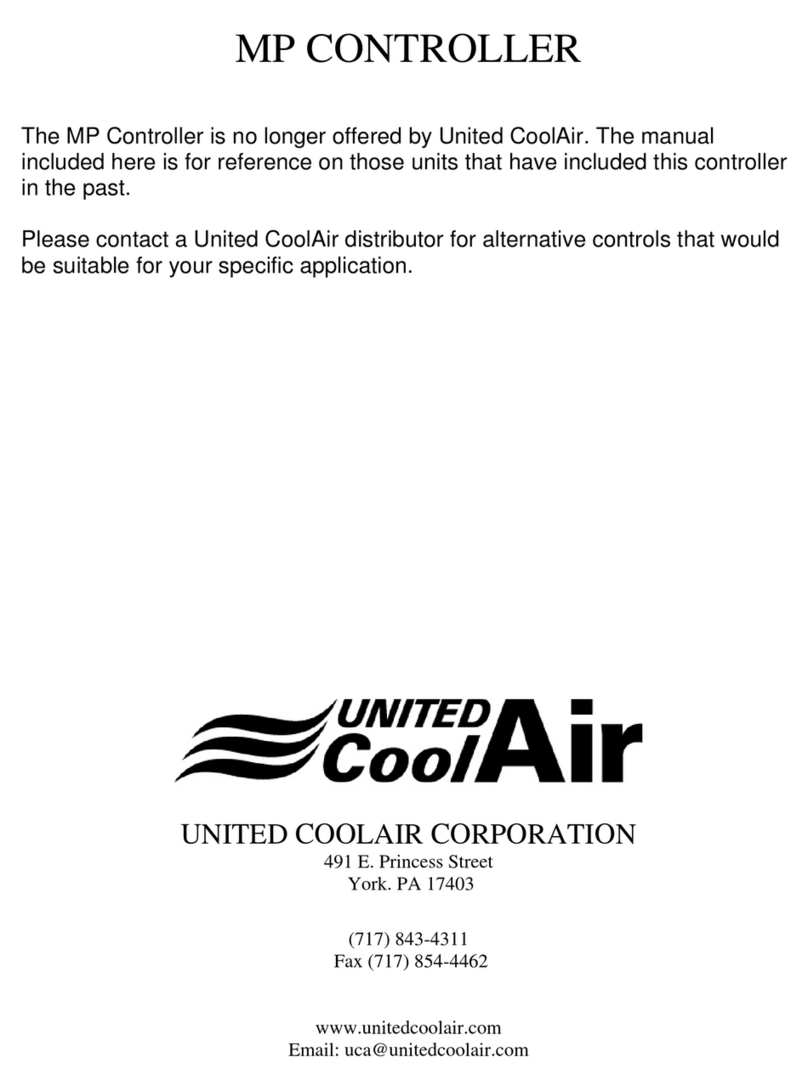
United CoolAir
United CoolAir MP Controller Installation & operating manual