SWR ENGINEERING SOLIDFLOW User manual

EN
SolidFlow
Monitoring of solids

Operating Instructions
2
CONTENTS Page
1. System Overview . . . . . . . . . . . . . . . . . . . . . . . . . . . . . . . . . . . . . . . . . . . . . . . . . . . . . . . . . . . . . . . . . . . . . . 3
2. Function . . . . . . . . . . . . . . . . . . . . . . . . . . . . . . . . . . . . . . . . . . . . . . . . . . . . . . . . . . . . . . . . . . . . . . . . . . 3
3. Safety . . . . . . . . . . . . . . . . . . . . . . . . . . . . . . . . . . . . . . . . . . . . . . . . . . . . . . . . . . .
. . . . . . . . . . . . . . . . . . . . 4
3.1 Regular Use . . . . . . . . . . . . . . . . . . . . . . . . . . . . . . . . . . . . . . . . . . . . . . . . . . . . . . . . . . . . . . . . . . . . . .
4
3.2 Identification of Dangers . . . . . . . . . . . . . . . . . . . . . . . . . . . . . . . . . . . . . . . . . . . . . . . . . . . . . . . . . . . . 4
3.3 Operational Safety . . . . . . . . . . . . . . . . . . . . . . . . . . . . . . . . . . . . . . . . . . . . . . . . . . . . . . . . . . . . . . . . . 4
3.4 Technical Progress . . . . . . . . . . . . . . . . . . . . . . . . . . . . . . . . . . . . . . . . . . . . . . . . . . . . . . . . . . . . . . . . . 4
4. Mounting and Installation . . . . . . . . . . . . . . . . . . . . . . . . . . . . . . . . . . . . . . . . . . . . . . . . . . . . . . . . . . . . . . 5
4.1 Delivery Range . . . . . . . . . . . . . . . . . . . . . . . . . . . . . . . . . . . . . . . . . . . . . . . . . . . . . . . . . . . . . . . . . . . . 5
4.2 Auxiliary . . . . . . . . . . . . . . . . . . . . . . . . . . . . . . . . . . . . . . . . . . . . . . . . . . . . . . . . . . . . . . . . . . . . . . . . . . 5
4.3 Mounting of the Sensor . . . . . . . . . . . . . . . . . . . . . . . . . . . . . . . . . . . . . . . . . . . . . . . . . . . . . . . . . . . . . 5
4.4 Mounting of the Evaluation Unit . . . . . . . . . . . . . . . . . . . . . . . . . . . . . . . . . . . . . . . . . . . . . . . . . . . . . . 8
4.5 Overview of the Optional Use of the C-Box . . . . . . . . . . . . . . . . . . . . . . . . . . . . . . . . . . . . . . . . . . . . 9
4.6 Use in Ex Hazard Array . . . . . . . . . . . . . . . . . . . . . . . . . . . . . . . . . . . . . . . . . . . . . . . . . . . . . . . . . . . . . 10
5. Electrical Connection . . . . . . . . . . . . . . . . . . . . . . . . . . . . . . . . . . . . . . . . . . . . . . . . . . . . . . . . . . . . . . . . . . 11
6. Commissioning . . . . . . . . . . . . . . . . . . . . . . . . . . . . . . . . . . . . . . . . . . . . . . . . . . . . . . . . . . . . . . . . . . . . . . . 12
7. Menu Structure of SolidFlow . . . . . . . . . . . . . . . . . . . . . . . . . . . . . . . . . . . . . . . . . . . . . . . . . . . . . . . . . . . 14
8. Menu Parameters . . . . . . . . . . . . . . . . . . . . . . . . . . . . . . . . . . . . . . . . . . . . . . . . . . . . . . . . . . . . . . . . . . . . . 16
9. Connection Examples . . . . . . . . . . . . . . . . . . . . . . . . . . . . . . . . . . . . . . . . . . . . . . . . . . . . . . . . . . . . . . . . . 25
9.1 Digital Input . . . . . . . . . . . . . . . . . . . . . . . . . . . . . . . . . . . . . . . . . . . . . . . . . . . . . . . . . . . . . . . . . . . . . . 25
9.2 Impulse Output . . . . . . . . . . . . . . . . . . . . . . . . . . . . . . . . . . . . . . . . . . . . . . . . . . . . . . . . . . . . . . . . . . . 25
10. Additional Information for the Use of FME 300 Unit with a C3-Box . . . . . . . . . . . . . . . . . . . . . . . . . 26
11. Maintenance . . . . . . . . . . . . . . . . . . . . . . . . . . . . . . . . . . . . . . . . . . . . . . . . . . . . . . . . . . . . . . . . . . . . . . . . . 28
12. Warranty . . . . . . . . . . . . . . . . . . . . . . . . . . . . . . . . . . . . . . . . . . . . . . . . . . . . . . . . . . . . . . . . . . . . . . . . . . . . 28
13. Trouble Shooting . . . . . . . . . . . . . . . . . . . . . . . . . . . . . . . . . . . . . . . . . . . . . . . . . . . . . . . . . . . . . . . . . . . . . 28
14. Technical Data . . . . . . . . . . . . . . . . . . . . . . . . . . . . . . . . . . . . . . . . . . . . . . . . . . . . . . . . . . . . . . . . . . . . . . . 29
15. Quick Start Guide. . . . . . . . . . . . . . . . . . . . . . . . . . . . . . . . . . . . . . . . . . . . . . . . . . . . . . . . . . . . . . . . . . . . . 30

Operating Instructions
3
Sensor
1. System Overview
Overview of the measuring system:
Fig. 3: Coupling and reflection of the microwaves.
and evaluation unit
2. Function
•SolidFlow is a measuring system especially developed for measuring the flow rate of conveyed solids in
metallic ducts.
•The SolidFlow sensor is based on the newest microwave technology. The sensor is usable in metal
ducts. Through the coupling of the microwave in the duct it is created a homogenous measured field.
•The microwave energy is being reflected by the solid particles and received by the sensor. These signals
are evaluated in frequency and amplitude.
•Because of the selective frequency evaluation only moving particles are measured.
•The measuring signal is independent of pressure and temperature in the duct. A measuring unit
consists of one sensor and the evaluation unit.

Operating Instructions
4
3. Safety
The measuring system SolidFlow was designed, built and tested to be safe and was shipped in safe conditions.
Nevertheless persons or objects may be endangered by components of the system if these are operated in an
inexpert manner. Therefore the operational instructions must be read completely and the safety notes must be
followed.
In case of inexpert or irregular use, the manufacturer will refuse any liability or guarantee.
3.1 Regular Use
•The measuring system must be installed for measuring the flow rate in metallic ducts only.
Other usage and modifications of the measuring system are not permitted.
•Only original spare parts and accessories of SWR engineering must be used.
3.2 Identification of Dangers
•Possible dangers when using the measuring system are marked by the following symbols in the
operating instructions:
Warning!
•This symbol in the operating instructions marks actions, which may represent a danger for life and limb
of persons when carried out in an inexpert manner.
Attention!
• All actions which may endanger objects are marked with this symbol in the operating instructions.
3.3 Operational Safety
•The measuring system must be installed by trained and authorised personnel only.
•Switch of the supply voltage for all maintenance, cleaning or inspection works on the tubes or on
components of the SolidFlow. Follow the notes of the chapter maintenance.
•Before hot-work the sensor must be removed from the piping.
•The components and electrical connections must be checked for damages regularly. If a damage is
found, it is to repaired before further operation of the instruments.
3.4 Technical Progress
•The manufacturer reserves the right to adapt technical data to the technical progress without particular
advance notice. If you have any questions, SWR engineering will be pleased to inform you on possible
changes and extensions of the operating instructions.

Operating Instructions
5
4. Mounting and Installation
4.1 Delivery Range
•Evaluation unit in the housing
•Weld on sensor accommodation
•Sensor (union nut, distance washers, seal-ring for adjustment)
•Operating instructions
•C-Box (optional)
4.2 Auxiliary
•Drill Ø 20 mm for steel
•32 mm wrench for union nut
•Pliers for circlips (Ø 20 mm) for adjusting the wall thickness at the sensor
4.3 Mounting of the Sensor
The sensor is to be mounted as follows:
•Determine the place of mounting on the duct. On horizontal or inclined ducts the sensor should be
mounted from top.
•In case of duct diameters greater than Ø 200 mm or a special application one has to install up to three
sensors which are located 120 mm apart from each other and moved by 120° towards each other.
•The distances are valid for the vertical and horizontal installation position.
•Follow the necessary distances of valves, bows, fans or cellular wheel sluices etc. and also other
measurement devices like temperature and pressure etc. to the sensor. (see fig. 4)
Fig 4: Minimal distances of the sensor to duct bends and baffles.
•With free fall applications (e. g. after screw feeders or rotary valves) a free fall height of at least 300 mm
would be perfect.

Operating Instructions
6
•Weld the sensor accommodation on to the duct.
•Drill the Ø 20 mm hole into the duct. Please use your own drill as there are different shafts available.
Take care that the hole is in line and rectangular to the surface to avoid trouble by inserting the sensor.
Warning!
•After drilling you have to check, if there is a burr resulted at the drilling walls from the drilling. If so, this
burr in the duct must be removed with an appropriate tool. If this burr is not removed, a calibration of
the sensor is not possible!
•If the sensor is not installed immediately, the dummy plug must be put in until the sensor will be
installed (see fig. 5). Use a 32 mm wrench for tightening the union nut.
Fig. 5: Installation of the sensor
accommodation and the dummy plug.
Distance washer 1 mm
O-ring-type sealing
ring 36 x 3
Sensor accommodation
Union nut
Circlips for shafts
Dummy plug
q
q
q
q
q
q
q
•Fig. 5: Installation of the sensor accommodation and the dummy plug.
•It’s important that the sensor does not intrude into the duct because otherwise the front end of the
sensor will be worn by abrasion. If necessary the wall thickness must be checked with a depth gauge.
Then position the circlip in the complying slot. The sensor may be submerged into the duct wall by up to
1 mm without creating an error of measurement.
Wall thickness (mm) Circlip for shafts position Number of distance washers
3,0
4,0
5,5
6,5
8,0
9,0
10,5
11,5
13,0
14,0
1
1
2
2
3
3
4
4
5
5
2
1
2
1
2
1
2
1
2
1
•Now the sensor is put into the sensor accommodation and screwed with the union nut according to
figure 6a.

Operating Instructions
7
•Look at the POLARIZATION - label to adjust the sensor along to the duct, fig. 6b.
Fig. 6a: Installation of
sensor accommodation
and sensor.
Sensor accommodation
O-ring-type sealing ring 36 x 3
Distance washer 1 mm
Circlip for shafts 20 x 1.2
Distance washer 1 mm
Union nut
Sensor
q
q
q
q
q
q
q
1
2
• Lock the sensor with the union nut dust proof and fix the sensor.
Fig. 6b: Adjustment of the sensor.
▼
Flow direction
• Make sure you install a drip loop with the cable anywhere it may get wet to prevent
water flow from reaching the sensor.

Operating Instructions
8
Fig. 7: Field housing evaluation unit.
Fig. 8: Field housing C-Box (optional).
4.4 Mounting of the Evaluation Unit
•The whole electronic equipment can be installed at a maximum distance of 300 m from the sensor.
The housing is prepared for wall mounting.
90 120
244
254
237
Sensor Evaluation Unit
PG11
98
86
36
64

Operating Instructions
9
The C-Box is an useful optional extension, if the distance between the sensor and the evaluation unit exceeds
the given standard length of 2 meters. The C-Box contains additional safety devices and terminal resistors to
guarantee the communication over the ModBus between the sensor and the evaluation unit even over longer
distances.
Sensor C-Box Evaluation Unit
2 m cable
of the sensor
manufactures firmly
up to 300 m,
at sufficient conductor
cross section
4.5 Overview of the Optional Use of the C-Box

Operating Instructions
10
4.6 Use in Ex Hazard Array
Marking DustEx: II 1/2D Ex tD IP 65 T84 °C
Zone 20: 0 °C _< Tprozess _< 80 °C
Zone 21: -10 °C _< Tamb _< 60 °C
- Group of equipment 2
- Equipment category: 1/2
Waveguide window zone 20 / Housing zone 21
- For combustible mixtures from air and inflammable type of dust
- IP-Code 65
- Maximum surface temperature 84 °C with Ta = 60 °C
Marking GasEx: II 1/2D Ex tD A20/21 IP 65 T84 °C
II 2G Ex d IIC T5/T3
- Group of equipment 2
- Equipment category: 2
- Zone 1
- For combustible mixtures from air and inflammable type of gas
- IP-Code 65
- Allowable process temperature 0 to 150 °C
- Class of temperature T3
- Maximum surface temperature 84 °C with Ta = 60 °C
Ex hazard array
DustEx zone 20
GasEx zone 1
Zone 21/22
Zone 1/2
No ex hazard array
Tmax = 60 °C
Tmax =
150 °C

Operating Instructions
11
Evaluation Unit
Terminal No. Connection
Connection of the Supply Voltage
L / + 24 V Input Supply Voltage 230 V / 50 Hz, 110 V / 60 Hz (optional 24 V DC)
N / 0 V Input Supply Voltage 230 V / 50 Hz, 110 V / 60 Hz (optional 24 V DC)
PE Protected Earth
Sensor Connection
I-out + Analogue Output +
- Analogue Output -
NA not available
NA not available
Min. /
Max.-
Relay
NO Potential-free Relay NO (Close)
C Potential-free Relay COM (Common Conductor)
NC Potential-free Relay NC (Open)
RS 232
RX RS 232 Intersection Data
TX RS 232 Intersection Data
GND RS 232 Intersection Ground
D-out + Digital Output +
- Digital Output -
RS 485
B RS 485 Intersection Data B
A RS 485 Intersection Data A
GND RS 485 Intersection Ground
D-in1 + Digital Intersection 1 (+)
- Digital Intersection 1 (-)
D-in2 + Digital Intersection 2 (+)
- Digital Intersection 2 (-)
Sensor
+ Supply Voltage 24 V (+) Cable No. 1
- Supply Voltage 24 V (-) Cable No. 2
A RS 485 Data A Cable No. 3
B RS 485 Data B Cable No. 4
5. Electrical Connection
Fig. 9: Electrical connection

Operating Instructions
12
6. Commissioning
•For start-up the measurement system it is necessary to adjust the sensor to the local conditions. After
switching on the power supply there is at least a warm-up time about 15 minutes required before any
adjustment starts.
Please check again:
•The correct cabling between sensor and the evaluation unit.
•The correct adjustment of the wall thickness at the sensor.
•In case that despite these steps a successful measurement is impossible, please contact SWR.
Commissioning of SolidFlow
For start-up the sensor has to be calibrated and parameterized to each product, which will be
measured. It is necessary to assign the mass flow to the display and initial value. The menu functions
are mostly self-explaining. Following a short introduction to the overview:
By leaving the menu level and confirming the memory function in menu 8 all values changed are
transferred.
Starting The menu is started by an invisible key in the upper right corner of the
the Menu touch-screen-panel. Now press approx. 5 seconds until the menu
appears. If the temperature indication is activated, the button for the
temperature indication is in the upper right corner, in this case must be changed
into the temperature indication first, in order to be able to access the menu.
Basic Function It is sufficient to carry out a two-point-calibration (normally min and max).
Enter the data in menu 4.2.
Current / The initial values are defined in the menu points 1.5 and 1.6.
Voltage- The output value (current / voltage) is assigned to the measuring range here.
Output Standard 0 = 4 mA
Max = 20 mA
The measuring range filter is used for the adjustment to slower working devices
or for a continuous output of the analog output.
Min-Point Set point 1 to 0, with no material flow but system running.
Max-Point Set point 2 to known maximum flow rate with normal conveying and calibrate as
well. (This value can be adjusted later on.)
Thus the basic function of the measuring system is given and it is now ready for
operation.
Adjustment See menu 1, point 1 to 3 for the adjustments to the individual local conditions
regarding material, measuring units, etc.

Operating Instructions
13
Alarms entered by the user in menu 2.
Analog Output is modified in menu 3 and can be adjusted to the individual requirements.
(e. g. 0 - 20 mA)
Auxiliary Points The linearisation can be examined by measuring the varying mass throughput.
This should be weighed out in each single case for the improvement of the
accuracy. If there are deviations the non-linearity can be corrected by a basic
table. According to the chosen and fixed points in menu 4.2 (minimum 2 for the
first start-up of the commissioning), it is now possible to enter a correction value
for the actual mass flow. (This value can be changed afterwards.)
Pulse Output The pulse output can be parameterized to the value displayed in point 5 of the
menu. This is done by declaring the number of pulses per mass unit e. g.:
the mass unit is set to 1 t! The pulse output is set on 10.0 impulse / unit.
So there will be one pulse every 100 kg.
Note: please make sure that the indicated pulses do not exceed 50 pulses per
second. After changing the pulse configuration you will have to do a total reset
of the evaluation unit by interrupting the power supply a few seconds.
Otherwise the changing wouldn’t be activated.
Digital Input All digital inputs may be used for a reset of the totalizer.
System Adjustment of the ModBus by entering the “baud rate” and address.
Correction of the contrast and the delay of the backlight for ergonomics.
Totalizer With the totalizer function it is possible to monitor the entire flow rate since the
last reset of the totalizer. A RESET can be accomplished over an external control
line (see digital input) or directly over the display by pressing the R-symbol.
Storage When leaving the system you will be asked, if adjusted values should be stored
or not. By pressing ok the adjustment is done, by pressing n it will be rejected.
C-Box Will only be used, if the distance between the sensor and the evaluation unit
exceeds 2 meters.

Operating Instructions
14
Following the menu parameters in detail:
7. Menu Structure of SolidFlow
1. Measuring Range
1.1 Tag No Adjust Material (10 Digits)
1.2 Unit Adjust Text e. g. kg
1.3 Time Scale Choose: h / min / s
1.4 Decimal Point Choose Position of Dec. Point
1.5 Beginning of Measuring Range Range 0 ... 999
1.6 End of Measuring Range Range 0 ... 999
1.7 Filter Value Range 0.1 ... 999.9 s
2. Alarm
2.1 Type of Alarm Choose: Min / Max
2.2 Value of Alarm -10 to 110 % in phys. Units
2.3 Alarm Dead Time Range 0.1 ... 99.9 s
2.4 Alarm Hysteresis 0.1 ... 99.9 %
2.5 Operation Mode Choose: Working- / Static
Current Principle
2.6 Alarm Sensor Malfunction Choose: on / off
3. Analog Output
3.1 Beginning of Measuring Range Range: 0 ... 22 mA (Standard: 4 mA)
3.2 End of Measuring Range Range: 0 ... 22 mA (Standard: 20 mA)
3.3 MIN Point Range: 0 ... 22 mA (Standard: 3 mA)
3.4 MAX Point Range: 0 ... 22 mA (Standard: 20 mA)
3.5 Value of Alarm Range: 0 ... 22 mA (Standard: 3 mA)
3.6 Filter Time Range: 0.1 ... 99.9 s (Standard: 1 s)
3.7 Calibration: 4 mA Adjust Current Output
(4 mA calibrated)
3.8 Calibration: 20 mA Adjust Current Output
(20 mA calibrated)

Operating Instructions
15
4. Calibration
4.1 Calibration Factor Range 0.01 ... 9.99
4.2 Calibration Filter Range 0.1 ... 999.9 s
4.3 Number of Calibration Points Range 2 ... 20 Auxiliary Points
4.4 Calibration Range 0.1 ... 999.9 s
4.4.1 Calibration Point 1
Meas. Value
Range of Beginning -
End of Measuring Value
(in phys. Units)
4.4.2 Calibration Point 1 Raw Value Adjust Initial Value
. . . (depending on the no. of calibration points)
4.4.(2*N) Calibration Point N
Meas. Value
Range of Beginning -
End of Measuring Value
(in phys. Units)
4.4.(2*N+1) Calibration Point N Raw Value Adjust Initial Value
5. Impulse Output
5.1 Number of Impulses / Mass Unit Range 0.01 ... 99.9
6. Digital Input
6.1 Digital Input 1
6.1.1 Function Choose:
None / Totalizer Reset
6.1.2 Direction of Action Choose: Current / Without Current
6.1.3 Filter Time Range: 0.1 ... 99.9 s
6.2 Digital Input 2
6.2.1 Function Choose:
None / Totalizer Reset
6.2.2 Direction of Action Choose: Current / Without Current
6.2.3 Filter Time Range: 0.1 ... 99.9 s
7. System
7.1 Baudrate Choose: 4800 / 9600 / 19200 / 38400
7.2 ModBus-Address Range: 1 ... 255
7.3 Contrast Adjust Contrast
7.4 Language Choose: D / F / E
7.5 Backlight
Backlight Constant = 0
or Delay of Backlight in Minutes
Range 1 ... 99 min
7.6 Temperature Display Temperature Display On / Off
7.7 Total Counter Total Counter On / Off

Operating Instructions
16
8. Menu Parameters:
1. MEASURING RANGE
1.1 Tag No.
Freely selectable symbols
of the measuring medium - or place,
max. 10 digits.
With and select the letters or symbols
with and select place of the letter
(1 ... 10); with delete the respective letter and with transfer the entry and
leave the menu level.
1.2 Unit
Entry of the measuring range
max. 6 digits.
With and select the letters or symbols,
with and select the letter (1 ... 6),
with delete the respective letter and with
transfer the entry and leave the menu level.
1.3 Time Scale
Choose of the time unit is important for the
Totalizer - Choose h / min / s
/ s per second
/ min per minute
/ h per hour
With and select according to the
display, with leave the menu without any change, with transfer the entry
and leave the menu level.
1.4 Decimal Point
Adjust the digit in the display.
With and shift the comma.
is without function here and with
transfer the entry and leave the menu level.
1.5 Beginning of Measuring Range
Enter the respective value of the measuring
range you will start with. Usually 0.0.
With set the value to 0.0 to start enter the
numbers of the measuring range, with
transfer the entry and leave the menu level.
¡
£
Meas. Range £
Tag No.
¤
Material C
¡ ¢ 8
¤
¢
8
C
£
C
8
Meas. Range £
Time Scale
¤
h C
8
C8
C8
Meas. Range £
Decimal Point
¤
000.0 C
8
¤
£ ¤
£ ¤
Meas. Range £
Unit
¤
kg C
¡ ¢ 8
¢
¡
Meas. Range 7 8 9
Set low 4 5 6
0.0 kg/h 1 2 3
C 08
C
8

Operating Instructions
17
1.6 End of Measuring Range
Enter the respective value of the measuring
range end.
With set the value to 1.0 to start enter the
numbers of the measuring range, with
transfer the entry and leave the menu level.
1.7 Filter Value
Adjustable damping for the display in
seconds.
Range: 0.1 ... 999.9 s
With set the value to 0.0 to start enter the
numbers of the measuring range, with
transfer the entry and leave the menu level.
2. ALARM
Effect onto the relay
With and select according to your
significance, with leave the menu without
any change, with transfer the entry and
switch to a deeper menu level.
2.1 Type of Alarm
None / min / max.
With and select according to your
significance, with leave the menu without
any change, with transfer the entry and
switch to a deeper menu level.
2.2 Value of Alarm
Threshold value.
Range: -10 ... 110 % of the measuring range
in phys. units.
With leave the menu without any change,
with transfer the entry and leave the
menu level.
C
8
Meas. Range 7 8 9
Set high 4 5 6
10.0 kg/h 1 2 3
C 08
C
8
Meas. Range 7 8 9
Filter 4 5 6
1.0 s1 2 3
C08
C
8
C
8
£ ¤
Alarm 1 £
Alarm Type
¤
low alarm C
8
C
8
£ ¤
Alarm 7 8 9
Alarm Value
4 5 6
1.0 kg/h 1 2 3
C08
2. Alarm £
2.1 Type low alarm
¤
2.2 Value 1.0
2.3 Delay 0.1 s C
2.4 Hysteresis 1.0 %
8
q

Operating Instructions
18
2.3 Alarm Dead Time
Threshold value how long the value must be
over or under the limit until the alarm relay
reacts. Range
: 0.1 ... 99.9 s
With leave the menu without any change,
with transfer the entry and leave the
menu level.
2.4 Alarm Hysteresis
Threshold value of the alarm
Range
: 0.1 ... 99.9 % of the measuring range.
With leave the menu without any change,
with transfer the entry and leave the
menu level.
2.5 Operation Mode
Choice of the contact work or interruption.
NO - Working current
NC - Static current
With and select according to the
display, with leave the menu without any
change, with transfer the entry and leave the menu level.
2.6 Alarm Sensor Error
Reaction by sensor error to the alarm and
current output. On / Off
With and select according to the
display, with leave the menu without any
change, with transfer the entry and leave
the menu level.
3. ANALOG OUTPUT
With and select according to your
significance, with leave the menu without
any change, with transfer the entry and
switch to a deeper menu level.
3.1 Starting Range
Value for the output min
(standard 4 mA) - Range 0 ... 22 mA
With set the value to 0.0 to start enter the
numbers of the measuring range, with
transfer the entry and leave the menu level.
C
8
8
C
Alarm 7 8 9
Hysteresis
4 5 6
1.0 % 1 2 3
C08
Alarm 7 8 9
Delay
4 5 6
1.0 s 1 2 3
C08
Alarm £
Operation Mode
¤
NO C
8
Analog Output 7 8 9
Range set low
4 5 6
4.0 mA 1 2 3
C08
C
8
£¤
Alarm £
Sensor Fault
¤
on C
8
C
8
£ ¤
C
8
£ ¤
C
8
3. Analog Out £
3.1 set low 4.0 mA
¤
3.2 End 20.0 mA
3.3 Minimum 0.3 mA C
3.4 Maximum 21.0 mA
8
q

Operating Instructions
19
3.2 End of Range
Value for the output max.
(Standard 20 mA)
Range 0 ... 22 mA
With set the value to 0.0 to start enter the
numbers of the measuring range, with
transfer the entry and leave the menu level.
3.3 MIN-Limit
Value for the MIN-Limit
Range 0 ... 22 mA
(Standard 3.0 mA)
With set the value to 0.0 to start enter the
numbers of the measuring range, with
transfer the entry and leave the menu level.
3.4 MAX-Limit
Value for the MAX-Limit
Range 0 ... 22 mA
(Standard 20 mA)
With set the value to 0.0 to start enter the
numbers of the measuring range, with
transfer the entry and leave the menu level.
3.5 Threshold Value
Value for alarm (Sensor error or internal
alarm) at the same time Rel 3 goes down.
Range 0 ... 22 mA
(Standard 3 mA)
With set the value to 0.0 to start enter the
numbers of the measuring range, with
transfer the entry and leave the menu level.
3.6 Filter Time
Adjustable damping for the current output.
Range 0.1 ... 999.9 s
(Standard 1 s)
With set the value to 0.0 to start enter the
numbers of the measuring range, with
transfer the entry and leave the menu level.
C
8
Analog Out 7 8 9
Lower-Limit
4 5 6
3.0 mA 1 2 3
C08
Analog Out 7 8 9
Range set high
4 5 6
20.0 mA 1 2 3
C08
C
8
C
8
C
8
C
8
Analog Out 7 8 9
Upper-Limit
4 5 6
20.0 mA 1 2 3
C08
Analog Out 7 8 9
Threshold Value
4 5 6
3.0 mA 1 2 3
C08
Analog Out 7 8 9
Filter Time
4 5 6
3.0 s 1 2 3
C08

Operating Instructions
20
3.7 Trim 4 mA
Value of current min.
Adjust to the external measuring system
(if display differs).
With and adjust fast, with and
adjust slowly the current to 4 mA.
With transfer the entry and leave the menu level, with leave the menu
without any change.
3.8 Trim 20 mA
Value of current max. Adjust to the external
measuring system (if display differs).
With and adjust fast, with and
adjust slowly the current to 4 mA.
With transfer the entry and leave the menu
level, with leave the menu without any change.
4. Calibration
With and select according to your
significance, with leave the menu
without any change, with switch to
a deeper menu level.
4.1 Calibration Factor
Global calibration factor of the measuring
on the display and as well the output range
from 0.01 to 9.99 - Setting is 1.0
With set the value to 0.0 to start enter the
numbers of the measuring range, with
transfer the entry and leave the menu level.
4.2 Calibration Filter
Damping filter for setting unsteady signals
during the calibration.
(Has no effect on output and display)
0.1 to 999.9 s
With set the value to 0.0 to start enter the
numbers of the measuring range, with
transfer the entry and leave the menu level.
4.3 Number of
Calibration Points
Set the number of the auxiliary points:
2 ... 5 points.
With set the value to 0.0 to start enter the
numbers of the measuring range, with
transfer the entry and leave the menu level.
.
<<
8C
Analog Out
Trim 4.0 mA
C
<< < > >> 8
>>
<
>
<<
8
C
>> <
>
Analog Out
Trim 20.0 mA
C
< < > >> 8
8
Calibration 7 8 9
Cal.-Factor
4 5 6
1.0 1 2 3
C08
8
C
8
C
C
Calibration 7 8 9
Filter
4 5 6
1.0 s 1 2 3
C08
Calibration 7 8 9
Segment Points
4 5 6
21 2 3
C08
C
8
£ ¤
4. Calibration £
4.1 Cal. Factor 1.0
¤
4.2 Filter 0.1 s
4.3 Aux. Points 2 C
4.4 Calibration
8
1.0
Other manuals for SOLIDFLOW
1
Table of contents
Other SWR ENGINEERING Measuring Instrument manuals
Popular Measuring Instrument manuals by other brands
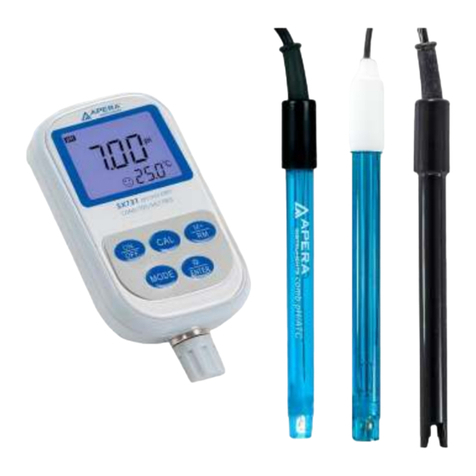
Apera Instruments
Apera Instruments SX731 user manual

Alcatel Vacuum Technology
Alcatel Vacuum Technology adixen AHC 2010 user manual

Water I.D.
Water I.D. Primelab 2.0 quick start
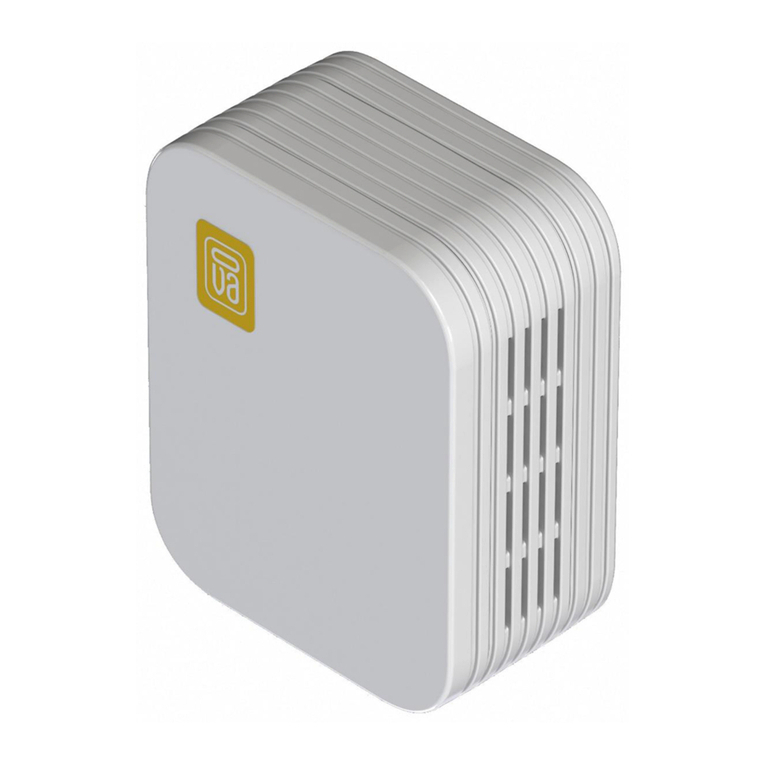
Nokeval
Nokeval Kombi-LoRaWAN manual
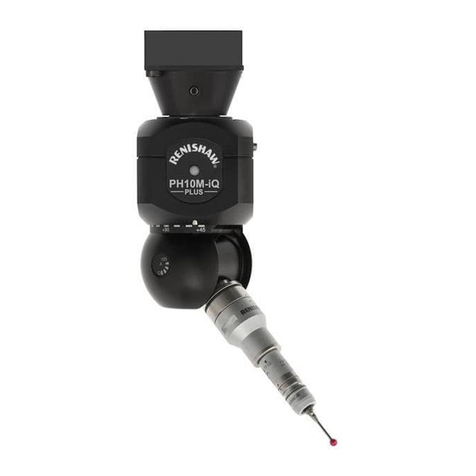
Renishaw
Renishaw PH10M-iQ PLUS Installation and user guide
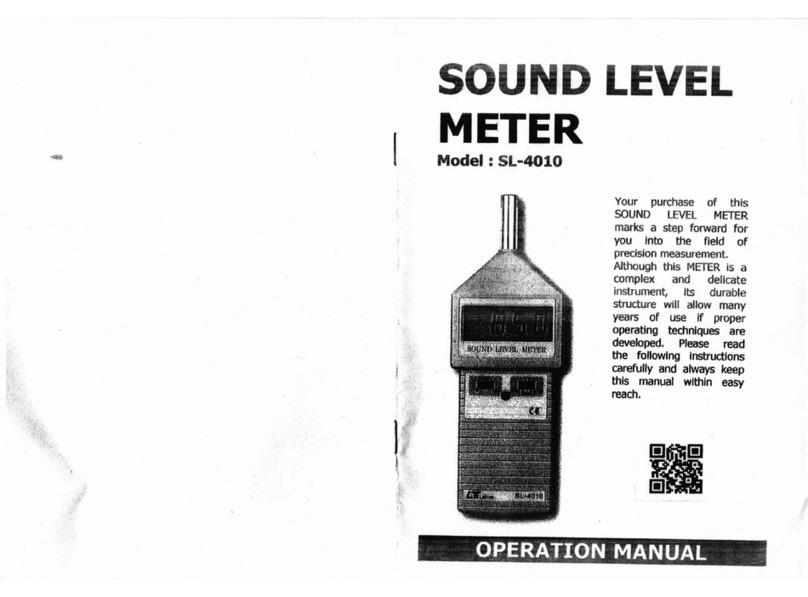
Lutron Electronics
Lutron Electronics SL-4010 Operation manual