Speeder Motion MicroStar B Series User manual

1
MicroStar B
Service manual MicroStar B rev06 0909
0909
09
MicroStar B
HIGH PERFORMANCE SOLUTION FOR INDUSTRIAL AUTOMATION
MicroStar B
B
rushless
&
dc
M
otor
D
rive
www.speedermotion.com
Service Manual
0909
0909
09
100%
Progettato
costruito collaudato
in Italia
&

2Service manual MicroStar B rev06
MicroStar B
0909
0909
09
Print in Italy 06/2009 rev 06/09
All the informations and concepts included in this user guide are copyright, and are
supplied to the user with the understanding that it may not be copied, disclosed or
duplicated in whole or in part for any purpose not authorised by the factory. All
specifications are subject to change without prior notification.
WARNING - Risk of damage and/or personal injury
Thisdrivesdoesn’tcontainanyuserserviceablepart. Attempting to replace any internal
component,may result indamage to theunit and/or personalinjury. This mayalso void
thewarranty.

3
MicroStar B
Service manual MicroStar B rev06 0909
0909
09
Chapter 1
1.1 Safety and note ........................................................................................................5
1.2 Operation mode and feedback.................................................................................6
1.3 Model and size .........................................................................................................7
1.4 View product.............................................................................................................8
1.5Ambient conditions ................................................................................................... 9
1.6 Dimensions ............................................................................................................10
1.7 Label description .................................................................................................... 11
1.8 Components description.........................................................................................12
1.9 Signal inputs and output.........................................................................................13
1.10 Potentiometer adjustements.................................................................................14
1.11 Indicator Leds and protections ............................................................................. 15
1.12 Internal adjustements......................................................................................16-17
1.13 Power supply notes .........................................................................................18-19
Chapter 2
2.1About Connections .................................................................................................22
2.2 Ground Connections ..............................................................................................23
2.3 Brushless motor Connections with encoder feedback ......................................24-25
2.4 Brushless motor Connections with fa-coder feedback ......................................26-27
2.5 Brushless motor Connections with only hall feedback ......................................28-29
2.6 Brush D.C motor Connections with Encoder feedback .....................................30-31
2.7 Brush D.C motor Connections withArmature feedback ....................................32-33
2.8 Velocity Speed input ...............................................................................................34
2.9 TPRC torque input.................................................................................................. 35
2.10 Enable input .........................................................................................................36
Chapter 3
3.1Adjustements with encoder feedback.....................................................................38
3.2Adjustements with armature feedback ..............................................................39-40
3.3 Speed offset adjustments....................................................................................... 40
3.4 Current adjustments...............................................................................................41
3.5 Ramp time adjustments.........................................................................................42
3.6 Dynamic adjustment...............................................................................................43
3.7Troubleshooting...................................................................................................... 44
Conformity.................................................................................................................... 45
Index

4Service manual MicroStar B rev06
MicroStar B
0909
0909
09
Chapter 1
Description
1.1 Safety and Note........................................................................................................ 5
1.2 Operation mode and feedback.................................................................................6
1.3 Model and size .........................................................................................................7
1.4 View product.............................................................................................................8
1.5Ambient conditions ...................................................................................................9
1.6 Dimensions ............................................................................................................10
1.7 Label description .................................................................................................... 11
1.8 Terminals description .............................................................................................12
1.9 Signal inputs and output.........................................................................................13
1.10 Potentiometer adjustements.................................................................................14
1.11 Indicator Leds and protections ............................................................................. 15
1.12 Internal adjustements......................................................................................16-17
1.13 Power supply notes .........................................................................................18-19

5
MicroStar B
Service manual MicroStar B rev06 0909
0909
09
Safety and note
1.1
Please read these notes carefully before powering up the drive
Warning!
Simbols security standard
Caution
Danger Sign
All the circuits in the Drive are potential sources of severe electrical shock, so follow these
rules to avoiding possible personal injury.
- Power off the drive and wait until all the leds are turned off before touching, removing,
connecting or any other critical action.
- Never disconnect any connectors before powering down the drive
Warning of Current being present
In case of doubt or in any case you don’t know as to behave yourself, before access to the
drive, power off the device and wait until all the leds are turned off.
May you have attention when you touch the drive because it may be hot.
Warning
It's used where the intent is to highlight useful considerations, prescriptions, indications,
and the correct execution procedures of every type of intervention and prevention of
damaging both systems and drives.
General Security Directives
Along with what is prescribed in the manual, pay attention to the security directives for
prevention of accidents and risks.
Always remove the power supply (disable) from both the system and the drive prior to any
type of intervention on electric or mechanical parts.
Itisvery importantmeetallapplicablesafetyrequirementsduringinstallationandoperating
of any motion control equipment.Any installer has to assume the responsibility to ensure
that he recognizes and complies all the relevant safety standards. Any installation, not
meeting the safety requirements, may damage the equipment or injury the user.
This motion control equipment shoul be handled, installed, setted-up and maintenanced
onlybycompetent personnelexpertandtrainedinthe installationofmotioncontrolelectronic
equipment. Such technicians should be aware of potential electrical and mechanical
hazards.Shallneverbeliableorhaveanyresponsabilityiftheproductshavebeenimproperly
stored, installed, used or maintened, or if the costumer has permitted any unauthorized
modifications, adjustments, and/or repairs to the products.
Users must keep well clear in mind that this motion control equipment is capable of
producing high forces and rapid movement so they must be used with attention especially
during the application program’s development.
This motion control equipments are sold as end-users products to be installed only by
practical staff in accordance with all local safety laws and regulations. The device have to
be enclosed such that any part is not be accessible while the system is powered on.
We strongly reccomend to follow these recommendations in order to avoid wrong uses of
the equipment that may be impaired all the protections provided by the device.

6Service manual MicroStar B rev06
MicroStar B
0909
0909
09
Operation mode and feedback
1.2
Description
Operation mode
General characteristic
Closing the velocity feedback loop to motor may be done in several different ways to
accommodate most applications. Five types of velocity feedback are available with these
Brushless or DC motors.
Velocity feedback
• AC Brushless motor with Hall effect + encoder
• AC Brushless motor with Fa-coder
•AC Brushless motor with Hall effect (internal PWMArmature)
• DC motor with encoder
• DC motor with internal PWM (Armature)
This is a drive capable of piloting both rotaryAC brushless motors and DC brush
motors, up to 2Nm. It's a High Performance full four quadrant drive. The mosfet output
power stage is controlled by a 20 Khz PWM (Pulse Width Modulation) signal that allows it
to drive servo motors where high dynamic performance and precise speed is required.
DESCRIPTION
ENABLE INPUT Drive Enable with range from >8Vdc to
+30Vdc (min/max) STANDARD
DRIVE OK
OUTPUT
Drive OK, open collector output 50mA
max. (Normally closed, opens when
in protection mode) STANDARD
2 ANALOG
OUTPUT
1 motor velocity monitor “TP”, with
range +/-8 Vdc output
1 current monitor "CURR", with range
+/-8 Vdc output
STANDARD
LED INDICATOR Five LEDs are located just in front of
the potentiometers and show the
current state of the drive STANDARD
DESCRIPTION
SPEED
CONTROL INPUT
It is speed piloting using an analogue
reference (differential or common
mode) STANDARD
TORQUE
CONTROL INPUT
It is torque piloting using an analogue
reference. This function allows you to
control the current from the drive. STANDARD

7
MicroStar B
Service manual MicroStar B rev06 0909
0909
09
Specifications
Model available
Size available
Model and size
1.3
The power supply voltage has to be a transformer-isolated voltage
TECNICAL DATA CHARACTERISTICS
Supply voltage output 0,9 Vdc Input
PWM frequency 20Khz
Operating temperature 0/+45°C
Storage temperature -10/+70°C
Drift analog input 0,5uV/°C
Analog inputs (+/-VEL) +/-10Vdc max, impedance 20Kohm cad.
Current monitor output (CURR) +/- 8Vdc = Peak current
Velocity monitor output (T.P) +/- 8Vdc = max velocity
Power supply output (+5V) +5Vdc max 130 mA
Power supply output (+/-10V) +/-10Vdc max. 4mA
Encoder max. frequency 250Khz with level >+2,8/24Vdc min/max
Drive OK output NPN 50mA max.
Enable input >+8V/+30Vdc (min/max)
Band width (current) 2KHz
Band width (velocity) 150Hz
Minimum Inductance motor 200uH
Weight 0,35kg 10.6oz
Contaminants 2°or better (Norms EN60204 e EN50178)
Altitude Up to 1000m without restrictions, from
1000 to 2000m power derating
1,5%/100m
Flammability rating 94V-0 Cover material, the PCB and the
electronic component meet 94V-0
CURRENT
Size Rated current (A) Peak current (A)*
2/4 2 4
4/8 4 8
7/14 7 14
10/20 10 20
*Peak current during 2 sec
POWER SUPPLY
Model 60 20 - 84 Vdc* 60Vdc **
Model 110 30 - 130 Vdc* 100Vdc **
Model 140 40 - 184 Vdc* 140Vdc **
* Power supply min/max **Typical
Max size available for SMB110 7/14A
Max size available for SMB140 4/8A

8Service manual MicroStar B rev06
MicroStar B
0909
0909
09
(1) Solder bridges
(2) Adjustement zone
(3) CalibrationPotentiometers
(4) Leds
(5) TP Test point (Encoder or Armature velocity)
(6) M1 Signal terminal 16 pins MC1,5/16-ST-3,81 (pitch 3,81)
(7) M2 Power Terminal 5 pins GMST 2.5/5-G-5,08 (pitch 5,08)
(8) Fixing screw
(9) Product Cover
(10) Product Label
View product
View product
1.4
1
2
9
10
8
8
3456
7
M1
M2

9
MicroStar B
Service manual MicroStar B rev06 0909
0909
09
Ambient conditions
1.5
Ventilation
N = Standard radiator (operating ambient temperature from 0 to 45°C)
V = Standard radiator + supplementary ventilation (operating ambient temperature from
0 to 45°C)
- - = Not available
Positioning in the electrical box
Environmental condition
The electrical box must have suitably filtered air vents.
Leave the necessary space both above and below the converters.
Periodically check drive case and fans for excess dust or dirt, that could interfere with the
correct dissipation of the drive.
This power drives are intended only for use in close locations, guarded from operator
contact, in an ambient that compliance with these characteristics: operating temperature
ofmaximum45°C"seethetablebelow",Humidity limitsbetween5%to 95% noncondensing
(Pollution degree 2 or better).
The drive is natural convection air flow cooled. To ensure the drive cooling and make the
installation easier for the operator it must be installed vertically leaving a free space of at
least 20 mm (0,78 inch) on each side of the device. Avoid mounting heat producing
equipmentinthe nearest of thedriveor any other devicethatcan obstruct natural orforced
conventionairflow.Forenvironmenttemperature above 45°C,forcedaircoolingisrequired.
Conductive mounting panel (zinc coated)
Supplementary ventilation may be requested in accordance to size. See the table below.
Warning!
Dimensions are
expressed in
millimeters.
202050
50
135
5,3"
Cable duct
Cable duct
Air cooling
SIZE
MODEL 2/4 4/8 7/14 10/20
60 N N N N
110 N N V - -
140 N N - - - -

10 Service manual MicroStar B rev06
MicroStar B
0909
0909
09
Dimensions
Dimensions
1.6
MECHANICALSPECIFICS
Type (Panel mount)
External dimensions 28 x 92 x 135,1 mm
Weigth 0,35 kg 10.6oz
Dimensions are expressed in millimeters.
135,1
28.00
90
92
27,5
17,50
45
18.00
5.31”
1.10”
3.54”
3.62”
1,08”
0.68”
1,77”
0.70”

11
MicroStar B
Service manual MicroStar B rev06 0909
0909
09
Humidity range From 5 to 95% NOT CONDENSING
Ambient Temperature: to 45°C
Protection Class : IP2 Pollution : 2 or better
Power Supply
Min - max (V)
SMB 6 2 -82 2,5-5 5-1
SMB 11 3 -13 8-16 1 -2
Ioutput
(A)
S.N
Drive label description
Contaminants
Pollutiondegree
Drive label
1.7
Ambient temperature
Output current
Power supply
min/max Vdc
Protection class
Ordering code
Ordering code
The Label printed above is a typical example. To identify the various options see below:
“Ordering code” is an internal production code. Use this number for any enquires.
Optional*: contact factory
001029 Serial number
SMB 10/20
Size (A): 2/4
4/8
7/14
10/20
60
Model:
60 - 110 - 140
E
Feedback:
E= Encoder
A=Armature
S
Comand:
S= Standard
P= Pwm+Dir *

12 Service manual MicroStar B rev06
MicroStar B
0909
0909
09
Description
M2 connector
Components description
1.8
M2 CONNECTOR
+HV (IN) Positive Power supply input
GND (IN) Negative Power Supply input (GND)
U(OUT) Motor connection U phase, or -M
V (OUT) Motor connection V phase, or +M
W (OUT)
Motor connection W phase
The drive system consists of the following components:
n°1 Servo Drive
n°1 M1 Signal terminal 16 pins "type MC 1,5/16-ST-3,81"
n°1 M2 Power Terminals 5 pins "type GMST 2,5/5-G-5,08"
Power connector
M2
M1
TP

13
MicroStar B
Service manual MicroStar B rev06 0909
0909
09
M1 Connector
Signal inputs and outputs
1.9
M1 CONNECTOR
1 CURR (OUT) Current motor monitor: +/-4Vdc=Rated current, +/-8Vdc=Peak
current output in Volts. This output may be used to monitor the
torque the motor is producing.
2 OK (OUT) Drive OK, open collector output max. 50mA
(Normally closed, opens when in protection mode)
3 TPRC (IN)
This signal can be used in 2 distinct modes
1) Motor Current limit mode:
A motor current limit mode connect an external resistor to
GND reduces the maximun current. Connect a 1/4W o 1/8W
resistor between the TPRC (pin 3) and GND (pin 4)
terminals. A 47Kohm external resistor reduces the current by
50%. (Note: The drive velocity loop remains active)
2) Current Reference (Torque Input)
Range: +/- 10V, which corresponds to the drives peak current
output. In this mode the velocity loop is automat
ically
disabled.
4 GND Signal Common Ground
Corrisponds to power supply's negative GND input
5 +10V (OUT) Power supply +10Vdc max 4mA
6 -10V (OUT) Power supply -10Vdc max 4mA
7 ENABLE (IN) Positive drive Enable with range >+8Vdc min. to +30Vdc max. It's
also possible to enable the drive with negative logic by
connecting a GND input, see chapter 2.10
8 +VEL (IN) Reference Positive differential input (Velocity command)
9 -VEL (IN) Reference Negative differential input (Velocity command)
10 CHA (IN) Encoder input Channel A (High logic level from >2,8V to +24Vdc
max. Low logic level <1,5V)
11 CHB (IN) Encoder input Channel B (High logic level from >2,8V to +24Vdc
max. Low logic level <1,5V)
12 +5V (OUT) Power supply +5V max. 130mA
13 GND Signal Common Ground. Corrisponds to power supply's negative
GND input.
14 HU (IN)
15 HV (IN)
16 HW (IN)
Hall Sensor inputs from the motor. Each input has a pull-up
resistor of 1 Kohm to internal +5V (High logic level >3,2V , Low
logic level <1,5V)

14 Service manual MicroStar B rev06
MicroStar B
0909
0909
09
Potentiometer adjustments
Potentiometer Adjustments
1.10
FUNCTION
VEL
Motor fine speed adjustement. Use this potentiometer to adjust the
maximum motor speed. Turn clockwise (cw) to increase the motor speed
and counter-clockwise (ccw) to reduce the motor speed. The range of the
adjustment is +/-20%. Note: Potentiometer is disabled in torque mode.
BIL Offset adjustment.
Adjust this potentiometer to cancel any motor speed
when the Velocity input is zero Vdc.
(Max Velocity compensation +/- 250mV).
KV
Gain potentiometer.
Use this potentiometer to increase or decrease the
dynamic behavior of the mo
tor. With a clockwise turn (cw) we increase the
gain of the PI “speed loop”, therefore, improving the response.
Note: Potentiometer is disabled in torque mode.
DER Derivative potentiometer.
Turning this potentiometer clockwise
decreases motor overshoot.
Note: Potentiometer is disabled in torque
mode.
ACC
Ramp adjustement.
The solder bridges 1, 2 and 3 select the acc/dec
function (ramp). With this potentiometer we can adjust the slope of the
acceleration and deceleration ramps. Turning the potentiomete
r clockwise
(cw) increases the ramp time from 0,1 to 1 Sec (with 10 V input velocity).
See chapter 3.5

15
MicroStar B
Service manual MicroStar B rev06 0909
0909
09
Leds
Indicator Leds and Protections
1.11
Five LEDs are located just in front of the potentiometers and show the current state of
the drive.
FUNCTION
OK
GREEN
Normally ON.
This indicator shows that the drive is operating correctly. If
this LED is Off, it is indi
cating at least one fault has been activated. The
faults that affect this LED are:
--Over/Under input voltage.--Over temperature.
--Short Circuit, Outputs shorted to each other or to ground.--Missing Hall.
IN
RED Normally OFF. This indicator is lit if t
he drive is in over nominal current
mode.
ST
RED
Normally OFF.
This indicator is lit when the drives internal temperature
reaches 70°C . Remove power and wait for the drive to cool before re-
applying power. If operating temperatures are close to the Max
operating
temperature of the drive, a fan, heat sink or air conditioner may be needed
to remedy the problem.
OC
RED
Normally OFF.
This indicator is lit if there is a short circuit between the
motor leads and/or ground. Remove power and examine the motor
connecting leads for shorts before re-powering the drive.
AH
RED
Normally OFF.
If lit it represents either missing Hall. Have a qualified
technician check the Hall Effect signals with a voltmeter or an oscilloscope.
This fault is a latching fault.
This DRIVE is equipped with protection circuits to safeguard both the motor and the
drive, in case of faults malfunctions. All faults are indicated by LEDs on the front.
The two types of interventions are Reversible and Irreversible
Reversible: The drive is automatically reset/restarted when the cause of intervention
has been corrected. - Nominal Current IxT limitation - Over/under voltage input
Irreversible: The drive is not reset/restarted. The power supply must be removed and
the cause of intervention eliminated, then the power supply can be replaced.
*Note:Amininum amount of time must pass inorder to ensure that thedrive is completely
off prior to replacing the power supply. - Short circuit motor - Over temperature drive -
Missing Hall Signals - Improper Hall Commutation
Protections

16 Service manual MicroStar B rev06
MicroStar B
0909
0909
09
Internal adjustement
Solder bridges
Adjustement zone
Internal adjustement
1.12
If changes need to made to the internal drive setting powering, please wait at least 40
seconds after the power has been removed and the OK LED is off.
Allofthe personalizations arelocatedinsideof the DRIVE. Togain access totheadjustment
pads and the Solder bridges, unscrew and remove the cover. (See figure above)
Solder point standard configuration
Solder bridges standard position are setting by
factory for:
- Encoder feedback
- Ramp time disabled
- Standard Dynamic constant
S1: Open
S2: Closed
S3: Open
S4: Closed
S5: Closed
S6: Open
S7: Open
S8: Closed
S9: Open
S10: Open
S11: Closed

17
MicroStar B
Service manual MicroStar B rev06 0909
0909
09
Adjustement zone
1.12 Internal adjustement
Solder bridges
FUNCTION
RENC Encoder resistor adjustement
RA Armature resistor adjustement
RCA Droop compensation for internal motor resistance (RI)
RIN Nominal drive current resistor
RIP Peak drive current resistor
RKV Resistor value that respectively form the proportional/integral network of the
velocity Loop gain. Disabled by opening solder bridge S4. Standard value 100k
and 47nF.
GAIN Changes static gain in the velocity loop. Open solder bridge S5 and insert R
GAIN if a change is required. Consult factory for the correct value.
RAMP Resistor for change RAMP function. See Chapter 3.5
CKV Capacitor value that respectively form the proportional/integral network of the
velocity Loop gain. Disabled by opening solder bridge S4. Standard value 100k
and 47nF.
CDER Derivative constant capacitor, increases the velocity loop derivative constant.
Consult factory for the correct value.
SOLDER POINT
1 & 3 Normally open (OFF) See Chapter 3.5 “Ramp time adjustment”
2 Normally closed (ON) See Chapter 3.5 “Ramp time adjustment”
4 Normally closed (ON)
If Open , install components in the adjustment zone, for
the dynamic velocity value CKV and RKV. (Standard value RKV=100Kohm ,
CKV= 47nF).
5 Normally closed (ON) If Open you must insert the GAIN resistor. (Static
Gain). Standard value= 27 ohm
6 Normally open (OFF)
If closed, when the IN protection operates the green
OK LED goes off.
7 Normally open (OFF) If closed the drive is set is for the armature feedback.
Insert also the resistance RA and RCA
8 Normally closed (ON) In this position the drive is set is for the encoder
feedback. If Open (OFF), are enable other type of feedback.
9 Normally open (OFF) If closed setting the drive for PWM+DIR comand
10 Normally open (OFF)
11 Normally closed (ON) If open (OFF), the alarm protection for missing Hall
Effect Signals will not disable the drive.

18 Service manual MicroStar B rev06
MicroStar B
0909
0909
09
Power supply construction
Transformer: ( T )
VDC = V2 * 1,41
Power supply
1.13
This component was designed to generate all required supply voltages in the Drive, so
only a simple single voltage power supply is needed. Use the schematic and formulas
providedbelowto design a supply thatwillbetrouble-free and handle the powerneededby
the drive.
NOTE:
Asingle ground is used in the Drive that is connected to GND, so DO NOT USEANAUTO
TRANSFORMER.
Use a standard heavy duty power transformer without center taps on the secondary as
shown in the schematic above.
The VArating should be 10% greater than the power needed by the system to insure cool
operation. DO NOT CONNECT ANY TRANSFORMER PRIMARY, OR SECONDARY
SIGNALS TO GROUND.
Keep the +HV GND wires, between the power supply and the drive, as short as possible.
Voltage:
Theprimaryvoltagedependson whatisavailablelocallyforasinglephase. Thesecondary
voltage is calculated from the motor’s voltage at the required operating speed.
The secondary voltage VDC is:
Example: If the secondary transformer is 44Vac, the VDC output is 44*1,41=63Vdc
The drives have to be supplied from an isolating rectified transformer secondary or a DC
isolated power supply.

19
MicroStar B
Service manual MicroStar B rev06 0909
0909
09
The transformer's nominal power is calculated based upon the sum of power from the
single motors driven:
Where: Pn Motor =Power absorbed motor in (W)
N=Max. speed of motor in RPM.
Cn =Nominal torque of motor in (Nm).
Pn Motor = N * Cn / 9,55
P(VA)=Pn1+Pn2+..
Power transformer
1.13 Power supply
VDC = Vdc motor / 0,85
Example: Brushless motor with the following data:
In =5 (A)
Ri = 1 (Ohm)
E=48 (V) at nominal speed 3000 (RPM)
Vdc motor = E+(Ri * In)
E = Ke * N° / 1000
Voltage motor
Where the Vdc motor is a sum of FCEM + the drop R*I for the winding resistance motor
The FCEM of the motor "E", may be calculated by the formula:
Vdc motor = 48 + ( 1 * 5) = 53V
VDC = 53 / 0,85 = 62,3V
62,3V is the VDC voltage request for the power supply. You'll use a transformer with the
secondary V2 = 62 / 1,41= 44Vac
When you use the transformer with V2= 44/48Vac, it is correct.
Note: In multi-axis applications, the transformer's power can be downgraded by 30%.
If the max. power transformer calculated is 6KVAcontact the factory.
Ifthe secondary voltageof powersupply is VDC, theVdc motor iscalculatedby the formu-
la:
Misure unit:
E = Ke *n°/1000 (Vdc)
Im = I motor (A)
Ri = Winding resistance (Ohm)
Ke =Voltage constant (V/kRPM)
n° = MAX speed (RPM)

20 Service manual MicroStar B rev06
MicroStar B
0909
0909
09
In regards to the capacitor filter we suggest a working voltage of:
100VDC for (Model-60)
150VDC for (Model-110)
Tipical value are from 4700uF to 20.000uF
Capacitor filter
Discharge resistor
Fusibili
Fuses or similar
F1 (A) = P (VA) trasfo. / VAC (V) * 1,2
1.13 Power supply
The bleeder resistor is used to drain the charge from the filter capacitor when power is
removed from the supply. This helps in bringing the supply voltage down quickly. This
resistor is mounted directly across the filter capacitor.
Warning!
Discharge resistor for:
VDC=60V is 3K9 / 4W,
VDC=100V is 15K / 4W
Fusesarerequired on both the primaryandsecondaryofthe transformer to protectagainst
harm to the system and the transformer itself. They need to be of the slow blow type to
handle current in-rush at power-up. Locate the primary fuse (F1) on the hot leg of theAC
input power and the secondary fuse (F2) on the + side of the secondary output, before the
rectifier.
Primary of the transformer: Use the formula below to calculate the correct values:
Secondary of the transformer: Use the table below
FUSE F2 (A) SIZE Drive (A)
5 2/4
8 4/8
12 7/14
16 10/20
This manual suits for next models
3
Table of contents
Popular DC Drive manuals by other brands
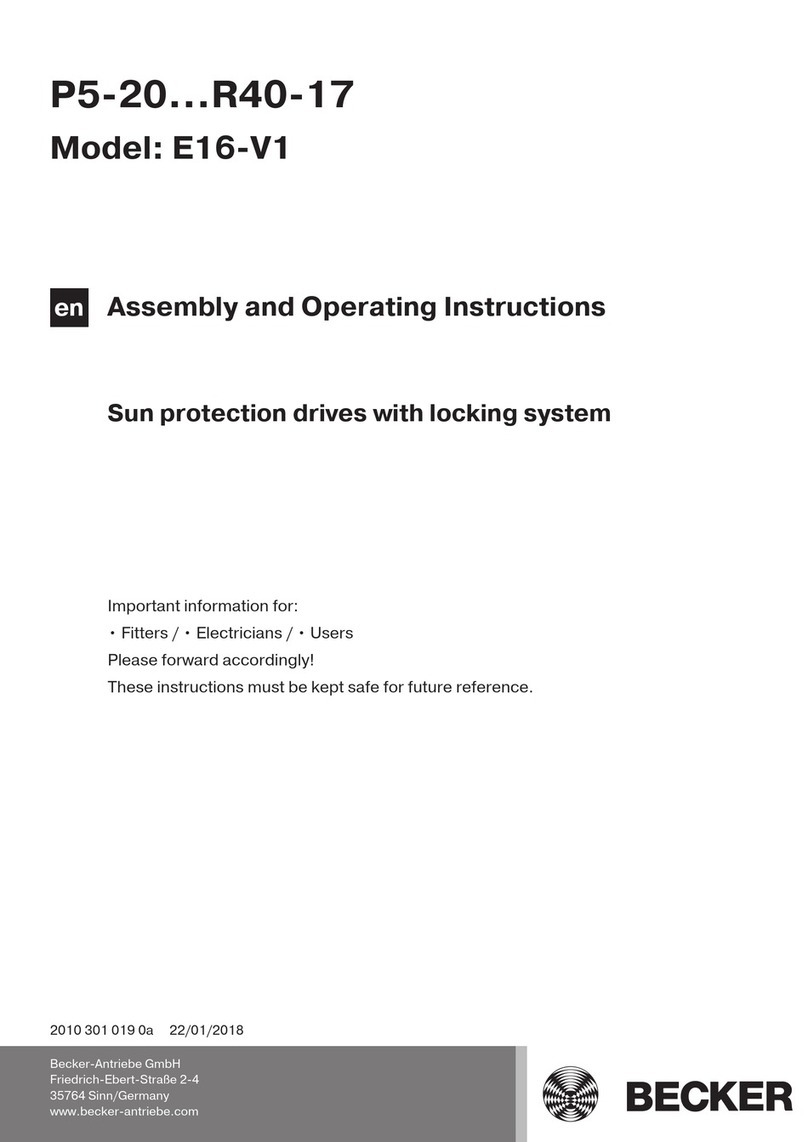
Becker
Becker E16-V1 Assembly and operating instructions

YASKAWA
YASKAWA SI-T3 MECHATROLINK-II A1000 Series installation manual
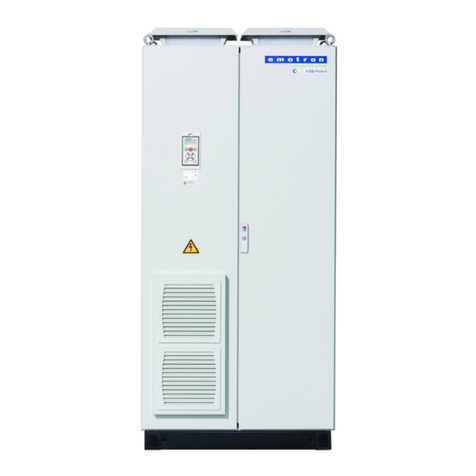
Emotron
Emotron VFX 2.1 instruction manual
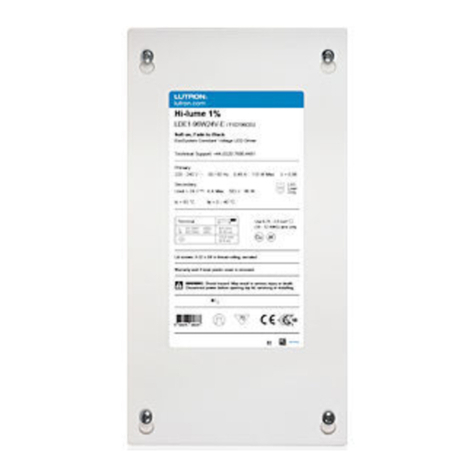
Lutron Electronics
Lutron Electronics Hi-lume EcoSystem Installation
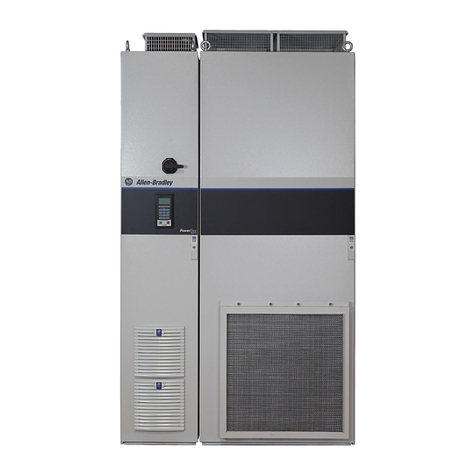
Rockwell Automation
Rockwell Automation Allen-Bradley PowerFlex 750 Series Service manual
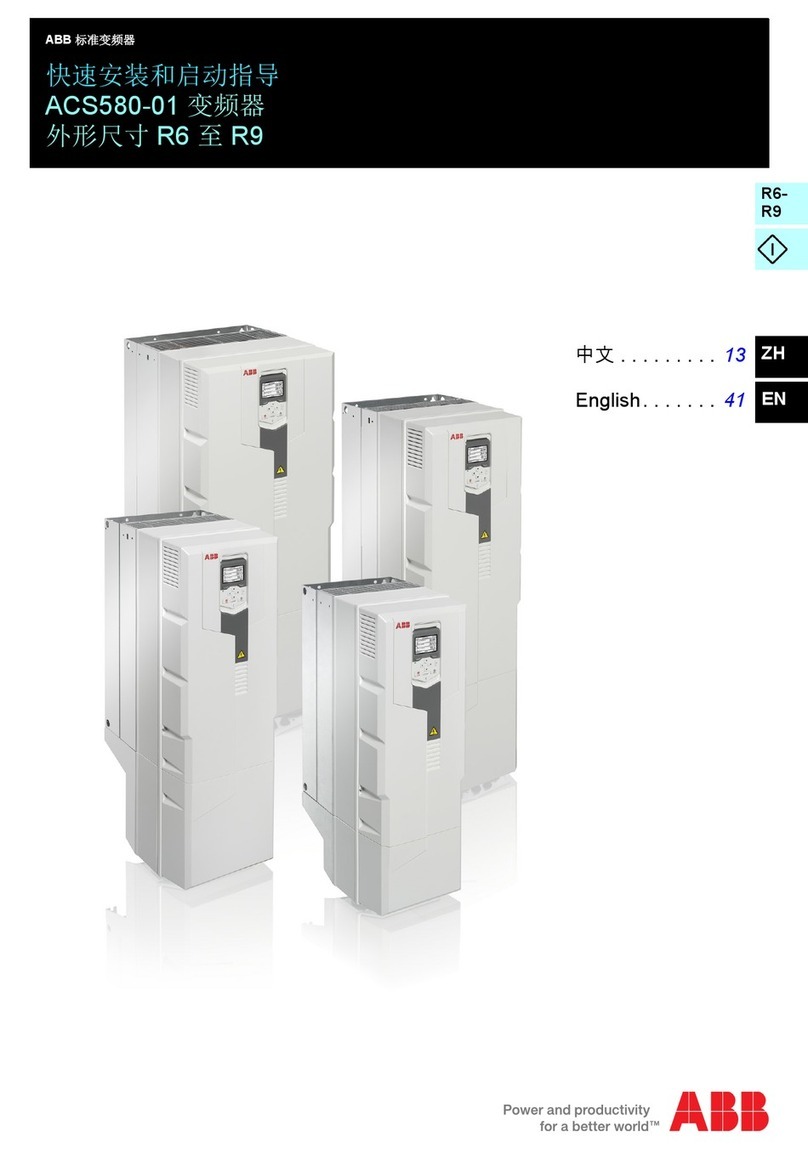
ABB
ABB EN Series Quick installation guide
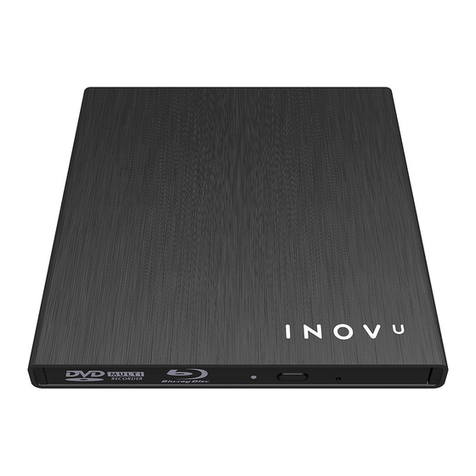
INOVU
INOVU BRD-01 user guide
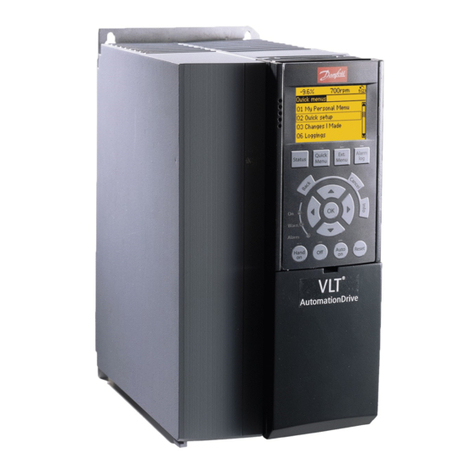
Danfoss
Danfoss VLT AutomationDrive FC 300 operating instructions
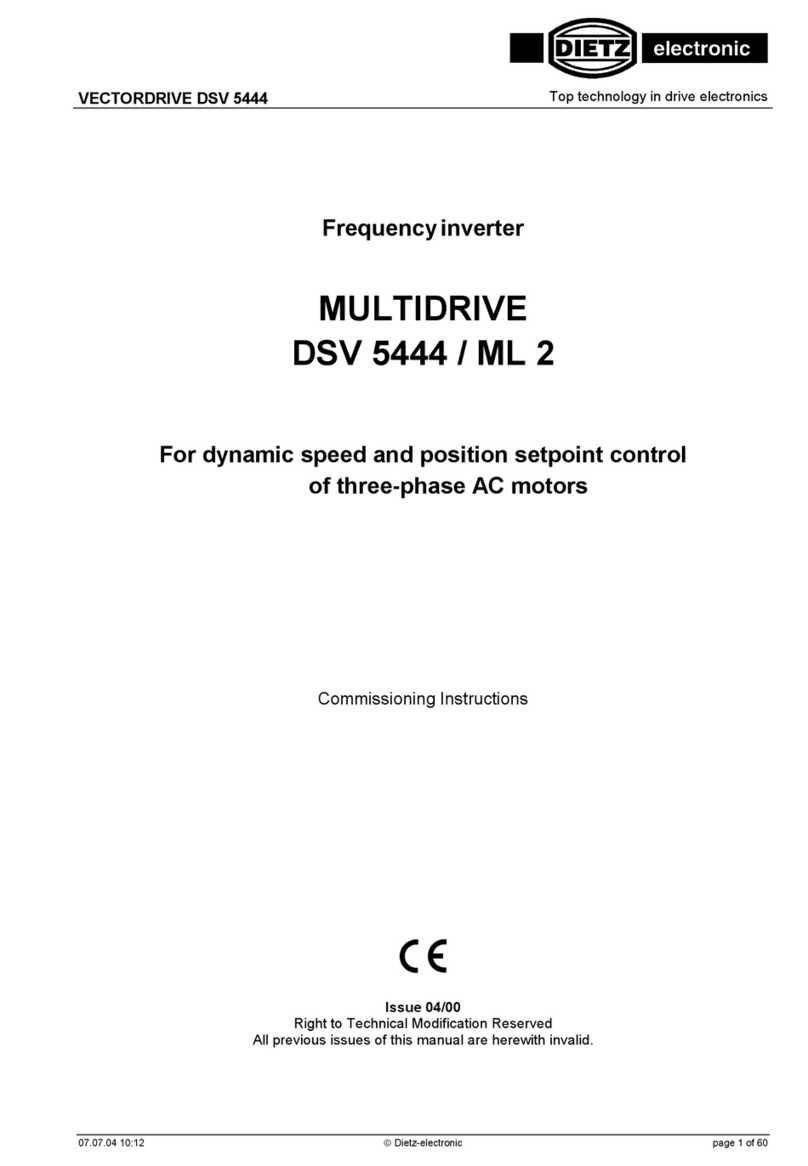
Dietz
Dietz DSV 5444 / ML 2 Commissioning instructions

PXM
PXM PX782 user manual
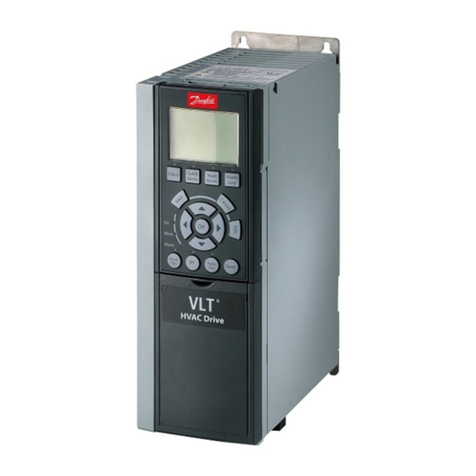
Danfoss
Danfoss VLT AutomationDrive FC 303 instruction manual
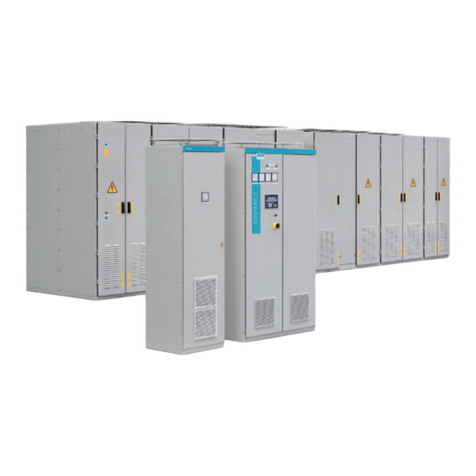
Siemens
Siemens SINAMICS GL150 Operating instructions & installation instructions