Stübbe Series MDM 902 Installation instructions

Diaphragm pressure
gauge guard
Original operating manual Series
MDM 902
Version BA-2017.09.21 EN
Print-No. 301 287
TR MA DE Rev001
ASV Stübbe GmbH & Co. KG
Hollwieser Straße 5
32602 Vlotho
Germany
Phone: +49 (0) 5733-799-0
Fax: +49 (0) 5733-799-5000
E-mail: [email protected]
Internet: www.asv-stuebbe.com
We reserve the right tomake
technical changes.
Read carefully before use.
Save for future use.

Table of contents
Table of contents
1 About this document ............................... 3
1.1 Target groups ................................. 3
1.2 Other applicable documents ................ 3
1.3 Warnings and symbols ....................... 3
2 General safety instructions ....................... 4
2.1 Intended use .................................. 4
2.2 General safety instructions .................. 4
2.2.1 Obligations of the operating company . .... . 4
2.2.2 Obligations of personnel ..................... 4
2.3 Hazardous media ............................ 4
3 Layout and Function ............................... 5
3.1 Type plate .................................... 5
3.2 Description .................................... 5
3.3 Layout ......................................... 5
4 Transport, Storage and Disposal ................. 6
4.1 Unpacking and inspection on delivery . . . . . . 6
4.2 Transportation ................................ 6
4.3 Storage ....................................... 6
4.4 Disposal ....................................... 6
5 Installation and connection ....................... 7
5.1 Preparing for installation ..................... 7
5.1.1 Check operating conditions ................. 7
5.1.2 Check the installed condition of the
fitting .......................................... 7
5.2 Planning pipelines ............................ 7
5.3 Installing the fitting ........................... 7
5.3.1 Fill the fitting .................................. 7
5.3.2 Installing and filling the pressure
gauge ......................................... 7
5.4 Installing fitting in pipe ....................... 8
5.4.2 Connection with solvent welding/butt-weld
spigot ends ................................... 8
5.4.3 Connection with internal thread fixed ....... 8
5.5 Performing the hydrostatic test .............. 8
6Operation ............................................ 9
6.1 Commissioning .............................. 9
7 Maintenance ......................................... 10
7.1 Servicing ...................................... 10
7.2 Maintenance .................................. 10
7.2.1 Removing fitting .............................. 10
7.2.2 Changing the separation diaphragm . ... . .. . 10
7.2.3 Replacement parts and return .............. 10
8 Troubleshooting .................................... 11
9 Appendix ............................................. 12
9.1 Technical specifications ...................... 12
9.2 Dimensions ................................... 12
9.3 Transmitter fluid .............................. 12
9.4 Tightening torques ........................... 12
9.5 Sectional drawing ............................ 12
List of figures
Fig. 1 Type plate (example) ........................ 5
Fig. 2 Layout ........................................ 5
Fig. 3 Sectional drawing ............................ 12
List of tables
Tab. 1 Other application documents, purpose and
where found .................................. 3
Tab. 2 Warnings and symbols ....................... 3
Tab. 3 Troubleshooting .............................. 11
Tab. 4 Transmitter fluid .............................. 12
Tab. 5 Tightening torques ........................... 12
2 MDM 902 BA-2017.09.21 EN 301 287

About this document
1 About this document
This manual
• ispartofthefitting
• applies to all series referred to
• describes safe and proper operation during all operating
phases
1.1 Target groups
Operating company
• Responsibilities:
– Always keep this manual accessible where the device
is used on the system.
– Ensure that employees read and observe this docu-
ment, particularly the safety instructions and warnings,
and the documents which also apply.
– Observe any additional country-specific rules and reg-
ulations that relate to the system.
Qualified personnel, fitter
• Mechanics qualification:
– Qualified employees with additional training for fitting
the respective pipework.
• Electrical qualification:
– Qualified electrician
• Transport qualification:
– Qualified transport specialist
• Responsibility:
– Read, observe and follow this manual and the other
applicable documents, especially all safety instructions
and warnings.
1.2 Other applicable documents
To download:
Resistance lists
Resistance of materials used to
chemicals
www.asv-stuebbe.de/pdf_resistance/300051.pdf
To download:
Data sheet
Technical specifications, conditions of
operation
www.asv-stuebbe.de/pdf_datasheets/301281.pdf
To download:
CE declaration of conformity
Conformity with standards
www.asv-stuebbe.de/pdf_DOC/300168.pdf
Tab. 1 Other application documents, purpose
and where found
1.3 Warnings and symbols
Symbol Meaning
• Immediate acute risk
• Death, serious bodily harm
• Potentially acute risk
• Death, serious bodily harm
• Potentially hazardous situation
• Minor injury
• Potentially hazardous situation
• Material damage
Safety warning sign
Take note of all information
highlighted by the safety warning
sign and follow the instructions to
avoid injury or death.
Instruction
1., 2., ... Multiple-step instructions
Precondition
→Cross reference
Information, notes
Tab. 2 Warnings and symbols
301 287 BA-2017.09.21 EN MDM 902 3

General safety instructions
2 General
safety instructions
The manufacturer accepts no liability for damages caused
by disregarding any of the documentation.
2.1 Intended use
The fittingisusedfortransmittingmediapressuretoapressure
gauge.
•Usethefitting exclusively transmitting media pressure.
•Usethefitting exclusively with a pressure gauge fitted.
•Usethefitting exclusively for technically pure media free of
solids (→Resistance list).
• Adhere to the operating limits (→Data sheet).
•Usethefitting exclusively in the following direction of instal-
lation:
– The bottom section mounted on the pressurized pipe
– The pressure gauge mounted on the upper part
2.2 General safety instructions
Read and observe the following regulations before carrying
out any work.
2.2.1 Obligations of the operating company
Safety-conscious operation
• Only operate the fitting if it is in perfect technical condition
and only use it as intended, staying aware of safety and
risks, and in adherence to the instructions in this manual.
• Ensure that the following safety aspects are observed and
monitored:
– Intended use
– Statutory or other safety and accident-prevention reg-
ulations
– Safety regulations governing the handling of haz-
ardous substances
– Applicable standards and guidelines in the country
where the pump is operated
• Make personal protective equipment available.
Qualified personnel
• Make sure all personnel tasked with work on the fitting have
read and understood this manual and all other applicable
documents, especially the safety, maintenance and repair
information, before they start any work.
• Organize responsibilities, areas of competence and the
supervision of personnel.
• The following work should be carried out by specialist tech-
nicians only:
– Installation, repair and maintenance work
– Work on the electrical system
• Make sure that trainee personnel only work on the fitting
under supervision of specialist technicians.
2.2.2 Obligations of personnel
• Observe the instructions on the fitting and keep them legi-
ble, e.g. type plate, identification marking for fluid connec-
tions.
• Only carry out work on the fitting if the following require-
ments are met:
– System is empty
– System has been flushed
– System is depressurized
– System has cooled down
– System is secured against being switched back on
again
• Do not make any modifications to the device.
2.3 Hazardous media
• When handling hazardous media (e.g. hot, flammable,
explosive, toxic, hazardous to health or the environment),
observe the safety regulations for the handling of haz-
ardous substances.
• Use personal protective equipment when carrying out any
work on the fitting.
• Collect leaking pumped liquid and residues in a safe man-
ner and dispose of in accordance with environmental reg-
ulations.
4 MDM 902 BA-2017.09.21 EN 301 287

Layout and Function
3 Layout and Function
3.1 Type plate
Type MDM 902
ID.No. 212970
Top G 1/4ʹʹ
Bottom DN20 - G 1/4ʹʹ
PN 10 FA17-28992
Materials
PVC-U
PTFE
1
6
2
3
4
5
Fig. 1 Type plate (example)
1 Fitting type
2 ID number
3 Internal thread diameter, upper part
4 Nominal diameter / internal thread diameter, bottom section
5 Nominal pressure
6 Materials
Fitting types
• MDM 902
3.2 Description
The fitting is a diaphragm pressure gauge guard The fitting is
mounted with the bottom section facing the pressurized pipe
carrying the medium. The pressure gauge is mounted on the
upper part. The separation diaphragm transmits the media
pressure to the pressure gauge via a transmitter fluid.
Separation diaphragm:
• EPDM diagram, PTFE coated on the medium side
Mounting position:
•any
• Pressure gauge preferably upright
On request the pressure gauge can be pre-assembled. The
version of the pressure gauges is described on the data sheet
(→Data sheet).
3.3 Layout
2
3
4
1
Fig. 2 Layout
1 Pressure gauge connection
2 Upper part
3 Separation diaphragm
4 bottom section
301 287 BA-2017.09.21 EN MDM 902 5

Transport, Storage and Disposal
4 Transport, Storage and Disposal
4.1 Unpacking and inspection on delivery
1. Unpack the fitting when received and inspect it for transport
damage.
2. Report any transport damage to the manufacturer immedi-
ately.
3. Ensure that the information on the type plate agrees with
the order/design data.
4. For immediate installation, dispose of packaging material
according to local regulations.
– For later installation, leave the fitting in the original
packaging.
4.2 Transportation
1. As far as possible, transport the fitting (incl. pressure
gauge) in the original packaging.
2. Lift fitting manually for transport. For weight specifications
(→Data sheet).
4.3 Storage
NOTE
Material damage due to inappropriate storage!
Store the fitting properly.
1. Make sure the storage room meets the following condi-
tions:
–Dry
– Frost-free
– Vibration-free
– Not in direct sunlight
– Storage temperature +10 °C to +60 °C
2. As far as possible, store the fitting in the original packaging.
4.4 Disposal
Plastic parts can be contaminated by poisonous or radioac-
tive media to such an extent that cleaning will not be suffi-
cient.
WARNING
Risk of poisoning and environmental damage from
medium.
Use personal protective equipment when carrying out any
work on the fitting.
Before disposing of the fitting:
– Collect escaping medium and dispose separately
according to local regulations.
– Neutralize residues of medium in the fitting.
Remove plastic parts and dispose of them in accordance
with local regulations.
Dispose of fitting in accordance with local regulations.
6 MDM 902 BA-2017.09.21 EN 301 287

Installation and connection
5 Installation and connection
5.1 Preparing for installation
5.1.1 Check operating conditions
1. Ensurethedesignofthefitting is consistent with the pur-
pose intended:
– Materials used (→Type plate).
–Medium(→Order and design data).
2. Ensure the required operating conditions are met:
– Resistance of the materials of the body, separation
diaphragm and seals to the medium (→Resistance
list).
– Media temperature (→Data sheet).
– Operating pressure (→Data sheet).
3. Consult with the manufacturer regarding any other use of
the device.
5.1.2 Check the installed condition of the fitting
Check the installed condition of the fitting and depending
on the situation proceed as follows:
– Fitting not filled with the transmitter fluid, pressure
gauge not fitted: Install fitting (→5.3 Installing the
fitting, Page 7 ).
–OR–
–Fittingfilled with the transmitter fluid, pressure gauge
fitted: Installing fittinginpipe(→5.4 Installing fitting in
pipe, Page 8 ).
5.2 Planning pipelines
WARNING
Risk of poisoning and environmental damage from
medium.
Leaks due to impermissible pipework forces.
Ensure that the fitting is not subject to any pulling or thrust-
ing forces or bending moments.
1. Plan pipes safely:
– No pulling or thrusting forces
– No bending moments
– Adjust for changes in length due to temperature
changes (compensators, expansion shanks)
–Optionalflow direction
– Optional installation position and direction
2. Dimensions (→Data sheet).
5.3 Installing the fitting
Before installation in the pipeline, the fitting must be filled
and the pressure gauge must be filled and mounted.
Follow the section drawing for assembly (→9.5 Sectional
drawing, Page 12).
Use the recommended transmitter fluid (→9.3 Transmitter
fluid, Page 12).
5.3.1 Fill the fitting
1. Fill the upper part (2) with transmitter fluid (4), excluding
any air bubbles.
2. Insert the gasket (5) into the upper part (2).
The fitting must be filled and prepared for assembly to the
pressure gauge.
5.3.2 Installing and filling the pressure gauge
The fitting must be filled
The compressed air supply must be available
NOTE
Damage to the separation diaphragm due to lack of trans-
mitter fluid!
Before commissioning, make sure that the fitting is suffi-
ciently filled with transmitter fluid.
NOTE
Damage to the separation diaphragm due to compressed
air!
Apply compressed air to the fitting only for very short peri-
ods of time. When doing so, do not exceed the permissible
pressure of the pressure gauge that is used.
1. Screw the pressure gauge (1) clockwise into the upper
part (2) (→9.4 Tightening torques, Page 12).
2. Rotate the fitting until the pressure gauge (1) is facing ver-
tically downwards.
3. Connect the compressed air supply to the bottom sec-
tion (6).
4. Switch on the compressed air supply and apply com-
pressed air to the fitting for short periods of time.
The transmitter fluid is pushed into the pressure gauge.
5. Switch off the compressed air supply and carefully detach
it from the fitting.
6. Rotate the fitting until the pressure gauge (1) is in the
upright position.
7. Unscrew the pressure gauge (1) from the upper part (2).
301 287 BA-2017.09.21 EN MDM 902 7

Installation and connection
8. Check the fill level in the upper part (2) and depending on
the situation proceed as follows:
–Ifthefill level is sufficient: continue with process step 9.
–OR–
–Ifthefill level is too low: Top up the transmitter fluid
(4) in the upper part (2). Repeat process steps 1 to 8
until there is sufficient transmitter fluid in the pressure
gauge.
9. Check the thread seal, and depending on the type of thread
proceed as follows:
– Imperial thread: Ensure that the gasket (3) seals the
pressure gauge.
–OR–
– Pipe thread and NPT thread: Wrap a maximum of 4
turns of sealing tape around the thread of the pressure
gauge (1).
10. Screw the pressure gauge (1) clockwise into the upper
part (2) (→9.4 Tightening torques, Page 12).
11. Ensure the pressure gauge (1) is zeroed.
The fitting is now ready for mounting on the pipeline.
5.4 Installing fittinginpipe
The pressure gauge must be mounted on the fitting.
The fitting must be filled with the transmitter fluid.
Thepressuregaugemustbefilled with the transmitter fluid.
WARNING
Risk of poisoning and environmental damage from
medium.
Leak due to faulty installation.
Installation work on the pipes should only be performed
by technicians who have been specially trained for the
pipework in question.
NOTE
Material damage due to contamination of the fitting!
Make sure no contamination reaches the fitting.
Flush the pipe with a neutral medium.
5.4.2 Connection with solvent welding/butt-weld
spigot ends
Use suitable solvent welding/fusion socket ends.
1. Prepare pipe ends according to connection type.
2. Align the fitting together with the pressure gauge, prefer-
ably upwards.
3. Adhesively apply or weld fitting with solvent welding/fusion
socket ends.
5.4.3 Connection with internal thread fixed
1. Prepare pipe ends according to connection type.
2. Check the thread seal on the bottom section of the fitting,
and depending on the type of thread proceed as follows:
– Imperial thread: Mount a gasket on the threaded con-
nector.
–OR–
– Pipe thread and NPT thread: Wrap a maximum of 4
turns of sealing tape around the thread of the threaded
connector.
3. Align the fitting together with the pressure gauge, prefer-
ably upwards.
4. Screw the fitting on to the threaded connector
(→9.4 Tightening torques, Page 12).
5.5 Performing the hydrostatic test
Pressure test using neutral medium, e.g. water.
1. Pressurize the fitting, ensuring
– Test pressure < permissible system pressure
– Test pressure < 1.5 PN
– Test pressure < PN + 5 bar
2. Check the fitting for leaks.
8 MDM 902 BA-2017.09.21 EN 301 287

Operation
6 Operation
6.1 Commissioning
The fittingmustbecorrectlymountedandfilled with trans-
mitter fluid.
The fitting must be correctly mounted in the pipeline.
WARNING
Risk of injury and poisoning due to medium spraying out.
Use personal protective equipment when carrying out any
work on the fitting.
NOTE
Damage to the separation diaphragm due to lack of trans-
mitter fluid!
Before commissioning, make sure that the fitting is suffi-
ciently filled with transmitter fluid.
After the first loads from pressure and operating tempera-
ture, check that the fitting is not leaking.
301 287 BA-2017.09.21 EN MDM 902 9

Maintenance
7 Maintenance
WARNING
Risk of injury and poisoning due to hazardous media liq-
uids!
Use personal protective equipment when carrying out any
work on the fitting.
7.1 Servicing
1. Visual and function check (every three months):
– Normal operating conditions unchanged
–Noleaks
– No unusual operating noises or vibrations
2. Clean fitting with a moist cloth if necessary.
7.2 Maintenance
WARNING
Risk of injury and poisoning due to hazardous or hot
media.
Use personal protective equipment when carrying out any
work on the fitting.
Safely collect the media and dispose of it in accordance
with environmental regulations.
If the separation diaphragm is defective, collect the trans-
mitter fluid with the admixture of medium, and dispose of it.
7.2.1 Removing fitting
1. Ensure that:
– System is empty
– System has been flushed
– System is depressurized
– System has cooled down
– System is secured against being switched back on
again
2. Remove fitting from the pipe.
3. Decontaminate fitting if required.
–Deadspaceinthefitting may still contain medium.
7.2.2 Changing the separation diaphragm
The fitting must be removed from the pipeline
When changing the separation diaphragm, refer to the sec-
tional drawing (→9.5 Sectional drawing, Page 12).
ASV Stübbe recommends a contact adhesive (such as Pat-
tex Kraftkleber) to bond the bottom section to the upper
part.
1. Unscrew the pressure gauge (1) anti-clockwise from the
upper part (2).
2. Carefully drain the upper part (2). Collect the transmitter
fluid (4) with the admixture of medium, and dispose of it.
3. Unscrew the upper part (2) anti-clockwise from the bottom
section (6).
4. Take the separation diaphragm (5) off the bottom sec-
tion (6) and dispose of it.
5. Insert a new separation diaphragm (4) into the bottom
section. When doing so, make sure that die side of the
diaphragm that is coated with PTFE and is slightly convex
faces towards the bottom section (4).
6. In the upper part (2), apply contact adhesive to the middle
turns of the internal thread. In so doing, apply the contact
adhesive as a ring of width approx. 2–3 mm.
7. Screw the upper part (2) to the bottom section (6).
(→9.4 Tightening torques, Page 12).
8. Install fitting (→5.3 Installing the fitting, Page 7 ).
9. Installing fitting in pipe (→5.4 Installing fittinginpipe,
Page 8 ).
7.2.3 Replacement parts and return
1. Have the following information ready to hand when order-
ing spare parts (→Type plate).
– Fitting type
– ID number
– Nominal pressure and diameter
– Body and seal material
2. Please complete and enclose the document of compliance
for returns (→www.asv-stuebbe.com/service/downloads).
3. Only use spare parts from ASV Stübbe.
10 MDM 902 BA-2017.09.21 EN 301 287

Troubleshooting
8 Troubleshooting
WARNING
Risk of injury and poisoning due to hazardous or hot
media.
Use personal protective equipment when carrying out any
work on the fitting.
Safely collect the media and dispose of it in accordance
with environmental regulations.
Consult with the manufacturer regarding faults which are not
identified in the following table, or which cannot be traced to
the indicated causes.
Error Possible cause Corrective action
Incorrect
Measurement value
Air bubbles in the transmitter
fluid
Check that the fitting is sufficiently filled with transmitter fluid, top it
up if necessary (→5.3 Installing the fitting, Page 7 ).
Medium in the
transmitter fluid
Defective separation
diaphragm
Changing the separation diaphragm (→7.2.2 Changing the
separation diaphragm, Page 10).
Medium is leaking Defective seal Check the seal at the connection to the pipeline and replace it if
necessary (→5.4 Installing fitting in pipe, Page 8 ).
Tab. 3 Troubleshooting
301 287 BA-2017.09.21 EN MDM 902 11

Appendix
9 Appendix
9.1 Technical specifications
Technical data (→Data sheet).
9.2 Dimensions
Dimensions (→Data sheet).
9.3 Transmitter fluid
ASV Stübbe recommends the following transmitter fluids
Transmitter fluid
Glycol (ethylene glycol)
Antifreeze (such as Glysantine or Aral Antifreeze)
Demineralized water*
Tab. 4 Transmitter fluid
*) when used in a potable water area
9.4 Tightening torques
Description Torque
Pressure gauge hand-tight, maximal 15 Nm
Upper part 30 Nm
bottom section hand-tight
Tab. 5 Tightening torques
9.5 Sectional drawing
2
3
4
5
6
1
Fig. 3 Sectional drawing
1 Pressure gauge
2 Upper part
3 Gasket
4 Transmitter fluid
5 Separation diaphragm
6 bottom section
12 MDM 902 BA-2017.09.21 EN 301 287
Table of contents
Other Stübbe Measuring Instrument manuals
Popular Measuring Instrument manuals by other brands
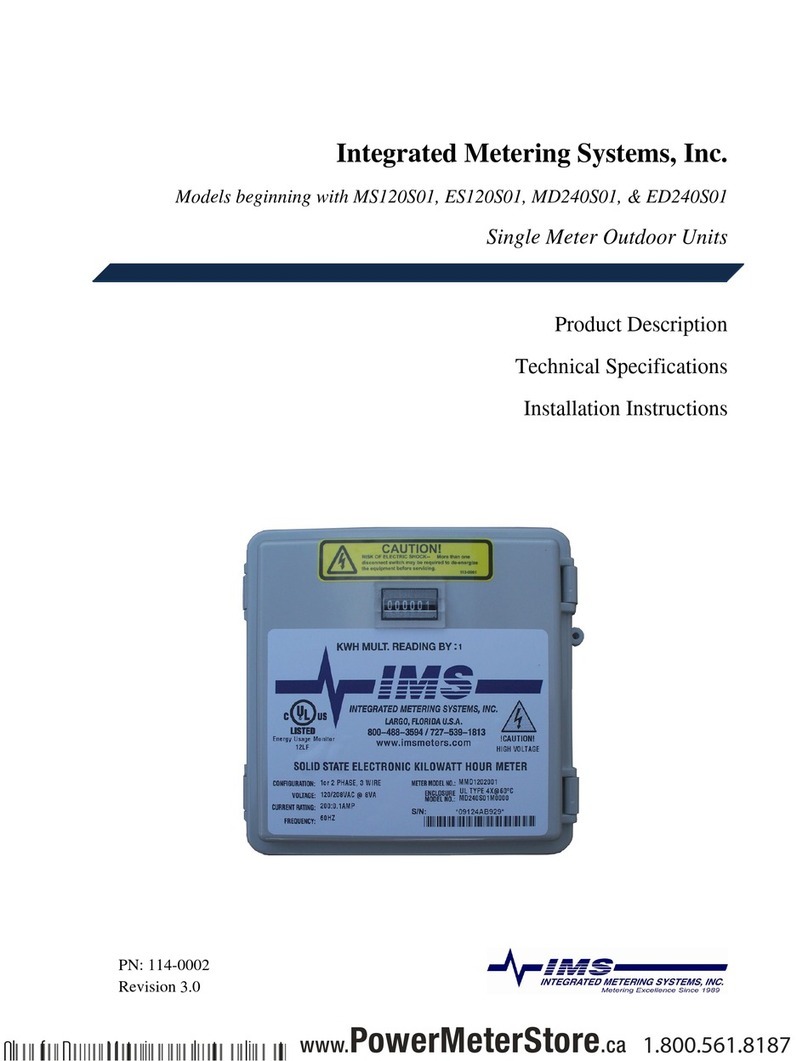
Integrated Meterting Systems
Integrated Meterting Systems MS120S01 Technical specifications and installation instructions
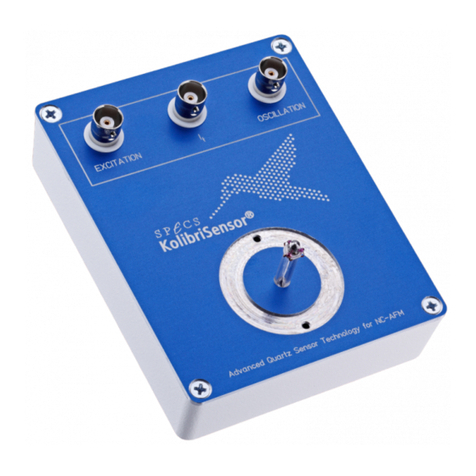
SPECS
SPECS KolibriSensor user manual
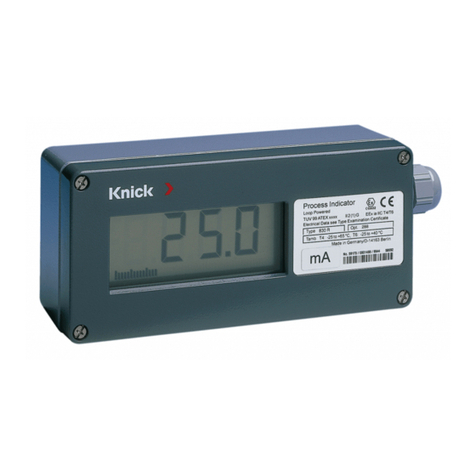
Knick
Knick 830 R manual
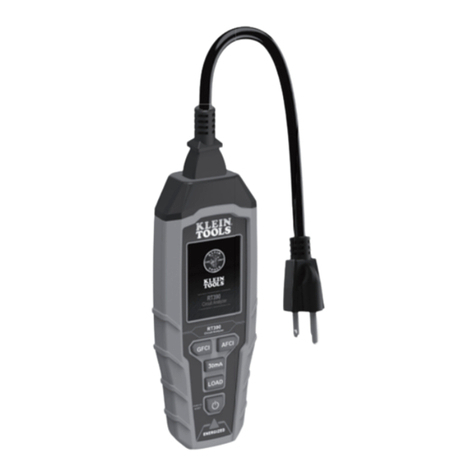
Klein Tools
Klein Tools RT390 instruction manual

Niigata seiki
Niigata seiki GVC Series instruction manual
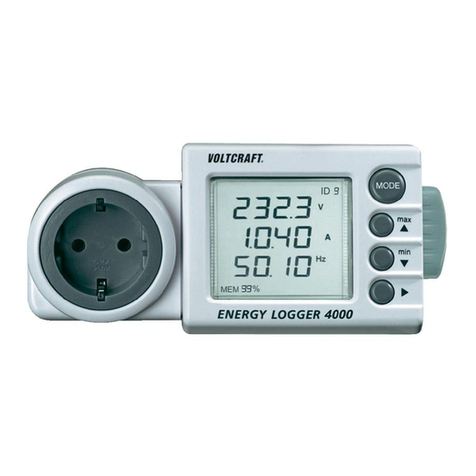
VOLTCRAFT
VOLTCRAFT Energy Logger 4000 operating instructions