STORK TRONIC ST48-WHDVM.04 User manual

ST48-WHDVM.04
Differential temperature controller
Order number 900304.006
Old Id.Nr.: 141648
Wiring diagram
Product description
The PID differential temperature controller with two 3-digit LED seven segment displays, 4 keys
and 3 relays is variably applicable due to its freely programmable general functions. The relay
contact K1 directly affects the main setpoint, formed by reference variable and the given offset
temperature. Contact K2 affects the secondary setpoint which is formed by the main setpoint via
overlap or which alternatively can be freely defined. Contact K3 affects adjustable limit values.
Sensor: Pt100
Range: -99...750◦C
Front size: 48mm x 48mm
Panel cut-out: 45.2mm x 45.2mm
Connector: plug and socket
1

2

SOFTWARE .04
Adjustment options
Key UP
Pressing this key you can increase the parameter or parameter value or scroll the
parameter list.
Key DOWN
Pressing this key you can decrease the parameter or parameter value or scroll the
parameter list. At alarm the buzzer function can be switched off with this key.
Function key 1
Different functions are assigned to this key by help of parameters.
Key SET
Holding this key, the desired value is indicated.
Additionally, this key is used for setting parameters.
First control level:
Parameter setting of the main setpoint
If none of the keys is pressed, the display indicates the actual value of the temperature. Pressing
the SET key, the setpoint (difference value) shows on the display.
If the setpoint is to be changed, the SET key is to be kept pressed while adjusting the setpoint with
the keys UP and DOWN.
Please note that the setpoint can only be changed within the set setpoint limits.
The setpoint S1’ (if available) can be adjusted in the same way. If setpoint S1’ is activated it is
indicated and relevant for the control in case of closed switching input.
Para-
meter Function description Adjustment range Standard
setting Custom
setting
S1
Setpoint 1, difference value P4 ... P5 0.0°C
S1’ Sollwert 1’, difference value or
freely adjustable setpoint -99.0 ... +99.0 K (if A33=1)
-99 ... 999°C (if A33=2) 0.0°C/K

Second control level (P parameters):
Setting of control parameters
Simultaneously pressing the UP and DOWN key for at least 4 seconds opens a parameter list
containing control parameters. With the UP and DOWN keys the list can be scrolled in both
directions. Pressing the SET key will give you the value of the respective parameter. Pressing also
the UP or DOWN key at the same time the value can be adjusted.
Return to the initial position takes place automatically, if no key is pressed for 60 seconds.
Para-
meter Function description Adjustment range Standard
setting Custom
setting
P1 Setpoint 2 or
Delta W -99 ... 999°C
-99 ... 99.9 K
+10.0 K
P2 Hysteresis contact K1 0.1 ... 99.9 K 1.0 K
P3 Hysteresis contact K2 0.1 ... 99.9 K 1.0 K
P4 Control range limitation –
minimum difference value -99°C ... P5 -99°C
P5 Control range limitation –
maximum difference value P4 ... 99,9°C 99,9°C
P7 Proportional band 0.1 ... 99.9 K 15.0 K
P8 Reset time Tn, I-factor 0...999 sec.
(0 sec. = inactive) 500 sec.
P9 Lead time Tv, D-factor 0...999 sec.
(0 sec. = inactive) 50 sec.
P10 Cycle time 2...100 sec. 8 sec.
P19 Key-lock 0: no key-lock
1: key-lock 0
P20 Following value display ----- -----
P21 Following value correction -10.0 ... 10.0 K 0.0 K
P22 Leading value display ----- -----
P23 Leading value correction -10.0 ... 10.0 K 0.0 K
P30 Lower limit value of the following
value for alarm contact -99°C/K...P31 -10 K
P31 Upper limit value of the following
value for alarm contact P30...999°C/K +10.0 K
P32 Hysteresis alarm contact 0.1 ... 99.9 K 1.0 K
P33 Lower range limitation for fixed
setpoint control -99 ... 999°C -99°C
P34 Upper range limitation for fixed
setpoint control -99 ... 999°C 999°C
P40 Analogue output 0: PID-control value (P43-P45)
1: following value (P41, P42)
2: leading value (P41, P42)
0
P41 Indication value for 0V at
analogue output -99...999°C 0°C
P42 Indication value for 10V at
analogue output -99...999°C 100°C
P43 Indication value full heating
performance (100%) -10.0 ... +10.0 V +10.0 V
P44 Indication value "0" performance -10.0 ... +10.0 V 0.0 V
P45 Indication value full cooling
performance (100%) -10.0 ... +10.0 V 0.0 V

Para-
meter Function description Adjustment range Standard
setting Custom
setting
P46 Lower limit of the following value
for 0 or 10V at analogue output -99...999°C 0,0°C
P47 Output voltage for values lower
than P46 0: 0V
1: 10V 0
P48 Upper limit of the following value
for 0 or 10V at analogue output -99...999°C 10,0°C
P49 Output voltage for values higher
than P48 0: 0V
1: 10V 1
P50 Hysteresis at limit values P46 and
P48 0,1...99,9K 1,0K
Pr Program version --

Parameter description:
P1: Setpoint / DeltaW for control circuit 2
Adjusting the setpoint of control circuit 2.
If A5=1, the setpoints for control circuit 1 and 2 are linked with one another via switching difference
DeltaW, which can be adjusted with P1. (operation with DeltaW)
The following applies: setpoint thermostat 2 = setpoint control circuit 1 + delta W2.
This difference can take positive or negative values. Thus, a leading or following contact can be
realised.
P2: Hysteresis contact K1
P3: Hysteresis contact K2
The hysteresis can be set symmetrically or one-sided at the setpoint (see A40, A41).
At one-sided setting, the hysteresis works downward with heating contact and upward with cooling
contact. At symmetrical hysteresis, half of the hysteresis’ value is effective below and half of the
value above the switching point (see fig. 1 and 2).
Fig. 1: Heating controller, Fig. 2: Cooling controller,
one-sided hysteresis symmetrical hysteresis
The hysteresis is only effective with thermostatic control, if PID mode is activated the hysteresis
becomes ineffective.
P4: Control range limitation –minimum value
P5: Control range limitation –maximum value
The adjustment range of the setpoint can be limited in both directions. This is to prevent the end
user of a unit from setting inadmissible or dangerous setpoints.
Parameters P7…P10 are only available if either K1 or K2 operates in PID mode
(A6 = 1 or A7 = 1)
P7: Proportional band at PID regulation
The proportional part works in such a way that with approximation of the actual value to the
setpoint the variable is reduced linearly from +-100% to 0%.
P8: Reset time Tn, I-factor
P9: Lead time Tv, D-factor
These settings determine the intensity and effect of the I-and D-portion. If "0" is set, then the
portion is inactive.
P10: Cycle time Tp
The cycle time is the time, in which the control output runs through one switching period, i.e. once
switched out and once switched on. The smaller the cycle time, the faster the regulation. By
consequence, however, there is also an increased switching frequency of the exit, which can lead

to rapid wear of relay contacts. For very fast control ways with the respective high switching
frequency a voltage output is therefore of advantage.
P19: Key-lock
The key-lock allows blocking of the control keys. In locked condition parameter adjustments with
keys is not possible. At the attempt to adjust the parameters despite key-lock the message "==="
appears in the display.
P20: Following value display
When this parameter is selected, pressing the SET key display the actual value of the following
input. The value can be adjusted with parameter P21.
P21: Following value correction
This parameter allows the correction of actual value deviations caused for example by sensor
tolerances or extremely long sensor lines. The regulation measure value is increased or decreased
by the here adjusted value.
P22: Leading value display
When this parameter is selected, pressing the SET key display the actual value of the leading
input. The value can be adjusted with parameter P23.
P23: Leading value correction
This parameter allows the correction of actual value deviations caused for example by sensor
tolerances or extremely long sensor lines. The regulation measure value is increased or decreased
by the here adjusted value.
P30: Lower alarm value
P31: Upper alarm value
The exit alarm is a boundary alarm or a range alarm. Both at the boundary alarm and the range
alarm, limit values can be relative, i.e. going along with the setpoint S1/S1’, or absolute, i.e.
independent of the setpoint S1/S1’. Note that in case of differential control the main setpoint
always is formed by the addition of the actual leading value and the adjusted difference value S1. If
setpoint S1’ is activated the new difference value is either S1+S1’ or only S1, depending on
parameter A35.
If only one switching point is required in case of boundary alarm, the not-used second switching
point should be adjusted to a value above or below the control range and the limit values should be
absolute (see parameter A30).
Boundary alarm function (see fig. 3):
The alarm contact is closed if the process
temperature is above the upper or below the
lower boundary value.
Fig. 3: Boundary alarm, rel. boundaries
Range alarm function (see fig. 4):
Opposite switching behaviour to the boundary
value alarm. The alarm contact is closed if
the actual value remains between the
boundary values.
Fig 4: Range alarm, abs. boundaries

P32 Hysteresis alarm contact
The hysteresis can be set symmetrically or one-sided at the adjusted limit values. (see A42). It
becomes effective depending on alarm definition. At one-sided setting and boundary alarm the
hysteresis is effective above the lower and below the upper limit value. At one-sided setting and
range alarm the hysteresis is effective above the upper and below the lower limit value. At
symmetrical hysteresis, half of the hysteresis’ value is effective below and half of the value above
the switching point.
P33: Lower range limitation for fixed setpoint control on following sensor
P34: Upper range limitation for fixed setpoint control on following sensor
P33 and P34 are the limit values for the main setpoint, formed by reference variable and the given
offset temperature. If the main setpoint is above the upper or below the lower limit value the value
of P33 or P34 becomes effective as new setpoint and the leading value has no more effect on the
setpoint. When the temperature range between P33 and P34 is reached again the control returns
to the main setpoint as before.
P40: Analogue output
This is to define whether the analogue output carries reference variable, the actual following value
or the actual leading value. In case of reference variable display, the sign can change, depending
on whether heating or cooling is required. The actual values, however, are always indicated with
positive sign.
P41: Indication value for 0V at analogue output
P42: Indication value for 10V at analogue output
Indication of the actual value is subject to the following range adjustment:
If temperature reaches the value set in P41, voltage is 0 V.
If temperature reaches the value set in P42, voltage is 10 V.
P43: Indication value full heating performance (100%)
P44: Indication value "0" performance
P45: Indication value full cooling performance (-100,0%)
Indication of the variable is subject to the following range adjustment:
If heating is to be performed with 100 %, voltage is as set at P43.
If neither heating nor cooling is requested, voltage is as set at P44.
If cooling is to be performed with 100 %, voltage is as set at P45.
On the following page there are some scaling examples.

Scaling examples of analogue output:
Scaling example 1:
Indication range of the variable for heating
and cooling is -10.0 ... +10.0 V
with P43 = 10.0; P44 = 0.0; P45 = -10.0.
This is the standard setting.
Heating
performance
100%
0%
100%
Cooling
performance
-10 V 0 V +10 V
Analogue output
P 43
P 44
P 45
Fig. 5
Scaling example 2:
Indication range of the variable for heating is
+2.0 ... +10.0 V
with P43 = 10.0; P44 = 2.0; P45 = 2.0.
Heating
performance
Cooling
performance
100%
0%
100%
+2 V +10 V
Analogue output
P 43
P 44
P 45
Fig. 6
Scaling example 3:
Indication range of the variable for cooling is
–2.0 ... –8.0 V
with P43 = -2.0; P44 = -2.0; P45 = 8.0.
Heating
performance
Cooling
performance
100%
0%
100%
-8 V 0 V
Analogue output
P 43
P 44
P 45
Fig. 7
Notes concerning parameters P40 -P45:
If the reference variable is selected with
parameter P40, the parameters P41 and P42
are still adjustable, but without function. The
same applies to the parameters P43-P45, if
the actual value is selected with parameter
P40.

P46: Lower limit of the following value for 0 or 10V at analogue output
If the following value drops below this limit, the output voltage is according to parameter P47.
P47: Output voltage for values lower than P46
Output voltage below the limit set with parameter P46.
P48: Upper limit of the following value for 0 or 10V at analogue output
If the following value goes above this limit, the output voltage is according to parameter P49.
P49: Output voltage for values higher than P48
Output voltage above the limit set with parameter P48.
P50: Hysteresis at the limit values P46 and P48
The here adjusted hysteresis is set symmetrically at the setpoints according to parameters P46
and P48.
Pr
Program version

Third control level (A parameters):
Setting of control parameters
Access to the third control level is granted when selecting the last P-parameter on the second
control level. Continue to press the UP key for approximately 10 seconds until “PA” appears.
Continue to press the UP key and additionally press the DOWN key for about 4 seconds and the
first A-parameter of the third control level is indicated.
With the keys UP and DOWN you can scroll the list in both directions. Pressing the SET key will
give you the value of the respective parameter. By pressing the UP or DOWN key at the same time
the value can be adjusted.
Return to the initial position takes place automatically, if no key is pressed for 60 seconds, or by
simultaneously pressing the UP and DOWN key for approx. 4 seconds.
Para-
meter Function description Adjustment range Standard
setting Custom
setting
A1 Switch mode contact K1 0: heating contact
1: cooling contact 0
A2 Switch mode contact K2 0: heating contact
1: cooling contact
1
A3 Function of contact K1 at
sensor error 0: relay off
1: relay on 0
A4 Function of contact K2 at
sensor error 0: relay off
1: relay on 0
A5 Selection setpoint 2 or DeltaW 0: operation with setpoint 2
1: operation with DeltaW
1
A6 Control characteristics
contact K1 0: thermostatic
1: PID
1
A7 Control characteristics
contact K2 0: thermostatic
1: PID 0
A8 Display mode 0: both displays without
decimals
1: both displays with decimals
1
A10 Indication value for lower value
linear analogue input -99...999°C 0°C
A11 Indication value for upper value
linear analogue input -99...999°C 100°C
A19 Parameter lock 0: no lock
1: A-parameter locked
2: A-and P-parameter locked
0
A20 Minimum action time contact
K1 ”Off” 0…999 sec. 0 sec.
A21 Minimum action time contact
K2 ”Off” 0…999 sec. 0 sec.
A22 Delay after “Power-on” 0…999 sec. 0 sec.
A23 Alarm suppression after
"Power-On" 0…999 min. 0min.
A30 Function alarm exit 0: Boundary alarm, relative
1: Boundary alarm, absolute
2: Range alarm, relative
3: Range alarm, absolute
0

Para-
meter Function description Adjustment range Standard
setting Custom
setting
A31 Special function at boundary
alarm 0:no special function
1:buzzer
2:flashing display
3:flashing display and buzzer
4:like 3, buzzer can be
cancelled
5:like 4, cancelled buzzer
restarts after 10 min.
6:like 4, cancelled buzzer
restarts after 30 min
0
A32 Special function of upper
display 0: following value
1: setpoint
2: setpoint, if no differential
control
3: desired difference value, if
differential control
4: actual difference value
0
A33 Special function of lower
display 0: following value
1: setpoint
2: setpoint, if no differential
control
3: desired difference value, if
differential control
4: actual difference value
0
A34 Indication with function key 1,
if b1=2 0: leading value
1: desired difference value
2: actual difference value
1
A35 Type of setpoint S1‘ if b1=0 0: additive differential
temperature
1: alternate differential
temperature
2: freely adjustable setpoint
1
A40 Hysteresis mode contact K1 0: symmetrically
1: one-sided 0
A41 Hysteresis mode contact K2 0: symmetrically
1: one-sided 0
A42 Hysteresis mode alarm contact
0: symmetrically
1: one-sided
1
A60 Sensor type 4: Pt100 3-wire
5: PTC (KTY81-110)
6: 0...10 V, 0...20 mA
7: 2...10 V, 4...20 mA
4
A70 Software filter 0...10
(0 = inactive) 1
A80 Temperature scale 0: Fahrenheit (50 Hz)
1: Celsius (50 Hz)
2: Fahrenheit (60 Hz)
3: Celsius (60 Hz)
1
U1 Function output K1 0: no connection
1: connection to contact K1
2: connection to contact K2
3: connection to alarm contact
4: connection to ready message
1

Para-
meter Function description Adjustment range Standard
setting Custom
setting
U2 Function output K2 0: no connection
1: connection to contact K1
2: connection to contact K2
3: connection to alarm contact
4: connection to ready message
2
U3 Function output K3 0: no connection
1: connection to contact K1
2: connection to contact K2
3: connection to alarm contact
4: connection to ready message
3
U4 Function output K4 0: no connection
1: connection to contact K1
2: connection to contact K2
3: connection to alarm contact
4: connection to ready message
4
b0 Function input E1 0: no function
1: setpoint S1‘ activated
2: standby function
1
b1 Function key 1 0: no function
1: standby function
2. display according to
parameter A34
0
b3 Text if in standby mode, if
b0=2, b1=1 0: standby text "OFF"
1: standby text "AUS" 0
L0 Individual address (Node) 1...126
1
L1 Individual address (Subnet) 0...255
1
Lr Reset parameters 0: no reset
1: reset parameters, including
Lr
0

Parameter description
The following values can change the equipment characteristics
and are therefore to be set with utmost care.
A1: Switch mode contact K1
A2: Switch mode contact K2
The switch mode for the relays, i.e. cooling or heating function, can be programmed independently
at works. Heating function means that the contact opens as soon as the setpoint is reached, thus
power interruption. At cooling function the contact closes, if the actual value is above the required
setpoint.
A3: Function of contact K1 at sensor error
A3: Function of contact K2 at sensor error
In case of open-circuit or short-circuit at sensor 1 the display indicates a flashing “F1”, at sensor 2
a flashing “F2”. At sensor error the selected relay falls back into the condition pre-set here.
A5: Selection setpoint 2 or DeltaW
This parameter determines whether the setpoints for thermostat 1 and 2 independently adjustable
(A5=0) or whether they are tied with one another via a switching offset DeltaW (A5=1). This
parameter applies only to contact K2 (see parameter P1).
A6: Control characteristics contact K1
A7: Control characteristics contact K2
Independent choice of either PID or thermostatic characteristics for each contact. If contact K2 is
set as PID-contact, it operates with setpoint 1.
A8: Display mode
The value can be indicated in integrals or with decimals. In general, all parameter indications are
presented with decimals.
A10: Indication value for lower value linear analogue input
A11: Indication value for upper value linear analogue input
Only relevant, if the controller is programmed for a voltage input (0…10V linear) or a current input
(4…20mA linear). These parameters allow scaling of the linear analogue input. The value to be
indicated for the lower and upper entrance value then defines the range the controller will indicate.
For input range 4…20mA the display will show sensor error if the input signal drops below 4mA.
A19 Parameter lock
This parameter enables locking of each parameter level. If third level is locked, only parameter A19
may be changed.
A20: Minimum action time contact K1 ”Off”
A21: Minimum action time contact K2 ”Off”
These parameters permit a delay in switching off the relay in order to reduce the switching
frequency. The adjusted time sets the entire minimum time period for a switching-off phase. If PID
characteristics are selected the minimum action times are set to zero.
A22: Delay after “Power-on”
This parameter allows a switching-on delay of relays after switching-on the mains voltage. This
delay corresponds with the time set here. The delay is only active when the controller is switched
on the first time. The delay applies not to the alarm contact.

A23: Alarm suppression after "Power-On"
This parameter allows a switching-on delay of the alarm contact after switching on the mains
voltage. This suppression corresponds with the time set here. The suppression is only active when
the alarm is activated the first time. The suppression not to the contacts K1 and K2.
A30: Function alarm exit
The alarm exit evaluates an upper and a lower limit value (see parameters P30 and P31), whereas
a selection is possible as to whether the alarm is active if the temperature lies within these two
limits (range alarm), or whether the alarm is released if the temperature lies beyond them
(boundary alarm). In the case of sensor error, the alarm is activated as follows: at range alarm
function the alarm relay is off and at boundary alarm function the alarm relay is on. In case of
parameter memory error all contacts will be switched off.
A31: Special function at boundary alarm
6 different special functions can be selected in the case of an alarm. At functions 1-3 the buzzer
can not be switched off, therefore the alarm terminates as soon as the error is eliminated. At
functions 4-6 it is possible to switch off the buzzer, whereas a repetition after two different time
intervals is possible.
A32: Special function of upper display
A33: Special function of lower display
This parameter permits a permanent special display in the upper or lower display. It is possible to
indicate the setpoint, formed by reference variable and the given offset temperature, the offset
temperature (if differential control) or the actual differencevalue. In this case, the usually indicated
following or leading value is not available in the first parameter level.
Note: If offset temperature is selected and there is no differential control, the following value is
indicated in the upper display and the lower display is off. The lower display stays off, if no special
function is selected or if there is no differential control.
A34: Indication with function key 1
If activated with b1=2, function key 1 can be parametered to indicate the leading value, the offset
temperature or the actual difference. This feature is important especially for units with only one
display.
A35: Adjustment of setpoint S1‘ (not available on all types of controllers)
The functions of this parameter are only effective if there is a switching input E1 available. By
closing switching input E1, setpoint S1 can be switched to a setpoint S1’. Setpoint S1’ can be
either added to the difference value S1 (S1+S1’) or an independent, freely adjustable, difference
value or an independent, freely adjustable setpoint. In case of a freely adjustable setpoint the
leading value has no more influence on the setpoint end the respective sensor can be
disconnected; an error message will be suppressed. The lower display remains deactivated as
long as there is no special function set with parameter A33.
The setpoint S1’ can only be indicated and adjusted by means of the SET key if input E1 is closed.
A40: Hysteresis mode contact K1
A41: Hysteresis mode contact K2
These parameters allow selection as to whether the hysteresis values which are adjustable with P2
and P3, are set symmetrically or one-sided at the respective switching point. At symmetrical
hysteresis, half of the hysteresis’ value is effective below and half of the value above the switching
point. The one-sided hysteresis works downward with heating contact and upward with cooling
contact. The hysteresis is only effective in case of thermostatic control. With PID characteristics the
hysteresis has no effect.
A42: Hysteresis mode alarm contact
These parameters allow selection as to whether the hysteresis value which is adjustable with P32,
is set symmetrically or one-sided at the respective switching point. At symmetrical hysteresis, half

of the hysteresis’ value is effective below and half of the value above the switching point. The one-
sided hysteresis works downward with heating contact and upward with cooling contact.
A60: Sensor type
These parameters permit selection of the sensor type, if the needed hardware prerequisites are
available.
A70: Software filter
With several measuring values, it is possible to obtain an average value. This parameter can
determine by how many measured values an average value is to be formed. If a sensor with a very
fast reaction to external influences is used, an average value ensures a calm signal process.
A80: Temperature scale
Indication can be switched between Fahrenheit and Celsius. At conversion, the parameters and
setpoints maintain their numerical value and adjustment range. (Example: A controller with the
desired value of 0°C is switched to Fahrenheit. The new desired value is then interpreted as 0°F,
which corresponds to a temperature of -18°C).
NOTE: Indication limits with °F can be smaller than the actual measuring range!
U1: Function output K1
U2: Function output K2
U3: Function output K3
U4: Function output K4
Generally, the outputs are exchangeable with parameter adjustments, in order to achieve an
optimal relation of the existing hardware with regard to contact rating, kind of contact and cycle
number. Therefore, these parameters first assign the outputs to the controller function.
b0: Function E1
With this parameter function of the ext. input E1 can be set. With b0=0 the E1 is not evaluated.
With. With b0=1 setpoint S1 is switched to setpoint S1’ when input E1 is closed. With b0=2 the
controller is switched to the standby mode.
b1: Function key 1
This parameter activates a special function for function key 1. This can be the either the standby
function or the activation of the display according to parameter A34. If the standby function is set
parameter b3 selects an English or German text.
b3: Text if in standby mode
With this parameter one can select the text to be displayed if the controller is in standby mode. A
German or an English text can be selected.
L0: Individual address (Node)
L1: Individual address (Subnet)
STOERK TRONIC devices can be hooked with "self installation". In this case, however, each
participant has to be assigned a clear address. This address corresponds to the knot address and
subnet address with Domain=0.
The address of the knot can only be changed, if the knot was not tied externally (SNVT
"nciNetConfig" = CFG_LOCAL), otherwise the changed value is not saved (after releasing the set
key the old value is reset).
Lr: Reset parameters
This parameter is special as it can reset all parameters to the condition ex works. At setting Lr = 1
reset takes place, and Lr itself is reset to zero again. Note that customised values will become
effective if these were adjusted prior to delivery.

LON-bus and serial communication
General note
The control program has some standardized variables of type “SNVT” which permit the
communication with external units via LON-bus. There are input and output values. The input
values permit settings for the controller, which are directly available for the control process. The
output values indicate measuring values and status information of the unit.
Automatic update of variables
At each adjustment of the values in the controller the corresponding output variables are updated.
If there are no condition changes the values will be updated every “nciMaxSendTime” seconds. If
“nciMaxSendTime” is less than 1.0 sec. the values are no more updated in intervals but only if
there is any change.
Adjustments of the input variables will be applied to the controller immediately and cause an
EEProm write access. Keep in mind the limited amount of save cycles.
Definition of the interface variables
Object "Differenzregler"
Name of variable Type Input/Output
Values Resolution
nviSetDiffTemp SNVT_temp_p Input –273.17...327.66 °C 0.01 °C
nviStandbyMode SNVT_lev_disc Input 0...255 -----
nvoActualTemp1 SNVT_temp_p Output –273.17...327.66 °C 0.01 °C
nvoActualTemp2 SNVT_temp_p Output –273.17...327.66 °C 0.01 °C
nvoActualSetPt SNVT_temp_p Output –273.17...327.66 °C 0.01 °C
nvoRelayState SNVT_state Output On/Off for K1...K3 -----
Object "0"
Name of variable Type Input/Output
nvoStatus SNVT_obj_status Output object status, see SNVT-list
nciNetConfig SNVT_config_src Input configuration, see SNVT-list
nviRequest SNVT_obj_request Input object request, see SNVT-list
Connection information
Simultaneously pressing all keys sends a „Service-Pin“ message (the program version of the
software is indicated in the display.
The controller responds to a “wave” command with a display flashing 3 times.
Note that if a data logger is used the node number may be changed at connection (the domain
must remain “0”). After a controller reset the new address can be queried with parameter “L0” and
“L1”. These parameters may not be changed after connection (ensured by “nciNetConfig“).

Connection to data logger
General note
The following listed measuring values as well as the inputs and outputs are available for the data
logger TRL1 via LON interface. In general the setpoints and parameters all are accessible.
Data logger protocol
Parameter values (read/write)
Adjustable parameters P1,P2,P3,P4,P5,P7,P8,P9,P10,P19,P21,P23,
P30,P31,P32,P33,P34,P40,P41,P42,P43,P44,P45,
A1,A2,A3,A4,A5,A6,A7,A8,A10,A11,A19,A20,A21,A22,A23,
A30,A31,A32,A33,A34,A35,A40,A41,A42,A60,A70,A80,
U1,U2,U3,U4,b0,b1,b2,b3,L0,L1,Lr
Adjustable setpoints S1, S11 (=S1')
Actual values (only read) Memory
address
Actual following value A1 0
Actual leading value A2 1
Actual setpoint A3 2
Controller status (only read) D1
Bit 0: Standby-mode ("1", if "on")
Bit 1:
Bit 2:
Bit 3:
Bit 4:
Bit 5:
Bit 6: switching state control contact 1
Bit 7: switching state control contact 2
Bit 8:
Bit 9:
Bit 10:
Bit 11:
Bit 12:
Bit 13:
Bit 14:
Bit 15: Alarm (=K7) active
3
Status (write)
Controller status Bit 0: Standby-mode ("1", if "on")
0

Status messages
Message Cause
Error elimination
F 1 Sensor error
(open-or short-circuit at sensor F1) Check sensor
F2 Sensor error
(open-or short-circuit at sensor F2) Check sensor
_ _ _ Keyboard lock active see Parameter P19 or A19
Flashing display
Temperature alarm (see A31) cancel buzzer with DOWN button
EP Data loss at parameter memory
(Contacts K1 and K2 are switched off) If error cannot be eliminated by
switching on/off, the controller must be
repaired

Order No.: 141648
Technical data of ST48-WHDVM.04
Measuring input
F1: Sensor following value
F2: Sensor leading value
Sensor type Resistance thermometer Pt100
Measuring range: -99°C...+750 °C
Measuring accuracy at 25°C: +/-0.5K +/-0.5% of measuring range
Outputs
K1: Relay, normally-open contact, 8(1,5)A 28V, function see parameter U1
K2: Relay, normally-open contact, 8(1,5)A 28V, function see parameter U2
K3: Relay, normally-open contact, 8(1,5)A 28V, function see parameter U3
Installed buzzer, ca. 85dB
Analogue output
S1: linear voltage output 0...+10V
Display
One 3-digit LED-display, height 13mm, colour red
One 4-digit LED-display, height 10mm, colour red
Three LEDs, for status display of the outputs K1, K2, K3.
LON communication interface
shielded 2-wire line, Twisted Pair, 78kBaud, not polar, maximum cable length 100m
Interface driver: RS485, galvanically not separated.
The network has to be installed in line topology and terminated with 120Ohm at each side.
Power supply
12-24V AC +/-10%(50/60Hz) or 16-36V DC
Power consumption max. 3VA
Connectors
Plug and socket
Clamp A: 8-pole, spacing 5,0mm, for cable up to 2.5 mm²
Clamp B: 11-pole, spacing 3.5 mm, for cable up to 1.5 mm²
Ambient conditions:
Storage temperature: -20...+70°C
Operating temperature: 0...+55°C
Relative humidity: max. 75% without dew
Weight
ca. 130g
Enclosure
Front IP65, IP00 from back
Installation data
Unit is to be installed in an instrument panel.
Front size: 48 x 48 mm
Panel cut-out: 45.2 x 45.2 mm
Installation depth: ca. 120 mm
Mounting by fixing strap.
Table of contents
Other STORK TRONIC Temperature Controllers manuals
Popular Temperature Controllers manuals by other brands

Heatcraft Refrigeration Products
Heatcraft Refrigeration Products Masterlog 4 User handbook
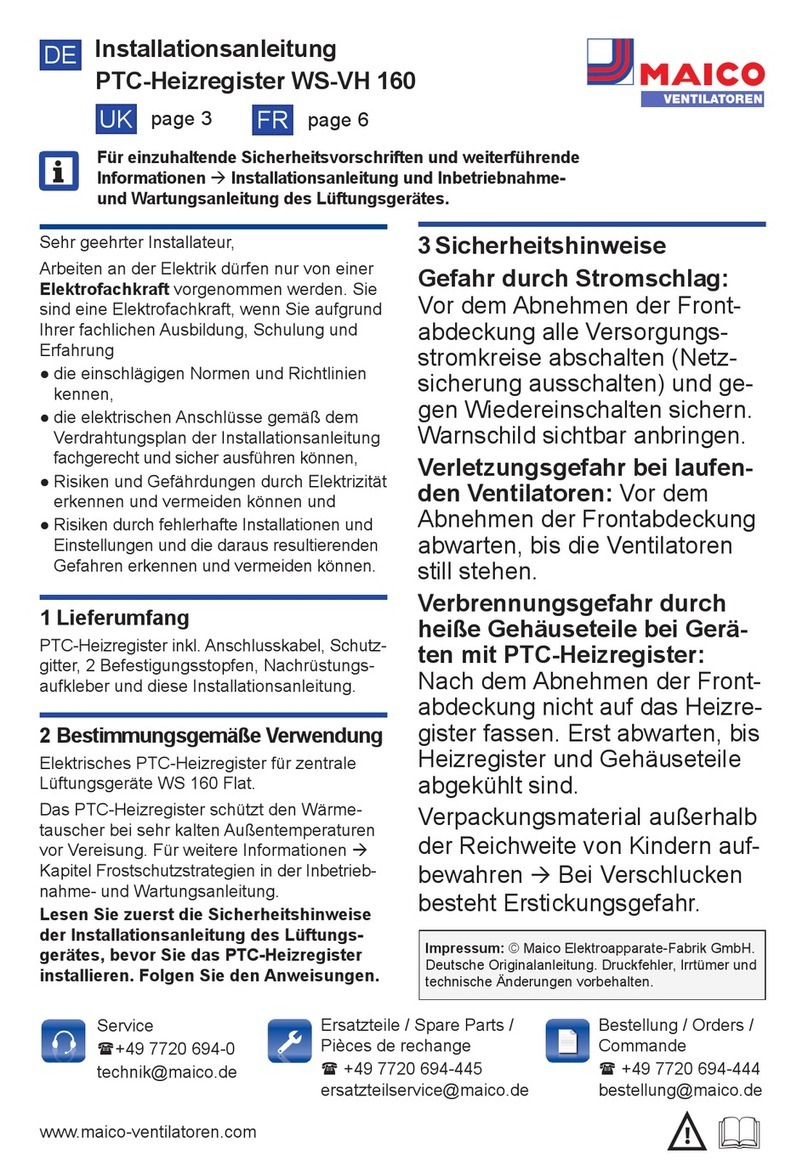
Maico
Maico WS-VH 160 installation instructions
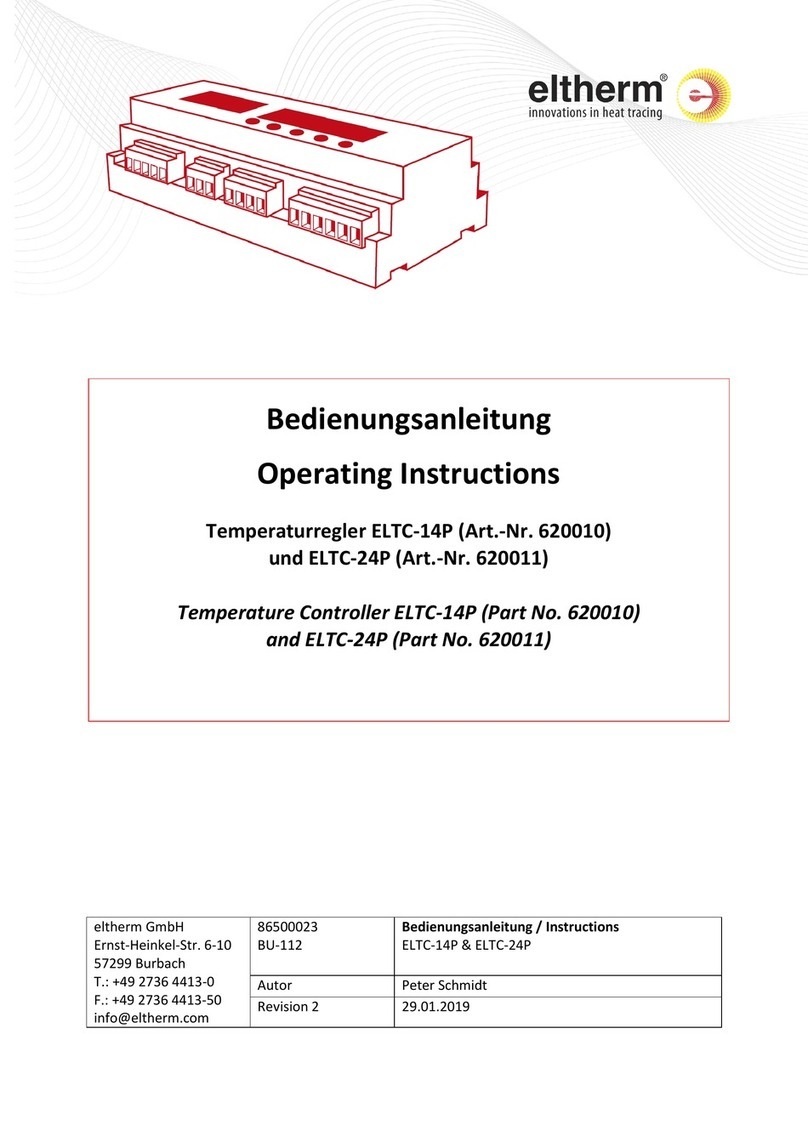
eltherm
eltherm ELTC-14P operating instructions
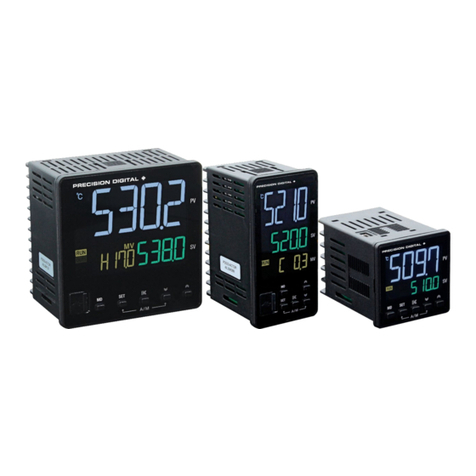
Precision Digital Corporation
Precision Digital Corporation SuperNova PD500 instruction manual
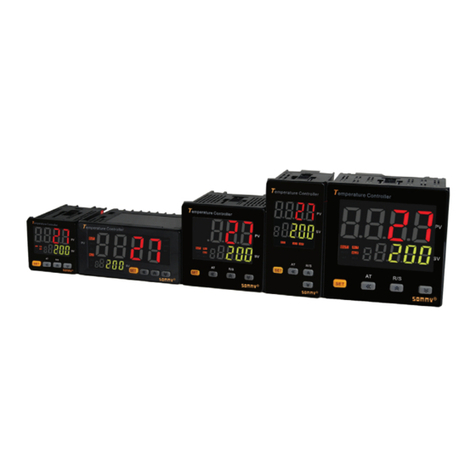
SOMMY
SOMMY TFY-A user manual

Berker
Berker 204620 Series operating instructions