SYNAPTICON SOMANET Node 400 User manual

Hardware Manuals
Documentation v 4.18.2 | Built 2022-01-12
© 2021 Synapticon GmbH

Table of Contents
1 Hardware Manuals
1.1 Handling instructions
1.1.1 Electrostatic discharge
1.1.2 Magnetic sensitive devices
1.2 SOMANET Circulo
1.2.1 Overview
1.2.1.1 Technical specifications
1.2.1.1.1 Power Specification
1.2.1.1.2 General Specification
1.2.1.1.3 Optional Integrated Encoders
1.2.1.1.3.1 Accuracy and repeatability of the integrated encoders
1.2.1.1.4 Optional Integrated Brake
1.2.1.1.5 Ordering information
1.2.1.2 Load cycle
1.2.1.3 Thermal Mounting Considerations
1.2.1.3.1 Current as a function of mounting temperature
1.2.1.3.2 Ambient air
1.2.1.4 Downloads
1.2.1.4.1 Documents
1.2.1.4.2 CAD Files
1.2.2 Installation Guide
1.2.2.1 Wiring instructions
1.2.2.1.1 Power and brake
1.2.2.1.1.1 Supply and phases
1.2.2.1.1.2 Connecting a brake
1.2.2.1.2 Encoders and IO
1.2.2.1.2.1 Encoder overview
1.2.2.1.2.2 Analog Input
1.2.2.1.2.3 Encoder ports
1.2.2.1.2.4 Digital IO
1.2.2.1.2.5 EtherCAT / STO-SBC IN & OUT
1.2.2.1.3 Analog input specification
1.2.2.1.3.1 Differential
1.2.2.1.3.2 Single-ended
1.2.2.1.4 Temperature sensor
8
14
14
15
16
20
23
23
23
25
27
28
29
30
31
32
34
35
35
35
36
37
39
39
42
44
44
45
46
51
53
58
58
59
60
Hardware Manuals
© 2021 Synapticon GmbH | Daimlerstraße 26 | D-71101 Schönaich Documentation v 4.18.2 | Built 2022-01-12 2/224

1.2.2.1.4.1 Specification for the single-ended temperature sensor input
1.2.2.1.5 Battery for Multi-Turn
1.2.2.1.5.1 Suitable batteries
1.2.2.1.6 EtherCAT-STO Cable
1.2.2.1.6.1 Overview
1.2.2.1.6.2 Pinout of the connectors
1.2.2.1.6.3 Instructions for manufacturing the cables
1.2.2.1.7 Maximum cable lengths
1.2.2.1.8 Mating parts
1.2.2.1.8.1 Connector details and mating part numbers
1.2.2.2 Mechanical integration
1.2.2.2.1 Circulo Mounting Example
1.2.2.2.1.1 Mounting the encoder disc
1.2.2.2.1.2 Mounting a hollow-shaft secondary bearing
1.2.2.2.1.3 Routing the motor phase cables
1.2.2.2.2 Dimensions and Drawings
1.2.2.2.2.1 Dimensions
1.2.2.2.2.2 Weight and inertia of the encoder rings
1.2.2.2.2.3 Drilling patterns
1.2.2.2.2.4 Mounting a bearing
1.2.2.2.2.5 Side view with phase connectors
1.2.2.2.3 Mounting encoder rings
1.2.2.2.3.1 Axial distance tolerances
1.2.2.2.3.2 Planar displacements
1.2.2.3 Encoder Calibration
1.2.2.3.1 Encoder accuracy
1.2.2.3.1.1 Narrow angle errors (encoder system-specific non-linearity)
1.2.2.3.1.2 Wide angle error (installation-dependent non-linearity)
1.2.2.3.1.3 Detecting the encoder non-linearity
1.2.2.3.2 Calibration Procedure
1.2.2.3.2.1 Prerequisite
1.2.2.3.2.2 Performing the procedure
1.2.2.3.2.3 Troubleshooting
1.2.2.3.2.4 Encoder system diagnostic
1.2.3 LED signals
1.2.3.1 Overview
1.2.3.1.1 Legend
1.2.3.2 Status LED
62
64
64
65
65
66
69
74
75
75
77
78
79
80
81
83
83
87
87
90
91
93
93
95
97
98
99
100
101
102
102
102
107
109
115
115
115
116
Hardware Manuals
© 2021 Synapticon GmbH | Daimlerstraße 26 | D-71101 Schönaich Documentation v 4.18.2 | Built 2022-01-12 3/224

1.2.3.2.1 Firmware
1.2.3.2.2 Bootloader
1.2.3.3 EtherCAT LED
1.2.4 Safety functions (STO-SBC)
1.2.4.1 Safety specifications
1.2.4.1.1 System requirements
1.2.4.1.2 Technical specifications
1.2.4.2 Safety connectors
1.2.4.3 Wiring the safety inputs
1.2.4.3.1 Cabling lenghts
1.2.4.3.2 Connection diagrams for the STO inputs
1.2.4.3.2.1 Manual switch + drives
1.2.4.3.2.2 Safety PLC PM (Plus-Minus output) + drives
1.2.4.3.2.3 Safety PLC PP (Plus-Plus output) + drives
1.2.4.3.3 Connection diagram for the brake
1.2.4.4 Using the safety functions
1.2.4.4.1 Timing diagrams
1.2.4.4.1.1 Timing diagram for STO-function without connected brake
1.2.4.4.1.2 Timing diagram for STO-function with SBC-function
1.2.4.4.2 Truth table for digital inputs
1.2.4.4.3 Diagnostic functions
1.2.4.4.3.1 Software diagnostics
1.2.4.4.4 STO-SBC status register
1.2.4.5 Examples for realising safety functions
1.2.4.5.1 Emergency stop
1.2.4.5.2 Stop category 1 emergency stop (Safe stop 1)
1.2.4.5.2.1 Prerequisites
1.2.4.5.2.2 Wiring
1.2.4.5.2.3 Configuration
1.2.4.5.2.4 Verification
1.2.4.5.3 Prevention of unexpected start-up
1.2.4.6 Commissioning and maintenance
1.2.4.6.1 Commissioning
1.2.4.6.2 Maintenance
1.2.4.7 Changelog of the safety-related documentation
1.3 SOMANET Node
1.3.1 SOMANET Node revisions
1.3.2 SOMANET Node rev. E.1
116
117
117
118
119
119
119
122
123
123
123
124
124
125
125
126
126
126
127
129
129
129
129
131
132
133
133
134
134
135
136
137
137
137
138
139
141
142
Hardware Manuals
© 2021 Synapticon GmbH | Daimlerstraße 26 | D-71101 Schönaich Documentation v 4.18.2 | Built 2022-01-12 4/224

1.3.2.1 Overview
1.3.2.1.1 Technical Specifications
1.3.2.1.1.1 Power Specifications
1.3.2.1.1.2 General specifications
1.3.2.1.2 Load cycle
1.3.2.1.3 Thermal mounting considerations
1.3.2.1.4 Downloads
1.3.2.1.4.1 Documents
1.3.2.1.4.2 CAD Files
1.3.2.2 Installation Guide
1.3.2.2.1 Wiring instructions
1.3.2.2.1.1 Overview of connectors
1.3.2.2.1.2 Power and brake
1.3.2.2.1.3 Encoders and IO
1.3.2.2.1.4 Connector details and mating parts numbers
1.3.2.2.2 Mounting instructions
1.3.2.2.2.1 Heat dissipation
1.3.2.2.2.2 Dimensions
1.3.2.2.2.3 Interference with magnetic fields
1.3.2.2.3 On-site installation guide (UL)
1.3.2.2.3.1 Branch fuse required
1.3.2.2.3.2 Field wiring terminal marking
1.3.2.2.3.3 Downloads
1.3.2.3 LED signals
1.3.2.3.1 Overview
1.3.2.3.1.1 Legend
1.3.2.3.2 Core LED
1.3.2.3.2.1 Firmware
1.3.2.3.2.2 Bootloader
1.3.2.3.3 Drive LED
1.3.2.3.4 Com LED
1.3.2.4 SOMANET Node Safety (Original instructions)
1.3.2.4.1 Dimensions
1.3.2.4.2 Specifications of the safety functions
1.3.2.4.2.1 System requirements
1.3.2.4.2.2 Technical specifications
1.3.2.4.2.3 Block diagram
1.3.2.4.3 Setup of the safety functions
143
144
144
144
147
148
150
150
150
151
152
152
153
158
167
168
168
168
170
171
171
172
173
174
174
174
175
175
176
176
177
178
179
180
180
180
182
183
Hardware Manuals
© 2021 Synapticon GmbH | Daimlerstraße 26 | D-71101 Schönaich Documentation v 4.18.2 | Built 2022-01-12 5/224

1.3.2.4.3.1 Connecting the STO/SBC inputs
1.3.2.4.3.2 Connection diagram for the brake
1.3.2.4.3.3 Connector mating parts and cable lengths
1.3.2.4.4 Using the safety functions
1.3.2.4.4.1 Timing diagrams
1.3.2.4.4.2 Truth table for digital inputs
1.3.2.4.4.3 Diagnostic functions
1.3.2.4.4.4 STO-SBC status register
1.3.2.4.5 Examples for realising safety functions
1.3.2.4.5.1 Prevention of unexpected start-up
1.3.2.4.5.2 Stop category 0 (STO)
1.3.2.4.5.3 Stop category 1 (SS1)
1.3.2.4.6 Commissioning and maintenance
1.3.2.4.6.1 Commissioning
1.3.2.4.6.2 Maintenance
1.3.2.4.7 Changelog of the safety-related documentation
1.4 SOMANET Accessories
1.4.1 SOMANET Braking Chopper 48V 500W
1.4.1.1 Overview
1.4.1.2 Technical Specs
1.4.1.3 Installing the module and setting the threshold voltage
1.4.1.4 Connecting the Board to DC-BUS
1.4.1.4.1 Suitable cables
1.4.1.4.2 Wiring
1.4.1.5 Failsafe Behavior
1.4.1.6 Multi-board option
1.4.1.7 LED
1.4.1.8 Dimensions
1.4.2 Sin/Cos Encoder Cable Adapter
1.4.2.1 Overview
1.4.2.2 Block Diagram
1.4.2.3 Connectors
1.4.2.3.1 Encoder Connector Top
1.4.2.3.2 Encoder Connector Bottom
1.4.2.3.3 Interface Connector
1.4.2.4 Mounting remarks
1.4.2.5 Strain relief
1.4.2.6 Soldered cables
184
187
189
190
190
193
193
194
196
196
196
197
200
200
200
201
202
203
203
204
205
206
206
206
207
207
208
209
210
210
210
211
211
212
212
213
214
214
Hardware Manuals
© 2021 Synapticon GmbH | Daimlerstraße 26 | D-71101 Schönaich Documentation v 4.18.2 | Built 2022-01-12 6/224

1.4.3 Industrial I/O Cable Adapter
1.4.3.1 Overview
1.4.3.2 Block diagram
1.4.3.3 Pinouts
1.4.3.4 Connector details and mating parts
1.4.3.5 Strain relief
1.4.3.6 Soldered cables
1.4.3.7 Attaching the adapter
1.4.4 ABI/BiSS Encoder Cable Adapter
1.4.4.1 Overview
1.4.4.2 Block Diagram
1.4.4.3 Connectors
1.4.4.3.1 Encoder Connector Top
1.4.4.3.2 Encoder Connector Bottom
1.4.4.3.3 Interface Connector
1.4.4.4 Mounting remarks
1.4.4.5 Strain relief
1.4.4.6 Soldered cables
1.4.4.7 Downloads
215
215
215
217
217
218
219
219
220
220
220
221
221
222
222
223
224
224
224
Hardware Manuals
© 2021 Synapticon GmbH | Daimlerstraße 26 | D-71101 Schönaich Documentation v 4.18.2 | Built 2022-01-12 7/224

1 Hardware Manuals
Attention
When dealing with electronic devices, always consider these handling instructions!
SOMANET Circulo
The SOMANET Circulo series is a combination of servo drive, position feedback sensor (encoder), mechanical
integration solution, providing a pin brake and safe motion option, specifically designed for collaborative
robot (cobot) joints and smart actuators.
Overview Circulo
Technical specifications
Load cycle
Thermal considerations
Downloads
Installation guide
Wiring instructions
Power and brake
Encoders and IO
Analog input specification
Temperature sensor
Battery for Multi-Turn
EtherCAT-STO Cable
Maximum cable lengths
Mating parts
Mechanical integration
Mounting Example
Dimensions
Mounting encoder rings
Thermal Mounting Considerations
Encoder calibration
Encoder accuracy
Calibration Procedure
LED signals
Hardware Manuals
© 2021 Synapticon GmbH | Daimlerstraße 26 | D-71101 Schönaich Documentation v 4.18.2 | Built 2022-01-12 8/224

Safety functions (STO-SBC)
Specifications of the safety functions
Safety connectors
Wiring the safety inputs
Using the safety functions
Examples for realising safety functions
Emergency stop
Stop category 1 emergency stop (Safe stop 1)
Prevention of unexpected start-up
Commissioning and maintenance
Changelog of the safety-related documentation
Note
Please note that previously released samples of SOMANET Circulo were available which differed in
several aspects, such as pin-out and dimensions.
Sample B.1
Hardware Manuals
© 2021 Synapticon GmbH | Daimlerstraße 26 | D-71101 Schönaich Documentation v 4.18.2 | Built 2022-01-12 9/224

Overview Circulo Sample B.1
Technical specifications
Installation guide
Wiring instructions
Power and brake
Encoders and IO
Temperature sensor
EtherCAT-STO Cable
Mating parts
Dimensions and mechanical mounting
Mounting encoder rings
Mounting a bearing
Encoder accuracy
Encoder Calibration
LED signals
Safety functions (STO-SBC)
Specifications of the safety functions
Safety connectors
Wiring the safety inputs
Using the safety functions
Examples for realising safety functions
Emergency stop
Stop category 1 emergency stop (Safe stop 1)
Prevention of unexpected start-up
Commissioning and maintenance
Changelog of the safety-related documentation
Hardware Manuals
© 2021 Synapticon GmbH | Daimlerstraße 26 | D-71101 Schönaich Documentation v 4.18.2 | Built 2022-01-12 10/224

Sample A.2
Overview Circulo Sample A.2
Technical specifications
Installation guide
Wiring instructions
Power supply and motor brake
Encoders and IO
Temperature sensor
Mating parts and encoder battery
Dimensions and mechanical mounting
Mounting encoder rings
Encoder accuracy
LED signals
Safety functions (STO-SBC)
Specifications of the safety functions
Wiring the safety inputs
Using the safety functions
Commissioning and maintenance
SOMANET Node
Note
Different revisions and sizes of SOMANET Node are available which differ in their specifications as well
as in their pinouts. If you are not sure about the revision of your servo drive please check our revision
guide
Hardware Manuals
© 2021 Synapticon GmbH | Daimlerstraße 26 | D-71101 Schönaich Documentation v 4.18.2 | Built 2022-01-12 11/224

Revision E.1
Overview Node E.1
Technical specifications
Load cycle
Thermal considerations
Downloads
Hardware diagrams
Installation guide
Wiring instructions
Power and brake
Encoders and IO
Connector types and mating parts numbers
Mounting instructions
On-site installation guide (UL)
LED signals
Safety functions (STO-SBC)
Specifications of the safety functions
Setup of the safety functions
Using the safety functions
Examples for realising safety functions
Commissioning and maintenance
Changelog of the safety-related documentation
Revision D.3/D.4
Overview Node D.3/4
Technical specifications
Hardware diagrams
Installation guide
Wiring instructions
Connector pinouts
Grounding and connecting a brake
Mounting instructions
LED signals
Hardware Manuals
© 2021 Synapticon GmbH | Daimlerstraße 26 | D-71101 Schönaich Documentation v 4.18.2 | Built 2022-01-12 12/224

Revision C.4
Overview Node C.4
Technical specifications
Hardware diagrams
Installation guide
Wiring instructions
Connector pinouts
Grounding and connecting a brake
Mounting instructions
LED signals
SOMANET Accessories
SOMANET Braking Chopper 48V 500W
Sin/Cos Encoder Cable Adapter
Industrial I/O Cable Adapter
ABI/BiSS Encoder Cable Adapter
Hardware Manuals
© 2021 Synapticon GmbH | Daimlerstraße 26 | D-71101 Schönaich Documentation v 4.18.2 | Built 2022-01-12 13/224

1.1 Handling instructions
1.1.1 Electrostatic discharge
All our products are sensitive electronic devices, please respect the following guidelines when handling them.
Attention
Static electricity can damage electronic devices and your system. To avoid damage, keep static-
sensitive devices in their static-protective bags until you are ready to install them.
To reduce the possibility of electrostatic discharge, observe the following precautions:
Wear ESD protection gear such as wrist bands, ESD gloves, ESD shoes or use ESD-mats.
Limit your movement. Movement can cause static electricity to build up around you.
Handle the device carefully, holding it by its edges or frame.
Do not touch solder joints, pins, or exposed printed circuitry.
Do not leave the device where others can handle and possibly damage the device.
While the device is still in its anti-static bag, touch it to an unpainted metal part of the system unit for at
least 2 seconds. (This action removes static electricity from the package and from your body).
Remove the device from its package and install it directly into your system, without putting it down. If it is
necessary to put the device down, place it onto its static-protective bag. (If your device is an adapter, place
it component-side up.) Do not place the device onto the cover of the system or onto a metal table.
Take additional care when you handle devices during cold weather. Indoor humidity tends to decrease in
Hardware Manuals
© 2021 Synapticon GmbH | Daimlerstraße 26 | D-71101 Schönaich Documentation v 4.18.2 | Built 2022-01-12 14/224

cold weather, causing an increase in static electricity.
1.1.2 Magnetic sensitive devices
The encoder rings of “Sense” products are magnetized with a magnetic pattern that can be changed by
various influences.
Special precautions must be taken to maintain the quality of the magnetic pattern permanently:
Remove all strong magnets near the encoder rings - the stronger the magnet, the higher the risk of
damage.
Keep strong magnets away from the encoder rings even for short moments. The farther away, the lower
is the effect on the rings.
Make sure that no contact can occur between the encoder rings and strong permanent magnets or
electromagnets during assembly.
Avoid all materials between the encoder ring and, for example, a magnetic brake, being magnetic.
When storing, supplying and picking parts, make sure the encoder rings are not transported or stored
with other magnets. This includes permanent magnets for electric motors.
Remove all tools with magnetic properties from the assembly area, including magnetized screwdrivers
(often indicated by a black tip).
Do not use magnet holders or handling magnets for the encoder rings.
Remove all bags or garments with magnetic closures when working with the encoders rings.
Avoid possible inductances caused by high voltage power lines near the encoder rings.
Do not store encoder rings in a contiguous way as this may cause magnetic interference.
Observe the minimal distance between the rings of 5 mm.
Hardware Manuals
© 2021 Synapticon GmbH | Daimlerstraße 26 | D-71101 Schönaich Documentation v 4.18.2 | Built 2022-01-12 15/224

1.2 SOMANET Circulo
The SOMANET Circulo series is a combination of servo drive, position feedback sensor (encoder), mechanical
integration solution, providing a pin brake and safe motion option, specifically designed for collaborative
robot (cobot) joints and smart actuators.
Attention
When dealing with electronic devices, always consider these handling instructions!
Overview Circulo
Technical specifications
Load cycle
Thermal considerations
Downloads
Installation guide
Wiring instructions
Power and brake
Encoders and IO
Analog input specification
Temperature sensor
Battery for Multi-Turn
EtherCAT-STO Cable
Maximum cable lengths
Mating parts
Mechanical integration
Mounting Example
Dimensions
Mounting encoder rings
Thermal Mounting Considerations
Encoder calibration
Encoder accuracy
Calibration Procedure
LED signals
Safety functions (STO-SBC)
Specifications of the safety functions
Safety connectors
Hardware Manuals
© 2021 Synapticon GmbH | Daimlerstraße 26 | D-71101 Schönaich Documentation v 4.18.2 | Built 2022-01-12 16/224

Wiring the safety inputs
Using the safety functions
Examples for realising safety functions
Emergency stop
Stop category 1 emergency stop (Safe stop 1)
Prevention of unexpected start-up
Commissioning and maintenance
Changelog of the safety-related documentation
Note
Please note that previously released samples of SOMANET Circulo were available which differed in
several aspects, such as pin-out and dimensions.
Sample B.1
Hardware Manuals
© 2021 Synapticon GmbH | Daimlerstraße 26 | D-71101 Schönaich Documentation v 4.18.2 | Built 2022-01-12 17/224

Overview Circulo Sample B.1
Technical specifications
Installation guide
Wiring instructions
Power and brake
Encoders and IO
Temperature sensor
EtherCAT-STO Cable
Mating parts
Dimensions and mechanical mounting
Mounting encoder rings
Mounting a bearing
Encoder accuracy
Encoder Calibration
LED signals
Safety functions (STO-SBC)
Specifications of the safety functions
Safety connectors
Wiring the safety inputs
Using the safety functions
Examples for realising safety functions
Emergency stop
Stop category 1 emergency stop (Safe stop 1)
Prevention of unexpected start-up
Commissioning and maintenance
Changelog of the safety-related documentation
Hardware Manuals
© 2021 Synapticon GmbH | Daimlerstraße 26 | D-71101 Schönaich Documentation v 4.18.2 | Built 2022-01-12 18/224

Sample A.2
Overview Circulo Sample A.2
Technical specifications
Installation guide
Wiring instructions
Power supply and motor brake
Encoders and IO
Temperature sensor
Mating parts and encoder battery
Dimensions and mechanical mounting
Mounting encoder rings
Encoder accuracy
LED signals
Safety functions (STO-SBC)
Specifications of the safety functions
Wiring the safety inputs
Using the safety functions
Commissioning and maintenance
Hardware Manuals
© 2021 Synapticon GmbH | Daimlerstraße 26 | D-71101 Schönaich Documentation v 4.18.2 | Built 2022-01-12 19/224

1.2.1 Overview
The SOMANET Circulo series is a combination of servo drive, position feedback sensor (encoder), mechanical
integration solution, providing a pin brake and safe motion option, specifically designed for collaborative
robot (cobot) joints and smart actuators.
Attention
When dealing with electronic devices, always consider these handling instructions!
Hardware Manuals
© 2021 Synapticon GmbH | Daimlerstraße 26 | D-71101 Schönaich Documentation v 4.18.2 | Built 2022-01-12 20/224
Other manuals for SOMANET Node 400
3
This manual suits for next models
5
Table of contents
Other SYNAPTICON Servo Drive manuals
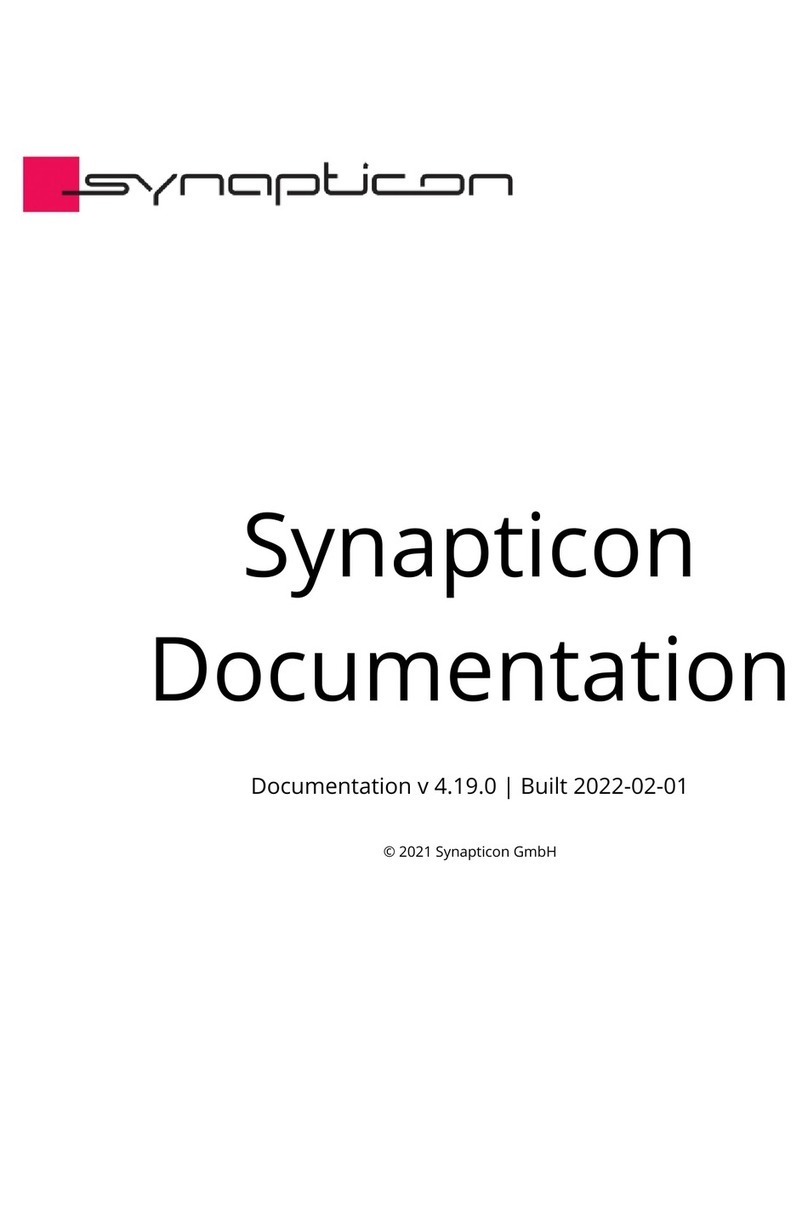
SYNAPTICON
SYNAPTICON SOMANET Circulo 7 Operator's manual
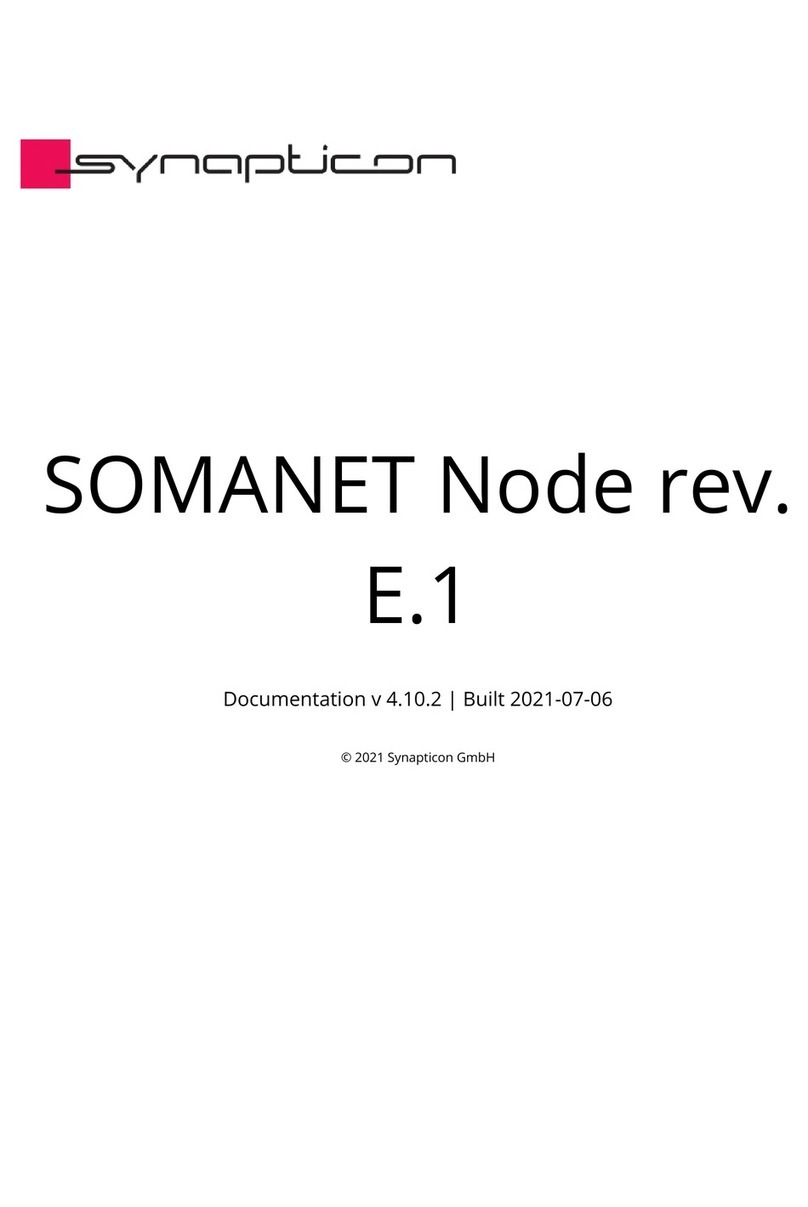
SYNAPTICON
SYNAPTICON SOMANET Node 400 User manual

SYNAPTICON
SYNAPTICON SOMANET Circulo 7 User manual
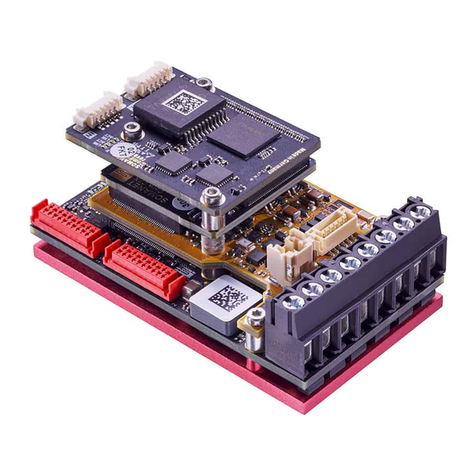
SYNAPTICON
SYNAPTICON SOMANET User manual
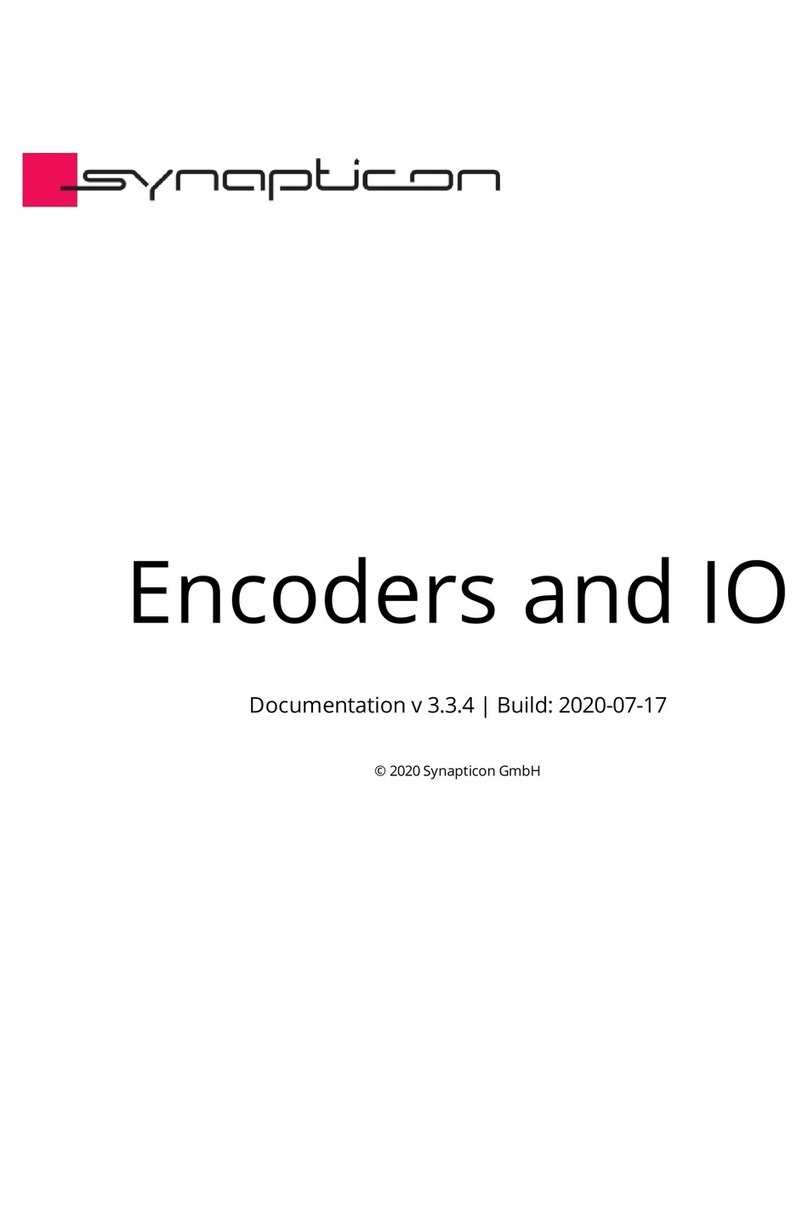
SYNAPTICON
SYNAPTICON SOMANET Circulo Series User manual
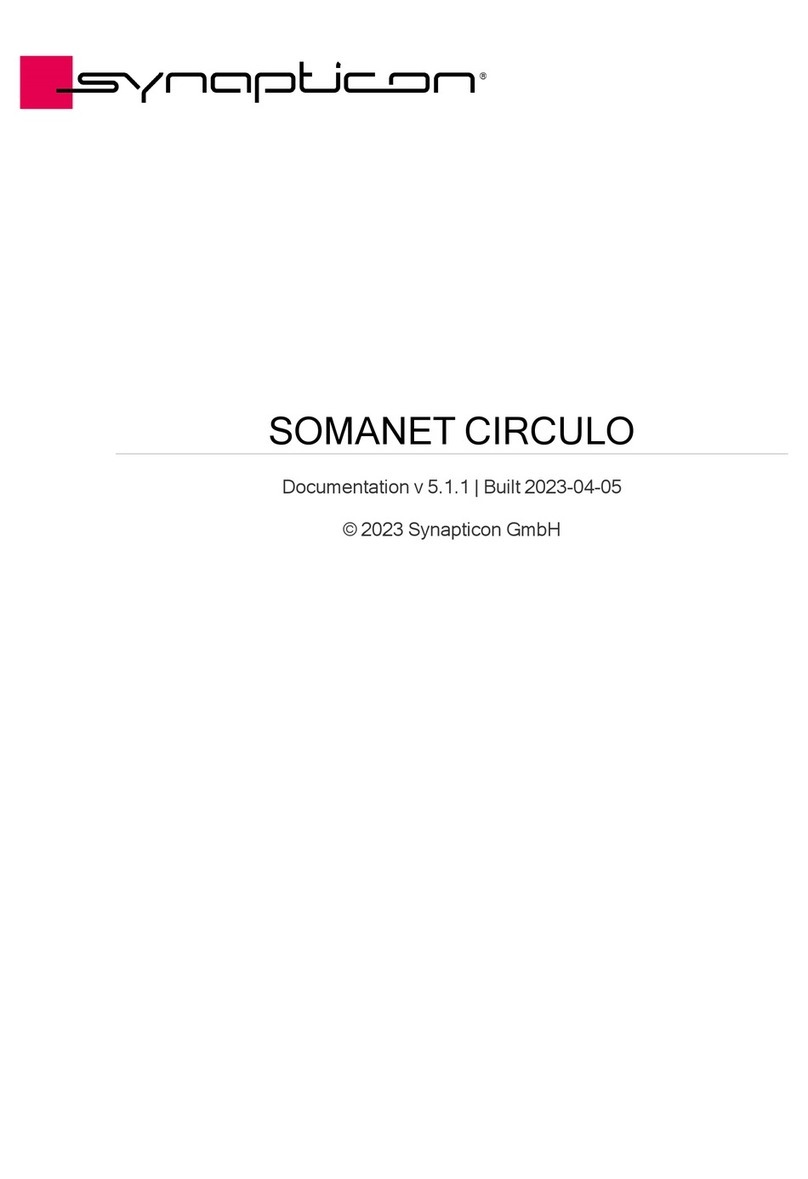
SYNAPTICON
SYNAPTICON SOMANET Circulo 7 User manual
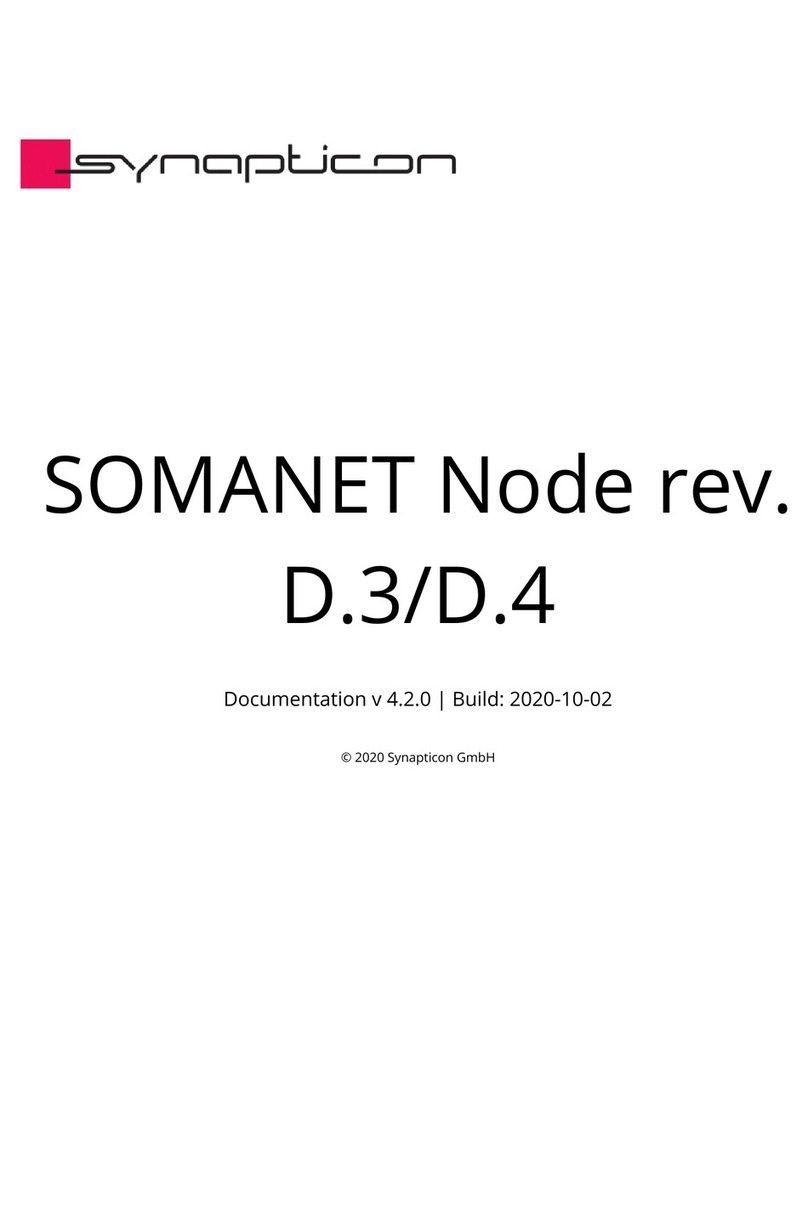
SYNAPTICON
SYNAPTICON SOMANET Node 400 Operator's manual
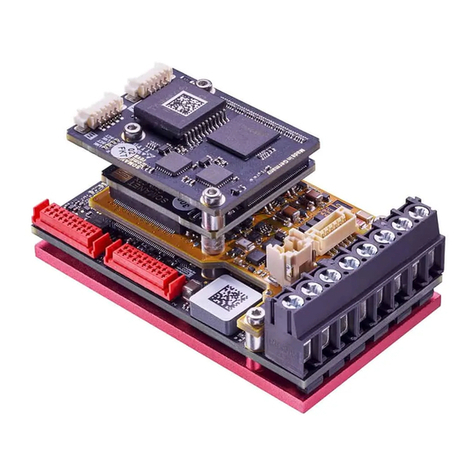
SYNAPTICON
SYNAPTICON SOMANET Node 400 User manual
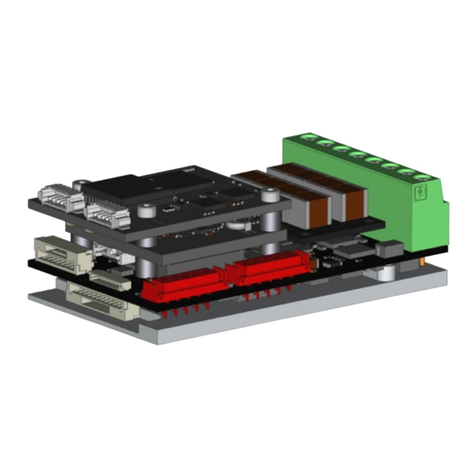
SYNAPTICON
SYNAPTICON SOMANET Node User manual
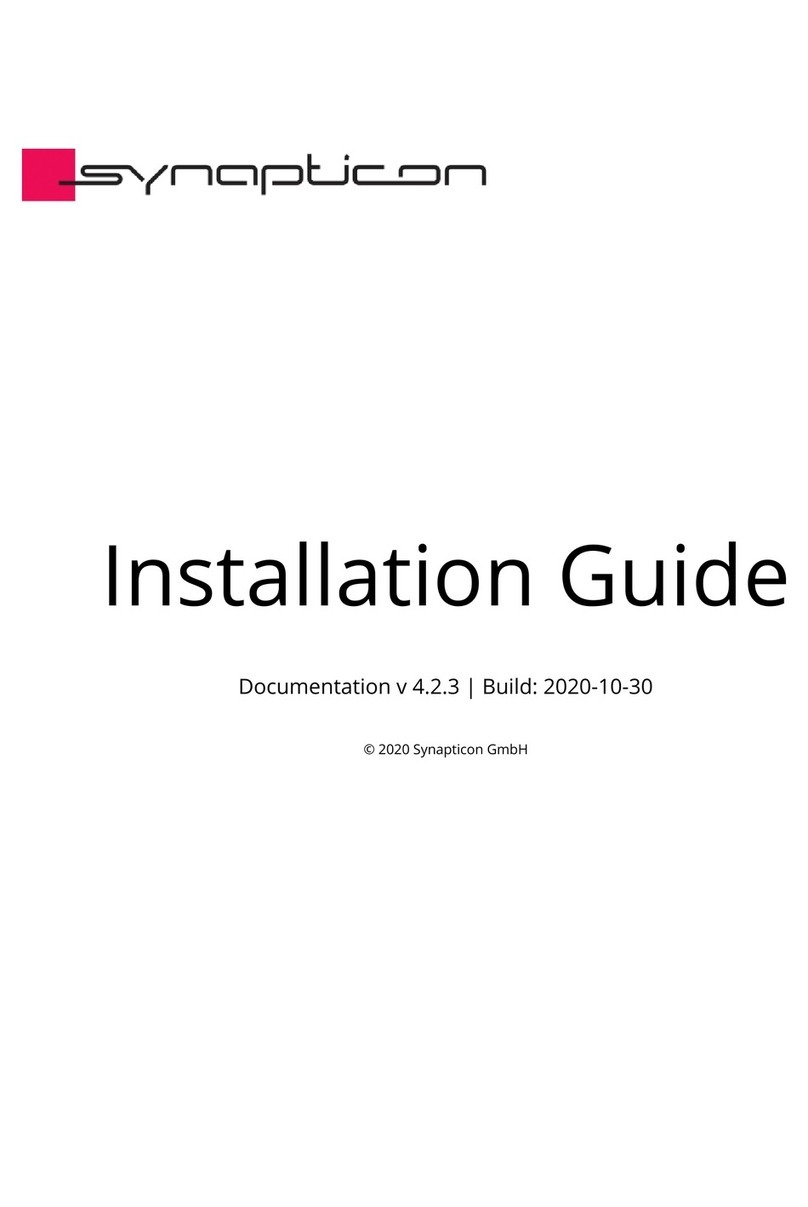
SYNAPTICON
SYNAPTICON SOMANET Circulo Series User manual