Stübbe DFM Series Installation instructions

Flowmeter
Original operating manual Series
DFM 165 – 350
Version BA-2016.08.09 EN
Print-No. 300 458
TR MA DE Rev002
ASV Stübbe GmbH & Co. KG
Hollwieser Straße 5
32602 Vlotho
Germany
Phone: +49 (0) 5733-799-0
Fax: +49 (0) 5733-799-5000
E-mail: [email protected]
Internet: www.asv-stuebbe.com
We reserve the right to make technical changes.
Read carefully before use.
Save for future use.

Table of contents
Table of contents
1 About this document ............................... 3
1.1 Target groups ................................. 3
1.2 Other applicable documents ................ 3
1.3 Warnings and symbols ....................... 3
2 General safety instructions ....................... 4
2.1 Intended use .................................. 4
2.2 General safety instructions .................. 4
2.2.1 Obligations of the operating company . .... . 4
2.2.2 Obligations of personnel ..................... 4
2.3 Specific hazards .............................. 4
2.3.1 Hazardous media ............................ 4
3 Layout and Function ............................... 5
3.1 Marking ....................................... 5
3.1.1 Name plate ................................... 5
3.2 Description .................................... 5
3.3 Layout ......................................... 5
4 Transport, Storage and Disposal ................. 6
4.1 Unpacking and inspection on delivery . . . . . . 6
4.2 Transportation ................................ 6
4.3 Storage ....................................... 6
4.4 Disposal ....................................... 6
5 Installation and connection ....................... 7
5.1 Check operating conditions ................. 7
5.2 Planning pipelines ............................ 7
5.2.1 Specify pipes and fittings .................... 7
5.2.2 Providing safety and control devices
(recommended) .............................. 7
5.3 Install device .................................. 8
5.3.2 Connection with union nut and insert . . . . . . . 8
5.3.3 Connection with flange ...................... 8
5.3.4 If necessary: Attach special scale .......... 8
5.4 Performing the hydrostatic test .............. 8
6Operation ............................................ 9
6.1 Commissioning .............................. 9
6.2 Read measurement .......................... 9
7 Maintenance ......................................... 10
7.1 Servicing ...................................... 10
7.2 Maintenance .................................. 10
7.2.1 Removing fitting .............................. 10
7.3 Replacement parts and return .............. 10
8 Troubleshooting .................................... 11
8.1 Clean measuring tube and float ............. 11
9 Appendix ............................................. 12
9.1 Technical specifications ...................... 12
9.1.1 Mechanical specifications ................... 12
9.1.2 Dimensions ................................... 12
9.2 Tightening torques ........................... 12
9.3 Accessories ................................... 12
List of figures
Fig. 1 Name plate (example) ....................... 5
Fig. 2 Layout ......................................... 5
List of tables
Tab. 1 Other application documents, purpose and
where found .................................. 3
Tab. 2 Warnings and symbols ....................... 3
Tab. 3 Servicing activities ........................... 10
Tab. 4 Troubleshooting .............................. 11
Tab. 5 Mechanical specifications ................... 12
Tab. 6 Tightening torques ........................... 12
Tab. 7 Accessories ................................... 12
2 DFM 165 – 350 BA-2016.08.09 EN 300 458

About this document
1 About this document
This manual
• is part of the equipment
• applies to all series referred to
• describes safe and proper operation during all operating
phases
1.1 Target groups
Operating company
• Responsibilities:
– Always keep this manual accessible where the device
is used on the system.
– Ensure that employees read and observe this docu-
ment, particularly the safety instructions and warnings,
and the documents which also apply.
– Observe any additional country-specific rules and re-
gulations that relate to the system.
Qualified personnel, fitter
• Mechanics qualification:
– Qualified employees with additional training for fitting
the respective pipework.
• Electrical qualification:
– Qualified electrician
• Transport qualification:
– Qualified transport specialist
• Responsibility:
– Read, observe and follow this manual and the other
applicable documents, especially all safety instructions
and warnings.
1.2 Other applicable documents
Resistance lists
Resistance of materialsusedtochemicals
www.asv-stuebbe.de/pdf_resistance/300051.pdf
Data sheet
Technical specifications, conditions of
operation
www.asv-stuebbe.de/pdf_datasheets/300464.pdf
CE declaration of conformity
Conformity with standards
www.asv-stuebbe.de/pdf_DOC/300168.pdf
Tab. 1 Other application documents, purpose
and where found
1.3 Warnings and symbols
Symbol Meaning
• Immediate acute risk
• Death, serious bodily harm
• Potentially acute risk
• Death, serious bodily harm
• Potentially hazardous situation
• Minor injury
• Potentially hazardous situation
• Material damage
Safety warning sign
Take note of all information
highlighted by the safety warning
sign and follow the instructions to
avoid injury or death.
Instruction
1. , 2. , ... Multiple-step instructions
Precondition
→Cross reference
Information, notes
Tab. 2 Warnings and symbols
300 458 BA-2016.08.09 EN DFM 165 – 350 3

General safety instructions
2 General safety instructions
The manufacturer accepts no liability for damages caused
by disregarding any of the documentation.
2.1 Intended use
The device measures the flow of a liquid or gaseous medium.
• Device must only be used for measuring the flow in liquid
or gaseous media.
– Measuring tubes made of PVC may not be used for
gaseous media (danger of splintering)
• Only use the device with suitable media
(→resistance lists).
• Adhere to the operating limits (→Data sheet).
2.2 General safety instructions
Observe the following regulations before carrying out any
work.
2.2.1 Obligations of the operating company
Safety-conscious operation
• Only operate the device if it is in perfect technical condition
and only use it as intended, staying aware of safety and
risks, and in adherence to the instructions in this manual.
• Ensure that the following safety aspects are observed and
monitored:
– Intended use
– Statutory or other safety and accident-prevention reg-
ulations
– Safety regulations governing the handling of ha-
zardous substances
– Applicable standards and guidelines in the country
where the pump is operated
• Make personal protective equipment available.
Qualified personnel
• Make sure all personnel tasked with work on the device
have read and understood this manual and all other appli-
cable documents, especially the safety, maintenance and
repair information, before they start any work.
• Organize responsibilities, areas of competence and the
supervision of personnel.
• The following work should be carried out by specialist tech-
nicians only:
– Installation, repair and maintenance work
– Work on the electrical system
• Make sure that trainee personnel only work on the device
under supervision of specialist technicians.
2.2.2 Obligations of personnel
Only complete work on the device if the following requirements
are met:
• System is empty
• System has been flushed
• System is depressurized
• System has cooled down
• System is secured against being switched back on again
• Do not make any modifications to the device.
2.3 Specific hazards
2.3.1 Hazardous media
• When handling hazardous media, observe the safety reg-
ulations for the handling of hazardous substances.
• Use personal protective equipment when carrying out any
work on the device.
• Collect leaking pumped liquid and residues in a safe man-
ner and dispose of in accordance with environmental reg-
ulations.
4 DFM 165 – 350 BA-2016.08.09 EN 300 458

Layout and Function
3 Layout and Function
3.1 Marking
3.1.1 Name plate
The name plate is found on the packing box.
1
2
3
4PN/DN
10/65
Range
25-250 l/min Wasser
FA16-61906
Type DFM 350
Id. No. 2215870030
Materials
PVC-U
EPDM
PTFE
5
DFM350 PVC EDPM DN65 PVC
Fig. 1 Name plate (example)
1Type
2 ID number
3 Measurement range
4 Nominal pressure [bar] / Nominal diameter [mm]
5 Materials (body, ball, other seals/gaskets)
3.2 Description
The device measures the flow of a liquid or gaseous medium.
The medium flows through the flowmeter vertically from bot-
tom to top. The float is lifted by the flow forces. On the upper
reading edge (largest diameter), the flow quantity (in volume or
mass)canbereadonthemeasuringtubescale.
The displayed value only applies for the medium and medium
temperature for which the device has been calibrated.
3.3 Layout
1
2
4
5
6
3
3
3
1
2
4
5
6
Fig. 2 Layout
1 Union nut
2 Union end
3 Union end (stop)
4Float
5 Setpoint indicator
6 Measuring tube
300 458 BA-2016.08.09 EN DFM 165 – 350 5

Transport, Storage and Disposal
4 Transport, Storage and Disposal
4.1 Unpacking and inspection on delivery
1. Unpack the device when received and inspect it for trans-
port damage and completeness.
2. Check that the material specifications on the name plate
(see packing box) and order/sizing data match.
3. Report any transport damage to the manufacturer immedi-
ately.
4. If fitted immediately: Dispose of packaging material
according to local regulations.
–Iffitted at a later point: leave device in its original pack-
aging.
4.2 Transportation
Device should preferably be transported in the original
packaging.
4.3 Storage
NOTE
Material damage due to inappropriate storage!
Store the device properly.
1. Make sure the storage room meets the following condi-
tions:
–Dry
– Frost-free
– Vibration-free
– Not in direct sunlight
– Storage temperature +10 °C to +60 °C
2. Device should preferably be stored in the original packag-
ing.
4.4 Disposal
Plastic parts can be contaminated by poisonous or radioac-
tive media to such an extent that cleaning will not be suffi-
cient.
WARNING
Risk of poisoning and environmental damage from
medium.
Use personal protective equipment when carrying out any
work on the device.
Prior to the disposal of the device: Neutralize residues of
medium in the device.
1. Remove battery and dispose of in accordance with local
regulations.
2. Remove electronic parts and dispose of in accordance with
local regulations.
3. Dispose of plastic parts in accordance with local regula-
tions.
6 DFM 165 – 350 BA-2016.08.09 EN 300 458

Installation and connection
5 Installation and connection
5.1 Check operating conditions
WARNING
Splintering measuring tube!
Do not use measuring tube made of PVC for gaseous
media.
1. Ensure the required operating conditions are met:
– Resistance of body and seal material to the medium
(→resistance lists).
– Media temperature (→Data sheet).
– Operating pressure (→Data sheet).
2. Consult with the manufacturer regarding any other use of
the device.
5.2 Planning pipelines
5.2.1 Specify pipes and fittings
1. Ensure installation position:
–vertical
– Direction of flow from bottom to top
– Device is freely accessible from all sides
2. Ensure pipe connection without tension.
– If necessary, equip with expansion shanks or pipe com-
pensators
3. Straight pipe lengths before and after device (recom-
mended to avoid vibration of the float)
– DN = DN device
– Length > 5–7 x DN device
– Length > 10 x DN device for large differences between
nominal diameters between pipe and device
4. If necessary:
– For gaseous media, equip with vent valve at highest
point of inlet and outlet pipe
– For condensing gaseous, equip with vent valve at low-
est point of inlet and outlet pipe
5. Allocate control valves after device.
6. Allocate throttle valves before or after the device.
– For gasses, only after the device (to prevent vibrations
of the float)
5.2.2 Providing safety and control devices
(recommended)
Avoid contamination
1. Install filter into supply line.
2. Install a differential pressure gauge to monitor contamina-
tion.
Make provisions for isolating and shutting off the pipes
For maintenance and repair work.
1. Provide shut-off devices (V1, V2) in the inlet and outlet line.
2. If removal of the device during operation is necessary:
Install bypass line (V3).
300 458 BA-2016.08.09 EN DFM 165 – 350 7

Installation and connection
5.3 Install device
Process pipework has been properly prepared.
Process pipework has been secured against unintentional
opening with shut-off values.
Installation position vertical, direction of flow from bottom
to top.
WARNING
Risk of injury and poisoning due to medium spraying out.
Ensure that in case of a break in the measuring tube, no
hazards result from escaping media.
Do not use measuring tube made of PVC for gaseous
media.
WARNING
Risk of injury and poisoning due to medium spraying out.
Use personal protective equipment when carrying out any
work on the fitting.
1. Ensure that measuring tube (6) and float (4) are clean and
free of foreign matter.
2. Remove transport lock (holds the float).
3. Ensure that the float (4) can move freely.
5.3.2 Connection with union nut and insert
1. Unscrew both union nuts (1) (→Figure Layout, Page 5 ).
– Secure float (heavy) from falling
2. Push union nuts (1) onto spigot of process pipes.
Check mounting direction.
3. Weld union end (2) of device to spigot of process pipes.
4. Check fitofO-rings.
5. Connect device to the process pipework. Tighten union
nuts (1) by hand only.
5.3.3 Connection with flange
1. Prepare pipe ends according to connection type.
2. Radially push the fitting and flat seal between the flange
ends.
3. Bolt fitting and flange with flange screws, nuts and wa-
shers.
While doing so, observe tightening torques:
(→9.2 Tightening torques, Page 12).
5.3.4 If necessary: Attach special scale
1
2
1. With a pen, mark the lowest reading point of the existing
scale on the measuring tube (1).
2. Pull current scale off.
3. Stick new scale on so that the marking on the measuring
tube matches with the lowest reading point (2).
5.4 Performing the hydrostatic test
Perform hydrostatic test using neutral medium, e.g. water.
1. Pressurize the device, ensuring
– Test pressure < 1.5 x PN(Nominal pressure)
– Test pressure < PN+5bar
– Test pressure < permissible system pressure
2. Check that the device is not leaking.
8 DFM 165 – 350 BA-2016.08.09 EN 300 458

Operation
6 Operation
6.1 Commissioning
Device is connected properly to the process pipework.
1. Open throttle valves in inlet and outlet line.
2. Ensure that the float can float freely and measures a plau-
sible value.
6.2 Read measurement
For the measurement range 2,500-25,000, the reading
edge is below the float fixture (largest diameter)
1
1 Reading edge
Read measurement using face (1) of float.
300 458 BA-2016.08.09 EN DFM 165 – 350 9

Maintenance
7 Maintenance
WARNING
Risk of injury and poisoning due to hazardous or hot
media.
Use personal protective equipment when carrying out any
work on the device.
Allow device to cool.
Make sure the device is depressurized.
Block the media supply to the device.
Empty the process pipework, safely collect the media and
dispose of it in accordance with environmental regulations.
Switch off the power supply to the system.
Secure power supply against being switched back on
again.
Provide warning of maintenance and repair work and set
up warning signs.
7.1 Servicing
Interval Action
As necessary Clean device with a damp cloth.
Six-monthly Visual and function check:
– Normal operating conditions
unchanged
–Noleaks
– Measuring tube and float for
deposits or changes to surface
Tab. 3 Servicing activities
Perform maintenance tasks according to the table.
7.2 Maintenance
WARNING
Risk of injury during disassembly!
Wear protective gloves, components can be very sharp-
edged due to wear or damage.
7.2.1 Removing fitting
1. Ensure that:
– System is empty
– System has been flushed
– System is depressurized
– System has cooled down
– System is secured against being switched back on
again
2. Remove fitting from the pipe.
3. Decontaminate fitting if required.
–Deadspaceinthefitting may still contain medium.
7.3 Replacement parts and return
1. Have the following information ready to hand when order-
ing spare parts (→3.1.1 Name plate, Page 5 ).
–Devicetype
– ID number
– Nominal pressure and diameter
– Connection and gasket material
2. Please complete and enclose the document of compliance
for returns (→www.asv-stuebbe.com/service/downloads).
3. Only use spare parts from ASV Stübbe.
10 DFM 165 – 350 BA-2016.08.09 EN 300 458

Troubleshooting
8 Troubleshooting
WARNING
Risk of injury and poisoning due to hazardous media liq-
uids!
Use personal protective equipment when carrying out any
work on the device.
Additional troubleshooting
Error Possible cause Corrective action
Medium is leaking out of the flange Pre-tension of the O-ring too small Retighten union nut by hand.
Scale dirty or damaged Clean scale.
Replace scale.
Measurements difficult to read
Measuring tube dirty Clean or replace measuring tube
(→8.1 Clean measuring tube and
float, Page 11).
Float jammed Clean measuring tube and float
(→8.1 Clean measuring tube and
float, Page 11).
Defective display
Float weight defective Check weight of float:
• Ask for weight from manufacturer
• If weight differs, remove device,
insert new float and re-install device
(→8.1 Clean measuring tube and
float, Page 11).
No display (only for measurement sensor
ZE3000, ZE3075 or limit sensor)
Float installed incorrectly Ensure that a float with magnet is
used.
Tab. 4 Troubleshooting
8.1 Clean measuring tube and float
System is empty.
System has been flushed.
System is depressurized.
System has cooled down.
System is secured against beingswitchedbackonagain.
1. Unscrew both union nuts.
–Securefloat (heavy) from falling.
2. Remove device from pipe.
3. Ensure that measuring tube and float are clean and free of
foreign matter.
– If necessary, replace with new device.
4. Ensure that the float can move freely.
5. Install device (→5.3 Install device, Page 8 ).
300 458 BA-2016.08.09 EN DFM 165 – 350 11

Appendix
9 Appendix
9.1 Technical specifications
9.1.1 Mechanical specifications
Size Value
Process conditions (medium)
Pressure and temperature See material-dependent
pressure/temperature
diagram (→Data sheet).
Materials in contact with medium
Measuring tube PVC, PSU, PA, PVDF
Float PVDF
Float catcher PVDF
Insert PVC, PP, PVDF
O-ring FPM, EPDM
Materials not in contact with medium
Setpoint indicator PE
Union nut PVC, PP, PVDF
Tab. 5 Mechanical specifications
9.1.2 Dimensions
Dimensions (→Data sheet).
9.2 Tightening torques
Tightening torque [Nm]
for the sizes d [mm]
Description
16 20 25 32 40 50 63 75
Flange
GFK 5710 15 20 25 32 37
Flange
PP/steel -10 15 15 20 25 35 40
Tab. 6 Tightening torques
1) Greased housing screws (hex screws, hex nuts)
9.3 Accessories
Description
Flow data sensor
• ZE 3000 – magnet angle sensor
• ZE 3075 – Reed chain
Float with liquid-tight encapsulated magnet
(available complete with measuring tube)
Limit reed switch
Tab. 7 Accessories
12 DFM 165 – 350 BA-2016.08.09 EN 300 458
This manual suits for next models
2
Table of contents
Other Stübbe Measuring Instrument manuals
Popular Measuring Instrument manuals by other brands
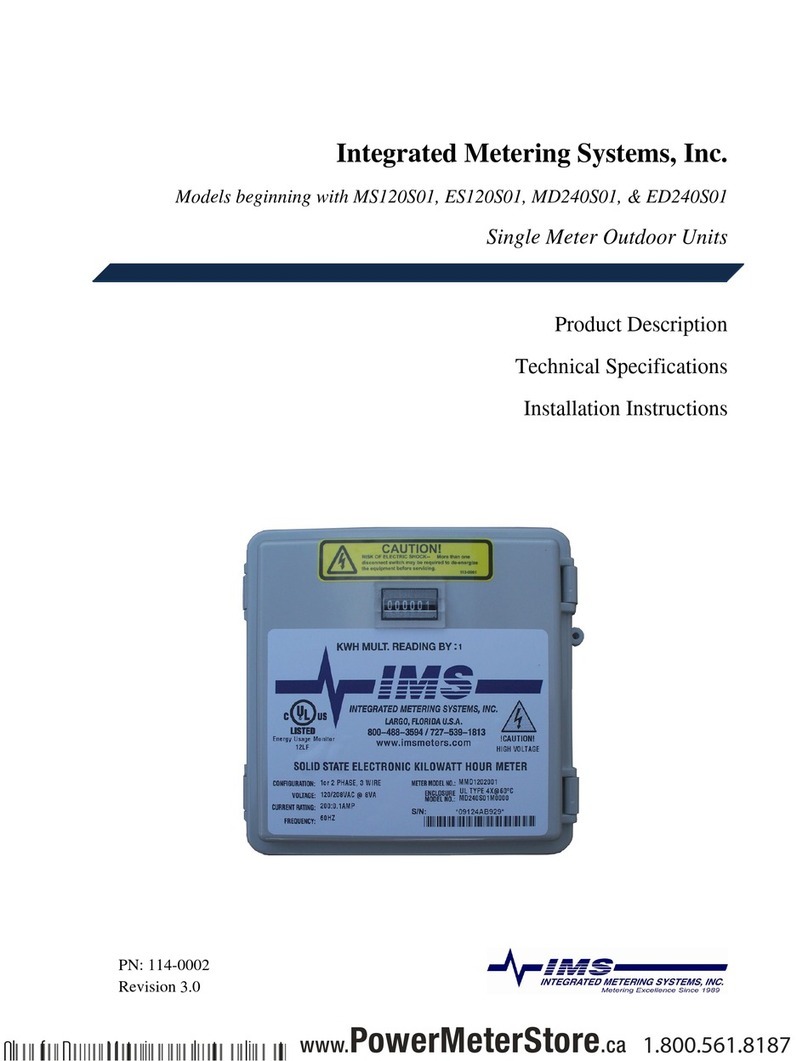
Integrated Meterting Systems
Integrated Meterting Systems MS120S01 Technical specifications and installation instructions
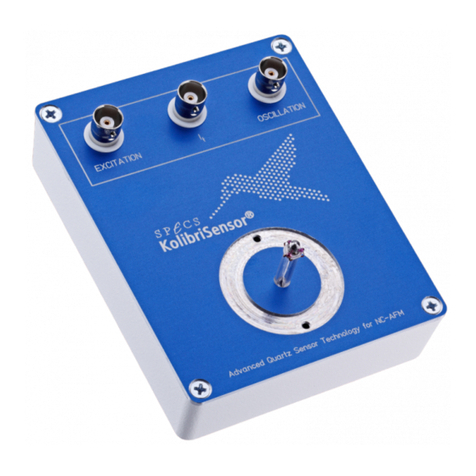
SPECS
SPECS KolibriSensor user manual
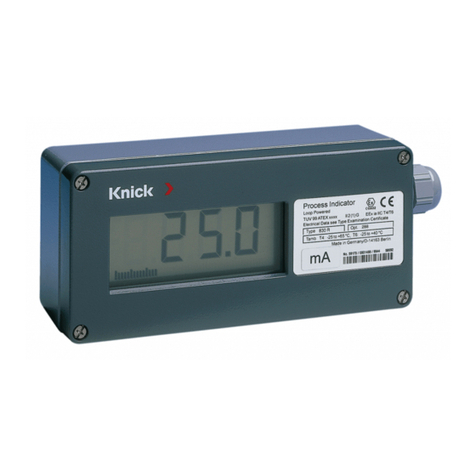
Knick
Knick 830 R manual
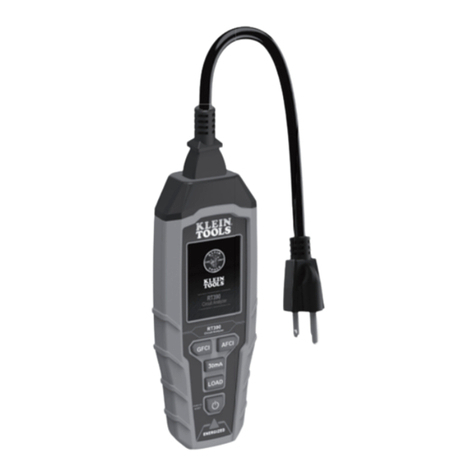
Klein Tools
Klein Tools RT390 instruction manual

Niigata seiki
Niigata seiki GVC Series instruction manual
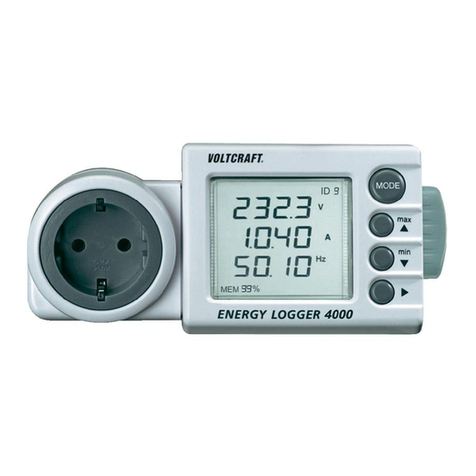
VOLTCRAFT
VOLTCRAFT Energy Logger 4000 operating instructions