STR Electronics Talon SRX User manual

217-8080
Talon SRX - User’s Guide
crosstheroadelectronics.com vexpro.com
Copyright 2017, Cross The Road Electronics, VEX Robotics Inc.
Updated: 2017-02-03
1
Talon SRX –User’s Guide
Cross The Road Electronics
www.crosstheroadelectronics.com

217-8080
Talon SRX - User’s Guide
crosstheroadelectronics.com vexpro.com
Copyright 2017, Cross The Road Electronics, VEX Robotics Inc.
Updated: 2017-02-03
2
Table of Contents
The Talon SRX at a Glance:.................................................................................................................4
Electrical/Mechanical Specs: ................................................................................................................5
1. Installing a Talon SRX ......................................................................................................................7
1.1. Wiring the Motor Output..............................................................................................................7
1.2. Wiring the Power Input ...............................................................................................................7
1.3. Wiring the Talon SRX Signal Input .............................................................................................8
1.3.1. Configuring a Talon SRX with CAN bus on a roboRIO........................................................8
1.3.2. Wiring the Talon SRX for use with CAN bus......................................................................10
1.3.3. Wiring Talon SRX for PWM Control...................................................................................12
1.3.4. Firmware requirements (PWM and CAN bus)....................................................................14
1.4. Wiring Sensors to the Talon SRX.............................................................................................17
1.4.1. Data Port Pinout.................................................................................................................17
1.4.2. Analog Input.......................................................................................................................18
1.4.3. Quadrature Encoder Input .................................................................................................19
1.4.4. Forward & Reverse Limit Switch Inputs.............................................................................20
1.4.5. Connecting to the Data Port...............................................................................................22
1.4.6. Encoder (and Limit Switch) Breakout.................................................................................23
1.4.7. Analog 5V Encoder (and Limit Switch) Breakout ...............................................................25
1.4.8. Heat Shrink Use with Breakout..........................................................................................26
1.5. Mounting the Talon SRX...........................................................................................................27
1.6. General Robot Wiring Guidelines .............................................................................................27
1.7. Applying Power for the First Time.............................................................................................28
2. Additional Information .....................................................................................................................29
2.1. Brake & Coast Modes...............................................................................................................29
2.1.1. Switching Between Brake & Coast Using the B/C CAL Button:.........................................29
2.1.2. Switching Between Brake & Coast Using CAN bus:..........................................................29
2.1.3. Switching Between Brake & Coast Using CAN Control Frames........................................29
2.2. PWM Calibration.......................................................................................................................30
2.2.1. To Calibrate the Talon SRX:..............................................................................................30

217-8080
Talon SRX - User’s Guide
crosstheroadelectronics.com vexpro.com
Copyright 2017, Cross The Road Electronics, VEX Robotics Inc.
Updated: 2017-02-03
3
2.2.2. To Restore Default Calibration:..........................................................................................31
2.3. Blink Codes...............................................................................................................................32
2.3.1. Blink Codes –Damaged Hardware....................................................................................33
2.4. Performance Data.....................................................................................................................34
2.5. Frequently Asked Questions:....................................................................................................35
3. Troubleshooting..............................................................................................................................39
4. Compliance.....................................................................................................................................43
5. Revision History:.............................................................................................................................44

217-8080
Talon SRX - User’s Guide
crosstheroadelectronics.com vexpro.com
Copyright 2017, Cross The Road Electronics, VEX Robotics Inc.
Updated: 2017-02-03
4
Talon SRX –User’s Guide
The Talon SRX is a speed controller designed through collaboration between VEX Robotics
(VEX.com) & Cross the Road Electronics (crosstheroadelectronics.com) that allows fine control and
high performance of brushed DC motors in competition robotics applications. The Talon SRX handles
high current loads with minimal voltage drop and heat generation. Its linear output and Brake/Coast
options allow for precise motor control, making it well suited for everything from drivetrains to shooter
wheels.
The Talon SRX’s Data Port and CAN bus features make it the most capable motor controller
available for competition robotics. The Data Port allows Quadrature Encoders, Limit Switches and
Analog Sensors to be connected directly to the motor controller. Sensors that are connected through
the Data Port are directly processed by the Talon SRX, freeing up resources in the primary robot
controller for more complex user code. When using CAN bus, up to 63 Talon SRXs can communicate
with the primary robot controller for tasks like field-upgrade, Data Port Configuration, dynamic
Brake/Coast toggling, and motor control.
The lightweight aluminum case was designed using extensive Finite Element Heat Transfer Analysis
(FEHTA). The result is a fully sealed design that makes fans optional. This, combined with a 3.25 sq.
in footprint, a variety of built-in mounting options, and super-flexible/high-strand-count leads, makes
installation a breeze.
The Talon SRX at a Glance:
(M-)
Signal
Wires
Data Port
Positive
Output
(M+)
Positive Input
(V+)
Signal
Wires
Output GND
(M-)
Status
LEDs
B/C Cal
Button
Input GND
(V-)

217-8080
Talon SRX - User’s Guide
crosstheroadelectronics.com vexpro.com
Copyright 2017, Cross The Road Electronics, VEX Robotics Inc.
Updated: 2017-02-03
5
Electrical/Mechanical Specs:
Talon SRX Specs
Outside Dimensions
2.75” x 1.185” x 0.96”
[69.9mm x 30.2mm x 24.4mm]
Weight
0.23 lbf [0.10 kgf] (excluding wiring)
Supported Communication
Protocols
PWM, DWCAN bus (1Mbps)
Nominal Voltage
12V
Min/Max Voltage
6 –28V
Continuous Current
60A
Surge Current (2 sec)
100A
PWM Input Pulse
(High Time)
1 –2 ms Nominal
0.6 –2.4ms max
PWM Input Rate (Period)
2.9 –100ms
PWM Output Chop Rate
(Switching Frequency)
15.625 kHz
Minimum Throttle (Dead band)
4%
PWM Logic High
Min Voltage Threshold
1V
PWM Logic Low
Max Voltage Threshold
0.4V
PWM Input Min Current
< 1mA
Max Quadrature CPR(1)
80,000,000 / Peak RPM
Max Quadrature RPM(1)
80,000,000 / CPR
Logic High
Min Input Voltage
Quad A/B/Idx/Limit Fwd/Rev
2.64V
Logic Low
Max Input Voltage
Quad A/B/Idx/Limit Fwd/Rev
0.66V
Min/Max Voltage
Analog Input
0 –3.3V
Min/Max Voltage
Quad A/Limit Fwd/Rev
0 –5V
Min/Max Voltage
Quad B and Quad Idx
0 –3.3V(2)(Talon revision 1.5 and earlier)
0 –5V (Talon revision 1.6 and on)
Data Port Max Current
3.3V (pin1) : 33mA
5V (pin2) : 50mA
Note 1: This is based on the maximum quadrature edge-to-edge rating of 187.5ns.
Note 2:A late errata on the microcontroller was released after Talon SRX 2015 season production, indicating the Quad B and Quad Idx are
not 5V tolerant. As a result, Talons with revision 1.5 (and earlier) should not use sensor cable/breakouts that allow >3.6V on Quad B or Quad
Idx, as this may damage Talon SRX. See Talon SRX Software Reference Manual (Section 2) for how to detect Hardware Revision. See
Section 1.4.6.1 for the updated breakout solution.

217-8080
Talon SRX - User’s Guide
crosstheroadelectronics.com vexpro.com
Copyright 2017, Cross The Road Electronics, VEX Robotics Inc.
Updated: 2017-02-03
6
The power inputs and outputs of the Talon SRX are indicated by markings on the housing.
They are also shown in the table below:
Wire
Case
Marking
Wire Color
Wire Gauge
Wire Length
± 0.25in [6.35mm]
Positive Input
V+
Red
12 AWG
(600 strand min)
5.5in [139.7mm]
Input Ground
GND
Black
12 AWG
(600 strand min)
5.5in [139.7mm]
Positive Output
M+
White
12 AWG
(600 strand min)
5.5in [139.7mm]
Output Ground
M-
Green
12 AWG
(600 strand min)
5.5in [139.7mm]
CAN-High/
PWM Signal
None
Yellow
22 AWG
11.0in [279.4mm]
CAN-Low/
PWM Ground
None
Green
22 AWG
11.0in [279.4mm]
Note: There are (2X) yellow and (2X) green 22AWG signal wires on each Talon SRX. Signal wires of
the same color are electrically identical.

217-8080
Talon SRX - User’s Guide
crosstheroadelectronics.com vexpro.com
Copyright 2017, Cross The Road Electronics, VEX Robotics Inc.
Updated: 2017-02-03
7
1. Installing a Talon SRX
Wiring a speed controller has never been easier than with the Talon SRX. By following a few quick
steps, your robot will be up and running in no time.
1.1. Wiring the Motor Output
Connect the white wire to the M+ side of the motor and the green wire to the M- side of the motor
using tightly crimped connectors.
If the motor’s inputs are not marked, the polarity of the input may be chosen by the user. Be sure to
connect the output wires to motors with consistent polarity so each motor will rotate the same
direction when given the same PWM signal. Reversing the output wire connections will result in the
motor rotating the opposite direction when given the same PWM signal.
In many cases, the output leads of the Talon SRX will not be long enough to reach the motor it is
controlling, so an extension cable will be required. Extension cables should be made using
appropriately sized wire and connected using tightly crimped connectors.
Note: For the most robust connection, it is highly recommended that all connectors are crimped and
soldered.
1.2. Wiring the Power Input
WARNING: TO MAXIMIZE PERFORMANCE, THE TALON SRX DOES NOT INCLUDE
REVERSE POLARITY PROTECTION. IF POWER IS APPLIED BACKWARDS, THE
TALON SRX MAY BE PERMANENTLY DAMAGED.
To power the Talon SRX, connect the positive input (red) wire to the selected positive terminal of the
Power Distribution Panel (PDP), and the input ground (black) wire to the corresponding ground
terminal. In many cases, the Talon SRX may be wired directly to the robot’s PDP without extension
cables –this is preferable since it reduces the number of electrical connections. If the robot’s design
does not allow for a direct connection to the PDP, extension cables may be used.
Always keep good electrical practices in mind when designing a robot's electrical system. The Talon
SRX’s source voltage should never exceed 28V. In addition, a 40A or smaller breaker should be
used in series with the Talon SRX’s positive input.

217-8080
Talon SRX - User’s Guide
crosstheroadelectronics.com vexpro.com
Copyright 2017, Cross The Road Electronics, VEX Robotics Inc.
Updated: 2017-02-03
8
1.3. Wiring the Talon SRX Signal Input
The Talon SRX is capable of being controlled using either CAN bus or a PWM signal. Each input type
has its own pros and cons that should be carefully considered before wiring and programming.
The CAN bus capability of the Talon SRX is one of its most powerful features. It allows up to 63 Talon
SRXs to be daisy chained –this means Talon SRXs can plug into each other and only require a
single output on the primary robot controller. CAN bus also allows two-way communication between
the Talon SRX and the robot controller, which enables tasks like field-upgrade, Data Port
configuration, dynamic Brake/Coast toggling, and motor control. When using CAN bus, sensors that
are connected to the Data Port are monitored by the Talon SRX meaning that the primary robot
controller has more processing power to devote to other tasks.
One of the simplest ways to control a Talon SRX is using a Pulse Width Modulation (PWM) signal.
Unlike CAN bus control, using PWM requires that each Talon SRX must be individually connected to
a different output on the system’s primary robot controller –Talon SRXs cannot be daisy chained in
PWM mode. When using PWM to control the Talon SRX, only limit switches (or equivalent binary
switches) may be used with the Data Port. Encoders or Analog sensors cannot be used.
1.3.1. Configuring a Talon SRX with CAN bus on a roboRIO
Talon SRX automatically detects CAN bus traffic so there is no need to select “CAN” vs “PWM”. The
only configuration that is necessary is assigning Device IDs to prevent common-ID Talons (more than
one Talon with the same device ID). This is a common problem condition that prevents reliable
communication between the primary robot controller and other CAN devices.
However the roboRIO Web-based Configuration page is tolerant of common-ID Talons to a degree
(up to typically five or less common-ID Talons), so you can discover, firmware update, modify settings,
and change the device ID of a common-ID Talon to an unused device ID. More information can be
found in the Software Reference Manual.

217-8080
Talon SRX - User’s Guide
crosstheroadelectronics.com vexpro.com
Copyright 2017, Cross The Road Electronics, VEX Robotics Inc.
Updated: 2017-02-03
9
Another option is to explicitly ensure each Talon SRX has a unique ID assigned to it prior to wiring the
entire CAN bus harness. To do this, connect a yellow signal wire to the NI roboRIO CAN terminal
marked “H” and connect a green signal wire to the NI roboRIO CAN terminal marked “L” as shown in
the figure below. Connect the remaining green and yellow signal wires using a 120 Ω resistor as
shown in the figure below. Alternatively the Power Distribution Panel’s CAN interface can be wired
instead of a 120 Ω resistor since the PDP has an integrated resistor.
After the Talon SRX has been connected to the roboRIO, ensure there are no shorts, then apply
power and use the roboRIO Web-based Configuration page to assign the Talon SRX a unique ID.
TIP: Avoid using the default ID “0”, this makes adding new default Talons easier. The unique
ID is a 6-bit number; valid numbers are from 1 to 62. After the unique ID has been assigned, remove
power and repeat the process for each Talon SRX.
WARNING: When applying power to the Talon SRX for programming its unique ID, it may be
tempting to connect it directly to a 12V robot battery without a breaker –this is NOT recommended. If
the temporary power connectors short without a breaker protecting the wires, there is a high risk of an
electrical fire.
To CAN “L” Terminal
120 Ω
Resistor
or PDP
To CAN “H” Terminal

217-8080
Talon SRX - User’s Guide
crosstheroadelectronics.com vexpro.com
Copyright 2017, Cross The Road Electronics, VEX Robotics Inc.
Updated: 2017-02-03
10
1.3.2. Wiring the Talon SRX for use with CAN bus
To wire CAN bus, connect a yellow signal wire to the CAN terminal marked “H” on the NI roboRIO
and connect a green signal wire to the CAN terminal marked “L” on the NI roboRIO.
To connect additional Talon SRXs, use tightly crimped connectors to connect the signal wires green-
to-green & yellow-to-yellow as shown below. For the best connection, it is highly recommended that
each connector is crimped and soldered. The yellow and green wires should also be wrapped in a
twisted pair fashion (not illustrated) to maximize tolerance to electrical noise.
Note: Signal wires of the same color are electrically identical –it does not matter which wire is used
as long as the color is correct.
After all of the Talon SRXs have been wired, there will be 2 remaining signal wires –connect these
two wires using a 120Ω resistor or to the CAN interface on the Power Distribution Panel (PDP) to
properly terminate the cable end.
120 Ω
Resistor
or PDP
To CAN “H” Terminal
To CAN “L” Terminal

217-8080
Talon SRX - User’s Guide
crosstheroadelectronics.com vexpro.com
Copyright 2017, Cross The Road Electronics, VEX Robotics Inc.
Updated: 2017-02-03
11
1.3.2.1. CAN Connector
The CAN Connector can be used to chain Talon SRX’s together without crimping connectors or
soldering. Each CAN Connector contains a four channel Weidmuller terminal block with two CAN
pairs (similar to other FRC CAN devices such as the Power Distribution Panel and Pneumatic Control
Module). The four holes can be used to provide strain relief to the CAN wires. Additionally the holes
can be used for mounting to the robot frame. Spacers or electrical tape may be used to prevent
shorting to the robot frame.
1.3.2.2. CAN Bus Wire Selection
Teams should consult the FRC game rules for CAN wiring requirements. However it is
recommended to use yellow for CANH and green for CANL for the following reasons…
Makes robot inspection and troubleshooting easier.
The colors match what is labeled on the FRC Robot Controller, Power Distribution Panel,
and Pneumatic Control Module.
The colors match the Talon SRX cable harness.
AWG 22 or similar gauge wiring can be used. An electric drill can be used to twist the CANH/CANL
wire pair.

217-8080
Talon SRX - User’s Guide
crosstheroadelectronics.com vexpro.com
Copyright 2017, Cross The Road Electronics, VEX Robotics Inc.
Updated: 2017-02-03
12
1.3.3. Wiring Talon SRX for PWM Control
Before the Talon SRX can be controlled using a PWM signal, a standard 3-pin (0.1in pitch) PWM plug
must be connected to the Talon SRX’s signal wires. This can be done in one of two ways:
PWM housings and pins or sockets may be assembled directly on the Talon SRX’s
signal cables. If many Talon SRXs are being wired, this option will be cheaper but may
be more difficult for inexperienced users and may have a higher initial investment due
to the need of a specialized crimper.
A pre-assembled PWM cable may be cut and spliced onto the Talon SRX’s signal
wires. This option is more expensive if many Talon SRXs are being wired, but may be
easier for inexperienced users and may require a smaller initial investment.
In either case, the PWM cable should be wired such that the green (PWM ground) and yellow (PWM
signal) wires are on the outside of the PWM connector, as shown below. The center pin requires no
wire.
When purchasing components, be sure to order the correct gender PWM connector –different control
systems require different genders of PWM connectors. (The NI roboRIO requires a female PWM
connector.)
Only (2X) of the (4X) signal wires are needed to control the Talon SRX with PWM. Do Not connect
(2X) PWM connectors to a single Talon SRX. The (2X) wires that are not used for PWM control
should be electrically isolated using tape or heat shrink tubing and neatly bundled out of the way to
prevent damage.
Note: Signal wires of the same color are electrically identical –it does not matter which wire is used
as long as the color is correct.
After a PWM connector is installed, the Talon SRX will readily interface with the NI roboRIO and
many other microcontrollers. The PWM signal used to control the Talon SRX must be between 1-2ms
in duration with a center (neutral) pulse of 1.5ms and a period between 2.9-100ms.
Female 3-pin plug
required for NI roboRIO
Standard Male 3-pin
Extension Cable
Standard female 3-pin
Extension Cable
Male 3-pin plug required
for some control
systems

217-8080
Talon SRX - User’s Guide
crosstheroadelectronics.com vexpro.com
Copyright 2017, Cross The Road Electronics, VEX Robotics Inc.
Updated: 2017-02-03
13
Multiple Talon SRXs may be driven using a single PWM signal if a Y-Cable equivalent is used to
connect multiple PWM inputs to a single PWM output.
Note: The PWM period is how fast the robot controller can send a new PWM pulse. The amount of
time between the rising edges of two subsequent PWM pulses should not be less than 2.9ms nor
greater than 100ms.
Note: The PWM input has a logic-high minimum threshold voltage of 1.0 V. The logic-low maximum
threshold is 0.4 V. The PWM input current requirements are negligible (<1mA). This is sufficient for
most 3.3V and 5V based microcontrollers that generate PWM.
Connecting a Talon SRX to an NI roboRIO using PWM:
To connect a Talon SRX to the NI roboRIO controller, simply plug the Talon SRX’s PWM cable into
the desired PWM header in the roboRIO’s PWM output with the yellow (signal) wire on the “S” or
“inside” of the controller. The green wire will connect to the “GND” or “outside” of the controller. If an
extension cable is needed for the Talon SRX to reach the roboRIO, a standard 3-wire extension cable
should be used –these extension cables are available from VEX Robotics as well as many other
online retailers.

217-8080
Talon SRX - User’s Guide
crosstheroadelectronics.com vexpro.com
Copyright 2017, Cross The Road Electronics, VEX Robotics Inc.
Updated: 2017-02-03
14
1.3.4. Firmware requirements (PWM and CAN bus)
Typically a Talon is shipped with firmware version 0.28. Teams should always check the FRC game
rules to determine what is the required minimum firmware version for Talon SRX (PWM / CAN bus).
Teams that utilize CAN bus will likely want to field-upgrade to the latest available firmware for the
latest features and improvements (1.1 or newer). Instructions can be found in the Software
Reference Manual. Additionally teams may need to field-upgrade to meet the minimum firmware
version in the FRC game rules.
Teams that utilize PWM may still require a firmware update if an out-of-the-box Talon has older
firmware than 0.28. Firmware that predates 0.28 will have these symptoms:
Press and holding B/C CAL Button will not enter calibration mode (red/green LED
blink).
Limit switch features not present (closing limit switches has no impact).
Boot up sequence will illuminate the B/C CAL Button for ~500ms.
1.3.4.1. PWM - Checking firmware version
As a result, it is recommended that teams using PWM first determine if a Talon has adequate
firmware by press and holding the B/C CAL button and confirming that the Talon enters calibration
mode (LEDs will blink a red/green pattern). See Section 2.2.1 for full procedure on entering
calibration mode.
IMPORTANT --- Do not drive the Talon while performing these steps unless you deliberately want to
recalibrate your Talon. For this reason, it’s best to perform this check while robot is disabled. As a
result, when you release the B/C CAL button, the Talon will blink red, indicating that it did not modify
the calibration data.
If the Talon does enter calibration mode (does blink red/green) then it has adequate firmware for
complete PWM functionality and no more steps are necessary (however FRC legality should be
checked against the game rules).
If the Talon instead just changes the brake LED (brake vs. coast) and does not enter calibration
mode then it needs to be updated once using CAN bus. See Section 1.3.4.2 for a simplified
procedure on how to do this.
Additional functional limitations of the “ship” firmware may be found in section 21 of the Talon SRX
Software Reference Manual. Although most of the limitations relate to CAN bus features, it is
recommended that teams always check section 21 for additional functional limitations that may affect
them.

217-8080
Talon SRX - User’s Guide
crosstheroadelectronics.com vexpro.com
Copyright 2017, Cross The Road Electronics, VEX Robotics Inc.
Updated: 2017-02-03
15
1.3.4.2. PWM –Updating firmware for PWM use.
If the steps in Section 1.3.4.1 reveals that a Talon intended for PWM use has too-old firmware, field
upgrading a Talon can be done quickly with the following procedure...
Power off robot and disconnect Talon SRX from roboRIO’s PWM port if it’s connected.
Locate the free yellow/green CAN wire pair from the Talon. Since PWM-use only
requires one yellow/green wire pair, the other should be free to use.
If the roboRIO CAN bus port is in use, disconnect the CAN bus wires to free the
roboRIO’s CAN bus port. This is done be pressing the Weidmuller connector buttons
on the roboRIO and pulling out the CAN bus wires.
Insert the Talon’s free yellow/green wire pair directly into the roboRIO’s CAN bus.
Note 1: Although CAN bus requires 120Ω resistor (or PDP) at each of the two
ends of the CAN bus, when connecting a single Talon to a roboRIO for the
specific purpose of updating a single Talon, you can likely skip terminating this
end. This is because the short bus length of a single Talon, and the 120Ω resistor
integrated in the roboRIO is generally sufficient for the purpose of this procedure.
This is convenient since in this specifc case, the Talon wire pair not connected to
the roboRIO’s CAN bus port will likely have a PWM connector crimped onto it.
Power the robot on and follow the firmware update steps in the Software Reference
Manual, Section “2.3 Firmware Field-upgrade a Talon SRX”. The attached Talon
will likely have a device ID of zero. Generally it’s best to update to the latest crf file.
Disconnect the Talon SRX from roboRIO CAN bus port. If there are additional Talons
to update, go back and re-perform this procedure. Although the roboRIO and Talon
Directly to roboRIO CAN “H” Terminal
120 Ω Resistor or PDP (Note 1)
Directly to roboRIO CAN “L” Terminal

217-8080
Talon SRX - User’s Guide
crosstheroadelectronics.com vexpro.com
Copyright 2017, Cross The Road Electronics, VEX Robotics Inc.
Updated: 2017-02-03
16
software does not require you to power cycle the robot before re-flashing each Talon,
making wire changes while the robot is powered is a risk factor for shorting. Use best
judgment on how to safely replace the upgraded Talon with the “next” Talon to field-
upgrade.
TIP: Robot Inspectors at competition will likely check your Talons using the same steps
documented here for firmware legality, so be sure to update your competition robot
Talons before the ship date for expedient robot inspection at competition.

217-8080
Talon SRX - User’s Guide
crosstheroadelectronics.com vexpro.com
Copyright 2017, Cross The Road Electronics, VEX Robotics Inc.
Updated: 2017-02-03
17
1.4. Wiring Sensors to the Talon SRX
1.4.1. Data Port Pinout
Sensors may be connected directly to the Talon SRX via the Data Port. The Talon SRX supplies the
voltage and ground to the sensor devices. Do not supply external voltages or ground into the Data
Port.
The Data Port accepts a 2x5 0.05 inch pitch keyed cable that is available from many online retailers
as well as VEX Robotics. The ribbon cable used by the Data Cable is very thin; as a result, some
teams may find a breakout board helpful when wiring sensors.
Note: Leave unused Data Port Pins floating.
+3.3V 1
Analog Input 3
Quadrature B 5
Quadrature A 7
X
2 +5V
4 Forward Limit
8 Reverse Limit
10 GND
X
9
Data Port Pinout
6 DO NOT CONNECT
Pin 1
Data Port
Quadrature Index

217-8080
Talon SRX - User’s Guide
crosstheroadelectronics.com vexpro.com
Copyright 2017, Cross The Road Electronics, VEX Robotics Inc.
Updated: 2017-02-03
18
1.4.2. Analog Input
Attach the analog sensor as shown. Do not connect the GND line elsewhere. Only use 3.3V as the
analog sensor voltage source. Although the figure explicitly shows a potentiometer, a 3.3V Analog
Encoder can also be wired similarly.
+3.3V 1
Analog Input 3
Quadrature B 5
2 +5V
10 GND
Quadrature A 7
X
Quadrature Index 9
4 Forward Limit
6 DO NOT CONNECT
Analog Sensor Input
X
8 Reverse Limit
Analog
Sensor

217-8080
Talon SRX - User’s Guide
crosstheroadelectronics.com vexpro.com
Copyright 2017, Cross The Road Electronics, VEX Robotics Inc.
Updated: 2017-02-03
19
1.4.3. Quadrature Encoder Input
Attach the Quadrature Encoder as shown. Do not ground the GND line elsewhere. Connect either
the 3.3V or 5.0V as required by your sensor. DO NOT CONNECT THE 3.3V OUTPUT TO THE 5V
OUTPUT.Some encoders may have an Index pin. Talon supports counting the rising edges on the
Index rail so that robot controller can react to it. However wiring index is not required for decoding the
position and velocity of the encoder.
X
Quadrature Index 9
(Not required)
+3.3V 1
Analog Input 3
Quadrature B 5
Quadrature A 7
2 +5V
4 Forward Limit
6 DO NOT CONNECT
8 Reverse Limit
10 GND
Quadrature Encoder Input
Quadrature
Encoder
Optional 10k Pull Up
Resistor if required by
sensor
X

217-8080
Talon SRX - User’s Guide
crosstheroadelectronics.com vexpro.com
Copyright 2017, Cross The Road Electronics, VEX Robotics Inc.
Updated: 2017-02-03
20
1.4.4. Forward & Reverse Limit Switch Inputs
Attach the Forward/Reverse Limit Switch as shown. Do not connect the GND elsewhere. The Talon
SRX provides a pull-up to 2.5v, so typically an external pull-up is not needed. Only use Talon SRX
3.3V or 5.0V power if an external pull-up is used. The default setting of “Normally Open” ensures an
“out of the box” Talon SRX functions even if no limit switch is connected. See the Software
Reference Manual to change the default Limit Switch behavior from “Normally Open”.
+3.3V 1
Analog Input 3
Quadrature B 5
Quadrature A 7
2 +5V
4 Forward Limit
6 DO NOT CONNECT
X
8 Reverse Limit
10 GND
Quadrature Index 9
Forward Limit Switch - Normally Open (default)
Forward Limit Switch - Normally Closed
+3.3V 1
Analog Input 3
Quadrature B 5
Quadrature A 7
2 +5V
4 Forward Limit
6 DO NOT CONNECT
X
8 Reverse Limit
10 GND
Quadrature Index 9
Table of contents
Popular Controllers manuals by other brands
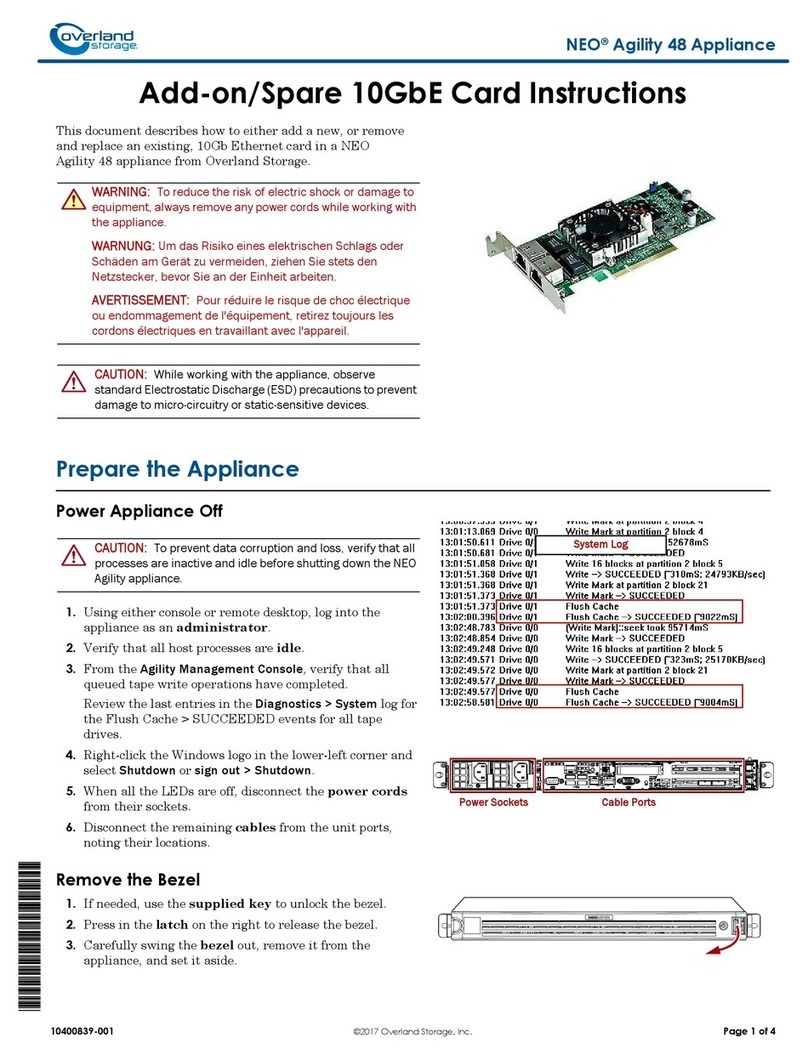
Overland Storage
Overland Storage NEO Agility 48 10GbE Card instructions

Danfoss
Danfoss AK-PC 560 user guide

Marshall Electronics
Marshall Electronics VS-PTC-50 user manual
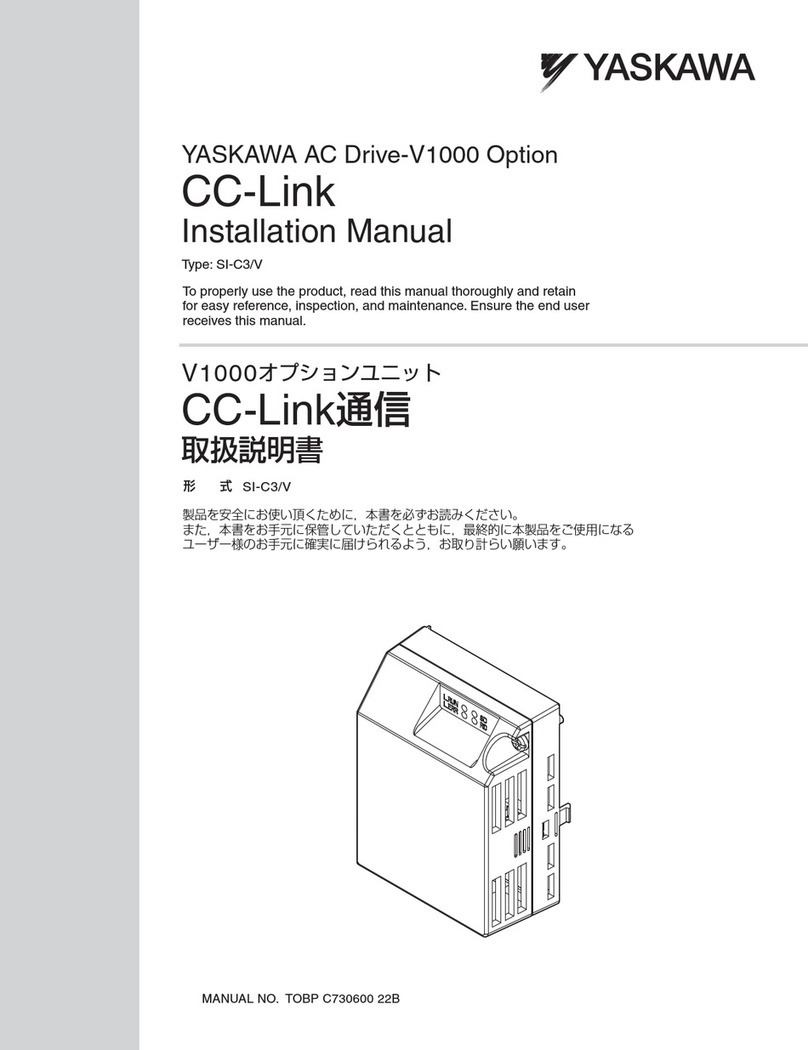
YASKAWA
YASKAWA PROFINET V1000 installation manual
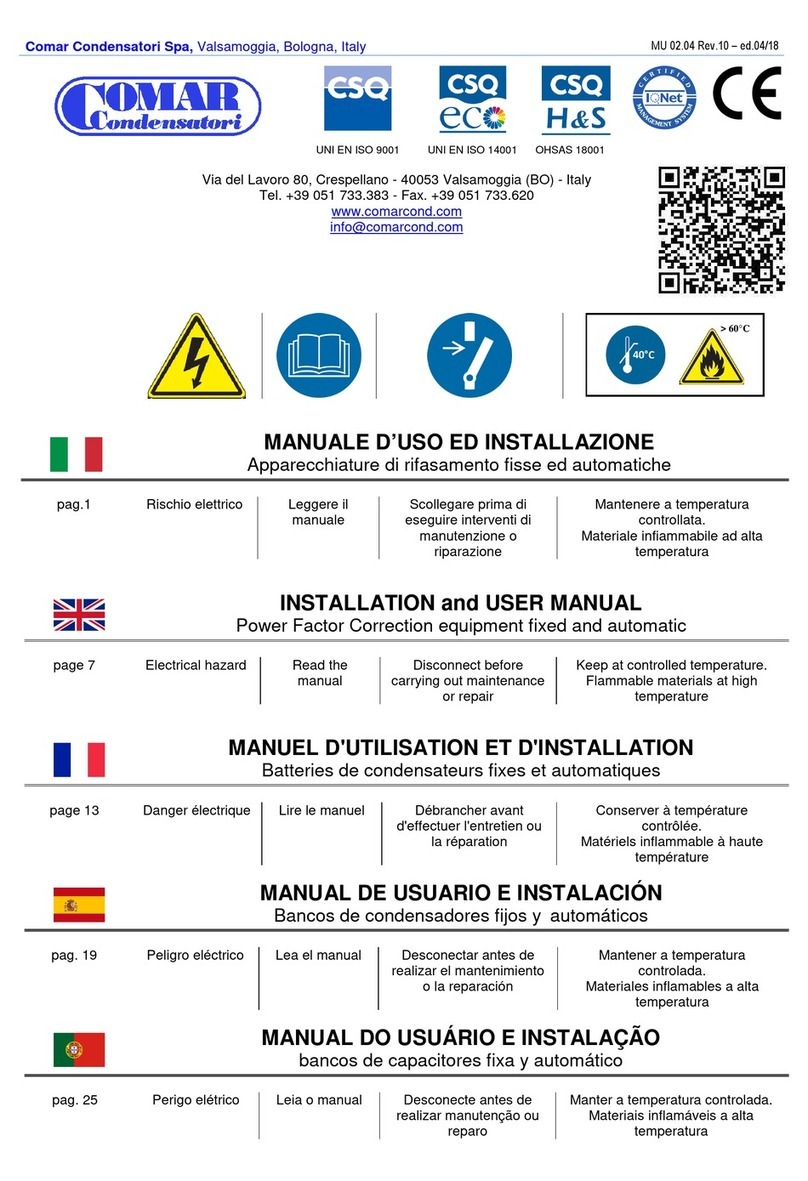
Comar Condensatori
Comar Condensatori BMR4 Installation and user manual

Tres
Tres 09286405 manual