STATUS SCIENTIFIC CONTROLS FGD4 User manual

STATUS SCIENTIFIC CONTROLS
Issue:
5
Date:
21/1/19
Firmware:
V1.0.7
Installation, Commissioning &
Routine Gas Testing Manual
Gas Detector
Type FGD4


Declaration of Conformity
We declare that, on the date the equipment accompanied by this declaration is placed on the market, the equipment conforms with all
technical and regulatory requirements of the directives listed below.
Description of Equipment:
The FGD4 Series of Fixed Gas Detectors for the detection of Oxygen, Toxic or Flammable gases.
Non-certified apparatus for safe area use only.
2004/108/EC –Electromagnetic Compatibility
Harmonised Standards Used:
EN50270:2006 Electromagnetic compatibility - Electrical apparatus for the detection and measurement of combustible gases, toxic gases
or oxygen. (Performance criterion ‘C’ )
EN61000-6-2:2005 Electromagnetic compatibility. Generic standards. Immunity standard for industrial environments.
EN61000-6-4:2007 Electromagnetic compatibility. Generic emission standard. Industrial environment.
2006/95/EC –Low Voltage Directive (LVD)
Harmonised Standards Used:
EN 61010-1:2010 Safety requirements for electrical equipment for measurement, control, and laboratory use -- Part 1: General
requirements.
Place of Manufacture:
Mansfield, Nottinghamshire, UK.
ISO 9001:2015 Quality Management System:
Certificate No. GB93/1938
Authorised Signatory to this declaration, on behalf of the manufacturer:
Name: David Stuttard Title: Managing Director
Address: Status Scientific Controls Ltd, Hermitage Lane Industrial Estate, Kings Mill Way
Mansfield, Nottinghamshire, NG18 5ER, United Kingdom
Signature Date: 21/1/19


STATUS SCIENTIFIC CONTROLS
Installation, Commissioning & Routine Gas Testing
FGD4 Gas Detector
TD19/001
Issue:
5
Change Note:
1869
Page 4
CONTENTS
1. PACKAGE CONTENTS ......................................................................6
2. SCOPE OF THE MANUAL..................................................................6
3. DESCRIPTION....................................................................................7
3.1. GAS TYPES .................................................................................7
4. INSTALLATION ..................................................................................8
4.1. CABLE ENTRIES...........................................................................8
4.2. FGD4 CONNECTIONS...................................................................8
4.3. WIRING DETAILS..........................................................................9
4.3.1. FGD4 Toxic current sink ...................................................................... 9
4.3.2. FGD4 Toxic current source.................................................................. 9
4.3.3. FGD4 Infrared current sink................................................................. 10
4.3.4. FGD4 Infrared current source ............................................................ 10
5. COMMISSIONING.............................................................................11
5.1. APPLYING POWER......................................................................11
6. INITIAL GAS TESTING.....................................................................12
6.1. ZERO GAS.................................................................................12
6.2. TEST GAS .................................................................................14
6.2.1. Gas connection points........................................................................ 14
6.2.2. Sampling time..................................................................................... 14
6.2.3. Suggested calibration gas levels. ...................................................... 14
7. CALIBRATION..................................................................................15
7.1. SENSOR ZERO ..........................................................................15
7.2. SENSOR SPAN ..........................................................................16
7.3. CALIBRATION /CONFIGURATION KEYPAD.....................................17
7.4. MENU MODE SELECTION............................................................19
7.4.1. E : 1 –Sensor Zero............................................................................ 20
7.4.2. E : 2 –Sensor Span........................................................................... 20
7.4.3. E : 3 –Sensor Fsd.............................................................................. 20
7.4.4. E : 4 –Output Zero (4mA).................................................................. 20
7.4.5. E : 5 –Output Span (20mA)............................................................... 20
7.4.6. E : 8 –Factory restore........................................................................ 21
7.4.7. E : 9 –Engineer diagnostics .............................................................. 21
7.4.8. E : 17 –Sensor gain........................................................................... 22
7.4.9. E : 19 –Positive Zero Suppression.................................................... 23
7.4.10. E : 20 –Negative Zero Suppression.................................................. 23
7.4.11. E : 25 –Positive Zero Temperature Compensation .......................... 24
7.4.12. E : 34 –Positive Span Temperature Compensation ......................... 24
7.4.13. E : 35 –Negative Span Temperature Compensation........................ 24
7.4.14. E : 36 –Positive Zero Temperature Compensation .......................... 24
7.4.15. E : 77 –Firmware Version.................................................................. 24
8. CALIBRATION..................................................................................25
8.1. SENSOR CALIBRATION ...............................................................25
8.1.1. Sensor Zero........................................................................................ 25
8.1.2. Sensor Span....................................................................................... 26

STATUS SCIENTIFIC CONTROLS
Installation, Commissioning & Routine Gas Testing
FGD4 Gas Detector
TD19/001
Issue:
5
Change Note:
1869
Page 5
8.2. ANALOGUE OUTPUT CALIBRATION ..............................................27
8.2.1. Analogue Output Zero........................................................................ 28
8.2.2. Analogue Output Span....................................................................... 28
9. ROUTINE GAS TESTING..................................................................29
10. FUSES ..............................................................................................30
11. SPECIFICATION...............................................................................30
12. DIMENSIONS & MOUNTING DETAILS ............................................31

STATUS SCIENTIFIC CONTROLS
Installation, Commissioning & Routine Gas Testing
FGD4 Gas Detector
TD19/001
Issue:
5
Change Note:
1869
Page 6
1. PACKAGE CONTENTS
The FGD4 is supplied in a box containing the following items:-
Description
Stock
No
FGD4 Gas Detector
*
Installation manual
**
Calibration certificate
Optional:-
Weather guard
Calibration / Configuration Keypad
* Refer to www.status-scientific.com for Stock No’s for various gas types.
** The manual may be supplied on a CD
2. SCOPE OF THE MANUAL
This manual relates specifically to the version of the FGD4 gas detector fitted
with one of the following sensor types:-
•An Oxygen sensor.
Or
•An electrochemical Toxic sensor.
Or
•An Infrared sensor.

STATUS SCIENTIFIC CONTROLS
Installation, Commissioning & Routine Gas Testing
FGD4 Gas Detector
TD19/001
Issue:
5
Change Note:
1869
Page 7
3. DESCRIPTION
The FGD4 is a fixed gas detector for use in non-explosive atmospheres.
The unit comprises an instrument housing having one cable gland entry.
The housing containing the gas sensor has an M27 thread and is screwed
into the bottom of the unit. The sensor housing itself is a certified component
and must not be removed in service.
The main electrical features of the unit are:-
•Power supply –8 to 24 volts dc (non-intrinsically safe)
•Loop powered 4 to 20mA dc
•Gland entry threads available –20mm, ½” or ¾” NPT
3.1. Gas types
Versions of the FGD4 Oxygen Toxic are available for detection of gases,
fitted with any of the following sensor types:-
•O2, H2S, CO, SO2 and CO2

STATUS SCIENTIFIC CONTROLS
Installation, Commissioning & Routine Gas Testing
FGD4 Gas Detector
TD19/001
Issue:
5
Change Note:
1869
Page 8
4. INSTALLATION
To ensure effective gas detection, the FGD4 must be located at a height
appropriate to the density of the target gas relative to air.
4.1. Cable entries
The cable entry threads is 20mm female.
The FGD4 enclosure is manufactured from injection moulded poly carbonate
and as such care should taken not to over-tighten the gland.
4.2. FGD4 connections
FGD4 Oxygen / Toxic Infrared
Sensor
Keypad Zero
Span
+Ve
-Ve
Sensor
Keypad
Zero Span
4/20mA
0V Supply
+Ve Power

STATUS SCIENTIFIC CONTROLS
Installation, Commissioning & Routine Gas Testing
FGD4 Gas Detector
TD19/001
Issue:
5
Change Note:
1869
Page 9
4.3. Wiring details
The infrared gas detector is a 4 to 20 mA loop powered device that operates
from a supply of 8 –24 volt dc supply and as such only requires two wires.
4.3.1. FGD4 Toxic current sink
4.3.2. FGD4 Toxic current source
Sensor
Keypad Zero
Span
0V
+24 Vdc
I4- 20mA
Fig4b
0V
+24 Vdc
I( 4-20mA)
Fig4a
Sensor
Keypad Zero
Span
+Ve
-Ve

STATUS SCIENTIFIC CONTROLS
Installation, Commissioning & Routine Gas Testing
FGD4 Gas Detector
TD19/001
Issue:
5
Change Note:
1869
Page 10
4.3.3. FGD4 Infrared current sink
Sensor
Keypad
Zero Span
0V
I( 4
-20mA)
+24Vdc
Fig4c
4.3.4. FGD4 Infrared current source
Sensor
Keypad
Zero Span
0V
+24 Vdc
I4- 20mA
Fig4d

STATUS SCIENTIFIC CONTROLS
Installation, Commissioning & Routine Gas Testing
FGD4 Gas Detector
TD19/001
Issue:
5
Change Note:
1869
Page 11
5. COMMISSIONING
Following completion of the installation:-
Replace the cover, taking care not to trap the wiring and fix with the 4 allen
screws, do not over tighten.
5.1. Applying power
Once the installation is complete and the covers are secure then power can
be applied. The power source should be between 12 and 24 volts dc.

STATUS SCIENTIFIC CONTROLS
Installation, Commissioning & Routine Gas Testing
FGD4 Gas Detector
TD19/001
Issue:
5
Change Note:
1869
Page 12
6. INITIAL GAS TESTING
FGD4 units are factory calibrated as detailed on the calibration certificate
supplied with the instrument. However, it is always advisable after installation
to confirm that the instrument reads zero with no gas present and responds
accurately when presented with an appropriate concentration of the target
gas.
The FGD4 sensor should be allowed to stabilise for the period specified on
the associated calibration certificate before attempting to check the zero
setting and gas response.
6.1. Zero gas
With no gas present check that the associated control panel display reads
zero.
a) If the instrument reads zero then no adjustment is required and gas
response testing may now be carried out as described in Section 6.2.
b) If the instrument does not read zero then adjustment of the zero setting
is required as described in Section 8.1.1. - Sensor Zero.
c) If the analogue signal is connected to an associated control panel,
confirm that when the FGD4 display reads zero, the control panel
display also reads zero or, adjust as necessary in accordance with the
control panel manufacturers’ instructions.
* Note –If there is the possibility of a background gas being present then
zeroing of the detector should be carried out using a test gas cylinder of air in
nitrogen.

STATUS SCIENTIFIC CONTROLS
Installation, Commissioning & Routine Gas Testing
FGD4 Gas Detector
TD19/001
Issue:
5
Change Note:
1869
Page 13
Figure 7 –Arrangement for Application of a Certified Test Gas
Certified Test Gas
Cylinder
Flow Regulator
(1 Litre/min)

STATUS SCIENTIFIC CONTROLS
Installation, Commissioning & Routine Gas Testing
FGD4 Gas Detector
TD19/001
Issue:
5
Change Note:
1869
Page 14
6.2. Test gas
Figure 7 shows a typical arrangement for the application of a certified test
gas.
The purpose of the test gas response check is to confirm that that the
reading on the instrument corresponds with the test gas concentration.
a) If the associated control panel reads correctly then no adjustment is
required.
b) If the above checks are satisfactory then the installation is now
complete.
c) If the instrument does not read correctly then adjustment of the sensor
span setting is required as described in Section 8.1.2. - Sensor Span.
6.2.1. Gas connection points
Certified test gas is applied directly to the FGD4 via the appropriate
sampling/calibration adaptor.
6.2.2. Sampling time
Apply the test gas and allow a sufficient time for the sample to reach the gas
detector. The response time will vary according to the length of the sampling
tube.
6.2.3. Suggested calibration gas levels.
Oxygen sensor:
Zero N2.
Span 20.9 %v/v oxygen balance nitrogen.
Toxic sensor
Zero Gas free air, must have oxygen.
Span 50 % of measuring range (FSD).
Infrared sensor:
Zero N2.
Span 50 % of measuring range (FSD).

STATUS SCIENTIFIC CONTROLS
Installation, Commissioning & Routine Gas Testing
FGD4 Gas Detector
TD19/001
Issue:
5
Change Note:
1869
Page 15
7. CALIBRATION
Calibration of the sensor can be carried out by using the buttons on the circuit board
as seen in Fig1 and Fig 2.
These buttons only work when the FGD4 Infrared has been powered for a minimum of
10 minutes.
7.1. Sensor Zero
Infrared Oxygen / Toxic
Ensure the sensor is in a zero-gas environment.
Note: Where a purging gas has to be applied, use a flow rate of
between 300 and 1000 cc/min. Allow sufficient time for the
sensor to respond.
Press the Zero button zero and hold for a minimum of 5 seconds
to zero the sensor.
Sensor
Keypad Zero
Span
Sensor
Keypad
Zero Span

STATUS SCIENTIFIC CONTROLS
Installation, Commissioning & Routine Gas Testing
FGD4 Gas Detector
TD19/001
Issue:
5
Change Note:
1869
Page 16
7.2. Sensor Span
Always zero the sensor prior to performing a span operation.
Infrared Oxygen / Toxic
Infrared Oxygen / Toxic
Infrared Oxygen / Toxic
Apply a known concentration of gas (applicable to sensor type) at a
flow rate of between 300 and 1000 cc/min. Allow time for the sensor
to respond.
Press the Span button span and hold for a minimum of 5 seconds
to span the sensor.
Turn off and disconnect the calibration gas.
Note: The calibration gas level must match with the level stored in
the instrument. If the gas level is does not match then the
keypad must be used to set the correct gas level.
Sensor
Keypad Zero
Span
Sensor
Keypad
Zero Span

STATUS SCIENTIFIC CONTROLS
Installation, Commissioning & Routine Gas Testing
FGD4 Gas Detector
TD19/001
Issue:
5
Change Note:
1869
Page 17
7.3. Calibration / Configuration Keypad
The FGD4 sensor can be calibrated via a purpose designed keypad. The
keypad allows the user to carry out the following:
1) calibrate the sensor.
2) calibrate the 4 to 20 mA loop.
3) View the current gas level.
4) View the sensor raw data for diagnostic purposes.
Connect the keypad into the FGD4 as shown below:
The display will give the following messages:
SSCL Company
- - - -
88:88 Segment test
SSCL Manufacturer
1.0.3 Firmware version
- - - -
0.0 Gas reading
Note: if the display is continually showing - - - - then the instrument is not
communicating with the keypad.

STATUS SCIENTIFIC CONTROLS
Installation, Commissioning & Routine Gas Testing
FGD4 Gas Detector
TD19/001
Issue:
5
Change Note:
1869
Page 18
The menu system featured within the keypad calibration unit allows all
calibration and configuration activities to be performed.
MENU
The keypad has the following functionality:
Button
Function
Alternate Function
MENU
MENU
Open / Close Menu
Password
UP
Next / Increase
1
DOWN
Previous / Decrease
2
ENTER
Accept selection
3
This section of the manual discusses how the available menu options can be
accessed, how the associated parameter may be changed via the selected
menu option and what effect the change to the parameter has on the
operation of the FGD4 Infrared gas detector.
Note: It is important that that the FGD4 is correctly configured for the sensor
in use, prior to performing any feature available in the menu system.

STATUS SCIENTIFIC CONTROLS
Installation, Commissioning & Routine Gas Testing
FGD4 Gas Detector
TD19/001
Issue:
5
Change Note:
1869
Page 19
7.4. Menu Mode Selection
The external Calibration / Configuration Keypad is used in its simplest form to calibrate
the sensor for zero or gas drift.
It may also be used to configure the FGD4.
The following features are available via the Calibration / Configuration Keypad menu
system: -
Menu Option
Notes
E : 1 –Sensor Zero
E : 2 –Sensor Span
E : 3 –Sensor FSD
E : 4 –Output Zero (4mA)
E : 5 –Output Span (20mA)
E : 8 –Sensor restore
Oxygen / Toxic sensor
E : 9 –Diagnostics
E : 17 –Sensor Gain
Toxic sensor
E : 19 –Positive zero suppression
Toxic sensor
E : 20 –Negative zero suppression
Toxic sensor
E : 25 –Zero temperature compensation +ve
Toxic sensor
E : 34 –Span temperature compensation +ve
Toxic sensor
E : 35 –Span temperature compensation -ve
Toxic sensor
E : 36 –Zero temperature compensation -ve
Toxic sensor
E : 77 –Firmware version
The menu options are selected as follows:
•Press the MENU button, E: 1 appears on the display.
•Press or until the required menu option is displayed, see
following options.
•Press to select the menu option.
•To exit the menu press MENU.
While the instrument is in menu mode –any data displayed on the screen will alternate
between the menu number and the reading.
Table of contents
Other STATUS SCIENTIFIC CONTROLS Gas Detector manuals
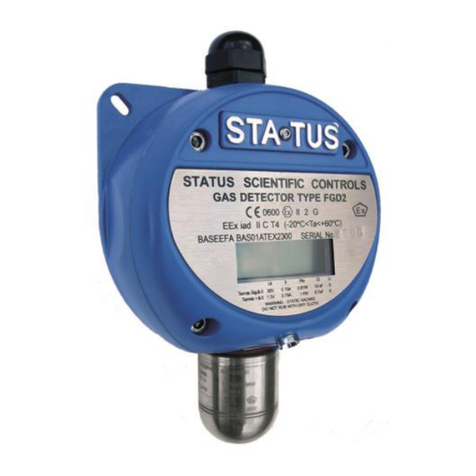
STATUS SCIENTIFIC CONTROLS
STATUS SCIENTIFIC CONTROLS FGD2 User manual

STATUS SCIENTIFIC CONTROLS
STATUS SCIENTIFIC CONTROLS FGD10B Series Guide

STATUS SCIENTIFIC CONTROLS
STATUS SCIENTIFIC CONTROLS FGD10A-M User manual
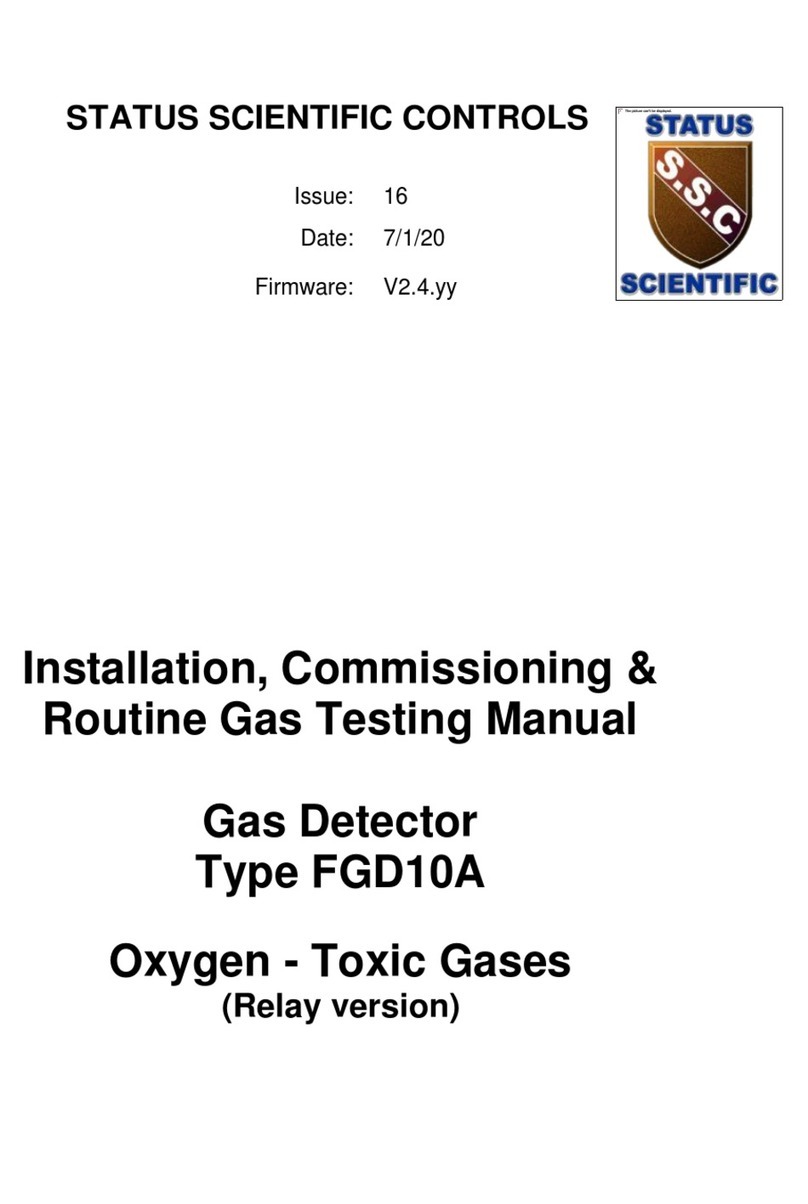
STATUS SCIENTIFIC CONTROLS
STATUS SCIENTIFIC CONTROLS FGD10A User manual
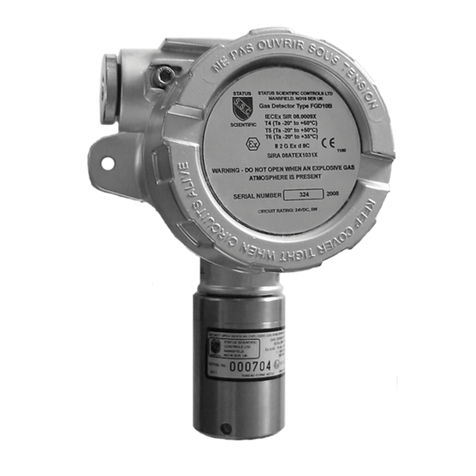
STATUS SCIENTIFIC CONTROLS
STATUS SCIENTIFIC CONTROLS FGD10B Series User manual
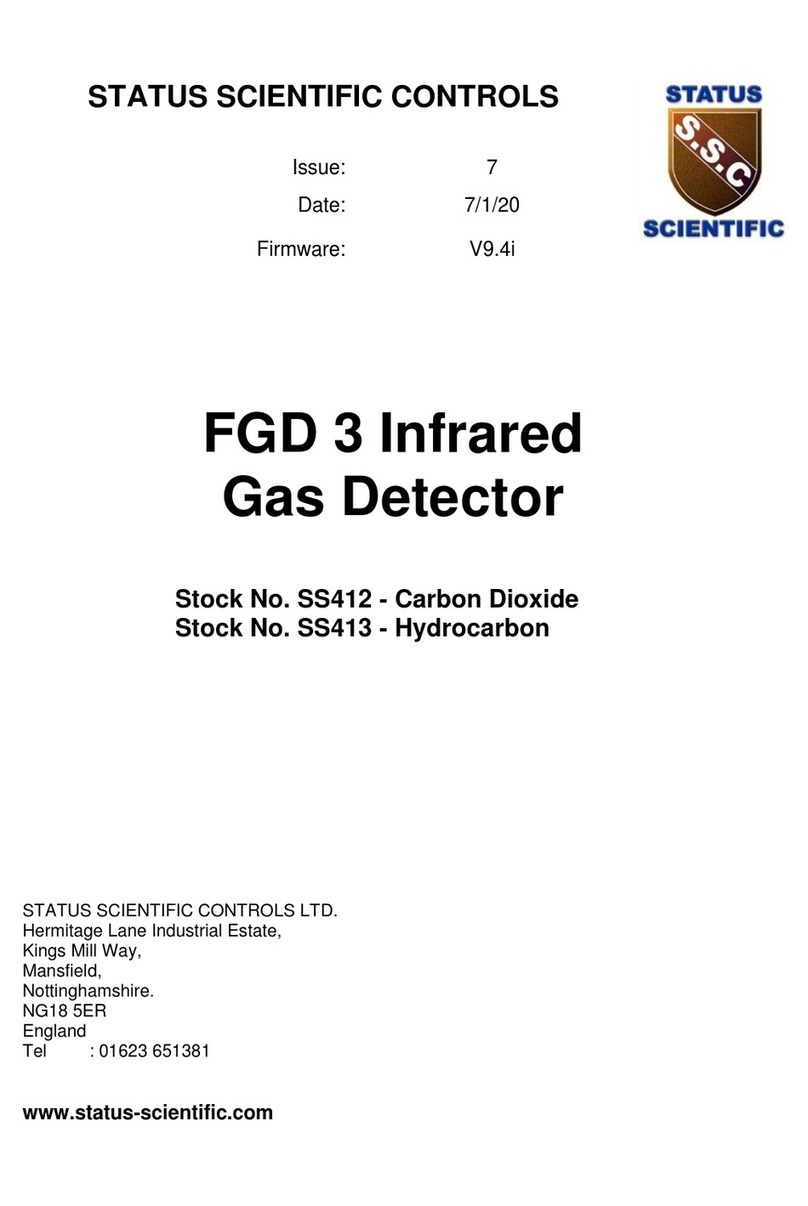
STATUS SCIENTIFIC CONTROLS
STATUS SCIENTIFIC CONTROLS FGD 3 Series User manual