StoneAge PROPOSITIONER PROP-DBP User manual

PL 688 REV D
(08/2020)
PROPOSITIONER™
(PROP-DBP) ACCESSORY
USER MANUAL

2866-795-1586 • WWW.STONEAGETOOLS.COM
SUB-ASSEMBLY COLOR CODE DIAGRAM..................................................... 4
MANUFACTURER’S INFORMATION ................................................................ 5
SPECIFICATIONS ........................................................................................ 5
DESCRIPTION OF EQUIPMENT AND INTENDED USE ................................... 5
KEY FEATURES........................................................................................... 5
EC DECLARATION OF CONFORMITY........................................................... 6
WARNING AND SAFETY INSTRUCTIONS ....................................................... 8
OPERATOR TRAINING................................................................................. 8
PERSONAL PROTECTIVE EQUIPMENT REQUIREMENTS.............................. 8
SAFETY LABEL DEFINITIONS....................................................................... 8
PRE-RUN SAFETY CHECK .......................................................................... 9
PACKAGE CONTENTS - OVERVIEW ........................................................ 10
PROP-DBP-XXX PACKAGE CONTENTS ....................................................... 10
OPTIONAL EQUIPMENT .............................................................................. 11
SUB-ASSEMBLY 1 (ABX-PRO, ROLLERS, COLLET BLOCK, GUIDE TUBE) ... 12
CHANGE ROLLERS IN THE ABX-PRO TRACTOR........................................... 12
INSTALL COLLET BLOCK............................................................................. 13
INSTALL ANGLED GUIDE TUBE .................................................................... 14
INSTALL CAMERA AND CAMERA MOUNT ON GUIDE TUBE .......................... 15
SUB-ASSEMBLY 2 (LINEAR DRIVE HANDLE).................................................. 15
REPLACE THE ADJUSTABLE HANDLE ON THE LINEAR DRIVE ...................... 15
SUB-ASSEMBLY 3 (RAIL MOUNT, SNOUT, AND HIGH PRESSURE HOSE)..... 16
INSTALL BANSHEE TOOL ............................................................................ 16
INSTALL SNOUT ONTO RAIL MOUNT ........................................................... 16
LOADING LANCE AND TOOL THROUGH SNOUT .......................................... 16
SUB-ASSEMBLY 4 (CONTROL BOX AND CAMERA) ....................................... 17
CONNECT THE PNEUMATIC LINES TO THE CONTROL BOX ........................ 17
CONNECT THE MONITOR MOUNT, MONITOR, AND POWER PACK ............... 18
SUB-ASSEMBLY 5 (OPTIONAL DUMP SYSTEM SET-UP) ............................... 19
CONNECT FOOT CONTROLLED DUMP ....................................................... 19
CONNECT HAND CONTROLLED DUMP....................................................... 19
TABLE OF CONTENTS
ASSEMBLE THESE BEFORE
“POSITIONER SET-UP INSIDE
DOMED BUNDLE”

3
866-795-1586 • WWW.STONEAGETOOLS.COM
POSITIONER SET-UP INSIDE DOMED BUNDLE ............................................. 20
INSTALL SPIDER PLATE ONTO TUBE FACE ................................................. 20
INSTALL ROTARY DRIVE AND DRIVE RAIL ONTO SPIDER PLATE ................. 22
INSTALL LINEAR DRIVE AND RAIL PLUG ON DRIVE RAIL ............................. 23
INSTALL SUB-ASSEMBLY 1 ON THE LINEAR DRIVE..................................... 24
SET THE DRIVE RAIL AND LINEAR DRIVE IN PLACE..................................... 25
SET-UP DIMENSIONS FOR A 69” (1753 mm) TUBE FACE.............................. 26
CONTROL BOX CONNECTIONS TO POSITIONER.......................................... 28
AIR LINE CONNECTIONS FROM CONTROL BOX TO POSITIONER................ 28
CAMERA CONNECTION FROM POWER PACK TO POSITIONER.................... 28
RAIL MOUNT INSTALLATION ......................................................................... 29
ICM (TOP MOUNT) RAIL MOUNT TO MAN WAY FLANGE .............................. 29
DELTA T (SIDE MOUNT) RAIL MOUNT TO MAN WAY FLANGE....................... 30
HIGH PRESSURE HOSE AND SNOUT INSTALLATION.................................... 31
LOADING THE H.P. HOSE INTO THE ABX-PRO HOSE TRACTOR.................. 31
INSTALL THE SNOUT ONTO THE ABX-PRO HOSE TRACTOR ...................... 31
OPERATION...................................................................................................... 32
CONTROL BOX SETTINGS........................................................................... 32
CONTROL PANEL OPERATION..................................................................... 32
TEST RUN AND RUN PROCEDURES ............................................................ 33
MAINTENANCE AND TROUBLESHOOTING .................................................... 34
STORAGE, TRANSPORTATION, AND HANDLING ........................................... 34
PART DIAGRAMS ............................................................................................. 35
PART DIAGRAMS TABLE OF CONTENTS ...................................................... 35
TERMS AND CONDITIONS AND WARRANTY INFORMATION ........................ 52
TABLE OF CONTENTS

4866-795-1586 • WWW.STONEAGETOOLS.COM
SUB-ASSEMBLY COLOR CODE DIAGRAM
REVIEW THIS BEFORE STARTING ASSEMBLY:
THE FIVE COLOR CODED SUB-ASSEMBLIES NEED TO BE ASSEMBLED BEFORE
CONNECTING EVERYTHING TO THE DOMED BUNDLE. THE COLORS ARE ASSOCIATED TO
THEIR RESPECTIVE SECTIONS IN THIS MANUAL. THE HOSE CONNECTIONS WILL BE MADE
IN A LATER SECTIONS OF THIS MANUAL
SUB-ASSEMBLY 3
(RAIL MOUNT, SNOUT, AND TOOL)
SUB-ASSEMBLY 2
(LINEAR DRIVE HANDLE)
SUB-ASSEMBLY 1
(ABX-PRO, ROLLERS, COLLET
BLOCK, GUIDE TUBE)
*INDIVIDUAL COMPONENTS
TO BE INSTALLED LATER IN
THE MAIN INSTALLATION
SUB-ASSEMBLY 5
(OPTIONAL DUMP
SYSTEM SET-UP)
SUB-ASSEMBLY 4
(CONTROL BOX AND CAMERA)
*Spider
Mount
*Rotary
Drive
*Rotary Drive
Rail

5
866-795-1586 • WWW.STONEAGETOOLS.COM
MANUFACTURER’S INFORMATION
StoneAge Inc.
466 S. Skylane Drive
Durango, CO 81303, USA
Phone: 970-259-2869
Toll Free: 866-795-1586
www.stoneagetools.com
StoneAge NL
Reedijk 7Q
3274 KE Heinenoord
Netherlands
(+31) (0) 85 902 73 70
This manual must be used in accordance with all applicable national laws. The manual shall be regarded as a part of the machine and shall
be kept for reference until the nal dismantling of the machine, as dened by applicable national law(s). Please see separate User Manuals for
the ABX-PRO Hose Tractor and PROP-300 Positioner.
For detailed up to date information on these components.
https://www.stoneagetools.com/manuals
DESCRIPTION OF EQUIPMENT AND INTENDED USE
The Domed Bundle Accessory for the ProPositioner can be
vertically mounted to a variety of heat exchanger tube bundles
and has pneumatic powered linear and rotary drives. It is intended
to be used with AUTOBOX®(ABX-PRO) TRACTOR, Control Box
(CB-PROP-P), and ProPositioner (PROP-300).
The ProPositioner has been designed to provide a lightweight,
low cost, entry level, option for contractors just starting out with
hands free waterblasting equipment.
KEY FEATURES:
• Modular system designed for portability and easy assembly
• Quick install with minimal tools
• Utilizes 2.5 in. (64 mm) aluminum slotted box rail
• Adjustable handles and Push-to-Connect air connections
allow for quick adjustments.
SPECIFICATIONS
PROP-DBP POSITIONER Imperial Metric
Weights ABX-PRO Tractor, Guide Tube/Collet
Block, and 12in Guide Tube 27 lbs 12.2 kg
Spider Plate Mount 6 lbs 2.7 kg
Linear Drive 11.5 lbs 5.2 kg
Rotary Drive 32 lbs 14.5 kg
Dimensions Standard Slotted Rail 2.5 x 2.5 x 45 in. 64 x 64 x 1219 mm
Slotted Rail with extension 2.5 x 2.5 x 61 in. 64 x 64 x 1549 mm
Spider Plate Mount 11 x 7 x 4 in. 279 x 178 x 102 mm
Linear Drive 13 x 8 x 6 in. 330 x 203 x 152 mm
Rotary Drive 8 x 11 x 9 in. 203 x 279 x 229 mm
Usable Exchanger Diameter Range
Options
60 , 69 , 84 in. or
96 in. with rail extension
1524 , 1753, 2134 mm or
2438 mm with rail extension
Power Camera System Input power requirements 100-240V AC 1.8A
ABX-PRO TRACTOR For detailed up to date information on these components.
https://www.stoneagetools.com/assets/pdf/manuals/ABX-PRO_manual.pdf
CB-PROP-X (-P or -S) For detailed up to date information on these components.
https://www.stoneagetools.com/assets/pdf/manuals/PROP-300_manual.pdf

6866-795-1586 • WWW.STONEAGETOOLS.COM
EC DECLARATION OF CONFORMITY
Manufacturer: StoneAge Incorporated
466 South Skylane Drive
Durango, CO 81303
USA
Authorized Representative: StoneAge Netherlands BV
Reedijk 7Q
3274 KE Heinenoord
Netherlands
Bob Van Wordragen, Operations Manager StoneAge NL
Declare that: ProPositioner for Domed Bundle (PROP-DBP) and Control Box (CB-PROP-P)
for high pressure water cleaning of system parts.
Is compliant with the following Directives and Standards:
Directive 2006/42/EC (Machinery Directive)
EN ISO 12100:2010 (E) Safety of machinery – General principles for design – Risk assessment and risk reduction
The Technical File for ProPositioner for Domed Bundle (PROP-DBP) and Control Box (CB-PROP-P) is maintained at:
StoneAge Incorporated, 466 South Skylane Drive, Durango, CO 81303, USA and was compiled by the Engineering Manager.
The Technical File is available through the Authorized Representative.
This Declaration of Conformity is issued under the exclusive responsibility of StoneAge Incorporated.
________________________________________ 11/01/2019
StoneAge Incorporated, Durango, CO, USA Date
Adam Markham, Engineering Manager, Robotics
NOTES

7
866-795-1586 • WWW.STONEAGETOOLS.COM
NOTES
PAGE LEFT BLANK INTENTIONALLY

8866-795-1586 • WWW.STONEAGETOOLS.COM
OPERATOR TRAINING
Managers, Supervisors, and Operators MUST be trained in Health
and Safety Awareness of High-pressure Water Jetting and hold
a copy the Water Jetting Association (WJA) Code of Practice, or
equivalent (see www.waterjetting.org.uk).
Operators MUST be trained to identify and understand all applicable
standards for the equipment supplied. Operators should be trained
in manual handling techniques to prevent bodily injury.
Operators MUST read, understand, and follow the Operational and
Training Requirements (Section 7.0) of WJTA-IMCA’s Recommended
Practices For The Use Of High-pressure Waterjetting Equipment, or
equivalent.
Operators MUST read, understand and follow the Warnings,
Safety Information, Assembly, Installation, Connection, Operation,
Transport, Handling, Storage, and Maintenance Instructions detailed
in this manual.
StoneAge has designed and manufactured this equipment
considering all hazards associated with its operation. StoneAge
assessed these risks and incorporated safety features in the design.
StoneAge WILL NOT accept responsibility for the results of misuse.
IT IS THE RESPONSIBILITY OF THE INSTALLER/OPERATOR
to conduct a job specic risk assessment prior to use. Job specic
risk assessment MUST be repeated for each different set up,
material, and location.
The risk assessment MUST conform to the Health and Safety at
Work Act 1974 and other relevant Health and Safety legislation.
The risk assessment MUST consider potential material or substance
hazards including:
• Aerosols
• Biological and microbiological (viral or bacterial) agents
• Combustible materials
• Dusts
• Explosion
• Fibers
• Flammable substances
• Fluids
• Fumes
• Gases
• Mists
• Oxidizing Agents
WARNING AND SAFETY INSTRUCTIONS
PERSONAL PROTECTIVE EQUIPMENT REQUIREMENTS
Use of Personal Protective Equipment (PPE) is dependent on
the working pressure of water and the cleaning application.
Managers, Supervisors, and Operators MUST carry out a job
specic risk assessment to dene the exact requirements for PPE.
See Protective Equipment for Personnel (Section 6) of WJTA-
IMCA’s Recommended Practices For The Use Of High-pressure
Waterjetting Equipment for additional information.
Hygiene - Operators are advised to wash thoroughly after all
waterjetting operations to remove any waterblast residue which may
contain traces of harmful substances.
First aid provision - users MUST be provided with suitable rst aid
facilities at the operation site.
PPE may include:
• Eye protection: Full face visor
• Foot protection: Kevlar® brand or steel toe capped,
waterproof, non-slip safety boots
• Hand protection: Waterproof gloves
• Ear protection: Ear protection for a minimum of 85 dBA
• Head protection: Hard hat that accepts a full face visor and
ear protection
• Body protection: Multi-layer waterproof clothing approved for
waterjetting
• Hose protection: Hose shroud
• Respiratory protection: May be required; refer to job specic
risk assessment

9
866-795-1586 • WWW.STONEAGETOOLS.COM
WARNING
Operations with this equipment can be potentially hazardous. Caution
MUST be exercised prior to and during machine and water jet tool
use. Please read and follow all of these instructions, in addition to
the guidelines in the WJTA Recommended Practices handbook,
available online at www.wjta.org. Deviating from safety instructions and
recommended practices can lead to severe injury and/or death.
• Do not exceed the maximum operating pressure specied for
any component in a system.
• The immediate work area MUST be marked off to keep out
untrained persons.
• Inspect the equipment for visible signs of deterioration, damage,
and improper assembly. Do not operate if damaged, until
repaired.
• Make sure all threaded connections are tight and free of leaks.
• Users of the ProPositioner PROP-DBP and accessories MUST
be trained and/or experienced in the use and application of
high-pressure technology and cleaning, as well as all associated
safety measures, according to the WJTA Recommended
Practices for the use of High-pressure Waterjetting Equipment.
• An anti-withdrawal device (back-out preventer) MUST be used
at all times. The back-out prevention device is the Hose Stop
Collet located within the Hose Guide Assembly. StoneAge
offers several different size Hose Stop Collets. The Collet Size
Reference guide is located on the top of the ABX-PRO Hose
Tractor.
• The Control Box should be located in a safe location where the
Operator has good visibility of the operation. The ProPositioner
PROP-DBP and Control Box MUST be supervised at all times
and should never be left unattended.
• Always de-energize the system before servicing or replacing any
parts. Failure to do so can result in severe injury and/or death.
• When moving the ProPositioner PROP-DBP and accessories, lift
with care to prevent bodily injury.
HIGH-PRESSURE HOSE
• The ABX-PRO Hose Tractor is designed to be used with Parker
Pro-Lance® and/or Spir Star Blast-Pro® hose ends. Standard
hose ends may not t into Hose Tractor and/or Guide Tubes.
NOTE: MAXIMUM hose end diameter must NOT exceed .74
in. (19 mm)
• Only high quality hoses intended for waterblast applications should
be used as high-pressure hoses. Pressure rating of high-pressure
hoses MUST NEVER be exceeded.
• Do not use a shrouded hose or hose with a steel protective cover.
This will cause severe damage to the Drive Rollers.
• Verify that the high-pressure hose is properly installed in the
back-out preventer. Operate the high-pressure hose and waterjet
tool at full pressure to test the clamp force. Proper clamp force will
provide good control of the hose in forward and reverse directions,
and keep the hoses synchronized at full retract and full extend
positions.
• Always ush out hoses before attaching tools to keep particle
debris from damaging the tool.
PRE-RUN SAFETY CHECK
Refer to WJTA-IMCA’s, Recommended Practices For The Use Of
High-pressure Waterjetting Equipment and/or The Water Jetting
Association’s, WJA Code of Practice for additional safety information.
• Complete a job specic risk assessment and act on the resulting
actions.
• Adhere to all site specic safety procedures.
• Ensure the waterblasting zone is properly barricaded and that
warning signs are posted.
• Ensure the work place is free of unnecessary objects (e.g. loose
parts, hoses, tools).
• Ensure all Operators are using the correct Personal Protective
Equipment (PPE).
• Check that the air hoses are properly connected and tight.
• Check all hoses and accessories for damage prior to use. Do
not use damaged items. Only high quality hoses intended for
waterblast applications should be used as high-pressure hoses.
See the “Hose” section in this manual for more detail.
• Check all high-pressure threaded connections for tightness.
• **Ensure that any anti-withdrawal devices (back-out
preventers), whip checks (hose whips), and all other
applicable safety devices are installed and set-up
properly.**
• Ensure the doors of the ABX-PRO Hose Tractor are closed and
securely latched.
• Test the Control Box before operating the system with high-
pressure water to verify the control valves move the hose in the
intended direction, and that the dump valve and hose clamp are
working properly.
• Ensure that Operators never connect, disconnect, or tighten
hoses, adapters, or accessories with the high-pressure water
pump unit running.
• Ensure no personnel are inside the dome and/or hydroblasting
zone.
WARNING AND SAFETY INSTRUCTIONS

10 866-795-1586 • WWW.STONEAGETOOLS.COM
PART ID PART ID
CAM 102-V2
MONITOR
CB 488
MONITOR MOUNT
CAM 200-AC-US
AC POWER PACK
CAM 220
CAMERA HOUSING
CAM 210 CIRCULAR
CONNECTOR
CAM 245
CAMERA CABLE
CB 755-15-C
PRODRIVE SUPPLY
HOSE WITH CAMERA
CABLE
PROP 430-001
SPIDER PLATE
ASSEMBLY
&
PROP 187-XXX-K
EXPANSION PLUG KIT
PRO 174-54
ROLLERS FOR 8/4
HOSE
PROP 460-BN24
GUIDE WELDMENT
BN24
PROP 337
ADJUSTABLE HANDLE
PROP 339
WASHER
PROP 440-24
CAM MOUNT FOR
DBP
DBP 305
RAIL PLUG
PROP 580-1.33-001
2.5” BOX RAIL
EXTENSION KIT
*PROP 420-ICM
RAIL FLANGE MOUNT
ASSEMBLY FOR TOP
MOUNT DOMED
BUNDLES
*PROP 420-DT
RAIL FLANGE MOUNT
ASSEMBLY FOR SIDE
MOUNT DOMED
BUNDLES
SEE “PART DIAGRAMS” SECTION AT THE BACK OF THIS MANUAL FOR MORE DETAILED PART BREAK DOWNS.
*ONE RAIL MOUNT ASSEMBLY FOR EITHER ICM (TOP MOUNT) OR DELTA T (SIDE MOUNT) INSTALLATIONS
PROP-DBP-XXX-PKG CONTENTS

11
866-795-1586 • WWW.STONEAGETOOLS.COM
PART ID PART ID
∆PROP-300
PROPOSITIONER
(SEE PROP-300 USER
MANUAL FOR MORE
INFORMATION)
∆ CB-PROP-P
CONTROL BOX-
PEDESTAL STYLE
WITH UMBILICAL
HOSE CONNECTIONS
OACDA 61020019-K
AIR ACTUATED DUMP
VALVE WITH FITTINGS
AND 1/4” TUBING
O FPA-SKR
FOOT PEDAL DUMP
WITH PRESSLOCK
FITTINGS AND 1/4”
TUBING
∆ THE PROP-DBP ACCESSORY IS DESIGNED TO BE USED WITH THESE ITEMS.
THEY ARE NECESSARY TO THE FUNCTION OF THE ENTIRE PROP-DBP SYSTEM.
OTHESE ARE OPTIONAL ACCESSORIES PROP-DBP SYSTEM.
OPTIONAL EQUIPMENT

12 866-795-1586 • WWW.STONEAGETOOLS.COM
REMOVE ROLLERS IN ABX-PRO TRACTOR
The standard roller size on the ABX-PRO Tractor is Ø.46 IN. The
PROP-DBP accessory comes with a set of Ø.54 IN. replacement
rollers to accommodate 8/4 hose.
The replacement rollers must be installed on the ABX-PRO
Tractor before inserting it into the man way. This process will be
typical for Poly Roller replacements on the ABX-PRO Tractor
Assembly.
WARNING
Always de-energize the system before servicing or replacing any
parts. Failure to do so can result in severe injury and/or death.
Keep hands, hair, and clothing clear of rotating parts.
1. Open the back cover of the ABX-PRO Tractor by pulling
the top two Quick Release Pins in the outward direction.
(Figure 1)
2. Push the Adjustable Handle in the counterclockwise
direction to loosen the CAM Lever. Push the CAM Lever in
the counterclockwise direction, moving the indicator pin to
“Disengaged”. (Figure 2)
3. Loosening the Cam Lever opens up the space between the
Roller Assemblies. (Figure 3)
4. Using a 1/4” Hex Key, remove the Screws, Roller Washers,
Outer Hub Plates, and Rollers from the Idler and Drive Hubs.
(Figure 4)
SUB-ASSEMBLY 1 (ABX-PRO, ROLLERS, COLLET BLOCK, AND GUIDE TUBE)
FIGURE 3
Idler Roller
Assembly
Drive Roller
Assembly
FIGURE 1
Quick
Release
Pin (x2)
FIGURE 4
Roller (x2)
Idler hub
Drive hub
Outer Hub
Plate (x2)
Roller
Washer (x2)
5/16”
SHCS
(x2)
Cam Lever
Indicator
Pin
“DISENGAGED”
Adjustable Handle
FIGURE 2

13
866-795-1586 • WWW.STONEAGETOOLS.COM
SUB-ASSEMBLY 1 (ABX-PRO, ROLLERS, COLLET BLOCK, AND GUIDE TUBE)
INSTALL ROLLERS IN ABX-PRO TRACTOR
1. Slide the PRO 174-54 Poly Rollers onto the Drive and Idler
Hubs. Using a 1/4” Hex Key, fasten the Outer Hub Plates
and Roller Washers onto the Rollers with two 5/16” socket
head cap screws. Use anti-seize on the threads of the
screws. (Figure 5)
2. Push the back cover up into the closed position and secure
the two Quick Release Pins on the top of the
ABX-PRO Tractor. (Figure 6)
FIGURE 6
Quick Release
Pins
FIGURE 5
Roller (x2)
Idler hub
Drive hub
Hub outer
Plate (x2)
Roller
Washer (x2)
5/16”
SHCS
(x2)

14 866-795-1586 • WWW.STONEAGETOOLS.COM
SUB-ASSEMBLY 1 (ABX-PRO, ROLLERS, COLLET BLOCK, AND GUIDE TUBE) SUB-ASSEMBLY 1 (ABX-PRO, ROLLERS, COLLET BLOCK, AND GUIDE TUBE)
SUB-ASSEMBLY 2 (LINEAR DRIVE HANDLE)
INSTALL THE COLLET BLOCK ASSEMBLY
1. Remove the Slide Block with a 6mm hex key. Rotate it so that
the end with the most distance from the screws is pointing
down. Align the holes in the Slide Block with the holes in the
Collet Block as shown in (Figure 7). Fasten with the two screws
that were removed.
2. Loosen the Collet Block Cap with a 1/4” hex key and slide the
Collet Block onto ABX-PRO Tractor Guide into the until it comes
to a stop. The Air Fittings on the ABX-PRO Tractor should be
opposite the Collet Block and the Slide Block should be on the
same side ABX-PRO label. (Figure 8)
FIGURE 8
Collet Block
Cap Air Fittings
ABX-PRO
Tractor Guide
1/4” Hex Key
FIGURE 7
Collet Block
Slide Block
Guide Tube
Orient as shown
Collet Block
FIGURE 9
Collet Block
Cap
INSTALL THE ANGLED GUIDE TUBE
3. Loosen the Collet Block Cap with a 1/4” hex key and slide
the Guide Tube into the Collet Block until it comes to a stop.
Orient the Guide Tube as shown in (Figure 9) and tighten
the screws on the Collet Block Cap when the Guide Tube is
in place.
This side
down
Slide
Block
6mm Hex Key
1/4” Hex Key

15
866-795-1586 • WWW.STONEAGETOOLS.COM
FIGURE 15
Adjustable
Handle
Optimal
Camera
Position
Range
Guide
Tube
Loosen
FIGURE 10
SUB-ASSEMBLY 1 (ABX-PRO, ROLLERS, COLLET BLOCK, AND GUIDE TUBE)
SUB-ASSEMBLY 2 (LINEAR DRIVE HANDLE)
INSTALL THE CAMERA MOUNT ANGLED GUIDE TUBE
4. Loosen the adjustable handle on the Camera Mount and
slide it up the guide tube.
5. Orient the Camera as shown and tighten the adjustable
handle when in place. The Camera has a wide viewing area,
but may need to be repositioned on the Guide Tube after
the whole assembly is complete. (Figure 10)
Set This Assembly aside when complete.
PROP 339
Washer
Blue Goop®
or
equivalent
anti-seize
PROP 337
Handle
REMOVE
PROP 336
Handle Assembly
5mm
Hex Key
REPLACE THE ADJUSTABLE HANDLE ON THE LINEAR DRIVE
1. Remove the PROP 336 Handle Assembly with a 5mm Hex
Wrench. (Figure 11)
2. Lightly coat the threads of the PROP 337 Handle with Blue
Goop®or other equivlent anti-seize.
3. Install the PROP 339 Washer with PROP 337 Handle by hand
screwing it into the clamp block until it is tight. (Figure 12)
Set This Assembly aside when complete.
FIGURE 11 FIGURE 12

16 866-795-1586 • WWW.STONEAGETOOLS.COM
LOAD THE HIGH-PRESSURE HOSE INTO THE SNOUT ON THE RAIL MOUNT
Before installing High-Pressure hose, please be sure to review the “HIGH-PRESSURE
HOSE” information in the “WARNING AND SAFETY INSTRUCTIONS” section of this
manual. Always ush out hoses before attaching tools to keep particle debris from
damaging the tool.
1. Lay the Rail Mount, Snout, and High Pressure Hose on the oor.
2. Insert the High Pressure Hose into the Camlock on the Snout Carriage and
through the entire Snout. (Figure 13)
3. Leave enough hose slack coming out of the end of the Snout to continue to
push the end of the hose through the ABX-PRO Tractor and into the Guide
Tube later in the assembly. (Figure 13)
4. Connect the Female, Threaded, Camlock end of the Snout to the Male end of
the Snout Carriage. (Figure 13)
5. Install the Hose Stop on the hose behind the Snout Carriage. It will be
adjusted into the proper location after the system is operational. (Figure 13)
SUB-ASSEMBLY 3 (RAIL MOUNT, SNOUT, AND HIGH PRESSURE HOSE)
FIGURE 14
Welded
Camlock
Threaded
Camlock
Hose Hose Stop Snout
Carriage
Rail
Mount Assembly
*ICM (top mount) style
shown here
FIGURE 13
Set This Assembly aside when complete.(Figure 14)
Snout

17
866-795-1586 • WWW.STONEAGETOOLS.COM
SUB-ASSEMBLY 4 (CONTROL BOX AND CAMERA)
CONNECT THE PNEUMATIC LINES TO THE CONTROL BOX
1. Organize the supplied Air Line Umbilicals. (Figure15)
FIGURE 17
CONTROLLER TOP VIEW
FIGURE 16
Linear Drive
Color Coded
Push Connections
Rotary Drive
Color Coded
Push Connections
ABX-PRO
1/2” JIC Connections
Main Air Supply
(Chicago Style Fitting)
ON/OFF
Air Valve
2. Connect the customer supplied, Main Air Supply
line (Chicago Style Fitting) to the Control box.
(Figure 16)
3. Connect the color coded 3/8” Tubing to their
respective push connect ttings, located above
the “ROTARY” and “LINEAR” labels on the base
of the Control Box. (Figure 16)
4. Turn the Air Valve ON and operate the “Linear”
and “Rotary” levers on the control box to blow
out the 3/8” Tubing lines.
(Figures 16 & 17)
5. Hand fasten the color coded 1/2” Pneumatic
Hoses to the Color Coded JIC Fittings on the
Control Box. Then tighten with a 7/8” wrench.
(Figure 17)
6. Operate the “Feed” lever on the control box to
blow out the 1/2” Pneumatic Hoses. (Figure 17)
Control Box to ABX-PRO and Camera
1/2” JIC and Camera Connections
Control Box to Linear and Rotary Drives
3/8” Color Coded Tubing
Umbilicals
(Come contained
in sheaths)
FIGURE 15

18 866-795-1586 • WWW.STONEAGETOOLS.COM
SUB-ASSEMBLY 4 (CONTROL BOX AND CAMERA)
CONNECT THE MONITOR MOUNT, MONITOR AND POWER PACK TO
THE CONTROL BOX
1. Attach the Monitor to the Monitor Mount Assembly with the supplied
screws, washers, and wing nuts as shown in (Figure 18). Tighten by
hand.
2. Loosen the thumb screws on the Controller box and Monitor Mount.
Remove the Controller Box from the stand and slide the Monitor Mount
on. (Figure 19) Return the Controller Box to the Stand and tighten
the Thumb Screw. The Monitor Mount collar should sit just under the
Controller Box Collar.
3. Hang the Power Pack by the handle from the Monitor Mount (Figure 20)
4. Plug the cable coming from the Monitor into the “OUTPUT” port and the
Camera Cable into the “INPUT 1” port on the side of the Power Pack
(Figure 21) INPUT 2 would be for an additional camera.
FIGURE 20 FIGURE 21
FIGURE 18
Monitor Mount
Assembly
Monitor
Power
Pack
Output
Port
Input 1
Port
FIGURE 19
Stand
Thumb
Screws
SUB-ASSEMBLY 5 (OPTIONAL DUMP SYSTEM SET-UP)
Controller
Box

19
866-795-1586 • WWW.STONEAGETOOLS.COM
WARNING
Always use Hose Whip Restraints. Failure to do so can result
in severe injury and/or death. It is the responsibility of the user
to properly install the Hose Whip Restraints. Never exceed safe
working load. Follow manufacturer’s recommendations and
ratings.
OPTIONAL PNEUMATIC DUMP CONTROL CONNECTIONS
StoneAge recommends the use of some kind of dump valve for all
waterblasting operations. We offer a variety of dump valve options.
The included Control Box has a Hand Controlled Dump Lever on
the Control Panel. A Foot Dump can be used instead of the Hand
Control. See the respective connection diagrams below for either
option.
FOOT CONTROLLED DUMP CONNECTION (Figure 28)
1. Install the hose with the female JIC ends between the Ball Valve
with the male 90°JIC Fitting located on the side of the Control
Box and the tting marked “SUPPLY”on the Foot Dump Valve
Control.
2. Install the 1/4 in. (6 mm) O.D. Poly Tubing between the tting
on the Pneumatic Dump Valve Assembly and the tting marked
“DUMP”on the Foot Dump Valve Control.
3. Install the Main Water Supply and Flex Lance Hose onto the
Pneumatic Dump Valve Assembly. Be sure to use the appropriate
anti-seize, thread lubricant, and/or pipe tape as recommended
in the StoneAge Tool Fittings and Accessories Catalog at the link
below.
FIGURE 22
1/4 in. (6 mm)
O.D. Tubing
Foot Dump Control
“Supply” “Dump”
Pneumatic
Dump Valve
Assembly
Hose Whip
Restraint
Flex Lance
Main Water
Supply Hose
from pump
Ball Valve with
90°JIC Fitting
HAND CONTROLLED DUMP CONNECTION (Figure 29)
1. Install the 1/4 in. (6 mm) O.D. Tubing between the Push Connect
Fitting located on the back of the Control Box and the Push
Connect Fitting on the Pneumatic Dump Valve Assembly.
2. Install the Main Water Supply and Flex Lance Hose onto the
Pneumatic Dump Valve Assembly. Be sure to use the appropriate
anti-seize, thread lubricant, and/or pipe tape as recommended in
the StoneAge Waterblast Catalog.
FIGURE 23
1/4 in. (6 mm)
O.D. Tubing
Pneumatic
Dump Valve
Assembly
Hose Whip
Restraint
Flex Lance
Main Water
Supply Hose
from pump
Push
Connect
Fitting
SUB-ASSEMBLY 5 (OPTIONAL DUMP SYSTEM SET-UP)
DANGER
Keep dump connections neat and out of the foot path. Pinching
the dump connections will cause the dump valve to function
incorrectly, possibly leaading operator injury or death.
https://stoneagetools.com/assets/pdf/catalogs/waterblast_2020/2020_Waterblast_Catalog_web_spreads.pdf

20 866-795-1586 • WWW.STONEAGETOOLS.COM
PROPOSITIONER ATTACHMENT TO DOMED BUNDLE
POSITIONER STEP BY STEP SET-UP INSIDE THE DOMED BUNDLE
TECH TIP:
It is highly recommended to put ve necessary tools in a tote for the
installer to take inside the dome.
• Tape Measure
• 1/2” Ratcheting Socket Wrench
• 3/4” Ratcheting Open-End Box Wrench (QTY. 2)
• Wrenches specic to the Banshee for installation of the tool on lance.
INSTALL SPIDER PLATE ONTO TUBE FACE
1. Loosen the four bolts on the legs of the Spider Plate Assembly with a
3/4” Ratcheting Open-End Box Wrench, so the legs are free to slide in
the slots of the Hub Plate but do not come off. (Figure 24)
2. Loosen the Expansion Plugs (x4) on each leg with the adjustable knobs.
(Figure 24)
ICM (TOP MOUNT) DOMED BUNDLE DELTA-T (SIDE MOUNT) DOMED BUNDLE
Man Way
Man Way
Legs (x4)
Loosen
3/4” Wrench
Loosen
3/4” Wrench
Adjustable
Expansion
Plug (x4)
SPIDER PLATE ASSEMBLY
FIGURE 24
FIGURE 26
FIGURE 25
3. Hand the Spider Plate Assembly through the Man Way to someone
positioned inside the Domed Bundle. (Figures 25 & 26)
WARNING
The rst four exchanger tubes the Expansion Plugs
will be inserted into must be free of debris. Follow all
workplace safety procedures and utilize appropriate
PPE when cleaning out the exchanger tubes prior to
plug installation to avoid injury.
Table of contents
Other StoneAge Valve Positioner manuals
Popular Valve Positioner manuals by other brands
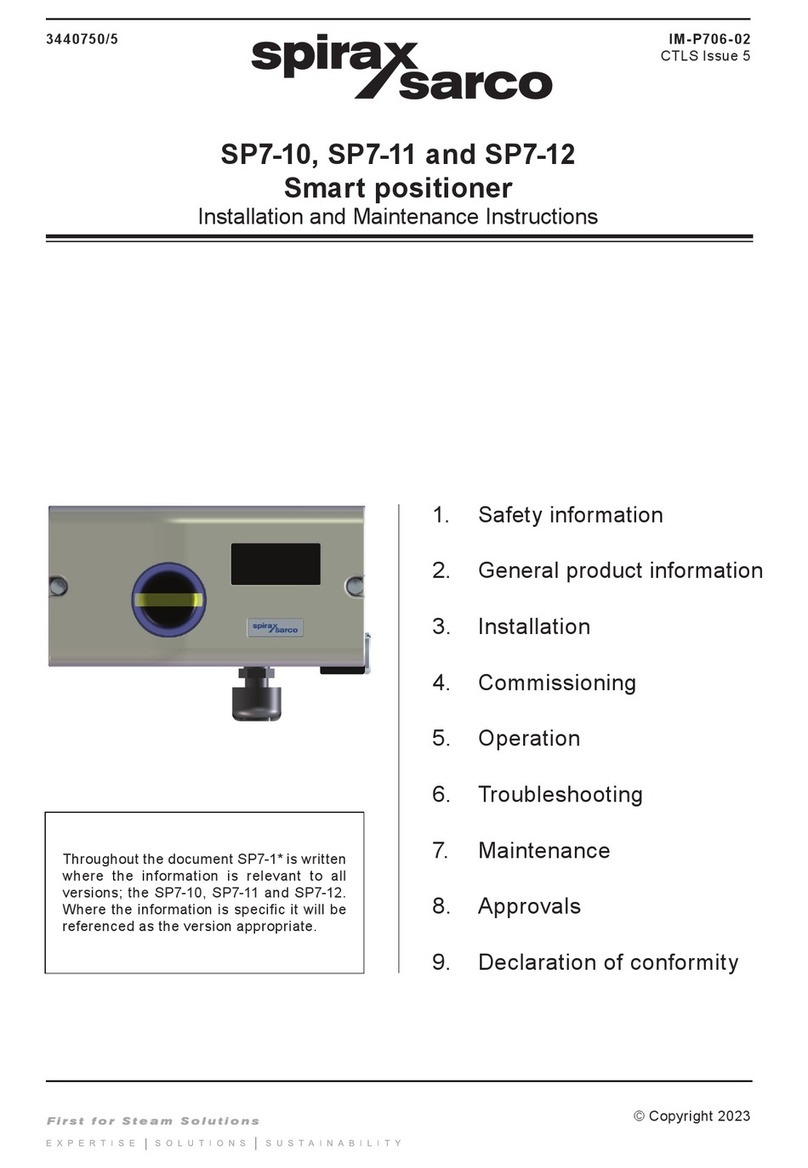
Spirax Sarco
Spirax Sarco SP7-11 Installation and maintenance instructions
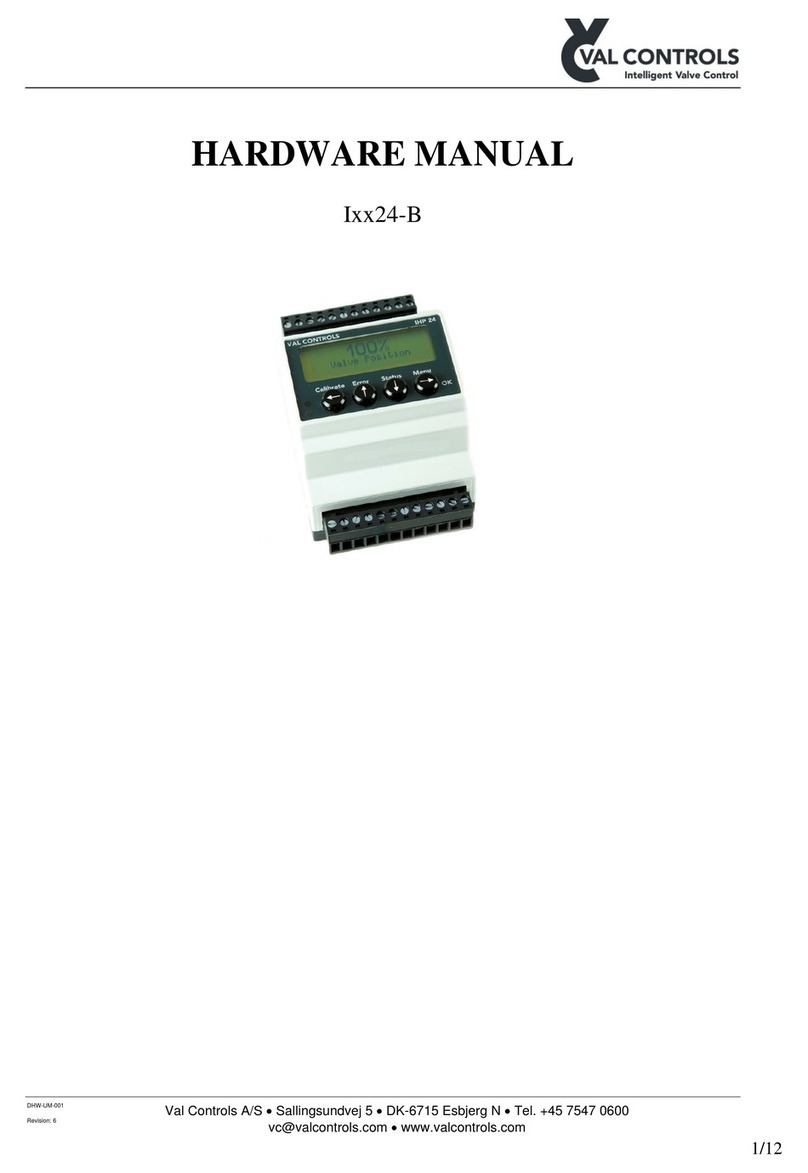
Val Controls
Val Controls I 24-B Series Hardware manual
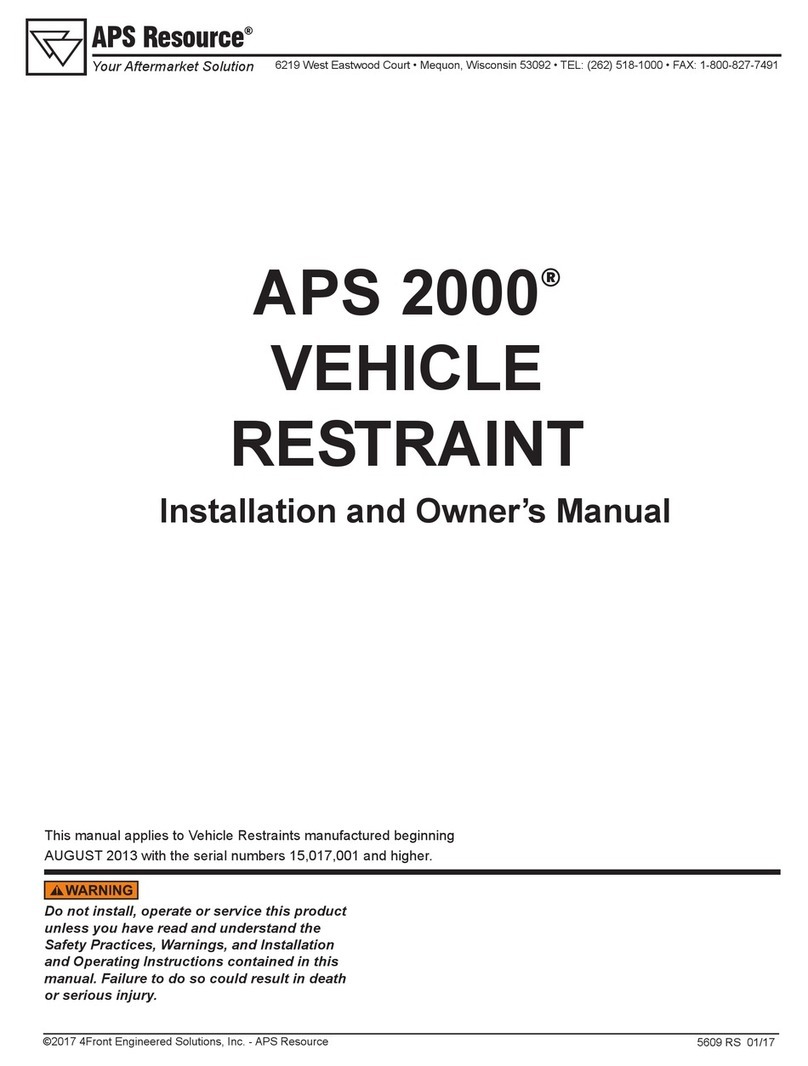
APS
APS 2000 Installation and owner's manual
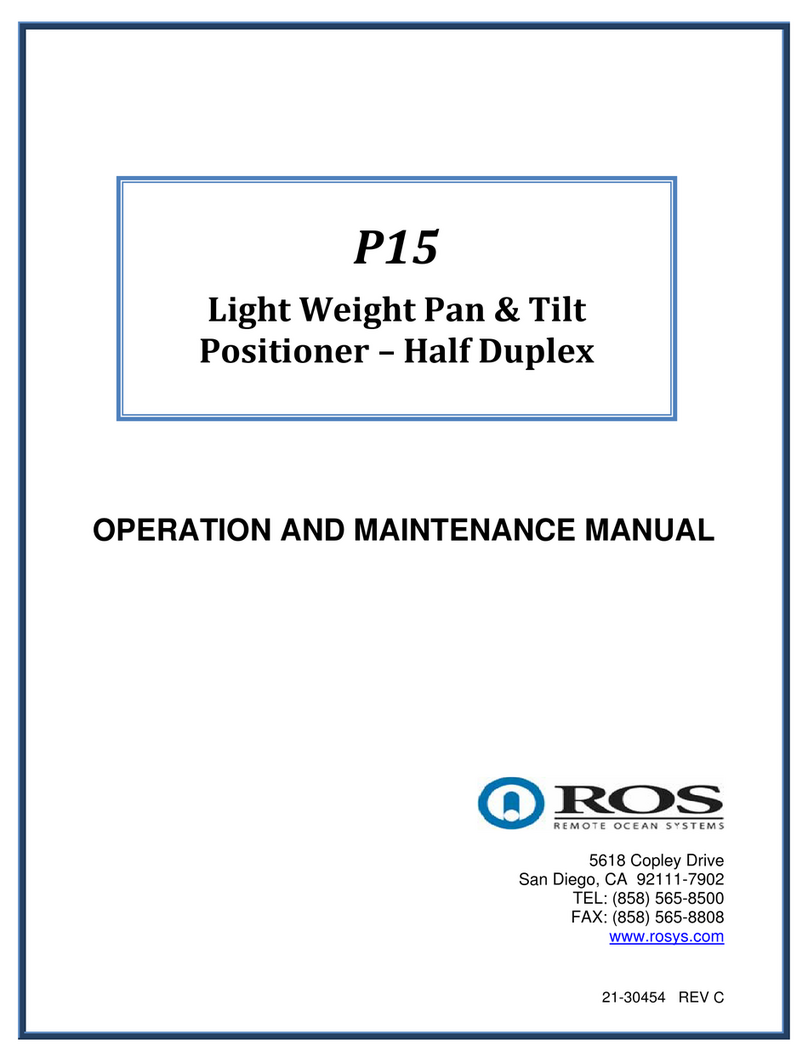
Ros
Ros P15 Operation and maintenance manual
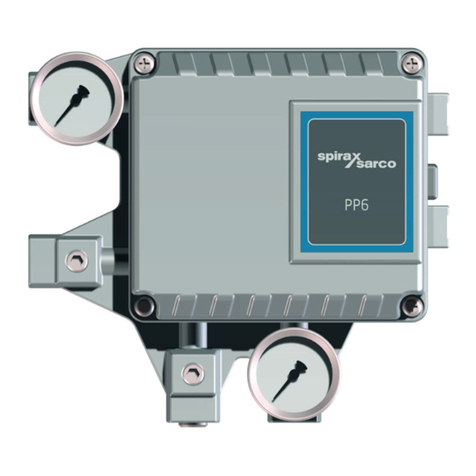
Spirax Sarco
Spirax Sarco PP6 quick start guide
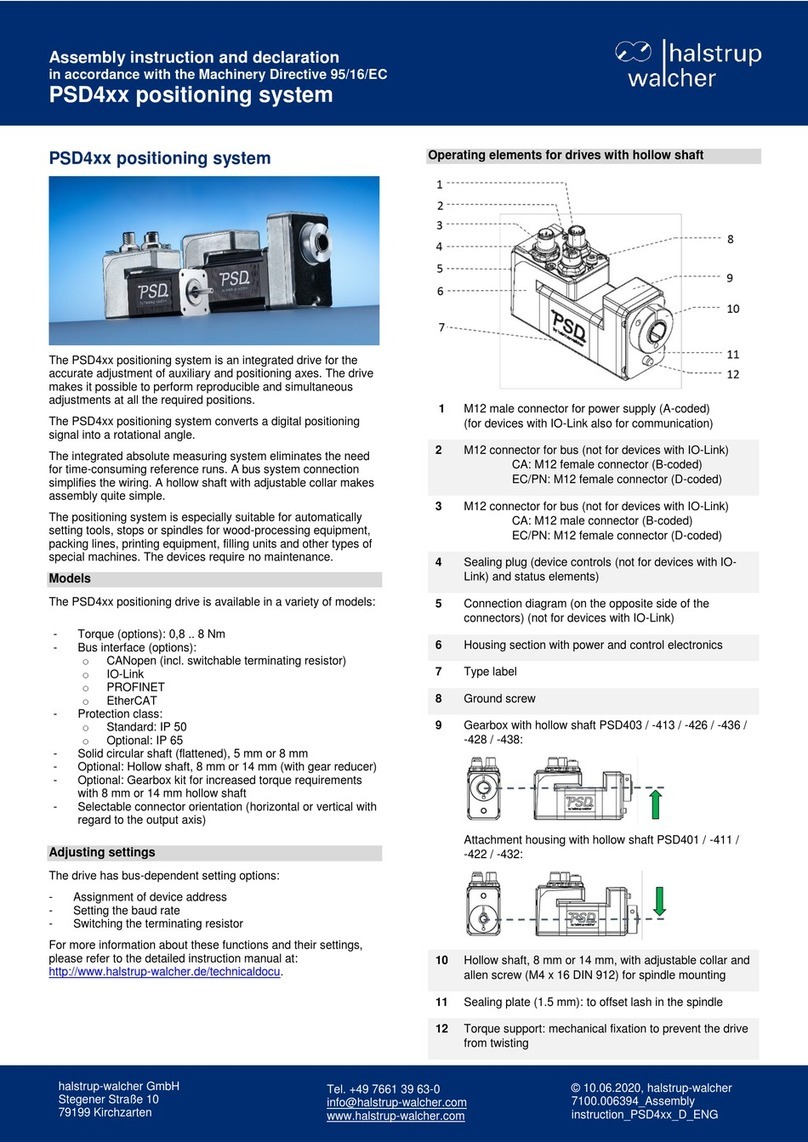
halstrup-walcher
halstrup-walcher PSD4 Series Assembly instruction and declaration